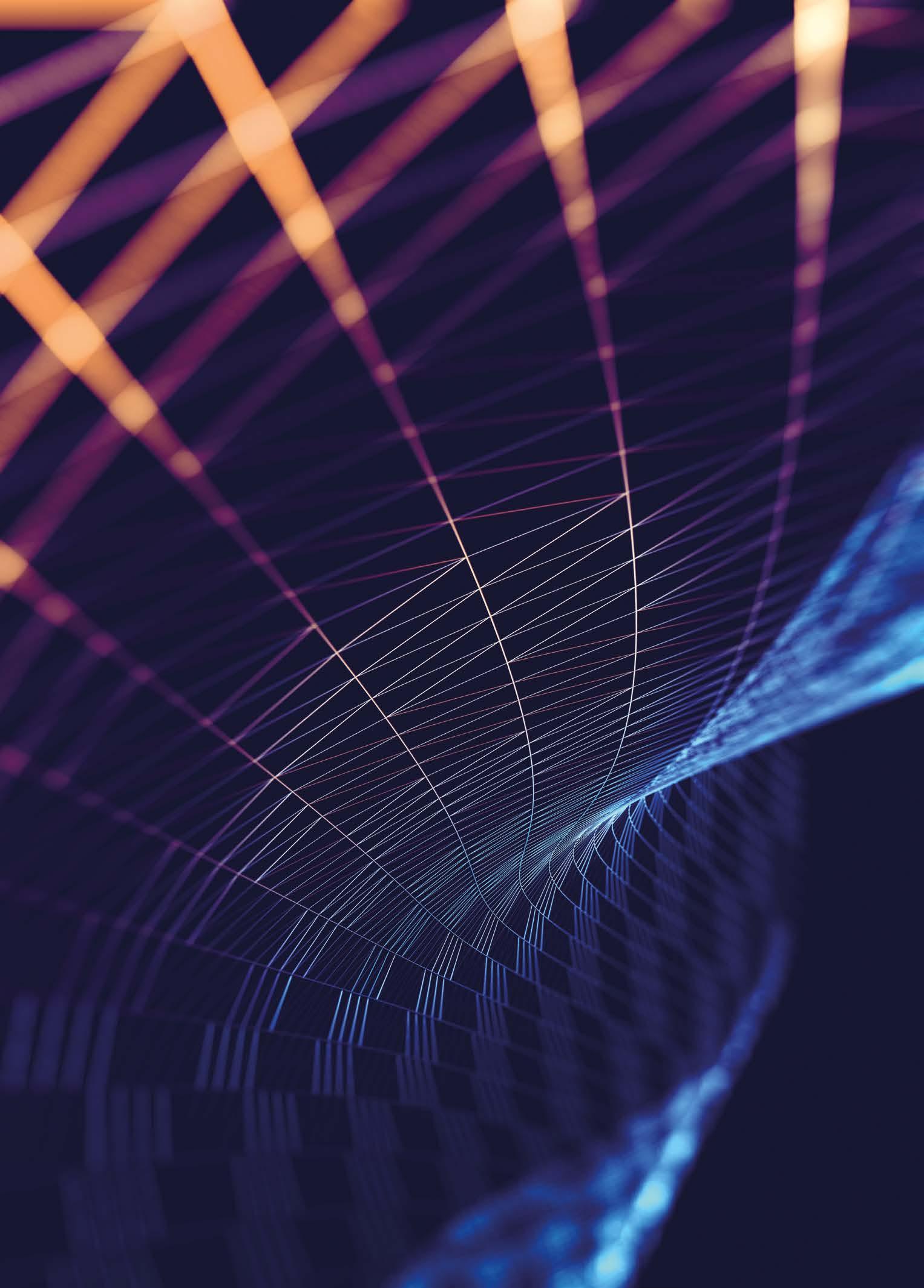
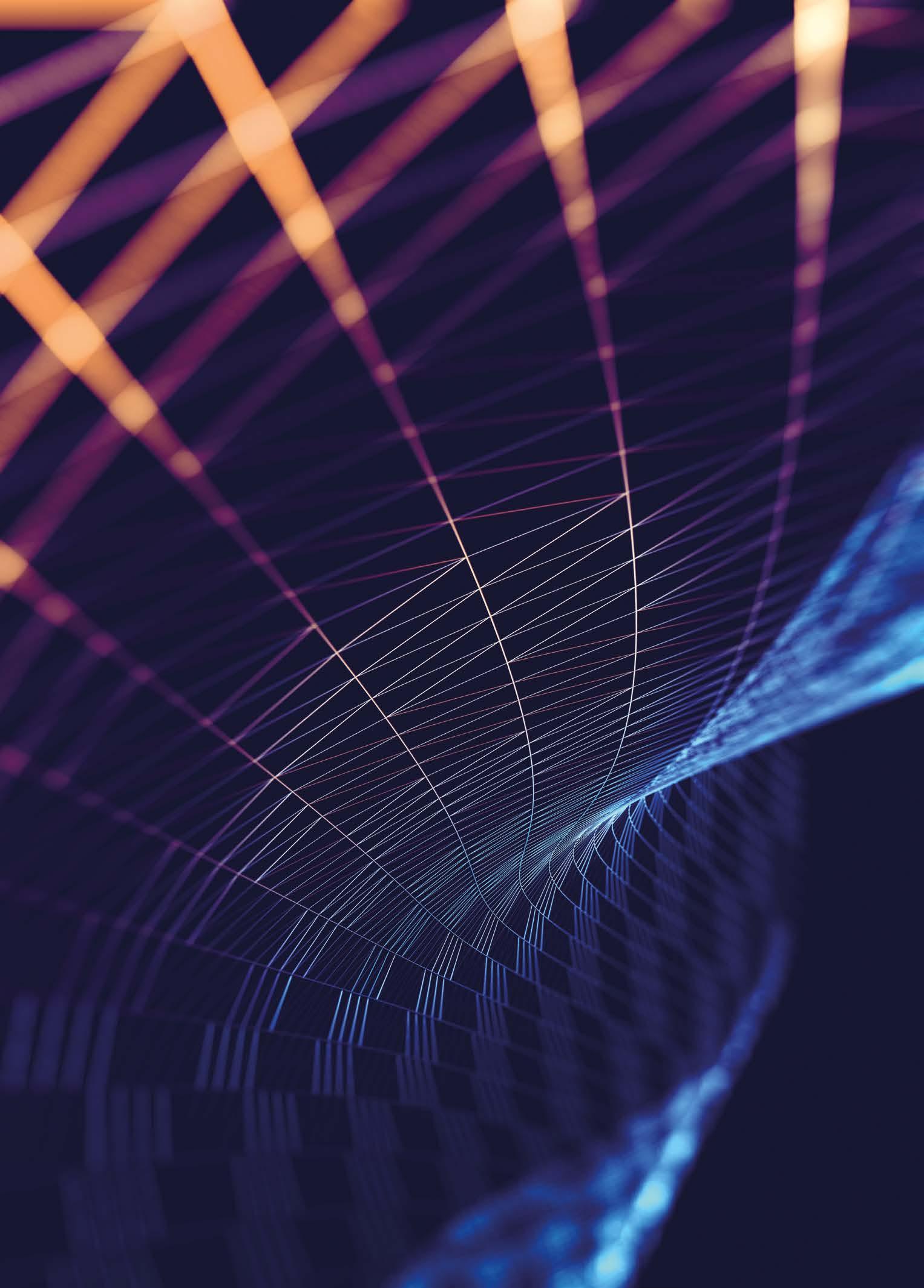
Inocart Powder Manual Coating Equipment
User-friendly and ergonomic manual powder gun
LIFETIME FINISH QUALITY: Long life waterfall durability and HV performance
BALANCED AND ERGONOMIC DESIGN: No repetitive strain damage, less fatigue
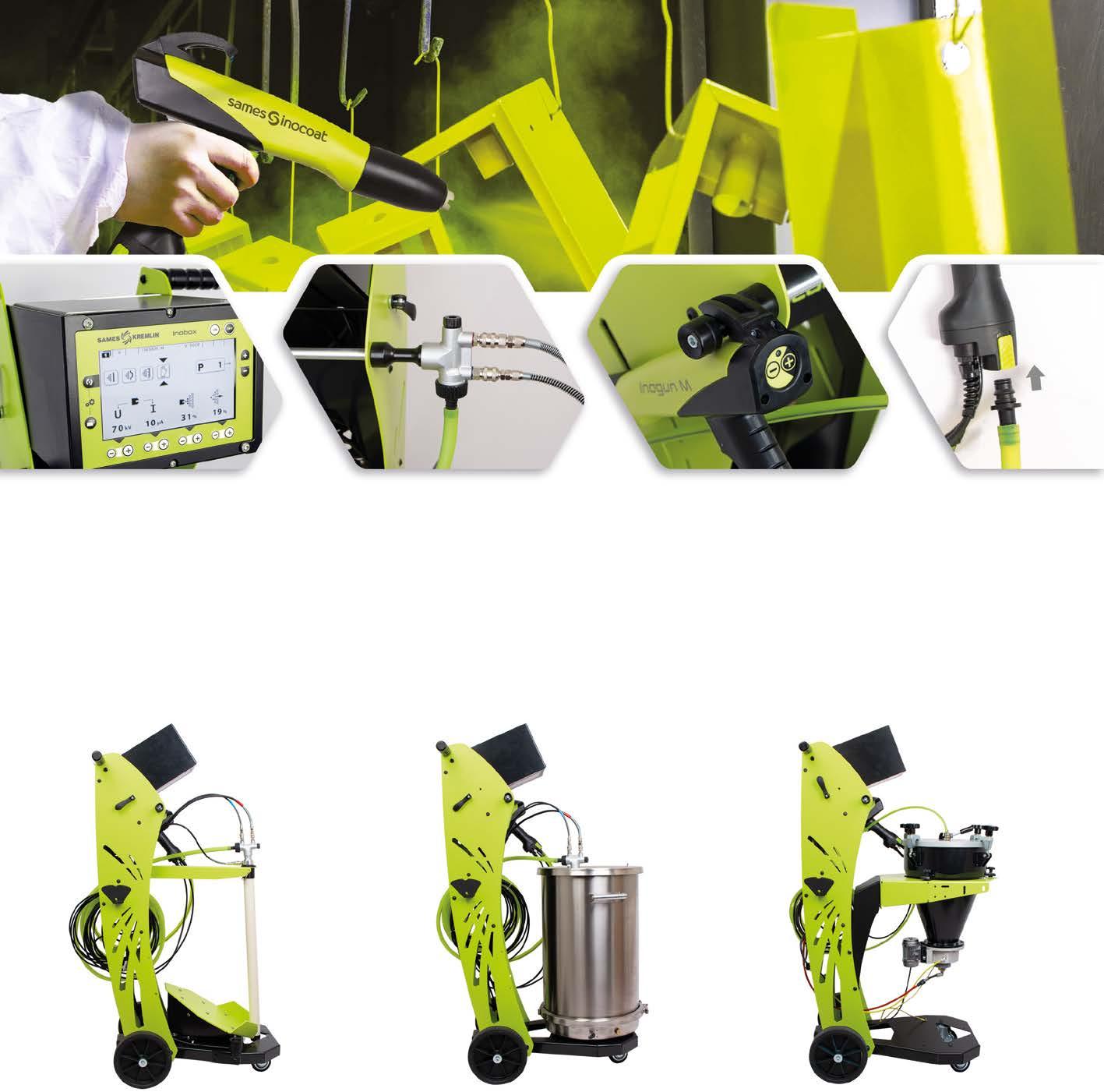
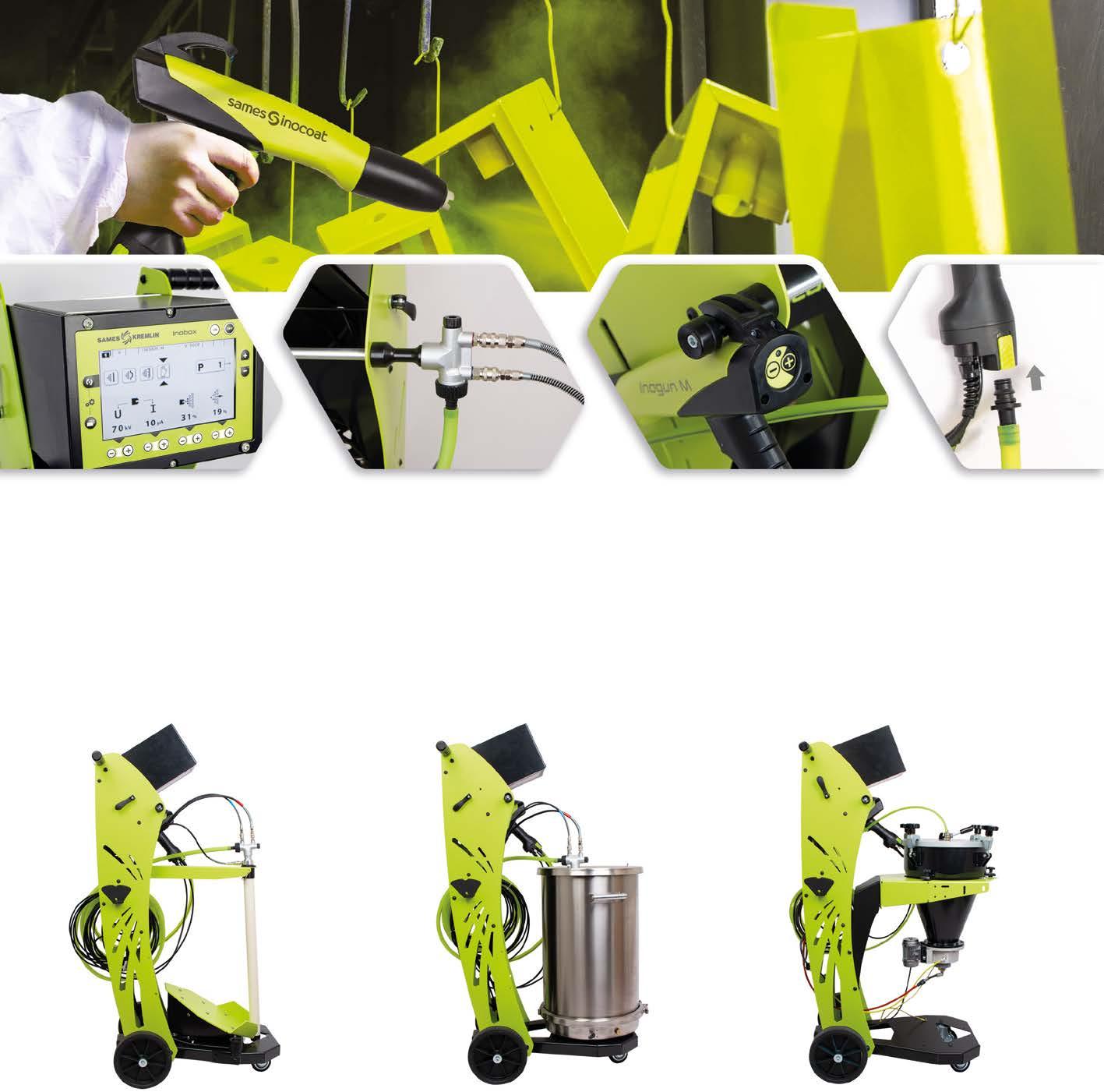

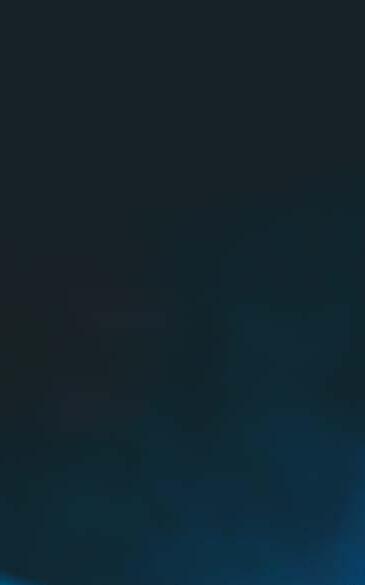
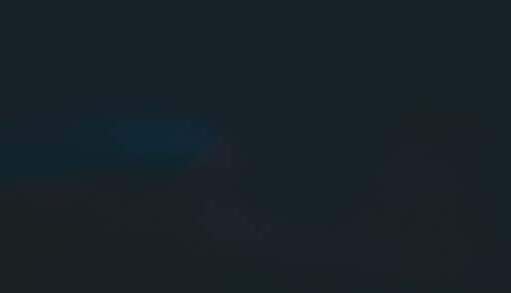
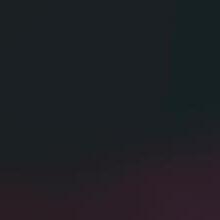
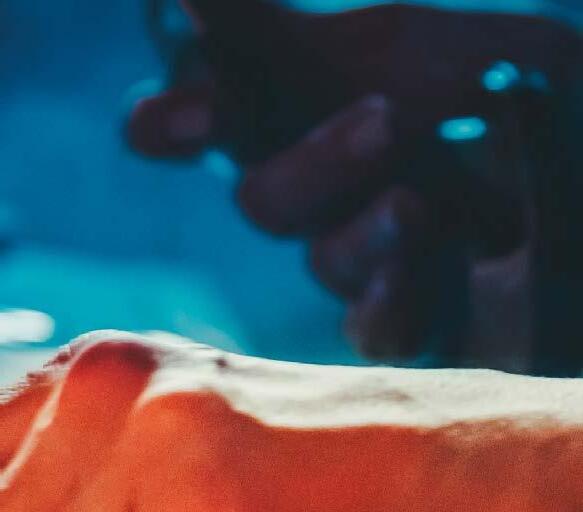
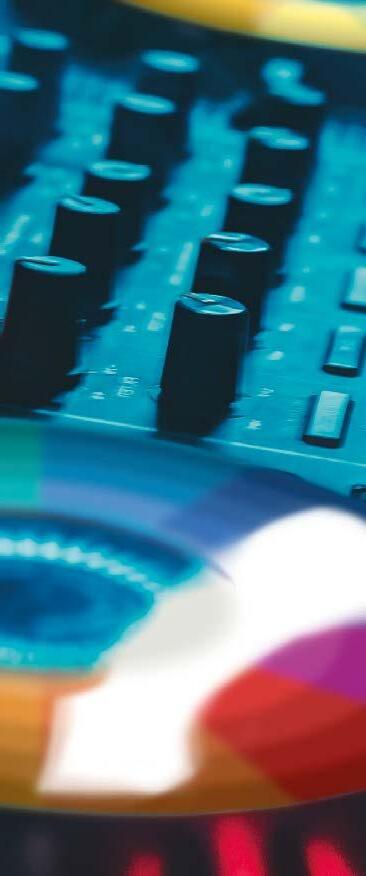
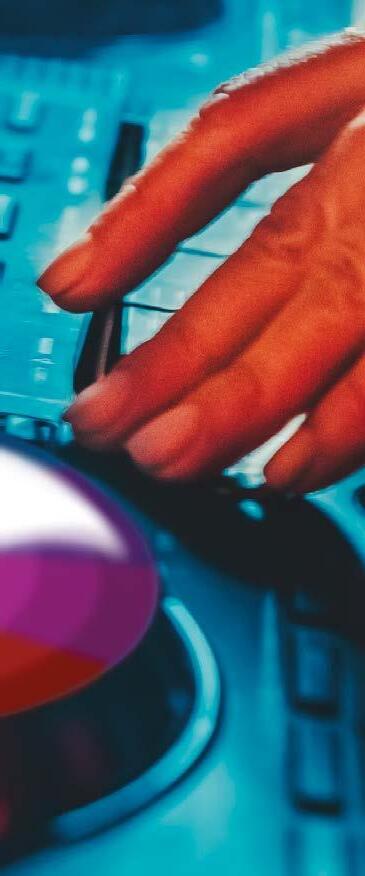
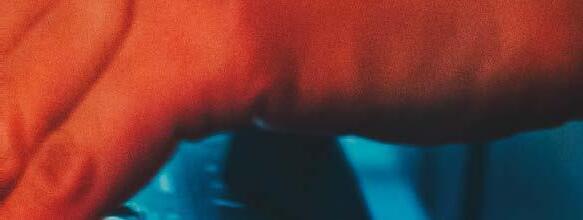
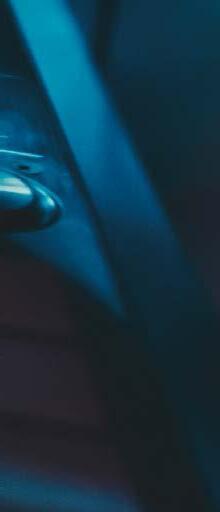
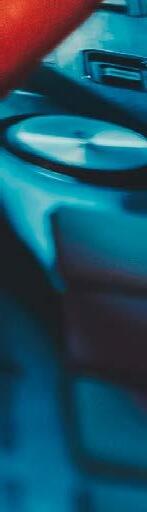
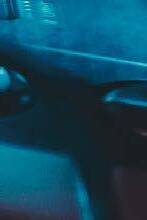
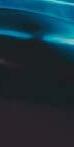
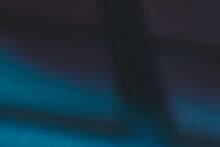

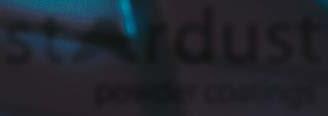

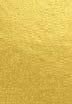
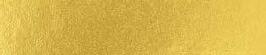
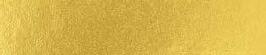
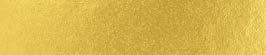
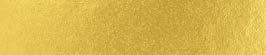




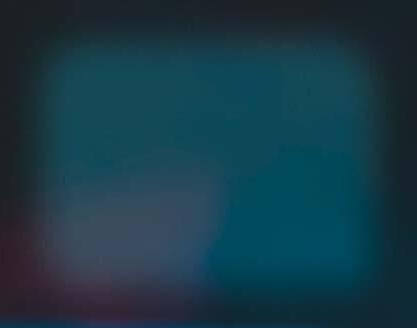


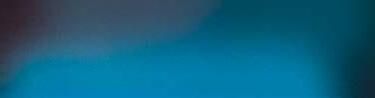
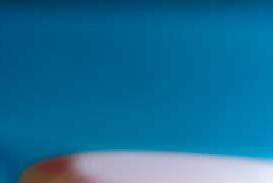


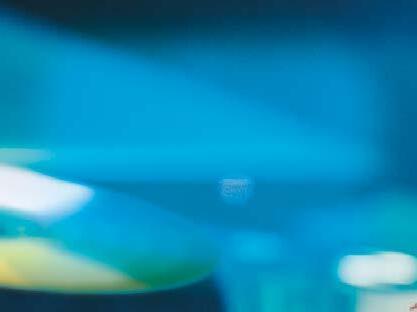
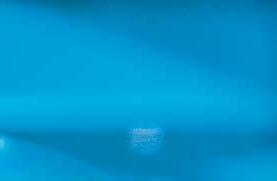
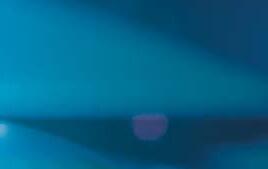

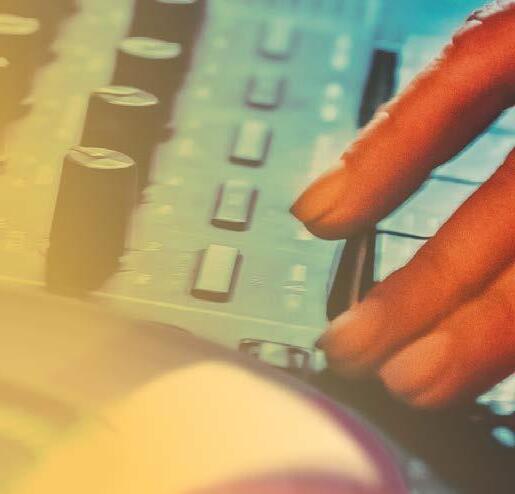
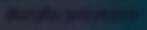
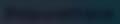

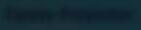


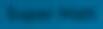


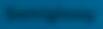











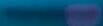

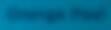



North America’s Largest Metal Forming, Fabricating, Welding and Finishing Event
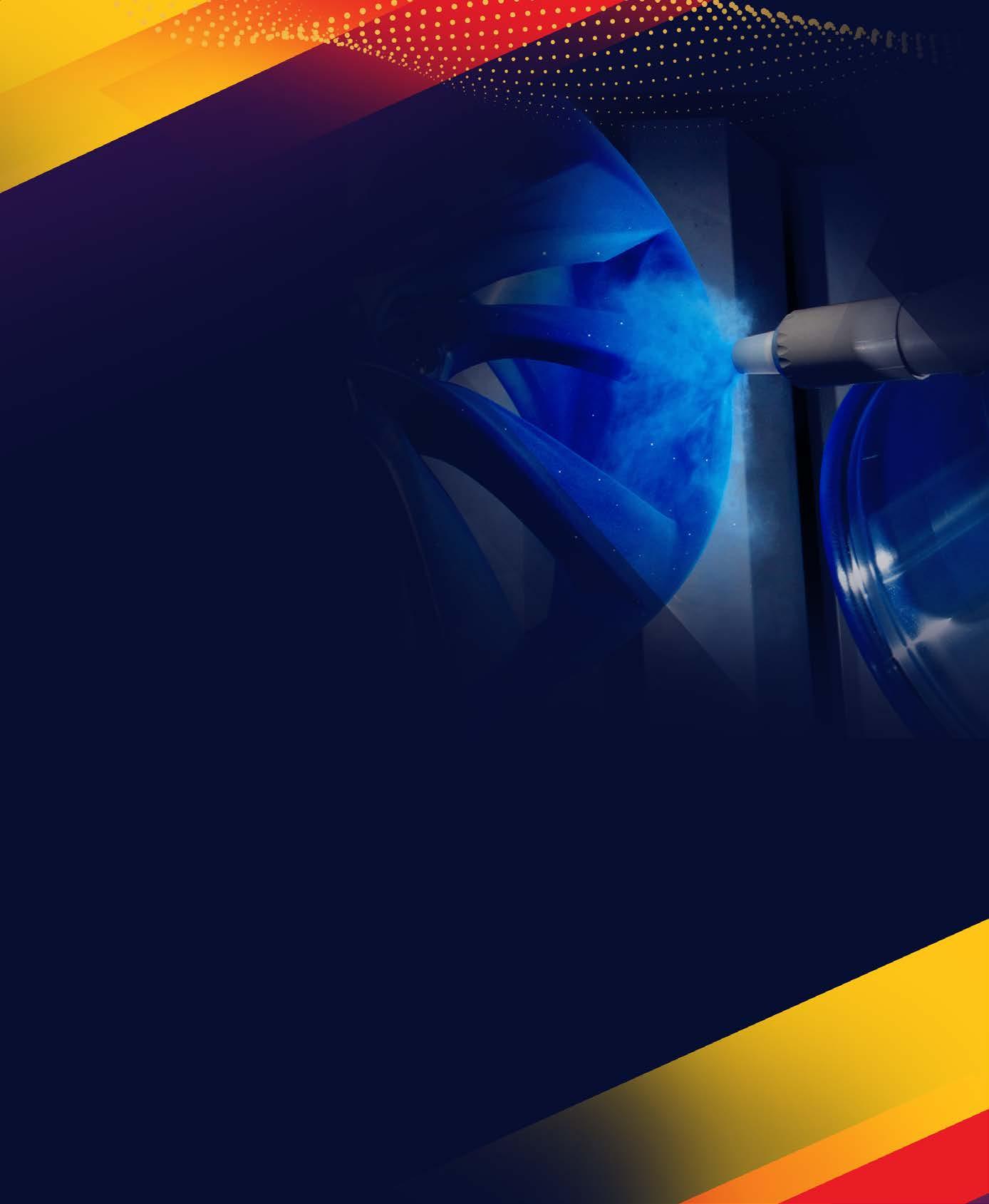
Driving Manufacturing Forward
Technology is advancing at a rapid pace. FABTECH brings the industry together to see the innovations transforming manufacturing.
Explore the latest trends, network with peers, and discover the solutions to take your business to the next level.
SEPTEMBER 11-14, 2023
Chicago, IL | McCormick Place
CLEAN IT. COAT IT. CURE IT.
CLEAN IT. COAT IT. CURE IT.
CUSTOM BUILT Engineered finishing systems: Blast, Pretreatment, Conveyors, Booths, applicators, robotics, and ovens.
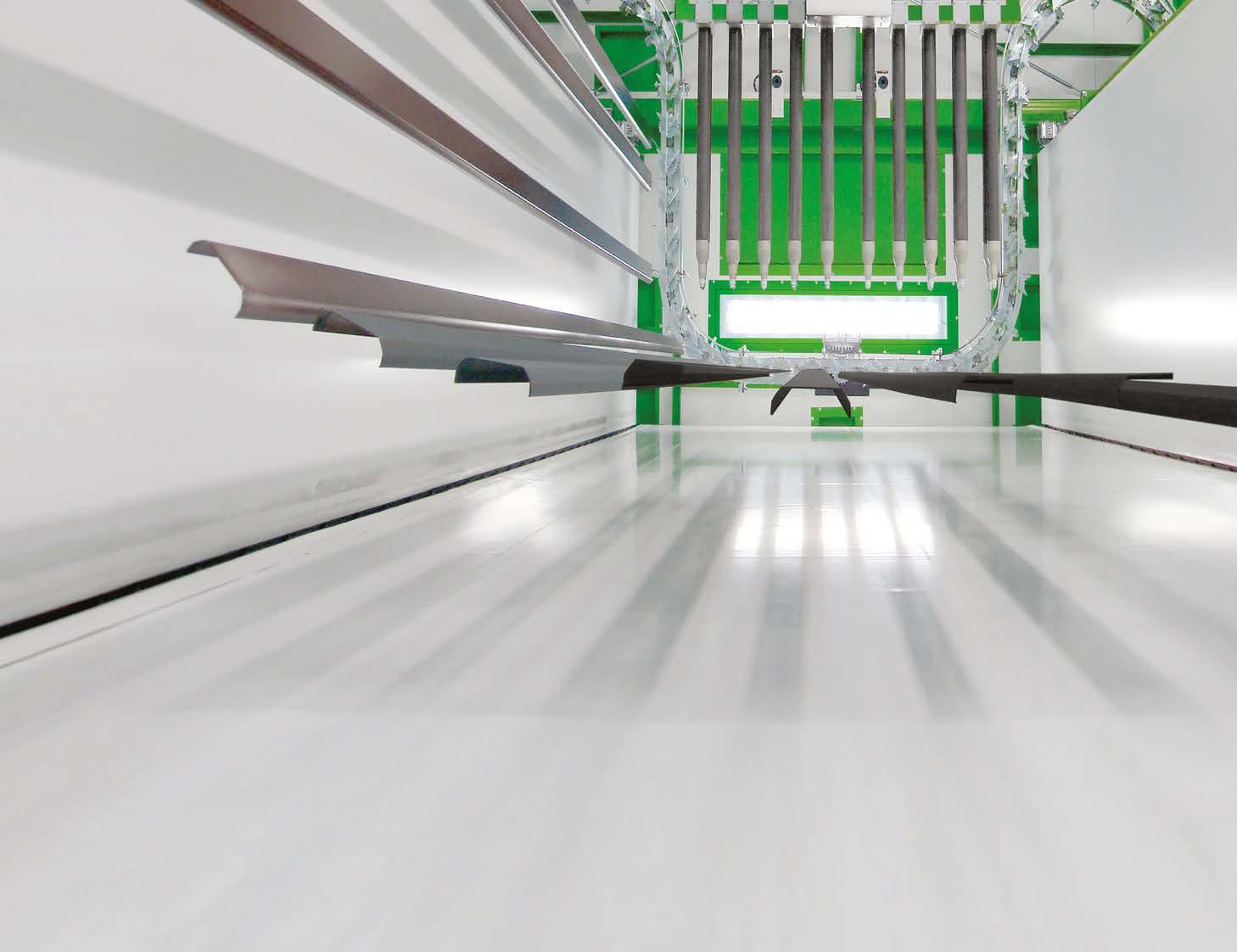
Total Finishing Systems is a leading designer and integrator of high-quality and complex industrial finishing systems. Whether you need an in-depth process analysis or require finishing equipment and components, our equipment exceeds expectations and our innovation and automation is industry leading.
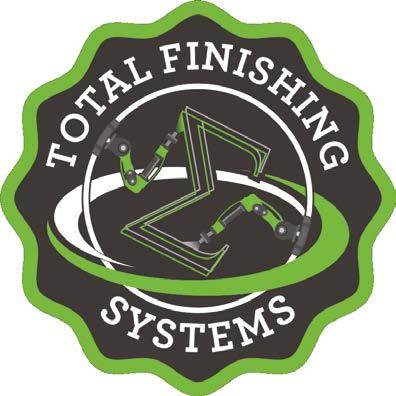
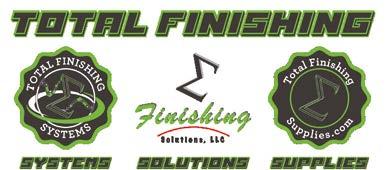
HIGHLIGHT OF THE MONTH
Srl
36
Market Trends in the Industrial Water Treatment Sector: An Analysis by Idrotecnica FOCUS
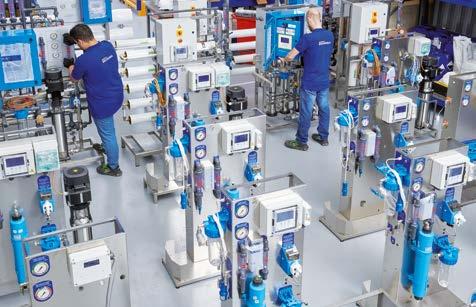
FOCUS ON TECHNOLOGY
62
58 RESEARCH BREAKTHROUGH
The ‘Invisible’ Cellulose Coatings that Mitigate Surface Transmission of Pathogens
60 ROAD TO 2050
EcoBell4: Application Efficiency of up to 98% Saves Huge Amounts of Paint and Rinsing Agent
68 HIGHLIGHT OF THE MONTH
Lechler Tech: Industrial Coatings for Every Opportunity
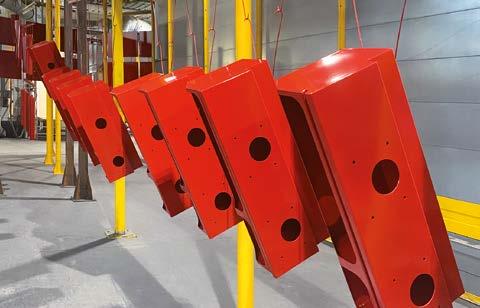
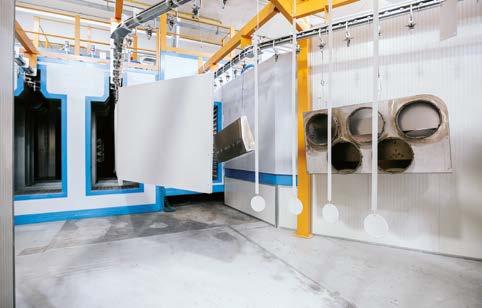
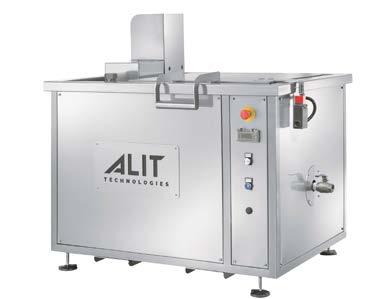
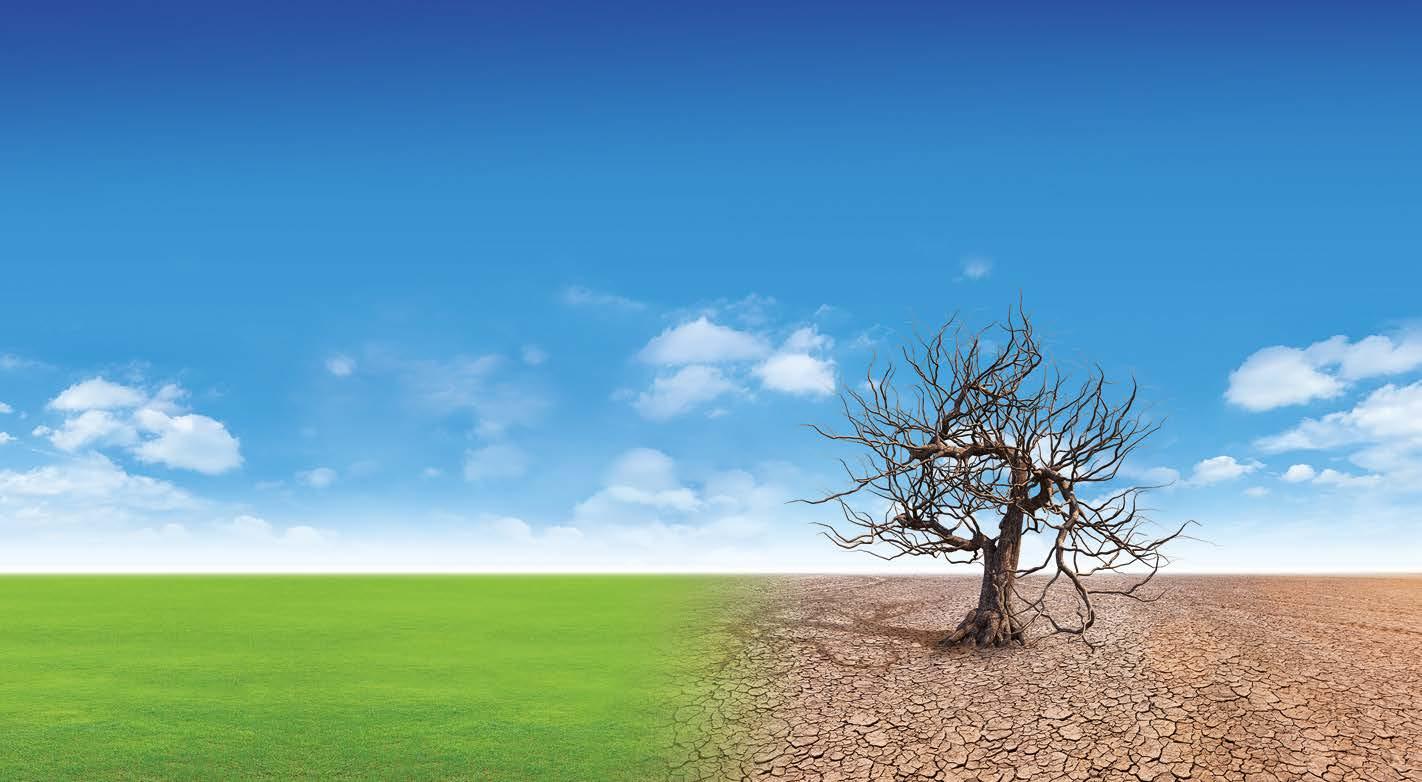
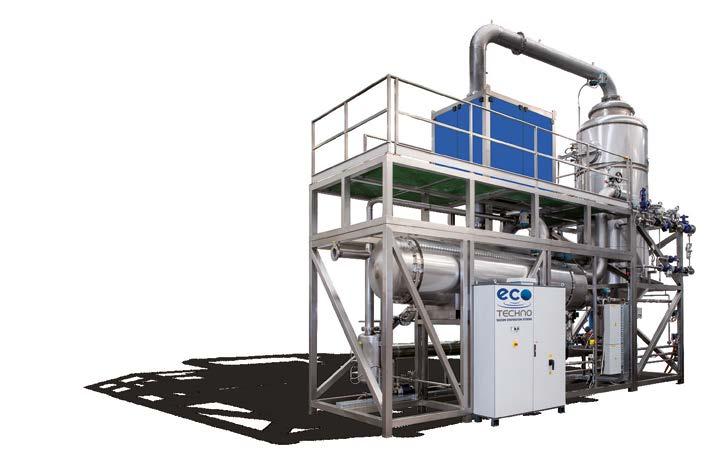
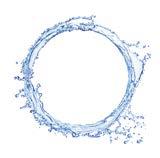
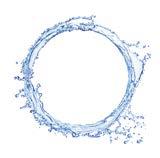
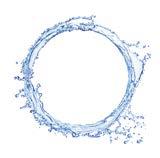
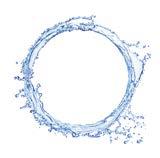
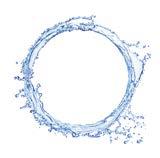
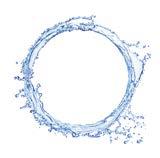
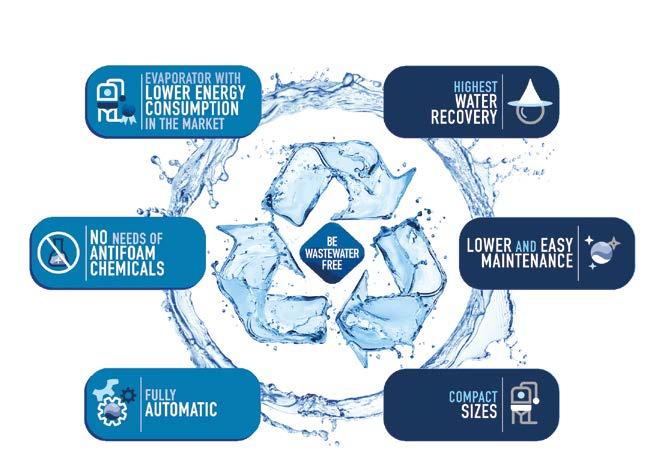
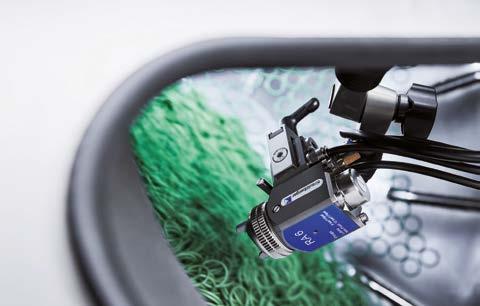
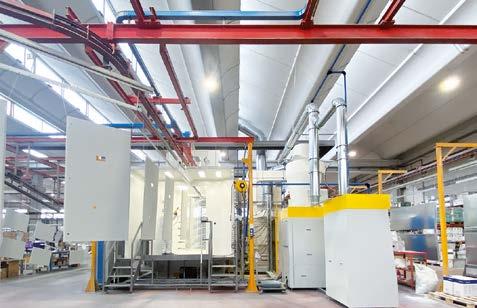
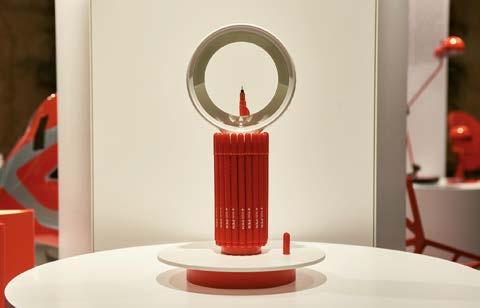
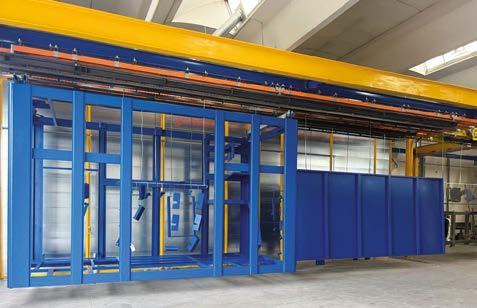
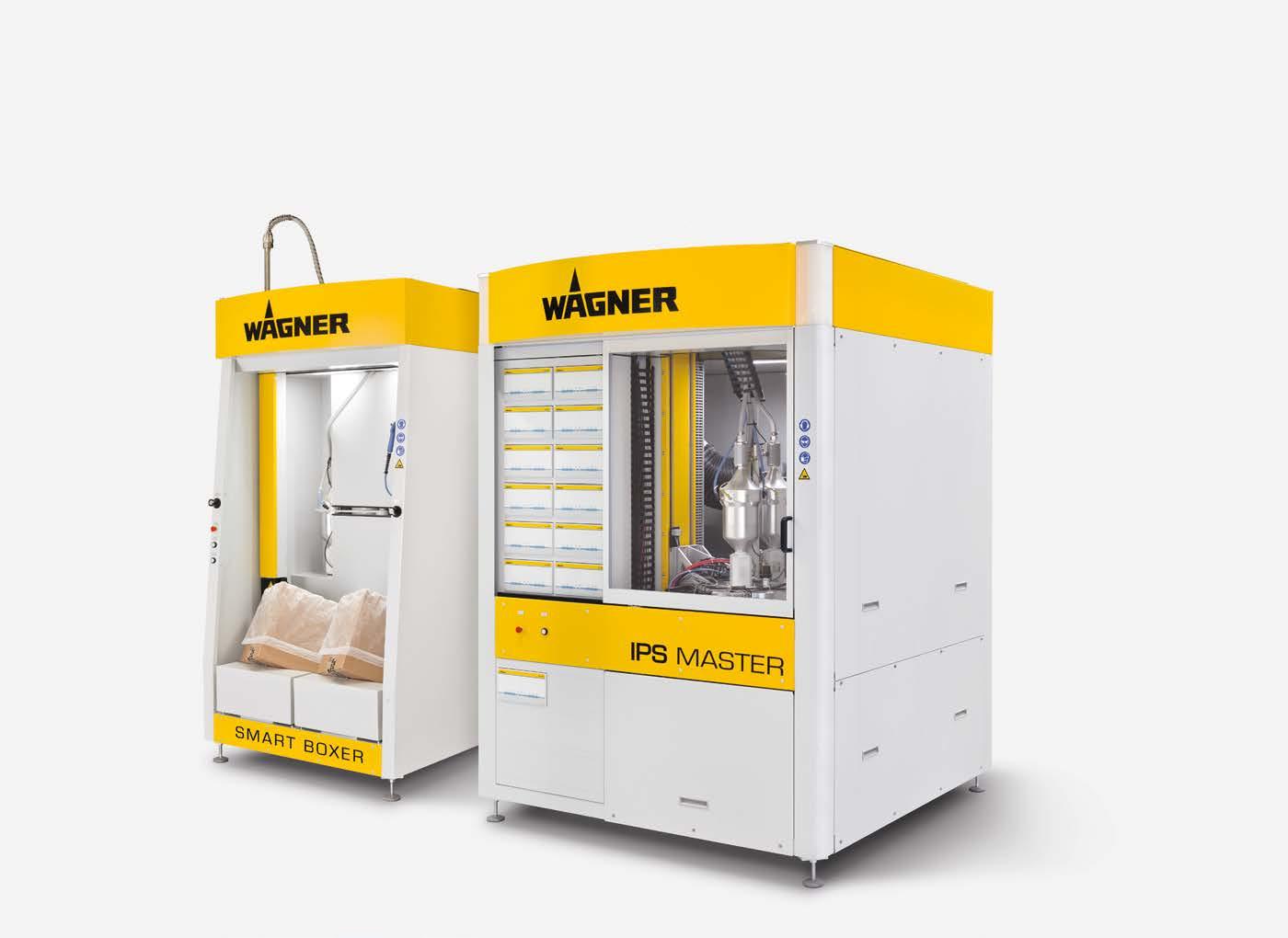
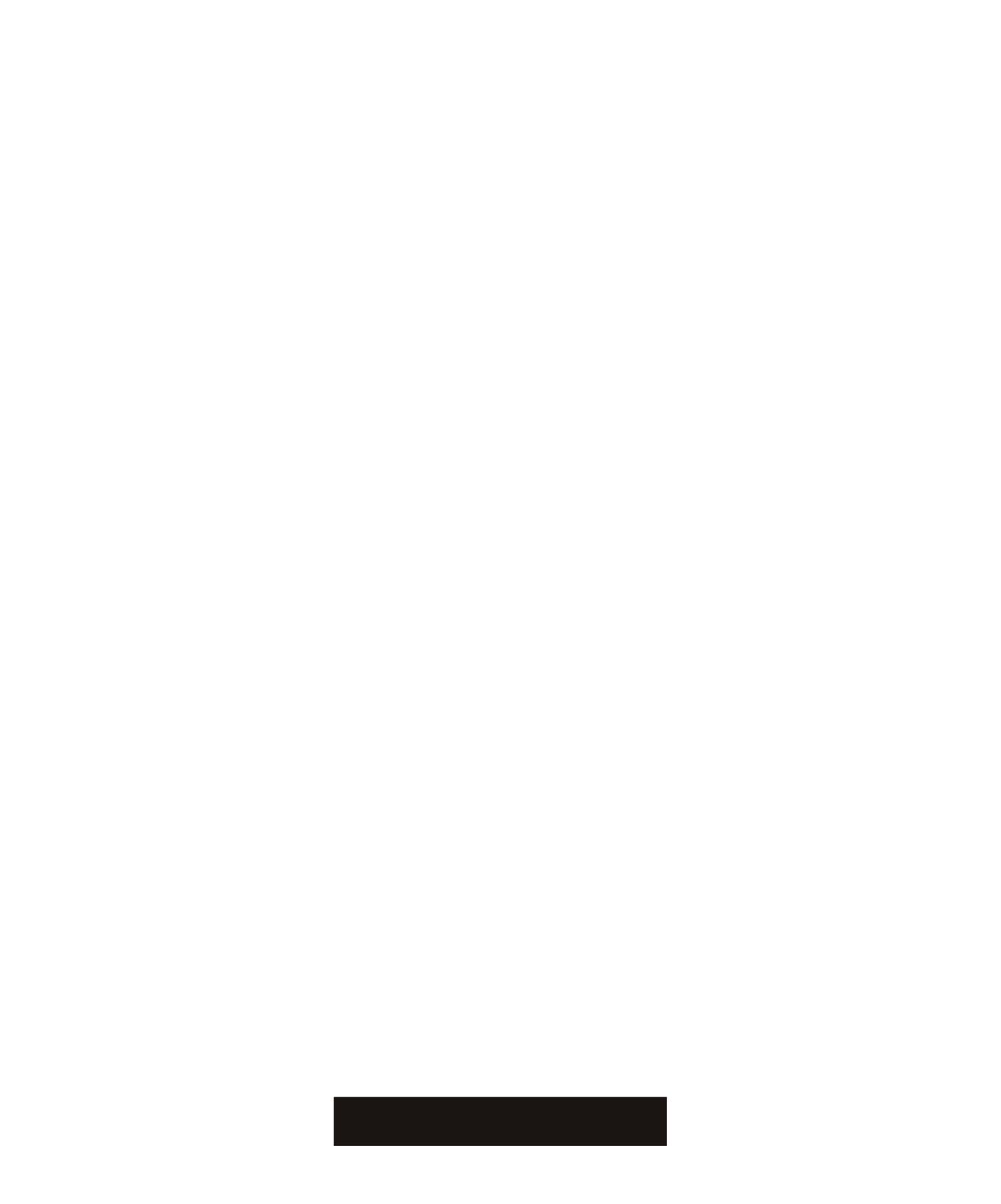
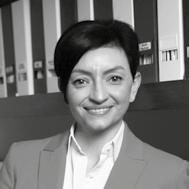
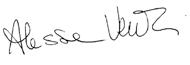
We are living in what sociologists and philosophers define as the information society, a concept familiar and dear to all those who – like me – have studied communication techniques and dynamics. In this society, whose pillars are information technology and telecommunications, an intangible good, namely information, prevails over the industry and the service sector.
As an operator in the communication sector, and a niche one at that, it is therefore natural to wonder what is the role of specialised information in the contemporary world, with information being placed in such a central position and considered a resource and a factor of social and economic development, growth, and cultural richness1
Specialised technical information, such as that which ipcm® has been offering for almost fifteen years with its four magazines devoted to surface treatment-related topics in the general, heavy, and automotive industries, is a source of in-depth knowledge, industrial culture, and understanding of innovation.
ipcm®, in particular, provides information that captures the essence of innovations and connects it with industrial reality. Through our reports about the end-users of surface treatment technologies, the conversation truly moves from abstract to concrete. Our articles portray the market, its needs, and how it is developing, growing, and incorporating new technologies. They assess its efficiency, effectiveness, advantages, and disadvantages with a tone of voice that is as objective as possible.
They provide information that breaks away from the clinical cleanliness of scientific or technical articles written by companies’ laboratories.
High-quality information that is verified and verifiable, sometimes even uncomfortable because it opens up to disruptive technologies deviating from the past and from what is already known.
First-hand information that is very costly for the publisher, because it involves travel, transfers, hours of work. But also the type of information most appreciated by readers, who can recognise themselves, their companies, and their needs in it.
In a way, even an “insurance policy” against the kind of distinctly advertising-oriented information that many international magazines thrive on.
This vertical approach to information and such an extreme specialisation of content have helped us build a community of readers with whom we can engage in a conversation that from printed magazine crosses over into digital channels, our social media, and our website, which is not a simple platform to publish our issues online but is also aimed at offering daily first-hand news, expanding our magazines’ content, and fostering contact among businesses, between supply and demand.
With the hope that you, our readers, our most valuable resource, will continue to appreciate such content, but also to give us constructive criticism if necessary and even to start technical debates, I wish you a good summer and happy reading of this summer issue of ipcm®
1 Source: https://www.treccani.it/enciclopedia/societa-dell-informazione_%28Enciclopedia-della-Scienza-e-della-Tecnica%29/
AkzoNobel Powder Coatings Introduced the e-Commerce Platform My Interpon Portal
My Interpon Portal enhances the digital services of AkzoNobel, providing quick and easy access to information on powder coatings.
AkzoNobel has launched My Interpon Portal, an extended digital e-Commerce platform with enhanced features and functionalities that will ensure customers will have fast and easy access to information and products for powder coating.
The online resources platform helps coaters to discover the range of Interpon powder coatings and also experience how the multitude of colours and textures will perform, thanks to a 3D lightbox colour visualisation tool. As a matter of fact, its functionality enables customers to easily navigate the site and search for, find and compare hundreds of powder coatings.
“The launch is further evidence of the commitment to customers of AkzoNobel. We strive to make things easier for our customers with practical tools and support that makes us collectively more efficient,” has declared Jeff Jirak, the director of the Powder Coatings business unit of AkzoNobel. “A significant development of our existing e-commerce
site, we will continue to enrich and enhance the functionality of My Interpon Portal with new features to help customers access the powder coatings they need for the most urgent of urgent jobs.”
My Interpon Portal makes it easy to manage new, ongoing and repeat orders. Users can instantly visualise the products in stock – with the corresponding technical specification data which can be downloaded –and how quickly they can be shipped.
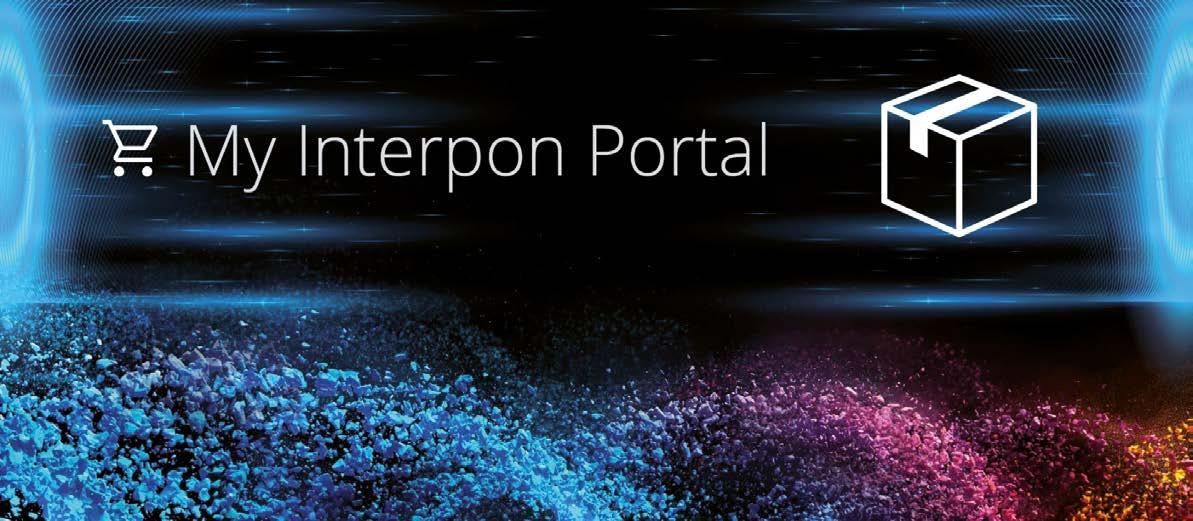
In addition, the Track and Trace feature enables to check how the order is progressing, while past and present invoices can also be accessed, reviewed, printed and filed.
The online portal is already live in United States, United Kingdom, Germany and Australia, and is being rolled out in Canada, Czech Republic, Poland, India, and New Zealand in the upcoming months.
For further information: www.interpon.com
ChemQuest Appointed
Eric Casebolt as New Director
Eric Casebolt will support ChemQuest to improve its business strategy services for the specialty materials industry.
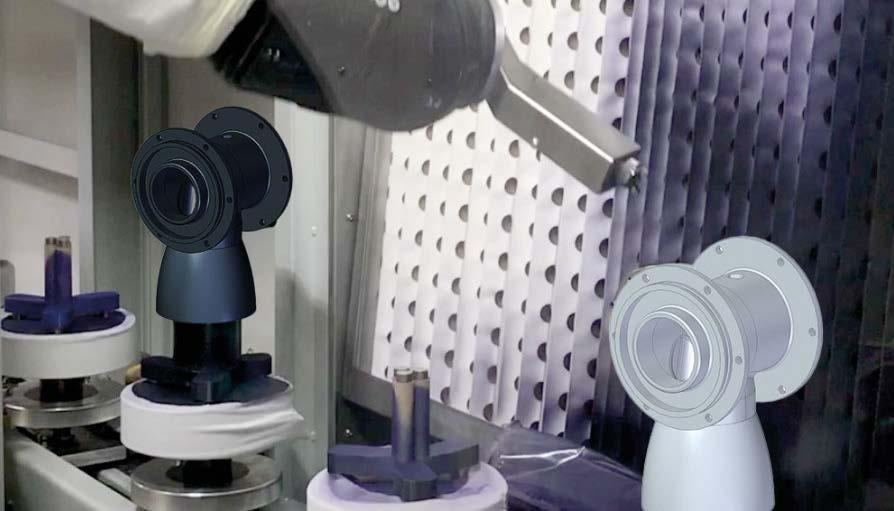
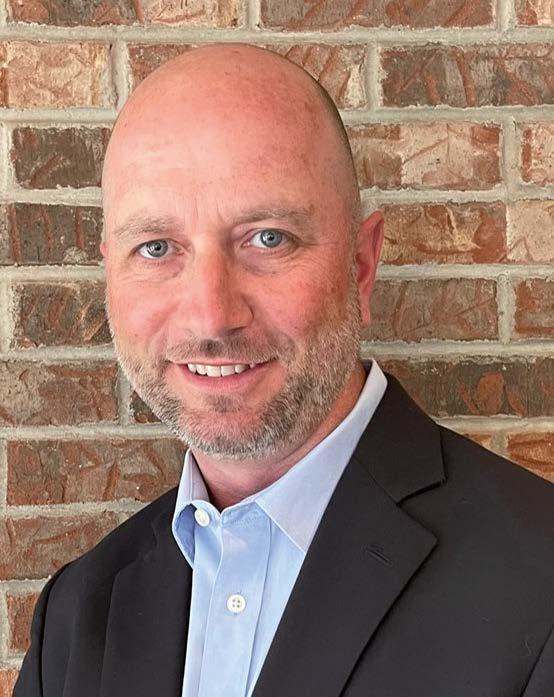
The ChemQuest Group has recently announced that it has named Eric Casebolt as a new director of the company. Casebolt has a vast experience in managing international businesses and a deep knowledge of the additives used in coatings, packaging and construction applications. So, he will support ChemQuest by focusing on market development, product innovation and business strategy services. “Eric has had an accomplished career, excelling in business development and strategy. In addition, I anticipate that his work building innovation pipelines for diverse product lines will bring value to our teams working on product development at ChemQuest Technology Institute and ChemQuest Powder Coating Research. I’m delighted to have him on the team,” has stated Daniel Murad, the CEO of ChemQuest. The newest director of ChemQuest holds three important qualifications: a bachelor’s degree in chemistry from the University of Wisconsin Parkside, a master’s degree in chemistry from the DePaul and an MBA from the Wake Forest University.
“I am excited and honored to become part of the ChemQuest team, a top-tier consulting organization that provides unmatched resources and expertise to the chemical industry. I look forward to working with the team and collaborating with our clients to help their businesses thrive in the markets they serve,” has commented Casebolt.
For further information: https://chemquest.com
FORGET ABOUT PRODUCTS. IT’S A PROCESS.
challenge is different. And so are our solutions. We offer individualized finishing technologies, tailor-made for your application.
RMIT Europe Will Take Part in the ALCOAT Research Project for Aluminium Alloy Coatings
The European hub of the global university of technology, design and enterprise RMIT has recently announced that it has been granted the sum of $294,000 (around €272,500) to contribute to the ALCOAT research project, which aims to develop aluminium alloy coatings as a more sustainable alternative to zinc galvanisation.
ALCOAT is a 42-month project sponsored by the EU Research Fund for Coal & Steel (RFCS) that will develop two new families of recycled aluminium alloy coatings with chemically tailored electrochemical potential, in order to create an alternative to zinc for the galvanisation of steel products.
Steel is one of the most important metallic construction materials, thanks to its mechanical properties, availability and affordability. However, when left untreated, steel is susceptible to oxidation and subsequent deterioration, with telltale signs of damage such as cracking and rusting especially prevalent in moisture-rich environments.
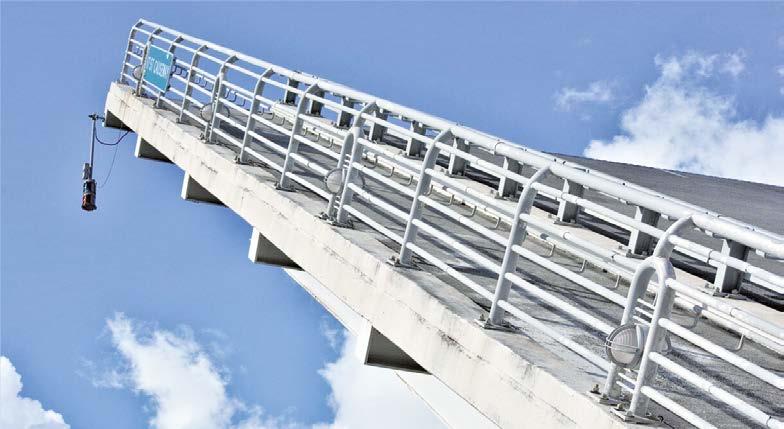
The protection of steel structures against corrosion is therefore necessary to lengthen the service life of steel products and ensure the fulfilment of safety requirements by averting material failure.
Although zinc is widely used to protect steel from corrosion and is highly effective, it is also difficult to recycle. Recycling aluminium destined for landfill to create an alternative for the galvanisation of steel products will then ensure effective and sustainable coatings for the protection of wind towers, ships and other structures exposed to sea water and
atmosphere as well as steel sheet products for automotive, building and home appliance industries.
“Scrap aluminium is widely available but being contaminated with iron and magnesium makes it brittle and unusable for many applications, meaning it is often either discarded or used for lower-level purposes such as pellets,” has stated Ivan Cole, the Research Director of RMIT Europe. “However, this aluminium is exactly what we need to produce a good coating for steel as the contaminants it contains actually stop oxide from forming. ALCOAT will address a sustainability issue rather than a performance problem.”
The aluminium alloy coatings developed by the project are expected to have several advantages, such as a lower corrosion rate and a reduced risk of hydrogen embrittlement. They will also be lighter,
thinner and more sustainable given the reduction in the quantity of primary raw materials required, thereby also boosting efforts in the circular economy.
“Using existing scrap materials will prevent the energy-intensive process of mining and processing virgin zinc and the associated negative costs to the environment. Compared to traditional coating development processes, the procedure proposed by ALCOAT is highly innovative and advanced and will ensure a dramatic shortening of the development process and reduce costs,” has concluded Cole.
The ALCOAT project is coordinated by the University of Chemistry and Technology of Prague and will start on 1st September 2023.
For further information: www.rmit.edu.au
The ALCOAT project will develop two new families of recycled aluminium alloy coatings as a more sustainable alternative to zinc galvanisation.
The Adapta Color Headquarters Becomes a Cardiac-protected Area
In order to improve the safety of staff and visitors, Adapta Color has updated its emergency and first aid plan.
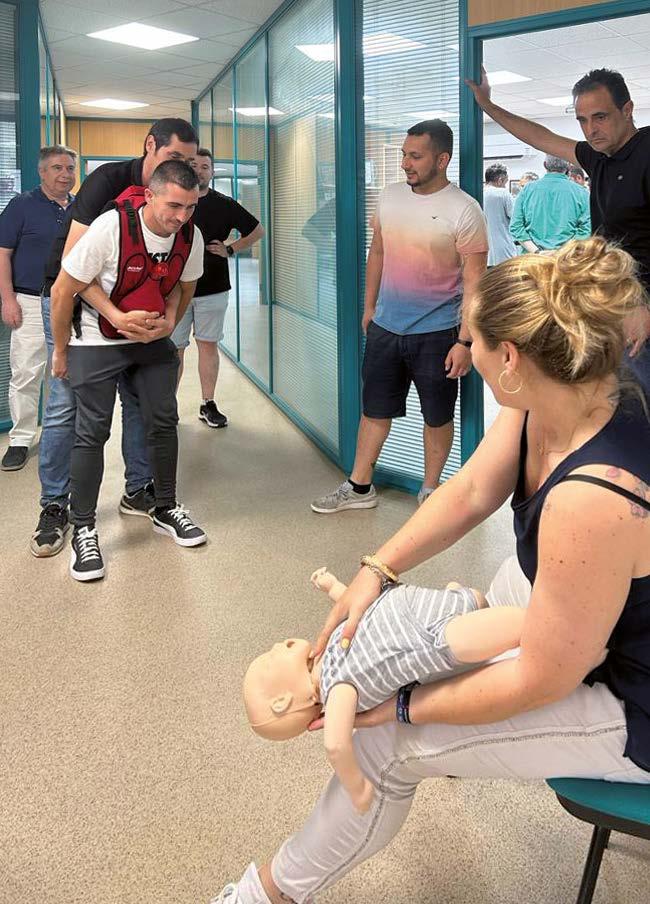
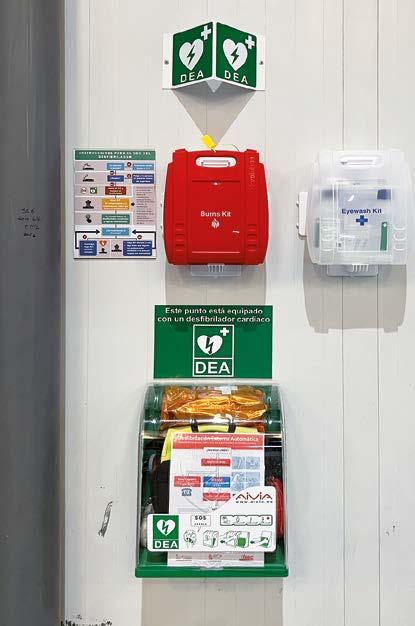
Adapta Color, a Spanish manufacturer of powder coatings, has always paid attention to the safety of its employees and collaborators. For this reason, the company has recently launched a series of initiatives with the aim of improving its emergency plan in its headquarters located in Peñiscola, Spain. 65 people from Adapta have obtained the certification of the course in Basic Life Support (SVB - soporte vital básico) and for using the semi-automatic external defibrillator (DESAdesfibrilador externo semiautomático) approved by EVES (Escola Valenciana d’Estudis per la Salut). In addition, two semi-automatic external defibrillators,
burn kits, control bleed kits and eye wash kits have been installed. The equipment will help to significantly increase the survival rate in the event of an emergency.
“On behalf of the management, I would like to thank all the participating staff for their involvement and congratulate Ruth and Ximo from IRTA Asistencia Médica Integral S.L. for their professionalism and the training provided”, said David Pellicer Roca, General Manager at Adapta Color S.L.
For further information: www.adaptacolor.com
From the in-stock small and thin hook to the special hook Ø30 with EU certification and loading capacity calculation, for both small and heavy parts to be coated.
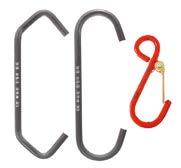

Evonik Presents TEGO ® Rad 2550
Slip and Defoamer Additive for Radiation-Curing Coatings and Inks
The new additive developed by Evonik provides slip and scratch resistance as well as defoaming and hydrophobicity for UV and UV-LED curing inks and coatings.

The Coating Additives business line of Evonik has expanded the TEGO® Rad range of tailored silicone acrylates with TEGO Rad 2550, a new clear and low viscosity liquid cross-linkable additive that effectively reduces static and dynamic surface tension in both conventional UV- and LED-cured formulations. Acrylated products allow to minimise migration and obtain very pronounced and long-lasting effects. The new additive for radiationcuring paints, coatings and printing inks provides also a low coefficient of friction (COF), high scratch resistance, good defoaming and the ability to create hydrophobic surfaces. Moreover, it ensures improved flow and levelling and optical appearance and prevents cratering. Finally, it allows formulators to
create products with the desired level of slip and flow and compatibility. “Due to its unique property profile, TEGO Rad 2550 is truly an excellent additive for the formulation of matte coatings, pigmented inks and roller-applied wood top-coats. It offers a tailored cross-linkable performance. For inks and coatings formulators, this means great long-term effectiveness in the final product, high resource-efficiency and a sustainable solution compared to alternative technologies,” says Courtney Thurau, the head of the global market segment for printing inks of Evonik Coating Additives.
For further information: www.coating-additives.com/en
PPG Provides E-Coat System for Aerospace Parts to Satys
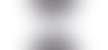
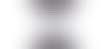






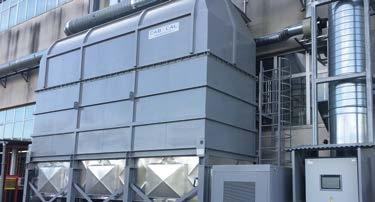
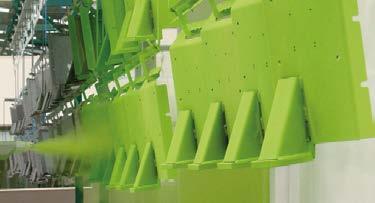
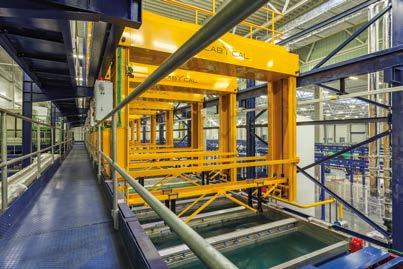
Satys will use the PPG AEROCRON™ e-coat primer system for components destined to the aerospace industry.
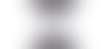


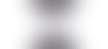


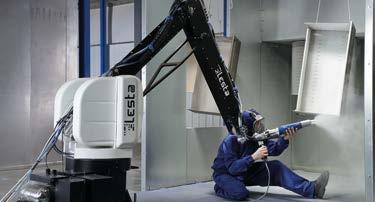
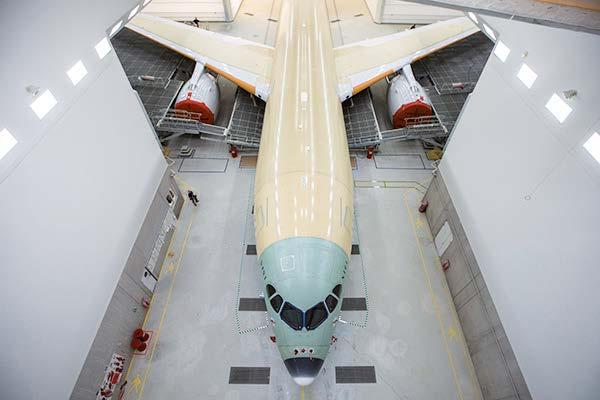
The international coatings manufacturer PPG has recently announced that it has signed a collaboration partnership with Satys, a French industrial group operating in the aerospace industry and dedicated to sealing, painting and surface treating aircraft components. The company will then provide its waterborne PPG AEROCRON™ e-coat primer system to the facility in Dugny.
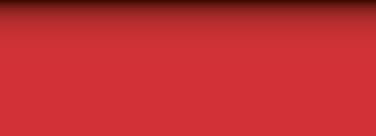
“PPG is proud to partner with Satys to provide our innovative e-coat technology in close proximity to key aerospace OEMs. Our customers in France will benefit from the PPG Aerocron system, which produces a more uniform finish on the aircraft parts, using less paint than traditional spray-applied methods,” stated Sam Millikin, the global director of coatings and sealants for the Aerospace division of PPG. With the AEROCRON™ system, metal aerospace components will be dipped into a 2,100-gallon
(8 m3) bath – the largest in Europe – of chromefree electrocoat primer and charged with electrical current to apply the coating. This ensures corrosion and chemical resistance, meeting industry standards, and provides an even surface finish and a consistent coating thickness, without drips, runs or sags in the dried film. In addition, PPG's sustainable solution produces minimal waste, has low volatile organic compounds (VOCs) and helps to reduce fuel consumption due to weight savings provided by lower paint usage.
“We are always looking for innovative and efficient ways to improve our aircraft painting capabilities for our customers, as well as contributing to the decarbonization of the aerospace industry,” said Christophe Cador, the president and CEO of Satys.
For further information: www.ppg.com
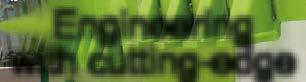
Graco Presented the New Electric-Operated Double Diaphragm QUANTM Pump

The new pump for industrial and hygienic applications developed by Graco is a lightweight and easy to maintain solution for harsh environments.
The international manufacturer of fluid handling equipment
Graco has recently announced the release of its next-generation electric-operated double diaphragm QUANTM™ pump, which features a new electric motor design.
It is suitable for almost all fluid transfer applications and offers a wide range of materials of construction to support multiple industrial and hygienic operations, such as paint manufacturing, water treatment and chemical processing.
“The QUANTM pump is not a new twist on old technology. It’s an entirely innovative design that changes how pumps perform in factories and other installations around the world. We are excited to have created an advanced, extremely efficient design that is lightweight and provides significantly lower lifetime costs than other pump technologies. The pump modernises operations by greatly reducing energy costs. This empowers industrial manufacturers to protect and grow margins and measurably contribute to energy savings, compliance
and environmental stewardship efforts,” has stated Bart Clerx, the product marketing manager for the EMEA region of Graco.
The new pump is designed to be a highly reliable drop-in replacement for current pneumatic pumps or greenfield construction, as it can withstand harsh industrial or hygienic environments and its design with built-in controls and no gearbox is lightweight and easy to maintain.
“Our new QUANTM pump is the perfect solution for upgrading your less-efficient air-operated pumps. The same great self-priming, stalling, seal-less design is a must-have for in-process applications, filling systems and hygienic applications. The powerful new FluxCore™ motors and drives deliver up to eight times more continuous torque at low speeds than conventional motors. The plug-and-play installation allows you to replace existing pumps without additional investment or infrastructure rework easily,” has concluded Clerx.
For further information: www.graco.com
SONGWON Will Cooperate with KRAHN Italia for the Coatings Business
Through the distribution partnership, SONGWON will enhance its position in the Italian paints and coatings market.
The international supplier of specialty chemicals and polymer stabilisers SONGWON has recently announced a distribution partnership with KRAHN Italia for the coating business. Effective from July 1st 2023, KRAHN Italia is the exclusive distributor of SONGNOX® CS antioxidants, SONGSORB® CS UV absorbers and SONGSORB® CS HALS products in Italy. The company wants to enhance its position in the Italian market, which is considered to be one of the key regions in Europe for the paints and coatings industry.
“Italy is an important market for us and we are very pleased to have such an experienced partner join SONGWON’s extensive global distributor network. We are confident that KRAHN Italia’s expertise, strong market relationships and excellent customer service, combined with SONGWON’s products, will help us build and cement our position as the supplier of choice for additives for liquid coatings in Italy,” has stated Simona De Gradi, the sales manager for the EMEAI region of SONGWON.
KRAHN Italia is specialised in the distribution of specialty chemicals. It offers an extensive and high-quality product range and comprehensive technical services as well as an in-house laboratory to support its partners. Leveraging the deep knowledge of the Italian paints and coatings sector, SONGWON will then benefit from a targeted and sustainable product marketing approach.
“We are delighted to be chosen to represent SONGWON in the Italian market. This partnership presents a great opportunity for both companies to actively collaborate and grow, not only our businesses but also to add value for our customers in Italy as well. Expanding KRAHN Italia’s strong portfolio with SONGWON’s high-quality additives for coatings not only allows us to better meet customers’ needs but also enables us to increase SONGWON’s visibility and expand its position in the coatings market in Italy,” has added Enrico Bozzi, the managing director of KRAHN Italia S.p.A.
For further information: www.songwon.com
EQUIPMENT FOR powder coating
DESIGN
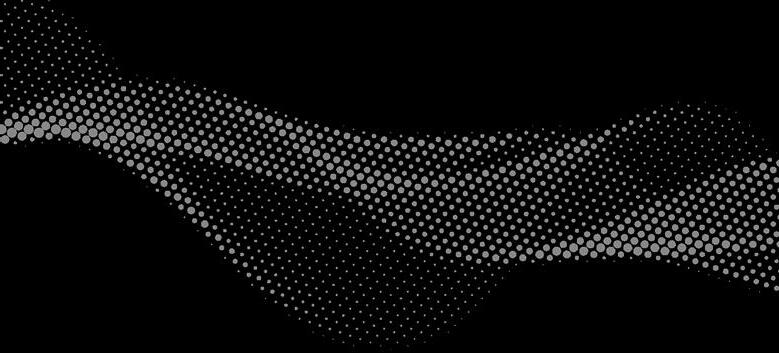
Our powder coating systems and accessories are designed and manufactured with the utmost attention to details
RESPONSIBILITY
We are loyal to the customer and to the product: we build a real relationship of trust and responsibility day by day
PROFESSIONALISM
We follow each customer from design to implementation, from installation to after-sales training
MADE IN ITALY
about ZEUS
www.zeus-el.it
ALIT Technologies Launches FASTRIP T2-120 MIX
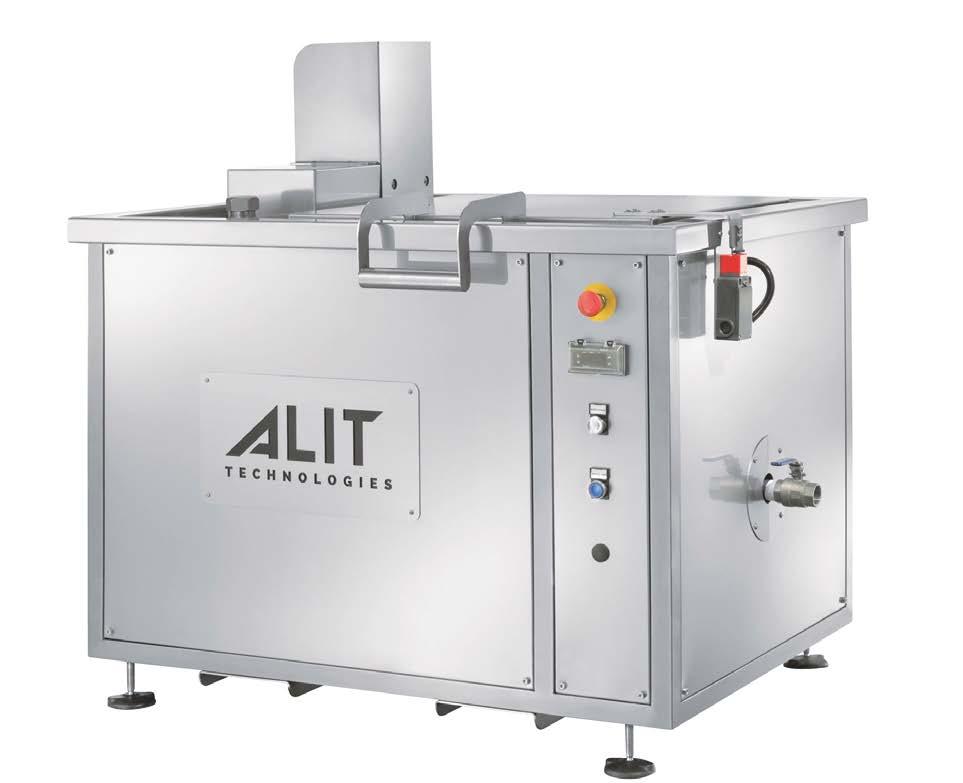
ALIT Technologies is pleased to announce FASTRIP T2-120 MIX, the T2’s range most compact paint stripping system.
ALIT Technologies, a leading manufacturer of machines and products for the surface treatment of metals, is pleased to announce the launch of FASTRIP T2-120 MIX, an even more compact evolution of the T2 system, designed for an effective and a rapid paint removal.
Any company that coats metal parts in-house typically needs to paint strip two types of items: the frames or hooks used for hanging operations and any defectively painted workpieces. ALIT Technologies has developed the FASTRIP T2-120 MIX, the most compact paint
stripping machine in the T2 range, in order to offer an efficient and space-saving solution.
“ALIT TECHNOLOGIES has developed FASTRIP T2-120 MIX based on its many years of experience in the paint stripping industry” says Loris, CEO of ALIT Technologies. “This machine does not use ultrasound, as the mechanical action of the paint stripper on the parts’ is ensured by the hydrostatic thrust generated by the mixer. The fact that ultrasound has been replaced by a mixer is precisely what distinguishes FASTRIP T2-120 MIX from our top-of-the-line model FASTRIP T2-100. This makes
the former a quieter machine that can also operate with a more polluted paint stripper; the absence of ultrasound also allows for the use of electronic components that are less sensitive to the heat developed during normal machine operation. Overall, these choices have resulted in the design of an extremely robust, reliable, safe, and well-functioning system”.
The process
With FASTRIP T2-120 MIX, paint stripping is performed by immersing the workpieces in a tank containing a liquid paint stripping solution that is heated and kept under constant agitation through a special paddle mixer. At the end of the paint stripping cycle, the basket containing the parts is removed from the process tank; after a rinse, these can be reprocessed normally.
The required process steps are the following:
1. Loading of the basket with the components to be stripped;
2. Manual immersion of the basket in the FASTRIP T2-120 MIX tank;
3. Paint stripping;
4. Manual extraction of the basket;
5. Dripping above the paint stripping tank;
6. External rinse of the treated workpieces.
Technical features
FASTRIP T2-120 MIX is made entirely of AISI 304 stainless steel and it includes the following elements:
• Rectangular paint stripping tank with a clear dimension of approximately 450 x 700 x h300 mm and 20/10 thick walls, with a filling volume of about 120 liters. It has a 1” stainless steel bottom valve for full emptying, a temperature sensor for the paint stripping fluid, and a liquid level sensor. It is also equipped with a 2” upper sleeve for possible connection to a suction system.
• Steel mixer located on the short side of the tank. It keeps the liquid constantly circulating to ensure greater stripping efficiency and better performance of the heating system.
The coupling of the motor with the shaft is not direct, but it occurs through a belt-pulley transmission system that protects the motor against both direct heating by the liquid and vapours from the paint stripper.
• Electric heating elements fixed on the tank’s exterior wall, which allow the maximum temperature of the paint-removing liquid to be reached at 80°C. The choice of placing the electric heating elements externally avoids direct contact between the paint stripping liquid and the heating source, thus meeting the highest safety standards.
• Lid entirely made of steel, complete with thermal insulation and 2 pistons to facilitate manual opening and closing operations. The lid’s closure is shaped in such a way as to collect the condensation formed on it during the paint stripping cycle.
• Electric lock ensuring that the mixer stops if the lid is opened.
• Integrated control panel and external electromechanical switches for process parameter management. The panel is located below the tank and mounted on a
mechanical slide that allows it to be removed for inspection or maintenance operations. It enables to adjust the temperature of the liquid and of the heating elements and to control the electric lock and the mixer.
• Thermal insulation on all sides of the tank, made of rock wool with a high insulation coefficient.
• Side panel made of AISI 304 stainless steel, easily removable for maintenance.
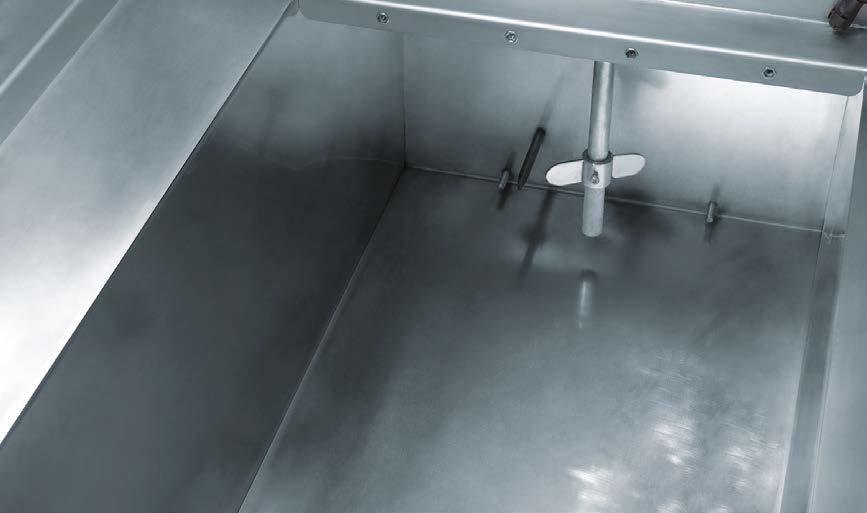
ALIT Technologies
ALIT Technologies is a privileged partner of many high-technology industries operating in the coating sector which require highly efficient products for the pre-treatment of metal components.
In addition to Drizzling, the new dosing and application system for the passivation of metal parts, from its headquarters in the province of Verona ALIT Technologies is also able to supply innovative in line chemical paint stripping systems with the Fastrip series and high performance and low environmentalimpact chemical products.
The “Ask an Expert” Column
Kevin Biller kbiller@chemquest.comHi Tu,
Thank you for your message. I think I understand your problem. Here are some things I would investigate:
1. Particle size - this is the single most important property when it comes to transfer efficiency. Questions: what is your median (D50) particle size? More important what is the percent below 10 microns and above 100 microns? How do you measure particle size distribution? How do you control it? You should target a median particle size of 35 to 40 microns and have less than 7.0% by volume particles less than 10 microns. In addition, you should target <1.0% by volume particles greater than 100 microns.
2. What is the specific gravity of your powder? Is it similar to the competitive product? Is it higher? Higher SG can reduce transfer efficiency by losing particles due to gravity (falling to the booth floor).
A word from our expert Joe Powder to solve more or less conventional powder coating issues all over the world, from Vietnam to South Africa.
3. How well does your customer maintain their application system? Do they have good grounding (earth) on the hangers and hooks? Are the spray guns well-maintained? How often do they provide maintenance for their equipment? You may be experiencing poor application performance due to poor maintenance on the spray guns, reclaim and booth.
Hi Joe,
Thank you for giving solutions in the past that have helped us improve our powder coating products. We will try to learn to develop our products more. However, if you don’t mind. Please advise us on another issue.
We are struggling to compete with competitors in the market. At the same application system conditions: the same type of powder coatings gun, the same voltage level, the same flow, the same line speed. The resin ratio in the formula is 60-70% and we use a special anti-stat additive but our powder coating only gives the product a thickness of 30-40 micrometers, while the powder of the rival company can produce products with a thickness of 60-70 micrometers.
What’s the problem with our product? We are trying to find the best solution, hopefully get comments from you.
Best regards,
Tu Nguyen Alphabet Coatings VietnamBTW, I’m not a big fan of adding electrostatic additives to powders. I think that it’s a band aid approach and should be tried after all else fails. Please let me know if you have further questions?
One last thing, where is your company located? It would be nice to visit you someday.
Kind regards, Joe
Dear Joe,
Greetings from Johannesburg. I have a question. How can I increase the fluidity of my powder coatings?
Thank you, Johann
Kunneke South AfricaHi Johann, Increasing the fluidity of a powder coating and really any powder can be tricky business. For our listeners unfamiliar with fluidity, we’re talking about the behavior in which a powder can allow air to evenly space the
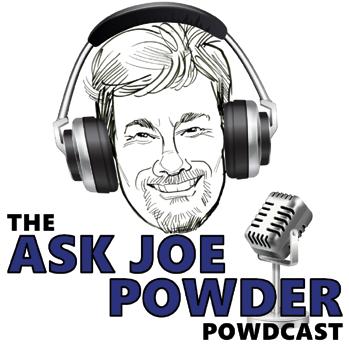
powder particles from each other in air. This is a critical property in the application of a powder coating.

