Smart Substation with Automatic Monitoring, Smart Controlling and Overload Protection of transformer using PLC and SCADA
Kunal1,2,3,4Students, Department of Electrical Engineering, Government College of Engineering Nagpur, Maharashtra, India
5Head of the Department Electrical Engineering, Government College of Engineering Nagpur, Maharashtra, India ***
Abstract - Electricity plays an indispensable role in modern society as it powers almost every aspect of our lives. However, [6] with the increasing demand for energy, the importance of efficient and reliable power distribution systems has become more apparent. [2][4][6 The traditional power distribution system has several limitations, including inadequate monitoringandcontrolcapabilities,whichcanresultinsystem failures and power outages. The power system comprises generating stations, transmission lines, and distribution systems. Load flows necessitate careful planning, monitoring, and controlling to ensure efficient operation and to minimize production costs. Each process has a distinct mechanism for acquiring data and controlling it. [1][5]Supervisory Control and Data Acquisition (SCADA) is a monitoring system that monitors numerous parameters ina substation. Theproposed system's central control room is equipped with SCADA, which provides anintuitive interface fortheoperatortomonitorand control the system. In the event of any abnormalities, the SCADAsystemdisplays real-timedata andalertstheoperator. Furthermore, the operator can remotely control the system usingtheSCADAsystem, increasingthesystem'sflexibilityand reducing response time in emergencies. This project replaces large control panels with a single PC, making it highly dynamic and cost-effective. The SCADA monitoring system does not experience mechanical wear and tear. The Programmable Logic Controller (PLC) serves as the system's brain. SCADA and PLC work in tandem to operate and control the power system remotely. This automatic network can manage loads, maintain quality, and detect electricity theft. The system also provides the operator with an overall view of the entire network. Pilferage points can be identified, and human errors that cause tripping can be eliminated, increasing reliability and lowering operating costs. Our project integrates network monitoring functions with geographic mapping and fault location to provide a comprehensive power distribution system.
Key Words: PLC, SCADA, Automation, Protection, Load flow, Dynamic, Reliability

1. INTRODUCTION
Asubstationisacrucialcomponentofanelectricalsystem thatencompassesgeneration,transmission,anddistribution. It serves multiple purposes, such as transforming voltage
fromhightolow,orviceversa,andexecutingvariousother vitalfunctions.Theelectricalutilityorsignificantindustrial or commercial customers can own and operate these substations. Theterm"substation"hasitsoriginsinthepregrid distribution system era. With the growth of central generation stations, smaller generating plants were transformedintodistributionstations,whichreceivedtheir energy supply from a larger plant rather than using their owngenerators.Initially,thefirstsubstationswerelinkedto onlyonepowerstation,whichhousedthegenerators,and wereregardedassubsidiariesofthatpowerstation.
1.1 Substation Automation
Substation automation is a process of using advanced technologies and intelligent devices to automate the monitoringandcontrolofpowersubstations.Thisresults inamoreefficientandreliableoperationofthepowergrid. Substationautomationsystemstypicallycomprisevarious equipment,suchassensors,controllers,andcommunication devices. These devices work together to monitor the substationanditscomponentsinreal-time,andthedatais transmitted to a central control system. This allows operatorstomakeinformeddecisionsabouttheoperationof thesubstation.[1][2][5]Substationautomationhasseveral advantages, including improved reliability and reduced downtime. With automated monitoring and control, potentialissuescanbedetectedandresolvedswiftly,which prevents equipment failures and power outages. Furthermore,itenablesthemoreefficientuseofresources like energy and manpower by automating tasks such as switching and fault detection. This, in turn, frees up operators to focus on more complex tasks and decisionmaking.Insummary,substationautomationisessentialfor modernpowersystems.Itallowsutilitiestooperatemore efficientlyanddeliverreliablepowertocustomers,reducing thelikelihoodofcostlyoutagesandfailures.Duringtheearly stagesofelectricalsubstations,theprocessrequiredmanual switchingoradjustmentofequipment.Additionally,datafor load,energyconsumption,andabnormaleventshadtobe collected manually. However, as distribution networks became more complex, it became necessary to automate supervisionandcontrolofsubstations.Thiswasdonefroma centrallyattendedpointtoallowoverallcoordinationincase ofemergenciesandreduceoperatingcosts.
