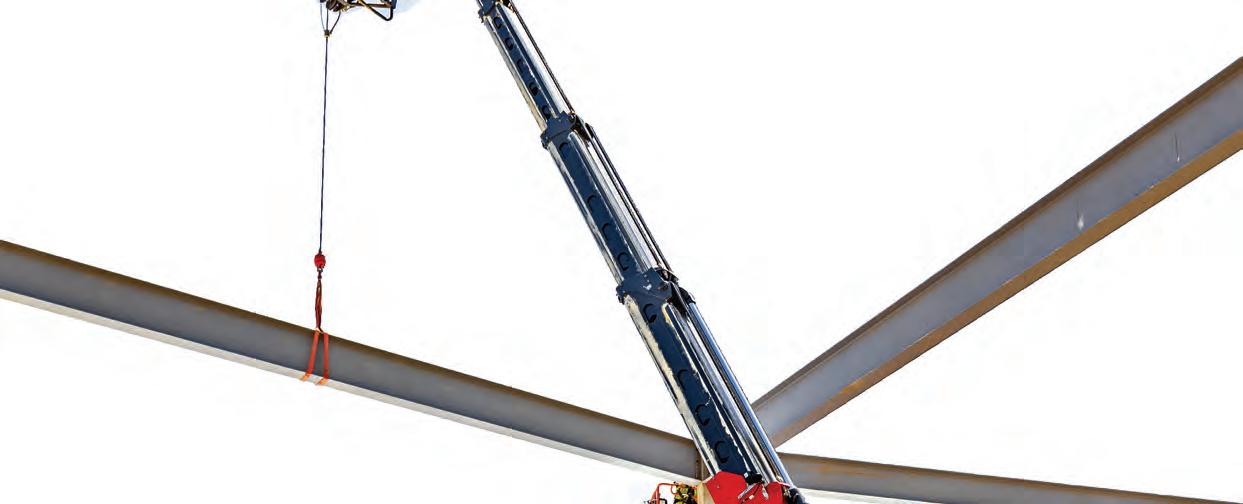
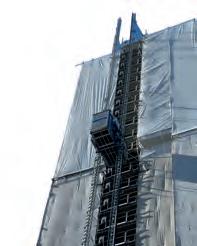
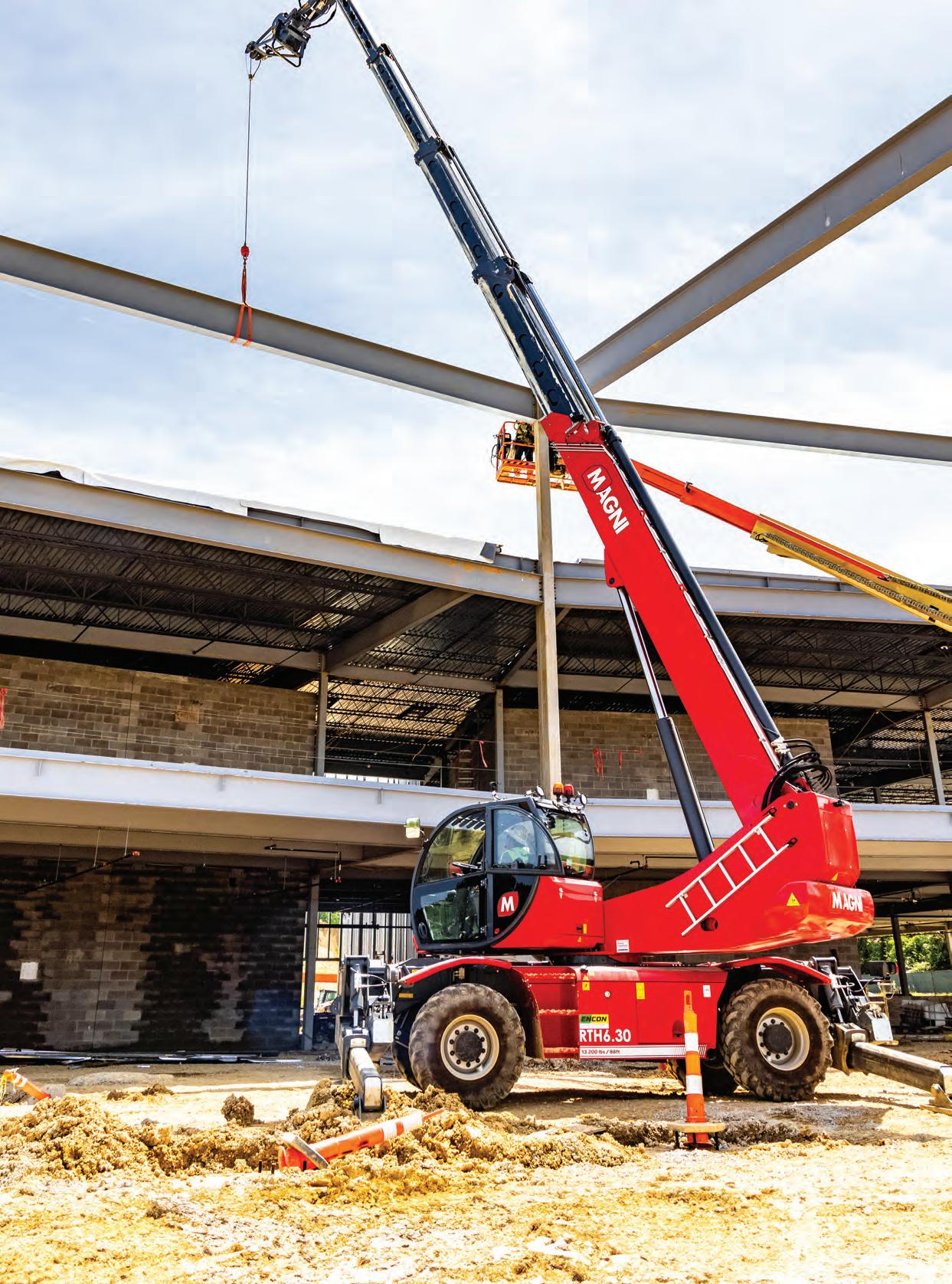
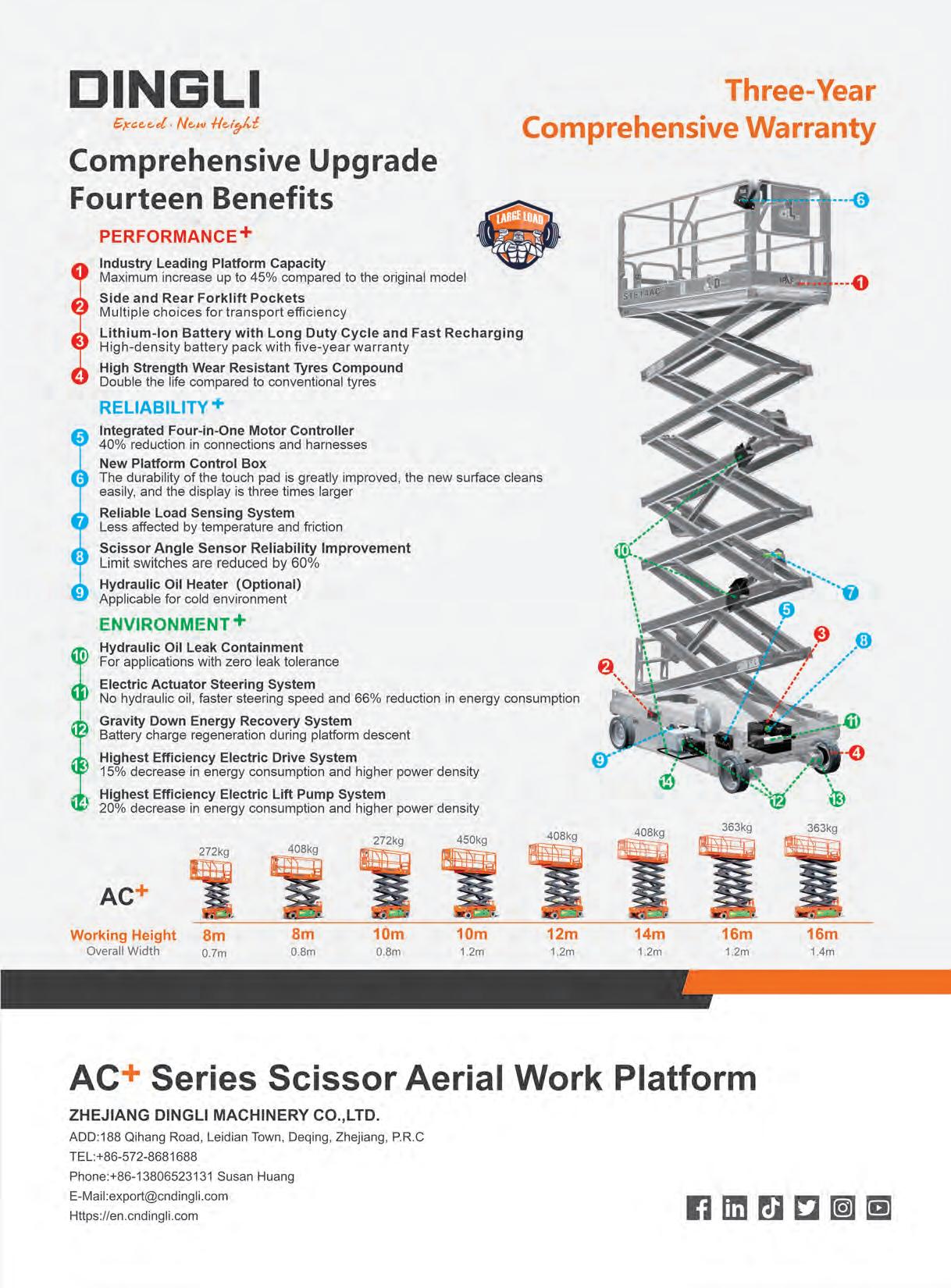
Editor:
Lindsey Anderson 517-420-0918
lindsey.anderson@khl.com
Group editors:
Andy Brown, D.Ann Shiffler, Leila Steed, Euan Youdale
Director of content: Murray Pollok
Client success & delivery manager: Charlotte Kemp charlotte.kemp@khl.com
Client success & delivery team:
Ben Fisher, Olivia Radcliffe, Alex Thomson
Group design manager: Jeff Gilbert
Group designer: Jade Hudson
Event manager: Steve Webb
Event design manager: Gary Brinklow
Creative designer: Kate Brown
Audience development manager: Anna Philo anna.philo@khl.com
Circulation executive: Vicki Rummery vicki.rummery@khl.com
Admin assistants: James Dick-Cleland, Maria McCarthy, Hannah Parry
Vice president sales –global rental and access division
Tony Radke 480 478 6302 tony.radke@khl.com
Vice president global sales: Alister Williams 843 637 4127 alister.williams@khl.com
Accounts assistant: Emily Roberts
Client success & digital director: Peter Watkinson peter.watkinson@khl.com
Facilities & HR administrator: Philippa Smith philippa.smith@khl.com
Chief executive officer: James King
Chief financial officer: Paul Baker
Chief operating officer: Trevor Pease
It seems like not too long ago, major industry technological advancements consisted of rental software or telematics debuts that boasted GPS-enabled fencing and tracking. It was a new era for fleet owners who could now keep equipment on sites from being stolen.
We’ve come leaps and bounds since those early digital adaption days.
Words and phrases like, “artificial intelligence,” “robots,” “augmented reality” and “autonomous equipment” are becoming more commonplace when talking about everything from machine design to training. Access equipment and fleets are smarter than ever, with many “connected” for maintenance, fleet availability and general monitoring – across machines and rental yards.
“There’s a lot of talk about ‘the jobsite of the future’ — a place and time where electrification, autonomous technology and intelligent processes combine to drive efficiencies, maximize safety and increase overall productivity,” said Rogerio dos Santos, JLG’s vice president of strategy and product management. “These ideals may seem like a far-off concept that’s years away. But, in reality, as the industry continues to take steps towards connection and optimization, that future has already arrived. This transition is transpiring in stages with ‘moments of autonomy.’ It’s not going to be like one day you’re on a totally disconnected job site, and the next day, it’s completely a new world — it is actually happening now.”
I recently spoke with dos Santos and Joel Honeyman, Doosan Bobcat’s vice president of global innovation, about what the actual state of autonomy is like right now within the access and telehandler industries. Both had loads of insights to share, from the small components that lend themselves to bigger solutions, to current developments on recent partnerships and news.
“We think of technology related to electrification, autonomy and advanced connectivity as building blocks,” said Honeyman. “We are working across different areas because it’s not ‘one-size-fits-all.’ These things are coming together under a strategy, but the solutions are unique depending on the vehicle and the application.”
To read more about how these building blocks are actually being utilized in the present, read our piece on autonomous equipment and solutions in this issue.
We also feature our annual AERIALS20 ranking of North America’s largest access equipment rental fleets. Despite recent news of some rental firms reducing their CapEx guidance for the remainder of their fiscal year, the AERIALS20 reflects another steady increase in fleets year-overyear. Healthy growth is seen from the top to bottom, and many rental companies have reported they expect continued momentum in the market due to mega project activity, data center construction and the IIJA.
To see who made the top 5 – and the entire ranking – check out page 15. Thanks for reading.
The 661/992 lbs dual capacity design for enhanced productivity.
Swing out engine tray for easy access and maintenance.
Proportional control ensures smooth driving, precise positioning and comfortable operation.
Self-leveling platform together with hydraulic platform rotation delivers exceptional productivity.
Intelligent self-diagnostic system for quick troubleshooting.
Former Home Depot executive Matt Schweickert has joined the board of directors at BigRentz. KHL Editor Jenny Lescohier sits down with him to get the scoop.
The proof is in the (numbers) pudding. This year’s AERIALS20 toplist shows solid growth for North American access rental fleets. ALH reports on market drivers and coming expectations..
JLG telehandler sales soar; Genie sees ‘healthy’ demand; Manitou forecasts slower half; Merger creates largest Texas independent; ARA downgrades growth forecast; United updates forecast; Sunbelt ‘outperforms’ market; H&E expects lowered activity; New N.A. VP for IPAF; BigRentz brings on Home Depot exec; plus Events, Highlights, By the Numbers and more.
MEWPs hit high prices at Euro Auctions; Kranpunkten further invests in going ‘green;’ Pearson retires from access; plus Highlights and more.
Through a joint venture with the Scaffold & Access Industry Association, KHL Group acquired Scaffold & Access Magazine in late 2021. Readers will find SA as a standalone publication located within the middle of Access, Lift & Handlers
MEMBER OF
Another round of speakers have been confirmed for Access, Lift & Handlers' and IPAF’s Working at Height Conference on November 20. Lindsey Anderson reports.
Operator-less machinery? Robots completing repetitive tasks? Lindsey Anderson takes a look at how today’s technology is shaping tomorrow’s equipment.
Rotating telehandlers are changing the landscape of construction. ALH speaks with manufacturers on their latest launches and developments.
28
New technologies paired with compact designs are fueling the latest developments within the truck-mount sector. Lindsey Anderson and Euan Youdale report.
IPAF appoints Randy Marzicola; IPAF’s ePAL app updated; OSHA’s Safe & Sound Week 2024; Updates to IPAF's service, inspection and maintenance of MEWPs leaflet.
To subscribe to Access, Lift & Handlers or any magazine in the KHL portfolio, go to: www.khl.com/subscriptions.
Rotating telehandlers, like this Magni unit, continue to gain market share from contractors and rental companies alike in North America. See our report on page 24 for more.
Access and telehandler sales across North America helped boost JLG’s Q2 results to $1.41 billion, up 5.9 percent year-over-year for the three months ending June 30, parent company Oshkosh Corp. has announced.
JLG’s operating income in the second quarter increased 16.4 percent to $246.5 million, or 17.5
percent of sales, compared to $211.7 million, or 15.9 percent of sales, in the second quarter of 2023. The increase was primarily due to higher sales volumes across North America, favorable price/cost dynamics and improved sales mix, offset in part by increased selling, general and administrative costs, the company said.
Telehandler sales hit record numbers for JLG during its second quarter results this year.
Sept. 11-12
VERTIKAL DAYS
Newark Showground, UK www.vertikaldays.net
Sept. 30 – Oct. 4
SAIA ANNUAL CONVENTION & EXPOSITION Denver, CO www.saiaonline.org
Oct. 1-2
POWER PROGRESS SUMMIT Chicago, IL www.dieselprogresssummit.com
Nov. 19-20
WORKING AT HEIGHT CONFERENCE & AWARDS Nashville, TN www.workingatheightevent.com
Nov. 25
IRC ASIA Shanghai, China www.khl-irc.com
Breaking down the sector, aerial sales for Q2 totaled $675.6 million, a 1.5 percent increase, while telehandler sales amounted to $428.6 million, which represents the strongest quarter of telehandler sales for JLG in recent history.
Despite the growth and high demand, the company noted its Q2 orders were lower than expected, but attributed it to the “normalizing of market conditions.” The company added it expects Q3 access sales to be lower, but is forecasting “a
significant increase in Q4.”
“As we look forward, we have a positive outlook for 2025,” said John Pfeifer, president and chief executive officer of Oshkosh.
“Based on discussions with
customers and our expectations for ongoing infrastructure investments, mega projects, industrial onshoring and current fleet age, we expect [JLG] sales in 2025 to be in the range of 2024 sales.” ■
Terex Corp’s aerial work platform division, Genie, posted a 6.9 percent increase in second quarter revenues to $882 million, driven by continued “healthy demand” in North America.