In a powder application system, the bulk powder is introduced into a fluidized hopper. The fluidized hopper is either a cylindrical or box shaped container that has a porous Teflon© plate at its bottom. Compressed air is passed through this porous plate to fluidize or prepare the powder to be transported through a powder pump then hoses and finally through a spray gun. And fluidity is crucial in getting the powder to feed evenly through the system.
Now to your question, Johann. A few factors are important in optimizing fluidity. First, particle size distribution is critical. Note that I said “distribution” and not just particle size. This means that you have to manage the entire size distribution of particles. Most important is to minimize “fines”. Fines can be defined as particles below 10 microns in diameter.
Less is better and you should strive to have less than six or seven percent fines. Too many fines will cause clumping, agglomeration and poor fluidity. Ditto for large particles. By large, I’m talking about 100 microns and above. These are more difficult to physically move with compressed air and therefore should be minimized. I would target less than one percent over 100 microns for the best fluidization behavior.
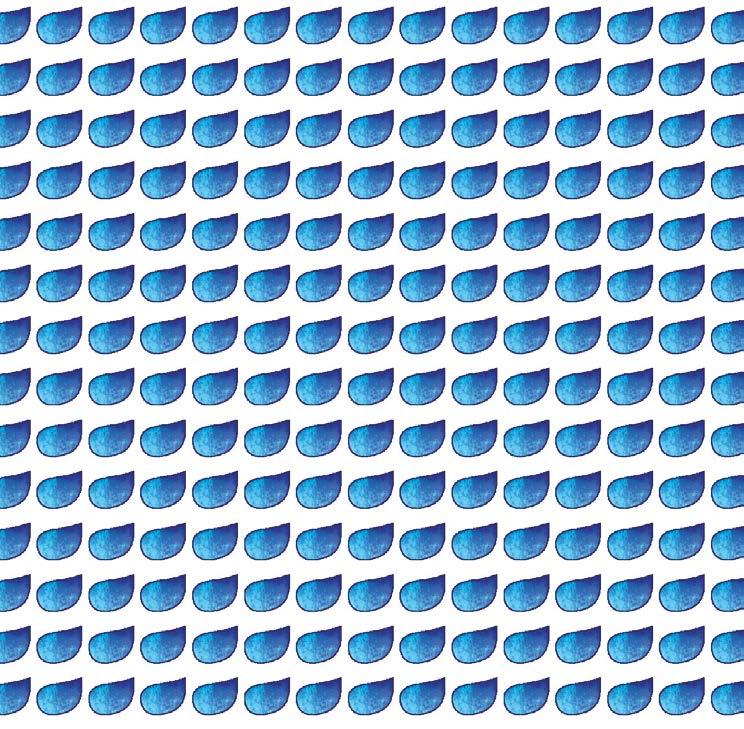
After you nail your particle size distribution, it’s time to incorporate a fluid flow or dry-blend additive. These are fumed silicas or a fumed alumina and act as ball bearings between the powder particles. Keep in mind that a little goes a long way. The addition should be made during the powder coating manufacturing process after the extrusion process. Typically, people add the fumed material with the extrudate chips (flakes) just prior to the pulverization process. This ensures that the agglomerated fumed silica or alumina is evenly dispersed. Otherwise, it can cause seeds and bits in the finished powder film.
One problem is that the fumed material can get pulled out of the grinding system and into the waste stream that deposits into the baghouse. Some manufacturers have devised ways to introduce the silica after the grinding process with a deagglomeration technique. I mentioned a little goes a long way – I would shoot for a concentration well under 1%, say closer to 0.2%.
Hope this helps and that you and your loved ones are all doing well in SA.
Warm regards,
Joe PowderTurn key solutions for industrial wastewater treatment

Design and manufacturing of plants and chemicals for industrial wastewater treatment
Chemical-physical plants
Sludge treatment and compactor systems
Ion exchange demineralization systems and reverse osmosis systems
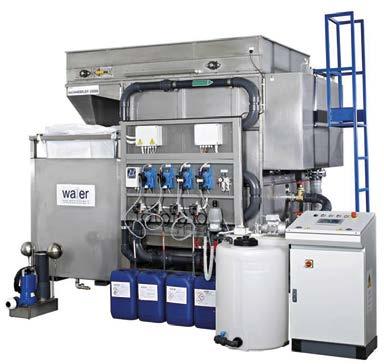
Oil separators
Filtering systems
Batch type systems
Flotation units
Chemicals and spare parts for water treatment
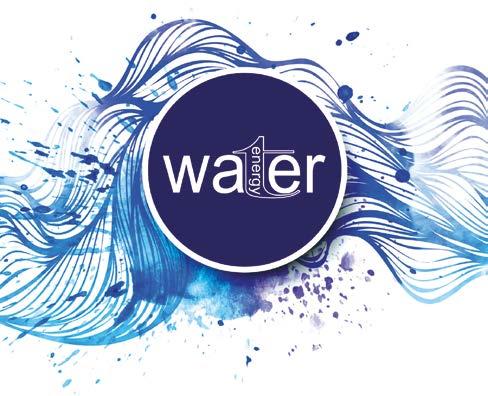
Technical service, support and maintenance of wastewater treatment plants

HIGHLIGHT OF THE MONTH
A Change of Look for Zeus Electrostatic System and Its Product Range
From an interview with Massimo Ricci owner of Zeus Electrostatic System
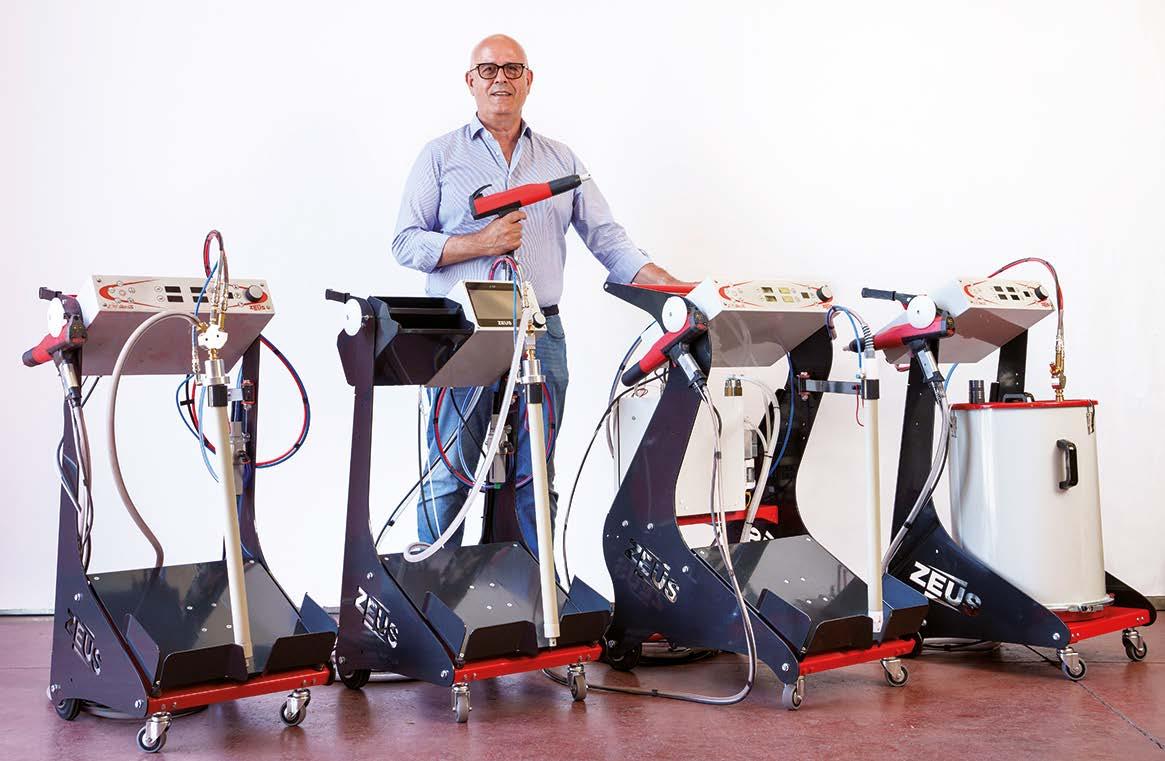
The new corporate image, the restyling of the range already on the market, and the launch of new products are the results of a strategic vision aimed at expanding internationally and providing the market with state-of-the-art powder coating solutions.
“Appearance matters too, but there is much more behind” . This is what Massimo Ricci, the owner of Zeus Electrostatic System, an Italian company specialising in the design and production of systems and accessories for powder coating operations, said during an interview with ipcm®_International Paint&Coating Magazine. For a small company aimed at the national market, moving to an international market requires acting on all corporate aspects; Zeus is
not known and nowadays, in order to be successful worldwide and be perceived as a reliable and highly professional partner, companies need to pay close attention not only to the quality and efficiency of their products but also to their corporate identity, i.e. the set of graphicvisual elements that communicate the company’s values and mission to customers.
Starting from this concept, Zeus, a company based in Argenta, in
the province of Ferrara (Italy), undertook a series of marketing and corporate communication activities with the aim of improving its market positioning at the international level. Zeus’ new image reflects the evolution of the company and in particular the mission increasingly aimed at placing the customer at the centre. Similarly, its product portfolio was also restyled in terms of both technology and graphics.
A new corporate image, the same values as always
This corporate image renovation project came about after a careful study in collaboration with a local communications agency and aims at making the Zeus brand more modern and internationally appealing. “The internationalisation process of a small company like ours can be long and not always easy, as numerous organisational changes have to be implemented in every department of the company, from production to marketing,” stated Massimo Ricci. “As for graphics, we decided to keep the company logo intact and to refresh the colours and design of our website, social profiles, and promotional materials such as brochures, catalogues, and advertisements, with a more appealing and modern style in line with current graphic design trends, which favour minimal and simple aesthetics, as well as the use of a few contrasting colours (in this case, red for the logo and highlights anthracite gray for the background)".
In addition to digital and offline communication, the project also involved all products in the Zeus range, whose design was technologically and aesthetically restyled to make the brand recognisable at all times. “The new corporate image project is the result of Zeus’ desire to expand its presence in new markets, especially at the European level. However, despite these changes, the management and all the company’s employees have never lost sight of the identity and fundamental values that have distinguished us since the company’s foundation in the 1970s’,” added Ricci.
“We follow each customer from design to implementation, from installation to after-sales training; we provide support in the purchasing process, guaranteeing the ethics and quality of our suppliers (all rigorously selected in Italy and Europe) and we deliver a product completely made in Italy. In recent years this has allowed us to consolidate real relationships of trust and mutual responsibility with those who choose us. From all this comes our new payoff, which we have adopted for the first time: Coating your world”.
The new series of powder coating operation control units
In order to meet all the needs of the professionals involved in powder coating operations, Zeus also plans to launch a line of next-generation powder coating control systems. “This new series, called J2, will complement the J1 model that is currently in production, and represents a leap forward in terms of connectivity and control. To complete the

range, the JE-asy project aimed at a simpler and lower-cost market will follow. The three devices are characterised by different designs, technical features, and special accessories. The combination of these three factors gives rise to a series capable of meeting any requirement in terms of production and costs,” indicated Zeus’ owner.
J2, the flagship product of this new series, which will be launched on the market in the coming months, is the result of a collaboration with an international designer who carried out thorough research to create a user interface that is different from the standard, with sophisticated icons and a modern layout. The J2 electrostatic control unit features as follows:
• a user-friendly interface thanks to a 7-inch touch screen that displays all system information and warnings on one page;
• modules that can be expanded and easily integrated into Industry 4.0 systems;
• easy access to process parameter settings to control and manage quality and productivity;
• possibility of carrying out software updates remotely and independently, without the need for the intervention of a Zeus technician.
In addition to the new control units, there is a long series of innovations that will follow in the coming months: a sign of a dynamic and constantly evolving company.
Total Finishing Systems Introduces New PVC Cyclone Powder Booth
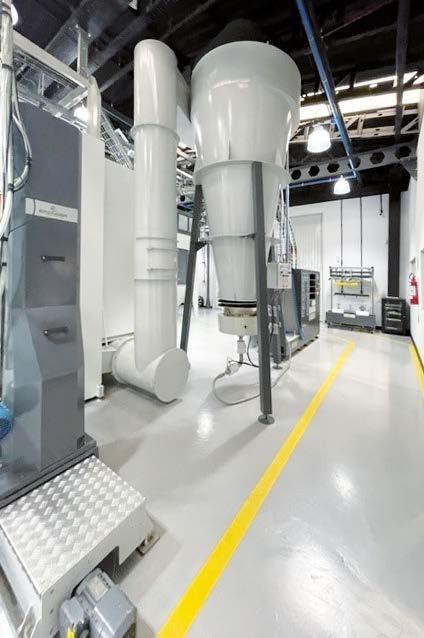
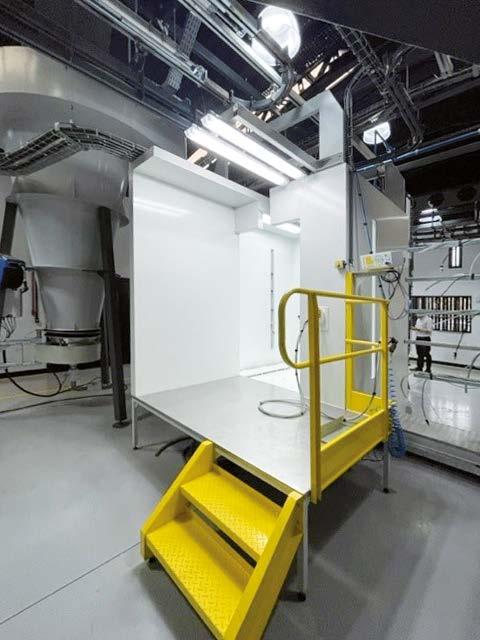
At Fabtech Chicago, which will be held from 11 to 14 September 2023, Total Finishing Systems will exhibit a new PVC Cyclone Powder Booth Systems developed in collaboration with Erzinger.
Total Finishing Systems is pleased to announce an expansion of its partnership with the Erzinger Equipment, Brazilian manufacturer of coating equipment, by introducing their PVC Cyclone Powder Booth Systems into the North American market. Along with the Cyclone booth, we will also be introducing their stateof-the-art Smart In-Line Control System, Application Automation and Powder Distribution Centers.
This expanded product line will provide new and affordable options for our customers and is a complete solution for all your powder coating needs. The company will display these solutions at the booth D40351 in hall D at Fabtech Chicago, taking place 11-14 September 2023 at McCormick Place, Chicago, US.
About Total Finishing Systems
Operating across North America, Total Finishing Systems is a leading
designer and system integrator of high-quality and complex industrial liquid paint and powder coat finishing systems.
The company, located in Riverside, California, US, specializes in surface finishing, materials process automation, and sophisticated installations of fluid and dry coating systems, including thermal treating equipment.
In addition to the Systems group, the Total Finishing family includes: Total Finishing Solutions, which is specialized in the supply of spray booths, UV and IR ovens, abrasive blasting equipment, and industrial automation; and Total Finishing Supplies, the division devoted to the supply of all consumable materials and equipment necessary to maintain the operation and efficiency of plants.
For further information: https://totalfinishingsystems.com
Your partner for green chemical processes



Chemtec’s mission is to update tradition.
Our revolutionary chemicals are designed to have a very limited environmental impact, to reduce consumption of resources and for a greater operational simplicity. With Chemtec technologies you can replace zinc&iron phosphate:
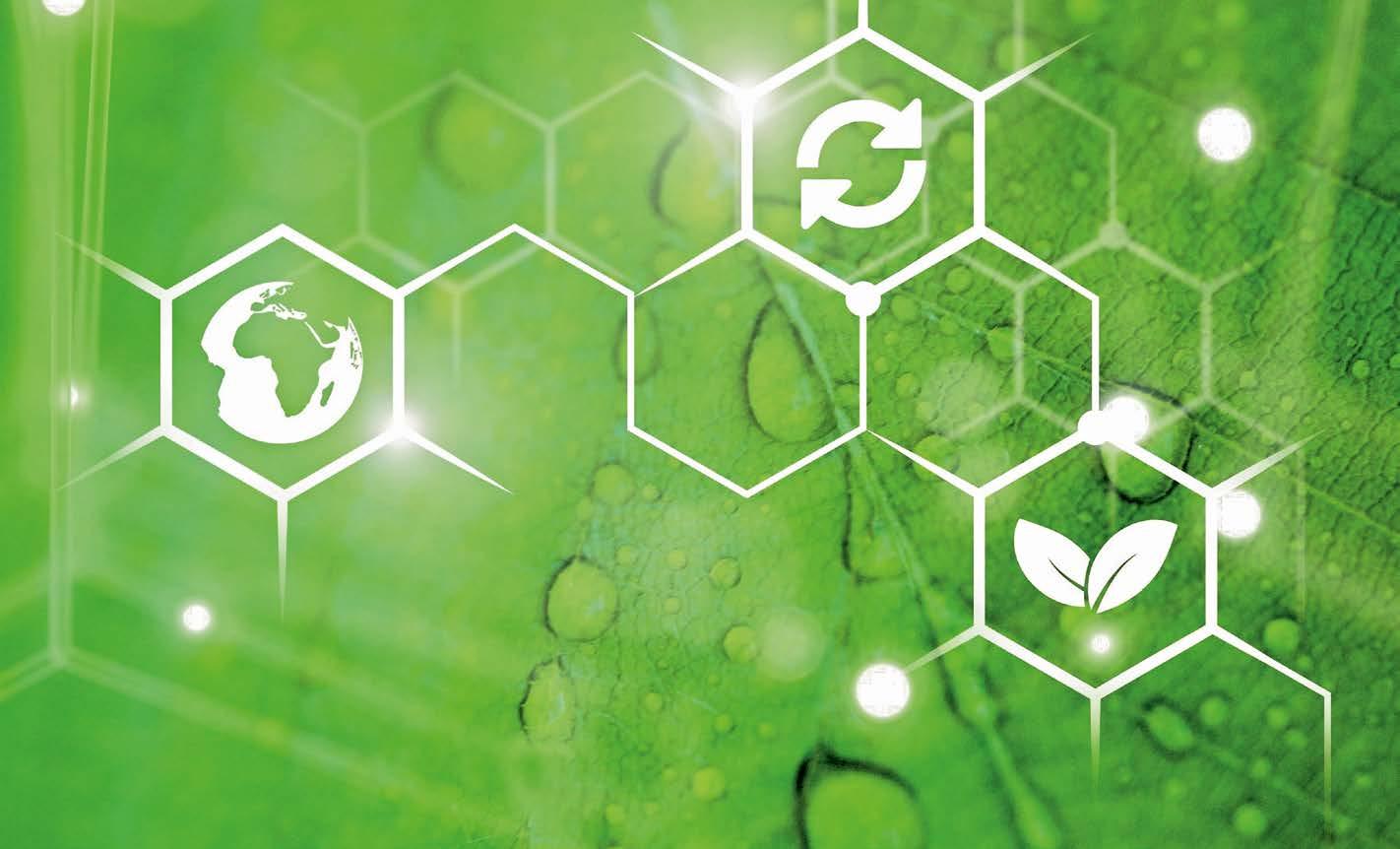
Want to use less energy, get rid of heavy metals and create a safer environment? Want to replace Zinc Phosphate?
Choose PRONORTEC
PRONORTEC nanotechnology is a new and innovative chemical process for multi-metal surface treatment, based on the use of organic Phosphorus compounds. It is a 1k process, it doesn’t need any additive to correct pH, nor any concentration of other metals. This process is highly revolutionary both for its ease of use and for the quality of results. It does not create any kind of sludge. It can be applied by spraying, immersion, or nebulization.
Choose TORAN 3®
Want to save energy, use no water, create no emissions and waste?
Want to replace Iron Phosphate?
Single-stage, room temperature multi-metal pre-treatment process, with no VOC emissions, no rinsing, no pre-degreasing, no creation of wastewater or sludge. The unique and innovative anhydrous process is based on organic high-boiling fluids and guarantees degreasing as well as immediate protection against oxidation, leading to excellent performances in the finishing cycle. The TORAN 3® treatment is a valid, less expensive alternative to phospho-degreasing and phosphating and passivating processes.
Choose WASTE WATER TREATMENT SYSTEMS

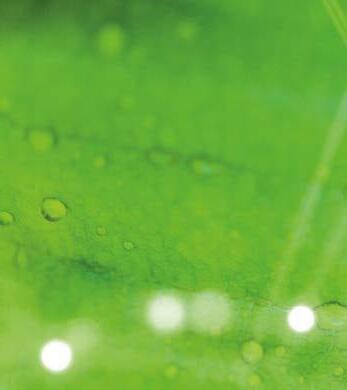
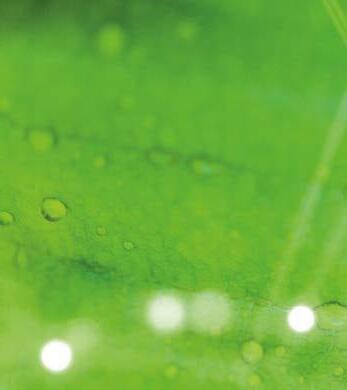
Want to save water, be more sustainable, create less waste?
The combination of Chemtec water treatment equipment (chemical-physical plant, skimmers, filters) with specific chemicals allows the purification and re-use of industrial polluted water in many different industrial applications. Water consumption is significantly cut and water discharge is no more a problem. Waste water are purified and re-circulated instead of discharged to meet the demand of circular economy.
Impact Coatings to Open New Headquarters in Sweden in 2024
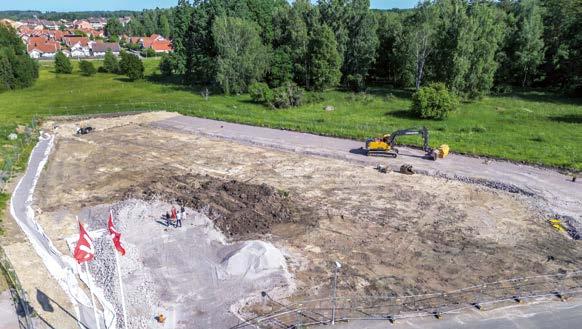
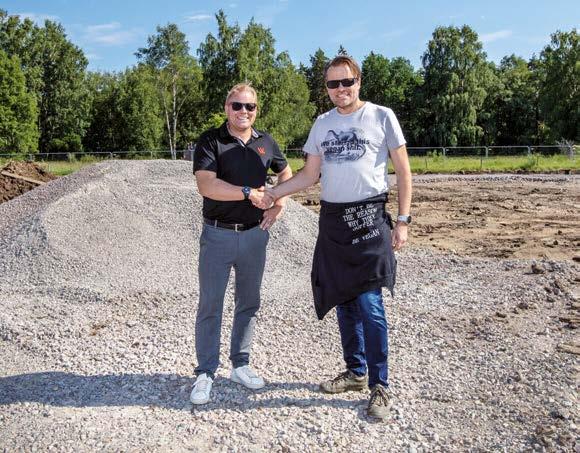
The new site will double the production capacity of Impact Coatings and include an updated laboratory to test coating systems and technologies.
Impact Coatings has recently announced the beginning of the construction of a new plant and headquarters in Linköping (Sweden). The new premises are located adjacent to Linköping University and Linköping Science Park, in close proximity to its innovation hotspots. The company expects to move in during the second half of 2024. The new facility will consist of around 3,000 m², doubling the current production area and thus resulting in a significantly increased capacity for the assembly of coating systems as well as an expanded space for the Swedish Coating Service Center.
Besides providing a better capacity to support the clients and continue to grow the operations of the company, the new Swedish site will also host new departmental offices and conference rooms, an updated laboratory, a pre-production zone for washing and blasting and a logistics hub. In addition, the Coating Service Center will enable Impact Coatings to carry out tests of coating technology and customers to learn more about complete coating solutions first-hand.
“The new headquarters are an important puzzle piece in our growth journey. With a new attractive and advantageous logistical location and production-optimized workspaces in modern premises, we will be able to continue to attract the region’s top talents. At the same time,
we can continue to grow our company and streamline and automate our production flows. Key aspects to be able to fully support the fastgrowing industries that together with us work on the next generation of energy and transportation solutions”, has stated Torbjörn Sandberg, the CEO of Impact Coatings.
The headquarters is being built in close collaboration with Wilzéns Fastighetsförvaltning, that will own and manage the property. The construction works for the new plant are taking place at the same time as production in the new Coating Service Center in Shanghai (China), while the company is also planning to build another site in the United States of America in 2024.
“It is gratifying to carry out this project for Impact Coatings, not least considering their commitment in the green technology sector and use of sustainable production methods, which goes hand in hand with our values. I would also like to commend Linköping municipality, for the fast pace and positive attitude throughout the planning process,” has commented Andreas Wilzén, the CEO of Wilzéns Fastighetsförvaltning.
For further information: www.impactcoatings.com
New Shot Blasting and Coating Plants Confirm Cos.Eco. as a Company of Excellence in Southern Italy
Monica Fumagalli ipcm®Being a Southern Italian firm of excellence means combining innovation and sustainability in increasingly high-performance products. This article presents the success story of Cos.Eco., based in the Apulia region, the fourth company in Europe for the production of environmentally friendly vehicles. It chose an OMSG shot blasting machine to optimise substrate preparation and ensure greater adhesion and durability of its coatings, which it applies in a new Savim system, also improving work comfort for its employees and the sustainability of its production processes.

According to the figures recently updated by the European Parliament, 2.2 billion tonnes of waste are produced within the EU every year1. Municipal solid waste, i.e. waste generated every day mainly by private citizens, then collected and treated by municipalities, accounts for more than a quarter, about 27%.
1 https://www.europarl.europa.eu/news/en/headlines/society/20180328STO00751/ waste-management-in-the-eu-infographic-with-facts-and-figures
According to the report, “From 2018 to 2021 the average amount of municipal waste as measured per capita increased in the EU. However, trends can vary by country. […] Even though the waste generated per capita has increased, the way we manage waste has improved - with more recycling and composting and a decrease in landfill.” In fact, one of the EU’s circular economy objectives is to promote not only waste prevention but also the reuse of products whenever possible, with a focus on recycling, composting, and incineration.
The same increasingly sustainable approach characterises the sector of vehicles for the collection and transport of urban solid waste. Giuseppe Debernardis, the sole director of one of Italy’s national and international leading manufacturers of municipal waste transport vehicles, explains: “Cos.Eco. Industrie Group Srl specialises in the design, construction, marketing, and after-sales technical assistance of equipment for the collection, transport, and disposal of municipal solid waste, such as compactor trucks, dumpers, and bin washers. Since 2015, we have been carrying out every necessary design, raw material processing, assembly, and coating phase in-house, including testing of each individual product, within a complete, fully integrated, and environmentally friendly production cycle. “Our vehicles must convey an idea of cleanliness and sustainability even in their aesthetics, which is why our substrate preparation and actual coating operations are particularly strategic. This is also the reason why in a manufacturing flow
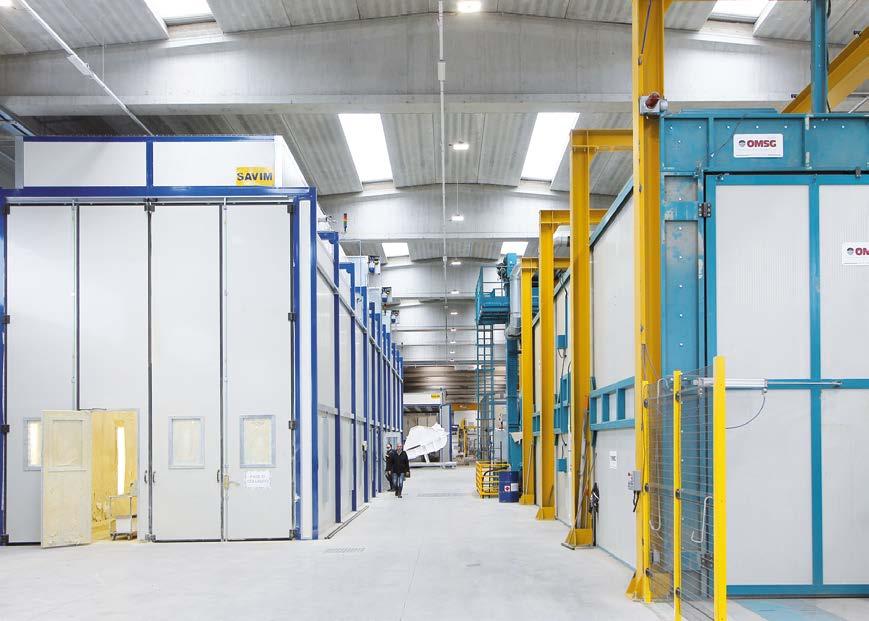
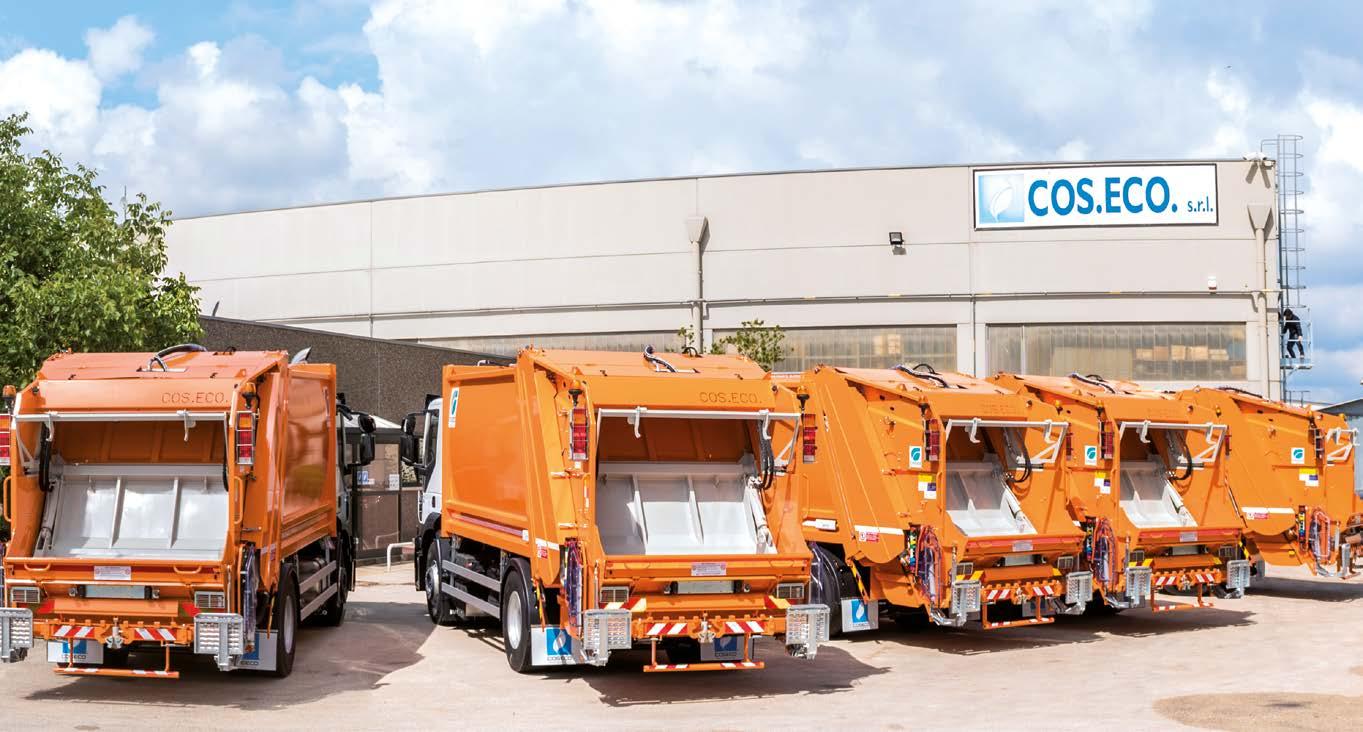
like this, when the surface treatment phase turns into a bottleneck, the problem must be solved with extreme urgency.” Indeed, about a year ago, Cos.Eco. completely renovated its paint shop by equipping itself with a new automatic shot blasting machine, designed and installed by OMSG - Officine Meccaniche San Giorgio (Villa Cortese, in the province of Milan, Italy), and a new coating system supplied by Savim Europe Srl (Arbizzano, Verona, Italy).
Cos.Eco.: a success story from Southern Italy
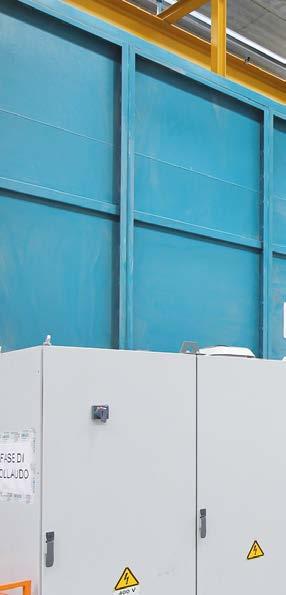
The story of this flagship company in Apulia’s Murge area started with the entrepreneurial idea of two men: Nicola Farella and Donato Debernardis, who founded DI.CAR. in Altamura in the 1970s as a manufacturer of transport equipment. At the beginning of the 1980s, after a serious setback due to the 1981 earthquake that brought companies in Lucania to their knees as they were no longer able to meet any payments due, Nicola Farella decided to focus exclusively on the production of municipal vehicles, including compactor trucks, street sweepers, and school buses. “In that same period,” says Nicola Farella himself, recently appointed Cavaliere della Repubblica for his professional and social commitment, “we decided to sell the entire fleet of trucks we previously used for transporting goods and to establish Cos.Eco. Costruzioni Ecologiche Srl, later moving our headquarters from Altamura to Grumo Appula. Here, we eventually abandoned the
transport sector to devote ourselves entirely to the production of ecology equipment.”
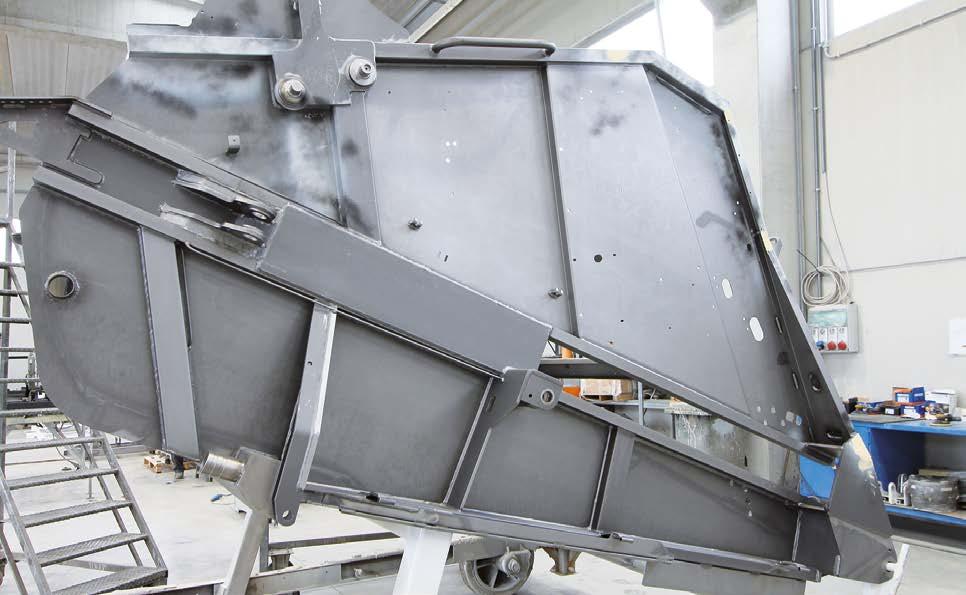
“Through continuous technological innovation and the utmost care taken in every process step,” adds Farella, “we have succeeded in establishing ourselves also at the European level, despite being based in a complex area such as Southern Italy, characterised by numerous resources but also still with some gaps to fill in terms of industrial development. And Cos.Eco. has certainly contributed to the growth of this area, fostering the creation of numerous companies revolving around our business and providing numerous jobs. Currently, we have 110 employees working in our 44,000-m2 plant. We are present in 40 countries, from the closest markets such as Northern Europe, Spain, and the United Arab Emirates to more distant ones such as South Africa, Singapore, and New Zealand. We have built our leadership over time thanks to technologically advanced machinery, specialised personnel, and the attention that our company has always paid to its customers all over the world.”
“To guarantee a high quality level of products and services,” indicates Debernardis, “we have obtained both the ISO 9001 and ISO 14001 certifications, which, in addition to product quality, verify the organisational structure of the company itself also in terms of effective management, especially with regard to the most significant environmental aspects. Further certifications attest to the quality,
mechanical, and technological characteristics of the materials we employ, such as for example Hardox, one of the most abrasionresistant steels, and S355 and S275 carbon steels.”
A fully insourced production cycle
“Given the difficulty of finding contractors in our area but also for greater control of our production flow, we have insourced all our production phases, from the machining stages such as cutting, bending, and welding to the surface treatment ones, that is, shot blasting and coating,” explains Farella. Before mechanical pretreatment, the parts are cleaned manually with a high-pressure cleaner to remove machining oils and the different materials deposited during welding. “Thanks to this cleaning operation,” notes Debernardis, “we also preserve the quality of the grit, which remains cleaner and can thus be recovered. To achieve our specified surface roughness profile, we use angular steel grit.”
GLOBAL SOLUTIONS FOR WATER TREATMENT
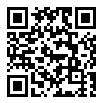
with a complete service that includes system design manufacturing, installation, technical support and chemicals
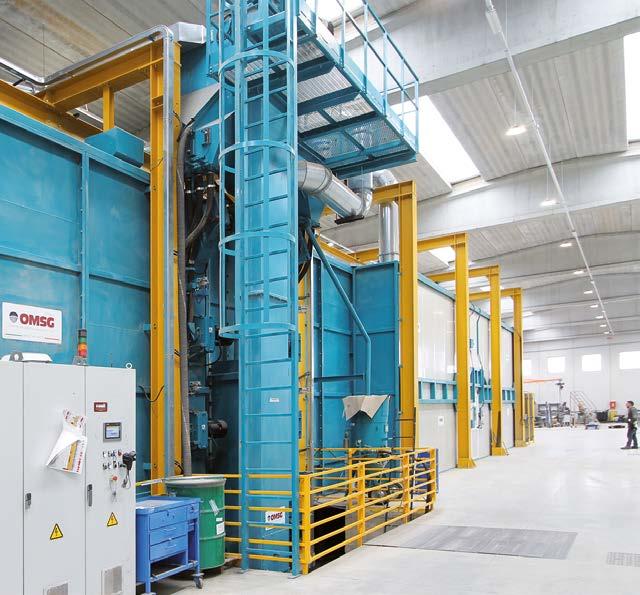
SPRAY BOOTHS WATER SLUDGE REMOVAL
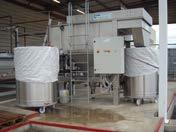
RESIN DEMINERALIZATION SYSTEMS
REMEDIATION OF CONTAMINATED SITES
BIOLOGICAL SYSTEMS
BATCH TREATMENTS
PHYSICAL-CHEMICAL SYSTEMS
ADSORPTION FILTRATION
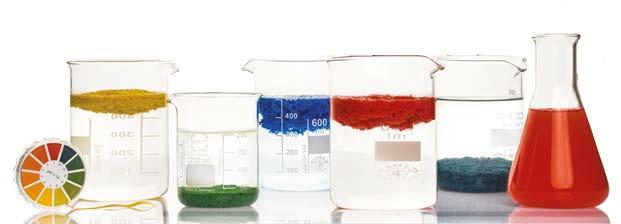
REVERSE OSMOSIS
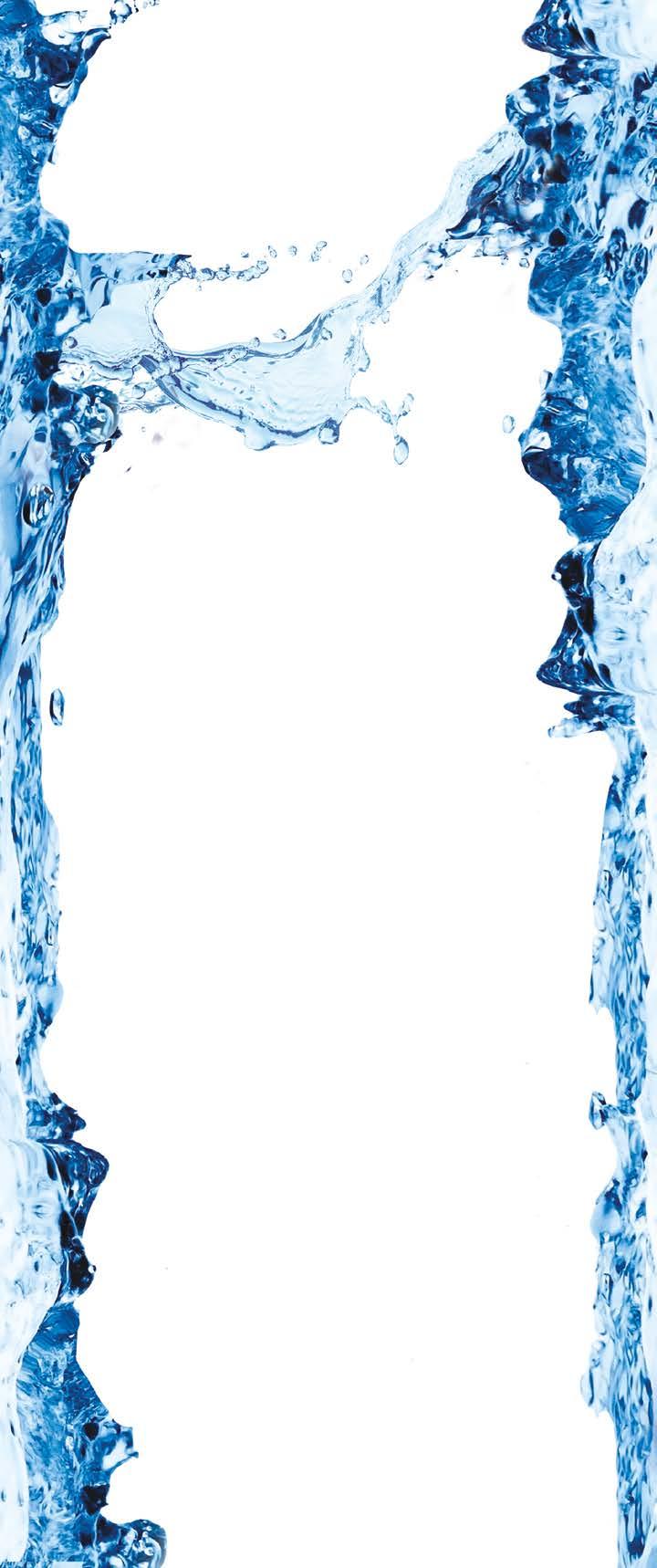
MEMBRANE SYSTEMS
EVAPORATORS
BIOGAS BIOMASS SYSTEMS
OIL SEPARATORS
DESANDERS
DESALINATION SYSTEMS


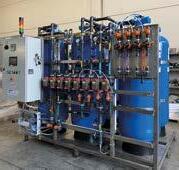
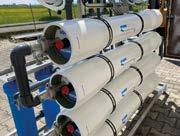
PYROCHAR
OTHER SYSTEMS
CHEMICALS
- The treated workpieces can have a length of up to 11 m.
- Overview of the shot blasting system.
The new OMSG automatic tunnel shot blasting machine was installed about a year ago to solve a production bottleneck. “We used to carry out a manual mechanical pre-treatment operation, which was burdensome for our employees in terms of both handling, due to the weight of the large components, and application, because it required their physical presence inside the blast chamber. Now, we carry out manual shot blasting operations only on smaller parts and we use our automatic machine to pre-treat products such as semi-trailers, with dimensions up to 11 x 2.5 x 2.5 m.”
The workpieces’ surfaces are then blown and the grit is recovered. Afterwards, the parts reach the coating plant, equipped with a manual static booth. “In this case, we ruled out automation because our components’ conformations are too varied to be able to take full advantage of the benefits of an automated system. We apply high-solid liquid polyurethane paints in three coats using WAGNER spray guns. Our system consists of several stations for primer application, drying, sealing, and topcoat application, which is done in two coats. After application of the primer, sealing is carried out in a chamber that can be heated as needed to evaporate the solvent-based paint product or cure the sealant. This is in fact one of the most interesting features of the coating system designed and installed by Savim: its partitioning through
shutters allows us to heat individual zones to the required temperature depending on the operations we have to perform. Then, the workpieces reach the drying oven where they are left to dry, sometimes even at room temperature without the need for heating, thanks to the high temperatures typical of our area.”
Features of the new shot blasting plant
The company selected an automatic shot blasting plant type Tunnelblast 2535/16 H26 C. “It treats parts with a maximum cross-section of 2.5 x 3.5 m,” indicates Enzo Dell’Orto, the CEO of OMSG. “The system is equipped with 16 single-disc turbines featuring direct drive motors with a power of 7.5 kW each. The electrical panel is equipped with 16 inverters to control the rotation speed of the turbines and therefore the kinetic energy of the steel abrasive
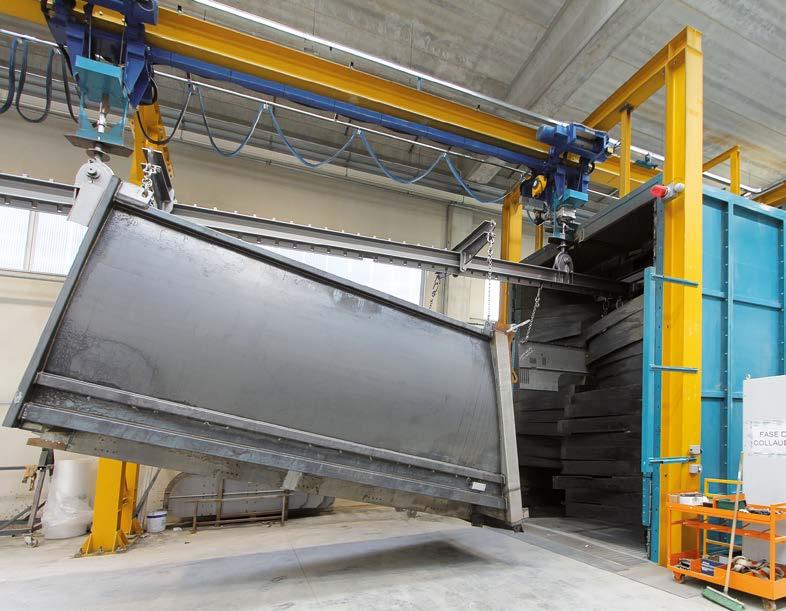
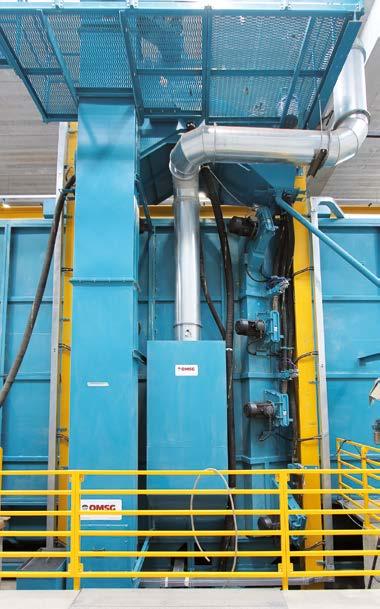
projected onto
the workpieces. In addition to inverters, the shot blasting machine has special turbine feed valves, featuring a double pneumatic cylinder to regulate the flow of abrasive to the turbines. The overhead conveyor, which has an extension outside the plant of 12 m at the inlet and 12 m at the outlet, is equipped with a pair of hoists with a capacity of 6,000 kg each. We also installed a manual shot blasting cabin downstream of the tunnel to touch up any masked areas or undercuts that cannot be reached by the
direct impact of the abrasive projected by the turbines. Its size is 15 x 5 x 4.7 m. The simple blowing operations are also carried out inside the booth to remove the abrasive deposited on the pieces.”
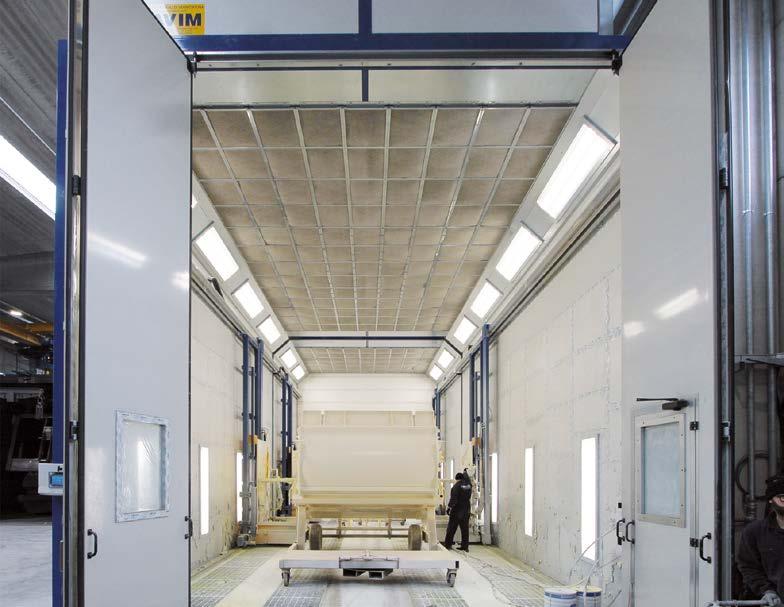
“The entire plant,” adds Dell’Orto, “is Industry 4.0-oriented. The work cycle is managed by a PLC and the machine is equipped with sensors to control the level of metal abrasive in the separator and the rotation of the elevator’s lower pulley, remote assistance devices, a bar code reader, and digital amperometric controls. Both the turbine shot blasting machine and the manual cabin are equipped with cartridge filters made with antistatic polyester cartridges and ATEX components, the former with a capacity of 20,000 m3/h, the latter of 7,500 m3/h.”
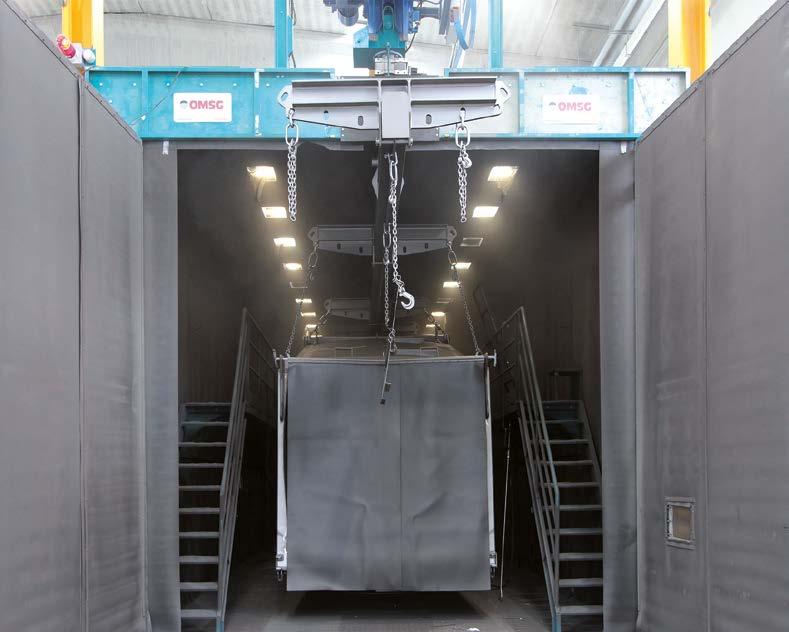
The advantages of the new system combination
“One of the main benefits brought by our new mechanical pre-treatment plant,” says Debernardis, “has been the reduction of our production times. Today we can produce two compactor trucks per day, as well as various components such as tanks made of welded steel or aluminium sheet and other smaller vehicles. The shot blasting operation takes 20 minutes, compared with the about 5 hours required by the previous manual operation. This is our first experience with an OMSG machine, but we can only be satisfied with it. At the same time as we upgraded the shot blasting department, we decided to build a new paint shop because the previous one only consisted of one booth where we applied both primers and topcoats. To do this, we turned to another well-established company with profound expertise, Savim. Relying on companies with a sound corporate structure is our precise choice to make sure that in the event of a plant issue of any kind, the solution will be quick and effective. For us, stopping the shot blasting or coating system means stopping the entire production cycle.”
Conclusions
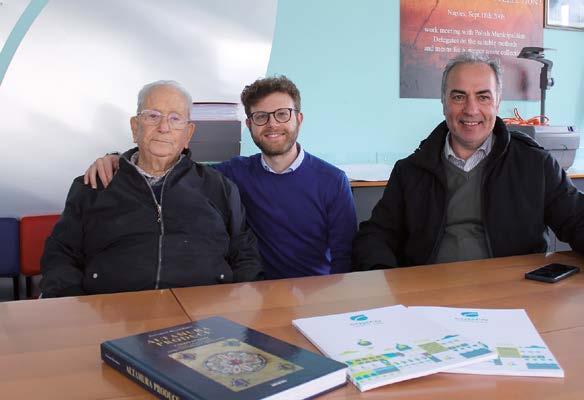
“More careful environmental waste management,” summarises Debernardis, “is one of the targets the European Union has set for itself by 2050. The road is certainly one of the most difficult ones to travel, because modifying the collection methods used so far involves changing the mentality not only of private citizens but also of public bodies. But whatever the method chosen, Cos.Eco. is ready for it: in addition to the attention we have been always paying to the impact of our production cycles, for some time now we have been making electric vehicles available to municipalities, which are becoming very popular. We have also launched a new, patented solar-powered waste
compactor truck equipped with an internal weighing system, which cuts its costs and environmental impact while reducing noise and emissions to zero. This continuous search for innovative and environmentally friendly solutions has always characterised the history of our company and the entrepreneurial strategy of our founder, Nicola Farella. The search for innovative solutions also calls for collaboration with highly skilled, well-established companies, such as OMSG and Savim, with which we have updated and optimised our paint shop: today, coating has turned from a critical phase into one of our main production resources, enabling us to confirm ourselves as a company of excellence in Southern Italy.”
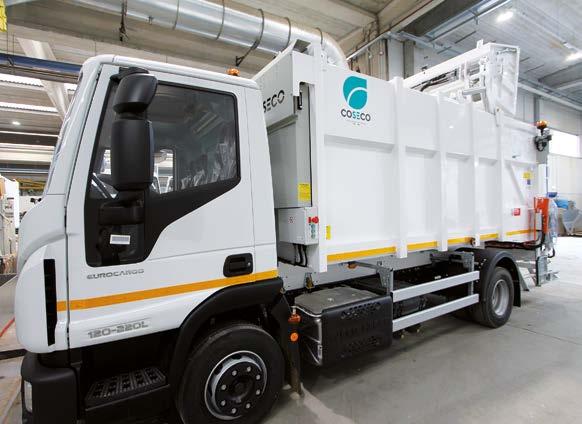
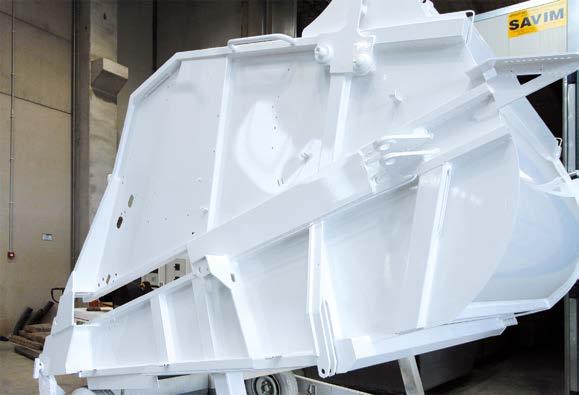
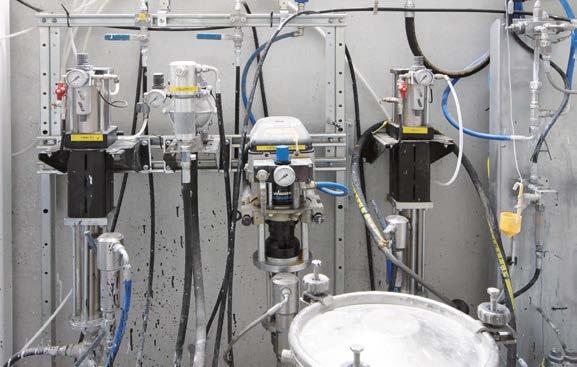


under the patronage of:







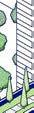


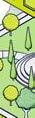















Products, networking, business and training.

WHERE WE HAVE BEEN
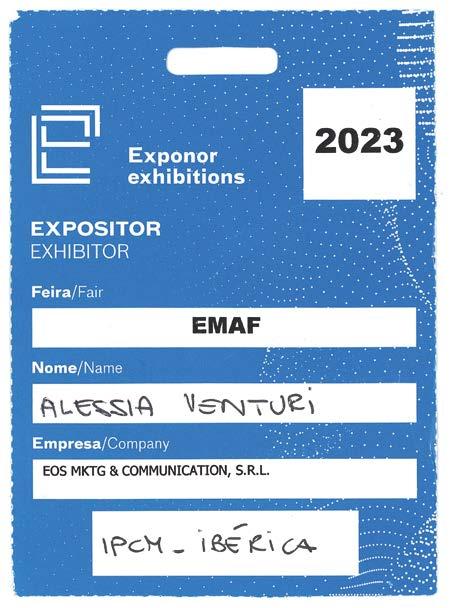
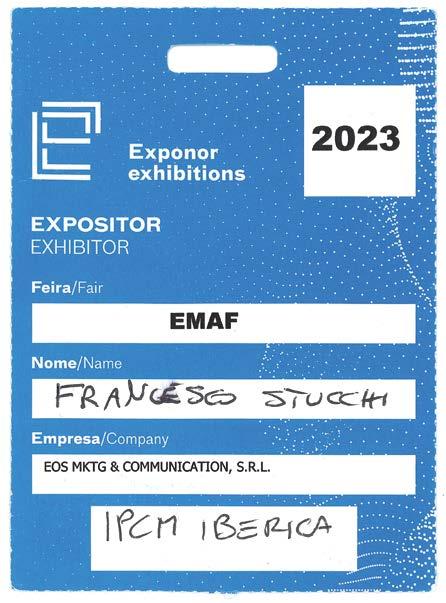
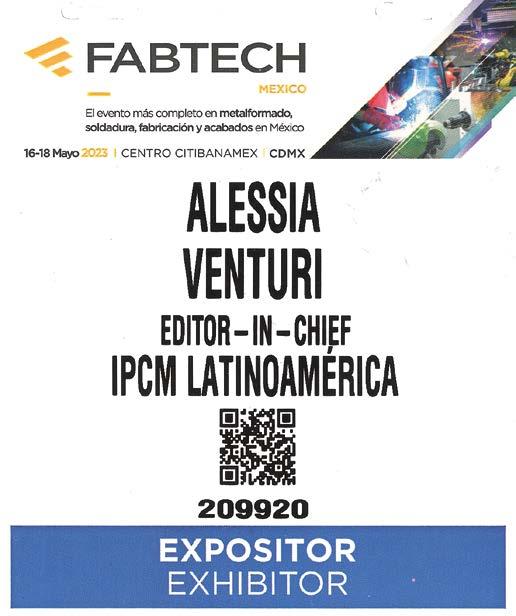

How to Reduce Edge Corrosion with a New-Generation Primer
Andrea Perelli Pulverit Spa – Milan, Italy a.perelli@pulverit.itPulverit has developed Endurance, a series of new protective primers with increased corrosion resistance, especially on parts’ edges.
How much does metal corrosion cost? In industrialised countries, it is approximately equal to 6-8% of GDP, with estimated costs for the whole of Europe of more than €750 billion per year. Given the costs associated with corrosion, therefore, the durability of products becomes of vital importance.
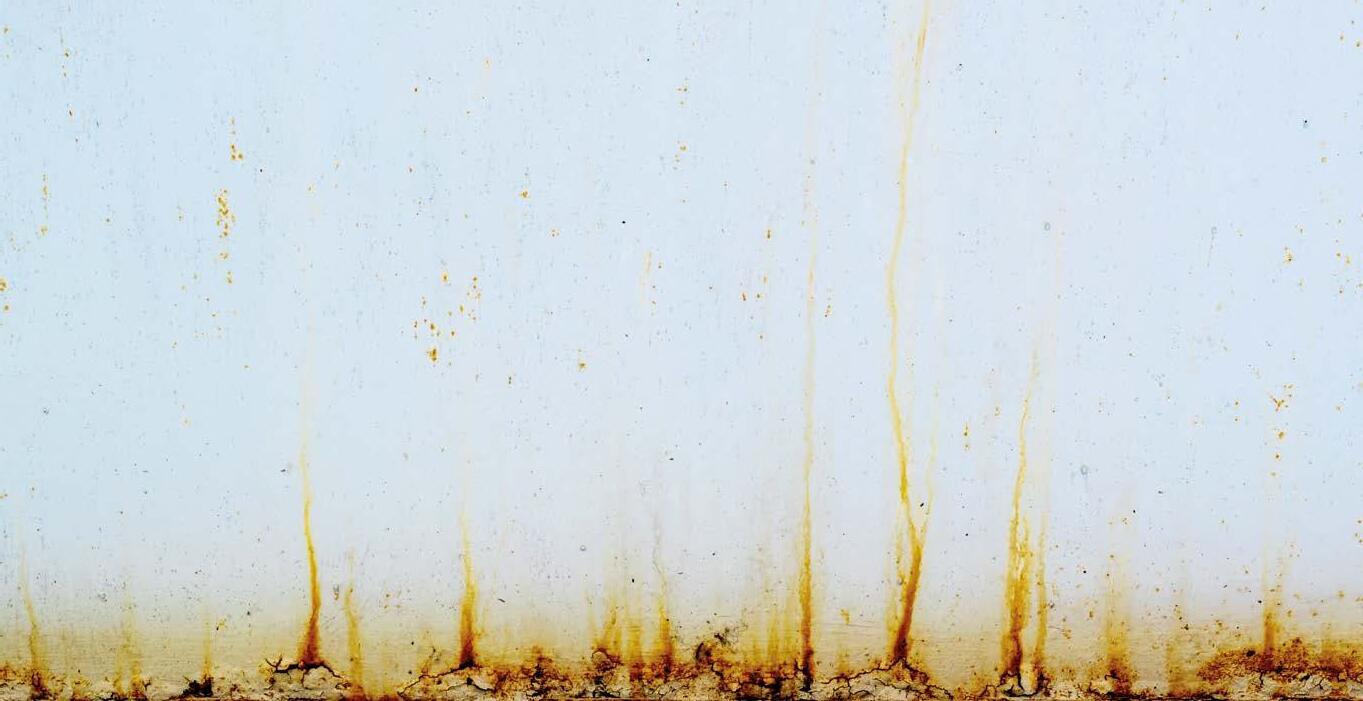
The corrosion of a metal part generally starts at critical surface points and then, once triggered, it spreads to the rest of the component. Such critical points include areas where the part has suffered mechanical impacts or scratches that have affected the paint film, but
also sharp edges. Impacts and scratches can be prevented through proper handling and/or packaging. The criticality of edges, however, is more difficult to curb. In this framework, the Pulverit laboratories have developed a series of primers called Endurance, which increase corrosion resistance even on the edges of workpieces.
The Endurance 16J0 series, in particular, combines a slightly wrinkled epoxy base coat with barrier-effect and passivating additives to provide optimal edge coverage, excellent corrosion protection, and primer overcoatability.
The causes of edge corrosion
The main causes of corrosion on parts’ edges can be different, including faulty design, inadequate pre-treatment, and the inherent difficulty of covering sharp edges with paint. Why is it so difficult to achieve adequate edge coverage? On the one hand, this is due to the difficulty of painting a narrow, thin surface and, on the other hand, to the viscosity of the coating systems used. Conventional primers are normally smooth epoxy products, which as such tend to slip on edges. Figures 1 and 2 show microscopic images of some parts’ sections coated with a traditional primer and a top coat: as can be seen in Figure 1, the paint thickness at the edge is much lower than on the flat side, and this difference cannot be compensated for even by applying a second layer, as shown in Figure 2.
The Endurance primers
Pulverit has developed its Endurance primers to solve this problem: their different rheology and the action of special additives make it possible to considerably increase the thickness of powder deposited on edges. As can be seen in the microsection of Figure 3, edge protection is complete: from a traditional primer thickness of less than 10 µm in Figure 1, a value of over 100 µm was obtained with the Endurance primer in Figure 3 The same top coat as before, however, began to slip again after application, as can be observed in Figure 4: this means that the protective effect is guaranteed almost exclusively by the Endurance primer.
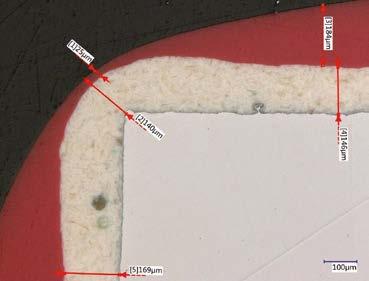
Test results proving these products’ effectiveness
We performed a comparative cyclic corrosion test (KSP) by applying two different primers on sheets that were pre-treated with zinc phosphating technology and painted with the primers alone. The edges were not mechanically rounded. In both cases, the primer’s thickness ranged between 70 and 90 µm. At the end of the test, the sheet coated with the standard primer showed the complete detachment of the paint film in the area around the holes as well as the first traces of corrosion on the edges (Figure 5). Conversely, with the new embossed primer 16J, no film delamination or edge
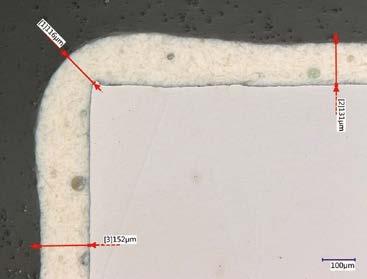
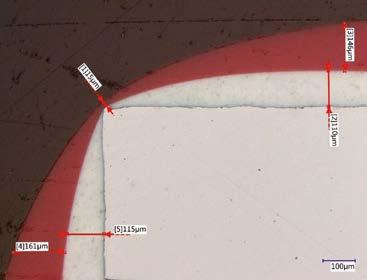
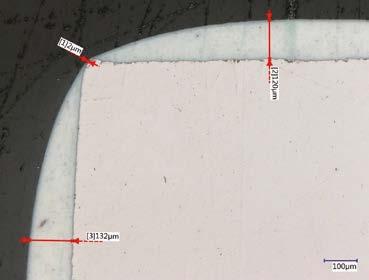
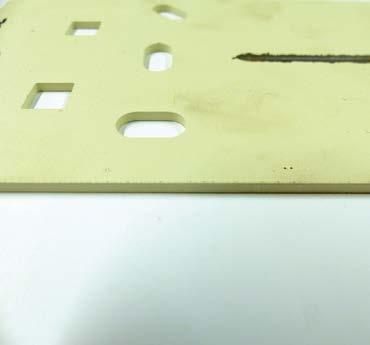

corrosion could be detected (Figure 6). The duration of the KSP test was 720 hours. Since the sharper the edge, the higher the level of criticality, we also carried out an “extreme” test with commercially available razor blades. These were painted both with one coat of primer and with a primer + top coat two-coat system: also in this case, the photos taken under the microscope are highly explanatory. When looking at Figures 7 and 8 (razor blades painted with primers alone), one can see that in Figure 7 (standard primer) the cutting edge is not covered by the primer, to the extent that the blade shimmers through, whereas in Figure 8 the Endurance primer also covers the cutting edge and the surface looks well rounded. The result becomes even clearer when analysing the cross-section images. Figures 9 and 10 show the double-coated razor blades. In Figure 9, despite the two layers deposited on the cutting edge of the blade, the thickness of the film cannot even be measured. Conversely, with the Endurance 16J primer, a thickness of 61 µm is also achieved at the tip of the blade (Figure 10). This means that optimal protection against edge corrosion can be guaranteed even under the most critical conditions. Finally, we tested our primers through an NSS accelerated corrosion test of over 2000 hours with a twocoat system composed of Endurance primer 16J0/0083 + RAL 7031 polyurethane top coat (pre-treatment with high-thickness iron phosphating technology and passivation without rinsing, Haug). After 2000 hours, delamination at the cut was between 0 and 1.5 mm and corrosion at the cut was between 0 and 1.5 mm (Figure 11). Very good results were also obtained on the edges of the sheet, where no corrosion points could be detected (Figure 12).
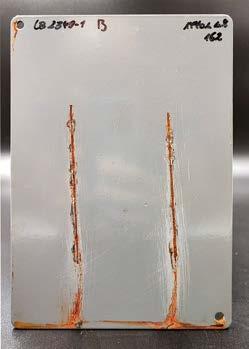
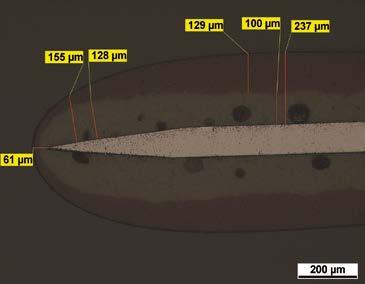



