YEARS
Game changer in chemistry since 1998
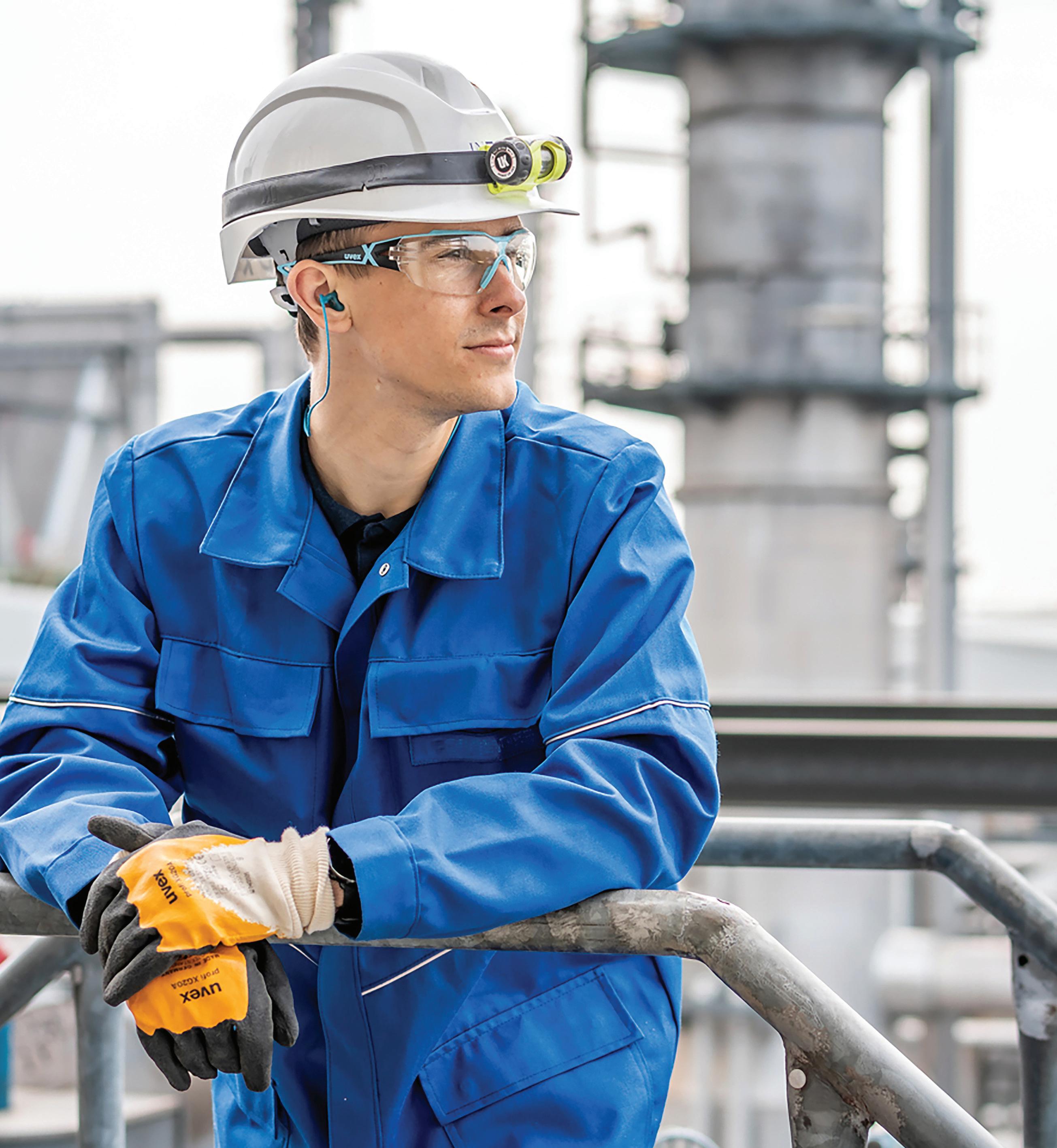
YEARS
Game changer in chemistry since 1998
Making the seemingly impossible possible. That’s what INEOS has been doing for 25 years. We arrived on the scene in 1998 in Zwijndrecht as a new player in an established sector, acquiring a chemical company with a turnover of 400 million dollars.
We have since grown into an industrial conglomerate with a turnover of 65 billion dollars, operating in the chemical, automotive, sports, fashion and hygiene sectors. What’s the reason for our success? Our employees. Open to change, they never take ‘no’ or ‘that’s not possible’ for an answer.
During those 25 years, we have made some bold moves. Like the 2005 takeover of Innovene, a company with a turnover three times larger than ours at the time. Or the virtual pipeline that we built between the US and Europe to bring gas to our continent. From constructing terminals to converting ships to transport gas, it was a feat we accomplished in just two years.
Or what about the multibillion-dollar Project ONE investment in Antwerp to build a state-of-the-art cracker with by far the lowest CO2 footprint in Europe. Being a private company means that we are able to make such ambitious – and maybe unconventional – investments without having to worry about the vagaries of the financial markets.
At INEOS, we prefer to steer clear of ‘corporate talk’ and formulating vague objectives. Instead of
using big words, we prefer to talk about our current work and past accomplishments. Growing steadily, we are adapting to the world and the opportunities around us, with a constant focus on sustainability. We are developing polymers that are easier to recycle, as well as working on hydrogen technology and CO2 capture. With an eye to demographic shifts, we are building up our foothold in Asian growth markets, alongside our existing activities in the US and Europe.
The INEOS corporate culture greatly resembles that of a 25-year-young start-up. Our organisation is run as a set of separate enterprises, with each business unit managed as an entity on its own.
Our hierarchy is extremely flat, and we have no corporate headquarters. This makes communication between the shop floor and the top very short, enabling decisions to be made quickly.
This approach means that our employees are given a lot of responsibility and remain committed to the exciting journey that we are on together. Looking back on the past 25 years, we are immensely proud of what we at INEOS have achieved together. We have made the seemingly impossible possible and are determined to keep on doing so. With perseverance and commitment. And with a healthy dose of humour.
Looking forward to the next 25 years of INEOS!
‘At INEOS, we do business with passion and commitment. We are ambitious, and challenge people to take their foot off the brake and discover their true potential. This philosophy brought us together 25 years ago and is what has held us together throughout our growth and diversification.
On 5 May 1998, no one could have predicted where we would be today.’
Sir Jim Ratcliffe, Founder and chairman of INEOS
predicted where we
At the port of Antwerp, INEOS is building Project ONE – a new ethane cracker – for which the chemical company has earmarked 4 billion euros. The investment is not only the biggest in the sector for a quarter of a century, but also symbolises belief in the European petrochemical sector.
‘Twenty years ago, Europe accounted for 27 per cent of worldwide investments in the petrochemical industry. That figure has since dropped to 12 per cent. A lot of investment has shifted to other regions, especially China.’ John McNally, CEO of Project ONE, makes no bones about it. ‘To secure the future of the petrochemical sector, you need investment. And when you invest, you do so in new technology.’
With its investment of around 4 billion euros, INEOS is underlining its belief in the future of the European petrochemical sector. Moreover, the company wants to restore the balance with the US
and Asia, regions where several new crackers have been built over the past few years.
‘It’s more than twenty years since an ethane cracker was built in Europe’, says Ralf Gesthuisen, Process Technology Manager at INEOS. ‘Unlike existing crackers, our plant is designed to achieve zero emissions, with most of the heat required generated using hydrogen, itself a by-product of the cracking process. Combined with the excellent energy efficiency of the new cracker, this will ensure a CO2 footprint more than twice as low as that of the next best cracker in Europe.’
