JABRA
JARED ABRAHAMIAN
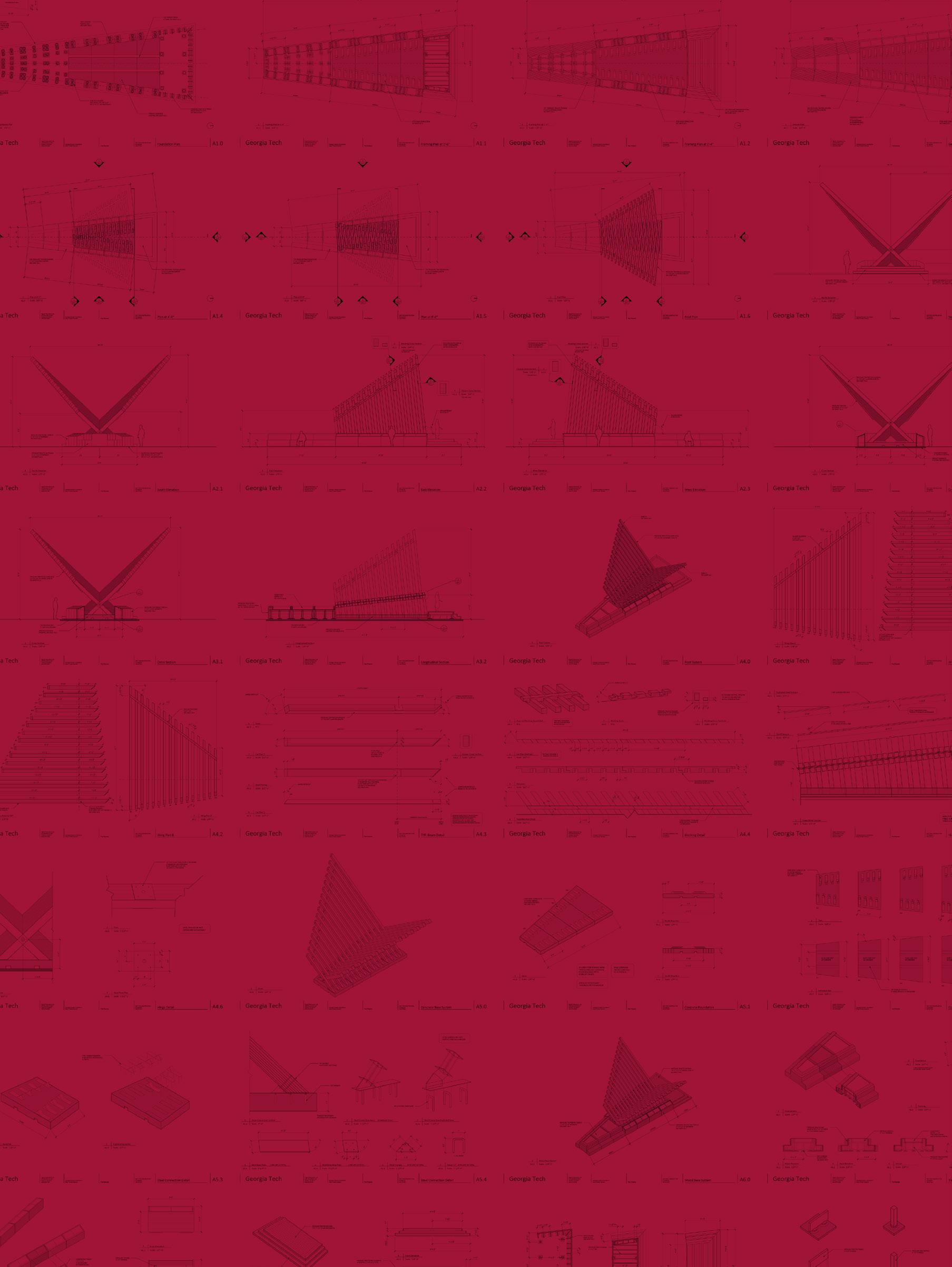

timber technologies
1. ATLANTA PHOENIX - PHASE 1 - PHASE 2
2. 255 ARTISAN YARDS
3d printing
3. WITH A TWIST
4. INITIATIVE 99 COMPETITION
5. HYDROPONIC PAVILION
6. JUGTOWN - PHASE 1: FABRICATION - PHASE 2: MUSEUM DESIGN
fabrication & computation
7. MEDUSA.I.
8. TRAVELING FUN PALACE
ARCH 4017: Senior Capstone Studio Competition
Location: Ponce City Market in Atlanta, Georgia
Interdisciplinary Team: Katy Bradford (PhD Engineering), Ben Ullrich (Production), Daniel Hsu (Large-Scale Fabrication)
Role: Artist, Project Team Manager, Lead Designer Spring ‘22 -Summer ‘23
1st Place
Best Overall Project: Capstone Senior Design Expo
In collaboration with the Digital Fabrication Lab, the Georgia Forestry Foundation’s senior capstone competition initiated a Mass Timber Design Studio, uniting students across Architecture, Civil Engineering, and Construction Management. Phoenix emerged as an educational, mobile mass timber pavilion designed for deployment. Inspired by the bird’s form, the pavilion features a wing-like canopy that pulls people underneath it to the educational display.
This project features the unique story of architectural student work continuing outside of studio and becoming a professional, real-world project.
In partnership with the Georgia Forestry Foundation, Jamestown, Formations Studio, and Georgia Tech this student-designed mass timber sculptural pavilion is planned to be installed in the high-profile location, Ponce City Market in Atlanta, Georgia. I served as the artist and student team leader for the project through the schematic design phase. The project is now being forwarded through construction by Formations Studio.
