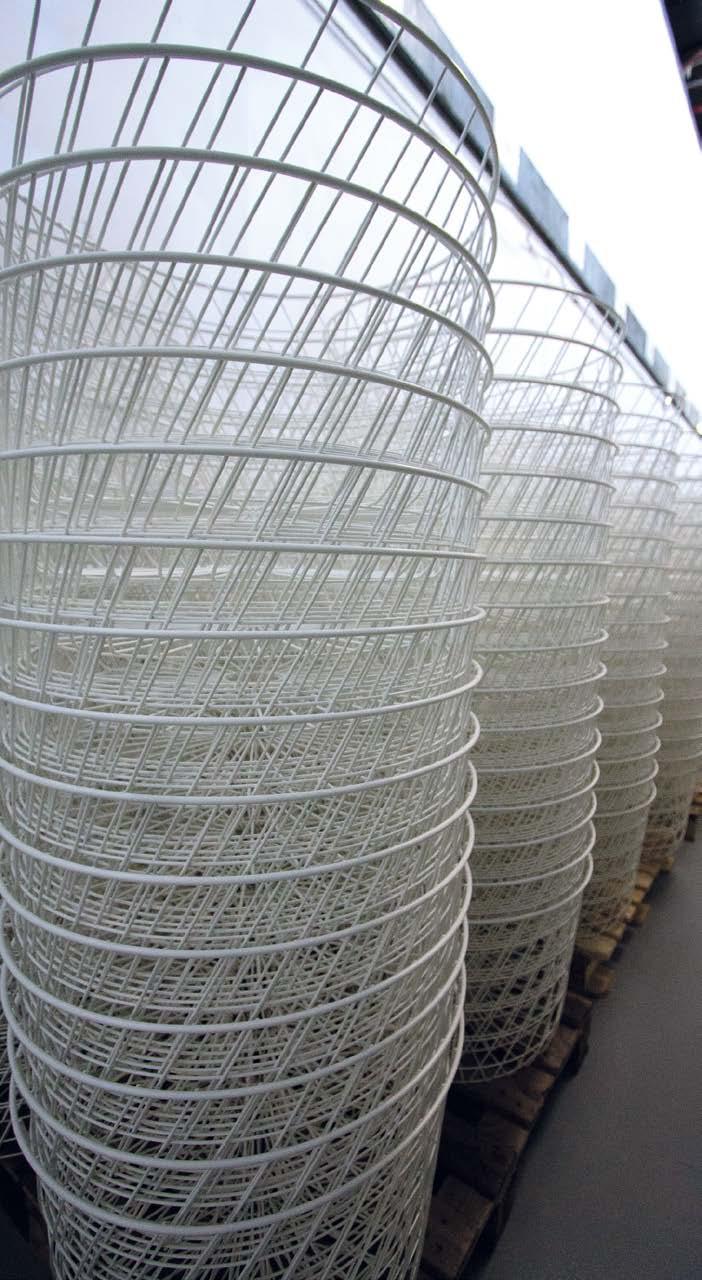
26 minute read
APUESTA POR LA TECNOLOGÍA FOCO NA TECNOLOGIA
En Dradura, el sistema de aplicación de última generación optimiza el recubrimiento en polvo de los cruces de las mallas metálicas
¿Es posible, hablando de pintura, conciliar la máxima capacidad de producción, la justa homogeneidad de la película de pintura en los puntos más críticos y el mínimo derroche de pintura utilizada? En Dradura, una empresa especializada en la fabricación y acabado de alambre metálico para componentes de electrodomésticos y mobiliario, la respuesta es afirmativa gracias a la cabina de pintura de última generación creada por Wagner, al sistema de suspensión concebido por Rostirolla y a las soluciones de instalación de la línea desarrollada por O.M.SA.
© ipcm
Las cestas son una de las principales producciones de Dradura. Uma das principais produções atuais da Dradura são os cestinhos.
Na Dradura, o sistema de aplicação de última geração otimiza o revestimento a pó das intersecções das malhas de metal
Na pintura, é possível conciliar a máxima capacidade de produção, a homogeneidade adequada da película de tinta nos pontos mais críticos e a máxima economia na quantidade de tinta utilizada? Na Dradura, empresa especializada no processamento e acabamento de fios metálicos para componentes de eletrodomésticos e de móveis, a resposta é afirmativa, graças à cabine de pintura de última geração desenvolvida pela Wagner, ao sistema de penduramento estudado pela Rostirolla e às soluções de engenharia industrial da linha desenvolvida pela O.M.SA.
La forma de un objeto es lo que caracteriza su aspecto estético y funcional: la tarea de la pintura es recubrir sus contornos permitiendo que la película se deposite sobre su superficie. Uno de los problemas más comunes de la fase de aplicación es la falta de homogeneidad del espesor entre la capa aplicada en los bordes y la que se observa en la superficie plana del producto. En el caso de un componente tridimensional con geometrías complejas, las mayores criticidades se detectan en las contrasalidas y en las áreas cóncavas que forman su perfil. La aplicación resulta aún más compleja cuando se intenta optimizar la pulverización de artículos fabricados con red de alambre de malla ancha: no se trata únicamente de encontrar la mejor tecnología de aplicación para evitar un derroche excesivo de pintura, sino también de estudiar el sistema más adecuado para aplicar la justa cantidad de pintura en los cruces de la malla metálica a fin de obtener una capa homogénea, y para lograr el espesor mínimo necesario para satisfacer al cliente. Dradura Italia, empresa veneciana de San Donà di Piave (Venecia), actualmente parte del grupo alemán Dradura, está especializa en la fabricación y acabado del alambre con el que realizan por cuenta ajena componentes destinados principalmente al sector del electrodoméstico y del mobiliario.
