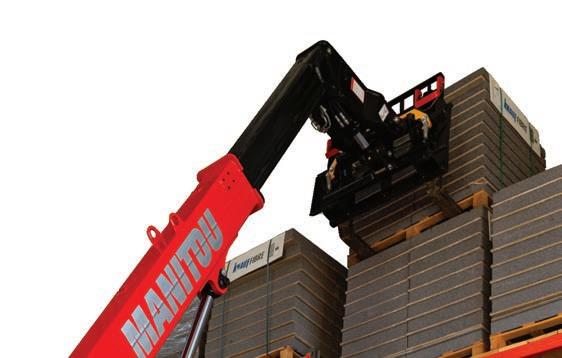
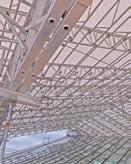
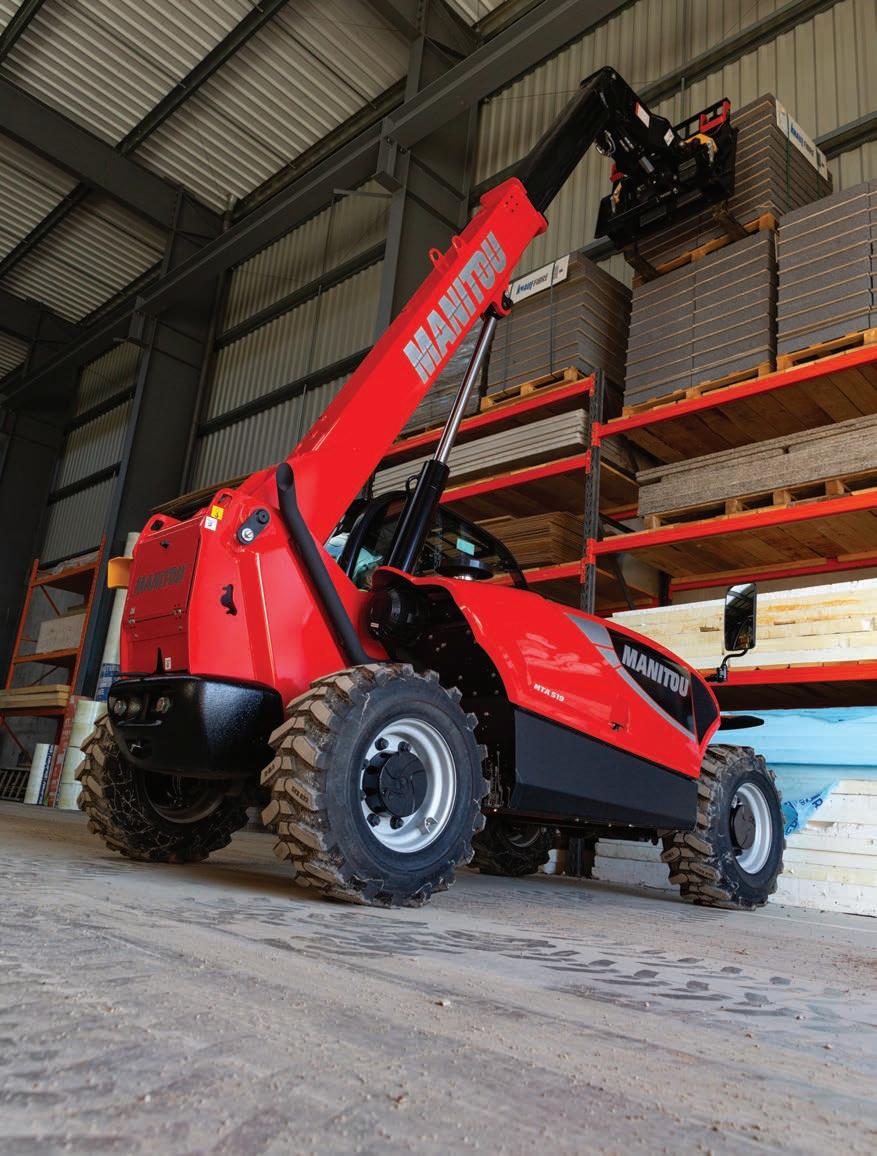
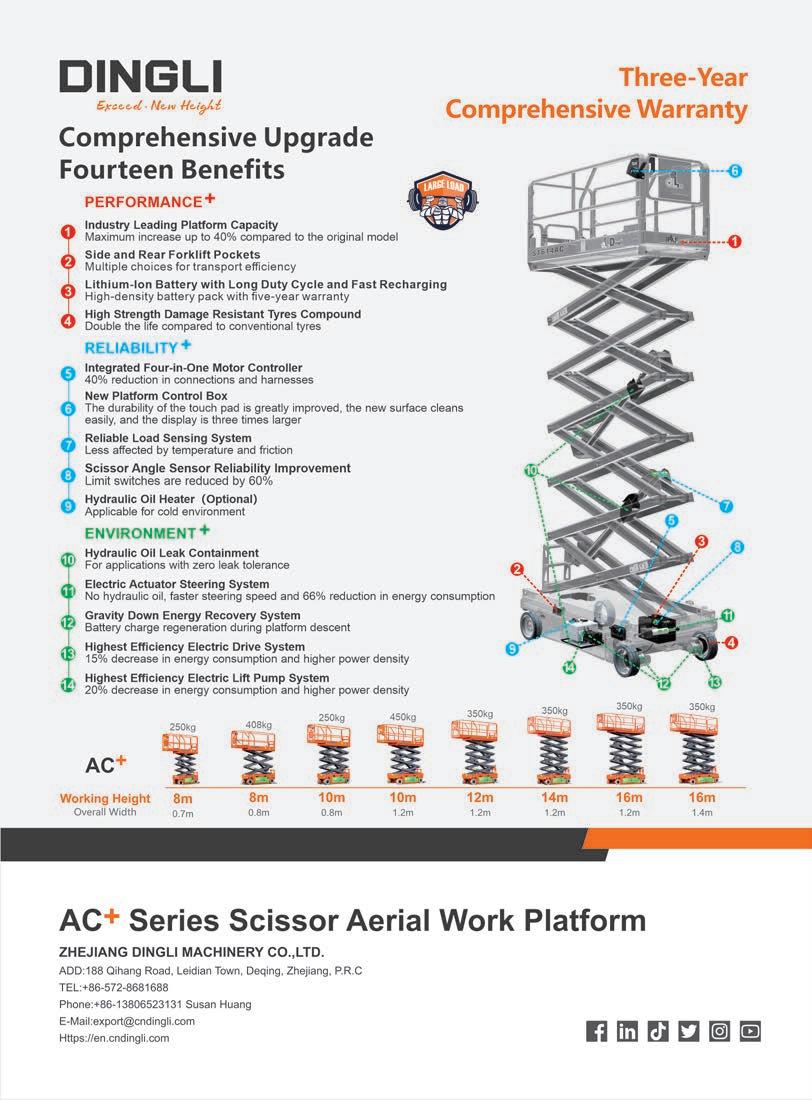
Editor: Lindsey Anderson
517-420-0918
lindsey.anderson@khl.com
Group editors:
Andy Brown, D.Ann Shiffler, Leila Steed, Euan Youdale
Director of content: Murray Pollok
Client success & delivery manager: Charlotte Kemp
charlotte.kemp@khl.com
Client success & delivery team: Ben Fisher, Alex Thomson
Media production manager, Americas: Brenda Burbach brenda.burbach@khl.com
Group design manager: Jeff Gilbert
Group designer: Jade Hudson
Event manager: Steve Webb
Event design manager: Gary Brinklow
Creative designer: Kate Brown
Audience development manager: Anna Philo
anna.philo@khl.com
Circulation executive: Vicki Rummery vicki.rummery@khl.com
Admin assistants: James Dick-Cleland, Maria McCarthy, Hannah Parry
Vice president sales –global rental and access division
Tony Radke 480 478 6302
tony.radke@khl.com
Vice president global sales: Alister Williams 843 637 4127 alister.williams@khl.com
Accounts assistant: Emily Roberts
Client success & digital director: Peter Watkinson peter.watkinson@khl.com
Facilities & HR administrator: Philippa Smith philippa.smith@khl.com
Chief executive officer: James King
Chief financial officer: Paul Baker
Chief operating officer: Trevor Pease
Adecade ago we launched the very first ALH Conference & Awards. Don Ahern was the keynote speaker, followed by talks from MEC's President David White, Acme Lift's Founder and CEO Woody Weld, Acme's President and COO Mike Crouch (now Presidnet of RMC Consults,) IPAF's Tony Groat, NES Rentals' Mike Disser, Terex AWP's Brad Allen, JLG's Tim Morris, Genie's Scott Owyen, Rouse Services' EVP Gary McArdle (now EVP of RB Global,) Skyjack's then-President Brad Boehler, renowned economist Scott Hazelton and many more.
The Coneference & Awards fared well during its in-person lifespan and its virtual spree, especially with the help of our partner, IPAF, which aligned its Innovate workshop with the ALH Conference & Awards.
But it was time for a change.
Through a joint partnership with IPAF, we are thrilled to announce the first-ever Working at Height Conference & Awards, set for Nov. 20 in Nashville. By working together with IPAF, we have worked to combine the best of the best - industry expert presentations, work-at-height trends and topics, top-notch networking events, and an evening awards dinner that will rival the IAPAs. (Sorry, Euan.)
Speakers will be announced soon, but attendees can expect to hear presentations that cover: Growing markets and trends in rental, Training and technology, How to cultivate a safety culture, How tech impacts working at height, The human factor (labor, mental health, etc.,) How to select the proper PPE, and more.
The event kicks off with a networking reception on the evening of Nov. 19 with the conference and an awards dinner taking place Nov. 20 at Music City Center in Nashville. Registration will open soon, and even sooner you'll hear more about our awards (and how to enter.)
The day-long conference is for buyers and users of aerial platforms, including rental companies and contractors, and will champion the safe and effective use of mobile elevating work platforms through the latest industry innovations, technology and best practices. These include: Equipment rental managers and owners, safety professionals in the construction industr, access rental specialists, afety consultants, MEWP OEMs and distributors and anyone else who has a toe in the work-atheight pond.
So spread the word and mark your calendars for November 19 and 20. You won't want to miss it. For more information, visit www. workingatheightevent.com or www.accessbriefing.com. Thanks for reading.
With light weight and compact size, it can be used both indoor and outdoor.
Self-leveling chain system, and each mast can rise and fall synchronously.
Hinged double opening cover for easier maintenance.
Standard with extension deck and large working capacity.
REIC Founder Kevin Fitzgerald talks with KHL Editor Jenny Lescohier about REIC’s increased focus on specialty renta and what the company is planning for in the future.
While it’s not the double-digit growth of 2023, this year’s Telehandler30 still shows a market experiencing strong demand. Lindsey Anderson dissects the data and provides the latest.
JLG provides outlook on Mexico; Altec acquires Teupen; Magni opens new HQ, expands product lines; Terex Utilities debuts new machine; All Access Equipment develops dual-purpose MEWP; Rental and OEM quarterly results, plus Share Index and more.
Mollo to up investment in green equipment' Platform Basket launches France-friendly lift; Falcon soars to new heights with launch; Sinoboom introduces first diesel articulated boom to Europe.
Through a joint venture with the Scaffold & Access Industry Association, KHL Group acquired Scaffold & Access Magazine in late 2021. Readers will find SA as a standalone publication located within the middle of Access, Lift & Handlers
Fueled by favorable market headwinds, construction activity across the U.S. has created a growing demand for telehandlers. Lindsey Anderson provides an in-depth update.
The RT scissor market is holding strong across North America, with multiple factors fueling demand. ALH takes a look at the market and rounds-up recent product news and debuts.
Sam Wyant, president of international sales at Ritchie Bros., reveals his take on the used equipment and auction markets, progress for Rouse and SmartEquip and the company’s approach to technology. KHL Editor Lewis Tyler reports.
IPAF North America welcomes new members; MEWP Rental Report 2024; IPAF Accident Reporting; IPAF 2023 annual report available.
To subscribe to Access, Lift & Handlers or any magazine in the KHL portfolio, go to: www.khl.com/subscriptions.
Manitou debuted its latest compact telehandler, the MTA 519, earlier this year. To read about the compact telehandler market, turn to page 23.
Sept. 11-12
VERTIKAL DAYS
Newark Showground, UK
www.vertikaldays.net
Sept. 30 – Oct. 4
SAIA ANNUAL CONVENTION & EXPOSITION
Denver, CO
www.saiaonline.org
Oct. 1-2
POWER PROGRESS SUMMIT
Chicago, IL
www.dieselprogresssummit.com
Nov. 19-20
WORKING AT HEIGHT
CONFERENCE & AWARDS
Nashville, TN
www.workingatheightevent.com
Nov. 25
IRC ASIA
Shanghai, China
www.khl-irc.com
JLG Q1 sales for the three months ending March 31 increased 3.7 percent to $1.24 billion as a result of higher sales volume in North America, but was offset in part by lower sales volume in Europe, the OEM’s parent company Oshkosh Corp. reported.
Access segment operating income in the first quarter increased 54.1 percent to $208.1 million, or 16.8 percent of sales, compared to $135 million, or 11.3 percent of sales, in the first quarter of 2023.
“Demand for aerial work platforms and telehandlers in North America continues to be solid, supported by infrastructure investments, mega projects and industrial onshoring projects as well as elevated fleet ages,” said John C. Pfeifer, Oshkosh president, CEO and director.
The company also marked its first anniversary of its Mexico warehouse, aimed at the growing Mexico and Latin America markets.
Altec has acquired Germany-based spider lift OEM Teupen.
The acquisition by U.S.-based, vehicle-mount producer Altec will allow the company to expand its footprint worldwide and provides a complementary offering to its line of products and services, which are designed for the utility, telecommunications, tree care and lights and signs markets.
Martin Borutta, who owned Teupen before the sale, will continue to oversee the business.
It is also understood that before the deal was signed Teupen bought back the stake that Dingli had made in the company in 2020. As well as its manufacturing HQ
Teupen debuted its new Leo 27GT Plus at Intermat this year.
PHOTO: TEUPEN
According to Mike Brown, vice president of sales and market development in Latin America for JLG, Mexico’s construction market is witnessing a significant surge, establishing itself as a major hotspot for global manufacturers; “As a strategically located manufacturing powerhouse, Mexico is living a unique moment, bolstered by global ‘nearshoring’
In less than five weeks’ time, Magni debuted a new compact telehandler and a new rotating telehandler while also kicking off construction on its new headquarters in New Jersey while signing on a new U.S. dealer. also signed on Cat dealer MacAllister to expand its footprint. The company’s new American headquarters, located in
Kenilworth, NJ, will be “a testament” to its commitment to sustainability and environmental responsibility, Magni said. Drawing inspiration from its parent company in Italy, Magni America is poised to set new standards in ecofriendly corporate infrastructure.
The company’s new RTH 10.37 rotating telehandler model, a 22,700-pound-capacity behemoth, features a lifting height of 120 feet, 5 inches where its max capacity will
Magni’s new 22,700-pound rotating telehandler, the RTH-10.37.
towards the world’s largest marketplace, the U.S.”
The company also said the market in Mexico has grown to a size that rivals Brazil’s, sparking optimism within JLG about the future of their business there. Brown said that JLG will continue investing to expand its presence in Mexico, underlining its unwavering commitment to this rapidly developing market. ■
in Germany, Teupen has a U.S. stock and service base in Charlotte, NC.
“Altec is excited to be offering the Teupen product to customers across several of the company’s core industries,” said Paul Crane, MD of Altec Worldwide. “These products are designed with bestin-class reliability, durability and versatility in mind. They will allow us to provide our customers with a new type of equipment while still receiving the Altec experience they know and expect.” ■
Construction has kicked off for Magni’s new headquarters in New Jersey.
■ EquipmentShare could go public as early as next year (2025), according to a report by Bloomberg. The business is at the early stages of exploring an initial public offering sources told the news service. Any IPO for the business, could see a first-time share sale within 12-18 months.
■ MEC has announced the appointment of Rick Penkert as national account manager. In this role, Penkert will be responsible for overseeing and nurturing relationships with key accounts across North America.
■ Revenue at Manitou rose 3 percent in the first quarter of 2024 to €685 million, despite an environment of slowing markets, said the company, with an ease in the supply chain also having a significant impact.
■ Haulotte has reported a drop in revenue in the first quarter of 2024, set against a particularly successful first three months in 2023, said the company. Haulotte posted overall sales of €157 million in the first quarter of 2024, compared to €196 million in the same period last year.