ARCH 4017: Senior Capstone Studio Competition
Location: Atlanta, Georgia
Client: Georgia Foresty Foundation
Interdisciplinary Team: Katy Bradford (PhD Engineering), Ben Ullrich (Production), Daniel Hsu (Large-Scale Fabrication)
Role: Artist, Project Team Manager, Lead Designer Spring ‘22
1st Place
Best Overall Project: Capstone Senior Design Expo
The client asked for a design of something that unconventionally showcases mass timber. The project needed to be mobile to an extent as the original problem was that it would travel across the state of Georgia on exhibition.
Mass timber is traditionally immobile due to its size and weight. Because of this challenge, I naturally stumbled into the concept of deployable structures early in the research phase of the project.
The driving idea of this project is that the ‘wings’ fold into each other and flat-pack in sets of modules that can be laid on the bed of a truck. The original concept became that of a sail, reaching up into the atmosphere. As the project progressed, the engineering calculations made it evident that changes were necessary to sustain wind loads.
The original geometry was then rotated 45° to a more stable form, and thus the Phoenix was born.
The model image on the right depicts the final concept of the Phoenix presented to the client on the final review day. The wings hold an ETFE canopy that collects rain and channels it to the flower bed. The entire sculpture illuminates at night to call people to the exhibit.
Summer Internship Continuing Project
Company: Georgia Tech
Supervisors: Tristan Al-Haddad & Russell Gentry
Client: Georgia Forestry Foundation
Location: Ponce City Market in Atlanta, Georgia
Role: Artist Summer 22’ - Summer ‘23
Originally, this project was part of a competition among senior students at Georgia Tech. The client chose my group’s concept, and we won 1st Place at the Georgia Tech Senior Capstone Expo.
As the only student on the team who wasn’t graduating a year ahead in my studies, I was able to continue the project professionally.
With Ponce City Market’s new initiatives, including the construction of a mass timber office building, the Phoenix was naturally the perfect sculpture for the site. After receiving tentative approval for the site, the project needed to be taken from a studio project to something that could be built.
As an intern at Georgia Tech’s Digital Fabrication Lab, I forwarded the project through the schematic design phase with mentorship from the course teachers and Formations Studio. The Phoenix awarded me the opportunity to speak at the Georgia Forestry Conference on behalf of the client. I even gave a talk to newly elected state representatives on the future of mass timber construction!
Following the summer of 2022, the Phoenix officially became a Formations Studio project after it was priced at ~$500,000 to build. I was brought on to Formations Studio to continue the project. In the late spring of 2023, the project had to be conceptually redesigned to accommodate a reduced budget and conform to the engineering load restrictions of the site upon further inspection.
This past summer, I worked as a design and fabrication intern drawing the design development set for the new concept, ‘Forest,’ not featured in this portfolio due to client confidentiality. The mass timber pavilion is tentatively planned for construction in 2024.
The Phoenix became my day and night for the year from 2022 to 2023 and was my first significant project as a professional, opening many doors and exposing me to the business side of the industry.
Ponce City Market Flyover
Developing a Pricing Set
My major task as a summer intern at the Georgia Tech Digital Fabricaiton Lab was the opportunity to independently draw a cohesive pricing set for the Phoenix.
The pricing set is 37 pages in length composed of a total of 88 drawings. I also created renderings and a concept video to help secure donations for the project.
After the site location was confirmed at Ponce City Market, the structure no longer was going to be considered mobile so the deployability function of the design was lost. The sculpture was redesigned to be placed over the preexisting foundation on the main lawn at Ponce. While the form was inherently the same on the outside, the foundation was redesigned for this drawing set to accommodate the site conditions.
This pavilion is made with 8-ply glulam beams composed of 2x8s of varying lengths in conjunction with an NLT and concrete base. This is a modular system meant to be moved to several locations. The canopy is formed by 4 modules of 8 beams each which deploy about a central hinge point.
Scan For Full 37 Page Pricing Set
A5.4|STEEL CONNECTION AXON
A6.5|FOOTING TYPE 1
STEEL CONNECTION PIECE
STEEL CONNECTION PIECE 8 PER MODULE (4 MODULES)
14" LAG BOLT (4 PER UNIT, 128 TOTAL)
14” LAG BOLT (4 PER UNIT, 128 TOTAL) a5.3.1|ISOMETRIC
CAST IN PLACE
CAST REBAR IN PLACE
*CONSULT NECESSARY THICKNESS WITH ENGINEER
*CONSULT NECCESSARY THICKNESS WITH ENGINEER
Internship Continuing Project Formations Studio
Client: Georgia Forestry Foundation
Location: Ponce City Market, Atlanta, Georgia
Role: Artist / Drafter Summer ‘23
A New Concept Is Born
After the pricing was established, it was sent to an engineering firm. However, following a site review, it was determined that the structure was too heavy for the lawn, situated atop a parking garage.
Formations Studio reimagined it as a ‘forest,’ evenly dispersing the weight of the mass timber and eliminating the need for Phoenix’s concrete footing.
Standing at a height of 36 feet, the Forest offers an interactive exhibit experience, simulating a ‘forest’ with elements interspersed among mass timber trees. Construction is tenatively planned for 2024.
My Involvement
Under my boss’s supervision, I created a 34-page design development drawing set for Forest. Forest was designed proactively with fabrication in mind, making it more economical than Phoenix. The same profile shape for the columns will be milled 38 times. Additionally, I constructed a 3’ x 3’ x 3’ scale model of Forest, which was displayed at the 2023 Georgia Forestry Conference. I also developed a flyover video using Enscape and created presentation materials for the client.
See How Its Made
A3.10|Section B
A2.10|South Elevation
CLT COLUMN LIES OVER RUNNEL1103 Ryan Roark Studio
Location: Mechanicsville, Atlanta, Georgia
Individual Studio Project Summer ‘21
Mechanicville 2030
Exhibited at the Atlanta Preservation Center, 2021
Artisan Yards, situated in isolated Mechanicsville, lacks essential amenities, falling behind neighboring districts due to natural barriers. The proposed mixed-use development at 255 Forsyth St SW aims to rejuvenate the area by providing an affordable pharmacy, offices, apartments, and more. Retaining the historic steel structure, the design removes non-historic walls to open up space while integrating recycled brick, reclaimed wood, and natural materials for sustainability.