The Genie backlog reduced significantly in the quarter to $1.82 billion compared to $2.4 billion in the previous quarter and from $2.8 billion in the same period in 2023.
The backlog has fallen from
Rental companies Synergy Equipment and Opifex Enterprises have announced they will merge.
The deal will see Avance Investment Management, a private investor that first invested in Synergy in 2022, acquire Opifex.
It will also create the largest independent equipment rental company in the markets of Florida and Texas in the process.
Founded in 2018, Opinex is headquartered in Austin, TX, and also has locations in San Antonio and Bryan-College Station. It operates a fleet that includes aerial platforms, forklifts, excavators, pumps and wheel loaders.
Meanwhile, Synergy was established in 2012 in Tampa, FL, to focus on all segments of the Florida market. The company operates 17 branches across the state of Florida, five in Georgia and one in Alabama.
Genie's 2024 revenues are now expected to be in the $3.15-$3.25 billion range, up from the previous outlook of $3.0-3.1 billion.
the peaks of $2.8-$3.0 billion in 2022 and early 2023, but remains significantly higher than the preCovid levels of around $700 million.
Operating profit for the AWP division was $133.8 million, almost identical to 2023, although the profit margin was down from 16.2 percent to 15.2 percent of net sales, impacted by “start-up inefficiencies” relating to the new production facility in Monterrey, Mexico.
Terex said its aerials division continued to benefit from megatrends such as investment in data centers, electrification of power grids and U.S. federal infrastructure investment. ■
Manitou has reported a positive half year, set against a slower than expected increase in U.S. production, and says the performance will not be repeated in the rest of the year.
Group sales were stable at €1.4 billion, amounting to a 0.4 percent
increase on the first six months in 2023, while operating income saw a big rise of 44.7 percent to €127.5 million, comparted to the same period in 2023.
Michel Denis, President & CEO, said, “The group closes a very good half-year in a context of contrasting
■ Bobcat Company has completed a $3.26 million renovation at its Buford, GA, location, which is home to its North American material handling sales, service, marketing, parts and logistics departments. China-based access equipment manufacturer Sinoboom has held a groundbreaking ceremony at Silao, Mexico, for its new factory. The company also announced the appointment of Ian Pratt, who will head up its new Telescopic Handler Business Unit, which includes the manufacturer’s first three models, launched in April.
■ Global Lift Makina Türkiye has become the official dealer for Genie in Turkey. The company has been an Authorized Service Provider (ASP) for Genie since 2018 and has acted as a Genie dealer since 2020.
■ H&E Rentals (H&E) has opened a number of new branches, including locations in: Frederick, MD, Cedar Rapids, IA and Springfield, MO. H&E has opened 24 new branches across the U.S. Visit www. accessbriefing.com for details.
The American Rental Association (ARA) is forecasting slower growth this year in the U.S. and Canada for equipment rental.
According to the ARA, construction and general tool rental in the United States is softening, and will now see an 8.9 percent increase in revenue in 2024, totaling $78.7 billion and 5.3 percent growth in 2025.
This is a decrease from the ARA’s projection in the previous quarter that revenue would rise 9.7 percent this year, totaling $79.2 billion.
Broken down by segment, construction and industrial rental revenue (CIE) is projected to be $62.3 billion, while general tool hire has been readjusted to $16.4 billion.
“While the rental industry and opportunities continue to expand, we are experiencing softer growth,” said Tom Doyle, ARA vice president, program development. “The ARA quarterly survey results confirm this softening.”
33
Depots opened by Sunbelt in Q1
-0.2%
Fall in July U.S. construction spending according to the ABC
$6.1 billion
China’s investment into data center projects for betterplaced storage
6.6% ARA's expected growth for Canadian equipment rental
the forecast for construction and industrial had not changed much since last quarter.
“The market is still doing well but slowing. Next year’s GDP growth is lower than trend at 1.6 percent growth, the trend is around 2.1 percent. The overall view of rental is positive moving forward, but there is uncertainty out there.” ■ Construction rental revenue is projected to be $62.3 billion this year, according to
activity and outlook.
[This was] driven by a stronger than expected momentum in Southern Europe, growth in Europe offset the decline in North America.
Scott Hazelton, managing director at S&P Global, added that
United Rentals has narrowed its forecast for the 2024 financial year and said that it remains well placed to capitalize on opportunities for long-term growth.
The company now expects revenue for the year to be in the region of $15 billion to $15.3 billion, a revision of its previous guidance
of between $14.95 billion and $15.45 billion.
EBITDA has also been revised and is now expected to be between $7.09 billion to $7.24 billion.
Meanwhile, the company expects to maintain its previously announced capital expenditure for the year of up to $2.3 billion. ■
-1.24%
slower than expected ramp-up of our U.S. industrial capacities, both of which we are gradually rectifying.”
“Our ambitions for further growth in North America have been compromised by a lack of operational fluidity and by a much Manitou experienced a decline in North American sales for its first half results.
■ LGMG has set up a subsidiary in the UK in a bid to build its presence and services in the UK and Ireland, with a new headquarters in Liverpool. The establishment of LGMG Machinery UK brings to an end the wide-ranging distributor deal Lingong Heavy Machinery (LGMG) has had with Access Platform Sales (APS) since 2019.
■ Oshkosh Corporation, owner of MEWP and telehandler manufacturer JLG, has completed the acquisition of Ausa. Based near Barcelona, Spain, Ausa is a manufacturer of telehandlers, dumpers and forklifts.
Brian Thompson and William Wallwin will focus on the central USA region and come with extensive industry experience in their sectors.
Wallwin has held prominent positions in the industry for over 20 years in sales and account management and has an understanding of market dynamics, long-standing industry relationships and strategic approach to sales will be instrumental in supporting customer initiatives.
With over 10 years of experience in the industry, Thompson’s leadership, sales strategies and strong customer relationships are a great match to MEC’s core value, said the company.
IPAF has appointed Randy Marzicola as vice president of North America.
With an extensive background in business development, strategic partnerships and market expansion, Marzicola brings a wealth of experience to IPAF and will play a key role in enhancing IPAF’s services and member recruitment across North America.
His most recent position was director of business development at JLG’s Industrial Solution Group, focused on strategic growth initiatives.
Marzicola’s primary focus will be on recruiting new members to the IPAF, while the federation’s North America Regional Manager Tony
Groat will continue to focus on standards, current members and training operations and the IPAF North American council. ■ For more on this story, see IPAF’s news pages in this issue.
BigRentz has appointed former Home Depot chief strategy officer, Matt Schweickert, to its board of directors.
Schweickert’s career spans over two decades and is defined by his ability to scale global organizations and drive profitability, according to a release from BigRentz. While at The Home Depot, he
simultaneously served as CSO, functional CFO for technology and chief product & user experience officer.
His efforts in integrating technology and data into operations enhanced Home Depot’s operational efficiencies and customer experience. He has since been involved in advising, scaling
Brad Barber, CEO of H&E Equipment Services, said the company is expecting a more moderate level of construction activity, with curtailed spending by smaller contractors in particular.
“We reiterate our view of a more moderate level of spending and project starts as the construction industry continues to transition to a lower level of activity compared to levels in 2022 and 2023,” Barber said. “Higher project financing costs and more stringent lending standards have led to curtailed spending, especially among smaller contractors.”
However, he added that mega-project and infrastructure activity continued to grow; “H&E’s participation in these projects continues to rise as the company fully leverages its increased scale in the United States."
and helping drive liquidity events for several start-ups across retail, technology as well as the home, health and wellness categories. ■ For more on this story, see our interview with Schweicker on page 12.
Ashtead Group, owner of Sunbelt Rentals in the U.S., Canada and the UK, has said its strategy of growing its specialty businesses and
broadening end markets has seen it outperform the market.
In its financial results for Q1 of 2024, the company said its
KHL Group, publisher of Access, Lift & Handlers and Scaffold & Access magazine, has created a new corporate website targeted at customers and clients explaining the marketing services that can be delivered via its multi-channel approach to audience engagement.
The site, at www.khl.com, explains how suppliers to the construction and power sectors can target specific audiences, domestically, regionally and globally through a wide variety of channels, including daily briefings, newsletters, websites and traditional print media. Information about KHL’s recently launched Content Studio, which creates commercial content for clients, is also available.
specialty segment grew by 17 percent for the second year running. By comparison, its general tools businesses grew by 3 percent.
Revenue for the group was $2.7 billion (€2.4 billion), up by 2 percent on 2023, while rental revenue was up by 7 percent to $2.5 billion (€2.2 billion) for the quarter.
In the United States, rental only revenue was up by 7 percent to $1.7 billion, which it said was driven by both volume and rate improvements. ■
Nano electrophoretic paint: Exceptional precision and quality
World-class components
Versatile certified product line for both indoor and outdoor use
Maintenance free batteries
Comprehensive features included as standard for peak performance
A product line offering both diesel and electric options
Best In Class After-Sales Support
Smart Training Eco-System
Manitou takes on your toughest challenges in 2024 with trusted solutions and new innovations designed to help you own the jobsite and deliver results that keep you ahead of schedule and under budget. Learn more at manitou.com.
See our full range of solutions for your business at Manitou.com.
UK-based Star Platforms has announced the retirement of longstanding access industry professional Andy Pearson, with a career spanning over 30 years. Pearson’s journey in the hire industry began at Chislett Tool Hire, before he moved on to roles at Stephens and Carter and Key Scaffold in 1993. This became a significant career milestone with Key Scaffold becoming A.M.P Access in 1995. Over the years, Pearson progressed through various roles including sales manager, sales director and eventually managing director. During his tenure as managing director, he played a crucial role in the successful sale of A.M.P Access to Nationwide Access which was later rebranded Nationwide Platforms by its owners the Lavendon Group Plc and has since been acquired by Loxam Group.
Following this, Pearson served as south west regional director at Nationwide Access (Lavendon Group Plc) from January 2007 to 2010. He then took on the role of managing director at Prolift Access from 2010 to 2019, where he led the growth of the company from 35 to 900 MEWPs before its sale to Speedy in November 2017.
In his most recent position, Pearson served as south west regional director at Star Platforms from January 2021 until July 2024.
Sales at the latest Euro Auctions event reached UK£41.2 million ($54 million), with a record number of MEWPs, including 160 boom lifts and over 200 telehandlers, in the catalogue.
Europe’s largest auction house held the UK sale July 31 - August 3, featuring over 7,500 lots from 650 vendors across 25 countries, across
a diverse range of heavy plant and machinery attracted buyers and sellers from around the world. With 44 percent of buyers coming from the UK, 49 percent of buyers were from Europe and the remainder from the rest of the world. The top buying countries by hammer total were the UK (£18.3 million), Republic of Ireland (£6.5
■ France-based rental company Kiloutou has said that it has reached a “new milestone” with the addition of 760, 100 percent electric units. The investment includes the Volkswagen ID.3 Pro Life Max, Hyundai Kona and Volkswagen ID Buzz Cargo models.
■ Aerial platform rental company cooperative PartnerLift is expanding its network to Austria. Flott Arbeitsbühnen has joined the Germany-based cooperative with around 90 truck mount in its fleet.
■ Germany-based rental company HKL Baumaschinen has invested in new truck-mounted work platforms from Multitel. The order includes the MT204EX telescopic work platform from the Italian manufacturer.
million), Spain (£2.1 million), Poland (£1.9 million), and Belgium (£1.9 million).
Online bidding accounted for 72 percent of the overall sale activity, and of the 1,500 buyers, 83 percent placed their bids online. ■
Kranpunkten’s transition to a fully climate-neutral rental fleet continues with the Swedish rental company’s latest delivery of new machines, including fully electric boom and scissor lifts with working heights of up to 44 meters and 32 meters respectively.
During the spring and summer, Kranpunkten received deliveries of the BT 44 ERT boom lifts and 3225 DC scissor lifts from Dingli. The 44-meter BT 44 ERT is the highest fully electric straight boom lift on
the market, and Kranpunkten is the first equipment rental company in Sweden to include the lift.
“We continue to invest in fully electric lifts in line with our strategy of being completely
climate-neutral by 2030. This means we must place high demands on our equipment suppliers to continuously develop more environmentally friendly products. ■
The UK and Ireland’s largest semi-trailer manufacturer, SDC Trailers, has invested in multiple Sunward scissors, following the company’s switch from hiring to purchasing the lifts. The company added 11 new units to its fleet, seen being delivered, here.
Looking to scale its global impact and drive profitability into its digital platform, construction procurement software provider BigRentz has appointed former Home Depot Chief Strategy Officer Matt Schweicker to its board of directors.
Schweickert’s career spans over two decades, with more than five years spent at Home Depot where he simultaneously served as CSO, functional CFO for technology and chief product and user experience officer.
The appointment is a significant step for BigRentz, which is looking to further simplify equipment rental and management processes for its 6,000 supplier partners representing 14,000 locations and customers across the country.
And that “simplification,” according to BigRentz, will include the introduction of AI-infused software solutions to drive cost savings, break down communication silos and operate across more industry verticals, including staffing and financial services, to address evolving market demands, according to the company.
ALH sat down with Schweicker to find out what he hopes to achieve in his new role at BigRentz, as well as discuss what’s next for the construction and rental industries as they continue to evolve in this ever-changing digital age.
How does your background serve your new role at BigRentz?
Schweickert: My background is in investment banking, and when I joined Home Depot years ago, one of the things we really drilled into was the importance of the “pro” and understanding their business.
To give you the context, 3 percent of the customers at Home Depot generate 50 percent of the revenue, and those are the professional contractors. The reality is that 99.99 percent of all pros rent equipment. A typical morning for one of our best customers in those days would have them coming to Home Depot
Former Home Depot exec Matt Schweickert has joined the board of directors at BigRentz. Jenny Lescohier reports.
I really want to focus on the on the consumer experience; to make sure the guts of the software really work.
MATT SCHWEICKERT
to get their supplies, etc., and then going across the street to another rental yard and rent their equipment.
For us, the question was always, how do we capture that business from a convenience perspective? How do we get more of that spend from the professionals by helping them complete their projects more efficiently?
How is the professional contractor’s role evolving?
We all know there’s a skilled labor shortage, so anything that increases efficiency for them is valuable.
The construction professional used to be a guy who ran his business out of a pickup truck. But that professional is evolving to adopt more and more digital tools. This is happening in the rental space too. BigRentz’s online presence allows users to manage their rentals anywhere, anytime.
One of the biggest challenges for the industry is transparency around pricing and availability, those tend to be the biggest pain points for a customer who’s renting equipment. I’ve been an advocate for the rental space for years, and I’m also passionate about anything that provides additional efficiency and visibility within the construction and project industries. That’s why I was originally attracted to this role with BigRentz.
What’s the next step in the evolution of rental for the end user?
One of the biggest challenges on any project, once you actually find the equipment, get the right
BigRentz has 6,000 supplier partners across 14,000 locations.
BigRentz merged with Illinois-based Lizzy Lift in 2020.
good digital tools that provide transparency and easy procurement.
The core issues within the industry and what needs to happen to make it more efficient are exactly what BigRentz is working on.
What do you see in your crystal ball for the future?
going to be put on hold for a little bit, but I think the foundation of the demand will remain strong. With that in mind, there will probably be a little bit of a shift in terms of what sort of equipment is more heavily utilized in the near term. My guess is it will skew more toward compact equipment for smaller projects. Overall, I think it will balance out over time.
What do you hope to achieve at BigRentz? I really want to focus on the consumer experience; to make sure the guts of the software really work. The big piece I’m going to be focused on, and I hope I can provide some value on, is putting things in the lens of the professional, the contractor and what the rental experience looks like for them, now that the back end is all built. That’s really where my experience has been over time, on the technology and its application.
The industry has changed a lot since you got involved. Do you have any personal feelings about the direction it’s headed? In a world where mobile procurement, geofencing of an order, is the norm - I can geofence my order at Chick fil A, right? - the adoption of these basic tools are everywhere. If I can go on Amazon and order a swingset and have it delivered the next day, why can’t I have a similar experience in every other interaction?
price and get it delivered to the job site, is how to utilize it. How do you get quick training and become productive quickly?
Those are the broader pain points and challenges that we’re trying to address at BigRentz. So, yeah, more to come there.
On a more general level, what do you see as the most critical issues facing rental companies right now, and BigRentz in particular?
There’s always the question around demand - Is there project demand? Is there consumer demand? The good news is we see some great trends ticking back up for the second half of the year, after being a little soft for a short period of time. So I think the demand in the industry will remain solid and strong.
I think the challenges center on the overall fragmentation in the space and the lack of really
Usually, construction spend and rental spend are associated with what I’ve historically called “tragedy and dreams.” The tragedy is equipment need based on things like a roof collapse due to a fallen tree. That part of rental consumption will always remain solid.
What’s interesting right now is that the dreams element - like doing a massive renovation in your backyard or putting in a new pool - can get put on hold when money is tight. I do think a lot of those more discretionary dream projects are
Traditionally, there has been this unconscious bias in the industry, or maybe it’s a conscious bias, that construction professionals don’t actually want convenience - they want to work off a clipboard, they want to have a bunch of papers scattered on the floor mats of their pickup truck. That’s how they want to run their business. But when you see the adoption of other digital tools - and I call out things like ServiceTitan and Buildertrend, and other tools that are helping professionals - then the need for an equal advancement of technology in rental, hopefully, is better understood and appreciated.
Is there anything else you would like our audience to know about what’s coming from BigRentz?
The team is absolutely focused on improving product development, the core platform. There are some great things coming that utilize current technology, and it will be a huge gain for us. ■
Some of the biggest challenges for the industry are transparency around pricing and project availability, Schweickert says.