The decision on where INEOS should make this giga-investment was not made overnight. ‘Bringing in our raw materials by ship, we need a deep harbour. Why the port of Antwerp? Because we have access to pipeline networks covering the whole of North-Western Europe and essential for transporting our products to our customers.’
A second reason is of a historical nature: INEOS was born in Belgium. ‘We have a strong presence here’, emphasises McNally. ‘Moreover, we know how business works here. We have good
By deploying the latest technologies and choosing ethane as its resource, INEOS’ ethane cracker has the lowest carbon footprint of all steam crackers in Europe by a large margin. Project ONE will produce ethylene with a carbon footprint of just 0.29 tonnes of CO2-eq per tonne of finished product. That is less than half of the 10% best performing plants or today’s benchmark (0.69 tonnes of CO2 per tonne of product).
‘Twenty years ago, Europe accounted for 27 per cent of worldwide investments in the petrochemical industry. That figure has since dropped to 12 per cent. A lot of investment has shifted to other regions, especially China.’
John McNally, CEO Project ONE
© R F
relationships with the port community. So when all the financial calculations fell into place, it felt like a good decision.’
Project ONE will mainly produce ethylene and propylene – the basic raw materials for the petrochemical industry. ‘You’ll find them in every application you can think of’, says Gesthuisen.
‘They are the building blocks for all kinds of key sustainable applications: lightweight materials for cars, lubricants for wind turbines, disinfectants and plastic water and gas pipes.’
‘Project ONE is set to produce more than 1.5 million tonnes of ethylene and propylene a year’, says Gesthuisen. ‘Per tonne of high value chemicals, we will produce less than half the average CO2 emissions of the top 10 per cent of steam crackers in Europe. This means we have also raised the bar for other chemical companies in terms of sustainability.’
A project of this scale is often complex when it comes to financing. ‘The business model for this ethane cracker is pretty straightforward’, says McNally. ‘We know that the plant will be profitable from the day it starts operating in 2026. Ethylene is a raw material that grows in volume in line with GDP, at around 3 to 4 per cent a year. And
demand for our products is set to increase even more as a result of the energy transition. Ethylene is also found in the film protecting solar panels and in lubricants and resins for wind turbine components, for example.’ The 21 financial institutions shouldering the financing also saw things that way. ‘We secured 3.5 billion from all those banks. That doesn’t happen without a solid business plan.’
A substantial part of the investment will benefit Antwerp and the rest of Flanders directly. ‘We have just announced a €100-million contract with local civil engineering companies to start phase two of the works’, says Gesthuisen. ‘The construction of underground pipelines, electricity installations and the road network is set to start soon.’
The new plant will also create new jobs. ‘The 450 highly qualified employees we need will be recruited locally. Besides, our activities create a multitude of indirect jobs. On average, for every direct job, our plants create a factor of five in terms of local jobs. 450 direct jobs thus means 2,500 further jobs’, says Gesthuisen.
McNally sums up the permit process as ‘extremely laborious’. ‘The application took 2 years of preparation by recognised environmental and safety experts, experienced engineers and architects. More than 1,000 pages long, it received
favourable opinions from all authorised advisory bodies. An appropriate assessment was delivered, leading to us being granted an execution permit. One year later (this summer), this was annulled on appeal by the court. The legal uncertainty for investments in Flanders is unacceptable. Europe is throwing away opportunities for innovative projects, instead driving potential investors to invest in regions where environmental requirements are a lot less strict. It’s a lose-lose situation for both local prosperity and the climate. However, as perseverance is part of our DNA at INEOS, we are currently working on a solution.’
‘We need to invest in new technology’, says McNally. ‘And the technology must be constantly challenged: what can we do better, how can we do things differently? But if you don’t build anything, you can’t achieve anything. You remain lumbered with 50-year-old plants that will have the same footprint tomorrow as they did fifty years ago.’
Will the new cracker in Antwerp be the only one, or are there others in the pipeline? ‘Never say never’, grins McNally. ‘I wasn’t thrilled when Jim Ratcliffe insisted on calling it ‘Project ONE’. I thought it was a very unsexy name. But naturally, a ‘project one’ implies that there may someday be a ‘project two’. But let’s get this cracker up and running first!’ The aim is for it to start operating in 2026, with construction taking around four years.
‘Unlike existing crackers, Project ONE is designed to achieve zero emissions.’
Ralf Gesthuisen, Process Technology Manager at INEOS© Studio Dann
At 4 billion euros, Project ONE is one of INEOS’ biggest investments. In terms of the investment volume, it is the biggest investment the Flanders Investment & Trade (FIT) agency has ever handled.
In 2020, Flanders Investment & Trade awarded Project ONE the Exceptional Investment of the Year Trophy. ‘Because it shows that investments can still be made in large-scale industrial projects in Flanders’, says Joy Donné, CEO of FIT. ‘This project is setting standards for future investments in terms of emissions and environmental norms. INEOS’ ethane cracker is one of the most efficient investments of its kind in the world and complies with strict European standards and regulations.’
‘INEOS is aiming for the cracker to be CO2-neutral within ten years of starting operations, scheduled for 2026. This makes Project ONE a trendsetter raising the bar for all the other crackers in Europe. A key prerequisite for achieving climate neutrality is the availability of sufficient climate-friendly and attractively priced hydrogen. This is currently not the case. But through Project ONE, INEOS has created market demand for sustainable hydrogen, thereby driving the energy transition.’
For the past two years, the chemical sector has been engaging in dual teaching, with sector employees combining their job with part-time teaching in schools.
In so doing, they share their valuable practical experience, motivate youngsters to take up scientific and technical professions, and help alleviate the shortage of teachers. INEOS employees Dimitri Lenaerts and Sari Walscharts tell us why they like teaching.
A production engineer at INEOS Oxide in Zwijndrecht, Lenaerts has worked in the chemical sector for ten years. For him, the teaching assignment is a great opportunity to share his experience with young people. ‘Every Wednesday, I stand in front of a class and talk about lab automation. When I was at school, I sometimes wondered what the use of a certain subject was. I now understand that only too well, meaning that I enjoy sharing those insights with my pupils.’
Walscharts works as a process engineer at INEOS Inovyn in Zandvliet. She is one of the STEMfluencers wanting to inspire young people to go into technology and science. ‘Via my guest lessons and interactive experiments, I want to show them that there is nothing mysterious about chemistry, that it’s involved in so many things belonging to our daily lives.’
The contact with students is the main reason why Lenaerts enjoys teaching so much. ‘It makes a nice change from my job, while teaching challenges you. You have to know the subject matter really well yourself before you can teach others. In my job, I am mainly focused on doing everything as efficiently and faultlessly as possible. In the classroom, you have to dare to turn the tables and
let pupils make mistakes. That is often the lesson that sticks the most.’
While Walscharts is a STEMfluencer, she does not consider herself a role model. However, she does believe that the fact that the teacher from the sector is a woman has an impact. ‘I like hearing at the end of my lesson that the girls are also open to technical training. Filling as many young people as possible with enthusiasm for chemistry is basically the reason why we’re doing this.’
Most of the questions they get asked are about what the work entails. ‘“Operator in the chemical sector” is an extremely vague description and means something different in every company’, explains Lenaerts. ‘Almost all my pupils have family members who work in the chemical sector. They often know about the attractive employment conditions, but I always say that this should not be the main reason for choosing the sector. Above all, I give them concrete tips that will give them an edge in the workplace later on. That way, I can motivate pupils – and that makes for well-qualified applicants for jobs.’
Schools are also extremely enthusiastic about the system. ‘There are not enough specialist subject teachers. By teaching a few hours a week, we are helping to alleviate that shortage’, says Lenaerts. ‘I am a big fan of combining teaching and working in the field’, concludes Walscharts. ‘It’s the best way to give young people a good idea of what they can do later on.’