Organized sectionally, public functions occupy lower levels, while private residential spaces are elevated. The building’s facade reflects the artistic culture of Castleberry Hill from the South and the industrial typology of Mechanicsville and Summerhill from the North. Two back-to-back “C” shaped courtyards connect people and offer visible pathways towards Castleberry Hill and Mechanicsville, fostering community.
In line with smart city principles, the development prioritizes sustainability with recycled materials, energy-efficient systems, and a focus on urban heat island mitigation. The use of vegetation on roofs and walls, coupled with public green space along the Northern facade, addresses environmental concerns. As the building ages, the materials will return to the Earth, creating a harmonious blend of functionality and ecological consciousness.
This project was featured as a part of Mechanicsville 2030, an exhibition hosted at the Atlanta Preservation Center by our instructor, Ryan Roark. The exhibition served as a proposal for an urban adaptive resuse plan for several buildings located along Whitehall Street in Atlanta.
1Bed 1Bath Studio Cut Through Stores &
2Bed 2Bath
w/ Balcony w/ Balcony
Residential Section Perspective
Structures and Materials Lab Research
Location: To Be Installed on Georgia Tech Main Campus in Atlanta, Georgia Interdisciplinary Team: Katy Bradford, Aditya Jain, and Austin Sanderson Role: Designer, GCode Specialist, Print Operator Fall ‘22 - Present
About the Sculpture
We all face challenges that require us to adapt and grow. While these changes can be difficult, they provide the opportunity to emerge with a refined perspective and problem-solving capabilities. Currently, architecture and construction are evolving to meet the increasing demands placed on the built environment. This sculpture, which was 3D-printed in the shape of an architectural column, serves as a tangible embodiment of the digital transformation sweeping through the industry. This innovative technology not only represents a shift towards higher efficiency, but also enables more geometric freedom and design flexibility.
Sponsored by QUIKRETE ® Built at Georgia Tech’s Structures Laboratory
Our Story
Our group comprises a diverse team, including an undergraduate, graduate student, PhD candidate, and a Georgia Tech alumnus, along with numerous student collaborators. Over the past year, we have embarked on an exciting journey of research and exploration, delving into the geometric capabilities of Concrete 3D Printing. Starting from scratch at Georgia Tech, we initially had no experience in this field. Through persistent efforts, trial and error, we have acquired the knowledge and skills necessary to harness this cutting-edge technology. With our new knowledge, we have hosted educational workshops for over 20 students in the AEC industry, teaching them through immersion and live demonstrations of the technology.
Quikrete has been a valuable partner in our endeavor, generously providing us with the materials needed for our exploratory research. With these resources, we have crafted a unique design for a sculpture for Georgia Tech’s campus. Our goal is to use this sculpture as a showcase of the future of construction and to highlight the remarkable work being done by students at Georgia Tech.
Scan For Concrete 3D Print Video
Concept Model Clay 3D Print
Geometric Generation
When choosing a geometry, we had to find a balance between pushing the limits and what our printer and mix would allow us to print. We explored several bio-inspired geometries such as the starfish, coral inspired patterns, and more.
Geometry Generation Video
120 Degree Rotation
Process
The geometry was generated using a grasshopper script that took an initial 2D figure and extruded it vertically, twisting and changing its diameter based on a sine graph mapper. The 3m structure is then divided into 4 pieces that will fit within the print bed of the pritner. Each piece is printed as a hollow shell acting as permanent formwork, and then they are filled with light-weight concrete. The pieces are transported to the site, stacked, and tied together permanently by rebar spanning the entire structure. Then the sculpture is finished with a glow-in-the-dark thermochromic color changing paint.
Collection of Prints
Stacking Assemblies
Curing Room
Initiative 99 Competition
Location: Austin, Texas
Interdisciplinary Team: Katy Bradford (Engineering), Tripp Williams (Cost Estimates), Claire McKenna (PhD Sustainability)
Role: Sole Architectural Designer FALL ‘23
Competition Brief
Participants in the competition were tasked with designing affordable homes under a $99,000 budget, covering 3D-printing and finish-out costs. The focus was on creating one or more 3D-printed homes on the same print bed, meeting the specified budget and adhering to IBC Residential requirements in imperial measurements. Designs needed to cater to specific groups, include essential amenities, and allow for scalability. Winners are intended to be printed in Austin, TX using ICON technology, addressing the needs of individuals, couples, or those recovering from homelessness. Efficient layout planning, shared walls, and the potential for multiple homes on a single print bed were additional considerations. The goal was to foster creativity within set constraints for 3D-print-
Our Proposal
In East Austin, our team utilizes ICON’s 3D printing and proposed zoning regulations to transform multi-unit living for flexible families with six distinct print bed layouts. Residents can choose between detached homes or attached units, fostering a vibrant and diverse community. Our signature wave-patterned facades bring visual appeal and cohesiveness, departing from conventional uniformity. Inside, sustainability is prioritized with operable windows for clean indoor air, fossil-fuel-free operations, and open-plan spaces for social gatherings. Private bedrooms feature north-facing clerestory windows and warm wood ceilings, enhancing comfort and housing equity.
Our facades serve both aesthetic and orientation purposes, enhancing the overall ambiance with warm wood roofs against concrete
walls. The cost-effective and sustainable roof design includes shed-style and sawtooth roofs made from recycled timber and metal seam roofing. Mechanical systems ensure efficiency with all-electric heat pumps and an energy recovery ventilator, achieving a remarkable 45% annual energy savings over Energy Star standards.
To promote community interaction, our site layout features a pedestrian-only path accessible from unit backyards. Our innovative approach integrates sustainability, low maintenance, and occupant comfort, positioning us as pioneers in modern, sustainable architecture. As students of architecture, engineering, construction, sustainability, and housing equity, our participation in Initiative 99 is driven by a collective desire to address the challenges of inadequate and unaffordable housing while responding to the climate crisis in the cities we love.