Life is full of shortcuts. But operating mobile elevating work platforms without properly trained, tested operators is a dead end decision. Train right. Insist on the PAL Card as proof. A valid PAL Card proves the holder has passed an approved and audited IPAF theory and practical test, compliant to industry standards. Find an IPAF-approved training center near you at IPAF.org or scan here
This year’s annual ranking of North America’s largest access-equipment-owning fleets shows healthy growth and utilization across the board. ALH reports.
Aerial equipment is still in high demand across North America, as this year’s annual ranking of access equipment rental fleets shows yet another year of solid growth. Overall, the total number of aerials within N.A. fleets this year tops 500,000 for the first time ever on the ALH AERIALS20, with our total figure up 8.49 percent to 524,025 from last year’s 483,004.
Not one company on this year’s list saw a
United Rentals, the world’s largest equipment rental company, once again remains on our top spot, clocking in with 205,000 pieces of access equipment in its fleet. Looking at
firm, Sunbelt, with its estimated 175,000 pieces of access equipment, our top two rental companies combined make up 72 percent of the AERIALS20 total.
But the biggest mover and shaker on this year’s list isn’t from the top 5, nor even top 10. Even more surprising, it’s not an aerials specialist. Looking down our list to number 18, the largest increase by percentage belongs to Madison-based Ideal Crane Rental, who grew its access fleet by more than 36 percent year-overyear. Ideal’s fleet now is made up of more than 1,165 aerials, whereas last year the company reported 855.
Ideal has a range of MEWPs in its fleet, from JLG’s 1200 SJP to the company’s compact, crawler-based spider lifts. Their units have been deployed on sites across the area, ranging from the Milwaukee Brewers baseball stadium to the Overture Center for the Arts in Madison.
It’s a trend worth noting in the year to come – will more specialist rental companies (such as crane rental, etc.) look to diversify and add to their offerings?
United Rentals remains number one on the
Despite United’s solid Q2 results, the company narrowed its forecast for the 2024 financial year and said that it remains well placed to capitalize on opportunities for long-term growth.
The company now expects revenue for the year to be in the region of $15 billion to $15.3 billion, a revision of its previous guidance of between $14.95 billion and $15.45 billion.
EBITDA has also been revised and is now expected to be between $7.09 billion to $7.24 billion.
Meanwhile, the company expects to maintain
its previously announced capital expenditure for the year of up to $2.3 billion.
The revisions were announced in its latest financial report, which revealed record rental revenues for the second quarter of 2024. During the quarter rental revenues reached $3.2 billion, an 8 percent increase on 2022.
Its general equipment rental segment saw moderate growth of 0.9 percent in the quarter, reaching $2.2 billion, while its specialty segment saw the highest amount of growth at 27 percent year-over-year to a second quarter record of $1 billion.
The company said growth in specialty was largely impacted by its purchase of temporary
roadway rental business Yak Access, Yak Mat and New South Access & Environmental Solutions.
Looking at Sunbelt, meanwhile, the company’s Q1 results, which were announced in early September, saw U.S. rental revenues of $1.7 billion, up 7 percent year over year.
While overall CapEx was down on the same period in 2023, the company invested $855 million on fleet investment and depot expansion.
Continuing its goal of opening between 300 and 400 greenfield depots by the end of its Sunbelt 4.0 five year plan, the company added 33 locations in North America in Q1.
Two of these were through the acquisitions of generalist businesses RentalMax in the US and Canada-based Wave Equipment at a total cost of $53 million.
In terms of fleet, it invested $717 million (€649 million) in the quarter, down from $999 million in 2023.
Ashtead’s chief executive Brendan Horgan said the company is “in a position of strength” and has the “operational flexibility” to capitalize on structural growth opportunities.
While it seems that rental firms are gently pumping the brakes on taking on new fleet for the remainder of their fiscal years, activity and demand remains for aerials across North America. It will be interesting to watch how the next 12 months play out. ■
United Rentals saw its aerials fleet grow to 205,000 units, an increase of 9 percent.
Research for the AERIALS20 list was carried out during the Summer of 2024. Where companies were unwilling to provide data, we made our own estimates based on company financial reports and advice from industry experts. We thank those who participated and made our list stronger than ever. If you
Since our founding in 1959, our mission has never been to be the biggest, but to always be the best at what we do. It’s this focused dedication that has made the name Piranhaflex™ synonymous with high quality and innovation.
Manufactured at our state-of-the-art, Piranha Hose Products production facility in the heart of Northern Michigan, the Piranhaflex line of thermoplastic hydraulic hose offers a variety of products specially engineered to meet the challenges of the utility industry.
PF354NC Series
PFP354NC Series
• Meets or exceeds SAE J517 standards
• Tested to 1/2 SAE bend radius requirements
• Exceeds 100R7 impulse requirements
Low friction, Slither® cover allows for easy installation through tight hose bundles on aerial equipment such as scissor lifts and bucket trucks.
PF267NC Series
• Meets or exceeds SAE J517 standards
• Tested to 1/2 SAE bend radius requirements
• Exceeds 100R7 impulse requirements
Specially engineered kink resistance, up to 53% more force required to reach kink initiation*
Improved flexural properties, up to 16% less force required to bend.
Lifts assist in Norway
COUNCIL UPDATE MEWP
EVENT GUIDE SAIA Annual Convention & Exposition
ASC A92 Meeting details and agenda
Iwould like to take a moment to thank members and non-members alike who have registered to join us in Denver for the Scaffold & Access Industry Association’s (SAIA) 2024 Annual Convention & Exposition this Sept. 29 – Oct. 4.
As the industry’s official voice, the SAIA is thrilled to assist our members in not only becoming more efficient and profitable in their businesses, but to also lead the advancement and promotion of safety within our industry by utilizing resources, education and communication.
I encourage attendees to take a few minutes to review the program’s schedule (either via our website, www.saiaonline.org, or in the official program which will be handed out at the event) and learn more about the presentations and product demonstrations.
Attendees will hear from leaders in their fields and who will share their knowledge and expertise freely to benefit us all. You won’t have to choose whether to attend a general session or the exposition – there are dedicated show hours and exhibitor lunches that will allow you to learn about the latest trends in safety and equipment without missing a single presentation.
Also, if this is your first time at the convention, be sure to connect with the Ambassador Committee. They will help you to get acquainted with SAIA members and learn how to get more involved in the association.
I’d like to take this moment to thank our members who renewed in 2024 and those who joined us our events this year. Your involvement makes us stronger and safer, and I cannot thank you enough. After all, members are our most
WELCOME TO OUR NEW MEMBERS
Amarok Scaffolding Ltd.
Nyden Iron-Nighttraveller nyden@amarokscaffolding.ca
Approved Equipment, Inc.
Alfredo Gonzalez alfredo@aei.company
Deerfield Risk Advisors
Conor Kerins conor@deerfieldrisk.com
EASY Safety Training and Services
Scott Glynn scott@easysafety.ca
“I’d like to thank our Executive Committee, Board of Directors, Councils and Committees. It has been a pleasure to serve you as president and I am pleased to pass the gavel to Mike Bredl as the next president to lead us.”
TRACY DUTTING-KANE
important asset, and without you, there would be no SAIA. Many, many thanks also to our sponsors and exhibitors – your generous support has made SAIA’s 2024 Annual Convention & Exposition possible. Your commitment to the industry and our association makes this annual event a successful one every year. I also want to recognize the SAIA staff for their continued efforts to make SAIA meetings the best they can be. You are appreciated!
Next year, the SAIA will travel to the South. The event will take place August 5 – 8, 2025 in Ft. Worth, TX.
Lastly, I’d like to thank our Executive Committee, Board of Directors, Councils and Committees. It has been a pleasure to serve you as president and I am pleased to pass the gavel to Mike Bredl as the next president to lead us.
Engineered Supply, LLC Arlen Grant agrant@engineeredsupply.com
Global Site Solutions (GSS) Keith Sanders ksanders@at-pac.com
InCord Brian Cox bcox@incord.com
Marip Scaffolding Exports
Aj Ghotra info@maripscaffoldingexports.com
For more information, visit www.saiaonline.org
Net At Work Jessie Hall jehall@netatwork.com
Proscaff Enterprises Ltd. Rod Spurrell rod.spurrell@proscaffna.com
Revolution Industrial Taylor Olson taylor@revolutionindustrial.com
RW Scaffolding & Shoring
Ed Parrish ed@rwscaff.com
Urban Umbrella Jaron Orlando jaron@urbanumbrella.com
2022-2024
Tracy Dutting-Kane, P.E. President Layher, Inc.
Mike Bredl
President-Elect
Universal Manufacturing Corp.
Frank Frietsch
Vice President Layher, Inc.
Matt Morgan Treasurer
Mdm Scaffolding Services, Inc.
James Gordon
Secretary
Klimer Platforms, Inc.
Amy Johnson Member at Large SkyLine Scaffold, Inc.
Tom Brewer
Board Appointee
Brewer Equipment Co.
Chris Moody
Board Appointee
Direct Scaffold Supply (DSS)
Michael Paladino
Immediate Past President
Eagle Scaffolding Services, Inc.
Editor: Lindsey Anderson 517-420-0918
lindsey.anderson@khl.com
Director of content: Murray Pollok murray.pollok@khl.com
Client success & delivery manager: Charlotte Kemp charlotte.kemp@khl.com
Client success & delivery team: Ben Fisher | ben.fisher@khl.com
Olivia Radcliffe | olivia.radcliffe@khl.com
Alex Thomson | alex.thomson@khl.com
Group design manager: Jeff Gilbert
Group designer: Jade Hudson
Creative designer: Kate Brown
Event manager: Steve Webb
Event design manager: Gary Brinklow
Audience development deputy manager: Anna Philo
anna.philo@khl.com
Circulation executive: Vicki Rummery vicki.rummery@khl.com
Admin assistants: James Dick-Cleland, Maria McCarthy
Associate publisher: Tony Radke 480 478 6302 | tony.radke@khl.com
VP global sales: Alister Williams 843 637 4127 | alister.williams@khl.com
Accounts assistant: Emily Roberts
Client success & digital director: Peter Watkinson peter.watkinson@khl.com
Facilities & HR administrator: Sharron Brown sharron.brown@khl.com
Chief executive officer: James King
Chief financial officer: Paul Baker
Chief operating officer: Trevor Pease
Outgoing SAIA President bids farewell as the baton is passed during this year’s Annual Convention & Exposition in Denver.
Scaffold Builders Competition set for 2025; Altrad to acquire oil and gas provider; ‘Ritzy’ restoration calls for suspended solution; Performance Contracting opens new facility; Sunbelt supplies scaffold for historic renovation; plus recent OSHA news and reported violations.
The SAIA will host its Annual Convention & Exposition Sept. 30 through Oct. 4 in Denver. SA reports on what attendees can expect.
GEDA used various material and scaffolding hoists and lifts to supply a recent project in Oslo, Norway. For the full story, see our project report in this issue on page 17.
City Hall in Oslo, Norway’s capital, is currently undergoing extensive renovation – with the help of several GEDA units. SA reports.
The SAIA MEWP Council is working on updating and publishing a new industry best practices document for the mobile elevated work platform sector. Lindsey Anderson reports.
The ASC A92 Annual Meeting is set for Oct. 7-10 in Las Vegas. Scaffold & Access provides a look into what’s in store for this year’s gathering.
David Glabe breaks down how to navigate and understand OSHA regulations and requirements.
but KHL Group Americas LLC cannot be held responsible for any inaccuracies and the views expressed throughout the magazine are not necessarily those of the publisher. KHL Group Americas LLC cannot be held liable for any matters
resulting from the use of information within the magazine. The publisher is not liable for any costs or damages should advertisement material not be published.
Scaffold & Access is published six times a year by KHL Group Americas LLC 14269 N 87th Street, Suite 205, Scottsdale, AZ 85260, USA.
SUBSCRIPTIONS: Annual subscription rate for non-qualified readers is $160. Free subscriptions are given on a controlled circulation basis to readers who fully complete a Reader Subscription Form and qualify under our terms of control. The publisher reserves the right to refuse subscription to nonqualified readers.
Altrad, a global provider of industrial services, has announced a voluntary cash offer to acquire all outstanding shares of Beerenberg AS, a takeover bid valued at more than $97 million.
Beerenberg, headquartered in Bergen, Norway, is a supplier to the oil and gas, maintenance and modification services sector, and has been in business for 47 years. The acquisition will see Beerenberg’s 2,350 employees join Altrad Group once the deal is finalized at the end of 2024.
Altrad Group’s Co-CEO, Ran Oren said, “We have admired Beerenberg from a distance for many years and have been impressed
by the achievements of the management team and their talented people. Our objective is to add to this success by adding investment, skilled people, innovative products and a broader range of services to support their clients’ ambitions.”
Altrad generated sales and EBITDA of €5.3 billion and €674 million, respectively, for its fiscal year that ended August 31, 2023. Altrad has affiliates in more than 55 countries in Europe, Australia, the Americas, Middle East, Africa and Asia and derives sales from more than 100 countries.
The transaction is likely to be finalized at the end of 2024.
Think your scaffold crew has what it takes to be titled the best of the best? Then prove it.
The Scaffold & Access Industry Association (SAIA) is looking for teams to compete in its 2025 Scaffold Builders Competition, set for Jan. 21, 2025 during World of Concrete.
The SAIA Scaffold Builders Competition is a showcase of industry craftsmanship and a testament to both the speed and skill of scaffold crews and workforce. In 2024, eight teams competed to be crowned the best, with Superior Scaffold taking
home the top honors.
“This is a contest that also proves how important teamwork is to build and dismantle scaffold,” said SAIA Executive Director DeAnna Martin. “Judging will be based on safety, speed and teamwork.”
Following the success of the 2024 Scaffold Builders
Competition, next year’s event will be bigger than ever, with the SAIA extending the total number of teams allowed from eight to 20. Nine companies have already been confirmed. Teams consist of four
erectors and one coach. Crews confirmed for Vegas next year include:
■ Amarok Scaffolding Ltd.
■ Contractors Access Equipment
■ Heat Tech Industrial, LLC
■ KC Scaffold
■ Northwest Laborers - Employers Training Fund
■ Revolution Industrial
■ Scaffold Solutions, Inc.
■ SkyLine Scaffold, Inc.
■ Superior Scaffold Services, Inc.
To learn more about the event, visit the SAIA’s website or e-mail info@saiaonline.org.
Sunbelt Rentals recently worked with Gilbane Building Company to restore Winthrop University’s Byrnes Auditorium. The equipment rental company was called on for scaffold services, including design and build.
“Originally, we were brought in as a restoration project that was intended to be completed relatively quickly,” said Mike Webber, branch manager at Sunbelt Rental Scaffold Services
in Charlotte, NC. “But it turned out to be a more complex project due to the age and design of the building.”
Sunbelt utilized 20 truckloads of scaffold on the site during the project, with the scaffolding in the main auditorium measuring 125 feet long by 110 feet wide by 65 feet high.
Due to the complexity of the project, it took a month for Sunbelt Rentals to set up all the scaffolding for the auditorium. The attic alone took two weeks and builders moved specific scaffolding once a week for contractors to work on the HVAC ducts. In total, Webber estimated they had 20 truckloads of scaffold on the site during the project, with the scaffolding in the main auditorium measuring 125 feet long by 110 feet wide by 65 feet high.
“We built a scaffold deck below the ceiling that also served as a safety component for when the contractors were
Performance Contracting has opened a new 77,000-squarefoot facility in Denver to accommodate its growing presence in the region. The facility will house various operations, including the PCI’s glass and glazing, interior, cleanroom and insulated metal panel (IMP) scopes.
“The new facility represents a significant expansion for Performance Contracting and will provide the space and resources needed to enhance its manufacturing capabilities,” the company said. “The state-ofthe-art building will allow the
company’s teams to produce unitized glazing and other premanufactured systems on-site, leading to streamlined operations, improved efficiency, and more significant innovation in its product offerings.”
“We are thrilled to be taking this next step in our growth journey,” said Pat Roth, COO for Performance Contracting.
“This new facility will not only support our current operations, but also enable us to better serve our clients with advanced manufacturing capabilities and increased production capacity.”
This investment underscores
Performance Contracting’s commitment to delivering high-quality construction solutions and maintaining its competitive edge in the industry. The company aims to meet the growing demand for its services while continuing to uphold its standards of excellence and innovation, it said.
Superior Scaffold recently provided a range of access and scaffold equipment to a high-profile job in downtown Philadelphia.
The Ritz-Carlton Hotel in Philadelphia is a historic, 32-story-marble-clad hotel, and it has provided luxury services for nearly a century. Due to its age, the building’s marble dome
doing work in the attic,” Webber explained. “It reduced the exposure for injury because if someone were to have fallen
needed cleaning, repointing, and sealing. Additionally, the penthouse required marble repairs and anchoring.
Contacted by general contractor Pullman, Superior Scaffold was tasked with finding a solution to provide crews with double access to work zones while also keeping pedestrians below the job safe.
through the outlet, it would have been a direct fall, 65 feet to the ground.”
The scaffolding design met its intended use and allowed Gilbane and other contractors access to clean ducts and hard surfaces, and work on the electrical components in the in the building. Sunbelt also utilized a crane to lift materials to the roof or maneuvering into the attic and set up temporary fence panels around the perimeter of the project.
Superior thus decided to utilize traditional supported scaffold paired with Fixeos, a “lighter alternative to full blown, heavy mast climbers, or when the project can’t be swung with traditional suspended scaffold rigs,” the company noted.
The Fixeo product, produced by France-based Fixator, allows all standard domestic suspended scaffold equipment to be converted into a light-weight MCWP that provides a stable work area that will not sway in windy applications.