‘I want to show them that there is nothing mysterious about chemistry, that it’s involved in so many things belonging to our daily lives.’
Sari Walscharts, Process Engineer at INEOS Inovyn
‘In my job, I am mainly focused on doing everything as efficiently and faultlessly as possible. In the classroom, you have to dare to turn the tables and let pupils make mistakes.’
Dimitri Lenaerts, Production Engineer at INEOS Oxide© Christophe Ketels © Christophe Ketels
For a chemical giant like INEOS, R&D is very important, especially in a world in which sustainability is a priority for the consumer, society and the legislator.
‘Belgium plays an important R&D role within INEOS’, says Serge Bettonville, R&D Director at INEOS Olefins & Polymers. ‘But we don’t just work for our Belgian plants in Neder-Over-Heembeek. Our expertise is valued by the whole group.’
‘The fact that INEOS in Belgium puts such a focus on R&D has to do with the history of our sites but also with the expertise of our employees, the highly skilled labour market and the excellent researchers and universities we can collaborate with’, adds Dirk Dompas, Research, Technology & Engineering Manager at the PVC-producing INEOS Inovyn plant in Jemeppe-sur-Sambre.
The agendas of both researchers are strongly influenced by rapidly evolving laws and legislation. ‘The results of our research are noticed by consumers every day – for example, the caps now attached to drinks bottles, are a result of the new EU Directive on Single-Use Plastics’, says Bettonville.
‘Carbon footprints and recyclability are now just as important to our customers as price and quality’
‘At a customer’s request, we developed a special PVC foam for use in wind turbine blades.’
Dirk Dompas, Research, Technology & Engineering Manager at INEOS Inovyn
© Studio Dann
For a long time, polystyrene products – from food packaging and drinking cups to toy building bricks and vehicle components – ended up on a landfill site or in an incinerator at the end of their life cycle. Research into alternative recycling methods has been going on for years. As Head of Global R&D Laboratories at INEOS Styrolution, Michiel Verswyvel is closely involved in advanced recycling projects.
‘One of the new recycling techniques is depolymerisation. A high proportion (up to 90%) of the plastic waste collected from households is shredded, washed and transformed at high temperature into a brownish styrene oil. This is then purified to produce styrene which can be reused to make new products’, explains Verswyvel at the Zandvliet site at the Port of Antwerp.
‘Featuring the same properties as new material, the recycled plastic is suitable for applications requiring a high level of purity such as food packaging, toys or medical applications. At the end of its life cycle, that plastic can be recycled again. All this means that less crude oil is required, while greenhouse gas emissions amount to less than half in comparison to materials based on fossil resources.’
‘But it is not just packaging legislation that is driving research’, says Dompas. ‘The pursuit of carbon neutrality and the desire to develop a hydrogen business are further drivers, as is the goal to fully recycle all PVC waste.’
PVC is now one of the most recycled polymers in Europe thanks to the VinylPlus initiatives supported by INEOS Inovyn. The company is involved in a programme for developing advanced recycling technologies at its R&D centre in Jemeppe-surSambre.
Although a big challenge, the combination of regulations and business is leading to exciting R&D. ‘We can no longer separate the social and industrial motives determining our R&D’, Bettonville points out.
‘A product’s carbon footprint and recyclability are now just as important to our customers as its quality and price.’
The research and development of such products and sustainable solutions is extremely diverse. INEOS Olefins & Polymers is busy working on the
‘Thanks to our polyethylene pipes, gas and drinking water can be safely transported to our homes, while hydrogen can be transported for use in industry.’
Serge Bettonville, R&D Director at INEOS Olefins & Polymers
further development of polyethylene pipes set to play an important role in the energy transition.
‘These pipes are used for example to bring gas and drinking water to our homes safely. We have developed them further to bring green and renewable electricity from offshore wind farms to the mainland’, explains Bettonville. ‘When high-voltage cables run underground, they need protective sleeves able to withstand temperatures of 60 to 70 degrees Celsius, with even higher peaks.’
‘We have recently proven that our polyethylene pipes can also safely transport hydrogen, the fuel of the future. This is of crucial importance as green hydrogen can now be gradually fed into existing distribution networks to fuel our industry without having to completely rebuild the distribution network.’
INEOS is also committed to Design For Recycling: the development of simplified packaging structures that are easy to recycle. Bettonville puts it this way: ‘Over time, packaging has become more complex in order to guarantee effective protection. This has led to a multi-layered structure of various materials, but difficult to recycle. As a result, the packaging gets sent to landfills or is incinerated. At our R&D
centre in Brussels, we are developing films that are easy to recycle, without compromising the shelf life of food or violating food safety regulations.’
With the chemical industry a major energy consumer, there is much to gain here as well –through decarbonisation, for example. In its Electra Project, INEOS is developing a new technology to electrify the thermal cracking of dichloroethane – one of Inovyn’s intermediate products – at its Rafnes plant in Norway. ‘If the project is a success, the plant’s CO2 emissions will be reduced by 16,000 tonnes a year. Moreover, the technology will have significant potential for use at other locations’, says Dompas.
Another example of the efforts being made to improve energy efficiency at INEOS Inovyn is the brine concentration process at the Tavaux plant, where the necessary steam is now being generated by electricity instead of gas. ‘This will lead to a reduction in the plant’s primary energy consumption of more than 200 gigawatt hours and a reduction in CO2 emissions of more than 60,000 tonnes a year.’ Further projects in the pipeline should ensure that carbon emissions will
be reduced by 33 per cent by 2030, and by 100 per cent by 2050.
As a producer of plastics, INEOS is constantly innovating with new and sustainable applications for PVC, a plastic now used in many different forms: from classic pipes and window profiles to medical applications, vehicles, flooring, roofing, cables, etc.
‘At a customer’s request, we developed a special PVC foam resin for use in wind turbine blades. With blades getting longer and longer – up to 100 metres –, they need to be both light and sturdy, meaning that foam is the ideal solution’, says Dompas.
INEOS has also developed a PVC film to protect the steel masts of wind turbines against corrosion.
‘Wind turbines are exposed to harsh weather conditions which take their toll, especially in offshore wind farms. Covering the masts with PVC film makes them last longer and reduces maintenance –an expensive and difficult job at sea.’
Wall coverings made from recycled medical products: this completes the circle for PVC reuse in the medical world as well.
PVC resin produced by INEOS Inovyn in Jemeppe-Sur-Sambre is used to make medical products such as masks, tubes and IV bags. Today, these recyclable products are being
collected from ten Belgian hospitals to be processed and reused in vinyl wall coverings.
‘This is a hygienic and solid material that is resistant to chemicals and can take a beating from a bed, for example. Perfect for a hospital environment’, says Jean-Pol Verlaine, customer technical service at INEOS Inovyn.
Several recycling companies are working on the project. ‘This way, medical waste, which is otherwise incinerated in hospitals, gets a second life. Sorting and recycling plastic waste can significantly reduce both the environmental impact and expenses of hospitals that are related to waste.’
The chemical sector plays a key role in making our society more sustainable. But the circumstances under which this is taking place are by no means ideal, according to Ann Wurman and Hans Casier, respectively director essenscia Flanders and chairman of essenscia, the Belgian sectoral federation for the chemical industry. ‘If we are not careful, we will have a Green Deal on paper but lack the clout to achieve the ambitions within it.’
‘We need the chemical sector in order to realise the Green Deal’
Belgium has been home to the chemical sector for more than 150 years. Together with life sciences, chemical companies provide one of every five jobs in the country’s manufacturing industry. In 2021, they achieved a record turnover of just under 74 billion euros. Traditionally, the sector also invests heavily in innovation and development. Yet that added value only seems to be reflected in the sector’s image to a very limited extent.