The TL45l launched through the Terex Utilities and SDP Manufacturing partnership.
Terex Utilities has introduced a new track-based lift in partnership with chassis provider SDP Manufacturing.
The 47-foot working height TL45 articulated telescopic aerial platform with a jib, is installed by SDP Manufacturing on its rubber tracked chassis. The chassis has a hydraulic track drive that extends from 31.1 inches wide to 55 inches, making the unit ideal for working on sensitive terrain, such as backyards or sidewalks, or for accessing tight spaces, such as alleys.
Featuring a 900-pound capacity jib, the TL45 is designed to be a
flexible option for contractors that need to lift materials in difficult to access areas. Being insulated to 46 KV Category C, it is also an option for rental companies to offer to homeowner, as well as contractors, said the company. Other features include full continuous rotation, unlimited work zone, and corded remote drive and outrigger controls. The unit is also stable when driving on side slopes up to 20 degrees.
“We are seeing high demand for this specialty personnel and material handling equipment in the East and Midwest,” said Bradd Weibel, Terex/Genie services,
strategic account manager. Units are now available for delivery at various Terex Service Centers in these regions. ■
All Access Equipment/CMC has developed a new truck-mount system that allows a CMC Tracked Lift (up to 100 feet of working height) to operate as both a selfpropelled lift that can drive through a 36-inch gate and also as a rearmount forestry bucket truck/rearmount aerial lift on an under-CDL
truck, such as a Ford F550/F600.
The All Access Equipment Track Lift Truck Mount & Transport Deck system provides “two lifts for the price of one” solution.
According to All Access Equipment, “many very serious injuries occur to workers while climbing on/off/into high, truck-
hold up to 17,600 pounds.
Magni also announced its new partnership with MacAllister, a Cat dealer and provider of heavy construction equipment. The deal will see Magni grow its presence throughout Indiana and Michigan. The announcement came following Magni’s newest launches at Intermat 2024, including its first compact telehandler. (See our story on compacts in this issue for more.)
mounted aerial work platforms. This certified and proven truckmount system meets and exceeds both OSHA and DOT safety standards by providing a new and safer way to enter an aerial work platform without the need to climb up/down the top of a truck with unprotected cab guards.” ■
The All Access Equipment track lift truck-mount and transport deck.
Ashtead Group unveiled its new Sunbelt 4.0 five-year plan at an analysts meeting in Atlanta this May. The plan details its financial and operational targets, including an ambition to become a $14 billion business in North America by the 2029 financial year.
The company foresees compound annual growth rates in revenue of 6 to 9 percent in the U.S, 9 to 12 percent in Canada and 2 to 5 percent in the UK over the five year period.
Supporting that growth will be between 300 and 400 greenfield openings, comprising between 180 and 240 specialty locations and 120 to 160 general stores.
These new locations will generate up to 30 percent of the growth anticipated in the five year period.
Key to the plan is to further expand the density of locations, or clusters, within key rental markets in the U.S. It has already accomplished this for 21 of the top 25 market areas, and sees most opportunity to establish new clusters in the next seventy five largest markets, growing the number of clusters in these areas from 35 now to as many as 50.
United Rentals has upgraded its forecast for the 2024 financial year to the tune of $300 million, reflecting its acquisition of Yak Access and Yak Mat earlier this year.
The company had initially predicted revenues of between $14.6 and $15.1 billion.
The company said that it could now reach as much as $15.4 billion, buoyed by the completion of the purchase of the temporary
roadway rental business.
Matthew Flannery, chief executive officer of United Rentals, said the company is pleased with its start to 2024.
“Our acquisition of Yak last month provides another excellent example of our strategy to grow our specialty rental business, differentiate our one-stop-shop capabilities and capitalize on both secular growth and cross-selling opportunities,” he said. ■
Herc Rentals has reported record first quarter total revenues of $804 million for the three months that ended March 31, 2024, an increase of 9 percent compared to $740 million in the prior year. Rental revenues were up 10 percent for Q1 at $719 million for the same period.
Sunstate Equipment Co. is expanding its industrial solutions division with the opening of two new locations in Louisiana, its first in the state. The location in Saint Gabriel, serving the greater Baton Rouge area, is now open, while a second facility in Sulphur (Lake Charles) is set to start business in May.
Both will hold a fleet that is suitable for construction and industrial projects, including an expansion of pumps in a range of sizes.
The company said a third location in La Porte, TX, will open in the summer.
“We are off to a strong start in 2024, achieving record firstquarter revenue and adjusted EBITDA margin as we continue to capitalize on key growth markets, like semiconductor, data centers, renewables and public infrastructure, while also investing in our network scale through greenfields and acquisitions, and elevating our higher-return specialty product lines,” said Larry Silber, president and chief executive officer of Herc Rentals.
“Once again, our teams are delivering for customers both in the local markets and at the national level, capitalizing on our broad geographic coverage and
Japan-based rental company Kanamoto is exploring a move into North America, as it aims to break into the top five rental companies in the world.
Speaking to IRN, Tetsuo Kanamoto, president and CEO, said the market is a promising region to expand in and will support its goals to increase revenues from overseas; “We’ve already begun a feasibility study to look into that and we’re looking into the U.S. in depth. We can’t say right now if we are interested in any particular region, but we’re taking a deep dive into the market.”
The company ALH that its plans for global markets would see it more than double sales over the next six years.
⊲ For more on this story, see www.accessbriefing.com.
strong demand for our products and services.”
Herc also reported that it completed four acquisitions in Q1, adding 11 locations while additionally opening four greenfield locations for a total of 15 new locations.
As of March 31, the company’s total fleet was approximately $6.4 billion at OEC, an increase of 10 percent over 2023 Q1, and its average fleet age was 47 months.■
Nano electrophoretic paint: Exceptional precision and quality
World-class components
Versatile certified product line for both indoor and outdoor use
Maintenance free batteries
Comprehensive features included as standard for peak performance
A product line offering both diesel and electric options
Best In Class After-Sales Support
Smart Training Eco-System
Sinoboom has launched the AB15J Plus boom lift, representing the company’s first dieselpowered articulating boom that is available in the European market.
Based on the AB15J model, the new AB15J Plus includes a range of new features and upgrades including an increased platform loading capacity, now 300kg compared to 250kg, allowing operators to carry more tools and materials.
Sinoboom’s upgraded AB15J Plus.
Italian company Mollo Group has said that it intends to increase investment on fleet to €120 million over the next two years, as it aims to hit €150 million in revenue by the end of 2024.
The company said much of the investment will focus on adding hybrid and electric equipment to its Blue & Green range of environmentally friendly equipment launched in 2022.
Meanwhile, the company said it intends to continue a number of employee support initiatives, including fuel vouchers, contribution to expenses incurred by employees in the medical,
social and recreational fields, and contribution to expenses related to education.
The announcement was made during the 13th Mollo Group Convention in Alba, Italy, where the company revealed a 22 percent increase in turnover for the 2023 financial year (up to €127 million.)
The company also grew its depot network to 57 in the year, including its Manetta Noleggi operation which it gained through the acquisition of Manetta Noleggi.
For 2024, the company said it will expand its coverage again, adding a further eight depots across Italy.
■ Manitou Group has agreed to buy the assets of its South African dealer Dezzo Equipment. The investment will enable the group to sustain its activities and strengthen its service to customers in the region. The deal will be finalized in the third quarter of 2024.
■ Skyjack has appointed Andreas Stumpf to the position of Vice President Sales & Operations for Europe, Middle East and Africa.
■ LGMG has debuted its new hybrid boom lift, the articulating AR65JE-H. The new articulating unit is based on the manufacturer’s existing AR65JE electric boom lift and can be switched quickly between hybrid and pure electric mode using a clutch.
■ Axolift has reached an agreement with TSK Maskin to become the manufacturer’s distributor in Norway.
Efficiency is also enhanced by the introduction of an active oscillation function which operates in both stowed and raised positions and enhances climbing ability and continuous turntable rotation.
Under the hood, the function pump has been exchanged from a gear to a piston pump, enabling increasing oil flow and higher oil pressure, improving the function of the multi-boom and enhance operational efficiency and flexibility.
Falcon Lifts has unveiled the latest addition to its lineup, an electricpowered spider lift on wheels.
The new Falcon 330 Wheel builds on the manufacturer’s Falcon 290 Wheel (FS290), with a working height of 33m and an enhanced outreach of 14m.
Designed with indoor use in mind, the electric unit is powered by a 180 Ah AGM battery pack, charged using DC 220V/110V mains supply, offering enough power for one day’s work. Optionally, it can also be equipped with a 2.2kW AC motor or lithium battery pack for a faster charging time.
Platform Basket has launched a new version of its Heren 10 vertical mast lift at Intermat, designed for the French market, which is the birth country of the product type.
Since the sale of the intellectual rights of France-based vertical mast manufacturer ATN, there has been a gap in the market that Platform Basket aims to fill, said the company.
The Italian manufacturer
Basket’s new Heron 10 SB.
■ UK-based GTAccess has taken on the BigChange job management system. Running more than 3,000 powered access platforms nationwide, GTAccess said it had achieved 10 percent growth, doubled its depots and introduced paperless mobile working since implementing BigChange.
launched into vertical mast production only last year with the bi-energy Heron 10, available as diesel or battery powered, with a tracked undercarriage and light and compact design.
Both versions offer 9.6m working height and 3.45m maximum outreach, with an 8.3m height at the maximum outreach and a maximum platform capacity of 230kg with two persons. A key feature is the automatic stabilization with the push of a button, incorporating four independent outriggers.
The new Heron 10 SB, updated for the French market, has seen the stabilization system, radio control, interchangeable battery and winch stripped out of its sister Heron 10 product. ■
Five new MTA telehandlers — designed from the ground up and made in the USA — o er lifting heights of 19 to 55 feet and lifting capacities of 5,500 to 12,000 pounds. The new design o ers improved visibility around the machine and to the attachment, enhanced comfort and performance, and a lower total cost of ownership. The new driver’s station features an interactive intuitive dashboard, single joystick operation and noise pollution is greatly reduced to less than 80 dBA inside the cab.
Go Big. Go E cient. Go Quiet. With Manitou.
See
Miami-based Rental Equipment Investment Corp. (REIC) is a holding company made up of acquired independent rental companies which still operate under their original brands. The business model was founded by Kevin Fitzgerald, who saw it as a way for smaller companies to benefit from the availability of corporate funding while holding onto the legacies they’ve built over decades. The current business climate in equipment rental shows the big getting bigger, but there remains a place for independents. REIC offers itself as a hybrid of the two worlds, but also as a poster child for what an investment in specialty rental can do for cash flow and increased valuation.
To find out how it all works, we sat down with Kevin Fitzgerald, executive chairman of REIC, at The ARA Show in New Orleans this year. Here’s what he had to say about his company and where it’s headed, as well as the future of the industry.
Tell us about your role in the history of REIC.
Fitzgerald: I started advising Neff Corp. as an investment banker in ‘93-’94. That’s where I was first introduced to the rental business. I was hired as CEO of Neff Corp. in 1995 and I proceeded to execute a business plan; we bought 13 companies and did 26 green fields in five years. We took the company public in ‘98.
I left Neff in 2000 and went on to do business elsewhere, but decided to get back into rental in 2013. Then in 2014, I came up with a plan to start Rental Equipment Investment Corp.
The idea was to form a holding company and acquire rental assets under one umbrella, with different brand names underneath. I knew at the time I would never become United Rentals or Sunbelt, so I needed to distinguish myself in some other way. I decided the best way of doing that was to buy other companies, keep the brand names in place, and amalgamate them under one holding company with one bank source, one back office, etc.
I started the business in 2014 with my own money, along with some friends and investors. We put our pool of money together and proceeded to go online to look at companies to buy. We came across Midway Rental, based in Kalispell, MT, a four-store group. We closed the deal in December of 2014.
I think we’ll see some consolidation among the top five to 10 companies. The big guys will get bigger and bigger, and then there will be a bunch of us after that, and we will also get bigger and bigger.
KEVIN FITZGERALD, Executive chairman, REIC.
That gave me a mini platform with the back office. We now have acquired 19 companies and opened five green fields. We currently have 52 locations, 30 of which are what I call general rental, 22 are specialty rental. Specialty rental was a big move for us in 2020.
EBITDA and they’ll say fine, but what’s your maintenance CapEx?
How much of REIC’s business is focused on specialty rentals?
In 2021, specialty was still only 5 to 10 percent of our business. It was then that our shareholders decided they wanted more liquidity, so at the end of ‘21, we consummated a sales transaction with a private equity group in New York called Kinderhook Industries.
We ended up selling the business to them in December, 2021, seven years after I started REIC. We rolled over some of our equity into the new company and I remained as CEO until this year when I became executive chairman.
The majority of the company is owned by Kinderhook Industries.
By the end of 2023, specialty was around 45 percent of our business, and by the end of this year, it’ll be over 50 percent of our revenue stream.
We’re still growing general rental, of course, but specialty has become a big part of our business. Right now, we have HVAC and compressors, as well as some specialty hybrid light towers, direct-fire and indirect-fire heaters, chillers and dehumidifiers.
It seems obvious to me when running a rental business that you need to diversify and bring in assets that have a longer life and less maintenance CapEx. The flip side is if you want to buy those companies at higher multiples, then you need to have a lot of equity to do that.
A lot of individuals and sole proprietors don’t have that equity to put back in, but we do because we have our partners at Kinderhook who can provide, as appropriate, all the funding we need. To really grow in the rental industry, you need a large, well-funded equity partner. REIC has that in Kinderhook Industries.
Where do see this trend going for REIC?
If you were to look at us three to four years from now, I’d say REIC will probably be 60 to 65 percent specialty, with the remainder being general rental.
What prompted the move to get into specialty rental?
I knew specialty was an important way for a company like ours to get more long-lived assets. The maintenance CapEx is much less with specialty equipment, which is key to free cash flow, and therefore, the ability to fund is much easier and the multiples are higher on acquisition for specialty, compared to general rental.
Specialty rental/longer-lived assets don’t get beat up as much as construction assets, the dollar utilization for specialty is higher, and the CapEx is considerably less. The maintenance side is a key thing, particularly when it comes to financing. A lot of lenders will look at your
I think for REIC, we will continue to be acquisitive, and we will continue to add fleet to our existing stores for organic growth.
We’ll look very carefully at green fields. They’re tougher these days because you need to get a property location, which is expensive or not available. And the people issue... when you look at risk factors and things that are issues for the industry, it’s people. Finding and retaining people remains a key to growing the rental business.
When you talk about opening a new location, you need a whole team and that’s hard to find. That’s why it makes sense to buy companies... because you are essentially getting an assembled group of people.
Founded in 2014 and headquartered in Kalispell, MT, REIC is a regional rental equipment services company that has developed a reputation as a leading consolidator in the industry. REIC’s general rental fleet includes aerial, earthmoving, power, compressors and other small equipment pieces, while the specialty fleet focuses on HVAC equipment. The company services its customers from 46 strategic locations, comprised of 27 general rental and 19 strategic rental branches, covering the Pacific Northwest, upper Midwest and Northeast. Supported sequentially by institutional investors NewSpring Capital and Cyprium Partners, REIC completed 12 acquisitions between December 2014 and December 2021.
The firm was acquired by Kinderhook Industries in January 2022 via a partnership with management to orchestrate the next phase of growth. Under Kinderhook’s ownership, REIC has made four strategic acquisitions in 12 months, which included Total Construction Rentals, Cahill Services, Blackout Energy Services and Industrial Drying Solutions. These acquisitions demonstrate a shift from a Pacific Northwest M&A strategy toward a more geographically expansive approach focused on specialty rental. Kevin Fitzgerald, executive chairman of REIC, said, “Partnering with Kinderhook will allow us to accelerate our organic growth plan and further penetrate underserved markets. In addition, I’m very excited to pursue strategic add-on acquisitions and continue opening new specialty greenfield sites which will help grow our business and increase market share.”
In 2022, REIC achieved significant topline growth in the first year of Kinderhook’s ownership and, in 2023, added several general rental greenfield locations, while continuing to make strategic acquisitions that enhanced the company’s general rental and specialty rental divisions.
Here were some of the biggest acquisitions REIC made in 2023.
In January 2023, REIC acquired dehumidification and heating specialist Industrial Drying Solutions (IDS.) IDS is based in Franklin Park, IL and is a subsidiary of Power Rental Solutions.
It provides dehumidification, climate control and power generation rental products to multiple sectors, including industrial, construction, manufacturing, marine and emergency response.