Superior used the Fixeos on the top portion of the RitzCarlton’s building in order to get crews to spots where renovations and repairs were needed. The company also provided a canopy overhead protection system that wrapped around the entire building in order to protect pedestrians and automobile traffic below the work at height.
Crews then performed
WernerCo has announced that the company will change its name to ProDriven Global Brands.
The ladder, mobile tower and MEWP manufacturer said the change reflected its growth strategy in serving the construction, industrial and automotive industries.
Effective immediately, Justin White, managing director at ProDriven Global Brands for the UK, said it reflects a significant transformation for the company.
“Starting life as a safe access brand in North America, the company has continued to grow the WernerCo brand into a variety of industries worldwide. The new strategic name change reflects our ongoing commitment to innovation, growth and a diversified product and brand portfolio.”
pointing, cleaning and marble repairs, including restoring decorative pieces, and reconstructing the building’s parapet with cast stone elements. They also restored the hotel’s brass windows. GC Pullman expects the job to finish on time and without incident.
Following an airport hangar collapse at the Boise Airport in Idaho in January 2024 that killed three and injured eight, OSHA launched an investigation which found the building contractor ignored standard safety procedures and visible warning signs during construction.
OSHA inspectors discovered Big D Builders Inc. had begun erecting the hangar without using sufficient bracing or tensioned guy wires. OSHA also learned the construction contractor had ignored numerous indications that the structure was unstable, including visibly curved, bent and wavy structural I-beams, unbalanced columns and several snapped wire rope cables.
Despite these obvious concerns, federal inspectors determined Big D Builders continued to add 150-foot-long bays to the football field-sized project. OSHA found the bays were visibly not straight and that the contractor left many critical connecting bolts loose and, rather than installing additional bracing or temporary guy lines per steel erection industry standards, used straps to straighten the additional spans.
In addition, OSHA found the contractor failed to train workers to properly construct steel spans and allowed cranes and other construction equipment to operate in mud and standing water, exposing workers to risk of the equipment overturning.
OSHA cited Big D Builders for one willful violation and three serious violations of federal safety regulations and proposed $198,586 in penalties. The agency also cited Inland Crane Inc. of Boise with one serious safety violation and proposed $10,163 in penalties for exposing workers to collapse hazards due to failures to ensure stability during the hangar erection process.
Two federal workplace safety investigations have found a Chicagoarea framing contractor – already facing debt collection for more than $100,000 in fines for violations identified in 2022 – continuing to expose employees to deadly fall hazards and defying the U.S. Department of Labor’s requests for documents and information related to the contractor’s business and workers safety and health.
OSHA inspectors observed employees working at heights up to 30 feet without fall protection on January 29 at a residential construction site in River Grove, IL. Inspectors found employees of KW Framing Inc. without required protective equipment while they erected exterior walls on structures two to three stories high.
When inspectors returned to the site on February 9 and February 12, they again found workers exposed to similar fall hazards as they set joists and trusses. Wojciech Knapczyk, a management official at the company, dismissed the concerns of OSHA inspectors.
The U.S. Department of Labor has cited a New Jersey water tower painting company for three willful and 19 serious violations after finding the contractor failed to provide or install required safety equipment that would have prevented an employee from falling 80 feet to the bottom of a water tower and suffering severe injuries in January 2024.
Inspectors determined that U.S. Tank Painting Inc. employed workers to sandblast and paint the tower’s interior and exterior and replace a ladder attached to the structure to access the
PHOTO: HILTI In addition to failing to protect employees from fall hazards, U.S. Tank Painting exposed employees to silica dust. The hangar that collapsed near the Boise Airport in January.
On May 7, 2024, OSHA visited another KW Framing worksite in the same residential development and found, once again, the company allowing employees to sheath a more than 30-foot high roof without required fall protection.
As a result of the January and May inspections, OSHA cited KW Framing for one repeat violation for failure to provide eye protection and two willful citations for its lack of fall protection. In addition, the agency cited the company for four serious and two other-thanserious violations for not having guardrails or stair rails, misusing ladders, failing to ensure employers wore head protection and not maintaining records or certification that employees received fall protection training.
OSHA has proposed $317,644 in penalties.
tower’s peak. OSHA learned the injured worker fell while climbing a maintenance tube ladder into the water tank.
In addition to failing to protect employees from fall hazards, U.S. Tank Painting exposed employees to respiratory injuries and hearing loss while working in a permitrequired confined space, fire and explosion hazards and long-term lung damage related to unsafe levels of silica dust.
U.S. Tank Painting faces $485,580 in proposed penalties for violations identified at the site.
Alba MC 250 material hoist from Bee Access sets new standard in elevating performance.
When historic Hurricane Ian barreled its way through Florida’s southwest Gulf Coast in late September 2022, very few structures were left unscathed, with many either destroyed completely, or left in desperate need of repair and renovation.
Even two years later, many parts of the city of Ft. Myers and the surrounding areas continue to recover.
Condominium (condo) buildings dot the landscape in a place as favorably located as the southwest coast of Florida. And when a storm comes through, those in need of a makeover need it done as efficiently and affordably as possible.
Among a list of additional jobsite priorities, Miami (Fla.)-based Trekker Distributors understood these two as principal to the initial phase of said makeover for a particular condo building renovation they were positioned to set up scaffolding for in July 2024.
They also knew that renovating a condo building in a high-
density urban environment like south Florida presents a host of challenges. The need to skillfully transport heavy, awkward materials to elevated work areas without disrupting the surrounding community or compromising safety is paramount.
Moreover, the Trekker team was tasked with adhering to strict project timelines. However, according to Micah Turner, access division manager at Trekker Group, finding equipment with the necessary lifting capacity, safety features, and ease of operation wasn’t as challenging as it might have looked on paper.
“We required a material hoist that was not only robust and reliable, but also compact enough to fit into the tight confines of this urban jobsite,” he explains.
“Fortunately, I knew where to look.”
Trekker had recently utilized two Alba MC 250 material hoists from Bee Access (Bee) on a project involving the tallest building in
The MC 250 pivoting basket can swing 90 degrees for safe & easy unloading of materials
Scan the QR code to read the full story
Orange Beach, Alabama. “We had some scaffolding that got us up to the first level of that high-rise, but we needed another two hundred fifty feet above that,”
Turner recalls. “We’d used some other solutions, but they wouldn’t get us up to the height we needed. So, we met with Bee and asked them what they had that could help us with this issue.”
Turner’s contact at Bee showed him the Alba MC 250. “It ended up being a perfect fit for what we needed there,” he says.
So, when Turner needed a solution for the Gulf Coast condo job, he set up a visit (Bee Access is located just north of Trekker in West Palm Beach, Florida).
“They showed me the new MC 250 with the pivoting basket and battery solution,” he notes. “It was even more practical than the others we’ve used. It carries more weight and fits in tighter spaces.
“And it’s a standup basket that rotates a hundred and eighty degrees – so it really hit all the items we were looking for in a hoist to make our jobs easier and more efficient on this project.
“It has been an invaluable resource—we finished faster and with less manpower,” he adds, emphasizing that the savings have undoubtedly increased their margins on the job. ●
This article was produced by
in partnership with experts from Trekker utilized 2 Alba MC 250 Material Hoists from Bee Access to erect scaffolding for the Ft. Myers condo renovation
The SAIA will host its Annual Convention & Exposition Sept. 30 – Oct. 4 in Denver. SA provides a guide to what’s in store.
The Scaffold & Access Industry Association’s Annual Convention & Exposition brings together the largest global gathering of scaffold and access industry professionals. The Convention features industry-focused educational sessions and showcases the nation’s top scaffold and access exhibitors.
This year, attendees will descend upon Denver, where they will network, learn and celebrate from Sept. 30 – Oct. 4. SA has compiled a thorough guide to the event, highlighting speakers and conference topics, exhibitors, training opportunities, networking events and more.
Capping off the week will be the Association’s Member
From an economic outlook to project reports, this year’s conference program is tailored specifically for the scaffold and access industry. Here’s what attendees will hear about.
WEDNESDAY, OCT. 2
9 a.m. – 10 a.m.
ELEVATING SCAFFOLDING: STRATEGIC HIRING FOR CONSTRUCTION EXCELLENCE
Presented by Matt DiBara
The scaffolding industry is evolving rapidly with new technologies and changing market demands. This keynote will explore strategies such as adopting a candidate-centric approach in employer branding, effectively using skills assessments, and forming strategic partnerships that companies can employ to attract, develop, and retain the talent needed to succeed. Attendees will learn actionable insights to improve their hiring practices, creating a workforce that is skilled, diverse, and aligned with their company’s values.
Objectives:
■ Optimize Talent Acquisition: Discover innovative methods, like using employee-centric views, to attract and secure top talent in the construction industry, ensuring a competitive edge in today’s market.
■ Foster a Culture of Safety and Performance: Learn how to implement effective safety protocols and performance-based incentives to enhance workplace safety and productivity.
■ Retain and Develop Workforce: Understand strategies to create clear career paths and development opportunities, improving employee retention and fostering long-term growth.
Takeaways:
■ Build a Strong Employer Brand: Use your company’s culture and values to create a strong brand that attracts the best candidates, highlighting your
commitment to an inclusive work environment.
■ Craft a Tailored Hiring Plan: Develop a comprehensive hiring strategy that meets the specific needs of your construction company while exploring innovative approaches and tools to streamline your hiring process, ensuring you secure the best talent efficiently and effectively.
■ Implement Culture-Enhancing Initiatives: Learn practical steps to build and maintain a workplace environment that encourages growth, loyalty, and productivity among your team.
10 a.m. – 11 a.m. WILL CONSTRUCTION THRIVE OR DIVE IN ’25?
Presented by Ken Simonson
The construction industry has remained busy overall in 2024 despite a slowdown in some building sectors. The outlook will be influenced by decisions made by the Fed, the White House, and Congress—all of which may experience big changes in 2025. Ken Simonson, chief economist for the Associated General Contractors of America and one of the industry’s leading analysts, will sort through the possible scenarios and offer his fearless forecast for the year ahead.
2:30 p.m. – 3:30 p.m. EFFECTIVE NETWORKING STRATEGIES
Presented by Diane Darling
Whether you are an executive or starting out in your career, having a solid network that you can leverage is vital. Yet few schools include courses about building and maintaining relationships.
Effective networking is more than handing out business cards, having a LinkedIn profile, and hoping the phone rings. Whether you’re looking to connect within your organization, your industry, or are looking to get on boards, knowing who to contact – and having them return your call is essential. In this program, you’ll better understand how to create and maintain an effective network both in-person and online.
and Project Awards ceremony during the President’s Gala Dinner, which will be held on Oct. 3.
Categories for the Project Awards include:
■ MEWP Project of the Year
■ SAIA Commercial Collaborative Project of the Year
■ SAIA Industrial Collaborative Project of the Year
Key takeaways:
■ Mast Driven Hoists and Platforms Project of the Year
■ Innovation Award
■ Suspended Access Project of the Year
■ Supported Scaffold Project of the Year
■ Shoring Project of the Year sa
A look at the bustling exhibition hall during a previous SAIA Annual Convention & Exposition.
■ Better understanding of what networking is (and isn’t)
■ Ways to get started when you haven’t been in touch with people in your past
■ Tools and apps to organize your contacts so you can stay in touch
■ Overview of LinkedIn, how to set up a profile, and the elements to include
■ Identifying organizations and events that are worth your time, money, and effort
■ Clarifying the results you can expect from networking
■ Building alliances with others who can help you advance your career
3:30 p.m. – 4:30 p.m.
EXPLORING THE HEIGHTS: INNOVATIONS IN BUILDING ACCESS
Presented by Brian Andrews
This session will dive into various scaffolding methods for accessing areas on a building or structure.
THURSDAY, OCT. 3
10 a.m. – 11 a.m.
RIDICULOUSLY EASY TO DO BUSINESS WITH — FUTUREPROOFING YOUR BUSINESS BY BETTER RESPONDING TO A NEW GENERATION OF WANTS, NEEDS AND EXPECTATIONS
Presented by David Avrin
How, when and where we buy has changed dramatically in recent years. Winning today is often determined by those who can deliver faster and are ridiculously easy to do business with. In this revealing, thought-provoking and very entertaining presentation, popular Customer Experience expert David Avrin, CSP shines a light on the profound shift in customer expectation, while showing your team everyone’s role in eliminating friction in the buying process, responding to prospects, and creating customer experiences worth sharing. Participants of this session will: Better understand the cause and
pervasiveness of the shift in customer and client behavior, recognize the profound difference between customer service and customer experience… and why that matters. Understand a day in the life of their customer and create alignment between their needs and our deliverables. Recognize the profound impact of social media and the devastating ramifications of underperforming in the eyes of your customers.
2:30 p.m. – 3:30 p.m.
INNOVATIONS IN TURNAROUND PERFORMANCE
Presented by George Perrett
Presented at over 40 industry events, this session will outline global best practices complied by 16 multi-national companies as a way to combat declining softskill workforce. Innovations such as modular scaffolding, digital design and twin construction, along with part tracking has improved the construction performance at industrial sites in Texas and Louisiana yielding 20 percent labor savings, and 18 percent reduction in costs. In addition to the savings and specific construction solutions, companies participating in the presentation can take away one or more ideas to implement in their next construction project and be recognized as an high performance contractor to industry. Presentation covers products represented by multiple sources not highlighting any specific brand.
3:30 p.m. – 4:30 p.m.
HOW TO EAT AN ELEPHANT: ONE BAY AT A TIME
Presented by Shawn MacDonald
Working for a tiny scaffold company in the big city for more than 30 years and competing against huge corporations for contracts doesn’t just make you think outside the box, it makes you throw the box away. We’ll take a look at jobs that tackled the impossible through creativity, experience and teamwork.
Attendees celebrate the SAIA Awards winners last year. PHOTO: KHL
MONDAY, SEPTEMBER 30
7:30 a.m. 2024 SAIA Annual Convention & Exposition Golf Tournament
9 a.m. - 5 p.m. Train the Trainer Facilitator Skills Workshop
1:30 p.m. - 2:30 p.m. SSFI Meeting
3 p.m. - 4 p.m. ASC A11 Main Committee Meeting
TUESDAY, OCTOBER 1
8 a.m. - 5 p.m. SAIA Café
8 a.m. - 5 p.m. SAIA Registration & Information Desk
9 a.m. - 5 p.m. Competent Person Training – Suspended Scaffold
9 a.m. - 5 p.m. Competent Person Training – System Scaffold
9 a.m. - 9:30 a.m. Product Demo – Crew Tracks
10 a.m. - 11 a.m. Product Demo – Kewazo
11 a.m. - 1 p.m. Avontus User Group Meeting
12 p.m. - 1:30 p.m. Lunch
1 p.m. - 3 p.m. SAIA Board of Directors Meeting
3:30 p.m. - 4:30 p.m. Ambassador Council Reception –New member and first time attendees only
5 p.m. - 7 p.m. Welcome Reception with Exhibitors
WEDNESDAY, OCTOBER 2
8 a.m. – 5 p.m. SAIA Registration & Information Desk
8 a.m. - 5 p.m. SAIA Café
8 a.m. - 9 a.m. Breakfast in SAIA Café
8 a.m. - 9 a.m. AAC Meeting
9 a.m. - 11 a.m. Conference sessions
11 a.m. – 2:30 p.m. Exhibit halls open (with lunch)
1 p.m. – 2 p.m. Council Chair meeting (invitation only)
2:30 p.m. – 4:30 p.m. Conference sessions
5 p.m. – 7 p.m. Reception with exhibitors
Representatives from Bee Access at their booth on during the SAIA Annual Convention & Exposition’s exhibitors hours.
Along with a sold-out exhibition hall, the SAIA will also offer product demonstrations, training, a golf tournament and stellar speaker line-up. Below are further details.
TUESDAY, OCTOBER 1
9 a.m. – 9:30 a.m.
PRODUCT DEMO: CREWTRACKS
CrewTracks helps streamline communication between the office and the jobsite. You will see how CrewTracks tracks time, creates reports, and manages your documents and plans to keep the jobsite running smoothly.
10 a.m. – 11 a.m.
PRODUCT DEMO: KEWAZO
Houston-based German company KEWAZO presents LIFTBOT - a lifting robot for scaffolding, enhanced by a data analytics platform. LIFTBOT is a batterypowered, remote-controlled vertical material handling aid that saves up to 70 percent of man-hours and improves safety. LIFTBOT provides maximum installation flexibility automating jobs that today are completely manual.
“Come to the live demo and learn everything you might want to know about the world’s first scaffolding robot,” the company said. “See how quickly LIFTBOT is installed; Experience how it is handled with just the hands of two scaffold builders; Learn how LIFTBOT is automatically operated with remote controls; See how the safety sensors work and learn what it means to your scaffold builders; Watch videos of successful projects; Review technical details and; Learn how LIFTBOT can help your business.
11 a.m. – 1 p.m.
AVONTUS USER GROUP MEETING
Calling all Avontus software users: You’re invited to join Avontus for a special user group meeting. “We will show you how to ditch the tape measure and hand drawing by scanning a structure with your phone, explore scaffolding drawings in augmented reality (if you aren’t yet using the free Avontus Viewer app, we’ll show you why you’ll want to,) share the latest software updates, get feedback on upcoming features and answer product questions to ensure users are getting the most out of their software investment. A prize will be given to the best question asked, and Avontus will announce a drone giveaway. Register to join us for this lively interactive session.”
Changing the way scaffolding is planned, managed and executed.
