
6 minute read
Do You Schedule Your Maintenance Time or Does Your Machinery Do It for You?
By Ed Young, Fabricator’s Business Coach
The stone industry has come a long way in the use of technology since I worked with my first fabrication shop client over 20 years ago. Almost every shop I visit today has some or all of the following:
Advertisement
• CNC saws.
• Water jet cutting.
• Digital templating.
• Robotic sawjets.
Unfortunately, the most common form of maintenance I see for this expensive equipment is a break-fix approach — we fix it after it breaks. This creates a heavy reliance on the machine manufacturer to supply parts quickly. It also creates unnecessary and costly schedule interruptions for the fabricator.
A few shops do a decent job of preventive maintenance. This includes:
• Greasing a fitting.
• Changing lubricant.
• Changing filters.
Some fabricators even knock the dust and dirt off their machines from time to time. To run a fab shop effectively, a more robust approach to maintaining machinery is needed.
To get the most out of a machine you have invested hundreds of thousands of dollars in, you need to consider a Total Productive Maintenance (TPM) approach.
TPM is a process that maximizes the productivity of equipment for its entire life cycle and will extend the life of the equipment. Through the participation of all employees, TPM creates an environment that encourages improvement efforts in safety, quality, cost, delivery and creativity.
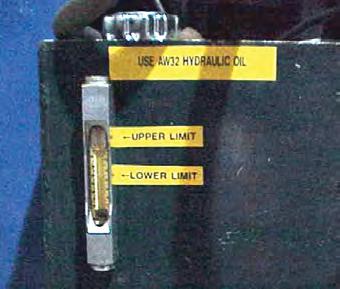
Sight glasses and tanks should show minimum and maximum levels.
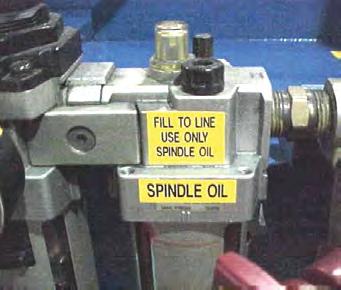
All fill points should be marked with the proper fluid used.
Daily Operator AM Checklist
o 1. Check coolant level through clear Plexiglas
o 2. Check heat exchanger fans (strings should be moving)
o 3. Check servo drive fans (string should be moving)
o 4. Check heat exchanger air filter (change when dark)
o 5. Check servo drive air filter (change when dark)
o 6. Check way lube reservoir (add when low)
o 7. Check main motor air filter (change when dark)
o 8. Check main motor cooling fan (string should move)
o 9. Check mist collector motor and air filter (change when dark)
o 10. Check bar feeder hydraulic motor air filter
o 11. Check bar feeder hydraulic oil level (add when low)

Figure 1 Place corresponding labels on a machine so any operator can easily follow the daily checklist.
If you don’t schedule time to maintain your equipment, your equipment will do it for you. If you don’t want surprise maintenance stoppages that always occur during a critical job, then you need to plan your maintenance.
TPM is the combination of the three types of planned maintenance:
1. Preventive maintenance
Preventive maintenance is intervalbased maintenance. It consists of periodically inspecting, servicing and cleaning equipment, and replacing parts to prevent sudden failure and process problems. This includes changing the oil every 500 hours of run time, applying grease to a fitting every week, and replacing the bearings every 3000 hours. This is the most common type of planned maintenance.
2. Predictive maintenance
Predictive maintenance includes inspecting and diagnosing equipment components to determine the service life of those components. The intent is to maximize the life of the components and to replace them before that life is exceeded.
Predictive maintenance includes activities like regular:
• Chemical analysis of lubricating fluids to determine if critical components are wearing appropriately.
• Vibration analysis of shafts and bearings to assess condition.
• Infrared temperature evaluation of mechanical and electrical components.
• Nondestructive testing of stressed components.