Initially, dedicated communication wires were used for remotecontrolofsubstations.Thesewireswereusuallyrun alongside power circuits. Over time, different communication technologies such as power-line carrier, microwave radio, fibre optic cables, and dedicated wired remotecontrolcircuitswereusedforSupervisoryControl andDataAcquisition(SCADA)systemsforsubstations.
Nowadays,SCADAsystemsarecommonlyusedinsubstation automation.Thesesystemsallowoperatorstomonitorand controlsubstationsfromacentralizedlocation.Theycollect real-timedatafromvarioussensorsandequipment,enabling operatorstomakeinformeddecisionsandquicklyrespondto issues. Additionally, SCADA systems support remote monitoringandcontrol,whichhelpsutilitiestoenhancethe reliability of their power distribution networks, reduce downtime and operating costs, and ensure customer satisfaction.
2. SUBSTATION AUTOMATION TASK:
[8]Thereare3maintaskofautomationsystem:
(1)Dataacquisition
(2)Supervision
(3)Control
(1) Data acquisition:
Data acquisitionistheprocessofgatheringand recording datafromdifferentsources,suchasmeasurementdevices, instruments, and sensors. This collected data can then be usedinvariousfieldssuchasengineering, manufacturing, automation, and science for monitoring, decision-making, control,andanalysis.
The process of data acquisition involves measuring both analoganddigitalsignalswhicharethentransformedinto digitalsignalsthatcanbeeasilyprocessedbycomputersor other devices. The converted signals are then stored in a database or transmitted to other systems for further processingoranalysis.[9]Thesystemusessensorstocollect data from various parts of the substation, which is then transmittedtothePLCsforprocessingandanalysis.
Thereareseveralcomponentsinvolvedindataacquisition which include sensors or measurement devices, signal conditioning equipment, data acquisition hardware, and software.Thesensorsormeasurementdevicesareusedto collect data from the physical environment. The signal conditioningequipmentamplifies,filters,andconvertsthe signalsintoasuitableformforprocessing.Dataacquisition hardware is responsible for converting the analog signals into digital signals that can be processed by a computer. Software is used to control the data acquisition process, storethedata,andperformanalysis.
Dataacquisitionisutilizedinabroadrangeofapplications suchasenvironmentalmonitoring,processcontrol,scientific research, and automation. It has become an essential componentinvariousindustriesthatalloworganizationsto collectandanalyzedataforinformeddecision-makingand improvingtheiroperations.

Inaccordancetothisprojectitis responsibleforcollecting thedatafromvarioussensorsinstalledinthesubstation.The collected data is in the form of measured values, such as current or voltage, or the state of contact points (open or closed).Thisdatacanbeusedlocallybythedevicecollecting it,senttootherdeviceswithinthesubstation,ortransmitted from the substation to one or more databases for use by engineers,operators,administrators,andplanners.
(2) Supervision:
Supervisioninsubstationautomationreferstotheprocessof monitoringandoverseeingautomatedsystemsinelectrical substations to ensure they are functioning correctly and efficiently. In electrical substations, various types of automated systems are used to control and monitor equipment such as transformers, breakers, and switches. [3]Theautomationsystemcanbeconfiguredtomonitorthe electricalparameterssuchasvoltage,current,powerfactor, andfrequencyinreal-time.Additionally,itcandetectfaults and take appropriate actions such as tripping a circuit breakertoisolatethefault.
Thesupervisionsystemplaysavitalroleinmonitoringthe statusofthetransformerandsubstationequipmentinrealtime.ItreliesonSCADAsoftwaretodisplaythestatusofthe equipment, alarms, and events as they occur in realtime.[10] The data collected from Programmable Logic Controllers(PLCs)isprocessedandmonitoredbasedonthe conditionsand status of the power system.Engineersand operators can monitor this information remotely on computerdisplays.[4]TheSCADAsoftwareprovidesauserfriendlygraphicalinterfacetotheoperator,whichmakesit easytomonitorthestatusoftheequipment.Thesoftware also generates alarms and events when it detects any abnormalitiesinthesystem,andsendsthemtotheoperator forfurtheraction.