In February 2023, REIC added Wyoming-based Black Mountain Rental (BMR) to its portfolio. Financial terms of the deal were not disclosed. Founded in 1997, BMR provides general rental
equipment, including excavators, haul trucks and garden tools to residential contractors, homeowners and commercial contractors from two locations in Alpine and Pinedale.
In May 2023, REIC acquired Midstream Equipment Corp, a specialty oil and gas rental and asset management business located in Calgary, Canada. The price was not disclosed.
Founded in 2015, Midstream rents equipment for critical applications in oil and gas and large industrial sites, including compressors, generators, process equipment modules (skids) and vapor recovery units.
It was REIC’s sixth acquisition since it was acquired by private equity firm Kinderhook in early 2022, and its 18th since its founding in 2014 by CEO Kevin Fitzgerald.
Fitzgerald said, “Midstream’s product offering and technical knowledge lead the market and we look forward to helping Kyle Twa and Jay Formenti grow the business.”
Twa and Formenti, who are co-presidents of Midstream, said they were looking forward to leading the company “to the next phase of our growth and we are delighted at the opportunity to join the REIC/Kinderhook portfolio.
“Increasing our access to the additional resources of REIC will help scale our business and, most importantly, continue to service our customers.”
In June 2023, REIC bought Colorado-based Aim High Equipment Rental.
Aim High, which was established in 1999, provides rental, sales and servicing for a range of general construction equipment, boom lifts, scissors lifts and forklifts, serving customers across the Denver area and beyond.
Amy Sepin, owner of Aim High, said, “We are elated to complete the sale of the company to REIC. Our combined teams have a common mission of providing exceptional services, and our customers and employees will benefit tremendously.”
“Aim High has established a strong reputation of providing high quality rental equipment and services that will fit seamlessly with our existing geographic footprint for our general rental division,” Fitzgerald added. “The addition of this location in Colorado will enable us to better serve our customers with additional equipment.”
The takeover deal, which was agreed for an undisclosed amount, was described as a strategic move designed to increase REIC’s footprint in the North America region.
In early 2023, REIC added Wyoming-based Black Mountain Rentals, which also specializes in access equipment like this Genie boom lift.
Where do you see the industry going
I think we’ll see some consolidation among the top five to 10 companies. The big guys will get bigger and bigger, and then there will be a bunch of us after that, and we will also get bigger and bigger.
For example, REIC is only in seven states in general rental. We can be across the country with the same model, so we have a lot of places we can go. I believe we have a lot of runway left at REIC to grow both specialty and general rental significantly.
Capital is the key growth driver now. The big guys have it, but a lot of companies do not. They’re individually owned, and they just don’t have the capital.
Rental has always been a cyclical business because it’s construction based, so it can be very volatile. This has traditionally been viewed as a negative in the public markets.
But Covid came and this industry did just fine. Most of us went down 5 to 10 percent, that’s it. It’s a capital-intensive industry, but it’s primarily discretionary capital expenditure. If we don’t want to spend capital, we don’t have to.
The levers that we have to control capital are very good, and I think the public markets have figured this out. Coupled with the fact that the big guys are in so many industrial businesses now, not as much tied to construction, these factors are making the industry trade higher.
The stigma of this industry being very cyclical will always be there, but I think it will be less so going into the future. And I think that’s an important point to drive home, because it’s one of the reasons why the industry is trading higher than it has been.
Five years from now, I think the industry will continue to trade higher, and the big guys will get bigger. There will continue to be Mom and Pops springing up all over the place. It’s all because the demand is there, and we’re still only at around 55% rental penetration in the U.S. ■
We currently have
52 locations, 30 of which are what I call general rental, 22 are specialty rental.
Pettibone has long set the standard for material handling equipment, a tradition that carries on with our next-gen X-Series Traverse and Extendo telehandlers.
» Tried-and-true hydraulics deliver efficient performance.
» Formed boom plates offer greater strength with less weight.
» Side pod engine provides easy service access and visibility.
» X-Command® telematics is standard for 2 years.
See the X-Series lineup at gopettibone.com
We’re continually updating your favorite workhorses to meet the demands of today’s most demanding worksites. And the newly remastered 8042 SkyTrak® Telehandler is built to deliver. Its redesigned build bears the same SkyTrak-strong reliability but is now more cost-efficient to transport. Enhanced tech options and improved cab styling heighten focus and productivity. All this and more without an ounce of compromise to its 8,000–lb capacity. In other words, you can work with confidence in a machine just as driven as you.
his year’s T30 ranking of North American telehandler rental fleets showcases steady growth for the industry, with every company listed – save one – adding units to their fleets.
This year’s T30 tops out 92,893 total units – a record number for our annual ranking – and is up 6.67 percent compared to last year’s total of 87,086. Looking at our top five, we see 6.75 While it’s not the double-digit growth of 2023, this year’s TELEHANDLER30 still shows a market that is experiencing strong demand. ALH reports on the data and provides an update from rental and OEMs. >
Michigan-based AeroLift says the opportunities for telehandler growth and use are aplenty.
percent growth in fleet sizes, with our top 10 pulling in the most growth at 6.77 percent.
This demand for one of construction’s most versatile pieces of machinery falls in line with current market drivers: infrastructure, mega projects, onshoring and aging fleet replacement.
According to a recent study published by OffHighway Research (OHR,) 2023 was a banner year for construction equipment sales in the U.S., with telehandler sales coming out on top.
“In the U.S., growth was robust and most of the individual product categories saw increased sales,” says OHR Global Managing Director Chris Sleight. “But the standout in terms of both
growth and volume was the telehandler.”
and
Total construction machinery sales for the year topped 305,000 units, up 8 percent yearover-year, marking the third consecutive record >
first time ever that more than 300,000 construction machines were sold in the U.S. According to OHR, telehandler sales rose by
Life is full of shortcuts. But operating mobile elevating work platforms without properly trained, tested operators is a dead end decision. Train right. Insist on the PAL Card as proof. A valid PAL Card proves the holder has passed an approved and audited IPAF theory and practical test, compliant to industry standards. Find an IPAF-approved training center near you at IPAF.org or scan here
more than a third, with 30,000 units coming to market, representing nearly 10 percent of total machine sales, which aligns with recent OEM quarterly results.
For its Q1, JLG reported telehandler sales of $373.4 million, a 9.37 percent increase yearover-year. JLG’s total access equipment sales for the quarter amounted to $1.24 billion, with aerials seeing $591 million in sales, and the company’s “other” category pulling in $273.1 million. When we remove “other” from JLG’s two core access categories, telehandler sales amounted to 38.7 percent of JLG’s sales.
“Demand for aerial work platforms and telehandlers in North America continues to be solid, supported by infrastructure investments, mega projects and industrial onshoring projects as well as elevated fleet ages,” said John C. Pfeifer, Oshkosh president, CEO and director. “We’re really pleased with the market in access. We see continued demand drivers going forward. We talked about the Q4 order book was really strong. The $940 million that we just booked was better than our expectations. So we’re booked well through 2024 right now.”
Speaking directly to the telehandler market, John Boehme, JLG’s senior product manager –telehandlers, said, “The overall market demand for smaller, versatile equipment like compact telehandlers is very robust right now with all
Research for the TELEHANDLER30 was carried out during the Spring of 2024. Where companies were unwilling to provide figures, we made our own estimates based on data from annual reports and advice from industry contacts. Thank you to everyone who contributed.
If you would like to be included in next year’s list or would like to get a head start on our upcoming AERIALS20 list, please contact editor Lindsey Anderson by emailing lindsey.anderson@khl.com. Please include the size of your current aerial or telehandler fleet, last year’s number and your company’s website address.
H&E Equipment Services grew its telehandler fleet by more than 12 percent.
PHOTO: H&E EQUIPMENT SERVICES
the infrastructure projects starting up this spring and summer. This means that the largest user of telehandlers continues to be general construction contractors.”
For OEM Manitou, the same sentiments are echoed. “We see excellent demand with these machines in homebuilding and related industries, such as concrete contractors,” says Steve Kiskunas, product manager — telescopic handlers, Manitou. “Overall demand is increasing — more telehandlers are being sold into the North American region across a number of markets. Part of the increased demand is because these units make telehandlers much more accessible – contractors who previously thought they could not afford a telescopic telehandler now realize it can be more practical and affordable than ever before.”
says the overall market demand for telehandlers is robust.
held its fleet at the same level as ’23 – Founder Jim Koontz says the telehandler’s adaptability and flexibility are what keep these machines in demand.
“We recognize that some of the most impressive percentage growth comes in the mini and maxi versions of telehandlers,” Koontz says. “The telehandler market in North America, and locally, continues to mature and incrementally grow. More and more trades see the benefit of this amazing tool. And the attachments that make it more versatile.”
Looking to rental, United’s Matt Flannery said the world’s largest construction equipment rental firm saw growth – and demand - across both construction, led by non-res, and industrial end markets, with particular strength in manufacturing, utilities and downstream.
“We are continuing to see solid demand across a variety of end markets, customer segments, and geographies in 2024,” Flannery told investors recently. “This diversification provides for growth and resiliency.”
United, however, which ranks number one on this year’s T30, grew its telehandler fleet minimally over the last 12 months, increasing its total number of units by 2.29 percent to 35,800.
Sunbelt, Herc Rentals and H&E Equipment Services, on the other hand, all saw double-digit growth in their telehandler fleets, with H&E expanding by more than 12 percent to a total of 8,300 units.
On the independent side, Michigan-based AeroLift – the aforementioned company that
New to this year’s list is Canada’s Cooper Equipment Rentals, which joined the T30 in 11th place, with an estimated 875 telehandlers in its fleet.
In 2022, Cooper invested CAD$175 million on fleet, and it expects that investment to continue, but with a flexible approach, says company CEO Doug Dougherty.
“When it was uncertain whether we could get equipment, we stocked up and said, lets buy,” Dougherty says. “Let’s keep it coming because we don’t know when it’s going to land, and we’ve landed a lot of equipment in the last two years. Now I think we can take a flexible approach to CapEx planning and say, OK, if we see the opportunity let’s write the cheque because we know we can get the equipment.
“We recognize that some of the most impressive percentage growth comes in the Mini and Maxi versions of telehandlers. The Rotators also have a greater presence. Currently those markets do not interest us as they do not suit our needs.” ■
For more on the telehandler market across North America, turn to our article on compact units in this issue.
Sign up for our Rental Briefing today and gain access to high-quality analysis of key issues and global best practices. Our briefing is designed to help you make the best decisions for your business and stay ahead of the competition.
Don’t miss out on this valuable resource that will help your business thrive!
SIGNING UP IS QUICK, EASY AND FREE... JUST SCAN THIS QR CODE
Innovation
PROJECT OF THE YEAR
Supported scaffold COUNCIL UPDATES Fall Protection | Canadian
FOR ALL YOUR SPECIALIZED PROJECT NEEDS
Quality and performance make PCI a trusted industry leader. Our knowledgeable experts help determine the most effective scaffold system to fit your specifications.
• Power Plants
• Chemical Plants
• Refineries
• Paper Mill
• Bridges
• Shoring
• Roof Systems
• Exterior Walls
• High Rise
• Auditoriums
• Stadiums
• Weather Enclosures
EXPLORE SINGLE SOURCE CONTRACTING WITH PCI.
Streamline projects with PCI’s integrated services, reducing delays and duplication while improving efficiency and scheduling. Experience the PCI difference today.
In 2022, nearly 1 in 5 workplace deaths happened in the construction industry – and 38.4 percent of these deaths were due to falls, slips and trips, a new report from The Center for Construction Research and Training (CPWR) shows.
CPWR’s Fatal and Nonfatal Falls in the U.S. Construction Industry, 2011-2022 study also highlighted that from 2011 to 2022, the number of fatal falls to a lower level increased 52.7 percent. And, for the 13th consecutive year in a row, the construction industry’s fall protection standard topped OSHA’s most-frequently cited list last year, with a total of 7,188 violations being recorded (dwarfing the second-highest citation, hazard communication, which had 3,227.)
This all comes despite ongoing efforts to provide workers with proper PFPE training and educational opportunities such as OSHA’s National Safety Stand-Down to Prevent Falls in Construction, which celebrated its 12th anniversary this May.
With ‘construction season’ in full swing, it’s imperative that companies promote the importance of safety, training and certification to our employees – our workers are our most valuable assets, after all.
If you’re scratching your head wondering where to start, a good first step would be reviewing and/or writing and revising any safety plans and programs your company has in place. It’s important to continually develop a safety culture, as it ensures your systems are up-to-date and meet relevant standards and requirements.
Next, verify your employees’ training and
WELCOME TO OUR NEW MEMBERS
A Buck Scaffolding
Michael Mcknight mmcknight@abuckscaffolding.com
Access Systems & Solutions
dba Scaffold Inspection & Testing Co.
Joan DeJesus joan@sit-co.com
BGB Renewables LLC
Benjamin Badham helen@bgbrenewablesllc.com
Coastal Industrial Services, Inc.
Mark Sonnier msonnier2@coastaltxs.com
“With
‘construction season’ in full swing, it’s imperative that companies promote the importance of safety, training and certification – our workers are our most valuable assets, after all.”
TRACY DUTTING-KANE
certification. Do they need any renewals? Has a long time passed since their last refresh? Are there new standards or requirements that need to be addressed? Make sure your people are properly trained for their given tasks, and know how to properly fit, wear and use PPE and PFPE.
For day-to-day operations, companies can host toolbox talks each morning that discuss specific safety topics. These aren’t marathon sessions, just 5- to 10-minute-long briefs that keep workers engaged.
Lastly, take the time to participate in safetyfocused programs and initiatives. As I mentioned above, OSHA’s annual National Safety Stand-Down to Prevent Falls in Construction is a yearly event where employers focus on talking directly to employees about safety, specifically fall hazards and the importance of fall prevention.
For resources and more information, visit OSHA’s website www.osha.gov/stop-falls-standdown.
Stay safe.
Independent Scaffold Inspections LLC
Timothy King info@isinspections.com
RAXTAR Inc.
Joanna Tomczyk joanna.tomczyk@raxtar.com
SafeCru Academy LLC
Dean Kinslow info@safecru.com
San Diego Scaffold Company
Desiree Daniels sandiegoscaffold@gmail.com
Tracy Dutting-Kane, P.E.
President
Layher, Inc.
Mike Bredl
President-Elect
Universal Manufacturing Corp.
Frank Frietsch
Vice President
Layher, Inc.
Matt Morgan
Treasurer
Mdm Scaffolding Services, Inc.
James Gordon
Secretary
Klimer Platforms, Inc.
Amy Johnson
Member at Large
SkyLine Scaffold, Inc.
Tom Brewer
Board Appointee
Brewer Equipment Co.
Chris Moody
Board Appointee
Direct Scaffold Supply (DSS)
Michael Paladino
Immediate Past President
Eagle Scaffolding Services,
Editor: Lindsey Anderson 517-420-0918 lindsey.anderson@khl.com
Director of content: Murray Pollok murray.pollok@khl.com
Client success & delivery manager: Charlotte Kemp charlotte.kemp@khl.com
Client success & delivery team: Ben Fisher | ben.fisher@khl.com Alex Thomson | alex.thomson@khl.com
Media production manager, Americas: Brenda Burbach brenda.burbach@khl.com
Group design manager: Jeff Gilbert
Group designer: Jade Hudson
Creative designer: Kate Brown
Event manager: Steve Webb
Event design manager: Gary Brinklow
Audience development deputy manager: Anna Philo anna.philo@khl.com
Circulation executive: Vicki Rummery vicki.rummery@khl.com
Admin assistants: James Dick-Cleland, Maria McCarthy
SALES
Associate publisher: Tony Radke 480 478 6302 | tony.radke@khl.com
VP global sales: Alister Williams 843 637 4127 | alister.williams@khl.com
Accounts assistant: Emily Roberts
Client success & digital director: Peter Watkinson peter.watkinson@khl.com
Facilities & HR administrator: Philippa Smith philippa.smith@khl.com
Chief executive officer: James King
Chief financial officer: Paul Baker
Chief operating officer: Trevor Pease
With ‘construction season’ in full swing, it’s imperative that companies promote the importance of safety, training and certification to our employees. Here are some top tips for conducting tool box talks, providing proper PFPE training, and more.
ScaffSource opens new HQ; A92.9 and A92.10 standards to undergo changes; Peri debuts new formwork system; Podcast with Harold Gidish; Doka aids in urban build; Registration open for SAIA Annual; plus OSHA news and more.