Dradura, el grupo líder en la elaboración de alambre
La empresa de San Donà cuenta con una larga historia que inicia en los años cincuenta con una pequeña empresa, denominada OMIM, dedicada A forma de um objeto é o que caracteriza seu aspecto estético e funcional: a tarefa da pintura é revestir seus contornos, permitindo que a película se acomode em sua superfície. Um dos problemas mais comuns referentes à aplicação é a falta de homogeneidade da espessura entre a camada aplicada nas bordas e na superfície plana do produto. No caso de um componente tridimensional com geometrias complexas, os principais problemas se encontram nos entalhes e nas áreas côncavas que distinguem sua forma. Porém, a aplicação é ainda mais complexa quando se trata de otimizar a pulverização em produtos feitos de fio metálico e caracterizados por malhas largas: não se trata apenas de identificar a melhor tecnologia de aplicação para evitar o desperdício de produto de pintura, mas também de estudar o sistema mais adequado para aplicar a quantidade correta de tinta nas intersecções da grelha metálica e obter uma camada homogênea e a espessura mínima necessária para satisfazer o cliente. A Dradura Italia, empresa veneziana de San Donà di Piave (Veneza), hoje parte do grupo alemão Dradura, é especializada no processamento e acabamento de fios metálicos com os quais produz, para terceiros, componentes destinados principalmente para o setor de eletrodomésticos e móveis.
Dradura, o grupo líder no processamento de fio metálico A empresa sandonatense tem uma longa história, que começou nos anos 1950 com o nome OMIM, uma pequena empresa que se
© ipcm
La instalación de pretratamiento de 6 etapas instalada por O.M.SA. Srl. O sistema de pré-tratamento de 6 estágios, instalado pela O.M.SA. Srl.
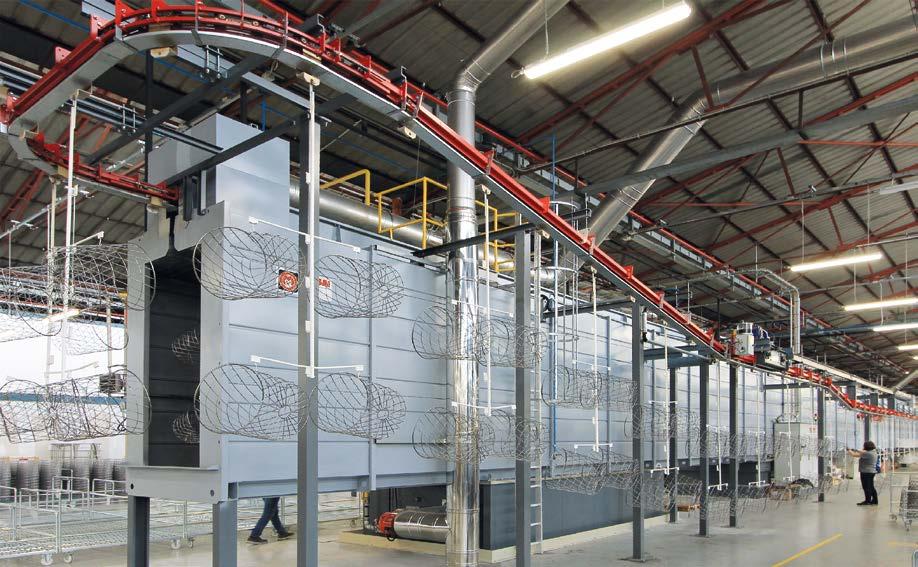
Salida de las cestas de la instalación de secado.
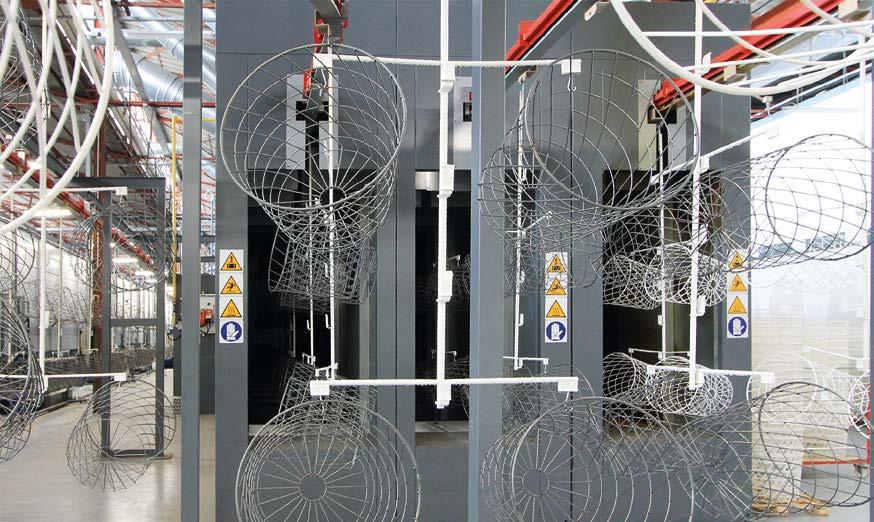
© ipcm
Os cestos saindo do sistema de secagem.
