
13 minute read
Sustainability Matters: Turning Over a New LEEF
By Max Le Pera & Jessica McNaughton
As we delve even deeper into holistic sustainability and how ISFA can help drive beneficial lasting change to the industry, we need to focus on alignment and continuity in the enterprise chain. This chain refers to stakeholders in the transactional field — primarily manufacturers, distributors and fabricators — for this discussion.
Advertisement
To this end, ISFA is looking at many ways to create a superhighway that aligns manufacturing with fabrication so that the sustainability story that begins with environmentally friendly, responsible factories and products do not end at the time of material dispatch from warehouses. Linking eco-vested fabricators to like-minded products and manufacturers will encourage the continuity of the sustainable story while driving a more significant and ultimately more responsible impact on the industry and the environment.
We see a growing number of data points for sustainable initiatives today, indicative of momentum. These include products, manufacturing environments and more. Companies can operate and report on their commitment to the environment, align with the growing demand for sustainable projects, and differentiate with a humanitarian flair. All good reasons, and yet their story and greater sustainable value proposition are not necessarily transferred from enterprise to installation. While it is not their responsibility to ensure such, manufacturers can play a vital role in helping to create alignment. Consistent with their stated missions, they should also want an aligned hand-off of their green efforts to a fabricator that will further support environmental and holistic stewardship.
So how can ISFA help design and encourage such an integrated alignment model? Well, a precedent has been set that we can follow. Much as architects and project owners seek to optimize their Leadership in Environmental and Energy Design (LEED) points, fabricators can and should do their part to support, complement and continue this leadership paradigm through a proposed ISFA designation: Leadership in Environmental & Energy Fabrication (LEEF) certification. Essentially LEEF certification will have ways for fabricators to earn LEEF points. The more points earned, the higher the designation on the LEEF tiered certification scale.
The 35,000-foot view here creates a formal way to acknowledge and incentivize investments in sustainable operations by a fabricator while facilitating the all-important continuum we are seeking. Whereas to date, sustainable investment in a fabrication business tends to stem solely from the personal beliefs and values of the company’s leadership, now we are looking to establish some potential financial incentives for fabricators to pursue eco-stewardship.
Theoretically, a LEEF fabricator could be a primary goto for a manufacturer with eco-friendly products and where environmental stewardship is a core value. This alignment helps to deliver an integrated solution to the architect or project owner while optimizing the care and concern component on environmental impact from cradle to bed (from manufacturing to installation).
To begin the evaluation process, we contacted a handful of companies more reasonably known for their penchant for sustainability. We asked their thoughts on their commitment to sustainability and how they might value and support a LEEF initiative.
Countertops & Architectural Surfaces polled DuPont (Corian Design), Lapitec and Cosentino for their thoughts.
CTAS: Tell us your sustainability story. What efforts in processes and products is your company making toward sustainable materials and manufacturing?
Corian Design: We take a three-pronged approach in our commitment to sustainability:
• Enabling a circular economy.
• Promoting transparency.
• Minimizing our environmental impact.

Corian Solid Surface Peppered Terrazzo
Enabling Circularity
Select Corian Solid Surface colors contain at least 6% and as much as 13% recycled material and are certified by Scientific Certification Systems (SCS) for stated recycled content.
Promoting Transparency
Corian Design materials are NSF 51 certified, UL certified as mold resistant, and do not contain bisphenol A (BPA) — all certifications that align with the American Institute of Architects (AIA) Materials Pledge. Corian Design materials have also received important independent certifications for environmental performance, including GREENGUARD Gold, National Green Building Standard (NGBS) Green Certified, and Living Building Challenge (LBC) Red List Free.
Reducing Environmental Impact
Corian Design is committed to using innovation expertise to reduce the environmental impact of its products and operations. Here are some of the ways we do this:
• Suppliers and raw materials are chosen responsibly, using pigments free of heavy metals and toxins.
• Pre-consumer waste in manufacturing has been reduced and recycled into new products, eliminating it from landfills since 2011.
• The process water used at our Corian Quartz facility is recycled.
• 100% of the electricity used to make our products in our North American facilities comes from renewable energy sources.
• Corian Design products have Product-Specific Type III Environmental Product Declarations (EPDs), providing the most credible, independently verified information about the
life cycle environmental impact of each, and Health Product Declarations (HPDs) that give information on human and environmental health.
• In a drive toward zero sample waste, we’ve updated our sample program to help keep materials out of landfills by facilitating the return of unused samples for recycling.
• We’ve also introduced the Corian Design Visualizer App, a digital approach to viewing the stunning array of Corian aesthetics in potential end-use applications and, again, reducing sample waste.