In an effort to educate the industry on the importance of fall protection equipment –including proper fit and use – the SAIA’s Fall Protection Council looks to expand its webinar series, as well as offer additional resources. Lindsey Anderson reports.
Scaffold & Access makes every effort to ensure that editorial and advertising information carried in the magazine is true and accurate, but KHL Group Americas LLC cannot be held responsible for any inaccuracies and the views expressed throughout the magazine are not necessarily those of the publisher. KHL Group Americas LLC cannot be held liable for any matters
Skyline Scaffold Ltd. took home the SAIA Project of the Year AwardInnovation for its work on the Justice Institute of British Columbia. Read the full story on page 24.
Scaffold Resource won the SAIA’s Supported Scaffold Project of the Year Award for its pivotal role in restoring one of Maryland’s National Treasures. SA reports.
Rick McKinlay provides an update on a new gaps analysis tool in development that will address the requirements for various types of scaffold and access equipment across Canada’s provinces. SA reports.
David Glabe addresses why falls from heights consistently remain a primary cause of injuries in the construction industry.
resulting from the use of information within the magazine. The publisher is not liable for any costs or damages should advertisement material not be published.
Scaffold & Access is published six times a year by KHL Group Americas LLC 14269 N 87th Street, Suite 205, Scottsdale, AZ 85260, USA.
SUBSCRIPTIONS: Annual subscription rate for non-qualified readers is $160. Free subscriptions are given on a controlled circulation basis to readers who fully complete a Reader Subscription Form and qualify under our terms of control. The publisher reserves the right to refuse subscription to nonqualified readers.
Scaffolding and shoring provider ScaffSource has opened a new headquarters just outside of Houston in Deer Park, TX, the company announced.
Compromising seven acres of land, the new facility is ScaffSource’s largest yard out of its nine current locations across the U.S. and will be capable of storing up to one million pieces of scaffold and/or shoring materials at any time, the company said. Additionally, more than 60 of the company’s employee’s will begin to work out the new office.
Formerly United Scaffolding, ScaffSource rebranded in 2022, and the new headquarters will serve “as a continuation of the productive road ahead for the company as it continues to stake its claim as one of the most reliable and comprehensive scaffolding and shoring solutions providers within the oil & gas and industrial sectors widespread throughout the competitive Houston and Gulf Coast markets,” it said.
“The new facility is ideal to support the volume of business demand that we are experiencing, and it also has spare capacity for storage, more truck lands and excess office space for customer-support functions,” said Justin Anderson, president of products group.
“Given the recent rebrand, we were looking to find a place that not only matched our growth trajectory, but one that would also be a good fit for our team and keep us strategically placed in the markets we serve,” said Jordan Narramore, ScaffSource’s business operations and marketing specialist. “Additionally, a new site like this gives us a boost – allowing us to enhance and expand on the opportunities we already have.”
Five GEDA 1500 Z/ZP transport platforms and three GEDA Maxi 120 S units were installed for a Prague apartment construction project recently. The five GEDA 1500 Z/ZP transport platforms were installed at a height of 34 meters and serve 15 floors. They are fitted with GEDA Comfort doors to ensure smoothness and safety when moving from the platform to the scaffolding. With a platform size of 1.45 m by 3.3 m and a load capacity of 2,000 kg, “the GEDA 1500 Z/ZP BS platform is ideally suited for the transport of heavy materials. But workers can also be brought to where they need to be without any problems because the GEDA 1500 Z/ZP can carry up to seven people,” the company said.
GEDA supplied the job with five GEDA 1500 Z/ZP transport platforms and three GEDA Maxi 120 S units. PHO-TO: GEDA GMBH
for welding work.
VIENNA TWENTYTWO – one of Vienna’s largest urban development projects – is being built in the 22nd district of Vienna’s Donaustadt.
Two diagonally positioned tower blocks and four lowrise buildings form a varied ensemble, with formwork and scaffolding solutions from Doka on site.
Developed by ARE Austrian Real Estate, the project’s design
included a multitude of modern details – from generous open spaces to fine-tuned wind optimization. Once completed, the tallest tower in the VIENNA TWENTYTWO multi-purpose ensemble will have an impressive height of 153 meters.
In addition to formwork solutions from Doka, the V22 HABAU-DYWIDAG consortium is also using Doka’s Ringlock modular scaffolding for the steel
“Rezidence Nuselsky Pivovar” was built to address the area’s growing population - and need for housing.
Doka says its formwork solutions helped construction work on the tower to progress rapidly.
Compromising seven acres of land, ScaffSource’s new HQ is home to the company’s largest yard out of its nine current locations across the U.S.
construction.
With the help of the preassembled Xclimb 60 protection screen from Doka, the tallest tower in the ensemble is growing upwards safely and quickly, according to the company.
The hydraulic climbing system with the Xbright frame enclosure protects against the effects of weather at great heights, thus ensuring stable working conditions.
Outriggers, a set of structural
Peri Formwork Systems, Inc. has launched the Alpha Column, a new formwork solution that caters to various size ranges for wall, column and slab formwork.
“In response to the growing U.S. construction market, Peri USA has identified a surge in demand for user friendly formwork solutions that cater to expansive size ranges for wall, column, and slab formwork,” said Francisco Gonzalez, product manager at Peri USA . “As a result, our team is continuously pushing the envelope, always looking at ways to empower construction professionals to do their jobs more safely and efficiently. Alpha Column is the most recent example of that ongoing endeavor.”
The new imperial Alpha Column is a column system
targeted to achieving tieless rectangular and square columns up to 36-inch by 36-inch. “The robust column system features
integrated accessories that reduce material on site and increase safety during assembly,” according to Peri.
It’s been more than three decades years since the training program for suspended scaffold in the U.S. has been updated. But that’s due to change as the Scaffold & Access Industry Association’s (SAIA) Suspended Scaffold Council finalizes a completely new program, manual and training materials. Head over to www.scaffoldmag.com for an exclusive podcast interview between SA Magazine and industry veteran and SAIA Suspended Scaffold Chair Harold Gidish. A
steel trusses to provide stability and connect the building core to vertical components while concealed from the outside, were installed on levels 16/17.
Doka’s Ringlock capitalized on its flexibility to fit around the steel structure.
Access for workers between levels was facilitated through a combination of staircases and ladder hatch decks.
The completion of the tallest part of the building is scheduled for the end of 2025.
Registration is officially open for this year’s Scaffold & Access Industry Association Annual Convention & Exposition. Set for Sept. 30-Oct. 4 in Denver at the Hyatt Regency Denver, the event brings together the largest gathering of scaffold and access industry professionals. For those interested in registering, don’t delay: an early bird rate is available until May 31.
This yearly event features industry-focused educational sessions and showcases the nation’s top scaffold and access exhibitors (see photo for floorplan and full list,) while also offering training and certification, a golf tournament, networking events and an awards ceremony.
To see the schedule of events, register for training or various networking events, visit www.saiaonline.org.
The Scaffold & Access Industry Association (SAIA) has announced that the A92 Main Committee has approved the splitting of A92.9 and A92.10 into two parts – Design and Safe Use/Training. The news comes just one year following the final approval of the new standards, which went into effect on March 1.
The changes will impact the ANSI/SAIA A92.92023 for Mast-Climbing Work Platforms Standard by splitting into A92.9A Establishing Design, Calculations, Safety Requirements and Test Methods for Mast Climbing Work Platforms (MCWPs), and A92.9B Safe Use and Establishing Training Content and Administrative Requirements for MCWPs. Additionally, the ANSI/SAIA A92.10-2023 for Transport Platforms standard will be splitting
Two contractors are facing Occupational Safety and Health Administration fines following the deaths of workers who fell from height.
A Georgia construction contractor’s failure to enforce safety regulations at a worksite led to a 31-year-old steel erector suffering fatal fall injuries, an incident caused by the same workplace safety violations for which federal inspectors cited the employer just 10 months earlier.
A U.S. Department of Labor OSHA investigation determined a three-person crew employed by Georgia-based Landmark Erecting Inc. of Hahira was installing metal roofing sheets on a building in November 2023, when one worker fell 12 feet onto a concrete slab below and suffered traumatic head injuries.
OSHA cited the employer for a repeat violation for again not ensuring a worker used fall protection as they walked along a roof frame. The agency cited the company for a similar violation at a Tallahassee workplace in January 2023.
“Landmark Erecting’s repeated failure to follow required safeguards to protect employees from falls, especially after we cited the company less than a year earlier for exposing workers to this potentially deadly hazard, is inexcusable,” said OSHA Area Director Danelle Jindra. “All employers – construction industry employers included – are legally obligated to provide workers with a safe and healthy work environment.”
Additionally, Sky Safety Inc. of East Boston faces $447,087 in OSHA penalties after a window cleaner’s fatal 29-story fall from a building in downtown Boston’s financial district, the agency announced May 2.
into two and changing the name from Transport Platforms to Mast Climbing Transport Platforms (MCTPs) to consistent with the ISO and CSA standards. These two proposed standards will be A92.10A Establishing Design, Calculations, Safety Requirements and Test Methods for Mast Climbing Transport Platforms (MCTPs) and A92.10B Safe Use and Establishing Training Content and Administrative Requirements for MCTPs will also look to be portioned into from its current ANS into two ANS, Design and Safe Use/Training.
Visit www.scaffoldmag.com for an update as soon as it becomes available.
Changes could be coming soon for MCWP and TP standards. PHOTO: ALIMAK
The window cleaning company failed to inspect and replace damaged or defective equipment, according to OSHA. Agency inspectors determined that Sky Safety willfully exposed employees to fall hazards by not ensuring personal fall protection systems and a rope descent system workers used were in proper working condition. Investigators learned the company hadn’t adequately inspected the rope and equipment for damage and other deterioration and hadn’t removed or replaced defective components from service before each work shift.
Six executives and employees, as well as the company they worked for –Valor Security and Investigations (Valor) – were charged with providing unearned certifications to thousands of New York construction workers, and the New York County District Attorney’s office alleged that one of those workers, named Ivan Frias, lost his life in 2022, as a result.
According to the charges, the company claimed it trained approximately 20,000 construction workers between December 2019 and April 2023. Valor said certificate holders received 40 hours of instruction and were trained on all aspects of construction safety inspection, planning, and security services.
Instead, the DA’s office alleged, the six Valor personnel and an additional 19 individuals brokered deals with certification seekers to circumvent the education by paying a fee, instead.
“The defendants issued cards for a fee certifying the required 40 hours of safety training… without providing training,” explained a statement from the DA’s office. “Valor charged anywhere from US$300 to $600 per filing for a basic safety training card.”
Certificate seekers paid for fake licenses, claimed the DA.
Valor’s more than one dozen alleged cohorts worked across several segments and businesses including Flow Right Pluming & Heating Corp., KCM Plumbing & Heating Co., DeMar Plumbing Corp., Alpha Construction Services, and the New York City Housing Authority (a public development corporation). They’ve been charged with Criminal Possession of a Forged Instrument in the Second Degree and Offering a False Instrument for Filing in the First Degree.
In an effort to educate the industry on the importance of fall protection – including proper fit and use – the SAIA’s Fall Protection Council looks to offer additional resources. Lindsey Anderson reports.
The mission of the Scaffold & Access Industry Association (SAIA) Fall Protection Council is to make a positive difference throughout the industry for both companies and the employees of those companies in their understanding, education and application of working at height issues.
Using research, guidelines, standards and regulations to recommend the best practices possible for the safety and wellbeing of SAIA members and non-members alike.
COUNCIL GOALS:
Work jointly with aerial lift manufacturers and fall protection manufacturers to come to a conclusive and definitive answer as to exactly what type of connecting device is best used in an aerial work platform.
Continue to educate the members of the SAIA and the industry in general on the most up to date working at heights practices and regulations.
Continue to develop and document standard operating procedures for different working at height applications/scenarios.
Falls from height, one of the industry’s “fatal four” safety hazards is the leading cause of death for construction workers. According to Bureau of Labor Statistics (BLS) data, there are more than 350 fatalities and 20,000 serious injuries annually, and in 2022, falls from heights took 395 construction workers’ lives.
Despite ongoing efforts to provide workers with proper PFPE training and educational event opportunities – one example being the Occupational Safety and Health Administration’s (OSHA) National Safety Stand-Down to Prevent Falls in Construction, which celebrated its 12th anniversary this year – the construction industry’s fall protection standard again topped OSHA’s most-frequently cited list in 2023 (for the 13th year in a row.) And even more concerning is that from 2011 to 2022, the number of fatal falls to a lower level increased 52.7 percent, while the rate increased 13.3
FallTech introduced the FT-One Fit full-body harness for women in 2021.
percent, according to data from the Center for Construction Research and Training (CPWR.) These preventable deaths, and increasing fatality numbers year-over-year, spurred the U.S. Department of Labor (DoL), OSHA, the American National Standards Institute (ANSI) and the Scaffold & Access Industry Association (SAIA) – and many more – to take action.
In May 2023, the DoL and OSHA formed a National Emphasis Program focusing on falls, and two months later, the DoL announced a potential rulemaking change to clarify the personal protective equipment standard for the construction industry, specifically pointing out that the current standard does not clearly state that PPE must fit each affected employee properly. And in August 2023, ANSI’s revised ANSI/ASSP Z359.14 standard for safety requirements on self-
The best way to identifying the proper protection needed is following the hierarchy of fall protection.
ACCESS
ADOBE.STOCK.COM
OSHA’S TOP 10 MOST-CITED STANDARDS
■ Standard/Number of Violations
■ Fall Protection – General Requirements: 7,188
■ Hazard Communication (1910.1200): 3,227
■ Ladders (1926.1053): 2,950
■ Scaffolding (1926.451): 2,835
■ Powered Industrial Trucks (1910.178): 2,550
■ Lockout/Tagout (1910.147): 2,539
■ Respiratory Protection (1910.134): 2,493
■ Fall Protection – Training Requirements (1926.503): 2,109
■ Personal Protective and Lifesaving Equipment
– Eye and Face Protection (1916.102): 2,064
■ Machine Guarding (1910.212): 1,635
Source: Occupational Safety and Health Administration
retracting devices (SRDs/SRLs) became effective following its approval in 2021.
In response to this evolving PFPE landscape, the SAIA’s Fall Protection Council convened during Committee Week 2023 and took the initiative to equip the industry with valuable resources.
During Committee Week, SAIA members were asked to write down the top three things they wanted to see more
There are several ways to protect workers that are working at heights. All too often personal fall arrest systems are automatically chosen, however the best way to identifying the proper protection is following the hierarchy of fall protection.
Eliminating the fall hazard or preventing exposure to a fall hazard is the most effective control measure. Preventing exposure may include modifying structure, isolating the worker from the hazard, changing a process, substituting equipment, or using work procedures organized in such a manner that the worker is not exposed to the fall hazard.
Passive fall protection methods are generally considered a higher level of protection than active systems since there is little or no reliance on the worker. Examples of passive protection include guardrails, which provide a physical barrier between the worker and the fall hazard, covers over holes which provide a load bearing barrier, scaffolds and working platforms with guardrails or barrier protection.
Fall restraint systems, involve the use of equipment assembled in such a manner that the worker cannot fall. Restraint systems are characterized by the worker remaining on the same surface they were working on if a fall should occur. Restraint systems do not allow a worker to free fall, therefore restraint systems do not generate the same amount of energy as fall arrest systems, reducing the risk of injury.
Personal fall arrest systems (PFAS) involve the use of personal fall protection equipment assembled in such a manner that an authorized person can fall. Fall arrest systems are characterized by the worker free falling some distance and the fall being arrested by the fall protection equipment. Fall arrest systems create additional concerns regarding the amount of force that the worker’s body will experience during the event, contacting structure and requiring rescuing the worker after the fall has been arrested. No matter what systems are chosen, detailed education should be given to the worker ensuring that employees know how to properly inspect, use and store the equipment, the SAIA says. If a personal fall arrest system is chosen, education on proper fit is key in protecting the worker from further injury.
information provided on, and PFPE was the most-brought-up topic.
SAIA Fall Protection Chair Becky Danielson (Ergodyne) and Co-Chair Micah Turner (Trekker Group) thus began working to develop a four-part webinar series on fall protection inspections and proper fit.
The series kicked off in October 2023 and wrapped this May. Topics included: harness inspections, lanyards/connectors, SRLs and vertical lifelines and anchorage connectors. (For anyone interested in viewing the webinars, visit the SAIA’s YouTube page.)
“We really like the webinar series, including providing supporting documentation,” Danielson tells SA. “We will likely continue [developing] those, as well as look at creative ways to support and
educate our members.”
