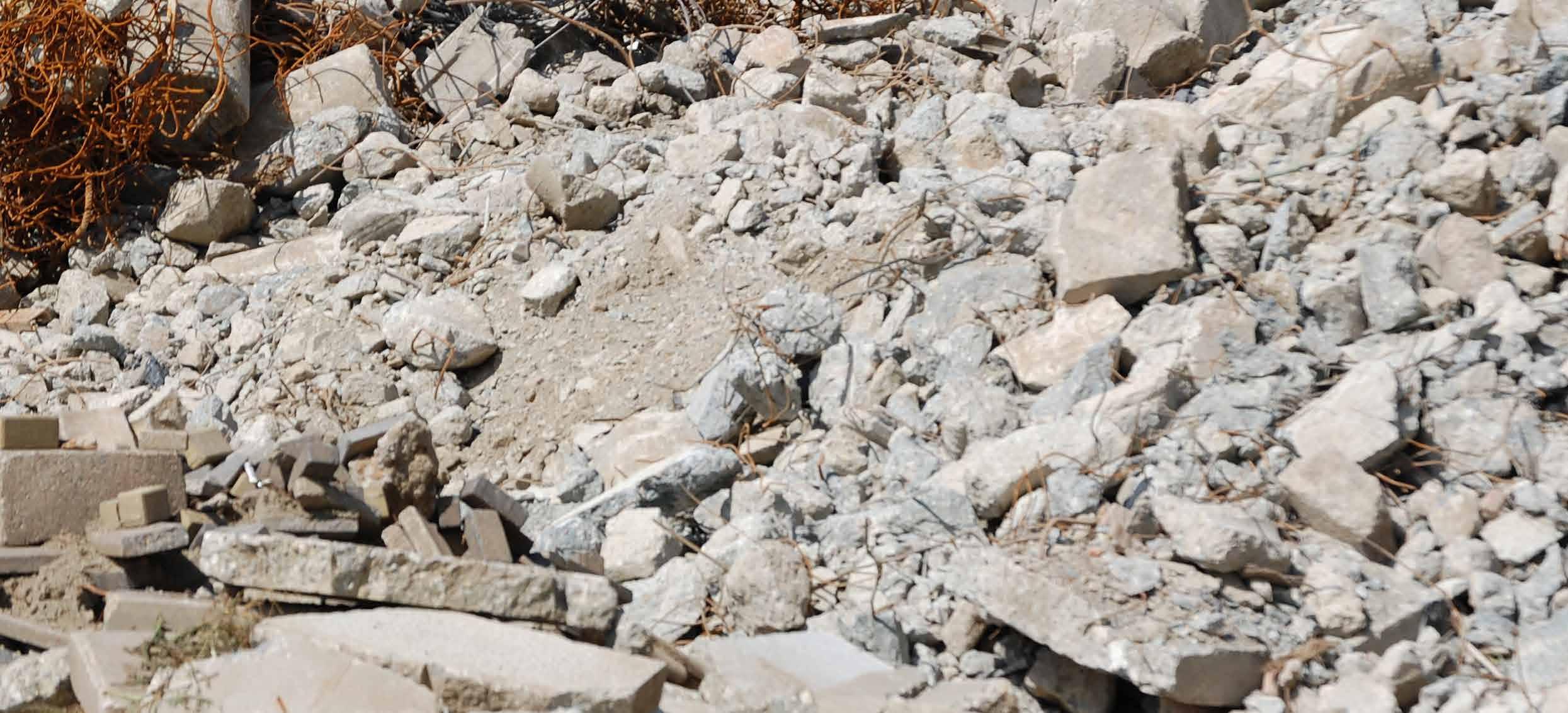
7 minute read
New smart cement: more sustainable roads and cities
from IM20214EN
Smart cement: more durable roads and cities
However it is built, it must be maintained and eventually renewed. Millions of tons of waste are released every year and new cement has to be produced, which causes extra CO2 emissions. In addition, the UN expects that by 2050 two-thirds of the world’s population will live in cities, which means that a huge amount of (concrete) buildings must have been built by then. To prevent a corresponding amount of CO2 -emissions as a result, these new cities and roads must be built with sustainable and smart concrete.
Advertisement
Engineers tackling this issue with smart materials typically enhance the function of materials by increasing the amount of carbon, but doing so makes materials lose some mechanical performance. By introducing nanoparticles into ordinary cement, Northwestern University researchers have formed a smarter, more durable and highly functional cement.
Cement is the most widely consumed material globally, with the cement industry accounting for 8% of human-caused greenhouse gas emissions. Aiming for cement composites with a reduced carbon footprint, the Northwestern Research team, lead by environmental engineering professor Ange-Therese Akono, investigated the potential of nanomaterials to improve mechanical characteristics. It is believed that nanomaterials reduce the carbon footprint of cement composites, but until now, little was known about its impact on fracture behaviour.