For Concrete 3D Print Video
The main floor plan is replicated across single, duplex, and trilex buildings, with slight variations while maintaining the same square footage. This design capitalizes on the freeform capabilities of 3D printing, incorporating curved walls to introduce distinct patterns that dignify each unit. Additionally, the walls curve out to create nooks, which serve as functional elements such as shelves, planters, and feature walls.
Georgia Tech Digital Fabrication Lab | Research Assistant to Logman Arja
Location: Hinman Research Lab in Atlanta, Georgia
Role: Research Assistant / Farm Manager / Fabricator Spring - Summer ‘23
About the Pavilion
In tackling urban food deserts, hydroponics has historically leaned towards functional but aesthetically lacking plastic structures. Our project takes a transformative step, envisioning hydroponics with a new visual and sustainable perspective by replacing plastic with ceramic through additive manufacturing. This is an immersive pavilion where visitors can freely explore amid the calming sounds of water, surrounded by lush, flavorful plants thriving in ceramic structures.This project serves as a community garden providing fresh, high quality produce for the Georgia Tech community and local Atlantans.
This innovative venture emerged as an extension of my additive manufacturing research within the framework of the 8903 Special Problems course, expertly guided by Professor Logman Arja. By seamlessly blending functionality with visual appeal, our project strives to position hydroponics not just as a solution to urban food challenges but as an integral and captivating aspect of sustainable urban agriculture.
In my role as a research assistant to Logman Arja, I played a crucial role in advancing the project. I took on the responsibility of guiding students through the operation of clay 3D printers in Logman’s absence, serving as a coach to navigate the project’s intricacies. Beyond the classroom, I actively contributed to on-site pavilion assembly. After the course concluded, I assumed daily responsibilities for managing and maintaining the community garden alongside Logman throughout the summer. Furthermore, I led the meticulous deconstruction of the entire pavilion post-growing season, ensuring it was well-prepared for seamless transport to its next exhibition site.
We presented the Research Pavilion to several students and faculty, focusing on its innovative features, especially the vertical growing systems. In my lectures, we explored the step-by-step process of cultivating vegetables within the pavilion and discussed the importance of sustainability in addressing urban food deserts. I highlighted our research, emphasizing the role of clay 3D printing technology for sustainable solutions. The sessions typically concluded with a hands-on experience, collectively harvesting fresh vegetables from the pavilion.
These presentations aimed to connect people to the potential of clay 3D printing and to provide a foundation on sustainable urban farming methods.
Over the summer, in collaboration with my research advisor, I spearheaded a significant initiative harvesting abundant quantities of hydroponically grown vegetables from the pavilion during a period when students were off-campus. These fresh assortments of lettuce were transported in cars to the local food pantry adjacent to Georgia Tech, exemplifying a hands-on approach to addressing urban food deserts and creating a direct impact within the local community.
The harvesting process involved pulling mature plants, removing their roots, and subsequently cleaning and packaging the vegetables. Notably, we also undertook the essential task of replanting the vegetables, with each growth cycle spanning approximately two weeks until reaching maturity.
ARCH 3016 Design Studio
Professor: Logman Arja
Location: Clermont, Georgia
Individual Studio Project Fall 21’
Awarded Best Overall Portfolio in the Studio
The North Georgia Pottery Museum, fondly called “Jugtown,” beautifully blends the historical essence of utilitarian pottery with contemporary artistry. Its architectural brilliance mimics diverse jug forms, integrating seamlessly with the landscape. The museum, emerging like a sculpture from the earth, features jug “necks” transformed into skylights, casting mystical light on curated artworks.
Jugtown pioneers sustainable construction through paste extrusion, converting site soil into a 3D-printed structure. It epitomizes a synergy of history and modernity, where eco-conscious practices and innovative construction coalesce. Beyond a museum, Jugtown is a captivating journey, paying homage to tradition, celebrating creativity, and illuminating a sustainable future. Welcome to Jugtown, where history stirs, and the present thrives.
Major Geographic Regions
Limestone Mountains Region
Piedmont Region
Costal Plain Region
I served as a research assistant to Logman Arja, the 2021 Ventulett NEXT Generation Fellow, for a year and a student in two of his courses the year prior. Our research focuses on raw earth additive manufacturing technologies. In my preliminary form-finding research for Jugtown, I printed various clay geometries.
The images on the bottom left depict my independent research, where I created a sustainable rapid protyping metholody of casting plaster into clay 3D prints. After the plaster sets, the clay is demolded and recycled to make another 3D printed mold.
The images on the right depict pieces of 3D printed pottery I made made as gifts.
Construction Process
This collection of physical models embodies innovation in clay additive manufacturing. These models explore intricate patterns and design possibilities, revealing the captivating interplay of light and dynamic effects through clay-based 3D printing. Each model represents a commitment to pushing boundaries, fusing technology with artistry, and unleashing
limitless potential. This exhibition highlights the transformative possibilities of clay additive manufacturing, igniting curiosity and celebrating the creative power materialized in clay.
In these illustrations, the convergence of jug-inspired architectural forms within an organically orchestrated arrangement unfolds. The intricate dance of these interconnected jugs takes center stage, weaving together to craft a mesmerizing architectural tapestry that captures the imagination. Moreover, the deliberate positioning of these vessels along the meandering waterways interlaces an enchanting sense of fluidity, bestowing upon the overall composition a playful charm and a testament to the ever-evolving dialogue between form and environment.
Floor Plan
The sections and floor plan unveil the building’s natural and harmonious design, where collaborating jug structures give rise to unique voids. These voids, each with its own character, breathe life into the spaces, echoing the diversity found in pottery and nature. By embedding the jug-inspired forms within the landscape, homage is paid to the earth’s roots in pottery and construction, forging a profound connection with the land. This design celebrates the fusion of art, architecture, and the primordial earth, connecting form, function, and origins.