THURSDAY, OCTOBER 3
8 a.m. - 3 p.m. SAIA Registration & Information Desk
8 a.m. - 3 p.m. SAIA Café
8 a.m. - 9 a.m. Breakfast in SAIA Café
9 a.m. -10 a.m. General membership meeting with Council updates
10 a.m. – 11 a.m. – Conference session
11 a.m. – 2 p.m. Exhibit halls open (with lunch)
2:30 p.m. – 4:30 p.m. Conference sessions
6 p.m. - 7:30 p.m. President’s gala reception
7:30 p.m. - 9 p.m. President’s gala dinner & awards –
Theme: A Night Under the Stars
9 p.m. - 11 p.m. President’s gala after party –
Theme: Mile High on Cloud Nine
FRIDAY, OCTOBER 3
8 a.m. - 10 a.m. Farewell breakfast in SAIA café
Training is an essential element of the SAIA Annual Convention & Exposition, and for anyone looking to take care of requirements needed to meet for educational, certification or compliance purposes, the following courses will be available to take in Denver.
TRAIN THE TRAINER FACILITATOR SKILLS WORKSHOP
Monday, September 30 | 9:00 A.M. - 5:00 P.M.
Course Fee: $545 member | $645 non member
COMPETENT PERSON TRAINING – FRAME SCAFFOLD
Tuesday, October 1 | 9:00 A.M. - 5:00 P.M.
Course Fee: $350 member | $450 non member
COMPETENT PERSON TRAINING – SYSTEM SCAFFOLD
Tuesday, October 1 | 9:00 A.M. - 5:00 P.M.
Course Fee: $350 member | $450 non member
COMPETENT PERSON TRAINING – SUSPENDED SCAFFOLD
Tuesday, October 1 | 9:00 A.M. - 5:00 P.M.
Course Fee: $350 member | $450 non member
FOR ALL YOUR SPECIALIZED PROJECT NEEDS
Quality and performance make PCI a trusted industry leader. Our knowledgeable experts help determine the most effective scaffold system to fit your specifications.
• Power Plants
• Chemical Plants
• Refineries
• Paper Mill
• Bridges
• Shoring
• Roof Systems
• Exterior Walls
• High Rise
• Auditoriums
• Stadiums
• Weather Enclosures
EXPLORE SINGLE SOURCE CONTRACTING WITH PCI.
Streamline projects with PCI’s integrated services, reducing delays and duplication while improving efficiency and scheduling. Experience the PCI difference today.
Frame
Tube
OSHA
Steel
Trash
3rd
Product
City Hall in Oslo, Norway’s capital, is currently undergoing extensive renovation – with the help of several Geda units. SA reports.
Oslo’s City Hall has great historical significance to Norway and still hosts important events today. The Nobel Peace Prize is awarded there every year on December 10. It also represents Norway’s
independence from Sweden.
Following several delays caused by the two World Wars, City Hall was inaugurated in 1950 and is today famous above all for its impressive interiors and carillon.
In recent years, the toll taken by weather, salt water and other factors meant that City Hall had to be renovated.
The first step in this was to set up scaffolding on the eastern tower with the help of Geda 300 Z scaffolding lifts. Then, everything was dismantled from the eastern tower and put up again on the western tower to continue with the renovation work there.
The decision to use Geda lifts was swayed by factors such as lifting height and speed.
The two towers each measure around 65 meters and are no problem for these units.
Two Geda 300 Z scaffolding lifts played a major part in the renovation work on City Hall in Oslo. The two units were used exclusively to put up the scaffolding while a GEDA Multilift P18 Premium was then used to transport workers and materials.
The 300 Z is a compact, robust lift and can be erected by a single person, according to GEDA. The platform, measuring 4.59 feet by 2.62 feet (1.4 meters by 0.8 meters,) can lift materials weighing up to 661 pounds (300 kilograms.) The scaffolding lift’s 90-degree swivel car ensures a safe transition and easy loading and unloading.
The GEDA 300 Z is available in a 230 volt or a 400 volt version and can therefore be
The Norwegian scaffolding company Materialhuset AS has been a customer of GEDA for almost 20 years. The two companies work and collaborate frequently together on projects. Materialhuset AS has been an authorized GEDA dealer since 2012 and is now also an authorized service partner.
Geda offers 11 models of its Multilift product, with some geared toward special applications and permanent installations. Features and benefits across the line include:
■ Uni-mast system that’s compatible with GEDA Transport Platforms
■ Twin-mast system designed to work with scaffold, concrete or steel installations
■ Assembly planks for installation and dismantle
■ Reduced lateral loads due to dual mast design
■ Modular system
■ Enclosed cars for added safety
■ The integrated base enclosure is ideal for shipping as one piece via container or truck transport, and provide for faster installations
■ Variable frequency drive for smooth start and stop
■ Pre-selection control for automatic drive option
■ Overspeed safety brake
■ Overload sensors
■ Patented flat power cable to prevent twisting
■ ANSI A10.4 Code compliant
The company also offers nine models of material hoists with various load capacities and speed ratings.
Building specialists such as scaffolders, roofers and building contractors, whether they are working on a new construction project or a renovation, are often faced with the same task: transporting a wide range of building materials and tools quickly and safely to extreme heights where the construction workers are waiting.
GEDA material hoists were developed specifically for that transportation of scaffolding materials and other heavy loads. Due to the rack and pinion hoist system behind the material, the company says its elevators are easy to use and offer fast transportation. “At the touch of just one button the material hoist takes over that energy-sapping dragging,” GEDA says. “However, they must only be used for the transportation of materials.”
adapted ideally to the power supply at the construction site.
The scaffolding company Oslo Stillas Utleie, which is responsible for the work on City Hall, chose the 400 V 300 Z partly because of its speed and lifting height.
The chosen scaffolding lift can rise to a lifting height of 328 feet (100 meters) at a speed of 98 feet/minute (30 meters/minute).
After the scaffolding had been put up with the help of the two 300 Z materials lifts, the Geda Multilift P18 Premium was installed there to continue the work and to transport workers and their materials.
The Geda Multilift P18 Premium can similarly rise to a lifting height of 328 feet (100 meters) at a maximum speed of 131 feet/minute (40 meters/
minute.) The personnel and materials lift’s E platform, measuring 12.1 feet by 4.59 feet (3.7 meters by 1.4 meters,) can transport either up to 25 people or 4,409 pounds (2,000 kilograms.)
At City Hall in Oslo, the unit serves 30 floors that are fitted with Geda Comfort doors to ensure safe transfers to the building. This project has the huge advantage for the customer that the same masts were already available for the Multilift P18 Premium following the use of the 1500 Z/ZP in previous projects.
Both units used Geda’s Uni X masts, low anchoring forces, and are easy to erect as they use the same components. sa
In recent years, the toll taken by weather, salt water and other factors mean that Oslo’s City Hall needed to be renovated.
The SAIA MEWP Council is working on updating and publishing a new industry best practices document for the mobile elevated work platform sector. SA reports.
Just a little over two years ago, the Scaffold & Access Industry Association’s (SAIA) Mobile Elevating Work Platform (MEWP) Council appointed Tony Groat as its new Chair.
Groat, who is the North American regional manager for the International Powered Access Federation (IPAF), has been in the construction equipment industry for more than four decades, including 31 years in the equipment rental industry and more than a decade and a half with IPAF. He is a recognized industry expert and has been directly involved in the development of MEWP industry standards, including ANSI/SAIA A92 and CSA B354. He is also a technical expert for the U.S. on ISO TC214 standards.
As the MEWP Council Chair, Groat has been working with the Council over the past 24 months on impactful changes for the industry, including complete revisions of some now-outdated industry best practices documents.
“The SAIA Mobile Elevating Work Platforms (MEWP) Council mission is to
promote Safety Awareness in compliance with ANSI/SAIA A92 MEWP standards through a more informed access industry,” Groat says. “While many users are locked into OSHA compliance only, industry standards are really the ‘how to be complaint with OSHA requirements for MEWP worker safety.’ This council will champion the specific needs and requirements for all its stakeholders including manufacturers, dealers/distributors, owners, employers, users, operators, regulators and educators.
Our main goal is to take a leadership role regarding issues facing the industry that will ultimately benefit the entire industry by elevating discussion and awareness.”
SA sat down with Groat recently to see where the Council stands, and what’s to come.
Over the past 12 months, what has the MEWP Council been actively working on?
Groat: One of our key committee’s key projects is the updating of industry best practices for MEWP operator training, performing site risk assessments, and guidance on fall protection for MEWPs.
These three best practice documents offer some easy-to-understand guidance and recommendations for users of MEWP to follow in their compliance with these topics.
These best practice documents were initially published in 2010-11 and were focused on key issues the industry identified at that time. Since they were published, new ANSI/SAIA A92 standards were also published, and they have added new requirements and while some industry issues continue, we must address different issues that we face today.
While equipment design standards provide more options and safety, there is
The MEWP Council is considering the need to create brand new best practices documents, such as a statement of best practices of rescue plans for mobile elevated work platforms.
equally a need for users to improve their practices to ensure all work is both more productive and operations are safer.
When did the work start?
The work began in January of this year with the initial work specifically focusing on the Statement of Best Practices of General Training and familiarization for Aerial Work Platforms.
While the SAIA MEWP council took the lead on this project, for it truly to be an industry best practice, we needed to join again with American Rental Association (ARA), Association of Equipment Manufacturers (AEM) and IPAF to have the unified voice of the industry to be heard.
All agreed that there is a need to update
“Our council is open to the needs of users and operators of MEWPs. Let us know what you think and if you have specific needs we may consider.”
TONY GROAT
these best practices, so the work began at the end of Q1. It is the intent to work on one statements of best practice documents through completion before work begins on the next.
Why was this chosen over another topic?
The statement of best practices have been on all of the partnering Associations website as well as many of their members. While the existing documents have great value, the need to align with today’s standards and best practices has been expressed for many years. It was time to pick up the torch and lead the project forward. These statement of best practices are still the foundation for key issues for MEWP users and operators today.
What is the deadline for completion/where does the project stand?
Today it seems like everyone has a full plate with their primary job and allocating time to work on outside projects is increasingly a challenge for people’s time. That said, the working group
members are committed to getting these reviewed, updated and republished. We hope to have the first statement of best practice, now renamed as the Statement of Best Practice of Operator Qualification and Requirements for Training, Familiarization and Retraining for Mobile Elevating Work Platforms (MEWPs), will be ready to republish in Q1 2025.
As the change of title indicates, the best practices will expand from the initial publications, layout and artwork updated, but will maintain the format of being concise, easy to read, and relevant.
We hope to condense the process for the remaining two Statement of best practices and get both completed by end of 2025.
Looking forward, what will the Council be focusing on in the coming year? As indicated earlier, we will keep our focus on moving the statement of best practices to completion in 2025. I add that we are considering the need for new best practices documents, such as a statement of best practices of rescue plans for mobile elevated work platforms.
Are there any upcoming changes to standards/regulations that will impact the Council? If so, what are they? And what are the impacts?
As the best practices must be aligned with ANSI/SAIA A92 MEWP standards, changes to the standards will impact the all industry stake holders.
This is critically true for MEWP users and operators who are not fluent with industry standards, or when and how they affect them. It is possible that some of the ANSI/SAIA A92 MEWP standards will be republished some time in 2025, so the committee will plan, when that does occur, to implement an awareness campaign to assist users and operator meet their responsibilities.
promote safety awareness in compliance with ANSI/SAIA A92 MEWP standards.
We have the ability to help educate those using MEWPs to be more effective at completing their tasks and be safe in the process. That’s not a bad return on your investment. sa
The SAIA Mobile Elevating Work Platforms (MEWP) Council shall promote Safety Awareness in compliance with ANSI/SAIA A92 standards through a more informed access industry. This council will champion the specific needs and requirements for all its stakeholders including manufacturers, dealers/distributors, owners, employers, users, operators, regulators and educators.
What would the Council like to relay to readers of SA Magazine?
Our number one message is that you are invited to be part of this committee and share your experience, knowledge and opinion into the work we are doing to meet our mission to
in any and all MEWP Council meetings or initiatives.
■ Utilize the MEWP Council at Committee Week and the Annual Meeting as a forum to openly discuss issues that impact the MEWP industry, then define initiatives to bring about resolution.
■ Take a leadership role regarding issues facing the industry that will ultimately benefit the entire industry by elevating discussion and awareness.
■ Increase and strengthen the participation within the MEWP Council by actively soliciting participation from all stakeholders, with a focus on users of MEWP equipment.
■ Participate in the action items that are reflected in the SAIA-OSHA Alliance, in particular those that are associated with the Best Practices regarding MEWP Training and MEWP Fall Protection.
WHAT:
2024 SAIA ASC A92 Annual Meeting
WHEN: October 7-10, 2024
WHERE:
Harrah’s Las Vegas
3475 Las Vegas Boulevard South Las Vegas, NV 89109
Registration and information: www.saiaonline.org/a92annualmtg
For more than 35 years, the Scaffold & Access Industry Association (SAIA) has been developing safety guides for the aerial platform industry. The SAIA serves as the Secretariat for the A92 series of standards and is responsible for adhering to the policies and procedures outlined in the ANSI Essential Requirements, which govern the consensus development process.
The ASC A92 Committee develops American National Standards for design, safe use and training related to vehicle-mounted rotating and elevating work platforms, airline ground support vehicle-mounted vertical lift devices, mobile elevating work platforms (MEWPs), mast-climbing work platforms (MCWPs) and transport platforms.
The ASC A92 Main Committee meeting is open to the public for those who have
The ASC A92 Annual Meeting is set for October 7-10 in Las Vegas. Here’s what’s in store for this year’s gathering.
an interest in the standards activities that establish consensus rules, guidelines or characteristics for activities, or their results in the aerial platforms industry. Consensus (industry) standards are voluntarily used by manufacturers, dealers, owners, users and operators of mobile elevating work platforms (MEWP). The purpose of the standards is the prevention of accidents and injuries as well as establishing criteria for the manufacturers. The standards also aid the manufacturers, dealers, owners, users and operators of the platforms to understand their responsibilities.
Standards are used by a range of organizations to enhance their products and services, improve safety and quality and meet industry best practices. By being involved, committee members are able to directly contribute to and shape the direction of their sector. The process can also support a committee
MONDAY, OCTOBER 7
7 a.m. - 8 a.m. Breakfast
7 a.m. - 3 p.m. Registration & Information Desk
8 a.m. - Noon A92.2 Subcommittee Meeting Noon - 1 p.m. Lunch
1 p.m. - 5 p.m. A92.2 Subcommittee Meeting
TUESDAY, OCTOBER 8
7 a.m. - 8 a.m. Breakfast
7 a.m. - 3 p.m. Registration & Information Desk
8 a.m. - Noon A92.20 Subcommittee Meeting
8 a.m. - Noon A92.9A (Design) Subcommittee Meeting
Noon - 1 p.m. Lunch
1 p.m. - 5 p.m. A92.22 Subcommittee Meeting
1 p.m. - 5 p.m. A92.9B (Safe Use & Training) Subcommittee Meeting
5:15 p.m. - 6:30 p.m. SAIA MEWP Council Meeting – Review of Best Practice Documents*
WEDNESDAY, OCTOBER 9
7 a.m. - 8 a.m. Breakfast
7 a.m. - 3 p.m. Registration & Information Desk
8 a.m. - Noon A92.24 Subcommittee Meeting
8 a.m. - Noon A92.10A (Design) Subcommittee Meeting
Noon - 1 p.m. Lunch
1 p.m. - 5 p.m. A92.7 Subcommittee Meeting
1 p.m. - 5 p.m. A92.10B (Safe Use & Training) Subcommittee Meeting
1 p.m. - 5 p.m. A92.22 Subcommittee Meeting
5:15 p.m. - 6:30 p.m. A92 Subcommittee Chairmen Meeting
6:30 p.m. - 8 p.m. A92 Reception
THURSDAY, OCTOBER 10
7 a.m. - 8 a.m. Breakfast
7 a.m. - 8 a.m. Registration & Information Desk
8 a.m. - Noon A92 Main Committee Meeting
In April, the A92 Main Committee approved the splitting of A92.9 and A92.10 into two parts – design and safe use/training.
member’s professional development by:
■ Enhancing their professional experience.
■ Building networks and learning from other experts in their field.
■ Representing and protecting the public interest.
Additionally, some professional organizations award continual professional development points for standards development involvement that count towards professional certification.
The committee is looking for volunteers in the C-5 Government (users, general interest) and C-11 Regulatory Agencies categories.
■ C-5 Government (Users, General Interest): Government. Includes consultants and professional societies/ not-for-profits that are sponsored by or represent the government.
■ C-11 Regulatory Agencies: A governmental agency that regulates businesses in the public interest. Includes consultants and professional societies/ not-for-profits that are sponsored by or represent regulatory agencies. sa
Buy direct from the authorized manufacturer of Bennu™ parts Sales (new/used) | Rentals | Service | Parts (Series #1, #2, #3)
The new Continuous-Climb Series #3 self-leveling hydraulic scaffolding platform
•Galvanized Units Available
•Easy! Single Button Operation
•20,000 lb. Capacity
•Important Safety Features:
1) Automatic Gearbox Brake
2) Spring-loaded Lock (Safety Dog)
3) Counter Balance Valve
•Made in the USA
Nov. 6, 2024 –
(13) Hoists are currently erected and operating in the States of PA; NJ; DE; MD; DC and VA. The hoists will be offered in (4) separate lots with multiple hoists offered per lot, within each geographic location. Bid closing is Wednesday, November 6, 2024 at 4:00PM Eastern. Please contact auction company to obtain a Sealed Bid Packet or to inquire about the hoist specifications, length of remaining rental contract and income stream. East Coast Hoist reserves the right to accept or reject bids submitted.