Thesupervisionsystemiscriticalforensuringthesafeand reliable operation of the power system. By monitoring the statusoftheequipmentanddetectingabnormalities,itcan help prevent equipment failures and minimize downtime. Additionally, it enables quick response and resolution of faults, reducing the impact on the power system and customers. In conclusion, the supervision system in substation automation is a critical component that allows engineersandoperatorstomonitorandcontrolthepower systemeffectively.ItreliesonadvancedSCADAsoftwareto providereal-timedataandauser-friendlyinterface,makingit easiertodetectabnormalitiesandrespondquicklytofaults.
(3) Control:
The control system is an essential part of substation automation,responsibleforregulatingtheoperationofthe equipment automatically. [6]Unlike traditional SCADA systemsthatrelyonhumansupervision,thecontrolsystem canfunctionindependently.Oneoftheprimarytasksofthe control system is to integrate the power system. This involves consolidating data from the Programmable Logic Controllers(PLCs)intoasinglepoint ofcontactwithinthe substation,streamliningdatamanagementandmonitoring. Dataacquisition,supervision,andcontrolareinterconnected insubstationautomation,andtheymustfunctionseamlessly. Thedataacquisitionsystemcollectsdatafromsensorsand othersources,whichthesupervisionsystemanalyzes.The control system then utilizes this information to regulate equipmentoperation,ensuringthatthesubstationoperates safelyandefficiently.Thecontrolsystemalsoplaysavital role in fault detection and resolution. By automatically detecting abnormalities in the system, the control system can take corrective action, preventing equipment failures andminimizingdowntime.
Inconclusion,thecontrolsystemisacriticalcomponentof substationautomation,enablingtheautomaticregulationof equipmentoperation.[7]PLCsalsoaddresstheimportanceof cybersecurity measures in the design of smart substation automation systems. The integration of substation data simplifiesdatamanagement,andtheseamlesscoordination of data acquisition, supervision, and control is crucial for maintaininga reliableandefficientpowersystem.Withits abilitytodetectandcorrectfaultsautomatically,thecontrol systemensuresasafeandstablepowersupply.
3. PROPOSED SYSTEM
SCADAbasedsystemsareessentialfortheproperfunctioning and coordination of individual systems. A dedicated ProgrammableLogicController(PLC)isusedfordatalogging and control operations. One of the key benefits of SCADA based systems is that each system can function independently,allowingothersystemstobeshutoffwhen notinuse.Thispaperprovidesacomprehensiveoverviewof various protocol implementations in creating a PLC-based unitandtheusageofanadvancedgraphicaluserinterfacefor processcontrol.Theuseofthispaperreplacestheneedfor largecontrolpanelsplacedinlargerooms.Allfunctionsare integrated into a single PC, making it highly dynamic and cost-effective. Supervisory Control and Data Acquisition (SCADA)isusedtomonitormultipleparametersavailablein asubstation,andinterlinkingprovidesaneasywaytoaccess dataandprovidecontrolfromacommonpoint.Thisreduces manpowerandtimedelays.Inthecontrolroom,theplantis monitored,andcommandsaregiventhroughtheuser.This methodiseconomicalandsafeforoperation.Ifthereareany modificationsorfutureextensions,theycanbeeasilyupdated inthePLCandSCADA.Inthesubstation,multipleswitches areused,andifoneswitchtrips,theparticularareacaneasily
be identified.[4][5] Automatic monitoring and control of powersystemparametersareachievedwiththeuseofvirtual instrumentationandagraphicalinterfaceunit.
