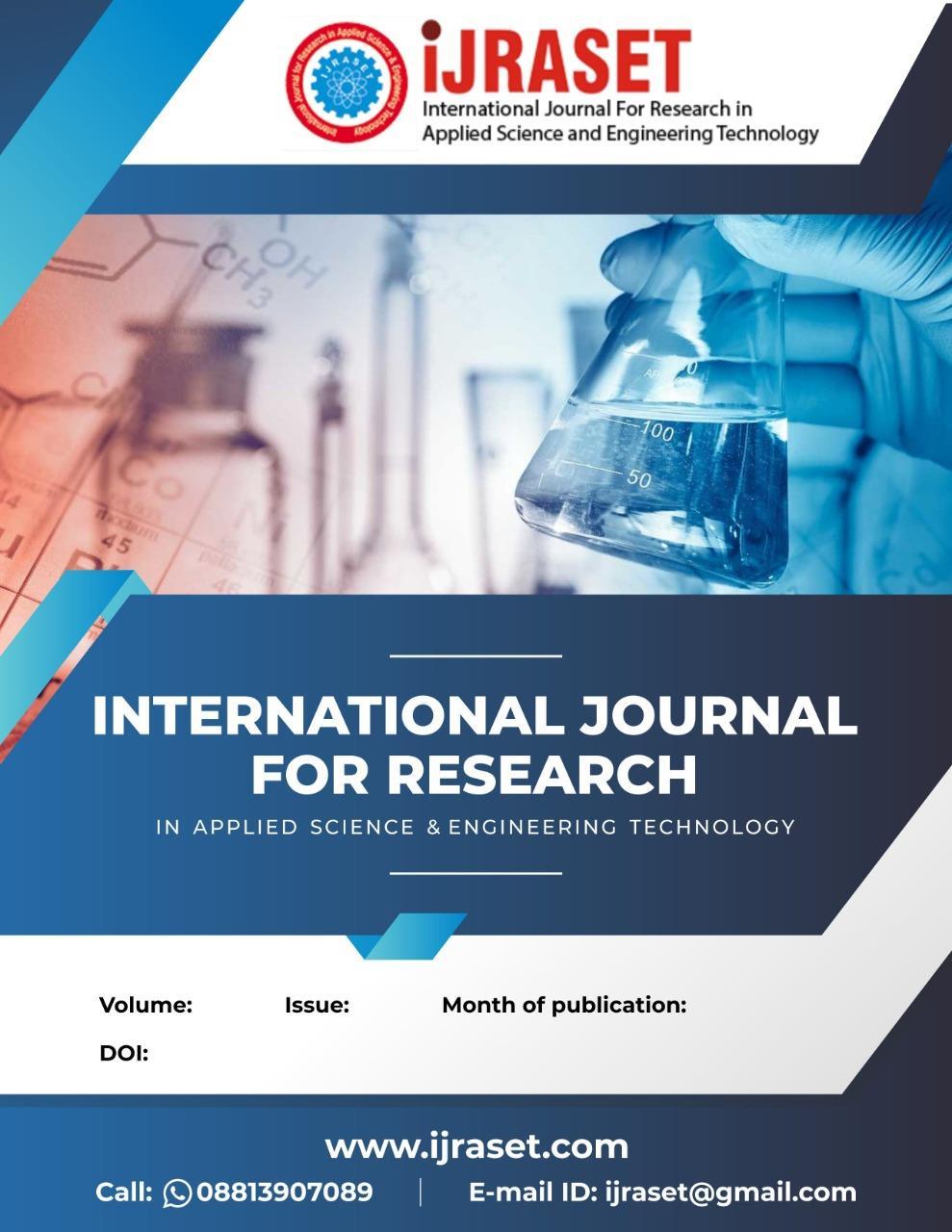
ISSN: 2321-9653; IC Value: 45.98; SJ Impact Factor: 7.538
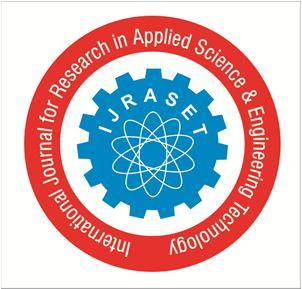
Volume 10 Issue XII Dec 2022- Available at www.ijraset.com
ISSN: 2321-9653; IC Value: 45.98; SJ Impact Factor: 7.538
Volume 10 Issue XII Dec 2022- Available at www.ijraset.com
Umang Jain1 , Dr. J. N.