‘Our public image could certainly be better’, says Hans Casier, who is also CEO of INEOS Phenol and INEOS Nitriles. ‘People may not realise it, but 95 per cent of all the products that you buy and materials that you use are linked directly to the chemical sector. We make crucial building blocks and basic components needed by other sectors to make their products.’
Ann Wurman: ‘Contrary to what many people think, the chemical sector is not the problem but a part of the solution. The products emanating from the chemical sector are necessary for us to achieve a sustainable future. Take for example insulating materials for use in
construction, or solutions to make vehicles lighter, to extend the life of batteries or to recycle products for the circular economy. Naturally, as we are at the beginning of all those value chains, we are less visible.’
Can the energy-intensive chemical industry continue to play that role despite higher energy and other costs?
Hans Casier: ‘Companies in Europe pay a lot more for their energy than their competitors around the world. Belgian companies are also hit by the automatic wage indexation which drives up wages. Similarly, our industry has to compete against large-scale support programmes in other EU Member States and other parts of the world. There is an urgent need for a level playing field to prevent the distortion of competition between countries.’
Ann Wurman: ‘Hans is referring to the US Inflation Reduction Act. While it has protectionist traits, it also encourages investment and rewards entrepreneurial risk-taking. The European approach – which is also reflected at Flemish and federal level – is based on a tight
4.5% Chemistry and life sciences are economic heavyweights, accounting for 4.5% of Belgium’s GDP.
5.8 billion euro
The sector remains committed to research and development. In 2022, investments amounted to 5.8 billion euros.
1,071
With 1,071 patent applications, 2022 saw the highest number of applications ever filed from the sector, accounting for a 41% share of all Belgian applications.
‘The European approach is not favourable to entrepreneurship at a time when companies are faced with huge investments and major technological challenges.’
Ann Wurman, Director Flanders at essenscia
framework of rules and regulations, restrictions and extra costs. That is not favourable to entrepreneurship at a time when companies are faced with huge investments and major technological challenges.’
Hans Casier: ‘In addition, we have few energy sources of our own in Europe, which means that we have to invest in infrastructure to get energy to us. But the EU is too much stick and not enough carrot – if at all. Europe also has to put up with a lot of red tape and is not technology-neutral in the quest for and transition to carbon neutrality. By contrast, the US is extremely dynamic. Support there is targeted, regardless of the solution chosen, be it for renewable energy or carbon capture and storage (CCS). As a result, the US has invested heavily in solar and wind farms, hydrogen and ammonia production and CCS. Europe risks burdening industry so much that it quits the continent.’
What does the sector need to ensure its future?
Hans Casier: ‘The industry needs a clear framework within which technological choices are not made in advance and no detailed plans are prescribed. The industry can decide for itself what works and what doesn’t. But above all, the support should be the same in every country, without too much red tape.’
Ann Wurman: ‘That is why essenscia advocates working towards a more efficient licensing policy in order to realise the crucial industrial
and logistical infrastructure. We must also ensure that we can continue to attract well-trained talent. Finally, we need ongoing innovation support so that new technologies can continue to be brought to the market.’
As well as driving innovation, the chemical sector has a key social role to play. Can you provide some figures to back this up?
Hans Casier: ‘Flanders has the biggest petrochemical cluster in Europe, accounting for 65,000 direct and more than 210,000 indirect jobs. Year after year, employment in the sector has gone up, with no less than 1,900 jobs added in 2022. Social security contributions total 2.6 billion euros, a figure unrivalled by any other sector. The chemical and pharmaceutical sector is also an export champion, accounting for 37 per cent of Belgium’s total exports.’
Ann Wurman: ‘Likewise, the figures speak for themselves as far as investments are concerned. A third of all industrial investments in Belgium are made by petrochemical companies, mostly foreign ones. According to Flanders Investment & Trade (FIT), foreign companies announced a record 5.26 billion euros worth of investments in Flanders in 2022, with chemical and pharmaceutical companies accounting for almost half of that amount. Over the past three years, the chemical and pharmaceutical sector in Flanders has attracted 115 foreign investment projects, accounting for more than 2,000 new jobs.’
‘CO2 is a chemical molecule. We are the sector for coming up with a solution to the CO2 problem.’
Hans Casier, Chairman of essenscia and CEO of INEOS Phenol and INEOS Nitriles© Studio Dann
1/3rd
The sector is export champion in Belgium, accounting for more than 1/3rd of total exports.
100,000
Since 2012, the sector has added 11,600 jobs, a growth of 11%. Today, the industry has 100,000 employees.
50%
In the long term, the sector continues to grow, for example, the sectoral trade balance has increased by more than 50% in ten years.
More investment, more activity and more production often also involve a greater environmental impact. Can you see the chemical sector becoming net zero by 2050?
Hans Casier: ‘We are convinced that the sector is important for both the prosperity of our country and the transition to a sustainable economy. That transition is under way, with companies investing heavily to make their operations more energy-efficient and climatefriendly. As an engineer, I believe in technological solutions. CO2 is a chemical molecule. We are the sector for coming up with a solution to the CO2 problem. But obviously, the question is whether any such solution is feasible and affordable.’
Ann Wurman: ‘I am optimistic too. I come from the industry myself and we owe it to ourselves to strive for climate neutrality. And that is exactly what we are doing. Since 1990, total production of chemicals has more than tripled, while energy consumption has only gone up by 40 per cent. In other words, energy efficiency has increased significantly. CO2 emissions have halved since 1995, despite the growth of our activities.’
Hans Casier: ‘Flanders is and will remain world-renowned as a leading chemical and pharmaceutical region, whether for innovation, production or logistics. But we need to move up a gear if we are to remain an attractive location for investment.’
Ann Wurman: ‘The investment decisions made in the next few years will determine our country’s industrial future. These decisions are often not made in Belgium but rather in international headquarters where investment strategy is carefully weighed up. Hence the need to strengthen our international competitiveness and come up with an industry policy with a long-term vision.’
A legend among beer-lovers, the De Halve Maan brewery has been brewing beer in the historic centre of Bruges almost non-stop for more than five centuries. And thanks to a plastic solution from INEOS, it can carry on doing so in a sustainable way.
For De Halve Maan, it is crucial to be able to continue brewing its beers at its historic brewery. To preserve that heritage and still be able to grow, a sustainable solution was needed to do away with the need for lorries to drive back and forth between the brewery in the city centre and the bottling plant in the Waggelwater industrial park. Hence the decision to construct an underground pipeline to pump the beer from the brewery to the bottling plant. Enter the plastic solution from INEOS: highdensity polyethylene (HDPE) suitable for pipelines.
A world first extensively covered by foreign media, the construction of the underground beer pipeline was also a technical feat. It runs for no less than 3 kilometres along public streets, under various watercourses, the historic canals and city ramparts and the ‘t Zand underground car park.
In addition to the route taken, there were also a number of other technical challenges. For instance, several control systems are needed to guarantee the quality of the beer at all times. And naturally,
everything has to be sterile and in accordance with strict food standards.
The polyethylene from INEOS provided the solution to these challenges. ‘High-density polyethylene (HDPE) is ideally suited for contact with food
because of its antibacterial properties’, explains Gaëlle Pannier of INEOS Olefins & Polymers Europe. ‘The quality we developed for the beer pipeline complies with the strictest drinking water regulations. Moreover, we conduct regular lab tests where a panel tests the polyethylene for possible influences on taste and smell, indicating a possible change in the material’s composition.’
