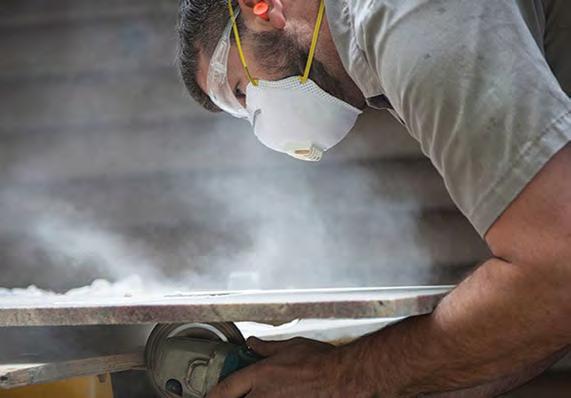
4 minute read
Prioritize Safety, Minimize Risk
By Austin Maxwell, ISFA President
In the world of countertop fabrication and installation, one primary concern is the presence of respirable crystalline silica (RCS). RCS is a common component in engineered and natural stone, and when inhaled, it can lead to serious health issues such as silicosis, lung cancer and other respiratory diseases. It’s crucial for countertop companies to implement safety measures to reduce RCS exposure in their workplaces.
Advertisement
Here are some ways countertop fabrication and installation companies can reduce RCS exposure and promote a safer workplace.
Use wet cutting methods. One of the best ways to reduce RCS exposure is to use wet cutting methods. Using wet cutting methods, fabricators can significantly reduce the amount of RCS exposure. Keep in mind cutting wet doesn’t necessarily mean your shop will be below the action level from Occupational Safety and Health Administration (OSHA). Wet cutting is just one of the tools in the toolbox for reducing RCS levels in your shop.
Implement proper ventilation. Another strategy for reducing RCS exposure is to implement adequate ventilation in the workplace. This can be achieved using dust collectors and air filtration systems, which capture and remove airborne particles.
Implement regular cleaning procedures. Regardless of your shop setup, keeping up with your housekeeping duties is imperative. Make sure the floors are constantly wet to ensure the slurry doesn’t dry and turn into dust that will become respirable. Use a floor scrubber with a vacuum to keep your floors clean. Regularly wipe down everything in your shop that accumulates silica dust. If you recycle your water, don’t use gray water to spray down the floors each day.
Use personal protective equipment (PPE). PPE is another essential tool for reducing RCS exposure if you can’t use wet cutting methods or aren’t able to get air quality levels in your shop below the OSHA thresholds. Properly fitting respirators can effectively reduce RCS exposure during cutting and grinding.
Use new machinery and tools. Advances in machinery and tools have made it easier than ever to measure and reduce RCS exposure. Most manufacturers now offer source capture cutting solutions that contain dust before it becomes airborne. For example, Trolex created the Air XS real time silica dust monitoring system that makes it easier than ever to measure, in real time, the RCS level in your shop.
Promote materials with less silica content. There are so many advances happening in surfaces today that give fabricators and their customers a lot of choices when it comes to materials. Cosentino’s Silestone line has been reinvented with HybriQ Technology, drastically reducing the amount of crystalline silica in its composition. Consider using alternative materials such as porcelain, sintered stone or solid surface.
Train workers on safety best practices. Making safety a priority in your shop is a must, and your safety program must include RCS mitigation practices. Include information on the proper use of equipment and tools and the safe handling and disposal of materials. Training should be ongoing and repeated frequently to keep it top of mind, and it should be updated regularly as new equipment, tools and improved fabrication techniques are developed. Be thinking about ways to reduce the amount of slurry created, such as using a sawjet to perform sink cutouts rather than a CNC router with a finger bit. A finger bit on a router removes more material than a blade or jet on a sawjet and, therefore, can increase the amount of RCS in your shop. Make safety documentation and resources readily available to everyone in your shop. Take advantage of Caesarstone’s Master of Stone online program to learn more about silica safety measures.
Test your air quality. Ensure the air quality in your shop is safe for your employees by testing at least annually. If you implement new machinery or change fabrication techniques, be sure to test after you’re up and running to verify your air quality levels are not negatively impacted by the change.
While machinery and material manufacturers continue to develop products and processes that minimize silica risk, it’s imperative that you take all the necessary actions to provide a safe and healthy work environment for your employees.