Vyas2
1M.E. Student, 2Professer, Department of Civil Engineering, Mahakal Institute of Technology and Management, Ujjain (M.P.), India
Abstract: With the development of science and technology in the field of structural engineering, it is possible to adopt preengineered buildings in both industrial and residential construction sectors. For important buildings it is more suitable to use pre engineered building as these are more safe and take less time in construction in comparison of RCC structures. In this paper, pre-engineered steel structure will be design and analyzed for wind and seismic analysis with different parameters using software Staadprov8i and analyzed with different loads on building i.e. dead load, live load, wind load, seismic load and load combinations on structure. The main objective of this work is to understand the concepts of PEB and find the least possible weight of structure and various displacement or significance of forces in each direction which will help the structure to be safe and stable. The pre-engineered construction concept involves pre-engineering and quality construction systems which will help to minimize the use of cost and time.
Keyword: Pre engineered buildings, StaadPro software, RCC structures.
Steel Industry is growing rapidly all around the world. To meet the increasing demand of construction, alternative ways of construction are developing. Advances in technology have greatly improved over the years, contributing tremendously to improving living standards through various new products and services. A pre-engineered building (PEB) is one such revolution. They use a defined stock of raw materials that have been time tested to meet a wide range of structural and architectural design specifications. The majority of steel structures being built are only low-rise buildings, which are generally of one storey only. Industrial buildings, a subset of low-rise buildings are normally used for steel plants, automobile industries, light, utility and process industries, thermal power stations, warehouses, assembly plants, storage, garages, small scale industries, showrooms, offices etc. The application of pre-engineered building concepts to low rise buildings is very economical due to its light weight and economical construction. PEB systems are extensively used in industrial and much other non-residential construction world-wide. These buildings were pre-designed or 'pre-engineered' into standard sizes, spans, bays and heights, and use standard details for fixing cladding, roofing, gutters, flashing, windows, doors etc. taking advantage of industrial practices of mass production of components economically.
In structural engineering, a pre-engineered building (PEB) is designed by a manufacturer to fabricated using a pre-determined inventory of raw materials and manufacturing methods that can efficiently satisfy a wide range of structural and aesthetic design requirements. Pre-engineering building primary frame structure is an assembly of I-shaped structural members. The I-shaped beams are usually formed in the factory by welding steel plates together to form the I-sections. The I-section beams are then assembled on site with bolted connections to form the entire frame of the pre-engineered building. Tapered sections are also used to achieve varying depth. The concept of PEB is the frame geometry which matches the shape of the internal stress (bending moment) diagram thus optimizing material usage and reducing the total weight of the structure. The use of steel structures is not only economical but also eco-friendly at the time when there is a threat of global warming. Here, “economical” word is stated considering time and cost. Time being the most important aspect, steel structures (Pre- fabricated) is built in very short period and one such example is Pre Engineered Buildings (PEB). Pre-engineered building are steel building wherein the framing members and other components are fully fabricated in the factory after designing and brought to the site for assembly, mainly by nut-bolts, thereby resulting into a steel structure of high quality and precision. Steel is an expensive material as compared to the rest but when it comes to the cost-savings during the life span of the structure, steel proves to be a very affordable material . Steel can also be made rust proof by the application of special coated paints. Apart from that, steel is an insect and termite resistant material and the maintenance cost is lower during its life span as compared to other materials. PEB are generally low rise buildings however the maximum eave height can go up to 30 metres, Clear span upto 90 meter wide are possible.