3. Corrective maintenance
Corrective maintenance includes improving various aspects of equipment and components so that maintenance and repairs can be carried out quickly and reliably. This frequently includes modifying access to components to improve visual evaluation, labeling wear items so the correct replacement part is used and marking the proper operating range on gauges.
TPM also integrates the operator in Autonomous Maintenance (AM). In AM, the machine operator performs daily activities to aid in detecting and correcting abnormalities to prevent reduced machine performance. This includes visual inspection, routine cleaning, lubrication and data collection. The most effective AM programs have detailed documentation allowing any operator to complete the daily activities. (See examples in Figure 1.)
To gauge the effectiveness of the above activities, TPM uses a metric called Overall Equipment Effectiveness (OEE). OEE assesses the availability of the equipment, the performance efficiency of the equipment and the rate of quality output. (See Figure 2.)
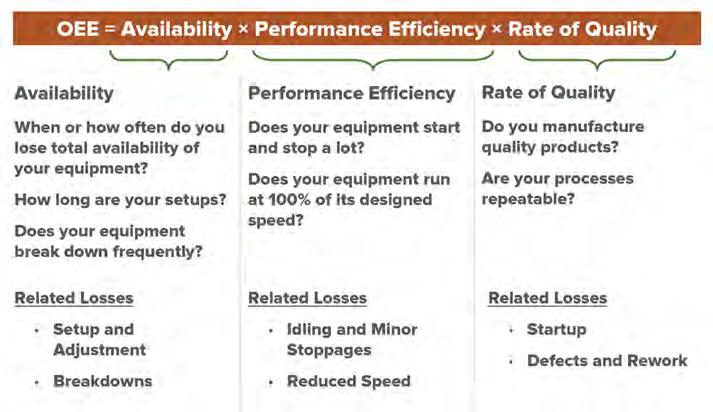
Figure 2 OEE assesses the availability and performance efficiency of the equipment and the rate of quality output.
There are several key steps to effectively implementing TPM.
1. Initial cleanup. Clean the machine until it looks like it did the day it arrived from the manufacturer. Cleaning helps you see any obvious areas of lubricant leaks, and since you have to physically touch every area of the machine, you will quickly identify any issues with loose electrical connections, compressed air leaks, broken latches, etc.
2. Assess the condition of the machine. Address the obvious items identified above. Also, assess whether the machine can perform to the original manufacturer speeds and process rates. Repair or replace any component that is needed to meet those original specs. This gives you a solid baseline from which to operate.
3. Standardize your maintenance procedures. Establish how you will label part numbers for consumables like filters and belts. Determine what corrective maintenance methods you will use. Document these items and train everyone on them.
4. Implement AM. Develop the daily routines required of machine operators and make these activities easy to perform correctly. Implement documentation for recording these activities and any anomalies found. Audit frequently.
As a shop owner, you have invested hundreds of thousands of dollars in the critical equipment needed to run your business. To ensure your business can consistently produce the quality products your customers expect and to meet your schedule commitments, you need to manage the condition of your equipment. If you don’t plan your downtime, your machines will do it for you. Your machinery needs to be kept in like-new condition so that it will operate at the speeds it was designed for. You need the consistent quality your equipment is designed to deliver. TPM is the best approach to ensuring your equipment supports your business goals.
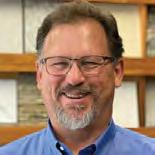
Ed Young is the owner of Fabricator’s Business Coach, a consulting firm designed to strengthen and elevate fabrication shops of all sizes. A former shop manager, Ed fully understands the challenges of today’s professionals. He has consulted with a range of businesses, from one-person startups to international Fortune 100 corporations, covering a broad array of products and processes. As a result, Ed knows that each business needs an appropriate structure for its unique situation. To learn more about how Fabricator’s Business Coach can take your shop to the next level, visit www. fabricatorscoach.com or reach Ed directly at Ed@fabricatorscoach.com.