4. IMPLEMENTATION OF SUBSTATION AUTOMATION
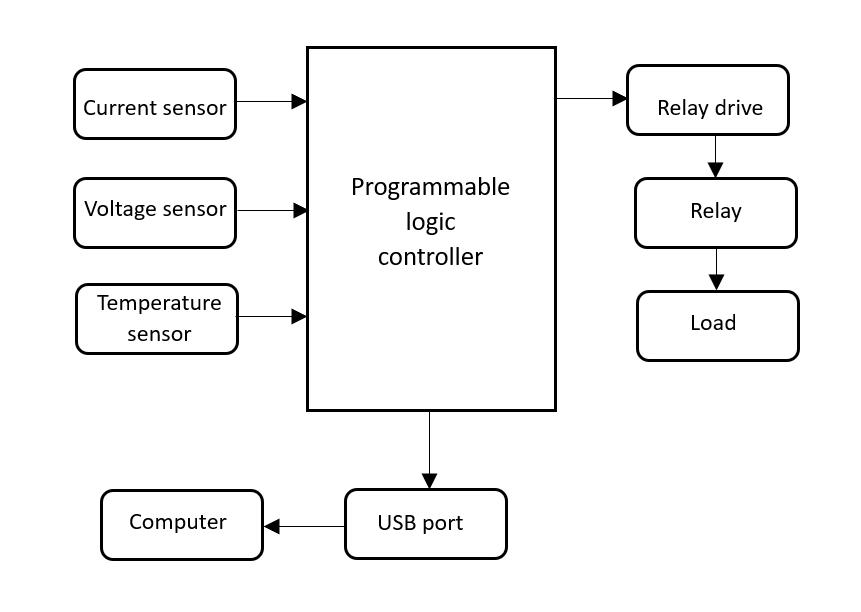
4.1 PLC
AProgrammableLogicController(PLC)isadigitalcomputer that is specifically designed to automate industrial electromechanical processes. These processes include controllingmachineryonassemblylines,amusementrides, and light fixtures. PLCs are commonly used in various industries and machines. PLCs are engineered to handle multipleanaloganddigitalinputsandoutputarrangements. Theycanoperateinextendedtemperaturerangesandcan resistelectricalnoise,vibration,andimpact.Programsthat regulate machine operation are typically stored in nonvolatilememoryorbattery-backed-upmemory.
PLCs have evolved over time to include various forms of control systems, such as sequential relay control, motion control, process control, distributed control systems, and networking.[7] Some modern PLCs offer data handling, storage,processingpower,andcommunicationcapabilities that are similar to those of desktop computers. Unlike regular computers, they are designed to be armored for harshenvironmentalconditionssuchasdust,moisture,heat, andcold.Theyalsocomewithextensiveinput/output(I/O) arrangements,whichallowthemtointerfacewithdifferent sensors and actuators. [3][4]PLCs are programmed to performspecifictaskssuchasmonitoringequipmentstatus, regulating voltage levels, and switching between different powersources.
Inconclusion,PLCsarespecializeddigitalcomputersthatare indispensable in automating industrial electromechanical processes.Theircapabilitieshaveevolvedtoincludevarious control systems and networking, making them a critical componentofmodernindustrialautomation.

The above figure shows basic block diagram of PLC (Programmable Logic Controller). The CPU of a PLC is typicallyprogrammedusingaprogrammingterminal,which canbeapersonalcomputeroradedicatedHuman-Machine Interface (HMI). The CPU consists of basic modules, includingexternalmodulesandInput/Output(I/O)modules, which can access bit, byte, word, and double-word addressablememorylocations.Oneofthecriticalfeaturesof a PLCisitsreal-timeperformance.AProgrammableLogic Controller (PLC) is considered a hard real-time system becauseitrequiresoutputresponsestobegeneratedwithin a predetermined timeframe based on input conditions.
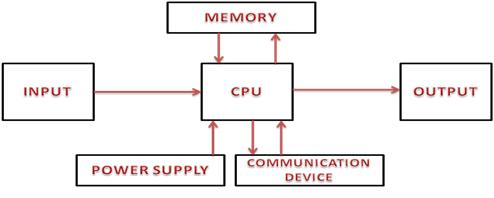
[4]This real-time capability ensures that the PLC can respondquicklytochangesintheinputsignalsandcontrol theoutputdevicesaccordingly.