a la fabricación de cestas de hierro para botellas de leche, que después amplía su oferta a las rejillas para refrigeradores y, posteriormente, a raíz del boom de los electrodomésticos de los años sesenta y setenta, abarca también las cestas para lavavajillas fabricadas con hierro plastificado. «La mayoría de nuestros productos – confirma Maurizio Scalabrino, Responsable de Ingeniería de Dradura – están fabricados con alambres de distintos diámetros recubiertos con diferentes acabados y están destinados a satisfacer las demandas de clientes importantes como Bosch, Electrolux, Liebherr e IKEA, por nombrar algunos. El negocio principal del grupo Dradura es la fabricación de cestas de lavavajillas a la que se dedican la mayor parte de los establecimientos del grupo alemán: la sede central en Alemania, otra planta de producción en Italia, en Conzano en la zona del Monferrato (Alejandría), un establecimiento en Francia, uno en Polonia, uno en la República Checa y otro en los Estados Unidos. La única planta productiva que dedica el 50% de su actividad al sector del mueble es la nuestra. Por ello, somos también la única realidad del grupo que ha sentido la necesidad de equiparse con una nueva línea de pintura a fin de poder hacer frente a una elevada capacidad de producción y lograr un recubrimiento óptimo del alambre. Además de las geometrías complejas que pueden adoptar las mallas metálicas, nuestra verdadera dificultad era la posibilidad de que el espesor de la película en los cruces del alambre no fuese homogéneo – ya que es la zona más complicada de recubrir – y el derroche de pintura en polvo debido a su pulverización en los huecos de las mallas. La solución a estas dudas nos la ofreció la empresa Wagner de Valmadrera (Lecco), parte del grupo internacional J. Wagner GmbH, especializada en el diseño y realización de tecnologías de aplicación de pinturas líquidas y dedicava à produção de caixotes de ferro para garrafas de leite, depois expandida com a de grelhas para frigoríficos e, posteriormente, como resposta ao boom dos eletrodomésticos dos anos 60 e 70, de cestos para lava-louças feitos de ferro plastificado. “A maior parte dos nossos produtos - confirma Maurizio Scalabrino, chefe de engenharia da Dradura – é feita com fios metálicos de diversos diâmetros revestidos com vários acabamentos e para satisfazer as exigências de clientes como a Bosch, Electrolux, Liebherr e IKEA, entre outros. A principal atividade do grupo Dradura é a produção de cestos para lava-louças, que são utilizados pela maior parte das outras fábricas pertencentes ao grupo alemão: a sede da Alemanha, outra fábrica na Itália, em Conzano, Monferrato (Alessandria), uma fábrica na França, uma na Polônia, uma na República Tcheca e outra nos Estados Unidos. A única fábrica que dedica 50% dos negócios ao setor de móveis é a nossa. Isso explica porque também somos a única empresa do grupo que sentiu a necessidade de se equipar com uma nova linha de pintura, para atender aos requisitos de elevada capacidade de produção e revestimento ideal do fio metálico. Além das geometrias complexas que as malhas metálicas podem ter, a verdadeira dificuldade para nós era a espessura da película não uniforme que poderíamos encontrar nas intersecções do fio - a área mais complicada de revestir - e o consumo excessivo de tinta em pó pulverizada descartada nos vãos da malha. A solução para esses problemas foi apresentada pela empresa Wagner, de Valmadrera (Lecco), parte do grupo internacional J. Wagner GmbH, especializado na projetação e realização de tecnologias de aplicação de produtos de pintura líquida e em pó, que nos disponibilizou o sistema de aplicação
en polvo, que nos ha puesto a punto un sistema de aplicación de última generación, el SuperCube, integrado con el sistema de gestión de polvos SuperCenter EVO».
No hay límites a las posibilidades de acabados
El proceso de producción inicia con el hilo precortado y procesado almacenado en almacén o directamente con la elaboración de la bobina metálica llevada a cabo por las distintas plegadoras 2D y 3D y por las máquinas CNC de control numérico. Después de la fase de elaboración, las piezas plegadas con geometría compleja se someten a las fases de pretratamiento y acabado con diferentes características en cada uno de los establecimientos del grupo. «En todos los centros de producción del grupo alemán – continúa Scalabrino – se utilizan diversos procesos de acabado elegidos en función de las necesidades técnicas del producto que se va a tratar: proceso de abrillantado o de galvanizado en barril, de cromado con NiCr o zinc, pasando por el pulido electrolítico, la pintura con colores RAL a elección, también aplicados en cataforesis, hasta llegar a la plastificación con polvo realizada con diferentes tipos de materiales como poliamidas, polietileno, epóxido, PTFE y poliuretano, tanto transparente como en distintos colores». El establecimiento de Dradura cuenta con 2 instalaciones de galvanizado y 2 de pintura transparente en polvo epoxi, poliéster y de poliuretano, ya que «con solo el tratamiento de galvanización no es suficiente para proteger las rejillas contra las bajas temperaturas o contra la humedad de última geração, SuperCube, integrado ao sistema de gerenciamento de pó SuperCenter EVO ”.
Nenhum limite para as possibilidades de acabamento O processo de produção começa com o fio pré-cortado e processado em estoque, ou diretamente do processamento da bobina de metal realizada por várias dobradeiras 2D e 3D e por máquinas a CNC. Após o processamento, as peças dobradas de geometria complexa são submetidas a pré-tratamento e acabamento com características diferentes em cada fábrica do grupo. “Em todas as fábricas do grupo alemão - explica Scalabrino - são utilizados diferentes processos de acabamento, escolhidos de acordo com as necessidades técnicas do produto a ser tratado: desde o abrilhantamento ou galvanização com tambor rotativo, da cromagem com NiCr ou zinco, passando pelo polimento eletrolítico, a pintura com a escolha de cores RAL também aplicadas em cataforese, até a plastificação em pó realizada com diferentes tipos de material, como poliamida, polietileno, epóxi, PTFE e poliuretano transparente e de várias cores». A fábrica da Dradura é equipada com 2 sistemas de galvanização e 2 utilizados para a aplicação de tinta transparente em pó epóxi, poliéster e poliuretânica pois, como diz Scalabrino: “a galvanização por si só não é suficiente para proteger as grelhas contra as baixas temperaturas ou a umidade dos ambientes aos quais se destinam - como geladeiras,
© ipcm
La cabina de pintura SuperCube de Wagner y, en primer plano, los bastidores concebidos por Rostirolla específicamente para Dradura. A cabine de pintura SuperCube, da Wagner e, em primeiro plano, os penduradores feitos especialmente para a Dradura, pela Rostirolla.
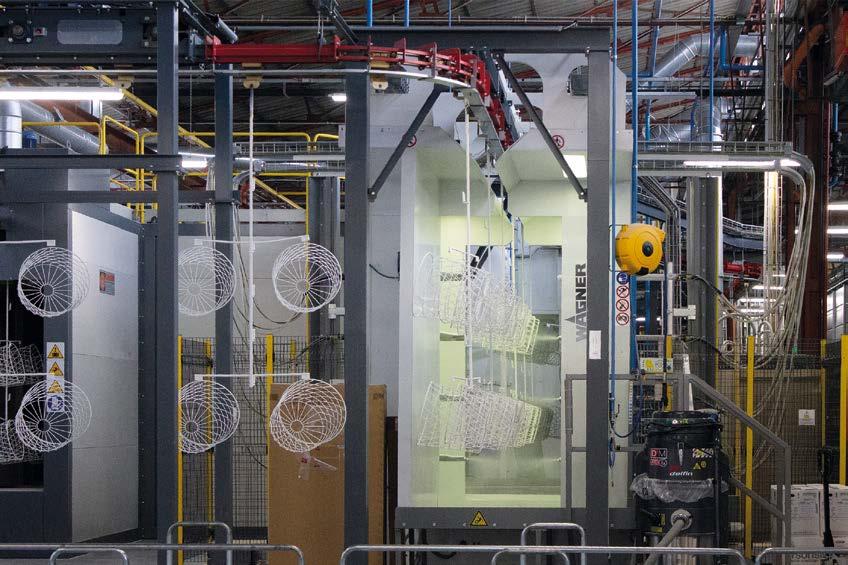
de los ambientes a los que están destinadas – como son los frigoríficos, cuartos de aseo o duchas – y para conseguir una resistencia en niebla salina correspondiente a las 144 horas mínimas exigidas por los clientes», continúa Scalabrino. Tras las primeras elaboraciones de las cestas de baño y el aumento progresivo de la demanda de productos con alambre pintado por parte de una famosa marca sueca, la gerencia de Dradura decidió instalar una nueva línea de pintura la cual empezó a funcionar en octubre de 2019 y que, en la actualidad, se dedica exclusivamente al recubrimiento de las cestas de malla metálica.