Danielson also adds that the “Fall Protection Council is here to help,” and urges SAIA members and Councils to reach out for collaboration or information. sa For more on the SAIA Fall Protection Council, visit its dedicated website: www.saiaonline.org/fallprotection.
Scaffold Resource won the SAIA’s Supported Scaffold Project of the Year Award for its pivotal role in restoring one of Maryland’s National Treasures. SA reports.
Constructed in 1772, Maryland’s State House is one of our nation’s most historical legislative buildings. Not only is it listed on the National Register of Historic Places as well as being crowed a National Treasure to the State, it is also the oldest U.S. state capitol still being actively utilized for legislative work.
Atop the Annapolis-based structure rests a large, wooden dome that measures 121 feet tall and 40 feet in diameter – and at more than 252 years old, it was due for a bit of TLC.
Enter Scaffold Resource.
Maryland-based access subcontractor, Scaffold Resource was contacted by The Christman Company, alongside the Department of General Services and the Maryland Historical Trust, to create a proposal that would see the company provide engineering, complete access installment and safety assessments throughout project’s duration.
The team at Scaffold Resource thus began its close collaboration and discussion with the general contractor to design and configure the best way to tackle the required work on the building while keeping its historical fabric intact.
“The first step that Scaffold Resource took to ensure the safety of the building, its occupants and the general public was to properly stabilize the structure by installing 16 modular braces within the dome through its hatch to the existing attic,” the company told SA. “This was a vital part of the process as the structure needed to withstand
Scaffolding covered 110,000 vertical square feet of the State House.
■ Collaborative efforts and teaming with general contractor superintendent to ensure proper access and equipment needed to facilitate required work.
■ Provide and install system scaffold at south side of structure by way of stair tower and runway to grant access where lower roof adjoins with base of dome.
■ System scaffold and stair tower were engineered and installed around exterior of dome (128 feet).
■ 16 modular braces installed to stabilize the dome during extensive reconstruction and spread load bearings from scaffold and personnel.
■ Trolley beam system with a leo cable hoist installed along exterior of dome for easy material removal and transfer to and from ground.
■ Debris containment/tan scrim wrap was designed to support wind loads and installed around scaffold to help contain loose materials from blowing into public space.
■ Overhead protection installed at stair tower location and integrated within design to accommodate safety of staff utilizing the access.
TYPE OF CONSTRUCTION
Historic renovation/stone removal access
SIZE OF PROJECT
110,000 square feet of exterior vertical work
CONTRACT VALUE
$771,000
CALENDAR
LENGTH OF PROJECT 10 months
PROJECT COMPLETION April 2022
PERCENTAGE OF WORK
SELF-PERFORMED 100%
the scaffold load, the various crews and materials, and any disturbance from the weather that could cause movement and shifting of the scaffolding.”
Scaffold Resource employed a crew of 10 OSHA-30-certified trained scaffold erectors to install industrial systems scaffold. Access from ground to roof, 10 level work decks to access each section of the dome, a Beta Max Maxial hoist and scrim were added to the scaffold. In order to such, the company had to build a 61-foot-tall access scaffold stair tower at the south side of the building up to the structure’s roof with approximately 14 linear feet of integrated overhead protection at the base.
Following the install, a scaffold runway from the stair tower across the lower roof to the base of dome at 42 linear feet was incorporated to accommodate the flow of work from ground to structure. Lastly, the dome access required precision, engineering, and site investigations before erecting a scaffolding system with stair tower access measuring 128 feet tall and encompassing an area 40 feet in diameter. The stair tower was to be “stepped in” as required by design to allow trades a flush access point to the dome façade at each deck level.
In total, Scaffold Resource provided about
Scaffold Resource faced many uphill battles during its time working on the Maryland State House dome rehabilitation. “These challenges were faced and overcome, making this the perfect project to submit and showcase our expertise in the construction industry,” the company said.
A few of the challenges:
■ Tight lay down area for materials led our team to build a delivery ramp across sidewalks and landscape to designated parking area for delivery trucks.
■ The Maryland State House remained opened and functional (including tours) during the restoration process, leading crews to work meticulously to resolve real-time access limitations and frequent work stoppages.
■ The scaffold team followed behind the millwork subcontractors to install tie-ins as each window was removed to ensure the historic fabric of the structure was not disturbed as no penetration to the façade was permissible.
■ Due to the historic nature of the building special measures were taken when anchoring and tying off the scaffold stair tower and dome system. Many days were spent restructuring the work decks as the job progressed to take into account the changing sequence of trades accessing the equipment.
110,000 square feet of scaffolding on the project.
The close relationship between the various tradesmen, the GC and Scaffold Resource was “imperative when it came to delivery and scheduling of the materials utilizing the Beta Maxial Hoist our crew installed,” Scaffold Resource said. “This system moved vertically along the scaffold to carry material up and down safely while the designated subcontractor utilized the stair tower.”
The engineering and planning that went into the installation had to consider the various weights of the materials being transferred and the impact it would have on the structure.
Additionally, the scaffold and hoisting system within had to be wrapped in a scrim to ensure that any loose material would stay safe within it confinements.
“The care, diligence, and pride taken by each individual on this project will be reflected in the final product when the MD State House Dome is complete,” the company concluded. “This project will not only preserve 250-plus years of history, but will allow visitors, government officials and Marylanders to learn about its country, heritage and the great state of Maryland.” sa
Maryland-based Scaffold Resource was contacted by The Christman Company to work together on the restoration project.
•Made
•Compatible
•Rentals
Rick McKinlay provides an update on a new gaps analysis tool in development that will address the requirements for various types of scaffold and access equipment across Canada’s provinces. SA reports.
The Scaffold & Access Industry
Association’s Canadian Council has a number of big-ticket projects it is currently working on for both Association members, and the industry as a whole, says Canadian Council Chair Rick McKinlay.
“The Canadian Council’s primary mission remains to unify, represent and enhance available resources for each provinces in the scaffold and access industry across Canada,” says McKinlay, who also serves as President of the Access Association of Canada. “Our mail goals and objectives continue to be to complete an industry gaps analysis, to review and modify all SAIA safety resources and make them relevant to each province, and to review and create training content to meet the needs of the Association’s Canadian members.”
SA recently sat down with McKinlay for an update on all things Canada. Here’s what he had to say.
Over the past 12 months, what has the Canadian Council been actively working on?
Our efforts have remained heavily focused on the gaps analysis tool that has been under development. The gaps analysis tool (or what we are probably more accurately referring to as a “side-by-side analysis”), lays out the requirements for the various types of scaffold and access equipment across each of the eight most populous provinces.
Specific key criteria as typically outlined in the various regulations for each equipment type can easily be followed across a row of
data, literally moving from one side of the country to the other, to see how the regional requirements for that equipment type may be similar – and more importantly to also see how they may differ.
We had set for ourselves a target to have the first working draft completed in time for last year’s Annual Convention in Vancouver, and the Council is happy to have been able to meet that goal.
Between Annual Convention and the recent Committee Week in Charleston, SC, the Council had been able to have the working draft document further refined
Toronto-based Etobicoke Ironworks Limited provides a range of scaffold and access services.
PHOTO: ETOBICOKE IRONWORKS LIMITED
through peer review, health and safety management perspective review, engineering perspective review, translated from French to English where relevant, and formatted and branded. The goal had been to have the tool ready for submission to the Regulatory and Review Committee for final review ahead of publication in time for or just after Committee Week – a target the Council was again happy to have been able to meet. During Committee Week, we were also
able to have a productive preliminary presubmission discussion with representation from the Regulatory and Review Committee and were able to receive some very helpful inputs that we agree would make for a better reading document and a better overall tool. We will shortly be working those recommended inputs in, with the expectation to be able to submit the gaps analysis/side-byside comparison tool to the Regulatory and Review Committee shortly.
Ontario-based Klimer specializes in mast climbing work platforms and transport platforms.
The Council continues to meet virtually, fairly regularly, with participants calling in from most of the provinces – which has certainly helped in keeping up the momentum.
Looking forward, what will the Council be focusing on in the coming year? The council is expecting to be able to fully cap off the first phase of the gaps analysis/sideby-side analysis project. Once the Regulatory and Review process has been completed, we expect to begin publishing, broadcasting and promoting the completed document to get it into the hands of those who can benefit from it, and who, in the past, would had to have taken this upon themselves individually to try to sort out and make sense of.
We are also planning to implement a periodic or annual review process, to ensure that any changes to the regulations are reflected in a living document.
Future activities will include translation into French language for the benefit of our Francophone members and colleagues, expansion to also cover rope access, bringing the remaining provinces and territories into the document, expanding the document scope to encapsulate the relevant CSA standards, as well as expansion in scope to include OSHA regulations and ANSI/UL standards – wouldn’t a full Canada and U.S. >
comparison be something else! Depending how ambitious the Council participants feel will determine plan of attack to begin chipping away.
Additionally, reflection on some of the recent occurrences in the field experienced by members and relating to interpretation of regulations and standards has also highlighted some areas of need for Council involvement; there are many “gray areas”
that seem to be popping up as member companies push for innovative and outside of the box thinking (e.g., access scaffold components being used in non-access scaffold applications), with regulations, codes, and standards often playing catch-up. The council is expecting to be making a push towards helping those member companies who find themselves caught up in those gray areas, and at the same time working with local
regulators and policy makers to help raise their awareness and education as our industry continues to evolve. This is certainly an area where leveraging of existing alliances can be of significant benefit.
Etobicoke manufactures, researches and provides design and engineering services on scaffolding and structural steel products.
Also, a recurring theme in many of the discussions that the Council has been involved in relates to training. It seems that a common challenge to most companies is a workforce shortage. Bringing in more and new workers inherently drives a need for increased training. The Council feels that this will likely be a near-future push, as well, and remains open to serve as a resource towards that end.
Are there any upcoming changes to standards/regulations that will impact the Council?
There have been rumblings that there are expected to be some upcoming changes to one or more of the Canadian regional occupational health and safety regulations relating to construction, as well as amendments/reviews currently underway for a few of the CSA standards governing our industry.
The importance (and value) in holding periodic reviews of the gaps analysis/sideby-side document is to ensure that any changes requiring update are captured and addressed in a reasonably timely manner. The periodic review process also provides a vehicle to communicate to the members that changes have occurred (or are coming), as well as what they are, further strengthening the association’s position and reputation as the voice of the industry. A further benefit in the way that the Canadian Council team is structured is that the geographic leaders tend to be in the best position to be able to communicate back to the team any upcoming changes that may be in the works.
What would the Council like to relay to readers of SA Magazine?
The Canadian Council remains an available resource for any of the other SAIA members or councils – if there are ways that the council can contribute and provide insight or an alternate perspective on any of the projects being undertaken or issues being experienced in the field, don’t hesitate to get in touch with the council chairs – we’re here for your benefit.
If there are Canada-specific challenges that need guidance or addressing, please also don’t hesitate to reach out. sa To learn more about the Canadian Council, visit its website at www.saiaonline.org/ canadian.
David Glabe addresses why falls from heights consistently remain a primary cause of injuries in the construction industry.
In an apparent effort to reduce or eliminate falls from heights, government agencies, industry institutes, associations, unions, employers, and others seemingly too numerous to list, have promulgated rules, regulations, guidelines, standards, requirements, codes, checklists, admonitions, fines and threats. Unfortunately, it doesn’t seem to be working too well. Falls from heights consistently are a primary cause of injuries in the construction industry.
The typical response to this fact is more rules and regulations in the belief that the problem will go away if we have more rules and regulations. An analysis of the written material on the subject suggests that perhaps too much
of the material is ineffective. One would think that in these United States – get it, united, there would be one source for regulations addressing fall protection. After all, if you fall in Maine, it will be pretty much the same as if you fall in Hawaii.
But such is not the case, apparently, since there are multiple federal and state agencies that have their own regulations addressing fall protection. Fortunately, most states have determined that workers should be protected from falling from scaffolds once they reach 10 feet above the level below. Not surprisingly, however, California is different and requires protection at 7-1/2 feet. But wait, there’s more. If
ABOUT THE AUTHOR
David Glabe is the founder of DH Glabe & Associates. He is also actively involved in the Scaffold & Access Industry Association and serves as a member on the ANSI A10.8 subcommittee for scaffolding.
you happen to be working on a ship where the OSHA Maritime Industry regulations apply, you have to be protected once you are 5 feet above the level below, whether on a scaffold or other work surface. Perhaps Maritime workers don’t know how to fall. Not to be outdone, the Army Corps of Engineers has its own requirements for fall protection. The Army Corps requires fall protection once the worker is 6 feet above the level below; it makes no distinction between working surfaces and scaffold platforms.
Not to be outdone by the federal government agencies, various states have managed to modify federal regulations to
their own liking by massaging the federal regulations or writing their own regulations. Washington state and Michigan are two examples. Not to be left out of the regulation writing contest, New York has decided that scaffolds require a guardrail system when the worker is more than 7 feet above the level below. But wait, we’re still not done with regulations. There are cities that have regulations governing fall protection and scaffolding. For example, New York City requires scaffold permits and
inspections. It is presumed that inspections would include fall protection.
Let’s see what we have so far. Depending where you are and whether you are on a working surface or a scaffold dictates when fall protection is required, ranging from 5 feet in the Maritime Industry to 10 feet in the General and Construction Industries. It seems the laws of physics apparently can be modified. Or perhaps not. As with life, there are exceptions. Scaffold erector fall protection is determined by the employer. And then there are steel erectors and roofers. Certain steel erectors can be exposed to fall heights up to 30
feet although they have to wear fall protection equipment at 15 feet but don’t have to hook up. Go figure. Roofers can be exposed to falls as long as they have a monitor ready to tell them when they are about to fall.
At least one can have fun with the regulations. The Army Corps specifies that the guardrail be lumber, a flat bar, or a pipe. What would happen if you used a steel angle, which is a common guardrail on frame scaffolds, or a tube in place of a pipe, common on many scaffolds?
We aren’t done.
The construction of a guardrail system, that is the assembly of the toprail, the midrail, and guardrail posts are addressed in a variety of ways in the various regulations.
Federal OSHA specifies that the toprail on scaffolds be between 38 and 45 inches. On other working surfaces, the range is 39-45 inches. Can it be assumed that workers are scaffolds are shorter? The Corps of Engineers specifies 42 inches, plus or minus 3 inches.
That appears to be the same as 39 to 45 inches, but you never know. California agrees with the Maritime folks and requires the toprail be installed 42 to 45 inches above the platform. Apparently seafarers and Californians are taller. And then there is the midrail.
General Industry, Construction Industry, and California regulations agree, there’s a surprise, that the midrail be installed approximately halfway between the toprail and the platform. Not so the Corps or Maritime where the midrail must be installed halfway; none of this approximate stuff. Interestingly, some regulations do not explicitly allow the use of a personal fall arrest system on scaffolds, only a guardrail system. At least, that is how some regulations are written.
It’s clear from a review of the voluminous regulations that science and physics have no influence on the numbers used. Admittedly, it can be reasonably concluded that the regulation writers recognize that falling from heights can be detrimental to one’s physical health. However, despite the indisputable fact that the further you fall and the quicker you come to a stop dramatically affects the force that your body receives, it appears that no one can agree on what the free-fall distance should be.
This brings us to an issue that frequently occurs on jobsites and that is how precise a guardrail system must be when it is installed. If a toprail is one inch too high or too low, does that a violation make? Does that a hazard create? I doubt it, but then I don’t enforce regulations.
There appears to be one thing that the regulations agree on and that is the strength of the toprail and midrail. If you don’t know what that is, look it up because if I give it to you, I may be wrong since I doubt I have found all the applicable regulations in existence.
One last thing; the regulations do not agree on how that load is applied. Some regulations say any outward and downward force, some say any horizontal and downward force. At least they don’t say upward force, but then the regulations can always be revised. sa
face without supporting it from the ground.
TYPE OF PROJECT: Scaffolding and access PROJECT DURATION: Started April 2022. Scaffold was dismantled November 2022. CONTRACT VALUE: $600,000. Completed within budget.
HOW SKYLINE INNOVATED: Building a track system and rolling the roof out from a stationary launch bay allowed for all work to be conducted with zero risk to the structure or the people working underneath.
When Skyline Scaffold Ltd. was contracted by Matra Construction to develop a solution to handle a skylight replacement over an active building lobby in the Justice Institute of British Columbia, in New Westminster, B.C., the company had to think outside of the box.
The project required a system that did not load the existing roof, while also being wide enough to span the 100-foot, two-way sloping roof.