4.2 INTERFACING WITH PLC SYSTEM

A system can be controlled using a Programmable Logic Controller.TheprogrammingofPLCincludescommandsto turnonandoffoutputsaspertheinputconditionsandthe internal program of PLC. Once a Programmable Logic Controller (PLC) takes control of the system, it utilizes sensor inputs to make informed decisions and updates outputs to actuate the system. The actuators perform the operationtoopenandclosethecircuitbreakers.Thisstates thatthecontrollerislimitedbythesensorsavailable.Thus,if aninputofPLCisnotavailablethenthecontrollerwillnot detectconditions.Thephysicalprototypemodelisinterfaced withtheProgrammableLogicController(PLC)usingitsfour outputsandfiveinputsinthisparticularmodel.Thefigure givenbelowistheimageactualworkingmodel.
Theinputsareconfiguredas:-
X0–VoltageSensor
X1–CurrentSensor
X2– SmokeSensor
X3–TemperatureSensor
X4–TemperatureSensor
Theoutputsareconfiguredas:-
Y0–Circuitbreaker1opened
Y1–Circuitbreaker1closed
Y2–Circuitbreaker2opened
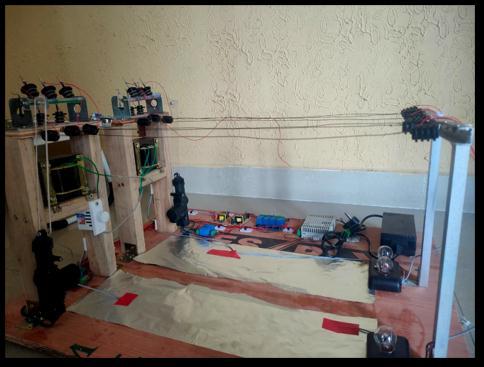
Y3–Circuitbreaker2closed
4.3 SCADA
[2] SCADA (Supervisory Control And Data Acquisition system)isacombinationoftelemetryanddataacquisition. ThesystemcollectsinformationthroughRemoteTerminal Units(RTUs),whicharethensentbacktoacentralsitefor analysisandcontrol.Theinformationisdisplayedonvarious operating screens or displays. SCADA systems are distributed and used to manage geographically dispersed assets over thousands of square kilometers, where centralizeddataacquisitionandcontrolarecrucialtosystem operation.
SCADA systems are used in distribution systems such as waterdistributionandwastewatercollectionsystems, oil and gas pipelines, electrical power grids, and railway transportation systems. The centralized monitoring and control of remote field sites via long-distance communication networks are carried out by the control center of a SCADA (Supervisory Control and Data Acquisition)system.Itmonitorsalarmsandprocessesstatus data,basedoninformationreceivedfromremotestations.[9] Automatedoroperator-drivensupervisorycommandscan bepushedtoremotestationcontroldevices,whichareoften referredtoasfielddevices.
[1][5]Fielddevicescontrollocaloperationssuchasopening andclosingvalvesandbreakers,collectingdatafromsensor systems, and monitoring the local environment for alarm conditions.ASCADAsystemgathersdatafromsensorsand instrumentslocatedinremoteareas,andtransmitsthedata to a central site for process monitoring by controllers. Automation systems are used to increase the efficiency of processcontrolbytradingoffhighpersonnelcostsforlow computersystemcosts.
5. WORKING
Wehaveasetupconsistingoftwolinesrepresentedbytwo towers.ThepowersupplyisregulatedbyaSMPS,orswitch modepowersupply,whichprovidespowertoourmodular Delta-madePLC,theDVP14SS2.Arelaycardwith24vand5v relays controls the motor of the actuator, two circuit breakers,andachangeoverswitch.ThePLCsendssignalsto the relays, and a voltage regulator is attached due to the presence of 5v relays. There are two automated isolators thatcanbeimplementedtoallisolators.Eachisolatorhasa motor actuator to open and close the contacts. Also two circuit breakers are present- one for each line. Relays are used to symbolize the circuit breakers. Additionally, two transformersandtwobulbsareattachedtosymbolizethe twoloads.
In operation mode, the SMPS is connected to the power supplyandprovidespowerwherenecessary.ToturnonLine 1, we send a signal from SCADA to the isolator actuator, whichwillconnectthecircuitforagivenamountoftime.To turn off Line 1, we simply open the isolator from SCADA, whichwilldisconnectthecircuitandstoppowerfrombeing suppliedtotheload.Allcontrollingsignalsareprovidedby thePLC.