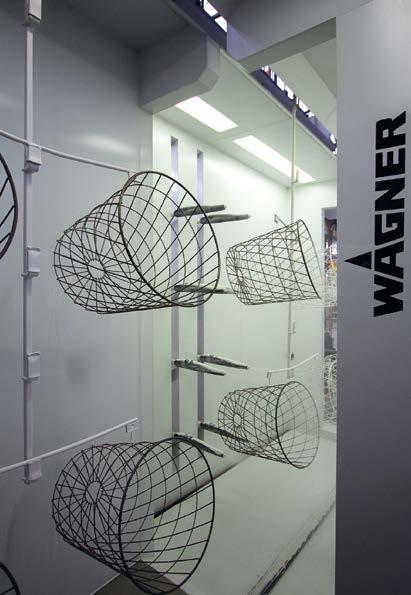
Una línea flexible preparada para proyectos futuros
«Puesto que la demanda sigue creciendo, toda solución que se adopte para poder intensificar la producción es fundamental para nosotros», precisa Scalabrino describiendo las principales características de la nueva instalación de pintura que el equipo técnico de Dradura ha concebido y optimizado junto con 3 empresas asociadas: Wagner, que ha diseñado e instalado el sistema de aplicación; Rostirolla que se ha ocupado del sistema de suspensión de las piezas, y O.M.SA. de Besana Brianza, en la provincia de Monza, que se ha ocupado de la línea de pintura y que Dradura ya conocía por ser el proveedor histórico de sus instalaciones tanto de pintura como de plastificación del alambre. «Este proyecto es el fruto de nuestra preeminente necesidad de aumentar el volumen de producción», continúa Scalabrino. «Pero no queríamos únicamente una solución que resolviese la emergencia actual, sino que permitiese también tratar el día de mañana cualquier tipo de nuevo pedido: la nueva línea resuelve plenamente ambas necesidades». «La instalación – explica Giovanni Sala, titular de O.M.SA. – se ha montado muy rápidamente debido al carácter urgente de la demanda del cliente. Algunos de los elementos que caracterizan el diseño y la realización de las instalaciones O.M.SA. Srl
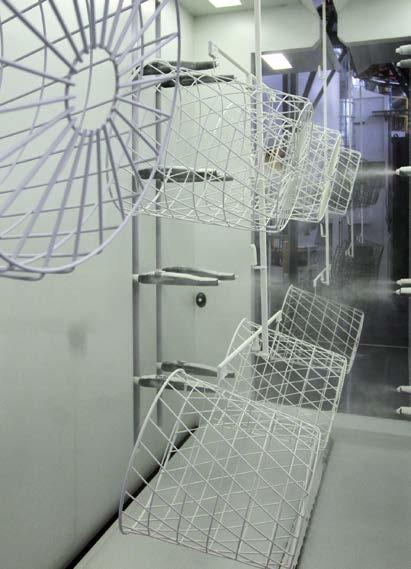
© ipcm
© ipcm
La cabina está equipada con 8 pistolas por lado. Los cruces de alambre son uno de los elementos más difíciles de pintar. A cabine é equipada com 8 pistolas de cada lado. Um dos elementos mais difíceis de pintar são as intersecções do fio metálico.
banheiros ou chuveiros - e obter uma resistência à névoa salina correspondente às 144 horas mínimas exigidas pelos clientes”. Depois dos primeiros processamentos de cestos para banheiro, o aumento dos pedidos de produtos em fio metálico pintado, por uma conhecida marca sueca, convenceu a direção da Dradura a instalar uma nova linha de pintura, que começou a funcionar em outubro de 2019 e atualmente é dedicada exclusivamente ao revestimento de cestos de malha metálica.
Uma linha flexível preparada para projetos futuros “Diante do contínuo crescimento das encomendas, cada solução adotada para intensificar a produção é fundamental para nós”, explica Scalabrino, descrevendo as principais características do novo sistema de pintura, que a equipe técnica da Dradura estudou e otimizou em parceria com três empresas: a Wagner, que desenhou e instalou o sistema de aplicação; a Rostirolla que cuidou do sistema de suspensão das peças e a O.M.SA., de Besana Brianza, província de Monza, responsável pela linha de pintura e que já era conhecida pela empresa veneziana como a fornecedora histórica dos seus sistemas, tanto para pintura, quanto para plastificação de fios. “O motivo principal do projeto foi enfrentar o aumento do volume de produção”, explica Scalabrino. “No entanto, queríamos uma solução não só capaz de responder à contingência de emergência, mas que possibilitasse tratar qualquer tipo de produto da Dradura também no futuro: a nova linha atende plenamente a ambas as necessidades”. “O sistema - explica Giovanni Sala, proprietário da O.M.SA. - foi instalado em pouco tempo, para resolver a urgência do pedido do cliente. Um dos elementos que caracterizam o projeto e a realização dos
son la calidad, la fiabilidad a largo plazo y la realización de un diseño de planta específico para optimizar los flujos productivos solicitados por Dradura. O.M.SA presta mucha atención a la construcción y fabricación de sus instalaciones. Por ejemplo, la estructura particular de nuestros paneles para la realización de los hornos está concebida para garantizar un elevado coeficiente de aislamiento térmico, así como para poder transportarlos fácilmente e instalarlos rápidamente. En concreto, hemos desarrollado para la línea de Dradura una instalación de pretratamiento multimetal de 6 etapas: desengrasado, 2 aclarados con agua de red y uno con agua desmineralizada, conversión nanotecnológica y el último aclarado con agua desmineralizada». Al salir del túnel de pretratamiento, las piezas entran en el horno de secado, tras el cual se encuentra una zona para la refrigeración de la superficie de los productos manufacturados antes de su entrada en la cabina de pintura, para después continuar en el horno de polimerización tradicional.