‘The pipeline is a perfect example of the innovation we strive for. It allows us to eliminate much of the lorry traffic between the brewery and bottling plant. Not insignificant in a city whose historic centre is a UNESCO World Heritage Site.’
German pipe manufacturer Egeplast used this material to produce a pipeline with a service life of at least 50 years. ‘Due to the specific properties of the polyethylene, it can be used to make extralong pipes, thereby keeping weld seams to a minimum and greatly reducing the risk of leaks’, says Pannier.
The HDPE pipeline has presented excellent results in terms of reliability and ease of maintenance. And there is now considerably less road traffic, less noise and fewer traffic jams, to the great satisfaction of the brewery and Bruges city council.
Pumping its beer from the city-centre brewery through the underground pipeline to the bottling plant means that De Halve Maan can continue to grow, while retaining its historic location attracting more than 100,000 visitors a year from Belgium and abroad.
Xavier Vanneste, Managing director
De Halve Maan
‘The quality we developed for the beer pipeline complies with the strictest drinking water regulations.’
Gaëlle Pannier, Technical Service & Development, INEOS Olefins & Polymers Europe
INEOS products can be found everywhere, including the everyday products that make our lives easier. From car upholstery and laptop shells to water pipes.
1
Solar panels consist of thin silicon wafers. To precisely cut the wafers, sawing wire and cutting fluid are used. Containing diethylene glycol (DEG) among other things, this fluid plays a crucial role in ensuring cutting efficiency and precision, providing lubrication, removing cutting waste and dissipating frictional heat.
2 The plastic pipes that bring fresh drinking water to your home are made from HDPE (high-density polyethylene). Unlike steel or concrete pipes, HDPE pipes are cheap, easy to install, hardly ever leak and can last up to 100 years.
3
When you drink a soft drink, all you want to taste is the soft drink and not the bottle cap. Bottle caps made from polyolefins (plastic) ensure that your drink retains its ‘organoleptic’ properties. In short: it tastes like it should. INEOS has also been developing bottle caps that, in line with European regulations, remain attached to the bottle when you unscrew them.
4
It is highly likely that the shell of your laptop contains ABS, a styrene-based plastic. This material makes your laptop sturdy, protects it against corrosive products and has mechanical properties that make it easier for designers to make your laptop look good.
5
Upholstery fabrics contain PTA, a purified terephthalic acid in the form of a polyester material. This durable material enables furniture to last for years, while giving it a soft and comfortable feel. Add to that easy maintenance and stain resistance and you have an ideal material for your home.
6
Oftentimes, polystyrene is found inside your refrigerator, keeping the inside nice and fresh and the heat out. It can also be found in insulated coffee cups and the take-away boxes used in restaurants. ABS, a plastic based on acrylonitrile, butadiene and styrene, provides an airtight seal for your refrigerator door, keeping the outside air out. The inside walls and shelves in your refrigerator are also often made from this easy-to-clean plastic.
7
While you choose window frames for their looks, you also want them to be robust and durable. With PVC frames, you can sleep at ease for years to come. They are also light, have excellent insulation properties and are easy to recycle.
8 INEOS supplies manufacturers of synthetic oils with the highgrade base oils that improve a car’s efficiency.
9
Acetone and phenol can be found in car headlights as well as in sunglasses. They are both used to produce polycarbonate, a transparent plastic with high impact resistance which makes it 250 times stronger than glass.
10
The EPDM rubber used to make your roof watertight contains the water-repellent ‘ethylidene norbornene’ (ENB). This product is also found in footballs and the rubber seals around car doors.
11
The Polestar 3 will be the first car model featuring faux leather upholstery made from bio-PVC, an INEOS innovation. This PVC has a carbon footprint no less than 70 per cent lower than that of classic PVC.
In charge of climate, energy and innovation policy at INEOS, Professor Greet Van Eetvelde is busy working on the climate neutrality roadmap for the chemical group. She makes no secret of the fact that the challenge to become net zero by 2050 is huge – the latest INEOS sustainability report talks about an investment of billions of euros. ‘That is inherent to energy-intensive industries. There are no miracle solutions – it will involve a mix of deploying new technologies, coming up with innovative solutions and spotting business opportunities.’
‘We want to tackle CO2 emissions at the source’
Drawing up a climate roadmap for the INEOS group is no mean feat, as Van Eetvelde knows. ‘The company can best be compared to a federation of more than thirty divisions, spread over two hundred locations in thirty countries. Each division will decide autonomously on how – and at what pace – it aims to achieve the climate targets for each site by 2030 and 2050. This bottom-up culture is very strong within INEOS, although there is, of course, a consolidated goal. By 2030, the combined greenhouse gas emissions of all sites should be 33 per cent lower than in 2019. And by 2050, we want to achieve net zero.’
‘To reduce our CO2 emissions, we are not only targeting process emissions. We are investing to prevent emissions at the source of the production process’, says Van Eetvelde. INEOS aims to reduce those direct emissions (scope 1) by improving processes and by using low-carbon technologies.
‘You can decarbonise energy but not the chemical process. That is the big difference between carbon as a fuel and carbon as a raw material for valuable products.’
Greet Van Eetvelde, Global Head of Climate, Energy & Innovation at INEOS
Professor Greet Van Eetvelde is an engineer by training, she holds a doctorate in chemistry and has been connected to the Faculty of Engineering and Architecture at Ghent University for 25 years. Besides her role within INEOS, she heads the Ghent University Energy & Cluster Management research group from her home base in Switzerland. The focus of her research is on ‘industrial symbiosis’: win-win scenarios for companies working in partnership to create added value, for example using waste material as a raw material or sharing infrastructure. Van Eetvelde is also a guest professor at Lausanne Polytechnic University (EPFL).
‘We are constantly improving the energy efficiency of our plants and investing in the electrification of peripheral equipment such as boilers or compressors. Project ONE, the ethane cracker to be built in Antwerp, is a good example. The cracker will only emit one third of the CO2 emitted by the average European steam cracker. This is due to a future-oriented choice of technology, maximum energy efficiency by reusing the heat from the furnaces and the cold from the raw materials (the cooled ethane) and above all by reusing hydrogen (a by-product of the cracking process) as a lowCO2 fuel.’
Van Eetvelde makes the important observation that you can decarbonise energy but not the chemical process itself. ‘A raw material for the chemical sector, carbon is used to make products with major added value for society. You can’t compare that with, say, heating a house, where fossil fuels are only used for combustion and CO2 is released into the atmosphere. That is the big difference between carbon as a fuel and carbon as a raw material for new chemical products. In addition, there is also a ‘short chain’ in the chemical industry whereby companies organise themselves as efficient clusters, exchanging residual flows and raw materials with each other.’
Even though the main objective is to reduce emissions at the source, in the short term capturing CO2 is set to play an important role in INEOS’
climate policy. ‘Where possible, we have been capturing CO2 for a long time and then reusing it. We are doing that in Germany, France and closer to home in Antwerp, for example. We use and sell CO2 as a gas, develop it as a raw material for methanol or mineralise it. At the beginning of March, Project Greensand started off the Danish coast where for the first time, CO2 from the INEOS Oxide plant in Antwerp has been stored deep in the North Sea.’
INEOS also sees a future for hydrogen both as a fuel and as a raw material. It doesn’t necessarily have to be green hydrogen, says Van Eetvelde. ‘In chemical processes such as cracking and dehydrogenation, hydrogen is released as a valuable by-product. We reuse it in our own plants or supply it to other companies, with both approaches contributing towards creating a lowcarbon economy and sustainable cycle.’