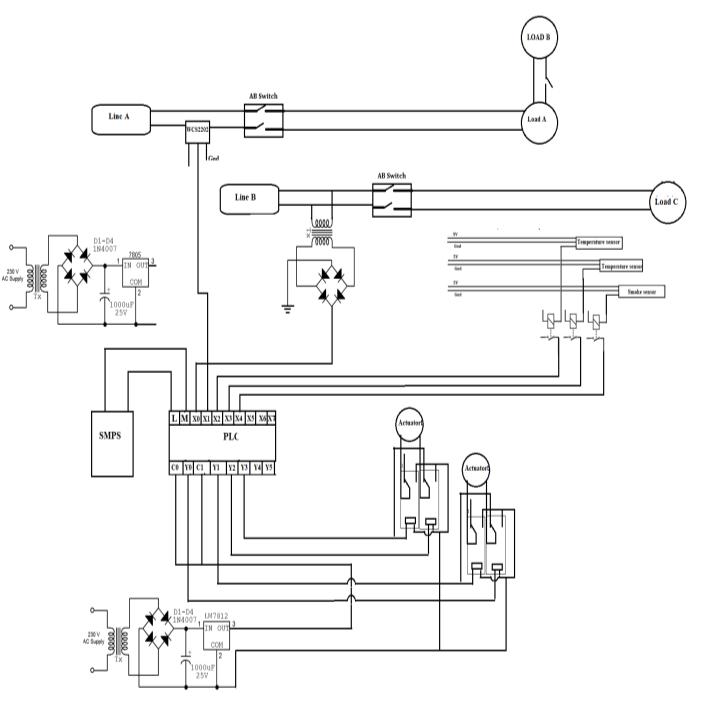
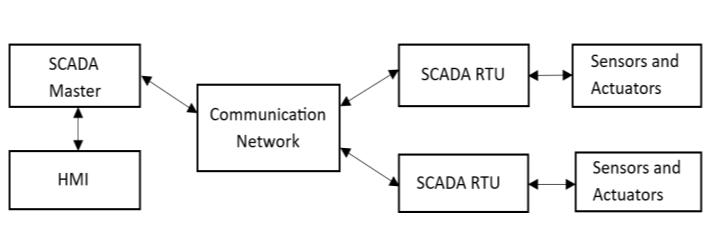
Intheeventofaproblemwithoneofthelines,wecanuse thechangeoverswitchtoswitchtheloadfromonelinetothe othertoprovidepower.
6. RESULTS
Thismodelhasensuredtheefficientworkingandsubstation automationusingPLCandSCADAbydetectingvariousfaults. Thefaultsincludeundervoltage,overcurrent,increase in temperaturelimitfaultsaswellasasituationoffire.During normal conditions the SCADA screen shows that all the indicators of the faults are green. At faulty condition the indicator of the particular fault will turn red and the automated system will open the circuit breaker of the particular line immediately .The Fig 6.1 gives the SCADA screenfornormaloperation, Fig6.2givestheSCADAscreen for the under voltage fault condition and Fig 6.3 gives the SCADAscreenfortheovercurrentfaultcondition.

6. CONCLUSION
Inconclusion,theadoptionofPLCandSCADAtechnologyfor theimplementationofaSmartSubstationholdsnumerous advantages for power utilities. These benefits encompass increased operational efficiency, enhanced reliability and security,andimprovedmonitoringandcontrolcapabilities. By integrating advanced communication systems and intelligent devices, real-time data and insights can be obtained, enabling power utilities to optimize their operationsandoverallperformance.However,thesuccessful implementation of such a system necessitates meticulous planning,design,execution,aswellasongoingmaintenance and upgrades. As the field of Smart Grid technology continuestoadvance,SmartSubstationsarepoisedtoplay an increasingly vital role in ensuring a dependable and sustainable energy supply. This project aims to replace outdatedpracticesthatinvolvephysicallyvisitingsitesfor faultdetectionandrepair,withmodernmethods.Moreover, italsooffersvaluablefeaturessuchastransformeroverload protection,firehazarddetectionandprevention,aswellas temperature and smoke sensing. These parameters hold significant importance for commercial, industrial, and distributionsectors,makingthisprojecthighlybeneficialfor theoverallsystem.