ISSN: 2321-9653; IC Value: 45.98; SJ Impact Factor: 7.538 Volume 10 Issue XII Dec 2022- Available at www.ijraset.com
The force exerted by the horizontal component of wind is to be considered in the design of buildings, towers etc. The wind force depends upon the velocity of wind, shape, size & location of buildings. Wind analysis calculation given below according to IS code 875 part 3:1987 ;
Design wind speed Vz = Vb k1 k2 k3Where, Vz =Design wind speed at anyheight z in m/s, Vb =Basic wind speed calculated from wind speed map of India,k1=Probabilityfactor (risk coefficient clause 5.3.1), k2=Terrain, height and structure size factor (clause 5.3.2) andk3=Topographyfactor(clause 5.3.3)
Design wind pressure Pz=0.6 Vz2Where, Pz=Design wind pressure in N/m2 at height z andVz =Design wind speed atanyheight z in m/s Wind load on individual structural member such as roofs, walls and cladding given as: F=(Cpe – Cpi) A PzWhere, Cpe=External pressure coefficient,Cpi=Internal pressure coefficient, A=Surface area of structural member or cladding unit andPz=Design wind pressure in N/m2 atheight z
Earthquake is a natural procedure of shaking ground due to movement of tectonic plate. The force of earthquake is random so the design engineer need to care full predict of these force and analyze the structure under these random force. Earthquake loads are to be carefully modeled so as to assess the real behavior of structure with a clear understanding that damage is expected but it should be regulated.
Earthquake plays an influential role in analysis and design of structures. Seismic analysis is a branch of structural analysis that involves calculation of a building's (or non building's) earthquake response. Analysis is the process to determine the behavior of structure under specified load combinations.
This is a very simple method of analysis. The main assumptions in these method are that the lateral force is equivalent to actual loading.
In these method, the Base Shear which is total horizontal force on the structure is calculated on the basis of the structure mass and its fundamental time period of vibration. The total design lateral force or design seismic base shear (VB) along any principal direction shall be determined with thehelp of following expression:
VB = Ah W
Where, Ah = Design horizontal acceleration spectrum using fundamental natural period Ta,W = seismic weight of all the Building
TheDesign horizontal SeismicCoefficient Ah for a Structure will be evaluated byexpression: Ah = ZI Sa 2 R g
Z= Zone Factor, I = Importance Factor
Sa/g = Averageresponse Spectrum Coefficient using soil type and fundamental timeperiodR = Response reduction factor
Above the Value of W, Z, I, Sa/g, and R are dependent on the IS 1893 (Part 1): 2016
In present study, single pitched roof industrial structure of portal frame type modeled. The steel structure of portal frame type analyzed using staadProV8i software. IS codes we used for wind load calculation IS 875 (part 3) : 1987 and for seismic load calculation IS 1893 (part 1) : 2016. The Behavior of industrial structure have been studied in terms of Displacement and unity checkapplied to achieve economical structure.