In terms of scope 2 emissions (indirect CO2 emissions resulting from the purchase of energy), INEOS is confidently switching to clean energies: from gas and oil to low-carbon fuels such as hydrogen, biogas, biosteam and biomethane, for example. ‘We also purchase green electricity. Over the past few years, we have concluded three Power Purchase Agreements (PPAs) in Belgium with the energy companies Engie, Eneco and the German RWE. Each 10-year PPA is for electricity produced by offshore wind farms.’
In order to work as sustainably as possible, INEOS is also involved in the circular economy. ‘We are demonstrating how we can recover as many of our materials as possible in order to reuse them as basic products. We are collaborating with partners across the whole value chain. In Flanders for example, we are making progress in collecting polystyrene packaging via the well-known blue bags used for collecting recyclable household waste. Just think of all those yoghurt pots, butter tubs and mushroom trays. Using an advanced technique (depolymerisation), we are recycling that plastic waste, turning it into polystyrene of the same quality as new material but with a smaller CO2 footprint and using less fossil fuel.’
Becoming climate-neutral will take a lot of innovation, Van Eetvelde realises. According to her, that is where Europe faces a major challenge. ‘Flanders has a fantastic research policy, yet it does not target what industry really needs. Take the capture of CO2, for example. An enormous amount of research still needs to be carried out in order to develop efficient systems that can also be used effectively on industrial sites. The current installations are often too big to add to existing sites, while their infrastructure is insufficient for capturing all the many emission points in a chemical plant. The breakthrough in technology needed here will require deeper collaboration between industry and universities.’
33%
By 2030, all INEOS sites combined will emit 33 percent less greenhouse gas emissions than in 2019.
‘It is thanks to pioneers like INEOS that Europe is leading the way in the race to net zero emissions. The first ever, full value chain for carbon capture and storage in Europe. You are showing that it can be done.’
Ursula von der Leyen, President of the European Commission
The captured CO2 from INEOS Oxide in Zwijndrecht was cooled and transported as a liquid in containers from the plant to the docks for the pilot project. The Aurora Storm then transported those containers from Belgium to Denmark.
At the beginning of March, the first CO2 – coming from INEOS Oxide in Zwijndrecht – was stored in an empty Danish oil field. A world first that INEOS is extremely proud of. The target is to capture and store 1 - 1.5 million tonnes of CO2 by 2025. And 4 - 8 million tonnes by 2030. In doing so, the chemical company is not just aiming to reduce its own CO2 footprint. ‘We are tapping a whole new market’, says Mads Weng Gade, Chief Commercial Officer at INEOS Energy. The capture and permanent storage of CO2 (CCS) is recognised as a necessary solution for achieving the European climate targets.
‘Experts expect the difference in price between storing CO2 and purchasing emission allowances to disappear by 2030. After that, the market for CO2 storage is set to grow rapidly.’
INEOS Oxide in Zwijndrecht produces ethylene oxide, among other things. During the production process CO2 is released, captured and then purified. As part of Project Greensand, the liquid CO2 is stored in ISO containers and transported by lorries to the docks, 10 kilometres away.
The containers of CO2 are loaded onto the ship for the journey to the depleted Nini West oil reservoir, off the Danish coast. The Aurora Storm has been modified in such a way that the ship can safely transport containers of liquid CO2. In time, a different type of vessel, the so-called CO2 carriers, will be used for large volumes.
The CO2 is pumped from the ship to the drilling platform at 200 bar and 5°C and then injected into the empty oil fields, 1,800 meters below the seabed. To achieve this, operators use a process that is inverted to the way oil is drilled up.
Project Greensand has tested how CO2 can be stored in an empty oil field for the first time under real conditions. ‘It was quite exciting to see the liquefied CO2 flow into the empty reservoir’, says Weng Gade, smiling. ‘Though our lab tests gave us the confidence we needed, you never know how CO2 is going to react in reality. Fortunately, everything is going as expected, especially as our engineers have invested a great amount of time studying the properties of the sandstone reservoir.’
The oil field lies 1,800 metres below the seabed in the Danish part of the North Sea and was exploited by INEOS Energy for more than 20 years. ‘The field is now empty, with no more oil being extracted from it’, says Weng Gade. ‘Incidentally, the sandstone in that reservoir contains glauconite, making the sand look green. Hence the name Project Greensand.’
A further aim of Greensand is to demonstrate the value chain of capturing, transporting and industrially storing CO2. ‘Now that the pilot has been successful, we need to scale up to make it financially viable’, says Weng Gade.
It currently costs more to store CO2 than to purchase ETS allowances, the so-called CO2 emission allowances. Experts expect the difference
in price to disappear by around 2030. ‘Just like with wind and solar energy, market growth is set to accelerate’, predicts Weng Gade. ‘Until then, we need sufficient subsidies and the right regulatory frameworks.’ For instance, a bilateral agreement was required between Belgium and Denmark to enable CO2 to be transported by sea.
The origin of the CO2 is also important for economic feasibility. ‘In Antwerp, we have an ethylene oxide plant’, says Johan Loots, Business Manager at INEOS Oxide. ‘The process used produces a stream of concentrated CO2. In the case of processes producing diluted CO2, a further step is needed to concentrate the CO2, incurring extra costs.’
INEOS is not only looking at capturing CO2 from its own activities. Exploiting the commercial possibilities of new technologies is part of the company’s DNA. ‘Europe sees the industrial storage of carbon as key to achieving its climate goals by 2050. Its aim is to store 50 million tonnes of CO2 by 2023, with that figure rising to 300 million tonnes by 2050. That’s a huge potential market’, concludes Weng Gade. ‘There is often an advantage attached to being a first mover, giving us an additional opportunity to develop this new market.’
The availability of high-grade, pure CO2 makes the ethylene oxide plant of INEOS located in Zwijndrecht the ideal candidate for the Greensand pilot project.
During the production of ethylene oxide, CO2 is released as a by-product. For decades this CO2 is being captured and since 2010 it is also being exploited as part of a cooperation contract with two industrial partners. The CO2 is used for example in the production of carbonated drinks, dry ice and greenhouse cultivation.
The pilot project had to show that the permanent storage of CO2 is possible and safe. The first official injection of CO2 from Antwerp in Denmark was successfully carried out in March 2023.
‘For over 10 years INEOS Oxide has been committed to reducing its carbon footprint by capturing CO2 emissions’, says Roel De Vil, site manager of INEOS Oxide in Zwijndrecht. ‘Due to the accumulated expertise in capturing, purifying, and liquefying CO2, we are particularly well-positioned to deliver the CO2 for the pilot project. Project Greensand allowed INEOS to pave the road for cross-border CO2 transport and permanent storage in the North Sea, in a depleted oil field in Denmark. We are playing a leading role in carbon storage and will thus make an important contribution to achieving the Flemish and European climate goals.’
By 2030, Project Greensand plans to store up to 8 million tonnes of CO2 annually in this area. The area is geologically extremely stable and forms a safe permanent storage site for CO2. Sensors perform seismic measurements to investigate how the CO2 behaves in the subsurface.‘Ethylene oxide production - unlike other processesgenerates pure CO2 and is therefore easier to capture.’
Johan Loots, Business Manager at INEOS Oxide
Over the next few years, INEOS is set to invest 2 billion euros in the production of carbon-free hydrogen. Despite its strong belief in the potential of this green fuel, the chemical giant is well aware that the business case is still not tied up.
‘Totally green hydrogen – produced on a large scale – is not going to be available tomorrow. Apart from needing time, the industry needs adapted regulations allowing it to use other types of hydrogen in the meantime.’