Conclusions
The Endurance 16J0 primer can be partially or fully cured before top coat application according to customer requirements. If a wrinkled top coat is used, it can also be applied wet-on-wet.
For the Endurance 16J0 primer, we chose two colours: 16J0/0083 RAL 1013 as a light hue and 16J0/0463 RAL 7021 as a dark hue. Since its wrinkled effect is very fine, the product can be recoated with any smooth top coat without altering its appearance. It can be safely said that this innovative primer sets a new benchmark in the field of corrosion protection primers.
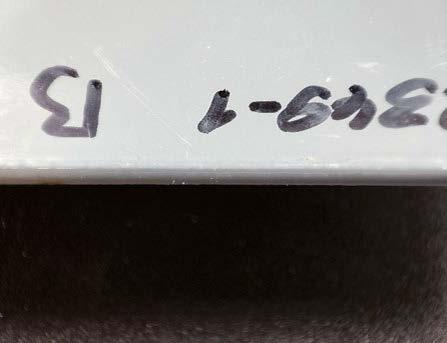
CHEMICAL MAKING SOLUTIONS
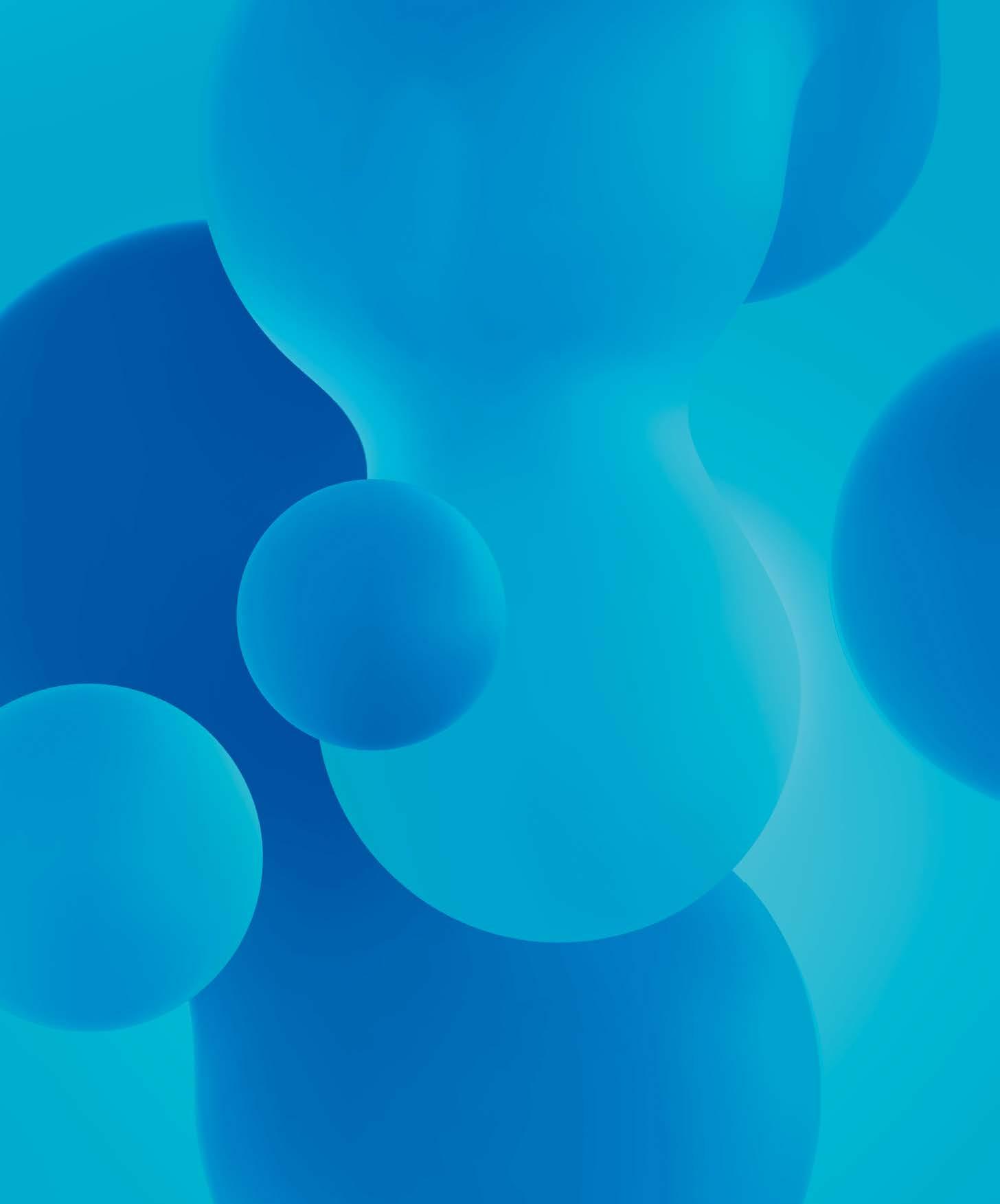
TRATTAMENTO ACQUE WATER TREATMENTS
SGRASSANTI INDUSTRIALI DEGREASERS
HIGHLIGHT OF THE MONTH
Market Trends in the Industrial Water Treatment Sector: An Analysis by Idrotecnica
From an interview with Federico Marcenaro,
CEO of Idrotecnica SrlIn its first thirty years of history, Idrotecnica, an Italian manufacturer of industrial water purification and demineralisation plants, has collected a long series of successes and achievements. In addition to being one of the first Italian companies to build a reverse osmosis treatment system, it now distributes its products almost all over the world while serving an increasingly significant number of industrial sectors. We interviewed its CEO, Federico Marcenaro, to outline the milestones in the history of Idrotecnica and analyse the current market trends in the field of water treatment.
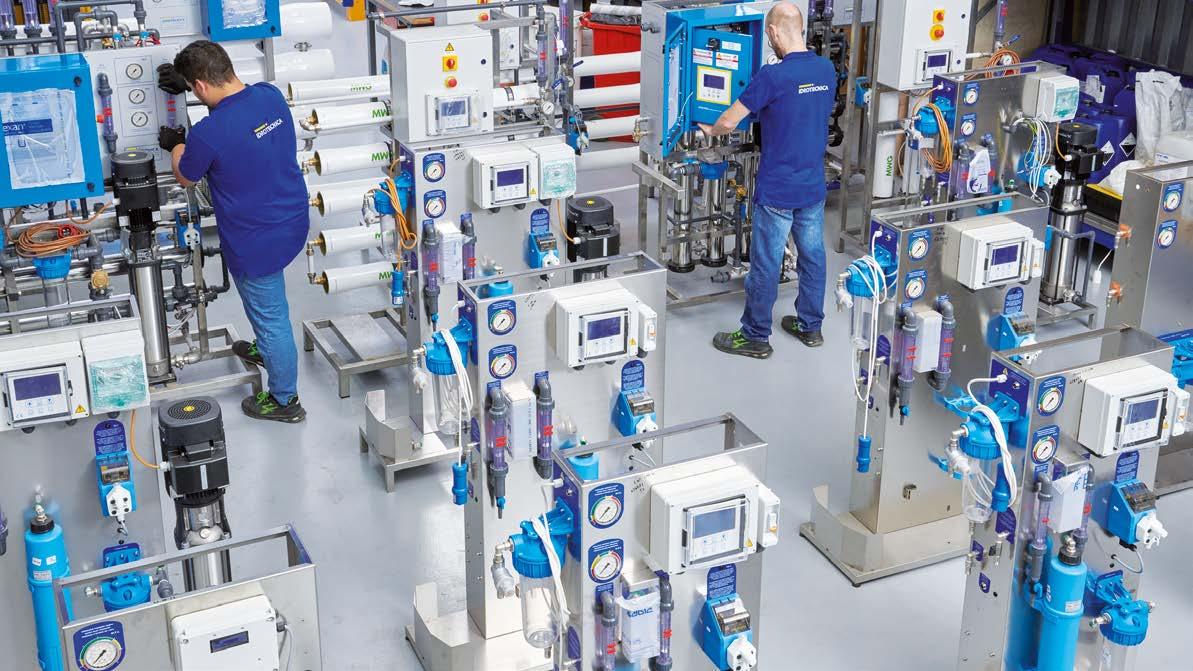
Water is a key resource in many industrial sectors and its treatment guarantees improved process performance as well as greater environmental protection. Purifying and/or demineralising water for industrial processes through purpose-built systems and plants is therefore a factor of primary importance, without which the entire production cycle would grind to a halt leading to significant production stoppages and cost and time increases.
In the case of the surface treatment sector, this plays an indispensable role in the pre-treatment phases prior to coating, as using demineralised water in the last rinsing stage enhances corrosion resistance and improves paint adhesion. The most common treatment technologies are reverse osmosis and ion exchange. ipcm®_International Paint&Coating Magazine delved into the main features and advantages of both processes in this interview with Federico Marcenaro, the CEO of Idrotecnica Srl (Genoa, Italy).
About Idrotecnica
The history of Idrotecnica Srl, an Italian company specialising in the production of water purification and demineralisation systems, began in 1991. Already with a considerable wealth of experience and expertise, its owners decided to use their skills and know-how to design and implement industrial water treatment solutions and specialised particularly in the production of ion exchange and reverse osmosis plants. In 1993, Idrotecnica was therefore one of the first companies able to supply the Italian market with this innovative technology, which was still little known at the time. From that moment on, the company began to collect a series of important successes and achievements: the continuously increasing demand allowed it to structure itself in a more complex manner, progressively hire more technicians, and move to a larger factory located in the Bolzaneto district of Genoa. In the early 2000s, Idrotecnica began exhibiting its technologies at numerous international trade fairs and industry events and it succeeded in reaching new markets and industrial sectors. Today, its plants are in use in almost every corner of the globe, from Europe to Latin America and from North Africa to Oceania, and serve a variety of industries, including coating, industrial cleaning, cosmetics, pharmaceuticals, and research and analysis laboratories.
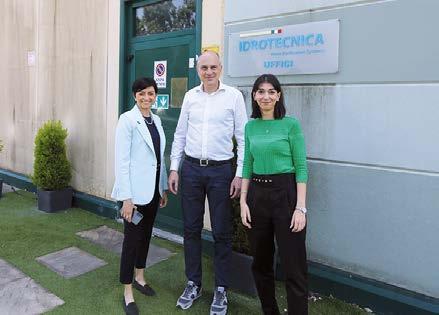
The choice to specialise exclusively in water demineralisation processes
Idrotecnica was founded based on a clear philosophy:
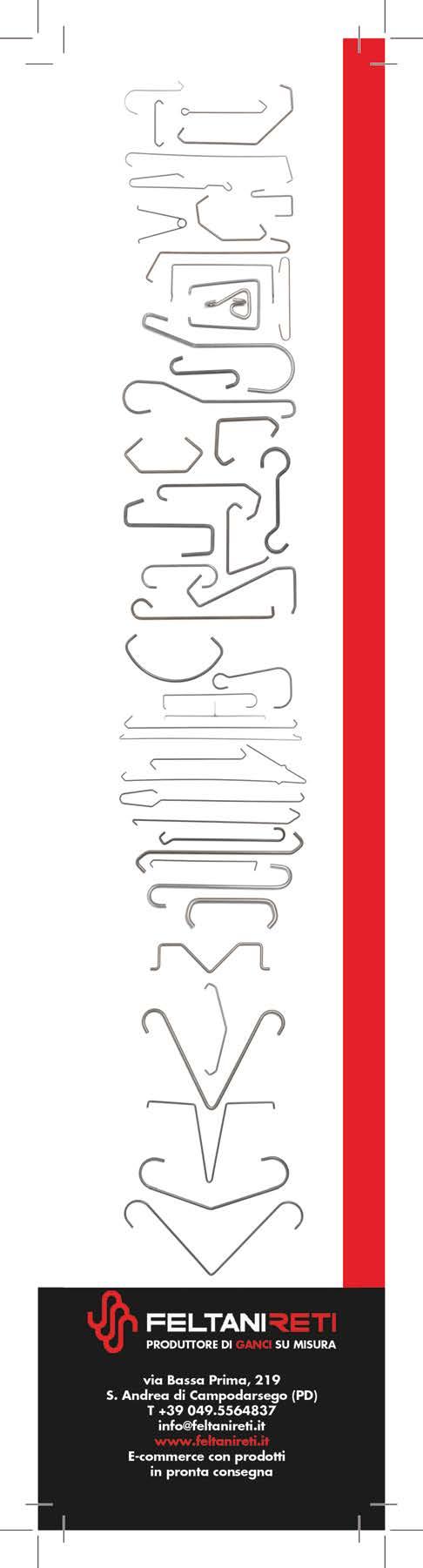
specialising in one core business, namely water demineralisation, and having in-depth technical knowledge of the application fields in which its plants can be installed. “Stemming from the desire to devote all our skills, time, and resources to a single industry, this choice enables us to offer our customers a fast and effective pre and after-sales service. Our team is always able to provide technical support in less than an hour, even in English and in different time zones for companies working in other continents, as well as shipping any spare parts in about 24 hours.”
“We are acutely aware of the responsibility our machines bear as they feed lines that are of far greater technical and economic importance and, for this reason, we invest daily in our customer service and work hard to develop systems that are extremely user-friendly and easy to install and use, yet robust and reliable.” This philosophy has certainly rewarded Idrotecnica, allowing it to position itself on the market as a trustworthy partner and to grow steadily in its first thirty years in business, operating in more and more industrial sectors and markets and supplying more and more companies with its systems.
A wide range of standard and customised plants
To meet customer needs, Idrotecnica’s production department is equipped to produce both standard and customised systems and devices. The standard range of water filtration and demineralisation plants using ion exchange and reverse osmosis technology includes around 130 different models, which are delivered in most cases in less than a month (often in one or two weeks). “The extreme modularity and flexibility of our plants enable us to offer ideal solutions that are in line with our customers’ production requirements. However, if our standard products do not meet their specifications, we can always tailor the most suitable plant solution in terms of technology, reliability, and running costs.”
Market trends
“In the early 1990s, Idrotecnica was one of the few Italian companies to believe in the potential of the reverse osmosis technology, based on a physical principle that at the time was still little known and widespread at the industrial level. For decades,
various industries have in fact continued to prefer ion exchange demineralisers. However, in recent years, our company has been experiencing an exponential increase in demand for reverse osmosis plants at the expense of the ion exchange technology in several industrial sectors, including the coating industry.” One of the main reasons why companies now prefer the reverse osmosis process is the absence of hazardous chemical agents such as hydrochloric acid and caustic soda, which results in greater safety for the environment and the operators and facilitates discharge operations. The reverse osmosis process ensures much more streamlined water management: the semi-permeable membrane that acts as a filter removes almost all the present substances from the liquid, which, with the right precautions and following the advice of a competent technician, can then flow into the sewer without further treatment. Furthermore, the performance degree of the reverse osmosis process depends neither on the presence or absence of salts in the feed water nor on the type of water (soft or hard): this further differentiates it from the ion exchange technology, whose performance is tightly related to water quality. The main disadvantage of reverse osmosis compared to ion exchange, on the other hand, relates to water saving, as ion exchange demineralisers can recirculate the liquid inside the cleaning tunnel and control its conductivity, thus significantly reducing water consumption.
“Despite the market’s preference for reverse osmosis treatments, Idrotecnica strives to identify the ideal solution together with each customer by taking into consideration several factors, including the company’s production cycle, the plants used in the factory, the technical skills of operators, and the way products are disposed of.”
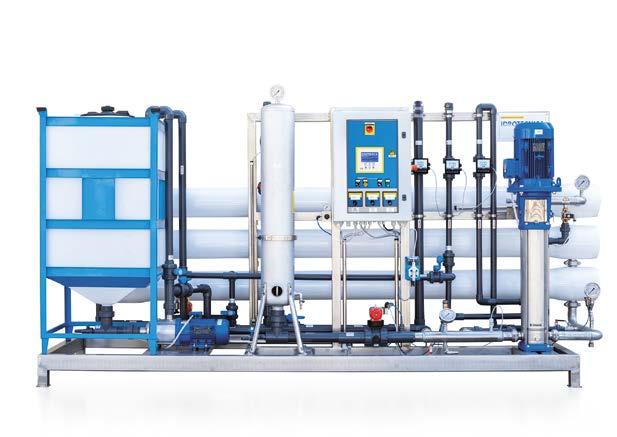

Future projects
“Idrotecnica is an extremely well-established company with significant experience, but it also maintains a fresh and dynamic approach typical of a start-up. At the same time, it has set itself the goal of putting its customers and their satisfaction at the centre of every activity and project since the year of its foundation. This is why, given the increase in demand that we have been experiencing over the past few years and that is continuing steadily, in the coming months we are going to hire further technical staff capable of supporting our customers and providing them with excellent service. In addition, to facilitate the management of our products, we plan to install some Industry 4.0-oriented systems even on cheaper and smaller plants. Currently, only our most complex systems are equipped with 4.0 solutions, but we believe it is crucial to provide both companies and plant engineering firms interfacing with end customers with the possibility to remotely manage all the components that make up their plants.”
E VOLUTION TO E -MOBILITY
Our 70 years experience in Surface Treatment is ready for the E-Mobility market.
Research, innovation, development.
In 70 years, our vision towards the future has never stopped. Today, Tecnofirma provides quality to the electric market which is the most evolving technology in the automotive industry. Our impregnation, cleaning and painting plants are the result of the constant commitment to offer cutting-edge solutions and products anytime, anywhere.
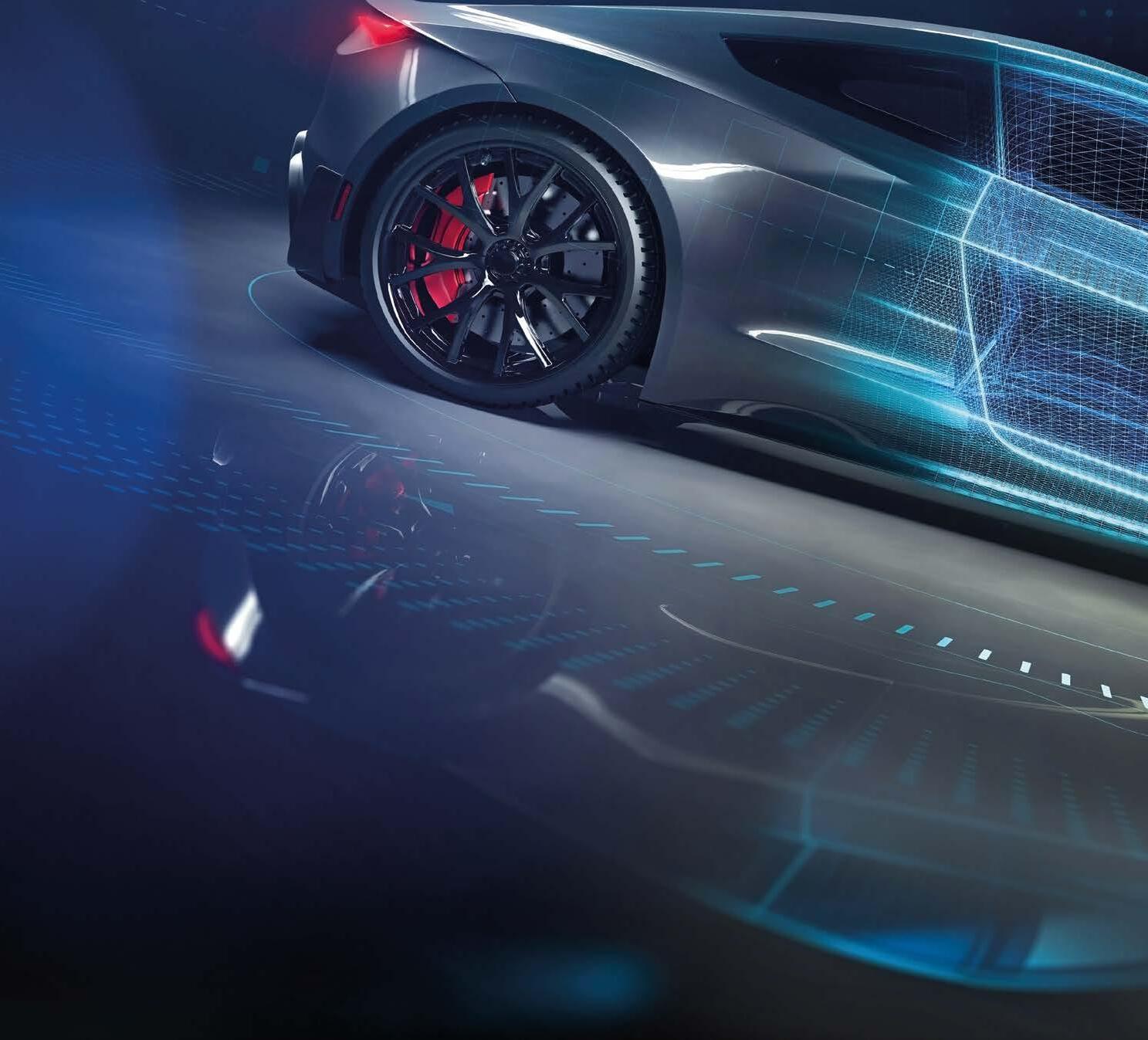

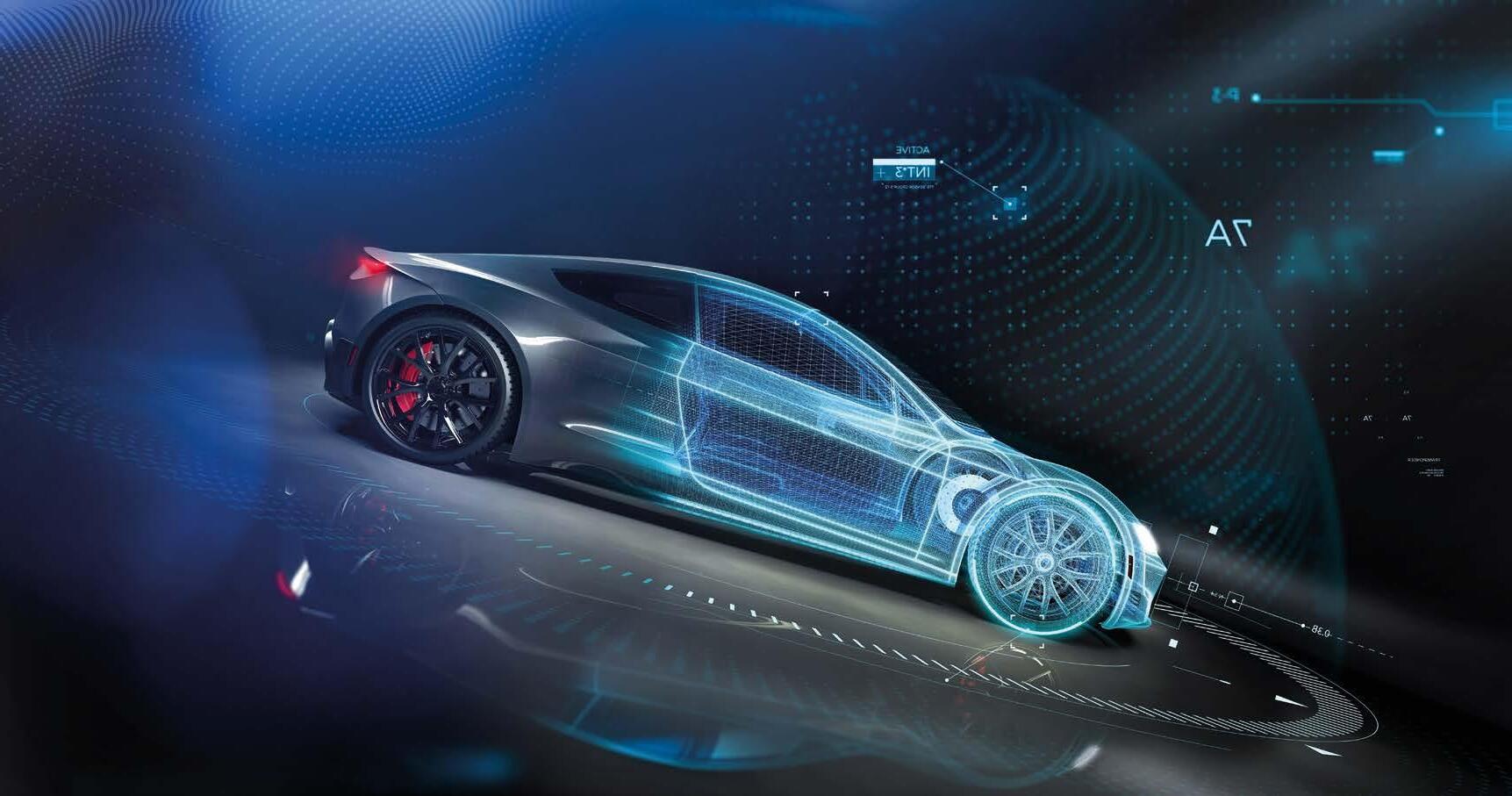
FOCUS ON TECHNOLOGY
In Portugal’s Bike Valley, a Winning Partnership with a Powder Coating Manufacturer Raises the Bar on Finishing Quality
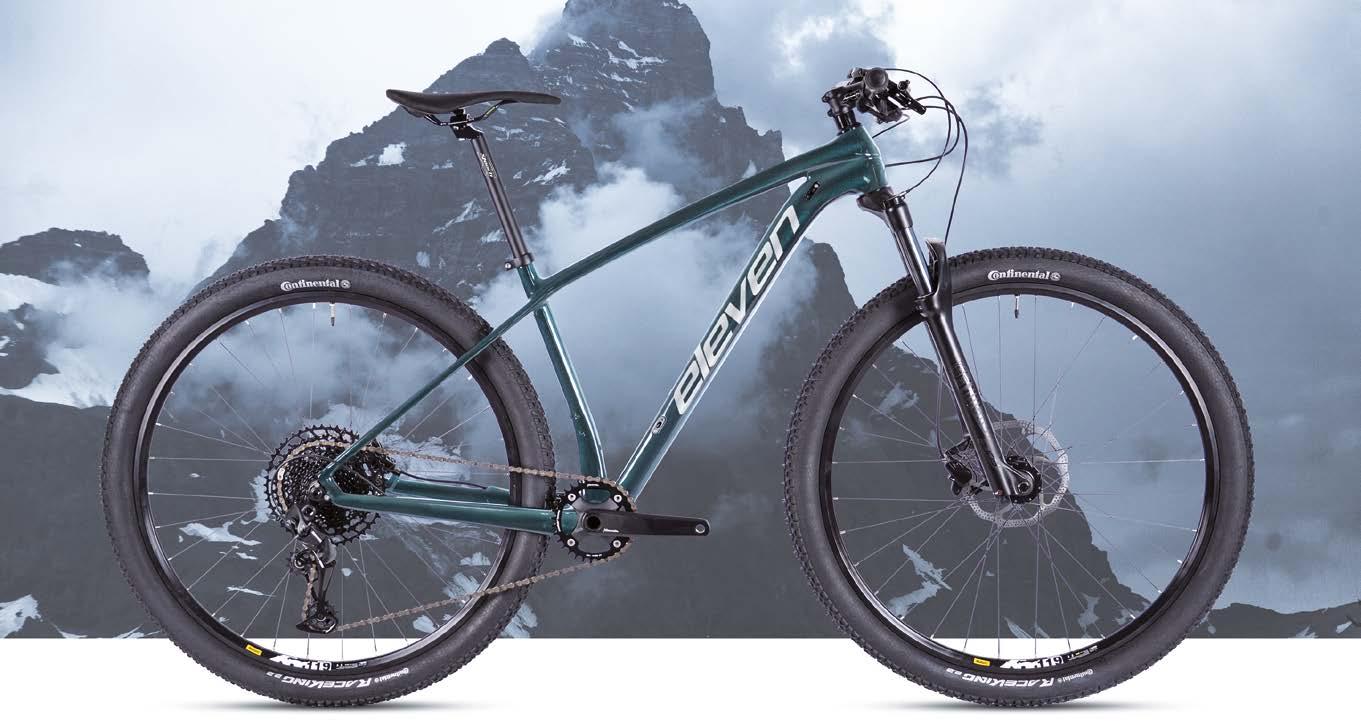
Development of polyester powder coatings and colour matching: these are the growth tools that Portuguese company InCycles, specialising in the assembly and sale of electric and traditional bicycles, has been implementing together with one of its paint suppliers, ST Powder Coatings. Its aim is to change the concept of urban mobility as we know it and raise the market’s appreciation of products coated with powders instead of liquid paints.
In February, the European Parliament decisively implemented its Cycling Strategy, instructing the Commission to double the number of kilometres of bike paths in Europe by 20301. According to the main industry associations, this marks an important turning point in the
1 https://www.europarl.europa.eu/doceo/document/B-9-2023-0102_EN.html
development of a more conscious approach to this rapidly developing sector at the European level. As stated in the press release of the European Cyclists’ Federation (ECF)2, “The call marks a recognition of cycling as a fully-fledged mode of transport and key industrial asset
2 https://ecf.com/civicrm/mailing/view?id=5606&reset=1
to meet long-term climate and clean manufacturing objectives.” The statement ends with a wish: “Cycling stakeholders also hope that the proposed designation of 2024 as the European Year of Cycling […] encourages national governments to take additional actions such as reducing VAT rates, multiplying initiatives to promote cycling and replicating the “Portugal Bike Valley” reindustrialisation success story in other regions, with targeted support from European funding programmes.”
The success case cited refers to the Águeda area, south of Porto, where the bicycle (particularly e-bike) manufacturing industry has become so flourishing that Portugal has become the largest producer of bicycles in the EU. This nation of 10 million people, just over 2% of the European Union’s population, produces a quarter of the continent’s bicycles. Such a development was the result of a growing passion for cycling in Europe particularly after the pandemic period and it has been completely changing the concept of urban mobility.
To provide an idea of how much this sector has developed, right in the heart of Portugal’s Bike Valley, we visited a company that has seen its turnover multiply 22-fold in the space of a few years – from 3 million Euros in 2018 to 65 million last year – and the number of its employees grow from 15 to 300. InCycles Bike Group (Águeda) specialises in the assembly, powder coating, and distribution of e-bikes and traditional bicycles both for major international brands and under its own brand, Eleven.
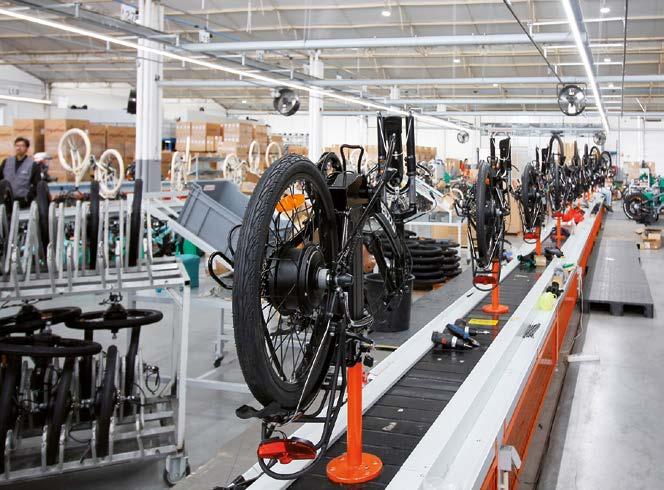
Today, coating operations play an increasingly important role in its production process, whose focus on paint sustainability is in line with
the vision of clean manufacturing as advocated by the European Parliament’s motion. “About three years ago,” explains Pedro Conceição, the General Manager of InCycles, “we started a winning partnership with the Italian powder coatings manufacturer ST Powder Coatings, which in 2018 opened a branch in Maia, in the industrial district of Porto, not far from our headquarters. From the outset, powders have been our main choice of finish for two reasons. Firstly, because they are characterised by greater resistance in harsh environmental conditions, which is a key element especially for our Northern European partners. Secondly, because they are environmentally friendly paints producing no VOC emissions and fully recyclable: an increasing number of customers consider this aspect a discriminating factor when choosing their supplier.”
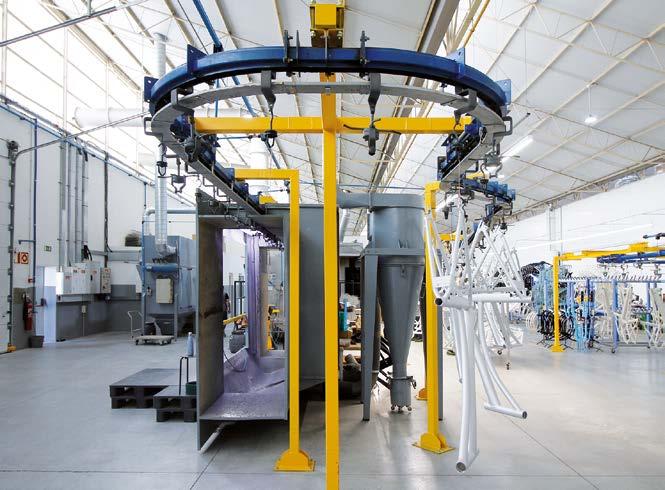
The future is electric even for bicycles
“We are riding the wave of the exponential growth of two-wheel mobility occurring all over Europe,” confirms Conceição. “We have been focussing on electric products and, to date, we can say that it has been the winning choice. This is evidenced, for example, by an important project aimed at making e-bikes available for hire in all major European cities.” To cope with the production peak, this Portuguese company recently invested in a new plant merging 1 coating system, 4 assembly lines (of which 3 are devoted to e-bikes and 1 to traditional bicycles,) and 6 lines for the production of wheels.
Paint shop manager Alberto Cardoso explains the main steps in InCycles Bike Group’s production process: “We receive our components already
shot blasted; we only perform manual sanding if necessary. The parts reach directly our coating department, where they are loaded onto the conveyor to be taken to the first station for manual powder application. They then move to the curing oven before the required water-based decals are applied. This is followed by a drying phase, the removal of decal masks, and the application of the final top coat, which can be glossy or matte. The coating cycle ends with the final curing phase in the oven. Afterwards, the parts are ready to be transported to the assembly department, where they are placed on one of the 4 designated lines and subsequently packed and stored for final shipment.”
Investment in coating
“The internationalisation of our production,” notes Conceição, “called for the increase in the number of our assembly lines, but also for a growing investment in the powder coating line we had installed three years ago. The continuing demand for high-quality surface coatings is so strong that we would have already installed a further plant, if the war in Ukraine and the resulting negative global financial outlook had not stopped our project, hopefully only temporarily. The reason why it is important for us to focus on coating at this time is that the quality of the paint applied on the components imported from Asia does not meet the minimum requirements. The European Union is also taking action on this aspect with anti-dumping measures, stemming largely from the realisation that we are excessively dependent on the Asian market in the bicycle sector, too. Currently, 90% of the components we assemble in our factory are
sourced from China.” This trend, however, is changing, as evidenced by the already mentioned motion of the European Parliament, and more and more manufactured goods are now being produced in Europe in the cycling sector as well. “At present, therefore, the strategy that we consider successful for establishing ourselves in this complex market is to guarantee the best possible coating performance with two main objectives: finishing quality and production flexibility.”
A perfect partnership for growth
“Our first contact with ST Powder Coatings was decisive in the choice of our supplier,” states Cardoso. “Although we also apply liquid paints for special projects, we already knew that powders would be the perfect solution, especially to meet the need of Northern European customers, who are more demanding in terms of finishing quality and resistance in harsher climatic conditions than those in Southern Europe. Until our encounter with this Italian manufacturer, we had been using epoxy paint. Thanks to the tests suggested by its team, however, we realised that polyesters were better suited to give our finishes greater outdoor resistance and durability, especially in conditions of proximity to the sea, low temperatures, and exposure to snow or ice.
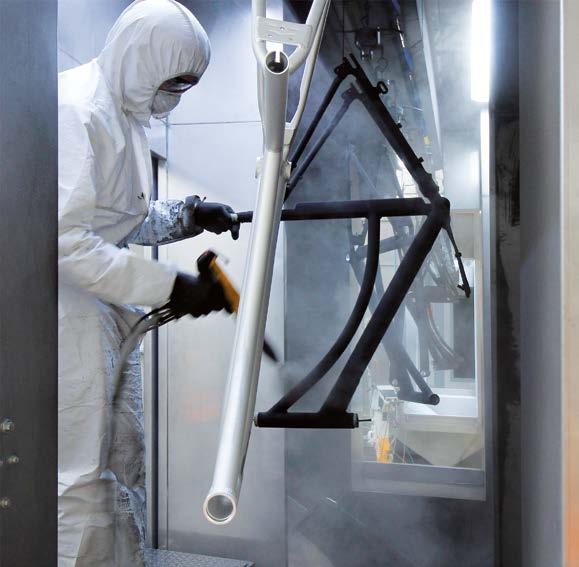
“Polyester powder coatings,” says José Carlos Manta, the general manager of ST Powder Coatings Portugal, “are available in both industrial and architectural quality. Polyester products are especially ideal for coating metals intended for outdoor use precisely because they ensure excellent resistance to chemical and weathering agents
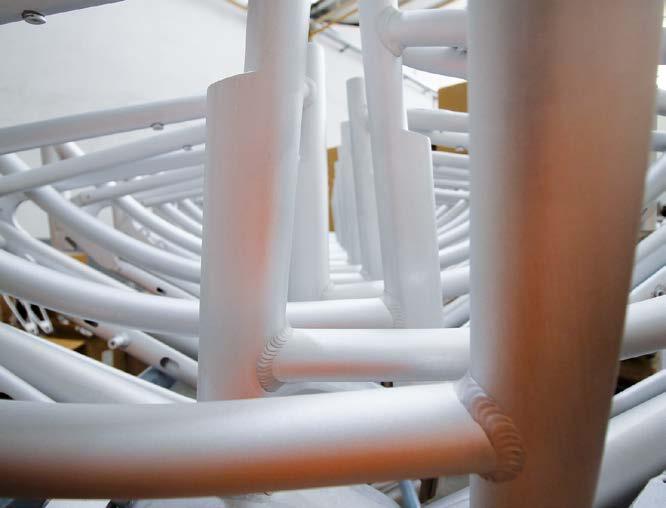
and excellent colour retention. Specifically, InCycles uses industrial polyester powders as standard and Qualicoat polyester powders for special requirements. Our laboratory formulates and develops powders according to every customer’s needs: for InCycles, we tried to develop the entire colour range they required to find the perfect colour match with the liquid-coated components from the Asian market. Actually, it is not always easy to find the perfect powder hue to match the distinctive, shiny, and sometimes “loud” metallic effect obtained with Chinese liquid paints. Colour matching with the coatings already applied on the components imported by InCycles is one of the most demanding challenges for our team.”
“Yet, ST Powder Coatings has managed to find the right balance,” notes Conceição. “Despite these issues, it has been able to provide us with colour matching solutions that meet all our customers’ requirements. The primers and powder top coats it supplies us with, even those with metallic and special effects, guarantee lowkey finishes that are definitely less showy than the liquid paints with the same effects or colours. This is why we are trying to convince our customers to choose powder coating whenever the hue developed by ST Powder Coatings is very close to that obtainable with a liquid product. The feedback from the market is currently very positive. In addition to such extreme care in searching for the most suitable solutions for our needs, we greatly appreciate other aspects, such as the speed and efficiency of ST Powder Coatings’ service and the reliability of its solutions. I guess this is partly due to its experience in
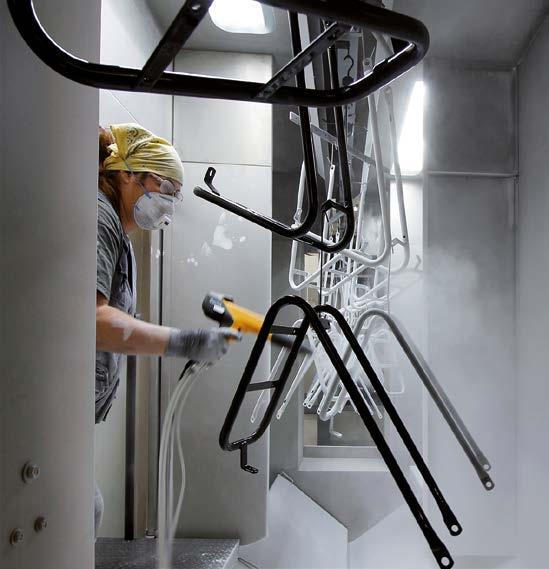
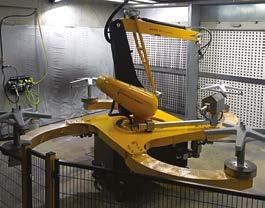
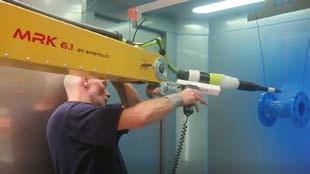
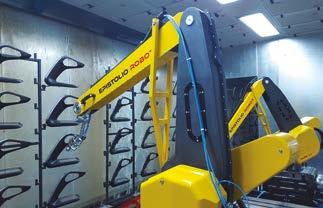

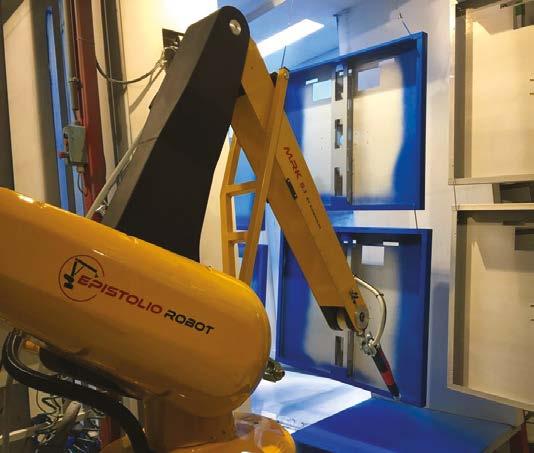
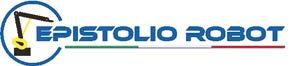
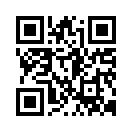
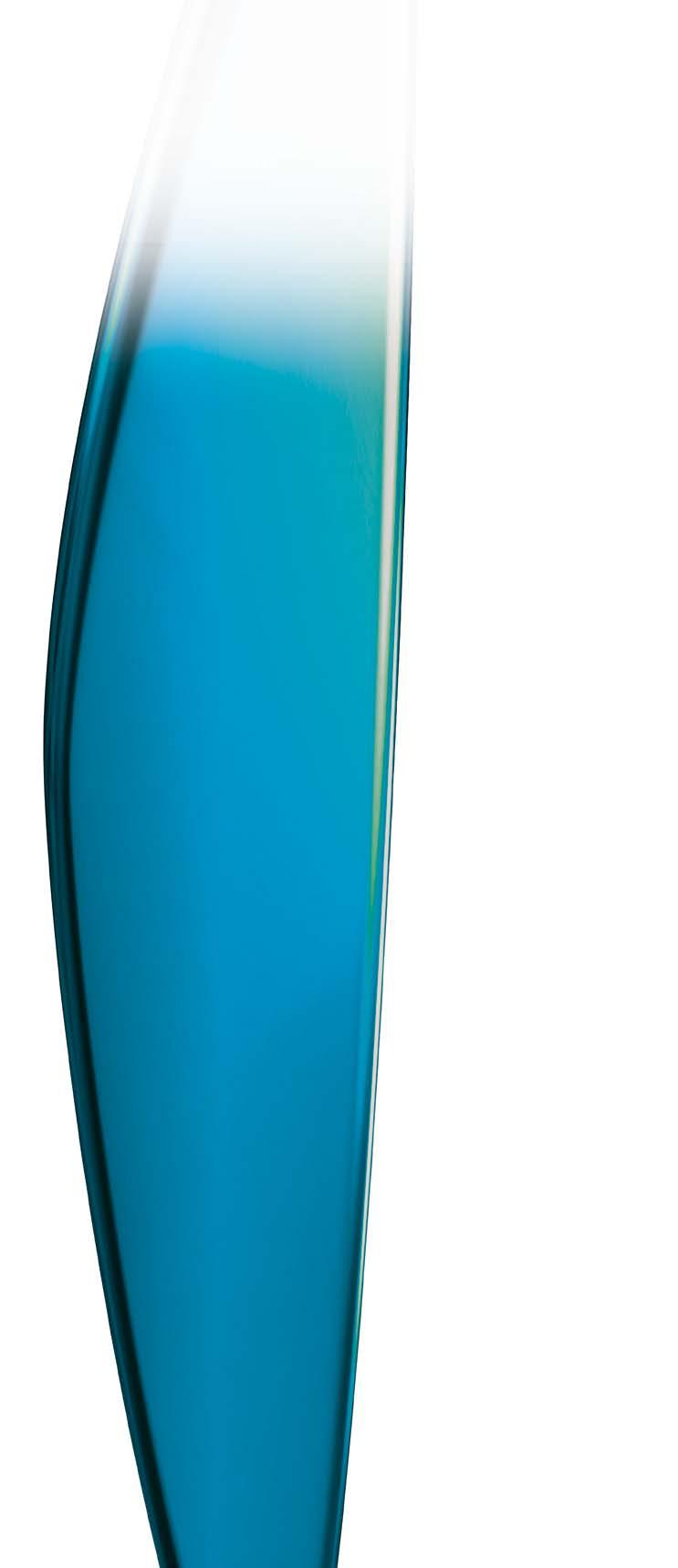
the field of bicycle manufacturing and coating, in which Italy and Veneto in particular, the home region of ST Powder Coatings, are more than well-established benchmarks.”
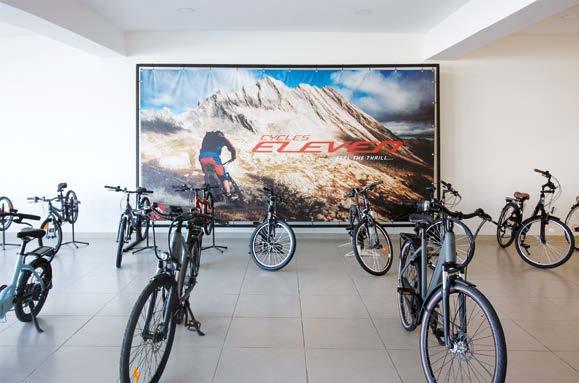
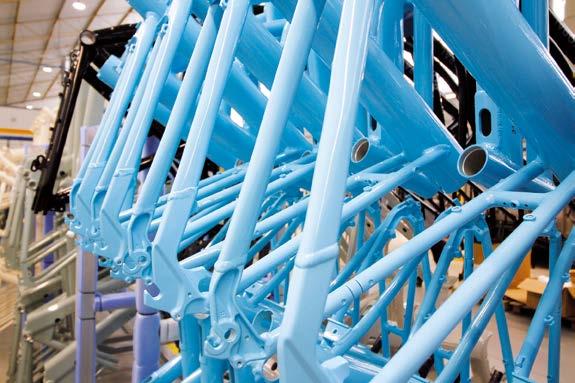
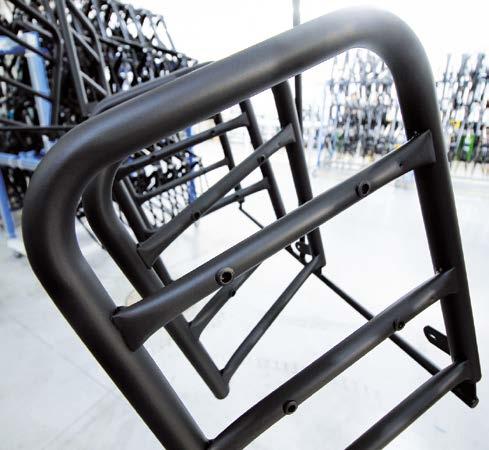
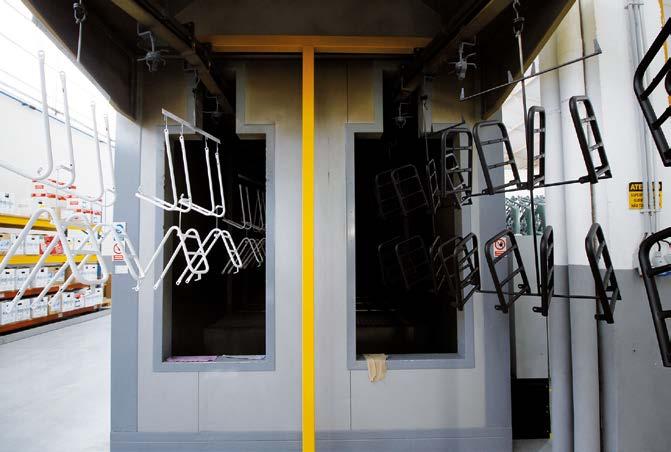
The bicycle becomes the protagonist of a sustainable mindset change
“We firmly believe that the daily use and acceptance of the bike as a means of transport,” concludes Conceição, “is an opportunity to implement non-polluting and sustainable mobility solutions that are an excellent alternative to traditional ones, with the ultimate aim
of improving the quality of life and human relations. The goal is to consolidate the change of mentality already initiated, which has become necessary in light of the current world economic situation, in which the restrictions imposed on low-cost products from the Asian market can be a boost to the growth of the European manufacturing sector. InCycles is ready to face this breakthrough with the support of skilled and flexible partners such as ST Powder Coatings, which has contributed decisively to the growth of our company, since powder coating is becoming an increasingly decisive strategic asset in the choices of our customers in terms of both finishing quality and sustainability.”
FASTRIP T2-120 MIX our brand new and most compact paint stripping system
FASTRIP T2-120 MIX uses the mechanical action of the paint stripper on the parts that is ensured by the hydrostatic thrust generated by a specially designed mixer.
• Rectangular tank in AISI 304 stainless steel, 450 x 700 x h300 mm, with 20/10 thick walls and a 1” bottom valve for easy emptying
• Steel mixer for continuous fluid circulation, enhancing paint stripping efficiency and heating system performance
• Motor is protected from heat and an electric lock that stops the mixer when the lid is opened

• Integrated control panel, removable lid with thermal insulation and pistons for easy access.
• Safety, efficiency, and superior quality.
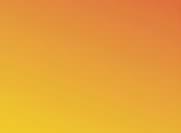
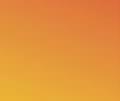
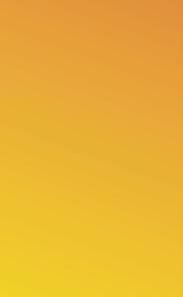
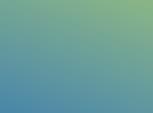
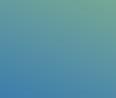
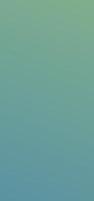
The Difference in the Pretreatment of Aluminium for Different Climatic Environments Based on the Example of GSB-Certified Coating Companies
Philipp Mader,In GSB’s field of activity, which is dedicated to the quality assurance of coatings on aluminium, steel and galvanised steel in the field of architecture, the question of the correct pretreatment for a particular environment is part of the daily business.
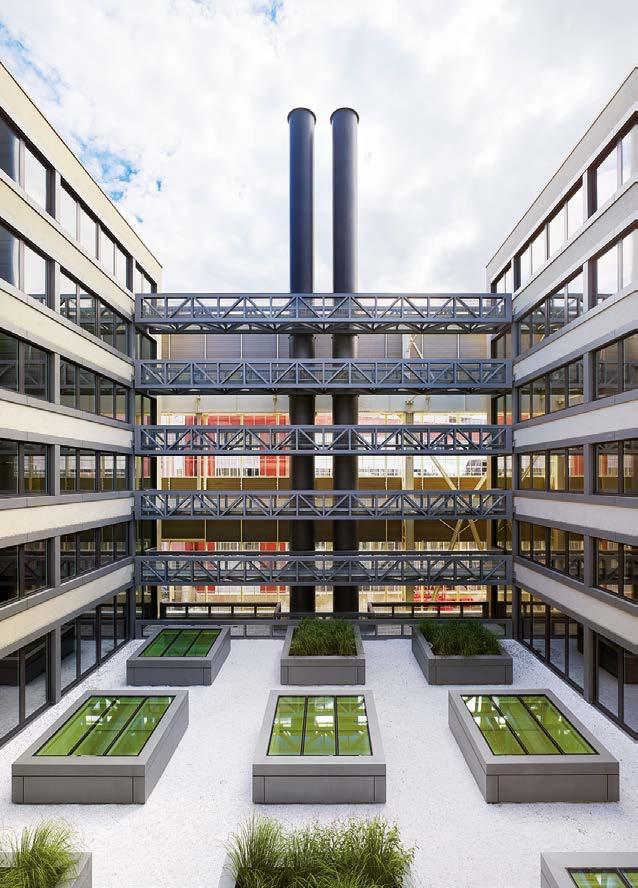
The quality assurance system has been developed over decades, and there are various GSB Quality Seals for different areas of application. So how is a quality assurance system dedicated to coatings for outdoor use by means of powder and liquid paint structured?
The GSB quality assurance system in a nutshell
The best way to understand how to select a pretreatment for an exterior coating is to go through GSB’s quality assurance system briefly. Today we will limit ourselves to the substrate aluminium.
A coating is only GSB-compliant if it has been pretreated with GSB-certified chrome or chrome VI-free pretreatment chemicals in an appropriate overall process. Alternatively, a pretreatment can also be carried out by means of pre-anodising - more on this later.
Furthermore, it is mandatory that the coating is carried out by GSB-certified coating companies and that GSB-certified coating powders or liquid paints (coating materials) are used.
Coater inspections are the centrepiece of securing the coating process chain. GSB-certified coating companies are audited twice a year unannounced by independent and accredited testing institutes.
Today we do not want to dwell too much on what are considered to be among the most stringent tests on the architecture market for pretreatment chemicals and coating materials, but rather on the inspections carried out at the coating companies.
Corrosivity categories and differences in GSB quality seals
There are different quality seals, which essentially differ in the corrosion tests carried out as part of the audits and the way how they are evaluated. In the case of coating companies that are certified with the Standard or Master
In the market of aluminium coatings, there is sometimes great confusion when it comes to planning and choosing the correct pretreatment.
Quality Seal without an additional seal, the inspector takes sample sheets from production as part of the audits. An acetic acid salt spray test is then carried out on the sheets (according to ISO 9227). The test lasts 1000 hours, the delamination at the T-cut must be at a maximum of dmax ≤ 1 mm. For the bubble degree, 0 S(0) is mandatory. The coatings by GSB Standard and Master Coaters are the choice for use in environments that can be characterised by the corrosivity category C3 (following ISO 9223).
In addition, there are GSB Master and GSB Premium Coaters that carry the additional seal Sea Proof. In addition to the AASS test, the filiform corrosion test is carried out in those cases (according to ISO 4623-2). Here, the maximum filament length shall not exceed 2 mm. Furthermore, there is a special value for the filiform corrosion. This value (F) is calculated from the average filament length multiplied by the filament frequency and must not exceed 0.3.
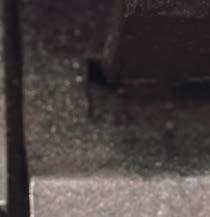
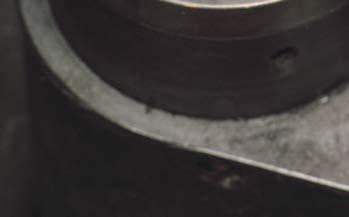
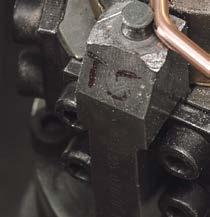
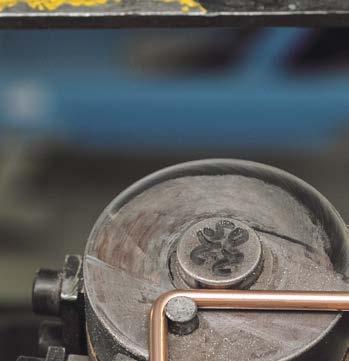
Coatings of GSB Master and Premium Coaters having the additional seal Sea Proof can be used in environments that can be characterised by the corrosivity category C4 (following ISO 9223). Then there are GSB Master and GSB Premium coaters, which have the

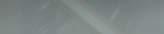
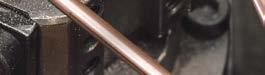

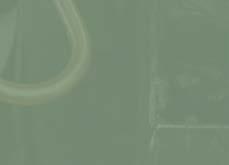

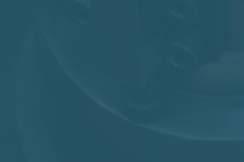
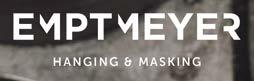
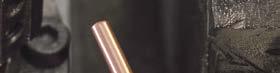
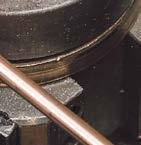

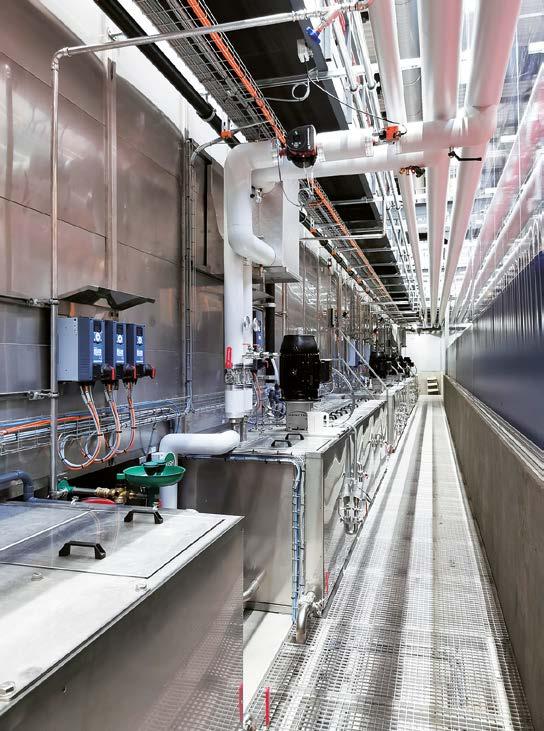
additional seal pre-anodisation Sea Proof Plus. Here, too, the maximum filament length shall not exceed 2 mm. However, the rule for F is stricter (F ≤ 0.1). Compared to coaters that do not carry an additional seal or the additional seal Sea Proof, coaters with the additional seal Pre-anodisation Sea Proof Plus carry out a pre-anodising. The difference between decorative anodising and pre-anodising is that in the case of pre-anodising, the pores remain open and thus help to ensure good adhesion of the coating applied afterwards. If a coating is to be used in an environment that can be characterised by the corrosivity class C5, coaters with the additional seal Pre-anodisation Sea Proof Plus are the companies of choice to carry out the job. Typically, such a corrosive environment is found on a coastline where the air has a high salt content for example.
Which corrosivity category applies to my application?

But how do you know which corrosivity category to use to characterise an environment? There are overview maps that divide countries into categories, for example. However, these maps can only be used as rough indicators. The corrosiveness of the environment can vary

enormously locally, even in small areas - for example, copper abrasion from overhead lines can increase corrosiveness. Industrial facilities or heavily frequented roads can also increase the corrosiveness. The only way to reliably determine the corrosivity category is to take a close look at the target location with an expert. ISO 9223 gives a guideline to determine the corrosivity class based on the mass loss for aluminium, steel, copper and zinc for the first year exposure. That would be the first way to determine the corrosivity class and is done by evaluation the uniform corrosion.
In this case, ISO 9223 states that it is not possible to determine uniform and localised corrosion of aluminium for the first year by outdoor testing of specimen. The reason for this is the passivation behaviour and the decreasing corrosion rates of aluminium over time. If the evaluation based on the corrosion rate is not possible, the ISO 9223 allows to determine the corrosivity category based on environmental information – of course this leaves room for interpretation.
If you are unsure and fluctuate between two corrosivity categories, for example, you should opt for the next higher corrosivity categoryespecially if you are uncertain about the corrosivity of the environment in the future. It is also important to consider possible future changes in the corrosiveness of the environment. These can result, for example, from new roads being built in the area - emissions and also input from road salt can additionally increase the corrosiveness.
At the end of the day, aluminium alloys used in construction (Profiles EN AW-6060 and EN AW-6063; for Sheets EN AW-5005/5005a and EN AW5754) can be left in normal weathering conditions without coating and without having to worry about structural damage. Matching the coating to the corrosiveness of the environment thus has a purely decorative
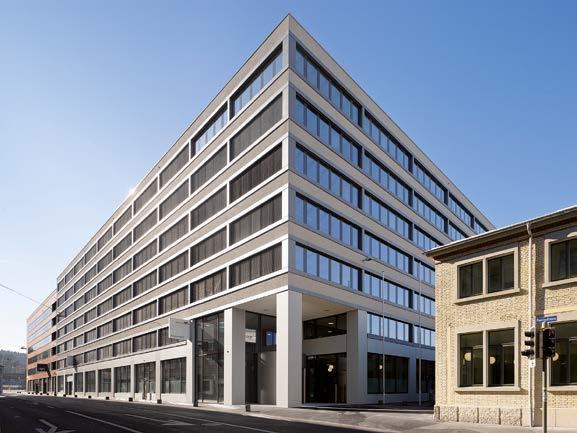
purpose in the case of aluminium (for the alloys mentioned above). “Matching the coating to the corrosivity category” goes far beyond ISO 9223, which does not take coatings into account. This is why the GSB has based the recommendations for coatings on aluminium for different environments on the corrosivity categories of the ISO 9223.
The coating is applied - a few words about cleaning
Now assume that the project has been completed and the coating has been properly planned and carried out by a GSB Coater. What happens next? Adequate cleaning is extremely important and the GSB makes recommendations here regarding cleaning intervals. For coatings for projects in environments that can be characterised by the corrosivity categories C3 and C4, the GSB recommends one cleaning per year. For projects in areas that can be characterised by the category C5, GSB recommends two cleanings per year. These cleaning intervals are part of the general terms and conditions of many GSB Coaters.
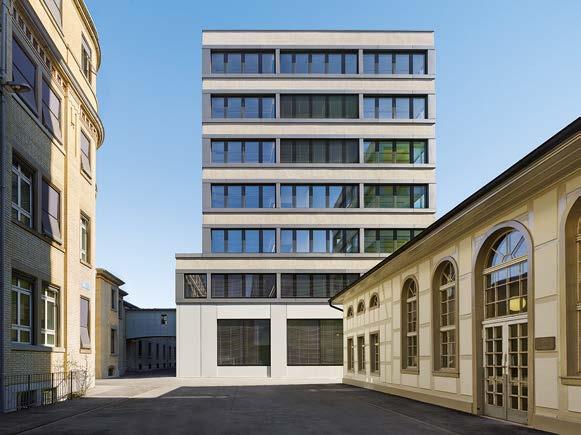
A final word on ISO 9223 and a practical recommendation
At the end of the day, the following is recommended for the coating of aluminium:
1. Determine the corrosiveness of the environment in the area of intended use.
2. Select GSB coater based on the corrosivity category:
• GSB Standard or Master without additional seal: C3
• GSB Master or Premium Coater with additional seal Sea Proof: C4
• GSB Master or Premium Coater with additional seal Pre-anodisation
Sea Proof Plus: C5.

The ILTOM Group’s Powder Coating Plant Provides Production Flexibility while Reducing Energy Consumption and Improving Quality
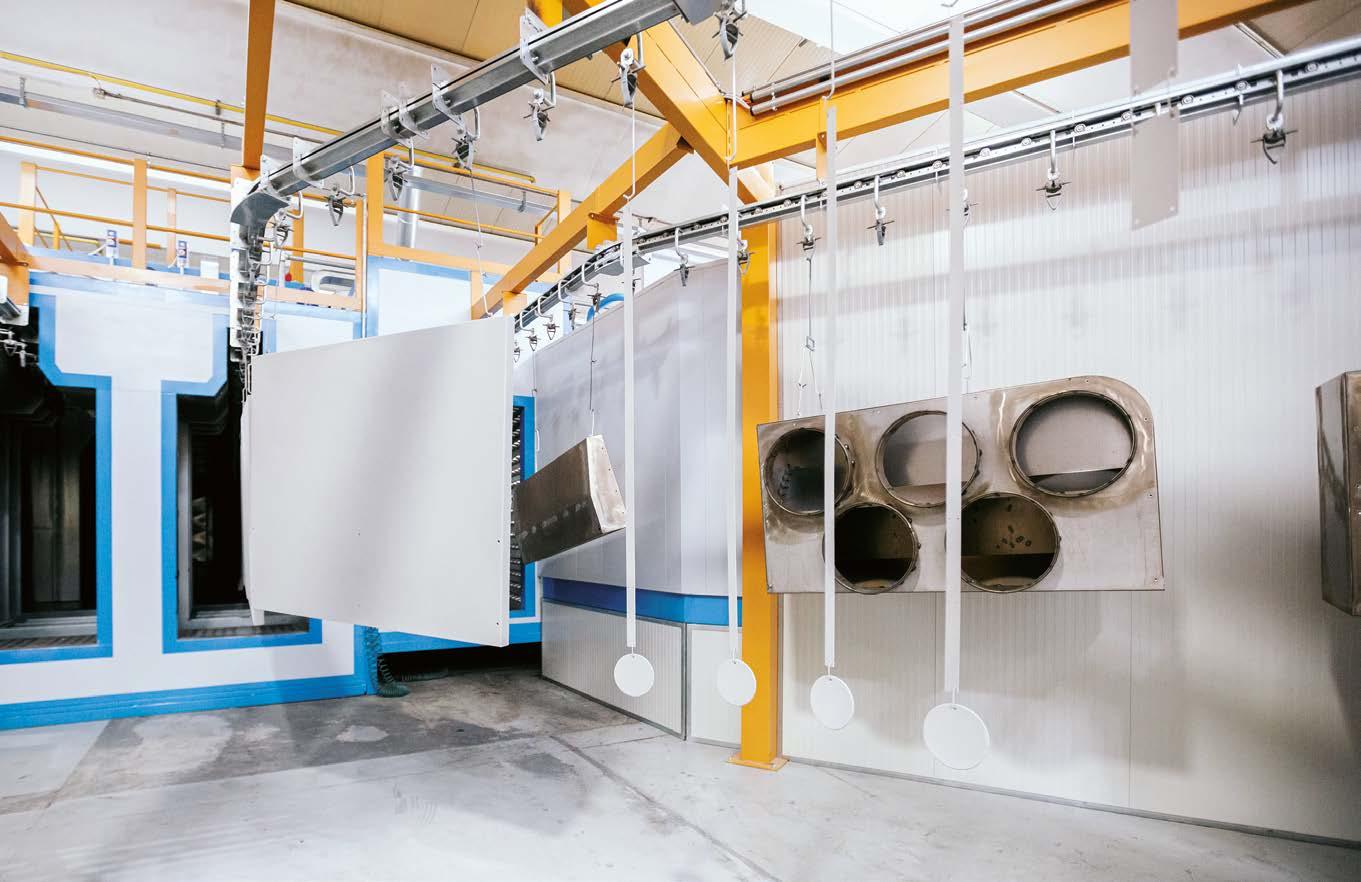
Over the years, the ILTOM Group has transformed itself from a small craft business into a renowned industrial holding company through a strategy of dimensional growth, production synergy, and innovative investment. Its latest acquisition was the new automatic powder coating plant designed and built by M.I. DUE, which allows it to handle components in different sizes and shapes while guaranteeing high quality, repeatability, and fast delivery.
Acommon strategy to stand out from competitors in an increasingly dynamic and global manufacturing environment is implementing highly efficient supply and logistics chains through smart devices, advanced technologies, and seamlessly interconnected processes that enable a timely and efficient response to customer needs.
The ILTOM Group is an international company headquartered in Romanengo (Cremona), whose implementation of this approach represents an Italian success case. Over the years, the company has pursued a growth strategy focusing on the acquisition of multiple production sites and their upgrade through technologically advanced and interconnected solutions, to ensure that all factories meet the same quality standards and can quickly satisfy any customer request. In doing so, it achieved a remarkable milestone last year, exceeding 100 million Euros in turnover for the first time. The ILTOM Group is a metalwork company with customers from several different industries and it is also strongly committed to environmental sustainability. That is why it has significantly invested in energy efficiency as well, with a focus on reducing its gas consumption. In line with its corporate strategy, the ILTOM Group recently invested in a new powder coating plant designed, built, and installed by M.I. DUE
S.R.L (Besana in Brianza, Monza e Brianza, Italy), which has enabled it to increase its production capacity while reducing energy consumption by 15% compared with conventional plants and always meeting the stringent technical specifications imposed by customers.
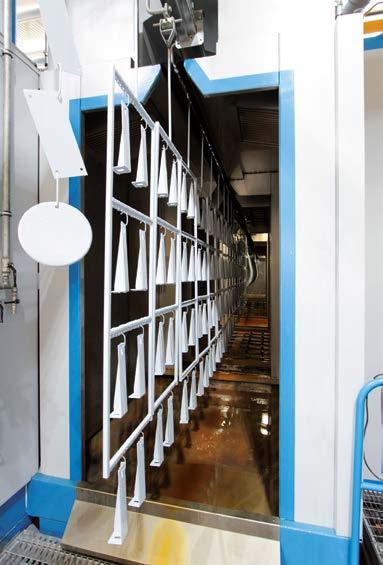
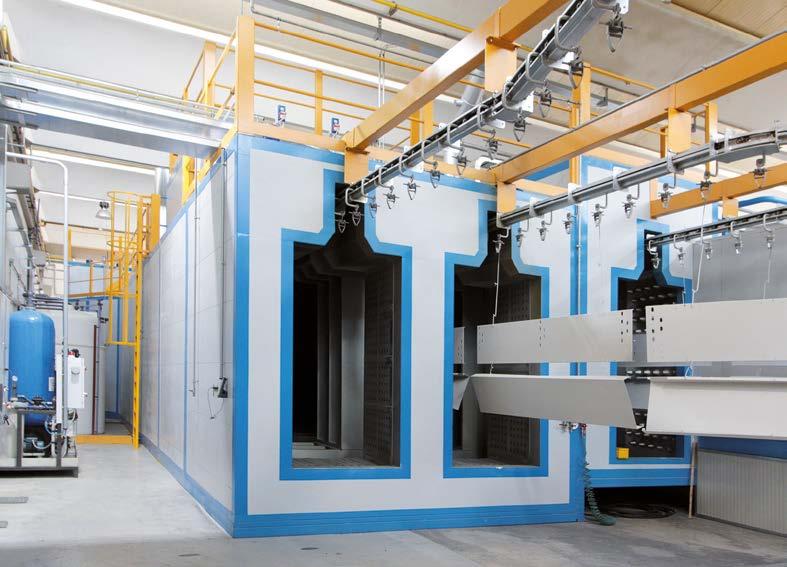
ILTOM: a family-run industrial holding company
The ILTOM Group is an industrial but family-owned holding company specialising in contract sheet metal processing. Founded in 1970 by Francesco Venturelli as a small workshop, it evolved over the years thanks to the entry of his sons Luca and Pierangelo Venturelli into the company in 1996, who fostered its growth exponentially. To support the increasing production rates, ILTOM acquired a new plant in Romanengo in 2000, where it still maintains its offices and some manufacturing departments today. Following the financial crisis in 2007, the Group also decided to expand into foreign markets, selling its products in France (which now accounts for 65% of its turnover), Switzerland, Hungary, Poland, Romania, and other non-European countries. “The ILTOM Group’s corporate structure is the result of a strategy in which production synergies, dimensional growth, innovation, and quality have always been considered the prerequisites to be competitive on the market. We have tried to grow gradually, combining
the increase in production volumes with the acquisition of other firms that would allow us not only to quickly meet our manufacturing needs, but also to expand into new sectors or geographical areas that we were previously unable to cover,” says Roberto Cagna, the purchasing and supply chain manager of ILTOM Spa. “These are all perfectly integrated into our Group’s logics: the SAP management system, production technologies, programming software, and quality procedures are in fact common elements for all our companies. This made it possible to obtain a Group’s quality certification and to become particularly flexible in handling peaks in demand; in the presence of any manufacturing issues, we can shift production among our various locations. The investment in a new coating plant provided by M.I. DUE, which replaced a previous line that was no longer able to meet our quality and repeatability requirements, was therefore part of this framework aimed at providing our international customers with a complete service, delivering readyfor-use parts in a short time and in compliance with the highest quality standards.”
From the selection of raw materials to the delivery of finished, packaged products
Today, the ILTOM Group produces structures and components for switchboards, electrical cabins, machine tools, food and beverage vending machines, air conditioning and heating systems, industrial and agricultural vehicles, medical and pharmaceutical instrumentation, and systems for the nuclear and electronics industries. Mould design and construction, precision sheet metal machining, and powder coating are integral parts of its core business. Its production flow starts with the acquisition of raw materials, i.e. coils or sheets of pickled, polished, galvanised, electrogalvanised, and aluminised steel sheet in different sizes, which are subjected to numerous machining processes such as blanking, punching, CO2 or fibre laser cutting, and bending with CNC machining centres. “As market demands are increasingly focusing on ever-smaller production volumes with just-in-time orders, the ILTOM Group has a variety of state-of-theart machinery and highly qualified personnel at its disposal to meet all requirements,” explains Roberto
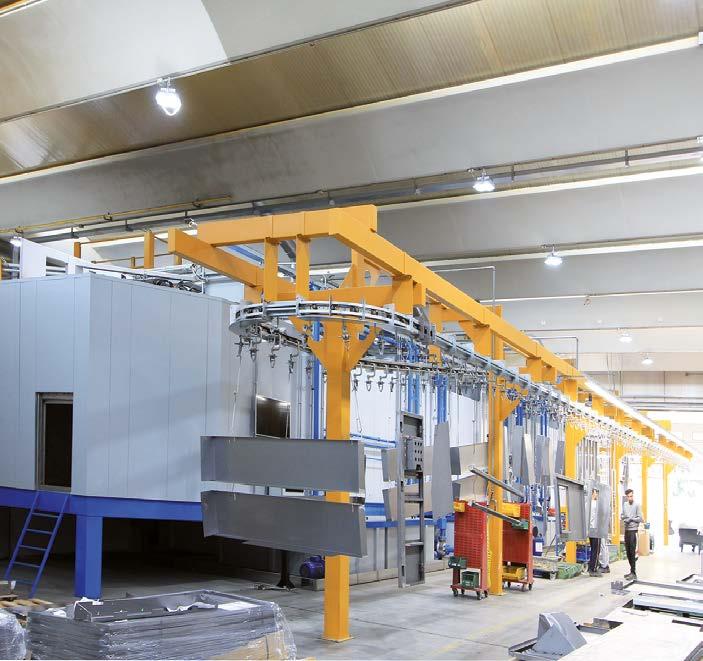
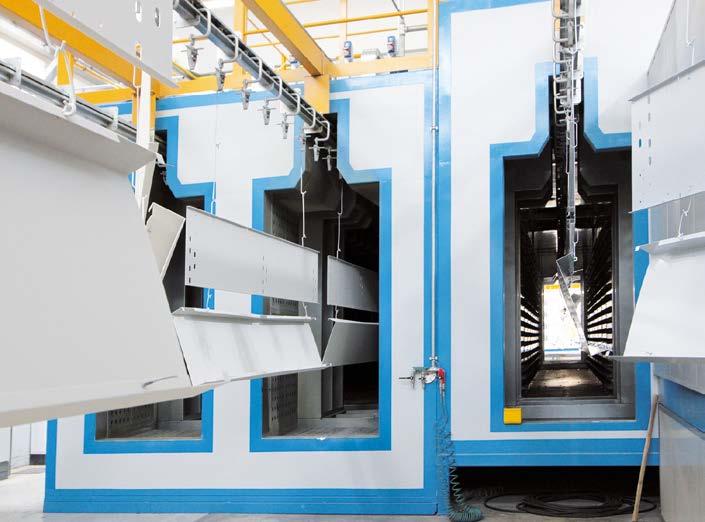
Cagna. After machining, the products are welded and assembled, powder coated, and finally mounted and packaged.
Different coating plants, same technical specifications

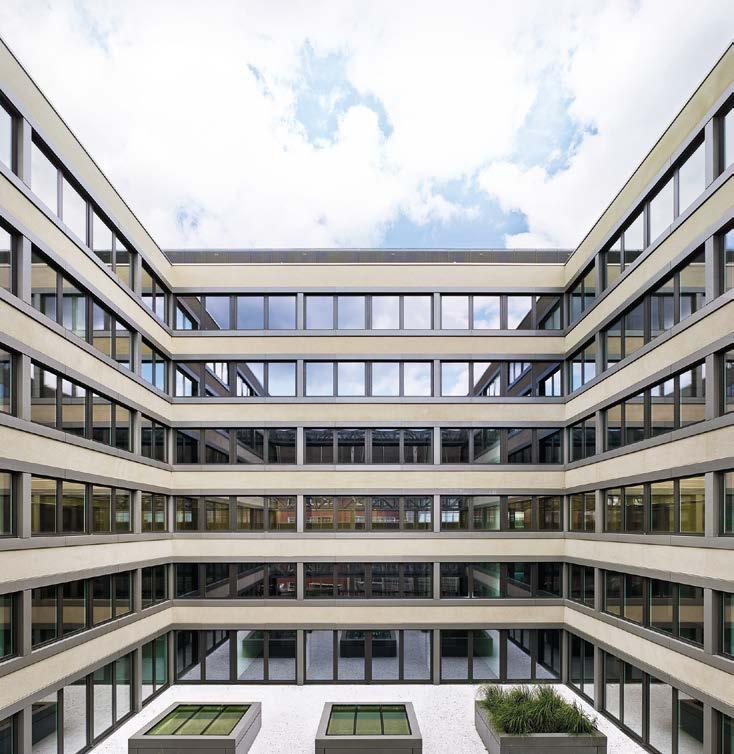
The ILTOM Group has many years of experience in the industrial coating sector thanks to the numerous powder application plants installed at its sites, which can treat all metal surfaces and guarantee the production of high-quality components with excellent corrosion resistance. “Powder coatings ensure high-quality finishes for a wide range of surfaces, providing excellent look and feel, long service life, high process efficiency, and the sustainable use of resources, as well as offering a wide range of colours and surface effects. This is why we have coating lines in our CMA, Paillet, Bruder Keller, and Bresto factories in France and in the Fraven one in Romania, in addition to the two lines installed at the Romanengo site, which allow us to guarantee very short delivery times despite the reduced warehouses,” adds Cagna.
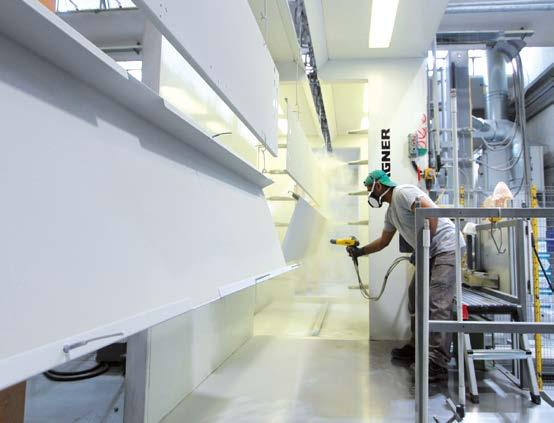
“With all this equipment available, however, it is essential to constantly monitor compliance with customer specifications to ensure the same levels of coating quality, film thickness uniformity, and result repeatability are achieved regardless of where the process is performed. For example, our main customer carries out regular audits of our plants and specific salt spray tests before allowing us to powder coat its low and medium-voltage circuit breakers and components for substations, servers, and switchboards.”
The Romanengo factory’s old powder coating system, however,


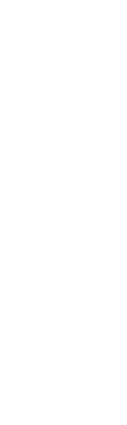
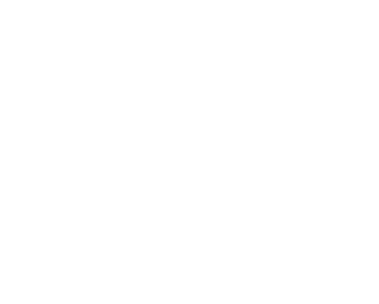
only performed three pre-treatment stages, which did not ensure the achievement of the quality standards imposed by the most demanding customers. This is why in 2022, ILTOM decided to invest in the new M.I. DUE plant.
The M.I. DUE automatic powder coating plant
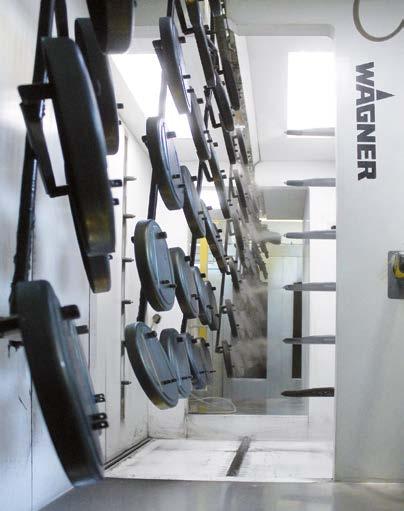
In August 2022, M.I. DUE designed, built, and installed a new powder coating plant, with a loading and unloading area where the operators can arrange the many components manufactured by the ILTOM Group, from small parts to large metalwork fabrications with a maximum size of 900 x 2,000 x 4,000 mm, on the load bars, each with a maximum capacity of 250 kg. The line’s one-rail conveyor takes them through the six-stage insulated spray pre-treatment tunnel, where they undergo alkaline degreasing, two rinses with mains water, one rinse with demineralised water, a conversion stage with the nanotechnology product Oxsilan®, and one final rinse with demineralised water. After exiting the pre-treatment tunnel, the parts move along a dripping area equipped with a platform that allows the water drained from the parts to be collected and reused. Subsequently, the load bars are taken to the drying oven and then to the powder coating booth, where an advanced, smart powder feed and preparation system enables colour changes to be carried out in just a few minutes. The booth is equipped with automatic guns, a pre-finishing station
with a Lesta self-learning articulated robot, and a manual post-finishing station. After curing in an oven with a double exchanger and a thermal oil battery, the workpieces are finally led to a special cooling zone, where unloading operations can also be carried out, and finally back to the loading/unloading area. This enables the staff to perform the unloading operations in two separate locations in order to optimise the logistics flows and the subsequent packaging activities. To this end, smart screens have been installed on the line that provide the personnel with the necessary information on how to package the products, any required checks, and the further processing steps.
Thermal oil-heated ovens for energy savings
“The powder coating plant went into full operation at the end of September 2022. We expressly asked M.I. DUE for a solution that could meet the quality requirements imposed by our customers but was also ecologically sustainable. Therefore, all motors are equipped with inverters and we use thermal oil to heat the ovens and the pre-treatment tunnel. This has reduced our energy consumption by 15%,” says Gianluca Cremonesi, the ILTOM Group’s paint shop manager. The line’s ovens are heated through thermal oil batteries to reduce gas consumption and avoid the use of burners, and therefore eliminate the presence of flames inside the building. The boiler, located outside the factory, heats
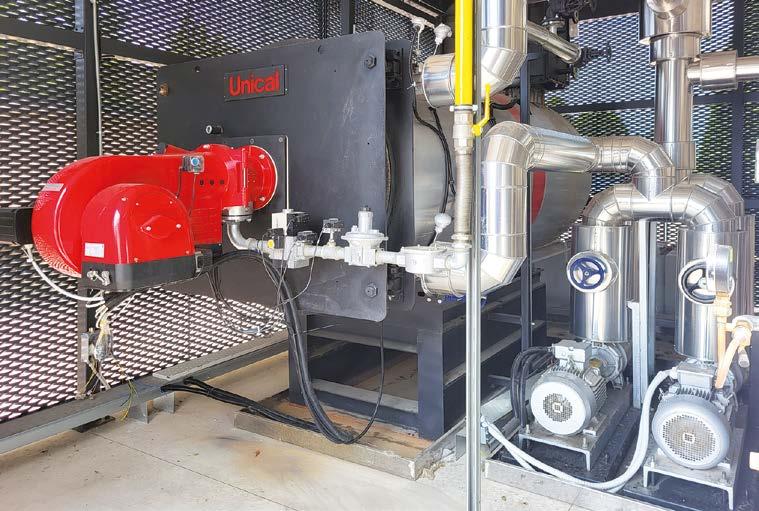
the recirculating oil and sends it to the batteries of the drying and curing ovens, where its temperature can be adjusted through temperature controllers and modulating valves. In addition, an oil-water exchanger heats the coils of the pre-treatment tunnel.