ISSN: 2321-9653; IC Value: 45.98; SJ Impact Factor: 7.538
Volume 10 Issue XII Dec 2022- Available at www.ijraset.com
Table 1: Structural properties ofmodel Geometric Details
Structure Industrial Structure
Types of Buildings Portal Frame Single Pitched Roof Structure
Plan Area 1050 m 2
Height of structure 7.5 m Area (LxW) 70mx15m
BaySpacing(Length wise) 7.11 m
BaySpacing(Width wise) 7.325 m
No. of Story Ground floor only
Roof Angle 5.71 degree
Length of canopy 2.5m
Brick wall height Upto 3m Purlin spacing 1.55 m
Location of structure Indore
Member Properties (Main frame and Gable end)
Size of Rafter
Starting (350/600mm x 5mm W)/(200mm x 10mm F)
Middle (350mm x 4mm W)/(165mm x 6mm F)
End (350/550mm x 5mm W)/(150mm x 6mm F)
Size of Column
Higher end column (300/600mm x 5mm W)/(215mm x 10mm F)
Lower end column (300/550mm x 5mm W)/(180mm x 8mm F)
Middle column (350mm x 5mm W)/(165mm x 6mm F)
Size of Canopy (300/500mm x 5mm W)/(165mm x 6mm F)
PrimaryLoad
Dead Load(Main frame) 0.635 KN/m
Dead Load(gable end) 0.342 KN/m
Live Load (Main frame) 4.41 KN/m
Live Load (Gable end) 2.2 KN/m
Seismic Zone III
Zone Factor (Z) 0.16
Response Reduction Factor (R) 5
Importance Factor (I) 1.0
Soil Type II
Damping Ratio 0.05
Analysis Software : StaadProV8i
B. Design Parameters
ISSN: 2321-9653; IC Value: 45.98; SJ Impact Factor: 7.538 Volume 10 Issue XII Dec 2022- Available at www.ijraset.com
Figure 1 – Isometric view
Figure 2 – 3D view
Table 2: Properties of Design Parameters
Parameter Value
Yield strength of steel
FYLD (HR) 345000KN/m FYLD (Pipe) 250000KN/m
Length in local Y axis for slenderness value kl/r, (Ly) 1.65m (on column)
Length in local Y axis for slenderness value kl/r, (Ly) 1.55m (on rafter)
Length in local Zaxis for slenderness value kl/r, (Lz) 8.96 m
Length in local Zaxis for slenderness value kl/r, (Lz) 7.50 m
Unsupportedlength for allowable bending stress (UNL) 1.55 m (on rafter)
Unsupportedlength for allowable bending stress (UNL) 1.65m (on column)
Cm value in local Y axis (CMY) 0.9
Cm value in local Z axis (CMZ) 0.9
K value in local Z axis, usuallymajor axis (Kz) 2 (Applied on all column full length)
Allowable L/R in compression (MAIN 1) 1
Allowable L/R in tension (TMAIN) 1
Allowable L/R in compression (MAIN 350) 350
ISSN: 2321-9653; IC Value: 45.98; SJ Impact Factor: 7.538 Volume 10 Issue XII Dec 2022- Available at www.ijraset.com
Wind and seismic analysis are being carried out in accordance with Indian Codes. The result are displayed in terms of displacements in X, Y and Z direction and Unity Check for optimized structure. As the structure is considered for pinned support connections there will be zero bending moment in X, Y and Z direction.
Displacement is taken from the software which have been further checked for permissible limits criteria (L/240) according to IS 800:2007 clause 5.6.1 table no. 6. The results in terms of maximum and minimum deflection for X,Y and Z direction shown below. Direction Node L/C X mm Ymm Zmm
MaxX 70 420.9DL+WLIP45 52.532 10.568 -0.327
Min X 83 14WRIS 180 -40.325 -8.536 -0.312
MaxY 113 12WRIS 135 -29.926 32.576 4.224
Min Y 109 420.9DL+WLIP45 42.583 -35.989 0.558
MaxZ 120 11WRIP 135 -17.884 0.211 14.594
Min Z 121 10WLIS 90 25.639 0.148 -14.653
Unity check have been performed by optimizing structure several times to get stable and economical structure. Utilization ratio permissible limit is 0.95 and to avoid getting over safe structure we considered utilization ration between 0.5 and 0.95 which gives us stable and economical structure. Theresults for unitycheck taken from the softwareare shown below in table.
