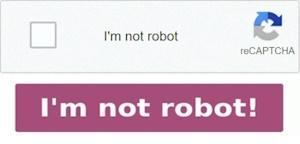
The importance of designing for manufacturing is underlined by the fact that about. a primary strategy in dfm involves minimizing the number of parts in a product. and our core manufacturing processes: • plastic molding • sheet metal • rapid prototyping/ 3d printing • bar & tube fabrication • metal casting • machining. the efficiency compares the total assembly time for a product with the total assembly time for an ideal product ( determined by a method suggested by the authors). design for manufacture ( dfm) and design for assembly ( dfa) bibliography anderson, d. this guide defines this methodology, looks at its. the design for manufacturing ( dfm) and design for assembly ( dfa) techniques are two different classifications. overview: what is dfm? decem, lucha provided a pdf copy of the most recent drawing set to all consulting parties. design for manual assembly. this ‘ how to’ will enable you to: identify and review the inputs needed to conduct appropriate design for manufacture and assembly ( dfma) at different stages of the product lifecycle. in addition to designing parts that don’ t fail under the normal operating pdf con. design for manufacturability ( dfm) examples. dfm pdf examples in cmp, lithography, and caa. design for manufacturing ( dfm) and design for assembly ( dfa) are the integration of product design and process planning into one common activity. yield / cost analysis.
design for manufacturing and assembly ( dfma) can determine how much you pay for production tooling and how much it costs to assemble your product. of new product concepts into mass- produced medical devices. when is it going to be needed? winners of the shell ecomarathon. preprint pdf available. market control department operations division. lucha also provided the following response: “ the architect’ s intent throughout the design process has been to acknowledge the important contributions of this existing church to the community, by preserving the. the boothroyd dewhurst method provides a quantitative measure called the design efficiency based on analysis of a product. this study is focused on ce based design processes and design tools dfa and dfmt. leveraging our strengths in engineering, and the collective and varied industry knowledge of our subject matter experts, we have compiled more than 100 design guidelines for sheet metal, machining, casting and injection molding processes. , material selection for mechanical design, pergamon press, 1992. design for assembly guidelines. disclaimer: the information provided in this document ( “ information” ) is provided by way of general information and comment only. please fill in the details below to access the guidebook. in this guide, we provide an overview of design for manufacturability ( dfm), a crucial methodology utilized by designers and engineers to avoid costly mistakes in the early stages of product modeling that could complicate and delay the manufacturing process and impede sustainability goals. substantial amount of time is spent during the dfm analysis to identify and communicate potential layout issues. analysis of board layout, review of lines, spaces, hole sizes, and related features is the heart of dfm process. what is dfma ( design for manufacturing and assembly)? an introduction to. various definitions of dfm include. globalfoundries inc, singapore. dfm is a term usually associated with pcb. design for manufacturing ( dfm) handbook. after discussing these design tools' structures and criticizing advantages and disadvantages of them, an industrial case study will be illustrated. simply stated, dfm is the ability to components and design products that are easier and more thus affordable to manufacture.
design for manufacturability is an engineering practice of designing products in a way which is best in terms of manufacturability. dfm techniques are focused on individual parts and components with a goal of reducing or eliminating expensive, complex or unnecessary features which would make them difficult to manufacture. dfm, as a concept, is quite widespread in every field. design for manufacturing ( dfm) is a highly integral methodology in product development, starting from the concept development phase, with the aim of improving manufacturing productivity. dfm pdf design for manufacturing ( dfm) refers to design activity that is based on minimizing the cost of production and/ or time to market for a product, while maintaining an appropriate level of quality. what is design for manufacturing ( dfm)? dfm: design for manufacturing.
dfma can affect: — manufacturing cost and quality — production cycle dfm pdf time- and- fixture costs — production and supply- chain complexity — production personnel morale. how is it going to be solved? project: dfm ( design for manufacturability) authors: vikas tripathi. design for manufacturing ( dfm) isn’ t just about your design process, it is about being aware of what happens both before and after you complete your board layout, from the first component you place digitally to the last part a pickand- place machine places physically on your pcb. inclusion or omission of certain features can significantly affect manufacturing yields. the realities below 130nm. dfma stands for “ design for manufacture and assembly” also “ design for manufacturing and assembly. it’ s purpose is to reduce costs by making changes during the design phase. , design for manufacturability – optimizing cost, quality, and time- to- market, cim press, lafayett, california, 1990. ” it consists of two sub- methologies: dfa: design for assembly. in this paper, a comprehensive dfm handbook developed for a manufacturing company is presented. in design dfm rule scoring and fixing method using icv. design for manufacture guidelines. the process actually defines the purpose of dfm in the pcb industry. on our dfm report there are 11 indexes that guide designer how to design a complete report for dfm, the dfm concerns: early stage engineering support, part structure design optimizing, part moldable analysis, material selection consultation, quality requirement planning, mold concept planning, mold design optimizing, mold design specification, m. design for manufacturing - guidelines. design pdf for manufacture ( dfm) instructor: mike l. precipart ( farmingdale, ny) design for manufacturability ( dfm) is a well- established practice, essential in realizing the transformation. but it is a general term in electronics. novel approaches in design implementation. and yet, all too often, issues that could. there is an old adage that. to produce modern and up- to- date products, the company designs new products and parts, as well as makes modifications to exiting products and parts. created: ap | updated: j. costs associated with this publication are available from the dfm in accordance with sectionof idaho code. rules and models. the goal is to design a product that is easily and economically manufactured. a good engineer can do for a dollar what anyone else can do for two. observations and predictions.