“The use of thermal oil enables to keep the temperature more stable and adjust it by as little as one degree, thus improving film distension and colour consistency during curing. This system was also designed with a view to heat recovery, so the boiler is equipped with a very efficient burner and a heat recovery unit that utilises the heat of fumes (300° C) to obtain hot water for raising the temperature in the alkaline degreasing tank. As a consequence, the company has increased both its energy savings and the safety of its working environment. Boiler maintenance is also facilitated and does not hinder production operations,” notes Andrea Mattavelli, the technical designer from M.I. DUE who was responsible for the development and construction of the new plant.
Flexibility and repeatability with self-learning robots



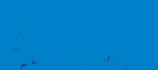


ILTOM uses a variety of powder coatings and performs an average of eight colour change operations per shift. The operational flexibility of the plant is therefore crucial. “The previous machine integrated a Lesta fiveaxis articulated robot with a self-learning function and an RFID management system, which we decided to maintain in this line as well for pre-finishing operations on components with complex shapes such as box profiles or parts with particular angles and curvatures,” says Cremonesi. “An operator performs the movements required to effectively coat a part using an ergonomic joystick and the robot saves the data so that it can replicate them independently. In addition, the entire plant is Industry 4.0-oriented. Through a tablet in the department and even with an app on the mobile phones available to staff, it is possible to set various operating parameters.”
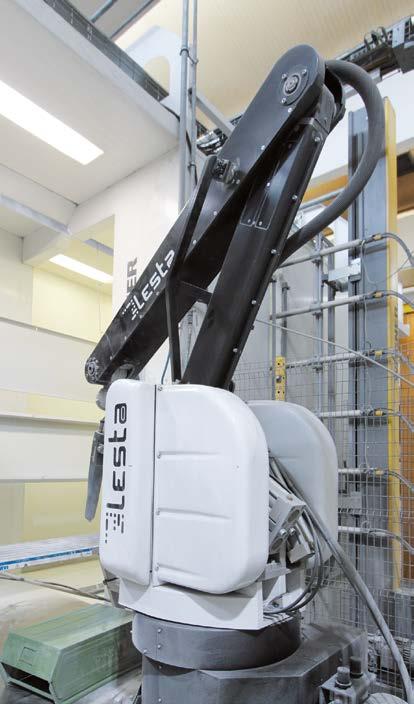

The ongoing collaboration with M.I. DUE
The strategic collaboration between the ILTOM Group and M.I. DUE was not, however, limited exclusively to the coating system installed at the Romanengo site. This plant engineering company, in fact, has repeatedly been responsible for updating and maintaining ILTOM’s other
plants. The Group also decided to rely on this partner for the construction of a coating line in one of its five production facilities in Romania. “M.I. DUE has always been professional, reliable, and helpful in finding the best solution to our needs. For example, when we moved to a new Romanian plant, they dismantled the existing coating system and immediately reassembled it at the second site: our production restarted without a hitch in less than one month. When our management decided to invest in a new plant for the Italian site, after a thorough benchmarking, MI.DUE’s offer proved to be the best in terms of technical characteristics, installation times, and assistance. The customisation level it is able to achieve and
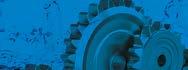
the expertise of its technicians have enabled us to continue to meet all the stringent specifications of our customers, whether for coating large components such as air conditioning, boiler, and refrigerator metalwork fabrications or for finishing small parts typical of the beverage distributor and electrical industries – all while reducing energy consumption and costs,” states Roberto Cagna.
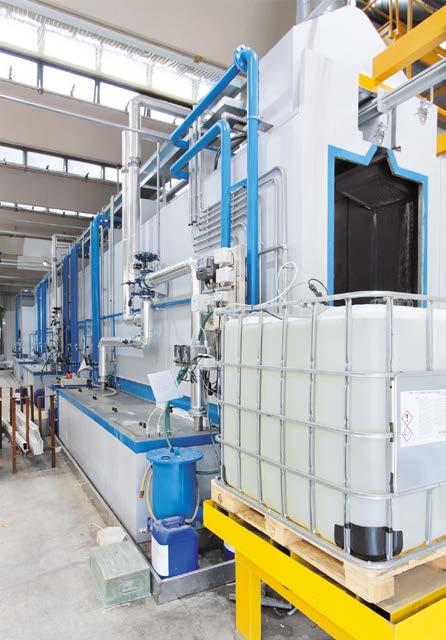
Cost-effective and green investment
In addition to achieving the quality degree required to meet the needs of the ILTOM Group’s diverse customer base, the new powder coating
plant supplied by M.I. DUE has a higher capacity than the old one, despite requiring lower energy consumption. “Equipping our site with a plant with much higher quality standards that could meet all our customers’ requirements was an absolute necessity, not least because of the risk of overloading due to work peaks or breakdowns. We are completely satisfied with this new chapter in our collaboration with M.I. DUE, as we have been able to increase our production capacity and quality standards while at the same time gaining economic benefits (thanks to reduced consumption) and improving our operations’ sustainability (thanks to flue gas heat recovery),” concludes Roberto Cagna.
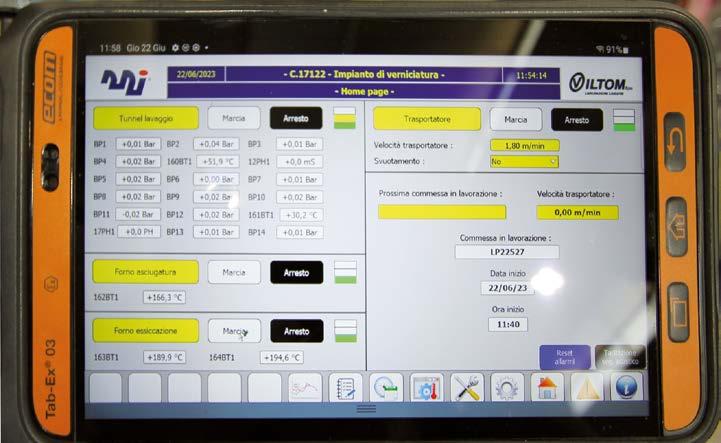
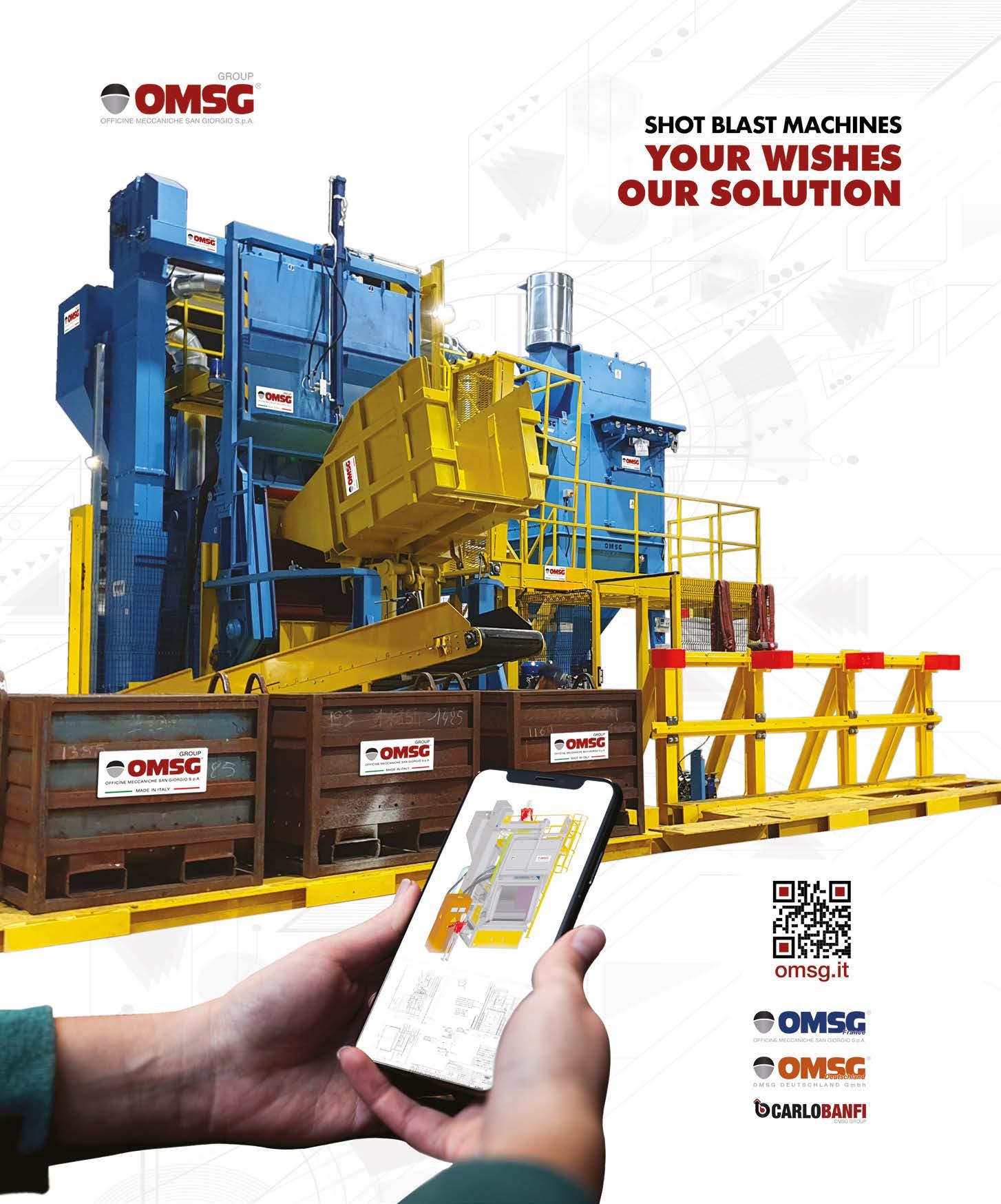
RESEARCH BREAKTHROUGH
The ‘Invisible’ Cellulose Coatings that Mitigate Surface Transmission of Pathogens
Edited by University of Birmingham Birmingham – United KingdomA thin film of cellulose fibre that is invisible to the naked eye, is suitable for use on high traffic objects such as door handles and handrails.
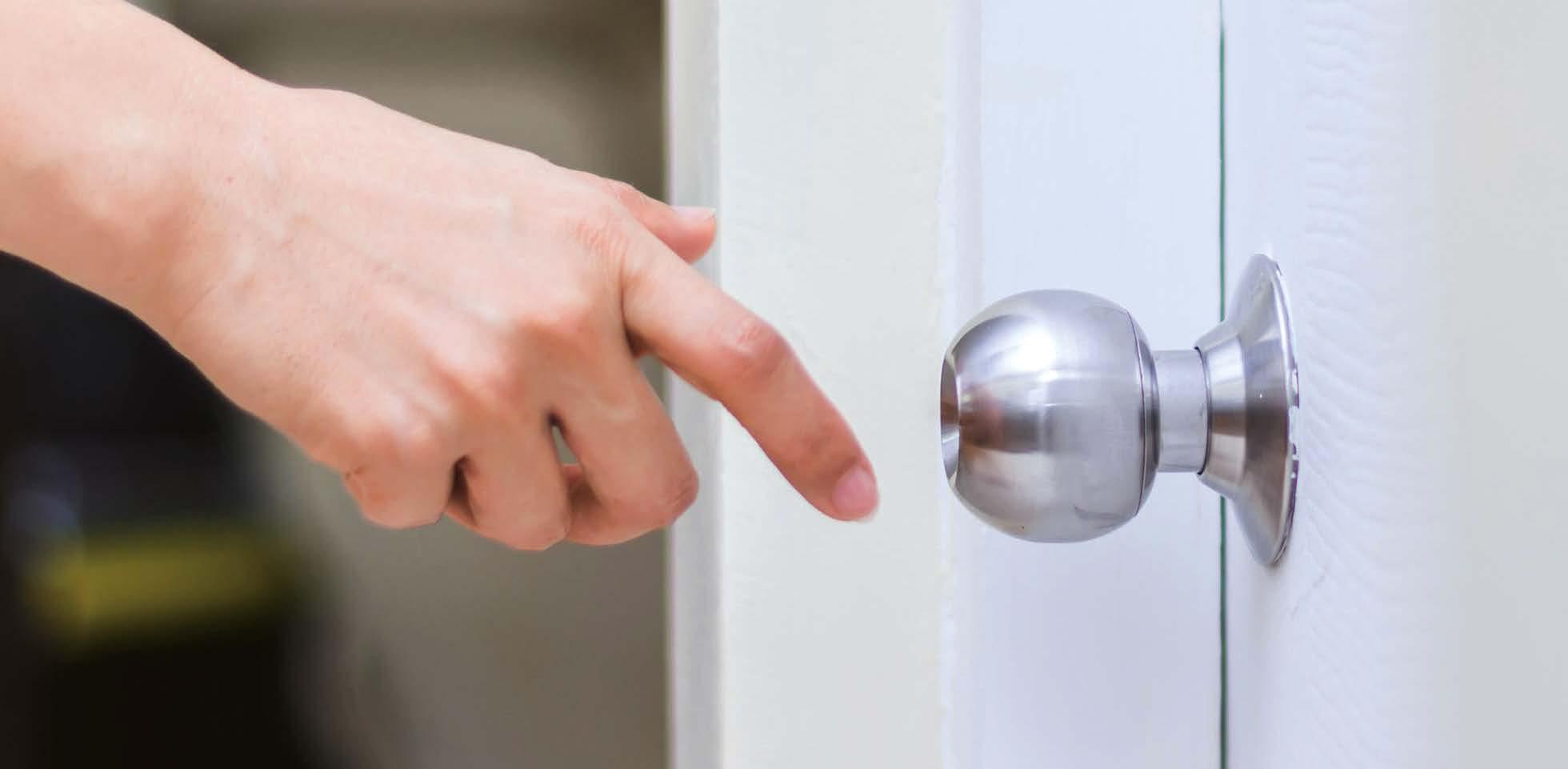
Research confirmed the stability of the coating, which showed no noticeable damage when dry, but easy removal from the surface when wetted, making it convenient and suitable for daily cleaning and disinfection practice. Research1 has shown that a thin cellulose film can inactivate the SARS-CoV-2 virus within minutes, inhibit the growth of bacteria including E.Coli, and mitigate contact transfer of pathogens. The coating consists of a thin film of cellulose fibre that is invisible to the naked eye, and is abrasion-resistant under dry conditions, making it suitable for use on high traffic objects such as door handles and handrails.
1 https://pubs.acs.org/doi/10.1021/acsami.2c23251
The coating was developed by scientific teams from the University of Birmingham, Cambridge University, and FiberLean Technologies, who worked on a project funded by the Engineering and Physical Science Research Council to formulate treatments2 for glass, metal or laminate surfaces that would deliver long-lasting protection against the COVID-19 virus.
While conventional chemical disinfectants and antiviral surface designs target either the structural proteins or nucleic acids, the researchers, led by Professor Zhenyu Jason Zhang, from Birmingham’s School of Chemical Engineering, focussed on drying out the respiratory droplets
2 https://www.birmingham.ac.uk/news-archive/2020/researchers-tackle-the-surfacetransmission-of-covid-19-in-new-partnership
that contain the viruses by the capillary force introduced by the porous structure. The COVID-19 virus is known to remain active for several days on surfaces such as plastic and stainless steel, but for only a few hours on newspaper. The team, which has expertise in surface chemistry and formulation engineering, investigated the structure and performance of a coating made from micro-fibrillated cellulose (MFC) provided by FiberLean Technologies, the leading global producer of MFC for the paper and packaging industry.
The researchers found that the porous nature of the film plays a significant role: it accelerates the evaporation rate of liquid droplets, and introduces an imbalanced osmotic pressure across bacteria membrane. They then tested whether the coating could inhibit surface transmission of SARS-CoV-2. Here they found a three-fold reduction of infectivity when droplets containing the virus were left on the coating for 5 minutes, and, after 10 minutes, the infectivity fell to zero. By contrast when droplets containing SARS-CoV-2 were left on a glass surface, their initial infectivity was still maintained after 10 minutes. The antimicrobial tests were repeated with droplets containing bacteria (E.Coli and S.epidermidis), and here again, the researchers saw substantial reductions in infectivity at 1 hour and 24 hours.
The experiments were repeated with aerosolized artificial saliva, and here the analysis suggested that the cellulose thin film is also effective in suppressing the contact transfer of respiratory aerosols.
Professor Zhang commented: “The risk of surface transmission, as opposed to aerosol transmission, comes from large droplets which remain infective if they land on hard surfaces, where they can be transferred by touch. This surface coating technology uses sustainable materials and could potentially be used in conjunction with other antimicrobial actives to deliver a long-lasting and slow-release antimicrobial effect.”
The researchers confirmed the stability of the coating by mechanical scraping tests, where the coating showed no noticeable damage when dry, but easy removal from the surface when wetted, making it convenient and suitable for daily cleaning and disinfection practice. University of Birmingham Enterprise has filed a joint patent application with FiberLean Technologies and Cambridge University covering a microfibrillated cellulose which can inactivate viruses by disrupting the lipid envelop of the virion.
WASTE WATER TREATMENT PLANTS

FOR METAL FINISHING LINES
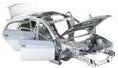



company in Zero Liquid Discharge for metal finishing industry

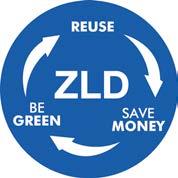
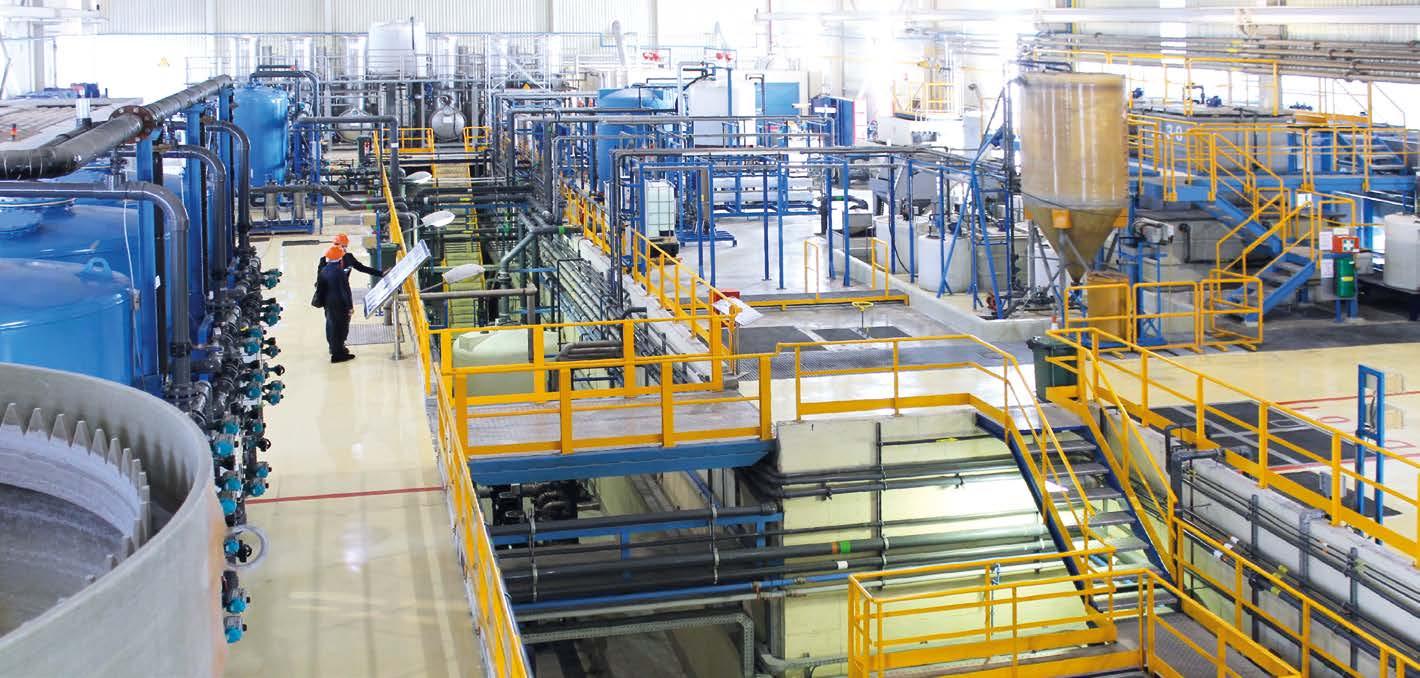
www.cieeng.com - info@cieeng.com
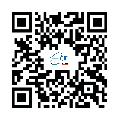

over 50 ZLD plants installed all over the world, CIE is a leader
EcoBell4: Application Efficiency of up to 98% Saves Huge Amounts of Paint and Rinsing Agent
With the new EcoBell4 atomizer family, Dürr is setting new benchmarks in sustainable production. The innovative application technology achieves efficiencies of up to 98 percent for clear coat. Paint losses and rinsing agent consumption can be reduced by 50 percent during colour changes, or even by up to 91 percent in combination with the EcoProBooth modular paint booth concept. The improvements are made possible by the unique 4-main needle technology as well as changes to the process parameters for paint application.
The higher the efficiency during paint application, the less material, resources, and energy are required. In other words, higher efficiency makes for more sustainable production. With the latest atomizer generation EcoBell4 Pro Hu with direct charging and EcoBell4 Pro Ux with external charging, Dürr is scaling new heights. For clear coat application, application efficiencies of 95 to 98 percent are achieved according to DIN EN 13966-1.
For the atomizer to apply the paint with maximum efficiency, the process parameters are set as follows: the speed and spray distance are significantly reduced. This maximizes the effect of the high voltage. The flow rate of the paint remains high. In addition, the shaping air is reduced to a minimum and the high-voltage control is adjusted. Dürr is testing the implementation of this painting process in a concrete automotive paint shop in a collaboration with interested OEMs. Existing systems can be retrofitted too.
How the measures impact the process
Reducing the shaping air volume to a rate of between 90 and 200 standard litres per minute produces a softer spray jet. Together with a lower bell disk speed, energy consumption is reduced. If the spray distance is decreased to around 100 millimetres at the same time, more paint reaches the car body. There are two reasons for this: firstly because the spray pattern is much less scattered, and secondly because a stronger electrical field between the bell disk and car body surface enables optimum use of the electrostatic force via a constant voltage.
The atomized paint therefore reaches the body to a far greater extent instead of being lost in the booth air. In order to achieve the required layer thicknesses in the given cycle time, a paint outflow rate of up to 400 millilitres per minute is possible. In total, the EcoBell4 Pro Hu with direct charging achieves efficiencies of up to 98 percent for clear coat in this way.
With the EcoBell4 Pro E atomizers with external charging for exterior painting, the efficiency for base coat also increases from 75 to 78 percent compared with the predecessor model EcoBell3. The EcoBell4 Pro Ci atomizer for interior painting also continues to achieve unrivalled high efficiencies of up to 70 percent. Efficient collaboration with OEMs and paint suppliers in the Dürr technical centre offers further potential for improving the efficiency and the quality of paint application.
Fast colour changes reduce paint and rinsing agent consumption
In addition to the painting process, technical innovations in the design elevate the EcoBell4 atomizer generation to a new quality level. The new generation makes the painting process more flexible and more efficient, and therefore more sustainable. Colour changes can be carried out more quickly with the EcoBell4 than with any other highspeed rotary atomizer on the market. This is because the patented 4-main needle technology not only saves time, but also reduces paint and rinsing agent consumption as well as VOC emissions. Here’s how the principle works: three of the four main needles are reserved exclusively for the most frequently used colours. All other colours go through the fourth main needle. Real-world evidence shows that in the automotive sector, 50 percent and more of the total number of bodies are painted in the three most frequently used colours. The technology leverages this fact and provides the three colours permanently via the main needles. These are located directly behind the bell disk. When a colour change is due, the system can switch to another main needle within four seconds without it being necessary to rinse and clean the channel. This reduces both the paint losses and the rinsing agent consumption associated with colour changes. If a less frequently used colour is requested, the colour can already be primed via the fourth channel while one of the three main colours are still being applied. This means that each colour is available for the next body within an extremely short time.
ROAD TO 2050
Further savings through the new paint booth concept
Compared with the predecessor model EcoBell3 (1C), the consumption of paint and rinsing agent is reduced by 51 percent in the conventional line setup. This is good for the environment and minimizes the process costs. The new atomizer generation is especially efficient and sustainable in combination with the EcoProBooth. Since the interior and exterior painting can be performed in a single booth, not only the colour change times but also the handling times are reduced compared with the line concept.
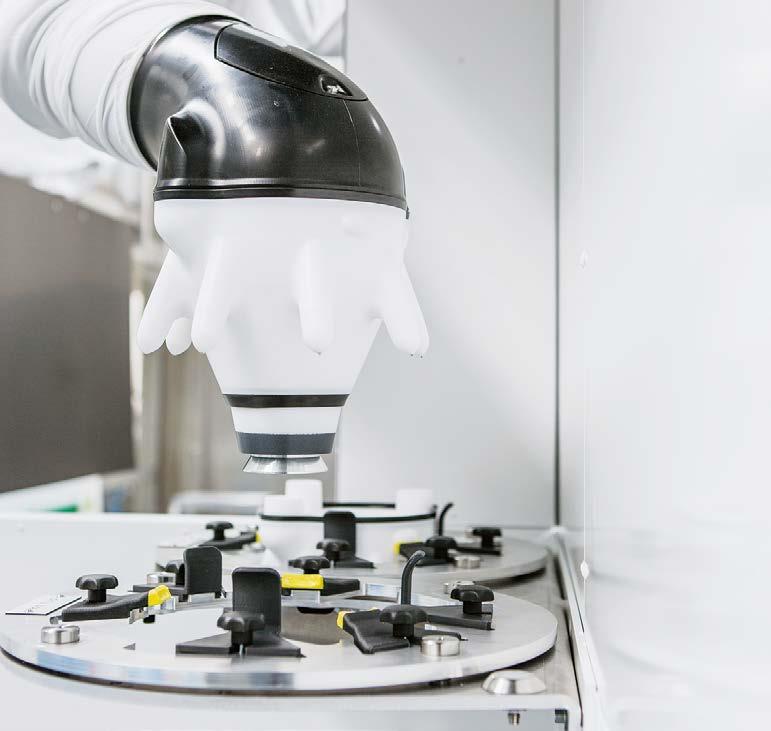
The universal atomizer EcoBell4 Pro Ux is a perfect match for the EcoProBooth. It is suitable for interior, exterior, and metallic painting, and uses one and the same bell disk/ shaping air ring system and external charging system for this.
The combination of the EcoBell4 Pro Ux and EcoProBooth even permits savings of up to 91 percent during colour changes by reducing paint losses and rinsing agent consumption. “This is a huge step. Our model calculations are based on a paint shop that uses 24 colours and coats 30 bodies an hour, working 230 days a year on a three-shift basis. The amount of paint saved would be enough to paint an additional 15,600 bodies,” says Frank Herre, Head of Application Technology Development at Dürr.
Just four robots reduce colour change and handling times
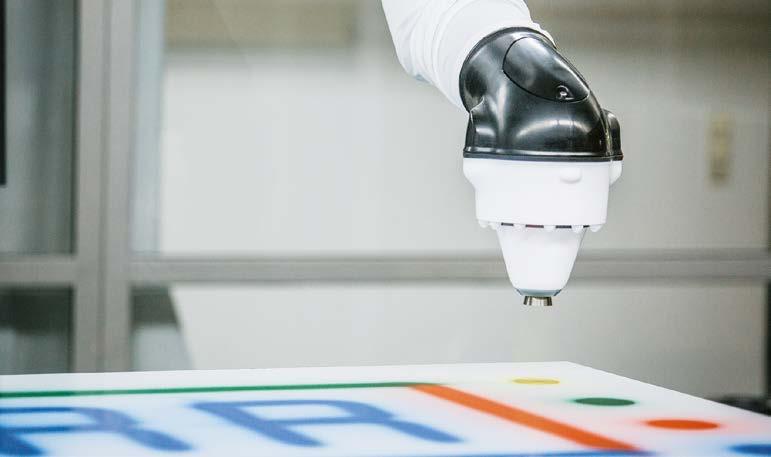
The system with up to four main needles covers all painting requirements, from the 4x1C solution for base coats to the 3x2C solution for clear coats. Dürr offers a total of ten different versions of the EcoBell4, for all exterior and interior painting applications with direct or external charging.
For the first time, the product family includes a basic version for standard applications as well as a pro version for special processes such as 4x1C or 3x2C.
Making the Best Use of Customers’ Time by Adding Value through State-of-the-Art Services: A Coating Contractor’s Bet on the Future
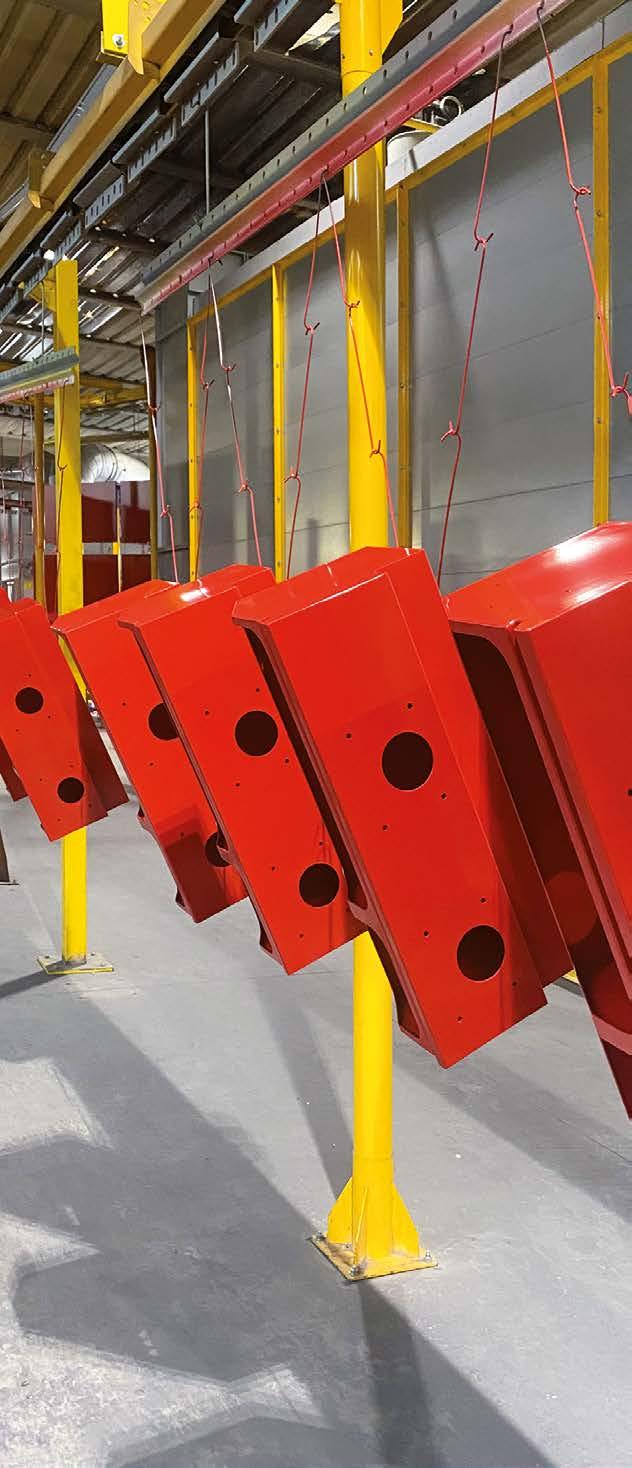
An innovative concept of contract coating, based on offering a service that does not end with the delivery of high-quality finishes but also includes the management of the time allocated by customers through state-ofthe-art systems. This is what stood out during our visit to the premises of Tecnologie Galvaniche Innocenti, a coating contractor that has recently integrated the latest generation of Gema Europe devices to project its production flow into the 4.0 future.
The term “contracting” generally refers to the services of a firm that performs certain processing steps or entire manufacturing processes on behalf of one or more other businesses. Typically, a company turns to a “third-party” firm and entrusts it with the processing of some of its products to optimise costs, to cope with production peaks that are difficult to handle in-house, or to rely on a partner with better or different technologies and skills than its own: this is the most frequent case in the contract coating sector. Customers turn to contractors intending to establish solid and reliable partnerships. This means that, in addition to taking advantage of their expertise, they also expect their orders to be managed within the required time frames.
“Recently, especially after the pandemic, the delivery time for coating components has dramatically reduced from five to two working days,” emphasises Leonardo Innocenti, the owner of Tecnologie Galvaniche Innocenti Srl (Anagni, Frosinone, Italy), which specialises in the contract shot blasting and liquid and powder coating of small, medium, and large metal parts for the most diverse sectors, from automotive to aerospace, from architecture to HVAC and the general industry.
“To adapt our factory to these new market requirements, we decided to equip it with the latest 4.0 technologies, taking advantage of the Italian government incentives for SMEs and turning to our long-standing suppliers of equipment and plant solutions, such as Gema Europe Srl (Trezzano sul Naviglio, Milan, Italy) and Euroimpianti (Valeggio sul Mincio, Verona, Italy).”
“I firmly believe in looking at contracting services from a different perspective,” adds Innocenti. “Contractors do not produce anything, but we rather manage the time that customers give us to carry out their required surface treatments. Reflecting on our work with a view to not only improving finishing quality but also optimising our customers’ production times is certainly more difficult. However, if we manage to do this and therefore enhance our service with the right plant solutions, we are on the right track to succeed.”
Tecnologie Galvaniche Innocenti: from the post-war period to the family’s fourth, all-female generation
The growth of Tecnologie Galvaniche Innocenti has gone hand in hand with the development of the contract coating sector from the post-war period to the present day, with one distinctive trait: Leonardo Innocenti, from the third generation of the family at the helm of the company, is now supported by his three daughters Cristiana, Giorgia, and Fabiana, who work in the administrative, production and planning, and sales departments, respectively. “The history of our company began with a small blacksmithing and painting workshop created by my greatgrandfather on the Tiber River right after World War II,” says Cristiana. “The business was then taken over by my grandfather. Towards the end
of the 1960s and the beginning of the 1970s, he decided to move its headquarters to the southeast of Rome, continuing to offer contracting services but specialising in galvanic treatments. The plant in which we are headquartered now in nearby Anagni was opened in 1995 to offer powder coating in addition to galvanic treatments, which we still carry out in our Rome plant. Here, in 2012, we also installed a plant for liquid coating and one for stainless steel pickling and passivation, which we perform at the request of an individual customer from the oil & gas sector.
“Currently, powder coating on any type of ferrous material accounts for 98% of our production. We apply liquid paints rarely, generally on components for special industries, such as boiler parts, which must withstand the highest temperatures. For all other sectors, our staff always suggests the use of powders, both because of the progress that this type of coatings has made over time, moving from a purely industrial product to a wide range of applications even in unexpected sectors – such as architecture and design, which are now increasingly demanding – and because of the smaller environmental impact of their application process.”
Revamping the automatic powder coating plant
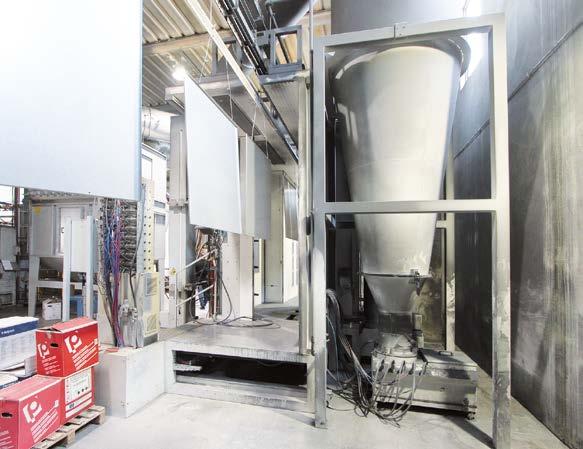
“We are equipped with three coating systems,” explains Cristiana, “including one liquid coating and two powder coating plants. Out of the latter, the manual one is devoted to large, heavy metalwork fabrications with a dimension up to 14 x 2.2 x 3 m and a weight up to 5000 kg handled through trolleys, whereas the automatic one treats small and medium-sized parts operating with a continuous flow on three shifts.

Euroimpianti designed and installed both lines. More recently, thanks to the Industry 4.0-related incentives, it also supported us in the revamping of the automated system, which started before the pandemic and was completed in 2022.”

The project entailed modifying the line’s design, switching from a ring layout that required two-coat systems to be applied in two passes to an “L-shaped” layout that ensures a faster, more linear cycle. This includes a booth exclusively applying primers equipped with already-existing Gema reciprocators, a hot-air oven for primer gelling and top coat curing, and a new Gema top coat application booth. “Our automatic plant is equipped with three booths in total: one for primer application, one for top coat application, and one that was previously used for applying top coats in any colours but is now devoted to performing manual touch-
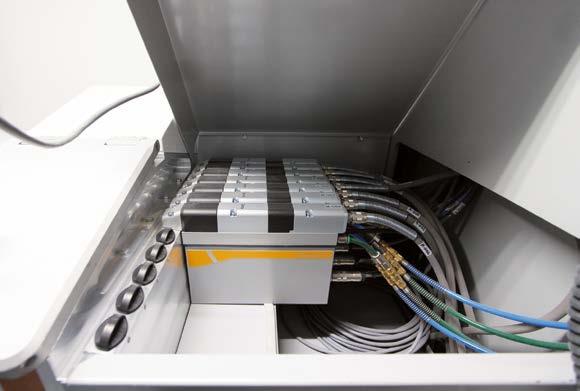

ups, to treat small batches, and to apply the most challenging colours in terms of colour change. In the past, our cycle time for two-coat systems was of up to 6 hours; today, the new layout and the addition of one booth enable us to perform the complete cycle in 4.5 hours.”
Gema’s last-generation booth
“Tecnologie Galvaniche Innocenti chose to install a MagicCylinder booth equipped with 10 automatic guns (5 on each side) and 4 manual guns, and OptiSpray AP 01 dense phase pumps, a 3D laser scanner system for shape recognition, and a powder management unit,” indicates Claudio Sergenti, area manager at Gema Europe. “The booth’s cylindrical design reduces powder accumulation, thanks to the absence of edges and corners where the paint product could accumulate. This guarantees
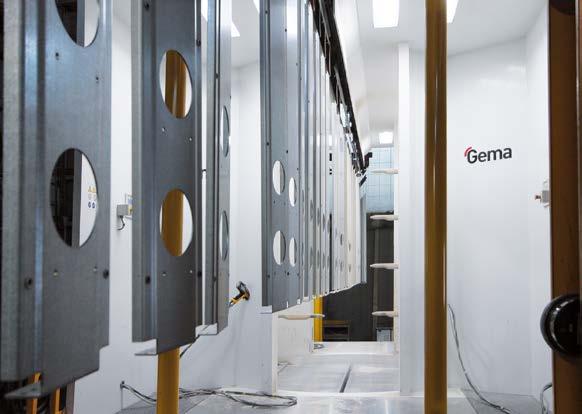
short cleaning times without the need for the operator to enter the machine. One of the special features of this line is the presence of two cyclones, which ensures optimum handling of light and dark colours through faster colour change operations and higher powder quality through the elimination of any contamination risk. In addition, the EquiFlow suction system creates the ideal work environment in every section of the coating booth: a consistent, homogeneous air flow in its central area guarantees the ideal conditions for paint application and prevents the powder from escaping from the plant.” “This company’s management decided to install the best devices available to optimise its line as much as possible,” concludes Sergenti. “The whole plant is interconnected with the central management system in line with the Industry 4.0 parameters. This allows managing paint programmes optimally and receiving reports about the daily consumption of paint and energy.”
“We have invested in the most advanced equipment on the market,” confirms Leonardo, “to guarantee that high finishing quality degree that was previously considered a minimum requirement only by certain types of customers, generally medium-large companies in particular sectors such as automotive and aerospace, but that today is included in every specification, often in association with increasing requests for special finishes ranging from textured to weathering steel and gold-effect ones, just to name the most recent trends. Alongside increasingly higher coating resistance, high aesthetics requirements can no longer be disregarded.”
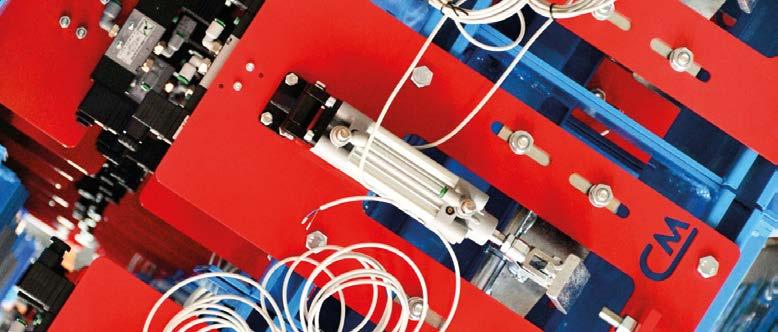
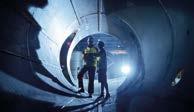
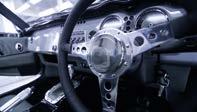
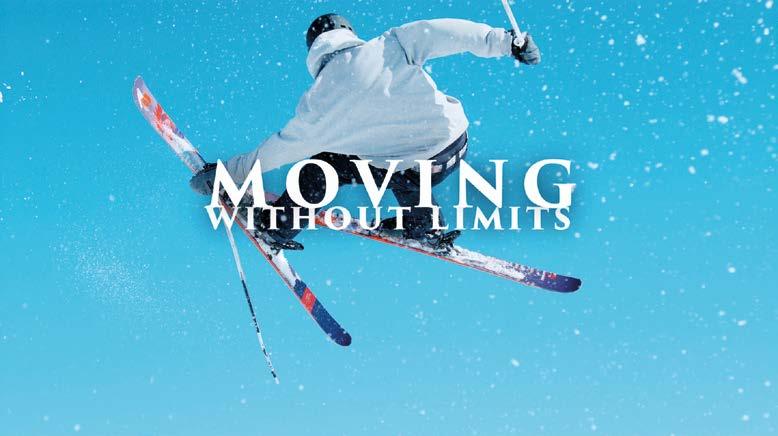
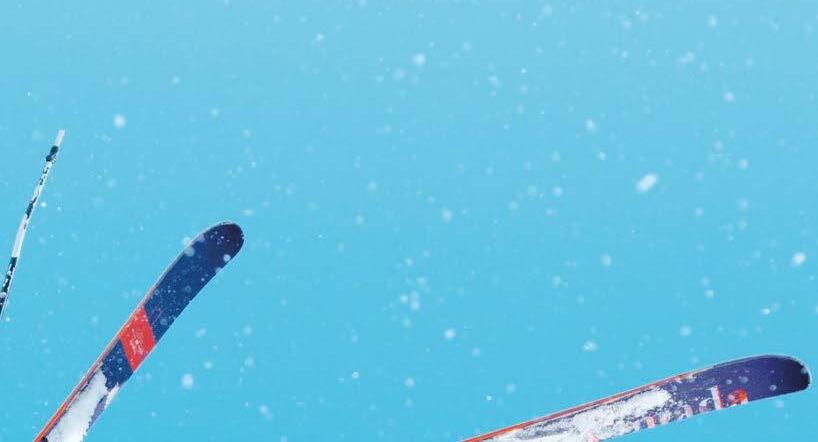
Advantages of the new booth
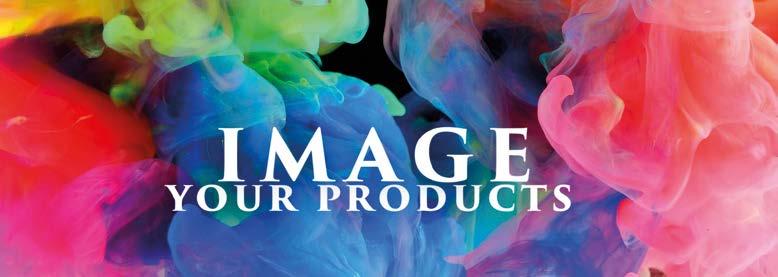
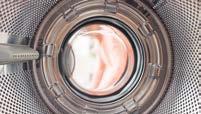
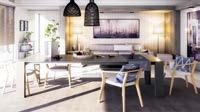
“Among the advantages we have obtained with the integration of the new booth and the new layout of our automated system,” says Cristiana, “we have improved the repeatability of our operations. Thanks to the pre-set programmes, we now have a reference standard and therefore a more efficient production flow. Automation has made the management of our coating phases easier because the booth does not have to be manned by an operator, who can thus be assigned to other tasks, such as the more complex ones required by the manual system. The operator is only active in the touch-up booth. This has halved the workforce employed on our automatic line from 4 to 2 operators. In addition, it has minimised the environmental impact of our processes, reduced product consumption thanks to the possibility of recovering 25% of the paint product, and zeroed waste disposal. Finally, the dense phase technology provides us with excellent coating consistency during application, which further enhances the aesthetic quality of the products we treat and fully meets our customers’ needs.”
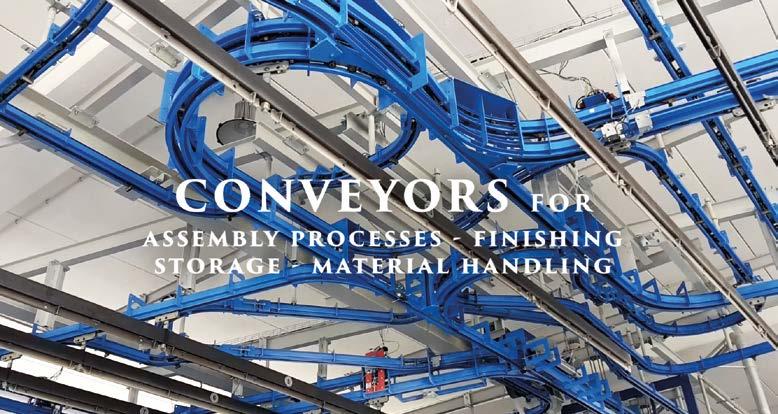
An innovative vision to overcome future challenges
“After the pandemic period, our company experienced a production peak related to the boom in the construction sector, which prompted us to take some significant decisions,” notes Leonardo.
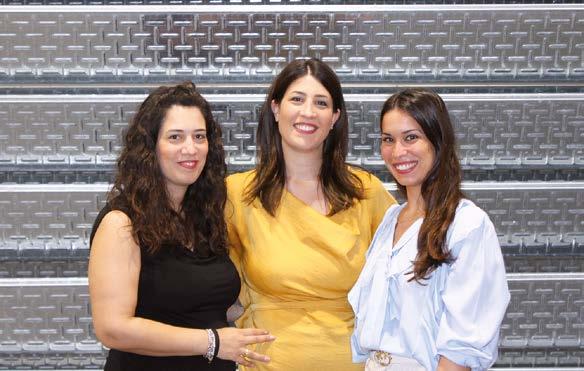
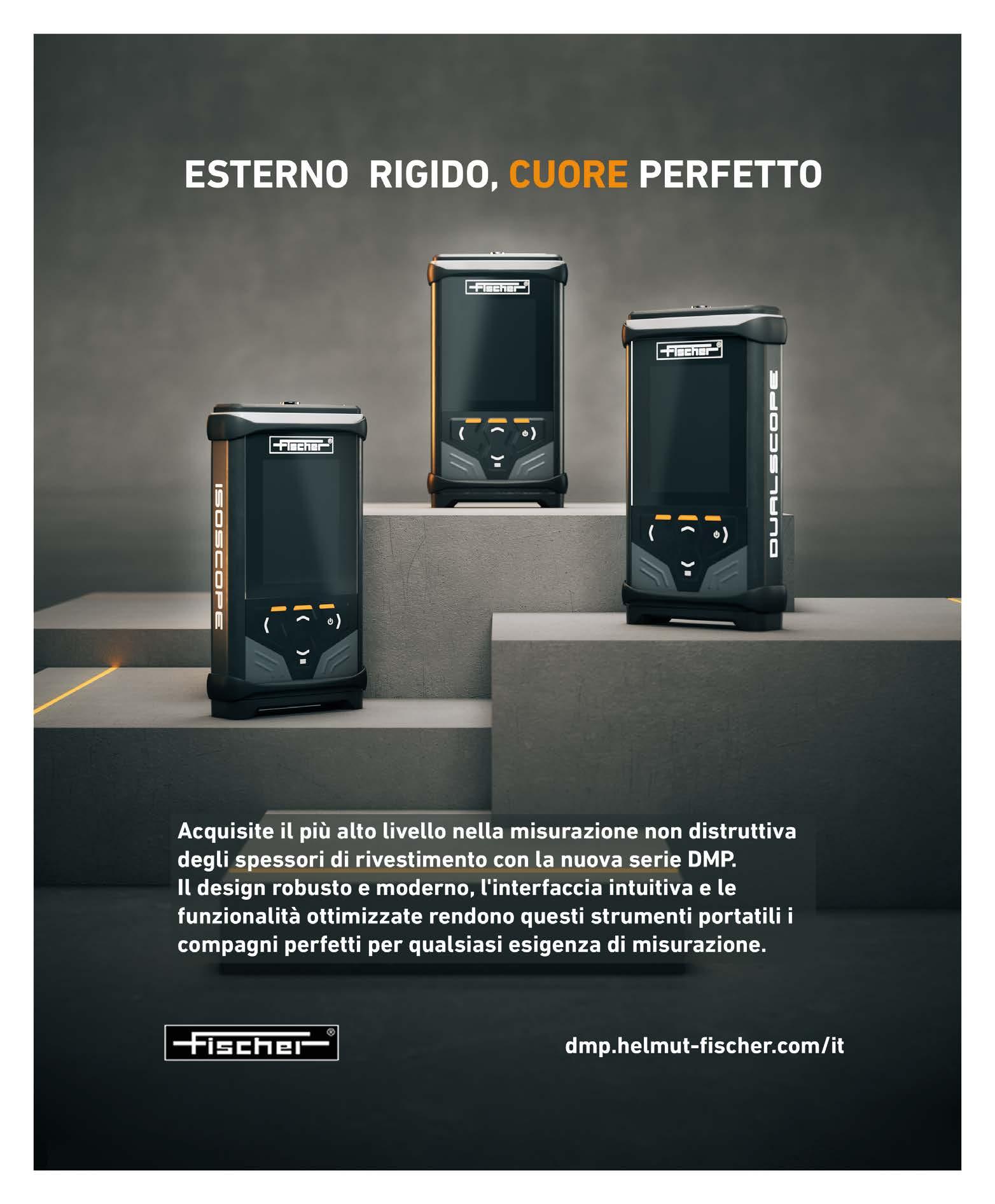
“In a very short space of time, we have tripled our staff and invested in the best technologies on the market, such as the equipment supplied by Gema, one of our long-standing suppliers and a company with longestablished expertise. Our MagicCylinder booth is one of its best and most innovative solutions, combined with 3D scanning, suction, and dense phase technologies. To create a facility that is fully managed in compliance with the Industry 4.0 parameters, another project we are going to implement within the next year is the integration of pre- and post-finishing robots.
“Finally, apart from investment in technology, the other project into which I am putting most of my energy is the continued growth and training of the new generation of people that are currently joining our company. These include my daughters, who will inherit the business founded by my grandfather, but also many newly-hired professionals, including a salesperson, who has a strategic role in communicating what we do and how we work to potential customers. The message I want to convey is that we need to know how to best manage the time that our clients give us to lay the foundations of future success. The required delivery times are getting shorter and shorter, and we must be able to cope with the continuous changes in the market not only through the most innovative technologies but also with the right attitude. This makes us reliable partners for our customers, rather than mere contractors.”
From top to bottom:
One of the special features of the plant is the presence of two cyclones, which allows the separate handling of light and dark colours.
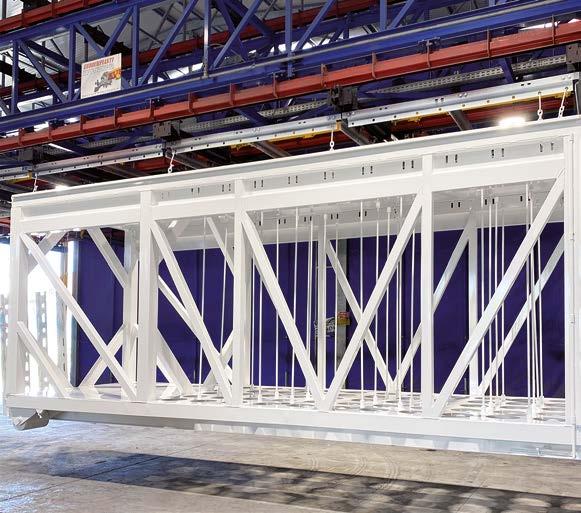
A large-sized component coated in the manual system.
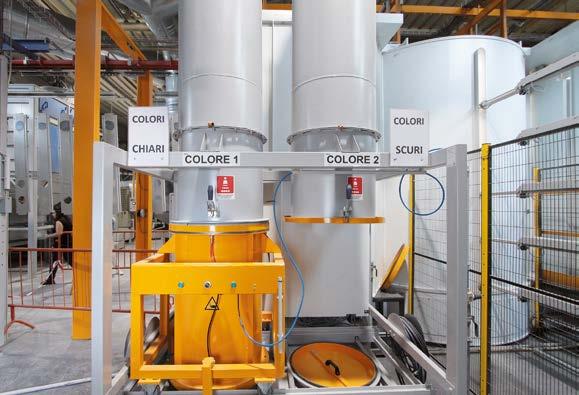
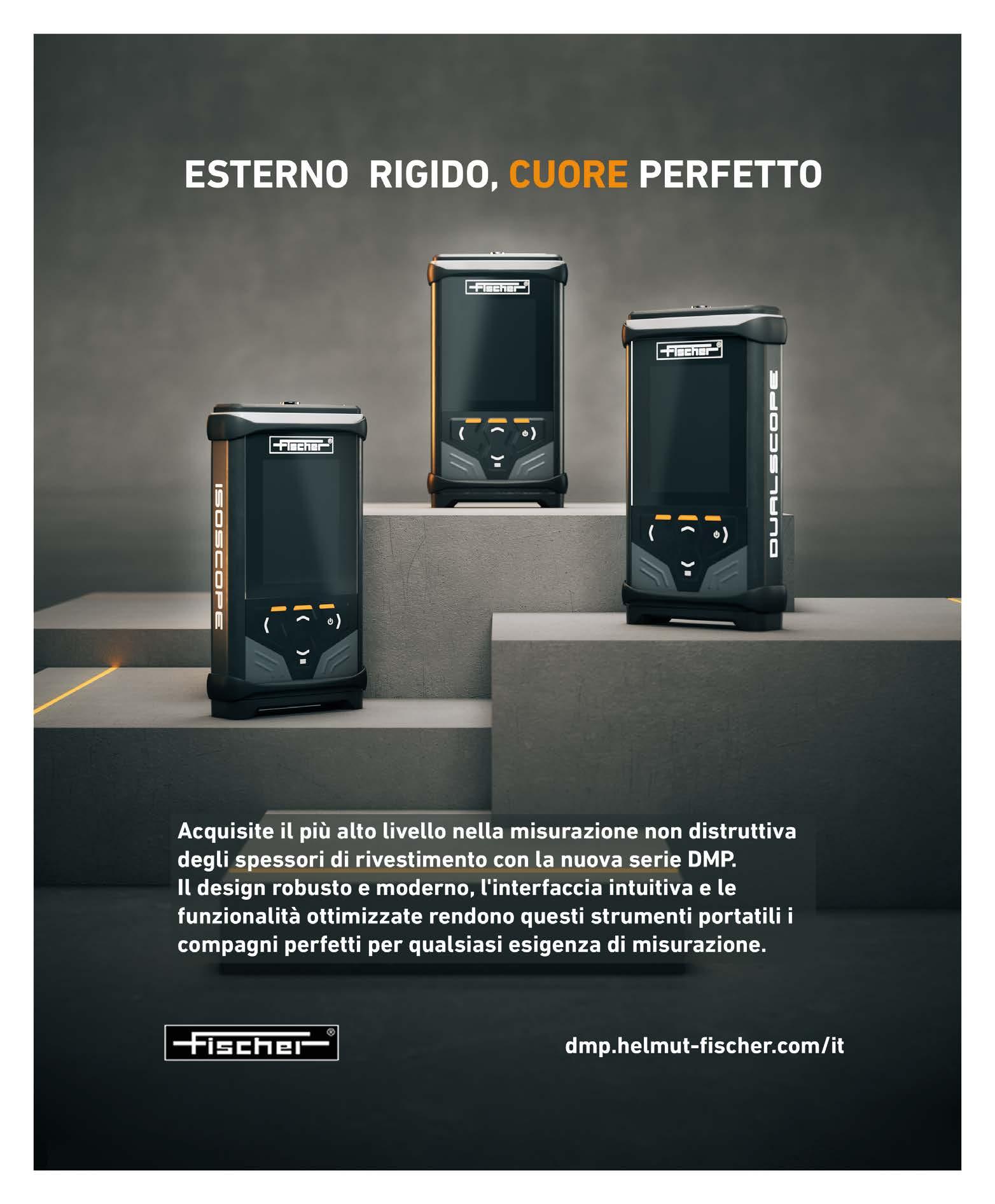
Lechler Tech: Industrial Coatings for Every Opportunity
Edited by Lechler Spa Como - Italy info@lechler.euThe treated substrate makes no difference, the paint applied on it does.
It is already well known that paint makes all the difference by enhancing the characteristics of a coated substrate, as well as improving its aesthetics and making it “eye-catching” through a variety of finishes. However, the design necessity to faithfully reproduce an exact colour point or effect regardless of the type of surface to be treated is often not easy to fulfil. In this article, we will tackle this issue with Lechler, which has made the replicability of colours and finishes on any substrate, be it plastic or metal, a goal and a significant strength. The refraction of light modifies the visual perception of tints on products made in different materials and with different shapes: in the design
phase, this should always be thoroughly addressed and assessed. To do this, Lechler offers endless technical and colour solutions with dedicated water and solvent-based systems for all sectors, including the general industry, appliances and consumer electronics (ACE), habitat, and original equipment manufacturer (OEM) fields. The wealth of solutions provided by Lechler Tech embraces any surface and application in the design world, enabling to work with any substrate and offering refined finishes capable of protecting and enhancing the parts over time. Out of the many colour solutions that Lechler makes available to its customers, Architectural X is the most innovative tool for the design industry.
Out of the many colour solutions that Lechler makes available to its customers, Architectural X is the most innovative tool for the design industry.
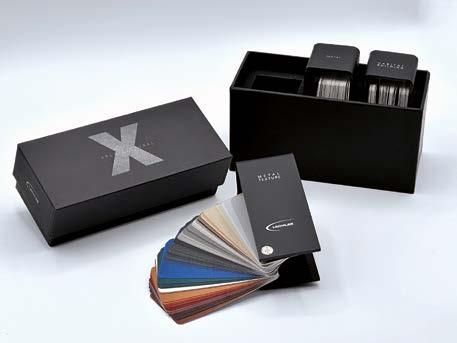
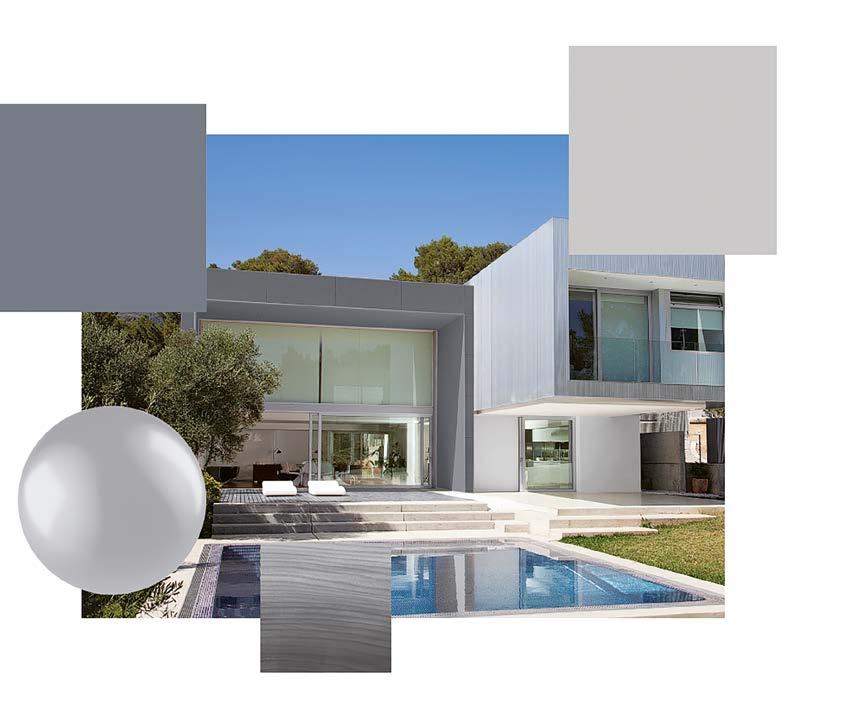
THE EASIEST WAY TO AUTOMATE YOUR PAINTING LINE
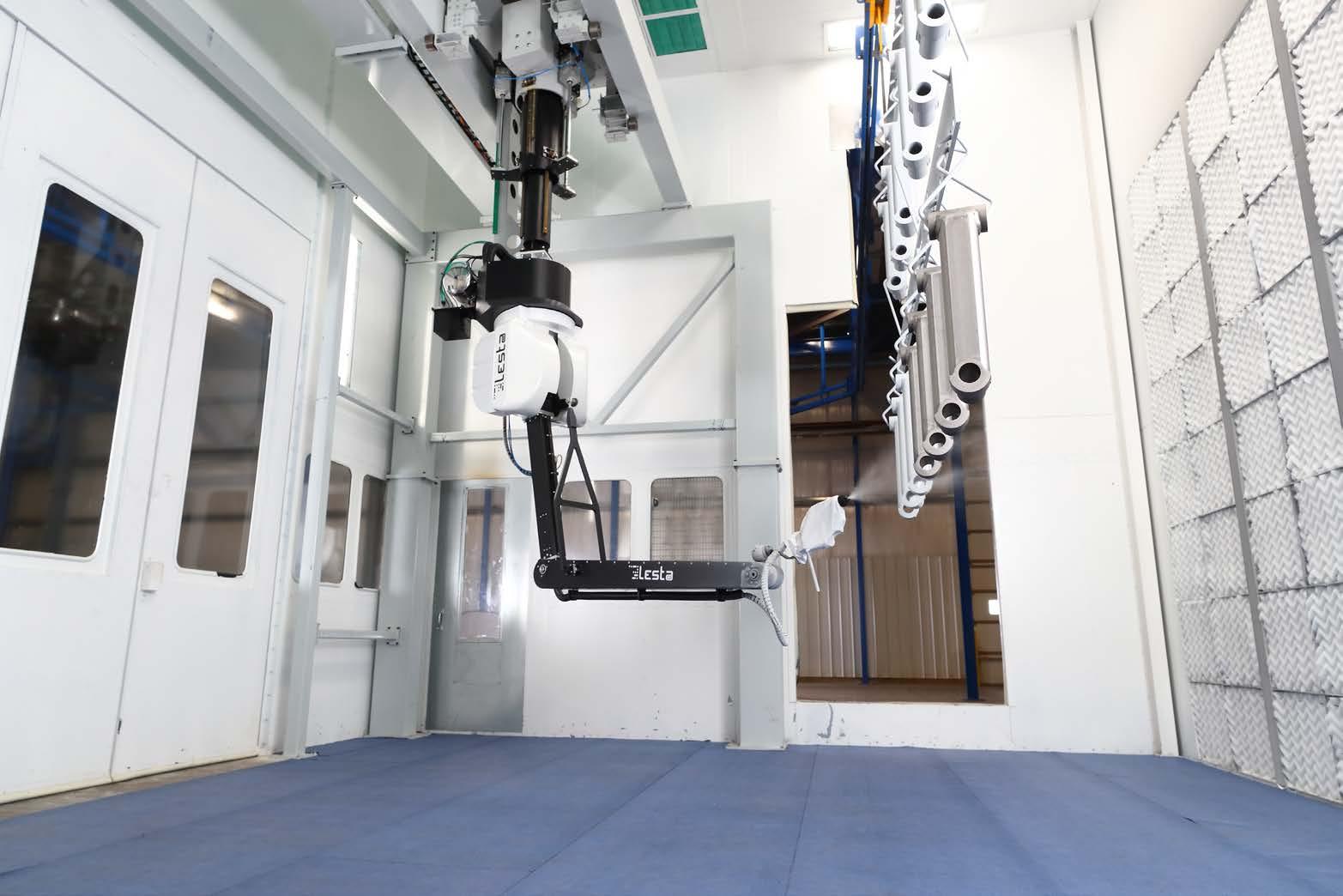
SELF-LEARNING ROBOT
1 OPERATOR REQUIRED
EUROPEAN ASSISTANCE
THE SCANNER RECOGNISES THE PARTS, THE ROBOT THEN PAINTS AUTOMATICALLY
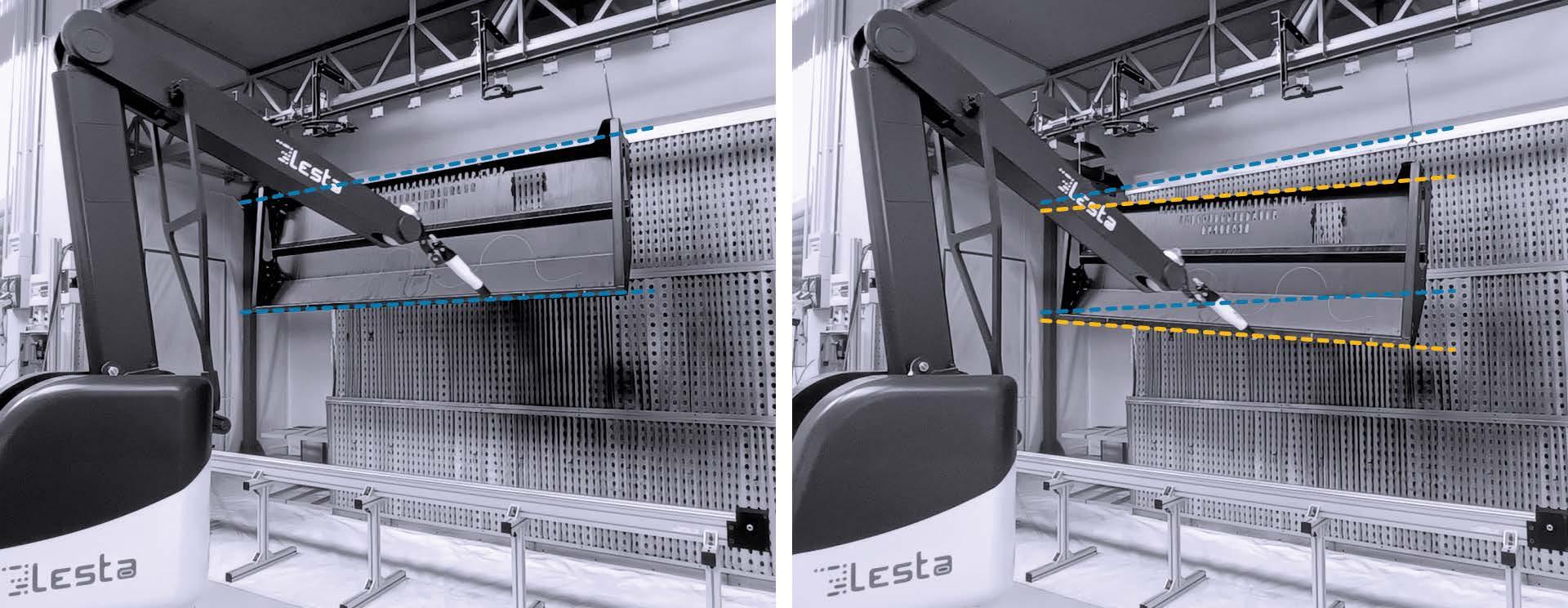
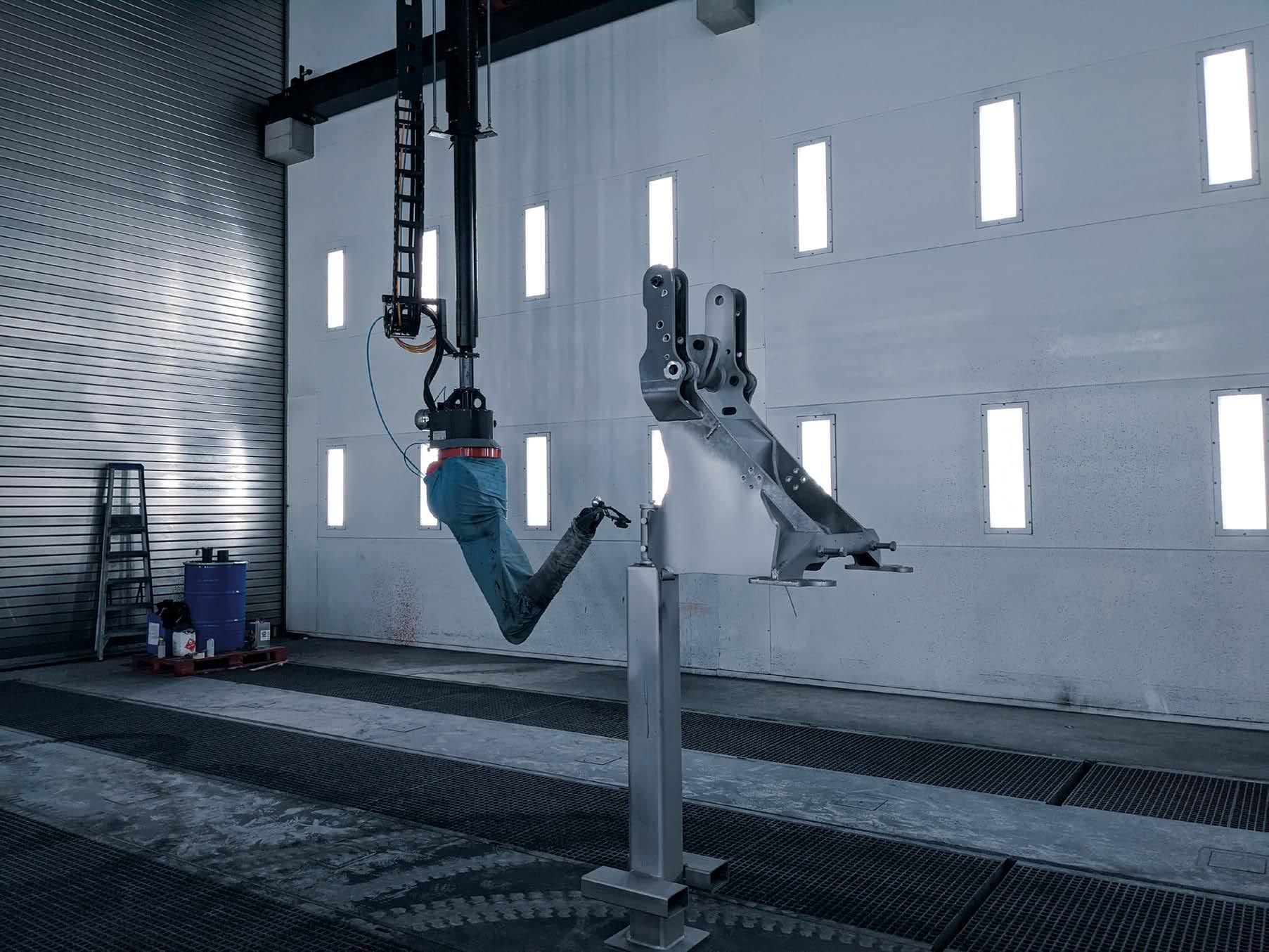
It consists of 3 special-effect palettes that complete its range of highly aesthetic effects and finishes, complying with low VOC emission requirements and including a univocal colour proposal with both water and solventbased products. The METAL, METAL TEXTURE, and HABITAT BUILDING palettes that make up this collection contain a complete range of finishes for the habitat sector, with a wide choice of metallic colours in glossy, matte, and textured versions. Their tactile effect allows experiencing these finishes with the sense of touch as well and makes it possible to meet any project requirement in architecture and design.
In particular, METAL TEXTURE includes products capable of creating fine surface structures through textured, fullbodied finishes, reducing the “cold” sensation of metal substrates and embellishing plastics with an elegant metallised effect. This also creates more rub-resistant, matte surfaces that mask any defects in the substrates. Ideal for both the contract and furniture worlds, the tints presented are in line with the demands of architecture, but also of the interior and product design sectors. The 29943 and YD943 binders were chosen to guarantee finish consistency with both solvent and water-based coatings. The latter version also complies with the international VOC emission requirements for the LEED, WELL, and BREEAM certifications.
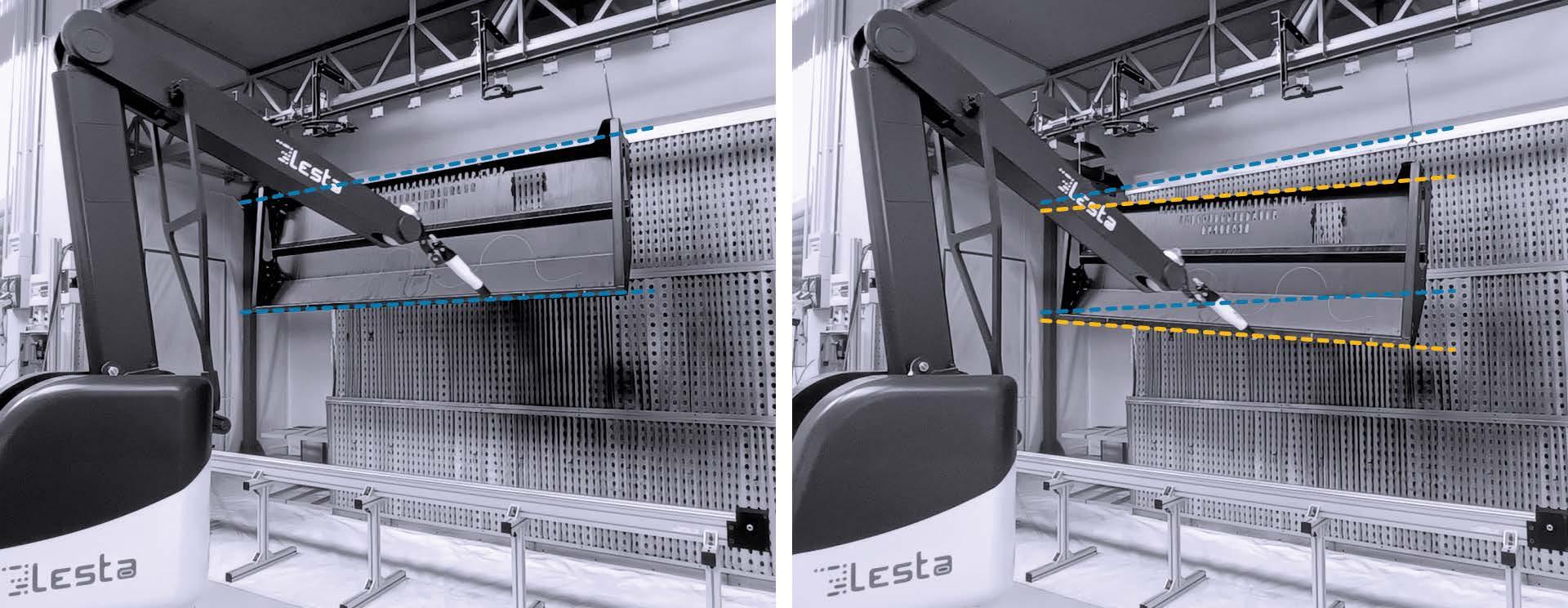
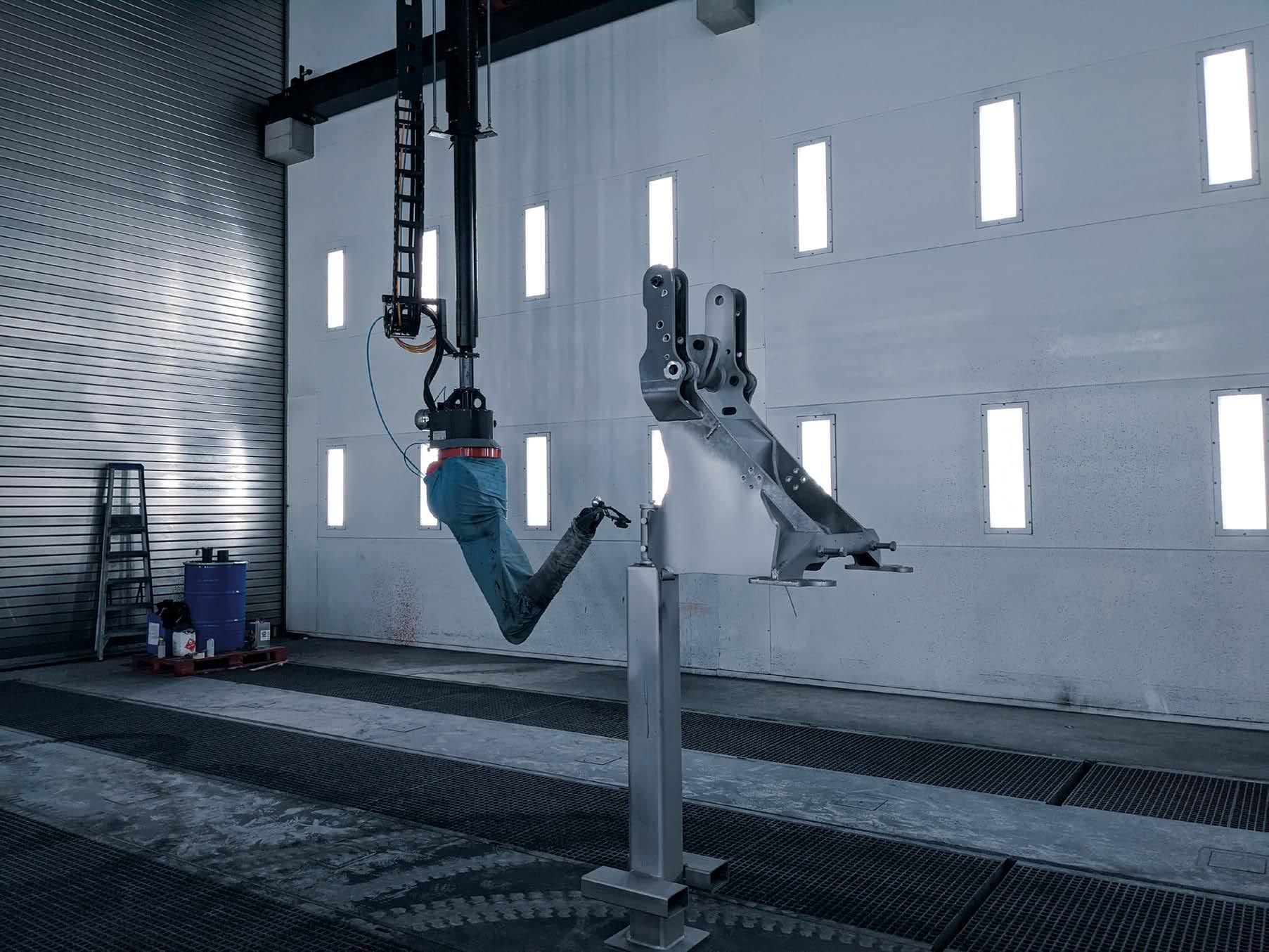
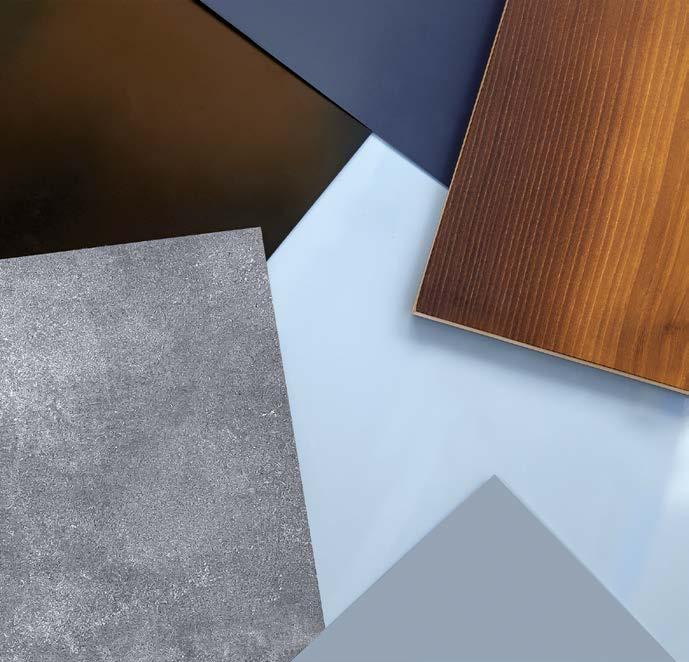
The HABITAT BUILDING palette, on the other hand, includes colours and finishes evocative of the classic materials used in architecture to improve the aesthetics of plastic components (such as PVC window and door frames) of façades, making them interact harmonically with their surrounding elements. Lechler’s solutions for coating PVC profiles are QB Profilés PVC revêtus1 certified and they include water-based systems for direct adhesion on PVC (Hydroframe Coat PVC Flex LH282) and solvent-based systems for direct adhesion on both plastic and metal (Framecoat PVC LS 282 and LS472, Plasticgrip 2K WS LS943).
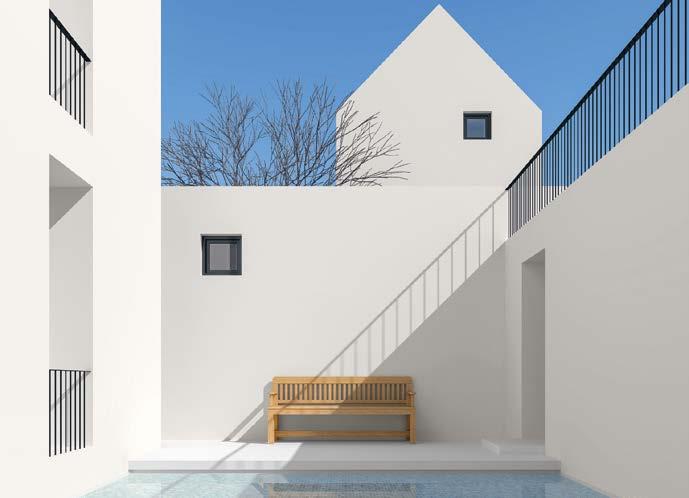
The Colour of Wind: When Wind Power Becomes an Aesthetic Icon
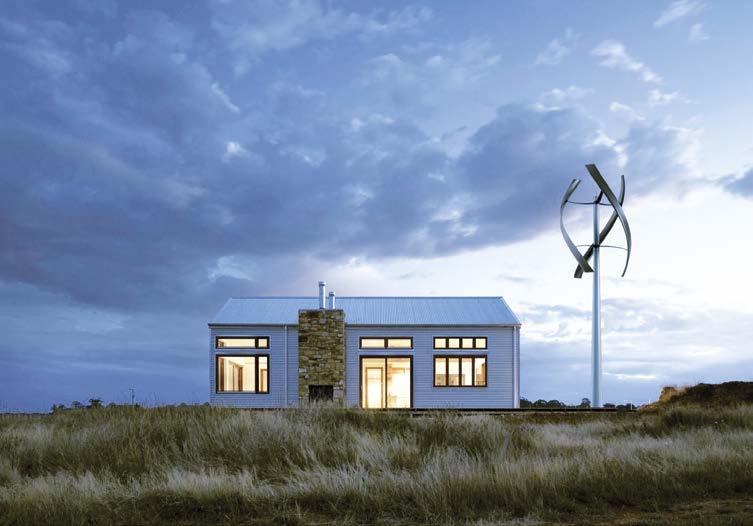
From green technologies criticised as being unaesthetic to street furniture elements to be installed in plain sight: a new culture of sustainability was born thanks to Enessere’s wind turbines for domestic use, characterised by sinuous, elegant lines and striking material colours.
Wind energy is among the most widespread renewable technologies. According to data reported by the International Energy Agency (IEA), wind-generated electricity increased by 265 TWh (+14%) in 2022 and wind power has been confirmed as the leading non-hydro renewable energy with over 2100 TWh produced, more than all other technologies combined1. However, as well as other energy generation devices such as for example solar panels, wind turbines are often at the centre of discussions because they are considered unsightly within the landscapes in which they are placed. Enessere (Vicenza, Italy) decided to revolutionise this perception by conceiving a new product with an innovative design and eye-catching colours, an object to be shown rather than hidden: a vertical microwind turbine to produce clean domestic energy by exploiting wind from
1 https://www.iea.org/energy-system/renewables/wind
any direction. We interviewed its founder, Alberto Tessaro, to find out how wind turbines have moved from being criticised as disfiguring for the environment to being seen as an aesthetic icon, almost a street furniture element.