«La cabina que hemos suministrado a Dradura – explica Venanzio Rosada, Responsable comercial de Wagner – es un modelo SuperCube de última generación. Está equipada con 8 pistolas por lado, con un total de 18 incluidas las 2 destinadas al pre y post retoque, y está predispuesta para el cambio de color rápido que, por el momento, el flujo de producción de la empresa no requiere ya que actualmente solo se usan 4 tonos de color: 2 blancos, un negro y un gris, pero que más adelante se podrá sistemas da O.M.SA. Srl são a qualidade, a segurança a longo prazo e a criação de um layout específico para a otimização do volume de produção exigido pela Dradura. A O.M.SA é muito meticulosa na construção e fabricação de seus equipamentos. Por exemplo, a estrutura especial dos nossos painéis para a fabricação de fornos é feita para garantir um elevado coeficiente de isolamento térmico, para facilitar seu transporte e agilizar sua instalação. Para a linha oferecida para a Dradura, desenvolvemos um sistema de pré-tratamento multimetal de 6 estágios: desengorduramento, 2 enxágues com água potável e um com água desmineralizada, conversão nanotecnológica e último enxágue com água desmineralizada”. Na saída do túnel de pré-tratamento, as peças entram no forno de secagem, seguido por uma área para o resfriamento da superfície dos produtos antes de entrar na cabine de pintura, para depois seguirem para o forno de polimerização tradicional.
O coração tecnológico da linha: a cabine de pintura “A cabine que fornecemos para a Dradura - explica Venanzio Rosada, diretor comercial da Wagner - é um modelo SuperCube de última geração, equipado com 8 pistolas de cada lado, totalizando 18, incluindo 2 para pré e pós-retoque e preparada para troca rápida de cor, necessidade que ainda não se apresentou no fluxo de produção da empresa - atualmente as cores utilizadas são apenas 4: 2 brancos, um preto e um cinza – mas preparada para gerenciar no futuro, graças
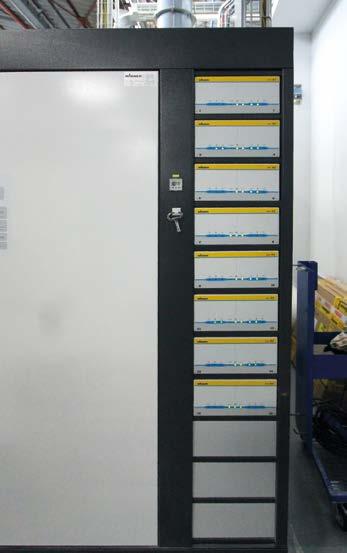
© ipcm
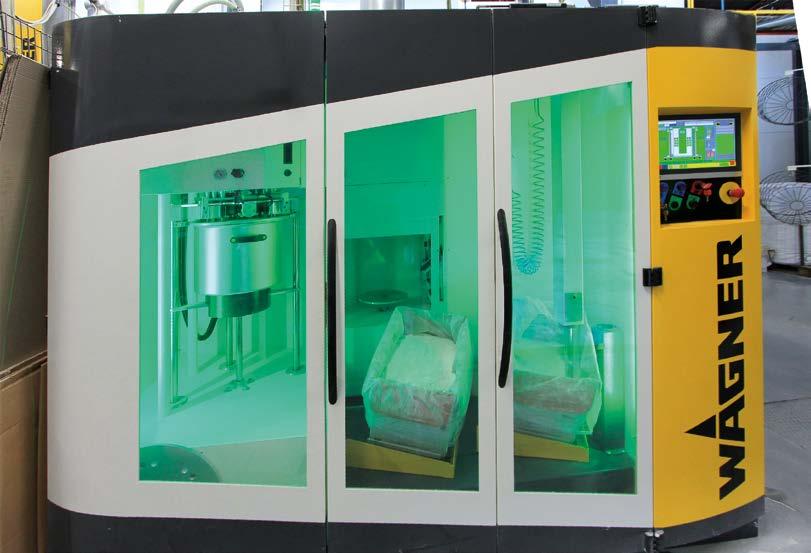
El SuperCenter EVO de Wagner. O SuperCenter EVO, da Wagner. Los generadores EPG S2. Os geradores EPG S2.
© ipcm
© ipcm
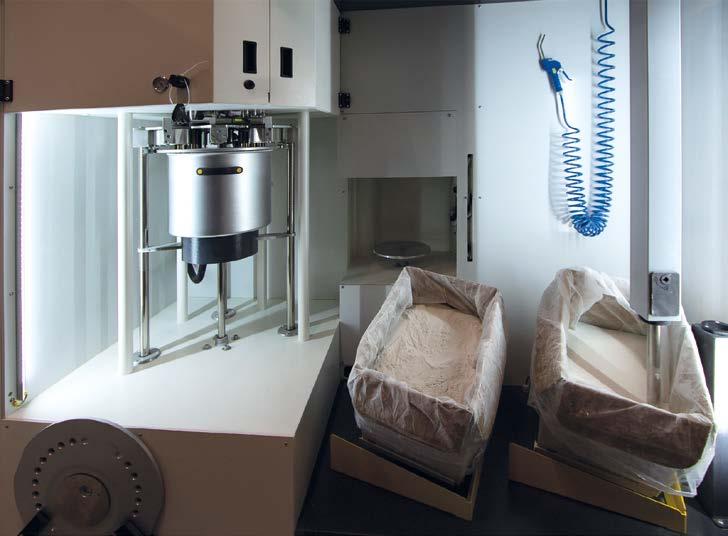
Interior del SuperCenter EVO con las dos celdas de carga de las cajas de polvo. Parte interna do SuperCenter EVO com as duas células de carga das caixas de pó.
Entrada en el horno de polimerización. Ingresso no forno de polimerização.