Beam Analysis Property Design Property Actual Ratio AllowableRatio 187
Taper Taper 0.664 1 186 Taper Taper 0.703 1 185 Taper Taper 0.756 1 184 Taper Taper 0.75 1 124 Taper Taper 0.587 1 123 Taper Taper 0.585 1 116
Taper Taper 0.505 1 115 Taper Taper 0.572 1 114 Taper Taper 0.505 1 113 Taper Taper 0.724 1 112 Taper Taper 0.72 1 111 Taper Taper 0.591 1 104 Taper Taper 0.506 1 103 Taper Taper 0.569 1 102 Taper Taper 0.503 1 101 Taper Taper 0.84 1 100 Taper Taper 0.813 1 99 Taper Taper 0.63 1 98 Taper Taper 0.67 1 97 Taper Taper 0.738 1 96 Taper Taper 0.752 1 95 Taper Taper 0.492 1
ISSN: 2321-9653; IC Value: 45.98; SJ Impact Factor: 7.538 Volume 10 Issue XII Dec 2022- Available at www.ijraset.com
94 Taper Taper 0.797 1 93 Taper Taper 0.797 1 92 Taper Taper 0.505 1 91 Taper Taper 0.75 1 90 Taper Taper 0.726 1 89 Taper Taper 0.674 1 88 Taper Taper 0.746 1 87 Taper Taper 0.589 1 86 Taper Taper 0.517 1 85 Taper Taper 0.554 1 84 Taper Taper 0.577 1 83 Taper Taper 0.576 1 82 Taper Taper 0.441 1 81 Taper Taper 0.538 1 80 Taper Taper 0.572 1 79 Taper Taper 0.755 1 78 Taper Taper 0.759 1 77 Taper Taper 0.612 1 76 Taper Taper 0.843 1 75 Taper Taper 0.552 1 74 Taper Taper 0.886 1 73 Taper Taper 0.741 1 72 Taper Taper 0.619 1 71 Taper Taper 0.914 1 70 Taper Taper 0.731 1 69 Taper Taper 0.633 1 68 Taper Taper 0.873 1 67 Taper Taper 0.829 1 66 Taper Taper 0.743 1 65 Taper Taper 0.873 1 64 Taper Taper 0.83 1 63 Taper Taper 0.743 1 62 Taper Taper 0.971 1 61 Taper Taper 0.755 1 60 Taper Taper 0.618 1 59 Taper Taper 0.916 1 58 Taper Taper 0.702 1 57 Taper Taper 0.616 1 56 Taper Taper 0.769 1 55 Taper Taper 0.784 1 54 Taper Taper 0.833 1 53 Taper Taper 0.834 1 52 Taper Taper 0.782 1
ISSN: 2321-9653; IC Value: 45.98; SJ Impact Factor: 7.538 Volume 10 Issue XII Dec 2022- Available at www.ijraset.com
51 Taper Taper 0.756 1 50 Taper Taper 0.733 1 49 Taper Taper 0.61 1 48 Taper Taper 0.533 1 47 Taper Taper 0.699 1 46 Taper Taper 0.715 1 41 Taper Taper 0.849 1 36 Taper Taper 0.862 1 35 Taper Taper 0.706 1 33 Taper Taper 0.5 1 32 Taper Taper 0.5 1 31 Taper Taper 0.584 1 27 Taper Taper 0.567 1 26 Taper Taper 0.914 1 22 Taper Taper 0.568 1 21 Taper Taper 0.914 1 20 Taper Taper 0.78 1 19 Taper Taper 0.51 1 18 Taper Taper 0.515 1 17 Taper Taper 0.536 1 16 Taper Taper 0.599 1 12 Taper Taper 0.58 1 11 Taper Taper 0.859 1 7 Taper Taper 0.54 1 6 Taper Taper 0.836 1 5 Taper Taper 0.744 1 4 Taper Taper 0.609 1 3 Taper Taper 0.536 1 2 Taper Taper 0.677 1 1 Taper Taper 0.718 1
This study explains the behavior of modeled pre engineered building for two most important load factors wind load and seismicload, the conclusion are explained below based on the extracted results:
1) The analysis shows that the value of maximum and minimum deflection for X direction is 52.532 mm and -40.325 mm respectively.
2) The analysis shows that the value of maximum and minimum deflection for Y direction is 32.576 mm and -35.989 mm respectively.