How did the idea of enhancing the aesthetic value of wind turbines, an electricity-generating device, come about?
“Enessere is a young company founded on the know-how acquired by its team in the automotive electronics sector. From the very beginning, we had an innovative project in mind, one that was unprecedented in the field of energy: combining advanced technology for the production of domestic electricity with attractive design to create a device that guaranteed extremely high functional performance while being able to be shown in plain sight and not hidden away. Ten years after its foundation, we can say that Enessere has achieved its goal thanks to
the careful study of its products’ structure, which is linear and sinuous, materials, and colours. Today, our small, 9 m-high wind turbines placed in gardens, parks, mountain landscapes, and on waterfronts have become “totems of sustainability”, symbols that are proudly displayed by our clients.”
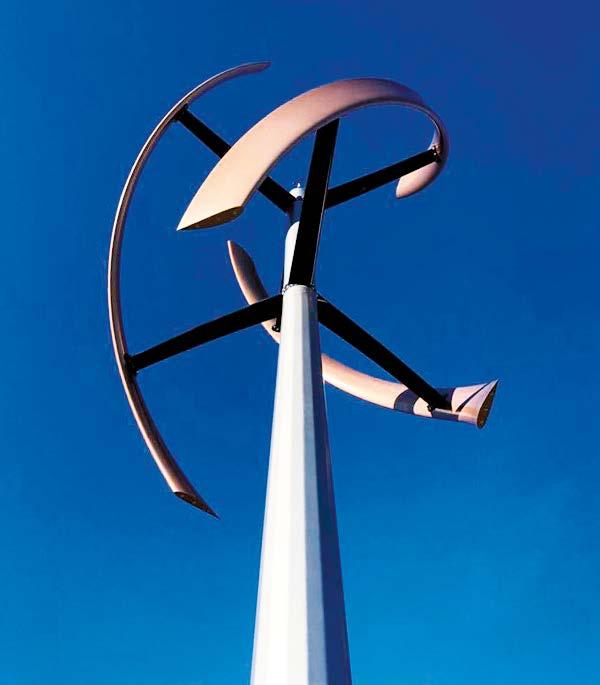
What are the special features that make your turbine special?
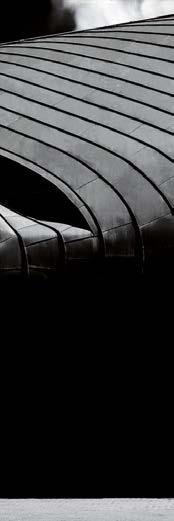
“First of all, the high-quality materials it is made of: wood, stainless steel, and carbon fibre. The first line of turbines we designed is called “Hercules” and features a 316 stainless steel support structure and wings covered with a dense weave of Paulownia wood slats to ensure perfect aerodynamics. The tower of our second line, “Pegasus”, is made of S355 N steel to which we apply three coating layers to protect its surfaces. The same paint, which can be customised in different colours, is also used to coat the wings, which feature a carbon structure just like the connecting struts that support them. Indeed, this possibility of personalising it with the colour chosen by each customer is the second important feature of our product.”
Why does colour play such a strategic role?
“Because it is also through colour that this type of product can be appreciated. In addition to their high functional performance, guaranteed by our consolidated experience, we have identified the colours that best suit our turbine blades together with Francesca Valan, an industrial designer specialising in colour, materials, and finish
design, and our paint supplier Lechler. In fact, we realised that giving customers the freedom to choose their preferred nuance often turns into a limitation and not an opportunity. Therefore, we decided to develop a palette from which everyone can select the most suitable tint depending on the specific landscape, creating a harmonic relationship between the turbine and the place where it is installed. The wings of Enessere’s wind turbines have the colours of the sky and of clouds, whereas their towers have warm and cold neutral colours matching the trunks of the trees and the urban environment. We aim at proposing material-inspired, natural, and “quiet” tints in the name of “chromatic silence”. Today, our towers in the colours of different materials (graphite, metal, titanium) can be combined with five wing colours inspired by earthly and celestial elements (silk, sky, metal, copper, and space) in six different combinations.”
How are the turbines coated?
“We outsource the coating phase. Our coater uses the same manual, spray application system utilised for automotive refinish applications. In compliance with the ISO 12944 standard, our coatings meet the requirements of the C5 class for very corrosive environments, as are those where our generators are installed and exposed to high pollution, humidity, and salinity conditions in seascapes. A three-layer coating system is applied, consisting of a protective primer, the pigmented paint chosen by customers, and a clear coat for UV protection. The finishing quality achieved is comparable to that of car bodies, uniform and pleasing to the eye, precisely because our wind turbines have to fit into particular landscape contexts, such as urban ones. That is also why we chose to use architectural paints that guarantee a service life of up to 25 years.”
You have offered something truly innovative to the market...
“I like to think that Enessere has not only “given beauty” to an object that has always been considered unaesthetic, but also succeeded in creating a “culture of sustainability” through colour, with turbines comparable to contemporary art sculptures – to be exhibited, rather than hidden. I think I can conclude that thanks to this innovative concept of renewable energy devices, we have finally managed to “colour wind”.”
Halved Colour Change Times and Tenfold-Reduced Powder Disposal Volumes: Nord Laser’s Experience
Alessia Venturi ipcm®An excellent partner in managing complexity. This is how Nord Laser Srl (Reana del Rojale, Udine, Italy), a metalwork company specialising in the processing of pickled and galvanised sheet metal for a variety of industrial sectors, defines itself. After a years-long process of vertical integration of production, it can now offer a complete contracting service for advanced industrial metalwork machining, assembly, and coating. The investment it made in a new-generation Wagner powder centre in 2022 has increased its coating efficiency tenfold, with colour change operations being performed without manual intervention, fast and consistent turnaround times, accelerated production, increased volumes, and maximised finishing quality.
In 2022 Nord Laser invested in a new application system, Wagner’s IPS powder centre, conceived with the same perspective as a machine tool to increase productivity, maintain high-quality standards, operate in a simple manner, and constantly reduce colour change times.
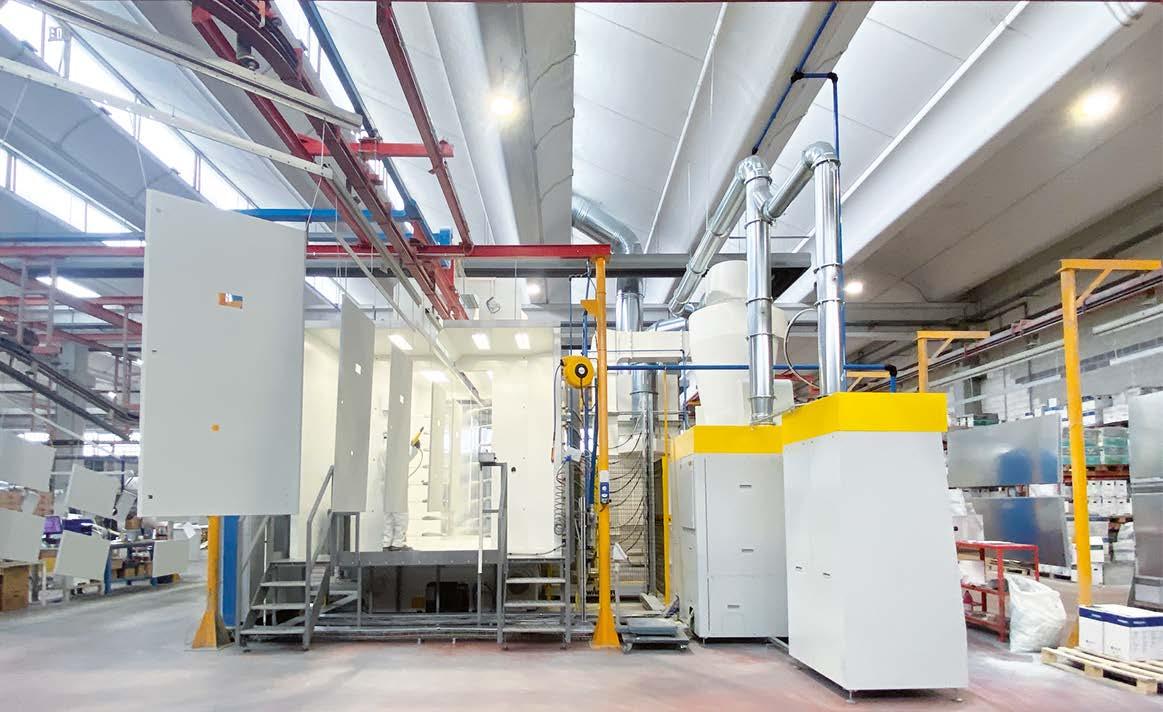
“Nord Laser’s key strength is the ability to simplify complexity through its strategic skills, its customer-oriented, problem-solving approach, and its capacity to manage any critical issue developed over forty years,” explains Marco Bovolini, the president of Nord Group Spa, the holding company to which Nord Laser and other companies in the food, fitness, and mining sectors belong. “At Nord Laser, each project is the story of an ethical, technological, and innovation challenge. Over the years, we have structured it to be ready even for the most unexpected requests aiming at always satisfying our customers, also in terms of delivery speed and adherence to the planned processing times. Punctuality is an essential value for Nord Laser,” adds Bovolini. “Our idea of partnership is very concrete. It requires complete operational development plans and involves each customer at every stage, from co-design to objective sharing, including cyclic and tightly integrated monitoring activities. In Nord Laser, customers can find a complete, verticalised service from a single source, thus avoiding all the disadvantages of long and complex supply chains.”
From analysis and production to coating and shipping, every stage is managed to guarantee excellent performance. It was precisely the coating operation that was the subject of a major capital investment in 2022 for switching to a new application system, Wagner’s IPS powder centre, conceived with the same perspective as a machine tool to increase productivity, maintain high-quality standards, operate in a simple manner, and constantly reduce colour change times.

From 1980s craftsmanship to 2000s integrated industrialisation
Nord Group’s history began in 1984, when Alessandro Bovolini founded Bovolini Snc to carry out welding and light metalwork processes for the local market.
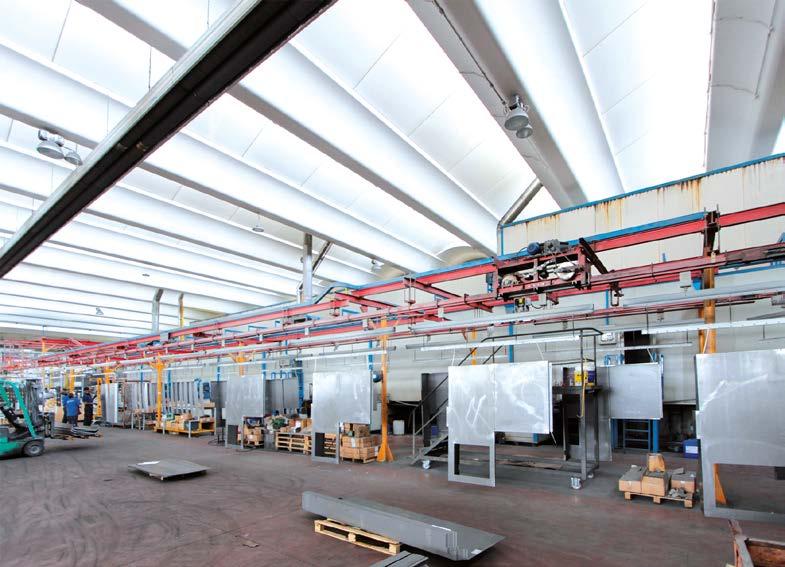
Over the years, the company has evolved to its current structure, where the holding company Nord Group Spa owns four other firms, i.e. Nord Laser and three startups: Canali System in the fitness sector, North Group Mining in the mining sector, and Gabin in the catering sector. Meanwhile, Nord Laser’s evolution has involved moving from purely manual operations to an increasingly technological approach, beginning with its first punching machine and continuing with the installation of laser cutting and many other advanced machines. Over the years, it has made several investments in the vertical integration of its production flow, up to the powder coating stage.
“We are a contracting company, but we have a highly verticalised production cycle: we start with the raw materials, namely pickled or galvanised metal sheets, and we supply machine parts or complete systems, also performing the final plant acceptance phases, including on-board electrical equipment,” says Bovolini. “We like to call ourselves “the production department of our customers”, which operate in various fields, including the steel, energy, textile, air conditioning, and machine tools industries, as well as the furniture and fitness ones in
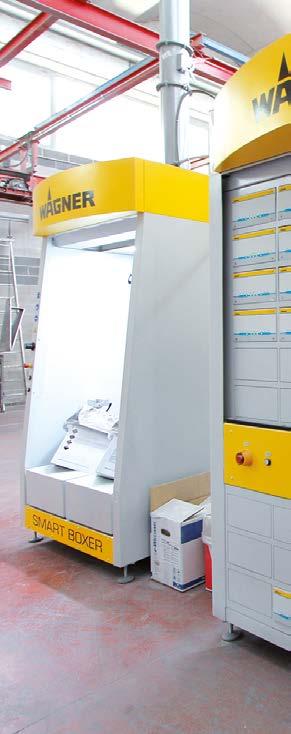
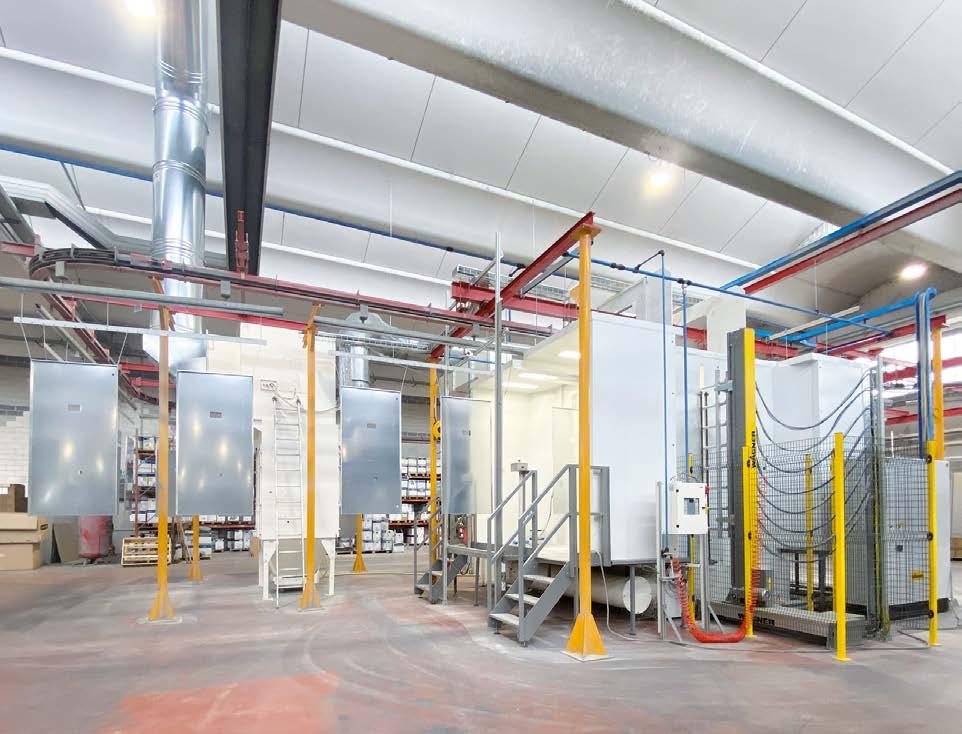
the case of Canali System, another of our Group’s companies. This means that the technical and quality specifications we have to meet vary greatly depending on the sector for which the parts are intended: they range from purely functional specifications with high corrosion resistance requirements to specifications where aesthetics are of the essence. Our strategy has been to vertically integrate production in order to offer a complete service and a net reduction of all the management costs of a conventional supply chain.
“With time, this approach has rewarded us so much that our customer base is now changing, moving more and more towards industrial companies. These new manufacturing requirements call for extreme production flexibility, definite lead times, and high quality. This, in turn, has led us to sophisticate our management control tools. We have implemented a robust Enterprise Resource Planning (ERP) system for production planning and management, an MES for data collection, and several other tools focusing on digitalisation and Industry 4.0 – like our latest investment, the Wagner IPS coating booth, which we believe is the new benchmark in powder application.”
A three-year investment period with a focus on coating
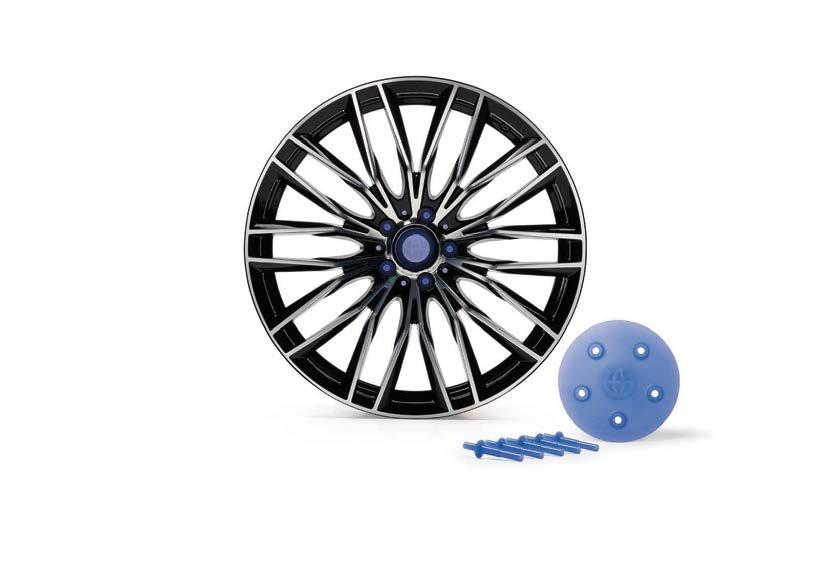
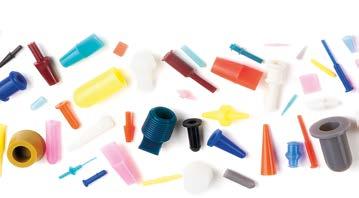
Over the past three years, Nord Group has invested around 5 million Euros in new technologies, renewing its laser cutting and bending machines, creating a new in-house machining department, installing five robotic welding stations, and upgrading its paint shop with a state-of-the-art Wagner booth.
“Our production cycle includes laser cutting, punching, deburring, bending, machining, welding, coating, and assembly. The vertical integration of all these services is a winning business proposition and coating is a strategic part of it: as it requires skills, expertise, and substantial capital investment, not all manufacturing companies are willing or able to integrate this special process in-house,” notes Marco Bovolini.Nord Laser currently operates in four factories of about 5000 m2 each, one of which is
devoted to painting. It is equipped with a coating line designed by Imel in 2000, which can treat parts up to 6 metres in length, 2 metres in height, and 1 metre in width.
From the left:
The Wagner spray booth, with two touch-up stations before and after the automatic coating phase, is part of the advanced IPS system.
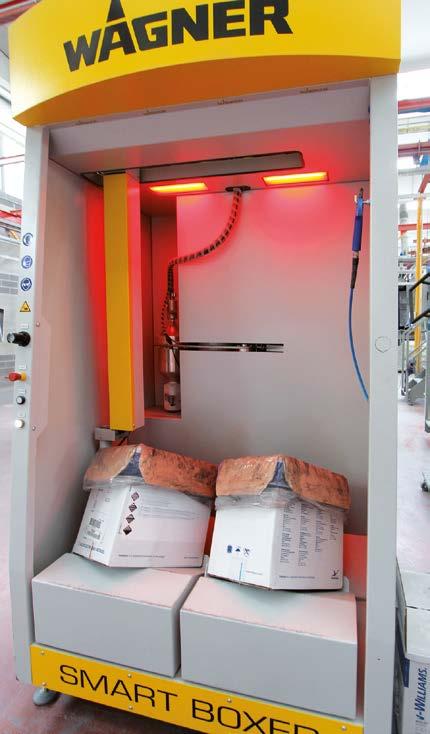
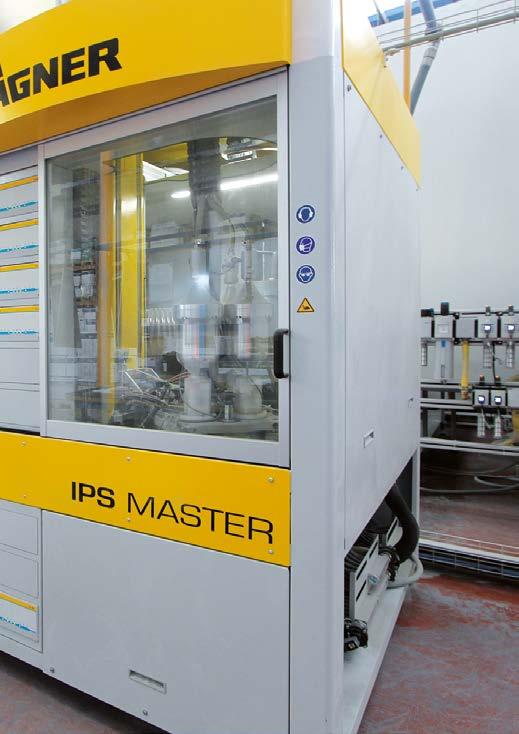
General view of the Integrated Powder System (IPS) combining powder preparation, feeding, dosing, and colour change in a fully automatic plant.
Smart Boxer, the smart virgin powder feeding system, during a colour change operation. This is activated at the push of a button.
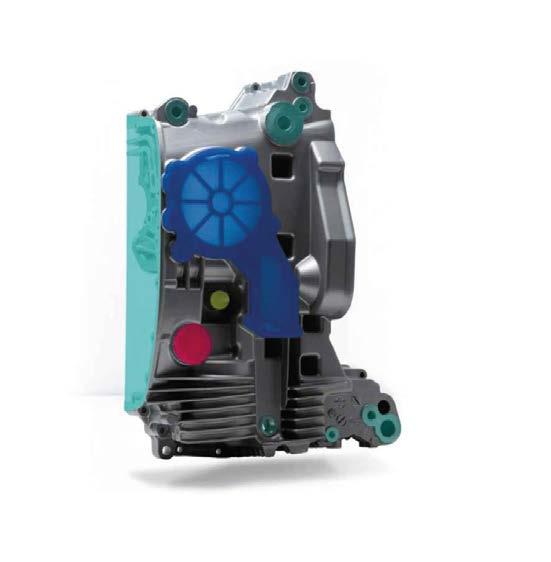
This system recently underwent two major updates. The first involved the pre-treatment process, which moved from 5 to 7 stages, including alkaline degreasing, mains water rinsing, phosphating, further mains water rinsing, demineralised water rinsing, atomisation of a nanotechnology passivation product, and final demineralised water rinsing.
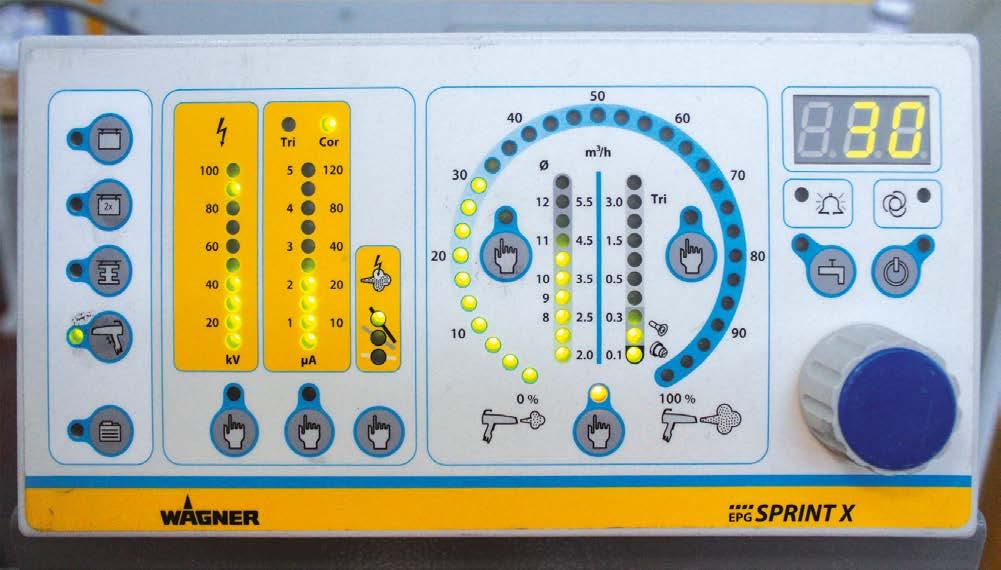
“The requirement behind this improvement was to pre-treat both of our raw materials to the same quality: as is well known, alkaline degreasing works best on galvanised sheets whereas phosphating is ideal for pickled sheets,” indicates Marco Bovolini. “In addition, we were facing a few issues in the pre-treatment of galvanised sheets along their laser-cut edges, at the separation between the galvanised surfaces and the cut ones. This is why we also introduced a deburring stage before chemical pre-treatment to radius their edges. Our coating process is Qualisteelcoat certified. We guarantee high corrosion resistance (class 3C) on galvanised sheet metal with pre-treatment + one layer of paint; we can achieve class C4 with the application of two layers of powder, but there is currently no demand within our market.”
“This update on our pre-treatment process is very recent and validation with Qualisteelcoat is currently in progress,” adds Bovolini.
“The second upgrade, the one that has brought us huge benefits in terms of coating efficiency, was the replacement of the old application booth with a latest-generation Wagner IPS system, which has led to a
drastic reduction in the disposal of spent powder, halved downtime required for colour changes, and improved coating film distension and homogeneity. In a nutshell: extreme application efficiency.”
The benefits of IPS
Nord Laser’s coating plant already had an automatic powder application booth, which had undergone a minor upgrade of its electrostatic generators to improve efficiency. However, the company’s spent paint disposal volumes were still very high, about 12 tonnes per year against a total consumption of 80-90 tonnes. In 2021, it began to make contact with some potential suppliers of a new automatic application technology and eventually chose to invest in Wagner’s advanced IPS system, a complete, innovative, and fully automatic solution ensuring consistent finishing results. This entailed a new operator approach to the coating cycle, a system meeting all 4.0 and IoT requirements, and the automation of tasks that used to be manual.
“We were assessing two application benchmark systems at the same level. Wagner’s IPS, however, changed the game,” says Marco Bovolini. “Because of our focus on technological advancement and our desire to stay one step ahead of the competition, we opted for IPS. This solution solved two problems that were very important to us: high powder consumption, as we had reached a peak of 12-13 big bags of fine dust to be disposed of per year, and the long downtimes required for our
colour changes, about 6 per day. When Wagner presented us with its IPS system, we immediately realised that this new-generation powder centre could allow us to better manage paint consumption as well as our spraying patterns. The advantages in terms of production process management were decisive, rather than those related to aesthetics, which were of less interest to us since industrial products account for 90% of our coating volumes.
“All powder management units on the market have a high level of automation; tasks are sequenced by the system and not managed by the operator. With IPS, the operators only have to clean the booth and the cyclone: for everything else, they only need to press a button. This has enabled us to set a standard process time for colour changes with extreme precision and consistency,” explains Bovolini. “With the old powder centre, we used to leave 12 load bars empty on the one-rail conveyor to guarantee enough chain length for the colour change. Sometimes, this was not even sufficient and the line would stop for up to 30-40 minutes. With IPS, we have reduced the space on the chain for colour changes to 6-7 load bars, i.e. 50% less than before, and we never need to stop the line. While maintaining the same performance degree of the Imel line, the switch to the IPS system has enabled us to cut our
NORD LASER, A CONCRETE PARTNER
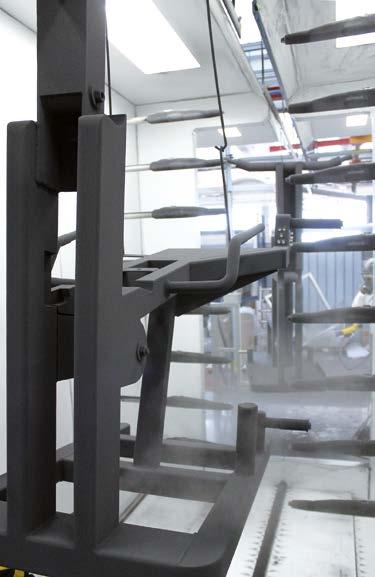
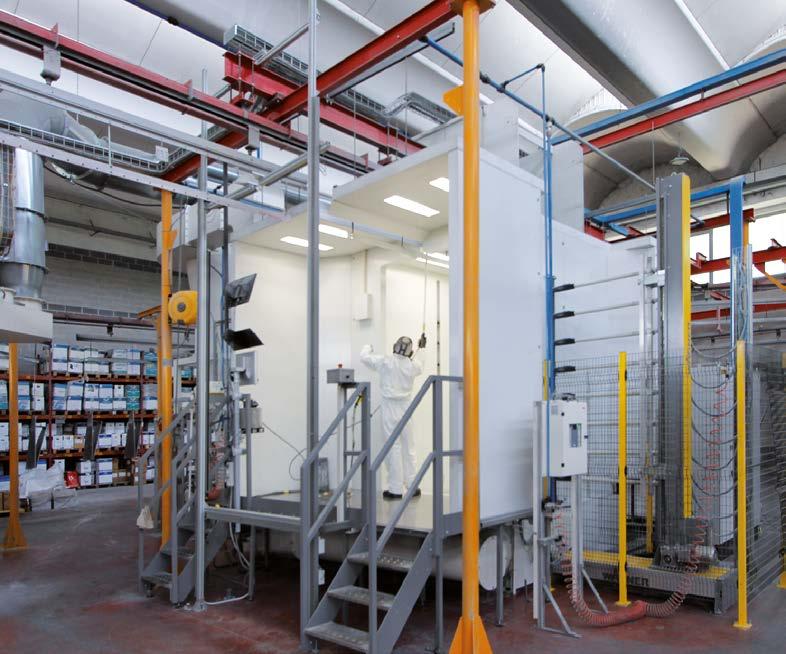
50,000 m2 surface area of which 18,000 are covered 20 million Euros in turnover (year 2022)
100 customers in 2022
10,000 t of processed material
130 employees
3-shift work
2D/3D Solidworks software
Business Intelligence
Quality Certifications
Lean Production
powder disposal volumes to 1 bag, i.e. a tenfold reduction compared with the previous requirements.”
“It is undeniable that the old system was more wasteful as it was not equipped with a parts detection bar, so that the paint guns, 6 on each reciprocator, were always on, with considerable dispersion of powder,” says Venanzio Rosada, Wagner’s sales agent for the Friuli Venezia Giulia region. “However, even if we had implemented a parts detection bar, we would not have achieved the same results in terms of consumption reduction, because IPS has a completely different approach in terms of overspray recovery and filtration, with a very soft suction and feeding mode that minimises the generation of fine dust. It is important to note that these data are related to products from the same powder coating suppliers, because particle size consistency also plays a key role in the creation of fine dust. In essence, IPS is a state-of-the-art powder management system that guarantees stable paint feeding conditions
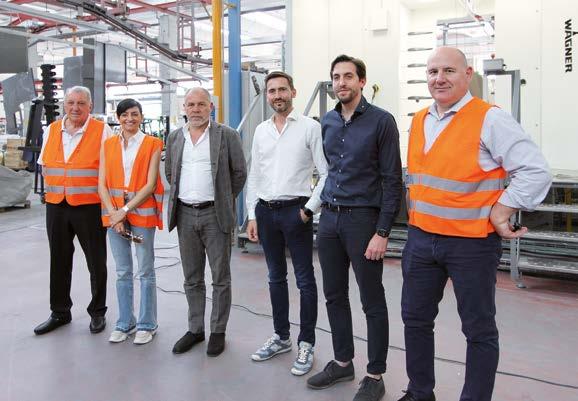
with a 0.5-bar VACUM unit and pressurised ultrasonic sieving,” summarises Rosada. “It also offers the highest level of colour change automation requiring no human intervention, centralised control of all process steps, and real-time powder consumption tracking.”
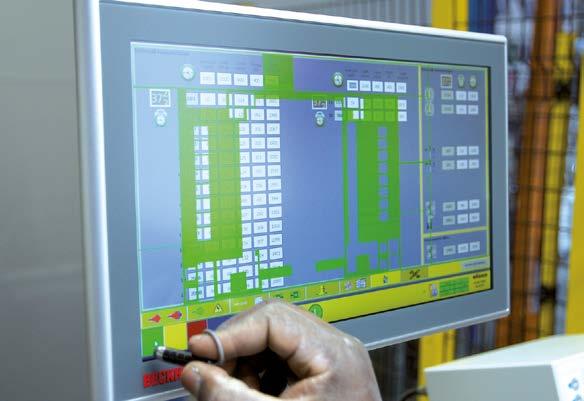
A new market benchmark?
“We are still working to fine-tune the management of all the booth’s parameters and understand in detail the behaviour of high-density application for optimising paint penetration into 3D parts,” states Marco Bovolini. “For Nord Laser, halving our colour change times was crucial because our plant’s capacity is always saturated. It is undeniable that the investment required was very high, but I believe that the return on investment is also going to be very high within a very short time. Not to mention that this technology could become a new market benchmark, with a very high future residual value.”
VERNICI E RIVESTIMENTI IN POLVERE POWDER COATINGS
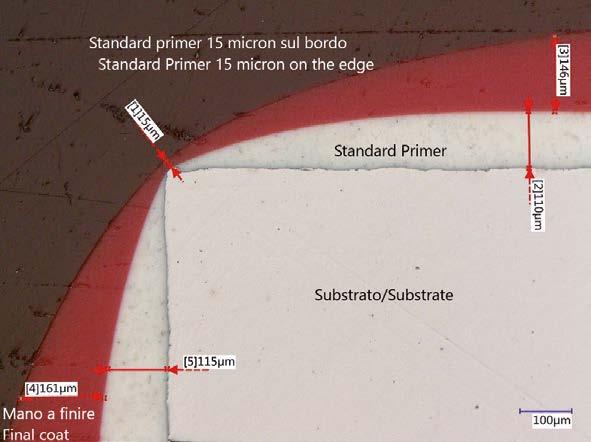

ENDURANCE
IL PRIMER COPRI SPIGOLI THE EDGE COVER PRIMER
ENDURANCE
La serie Endurance 16J0, realizzata con resina epossidica leggermente raggrinzata ed additivi ad effetto barriera e passivanti, garantisce un’eccellente copertura dei bordi e quindi un’eccellente protezione.
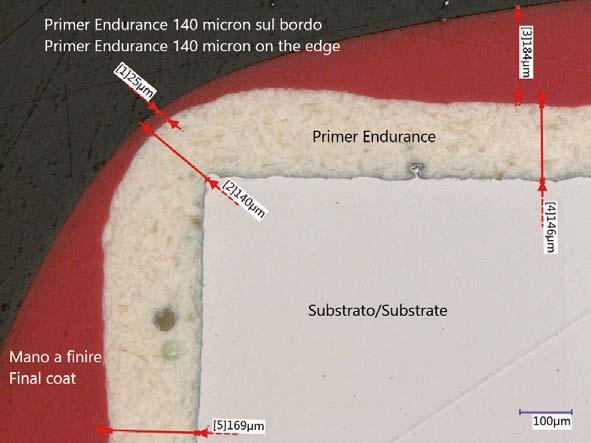
The Endurance 16J0 series, made with slightly fine textured epoxy resin and additives with a barrier and passivating effect, guarantees excellent edge coverage and therefore excellent protection.
Pulverit S.p.A. Italia
Via Carlo Reale, 15/4
20157 Milano-Italy
Tel +39 02 376751
email: pulverit@pulverit.it
Pulverit Polska Sp. z o.o.
ul. Strefowa 16
43100 Tychy-Polska
Tel. +48 32 329 14 11
email: biuro@pulverit.pl
Pulverit Deutschland GmbH
Im Wert 3
73563 Mögglingen- Deutschland
telef.: +49 7174 7193000
email: info@pulverit.de
Pulverit Iberia s.l.u.
c/ Caravis, 28, 1º 3ª
50197 Zaragoza
Tel. +34 607163259
email: iberia@pulverit.it
The Circular Economy’s Challenges to the Coating Industry and Chemtec’s Answers
Carlo E. Guidetti Chemtec Srl, Corbetta (Milan, Italy) info@chemtec.itThe world’s population has grown exponentially in recent decades and it has now exceeded 7 billion people. According to various demographic development forecasts, it is going to reach around 10-11 billion people in 2050. Around 54% of it lives in urban areas and this percentage is going to increase to 64% in 2050. Cities, in particular, are responsible for about 70% of anthropogenic emissions and contribute to generating about 70% of total civil emissions, 50% of global waste generation, and about 60% of greenhouse gas emissions1
The “Country Overshoot Day” is the day of the year when each country goes into ecological debt, i.e. it finishes using all available natural resources for that year in relation to its regenerative capacity. It is, therefore, a true environmental accounting tool: devised by the Global Footprint Network, it uses biocapacity and ecological footprint data to determine when humanity will come to use more resources than it has at its disposal, both globally and locally. As can be seen from the diagram in Figure 1, all advanced economies on the planet consume their resources within the first few months of each year. These data tell us incontrovertibly that the world’s economic system is exploiting the resources of our planet too rapidly.
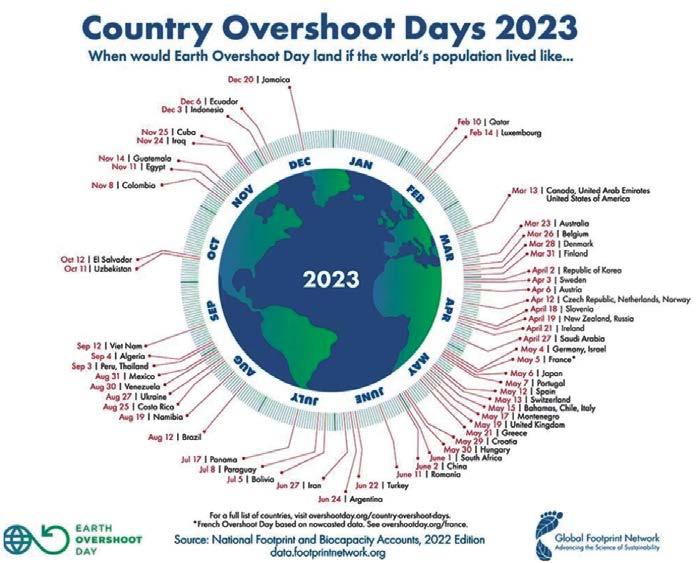
A global change is therefore required to set us on a path where our living needs are adapted to the available resources. In this framework, the manufacturing industry plays a very important role as a major user of natural
resources (gas, water) and energy and as a generator of air and solid emissions.
The shift from linear to circular economy
The historically existing economic model, referred to by scholars as “linear”, entails a very simple cycle: taking resources from the planet, processing them to produce goods (often using other resources and creating waste within the production cycle), selling and using the goods themselves, and disposing of them at the end of their service life. This traditional system is hardly compatible with
the current environmental context and the need for change described above. For some years now, the linear economic model has been countered by a new “circular” economic model, conceived to be regenerative. Here, the production model promotes the minimisation of environmental resource use and emissions and the consumption model is based on sharing, reusing, repairing, and recycling existing materials and products to reduce waste and resource consumption. The differences between traditional and circular economic models are summarised in Figure 2
The circular economy and the challenges for the industry
The circular economy model developed some years ago by the Ellen MacArthur Foundation shows that, in a circular system, every good is produced utilising as much renewable energy as possible, minimising the use of natural resources and designing objects in such a way that they are at least partially repairable, reusable, reconditionable, or recyclable through simple operations. Some elements of this economic model are already part of our system: let us think, for instance, of the market for refurbished smartphones or tablets.
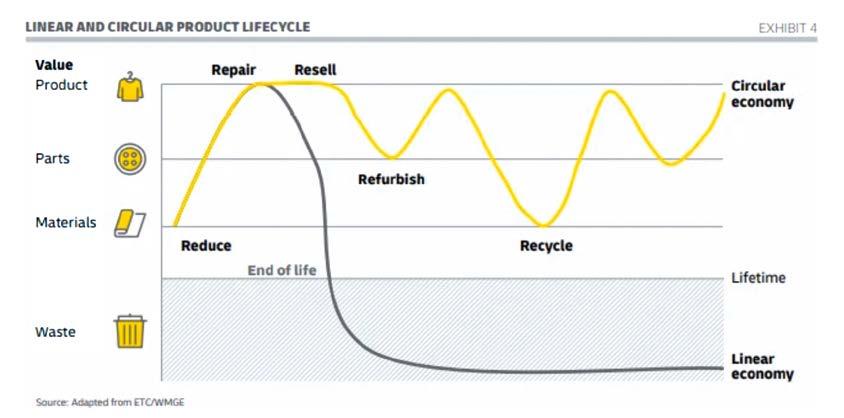
A few years ago, the International Organisation for Standardisation (ISO) started a formal regulatory process for the circular economy, with standards currently being developed from the ISO 59000 series. In Italy, the Italian Standardisation Body (UNI) has adopted the technical standard UNI/TS 11820:2022, which allows companies and organisations to measure their circularity rate by adopting shared criteria; the current version of this technical specification includes 71 circularity indicators, divided into six categories: resources and components, energy and water resources, waste and emissions, logistics, products/services, and human resources. It is therefore clear that we witnessing the beginning

of a shift from the linear to the circular economy. The ability to adapt to this change will be one of the key factors in the coming years for manufacturing companies, at least in Europe and in all the world’s mature markets. Companies such as Freitag2 are cited by the economists as examples of firms that are already taking advantage of this transition to create new business opportunities: Freitag manufactures bags and accessories from recycled truck tarpaulins, PET bottles, and unexploded airbags. Even giants such as IKEA3 have started to carry out major initiatives to reuse their furniture and components. In this new phase of the circular economic model, the challenges facing the manufacturing industry can be summarised as follows:
• minimised use of environmental resources – water and natural gas

• drastically reduced energy consumption from nonrenewable sources

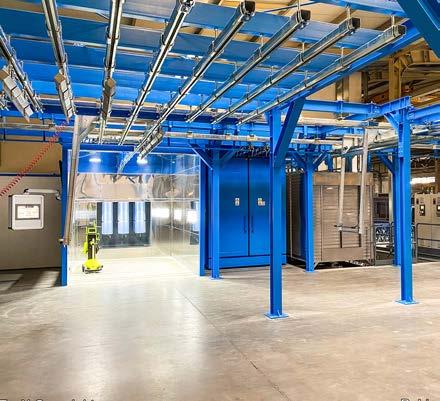
• no use of toxic substances in production cycles
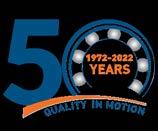
• reduced generation of discharges, waste water, byproducts, and solid waste.
Any manufacturing company that would like to anticipate the changes imposed by this shift will inevitably have to set itself these goals.
2 https://www.freitag.ch/en
3 www.ikea.com

Chemtec’s responses to the economic transition Chemtec, an Italian company based in Corbetta (Milan) and specialising in the formulation, production, marketing, and industrial application of chemical products for pre-painting surface treatment and industrial water treatment (waste and process water), can act as a strategic partner to support its customers in this transition.
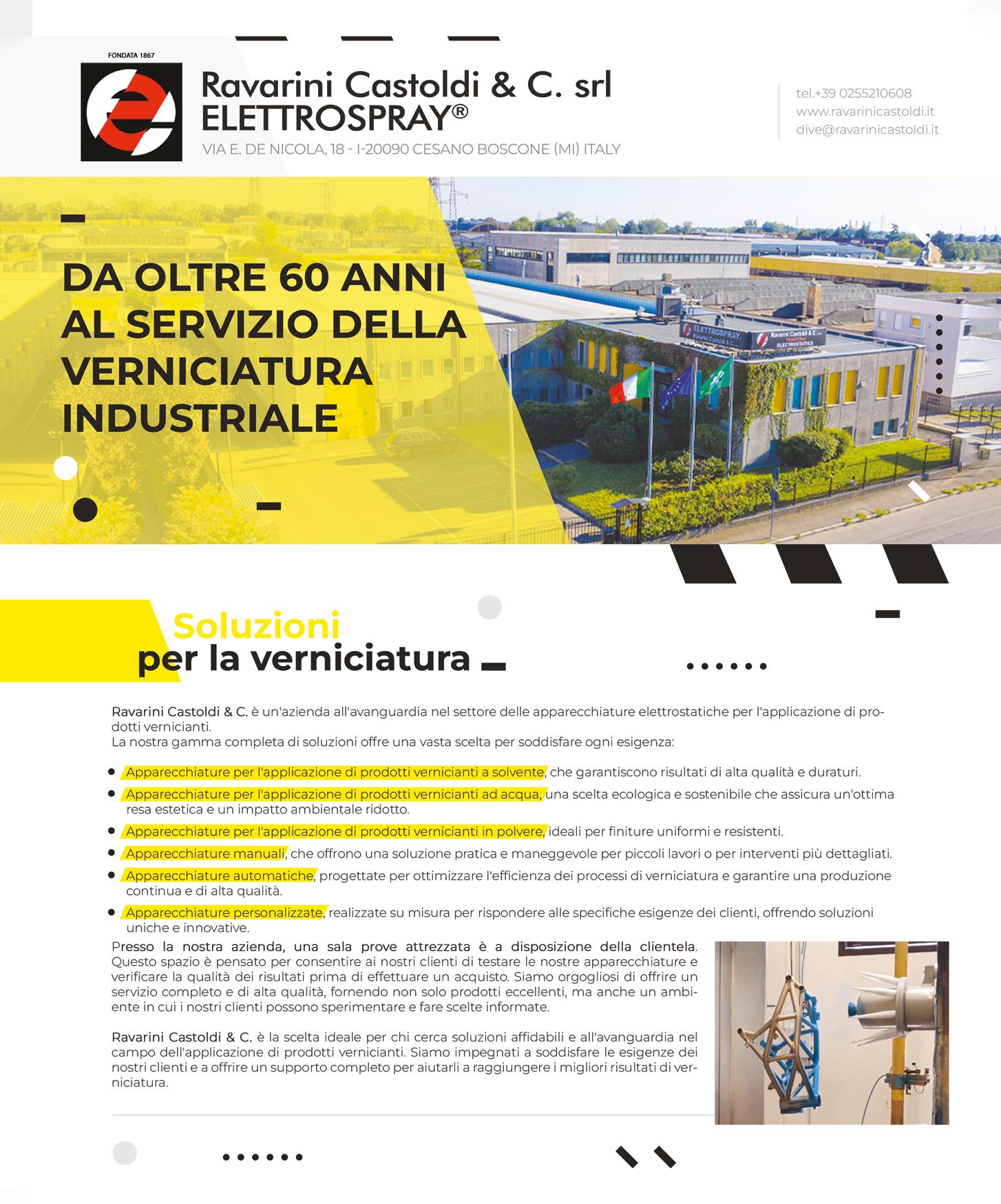
Overspray management
In the field of overspray treatment, there are two technologies available: dry filters and water curtain booths. Regardless of any economic evaluation, according to the principles of the circular economy described above, in many cases the latter are preferable to the former. Although water curtain booths do use water, through specific equipment and specially formulated chemicals (Figure 3) it is possible to turn the paint overspray into sludge with a low water content (dry residue of around 60-70%), thus purifying the booth water constantly and continuously
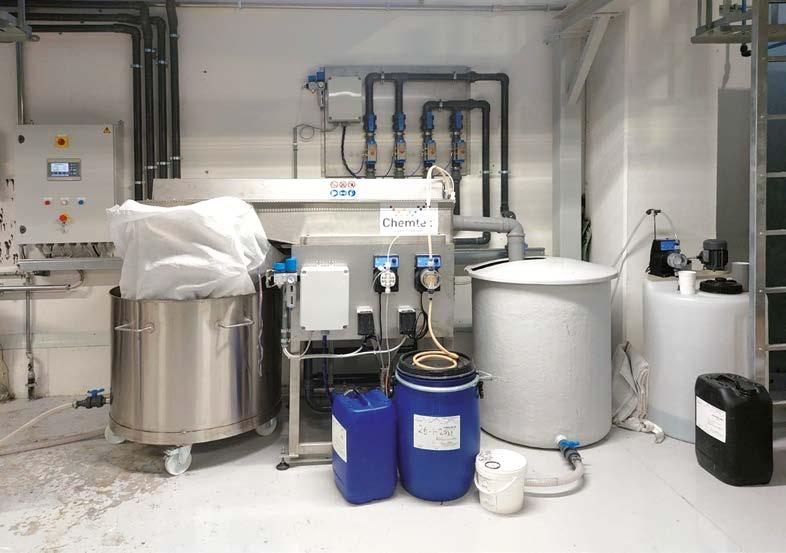
and avoiding frequent disposal. Chemtec is currently investigating a solution to reuse such sludge, turning it from waste into a by-product for reuse as components in new systems. Paint-impregnated dry filters, on the other hand, must be disposed of without the chance of giving them a second life.
Pre-treatment
The pre-treatment of metal surfaces before coating is one of the most environmentally impactful phases of a finishing process. Traditional processes consume large quantities of water (hundreds or thousands of m3 per year) and huge amounts of natural gas and electricity to heat or move the large volumes of aqueous solutions required for the cleaning and phosphating stages. These create solid sludge to be disposed of periodically and call for the replacement of the mass of liquid 1 to 4 times a year on average. It is easy to see why traditional cleaning and phosphating processes hardly reflect the circular economy parameters mentioned above. Chemtec offers some highly innovative
nanotechnology processes to eliminate or significantly reduce these issues. TORAN 3, for example, is an alternative to phosphodegreasing that does not contain or use water, does not need to be heated, and does not generate sludge or waste water of any kind. The processing oils eliminated in the degreasing stage are incorporated into the operation, becoming an active component of it and thus respecting one of the basic principles of the circular economy, namely the reuse of waste products. PRONORTEC, on the other hand, reduces water, energy, and natural gas consumption by around 40-60% compared to traditional processes by exploiting organic phosphorous compounds and, therefore, operating without the presence of any heavy metals such as chromium, nickel, zirconium, or titanium. The ease of use of these solutions also ensures a very low percentage of production waste, thus increasing the efficiency and quality of industrial processes.
Conclusions
The transition of the current economic model from linear to circular has already begun. Several large companies have already adopted changes in asset design, production, and their supply chains to reuse and recycle their manufactured goods and minimise the use of environmental resources. Companies that have not embarked on these projects yet or are looking for solutions in this field can find in Chemtec and its technically innovative processes a reliable partner to jointly tackle the challenges posed to the coating industry by the circular economy.
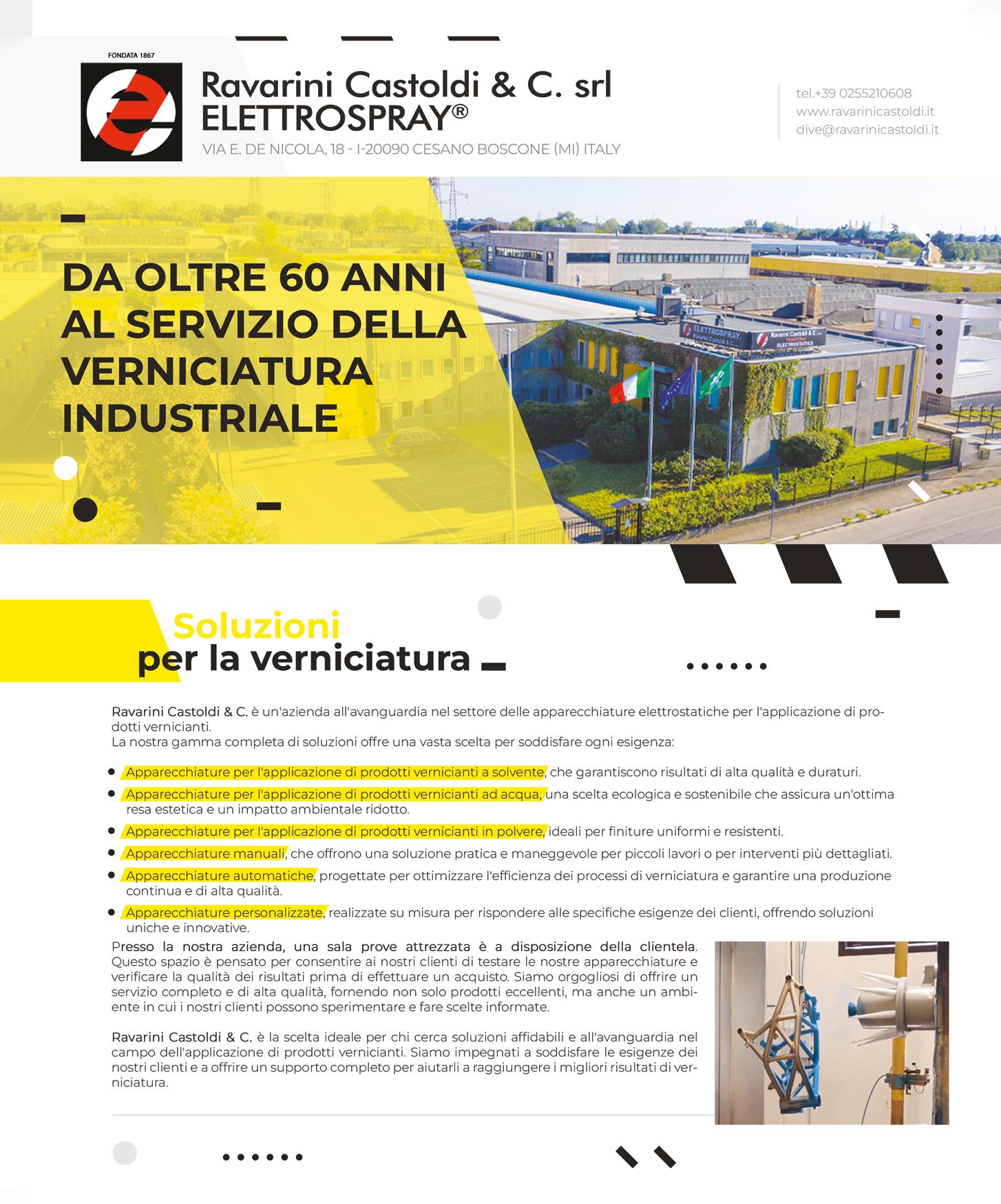
More Options for the Coating of Components for Electric Vehicles

The demand for sealing components made from elastomers is rapidly growing. A major reason for this increased demand is the e-mobility. To meet the requests of numerous coating job shops Walther Trowal has developed the new Rotamat R 100. Compared to its predecessor models the usable volume of this coater is practically doubled. In addition, the R 100 also allows the coating of sealing components with a wider range of materials such as different types of oil, wax and slow drying lacquers.
Rotamat coaters have established themselves as the ideal solution for coating sealing components made from elastomers, such as O-rings, with anti-friction lacquers. Rotamat machines are also used for coating thin-walled metal rings - for example, shaft seal ringswith a bonding agent.
Larger components and higher production volumes
For their drive trains and accumulator batteries e-vehicles require numerous sealing components. These are not only utilized for the accumulator cells but also for cooling purposes. Even components like control modules for e-vehicles have their own cooling systems with
heat exchangers, where elastomer sealing elements with sizes of up to 300 mm are utilized. At coating job shops, already handling millions of components, this technological trend created the need for coating systems with higher processing capacities. To meet this demand Walther Trowal developed the new Rotamat coater R 100. With a usable volume of 160 liters and a payload of 100 kg it can process about 1,000 sealing rings in one single batch. Compared to its predecessor model R 85 it coats twice as many components – within the same cycle time and with only marginally higher energy consumption and space requirements. The first R 100 will be delivered shortly to a coating job shop in Italy. The diameter of the rotary drum in the R 100 is 1,000 mm. To completely cover the entire internal drum space the machine is equipped with two spraying systems.
Processing of more oil and wax types
Another technological trend is the increased use of oil and wax for the coating of sealing components. For example, in medical engineering lacquers are being displaced by silicone oil as the predominant coating material for high value sealing elements. For obvious reasons: silicone oils are more compatible with the human body. Since they are applied in thin layers, but require a highly homogeneous surface coverage, precise dosing within a tolerance of a few grams is essential.
Walther Trowal achieves the required dosing precision of the coating materials by utilizing ultra-modern sensor technology and an electropneumatic valve. This guarantees that the precise quantity of coating material reaches the component’s surface within a given time period. The result is a consistent coating thickness and long-term quality of the applied coating material on the component.
Utilization of more types of lacquer
Several technical features in the new Rotamat coater now allow the application of a wider range of lacquers. Some lacquer types, respectively, coating media demand quick, sometimes even abrupt, cooling of the work pieces after the coating process. To achieve this Walther Trowal added a bypass for the exhaust air coming from the drum. It allows the air to bypass the heating unit after the spraying operation and guides ambient air into the drum. This prevents any residual heat from the heating unit from reaching the coated components. Therefore, they are not sticking to each other and are discharged from the drum as single pieces. The result: A higher yield of work pieces in “1a quality”. Walther Trowal generally equips the Rotamat coaters with a four-stage exhaust air system. It consists of a Papp labyrinth filter, a filter mat and two pocket filters. Therefore, solvents contaminating the exhaust air can never reach the environment. This solution has proven its effectiveness and reliability in many coating applications. With some lacquer types the overspray requires a longer time for curing and becoming dry dust. To prevent sticky lacquer mist from passing through the filter and migrate to the exhaust air system of the machine user, Walther Trowal has further optimized its filtration technology. If needed, fresh air is added to the exhaust air, which causes the residual lacquer particles to dry abruptly. The resulting dust particles are safely retained in the Rotamat filtration system – a significant benefit for occupational safety and the environment.
Higher degree of automation
The automatic drum inclination is another important step towards full automation of the Walther Trowal coating systems. A manufacturer
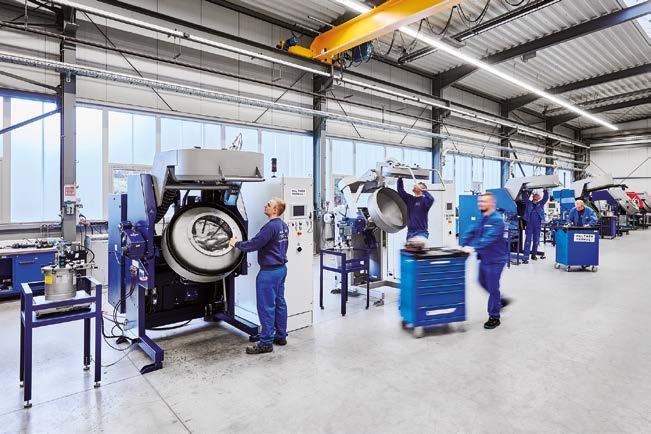
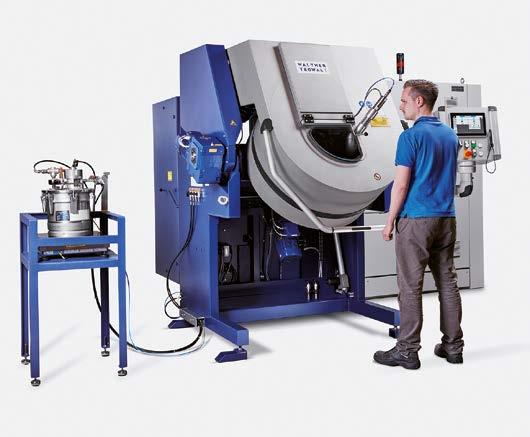
of sealing components reported that he had to frequently adjust the drum inclination during the coating process. He noticed that the components not yet coated displayed different tumbling characteristics than the components already coated. To date the inclination of the rotary drum was activated by an electromechanical drive but had to be initiated manually. In the new Walther Trowal Rotamat coaters the drum inclination is fully automated, and the respective process parameters are part of the PLC processing programs for the various work piece categories. The machines now automatically adapt the drum inclination to the required coating buildup on the work pieces and are, therefore, running fully automatically during the entire coating process. Even with applications requiring multiple changes of the drum inclination the only manual operations are the loading and unloading of the rotary drum.
Higher process stability
With the new control system for dosing the coating material Walther Trowal was able to further improve the process stability of the Rotamat coaters. The new system automatically adjusts the pressure so that under different operating conditions the specified amount of coating material is precisely applied to the surface of the components. In addition to the sophisticated temperature management and the exact fresh air flow, the new pressure regulator ensures optimal conditions in the rotary drum during the entire coating operation. However, the new
pressure control system improves not only the overall process stability, but it also simplifies the coating operation.
About Walther Trowal
For more than 90 years Walther Trowal has produced and sold modular and custom-engineered solutions for the most difficult challenges in the field of surface treatment and refinement.
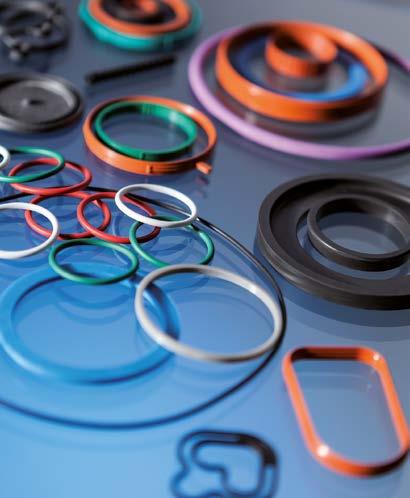
While initially focusing on mass finishing, over time Walther Trowal has continuously expanded its product portfolio. Today the company offers a broad range of mass finishing, shot blasting and coating equipment for surface refinement, cleaning and drying of a variety of work pieces as well as coating of mass-produced small parts.
Walther Trowal develops and implements complete surface treatment solutions: By linking and automating various processing modules
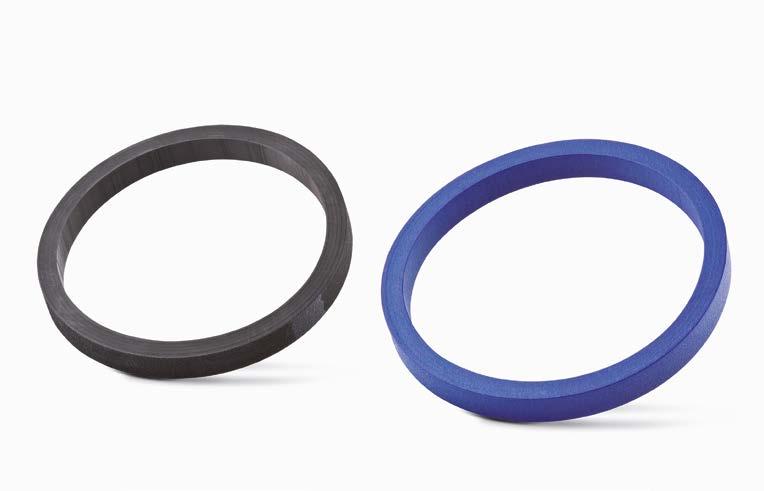
Walther Trowal adapts the respective process technology to the specific requirements of the customers. This also includes peripheral equipment such as process water cleaning and recycling systems. Comprehensive services like processing trials with the customers’ work pieces or the global repair and maintenance service are rounding off the company program.
Walther Trowal serves customers in a wide range of different industries all over the world, for example, automotive, aerospace, medical engineering and wind power.
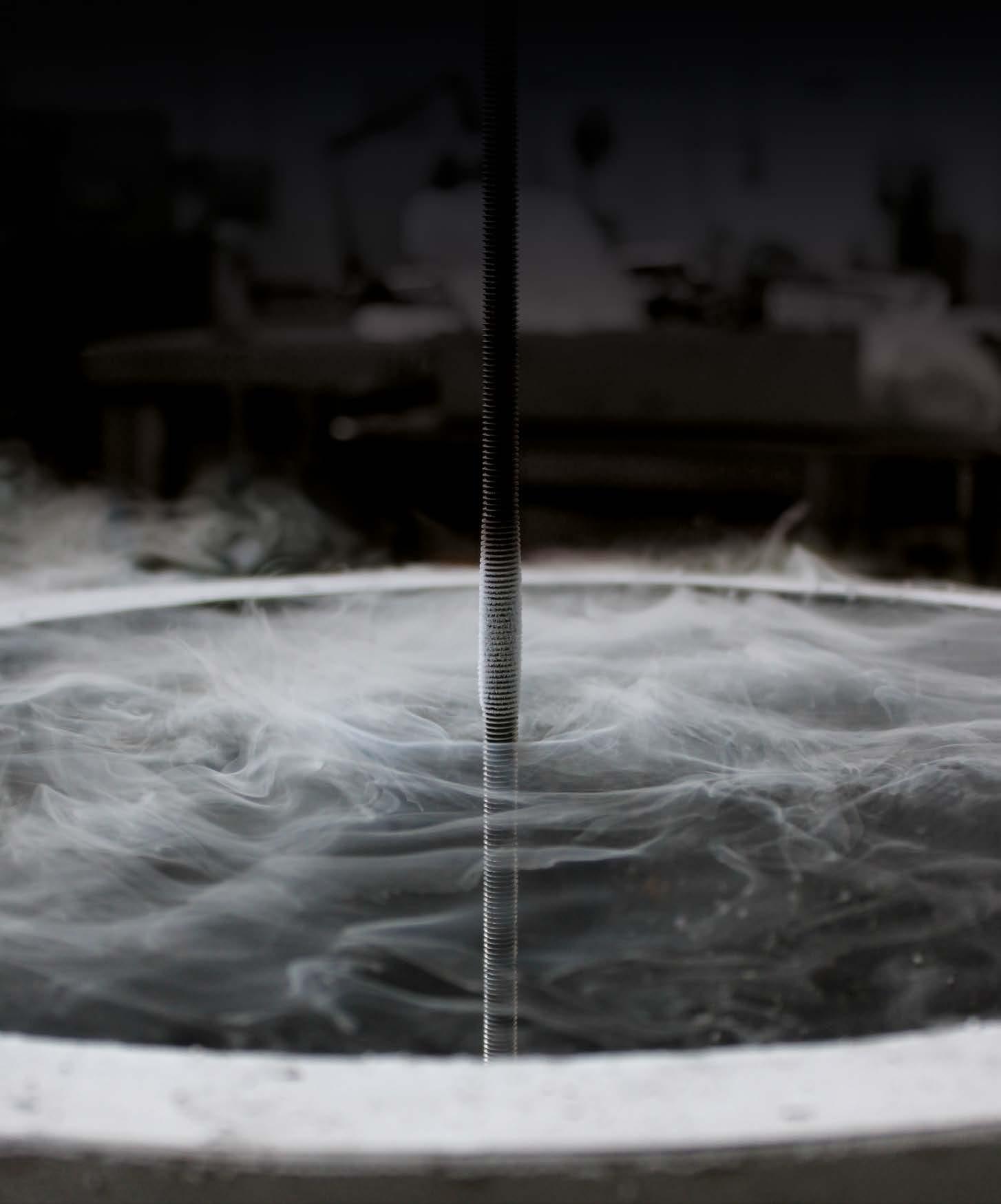
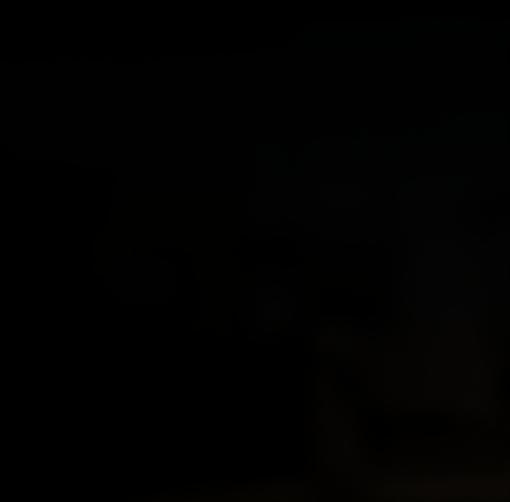
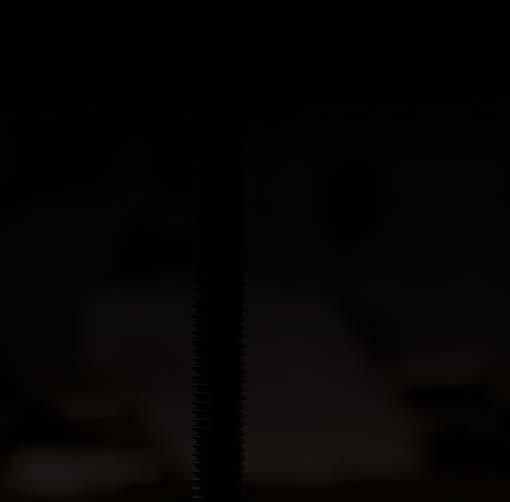
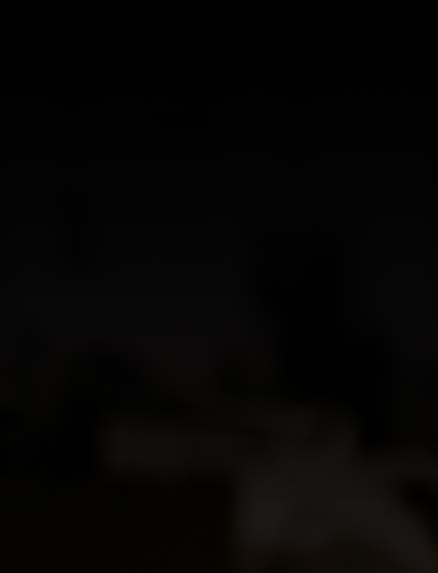
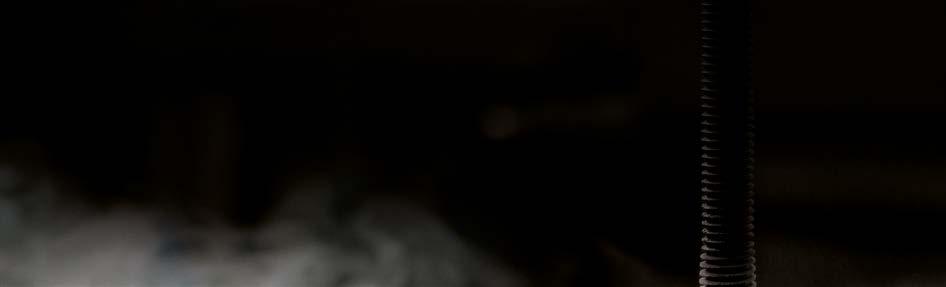
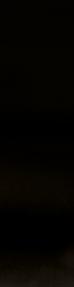
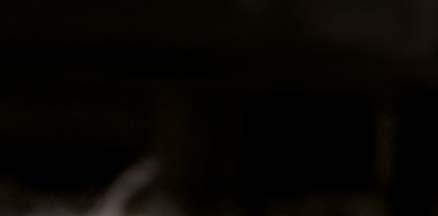
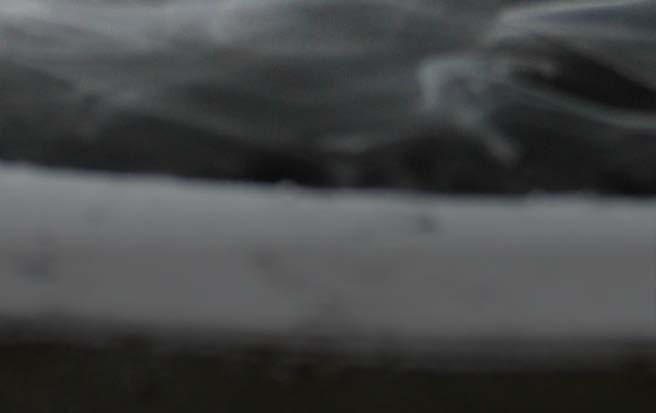
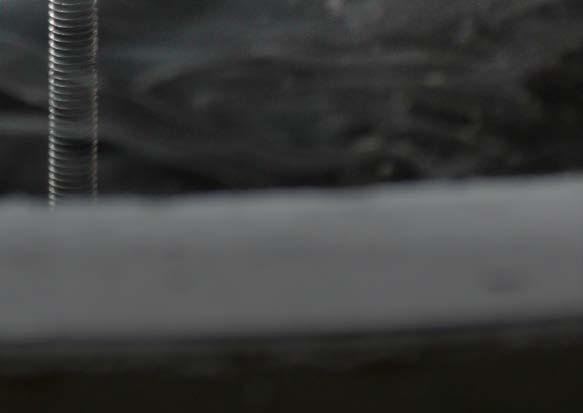
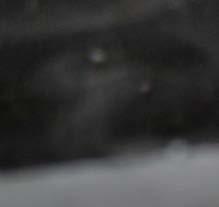
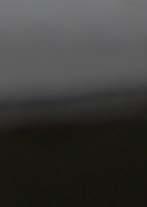