After reviewing site conditions and assessing the challenges posed by minimal roof-loading capacity, a clear span solution was found to be the only viable approach to redistribute loads from our system, workers and materials to the exterior walls instead via gantries on either side using our patented SkyTruss system, which is the lightest and
Skyline Scaffold Ltd. combined multiple elements into one cohesively functioning scaffold system in order to replace a skylight over an active building lobby –and took home the SAIA Project of the Year Award for Innovation for its work. SA reports.
Skyline Scaffold built temporary support towers to facilitate the building of its modular SkyTruss system to support the roof. The towers were removed once the roof was in place.
Double chord SkyTruss supported the 100-foot span Keder Roof to allow the removal and installation of new Skylight glass.
strongest unit beam on the market, according to the company.
A Layher Keder roof of approximately 100 feet by 100 feet was mounted over the company’s patented SkyTruss gantries on each side of the roof to create a load path through exterior shear walls and columns. Skyline Scaffold also constructed a large internal area platform to provide access to the underside of the skylight in addition to public protection.
“One of the many challenges was limited crane staging areas on the property,” the company noted. “Our SkyTruss system solved the issue of creating a span of this length with the significant loads of a large temporary roof and, being largely modular, we were able to
Founded in 1995, Skyline Scaffold Ltd. is a supplier of high-end, engineered access solutions designed to maximize productivity. The company has grown from a four-person operation out of the back of a pickup truck, to more than 65 full-time employees, and more than $15 million in scaffold assets.
construct it ‘in situ’ using 1m, 2m and 3m sections that were easily built by hand.”
The project involved combining multiple elements into one cohesively functioning scaffold system in order to span a two-way sloping skylight, all without loading the existing roof.
The interior scaffold was designed to provide a large span public protection deck using Layher 750mm over 750mm beams over an active diamond-shaped lobby that also provided access to the underside of the skylights for the glazers.
On the exterior, a clear span weather
protection system was required that had to be low enough to prevent wind-driven rains from entering from the sides. Additionally, it had to load paths to the exterior of the building as the existing design loads were too low to allow any scaffolding to be built on the roof.
“We delivered a very sophisticated and innovative engineering package using many ‘firsts’ in North America and very little in terms of ‘off-the-shelf’ systems,” Skyline said.
“After evaluating load paths, our SkyTruss system was determined to be the only viable solution, as steel beams would have been extremely heavy and costly at 35m long, and
This Scaffold & Access Industry Association’s Innovation Project of the Year award is presented to a member company that: ■ demonstrated a new or innovative way to utilize an existing product on a project, or ■ delivered a new product to the field. For more information, or to enter this year’s awards, visit www.saiaonline.org.
would have been impossible to place, given the lack of staging area for cranes.”
It was determined the SkyTruss gantry had to be reinforced and doubled as a result of side loads imposed from the 100-foot clear span Keder roof.
“SkyTruss can not only be double-, triple- and quadruple-chorded, but it can be stacked as well in all four configurations,” the company said. “Our in-house engineering team worked diligently with our project managers in collaboration with base-building engineers to design support towers in only four areas to resolve dead and live loads, as well as wind loads up to 90km/hour.” sa
Safely and consistently delivering personnel to perform work at height for more than a decade.
Century Elevators is ready to collaborate with your team on current or upcoming projects. With a balanced fleet of elevators, hoists and platforms, we are here to help safely deliver your personnel to height. As a critical infrastructure company, Century Elevators is open and operating, while supporting our customers and delivering lifting solutions during this critical time. With on-call service technicians and installation crews in the field every day, Century Elevators is your partner in productivity – call us for a quote today.
Fueled by favorable market headwinds, construction activity across the U.S. has created a growing demand for telehandlers on jobsites. Lindsey Anderson look into the latest trends and drivers, with a focus on compact units.
Telehandler sales soared in the U.S. last year, according to a new study published by Off-Highway Research (OHR.)
Dubbing 2023 a “peak year for construction equipment sales,” OHR said strong underlying market drivers such the IIJA, CHIPS Act and numerous mega projects saw activity surge across the country, and along with it, climbing construction equipment sales.
“In the U.S., growth was robust and most of the individual product categories saw increased sales,” says OHR Global Managing Director Chris Sleight. “But the standout in terms of both growth and volume was the telehandler.”
Total construction machinery sales for the year topped 305,000 units, up 8 percent yearover-year, marking the third consecutive record year for construction equipment sales – and the first time ever that more than 300,000 construction machines were sold in the U.S. According to OHR, telehandler sales rose by
more than a third, with 30,000 units coming to market, representing nearly 10 percent of total machine sales.
“The versatility of these machines and their application across both residential and nonresidential building put them in the sweet spot for growth,” Sleight adds. “It seems inevitable that 2023 will be the high-tide mark for the U.S. equipment market for this cycle.”
And manufacturers couldn’t agree more. ALH spoke with telehandler OEMs to get their take on trends, market expectations and new
product launches within the compact telehandler segment. Here’s what they had to say.
How is today’s overall North American market fairing for compact telehandlers? How do you see it playing out for the remainder of the year?
Keith Hovey, head of global marketing, Genie: The market for compact telehandlers continues to be strong and growing. There really are two things happening at the same time to drive adoption. The first is that, more and more, people are realizing the value of having a telehandler on their jobsite; as a result, more people are using them. The second is the ongoing need for new and upgraded infrastructure, and the ongoing investments in infrastructure. So, not only are telehandlers a staple on more jobsites, there are also more jobsites in general. For that reason, we expect demand will remain strong.
Lee Tice, product manager, JCB: If we look at what happened from, we’ll just say 2022 to 2023, the compact telehandler market almost doubled. So, market size grew tremendously from ‘22 to ‘23. We really see that continuing into 2024. We haven’t seen anything that’s going to indicate a market shift or slowdown in this compact sector and really contribute that growth to some of these infrastructure bills. The residential and related housing markets have kind of exploded, and commercial construction’s taking place all across North America – and that’s
During Intermat in Paris this year, manufacturers were keen to showcase their latest compact units. Some were new entrants to the market, others took an all-electric route. Please note: Not all of these machines are global offerings, so check with the manufacturer or your local rental company about availability. For additional launches, and more in-depth coverage, visit www.accessbriefing.com.
Magni’s first compact fixed boom telehandler, the TH 3.6.
Magni launched its first compact fixed boom telehandler, the TH 3.6, at Intermat. The unit features a 3-ton capacity and 19-foot working height.
The new TH 3.6 becomes the smallest model in the TH range, and is designed for construction, logistics and agriculture.
Capable of carrying a full load to a height of 17.7 feet, the TH 3.6 can lift 5,511 pounds at its maximum height and 2,425 pounds at more than 9.8 feet of horizontal reach.
XCMG’s range of telehandlers.
The company said the unit will be available to U.S. customers later this year.
Dieci used Intermat to launch its first allelectric telehandler, the Dieci-e, which is based on the chassis of its existing Apollo 26.6 model. The new unit features a load capacity of 2,600 kg, lifting height of 6m and a 19 kW traction motor and 22 kW hydraulic system motor for power. The Dieci-e is available with one or two lithium batteries, providing a maximum power output of up to 44 kWh and up to a full working day on a single charge.
XCMG launched two compact telehandlers for the North American market recently, the XT519U and XT519E. With a lifting height of 19 feet, 8 inches, the XT519U has a maximum lifting weight of 5,500 pounds and is equipped with Kubota V3307 engine. On the ‘greener side of the grass,’ XCMG’s XT519E is electric, equipped with a lithium battery, and features a maximum lifting capacity of 5,511 pounds.
Zoomlion Access launched a new compact telehandler at Intermat this year.
The ZTH2506 telehandler delivers a working height of 6.1m and a platform capacity of 2.5 tons. The model is designed for industrial applications, such as shifting cargo, but also adapts to various other job sites, including construction, agriculture and logistics. It can also be equipped with a range of attachments including floating fork, aerial platform, glass handling vacuum attachment, among others.
Supplied with a large screen displaying all relevant parameters, the model provides a smart control system allowing the operator to quickly access required information.
Zoomlion launched a compact telehandler at Intermat, the ZTH2506, seen here.
Applications for these compact machines vary greatly from the initial phases of a large construction project.
really where these machines shine. I think also more customers are realizing the benefits of compact telehandler and the ability to not only perform as a telehandler, but also the ground engagement.
John Boehme, senior product manager –telehandlers, JLG: The overall market demand for smaller, versatile equipment like compact telehandlers is very robust right now with all the infrastructure projects starting up this spring and summer. This means that the largest user of compact telehandlers continues to be general construction contractors.
That said, the applications for these compact machines vary greatly from the initial phases of a large construction project, where the machines can be found unloading trucks and delivering materials, to the closing stages, where they can be utilized for job site cleanup and landscaping. So, other big users of this size of telehandler are landscapers and hardscapers.
Other markets/applications that will often rent compact telehandlers include industrial and residential construction, commercial and retail operations, refurbishment and reconstruction projects, parking garage construction and event set-up and teardown, as well as a wide variety of maintenance work.
The market opportunities for compact telehandlers in agricultural applications, by farmers and ag producers, are also growing.
Steve Kiskunas, product manager — telescopic handlers, Manitou: Overall demand is increasing — more compact telehandlers are being sold into the North American region across a number of markets. Part of the increased demand is because these compact units make telehandlers much more accessible – contractors who previously thought they could not afford a telescopic telehandler now realize it can be more practical and affordable than ever before.
We see excellent demand with these machines in homebuilding and related industries, such as concrete contractors. The ability to load and unload trucks, pick and place materials in an all-terrain environment is key. They are also
Manitou showcased its MTA 519, seen here, at this year's ARA Show. PHOTO: MANITOU
ideally suited for rental because they are easy to own and operate, easy to transport, and flexible for many uses. These are great in landscaping because of the all-terrain capabilities, and the ability to use skid steer and CTL attachments interchangeably. These machines also provide excellent power with rubber tires that make them a strong option for snow pushes — and the telescoping abilities help with stockpiling. The auxiliary hydraulic capabilities make them a great option for sweepers as well.
Malcolm Early, vice president – marketing, Skyjack: They have become increasingly popular in recent years due to their ability to navigate in smaller areas, making them a great choice for indoor projects or outdoor job sites with limited space. 2023 saw sustained market growth that meant that levels were very much back to precovid levels.
Robby Hagan – senior vice president of sales, Xtreme Manufacturing / Snorkel: Both Xtreme and Snorkel have an increase year-over-year
in order intake for compact machines. Many general rental companies that wish to participate in the telehandler forklift rental market utilize the compact telehandlers as a point of entry. Often these smaller rental companies do not wish to include semi-truck and trailers into their delivery fleet as they are costly due to the acquisition, driver, and maintenance costs.
What are the biggest trends in the North American compact telehandler sector today?
Jamison Wood, product development specialist, Bobcat Company: Some of the notable trends in the North American compact telehandler sector include an increasing emphasis on telematics features to enhance productivity and efficiency. The growing adoption of telematics systems enables remote monitoring of machine health,
performance, and location, allowing rental companies to optimize fleet management and maintenance schedules. [Also], an increased focus on ergonomics means these units are coming equipped with more comfortable cabs, intuitive controls and improved visibility for the operator.
Hovey: There are really three trends: Increasing versatility through attachments; electrification; and the total cost of ownership.
greater consideration and adoption of compact telehandlers, which is evident by the speed in which they leave our dealer lots upon arrival. Old stigmas around “traditional” equipment categories seem to be going by the wayside more and more each day to the point where people will test and consider product categories that they might not be as familiar with.
While no one talks about emissions as much anymore, you still see a preference towards 74 horsepower machines when possible to avoid diesel exhaust fluid and to keep emissions control as hands-off as possible.
Operator comfort and user experience are just as important in compact telehandlers as they are in more full-sized equipment. And with project costs and material costs being what they are, business owners and fleet managers are spending more time analyzing what the addition of a piece of equipment does to their carrying costs and their total cost of ownership over the life of a machine — and the versatility of a compact telehandler delivers application flexibility that ensures a high rate of utilization and profitability. It’s a multipurpose machine that can help you reduce the need for other machines.
Telehandlers are already popular tools on a wide range of jobsites as a result of their versatility. Attachments allow these machines to be used for even more tasks, expanding their utilization. One example is the auger attachment Genie introduced at ARA for the GTH-5519 compact telehandler. Especially when there are obstructions like a ditch, the GTH-5519 with the auger attachment is the perfect choice for drilling holes because you can extend the boom to reach over the ditch, which isn’t possible with other types of equipment.
The second trend, as discussed above, is electrification. Our priority at Genie is to provide support for our customers that are keen on electrifying their fleets, while also making sure any electrified solution we introduce meets the high standards of equipment owners in terms of quality and total cost of ownership. Our goal is to address the existing pain points that are hindering widespread adoption to help facilitate a smoother transition to electrification.
at total cost of ownership. Equipment owners understand that it’s not just the initial purchase price that matters when growing their fleets, because the value of that machine really comes from what it adds to their business during the life of the machine. That value is created through utilization rates and residual value. It also includes factors like maintenance, and how much it costs — in money and downtime
— to own the machine. One of the reasons the GTH-5519 is a popular choice when it comes to compact telehandlers is that it has high utilization rates while being durable and easy to maintain, with a strong value on the used market, providing a lower total cost of ownership.
Boehme: One trend we see in the compact telehandler sector today is these machines are being used more and more in urban and suburban applications compared to larger models, or other types of equipment, is that they have a small footprint but still offer plenty of power. For example, trucks still need to be
Early: Any technology that contributes to drive ROI will be popular in 2023. Machine reliability and longevity, as well as flexibility for fleet movement, are increasingly important.
Skyjack’s telehandlers use SKYCODED, a proven and simplistic control systems using our color coded and numbered wiring system to make our machines the easiest to troubleshoot. Using a relay-based control system allows Skyjack’s telehandlers to operate with simpler components resulting in less maintenance and lower costs.
Advances that incorporates flexibility, such as FLEXCAB, will also be impactful in the coming years to allow for fast response to rental customer demands. FLEXCAB is an innovative cab design that allows fleet operators to easily convert between open and enclosed cabs with simple hand tools, providing increased flexibility for fleet movement and fast response to
There is a growing interest in Lithium-ion as the battery market is maturing. Other trends include more options such as cabs, carriages and fork sizes, as well as offering a large range of
Due to their size, compact telehandlers make good candidates for hybrid power/ electrification. Do you see this size category as a viable ‘green’ machine?
There continues to be an increase in offering compact equipment with alternative power. As technology advances and alternative power options become more readily available the number of machines being considered “green”
Hovey: The trend in our industry continues to be toward electrification, particularly when you’re talking about smaller machinery such as scissor lifts and compact booms. But, when you’re talking about more demanding equipment like telehandlers, there’s really a varied landscape in terms of the adoption of electrification. It’s a little bit like the auto industry and electric vehicles. You’ve seen the early adopters already moving toward electrification. But, not everyone is ready yet.
One reason is that internal combustion telehandlers are used on every type of jobsite, from new construction all the way through to tenant improvements, so the availability of charging infrastructure varies. So the industry still needs to solve for how they’re going to provide power to these machines throughout different phases of the job.
The second factor is financial. The technology needs to advance to a point where you can get the same performance at a price point that makes sense in terms of the total cost of ownership. In other words, the acquisition price, which is typically higher for electrified equipment, needs to be offset by things that reduce the total cost of ownership, like reduced maintenance.
Tice: JCB has obviously embarked on the zero emissions journey and the compact products we believe are a really good fit for this kind of class size of machine. And you kind of touched on some of the points there with getting power to jobsites and things like that where compact products are typically the machine that’s behind the contractor’s truck or they’re ones that we take home in the evening.
So, compact machines aren’t being dropped off on job sites and remain on the jobsite for the full length of the product. These are products that are typically traveling with the contractor or the customer, the end user. So that’s why we think they’re a very good fit for electrification. And
when you look at the electric products, it’s really based on looking at compact equipment as ‘the automobiles of the electric industry.’
Automobiles seem to be doing very well with electrification, but when you start getting up into the mid-range equipment, some of your backhoes, large telehandler, things like that, these would be more compared to our say, semis, larger trucks, delivery vehicles, things like that, where electrification may not be the answer. So we do have an electric 5 5, we do see it as a good fit in the compact industry and does very well with electrification, giving the operator all of the same benefits or performance that he would get from a diesel counterpart. So, no loss in performance by going to electric, you still get the full eight-hour runtime of telehandler use. So, we do see it as being a very good fit for the electric market.