‘Hydrogen brings the chemical and energy sectors together’
INEOS currently produces more than 500,000 tonnes of hydrogen a year, mainly as a by-product of chemical processes. ‘We are both a producer and a large consumer of hydrogen, and we expect that consumption to increase further. Just like electrification, hydrogen is an important lever for reducing our carbon footprint. It was thus logical for us to continue investing in hydrogen and hydrogen production and to set up a new business’, says Dirk Dupon, Senior Business Development Manager at INEOS Hydrogen.
Sustainably produced hydrogen is essential for the transition to a lowcarbon economy. Hydrogen seems to be the solution, especially in sectors that are difficult to electrify. INEOS already has the know-how required to produce large quantities of green hydrogen in-house.
‘Green hydrogen is made by means of electrolysis where H2O (water) is split into hydrogen and oxygen. INEOS Inovyn is currently Europe’s largest electrolysis operator’, says Wouter Bleukx, Business Director at INEOS Hydrogen.
‘We are right at the start. Affordable green hydrogen is not going to be available tomorrow, because its production is currently very expensive. We first need to be able to produce it more cheaply. This will require three things: sufficient and affordable renewable energy, support
measures for the technology needed to improve hydrogen production, and an upscaling in order to make hydrogen cheaper. That is why we also need to boost consumer demand for hydrogen. INEOS has the conviction, the know-how and the infrastructure to succeed in doing that.’
‘Power-to-Methanol Antwerp’ is an initial Belgian hydrogen project in the port of Antwerp. Under the impetus of INEOS Inovyn and six partners, new technology is being developed and tested on an industrial scale. ‘This plant captures CO2 released during industrial processes and reuses it as a raw material in conjunction with sustainably produced hydrogen to produce green methanol’, explains Bleukx. The methanol can then be used to produce other chemical molecules or as green fuel for ships, for example.
In the UK, INEOS Inovyn plans to upgrade the existing hydrogen production facility at its Runcorn site to enable it to supply fuel cellgrade hydrogen to the mobility and energy sectors. In Germany, there are plans to build a large-scale electrolysis plant to produce green hydrogen at the INEOS site in Cologne. That hydrogen will then be used to produce green ammonia, opening the door to the development of e-fuels (synthetic fuels based on hydrogen and CO2) via Power-to-Methanol applications on an industrial scale.
Hydrogen can be green – but also black, grey, yellow, pink, blue or turquoise. The energy source used to produce it, together with the associated CO2 emissions, determine the colour. The energy source for black hydrogen is coal, while grey hydrogen is produced using natural gas. In the case of blue hydrogen, the CO2 emissions are typically captured.
‘The chemical and energy sectors need each other’s expertise in order to develop hydrogen as an energy carrier.’
Dirk Dupon, Senior Business Development Manager at INEOS Hydrogen
500,000
INEOS currently produces more than 500,000 tonnes of hydrogen a year, mainly as a by-product of chemical processes.
The port of Antwerp-Bruges will also play an important role. ‘We see the port as a hub for importing hydrogen to Europe. And we support the government’s plans as well as those of the infrastructure companies to build a pipeline network in Belgium for supplying companies with hydrogen’, says Bleukx.
‘The energy companies will also play an important role. We’ve enjoyed a customer-supplier relationship with them for a long time. We need each other’s expertise in order to develop hydrogen as an energy carrier’, says Dupon. ‘The hydrogen story is a good example of where the energy sector and the chemical sector come together. Green hydrogen is ultimately the product of a chemical process that uses green energy.’
INEOS aims to become a major player in the hydrogen market, though Bleukx and Dupon are apprehensive to specify concrete numbers. ‘We believe strongly in this technology, as made clear by our plan to invest 2 billion euros in it. But obviously it must be economically viable’, says Bleukx.
According to the duo, that is where Europe faces a major challenge. ‘We are currently getting lost in discussions about the colour of hydrogen while companies in the United States are being encouraged to develop the green economy’, Bleukx points out.
‘They have a clear funding programme for hydrogen production with the lowest possible CO2 footprint, even though it may not immediately be 100 per cent green.
That is something Europe should also accept: hydrogen won’t be fully green immediately. We shouldn’t confuse long-term goals with shortterm solutions. This transition will take time and our industry needs to be given that time. Regulations need to enable other colours of hydrogen to be used over the next few years.’
‘Hydrogen won’t be fully green immediately. But we shouldn’t confuse long-term goals with short-term solutions.’© Sutdio Dann
It is no coincidence that INEOS’ hydrogen activities are largely controlled from Belgium. ‘Though Belgium will obviously not be the country where we can build a large production facility for green hydrogen due to our lack of sufficient solar and wind energy, we do have a well-developed knowledge economy. This means that we have the right people to develop those hydrogen projects. That expertise can make us a frontrunner. We can lay the foundations for hydrogen projects and concepts that will be rolled out later on worldwide’, says Wouter Bleukx.
INEOS is one of the eight companies belonging to the new Belgian Hydrogen Council (BHC) for the next two years. The aim of the BHC is to strengthen Belgium’s position in Europe and the world as a frontrunner for clean hydrogen. On the BHC, Bleukx represents the chemical industry, an important sector for the use of hydrogen.
This autumn, INEOS Inovyn will start construction of the HELIOS solar farm in Jemeppe-sur-Sambre. The biggest one in Wallonia, it is to be built in partnership with a Belgian energy company to exclusively supply energy to the INEOS Inovyn site. This project marks a further step towards carbon neutrality for the chemical company.
In 2021, INEOS Inovyn announced its intention to decarbonise all its industrial activities in the long term. Not just in Belgium but throughout Europe, INEOS wants to reduce CO₂ emissions by 33 per cent by 2030 and by 100 per cent by 2050. To help achieve that ambition, the HELIOS solar farm is soon to be constructed in Jemeppe-sur-Sambre.
Featuring 90,000 solar panels on a 30-hectare site – enough to produce more than 57,000 MWh a year (this equals power for around 16,000 families) –, the project will be the biggest solar farm ever to be built in Wallonia. The production and consumption of this renewable energy generated
‘Thanks to this new farm, solar energy will cover around 10 per cent of the energy demand of the INEOS Inovyn site.’
With 90,000 solar panels spread over 30 hectares, the HELIOS project will become the largest solar park in Wallonia.
Julien De Meersman, Energy and Utilities Manager at INEOS Inovyn
in Jemeppe will lead to an annual saving of no less than 14,000 tonnes of CO₂, while also allowing INEOS Inovyn to bring low-carbon products to the market.
Apart from the use of renewable energy sources, the decarbonisation plan has other aspects. ‘We are electrifying our processes where possible, replacing old equipment with energy-efficient alternatives, researching the possibility of CO2 storage and reducing our energy consumption by improving our efficiency. The best energy is the energy we don’t use!’, says site director Philippe Taranti.
INEOS Inovyn is building on its position as European leader in electrolysis to launch an ambitious investment plan for low-carbon hydrogen production. The first units are under development in various European countries.
‘Although our site in Jemeppe-sur-Sambre is selfsufficient when it comes to energy, it remains connected to the Belgian high-voltage grid’, explains Taranti. ‘Over the past few years, we have been working on making our production more flexible in collaboration with energy company Elia. This can help balance the high-voltage grid during peak periods when demand for electricity goes up.’
‘Thanks to this new farm, solar energy will cover around 10 per cent of the site’s energy demand’, says Julien De Meersman, Energy Manager for INEOS in Jemeppesur-Sambre. ‘Our site is a major consumer of electricity, most of which we generate ourselves using a combined heat and power plant. The idea is to partly replace the fuel – currently gas – with renewable energy.’
Over the past few years, the share of energy in the company’s production costs has increased significantly. ‘In 2018, it was about 20 per cent. It has since risen to 40 per cent. Saving energy therefore tops our list of priorities’, says Taranti.