ARCH 4833 Manufacturing Tech Applications
Professor: Logman Arja
Individual Research Project Spring 22’
The aim of this research is to delve into the potential of employing 3D printed clay formwork for casting purposes. Leveraging Potterbot technology, the objective is to devise a prototyping process that surpasses current widely adopted methods. This approach entails utilizing the same material to fabricate multiple molds, thereby streamlining the traditional casting with plaster procedure. Moreover, it facilitates the creation of molds that would be challenging to produce manually. The process boasts a quicker pace compared to clay 3D printing, courtesy of the rapid drying nature of plaster. Notably, it accommodates the generation of both positive and negative molds. Once the desired part is achieved, it becomes feasible to craft a reusable negative mold from plaster, offering a sustainable and efficient solution.
Formations Studio | Intern
Location: Atlanta, Georgia
“Born as the beautiful mighty daughter of mythological Greek sea gods, Medusa was cursed to become a terrifying snake-haired monster who would turn those who gazed at her into stone. As such, The Medusa Myth embodies both the omnipotent promise and humanity-ending threats ascribed to AI and robotics.
Unlike the mythological Medusa who continued to bestow death and destruction even after her own demise, the AI driven robotic medusai aims to instill movement, music and life in those who engage with her. While preserving the original alarming presence of the Greek Gorgon, medusai aims to bring forward the potential for transformational positive effect of AI and robotics on human expression and creativity.
Using computer vision, machine listening, and generative and interactive robotic behavior, medusai responds to human movement and sound through robotic dance and music, aiming to surprise and inspire her mortal collaborators.”
- Georgia Tech Center for Music Technology
My Involvement
In my internship at Formations Studio, I played a crucial role as a metal fabricator for MedusA.I.’s body. Using Rhino modeling, I generated cut files for the water jet and plasma cutter, shaping 10-gauge steel triangles. The assembly involved tack welding, integrating interior structural ribbing, segmenting the structure into five components, and fully welding the seams. The refinement stage included closing seams and sanding edges, for a clean finish.
Showcase | 09/12/23
The photo above shows the sculpture making its debut at Lux Stage within Trilith Studios, renowned as one of the world’s most advanced interactive virtual production facilities. Lux Stage features a fully enclosed virtual production volume housed in an 18,000 sqft purpose-built sound stage.
4016 Origami Studio Daniel Baerlecken
Location: Atlanta, Georgia
Individual Studio Project Summer ‘22
This mobile architectural marvel, aptly named “The Traveling Fun Palace,” showcases the seamless fusion of origami and pneumatic architecture. It stands as a dynamic public space ready to adapt to a diverse range of cultural events. With an expansive 6,350-square-foot footprint, the palace can host concerts, performances, art exhibitions, and weddings, promising comfort for up to 250 guests.
At the heart of this project is a technological dance, where parametric design principles, harnessed through Grasshopper and Rhino 7, give rise to an origami-inspired structure based on the auxetic triangle pattern. Inflated, this structure offers a flexible space, yet, remarkably, it can be effortlessly deflated for compact storage and transportation. The entire palace, including its ingenious origami flooring, neatly fits within just three shipping containers. These containers serve as more than transportation vessels; they ingeniously transform into storage spaces, artist studios, and even a customer bar upon assembly.
When night falls, this architectural wonder becomes a mesmerizing spectacle, gracing any cities skyline with a captivating light show. Its allure extends an open invitation to passersby, enticing them to immerse themselves in a world of cutting-edge technology and innovative design — a true marvel of the architectural realm.
The pavilion unfolds as a vibrant hub, ready to host a spectrum of events, from concerts to weddings, thanks to its open and adaptable layout. Imagine all the event essentials neatly tucked away in one shipping container, while another moonlights as a private changing room and office. A third container metamorphoses into a lively open bar and snack booth, injecting a playful spirit for the guests.
The pneumatic pavilion steals the spotlight with its mesmerizing tessellated origami pattern. Crafted from dichromatic material, it’s not just a structure; it’s a captivating spectacle seemingly defying gravity, producing dynamic spectrum effects as it playfully interacts with light throughout the day.
Master’s Thesis Project
Location: West Architecture Building, Georgia Tech
Project Advisor: Daniel Baerlecken
Thesis Lead: Daniel Hsu
Role: Fabricator
FALL ‘22
About the Bookshelf
The Lending Library was being designed for Georgia Tech’s Campus. The concept of the project is creating a sculptural bookself which functions in a nontraditional way. The project is meant to peak student curiosity and it acts as a sharing library where students take a book and leave a book. The 8-foot tall sculpture is inspired by the shape of stelagtites and is meant to represent their unique formation. The mass is created by aggregating several different cells or puzzle pieces together. Pockets for the books were designed with intetnion so that certain books of certain sizes are dispersed throughout the sculpture. The project is a part of Daniel Hsu’s graduate thesis project, where he led the design.
Hsu and I fabricated the prototype together. I served as the fabrication expert, overseeing all machine operation and concentrating on bringing the project to fruition. The images on this spread showcase the prototype design for a sculptural bookshelf concept.
The project was built with twelve sheets of 1/2” plywood via CNC fabrication processes. I took the model that Daniel designed and prepared the 2D drawings for machining. I then operated the CNC machine to make and label all of the custom pieces Next, Hsu and I sanded the pieces and assembled the sculpture together. For structural integrity small wood rectangles were inserted into inner unocupied pockets of the bookshelf to allow load transfer in the x,y and z directions.
Formations Studio | Intern
Location: Georgia Tech, Atlanta, Georgia
Role: Fabricator
Summer ‘23
This installation, commissioned for Georgia Tech’s College of Design and prominently situated in front of the East Architecture Building, stands as a vibrant and captivating welcome for both current and prospective students. Crafted from polycarbonate and laminated with dichromatic film, the sign seamlessly transforms ordinary light into a dynamic spectrum of colors, casting an intriguing play of reflections and projections.