Rolling Stock to Include: Grove Truck Crane; Gradalls and Forklifts; Knuckleboom Trucks; Truck Tractor; Trailers; Utility and Pickup Trucks; Rigging and Support Equipment
Complete Hoist Systems: (10) Tornborg FC7000 Dual-Car Hoist Systems will be sold complete with: 200’ of Tower; Tower Ties, Bases, Buffers and Counterweights; Doors and Screens; Hoist Car Motors, Limiters and Cat Heads.
Upgrade your Series #2 with new galvanized platforms!
Individual Hoists Cars: (85+/-) TORNBORG Rack and Pinion Hoist Cars to include: FC8000; FC7000, H7000; H and PH 6000; and H and PH5000
Large Quantity of Hoist Accessories to Include: Hoist Tower; Tower Ties; Tower Bases; Communication Systems; Doors and Screens; Trolleys; Gin Poles; Gear Boxes; Motors and Hoist Parts and Components Call (800) BID-N-BUY or Email sales@hunyady.com For Complete, Descriptive Brochure! www.Hunyady.com
David Glabe breaks down how to navigate and understand OSHA regulations and requirements.
The U.S. Occupational Safety and Health Administration, OSHA, was created when U.S. President Richard Nixon signed the Occupational Safety & Health Act on December 29, 1970. The act required, amongst other things, that employers provide a safe workplace for employees.
To assist employers in determining what constitutes a safe workplace, OSHA promulgated regulations that
define a safe workplace. And, knowing that employers may not want to fully cooperate with OSHA, the act includes an enforcement element whereby failure to comply can be quite detrimental, including fines and in some cases, jail time.
Less known is that the act also requires that employees “Shall comply with occupational safety and health standards and all rules, regulations and orders issued pursuant to
David Glabe is the founder of DH Glabe & Associates. He is also actively involved in the Scaffold & Access Industry Association and serves as a member on the ANSI A10.8 subcommittee for scaffolding.
this act which are applicable to his/her own actions and conduct.” Unfortunately, rare is the employee who knows this requirement exists. Fortunately, even rarer is any employee being cited for a violation of this obligation.
It’s no surprise that employees, and employers too, can be easily intimidated by the OSHA regulations. Frankly, reading the OSHA regulations can be a daunting task since a first look at the OSHA regulations can be a frightening experience, particularly when you consider there are literally thousands of regulations.
Fortunately, once it is understood that the regulations are organized in a logical manner, what was once insurmountable, now seems attainable.
While it might be difficult to accept, the OSHA regulations are actually arranged in a predictable fashion, making it easier for everyone, including employers,
employees and OSHA compliance officers, to find a specific regulation. Here is how it all works.
First, OSHA has regulations for the general, construction and maritime industries. This is important to know since each industry has its own regulations which means that there may be regulations that address a specific hazard in multiple industries. For example, there are scaffold regulations in both the maritime industry and in the construction industry. Fortunately, each industry uses the same numbering system. Next, to facilitate locating specific regulations, OSHA developed a numbering system that is used for all the regulations. To illustrate how the system works, let’s use the Construction Industry scaffolding regulations, which are designated 29 CFR 1926 Subpart L – Scaffolds. The 29 is Title 29 and is assigned to the Department of Labor (DOL). In other words, all the DOL regulations are in Title 29, including the OSHA regulations since it is
an agency within the DOL. CFR stands for Code of Federal Regulations. 1926 is known as a “Part” that identifies the Construction Industry regulations and each Part is divided into “Subparts,” which are lettered. In the Construction Industry regulations there are 28 Subparts, and in this example, the scaffold regulations are found in Subpart L.
So far, we have arrived at the subpart that includes all the scaffold regulations. The next step is to understand how the Subpart numbering system works to get to a specific regulation. The Subpart uses a hierarchy of sections, paragraphs, letters, numbers and Roman numerals to identify a particular regulation. The hierarchy starts with the Sections, followed by paragraphs, followed by sub-divisions and, believe it or not, this is where the actual regulation is hiding.
There are five sections within Subpart L where you will find the actual regulations that address hazards found in the erecting, dismantling, alteration and use of scaffolds. These five sections are:
■ 29 CFR 1926.450 –
Scope, application and definitions applicable to this subpart
■ 29 CFR 1926.451 –
General requirements
■ 29 CFR 1926.452 –
Additional requirements applicable to specific types of scaffolds
■ 29 CFR 1926.453 –Aerial lifts
■ 29 CFR 1926.454 –
Training requirements
There are also five appendices:
■ Subpart L, Appendix A –Scaffold specifications
■ Subpart L, Appendix B –
Criteria for determining the feasibility of providing safe access and fall protection for scaffold directors and dismantlers
■ Subpart L, Appendix C –List of national consensus standards
■ Subpart L, Appendix D –List of training topics for scaffold erectors and dismantlers
■ Subpart L, Appendix E –Drawings and Illustrations While you now are probably totally confused, perhaps an example will clarify how it all works.
Let’s use the regulation that specifies the size of a landing for a scaffold stairway used on a construction project to access a scaffold. The regulation specifies that “A landing platform at least 18 inches (46 cm) wide by at least 18 inches 46 (cm) long shall be provided at each level.” The regulation is identified as:
■ 29 CFR 1926.451(e)(4)(viii)
As previously described, 1926 indicates Construction Industry regulations. The number 451 is the section of Subpart L that is titled “General Requirements.”
The letter e is the paragraph and its title is Access. The number 4 is the subdivision of paragraph e and, believe it or not, is the actual regulation! The
Roman numeral viii, or number 8, is a sub-subdivision of the regulation and specifies the size of the landing, as quoted above. Summarizing, the regulation is found under access, which is in the General Requirements for scaffolding, used in construction. It is important to understand the significance of the hierarchy when applying the regulation. For this example, Subsubdivision (viii) only applies to Sub-division (4), which only applies to the Paragraph (e) which only applies to Section Number 451 which only applies to the Construction Industry Part 1926, which only applies to a Place of Employment in the United States. This means that this regulation cannot be applied, for example, to stairways used in general industry situations, or even to stairways used in construction to access a structure rather than scaffolding.
Another restriction on the use of regulations is that if there is a specific regulation that addresses a hazard, it supersedes a general regulation that addresses a topic. For example, the scaffold guardrail regulations in Subpart L supersede the guardrail system regulations
found in Subpart M – Fall Protection.
WE’RE NOT DONE YET…
Now that you fully understand how the system works, be aware this doesn’t apply everywhere in the United States. Certain states, including, but not limited to, California, Michigan, Washington, New York and Oregon, have regulations or numbering systems that may not agree with the federal OSHA regulations. Therefore, if you work in these states, or other states where the regulations vary from the OSHA regulations, you must also be familiar with them.
Now that you are an expert on the organization of the OSHA regulations, see if you can find this regulation: 29 CFR 1926(g) (4)(xiii). If you did not read that steel or plastic banding cannot be used as a toprail or midrail of a guardrail system, you’re in the wrong place.
Try again. Here is another challenge. What is the number of the regulation that specifies that scaffold user training must include information about the maximum intended load and the load-carrying capacities of the scaffolds used? Hint: 29 CFR 1926.??4(a)(?) sa
NEW TO THE LIGHTWEIGHT FAMILY
Superior Engineering Design Up to 10% weight savings
Seamless Integration
Protect your investment into existing Layher Decks & Allround
Enhanced Handling
Thanks to optimized steel caps and profiles
More Successful Projects
When benefits combine to support the bottom line
For more information: layherna.com
Safely and consistently delivering personnel to perform work at height for more than a decade.
Century Elevators is ready to collaborate with your team on current or upcoming projects. With a balanced fleet of elevators, hoists and platforms, we are here to help safely deliver your personnel to height. As a critical infrastructure company, Century Elevators is open and operating, while supporting our customers and delivering lifting solutions during this critical time. With on-call service technicians and installation crews in the field every day, Century Elevators is your partner in productivity – call us for a quote today.
Leaders of the IPAF team at a meeting earlier this year during the IAPAs.
Grab your harness and attach your lanyard – a brand-new access equipment and rental business event from ALH and IPAF is set for this November – and it’s one you won’t want to miss.
The Working at Height Conference and Awards will land in Nashville on November 19-20, kicking off with a networking reception on the evening of Nov. 19, followed by a day-long conference and awards event Nov. 20.
Co-organized by Access, Lift & Handlers (ALH) magazine and the International Powered Access Federation (IPAF), the Working at Height Conference & Awards combines the ALH Conference & Awards with IPAF’s Innovate Workshop, creating a world-class conference followed by an evening awards dinner celebrating the industry’s best.
From economic and market updates to how technology is helping safeguard the industry, this year’s Working at Height Conference will address best business practices, technology and more that will help to create safe and productive working environments. Confirmed speakers include:
Jim Dorris – “Creating a safety culture within the access/rental industry”
a strategy-driven product pipeline, leading the effort to drive business development and secure new partnerships and providing consultative expertise in building out commercial excellence for the organization.
His experience with architecting and leading a safety training and technology business, and bringing to market several innovative learning technologies, allowed him to make an immediate impact at NSC. Since 2017 he has served as a board member for the Campbell Institute and advisory board member at COVE: Center of Visual Expertise. He also served in safety leadership and business management roles at United Rentals, Cummins, Pfizer and PepsiCo.
Dorris will discuss why safety cultures matter and how to create a safety culture within the access and rental industries.
WHAT: Working at Height Conference and Awards
WHEN: Nov. 19-20
WHERE: Music City Center, Nashville REGISTRATION: www.workingatheightevent.com
Jim Dorris is the National Safety Council’s chief strategy officer, enterprise operations. Dorris leads the build-out of new operational and commercial capabilities and resources that will benefit the long-term growth and maturity of the organization.
Diego Bustamante – “MEWP accident statistics: How does the U.S. measure up?”
Diego Bustamante is the regional manager for Latin America at the International Powered Access Federation (IPAF) and a passionate advocate for safety in the powered access industry. With 17 years of experience, he has dedicated his career to driving innovation and collaboration across the sector, working with manufacturers, rental companies and industry associations to promote safer
Dorris focuses on areas that include leading the development and operationalization of a mature product development process, building >
practices and higher standards.
Known for his creativity and forward-thinking approach, Bustamante brings a unique energy to his role, constantly seeking innovative ways to engage industry professionals and improve safety protocols. His work has led to impactful safety campaigns and training programs that have not only raised awareness but also reshaped industry practices across Latin America.
Beyond safety, Bustamante’s enthusiasm for technology and education fuels his mission to make workplaces safer and more efficient. He is a dynamic leader who thrives on turning complex challenges into opportunities for growth, helping the industry move forward with fresh ideas and solutions.
A recognized figure across Latin America, Bustamante’s dedication to spreading the word on safety and promoting innovation continues to have a lasting impact on the powered access industry.
“The statistics we gather represent real people, real injuries, and, in some cases, real fatalities,” Bustamante says of IPAF’s accident and fatality research and data. “Every number in the IPAF Global Safety Report reflects an opportunity to save lives, protect workers, and improve operational safety. This data isn’t just a tool for reflection—it’s a catalyst for change. When we break down accident statistics, we’re able to pinpoint specific areas where training, equipment use, or operational procedures need improvement. The power of this report lies in its ability to guide the industry toward targeted interventions that can significantly reduce risks and prevent unnecessary tragedies.”
Attendees of this presentation will walk away with a profound understanding of the critical safety challenges facing the MEWP industry today. They’ll gain access to the latest insights from IPAF’s global accident data, learn how to
identify high-risk situations, and understand which operational adjustments can have the most significant impact on reducing accidents.
Nate Hoover – “Evolution of the jobsite: Ecosystem orchestration”
Nate Hoover is a director of product management at JLG.
Before joining JLG in 2018, he worked at IMI and W.L. Gore and Associates, holding various leadership and developmental roles within the Business Development, Manufacturing, Sales, Product Development, Marketing and Product Management functions.
Hoover will address how jobsites are evolving, and what the industry can prepare for in the future.
“In the rapidly evolving landscape of industrial innovation, companies like JLG, part of Oshkosh Corporation, are spearheading job site transformation through a strategic blend of technology and collaboration. This is accomplished through an intimate understanding of how to integrate electrification, autonomous technology and intelligent processes. For JLG, this is enabled by leveraging our organization’s global scope and vast technical depth.
“Our intention is to orient our focus on future job sites where the needs have evolved from standalone physical products to interconnected digital solutions, emphasizing data-driven insights and cross-industry orchestration. By fostering global partnerships, investing in smart engineering and developing integrated systems, we are creating products that not only complete tasks but also optimize workflows.
“This approach aims to redefine the expectations relating to operational efficiency, safety and job productivity. The ‘jobsite of the future’ is not a distant concept but an ongoing evolution of requirements that will be met
There will be plenty of networking opportunities
through innovation with a commitment to anticipating and meeting future challenges in an increasingly connected world.”
John McClelland, Ph.D. –“Rental industry market update and forecast” John McClelland has been with the American Rental Association (ARA) for more than 21 years. He is responsible for developing and implementing all ARA national and state political, legislative and regulatory strategies and programs, including the management of the ARAPAC, the association’s political action committee. McClelland also works with ARAmember state and local associations on issues that are important to the rental industry within those states.
McClelland, who has presented at previous ALH Conferences, will provide the most-recent market forecast and economic update for the North American equipment rental industry.
Scott Owyen – “How technology is changing the way MEWP training is delivered”
Scott Owyen is the director of training for Genie. His career at Genie spans nearly four decades, where he has worked in manufacturing, product management, sales, and, for the last 15 years, training.
Scott is responsible for overseeing the development of Genie Lift Pro operator training and Train-the-Trainer courses, to which he applied adult learning theories to make the material engaging and interactive. Since launching Genie’s online training courses, Scott and his team have been directly responsible for training more than 120,000 people around the world.
Always one looking for ways to make the industry safer, several years ago Scott embarked on a project to develop a quality virtual reality training tool. Launched earlier this year, Genie VR training complements classroom and hands-on training and gives operators the chance to learn how to avoid real-world MEWP operational hazards from the safety of a virtual world.
“Technology is expanding our ability to learn and make meaningful connections that can keep operators safer on the jobsite,” he said. “Imagine the ability to make a mistake and learn from mistakes that can cause a MEWP accident, without getting hurt.
“Virtual reality makes this possible. In the past, operators could learn from online and classroom training, but their first opportunity
to actually operate a lift required them to get into a lift,” he continued. “Today, VR makes it possible to get realistic-feeling experience, and learn to avoid real-world hazards that can cause jobsite accidents, from the safety of a virtual world.
“And, because our brains don’t recognize the difference between virtual and real worlds, it makes this an incredibly emotional and impressionable way to learn.”
TJ Lyons, CRIS, OHST, CSP –“MEWP incident prevention through machine design”
TJ Lyons is a recognized expert in prevention through design, he is a Certified Safety Professional (CSP) and Occupational Hygiene and Safety Technician (OHST), accredited by the BCSP, and a Construction Risk and Insurance Specialist (CRIS), certified by IRMI.
TJ spent most of his safety career with two of the largest construction firms in the US, spending several years working on defense project overseas. He recently retired from the construction industry and continues to push for a safer workplace. TJ is proud to have founded the successful “Ladders Last” efforts here in the U.S. to rid the workplace of those archaic devices.
A focused discussion on the philosophy of Prevention through Design (PtD) and examples of how firms are increasing efficiency and production while removing risk from the work. Prepare for blunt discussion on safety barriers in our industry and why just complying with OSHA is a recipe for failure.
Lyons will discuss how to reduce the need to work at heights while increasing the quality and speed of installations. He will speak directly about the efficiency of MEWP’s and the safety consequences those platforms can provide - lessons he has learned from the field. TJ will share a copy of his list of best practices you can take back to your firm; while providing “Well that’s a cool idea!” moments during the presentation you will appreciate. What you learn in this course will save lives.
Attendees tune in to a morning keynote held at a previous ALH Conference event.
Bart Krzysztofek – “Selecting the right PFPE”
Bart Krzysztofek is the product safety training supervisor at Skyjack, where he has spent the last 10 years. Krzysztofek came into the MEWP industry with a diverse background in the automotive manufacturing and supply chain sectors working in several management roles in quality assurance, materials management and operations. His training experience comes from more than a decade spent as a skydiving instructor, teaching both in-class theory and in-air practical skills for the Canadian Sport Parachute Association.
At Skyjack, Krzysztofek started out in manufacturing and worked on several new product launch teams before migrating into product safety training. For the last eight years, he has been training equipment operators and updating and developing Skyjack’s training programs. Krzysztofek is a member of the ANSI A92.22 and A92.24 sub-committees, the SAIA MEWP Council and IPAF’s North American Regional Council.
Tony Groat – “Exiting at height – how to be compliant”
Tony Groat has been in the construction equipment industry for more than four decades, including 30+ years in the equipment rental industry and 15+ years promoting safety with IPAF. He is a recognized industry expert, directly involved in the development of MEWP industry standards with ANSI/SAIA A92 and CSA B354 and is a technical expert for the U.S. on ISO TC214 standards. Groat also develops and delivers presentations and writes industry articles to raise awareness and promote the safe and effective use of powered access equipment. Further topics are as follows, with speakers to be announced soon:
■ Keynote address from one the world’s largest equipment rental companies
■ Panel: Technology’s role in working at height
For more information or to register, visit www.workingatheightevent.com. ■
There’s a lot of talk about “the jobsite of the future” — a place and time where electrification, autonomous technology and intelligent processes combine to drive efficiencies, maximize safety and increase overall productivity.