• Corian surfaces can be easily repaired, increasing the potential in-use lifetime of the products and reducing the need for frequent replacement.
We continue to examine ways to increase manufacturing efficiency and reduce waste in our production processes, as well as determine ways to recycle materials at the end of their life cycle. We are focused on providing sustainable solutions for our customers and the environment.
Cosentino: Cosentino has integrated sustainability into every facet of its business and has made incredible progress toward its goals.
All Silestone products are made with our pioneering HybriQ+ technology, a sustainable manufacturing process that uses 99% reused water, 100% renewable electric energy, zero water waste, and a minimum of 20% recycled raw materials within its composition. Also, this new manufacturing process significantly reduces the presence of crystalline silica to a maximum of 10% (HybriQ) or 50% (HybriQ+) — compared to 80%-100% for others in the industry — to aid in making the fabrication process safer than ever.
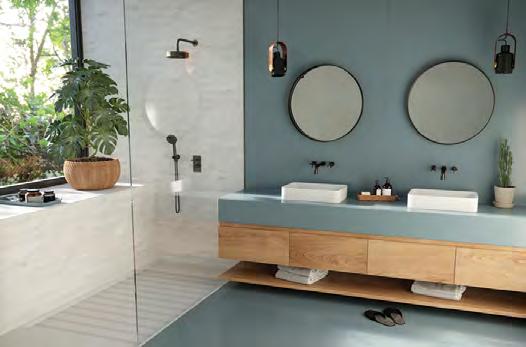
Cosentino Silestone Sunlit Days, Cosentino’s first-ever carbon neutral collection for Silestone, featured in Cala Blue.
Within our ultra-compact Dekton offerings, all products have been certified carbon neutral since 2020, representing the only cradle-to-grave carbon-neutral offering of its kind, while the Dekton plant recently received zero waste certification.
Outside of product manufacturing, our headquarters in Almeria, Spain, has the largest ground-mounted self-consumption photovoltaic plant in the country with nearly 37,000 solar panels, and we are working on placing more solar panels on the roofs of each of our factories to further lower energy consumption. This plant generates enough megawatts per year to cover approximately 20% of Cosentino’s annual electrical consumption. At our factory, we reuse 99% of the water that we consume. This year, our Wastewater Reclamation Plant will become active, putting the wastewater discharged by our neighboring communities to new use, marking another milestone in our sustainability efforts.
Finally, Cosentino has its own Waste Management and Recovery Plant, which enables the company to manage tons of solid waste, some of which can be recovered and used as recycled raw materials in our products.
Lapitec: Lapitec does not include any resin or oil derivatives, nor does it have any digital prints on its surface, which other materials use to imitate the effect of natural stone. Lapitec is created using exclusive technology: The process involves vacuum vibrocompression, joining feldspar mineral grains together without using binding resins, and then sintered at high temperatures. This results in a Lapitec slab that contains no crystalline silica. Lapitec is also manufactured with 15% pre-consumer recycled content, and all the water used during the production process is fully recycled and reused.
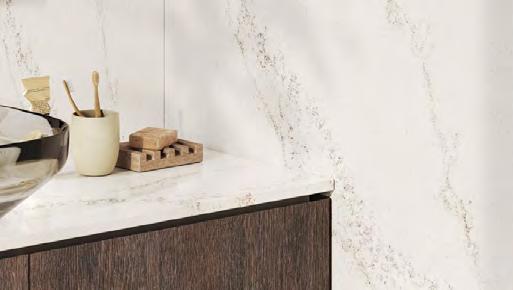
Lapitec slabs contain no crystalline silica and they’re manufactured with 15% pre-consumer recycled content. All the water used during the production process is fully recycled and reused.
CTAS: It’s clear you’ve been investing in sustainable products, processes and concepts, demonstrating your commitment to sustainability as a manufacturer. What are the driving forces behind your initiatives? For example, is sustainability viewed as a department with a function, such as marketing or logistics, or is sustainability a core value woven into all aspects of your organization where environment and products are just some of the yields for the focus?
Corian Design: Our long corporate commitment to sustainability drives us. Our sustainability strategy is grounded in our purpose to empower the world with the essential innovations to thrive, and inspired by the United Nations Sustainable Development Goals (U.N. SDGs). We’ve designed our nine 2030 Sustainability Goals to be challenging—to provoke technical breakthroughs and new ideas for addressing society’s biggest challenges while also addressing the material sustainability topics most relevant to our stakeholders.
Cosentino: Sustainability is woven into every aspect of our business, and we believe every employee at Cosentino plays a huge part in our sustainability progress. For us, it is more than just a trending topic. We base our development on respect for the environment and sustainability, and our ongoing corporate commitment to society and the local communities where we operate. We’ve been working hard to lessen our environmental impact for many years and plan to continue.