Conceived with the intention of serving its primary function upon initial observation, the sign transcends mere practicality to beckon a closer inspection. Comprising six distinct assemblies, meticulously arranged to spell out the word ‘DESIGN’ both forward and backward, the structure weaves an enigmatic tapestry. Its ethereal silhouette, reminiscent of a ghostly apparition, emerges as one gazes through its layers, inviting viewers to delve into a detailed exploration.
This installation is not merely a marker; it is an interactive piece that encourages contemplation and reflection, embodying the essence of the College of Design’s innovative spirit.
While the sign was designed by others at Formations, I played a pivotal role in the off-site fabrication, learning to work with new materials and mediums. This involved contributing to the robotic milling process for the letters, meticulously sanding and finishing the edges of the polycarbonate. Additionally, I participated in the lamination of the letters with dichromatic film and the assembly of the components using hardware.
ARCH 2017 Design Studio
Professor: Michille Rinehart
Location: Sweetwater Creek State Park, Georgia
Individual Studio Project Spring 21’
Nominated for Best Overall Project
This project aims to reconnect individuals with themselves and nature through architecture, drawing inspiration from traditional Chinese courtyard housing. Like the Beijing courtyard style, it seeks harmony between sky, earth, and human, creating hierarchical spaces that frame views of the natural elements. Utilizing materials like iron, wood, brick, and stone from the surroundings, the building integrates seamlessly with its environment. Positioned amidst the ruins of the New Manchester Manufacturing Mill, the wellness retreat embraces the natural landscape, with its design influenced by the site’s context. Divided into three main nodes aligned with the latitudinal and perpendicular axes, the retreat features central courtyards that facilitate circulation and offer uninterrupted views of the surrounding landscape.
As you round the corner of the ruins, an unexpected view of the creek appears drawing you into the main courtyard. Similar to a Chinese courtyard, you slip past the precedent wall and a floating glass box experiencing a dramatic contraction and expansion of space.
The courtyard creates an instantaneous connection between the human, sky, water, and Earth and removes you from the outside world. Once again as you round the corner you earn a glimpse of the exterior experiential pool, making you wonder how to get there.
ARCH 2017 Design Studio
Professor: Michille Rinehart
Location: Sweetwater Creek State Park, Georgia
Design Partner: Lauren Miraldi
Role: Designer Spring 21’
In these two exercises, participants were asked to explore how architecture can shape the user experience. In B1, the site was in Nebraska, the windiest state in the United States, consisting of rolling plains and prairie grass. The task was to carve an ordered path into the earth, leading to a simple tectonic element for shelter. The concept chosen was “wind as architecture” to leverage the location’s characteristics. The tectonic element, a fluted piece of aluminum, not only shielded from strong winds but also served as a wind funnel, casting musical notes across the field to beckon people to the path. The form itself was inspired by a paper airplane, appearing so light that the wind could effortlessly carry it away.
Project B2 focused on creating a habitable wall or wedge. Unlike B1, the site was much steeper and presented its own challenges. The task involved carving a wall into the landscape, at least a hundred feet in length, and creating a habitable space along the path. Drawing inspiration from the Vietnam Memorial in DC, the design followed the contours of the land. The concept was for the wall to obscure the view of the overlook but act as a guide toward it. The depth of the wall increased as one approached the view, and upon rounding the corner, it framed the landscape. From that point, visitors could choose to stay and enjoy the view or continue along the path.
ARCH 2017 Design Studio
Professor: Michille Rinehart
Location: Sweetwater Creek State Park, Georgia
Design Partner: Joseph L’Heureaux
Role: Designer Fall 20’
This semester–long project was a combined effort with my partner Joseph LHeureaux. The order in which we worked was reversed from a traditional studio, where we first researched Celtic Knot-work and then developed a mechanized system which formed our building. We took our knowledge from our research and used figures to create two different cells. Inspired by Conway’s Game of Life, we created a mechanized rule based system where cells either died and reconfigured or lived based on their spatial organization. While Celtic Knot-work is normally considered ornamentation, this system allowed ornament to become solely the structure of the building. After we received the program, we decided on creating a space for inventors and creators to collaborate with other like–minded people to work and produce projects. In the heart of Chicago surrounded by a college atmosphere, the average person does not have access to machines such as 3d printers and laser cutters. This studio provides a place to turn digital drawings into reality.
Precedent Study 1
1
In this phase we analyzed several pages of the Lindisfarne Gospels to grasp how Celtic Knotwork was constructed. We deconstructed each knot to centerlines and then to figures which is the simplest form. From our research, we were inspired by how this ornament holds a block like structure to the eye, while it is made out of curves.
Precedent Study 2
Study 2
We then took another approach to understand how the knot-work changes and still remains one continuous line or system. We found that the knot-work adapts based on its spatial organization.
After getting a firm grasp on Celtic Knots we created our own from figures we studied. We then treated the configurations as cells and mapped them across sheets to create a structured system.
We took our sheets and started bending them to create a variety of spatial conditions. We turned the inner sheets on an angle to allow more light into the space based off our sun study. Then the cellular rules were applied to the sheets. The cells die and reconfigure based on if the system can support them.
The line-work was thickened and ornament became structure. Thickening varies based on spatial organization of the cells. We then used the system and added floors according to the program.
A
Based on the cellular system, cells die, reconfigure, and create phenomenal qualities such as openings that form the circulation throughout the building. The curvilinear on the interior have their own set of rules to allow for these phenomenal experiences such as the bridges through the atrium. Being
one continuous system. The curves flow throughout the building and drive your eyes up and around to new spaces.
The Chicago snowy night render depicts the front facade which compliments the adjacent buildings. This facade is more open to allow light in from the South and fill the atrium which transforms the entire building. On the side facade light escapes the cellsadding to the phenomenal experience.
