
2 minute read
How to maximise the lifecycle cost of your pump
How to maximise the lifecycle cost of your pump Article by Franklin Electric
When procuring a pump, upfront cost is often a major consideration in the decision-making process. However, according to a report issued by the Victorian Government, the initial cost accounts for less than ten per cent of the lifecycle cost, with energy and maintenance making up the bulk of these costs at between 50 and 95 per cent. Therefore, it is important to consider the long-term costs when selecting a pump to get the most cost-effective solution. Here, we look at what factors can influence and maximise the lifecycle cost of your pump.
While there are inevitable costs that are hard to control such as environmental, disposal and installation costs, end users can realise long-term savings with reduced maintenance, energy costs and downtime.
Selecting a pump: quality over cost
One important choice when selecting a pump that will influence its lifecycle costs is the quality of the equipment. A quality, reliable, well-built pump will likely have a lower lifecycle cost than a cheaper, lightweight pump.
Going for a cheaper option may result in a lesser quality product, especially if the materials selected are not suitable for the application. If this is the case, lifecycle costs can quickly increase as there is a higher chance of premature failure or unexpected servicing and replacement costs.
Along with materials, a high-quality product will have gone through rigorous testing to ensure it will run reliably and will be defect-free at the time of purchase. A manufacturer with top quality service will be able to provide prompt technical support so that minimal downtime is experienced.
Companies with quality customer service will also be able to provide an expert opinion when selecting a pump to ensure it will be the best fit for your application.
Getting the right size pump
Selecting a correctly sized pump is imperative to reduce lifecycle costs. While it might be tempting to get a smaller pump to reduce costs or a larger pump to account for possible higher pumping requirements, these will ultimately result in higher costs in the long term.
An undersized pump will result in reduced water efficiency, while an oversized pump will have a higher installation cost, as well as higher energy usage and wear rate.
Maximising energy efficiency
For applications such as irrigation where variable speed and flow rates may be needed, investing in a pump with a variable frequency drive (VFD) will help reduce lifecycle costs.
VFDs can be programmed to run the pumps at a certain speed and flow rate for different connected zones so that it is always running to its best efficiency point (BEP).
While a VFD will increase the initial cost of the pump, if the pump is not running to its BEP, it will experience increased wear and require more frequent maintenance and parts replacement, and have high energy consumption.
Leading the industry in service standards Franklin Electric has over 75 years of experience providing industry-leading technical service to the irrigation industry, providing support and advice to keep you pumping in even the most rural areas.
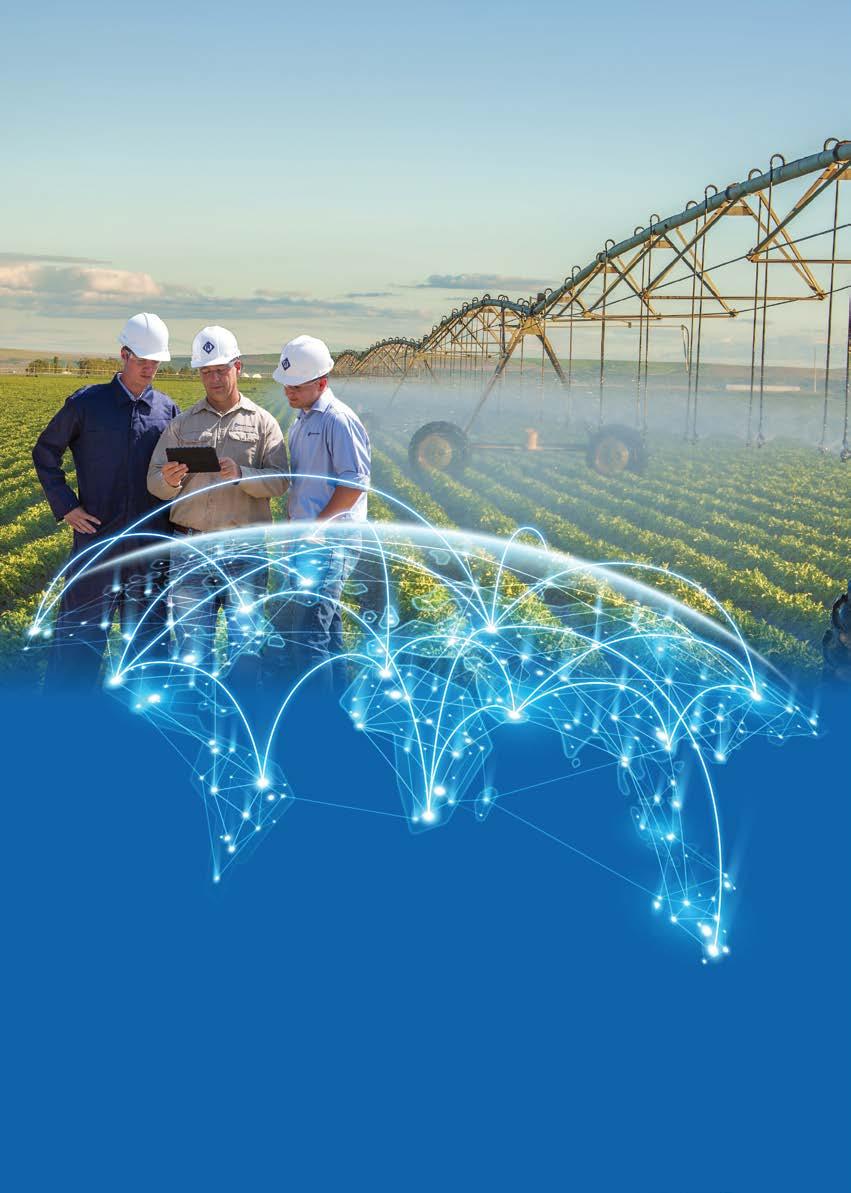