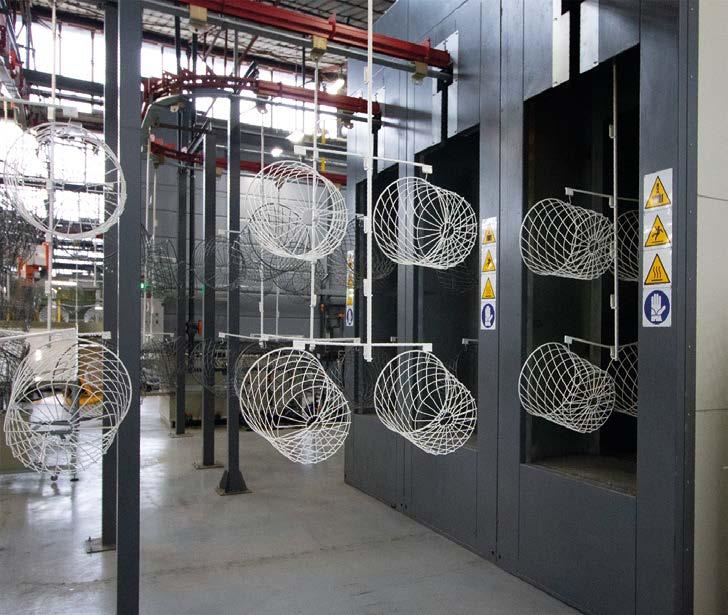
© ipcm gestionar como se desee, gracias al SuperCenter EVO, el centro de alimentación de polvo 4.0, el orgullo de Wagner». «Las mallas de alambre – interviene Scalabrino – son uno de los elementos más complejos de recubrir: las cestas de aproximadamente 30x40 cm de acero al carbono se caracterizan por tener poca superficie por pintar y mucho espacio libre, por lo que la dispersión del polvo es elevada. Además, según las indicaciones del cliente, el espesor de la película debía alcanzar las 50 micras y la principal dificultad fue conseguir este resultado en los cruces de la malla metálica. Gracias al sistema desarrollado por Wagner, actualmente podemos obtener una capa homogénea de pintura sobre toda la superficie del alambre, aplicando la cantidad correcta de polvo y recuperando el exceso». El corazón tecnológico de la instalación de pintura está constituido por el centro de alimentación de polvo cuyo sistema de pesaje integrado, además de mantener constante el polvo, permite también detectar su consumo. «El nuevo Powder Center es capaz de gestionar grandes lotes de producción y de mantener un control de los consumos gracias a la incorporación de dos celdas de carga en
ao SuperCenter EVO, o centro de pó 4.0, orgulho da Wagner“. “As malhas de fio metálico - diz Scalabrino – são um dos elementos mais complexos a serem revestidos: os cestos com cerca de 30x40 cm de aço carbono apresentam pouca superfície pintável e muito espaço livre, por isso a dispersão do pó é elevada. Além disso, de acordo com as indicações do cliente, a espessura da película deve atingir 50 μm e a principal dificuldade foi obter este resultado nas intersecções da malha metálica. Graças ao sistema desenvolvido pela Wagner, hoje conseguimos obter uma camada homogênea de tinta em toda a superfície do fio metálico aplicando a quantidade correta de pó e recuperando o excesso”. De fato, o coração tecnológico do sistema de pintura é a central de alimentação de pó, cujo sistema de pesagem integrado, além da manutenção constante do pó, também permite detectar o seu consumo. “O novo Powder Center consegue gerenciar
las que se posicionan y se pesan las dos cajas de polvo, y gracias al sistema de fluidificación que mezcla el polvo virgen con el que se recupera de la cabina» – interviene Rosada. «Se trata de una instalación de alta eficacia concebida para evitar el riesgo de sinterización, es decir, de aglomeraciones de polvo que podrían provocar descartes. El mantenimiento constante de la cantidad de polvo conlleva que su flujo sea constante hacia las pistolas mediante bombas Venturi de alta densidad las cuales utilizan una cantidad de aire de transporte inferior con respecto al anterior sistema Venturi. Para el control de las pistolas, el sistema está equipado con generadores EPG S2 que operan en combinación con el sistema de gestión central, totalmente automático y que puede almacenar hasta 200 recetas. Gracias al dispositivo de lectura de la cabina que reconoce la ubicación de las piezas en el transportador y detecta su perfil, la instalación puede activar las pistolas que deberán efectuar la aplicación y desactivar aquellas que, por el contrario, no deberán funcionar. Por último, otra solución técnica que caracteriza la cabina de SuperCube es la doble aspiración lateral, que sustituye a la de pavimento, para evitar las posibles depresiones del polvo aplicado en la parte central de la cabina: para nosotros esto supone también la correcta optimización de la pintura en artículos difíciles como las mallas grandes lotes de produção e manter o consumo monitorado, graças à integração de duas células de carga, nas quais duas caixas de pó são