ARCH 1855 Design Studio
Professor: Danielle Willkens
Location: Mechanicsville, Atlanta, Georgia
Individual Studio Project Spring 20’
This was an urban infill project located in Atlanta. The site is within an old factory and warehouse community that is slowly growing and being repurposed. The red buildings in the diagram depict the older red–brick buildings surrounding the site. We had to design a work/ live/ display space for two artists. This is the gallery workspace where people can view the muralist painting in the studios down below. A skylight casts light down to fill the space as if the sun was parting clouds. The glass-brick wall is the front of the building and allows northern light to fill the tightly packed urban space.
Parti Diagrams
The parti diagrams show the longitudinal system extending along the entire site. Due to the clients’ needs and the urban environment, the front and back facade, and the roof are the key access points for natural light which shaped the design of the project.
We were also given the opportunity to integrate an additional 10,000 square foot massing for a project that would also occupy the site. The decision was made to make the buildings work together as one by being similar in design and having shared circulation.
The plans show the shared circulation core between the massing and the proposal. The artist’s studio is imagined to be the part of the gallery itself. The audience is immersed into the environment so they can truly understand the work. The sections show the openness of the gallery space and the separation of public
and private space. The Renzo Piano inspired skylight system passes light into the triple height atrium that gives the building a sense of openness and feeling airy.
The buildings contextually fits within the area while making a statement of its own. The front facade holds the street line and some of the materiality characteristics of its adjacent such as red–brick, but features glass-brick which fades from the red–brick. It responds to the precedent facade on the South side of the
site with geometry and the apertures allowing essential light into the gallery and for the public to see inside.
ARCH 1855 Design Studio
Professor: Danielle Willkens
Location: Earth
Individual Studio Project Spring 20’
This project revisited a precedent where a spatially organized ‘cube’ was transformed through several different iterations to create a better understanding of formal and spatial systems of organization. This project focused the idea of using simple transformations to create a form that would become a pavilion. The driving concept derived from the transformations was ascension through an interlocking tubular system. The angels of the chamfer drive your eyes towards the top of the pavilion. Once inside you are drawn to climb up the ramps through the tubular system and travel to the light at the end of the tunnel. Even though a specific site was not provided for this project, one would imagine that at each end of the tube compelling views would be framed which would increase the experience. While this pavilion shields from the elements, it intentionally becomes a wind tunnel adding to the effect of movement and becoming a cooling space for anyone who enters.
The Precedent Cube
Cube Transformations
The driving concept derived from the transformations was ascension through an interlocking tubular system. The chamfer tool, scale tool, and make hole tool were used to create the general form and then other tools were used to create circulation through the system.
System
The systems diagram shows the concept of long tubular forms. The tubes protect from the elements while also controlling the views linearly. The Circulation shows how people approach the pavilion and have an experience of walking up a long and wrapping linear system. The nodes lie at the end of each tube or tunnel.
ARCH 1855 Design Studio
Professor: Danielle Willkens
Precedent Painting: The Annunciation
Individual Studio Project Spring 20’
The Annunciation was painted by Fra Angelico in 1426. I analyzed the painting and determined that it is organized into a three panel system. The progression is from left to right from unsavageable, to a word of good news, to the savior. I interpreted that the painting is a window through time that shows the reason for Christ and I then finished the story by adding baby Jesus.
After carefully studying the painting I translated the 2D work into a 3D form that both represents and extends the featured perspective, questioning the arrangement of the spatial layers and what is beyond the frame of the image. The display was made by cutting acrylic and wood. The spacing between layers was intentional as were the height of the pieces of acrylic. From eye level the pieces are on a slight incline to create the impression that as you walk up the stairs you are entering the painting. This was because Fra Angelico’s intentions for the painting were to be looked at as you ascend up stairs.
ARCH 1855 Design Studio
Professor: Danielle Willkens
Precedent Painting: The Annunciation
Individual Studio Project Spring 20’
This project ties to the previous one because we were required to place the painting within a precedent building in an intentional place after analyzing it. Maison de Verre literally translates to “Glass Box” which is represented in the parti diagram. This system allows for natural light to fill the space while eliminating the undesired view of adjacent buildings. This building was famous for the way public and private space interacted with one another.
The perspective features the painting, The Annunciation, by Fra Angelico which was placed on the existing structure of the building. The painting’s location allows one to view it as they ascend up the stairs as intended by the artist. Light comes in behind the heavenly painting and creates an aura effect. .
ARCH 1854 Design Studio
Professor: Harris Dimitropoulos
Location: J.S. Coon Building, Georgia Tech, Atlanta, Georgia
Individual Studio Project
This project was to design a study carrel for one to three people to study on Georgia Tech’s Campus. The site assigned was the facade of the J.S. Coon building, one of Georgia Tech’s oldest academic buildings. Requirements for the project detailed the space had to be raised off the ground while still being ADA accessible. The proposed study carrel connects a small bridge to the second floor of the building which leads to a nearby elevator. The concept was to use the prexisting trees as the main structure. The carrel focues on providing a view that escapes the city and immerses people into the natural environment.
The location of the carrel on the site was chosen because there is a corner of the Coon building that nests the carrel. Using the site to its potential while being sustainable led to the development of a tree house structure.
Directional Views
As one studies, there is a view showing repeating trees as they fade away in the distance. The view prevents distraction from pedestrian traffic which creates a peaceful place to study and escape the rest of the world. The view also faces North which is best for studying.
Accessibility
The carrel is easily accessible from the spiral staircase along the sidewalk. There is also ADA acessibility through the J.S. Coon Building.
