We look forward to serving you and providing your company with high quality forgings.

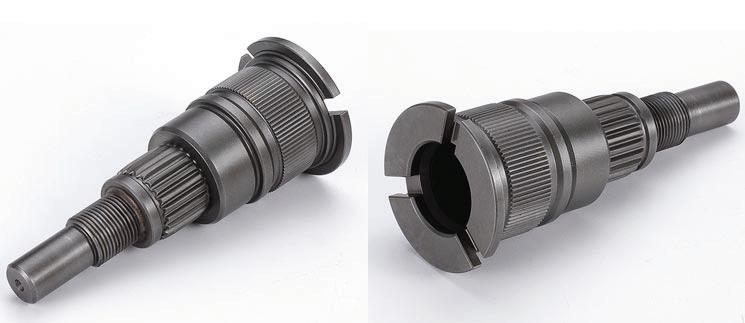
We look forward to serving you and providing your company with high quality forgings.
KDK Produces upset and press forgings. We have been producing them for some of the leading companies in America for more than fty years. Companies that demand the very best in precision and quality choose KDK. KDK began forging components in 1947. We have been making advancements in our processes ever since then.
We began as a company that was primarily making war time parts, WWII that is. Torsion bars were our main product and there was no shortage of work to be done during and after the war. Since then we have expanded into many di erent industries. We work in the automotive, agriculture, mining, industrial tool, and military industries to name a few. We have increased the amount of products that we used to produce by a few hundred fold.
Impression dies forging involves pressing or pounding metal between two dies (referred to as tooling) with the desired part's precut contour with the shaft forging process. This method may produce parts weighing between a few ounces and 60,000 pounds.
Graphical depiction of process steps:
Still Graphic
Animated Sequence
Video
The impression-die forging process, also known as closed-die forging, can create a virtually in nite variety of 3-D forms, ranging in weight from a few ounces to more than 25 tonnes, out of steel, aluminium, titanium, and other alloys. On hydraulic presses, mechanical presses, and hammers with capacities of up to 50,000 tonnes, 20,000 tonnes, and 50,000 lbs., respectively, impression-die forgings are regularly produced.
As the name suggests, as the forging stock deforms plastically, two or more dies carrying imprints of the component shape are brought together.
Cold forging is a variety of impression die forging, typically done as hot work at temperatures up to 2300 degrees F. To produce a wide variety of component forms, cold forging incorporates several operations, including bending, cold drawing, cold heading, coining, and extrusions with the shaft forging process. Cold-forged metals can range in temperature from ambient temperature to several hundred degrees.
To produce a wide variety of component forms, cold forging includes some techniques, including bending, cold drawing, cold heading, coining, extrusion, punching, thread rolling, and more. Varied shaft-like elements, cup-shaped geometries, hollow components with stems and shafts, various upset (headed) and bending shapes, and combinations are among them.