INEOS Inovyn has a leading position in the field of chlorovinyls. These are used in the construction and automotive sectors as well as in the construction of wind turbines and in the health sector.
‘If we want to keep that expertise and industrial activity in Europe, and in Belgium in particular, we need to keep energy costs competitive. The survival of our industrial network and employment in Belgium are dependent on that’, says De Meersman.
‘In 2018, energy accounted for about 20 per cent of our site’s production costs. Today this amounts to 40 per cent.’
Philippe Taranti, Site Manager and Regional Operation Manager Belgium & Germany at INEOS Inovynn© C. Ketels
• Joined INEOS Oxide in 1999 as a purchaser of raw materials and packaging materials.
• Progressed to become Supply Chain & Logistics Manager and senior manager.
• Moved to INEOS Phenol as Business Development Manager in 2015.
• Appointed Global Sustainability Manager at INEOS Phenol in 2020.
With a degree in chemical engineering, Peggy Gerits joined INEOS in 1999 – at the very beginning – as a purchaser at the Oxide plant in Zwijndrecht. She has since climbed the ladder to become Global Sustainability Manager at INEOS Phenol. How does she reconcile people and planet with prosperity today?
‘I really wanted to do it but also realised that it wouldn’t be easy’, she says, talking about the career switch to sustainability manager that she made three years ago. ‘The legislative framework surrounding sustainability is not always clear and is constantly changing. Additionally, production sites in Europe view the topic differently compared to those located in the US. Sustainability is much more sensitive here.’
Above all, Gerits found that INEOS as a company had to be part of the solution. ‘Shortages of raw materials, climate change… Confronted with the facts every day, we have an obligation as an individual, as a company and as an industry.’
As a producer of basic raw materials, INEOS Phenol is at the beginning of the value chain. ‘In many cases, our products are just a small part of the journey to the consumer product. That makes sustainability one big jigsaw puzzle for us.’
One small piece of that jigsaw puzzle is INVIRIDIS, a bio-product used by INEOS Phenol to reduce the carbon footprint of the phenol and acetone it produces. ‘Acetone and phenol are key building blocks for products such as vehicle lamps, insulation, bike helmets and adhesives. Our bio-line enables us to offer manufacturers a more climatefriendly and sustainable alternative.’
That logic works both ways: INEOS Phenol is investing in a more sustainable offering but expects its suppliers to do the same. ‘Two thirds of our emissions are connected to the raw materials we use. As Sustainability Manager, I also encourage our suppliers to “go green”.’
Sustainability is more than just reducing CO2 emissions and offering sustainable products. ‘The whole organisation has to follow suit: sales, procurement, operations and HR. “Softer” items are also an integral part of sustainability. People are increasingly asking themselves whether a company’s values are in line with their own.’
In that context, profitability is also vital. For Gerits, that mix of people, planet and prosperity is the biggest challenge. ‘You need ambition in this job but also a healthy dose of realism. The chemical sector has been operating for hundreds of years. While we can’t expect to change it completely within five years, the sector is an important partner in the transition to greater sustainability. For example, the demand for lighter-weight materials is set to increase. If the chemical industry doesn’t remain at the forefront, those goals become a lot harder to achieve.’
‘Sustainability calls for ambition and realism’
‘In many cases, our products are just a small part of the journey to the consumer product.’
Peggy Gerits, Global Sustainability Manager at INEOS Phenol
For the company, this challenge symbolises the freedom and responsibility given to employees to enable them to achieve the best results – whether in the desert or the workplace.
Jaro Beuckeleers, now Account Manager at INEOS Olefins & Polymers Europe, joined the Graduate Programme around four years ago and was immediately taken by the Namibian Challenge. ‘I’d always been a keen sportsman until I started working for INEOS abroad. When the opportunity
to take part in the Challenge came up, I didn’t hesitate for a second.’
After nine months of intensive training, Jaro set off on his adventure at the end of May. In his suitcase: plenty of sun cream, two pairs of running shoes, ear plugs (in case any of the other participants snored), a mask (so that he would be able to sleep under the bright starry sky) and a torch. ‘This unique physical experience is the culmination of a long journey. Before going to Namibia, you have to achieve a number of physical milestones: running a marathon and mountain biking on Lanzarote, a mountain-bike trek in Germany followed by a hike and a marathon in Barcelona.’
Although the company provides a comprehensive training programme, the Account Manager also enlisted the services of a personal trainer. ‘I decided to approach the whole thing seriously so that I would be able to enjoy the trek and complete the challenge.’ There was a lot more to it than just running 3 or 4 times a week. ‘I paid very close attention to my diet, eating enough vegetables, keeping away from sweets and crisps, drinking
Every year, a group of young graduates from INEOS heads to southern Africa for the adventure of a lifetime, accompanied by senior executives. There they spend six days running, climbing and cycling through the Namibian desert.
‘You only experience something like this once in a lifetime. It’s hard to put the memories into words.’
Jaro Beuckeleers, Account Manager at INEOS Olefins & Polymers Europe© Christophe Ketels
Young graduates at INEOS are given the opportunity to take part in the adventure of a lifetime. Over a period of 9 months, they are trained to complete a 340-km trek involving cycling, running and hiking in harsh desert conditions in just 6 days. The whole trek consists of around 42 kilometres of hiking, 84 kilometres of running and 212 kilometres of cycling. 15 Belgian employees took part in the 2023 Challenge.
very little, if any, alcohol – all these are crucial when taking on this kind of challenge. I intend to stick to this lifestyle after the challenge too, albeit less strictly.’
Two weeks later, Jaro is back at his desk, all the richer for the experience. ‘You only experience something like this once in a lifetime’, he grins. ‘It’s hard to put the memories into words. A great group, a tough physical challenge, impressive nature and beautiful surroundings made it a once in a lifetime experience.’
The group, made up of colleagues from all over the world, spent six days trekking through the desert. Thanks to his thorough preparations and favourable weather conditions (a fresh easterly wind), the physical aspect was not too much of a problem for Jaro. ‘Only cycling through the heavy desert sand was more difficult than expected. However, the good thing is that, if you do fall off, you get a soft landing.’
The most difficult part of the trip? ‘Climbing Brandberg, the highest peak in Namibia. We had to
tackle a steep 2,000-metre climb carrying a 15-kg backpack – I struggled with that. And I found it hard to sleep at the top, due to the cold and being afraid of night-time visits from bugs’, he admits. ‘But ultimately, you’re rewarded with an incredible sunset on that remote summit, an indescribable feeling.’
When asked what was the highlight of the trip for him, Jaro didn’t have to think twice. ‘Definitely the marathon. I had trained for it for so long and I was determined to make it to the end. I was really able to enjoy the scenery – running through that
landscape all alone made me feel I could tackle everything.’
The group dynamics also helped make the adventure unforgettable. ‘We’d already met each other briefly but it was still quite awkward at the beginning. What a contrast to saying goodbye after spending seven days living so close together. With no mobile phone reception, all we could use our phones for was to take photos. We were continuously swapping stories, something that we are no longer used to doing in this age of social media.
We experienced something unforgettable together. It will always be ‘our story’ that we all wrote together.’
And now, business as usual or the dreaded black hole? ‘It’s going to take me a few more days to work my way through my mailbox’, chuckles Jaro. ‘That’s part of it. I count myself lucky to have been given this opportunity. Now I can get back to focusing on my professional challenges.’
This unforgettable experience forces participants to let go of their mental inhibitions and shows them what they are capable of. Jaro will be taking with him the lessons he learned on the trip as he moves forward with his career. ‘The Namibia trip was a milestone, not the end of the road. I’m now looking ahead: what else do I want to do? Maybe all of us will set ourselves another goal. I also want to encourage future generations to go on this adventure.’