posicionadas e pesadas, e ao sistema de fluidificação que mistura o pó virgem com o recuperado pela cabine ”- diz Rosada. “É um sistema de alta eficiência projetado para evitar o risco de sinterização, ou seja, a aglomeração do pó que pode causar desperdício. Mantendo a quantidade de pó inalterada, se consegue um fluxo constante do mesmo para as pistolas, através de bombas Venturi de alta densidade, que utilizam uma quantidade de ar de transporte menor do que o sistema Venturi anterior. Para o controle das pistolas, o sistema é equipado com geradores EPG S2, que operam em conjunto com o sistema de gerenciamento central, totalmente automático e capaz de memorizar até 200 programas. Graças ao dispositivo de leitura da cabine que reconhece o posicionamento das peças na esteira e detecta a sua forma, o sistema pode acionar as pistolas que devem fazer a aplicação e desativar aquelas que não devem operar. Por fim, outra característica técnica da cabine SuperCube é a dupla aspiração lateral que substitui a aspiração no piso, para evitar qualquer depressão do pó aplicado na parte central da cabine: este aspecto também representa para nós a otimização efetiva da pintura em artigos difíceis, como as

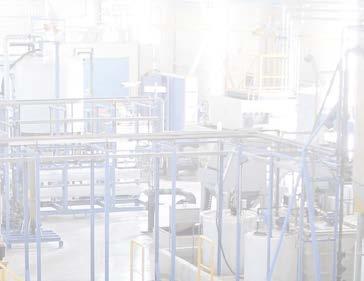
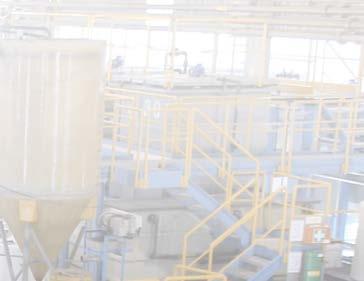
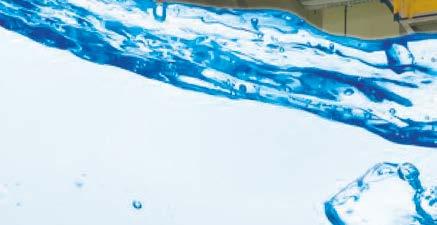
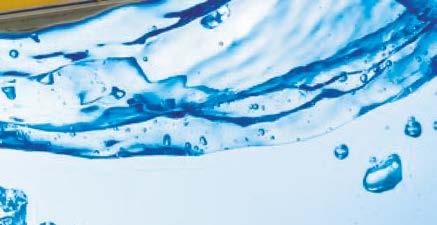

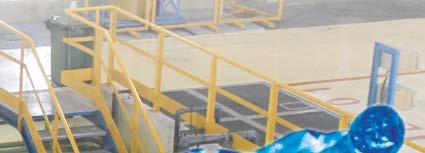
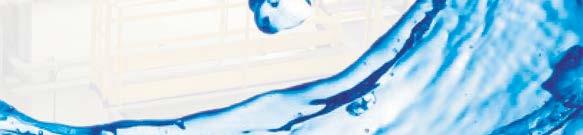
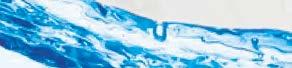
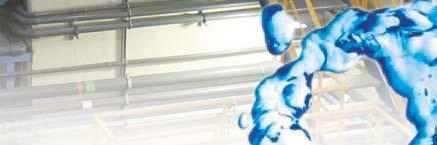
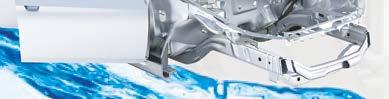
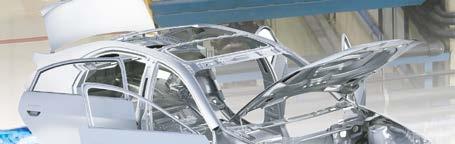
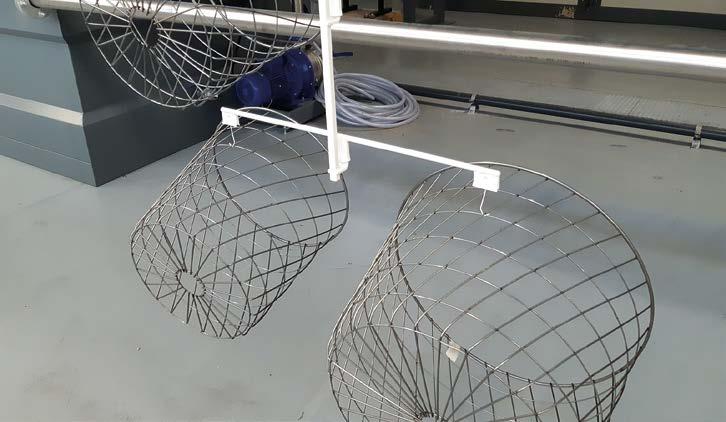
© Rostirolla
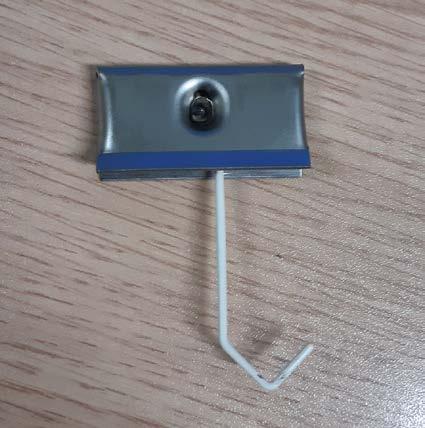
Detalle del peine P25. Detalhe do pente P25.
metálicas, no solo en términos de prestaciones, sino también de ahorro de consumo».
El proyecto no solo ha tenido en cuenta la necesidad de optimizar el proceso de pintura, sino también algunos aspectos que habitualmente se consideran secundarios en una línea de tratamiento superficial, como la colocación de ganchos y bastidores en el transportador. «Para este tema nos hemos encomendamos a la empresa Rostirolla Srl especializada en la producción de ganchos, bastidores y enmascarados – afirma Scalabrino – la cual nos presentó el proyecto de un nuevo tipo de bastidor justo cuando estábamos buscando una solución que optimizara nuestra capacidad productiva». Simone Rostirolla, titular junto a su hermano Pierluigi de Rostirolla Srl, explica las demandas del mandante: «Dradura buscaba una solución para colgar las piezas que fuese, antes que nada, modular para optimizar la eficacia de la instalación con artículos de diferentes formas y tipologías, robusta y duradera y, al mismo tiempo, fácil de manipular. Además el gancho de sostén debía poder sustituirse fácilmente, de manera que no fuera necesario despintar cada día todo el bastidor. Hemos propuesto nuestro sistema de suspensión P25 combinado con el sistema de acople de los ganchos HB. Este sistema se caracteriza por una barra central portante y una varilla horizontal con cajitas de chapa soldadas HB que albergan un gancho de alambre de Ø2mm. Todos los componentes utilizados para el bastidor de Dradura están estandarizados y se han sometido a ensayos a lo largo de los años por lo que garantizan su buen funcionamiento incluso tras numerosos ciclos de pintura. Por supuesto, las dimensiones de nuestros sistemas (altura y tipo de mango, altura útil, distancia y número de posiciones) se pueden personalizar».
© Rostirolla
El gancho GHB de 2 mm de diámetro. O gancho GHB, com diâmetro de 2 mm.
grelhas de metal, não só em termos de desempenho, mas também de economia de consumo“.