6. ACKNOWLEDGEMENT
It brings me immense pleasure and a profound sense of privilegetopresentthispapertitled"SmartSubstationwith
Automatic Monitoring, Smart Controlling, and Overload Protection of Transformers using PLC and SCADA." As students, we consider preparing a research paper a significant milestonein our academicjourney,and weare awarethatitssuccessfulexecutionisheavilyreliantonthe guidanceandsupportofourmentor.Thus,weextendour deepest gratitude to electrical engineering department of Government College of Engineering, Nagpur, for their invaluable assistance throughout the development of this paper.
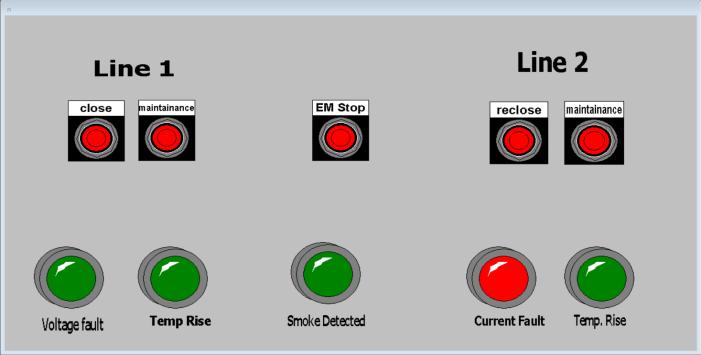
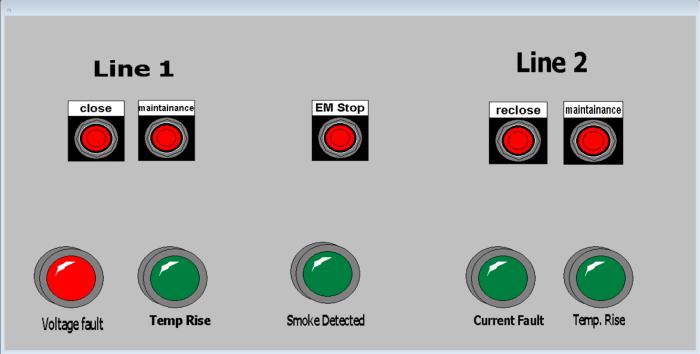
REFERENCES
[1]InternationalJournalofInnovativeScience,Engineering & Technology “Automation based power transmission control station using PLC and SCADA”, T.Vignesh, J. Kirubakaran.
[2] International Journal of Electronics and Computer Science Engineering 254 “Design And Implementation Of SCADA System Based Power Distribution For Primary Substation(monitoring system)”, Aye Min Zaw 1, Hla Myo Tun2.
[3] International Journal of Electronics and Computer Science Engineering 254 “Design And Implementation Of SCADA System Based Power Distribution For Primary Substation(controlsystem)”.KhinThuZarWin1,HlaMyo Tun2.
[4]MultidisciplinaryJournalofresearchinEngineeringand Technology“PLCSCADAbaseddistributionmonitoringand control”,SanthoshB.Belekar.
[5]Rajput, N. S., & Haldkar, V. K. (2017). Automated substation using PLC and SCADA. International Journal of Innovative Research in Electrical, Electronics, InstrumentationandControlEngineering,5(8),40-47.
[6]Gholami,M.,&Esmaeilian,M.(2019).Smartsubstation designformodernpowersystems:Areview.ElectricPower ComponentsandSystems,47(4),299-318.
[7]Singh,N.,&Jain,A.(2017).PLC-basedsmartsubstation automationsystem.InternationalJournalofEngineeringand Technology,9(1),436-440.
[8]Hwang,S.,Lee,S.,&Lee,H.(2015).SCADAsystemdesign for smart grid. International Journal of Control and Automation,8(3),1-10.
[9] Parashar, P., & Kaushik, S. C. (2016). Design of smart substation for monitoring and control of power system. InternationalJournalofComputerApplications,152(11),2630.
[10]Mousavi,S.S.,&Yousefi,G.R.(2018).Optimaldesignof smartsubstationusingPLCandSCADA.EnergyReports,4, 290-299.