An important question was to increase the fraction of carbon-based nanomaterials within cement matrices while controlling the microstructure and enhancing the mechanical performance. Specifically, the team looked at the fracture response of Portland cement reinforced with one- and two-dimensional carbon-based nanomaterials, such as carbon nanofibres, multiwalled carbon nanotubes, helical carbon nanotubes and graphene oxide nanoplatelets. Nanomaterials are shown to bridge nanoscale air voids, leading to pore refinement, and a decrease in the porosity and the water absorption. An
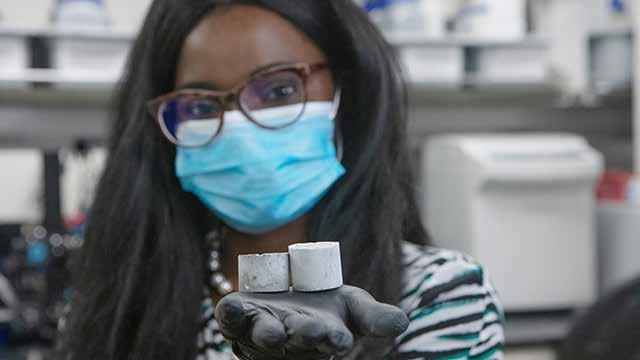
Ange-Therese Akono holds a sample of smart cement (Photo: Northwestern University)
improvement in fracture toughness is observed in cement nanocomposites, with a positive correlation between the fracture toughness and the mass fraction of nanofiller for graphene-reinforced cement. Thus, this study illustrates the potential of nanomaterials to toughen cement while improving the microstructure and water resistance properties.
More at Northwestern> The study, ‘Fracture toughness of one- and two-dimensional nanoreinforced cement via scratch testing,’ was published June 21 in the journal Philosophical Transactions of the Royal Society A. It is online>
A week of immersion in the world of 3D manufacturing!
December 6 to 10 2021, International multi-event – Benelux region
The International multi-event - 3D Delta Week - will be organized from 6 - 10 December 2021. The 3D Delta Week will create value for users and providers along the 3D Manufacturing Value Chain. It will be the 3D manufacturing meeting point for expert and layman, inside or outside the Benelux region.
The 3D Delta week is already gathering a dozen of renown events and will continue growing as the place-to-be, with activities aimed at specific sectors, at R&D and industry, at users and suppliers. The scheduling of events will allow participants to easily move from one activity to another. The Benelux area (the Delta) is a top region in terms of 3D production, with a myriad of academic and applied research centres, a particularly high number of 3D-printers and numerous promising start-ups and established enterprises. On the user side, the region boasts a multitude of application areas - all in all, an extremely versatile and high-quality ecosystem. Now, the appropriate podium has been created to bring this leading 3D production region to the fore.
The 3D Delta Week is an initiative initially set up by Brainport Eindhoven, Flam3D, Jakajima and Mikrocentrum.
www.3ddeltaweek.com
Ground breaking method for ReLiB-battery recycling
Researchers at the University of Leicester have developed a new method to recycle electric vehicle batteries using a totally new approach. This work was done by a Faraday Institution project on the recycling of lithium-ion batteries (ReLiB) led by Professor Andy Abbott at the University of Leicester.
The Faraday Institute was founded in 2017 and has since operated as the UK’s national research institute in battery science and technology. The Institute is mainly concerned with commercially relevant research needed for future battery development to power the transport and energy revolution for the UK. The Faraday Institute research is being conducted by or in collaboration with British universities, Leicester University in this case.