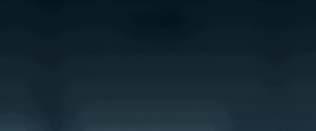
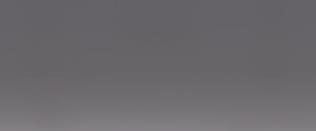
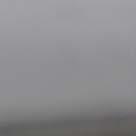
Brief Notes on the Development of Sustainability-oriented Technologies through Automation, Energy Efficiency, Digitalisation, and AI Used in Industrial Coating Processes
Alessandro Soba Verind Spa, Rodano (Milan) – Italy alessandro.soba@verind.itPart of the international Dürr Group, VERIND designs innovative technological solutions by integrating knowhow, industrial systems engineering, equipment, and specific eco-technologies for paint, coating, and waste water treatment processes. A common element of all economic developments is energy (and its consumption), which has always been seen as the engine of progress itself. Any industrial process can be analysed in terms of energy, efficiency, and environmental friendliness with a technological approach that directs the production process to minimise raw material consumption, improving the overall energy balance and thus waste and costs.
The final stage of a production process is generally a surface finishing operation. This has a significant impact on the environment in terms of emissions, creation of special waste, and water pollution. It is also an energy-intensive manufacturing stage with high energy consumption, which further impacts the environment by reducing natural resources.
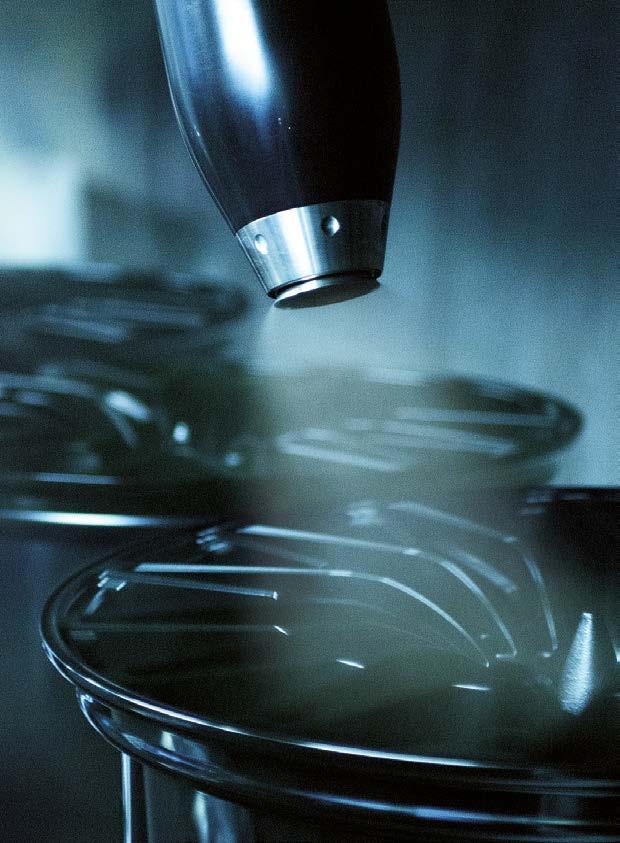
Technological innovation, automation, and processing of data derived from field sensors, supplemented by digitalisation and AI: this is the mix of skills that Dürr brings into play to meet today’s sustainability criteria.
With this in mind, innovative engineering choices are now being made more and more often for highly productive and environmentally friendly coating lines, with the following aims:
• Reducing the energy consumption of individual processes
• Reducing global CO2 emissions
• Reducing consumption of products used and raw materials
• Reducing liquid and gaseous discharges
• Increasing efficiency and quality
• Optimising the cost per unit produced
• Integrating automation and digitalisation
• Increasing efficiency through flexibility. Through innovation and applied research, the Dürr Group has developed, in particular, important technologies for the automotive and industrial sectors.
EcoBell electrostatic technology
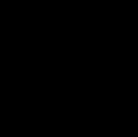
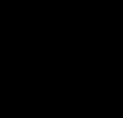
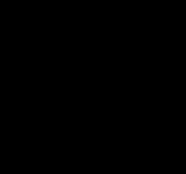
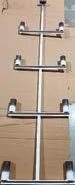
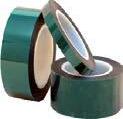
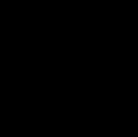
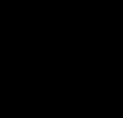
This rotary atomiser with 2- or 4-needle technology and a compact external loading unit, ideal for use on both automotive and general industry lines, guarantees maximum finishing quality, minimum coating product consumption, and quick colour change times. It especially allows saving paint in high quality and high productivity processes, thanks to the electrostatic effect that ensures high transfer efficiency values.
EcoSupply P technology


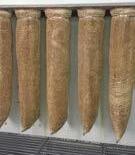
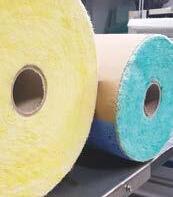


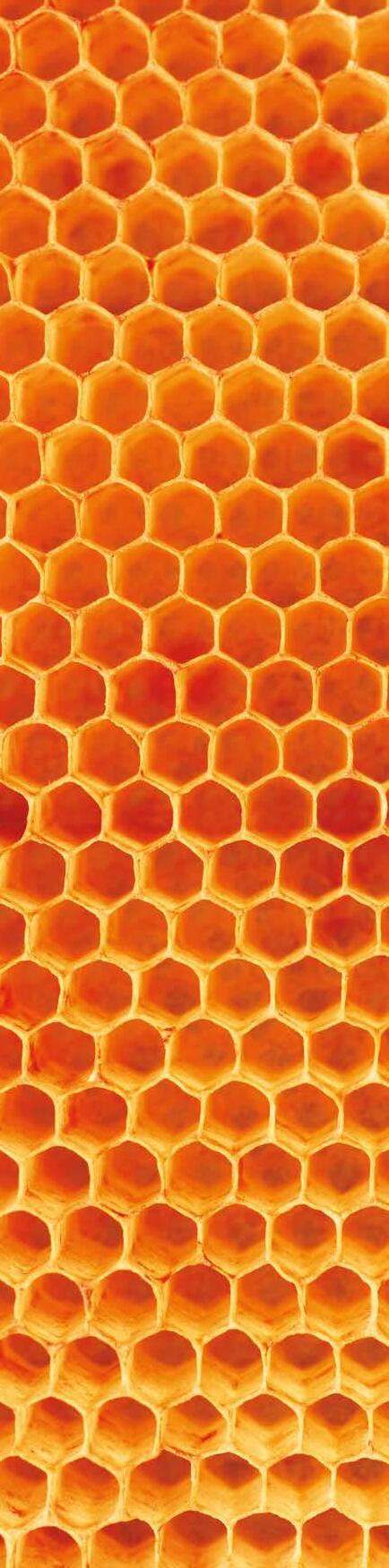
It is a standardised, modular paint feeding system with scraping technology that can be used for water- and solvent-based coating applications. Due
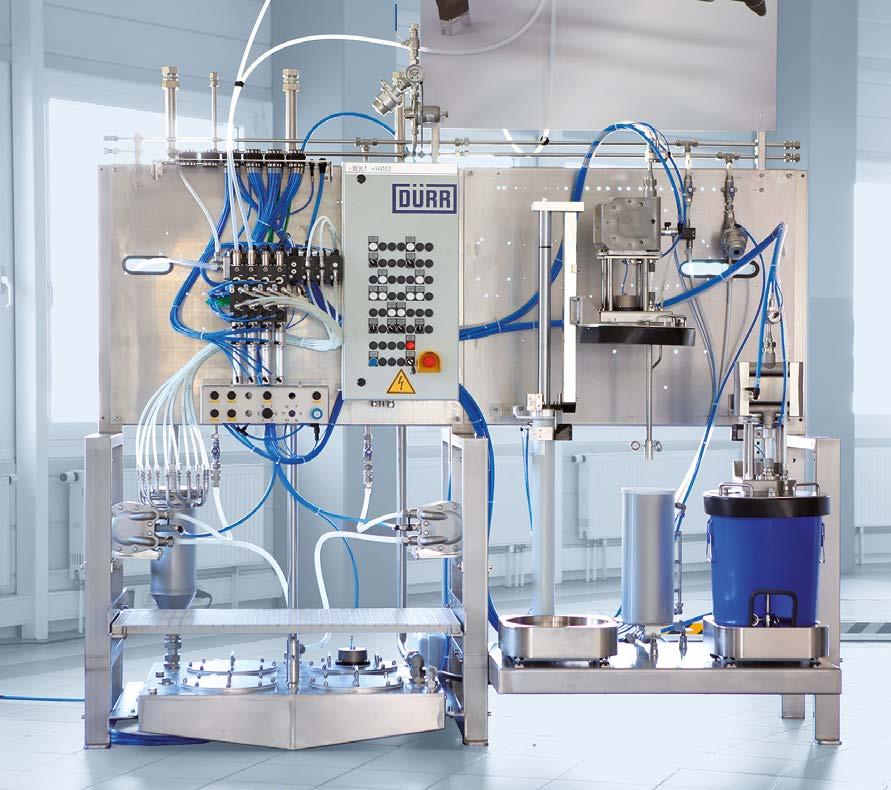
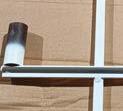
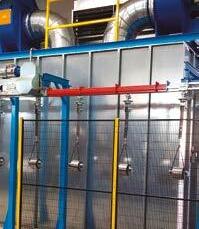
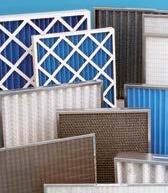
to the considerable increase in the variety of colours required by the automotive and commercial vehicle sector as well as the industry in general, the scraping technology has been used for a long time now both for handling special or customised colours and for colours to be applied on small batches. EcoSupply P allows saving paint and cleaning products, especially in production lines where frequent colour changes are required. Unused paint in the pipes is recovered in the paint drum and reused.
EcoPaintJet - OFA (Overspray Free Application) technology
High customisation: this is the prevailing demand of the market. Examples of this are the creation of

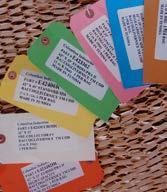
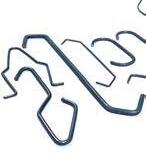
two-tone car roofs or the application of striped designs on various products. EcoPaintJet is an innovative system for automated, overspray-free coating, a perfect combination of robots, measuring systems, and applicators that guarantees selective paint application. Equipped with sensors, its measurement system monitors the surface to be coated and sends data to the plant’s management software, which constantly calculates in which tracks the applicator is to be guided and how much paint is to be dosed. It allows saving paint in production lines devoted, for example, to two-tone surfaces. It eliminates overspray and the need for masking operations and it reduces process energy consumption. In summary, this technology enables to perform highly sustainable processes.
Coating process digitalisation with DXQ
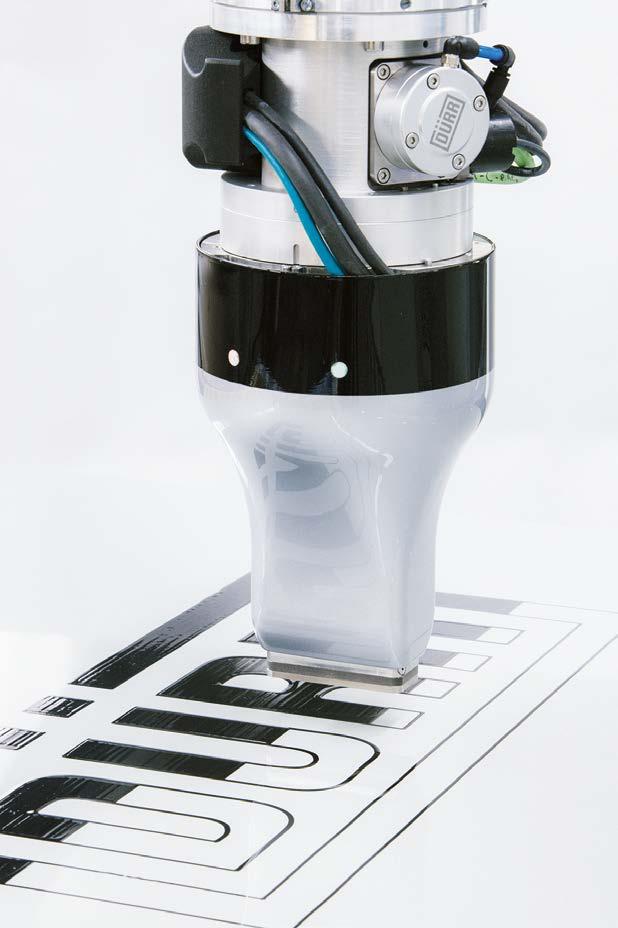
The goal is to apply efficiency measures at all phases of the coating process to systematically increase productivity, reduce unit costs while maintaining the highest quality, and improve sustainability. DXQ is a powerful industrial tool offering solutions for the operation, analysis, and control of modern industrial plants. It allows large volumes of data to be processed and analysed to optimise processes, thus guaranteeing optimised energy consumption, higher production rates, and smart spare parts ordering to minimise the impact of preventive maintenance.
Commitment to sustainability
Dürr also expressed its concrete commitment to sustainability by joining the “Business Ambition for 1.5 °C” coalition, a global initiative by Race to Zero and UN Global Compact, and by presenting its Sustainability Report according to the GRI standards as well as its ECOVADIS sustainability rating document.
There is a strength enclosed in the composition of Europolveri’s products, a formulation that determines their quality and which is reflected in the appearance and resistance of the treated surfaces
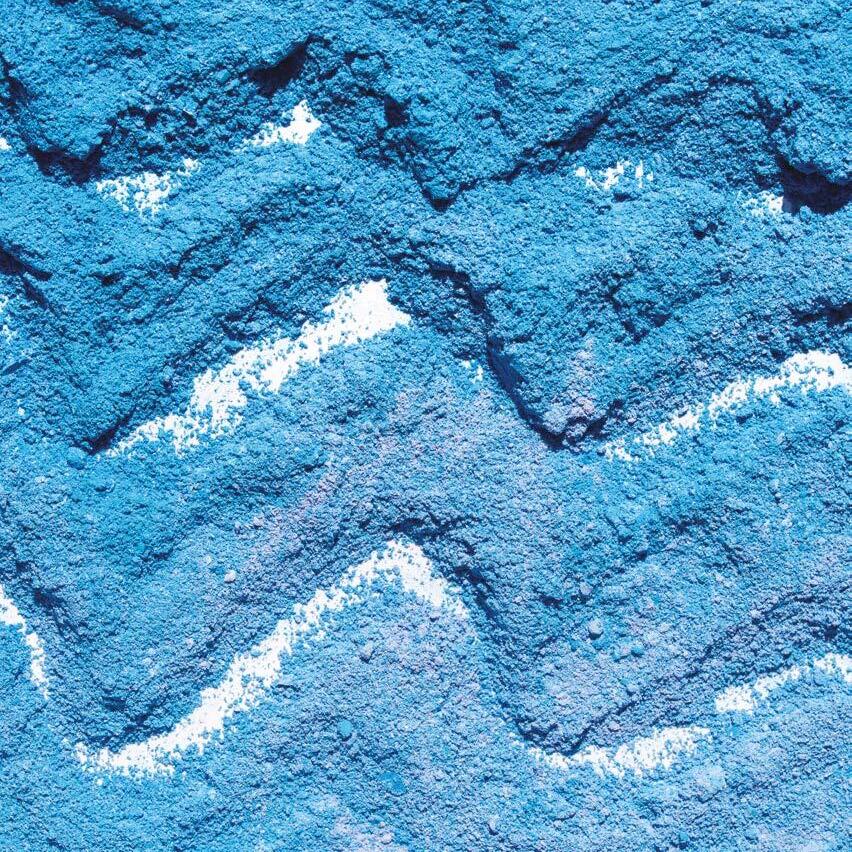
A quality that is never casual, but it is the result of a commitment to product development and industrial processes that have always been a guarantee of high resistance also in difficult enviroments

P o w e r i n s i d e d a d v a n c e d s o l u t i o n s f o r m e t a l s u r f a c e s t r e a t m e n t s i n c e 1 9 8 2


Eliminate Masking from Coating Operations with Lasers
Guillaume Jobin Laserax, Quebec – Canada gjobin@laserax.comLaserax has developed an innovative laser solution which can replace the manual masking operations of the areas that need to be protected before coating.
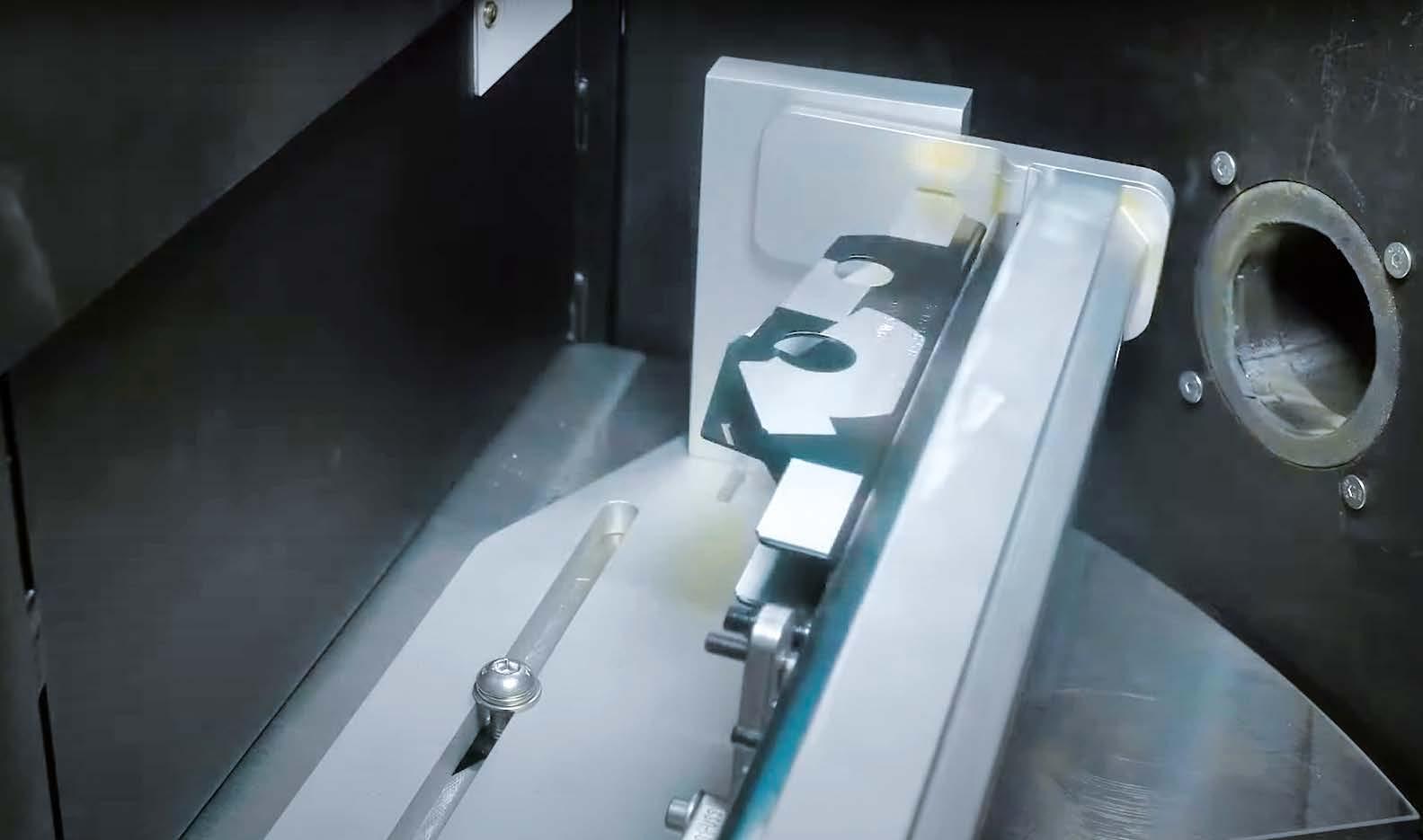
Masking is widely used in coating operations to cover or protect certain areas of a part that should not be coated. Common techniques include the application of specialized masking tapes, plugs, caps, and fixtures to protect specific areas from powder coating, e-coating, and other types of coatings. Masking can be a time-consuming process, especially for complex geometries. It is also expensive. Not only are masking consumables
costly, but they are typically applied manually, which is labor-intensive and can lead to inconsistent results due to manual errors. For many manufacturers, masking has become a necessary evil to ensure quality for sequential processes. For welding, surfaces must be free of contaminants that could penetrate the welds. For assembly, screws and bolts adhere better to bare metal surfaces than to coated surfaces.
Laser alternative to masking
There is another option. Laser coating removal1 is an innovative process that enables manufacturers to eliminate masking from coating operations. Instead of manually masking areas that need to be protected before coating, manufacturers can simply coat the entire part, and then use a laser to remove the coating from specific areas.
Lasers feature highly-efficient precision control, reducing errors and ensuring parts are ready for the next phase of production.
Laser coating removal: how it works
Coatings and metals have an ablation threshold2 — the temperature at which they vaporize into dust and fumes.
Lasers can be used to bring coatings to their ablation temperature to eject them from metal surfaces. Since the ablation threshold of metals is much higher than that of coatings, coatings can be removed without damaging
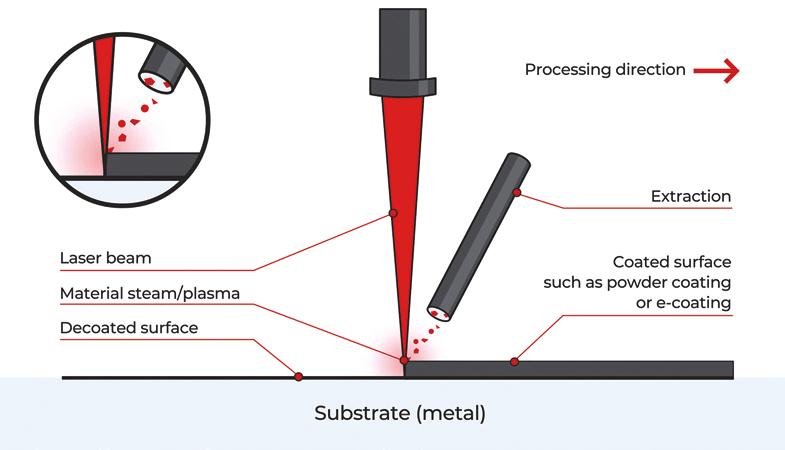
1 https://www.laserax.com/blog/coatings-removal 2 https://www.sciencedirect.com/topics/engineering/ ablation-threshold
the underlying metal. This process is done using a laser system, which generates laser beams that carry huge amounts of energy. A portion of this energy is absorbed by the surface, causing it to heat up.
The speed of laser coating removal is affected by the type of coating, its color, and its thickness. For example, thicker coatings will take a longer period of exposure to the laser or require multiple passes. Also, different types of coating have different ablation thresholds, and different colors absorb laser light at different ratios.
Manufacturers need a laser coating removal solution adapted to their needs. Depending on the operation and materials used, higherpowered lasers may be needed to accelerate the ablation process.
The benefits of laser coating removal
Laser coating removal offers several key benefits compared to traditional methods of masking.
Selective removal
Today’s laser systems provide micron precision. That enables them to remove coatings from specific areas without impacting other areas. For example, lasers can be used to remove coatings from areas to be used for welding or assembly without removing the coating from other areas.
With their smaller spot size, single-mode lasers are more precise than multi-mode lasers and are best suited when specific, repeatable shapes need to be cleaned, especially when working on more delicate or sensitive materials.
Speed of process
Lasers will significantly speed up the process by eliminating manual or machine masking. For manufacturers, this translates directly into more efficient throughput, efficiency, and productivity.
With their larger beam size, multi-mode lasers are ideal for processing larger areas. They can also reach higher laser power levels than single-mode lasers, allowing them to deliver more energy at once for faster coating removal.
No damage
Abrasives can cause damage to the bare metal surfaces, especially if it is soft or thin. Laser coating removal is a great alternative when abrasives create defects. As a noncontact process, it eliminates the risk of mechanical damage to the substrate. Unlike abrasive methods, it is possible to remove coatings without affecting surface roughness.
Improved adhesion
Laser cleaning can remove coatings and, at the same time, create a surface texture that increases friction. This improves the adherence of mechanical fasteners during assembly. It can also be used to improve the bonding of adhesives.
Consistent, repeatable processes
Masking is marred by imprecision, especially when handled manually. No matter how careful operators are, there will always be some level of deviation between applications.
Even experienced and well-trained operators suffer from errors3 due to the repetitive nature of masking. Lasers don’t make errors. They are computer programmed and are equipped with tools to adjust the laser process based on deviations.
Easier automation
Lasers are easier to automate than alternatives. Unlike abrasive blasting4, there are no dust contaminants to manage, little maintenance is needed, and the process is fully managed by a computer controller.
Lower operating costs
Compared to alternatives, lasers have significantly lower operating costs. Once they are programmed, they do not require operators and use no consumables. They are extremely low maintenance and are incredibly durable.
More environmentally friendly
Laser coating removal does not use harmful chemicals or generate hazardous waste. Pulsed laser systems also have a low power consumption and are extremely energy efficient, minimizing the environmental footprint. Lasers also work in a compact space, often reducing the space required for manufacturing and further reducing energy consumption.
3 https://www.assemblymag.com/articles/97027-top-5-human-errors-in-manufacturing 4 https://www.cdc.gov/niosh/topics/blasting/default.html
Enhanced safety
Today’s laser solutions are extremely safe. With a laser safety enclosure and a dust extraction system, operators do not need to wear PPEs near lasers. They also do not need to handle any dangerous chemicals or materials for use with the laser.
Limitations of laser coating removal
Laser coating removal offers attractive benefits. However, there are some challenges that manufacturers should know about in using lasers. Limitations include:
• Thicker coatings: laser coating removal works well with coatings that are 300 microns or less. But when coatings are thicker, the process may require several laser passes making it less efficient. The process can still be done, but it will take more time.
• Does not work for all coatings: clear coats and certain types of translucent coatings or varnishes do not absorb the laser’s light efficiently. They are simply bad candidates for laser coating removal.
• Heat generation: some materials may be sensitive to the heat from the laser, creating the potential for damage or discoloration.
• Fume filtration: a fume filtration and extraction system is needed in the laser enclosure to prevent toxic fumes from being released into the air. While lasers are low-maintenance equipment, they still require manual filter replacements.
• Large areas: if the coating that needs to be removed covers a large area, multiple lasers may be needed to meet cycle times. This quickly drives up costs and can negate the business case for purchasing a laser.
• Complex shapes or complete parts: laser coating removal may not be the best solution to clean complex shapes or complete parts, as adjusting the laser angle often may not be mechanically possible.
• Open space cleaning: performing laser coating removal in an open
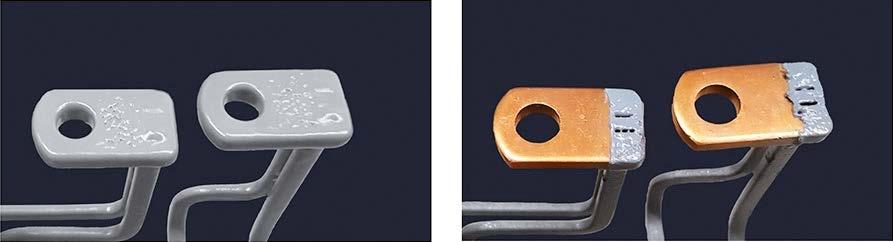
space is challenging because laser safety measures are difficult to apply. Typically, laser processing is done in a class-1 laser safety enclosure to contain the laser beam and its reflections.
An innovative solution for coating operations
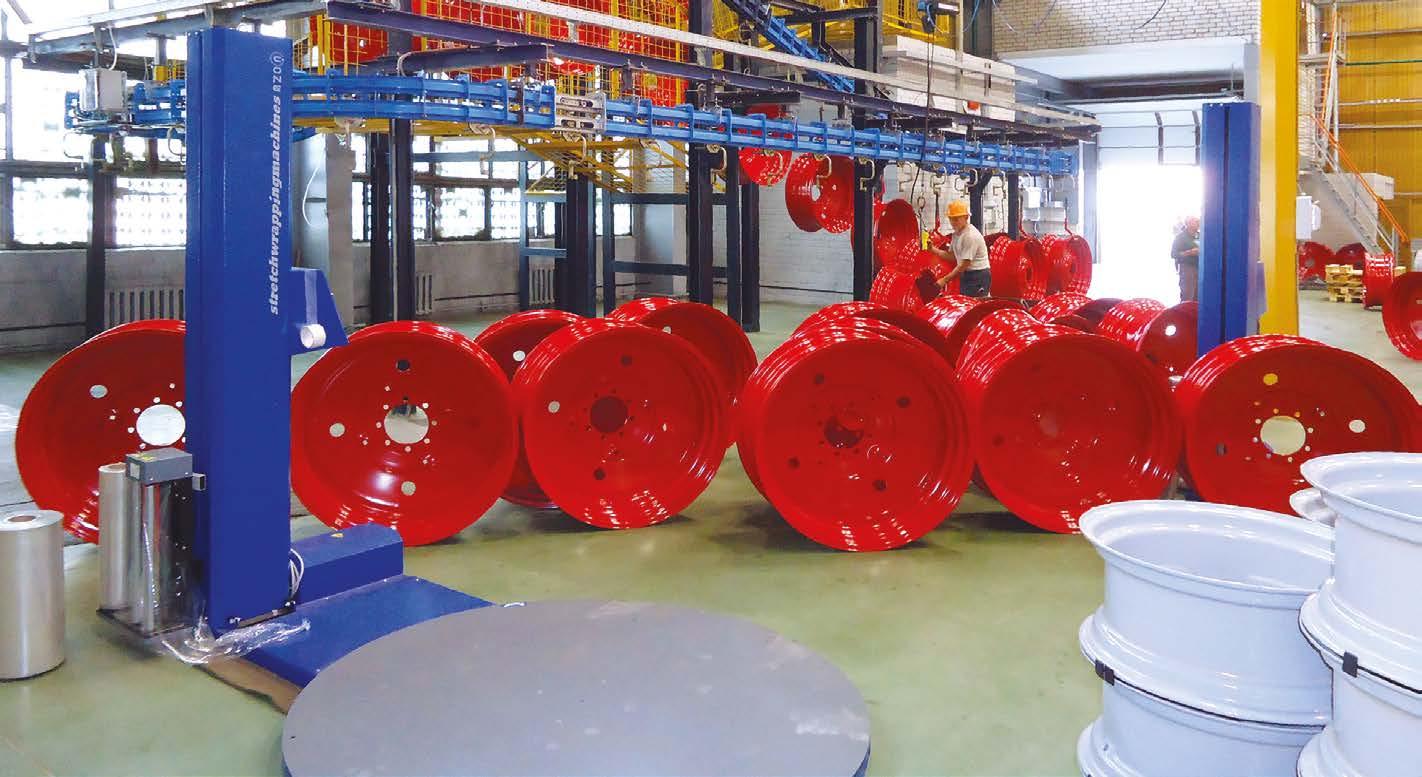
In today’s manufacturing environment where it’s increasingly difficult to recruit and retain a high-quality workforce, lasers can automate much of the masking and cleaning process to overcome labor shortages. Finding such efficiencies will be increasingly important for manufacturers. A recent report from Deloitte and the Manufacturing Institute reports that 2.1 million manufacturing jobs could go unfilled in the US by 20305
5 https://www2.deloitte.com/us/en/insights/industry/ manufacturing/manufacturing-industry-diversity.html
By embracing laser coating removal, manufacturers can unlock the potential for significant advancements in efficiency, quality, and productivity. Lasers represent an innovative way to manage coating operations and offer a promising future that paves the way for automation and improved quality control, delivering a competitive advantage in the marketplace.
About the author
Trained as a Mechanical Engineer, Guillaume Jobin has more than 10 years of experience in automation and control. He is Supervisor of Application Specialists at Laserax, where he oversees the team that analyzes clients’ needs and that designs the right laser solutions for them. He is also a member of the Corporate Sustainability Committee.
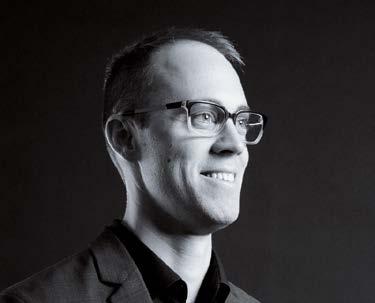
GENERAL INDUSTRY liquid or powder spray applications
70 years of experience and innovation in surface finishing lines

The Symbiosis of Industry and Design in the Exhibition “Red in Italy - I Colori del Rosso nel Design Italiano”
Edited by Hill + Knowlton Strategies for Campari GroupThe Italian Ministry of Enterprises and Made in Italy presented “Red in Italy - I Colori del Rosso nel Design Italiano”, an exhibition project devoted to red throughout the history of Italian design conceived by Campari Group and sponsored by Altagamma.
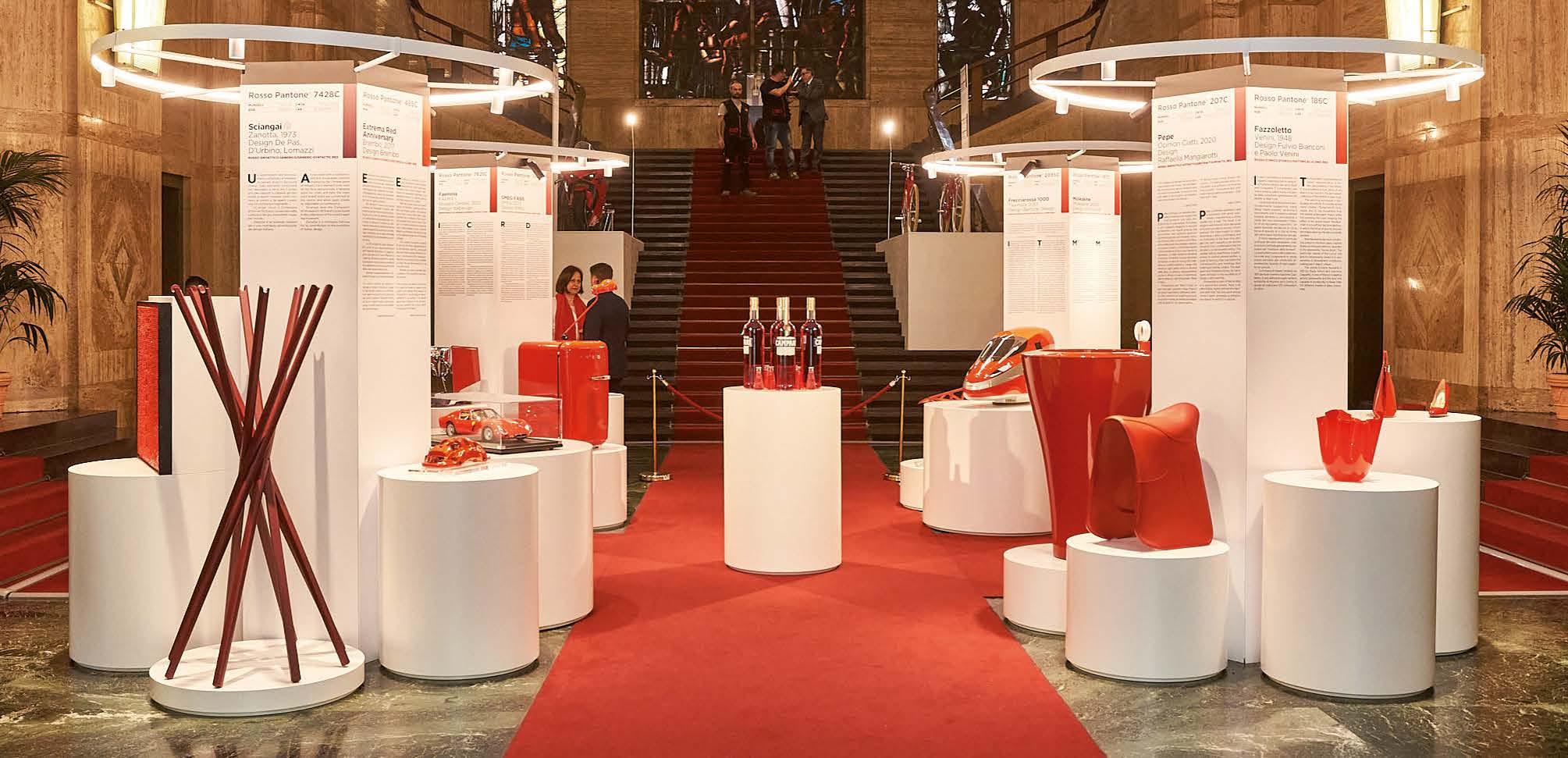
The exhibition “Red in Italy - I Colori del Rosso nel Design Italiano” (i.e. Red Colours in Italian Design) was inaugurated at Palazzo Piacentini, the headquarters of the Ministry of Enterprises and Made in Italy in Rome, on 31 May. It was conceived by Campari Group, one of the major international players in the spirits sector, and sponsored by Altagamma, the foundation established in 1992 to bring together the best companies from the high cultural and creative industry that strive to promote Italy’s excellence, uniqueness, and lifestyle around the world. This project, designed and curated by Francesca Valan with the staging by FG Confalonieri, is aimed at exploring all things red (whose history and evolution was analysed by an article1 in the previous issue of ipcm®, Ed.) through the display of a 1https://www.ipcm.it/en/open/ipcm/2023/81/178-180.aspx
series of objects that symbolise Italian design and spur many possible aesthetic and cultural comparisons. “This event and the inauguration of the “Red in Italy” exhibition are particularly significant for Italy, at a time when our country has shown more growth than many other Western economies. And the credit goes to our companies,” said Minister of Enterprises and Made in Italy Adolfo Urso during the opening ceremony. “Today, we can see many examples of Italian excellence here, from food to fashion, from design to cars, recognised worldwide for their high quality and value. We would like to thank Altagamma and Campari Group for this important project that contributes to spreading Italianness and our products of excellence around the world.”
“The “Red in Italy” exhibition weaves a common thread among the most
iconic objects manufactured by the numerous Altagamma member companies that embody the Italian lifestyle and our country’s creative and aesthetic skills,” stated Stefania Lazzaroni, General Manager of Altagamma. “Altagamma has been promoting Italian excellence for over thirty years now, representing a sector worth 144 billion Euros, around 7.4% of Italy’s GDP. We feel honoured to be at the side of the Ministry of Enterprises and Made in Italy and of Campari Group, one our member companies, for this high cultural-value project involving so many well-known design, automotive, and fashion brands. This is a virtuous example of institutional cross-sectoral cooperation, a distinctive trait of our foundation, and of talent enhancement.”
“After a début in Brussels in 2019, we are proud to have brought “Red in Italy” to Italy, where it all began, and we would like to thank the Ministry of Enterprises and Made in Italy and the Altagamma foundation for believing in this project,” said Sascha Cumia, the Managing Director of the Southern Europe, Middle East, and Africa division of Campari Group.
“This exhibition confirms Campari’s prominent role as an Italian company of excellence appreciated worldwide, among the most recognisable symbols of our lifestyle. It also emphasises the role of our Group as an active participant in the promotion of culture in Italy and abroad.”
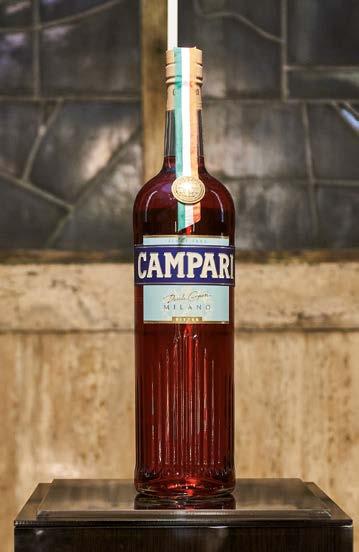
The exhibition starts with Campari’s iconic red, which inspires a reflection on the red hues that have characterised civilisations on a global level, to tell the story of the creations of some of the most famous designers of the 20th and 21st centuries, who have contributed to the symbolic construction of Italy’s image abroad by interweaving design,
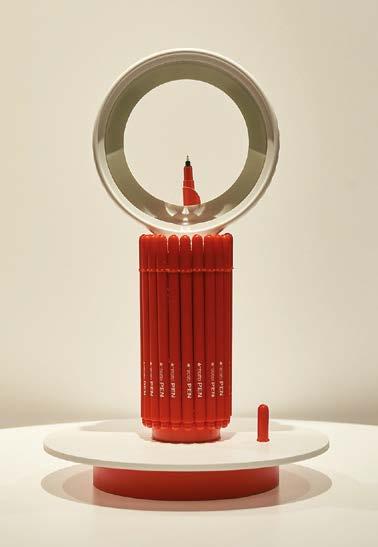
art, culture, and sociology – as did the rich and surprising history of this colour, which has evolved together with the expression of Italianness all over the world. The exhibition thus explores several Italian designer objects, guiding the visitor along a true immersion in colour at the discovery of the many Italian products of excellence characterised by red shades. In addition to the unmistakable Campari red, present with a limited-edition bottle created especially for the exhibition, other iconic reds are on display here, including those of companies Artemide, Brembo, Driade, Ducati, F.I.L.A. Fabbrica Italiana Lapis ed Affini, Ferrari, FontanaArte, Orsoni Venezia 1888, Gruppo Cimbali, Gufram, Magis, Moleskine, Alessi, Museo Kartell, Opinion Ciatti, Poltrona Frau, Rossignoli, Salvatore Ferragamo, Serralunga, Smeg, Stilnovo brand of Linea Light, Tecno, Trenitalia, Venini, and Zanotta, as well as Panzeri as the technical sponsor for the exhibition lighting system.
The “Red in Italy” exhibition created by Campari made its début in Brussels in September 2019, with the aim of promoting the iconic Italian brands that have contributed to the symbolic construction of Italy’s image in the world. Curated by Valan and FG Confalonieri with the coordination of Galleria Campari, this project was inspired by the success of the exhibition “I colori del Rosso” (i.e. The Colours of Red), organised at the Galleria Campari spaces in Sesto San Giovanni (Milan) in 2015 on the occasion of Expo Milano.
The Rome edition of “Red in Italy”, hosted by the Ministry of Enterprises and Made in Italy, was open to the public on Saturdays 3, 10, 17, and 24
June 2023.
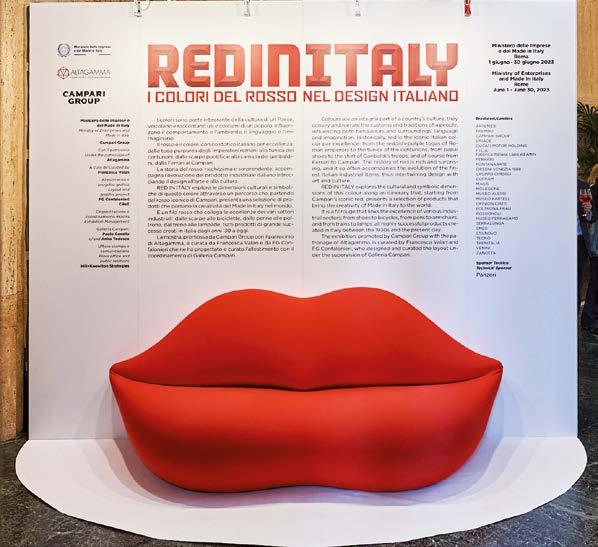
CEB Invests in Flexibility and Repeatability Through Robots Capable of Self-Generating Powder Coating Programmes
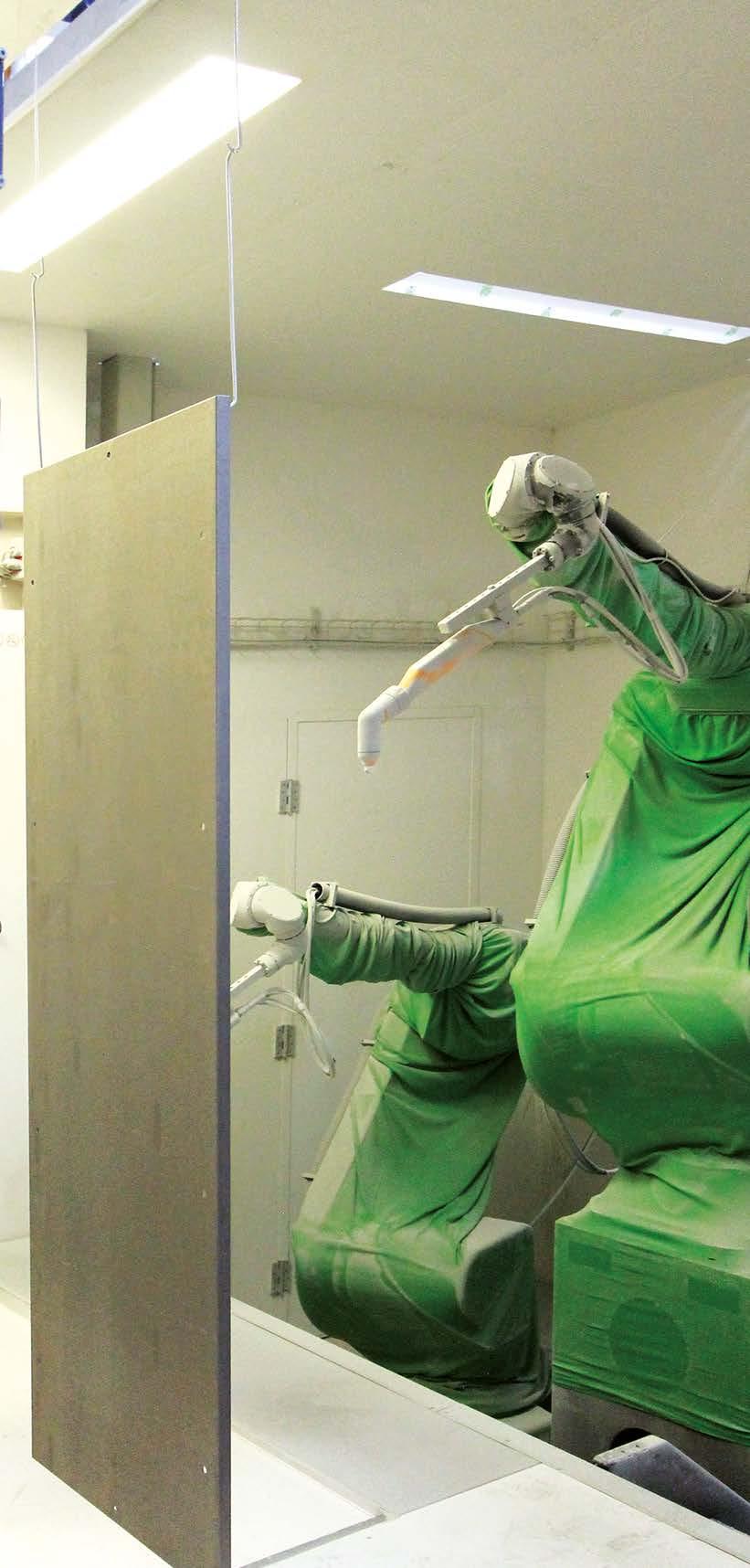
During the most difficult years of the economic crisis, CEB has distinguished itself by investing in improving the quality and speed of its production lines. Seven years after the installation of a new powder coating plant, it further enhanced its performance with two CMA Robotics robots capable of self-generating three-dimensional coating programmes through the AXPS-BOX system.
CEB S.p.A. is a company specialising in the processing of iron and stainless steel sheet parts for the production of electrical equipment such as cabinets, enclosures, and control desks, founded in 1980 in Montebello Vicentino (Vicenza, Italy). Its professional experience, technical skills, flexibility, and in-depth knowledge of manufacturing dynamics and market needs have made it highly competitive through the offer of a diverse and complete range of solutions to customers all over Italy, supplying both mass-produced and customised units to be installed indoors and outdoors and able to meet any requirement in the metallurgical, metalworking, and food industries. In addition to guaranteeing excellent safety and resistance properties to protect electrical circuits in the long term, CEB’s cabinets are also required to have finishes with a high aesthetic level and matching the main colours of the structures in which they are located. This is why in 2016, the company equipped itself with a modern powder coating plant
designed and built by Imel to cope with growing market demands, which was the subject of an in-depth article1. In addition, to further improve the quality of its offer and its lead times, it has recently installed two GR-680 articulated robots with their corresponding software package and the exclusive AXPS-BOX system, which uses three-dimensional scanning technology to allow identifying not only the type of workpiece entering the booth but also its incline degree and its position and adapting the automated coating programme and its trajectory accordingly.
Upgrading the powder coating plant
An operator hangs the parts onto the 31 load bars (with a maximum capacity of 5,500 x 1,000 x 2,200 millimetres and 500 kilograms) of the Futura Convogliatori Aerei two-rail overhead conveyor (with a speed of 2 metres per minute) so as to facilitate their draining following the spray pre-treatment process performed in a 5-stage tunnel (alkaline
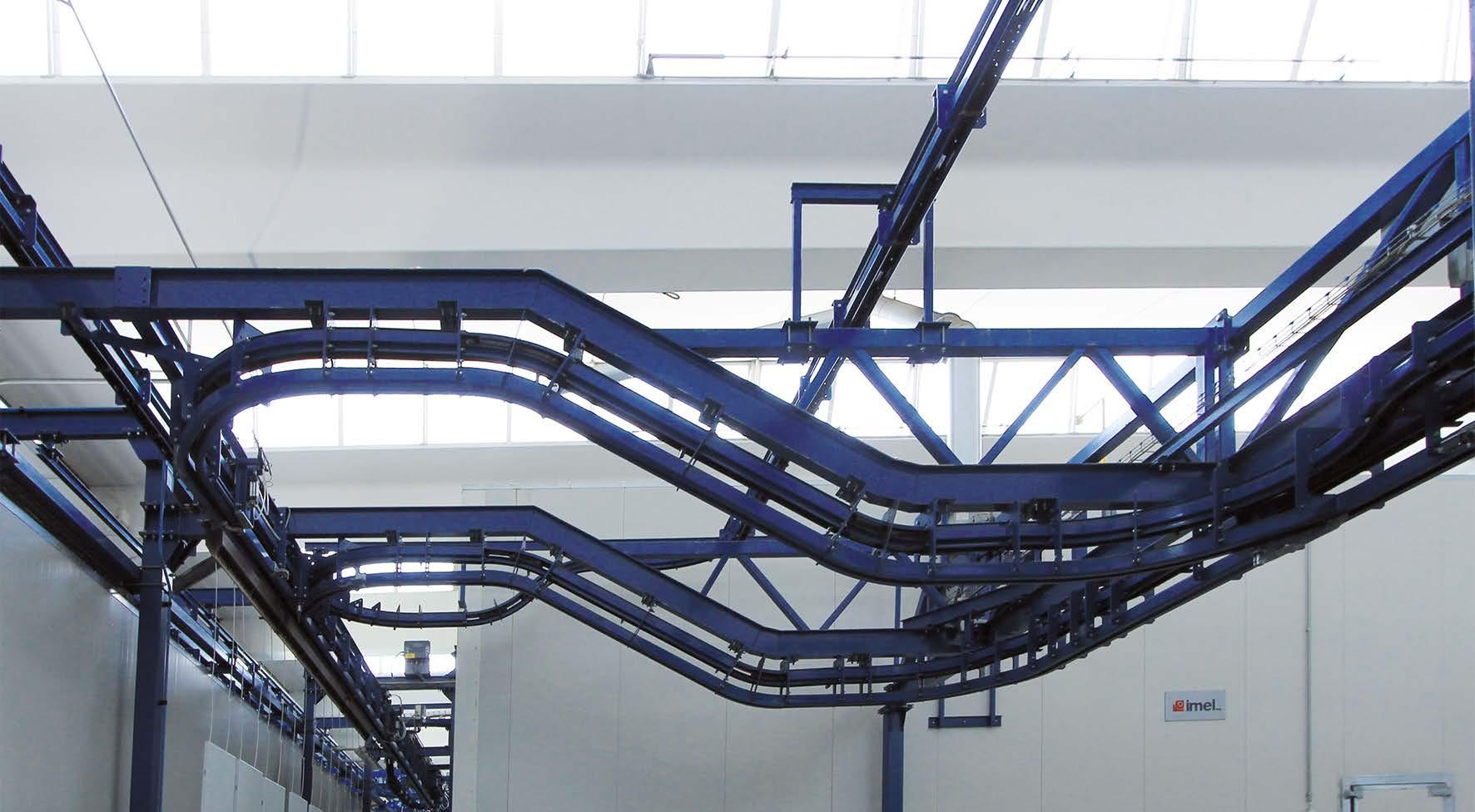
1 “A system for applying powders that guarantees high productivity, paint savings, and consistent quality for large components, M. Fumagalli, in ipcm®_International Paint&Coating Magazine no. 39.
degreasing at 55 °C, rinsing with mains water, rinsing with demineralised water, passivation with Chemetall’s nanotechnology product Oxsilan®, and final rinsing with demineralised water) and before entering the drying oven at 110° C.
Designed, built, and installed by Imel, the coating system is equipped with 2 Gema MagicCylinder® EquiFlow automatic booths with their own reciprocators for rapid colour change operations. These apply epoxy and polyester powder paints to the sheets that make up CEB’s cabinets, intended for outdoor use and therefore subject to harsh environmental conditions. However, due to their complex geometry, manual pre-processing used to be often necessary in the past. Indeed, this coating plant and all other recent technology upgrades have enabled CEB to increase its production capacity: this has also translated into a growing demand for complex-shaped enclosures, panels, and boxed parts with multiple cavities, curves, and angles. The booth applying different tints is equipped with quick colour change features and Venturi-technology injectors, whereas the single-colour application booth is equipped with OptiSpray AP 01 paint feed pumps.
The two articulated robots from CMA Robotics’ GR-680 series were recently installed on the latter.
“The coating process of these components starts with a pre-finishing phase on their inner surfaces. This was carried out by two specialised operators, who, however, after a few hours of work, experienced a physiological drop in performance, either decreasing the speed of their movements or increasing the distance between the spray gun and the workpieces. However, we want our coating quality level to be high and, above all, consistent. Therefore, this caused delays for the entire production, as well as wasting materials. We talked with Gema and Imel about the issue and they suggested we turn to an articulated robot manufacturer to find the best solution for our requirements,” says CEB owner Silvano Biasin.
Robots capable of self-generating coating programmes
The company, therefore, sent some samples to the Pavia di Udine (Udine, Italy) site of CMA Robotics, a manufacturer of automated paint
solutions, which performed different tests to better understand CEB’s needs. Two 6-axis electronically controlled articulated robots capable of self-generating three-dimensional coating programmes through the AXPS-BOX system were thus installed in June 2022. Like the entire range produced by CMA Robotics, the GR-680 robots are designed to spray both powder and liquid paints on metal, wood, and plastic surfaces and they are certified to operate in ATEX areas by a specialised external body. Another peculiarity is the special configuration of their wrists, which, by rotating each axis through 360°, makes it easy to reach any point on the workpiece to be coated.

Each robot can mount several guns or rotary bells at the same time and integrate perfectly with any airflow and paint control device through the internal control system, which has extremely sophisticated yet user-friendly software and diagnostic tools. “The 2D self-generation of coating programmes is a well-established feature for treating doors, windows, and frames, but the design of a 3D system for coating boxed profiles was also new to us. At CEB, the components entering the

coating booths are hung onto the conveyor with varying incline degrees depending on their size and weight: therefore, a normal scan would not have allowed the robots to correctly carry out the programme assigned to each type of part,” explains Marco Zanor, sales director at CMA Robotics. “However, we were not discouraged at all: after some trials, we managed to develop a tailor-made solution to meet all CEB’s needs. The 3D part-scanning device placed at the booths’ entrance does not only detect the shape of the incoming component but also its incline degree and its position. The AXPS-BOX system then uses pre-set rules to automatically self-generate the paint programme that ensures the coating is applied evenly to all its interior and exterior surfaces.”

In this way, also following the further coating operations occurring inside the Gema booths,
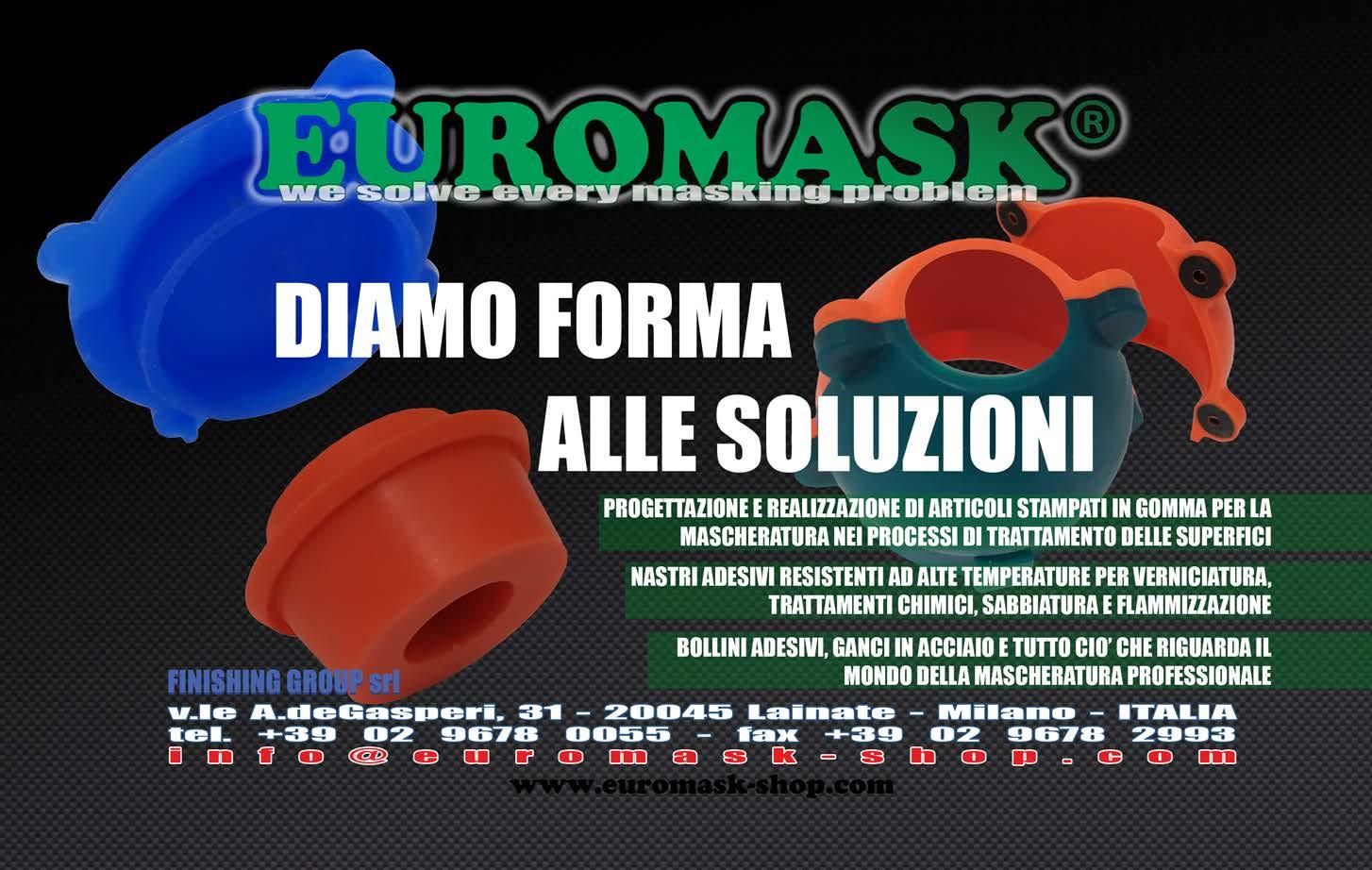
all products leave the system with a homogeneous coating layer and can be taken to the curing oven, where they dwell for 25 minutes at 180 °C, and then to a storage buffer for cooling at room temperature. Finally, the operators unload the parts, which are ready to be assembled, packed, and shipped.

Consistent and repeatable coating even with complex geometries
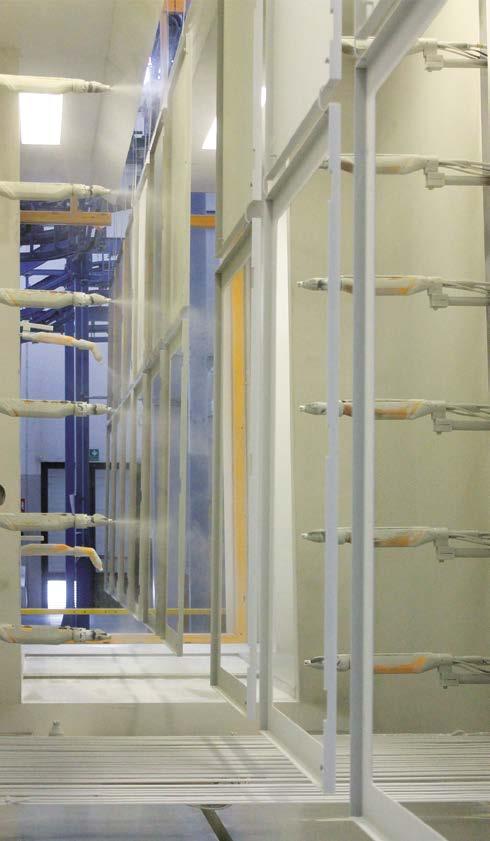
With this investment, CEB has therefore improved its production flow and the quality of its coated components. Previously, it was necessary to stop the chain or carry out post-finishing operations after assembly. “Now, our production rate is constant and the applied coating film is more uniform even on complex-shaped parts. As mentioned, the physiological fatigue inherent in activities like manual spraying makes it difficult for operators to faithfully repeat the exact same gesture for
extended periods of time. The two robots have enabled us to maintain a speed of 17 load bars per hour with components that can reach up to 2.20 metres in height. In addition, the operators previously employed for this coating phase are now assigned to the assembly and packaging one. This means that we have not only speeded up our coating operation but rather our entire production flow,” notes Matteo Biasin, the production manager of CEB.
“We did not know the full potential of this new system, but we decided to rely on the professionalism of CMA Robotics and this paid off. In your last article, I stated that the productivity of our new coating plant was still difficult to assess as it had only been operating for a while, but that some aspects, such as powder saving and coating speed and efficiency had already clearly improved. The same applies to this new
investment: our CMA robots have only been fully operational since the end of September 2022, but we have already seen an increase in the quality of the applied film and a reduction in the resources used. In fact, together with Imel, we are already studying how to lengthen the conveyor chain to create more storage buffers and expand the loading and unloading area. Imel’s technicians just helped us modify our line to accommodate the two robots and proved to be willing to listen to our needs and quickly implement the most appropriate solutions. This new upgrade could enable us to further increase the profitability of our entire powder coating plant,” says Silvano Biasin with satisfaction.
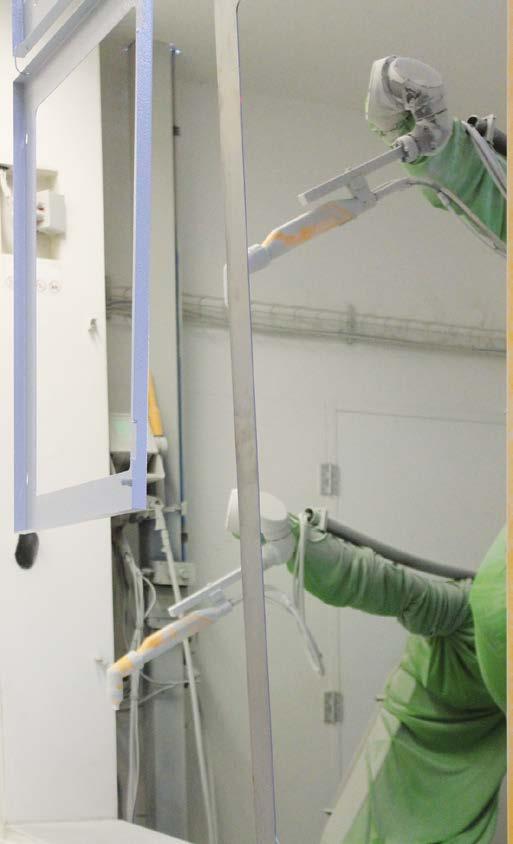






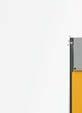


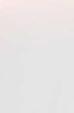

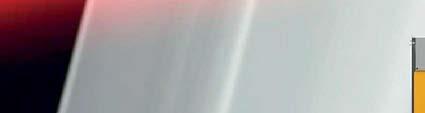
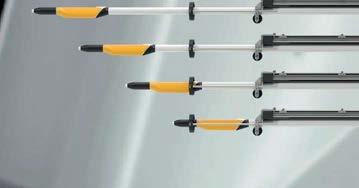
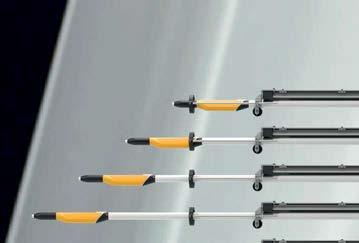

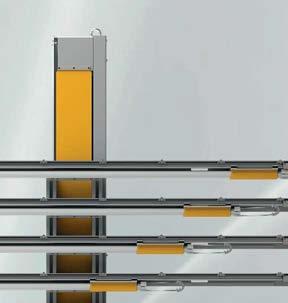




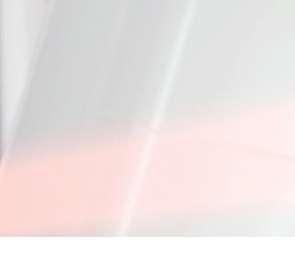


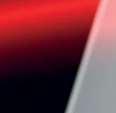


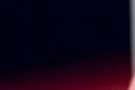









Seven Quality Tests for Coating Processes According to Argos ST

In order to verify the high quality of the coating processes it carries out, the Foresi plant of the Argos ST Group can generate measurement reports at its customers’ request, using three main methods: cross-hatch test for checking adhesion, thickness measurement, and gloss measurement. Four additional performance assessments can only be performed by certified laboratories, namely the continuous and alternating salt spray tests, the prolonged immersion test, and the accelerated ageing test.
Checking the quality of its coating processes at the request of customers. This is one of the activities of the Argos ST Group’s Foresi plant, a leading company in the field of surface treatments, including three types of industrial coating processes: cataphoresis (or e-coating), powder coating, and liquid coating, also with high-temperature liquids. These treatments are instrumental in preventing corrosion of materials such as iron, steel, and other alloys while ensuring greater resistance; specifically, coating with high-temperature liquids enables any metal part subsequently subjected to particularly high temperatures to maintain a good seal.
Measuring the quality of coating processes: Foresi’s tests
There are three types of checks that Foresi adopts to assess in-house the quality of its coating processes: cross-hatch test for checking adhesion, thickness measurement, and gloss measurement.
• Cross-hatch adhesion test: a method that uses a special comb tool and a standardised tape to determine the peel strength of paints and coatings with respect to the substrates by creating a right-angled grid on their surfaces. More precisely, the grid incisions performed must be the same distance apart both vertically and horizontally, reaching down to the substrate. By applying the adhesive tape over the entire incision area and then vigorously removing it, it is possible to visually determine the outcome of the test. If no squares have detached from the grid, if the detachment is limited to 5% of the area and to the intersections of the cuts, or if the paint has detached along the edges of the cuts and at the intersections in 5-15% of the area, the coating process carried out is deemed successful. On the other hand, if the paint has peeled off along the edges of
the cuts or in the squares in more than 15% of the area, depending on the extent of the damage, the surface needs to be scraped partially or totally before re-coating.
• Thickness assessment: the coating’s thickness can be measured on both smooth and rough surfaces using special instrumentation.
• Gloss measurement by reflectometer (BYK-Gardner Micro-TRIGloss): for a coating process to be considered of good quality, it must necessarily guarantee constant and uniform gloss, whatever the treated surface. Especially in the case of multi-component products, a uniform gloss degree is proof of the high quality of the treatment and, consequently, of the end material obtained. In order to measure gloss objectively, a glossmeter is therefore used, which can be employed on paints, plastics, and even mirror-like metals.
Four other useful tests for verifying the quality of treatments
Four additional assessments can be performed by certified laboratories to check the quality of the coating treatments performed: the salt spray test to monitor corrosion resistance, the cyclic corrosion tests, the adhesion test carried out after 24-48 hour water immersion, and the accelerated ageing test.
•The salt spray test is a standardised test to check how well a surface coating protects the substrate from corrosion. Corrosion resistance tests on cataphoresis layers last less than 500 hours, whereas test times for combined cataphoresis and powder coating applications extend beyond 500 hours. The test is carried out inside a chamber where the test salt solution (5% NaCl) is atomised at 35 °C; the resulting mist creates a particularly corrosive environment, which allows measuring the degree of corrosion of the sample by the end of the test. During the test, some partial outcomes can be recorded to monitor the progress of the corrosion process.
• A specific method called alternating salt spray test is similar to the one just described, but it is based on the alternation of phases when the material is exposed to salt spray and phases of rest, simulating the stress to which the treated part is going to be subjected over time. Such alternation can be programmed by the climatic chamber to perform several cycles with a different duration.
• The adhesion test is carried out by soaking the treated part in water for 24-48 hours. After this time frame, the paint’s adhesion degree can be assessed.
• Finally, the accelerated weathering test makes it possible to reproduce – in the laboratory and within a very limited time frame – the damage
Painting excellence for every surface
Bringing your surface to perfection. Verind offers painting solutions from manual to automatic application, high-quality and easy to integrate.
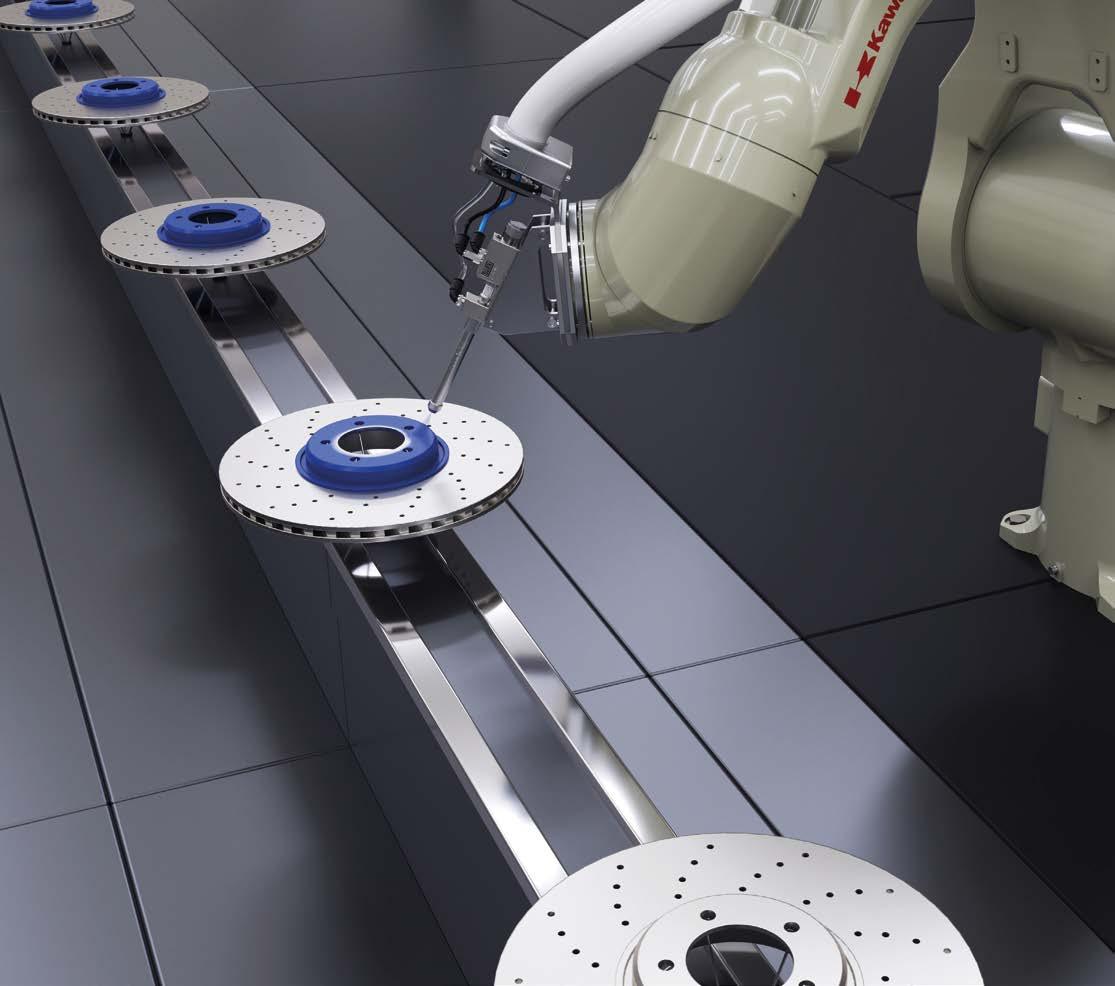

that the material would suffer if exposed to sunlight, rain, and dew for several months or years. Special UV lamps are used, so that the materials to be tested are subjected not only to high and controlled temperatures, but also to moisture.
“Coating processes undoubtedly contribute to excellent aesthetics, but they also play an important functional role,” commented Guido Ghilardi, the managing director of Argos ST’s plants in Gonzaga e Borgaro Torinese. “Although we are not a laboratory that can carry out official tests and issue certifications, we do perform tests at the request of our customers at our premises, which enable us to monitor the effectiveness of our coating processes. This is a very important activity for us, because it allows us to guarantee the high quality of our work and, if necessary, to take any corrective actions.”
About Argos Surface Technologies

Created by the Gradiente II private equity fund, the new Argos Surface Technologies Group was born in 2020 from the merger of major players in the metal surface treatments and coatings industry, with the aim of creating a leadership position in the sector. In 2020, the Group started with the acquisitions of Argos, Impreglon Italia and Aalberts ST. In 2021, it acquired the Emilia-based TSM (today Argos TSM) and Lualma Anodica (today Argos Lualma) and in 2022 the Bergamo-based TEC.RI.MET Srl, the Mantua-based FORESI S.p.A., and the Turin-based Rotostatic. The Group now boasts nine plants: Gonzaga (Mantova), Origgio (Varese), Cambiago (Milan), Calcio (Bergamo), Opera (Milano), Monteveglio (Bologna), Imola (Bologna), Minerbio (Bologna), and Borgaro Torinese (Torino), with more than 300 employees and a turnover in excess of €50 million.