These ideals may seem like a far-off concept that’s years away, but with the industry taking continuous steps towards connection and optimization, that future has already arrived. And this transition, according to Rogerio dos Santos, vice president of strategy and product management at JLG, this transition is transpiring not all at once, but instead in stages, or, “moments of autonomy.”
“It’s not going to be like one day you’re on a totally disconnected jobsite, and then the next day, it’s a completely new world,” dos Santos says. “It is actually happening now.”
One step at a time
In July, Doosan Bobcat’s board of directors announced its plans for Doosan Robotics to complete a merger with Doosan Bobcat by early next year. Under the plan, Doosan Bobcat would become a wholly owned subsidiary of Doosan Robotics. In a company presentation, Doosan said that the strategy is part of a plan to “become a global full-range autonomous/ automated solution provider.”
“We think of technology related to electrification, autonomy and advanced connectivity as building blocks,” says Joel Honeyman, Bobcat’s vice president of global innovation.
Honeyman, who has been with Bobcat for more than 27 years, leads a dedicated team that works across those three technology pillars, and through partnerships with tech companies and providers, have created solutions that Bobcat
a look at how today’s technology
can implement across a range of its product categories.
“For the last five years, we’ve been doing quite a bit of active work,” Honeyman says. “For example, we invested in a radar company in Kansas called Einstein, and this is our collision warning and avoidance system that we’re piloting right now, which will be commercialized here by the end of the year.”
That ‘active work’ Honeyman and his team have been conducting has seen Bobcat debut a number of autonomous prototypes and concepts over the last few years, including the Bobcat AT450X enabled by Agtonomy, the allelectric and autonomous RogueX2 loader, an autonomous mower designed to operate with Greenzie software, as well as the company’s MaxControl remote operation, Bobcat Machine IQ and more.
Could Bobcat’s telehandlers be next?
“We are working across different areas because
JLG’s self-leveling chassis technology, seen here on a JLG 670SJ boom lift, automatically levels the unit on slopes up to 10 degrees.
it’s not ‘one-size-fits-all,’” Honeyman explains about utilizing tech across different products. “We’re certainly looking to apply these similar technologies to our telehandler family.”
Currently, Bobcat is looking into systems that detect if an operator is in the seat of a telehandler or wheel loader’s cab. “This technology would lend itself to enable the controls to be activated within the equipment,” Honeyman explains. “We’ve also looked at applying radars for collision warning and avoidance.
“These things are coming together under a strategy, but the solutions are unique depending on the vehicle and the application.”
Since the dawn of the Industrial Revolution, successive waves of technology have made work significantly more productive and safer, and workers’ roles have also evolved. For example, until the 1970s, most factory production work takes
was performed by manual labor. During this decade, many manufacturers adopted robots for welding applications that required a high degree of precision. In part, they also adopted these automated solutions to compensate for a shortage of skilled labor. During this factory floor revolution, the role of human workers evolved to focus on oversight and inspection.
“The hunt for autonomous machines and technologies is not new,” says dos Santos with JLG. “If we want to envision where robotics in access equipment is headed, a great place to start is how it’s now being used in adjacent
product categories and industries.”
The automobile industry is one industry that is consistently 5-10 years ahead of the construction industry. With automobile OEMs, technology follows a familiar path: New technologies are often first introduced on luxury vehicles because of their initial high cost. As these technologies mature, they are adopted by more consumers and build economies of scale; then, they move downstream to less expensive car brands. Examples include self-driving cars, active body control and adaptive cruise control. All involve autonomous or semi-autonomous vehicle control, which could be broadly considered a type of robotics.
self-leveling ensures that the equipment remains stable, even on uneven ground, reducing the need for manual adjustments. Load sensing allows the machine to detect and respond to variations in weight, optimizing performance and preventing overload. Variable tilt enables the equipment to adapt its angle automatically, ensuring optimal operation across different scenarios.
“An example is JLG’s unique self-leveling chassis technology, which allows the JLG 670SJ boom lift to automatically level on slopes up to 10 degrees, enabling operation on uneven job site terrain. This innovative technology promotes safe operation and increases maneuverability, eliminating constant repositioning and saving time,” dos Santos says.
Honeyman explains that Bobcat sees autonomy and technology solutions as a means to combat the ongoing labor shortage.
“The one thing I always mention is that these solutions are not necessarily about removing the operator,” Honeyman says. “We think about, ‘How do we supplement labor better? And how do we support the current labor that we have?’”
Now, more than ever, access equipment manufacturers are searching for ways to boost equipment safety and efficiency by using automated solutions, dos Santos notes.
While the construction industry hasn’t moved to fully autonomous equipment yet, there have been plenty of flashes of innovation with equipment offering steps toward autonomy, dos Santos explains.
“This evolution in autonomy, and in turn robotics, is not just about replacing human effort but enhancing the overall efficiency and accuracy of the job at hand,” dos Santos says. “The biggest driver in advancing autonomy and robotics in access equipment is the constant need to improve productivity, streamline repetitive processes and reduce operating costs. Robotic technology can handle repetitive tasks faster and at a more consistent level of quality.”
Examples already being used in both work-atheight and material handling applications include self-leveling, load sensing and variable tilt. These features allow MEWPs and telehandlers to adjust independently to changing conditions, enhancing precision and efficiency. For instance,
“For example, the safest place for operators is on the ground. Access OEMs can help keep operators on the ground with robotics and autonomy, making strenuous work less taxing and making high-risk tasks significantly safer. Reducing the physical and safety barriers can lower the overall hazards associated with construction jobs. This shift benefits current workers by making their jobs more manageable and efficient; it also has the potential to attract a new, diverse workforce. People who previously viewed construction as too physically demanding or hazardous might now see it as a viable and appealing career option.”
JLG has been working alongside Palladyne AI and Construction Robotics (CR) to collaborate on future machine concepts and solutions. Through its partnership with Palladyne AI, JLG supplied a 450AJ articulated boom lift to be used as the Autonomous Working Vehicle (AWV) in a proofof-concept project called Outdoor Autonomous Manipulation of Photovoltaic Panels (O-AMPP), which automates the transfer, lifting and placement of solar panels during installation, dos Santos says. JLG has also supplied two machines for integration with CRs's new battery-powered compact MZ100 Material Unit Lift Enhancer (MULE): a JLG RT3394 scissor lift and a Hinowa TPX4000 tracked pallet jack.
JLG says this initiative aims to use robotics on machines commonly used by masonry and concrete contractors to lift and place concrete blocks, removing the cumbersome, repetitive construction task that often results in cumulative injury. ■
Rotating telehandlers are changing the landscape of construction. ALH speaks with manufacturers on their latest launches and developments.
With their versatility and the ability to do so many tasks from one small footprint, rotating telehandlers are definitely transforming the way construction is done.
“People who work in the construction industry are an innovative group, always looking for more efficient, safer, better practices for constructing buildings and putting things together, for getting their work done,” says Steve Kiskunas, product manager for telehandlers at Manitou. “The reason a telescopic handler even exists is because 50 to 60 years ago, contractors were breaking their backs hauling materials up ladders to get their work done. They needed a rough-terrain, four-wheel drive, four-wheel steer powered tractor with a boom to place the materials instead of hauling it up by hand.”
Today’s telehandlers are much more sophisticated, with cabs boasting some of the
latest technology for operators.
Kiskunas believes the market is going to further adapt to rotating units because of such.
“We’re going to see even greater use of technology in making the equipment easier to use,” says Kiskunas. “More telescopic handlers will have guided information to help operators who perhaps are not as skilled as the ones they are replacing, to help them learn the equipment and to be able to operate it correctly.”
We spoke with Manitou, Magni and JLG about the rotating market here in North America. Here’s their take on trends, opportunities, electric models and more.
What are the three biggest trends within the North American rotating telehandler sector currently? Why are these occurring?
Daliborka Ribeiro, director of product management — telehandlers, JLG: Telehandlers have long been a staple on North American jobsites, and right now, rotating telehandlers are the new trend. The ability to be a “3-in-1” machine is a key factor in the growing popularity of rotating telehandlers. With their heavy lift capacities, extended reach capabilities, and, most importantly, 360 degrees of continuous rotation, market acceptance continues to
more awareness, we believe they’ll soon become a mainstay on construction sites in the region. Joe Leinwol, chief sales officer, Magni America: At Magni, the trends continue to be higher capacity, enhanced safety and operator comfort. Rotating telehandlers are now more versatile than ever, equipped with a wide array of attachments that allow them to handle multiple tasks such as lifting, moving, and placing loads. This adaptability makes them indispensable on jobsites, particularly in tighter work sites and urban environments where space is at a premium. The ability to safely execute the tasks of a crane in many instances is a game changer and provides significant cost savings.
The integration of advanced technologies like Load Moment Indicator (LMI) and Load Limiting Technology control systems found in all Magnis further enhances safety and productivity. These innovations enable operators to manage loads more efficiently, significantly reducing the risk of accidents.
What regions of North America are you seeing increased demand and utilization for these machines? Why?
Ribeiro: Demand for rotating telehandlers in North America is increasing as worksite space decreases — whether operators need to lift and place, work at height, or move suspended loads, rotating telehandlers allow them to maneuver better in confined areas, completely transforming how crews work.
Within North America, the United States has now surpassed Canada in the number of rotating telehandlers in the market. As with all equipment, the United States naturally has a much larger market opportunity, but it wasn’t until the last couple of years that the United States started to gain an appreciation for rotating telehandlers.
As contractors better understand the benefits of rotating telehandlers, we expect to see a further increase in overall demand in both regions as North America continues to show positive growth potential for the future.
The market here is truly beginning to recognize the benefits of these machines, with rental companies and contractors adding rotators to their fleets and jobs to increase productivity and work efficiency. Looking at the rotator’s growth and utilization over the last handful of years in North America, how do you see 2025 playing out for sales and demand? What will be driving factors?
Ribeiro: Similar to the last few years, we expect that 2025 will continue to show growth in adopting rotating telehandlers in the region. As jobsites become more congested and equipment and labor shortages continue to impact project schedules, rotating telehandlers can offer solutions of multiple machines while remaining stationary on the job site.
The driving factor in adoption will be the wide range of applications in which these machines can
offers three rotating telehandler models in North America: R1370, R1385 and R11100 (pictured below).
Ideal Crane Rental has been a Manitou dealer for more than two decades, and just five years after joining Manitou’s network, the company added rotating units to its fleet.
“With over twenty years of experience with these products as a Manitou dealer, we have been able to introduce this impressive piece of equipment to many customers and they see the direct benefit in the versatility of these machines,” says Kurt Kalhagen, VP of operations, Ideal Crane Rental, Inc.
We sat down with the crane rental company to discuss the rotator’s place in any rental fleet.
How did you first learn about rotating telehandlers?
We’ve been a Manitou dealer since 2003 and started carrying the rotating telehandlers in 2008. We were intrigued by the possibilities of what this equipment could do. At the time there were very few options for rotating telehandlers in the US.
When and why did you add them to your fleet?
Rotating telehandlers can be used in a very compact area due to their availability to turn both left and right. They also give more horizontal and vertical reach than most of the regular telescoping boom forklifts. The rotators also offer good stability due to the outriggers and this also adds capacity.
What applications or types of jobs are your rotators most used on? Why?
Originally, they were used mostly for setting things on the floors of mid-rise buildings under construction. But now carpenter contractors have realized their advantages and we see many of them using rotating telehandlers for framing houses. As well, they are popular for large masonry projects, formwork and utilizing them with a man basket as an aerial platform.
How has the market for rotators changed or evolved in the U.S. over the last handful of years?
Our new Manitou Vision series offers remote control operation which many customers really like. As well, the machine telematics are now very comprehensive including data you can access from your phone, including maintenance schedules, GPS tracking and general fleet management.
be utilized. Rotating telehandlers are ideal for staging material on commercial construction jobsites — especially in urban settings where working space tends to be highly congested. And because of the unique features and benefits of these specialty machines, these machines can also be used in various other types of work, including renovation, masonry, roofing, demolition, cladding, tunneling, bridgework, facility and industrial maintenance, as well as shipyards and ports.
Leinwol: At Magni we foresee continued growth in demand for 2025. Magni rotators offer contractors a significant advantage. With their versatility and range of attachments, a single machine can handle tasks that would typically require three separate pieces of
equipment, leading to substantial cost savings. The efficiency of the 360-degree rotation eliminates unnecessary movements associated with traditional fixed boom telehandlers, saving valuable time on the job. Additionally, with Magni’s remote control, operators can work outside the cab, positioning themselves closer to the task at hand for increased precision and further time savings and in some cases reducing the need for more labor.
What was your company’s most-recent rotator debut and why was this launched? Did it fill a product gap? Was it a replacement?
Ribeiro: JLG offers three rotating telehandler models in North America: R1370, R1385 and R11100. This range boasts capacities from 11,000 to 13,000 pounds and maximum reach heights of 67 to 97 feet, with the R11100 being JLG’s highest-reaching telehandler.
Leinwol: Our latest innovation, the RTH 6.31 EC (extended cab) model, is a game-changer in our product lineup. This new version enhances the already impressive RTH 6.31 (13,200-pound
capacity/100 feet height) with an elevated cab that reaches 5 feet into the air and features a tilting function for superior visibility. It’s engineered to excel in challenging conditions where clear sightlines are crucial and to provide operators with an unparalleled level of comfort. The ergonomic design ensures optimal positioning, making it especially effective for handling delicate loads and using specialized attachments. This model not only sets a new benchmark for precision and safety but also significantly boosts operational efficiency.
We’ve seen some electric rotating telehandlers be teased and launched to market recently. Will this sector see more electrification on these machines in the coming year?
Ribeiro: JLG is very familiar with electrifying machine parts and developing all-electric systems for our machines. We continue to work closely with our customers to understand their needs for the jobsites of the future, and we remain committed to providing telehandler solutions that meet specific application and market requirements.
Kiskunas: We’re offering three different ways to achieve zero or low emissions. The first way is a standard, 680-volt battery back in the rotating machine. The second option is to have a double-battery pack – or two 680-volt
batteries – for a longer period of operation. And the third option is a 680-volt battery pack with a low-horsepower diesel engine to recharge that battery at the range extender – it’s not zero emissions, but it’s a very low-emission option. We expect it will be very popular in North America because we don’t have the zeroemission requirements that Europe does. But with that option, you can actually use the diesel engine to charge the battery if there isn’t a power source available on the jobsite.
When the machine does need to achieve zero emissions, it can be easily converted by taking out the diesel engine and running on just the battery.
The machine is designed so that the hybrid portion of the low-power diesel can be easily disconnected from the machine. Then if you want to operate it as a fully electric vehicle, just use your standard charger with a local power source.
Will you be launching any new rotators through 2025?
Ribeiro: Updates to our current rotating telehandler portfolio will include more commonality in operator controls. Achieving more uniformity with operator controls helps operators feel more confident when using different machine models from the same product family.
New product enhancements will also include new accessories, specialized attachments and a few updates to our existing attachment offering. These product changes will help our customers to improve their productivity as well as further expand the scope in how they are using rotating telehandlers today.
We are also excited to announce that JLG’s ClearSky Smart Fleet (Internet of Things) solution, the industry’s first two-way fleet management and communications platform, will be standard on our rotating telehandlers in 2025.
What are three top tips for a rental company considering to add rotators to their fleets?
Ribeiro: Rental companies considering the purchase of a rotating telehandler should keep these three things in mind: 1) How these machines will be used, 2) What lift capacities these machines can achieve and 3) What attachments increase the machines’ utilization. Leinwol: 1) Adding Magni rotators gives a rental company the ability to offer their customers better and safer solutions, 2) The ROI for rotators is very strong, and 3) As the leader in dealer support including in the U.S. parts availability, training, service and sales support, becoming a Magni dealer is the best investment possible. ■
Impressive Reach: Up to 75 ft working height and 48 ft 7 in outreach.
Powerful Capacity: Supports up to 550 lbs on the platform.
Compact Size: Fits in tight spaces with a width of just 7 ft 3 in.
Convenient Operation: No CDL or DOT medical card required.
Truck-Mounted: Mounted on a Ford Transit 350 chassis for easy mobility.
Fast Setup: Quick setup and breakdown for efficient job execution.
User-Friendly: Simple to drive and maneuver, ideal for various applications.
New technologies paired with compact designs are fueling the latest developments within the truck-mount sector. Lindsey
While the truck-mount market in North America isn’t quite as wellestablished as it is in Europe or the UK, the potential for growth and increased utilization across the U.S., Canada and Mexico is trending upward, according to Ebbe Christensen, president, Ruthmann Reachmaster N.A.
“Where both the small and truck-mounted lifts have had their domain in the utility world, there is a tremendous drive in a lot of new sectors, including wind power, building maintenance, construction and other applications,” Christensen says. “It is relatively unknown to the larger population of our industry that the truckmounted segment has expanded its footprint
into the more ‘general’ replacing less safe cheaper) solutions efficiency factors, along with safety concerns, has – have taken the driver’s seat in the market.”
According to Christensen, there are only three players in the North American, ultra-tall (250-feet or higher) truck-mount sector (which includes Ruthmann Reachmaster N.A.) When you compare that figure to the many, many scissor and boom lift OEMs present across the U.S., Canada and Mexico, it would seem that the market just isn’t interested in truck-mounted MEWPs. But Christensen sees it differently.
The Ecoline 270 is the latest addition to Ruthmann’s line up.
Palfinger’s new Tec Class line will be launched this year.
“Rental opportunities have not been here for these units before,” he says, adding, “There is a need for product education.”