Boehme: Industry-wide, customers are asking for more electrified equipment solutions, and yes, we believe that electrification of compact telehandlers is viable and will continue to evolve with advancing technologies.
Kiskunas: We see telehandlers in the compact size class as very viable for electrification, and have select units in the category that are available as electric models. These machines are often not working at a “production” pace, and because of that many applications will be able to get by with a whole day of work, and then allow it to recharge overnight. Many of these units may be used for either indoor work in large warehouse construction, or need to drive
Overall demand is increasing for compact telehandlers being sold into the North American region because of the machines' adaptability.
to electrified machines when you factor in the elimination of fuel and other maintenance items related to a combustion engine.
Early: Electrification, whether by hybrid of full electric technology is a discussion topic currently. Although it’s not the only alternative - telehandlers are more open to hydrogen based technologies since their use pattern allows for longer engine use, versus aerials for example where intermittent engine use tends to mitigate against hydrogen use. These alternatives may well have a place longer term although I would say that within North America the short term future is with the traditional ICE.
Hagan: The Snorkel SR5719E is equipped with a 300ah (400ah Option) lithium-ion battery package. The applications vary between food processing facilities, municipalities, and many other sensitive areas such as bodies of water. Not a fan of Hybrid. We prefer to go full Lithium-ion.
What are the most-recent design/ engineering updates or changes that your company has made to its compact telehandler line? Why were these implemented?
Wood: Current machines are equipped with several features not previously offered including our smart handling system, boom cushioning, advanced attachment control mode, and much more.
Hovey: When we designed the GTH-5519, it was done purposefully so that it would be a durable, reliable, easy-to-own piece of equipment. Since its introduction, it has been extremely popular, so any changes have been small and incremental, in line with our commitment to continuous improvement and our Quality By Design brand promise.
Where the bigger changes have occurred is with attachments. At ARA, Genie introduced an auger attachment, which was designed specifically for the GTH-5519, but also is compatible with skid steers. Our customers have responded well to the attachment, because it does increase versatility, which has a positive impact on utilization rates.
Boehme: Last year, JLG began the process of redesigning its popular SkyTrak telehandler line, starting with the all-new 6034 and 6042 models. Understanding the demands and challenges crews face on work sites day after day, JLG engineered the 6034 and 6042 models with features and capabilities to deliver customers’ most requested features, with zero sacrifice. Featuring a redesigned build, reworked functionality, reimagined technology and refocused serviceability, these 6,000-pound maximum lift capacity telehandlers are ideal for
pick-and-place applications, such as handling, loading and unloading bulk materials on demanding residential, commercial, urban and suburban job sites across America.
The brand-new 6034 telehandler replaces the previous 6036 model, while the 6042 telehandler has been updated with new features inspired by the way customers work. The design of the 6034 and 6042 models emphasizes convenience and productivity. These newly updated SkyTrak telehandlers both feature a new advanced control system that allows for more options like load stability indication (LSI), seatbelt engagement and operator presence (SEOP), along with improved diagnostics. The new cab design features a larger LCD display for a more data-rich interface and larger, single-page load charts for added convenience.
Productivity and operator confidence go even further with several optional systems. The optional multi-reverse camera system lets operators backup with confidence by displaying multiple views from behind the machine to the left, right and rear. This system can be used during the day and night, and it features four components: Left and right-side backup cameras, a rear backup camera and a tri-view monitor. Kiskunas: We’ve focused on that kind of versatility with the introduction of the new MTA 519 compact telehandler. The use of a skid steer quick attach system makes it extremely versatile. The cab is large for a compact machine and is extremely operator-friendly, and the controls are very intuitive and are comparable to those of a large machine.
While it’s a compact machine, we’ve built it in a very robust way to hold up against the stresses of the jobsite, including a ground-engaging boom that features the same thickness on the sides of the boom as on the top and bottom of the boom to ensure strong performance when using buckets and attachments.
We’ve mounted the boom low for better visibility.
We have excellent ground clearance for off-road operation.
And the engine is incorporated into the machine in a way that also allows for a low hood for excellent visibility, and easier access to service points to assist in better daily service practices and lower lifetime total cost of ownership.
JLG says more customers are beginning to ask about electricpowered units.
investment by building upon reliability and serviceability, a direct result of customer and operator feedback. Skyjack’s latest range of telehandlers feature two unique systems. First, a Rear Axle Stabilization (RAS) system that increases stability and provides jobsite flexibility with three operational modes: normal free pivot, restricted, and locked.
Based on the boom angle the RAS system kicks in automatically allowing the operator to perform fine tuning adjustments to place the load safely at height without having to lower the load to level the frame and then lift again.
Another thing we did with this new model was that we pre-loaded our parts network to ensure easy access to parts from the first day the machine was available to ensure speedy parts delivery and assist in uptime.
Early: Initially launched in 2015 and updated in 2021, Skyjack offers six models of telehandlers throughout North America, including the compact SJ519 TH. Recent updates have increased the return on our customers’
Second, SMARTORQUE allows Skyjack’s TH Series’ 74 hp engines to deliver the same on-site job performance as higher horsepower units. The improved gearing and high-efficiency hydraulics package does not require DPF, DEF or other active exhaust treatment, thus reducing operating costs. Hagan: The biggest engineering changes would surround the successful design and deployment of the lithium-ion equipped compact telehandlers. Many lessons are learned while implementing additional options for a customer to consider. We are now transferring our compact telehandler knowledge and feedback into large machine designs. Stay tuned! ■
The award categories will cover products, technologies, work processes and programs that enable safe and productive working at height.
■ Working at height safety innovation – OEM/supplier
■ Working at height safety innovation – Rental company
■ Rental company of the year
■ Technology innovation award
SCAN HERE TO ENTER
ENTRY DEADLINE October 1, 2024
■ Sustainability in rental award
■ Sustainability in rental award
■ New product award – Scissor lifts
■ New product award – Scissor lifts
■ New product award - Boom lifts
■ New product award - Boom lifts
■ New product award – Telehandlers
■ New product award – Telehandlers
201 Rep. John Lewis Way South, Nashville,TN 37203
Sam Wyant, president of international sales at Ritchie Bros., reveals his take on the used equipment and auction markets and the company’s approach to technology. Lewis Tyler reports.
The used equipment market has seen challenges in recent times, not the least of which are high prices resulting from supply chain issues over the past few years.
At the same time, regions such as Europe and the Middle East have seen an economic slowdown, while other regions have reported a weakening in demand.
However, the supply chain crisis has eased somewhat and used equipment availability is increasing. This is good news for equipment auction companies like Ritchie Bros.
“We’re coming to a point where we’re seeing increased supply into the market based on both the work backlogs that are out there along with the original equipment manufacturers having caught up on some of their supply bottlenecks,” says Sam Wyant, president of international sales at Ritchie Bros., who joined the company in 2016 upon leaving Volvo Construction Equipment.
“We’ve come out of a period of tight constrained supply in the industry, and that’s what we see. When there’s an upcycle and the manufacturers can’t keep up with demand, then equipment supply becomes tight.
“As things start to moderate, and I’d say we’re in that moderation phase now, you start to see
The acquisitions Ritchie Bros. has made in recent years has helped to streamline business operations, according to the company.
PHOTO: ALEX LYUBAR - STOCK.ADOBE.COM
better equipment availability or the need to leverage additional channels for disposition.”
All this points to a healthy market, with companies now in a position to sell old machines and OEMs able to clear order backlogs.
In its used equipment market trends report for Q3 of 2023, Ritchie Bros. noted a 28 percent increase in buyer demand for site dumpers in Europe through its Mascus online equipment listing service when compared with 2022. Meanwhile, there was a 32 percent increase in the volume of site dumpers listed for sale on Mascus.
It’s a similar story for other types of equipment and in other regions.
However, Wyant stops short of predicting a sustained period of stability, pointing to unpredictable geopolitical environments; “If we take early October [2023] and what happened again in the Middle East, you’ve got some instability. You’ve got additional instability in Europe in addition to what had already started before the beginning of this year. That all drives some concern. You see a lot of economies taking dramatic fiscal action that’s trying to drive some reduction in inflation.
“History would say they’re trying to slow the economy, which would mean that eventually, you’ll see some impact on the construction side of things as well as residential, industrial and commercial.
“That should mean a bit of slowing, and we’ve got supply of equipment now into the marketplace that’s been very robust for a handful of years. To me, that means that you’ll have to find a way to balance that equipment supply out.”
In terms of equipment demand, the company is seeing higher demand for platform lifts and telehandlers, while also noting heightened buyer engagement in channels, leading to what Wyant describes as “pretty robust activity.”
“We can see that supply is catching up on higher-volume construction equipment,” Wyant says, “such as mid-size loaders and mid-size excavators. There seems to be additional supply available on some of those assets, but you still have a lot of niche assets where we’re hearing that supply is still tight. Large mining
Ritchie Bros. has continued to develop its remote auctions since introducing its online bidding service in 2002, despite continued strong demand for in-person options.
Alta Equipment Group reported more than $1 billion in sales of new and used equipment in 2023, the first time it has done so.
The company, which has from 85 locations on the east coast of the U.S. as well as in Quebec and Ontario in Canada, reported total revenues of $1.87 billion, up 19.4 percent on 2022.
The business includes a large construction equipment rental operation, where revenues rose by 12.3 percent for the full year to $202.4 million. Sales of used rental fleet were $128.9 million. Gross capital expenditure on its fleet last year was $242.4 million.
Ryan Greenawalt, Alta’s CEO, said; “The momentum in our business continued throughout the balance of 2023 and as a result, we delivered solid financial and operating results for the fourth quarter and 2023 fiscal year.”
Greenawalt said the company’s diversified strategy was proving successful; “The 16 acquisitions we have completed since going public in 2020 are also major contributors to our success, providing $537 million in revenues and $65 million in adjusted EBITDA.
“We are continuing to pursue accretive acquisitions opportunities which would further expand the scale and scope of product offerings for our customers.”
He said the outlook for 2024 remained positive; “Non-residential construction starts are forecast to increase compared to 2023. The material handling industry is forecasting another year of strong lift truck deliveries that is likely to resemble, if not exceed, the record year of lift truck deliveries in 2023.”
Physical and online auctions have their place
Wyant was speaking to sister publication International Rental News during the Moerdijk Live Xperience, Ritchie Bros’ first in-person event outside the U.S. or Canada, post
> machines or mid-size mining machines seem to still be pretty tough to come by from an OEM standpoint.”
pandemic. While equipment auctions have historically taken place in settings like this, Ritchie Bros has continued to develop its remote auctions since introducing its online bidding service in 2002.
“We’ve been working over the past decade to drive more of an online and convenience orientation toward the process of selling equipment,” Wyant says. “We had seen a migration start where we had increased bidder
With Hydro Mobile's NEW M2 Motorized Access System, you can access a work platform at any height, any time.
No independent fall protection required.
No more climbing masts. No delays or cost for alternate access solutions.
Ride to
in
and
As companies add to their aerial fleets with used equipment, maintaining these machines and keeping up with inspection schedules is not easy. And finding - and keeping - qualified technicians can increase the burden to buyers.
ALH spoke with Francisco Martins, Customer Equipment Solutions Marketing at United Rentals, for his top tips on what to look out for prior to signing the dotted line.
Before purchasing used aerial equipment, what should buyers review related to the machine’s maintenance history - and why is it important to do this?
Martins: Before making a buying
Preventative maintenance and regular inspections help companies maintain ANSI/ OSHA/CSA compliance required on MEWPs.
decision, companies should review a mobile elevated work platform’s (MEWP) maintenance history to determine whether frequent and annual inspections were performed and the unit was properly maintained. Having an accurate maintenance history helps companies build a future maintenance and inspection plan and gain a better understanding of the MEWP’s lifecycle.
After purchase, what role can preventative maintenance play in helping to protect their equipment investment and extend equipment life?
A preventative maintenance and inspection program for MEWPs provides many benefits, including reduced unplanned equipment downtime and increased machine performance. In addition, regular maintenance and inspections can result in lower future repair costs.
In general, preventative maintenance and inspection programs can reduce occurrences of catastrophic equipment failure and the need for overtime in order to meet project deadlines if equipment breaks down on the job. These programs also provide utilization data and maintenance history, which deliver insight into when to sell equipment to maximize its residual value. When a company decides to sell a MEWP, having detailed maintenance and inspection records can boost equipment resale value.
How can preventative maintenance and regular inspections bring safety benefits for used aerial equipment buyers?
Preventative maintenance and regular inspections help companies maintain ANSI/OSHA/CSA compliance required on MEWPs. Ensuring proper compliance prevents penalties and fines that may result if inspections are not performed in a timely manner or by appropriately qualified technicians. Staying on top of maintenance and inspections helps prevent mechanical failures and worksite accidents.
Why should companies consider outsourcing maintenance and inspections for the used MEWPs they purchase?
A maintenance and management program managed by a reliable third-party service provider can optimize an entire fleet operation, increasing overall efficiency and cost savings. It provides dependable access to qualified service technicians with experience servicing of MEWPs. This reduces internal costs, enabling companies to have fewer maintenance staff, service trucks and repair tools. These programs allow companies to keep their focus on core areas of the business, such as work on-site or bidding on jobs.
What are key criteria when evaluating service providers to handle outsourced aerial equipment maintenance and inspections?
When evaluating service providers, key considerations include finding a provider that services varied fleets of aerial equipment and provides access not only to skilled labor but also to supply chain networks for parts. The provider should be able to manage a regular maintenance schedule by proactively scheduling and completing required inspection and maintenance services per time intervals and usage.
The provider also should be able to demonstrate that it accurately keeps maintenance history records, which can increase equipment resale value.
Ritchie Bros. say the industry has to “find a way to balance equipment supply out.”
activity online using the tools that were available to buy equipment.
“There was already a bit of a migration and then of course the pandemic required us to go fully online, which was a bit of a shift for the company, but because we had made those investments, we were able to continue on with our business.”
Wyant also observes that customers like the online channels, which offers them a “very high level of comfort with the online bidding process.”
Despite this, he still notes a sustained high turnout at many of the company’s physical auctions; “We see still a lot of foot traffic on the inspection days. There’s a lot of customers that in addition to the investments we’ve made to bring better information to the online world, there is still a desire by many to come and see and touch the equipment. We have that (online) process but there has still been really good foot traffic post pandemic.”
Aside from its auction services, Ritchie Bros. has diversified its offering with a number of acquisitions in recent years. Two notable purchases are Rouse Services, a U.S.-based specialist in used equipment and rental data, and SmartEquip, a platform facilitating parts procurement for rental companies and fleet owners, particularly across Europe, North America and Asia.
Wyant says its investment in the companies form part of a longterm goal to provide customers
Before making a buying decision, companies should review a mobile elevated work platform’s maintenance history.
with a comprehensive suite of solutions across an asset’s entire life cycle; “For us, there’s different customer subsets that the tools offered by Rouse and SmartEquip are very important to.
“It’s about the concept of being involved and aligned with our mission to be alongside the customer through their whole journey from acquisition to disposition.”
The contributions of Rouse in this life cycle involve providing customers with insightful data on fleet performance, operational costs,
optimal fleet utilization and more. In the case of SmartEquip, it can source spare parts for fleet owners via its ecommerce platform.
Then, at the disposal stage, Ritchie Bros. can offer its auction services either directly or through its IronPlanet business that it acquired in 2016.
Furthermore, Wyant says the companies are helping Ritchie Bros. to streamline business operations; “These are complementary tools to the transactional side of the business for Ritchie Bros., Rouse is its own entity and we’re also a customer of Rouse.
“It helps to give some of those macro trends and the macro understanding of the business. From a customer engagement perspective, we’re along the journey in a much better way with the customers from acquisition to disposition, but then there’s the additional benefits of us getting some insights on the macro side that help us guide the business.”
Evidence of this can be seen in the previously mentioned monthly market trends report, which provides insight into a number of industries and equipment types, covering regions like the Middle East, North America and Europe.
The strategy for solutions and services is to establish a presence in the European market. To achieve this, the company appointed James Atkinson as the vice president of Rouse &
SmartEquip EMEA earlier this year.
Speaking to IRN in Moerdijk, Atkinson said the companies have been able to benefit from their association with Ritchie Bros., enabling them to “open doors and engage with the right people.” On its own merit, Rouse is in the midst of transitioning its rental benchmarking tool, which has been available in North America for more than a decade, to Europe.
“They’re making good progress in helping the customers to understand the value of the tools and building those relationships,” Wyant says. “As we made those acquisitions during the pandemic, we were hampered coming out of that, but we’ve ramped up and invested in the team. It’s a real strategy of ours to help our international customers in the same way they’re helping their customers in North America.”