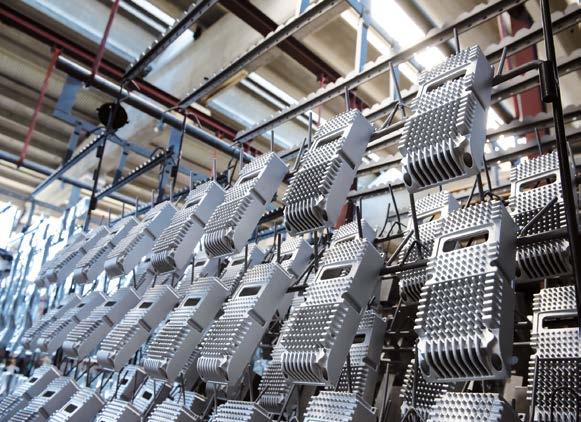
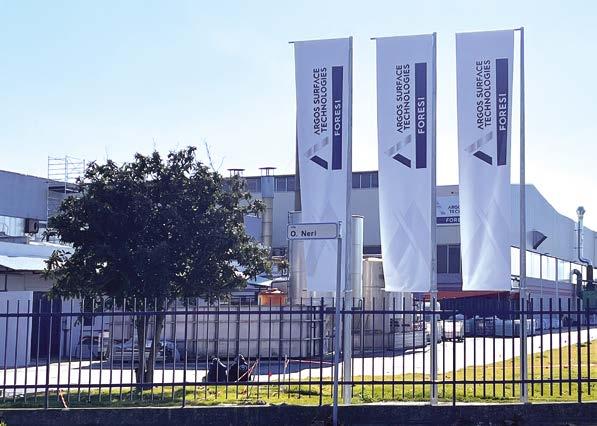
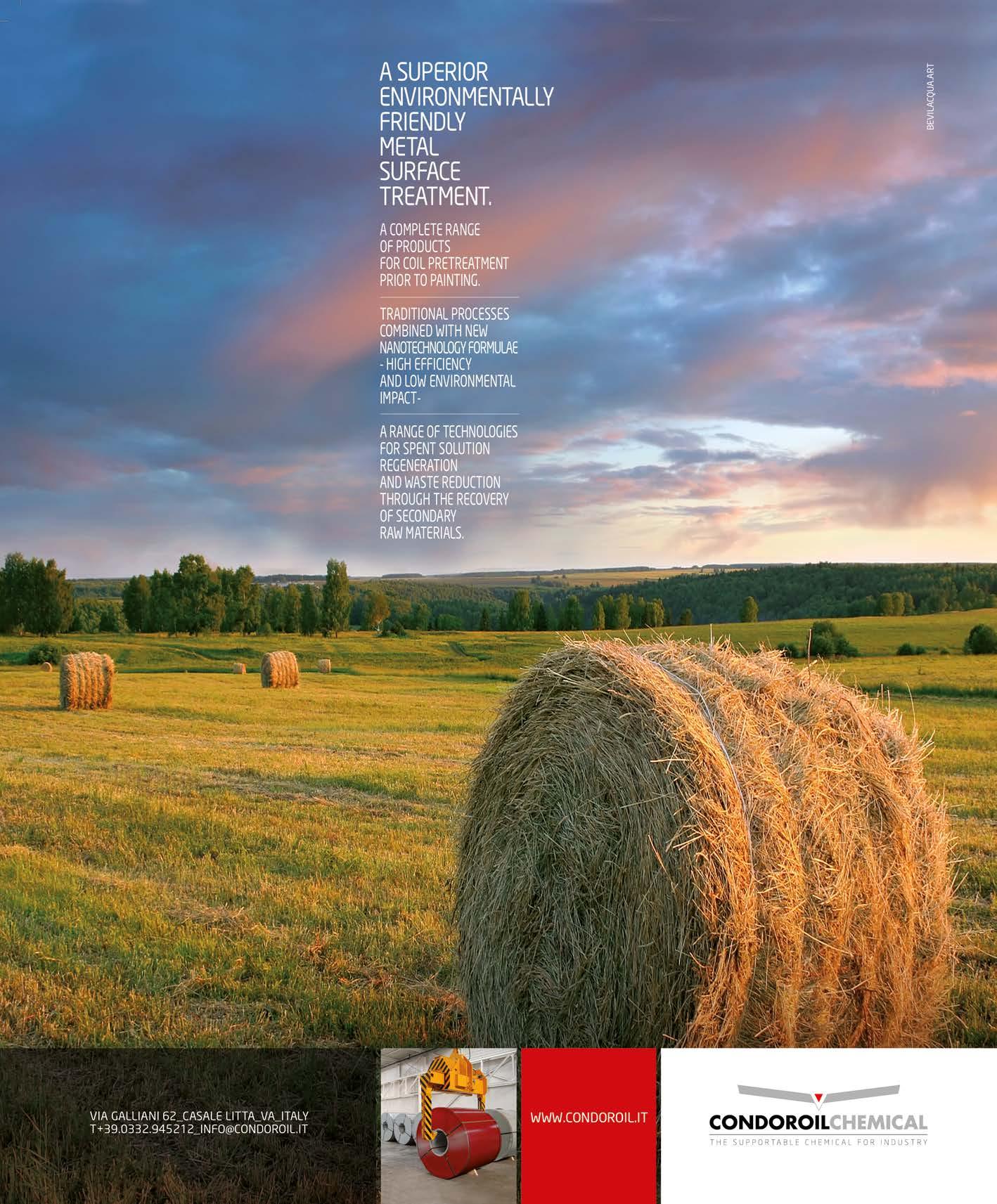
FOCUS ON TECHNOLOGY
T&G: The Loyalisation of the Coating Plant Engineering Partner to Support the Company’s Growth
Alessia Venturi ipcm®A coating contractor needs three things to grow: entrepreneurial spirit, specialisation in a few niches, and the right plant engineering partner. In its twenty-year history, T&G (Castione di Loria) has managed to combine all of them, in particular relying on Euroimpianti’s expertise for its equipment.
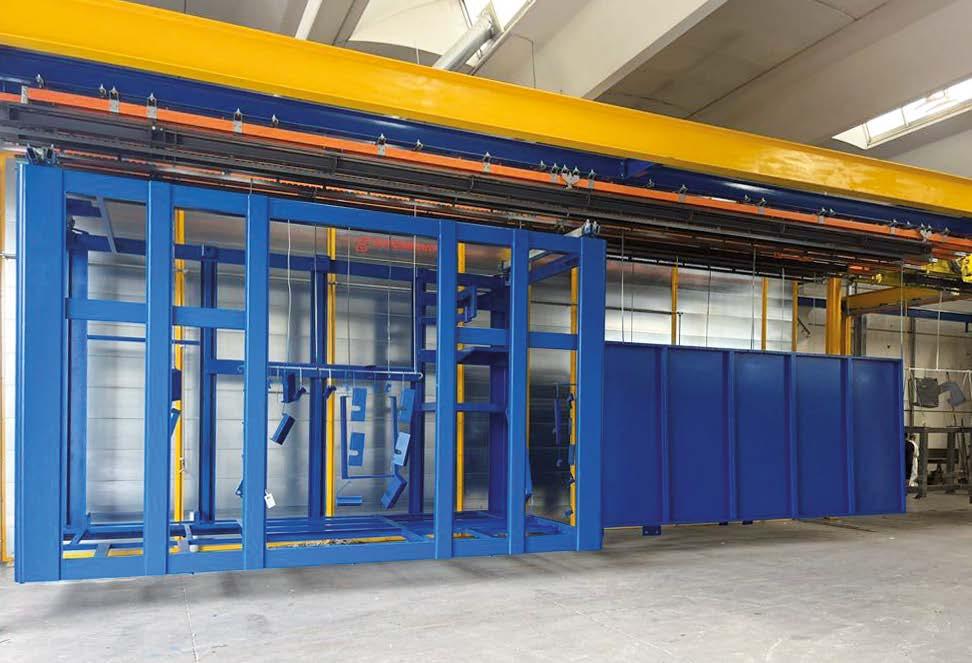
An entrepreneurial spirit is a mindset focusing on change, innovation, and continuous improvement. Audacity and risk are synonymous with entrepreneurship. Having such an attitude means taking responsibility (and therefore the risk) for one’s ideas
and choices and for the effects they will have on one’s business. Not everyone has it – not even many entrepreneurs. But there are also people who, on the contrary, have entrepreneurial spirit to spare, such as partners Enrico Troisi and Luca Girolimetto, two friends and
colleagues who founded T&G Verniciatura Industriale in 2002 after an experience as coaters at another local company.
In twenty years, Enrico and Luca have never shied away from the challenges posed by the market and they have made many bold investments to build what T&G is today: a leading liquid and powder coating contractor in the machine tool and automation sector, with three factory halls in Castione di Loria (Treviso, Italy), three powder coating plants, several liquid painting booths for the application of corrosion protection products, an automatic shot blasting machine, and a manual sandblasting cabin.
In addition to the resourcefulness of its two founding partners, T&G achieved such success also thanks to its ongoing partnership with coating plant engineering company Euroimpianti and the total trust placed in its owner, Gianluca Baruffaldi, who has always supported T&G’s growth by offering advice and consultancy on all things paints. With time, this partnership has led T&G to install the complete range of industrial coating equipment manufactured by Euroimpianti: first the Eurocar system, then the Euro90 automatic plant with a one-rail conveyor, and finally, a few months ago, a “hybrid” Komby system with an automatic load bar drive unit designed by Railtechniek. “Each of the modular lines in Euroimpianti’s range was well suited to meet our growth needs at a particular point in our journey,” notes Enrico Troisi. “Guided by Gianluca’s experience, we have chosen the most suitable system from time to time, modifying it or hybridising it to personalise it and adapt it to our production flow. Currently, our equipment enables us to meet a multitude of coating requirements from the mechanics and automation sectors, which are very flourishing in our area (around the city of Galliera Veneta, Editor’s note), with many manufacturers of heavy machinery, from drill rigs to pasta production lines, relying on contractors to paint their components.”
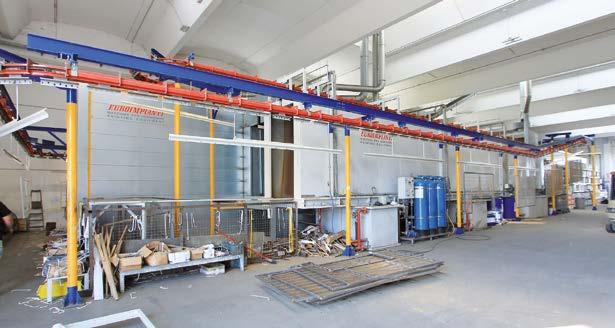

The history of T&G
Founded in 2002 and operational since March 2003, for the first five years T&G only offered liquid coating services in a small, 400 m2-wide factory. In 2008, the implementation of a powder coating process marked a turning point and the company moved to its current site in Castione di Loria.
“My encounter with Gianluca Baruffaldi and the beginning of our powder coating-oriented partnership dates back to that year, with the purchase of our first plant, Eurocar 5, capable of coating parts up to 10 metres long. This system enabled us to powder-coat both smaller and larger components, thus completing our offer in addition to the application of liquid products, especially corrosion protection ones. In 2008, we also purchased a manual sandblasting cabin to further improve the quality degree of both liquid and
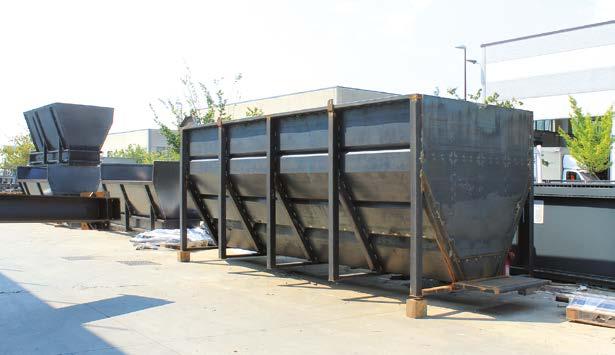
powder coatings through mechanical pre-treatment.
“In 2013, we decided to invest further to expand our range of surface treatment services,” adds Luca Girolimetto. “In two years, we bought a new building next to the first one to accommodate an OMSG automatic shot blasting plant, a Tunnelblast 3000x3000 system featuring a manual touch-up booth, 16 turbines, inverters, and a digital control panel. In 2016, we decided to move our static liquid coating booths to a third site and upgrade them with additional booths with a wall filtration unit, an internal air intake plenum, and an exhaust air extraction and purification system. At the same time, we revamped the manual sandblasting cabin, equipping it among other things with an opening roof, to enable the use of our overhead crane for handling the increasingly heavier products we were treating.”

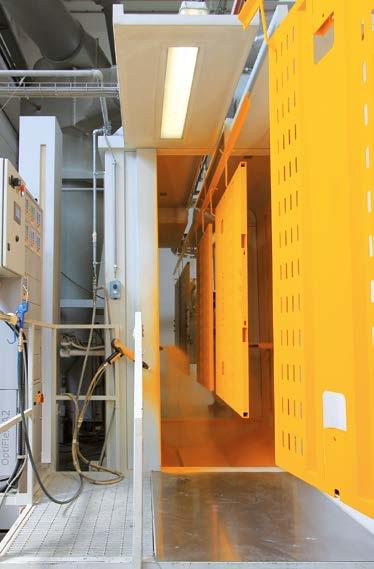
“We have grown together with our customers and their surface treatment needs,” says Enrico Troisi. “What changed was above all the size of the workpieces. At one point, the Eurocar plant was no longer sufficient. Therefore, we invested in an automatic Euro90 system, which enabled us to quickly coat ever-larger batches of small and mediumsized workpieces. Finally, in 2022, we installed a third powder coating plant for very large-sized components, as the maximum part dimension that could be handled by the Eurocar one was beginning to limit our further growth. We could have diverted these volumes to our liquid application plants, of course, but our business strategy was to drive our
customers as much as possible towards powders, limiting liquid coating to corrosion protection systems only.”
Three plants for three different coating requirements
Eurocar is the plant in Euroimpianti’s range for the semi-automatic industrial coating of large metal parts that, due to their size, are difficult to handle with a traditional overhead one-rail conveyor. In fact, it makes use of a special step-by-step roller handling all types of workpieces and consisting of two one-rail tracks connected by a load bar system, which shifts forward automatically through steps that are specifically timed for the various processing phases throughout the coating cycle. “Eurocar is available in various sizes depending on the maximum length of the parts to be treated. We chose model 5, handling components up to 10 m in length,” says Enrico Troisi. “However, after installing the Komby plant, we revamped the Eurocar one by replacing the booth, compacting the line, and downsizing it to a size 3, i.e. with a maximum piece length of 6 metres. As the new Komby machine can coat large and very large parts, we could turn the Eurocar one into a medium-sized, faster plant performing frequent colour changes.
Euro 90 is the plant for the industrial powder coating of semi-finished and finished metal parts fully automatically, built with standardised components for fast delivery and excellent value for money. The machine installed by T&G can accommodate a maximum part size of
3000 x 2000 x 80 mm and it is equipped with a one-rail conveyor, a chemical pre-treatment tunnel, a demineralisation plant, an automatic application booth, and drying and curing ovens. “This investment allowed us to increase our number of customers by enabling us to coat long series of parts quickly and efficiently,” indicates Luca Girolimetto. “We will soon add a second automatic in-line booth, to devote one to our standard colour and one to quick colour changes.”
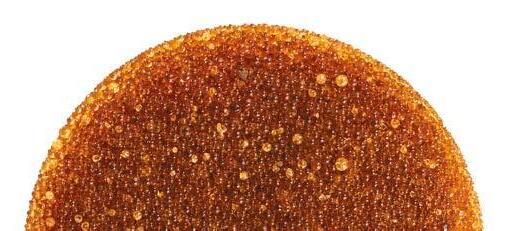
In the early 2020s, T&G was faced with a problem: the sizes of the machines built by its customers were getting bigger and bigger and its Eurocar plant, handling workpieces up to 10 metres in length, was no longer sufficient. This was the reason behind its most recent investment: a Komby line for manual coating, extremely adaptable to the most diverse metal parts, suitable for small production runs and touch-ups thanks to the possibility of loading different components with different dimensions and colour requirements on its overhead conveyor at the same time. Furthermore, its modular construction allows it to be upgraded and modified with additional modules over time. T&G chose a Komby model with two modules, namely paint application and curing, defined as “hybrid” because it has a fully automated one-rail conveyor for handling large and heavy workpieces instead of a manual directional roller. Its overhead trolley moving transversely to the fixed rails can carry up to
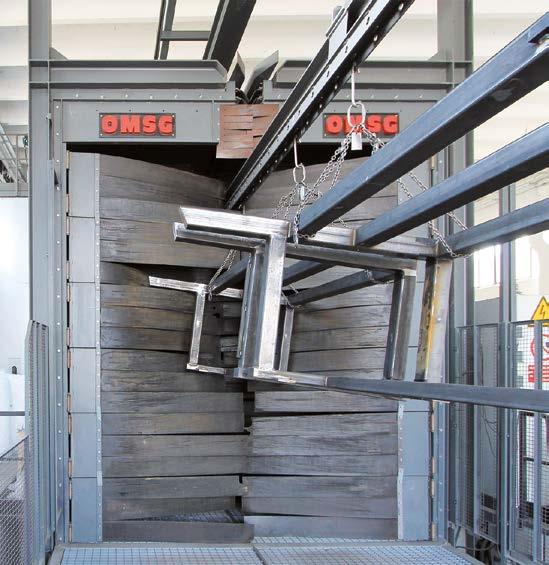
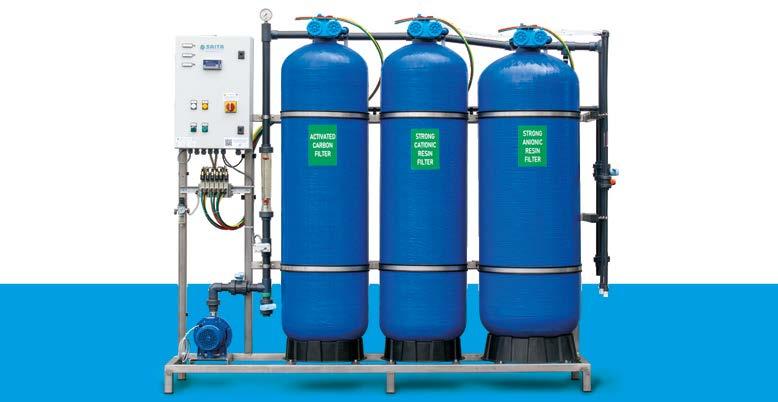
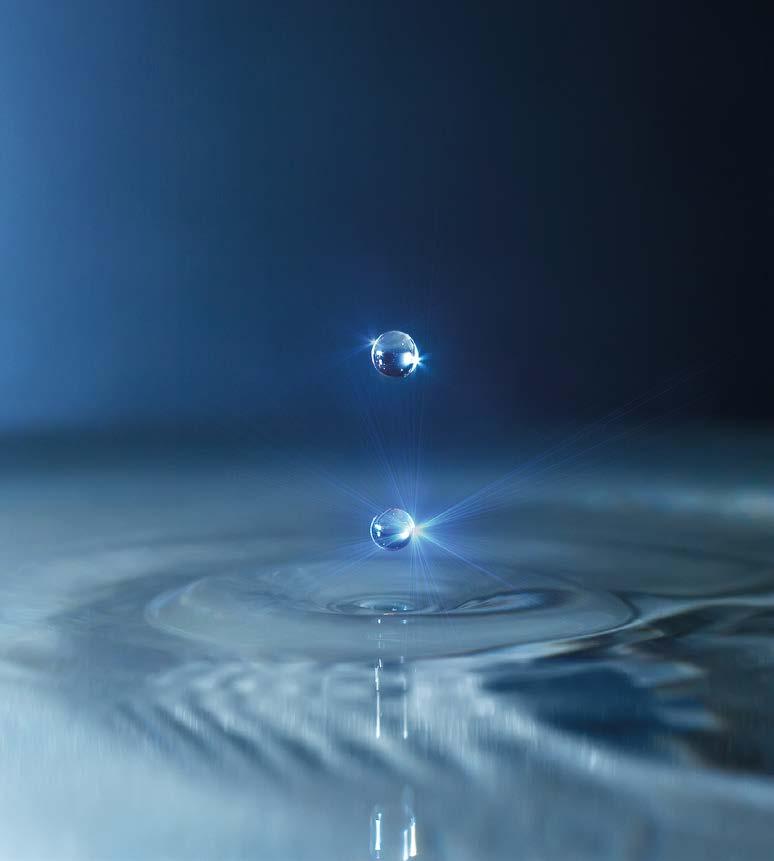
4,000 kg, distributed among two parallel workpiece-carrying bars. The load bars are 12,000 mm long. This handling system was designed by Dutch company Railtechniek, which also built four automatic feeders on board the trolley to allow inserting the load bars from both sides of the plant according to pre-set programmes for different work cycles.
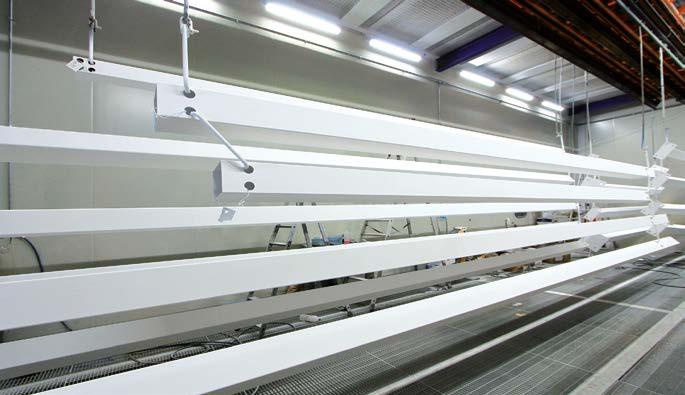
Conclusions
“Throughout our careers as entrepreneurs, our priorities have always been investing in our company, pampering our customers, and retaining them by solving their problems –in short, providing a high-quality service,” says Enrico Troisi. “Today, we have 45 employees and we specialise in the coating of automation systems and industrial machinery in general. In this niche, having always opted for mechanical pre-treatment has played an important role, through both manual sandblasting with Garnet and automatic shot blasting with mixed iron grit. Moreover, since staff training is a critical aspect for companies like ours, we believe that once operations have been optimised for a handful of target industries, it becomes uneconomical to go for others. T&G is an all-round contractor, specialising in highquality surface treatments and in the application of both powder and liquid coatings with a wide range of equipment to meet the most diverse requirements: we are proud of what our small business idea has become.”

From top:
Railtechniek designed a unique handling system for T&G’s Komby plant, which makes the transfer of parts between operating modules fully automatic. The Komby plant’s manual coating booth.
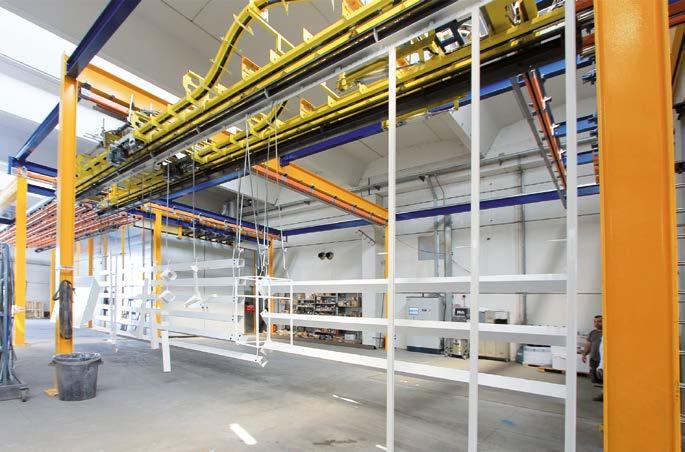
Super durable powder coating in anodized look
TIGER Drylac® Series 68 underscores the high demands of the architecture and facade industry on the performance of building envelops worldwide. The super durable product portfolio includes numerous anodized effects for smooth finishes in matte or flat matte aesthetics.
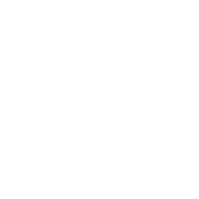
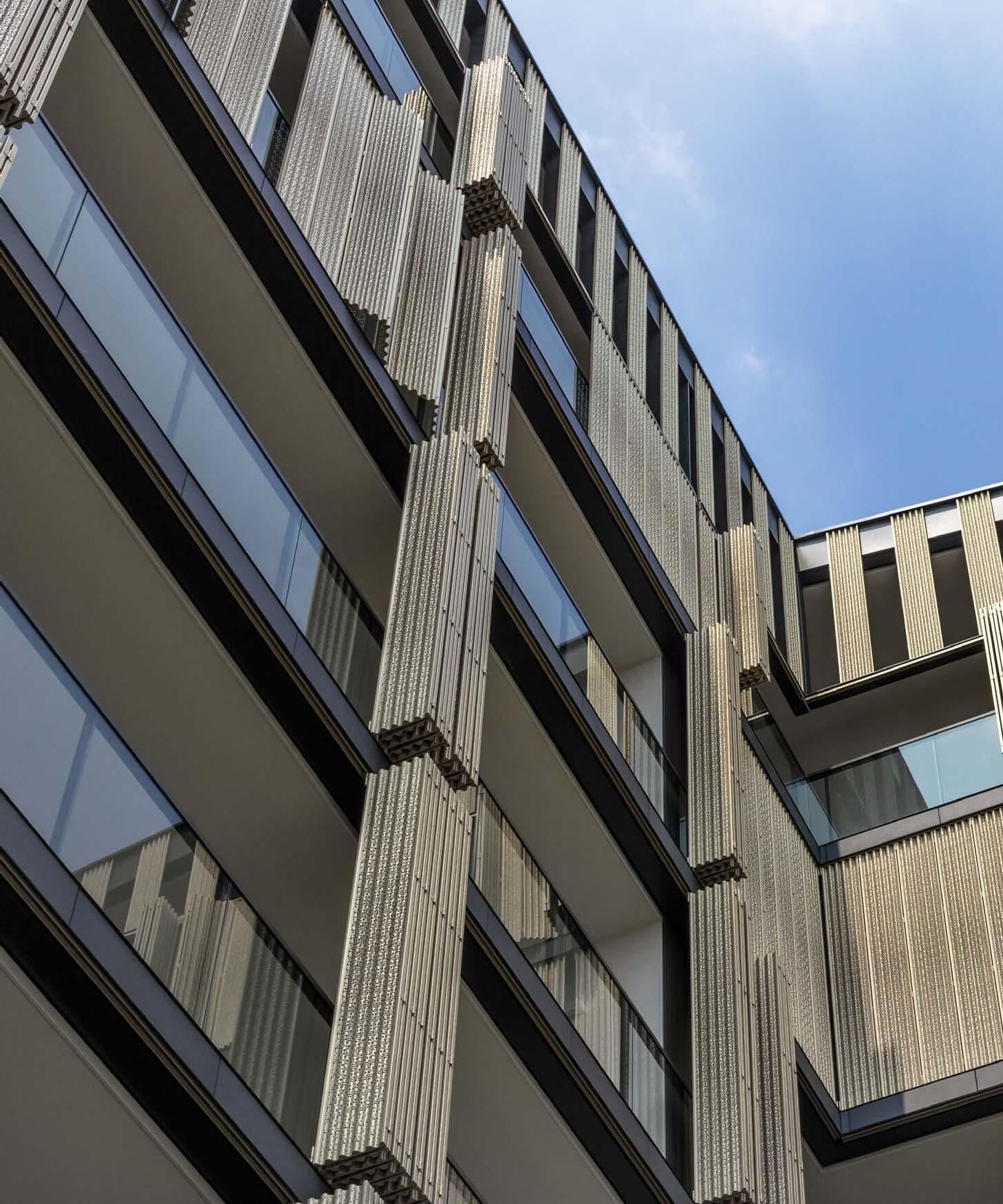
Your advantage: Not only aluminum, also steel and galvanized steel can be finished in a refined anodized look: cost-effectively, environmentally friendly and in just one coat. www.tiger-coatings.com
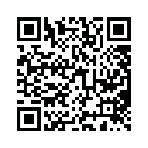
ART WITHIN SURFACES
AkzoNobel Helps Southwest Celebrate Hawaiian Culture with Imua One
Edited by AkzoNobel Aerospace Coatings Hamburg – GermanyThere are special liveries, and there are liveries that are special – to an airline and the people it serves.
So when Southwest® wanted to celebrate the fourth anniversary of serving the Hawaiian Islands, it wanted to create a unique design that captured the Hawaiian cultural concept of Imua, which means forward, and the strength, courage, and spirit of the islands’ people.
For the design of Imua One, the airline partnered with Oahu-based Osaki Creative Group, and received guidance from Herman Piikea Clark, the Kanaka Maoli/indigenous Hawaiian artist, designer and researcher. The design, on a Southwest Boeing 737 MAX 8, features a range of stunning colours including bold blues, warm reds and a sunrise yellow, with gradients and vignettes to symbolise the transition from night to day and reflect the history of Pacific travel using the sun, the moon and stars to navigate.
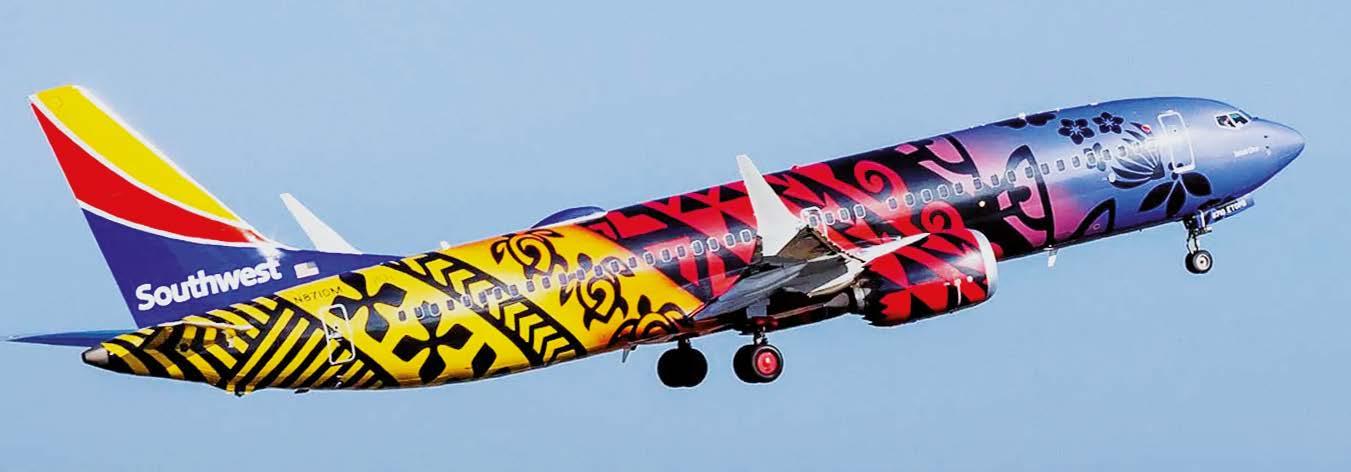
To bring its designs to life, the airline turned to AkzoNobel, for the quality of its aerospace coatings, and the expertise of its Technical Services Team.
The aircraft took 17 days to complete from a team of up to ten painters who worked in shifts in Spokane. The design used more than 90 gallons of paint comprising 16 different colours.
First the aircraft was painted black all over and a coat of Mica applied. A clearcoat set the Mica in place and was then sanded to give greater adhesion for the special colours that were to follow. Pre-mask stencils, expertly crafted by Solo Graphix, were then applied, with only very slight adjustments required. The ease with which the stencils could be used, combined with the speed of the paint material set-up, enabled the project to be completed two days ahead of schedule.
After the front design (pre-masking) was applied over the black it was scuffed, and the blue and purple added, along with a further coat of mica. The design was sealed with a clearcoat. The skilled paint team expertly handled the challenge of blending the orange of the aftersection design to deliver the desired effect For the middle section, the design blends (red to orange and purple to red) were completed at the same time. Both the after-section and the mid-section designs also featured a further coat of Mica sealed with a clearcoat.
With the design work completed, the airplane was unmasked, scuffed down, blown off for debris and tacked, and then three coats of clear were applied. The tail was worked on, and one final clear finish applied. Throughout the entire program, the paint went on with ease and no re-working was required.
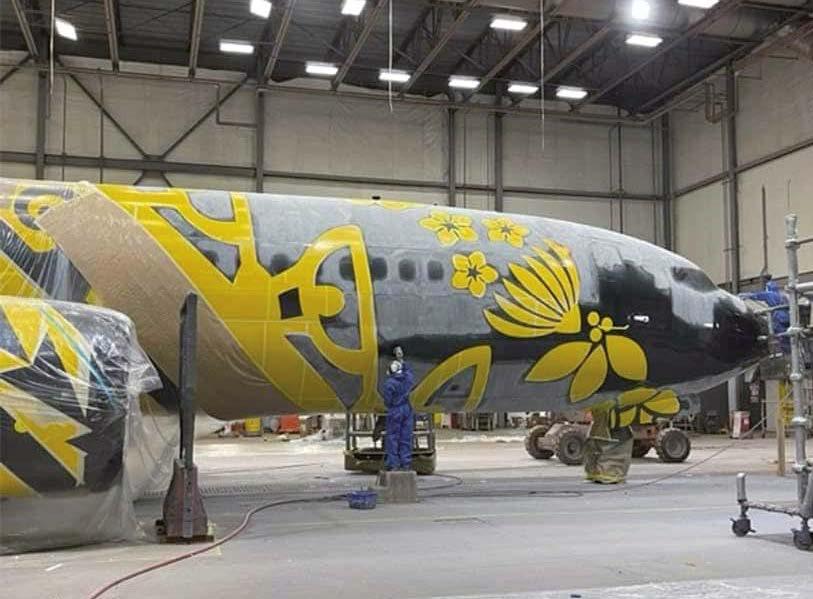
Mike Suhara, AkzoNobel Aerospace Coatings, says the team’s expertise was crucial to the success of the project: “The most challenging part of the project was choosing a Mica that would work with the different basecoats,” he explains. “We also had to develop five basecoat colours in less than our standard time, as well as an additional colour created on the spot during the customer visit. This took a huge effort from the colour development team in Troy.” Happily, the extra effort involved was worth it, for Mike says that in the light of day the airplane takes on a life of its own: “The design flows and the colours make it work so well,” he continues. “It is amazing to see and once you learn the meaning of the symbols and what they mean to the people of Hawaii, it means something special to all of us.”
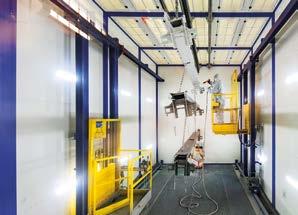
Eurotherm S.p.A.
T +39 011 98 23 500 | M info@eurotherm.eu
Eurotherm Oberflächentechnik GmbH
T +49-7571-92795-10 | M germany@eurotherm.eu
Eurotherm France S.A.S.
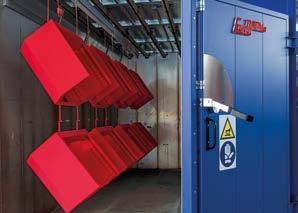
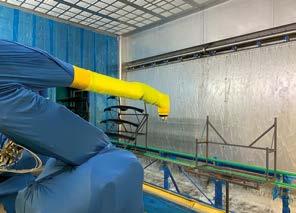
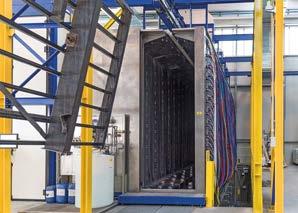
T +33 (0) 7 89 37 56 88 | M france@eurotherm.eu
Eurotherm Benelux
T +33 (0) 6 47 44 96 27 | M dekergorlay@eurotherm.eu
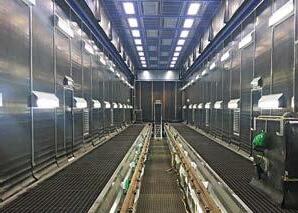
ADVANCEMENTS
The Latest Generation of CONDOROIL Stainless’ Dialysis Cells
Edited by CONDOROIL Chemical Casale Litta (Varese), Italy info@condoroil.itDialysis cells are essential for cataphoretic coating. Condoroil Stainless, a division of the Condoroil group, has developed a new cell concept with innovative features, ready to meet any market requirement.
Founded in 1972 by Franco Zavattoni, chemical company
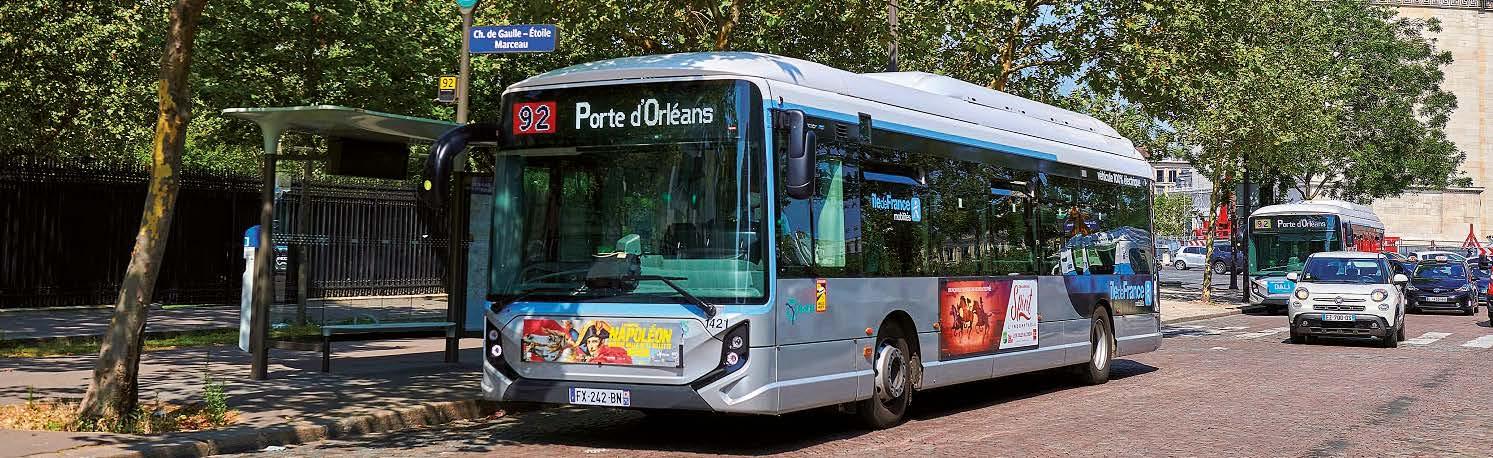
CONDOROIL currently has a portfolio of 3,000 products, 16 registered patents, and an innovative range of recovery, regeneration, and waste minimisation technologies to match its chemical formulations. Its plant in Casale Litta, in the province of Varese (Italy), covers a total area of 10,000 m2, of which 4,000 are covered, and consists of 5 buildings with a production capacity of 10,000 tonnes/year. Its technical division devoted to research and assistance employs on average 35% of its entire workforce and its chemical laboratories are its main flagship. Specialising in chemical solutions for the industrial coating sector, the company offers a diverse portfolio ranging from paint strippers to water purification agents, from pre-treatment solutions to electrophoretic coating products. For the latter field, in particular, the Condoroil Stainless division produces state-of-the-art dialysis cells already in use worldwide.
CONDOROIL Stainless’ dialysis cells
Condoroil has already installed a large number of cells both in Italy and abroad, proving that the features developed by its R&D division can meet a truly wide range of different customer needs. Such characteristics include as follows:
• protection: a “semi-rigid” mesh placed around the membrane protects it against accidental impact and therefore against damage. Typically, users needing to immerse sharp-edge parts in their cataphoresis tanks,
which may impact the cells while oscillating, choose this option.
• “super” length: when necessary, the length of the active membrane can exceed 4 metres, especially if bus, truck, or earth-moving equipment components have to be immersed in the tanks.
• beyond-standard features: the T1 and T2 cells, with anode diameters of 1.5” and 2” respectively, are suitable for general industrial applications; they offer an excellent membrane-to-anode ratio and the longest possible service life. The demand for this type of cells is going increasingly hand in hand with the demand from the automotive sector for T3 and T5 cells, which have anode diameters of 3” and 5” respectively and ensure the added advantage of having fewer connections than the smaller ones.
Dialysis cell features
Condoroil’s cells are equipped with ion exchange membranes and they are built by using wrapped and welded polymer sheets, with low deformability and electrical resistance but long service life and high current intensity characteristics. With its minimal thickness and therefore limited electrical resistance, this generates little heat, which is the primary cause of premature ageing of the membrane itself. Its limited expansion also prevents any short circuits between the membrane and the electrode. Whereas in conventional cells the water flow enters the electrode by physically touching it, in Condoroil’s cells it flows through a plastic tube closed at the opposite end with a plug to prevent the liquid from flowing back into the electrode.
In these tubular cells, the electrolyte is flushed from the top into the electrode and, rising from the bottom, allows any excess to leave the cell. In the event of electrode failure, this eliminates the risk of the creation of a preferential water path that would result in the electrolyte building up in the space between the electrode and the membrane. A further advantage is that, in the event of failure and/or breakage, it is not necessary to replace the full unit: these cells enable to replace the electrode alone while keeping the membrane. Another benefit relates to the fact that the standard solution was developed with an open top for easy inspection and simple maintenance. Especially in the case of pressurised cells, however, a “Closed Top” alternative is also available, with the application of a lid that is connected to the water circuit and the electrical cable.
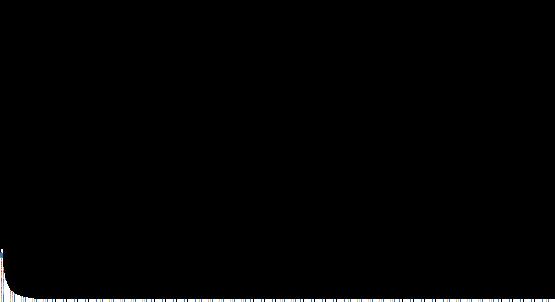
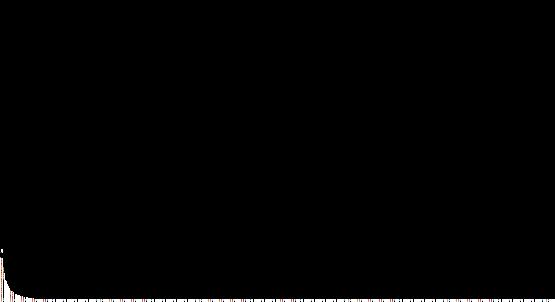
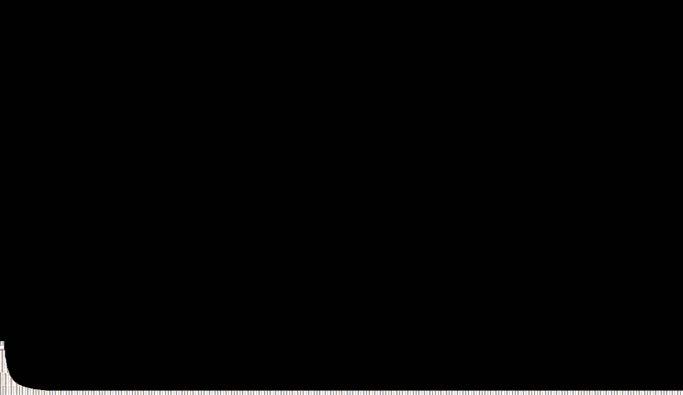
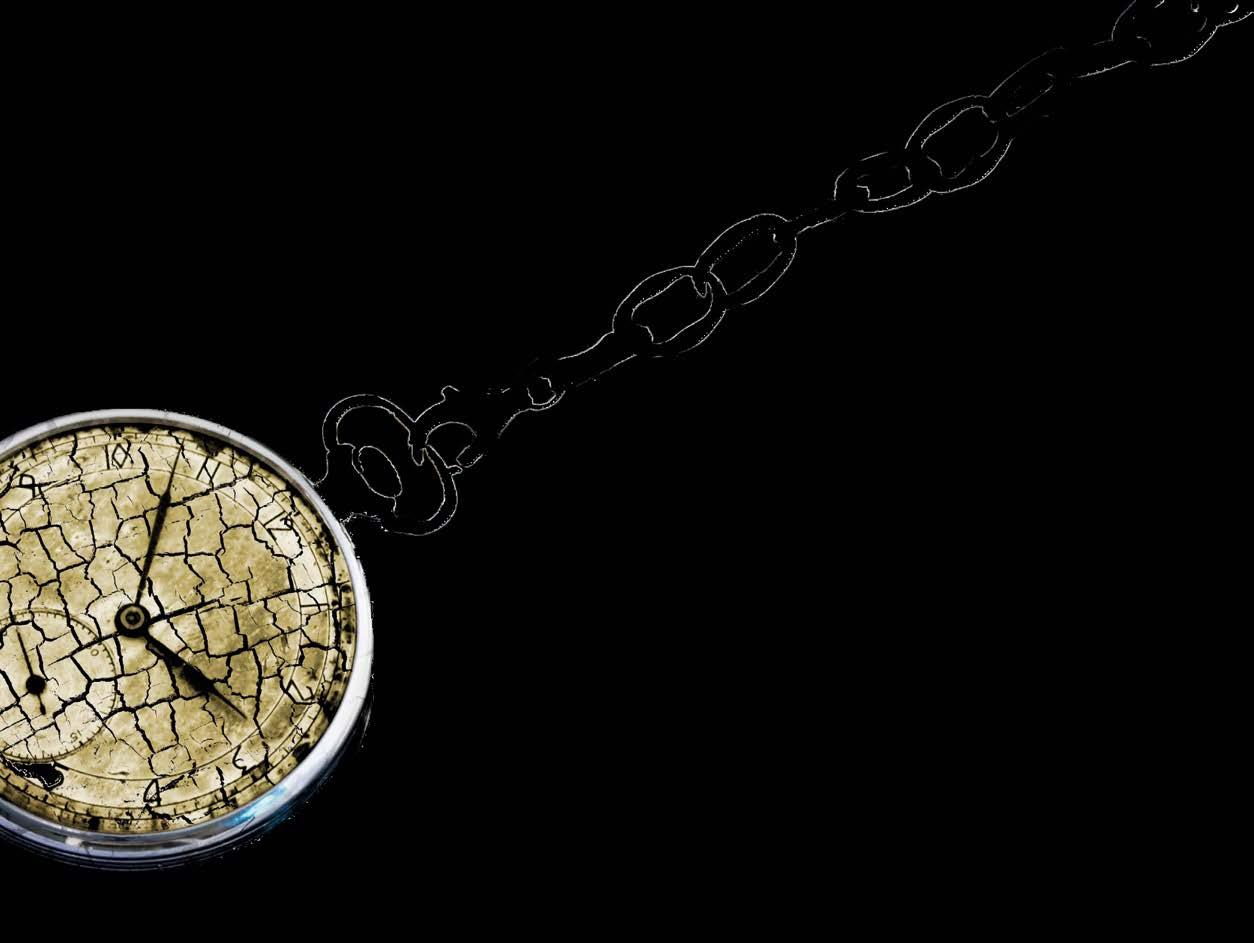
Once again, the Condoroil Stainless division of the Condoroil Group proved itself up to the demands of the market, capable of researching and finding dialysis cell solutions that meet the most diverse and complex requirements while optimising a product that is fundamental for cataphoretic coating processes.
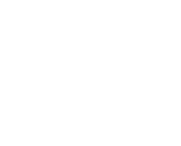
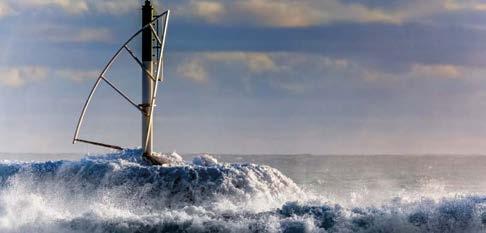

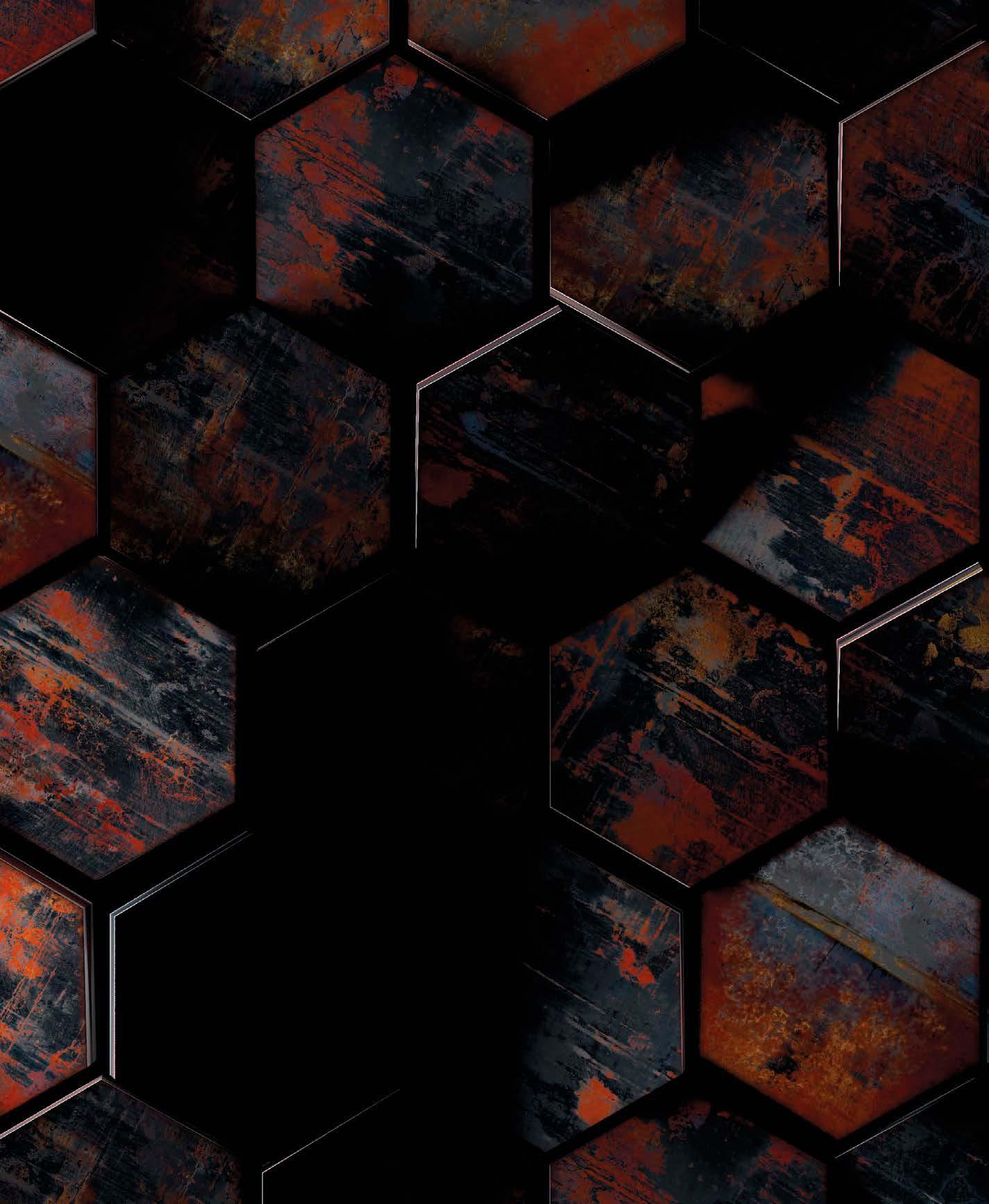
From left to right: The semi-rigid mesh around the membrane protects it against accidental impact; Especially in the case of pressurised cells, the alternative “Closed Top” type allows connecting the lid to the water circuit and the electrical cable.

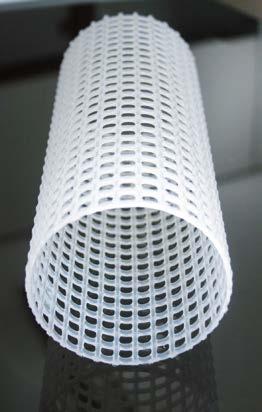
Deceiving Green COLOUR STUDY
Monica Fumagalli ipcm®From a venom-based pigment to a flag for ecological movements: green, the quintessential colour of nature, is one of the most difficult tints to synthesise and, perhaps for this reason, it is also associated with capriciousness and deception. Positivity and negativity of a colour with many nuances.
Green is the colour of sustainability and ecology par excellence, so much so that it is now common, particularly in technical communications for the manufacturing industry in which we work, to see companies defined as “green”. However, this is a misleading mental association with the world of nature and what is “clean” and sustainable: as green is one of the most difficult colours to synthesise, its production process is actually among the most complex and polluting ones, and the same is also true for its disposal. As chemist Michael Braungart stated in an interview with the New York Times a few years ago, “The colour green can never be green, because of the way it is made. It’s impossible to dye plastic green or to print green ink on paper without contaminating them. Ironic, isn’t it?”1
1 https://www.nytimes.com/2010/04/05/arts/05iht-design5.html
Obtained from the combination of yellow, the colour of joy, and blue, the colour of tranquillity, green nevertheless remains a positive colour precisely because of its connection with nature: it evokes feelings such as rebirth, freshness, vitality, and peace. Green promotes relaxation, which is why environments with elements in this hue are seen as peaceful, capable of nourishing our minds and even – it is believed –improving concentration. It is also the colour of hope, vitality, fertility, and abundance. In traffic lights, it gives us – literally – the green light, understood as the go-ahead, as opposed to red, which obliges us to stop. However, it is also the colour of envy, the medieval devil, disgust, and venom. In some cultures, it is associated with money (dollars are green) or the lack of it (in Italian, for example, “essere al verde”, literally “being to the green”, means “being broke”). Green has been appreciated since ancient times but, precisely because it is difficult to produce, it
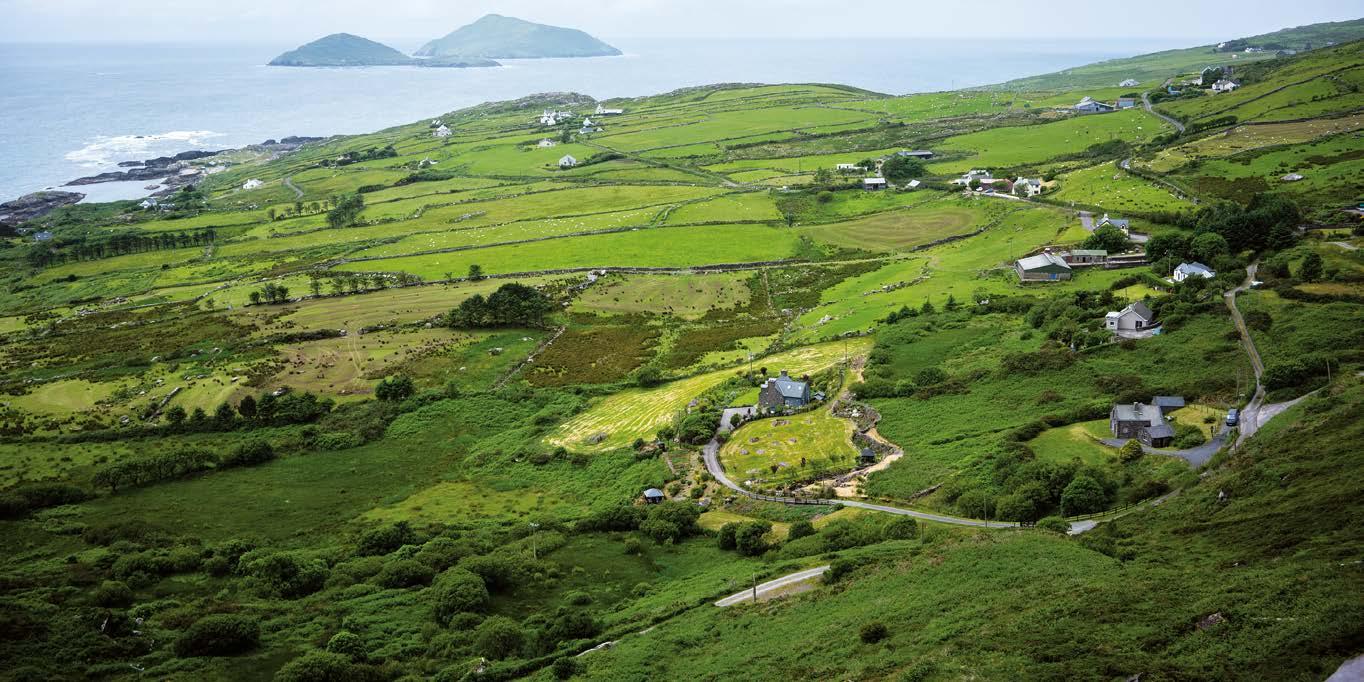
has always also been one of the most problematic colours for artistic production.
The origin of the word “green”
The ancients considered green2 (in Italian verde, in French vert, in Spanish and Portuguese verde, and in German grün) to be a shade of colour associated with yellow. This is revealed to us by the IndoEuropean root ghel, which also meant “bright”, “shining”, and the ProtoGermanic word gewalz, which indicated both tints. This gave rise to the Latin terms galbus (“pale green”) and galbinus (“yellow”).
The first to separate these two colours were the Greeks: in ancient Greek, the same Proto-Indo-European root evolved into khloròs, a word associated less ambiguously with pale green, later becoming itself the root of “chlorophyll”.
The English word “green” derives from the Proto-Indo-European ghrehand the Proto-Germanic groniz, which also, not at all coincidentally, gave origin to the verb “to grow”.
The Italian, French, Spanish, and Portuguese names followed the same path: they came from the Latin viridis, which later became virdis, which in turn was related to the verb vireo, i.e. “to sprout”, etymologically also connected to “vigour” and “vegetation” (from the Proto-Indo-European root weg-).
Green in ancient history
In contrast to blue and red, there is no trace of green in prehistoric paintings, perhaps because colours found in nature, of which we can no longer find any trace, were used on cave walls. The first evidence of the use of this colour dates back 5000 years, when the ancient Egyptians chose it to represent the vegetation and fertility of the Nile, which flooded the land with its waters making it lush. The Egyptian deity Osiris was often depicted with green skin to symbolise rebirth and fertility. Palettes of green facial makeup have been found in some tombs of the time, made from malachite, a green mineral rich in copper that was pulverised and used as a pigment: the Egyptians had the custom of making up the edge of their eyes with green dye to protect themselves from evil. The same belief also applied to the dead: small green amulets in the shape of scarabs, made of malachite, have been found inside tombs, probably left for the very purpose of protecting the deceased. In addition to malachite, pigments such as verdigris and Egyptian green were used to obtain the green tint: verdigris was a compound of copper acetate, obtained from the corrosion of metal, whereas Egyptian green was a mixture of malachite, azurite, and other minerals that was prepared synthetically. To become green, on the other hand, fabrics were first dyed yellow with saffron-based pigments and then soaked in blue dye made from the woad plant’s roots.
2 www.linkedin.com/feed/update/urn:li:activity:7001092899694129152
Shades of green in the Middle Ages
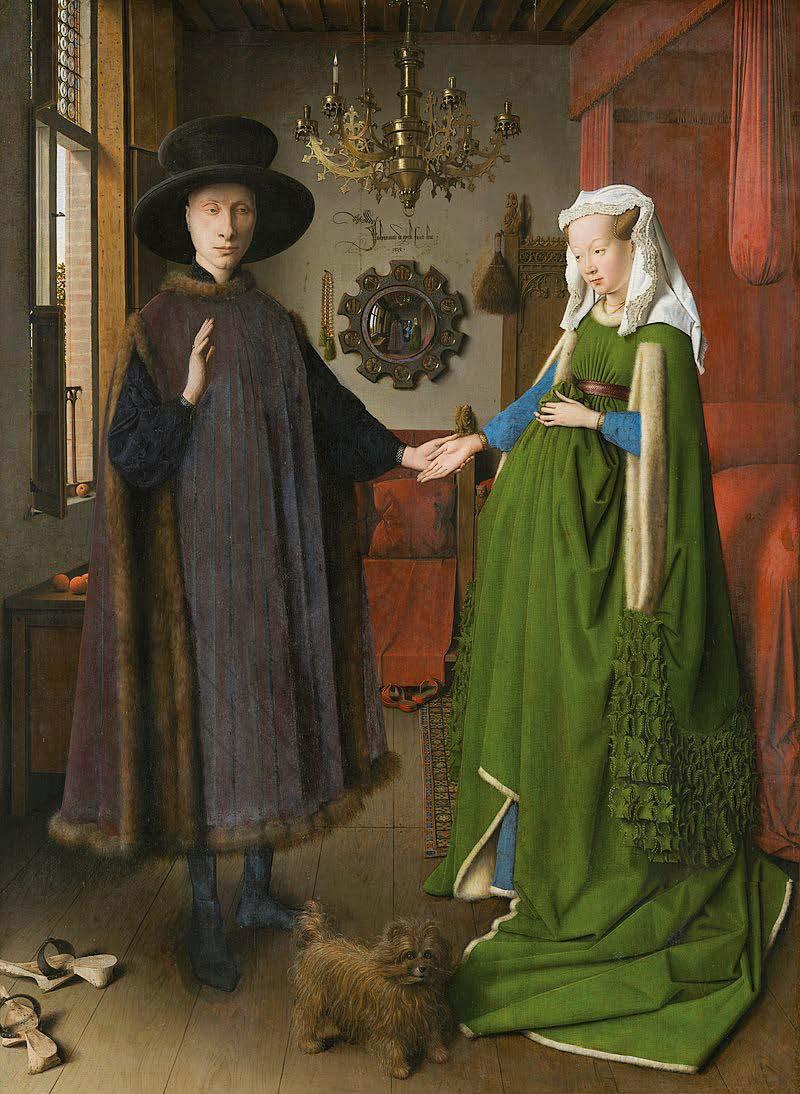
Whereas during the Late Roman Empire, newborn babies were wrapped in green mats to wish them good luck, in the Middle Ages this colour was chosen by girls seeking husbands and then, once married, as a wish for motherhood. However, perhaps because of its dye instability due to the difficult composition process, at that time green was also associated with deception and cunning and, therefore, to the devil, to witches, and to the most frightening fantastic animals such as dragons, monstrous snakes like the hydra and the basilisk, and mermaids.
From its earliest days, the colour green has also been associated with Islam because of a sentence in the Quran that states that those who are in paradise will “wear green garments of fine silk”. Therefore, mosques are decorated in various colours but almost always with predominant green tones and the tombs of Sufi saints, connected to the mystical dimension of Islam, are covered in green silk.
That is also why the tribe of prophet Muhammad had a green banner and why almost all Islamic countries use this colour in their flags. In Western history, green retained its controversial appeal even in the 15th and 16th centuries. Its association with good omens was confirmed in the famous “Arnolfini Portrait” by Jan van Eyck (1434-35), in which the woman is not pregnant, as one might guess due to the shape of her dress, but is thought to have been depicted in that position and with green clothes as a propitiatory rite for numerous offspring.
Venomous green
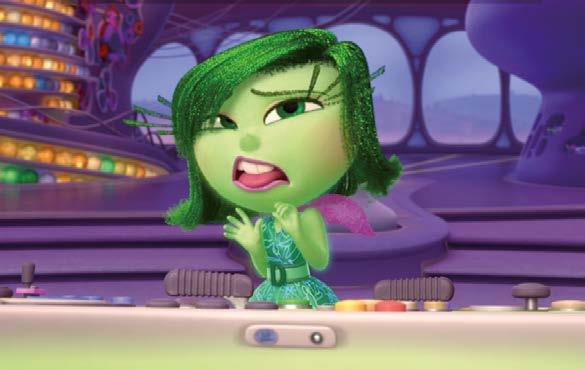
The turning point in the popularity of this colour in the art world and beyond occurred in the Victorian era, with the custom of obtaining green dye by adding arsenic, the highly toxic substance believed to be the cause of the deaths of many people who handled books, toys, and decorative objects or merely lived in rooms painted with it3. Both Scheele’s green, developed in 1775 by Swedish chemist Carl Wilhelm Scheele, which was an immediate success due to its intensity and resistance to light, and the Paris green or Schweinfurt green, consisting of arsenic and lead, with which Impressionist painters fell in love during the 19th century, are believed to have been responsible for poisonings that cost the health or lives of many who came into contact with their toxic green pigments. Just to mention one of the most famous cases, Napoleon Bonaparte’s residence in exile on the island of St. Helena, Longwood House, had its walls painted in this colour. In his “Theory of Colours”, it was Goethe who first described green as “soothing” and thus recommended for use in rooms intended for rest and conviviality.
3 https://www.focus.it/cultura/curiosita/verde-arsenico-timore-mistero
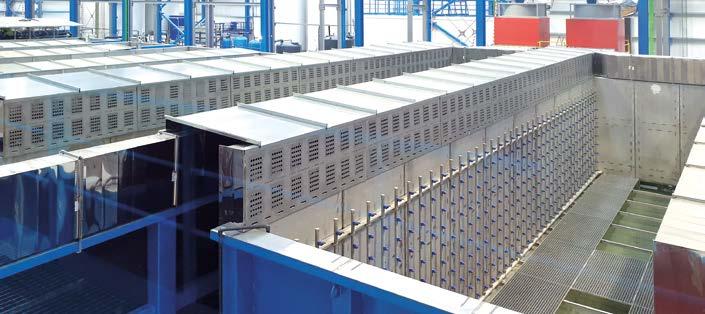
The Romantic movement of the late 1700s, finally, sanctioned green as the colour of nature, ecology, and the environment, as it has been up until today.
Fun facts
According to some theories, before Coca-Cola’s marketing move4, Santa Claus’ original suit was green to recall the “secular” origin of this figure, linked to the tradition of elves distributing gifts in some Northern European countries. According to the folklore of Ireland, the green island par excellence, green is the favourite colour of fairies. As for the negative connotations of this colour, the creators of the Pixar film “Inside Out” chose green for the character Disgust, alongside Joy (yellow), Sadness (blue), Anger (red), and Fear (purple); again, the ambivalence of green is however once again confirmed by this very character who, within the emotional concept of the film directed by Pete Docter and Ronnie del Carmen, also has a positive value because she allows the protagonist to protect herself from physical and social contamination.
A final oddity brings us back to the problems associated with the realisation of this colour: do you know why the Incredible Hulk’s skin is green? According to the well-informed, in the original portrayal of the Hulk, Stan Lee wanted him to be grey, but due to some printing issues in early copies of Marvel comics, his figure turned from grey to the green we are used to seeing in comics and films today.
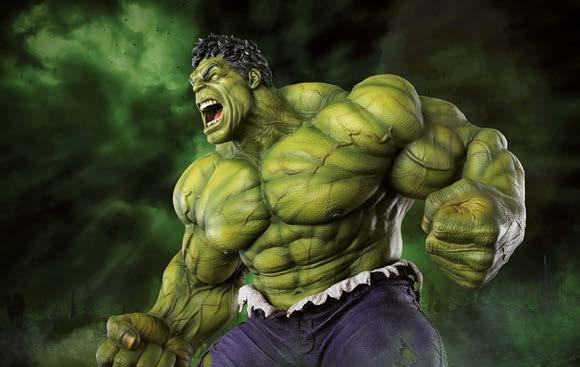
4 https://eosmarketing.it/en/did-coca-cola-invent-santa-claus/
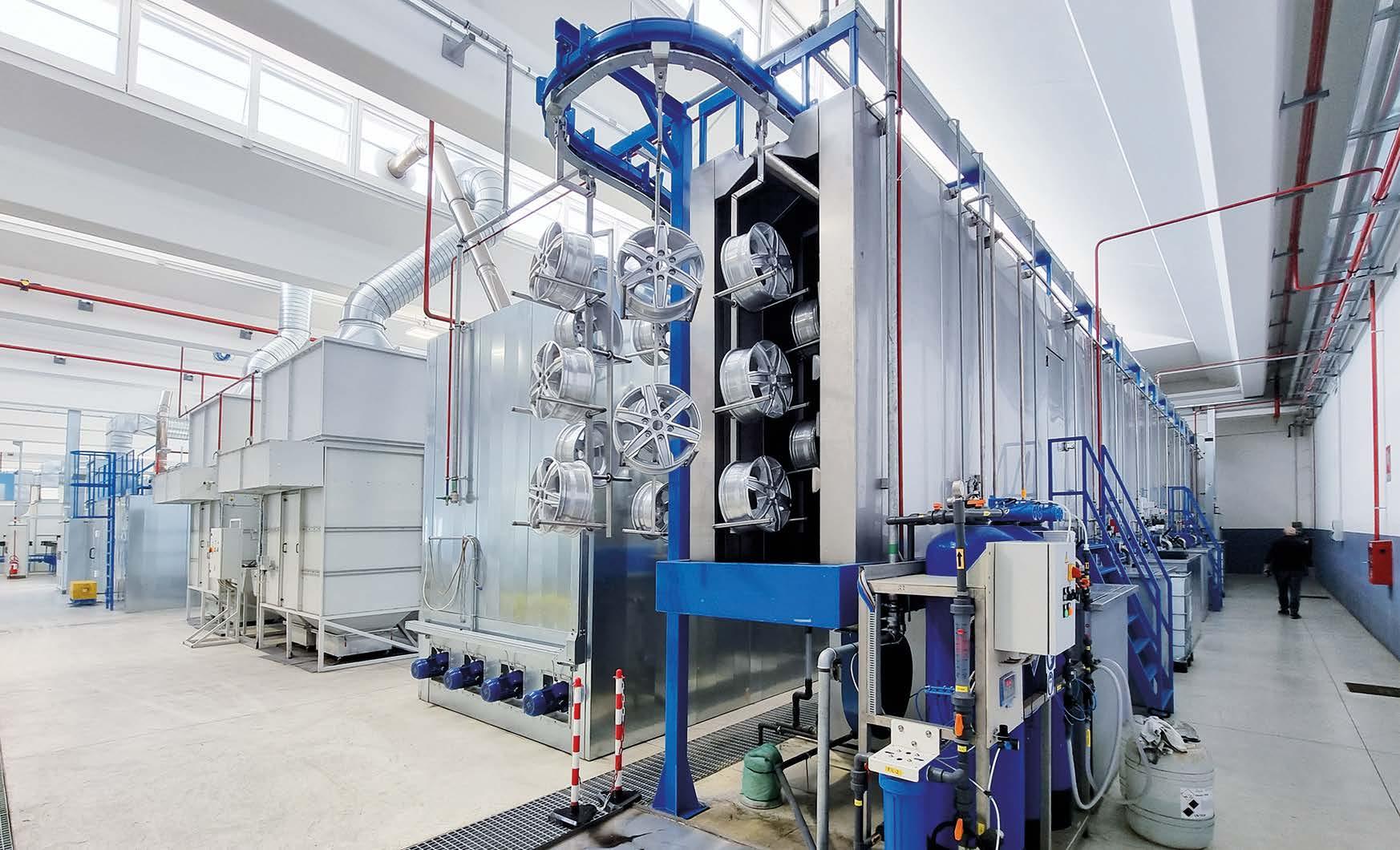

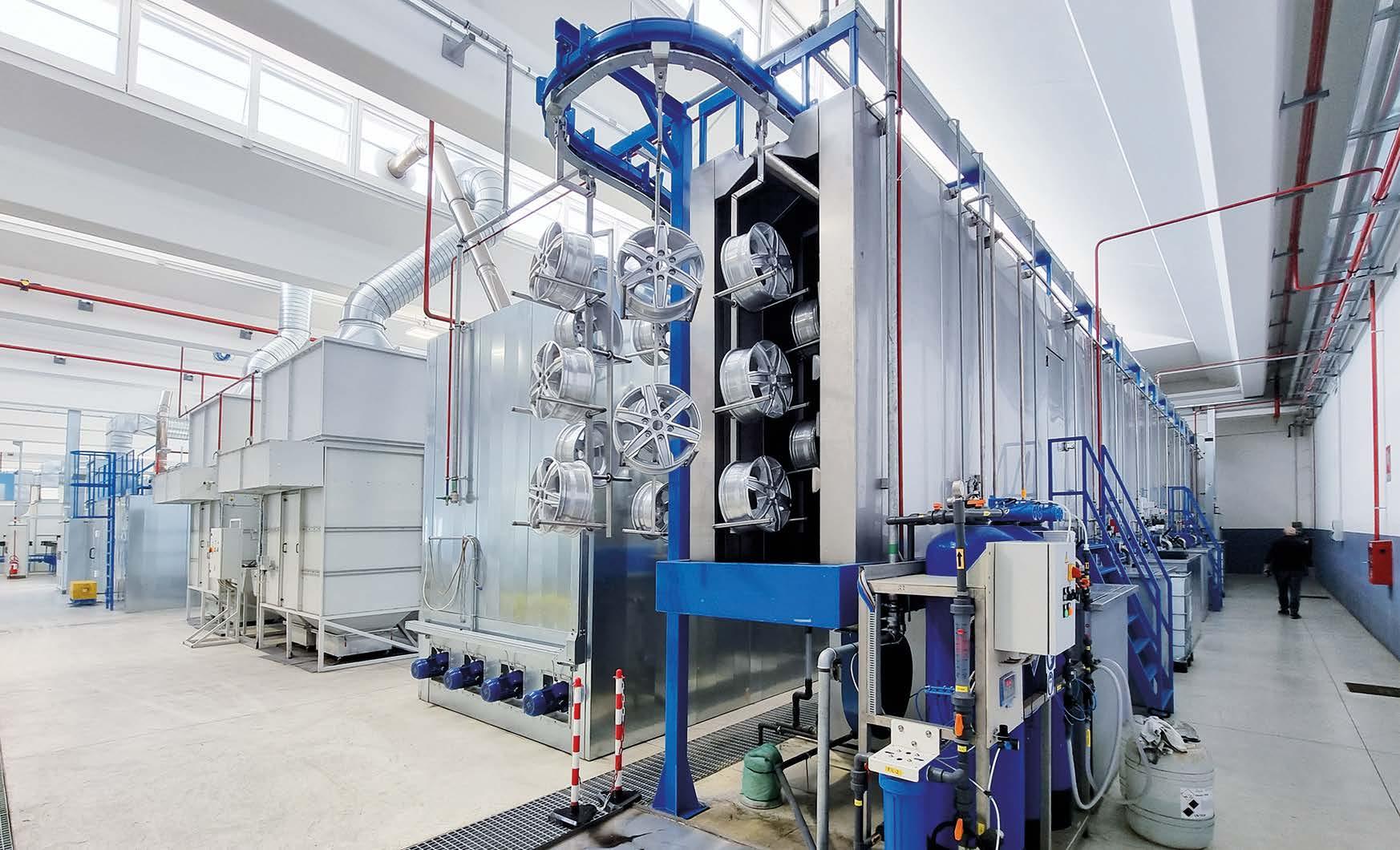
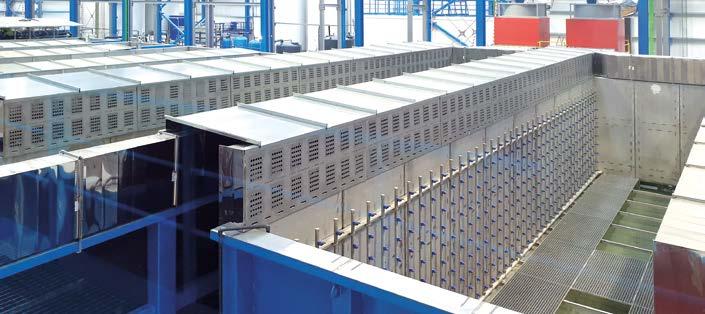
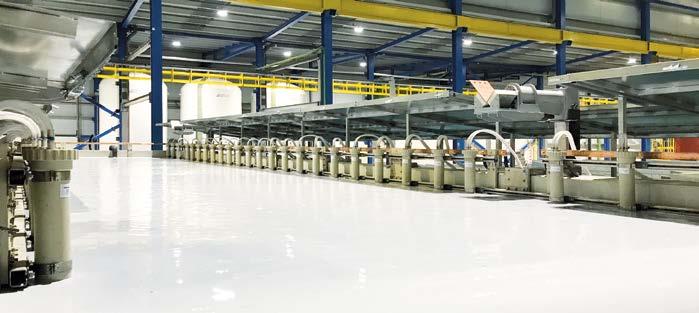