Lapitec: We’re currently working with our parent company, Breton, to document our efforts within a third-party verified sustainability report. All divisions are involved in this process, and a specific team has been created to commit to this goal. The core of the material itself is rooted in the very concept of using only sustainable minerals.
CTAS: How do you connect your sustainability story with fabricators and specifiers? What is the perceived value for fabricators to partner with you BECAUSE of your sustainability?
Corian Design: Our partnerships enable fabricators to leverage our knowledge of product stewardship and best practices for product recycling, reuse or renewal. These practices are not only cost-effective but also look at a long-term view of inherent customer benefits by reducing landfill waste where possible.
Cosentino: Our industry partners are very aware of our environmental initiatives and the competitive advantage it brings. In fact, each year, we bring together our partners in manufacturing and processing to discuss the latest innovations and how we can better the future of the industry together at our annual C.Next Fabricators Summit. We also provide educational workshops and training.
Sustainability is the future and something we as an industry must consider throughout the entire process, from manufacturing to fabrication. Our innovative technologies, like HybriQ and Quick Cut, allow us to deliver high-performance, sustainable products with beautiful designs. And as mentioned above, these sustainable innovations also allow for more safety in the industry. Silestone made with HybriQ Technology drastically reduces the percentage of crystalline silica in the product’s composition, creating a new product category. Cosentino is the only manufacturer that has invested in and worked for years toward this achievement, which transforms the composition of Silestone.
As more customers seek out and value sustainably made products, our partners know they don’t have to compromise with Cosentino.
Lapitec: Our sustainability story is deeply rooted in our products since Lapitec is completely inert and does not release any substance into the environment where it is fabricated and installed. Specifically, the fact that Lapitec is silica-free is an actual value for our fabricators since it’s a step toward improving their safety in the workplace, given the problems created by other materials that do contain this harmful mineral.
CTAS: If a group of fabricators who invested in and prioritized sustainable fabrication existed, how do you envision your company’s alignment with this group? Would it be valuable to you to connect with such a group to further your sustainability story and encourage alignment and optimization via the enterprise chain through to the installation of your products and values?
Corian Design: We have a long history of association with industry-leading organizations with an environmental focus. Corian Solid Surfaces would assess any new certification opportunities or organizational startups to determine whether the goals and values align with the Corian business and the larger DuPont corporate environmental and sustainability goals to determine if involvement makes sense.
Cosentino: Just as we value the sustainability certifications for our products, we would value this type of certification in our partners. It is important to partner and collaborate with other industry leaders whose sustainability goals are aligned with ours. However, we do want to distinguish that while these specific designations are important, our goal is to ensure that the fabricators, manufacturers and specifiers aim to lower their carbon footprint across all business areas. That’s why Cosentino is helping to push the architecture and design industry to become more aware of their sustainability practices as a whole.

Cosentino’s industrial park and self-consumption photovoltaic plant, which is one of the largest in Europe.
Summary
The last 25 years have seen several cycles of sustainability knocking at the industry’s door, only to have the momentum somewhat fade away until the next renaissance. What we see now, in 2023, is a movement that is not fading away; in fact, we have a zenith of impact, and this includes everything from eco-friendly products to manufacturers supporting zero-waste initiatives to manufacturers not only incorporating but proudly touting the use of renewable energies, and whose manufacturing environments are built and operating on firm sustainable pillars. This spinning wheel of holistic sustainability seems to be getting strong traction.
A chain is as strong as its weakest link. To that end, as manufacturers help set the bar for sustainability in the surfacing industry, supporting their efforts throughout the enterprise chain is compulsory for true success — actions that match the message. It’s about creating a reality where fabricators strengthen the sustainability chain by embracing the eco-friendly products offered, and proactively investing and deploying holistic, sustainable initiatives in their businesses. Like a tree in early spring, these fabricators help bud a new LEEF — a high-profile, sustainable fabrication business whose integrated and aligned role is essential for alignment and continuity.
Paul “Max” Le Pera is the president and founder of Proprietary Ventures LLC, a boutique-style global firm devoted to researching, discovering and deploying disruptive and sustainably oriented proprietary products and technologies. He serves on the ISFA board of directors as vice president of standards. He can be reached at paul.l@ proprietaryventures.com.
Jessica McNaughton serves as president atCaraGreen, a provider of sustainable building materials, including many alternative surfacing materials. She has 20 years’ experience in sales, marketing, business development and strategy. Previously the director of sales and marketing at CaraGreen, Jessica has maintained her status as a LEED Accredited Professional since 2009 and she hosts a podcast, Build Green Live Green. She can be reached at jessica@caragreen.com.