Alta produtividade da nova linha de pintura O projeto levou em consideração não só a necessidade de otimizar o processo de pintura, mas também alguns detalhes geralmente considerados secundários em uma linha de tratamento de superfície, como o posicionamento dos ganchos e penduradores no transportador. “Para isso contratamos a empresa Rostirolla Srl, especializada na produção de ganchos, penduradores e mascaramento - diz Scalabrino - que nos apresentou o projeto de um novo pendurador, justamente quando estávamos procurando uma solução para otimizar a nossa capacidade produtiva“. Simone Rostirolla, co-proprietário com o seu irmão Pierluigi, explica os pedidos dos clientes: “A Dradura estava procurando uma solução para pendurar as peças, que acima de tudo fosse modular, para otimizar a eficiência do sistema com artigos de várias formas e tipos, robusta e durável e, ao mesmo tempo, leve para manusear. Além disso, o gancho de suporte precisava ser facilmente substituído, de modo que não precisasse decapar todo o pendurador todos os dias. Propusemos nosso sistema de penduramento P25 combinado com o sistema de ganchos HB. Este sistema é caracterizado por uma coluna central e uma barra horizontal com latas soldadas HB, que acomodam um gancho de fio metálico de Ø2mm. Todos os componentes utilizados para o pendurador Dradura são padronizados e testados ao longo dos anos e garantem o bom funcionamento, apesar dos inúmeros ciclos de pintura. Claro que as medidas dos nossos sistemas (altura e tipo de alça, altura útil, distância e número de posições) podem ser personalizadas”.
«Ahora, para cada nuevo producto que debe ser tratado en la instalación – explica Scalabrino – preparamos la muestra y colaboramos con la oficina técnica de Rostirolla y con la de Wagner para decidir juntos la orientación y la disposición óptimas de los artículos y contribuir así a obtener un pretratamiento y una aplicación eficaces del polvo, como en el caso de las cestas que se están tratando actualmente colgadas de 4 en 4 en cada bastidor».
Conclusiones
Maurizio Scalabrino concluye que la elevada capacidad de producción de la línea ha tenido consecuencias importantes también desde el punto de vista de la lean production: «La fase de pintura se sitúa entre las elaboraciones mecánicas y el embalaje automático que se realiza mediante robots que envuelven con película extensible. Actualmente estamos trabajando en un proyecto de lean producción para optimizar el flujo de producción el cual, debido a la velocidad de la instalación de pintura, necesita aún pequeños buffers de acumulación tras la polimerización (unas 10 cestas). Además, en el tema del control de la producción, gracias al sistema de gestión automática de la pintura proporcionado por Wagner, el responsable del taller de pintura puede dedicar su tiempo a otras funciones: en caso de problemas, el sistema está equipado con alarmas que avisan de los posibles fallos o de si hay que sustituir la caja vacía del polvo cargado». Dado que un importante cliente se mostró muy satisfecho con el producto acabado, Dradura ha invertido mucho en este proyecto y ha efectuado más pedidos por lo que en el futuro manejará una producción con cantidades impresionantes. «A tal propósito, ya estamos estudiando una modificación del transportador monorraíl para bajar la cadena a fin de recuperar espacio y emplear un tercer nivel de altura para la suspensión de los bastidores: esta medida nos permitirá pintar un 33% más de cestas y aumentar aún más nuestra capacidad productiva confiando en las elevadas prestaciones de pintura que nos brinda esta nueva línea». “Então, para cada novo artigo a ser tratado pelo sistema - explica Scalabrino - preparamos a amostra e discutimos com os departamentos técnicos da Rostirolla e da Wagner, para identificarmos juntos a orientação e a disposição ideais dos artigos e, assim, contribuir com o bom resultado do pré- tratamento e aplicação do pó, como no caso dos cestos atualmente em produção pendurados 4 de cada vez, em cada quadro“.
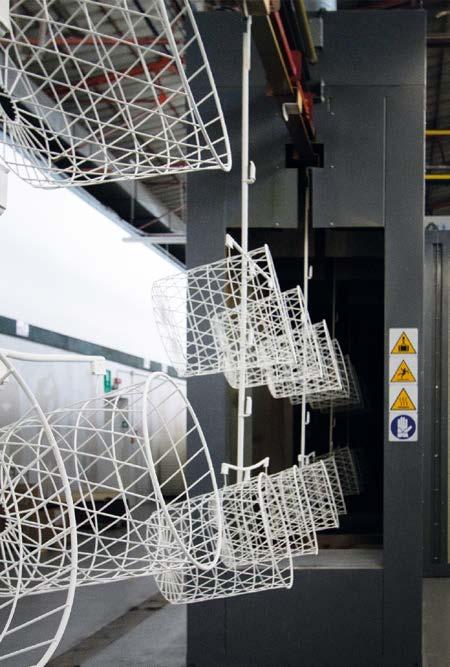
Conclusão Maurizio Scalabrino conclui que a elevada capacidade de produção da linha teve consequências importantes também em termos de lean production: “A pintura fica entre o processamento mecânico e a embalagem automática, feita por meio de robôs que embrulham com filme. Atualmente estamos realizando um projeto de lean production para otimizar o fluxo de produção que, devido à velocidade do sistema de pintura, ainda se caracteriza por pequenas áreas de acúmulo póspolimerização (cerca de 10 cestos). Além disso, em termos de controle de produção, graças ao sistema de gerenciamento automático da tinta, fornecido pela Wagner, o chefe do departamento de pintura pôde dedicar seu tempo a outras funções: em caso de problemas, o sistema está equipado com alarmes que sinalizam qualquer mau funcionamento ou que a caixa de pó vazia deve ser substituída”. Como um importante cliente ficou muito satisfeito com o produto acabado, a Dradura investiu bastante neste projeto e orçou novos pedidos, por isso terá que gerenciar volumes de produção impressionantes. “Com essa previsão, já estudamos uma modificação no transportador monotrilho, para abaixar a correia e otimizar o espaço, e aproveitar um terceiro nível para pendurar os ganchos: isto irá permitir pintar 33% de cestas a mais e aumentar ainda mais a nossa capacidade de produção sabendo do alto desempenho de pintura que esta nova linha nos garante”.
Después de la pintura, las cestas se dirigen a la zona de embalaje.
© ipcm