Swimming Across the Strait of Messina: The Verind Team’s Latest Feat
Sport is about unity, sharing, and effort to achieve a common goal: this is also the experience of Matteo Minelli, Claudio Orlando, and Francesca Orlando from Verind, who completed the crossing of the Strait of Messina by swimming after a year of training together.
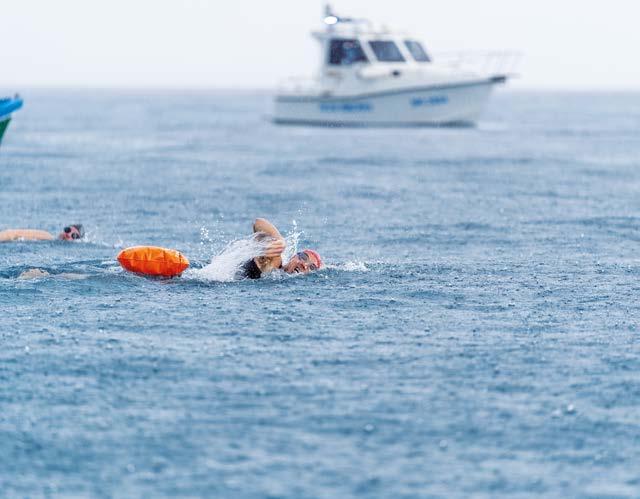
On 12 June, Verind accounting & controlling senior manager Claudio Orlando, his daughter Francesca, and Verind general manager Matteo Minelli crossed the incredible blue waters of the Strait of Messina, where the myth of Scylla and Charybdis still lives on. Their swim started on Sicily’s coast, near Torre Faro, and ended on Calabria’s beach of Cannitello, right in front of the church. During the crossing, the weather conditions changed abruptly and a severe thunderstorm raged for almost the entire time, only ceasing when they approached the Calabrian coast as the sun came out. In total, as confirmed by Matteo Minelli’s GPS watch, which also recorded the exact route followed, they swam 4,375 metres in 1:26’:04”, with 3,444 strokes.
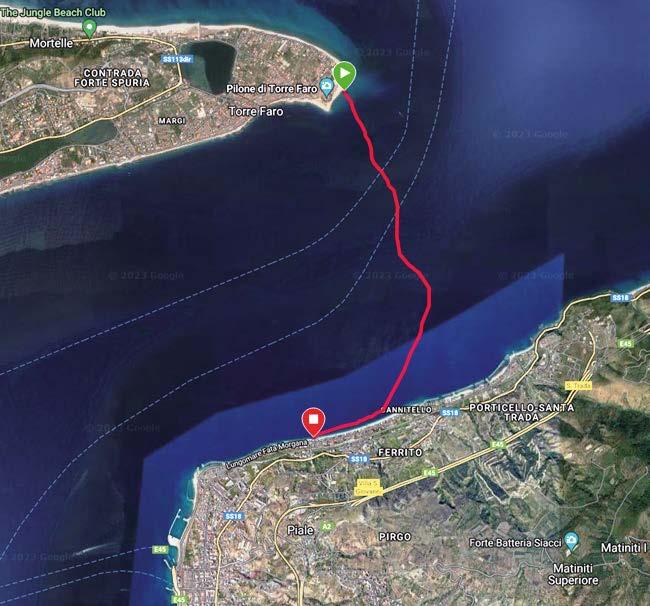
“I am passionate about open water swimming but, living in Milan, the options for practising this sport are few,” says Matteo Minelli. “My colleague Claudio Orlando shares this passion with me, and what was
a somewhat wild idea come up while chatting at work soon materialised into the common goal of swimming across the Strait of Messina in 2023. His daughter Francesca, a very sporty girl, joined us at a later stage.”
“For the safety of swimmers, since the Strait is characterised by heavy nautical and merchant vessel traffic, such an experience cannot be organised independently but requires the support of sports clubs that take care of the organisation, provide the support boats that follow the groups of swimmers, and fix a date for the crossing in agreement with the port captaincy. Claudio and I chose 12 June,” adds Matteo Minelli. “Unfortunately, the weather was not favourable, as the day started with overcast skies, which then turned into light rain and ultimately into a storm that hit us during the crossing. There were only a few of us, so we swam alone, each side by side with a support boat. The briefing was very simple: swimming by following the boat with our eyes and avoiding looking underneath so as not to get dizzy from the deep,
dark blue waters of the Strait. We finished the crossing with a time perfectly in line with our pool training, without even feeling excessive fatigue. We reached the Cannitello beach under the sun, where we were presented with the Diploma certifying the completion of the challenge. We are all very happy with this experience but also with the whole journey we took together to get ready.”
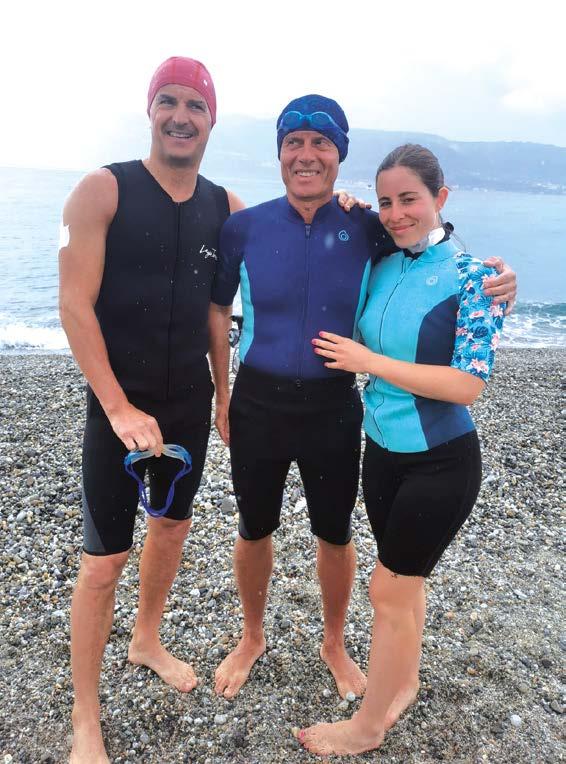
“Our aim was to achieve a common goal and we attained it through training and perseverance: we have worked side by side for many years and this experience has united us even more. As soon as I touched the Calabrian shore, I thought that our team had managed to connect the two Italian coasts well before the construction of the bridge over the Strait,” states Matteo Minelli with a smile.
For further information: www.verind.it
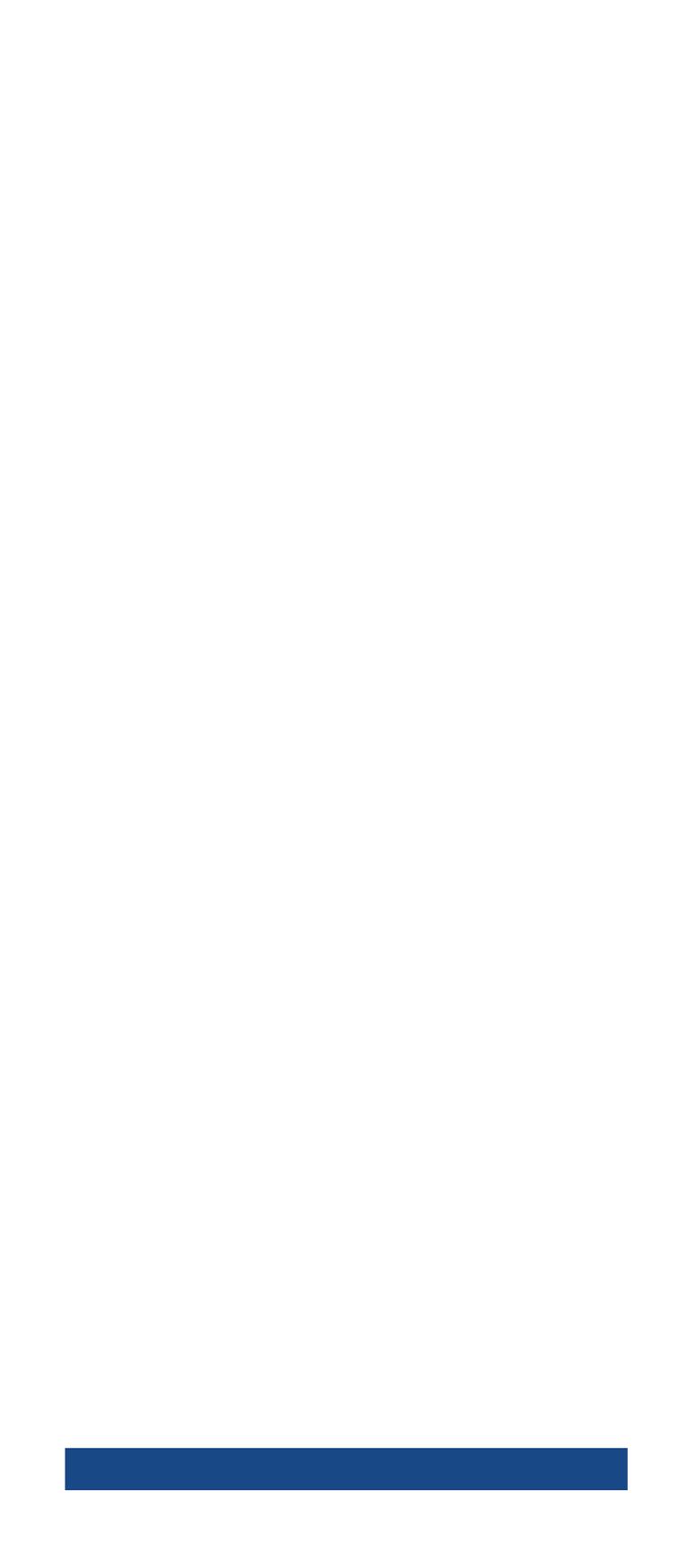
KANSAI HELIOS Austria Awarded Anna Gruber with the Sponsorship Prize
KANSAI HELIOS Austria awarded its sponsorship prize to Anna Gruber, who successfully completed the bachelor degree in Applied Chemistry at the IMC Krems University.
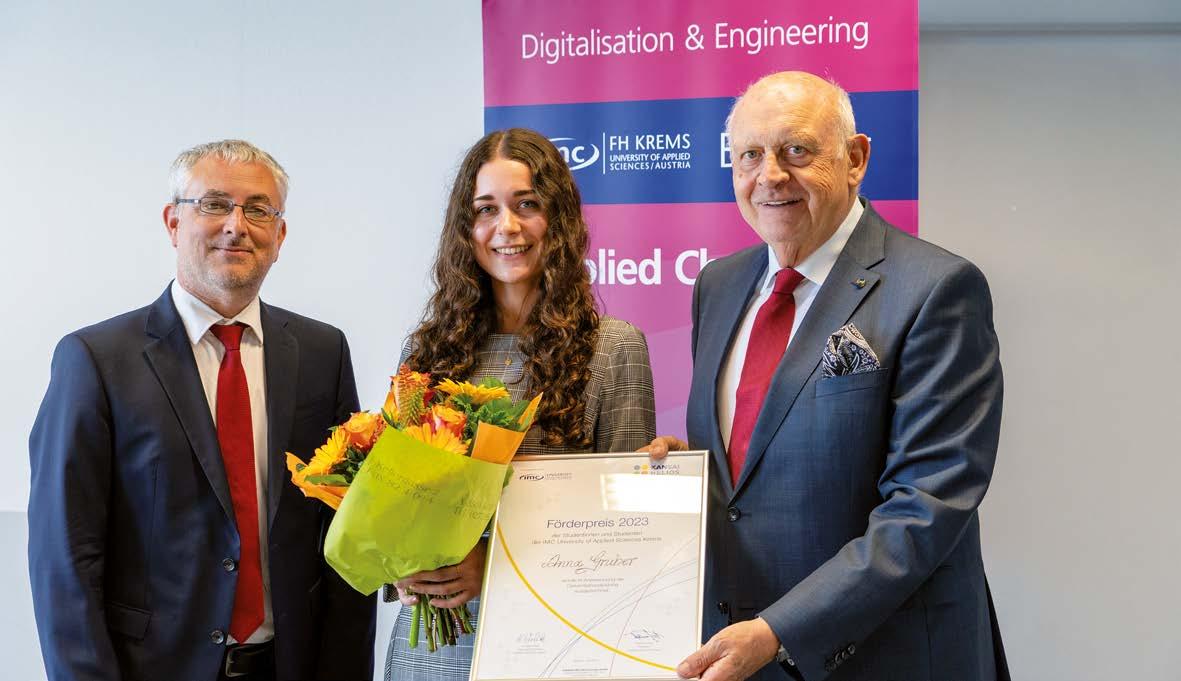
During the bachelor degree ceremony of the IMC Fachhochschule Krems (University of Applied Sciences of Krems), KANSAI HELIOS Austria awarded its sponsorship prize to Anna Gruber, who successfully completed her bachelor degree in “Applied Chemistry” and showed exceptional enthusiasm and initiative while writing her thesis. The prize was presented by Hubert Culik – the managing director of KANSAI HELIOS Austria – and Dr. Uwe Rinner, the Head of the Institute.
KANSAI HELIOS Austria has been supporting the English-language bachelor degree programme “Applied Chemistry” of the Austrian university for many years, as it is managed by professors from the academic sector and the chemicals industry focused on a solid and practice-oriented basic training in the field of chemistry, thus providing
promising future job opportunities for graduates. The Wien-based subsidiary (formerly Rembrandtin Lack GmbH) became part of the global KANSAI PAINT Group in 2017. Its core competencies include modern corrosion protection systems, innovative industrial coatings for the ACE segment and the railway vehicle industry as well as high-temperature resistant coatings and road marking paints. Currently, it has 190 employees, more than a quarter of which working in the Research & Development department. The sponsorship prize allows to support future professionals that might help the company to continue its growth.
For further information: www.kansai-helios.at
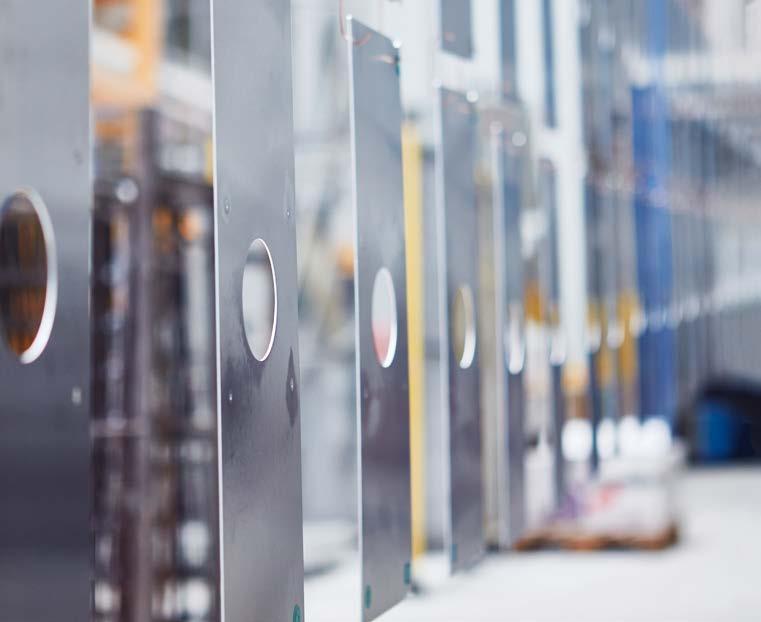
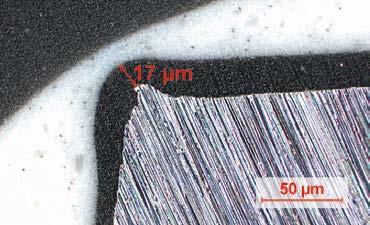
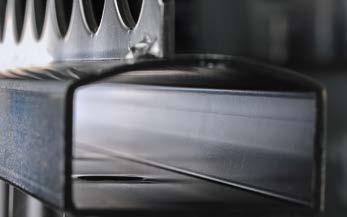
ADVANCEMENTS
New Dip-And-Spin Technologies Reduce Material and Labour Costs in the Metal Coating Process
Tim Hanna STC Dip Spin – Kalamazoo (Michigan), United States thanna@prab.comRecent supply chain disruptions and material shortages have strained almost every corner of the North American manufacturing sector, and the coatings industry has been no exception. From price hikes to order delays, the effects of a materials shortage are hard to understate. And if that has not been bad enough, persistent labour shortages continue to challenge manufacturing workforces.
At a time when every drop of coating material and workforce resource is precious, cutting back on material waste and operational inefficiencies is vital to the continued success of any coating operation. New advancements in coating technologies make that possible.

Labour savings, increased throughput, reduced downtime
According to the National Association of Manufacturers, companies report that it is 36% harder to find the right talent than it was just a few years ago, despite a high unemployment rate.
It is predicted that the skills gap could result in 2.1 million unfilled trades jobs in the U.S. by 2030. When every worker is more valuable than ever, dedicating multiple people to the same task constrains production capacity. Advanced coating systems automate the entire coating process—from the start of part loading to unloading—requiring minimal operator oversight. The systems take care of part dipping, excess coating removal, curing, transfer to and from the dipping unit, and more, and are highly programmable to meet the individual needs of the operation. This allows coating operations to free up their workforces for other responsibilities, combatting the rising difficulties associated with the labour shortage. Automated part coating systems also save time. Advanced systems include state-of-the-art touchscreen control systems that make running the equipment easy for operators. Additionally, automated dip and spin short and consistent cycle times of approximately 2 minutes help keep production moving. In the event that a mechanical problem occurs, remote troubleshooting can help accelerate a solution that minimizes equipment downtime.
Reducing coating consumption
The recently introduced Planetary Motion Technology by Forplan AG has significantly improved the process for removing excess coating from dipped parts. The process starts with automatic weighing capabilities to ensure consistent load sizes, with one batch consisting of two baskets of equal weight. Together these baskets are submerged into the coating, tilting and rotating at the same time to ensure all parts are coated.
After the system dips the parts into the coating material, the baskets rotate around themselves in a planetary fashion at high speeds. This engineering feature results in consistent coating and ensures that the parts inside the baskets are moving and re-orientating themselves for the best possible coating thickness. Excess coating material is recovered and returned to the dip tank for future use. The planetary motion technology is shown to reduce coating material consumption by up to 30%.
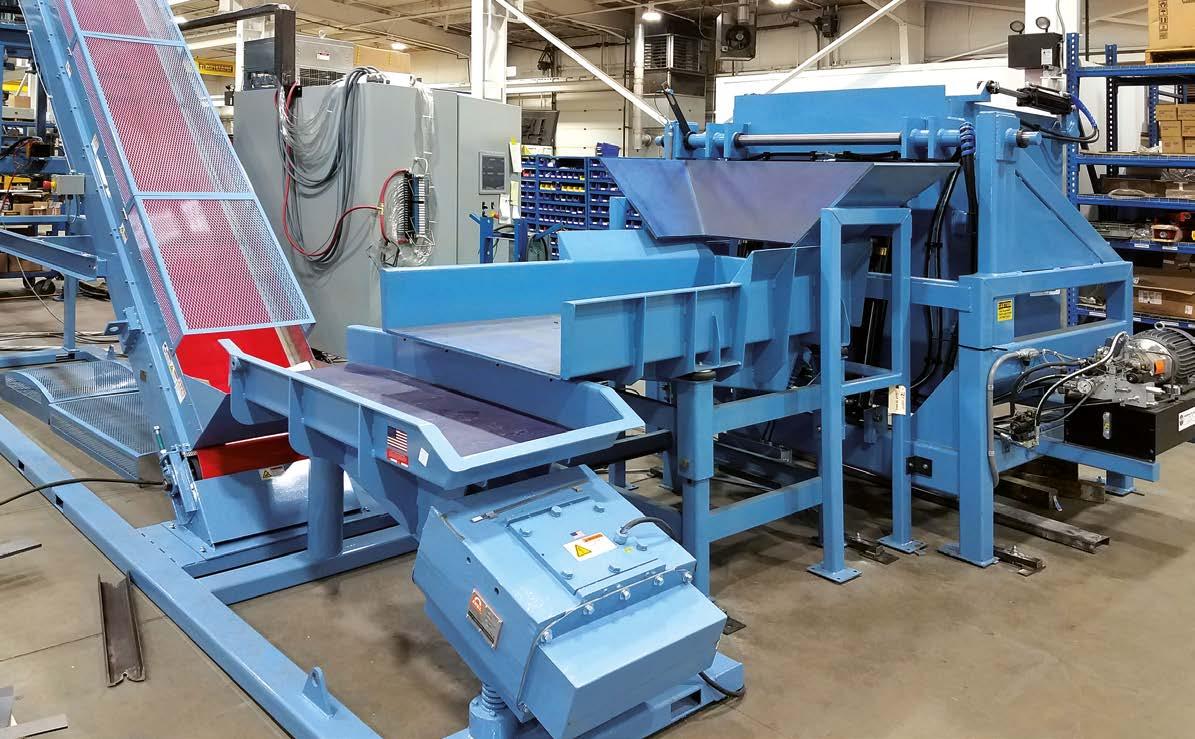
Space saving and lower carbon footprint
Due to an improved and innovative curing process this new equipment requires 35% less floor space than traditional dip and spin systems and can save 285 tons of CO2 compared to other common equipment. Typical ROI for these types of systems is less than one year.
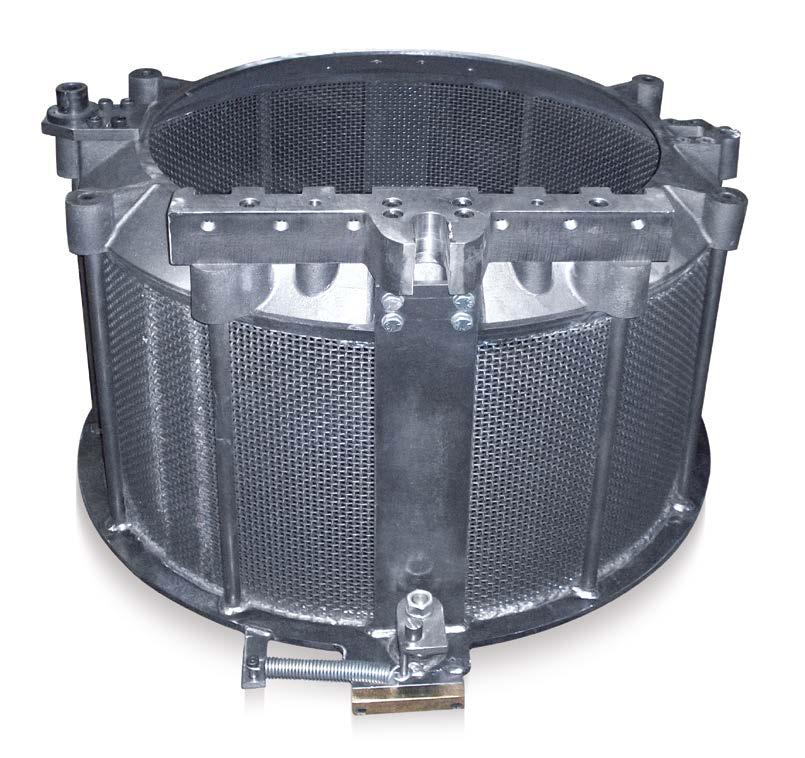
Conclusion
Demand in the coatings industry is booming. According to the “Paints and Coatings Global Market Report 2021,” the global paint and coating market is projected to reach $258.45 billion in 2025 at a compound annual growth rate of 4%. As demand increases, it’s likely that the cost of coating materials will rise. Fortunately, innovative part coating equipment can be the key to saving process time, labour, and material costs. Advanced coating systems not only help position coating operations to weather future challenges spurred by economic turbulence, but they put them in a favourable position to maximize growth. To take the first step toward more sustainable and steady production, consult with a trusted industry expert or manufacturer to
learn about the economic and environmental benefits of new planetary dip-and-spin technologies.
About the Author
Tim Hanna serves as the Vice President of Business Development and Sales Manager for STC Dip Spin/PRAB. With industry experience spanning over 30 years, Tim has extensive knowledge of the parts coating industry and the needs of its customers.
About STC Dip Spin
STC Dip Spin built its first dip spin coating machine in 1965. That machine is still in operation today. Since then, STC has worked to create the most reliable and consistent pieces of coating equipment possible. In 2020, STC partnered with Forplan AG, Brugg, Switzerland, which offers a variety of coating systems for mass-produced parts—both for bulk items and rack parts. Regardless of industry or operational needs, STC provides a wide variety of trusted equipment backed by comprehensive warranties and indepth expertise, tailored to fit the client’s needs every step of the way.
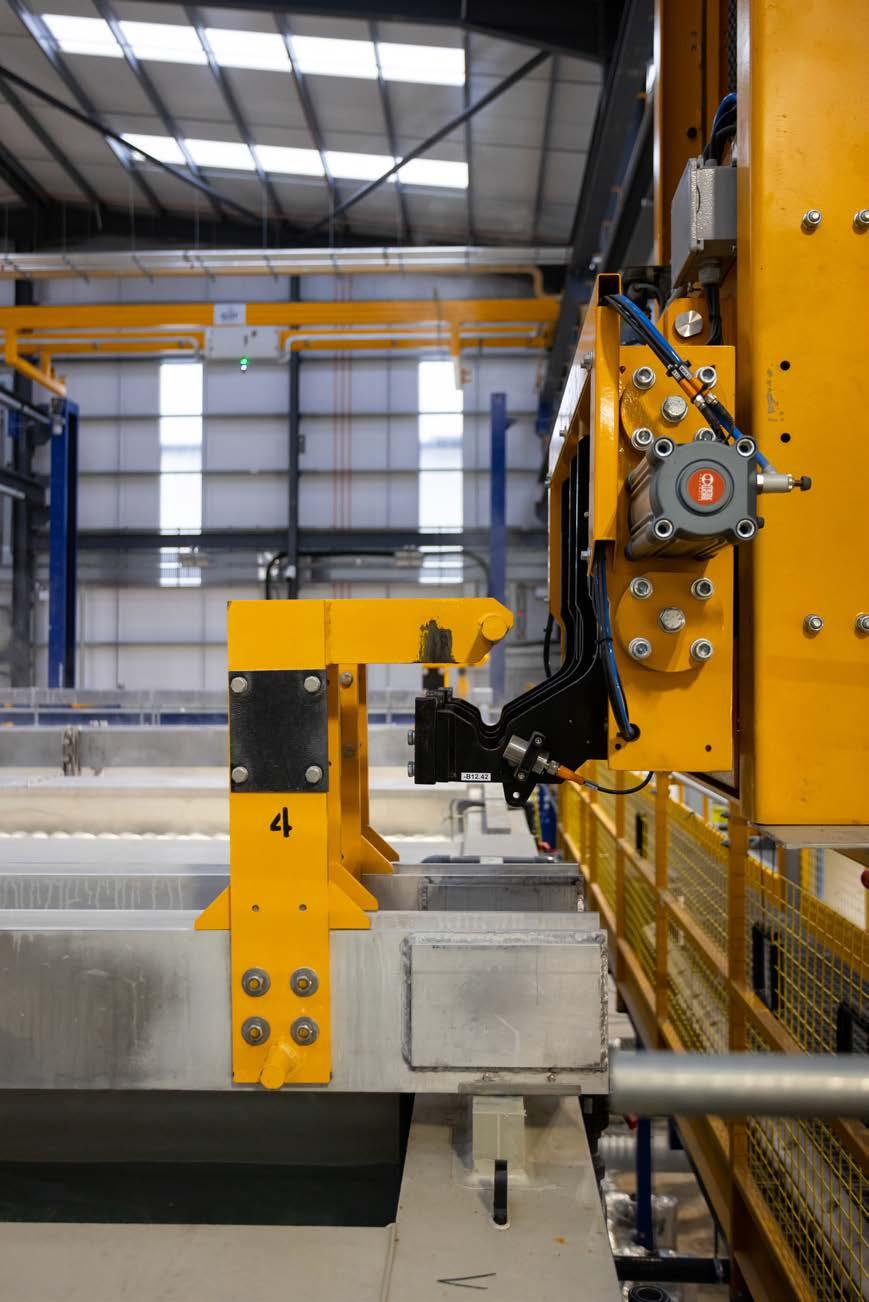
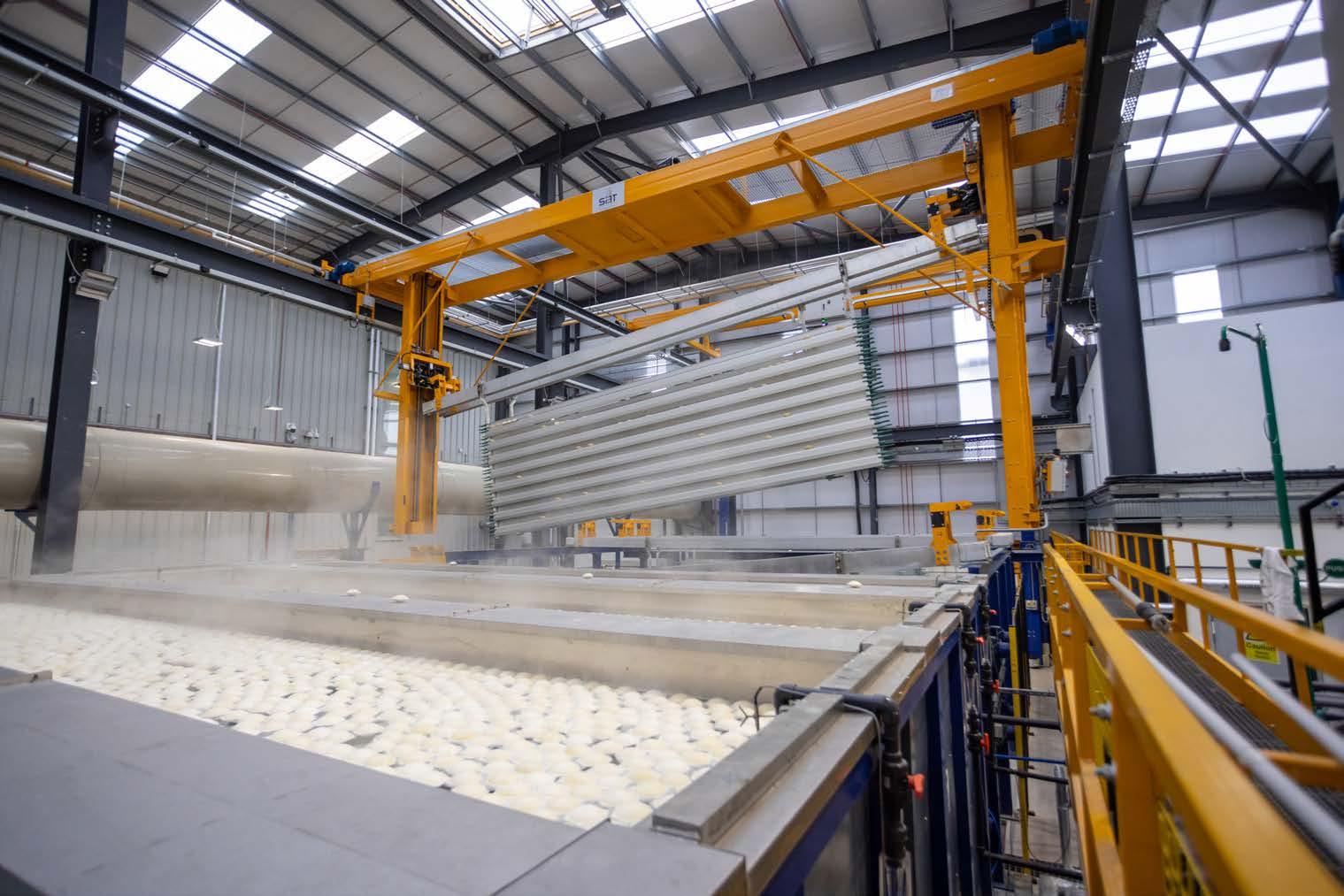

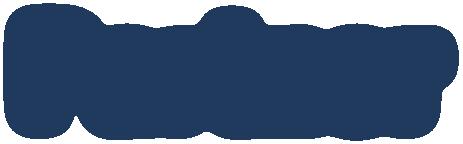
Research, Technology, and Innovation for a Sustainable Industrial Future
Alessandro Soba Verind S.p.A. – MilanOne of the most important objectives for laying the foundations of a more modern and sustainable industrial future is to consolidate the relationship between industry and academia: the seminar held at Politecnico di Milano, with the contribution of Verind S.p.A. and PPG S.r.l., for the university course in Advanced Organic Coatings was a perfect example of this.
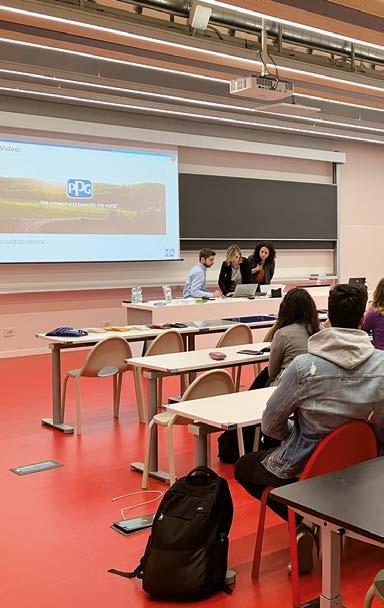
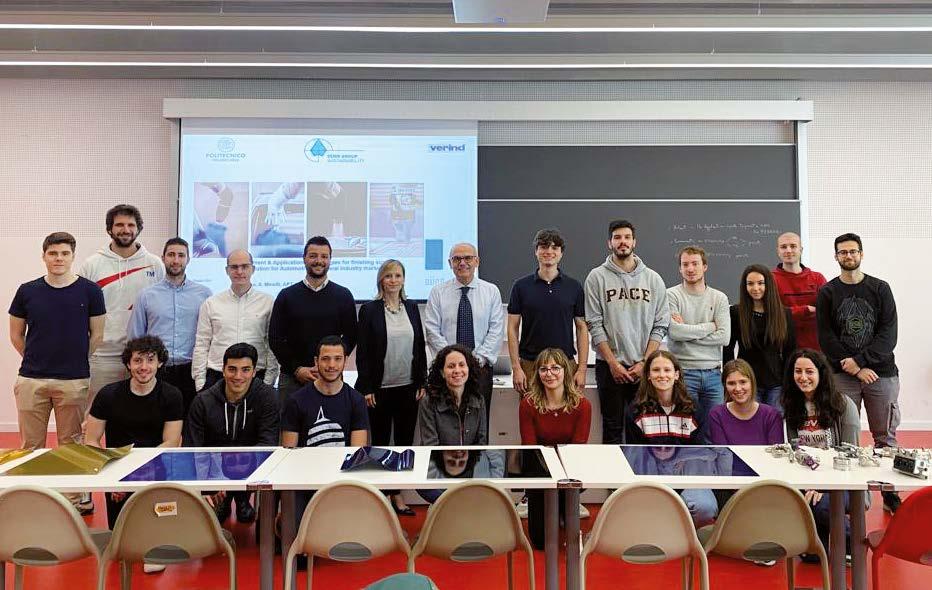
May and June saw the end of the second semester at Politecnico di Milano, Italy’s leading university for technical and scientific education and one of the top fifteen universities in the QS World University Rankings in the Engineering & Technology category1 The students of the Master’s Degree in Materials Engineering and Nanotechnology, aimed at training new technicians with a broad spectrum of knowledge in the fields of production, processing, and application of materials as well as in the more innovative field of nanotechnology, also had the opportunity to meet a few companies from the surface finishing industry.
1 https://www.topuniversities.com/university-rankings/university-subject-rankings/2022/engineering-technology
In particular, they examined a few industrial concepts applied to the automotive and industrial sectors:
• production of paint products and assessment of the quality of the applied film, with PPG;
• technologies and equipment for applying paint products, with Verind. The seminar held in English by Alessandro Soba from Verind S.p.A. (Dürr Group) and by Francesca Di Costanzo from PPG S.r.l. (Quattordio, Alessandria) for the Advanced Organic Coatings teaching course was a concrete example of the possible interaction between students and businesses. Led by Raffaella Suriano, associate professor at Politecnico’s Department of Chemistry, Materials, and Chemical Engineering “Giulio Natta”, the students were particularly interested and asked numerous
questions both during and at the end of the seminar. “I illustrated Dürr’s most innovative application technologies,” explained Alessandro Soba, “such as the EcoBell electrostatic device, the EcoDose 2k electronic dosing system using Coriolis mass flowmeters for 2k and 3k coatings, and the PIG and Robot Process Arm systems, all of which are solutions aimed at achieving consumption savings and higher efficiency in the painting process. Thanks to videos showing surface coating devices and plants used in the automotive and general industry sectors and to presentations of specific equipment for automatic and manual coating, we addressed several topics related to environmentally friendly application technologies with a view to sustainability, efficiency, and process digitalisation.”
“I presented PPG as a global leader in paints, coatings, and speciality materials,” explained Francesca Di Costanzo, PPG’s Colour Science Application and Quality Control Manager, “whose goal is to “protect and beautify the world” through its two industrial segments devoted to Performance and Industrial Coatings.”
This company’s mission includes three major drivers: Innovation, Sustainability, and Colour. The subject matter explored with the students was the Automotive OEM Business, with all the product lines included in the paint cycle of a car body, their functions, and of course their distinguishing feature: colour.
“Thanks to continuous classroom interaction” added Di Costanzo, “the students, together with some representatives of the Quality Control Lab
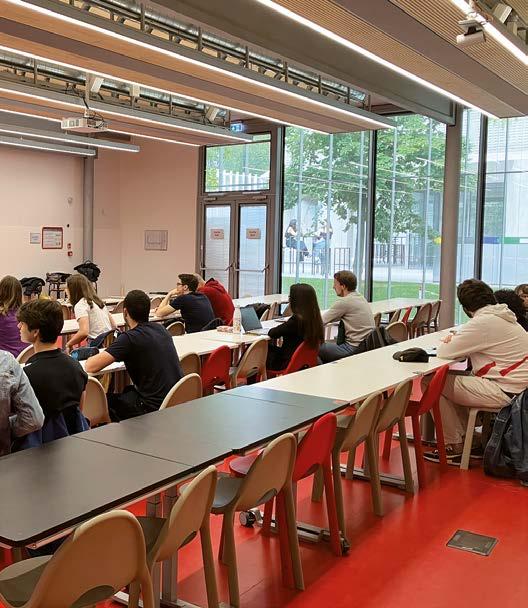
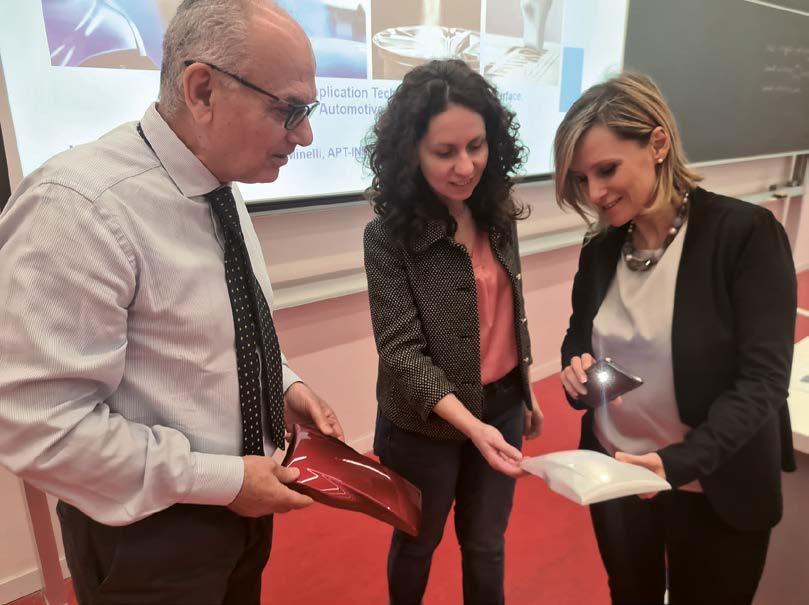
of the PPG plant in Quattordio, were able to see how certain defects typical of coating (craters, pinholing, sagging) and certain critical features are checked and tested during quality control operations.”
“Such a synergy between university and industry,” noted Raffaella Suriano, “was made possible thanks to the collaboration with PoliEfun, an association of the Politecnico di Milano university that promotes business culture in the surface treatment sector2. PoliEfun encourages the involvement of industrial players with the academic world also through in-person and online masters courses such as ISM10 (Industrial Short Master), now in its tenth edition, and TST2022, the digital conference that last year dealt with topics such as the circular economy and the development of sustainable bio-derived coatings obtained by recycling industrial agricultural waste such as tomato peels."
“Thanks also to the support of PoliEfun, the School of Industrial and Information Engineering of Politecnico, and the degree course in Materials Engineering and Nanotechnology, in this academic year 2022-23 the Advanced Organic Coatings teaching course has devoted 40% of its lecture hours to laboratory teaching, in order to further strengthen the skills and technical-scientific knowledge of future engineers with practical experience and experimental tests.”
2 https://www.poliefun.com/
ESG Criteria: From an Added Value to a Market Requirement
Manuela Casali, UCIF – Italian Surface Treatment Equipment Manufacturers’ Association, Milan, Italy info@ucif.netInterest in ESG, an acronym for Environmental, Social, and Governance, is not a recent phenomenon. Environmental and social transformations have long been the focus of companies and organisations. ESG issues were already being discussed back in 2005, although only recently do we have an abundance of data at our disposal to enable us to compile reports and statistics. What has changed substantially, however, is how companies today communicate their relationship with ESG criteria and their added value, to the point of making them not only a reputational issue but also and above all a commercial one. By realising that an increasing number of consumers are directing their choices according to ethical criteria, businesses have immediately responded by monitoring and defining parameters that can even contribute to compiling actual rankings of the most virtuous organisations. It is easy to imagine how from a parameter initially used by large companies to be more attractive in the marketplace, we are increasingly moving towards the focus on the same criteria and parameters by smaller organisations to demonstrate their environmental, social, and ethical commitment.
What is the state of the art in the mechanical industry?
Whether larger or smaller, there is now a growing conviction today that companies that can produce positive environment and societyrelated results are also better performers in terms of business results, in the long run. The letter E for Environment encapsulates various environmental criteria and values, with companies being assessed according to their environmental behaviours: for them, this means planning future investments and projects with a view to environmental
protection in terms of both company infrastructure and design of increasingly green plants. The letter S identifies the values related to the corporate activities’ social impact, considering not only the relations with employees, collaborators, suppliers, and customers, but also with the area in which the company operates, the community, and the people. Lastly, the letter G for Governance relates to a difficult subject, that of corporate management, which traditionally, in Italy, is seen as an aspect to be kept “confidential” and not communicated to the outside world, except for the obligations imposed by law. The issues under observation here include, for example, executive compensation, shareholder rights, and transparency in decision-making.
Are these new topics? Certainly not: there has been what we called “sustainable investment” before. The big difference between ESGdriven investment and sustainable investment, however, lies in the measurability of the former: every effort made and every action performed should have a positive and economically measurable return for investors and beyond – nowadays the focus is more and more on the community and the environment. In addition, apart from being measurable, the results produced should be understandable and clear. The outcomes of the environmental and social policies of a company or organisation working according to ESG criteria should be evident, bringing concrete improvements and data to support the actions taken. In the medium term, the collection of all this data is going to allow ranking companies based on what they declared compared to what they did. In fact, this is why it is more and more established that a virtuous company capable of producing positive results for the environment and society is also an organisation capable of achieving excellent business results in the long run.
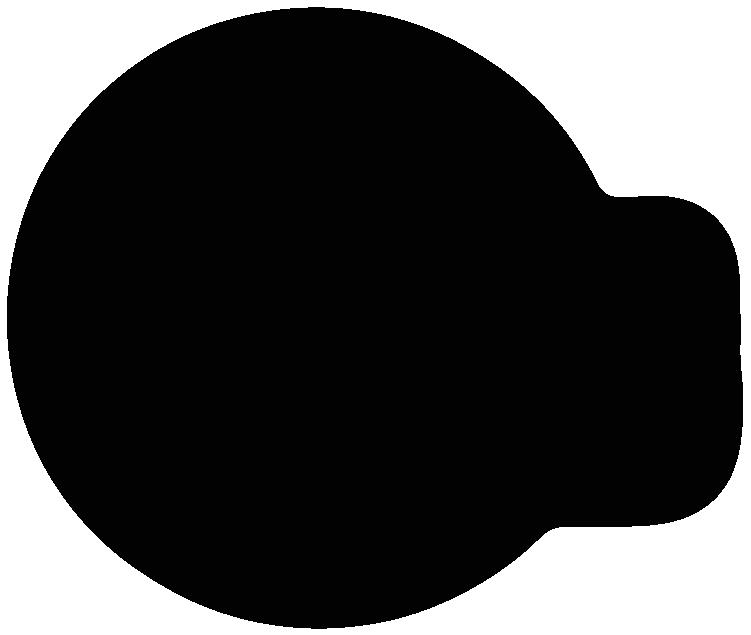
News and Developments in the Aluminium Business at the 12 th Aluminium Two Thousand
The next edition of Aluminium Two Thousand, which is organized in collaboration with ICEB World Congress, will take place from 19 to 23 September 2023 at the Royal Hotel Carlton in Bologna (Italy).
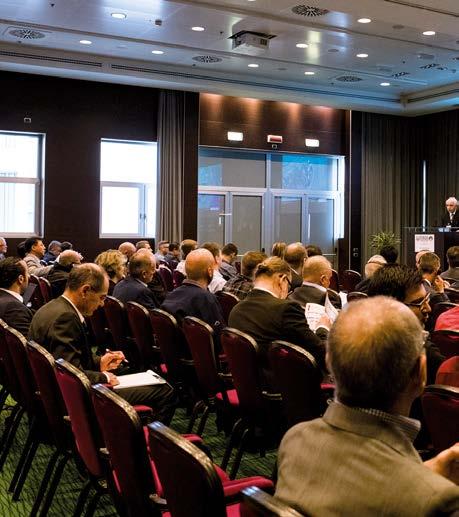
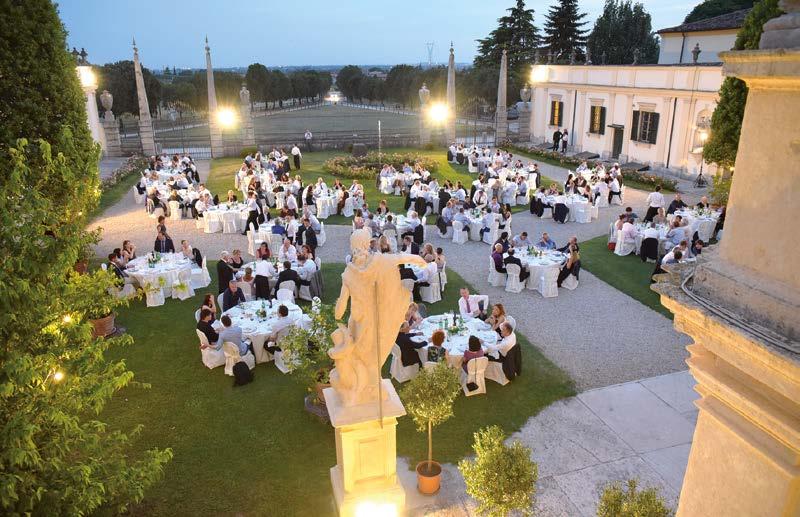
More than 80 highly qualified “aluspecialist” speakers from companies, universities and associations all over the world are coming together (as they have been doing every two years since 1990) to introduce the most innovative technologies and applications in the aluminium field to a specialised, international public.
Aluminium Two Thousand has become an irreplaceable networking occasion for all operators of the aluminium business (be it extrusion, foundry, melting, finishing or exhausted water treatment).
But how did it come to be? We asked its creator, Walter Dalla Barba, CEO of Italtecno Srl (Fiorano Modenese), president of Interall and of the Aluminium Two Thousand World Congress.
Walter Dalla Barba: “In the 80’s I used to attend international congresses about surface treatment and extrusion techniques, and I wondered why aluminium was only treated as one among many, despite it being the third most common element after oxygen and silicon and the most used metal (right after iron) to manufacture
millions of products. Fast forward to the end of 1988: having just come back from Paris Interfinish congress, I was talking with a longterm collaborator of Italtecno, journalist Velello Muratori, and another business partner of mine and we decided to organize ourselves a congress that would give due credit to this noble metal. We set the date of the first edition, March 1990, and the title, Aluminium Two Thousand, because of the nearing Y2K.
We had no way of knowing whether ten or a hundred people would have come to the Raffaello Hotel in Modena, and yet more than two hundred came, despite the odd Arab refusing to attend due to a lack of five stars hotels in the city.
Still, this made me realise we had attracted a high-end public and that our congress had to meet those expectations. We called in managers and businessmen from the most important businesses in the field, both from Italy and other manufacturing countries. And we were successful – not just with the scientific part, but also with the side activities we had planned: to get to north-west Sardinia, where we
would spend the following two days and nights, we had booked an entire Meridiana flight, but it was so full we had to leave some people out. Ever since 1990, all the activities we’ve offered – from gala dinners to sightseeing tours, from activities for those just accompanying to cooking classes (which Americans seem to really enjoy) – have gained more and more following”.
Who are the congress speakers?
Walter Dalla Barba: “According to topic, we have called in technicians from extrusion, anodizing, coating and melting companies, but also economists, like professor Cesare Garzia from Bocconi university, who are going to present their analysis of the trends and outlook of the aluminium business as well as the overlap with general economy.

We’ll talk about the different fields of application for extruded aluminium, about the issues with implementing various alloys and about applying aluminium to architecture, automotives, transportation, costume jewellery and furniture. We have indeed seen at the Salone del Mobile (Milan furniture expo) that aluminium is trending for home and office interior design. We’ll leave a lot of space to innovative technologies and scholarly research”.
About that, you have managed to have business and university meet through the synergy with the International Conference on Extrusion and Benchmark (ICEB), the biggest event in Europe for the newest development of extrusion
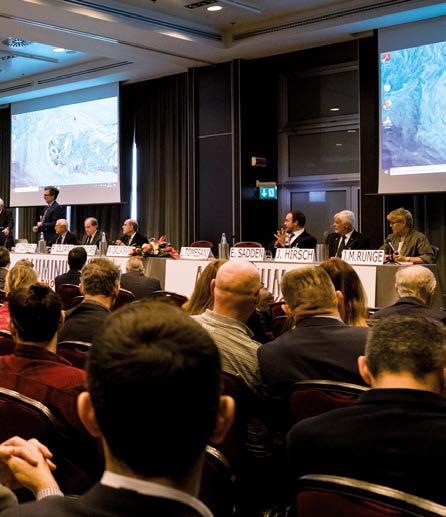
technology and its analysis through FEM simulation. When did the collaboration with ICEB first start?
Walter Dalla Barba: “It all began in 2003, when researchers from the Engineering Department of the University of Bologna came to our congress, which was in Rome that year. Now, ever since the 6th edition, we also host the International Conference on Extrusion and Benchmark, an event attended by researchers from all over the world which previously used to alternate between Bologna and Berlin. This is why I’m proud of my contribution, not just for enabling the highly desirable exchange between universities and manufacturers in a constructive, friendly setting, but also for bringing to Bologna the excellence of aluminium studies”.
What’s this year’s program?
For three whole days we’ll hold three parallel sessions to delve into the details of all topics. Each paper has been examined by the congress scientific committee in order to only select the most innovative studies and researches, the most recent manufacturing applications and the most interesting case studies.
At the same time, to ensure the best possible stay in Bologna, we’ll have entertaining side events every night: a gala dinner, an exclusive concert, a tour for accompanying people, a technical tour and a final, beautiful social tour through the charming historical cities surrounding Bologna, including Ravenna, capital of the Roman Empire from 408 to 476.
For further information: www.aluminium2000.com
Chicago – A FABTECH Kind of Town
The next FABTECH edition will take place from 11th to 14th September in Chicago (IL, United States).

led presentations that cover a wide range of technical topics for all finishing professionals. “It’s amazing how much the FINISHING Pavilion & Conference have grown since we became a part of FABTECH back in 2010,” notes CCAI Executive Director Anne Goyer. “The growth has been phenomenal since CCAI became the FABTECH Finishing partner and we are happy that the FINISHING Pavilion & Conference is set to exceed our pre-pandemic numbers as pre-registration numbers are very strong.” Training and education have always been at the forefront of CCAI’s mission. The conference program at FABTECH is the perfect platform for CCAI to showcase the expertise and knowledge of members and enlighten those who are new to the finishing industry or those who want to sharpen their skills and gain new insight. CCAI’s FINISHING Conference track features 27 sessions, encompassing a broad spectrum of technical presentations, from basic to advanced, addressing topics of interest for everyone involved in finishing technologies. Another highlight of the show will again be offered as CCAI marks its sixth edition of the FAB to FINISH Production Experience. The program gives attendees a first-hand opportunity to see a part produced from fabrication to finishing. Attendees can observe a souvenir part being laser cut and bent, then follow a production route to participating CCAI Corporate Member exhibitor booths to experience the part being cleaned, powder coated, and cured. Some routes will feature selective plating, while others will include coating thickness measurement. Each year the program grows in popularity as exhibitors and attendees alike want to participate.
FABTECH 2023 Finishing Conference Program and Finishing Pavilion Exhibitors
FABTECH returns to McCormick Place in Chicago, IL, from September 11-14. There is no better opportunity to explore the latest technology, share knowledge, network with industry peers, and gain insights into finishing and manufacturing trends that will help you prepare for what’s ahead. Everything you need for your finishing operations can be found all in one place in September. In their 14th year as a FABTECH partner, CCAI’s FINISHING Pavilion and Conference continue to thrive and offer great innovations and critical information on all aspects of industrial surface finishing. FABTECH provides a wealth of technology solutions, along with expert-
Take time to review the current FINISHING Conference Program and list of FINISHING Pavilion exhibitors found on the show website. To view the FINISHING Conference Sessions, select the “Conference” tab at the top of the home page and scroll down to SESSION DETAILS. Be sure to enter promotion code FINISHING30 to save 30% on your finishing sessions. You can view the complete list of FINISHING exhibitors on the CCAI website or select the Exhibitor Directory on the FABTECH website to view the floor plan or search the exhibitor list. Note that the FINISHING Pavilion and Conference sessions are located in the Lakeside Center East Building.
For further information: www.fabtechexpo.com
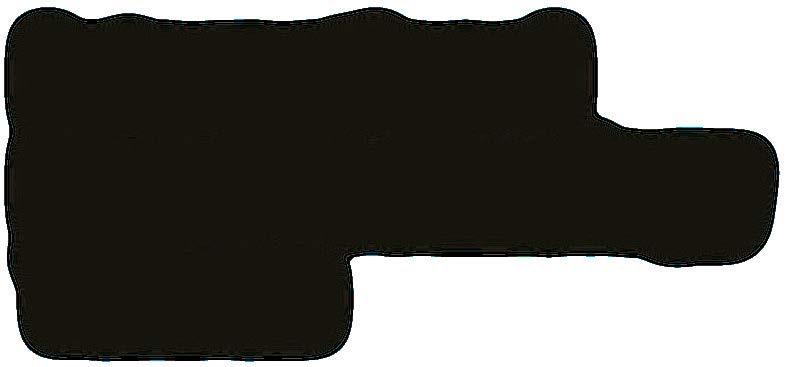

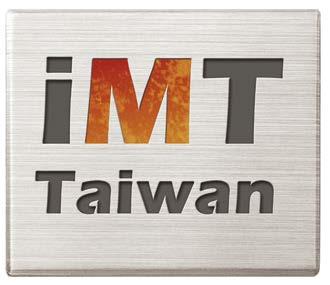
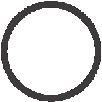

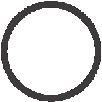

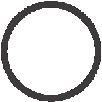

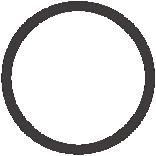
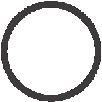

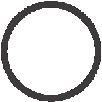
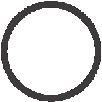
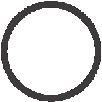

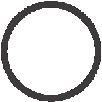
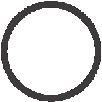
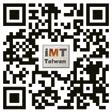
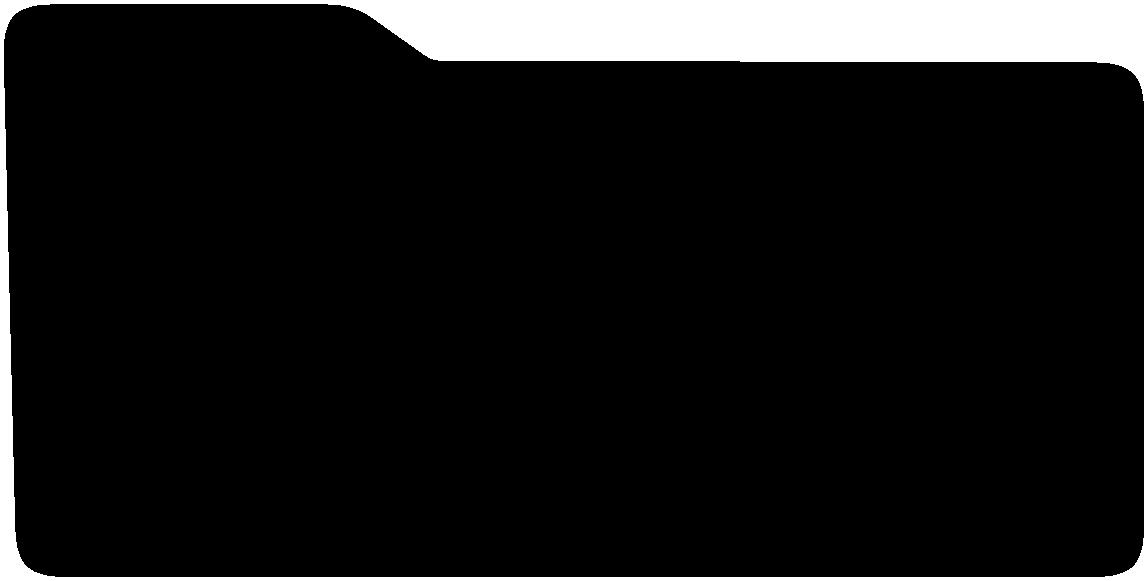
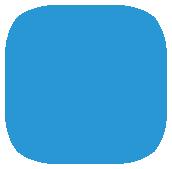
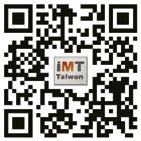

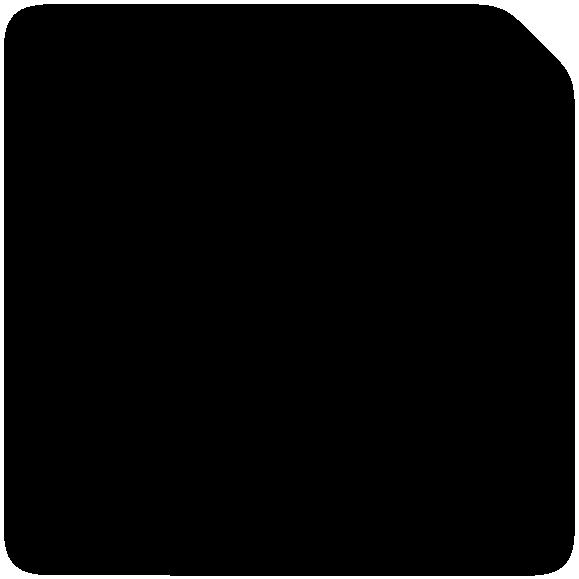
Current and Future Trends in Organic Coatings at the Conference Organised by the University of Trento
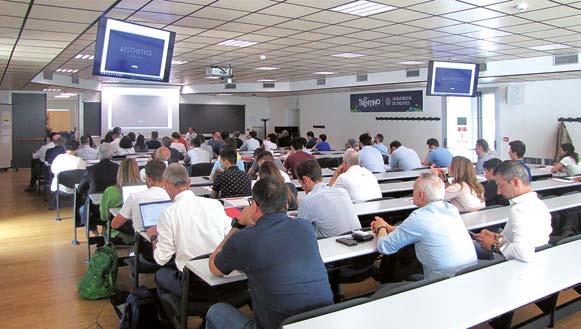
The future of organic coatings at a conference that brought together paint manufacturers and applicators and academia: the Department of Industrial Engineering at the University of Trento confirmed its strategic role in the research and scientific dissemination of the most up-to-date information to support the industry.
The first session of the day was opened by Lorenzo Soldavini from PPG Italia (Milan), who presented a talk about “High-performance powder coatings for corrosion protection”.
Maria Alba Fusco from Liberty Magona (Piombino, Livorno, Italy) gave a speech about “Reinventing steel for a sustainable future”, emphasising the importance of this material as a sustainable choice, thanks to its 100% recyclability, and of the research and development of energysaving solutions, such as the one her company designed together with the Laboratory to keep building roofs cool through the coating of a special coil.
“Alternative cataphoresis applications” was the topic of the report presented by Gian Luca Gazzola from Arsonsisi (Lainate, Milan).
Aconference about “Organic coatings, the solution for protection and aesthetics: trends and innovations in the sector” was held on 20 June at the Department of Industrial Engineering of the University of Trento (Italy).
Moderated by Professor Stefano Rossi, the head of the Coatings & Industrial Corrosion Control Laboratory, which has been collaborating with companies and research centres at the national and international levels for over thirty years, it was aimed at taking stock of the situation of organic coatings and understanding and discussing with several companies’ representatives what are the most complex challenges expected to be faced by this sector in future.
“Protection and aesthetics are longer enough,” stated Rossi during his introductory speech. “Today, coatings are required to do much more: reduce their environmental impact by becoming increasingly green, use raw materials from natural or recycled sources, add properties other than simple corrosion protection by increasingly becoming “smart coatings”, and create an infinite range of effects through colour and texture to the point of encompassing not only the sense of sight but also that of touch. To make the best use of paints not only based on their protective characteristics but also on their aesthetic-perceptive ones, it is necessary to be aware of the infinite possibilities that this type of coatings offer. This is why the Laboratory felt the need to organise this event together with some industrial partners.”
The first session of the conference ended with a presentation by Giovanni Ciafrè from Renner Italia (Minerbio, Bologna), “Wood coatings: a matter of aesthetics, protection, and application”.
After a coffee break and a visit to the stands of the event sponsors, CO.FO.ME.GRA, Liberty Magona, Nikon, Merck, and Pintarelli
Verniciature, the second part of the conference continued with the talk “What evolution can we expect for traditional building and corrosion protection coatings?”, presented by Gianfranco Di Tanna and Luciano Pau from the AITIVA Association of Piacenza.
Tiziana Pintarelli from Pintarelli Verniciature (Lavis, Trento) highlighted some of the problems encountered in the daily work of a coating contractor in her talk about “Paints, the applicator’s point of view”. Before the lunch break, the two reports by Stefano Corrado from Merck (Milan) and Francesca Valan from Valan Studio (Milan) concluded the second session, dealing respectively with “Pigments and colours in motion, a brief journey between emotion and innovation” and “Colour sustainability: timeless colours”.
In the afternoon, speakers and participants were able to visit the Department’s laboratories, equipped with the most advanced devices for the electrochemical characterization of surfaces and coatings, for accelerated ageing, surface abrasion resistance and microstructural characterization.
For further information: https://rb.gy/kv3uv
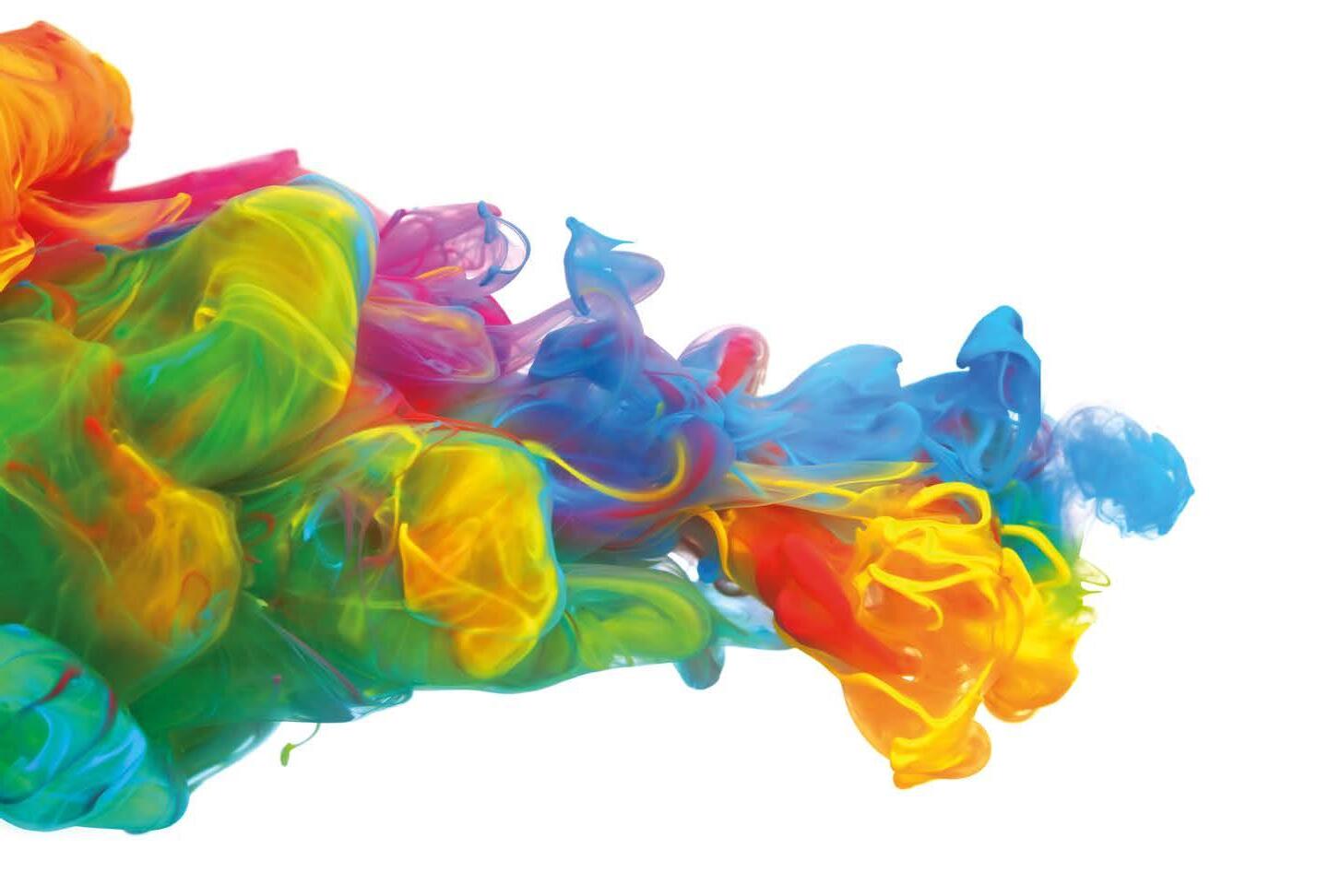
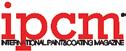

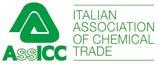

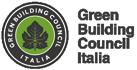
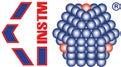
Redazione - Sede Legale:
Eos Mktg&Communication srl
www.eosmarketing.it - info@eosmarketing.it www.myipcm.com - info@ipcm.it
Via Pietro Mascagni, 8 - 20811 - Cesano Maderno (MB) - Italy Tel. +39.0362.503215 - Fax. +39.0362.1794768
EDITORIAL BOARD
Prof. Massimiliano Bestetti: Department of Chemistry, Material and Chemical Engineering, Politecnico of Milan –Section of Applied Chemistry and Physics
Prof. Paolo Gronchi: Department of Chemistry, Material and Chemical Engineering, Politecnico of Milan –Chemical Engineering Section
Kevin Biller: ChemQuest Powder Coating Research
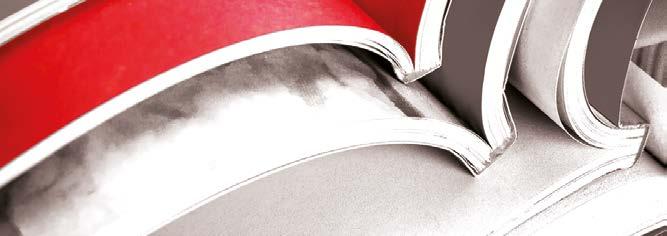
EDITOR IN CHIEF / DIRETTORE RESPONSABILE
ALESSIA VENTURI venturi@ipcm.it
EDITORIAL DIRECTOR / DIRETTORE EDITORIALE

FRANCESCO STUCCHI stucchi@ipcm.it
EDITORIAL OFFICE / REDAZIONE PAOLA GIRALDO giraldo@ipcm.it
MONICA FUMAGALLI fumagalli@ipcm.it
NICOLE KRAUS kraus@ipcm.it
MATTEO SOTTI sotti@ipcm.it
ILARIA PAOLOMELO paolomelo@ipcm.it
GABRIELE LAZZARI redazione@ipcm.it
EDITORIAL OFFICE AND GRAPHICS
ELISABETTA VENTURI grafico@ipcm.it
MEDIA SALES
FRANCESCO STUCCHI stucchi@ipcm.it
ILARIA PAOLOMELO paolomelo@ipcm.it
NICOLE KRAUS kraus@ipcm.it
CLAUS GÖRLICH goerlich@ipcm.it
The smart journal for surface treatments
This magazine is wrapped with a biodegradable and compostable film. Questa rivista è confezionata con un film biodegradabile e compostabile.
LAYOUT/ IMPAGINAZIONE ELISABETTA VENTURI
grafico@ipcm.it
PRINT/ STAMPA ROTOLITO SPA info@rotolito.com
Prof. Stefano Rossi: Material Engineering and Industrial Technologies, University of Trento - Product Design
Dr. Fulvio Zocco: Environment and quality
SUBSCRIPTION SERVICE - SERVIZIO ABBONAMENTI:
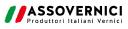
Sale only on subscription - Vendita solo su abbonamento E.mail info@ipcm.it
Subscription Rates 2023 - Tariffe Abbonamento 2023:
Annual subscription print + digital:
EMEA 110,00 € (postage included)
Rest of world 350,00 € (fast airmail shipping included)
Abbonamento annuale cartaceo + digitale:
EMEA 110,00 € (spese postali incluse)
Resto del mondo 350,00 € (spedizione via aerea inclusa)
Single copy: 15,00 € EMEA (postage included) - Rest of world (postage excluded)
Back issues: 30,00 € EMEA (postage included) - Rest of world (postage excluded)
Fascicolo singolo: 15,00 € EMEA (spese postali incluse) - resto del mondo (spese postali escluse)
Arretrati: 30,00 € EMEA (spese postali incluse) - resto del mondo (spese postali escluse)

Subscriptions can be made by bank transfer to the following account: Eos Mktg&Communication Srl IBAN IT97F0844033270000000084801 - SWIFT CODE CRCBIT22 or via payment online at: www.myipcm.com
Gli abbonamenti possono essere sottoscritti versando il relativo importo a mezzo b/b IBAN IT97F0844033270000000084801 intestato a eos Mktg&Communication Srl oppure con carta di credito direttamente dal sito www.myipcm.com
L’Iva sugli abbonamenti, nonchè sulla vendita di singole copie è assolta ai sensi dell’art.74 comma 1 lett. C DPR 633/72, DM 29/12/1989.
Registrazione al Tribunale di Monza N° 1970 del 10 Dicembre 2009Eos Mktg&Communication srl è iscritta nel Registro degli Operatori di Comunicazione con il numero 19244
POSTE ITALIANE S.P.A. – SPEDIZIONE IN ABBONAMENTO POSTALE –D.L. 353/2003 (CONV. IN L. 27/02/2004 N.46) ART. 1, COMMA 1 LOM/MI/4351

It is forbidden to reproduce articles and illustrations of “ipcm®” without authorization and without mentioning the source. The ideas expressed by the authors do not commit nor magazine nor eos Mktg&Communication S.r.l and responsibility for what is published is the authors themselves.
È vietata la riproduzione di articoli e illustrazioni di “ipcm®” senza autorizzazione e senza citarne la fonte. Le idee espresse dagli autori non impegnano nè la rivista nè eos Mktg&Communication S.r.l e la responsabilità di quanto viene pubblicato rimane degli autori stessi.
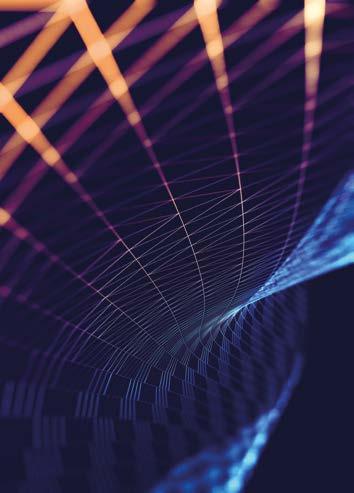
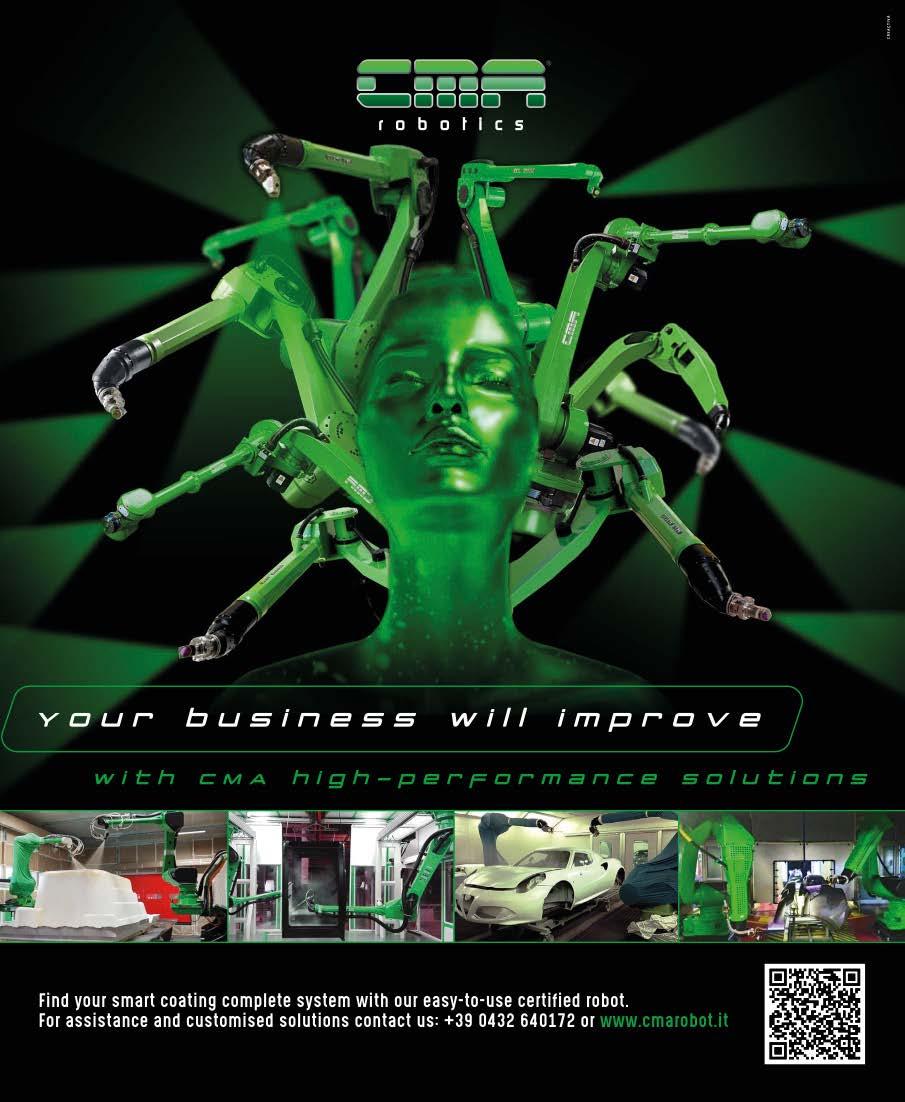
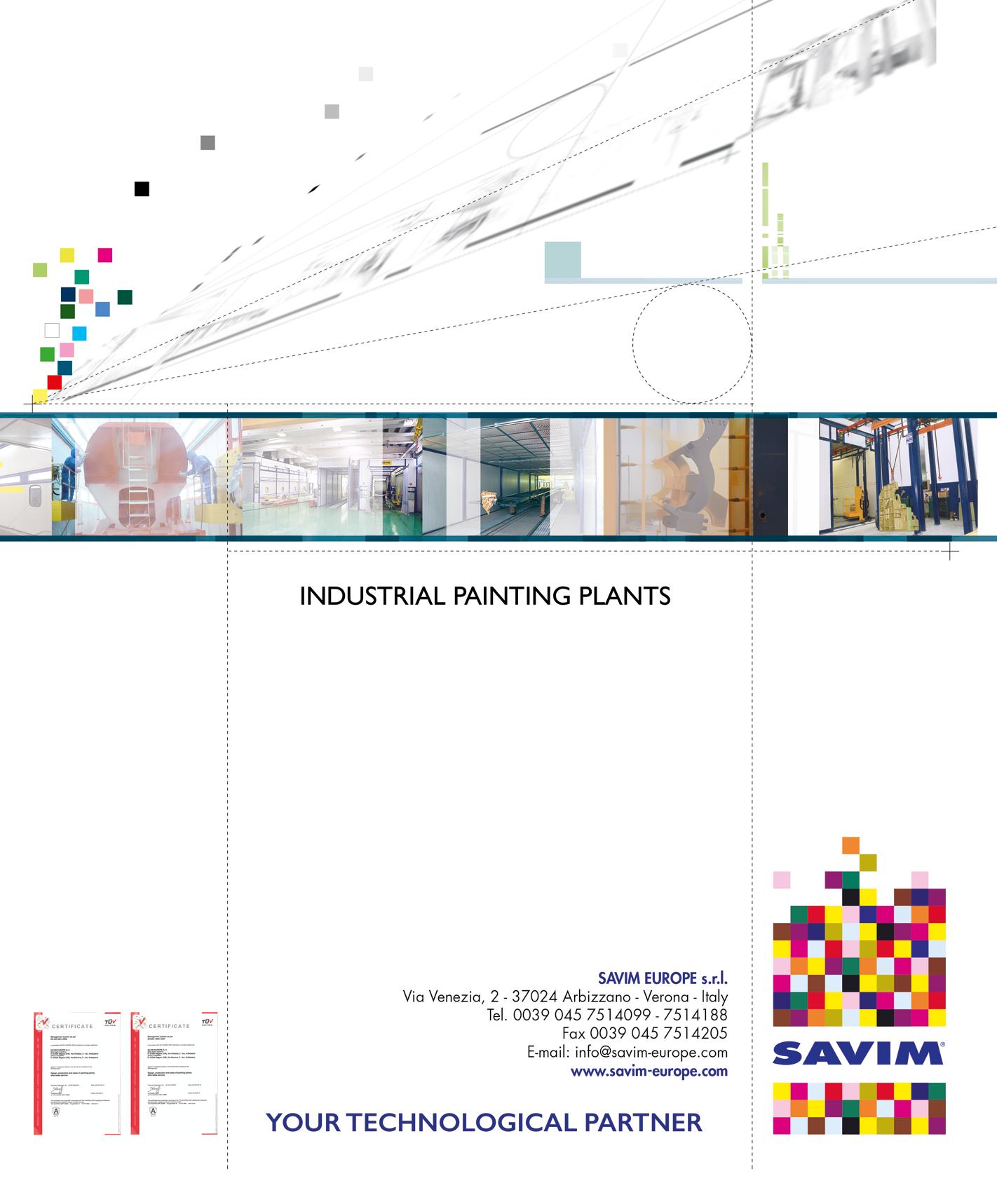