3) The analysis shows that the value of maximum and minimum deflection for Y direction is 14.594 mm and -14.653 mm respectively.
4) On comparing the results we get that deflection is highest for X direction in comparison of Y and Z direction. X directiongoes along width of the structure therefore width wise will attain highest deflection.
5) The Unity check results shows that the member properties are within limit between 0.5 and 0.95. Hence structure is stableand cost saving.
ISSN: 2321-9653; IC Value: 45.98; SJ Impact Factor: 7.538 Volume 10 Issue XII Dec 2022- Available at www.ijraset.com
[1] Shivani Mehar, Ruchita Nar, Saddicha Jagdale and Gautami Kalal (2018). “Design of Industrial Warehouse”. International Journal of Engineering Research & Technology (IJERT)ISSN: 2278-0181http://www.ijert.orgIJERTV7IS020170 , www.ijert.orgVol. 7 Issue02, February-2018302.
[2] Shaik Kalesha, B.S.S. Ratnamala Reddy, Durga Chaitanya Kumar Jagarapu (2020) “An analytical study on pre engineered buildings using staad pro”. Elsevier, Article history:Received24 February2020Receivedin revised form1 April 2020Accepted 5 April 2020
[3] Aejaz Ahmed Zende, A. V. Kulkarni and Aslam Hutagi (2013) “Comparative Study of Analysis and Design of Pre-Engineered-Buildings and Conventional Frames”. IOSR Journal of Mechanical and Civil Engineering (IOSR-JMCE) ISSN : 2278-1684 Volume 5, Issue 1 (Jan. - Feb. 2013), PP 32-43 www.iosrjournals.org
[4] Dale C. Perry, Herbert S. Saffir, James R. McDonald, "Performance of Metal Buildings in High Winds", Journal of Wind Engineering and Industrial Aerodynamics. 36 (1990) 985-999 985, Elsevier Science Publishers.
[5] Syed Firoz, Sarath Chandra Kumar B. S.Kanakambara Rao," Design Concept of Pre Engineered Building", WERA Vol. 2, Issue 2,Mar-Apr 2012. pp.267272http://www.jjera.com/papers/Vol2_issue2/AS22267272.pdf
[6] M.Suneethal Naresh Kumar, Gillela Reddy October 2016, "Design and Analysis of Industrial Building with Gable Roof by using STAAD.PRO* International Joumal of AdvanceTechnology In Engineeringand Science.
[7] Vaibhav B. Chavan, Vikas N. Nimbalkar And Abhishek P. Jaiswal, Vol.3, Issue 2, February 2014 " Economic Evaluation Of Open And Hollow Stuctural SectionsInIndustrial Trusses", Aci Structural Journal.
[8] C.M. Meera, June 2013 "Pre- Engineered Building Design of an Industrial warehouse". International Journal of Engineering Sciences and Emerging Technologies.
[9] Subhrakant Mohakul, Dr. Shaikh Yajdani, Abhay Dhurde,August 2014 "Design of industrial storage shed and analysis of stresses produced on failure of a joint". International Journal of Civil EngineeringandTechnology.
[10] Manan D. Maisuri, Hitesh K.Dhameliya, Hiten L.Kheni, Vol.1 Issue 12.December 2013,"Review Of Comparison Between Conventional Steel And Tubular Steel Section For Multi SpanIndustrial Shed WithTruss And Portal Frame" International Journal of Advance Engineering andResearch Development.
[11] Shaiv Parikh "Design of Steel Compression Members"(AccordingTo IS: 800)
[12] Design of steel structures byN. Subramaniam.
[13] IS 875- Part II (1987), Indian Standard Code of Practice for DesignLoads (Other ThanEarthquake) for Buildingsand Structures
[14] IS 1893-Part I (2002) Indian Standard Criteria for EarthquakeResistant of Design of Structures.
[15] IS 875- Part III (1987). Indian Standard Code of Practice for Design Loads(Other ThanEarthquake) for Buildingsand Structures.