Christensen points to Mateco’s involvement in Mexico’s growing equipment rental industry.
Mateco, a major European equipment rental company, officially entered the Mexican equipment rental market in 2022, and a year later, expanded its product offerings to include telehandlers, forklifts and truck-mounted aerials.
In April 2023, the rental company added additional Versalift and Ruthmann truck-mounts to its fleet.
Today, the company operates from two branch locations in the country, one in Tepotzotlán and the other in Puerto Morelos, and it offers a range of access and material handling equipment rental solutions. With 295-foot truck-mounts at its disposal, the company operates the highestreaching fleet of truck-mounts in the country.
“The interesting part is that rental opportunities had not been in Mexico, nor the U.S., before,” Christensen says. “But now they are happening.”
“The demand for these big units is spawning and rapidly growing,” Christensen says. “While
the Europeans refer to them as the 3.5-ton market – the limit before CDL in Europe – the units entering North America are modified versions that don’t have to observe the 3.5ton limit and can go much higher while still remaining below the U.S. CDL.”
Compactness with maximum performance has long been Ruthmann’s mantra. Its latest offerings include the Steiger Ampero TBR 260 E, the new version of the Ecoline 270, and the Steiger T 1000 HF.
The Ampero TBR 260 E electric truck mount was launched recently during the IFAT 2024 exhibition in Munich.
The fully electric unit features a unique concept where the Iveco eDaily’s battery centrally powers both the driving and lifting mechanisms. This enables silent and emissionfree operation on a 5.5- to 7.2-ton chassis.
There are plans for new hybrid and electric models with enhanced battery life, greater efficiency and reduced environmental impact. However, as Christian Roß, head of international sales at Ruthmann, points out, while the company has the capability to build nearly all its products on fully electric trucks, the market is not yet ready to buy these combinations.
“By investing in research and development, we aim to lead the industry in providing environmentally friendly alternatives that do not compromise on performance or reliability.”
Returning to traditionally powered models, the improved Ecoline 270 was introduced during Innovation Days in Hohenroda, Germany, this year.
It boasts a working height of 27 meters and a reach of 16 meters. Despite its powerful capabilities, it maintains a compact vehicle length of 7.53 meters and allows for setup at an incline of up to 5 degrees. Significant enhancements include a new user-friendly display, protected sensors and optimized hose routing, making it more robust and easier to operate.
Long-term, says Roß, “Our focus will be on enhancing performance, safety and environmental sustainability. We also aim to explore new markets and applications for our truck mounts.”
The main challenges in the sector, adds Roß, include maintaining stability, ensuring safety and optimizing weight distribution while providing longer outreach on a compact chassis.
“We are addressing these challenges through innovative engineering solutions, such as advanced materials, sophisticated stabilization technologies and comprehensive testing.”
Developing and expanding
The potential in the truck-mount market has driven OEM Palfinger to develop its access platform product line to run parallel to its massive crane division, which forms the basis of the company.
“Our goal is to expand the access platforms into a second strong product line in addition to our main product, the loader crane. That is where our Löbau site plays a very special role,” said Alexander Susanek, COO at Palfinger. “Here, we have made investments specifically in product development, know-how and quality. With a larger capacity assembly line and our focus on service, we are now hitting the ground running.”
In Köstendorf, close to the company’s headquarters in Bergheim, Austria, the company has set up a technology center for access platforms and have expanded it in recent years. During the past three years, Palfinger has
invested more than €14 million in expanding the Löbau site, in the Görlitz region of Saxony, meaning that an area of around 78,000 square meters is now home to a state-of-the-art production hall, an in-house test area, a service center and offices. A total of around 300 people are employed in Löbau, a fifth more than two years ago.
Since 2023 the site has assembled the large platforms, adding to the light and premium class models. The company also has a strategic focus in the North American region, particularly the U.S.
Palfinger’s CEO Andreas Klauser delved further into the subject.
“We see significant growth potential in the area of access platforms. The product is extremely versatile and is used worldwide in
various industries such as construction, energy, and logistics.”
Electrification will also play an important role in the company’s strategy, with the P 280 CK eDRIVE was one of the first low emissions access platforms on the market.
In addition to the fully electric chassis it is also possible to convert the existing fleet of access platforms to minimum emission operation quickly and easily using retrofittable eDrive battery packs. Because they are battery operated, these machines can work on job sites without a power supply at the same working speed as in diesel mode.
The new TEC Class line to be presented at Platformers Days, among other shows this year will be in the 19-meter to 28-meter working height range, which has been significantly
MEAN BUSINESS
Our new micro scissor range represents a significant new option in the low level access arena; ideal for easy accessibility into tight spaces.
AC electric drive provides outstanding duty cycles and increased return on investment through reduced maintenance needs.
The SJ3213 micro and SJ3219 micro cost of ownership with our renowned product support.
✓ 13 ft and 19 ft platform heights
✓ 500 lb platform capacity
✓ AC electric drive performance
✓ 20” rollout extension deck
✓ Low GVW, fits standard elevator
skyjack.com/mighty-micros
improved and visually redesigned, including the expansion of the eDRIVE capabilities. All models are equipped with the option of installing an eDRIVE battery pack as standard.
In addition, numerous performance upgrades have been made and modularity between components has been implemented in order to simplify servicing and make it more efficient. Digital solutions such as improved connectivity and integration into various fleet management systems have also been considered. All new models are also compatible with the new GSR2 regulations (General Safety Regulation.)
Versalift recently launched the updated VTL130-FZ and VDTL-160-FZ modified to fit the new 2024 Ford Ranger pickup, while the new V-200 is mounted on a 3.5-ton Iveco Daily.
The V-200 is a high-performance telescopic lift that comes with automatic stabilization as standard, and is installed on either the Iveco Daily or MB Sprinter.
In transport position, the V-200 is less than 3 meters tall, with a working height of 20.4 meters and a horizontal reach of 14 meters, while the wide working diagram provides versatility for operators.
The impressive maximum bucket capacity of 300 kilograms allows up to two operators to carry a good deal of equipment and tools with
them. Constructed from high-strength steel, both the V200 and the subframe are lightweight yet robust, offering ample spare payload to install additional Versalift hybrid systems like the e-Tech lithium battery pack system.
The Versalift automatic stabilization and levelling system enhances safety and makes stabilization maneuvering hassle-free and can be performed from the bucket or from the optional control panel located at the rear of the vehicle.
The company is constantly looking into the most modern fabrication methods to make the lifts as light and compact as possible.
In addition, the company says its receives a lot of requests for 100 percent electrical solutions, with vehicles with the longest ranges being favored. “With the e-Tech range of battery packs we can offer a hybrid solution for all of our lifts and we already offer installations on several fully electrical chassis and vans.”
CTE agrees that the main challenges in the industry is engineering, designing and manufacturing lighter structures to maintain stiffness and resistance to fatigue. The company is achieving this through its latest product, the ZETA 24 J, launched it at the GIS Expo in Italy, last October.
Set up on a 3.5-ton GVW chassis it has an articulated boom which allows maximum performance across the work area, and ideal for world of rental. It is also the only double articulated platform with jib, says the company, that can position the basket close to the ground for easy access.
The 24-meter model pairs with the smaller Zeta 22, that was introduced in 2022, and completes the updated range of double articulated pantograph lifts, with three section telescopic boom and fly jib, building on the concept of the
GSR, which specializes in easy-to-use equipment, most recently launched the 13.15-meter working height B270T Comfort XEE - a telescopic platform installed on a 3.5-ton vehicle. The highperformance machine in terms of height and outreach is designed to be very simple to use while remaining faithful to the company‘s design principle of robustness and reliability.
A new van-mounted version with a 14-meter height will be released soon. There will also be new fittings designed to be common to truck mounted models, which themselves are constantly evolving technically in terms of safety and energy saving.
“The challenge is the search for new technologies that increase performance and are easy to manage for our customers,“ said the company.
On the green energy side, the company said it is focused on this and will take on the challenge of producing an electric model in the near future. And trends are towards very low consumption internal combustion engines, or endothermic engines, “which are being talked about a lot at the moment.“ Hydrogen engines are also on the rise, says CTE.
original Z model of the '90s, while integrating the EVO management system.
A narrow jacking stabilizer is designed in combination with an up & over that are impressive, considering the small footprint of the narrow jacks, offering to the operator great versatility as well as excellent working envelope. Its main features: 24 meters of working height, 10.5 meters of outreach and a basket capacity of 250 kilograms. Going forward CTE is concentrating on new EU regulations in terms of GVW, without compromising performances of the MEWP.
There will also be a focus on installing the 20-meter working height electric-powered MP20EV on a new electric chassis, as part of the company’s Green project.
CTE’s plan is also to redesign and redefine MEWPS over 3.5 tons, introducing the EVO system on heavy duty units. Below 3.5 tons, there will be a focus on electric and hybrid.
Compactness is a focal point of Oil & Steel with its recently introduced Snake 16 and Snake 24FB at the GIS show in Italy last year, and the Snake 26 at the company’s open house in June.
Coming up soon will be the new range topping telescopic Scorpion 18, which completes the 3.5 ton range, with electric controls, H outriggers and variable stabilization as standard, the advanced HMI and electronic functions, as well as telematics and remote diagnostics.
Looking forward the company is also uncertain of the future of electric chassis, although is more convinced about electric lifts. “We have mixed signals from the market after an initial period of interest from customers, the demand has practically disappeared.”
“As far as hybrid machines are concerned, we are extending the application of the batteries to more models and at the same time working on the characteristics of battery packs themselvescompactness, cost, characteristics.”
New thinner higher strength materials are also in the mix, for different machine geometry and articulation.
Advanced designs are also on the menu for greater strength and less deformation. ■
The International Powered Access Federation (IPAF) is pleased to announce the appointment of Randy Marzicola as VP - North America. With an extensive background in business development, strategic partnerships, and market expansion, Marzicola brings a wealth of experience to IPAF and will play a key role in enhancing IPAF’s services and member recruitment across North America.
Marzicola joins IPAF with over two decades of experience in the industrial and construction machinery sectors. His most recent position was Director of Business Development at JLG.
Throughout his career, Marzicola has demonstrated proficiency in strategic planning, go-to-market strategies, and operational excellence.
At JLG, he played a key role in identifying market expansion opportunities and establishing successful partnerships, including a notable alliance with Hinowa,
which led to an acquisition in 2023. His innovative approach and commitment to profitability improvement have consistently delivered outstanding results, such as driving end-user adoption of the North American Power Towers portfolio into a high growth business.
Prior to his tenure at JLG Industries, Marzicola held significant positions at Timex Group USA, The Stanley Works, and Black & Decker. At The Stanley Works, he expanded the builders’ hardware programme to 600 Home Depot stores across North America, doubling market share and sales.
His leadership and Six Sigma expertise at Black & Decker resulted in substantial cost savings and process improvements.
Marzicola’s primary focus will be on recruiting new members to the federation whilst Tony Groat will
IPAF’s ePAL app is your digital wallet to store and share your IPAF powered access licences and qualifications, including the PAL Card for mobile elevating work platform (MEWP), mast climbing work platform (MCWP) and hoist operators. Competent Assessed Persons (CAP), MEWPs for Managers, Site Assessment (for MEWP Selection) all can be added.
Randy Marzicola
continue to focus on standards, current members and training operations, and the IPAF North American council. Both Randy and Tony will report directly to Peter Douglas.
To support IPAF’s objectives of promoting the safe and effective use of mobile elevating work platforms (MEWPs) and mast climbing work platforms (MCWPs), Marzicola will also organize and participate in trade exhibitions on behalf of IPAF, supervise marketing activities and speak at various conferences and seminars throughout the region.
“We are thrilled to welcome Randy to IPAF," said Peter Douglas,
Digital Training Records: A digital wallet to store and share IPAF powered access licences and qualifications, including the PAL Card for MEWPs, MCWPs and construction hoist operators.
Guided and Non-guided MEWP Pre-Use Checks: Streamlined digital versions for comprehensive assessments in adherence to OEM guidelines. Exportable Pre-Use Checks: Operators can now export and maintain records of their checks.
Visual Warning for Failed Checks: Immediate alerts if a machine fails the Pre-Use Check, enhancing safety measures.
Digital Logbook: Provides an overview of operating experience on various powered access machines.
Machine Familiarisation Record: Keep a record of machine familiarisation, enhancing operator proficiency. Share machine work logs using device
CEO and managing director of IPAF. "His extensive experience in business development and strategic partnerships make him an ideal fit to play a key role in our North American operations. We look forward to the positive impact he will undoubtedly bring to our organisation and members, and we are now even more optimistic about the future in this region. Welcome to IPAF, Randy!”
sharing tools, such as email and messages.
Safety Guides Access: Operator and site safety guides are readily available through the safety section of the app.
Reporting Accidents and Near Misses: Quick and anonymous access to report any accidents and near misses involving powered access machines, which helps IPAF to gather vital industry safety data.
Most functions of the app are available to non-IPAF trained users. The ePAL app is your daily tool to document your MEWP experience. Machine familiarization, daily pre-start inspections, days of use are some of the important requirements of an operator that can now be easily tracked.
If you have an IPAF wallet card or even those trained elsewhere, go to the app store and download the IPAF ePAL app today and see for yourself how you can record and track information that is vital to MEWP safe operations. Use the app to develop your skills and best practices to improve safety for you and others.
Available for both new and existing IPAF licence and qualification holders, the ePAL app is accessible via the Apple Store and on the Google Play Store.
The International Powered Access Federation (IPAF) is pleased to announce the release of its updated leaflet on the service, inspection, and maintenance of MEWPs. This comprehensive leaflet has been updated to reflect the current industry landscape and is now available in 10 languages: English, French, German, Italian, Korean, Chinese simplified, Portuguese, Spanish, Turkish and Dutch. Brian Parker, IPAF’s Head of Safety and Technical, states, “We emphasise three crucial elements to ensure the safe operation of MEWPs: Conducting pre-use checks, adhering to servicing and maintenance as per OEM recommendations, and ensuring periodic inspections/examinations are carried out by competent personnel. Our updated leaflet is now tailored to meet the needs of our global audience.”
MEWPs are among the safest methods for performing temporary work at height. To maintain their safety and efficiency throughout their operational life, it is crucial to keep MEWPs in optimal working
condition. This can be achieved through a threefold approach: pre-use inspections, scheduled servicing and maintenance, and periodic inspections. Each of these elements is distinct but interconnected, contributing to the overall safety and functionality of MEWPs.
Understanding the differences between these elements is vital for maintaining MEWP safety:
Pre-Use Inspections: Conducted by a competent MEWP operator before use.
Service and Maintenance: Regular servicing by a competent person, including checks of hydraulic and electrical components.
Periodic Inspections: In-depth inspections by authorised engineers/technicians at intervals specified by the OEM and regional standards.
A comparison between ensuring the safety of a car and a MEWP highlights the importance of each safety measure:
Pre-Use Checks: Just as drivers check their cars before driving, MEWP operators perform visual and functional checks before use.
Regular Inspections and Maintenance: Similar to car maintenance by qualified staff, MEWPs require regular inspections and maintenance to stay in good working order.
Government Approved Testing Centres: Just as cars undergo government-approved tests, MEWPs need thorough, impartial examinations by competent persons to ensure continued safety.
For more detailed guidance, download the complete leaflet at: www.ipaf.org/guidance.
IPAF is a strong advocate for industry participation in OSHA’s annual Safe & Sound week, which took place Aug 12-18. The annual event promotes workplace health and safety programs and offers information and ideas on how to keep America’s workers safe. IPAF believes planning is the key initial step to identify potential hazards and taking the steps to eliminate them or reduce their risk to workers while performing their task. ANSI/ SAIA A92.22 MEWP safe use standard additionally requires that all MEWP users develop a safe use program specific to MEWPs that ensures that prior to putting a MEWP into operation, safe use protocols
are in place to influence good behaviors. A plan also confirms the effective management of risks associated with the work, and risks specific to the type of work, have been considered. IPAF has developed a guide to assist MEWP users in developing this plan that can be downloaded from the IPAF website. As OSHA Safe & Sound program is broader than MEWP operations, IPAF encourages all employers participate and to take one of the Core Element challenges to be #SafeAndSoundAtWork. These include management, worker participation and fix and find hazard challenges. Visit www.osha.gov/ safeandsoundweek/ for more information.
MEWPs are inherently the safest means to gain temporary access to work at height, but all work at height is exposed to certain hazards, such as falls. Conducting a risk assessment is a required practice that can identify potential hazards involved with the site and task to be performed. Do you know what the potential hazards for MEWP operations when conducting your risk assessment?
History is the best way to predict the future, and reporting MEWP incidents is how the industry tracks history of incidents, such as the IPAF incident reporting portal (www. ipafaccidentreporting.org.)
How many MEWP incidents do you think were reported to date in the U.S. alone? (Answer 88) How many fatal accidents? (26) What were the leading hazards reported? (Answer – stability/ overturn followed by road traffic accidents).
Knowing, rather than guessing, is critical when making informed decisions and planning. If you are in the MEWP industry, consider reporting any MEWP incident at www.ipafaccidentreporting.org.
There’s only one place you’ll find the heavy hitters of concrete and masonry this January: Vegas, baby — at World of Concrete 2025, the largest and only annual international event dedicated to your business. Be here to mix with industry giants. Get your hands on the latest technologies revolutionizing safety, performance and speed. And learn what it takes to not only claim a piece of our industry’s massive projected growth but dominate the field. Join the power players of concrete and masonry.
EXHIBITS: JANUARY 21-23, 2025
EDUCATION: JANUARY 20-23
LAS VEGAS CONVENTION CENTER