Meanwhile, SmartEquip is already deeply rooted in Europe, with companies such as Boels, Loxam, Zeppelin, Wacker Neuson and Kiloutou all users.
Wyant says the satisfaction among customers regarding productivity gains and optimized technician and fleet utilization shows that the company is beginning to make its mark on the European market, despite still being in the early stages of penetration; “The customers that they’ve engaged with have been very happy with the productivity gains that they’ve had and how they’ve been able to maximize use of time of the technicians and a fleet in that process. ■
If you are in the rental equipment industry, it is vital that you have great information to support business decisions.
Economic and business forecasts are valuable tools to provide valuable information that could impact your business.
There are many reports to choose from, such as the American Rental Association’s rental forecast that provides great insights regarding trends and anticipated direction the rental market is heading. Knowing what others in your industry are thinking, planning and implementing can influence your future decision-making.
If you are involved with mobile elevating work platforms, having
the same insights on this specific equipment category can be critical in your planning. The IPAF Global Powered Access Rental Market Report, published annually, is the leading comprehensive overview of key global MEWP rental markets, exhaustively compiled by Ducker Carlisle with valued input from IPAF members and worldwide industry experts.
This report has been in place
for over a decade and has proven to be an asset to many in the industry. With key facts and figures such as fleet size, utilization rate and retention period, they help senior management to plan for future investments. They include an estimate of the size of the MEWP rental fleet worldwide, with a breakdown by region and machine type.
IPAF members that are rental companies, manufacturers, dealer/distributors and suppliers can obtain the report free of charge. Non-members may purchase the reports on the IPAF website. Perhaps it’s time to consider joining IPAF?
Members and non-members who log data in the IPAF accident reporting portal (www. ipafaccidentreporting.org) are now able to access improved dashboard functions that allow them to track their own safety statistics against
the wider industry. Those using the incident reporting dashboards can now apply multiple filters that will give a snapshot of member company incidents entered against all database entries, which of course are completely anonymous
so no company or individual can be identified.
While major accidents may hit the news or be found on OSHA FATCAT reporting, too many incidents are not identified, particularly when no one is injured or all near-misses. Our industry needs more data from across all sectors of industry to ensure we are adequately addressing the hazards and risk workers are facing.
ALL are invited to participate in the reporting that is 100% anonymous. This is not an accident investigation, only an incident report – no names wanted. Be part of the solution and register today to be able to see your reporting or just add a report anonymously at www.ipaf.org/accident.
If you are an IPAF member or a non-member interested in learning more about IPAF, the IPAF 2023 Annual Report is now available. The report offers insights into IPAF activities, key initiatives, and statistical highlights, as IPAF continues their mission to promote and enable the safe and effective use of powered access equipment worldwide. The report may be accessed via the IPAF website: www.ipaf.org/annual-report
IPAF and Trackunit are actively collaborating to provide simplified certification management, seamless access to powered access machines, and effortless documentation, addressing complexities and safety concerns. This partnership, leveraging ePAL’s extensive user base of over half a million downloads and Trackunit’s well-developed ecosystem, aims to build a safer and more efficient jobsite environment.
At the 2024 IPAF Summit hosted in Copenhagen, Denmark, Chris Greenbank, IPAF Digital Marketing Manager and Domokos Speeder (above), Vice President of Customer Success at Trackunit, demonstrated the unlocking of a scissor lift with the ePAL app via mobile phone, a transformational feature that will be launched in June 2024. The next phase of ePAL app updates will include the automatic completion of the logbook, scheduled for Q3.
IPAF is glad to welcome another company to our membership in North America, Sigalarm is recognized as a world leader in power line warning systems. Our mission is to save lives and equipment by preventing unintended power line contact. They offer a complete range of power line warning product, used across varying industries
including construction, fire trucks, television, pipeline, utility, concrete pumping, and military
just to name a few.
As OSHA has identified electrocution within their Focus four Hazards and IPAF accident reporting identifies electrocution as a leading cause of fatalities associated with MEWP operations, greater awareness of means to protect workers form this hazard is needed.
Welcome Sigalarm!
Everyone knows the secret to a successful business is fulfilling the needs of customers. In the MEWP
industry there is no one more qualified to express the needs of MEWP users than contractors,
Join IPAF as the North America Regional Manager, spearheading enhanced member services and recruitment efforts. Your role will entail promoting safe and effective powered access use across the region, conducting member visits, and building relationships with government and industry stakeholders.
With relevant business qualification and experience in the construction machinery sector, you’ll possess exemplary communication, negotiation, and organizational skills. Proficiency in Microsoft Office suite is essential, along with a valid driving license. Your proactive approach, ability to work both remotely and in-office, and willingness to travel will make you an ideal candidate. If you are passionate about safety, innovation, and driving positive change in an international environment, apply today! For more information on the role and how to apply, visit: https://www.ipaf.org/en-gb/jobs-ipaf
www.ipaf.org info@ipaf.org
IPAF USA
225 Placid Drive, Schenectady, NY 12303
Tel: (518) 280-2486
Fax: (518) 689-6800
tony.@ipaf.org www.ipaf.com
IPAF USA MEMBERSHIP OFFICE
800 Roosevelt Road, Suite C-312 Glen Ellyn, IL 60137
Tel: (630) 942-6583
usa@ipaf.org www.ipaf.org
IPAF WORLD HEADQUARTERS
Moss End Business Village, Crooklands, Cumbria LA7 7NU, UK
a leading user’s industry for this equipment. IPAF understands the need for contractor engagement and IPAF NA council member TJ Lyons has 36 years of experience in the construction safety field with the majority of his career working with two of the largest general construction contractors in the United States and abroad -Turner and Gilbane.
Tel: +44 (0)15395 66700
Fax: +44 (0)15395 66084 info@ipaf.org www.ipaf.org
TJ will lead an initiative to meet with regional general contractors in a facilitative format and learn from our customers about what they really want from the MEWP industry. This includes suggestions on MEWP design changes or
improvement they believe will make their work easier. The council will take their feedback and ID potential actions to address their ideas. This may include user feedback to specific manufacturers. If this creates fruitful results the council will expand into other regions.
One of the many activities IPAF undertakes on behalf of its members is active participation in the development of industry standards. IPAF staff serve as the ears and voice of our collective membership in the development of voluntary consensus standards that enhance the competitive position of all through standardization of design, safe-use and training for the equipment. As an example, a manufacturer would not want to have to design and manufacture a different machine for every country they sell into or nor would a user want to have machines that all looked an operated completely differently.
While MEWP ISO standards are typically adopted by individual countries (they could, as Canada adopts with Canadian deviations), the provide the foundation from which country standards are drafted.
ISO/FDIS 16368:2023, Mobile elevating work platforms – Design, calculations, safety requirements and test method: Publication is expected by November 2024.
ISO/FDIS 18893:2023, Mobile elevating work platforms – Safety principles, inspection, maintenance and operation: Publication is expected by November 2024.
ISO/DIS 18878:2023, Mobile elevating work platforms – Operator (driver) training: Could be published close to publication dates of ISO 16368 and ISO 18893. If not, publication would likely be before February 2025.
There’s only one place you’ll find the heavy hitters of concrete and masonry this January: Vegas, baby — at World of Concrete 2025, the largest and only annual international event dedicated to your business. Be here to mix with industry giants. Get your hands on the latest technologies revolutionizing safety, performance and speed. And learn what it takes to not only claim a piece of our industry’s massive projected growth but dominate the field. Join the power players of concrete and masonry.
EXHIBITS: JANUARY 21-23, 2025
EDUCATION: JANUARY 20-23
LAS VEGAS CONVENTION CENTER
Rising infrastructure spending and ongoing fleet replacement are just some of the drivers behind North America’s increasing demand for access equipment – including rough terrain scissor lifts.
“Construction activity is accelerating in North America as we enter ‘construction season,’ so we anticipate the current strong, steady demand for rough terrain scissor lifts to continue throughout 2024,” says Bob Begley, JLG’s director of product management – scissor lifts, vertical lifts and low-level access lifts. “That’s because despite utilization varying based on seasonality and concentration of construction activity in and around an area, these machines continue to be common jobsite tools thanks to their ability to expand users’ capabilities whether working on-slab or off.”
Like their slab sisters, RT scissors can be used in and around sensitive environments, such as work on data centers, hospitals, laboratories and industrial chemical facilities, and they’re also well-known for operating in extreme environments like below-freezing or high-heat temperatures.
It’s this jobsite adaptability that is propelling change within the rough-terrain market, specifically the industry’s push for more electric options, which, according to Begley, shows no signs of slowing down.
“One trend is the driving demand for electric models, which continues to grow as battery technology advances and environmental considerations become more and more stringent,” he says. “JLG offers both an enginepowered RT and an electric-powered RT (model designation ERT) model in each size class, providing buyers with a choice between an engine- or an electric-powered unit in each size.”
The RT/ERT lineup includes eight modes:
RT2669, ERT2669, RT3369, ERT3369, RT4069, ERT4069, RT4769 and ERT4769.
Like JLG, many manufacturers over the last half decade have launched refreshed and redesigned RT lines.
Genie’s GS-2269 DC, GS-3369 and GS-4069 DC scissor lifts are the company’s most recent rough terrain scissor debuts.
The GS-2669 DC is designed for indoor and outdoor construction, maintenance and installation applications with firm, level surfaces. Its rough terrain capability means it can easily adapt to dirt, sand and mud. A quiet, electric drive motor provides emissionfree performance, while a patented, full-time oscillating axle automatically adjusts the axle position based on ground conditions. With a 1,500-pound lift capacity and 35 percent
gradeability, it is suitable for a variety of applications.
For tough, construction-oriented jobsites, the GS-3369 RT is a purpose-built four-wheel drive machine with positive traction control that can drive and function at full height. The GS-3369
comes with foam-filled, RT tires and delivers 40 percent gradeability.
The GS-4069 DC was the industry’s first 40-foot RT scissor lift in this class able to drive at full height. Four-wheel drive and positive traction control enable up to 40 percent gradeability on slopes. It also has an oscillating axle and optional auto levelling outriggers. The unit’s 800-pound capacity platform also has a 5-foot slide out extension.
In 2020, Haulotte debuted its new Pulseo all-terrain scissor lifts, the HS4390 E and HS5390 E. Designed for North America, the units have platforms that can carry up to four people and a total of 1,650 pounds. They can be extended out to 19 feet long, and width is 6 feet, 2 inches.
chart-topping
indoors and outdoors, the SR2024E’s large deck – with extension – features from the rest of the RT range, including four-wheel drive with oscillating axles and 30 percent gradeability, designed for tough work environments. Also included is an overload sensor system, which stops the operator from using the machine if there is too much weight in the basket.
Lead-acid and Li-battery options
Platform height is 42 feet 8 inches for the HS4390 E, and 52 feet 6 inches for the HS5390 E. The scissors can be driven at height on uneven terrain.
The company says the battery-powered lifts emit no pollutants and operate at under a 60-decibel noise level.
The scissors are powered by a 48-volt battery pack that can handle a full day’s work on one charge. The batteries can be charged at the end of a shift on any standard 110- to 230-volt single-phase electrical network. Haulotte offers an optional accelerated charger in which the batteries can be charged up to 80 percent in three hours. It also offers an optional removable and interchangeable range extender for rapid recharge while the lift is operating.
LGMG launched its largest electric RT scissor lift to date at Intermat this year.
The SR2024E has a maximum working height of 71 feet and a large platform measuring 15 feet long by 7.5 feet wide with a maximum capacity of 1,653 pounds.
Able to accommodate up to four people
While they’re not your typical four-wheeled RT scissor, track-based scissor lifts offer users mobility, stability and capacities that some RT counterparts can’t.
New tracked units came to market this year from both AlmaCrawler and Goman.
AlmaCrawler’s Bibi 1090 EVO is a selflevelling scissor launched in North America by the company’s U.S. distributor, Ruthmann Reachmaster.
The lithium-powered Bibi 33BL PriMO is an updated version of AlmaCrawler’s Bibi 1090 EVO. The revamped model sees the addition of AlmaCrawler’s full electric, PRiMO technology that includes removable battery packs.
Alongside the unit’s removable power source system, the Bibi 33BL PriMO is all-electric drive, replacing the standard unit’s hydraulic drive.
are both available as options, alongside the combustion engine version.
In 2020, MEC renewed and expanded its RT scissor series with four models in both electric and diesel being offered. At 33- and 40-foot platform heights the enhanced features of the 69 Series include an oscillating front axle, larger deck, longer slide out extension deck with incremental lock positions, integrated sheet material rack and patented drywall tray and pipe rack.
Electric models are 2WD with direct electric drive for improved duty cycle. Diesel models are 4WD with traction control and optional outriggers. Fully featured, the 69 Series includes 40 percent gradeability, all motion alarm, automotive horn, flashing beacons and diagnostic readout as standard. The construction-grade RT scissors have flexible
Ebbe Christensen, president of Ruthmann ReachMaster said, “The new Bibi unit is not only offering the unparalleled bi-leveling and self-leveling capabilities the market has come to know from these units, but also a completely new way of thinking how to power – and charge – the next generation of electric powered units.”
Also launched earlier this year was China-based Goman’s S05C and S08C models.
Goman was founded 2003 and shifted its focus to North America in 2017. The company extended its lineup for North America with its S05C and S08C launch at this year’s ARA Show.
The new units are the combination of Goman’s slab scissor stacks and a new tracked chassis. They have working heights of 26 and 32 feet, respectively, and both models can work on a slope of more than 15 degrees on Y-axis (front/rear) and 12 degrees on the X-axis. There are a range of power options, like gas or diesel engines and lithium battery.
“Uneven ground in agriculture or construction sites needs crawler mounted scissor lifts,” the company says. “Whether it is a building a green house or tent, in agriculture or repairing a bridge, a self-levelling crawler scissor lift is most helpful as workers can use the big platform for various challenges on uneven ground.”
Skyjack’s SJ9250 RT scissor features a working height of 56 feet.
platform load options including the standard integrated sheet material rack, designed and approved by MEC, according to the company.
Skyjack also recently debuted a fully redesigned RT scissor lineup, as well, with a focus on increasing platform heights and larger decks.
The decision to move to increased platform heights was to compliment the growing trend towards urban intensification with taller buildings, higher siding and more work at increased heights,” the company says. “The large decks seen on Skyjack’s RT range remain the largest work platforms in the market, which is complimented by class-leading capacities.”
At just over 6 feet wide and 14.5 feet long, with the option of single or dual 5-foot extension decks, the all steel platforms on the line provide a large working space for personnel, tools and material. The range also saw platform heights increase to 33, 43, 53 and 64 feet, respectively.
Lastly, platform capacities have also increased across the series and range from 1,200 up to 2,750 pounds.
Sinoboom offers two RT models for customers, the 4389RD and the 5389RD. With working heights of 49 feet, 7 inches and 59 feet, 9 inches respectively, both units feature a maximum platform capacity of 1,499 pounds. The 4389RD features gradeability of 40 percent, while its larger sibling affords users 50 percent.
Snorkel has recently focused on expanding its high-capacity (HC) product line, which consist of large decks and ultra-high lifting capacities. The company offers three models: the S9031RT-HC, S9043RT-HC and the charttopping S9056RT-HC.
Designed with a twin extension deck and extra-wide pallet gate as standard, the S9056RT-HC features a working height of 62 feet and a maximum load capacity of 2,500 pounds.
With a maximum platform size of 25 feet by 7 feet, 6 inches when fully extended, the
S9056RT-HC provides a vast working area and help to reduce the number of times the operator needs to lower and elevate the lift. For material loading, the HC scissor lift lineup is designed with an integrated double material loading gate on the platform to allow a full-size pallet to be placed directly onto the deck. This makes the loading of materials onto the lift both safe and more efficient, as the correct material handling equipment can be used, according to the company.
China-based XCMG has launched 10 rough terrain scissor models for the North American market with working heights from 39 to 72 feet.
“These RT scissor lifts adopt high efficient and reliable axle balancing system, where the rear axle is integrated with the frame and the front axle swings efficiently,” XCMG says. “This system is more efficient than the negative pressure-levelling cylinder axle balancing system and more reliable than the rear axle half-axle balancing system.
“Meanwhile, it adopts safe and energy-saving gravity descent method. Compared with the traditional power descending method, this method is smoother and has better speed proportional control. And this method is safer, even if the platform continues to fall after overhauling the bracket support state, the operation will not cause damage to the product structure.” ■