With current recycling methods, discarded lithium-ion batteries are typically
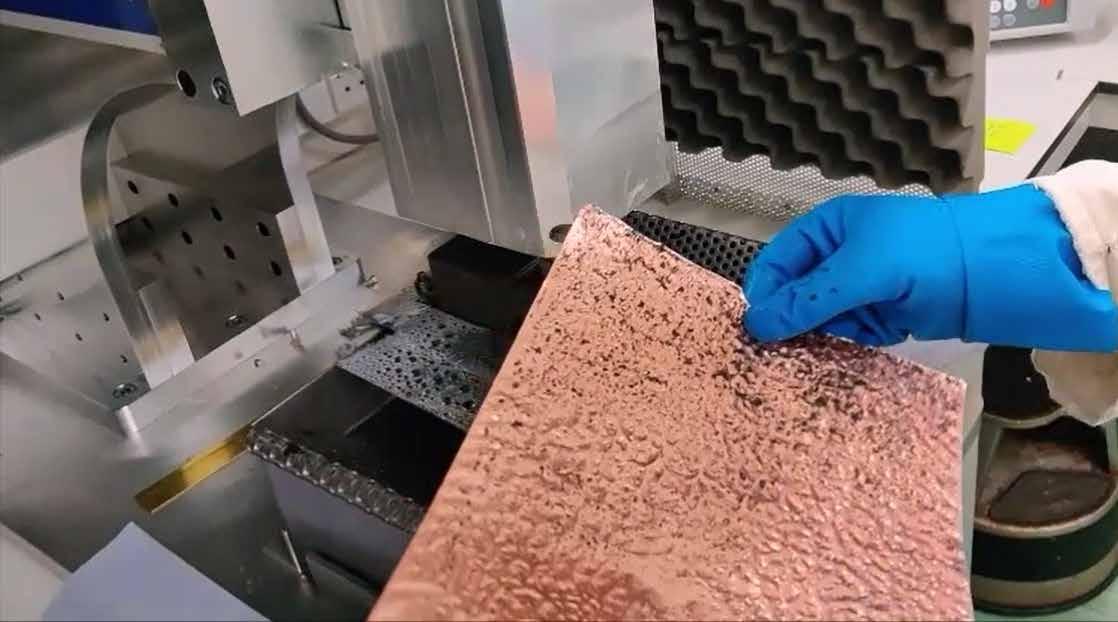
Photo: Faraday Institution, Leicester University
processed in a shredder or high-temperature reactor. Subsequently, a number of physical and chemical processes are required to recover the usable materials; a route that is very energy-intensive and inefficient. Abbott and his colleagues developed a new method, which uses high-power ultrasound. First, the batteries are disassembled and then the material is exposed to ultrasonic waves, causing cavitation and delamination of the various materials. The aluminium or copper electrodes remain behind. The process proved extremely effective in removing graphite and lithium-nickel-manganescobalt oxides, in short NMC. The research team further tested the technology on the four most common battery types and found that it performs with the same efficiency in each case.
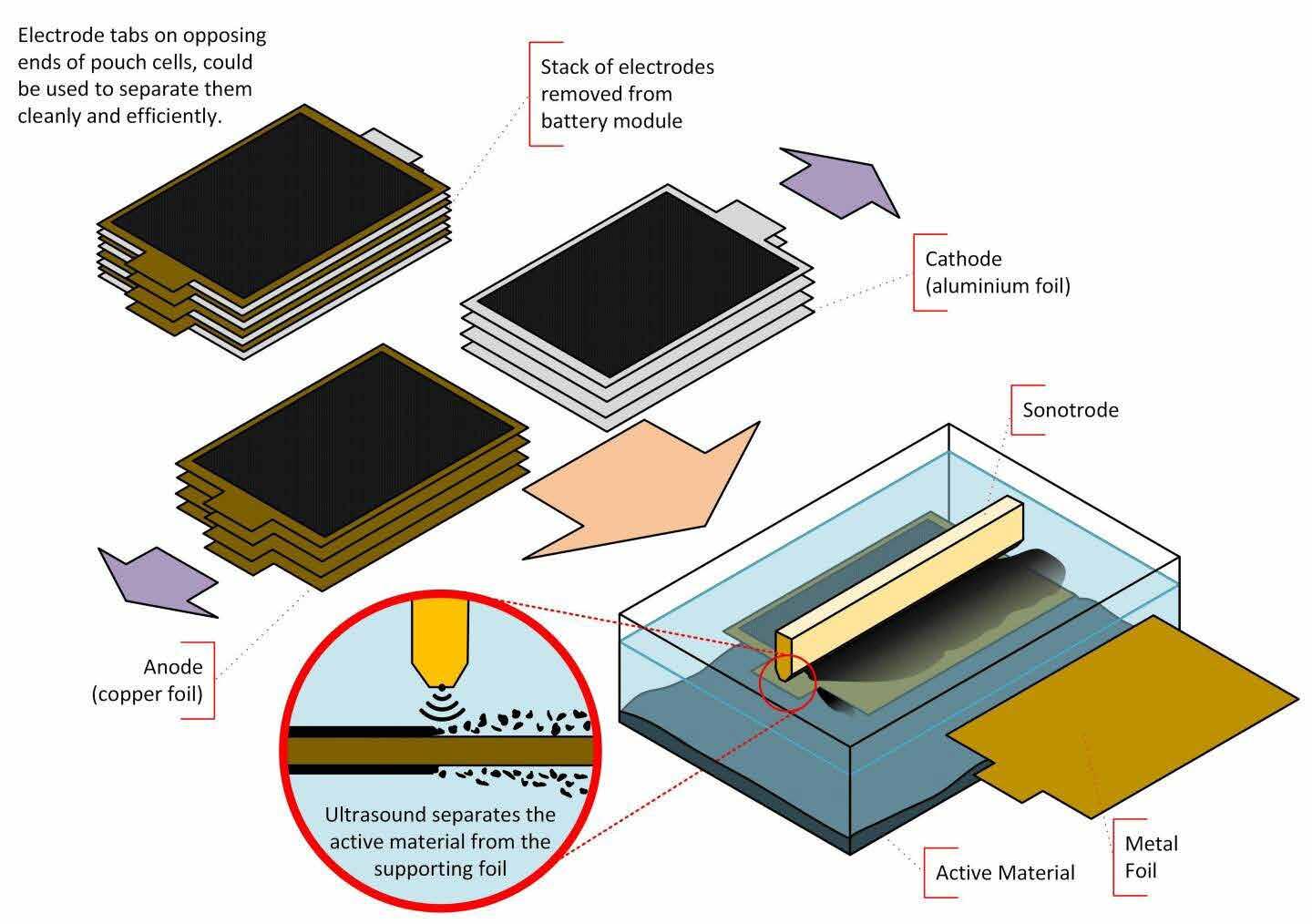
The results were published in Green Chemistry titled ‘ Lithium ion battery recycling using high-intensity ultrasonication’. It’s online>
Leicester University>
Diagram showing the ultrasonic process which assists in the delamination of lithium-ion batteries
Metallic wood 2.0
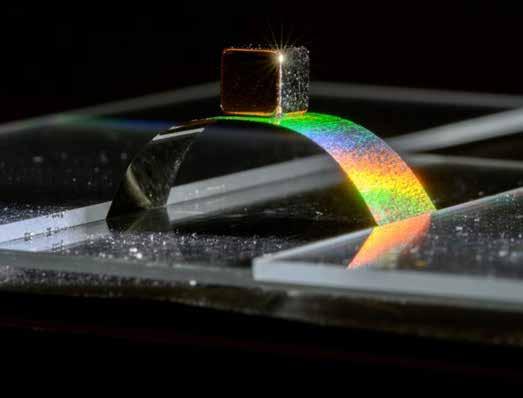
This strip of metallic wood, about an inch long and one-third inch wide, is thinner than household aluminum foil but is supporting more than 50 times its own weight without buckling. If the weight were suspended from it, the same strip could support more than six pounds without breaking (University of Pennsylvania’s School of Engineering)
For the past three years, engineers at the University of Pennsylvania’s School of Engineering and Applied Science have been developing a type of material called ‘metallic wood.’ As with wood, metallic wood is full of regularly spaced cell-sized pores that radically decrease its density without compromising the strength of the material. The precise spacing of these gaps not only gives metallic wood the strength of titanium at a fraction of the weight, but also unique optical properties, allowing the material to potentially be used for sensors.