ARCH 1854 Design Studio
Professor: Harris Dimitropoulos
Location: Atlanta, Georgia
Individual Studio Project Fall 19’
A cozy, single-person space was designed without complex mechanics, resembling a tiny house with a compact 1,700 cubic feet footprint. It features areas for studying, eating, and sleeping. Large windows and clerestories from the North provide ample natural light, while overhangs on the South side mitigate harsh sunlight. The sleeping area is lofted to optimize space, and the design prioritizes bringing the outdoors in. The South-facing wall can be opened to create a shaded porch, allowing the occupant to study in natural surroundings. The repeated orthogonal windows create intriguing interior shadows, enhancing the space’s ambiance for various activities.
tree house
ARCH 1060
Professor: Vernelle Noel & Ryan Roark
Location: Georgia Tech, Atlanta, Georgia
Individual Project Fall 19’
This semester, we were required to choose and analyze something from our surrounding environment and derive a concept from it. The Kessler Campanile, located at Georgia Tech, is a tall, futuristic obelisk constructed of stacked metal plates twisted in a corkscrew fashion. The conceptual idea was twisting a rectangular object to create a unique appeal and transform a design. When looking at the spire, it represents a symbol of power and nobility. The Campanile is inspiring because it reaches into the sky, glorifying the mindset that the sky is the limit at Georgia Tech. The model is constructed of rectangle pieces that interlock to form a complex and stable structure; it was designed so that it can be flipped to express the concept in multiple ways. The simple geometric shapes come together to make a complex form. The squares twist up and create the illusion of infinity.
ARCH 1854 Design Studio
Professor: Harris Dimitropoulos
Location: Georgia Tech, Atlanta, Georgia
Individual Studio Project
This project was to hand-craft three different maps of your hometown all at different scales. Being our first project at the school, the objective of this project was really too work on developing craft skills. Georgia Tech is my home for this project and the maps were created (1”=3,000’, 1”=300’, 1”=30’) by analyzing Google Earth and cutting paper accordingly. This project became really interesting because it make you analyze your home in three different scales and lead to discovering things I hadn’t really noticed before. The map of Atlanta does not appear as it would traditionally on Google Earth key, this shows the densest urban areas black, less dense areas in gray and major roads in white. The Georgia Tech campus map has several locations that are dark gray representing special features; for example, Bobby Dodd stadium and Tech green are places for mass gatherings on campus so that is why they earned this color. Lastly, the Glenn and Tower’s dormitories were both previous residencies of mine and in this map I showed how they surround the Quad or courtyard where students hang out and enjoy time outside.
ARCH 1854 Design Studio
Professor: Harris Dimitropoulos
Location: NA
Individual Studio Project Fall 19’
In this project the stipulations were that you had several different sized cubes and had to fit them all together to create a unique form within a 10”x10”x10” cube. This project was a major test of our craft skills and really challenged me to make seamless models. Each of the required cubes could be incorporated into the form by the addition or subtraction of space. The first form had to be arranged orthogonally. I focused on the experience created within space. Light floods down from a small skylight filling a tight and compact dark space with warmth and the feeling of openness. This form was designed to emulate the experience of a cave. The second iteration allowed rotations; I chose to make every cube additive to create a massive and imposing form. This iteration tested the limits through complex rotated additions. The final form was designed to emulate a large building structure.
ARCH 2211 Construction Tech
Professor: Charles Rudolph
Location: Georgia Tech, Atlanta, Georgia
Role: Individual Project Fall ‘20
Selected as a Top 3 Project
We had to design a bus stop for Georgia Tech and the site is situated between the CULC and the architecture buildings. The hexagonal system was first conceptualized when trying to figure out how to relate architecture to Georgia Tech to create a more personal experience. The hexagons come out of the ground from where they are nested and then arc to create a canopy. The structure of the bus stop is exposed to create a contrast between both sides. The smooth back draws people with light and then the underside creates interest for the eyes through repetition. The cracks between the structure coupled with the use of translucent glass creates a phenomenal experience that gives the sense of warmth. Light seeps out of the bus stop to create the stripes of the Yellow Jacket.
ARCH 1020 Media & Modeling 1
Professor: James Park
Location: Takahashi, Japan
Partners: Linna Xia & Khin Mahar
3D Modeling and Rendering Spring 20’
This project was precedent study of Tadao Ando’s Nariwa Museum of Art in Takahashi, Japan. We reconstructed this building in Rhino by following Ando’s plans. In this project we improved our modeling skills and learned how Ando uses angles to create an experience in harmony with nature.
Concept
The diagram shows a geometrical analysis intended for further understand the building. The intentionality by Ando with the difference in ceiling height space can also be seen in the section.
Inside the Museum
The rendered interior view features the atrium hallway space, often also used as an exhibition hall, and one of Ando’s unique angled concrete stair cases.
ARCH 2020 Media & Modeling 2
Professor: Daniel Baerlecken
Location: Shanghai, China
Individual Project Summer 20’
Sited adjacent to Jin Mao Tower and Shanghai World Financial Center, Shanghai Tower rises at 632 meters ranking as China’s tallest building. With over 575,000 square meters of building space and an impressive 128 floors Shanghai Tower is the skyline’s most prominent icon. As the glass tower rises it twists and tapers conveying a feeling of movement and growth. The spiraling cut into the building makes the building aerodynamic. Geometrically, Shanghai Tower is slim and is based off of a reuleaux triangle helping it withstand the typhoon–force winds subject to the area. Designed to simulate and embrace the life of the city, the tower includes office spaces, a luxury hotel, sky gardens, restaurants, and living spaces. The skyscraper comprises nine cylindrical buildings stacked on top of one another. The central core of the building is surrounded by a double–skinned curtain wall facade that serves as a thermal buffer zone to minimize heat. The tower has been awarded a China Green Building Three Star rating and a LEED® Platinum Certification.
Structural Core
2D Parti: Roation & Scaling 120°
Parti Variations: Rotation
2D Parti Variations: Scaling
-.005 Scaling 120 ° Rotation
Number of Floors = 120 Floor to Floor Height: 5m
Structural Columns
Structural Core Detail
Core
Floors
PUBLISHED ARTICLE ABOUT JARED