However, there is a problem. Until now, it was impossible to produce the material in a usable size due to ‘reverse cracking’ during synthesis. An inverted crack, by contrast, is an excess of atoms; in the case of metallic wood, inverted cracks consist of extra nickel that fills in the nanopores critical to its unique properties.
These inverted cracks stem from the way that metallic wood is made. It starts as a template of nanoscale spheres, stacked on top of one another. When nickel is deposited through the template, it forms metallic wood’s lattice structure around the spheres, which can then be dissolved away to leave its signature pores. However, if there are any places where the spheres’ regular stacking pattern is disrupted, by cracks for instance, the nickel will fill those gaps, producing an inverted crack when the template is removed. In the aqueous environment in which the process took place, the surface forces of water flowing are so strong that they drive the particles apart and form cracks. These cracks are very difficult to prevent, so the scientists developed a new strategy that allows them to self-assemble the particles while keeping the template wet. This prevents the films from cracking, but because the particles are wet, we have to lock them in place using electrostatic forces so that we can fill them with metal.
According to Penn the new manufacturing approach makes it possible to create larger, more consistent strips of metal wood. According to Peen, this new opens the way to make porous metals that are three times stronger than previous porous metals at similar relative density and 1,000 times larger than other nanolattices which can by used as membranes to separate biomaterials in cancer diagnostics, protective coatings and flexible sensors.
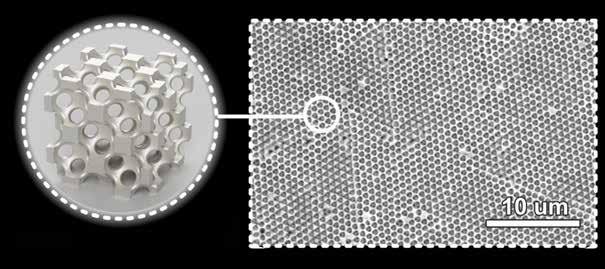