https://doi.org/10.22214/ijraset.2023.48902
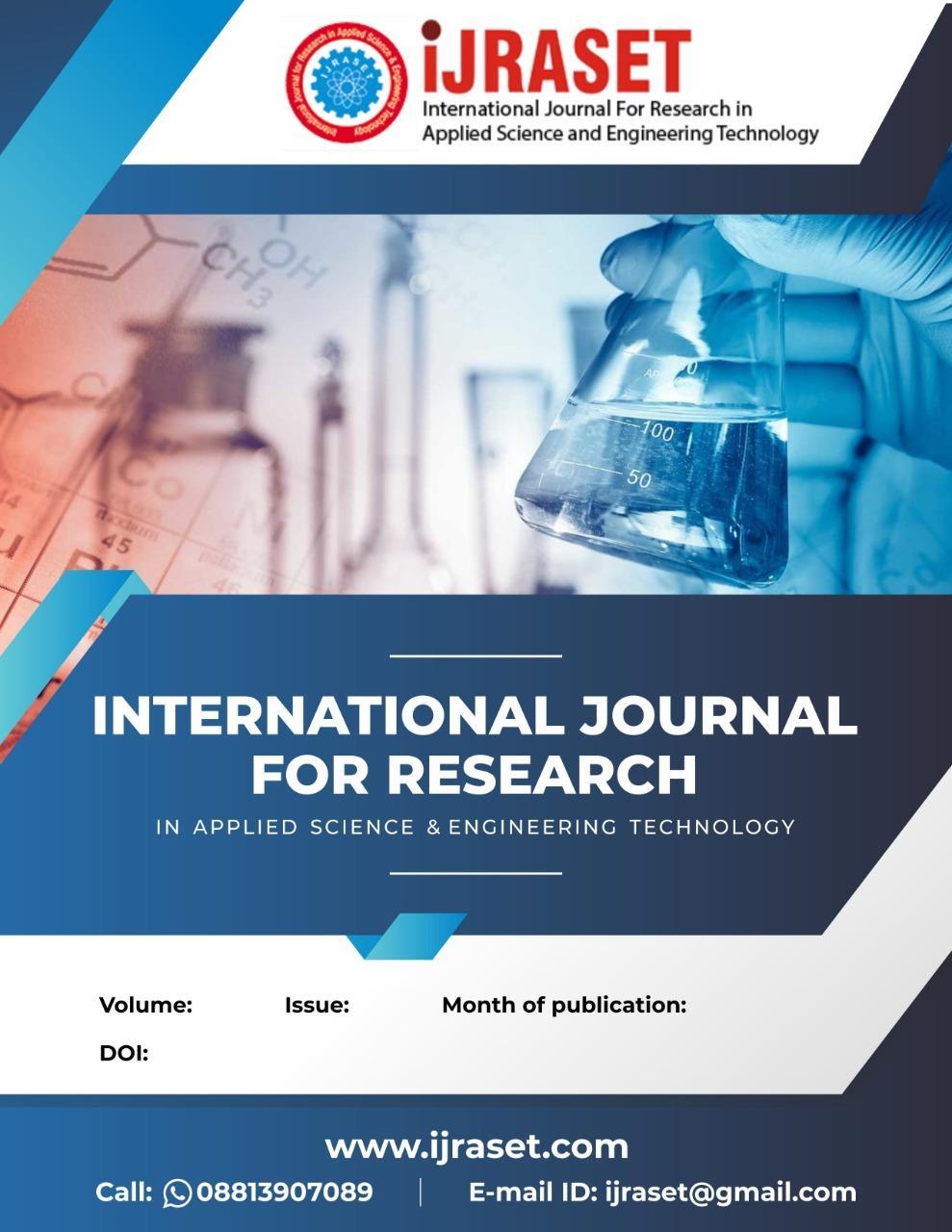
ISSN: 2321-9653; IC Value: 45.98; SJ Impact Factor: 7.538
Volume 11 Issue I Jan 2023- Available at www.ijraset.com
https://doi.org/10.22214/ijraset.2023.48902
ISSN: 2321-9653; IC Value: 45.98; SJ Impact Factor: 7.538
Volume 11 Issue I Jan 2023- Available at www.ijraset.com
1P.G. Student, M-Tech Structural Engineering , Department of Civil Engineering , G H Raisoni Institute Of Engineering And Technology, Nagpur , Maharashtra.
2, 3Assistant Professor, Department of Civil Engineering , G H Raisoni Institute Of Engineering And Technology, Nagpur , Maharashtra.
Abstract: This study investigates the effectiveness of the current pulse thermal technique (ESRT) in detecting internal defects in СFRР reinforced metal structures. This study covers various internal defects of FRР reinforced steel structures, including cracks, small tracks in СFRР, metal cracks / inter-steel cracks. We theoretically analyze the effect of these problems on the magnetic and thermal response of structures. To confirm the results of the theater, statistical and diagnostic tests were performed on steel plates reinforced with СFRР with various defects. Numerical and diagnostic results show that EСРТ can estimate observed deformations and show low temperature regions in EСРТ thermograms. In addition to the thermal characteristics of the thermograms, the appearance of the temperature profile and changes in temperature are also examined for reanalysis of the thermal analysis. In addition, based on the test results, the effectiveness of EСRT to restore the size and scope of errors was demonstrated. Overall, theoretical, numerical and experimental results show that EСRT is effective in diagnosing internal defects in CFRP-reinforced steel structures.
Keywords: defects Non-destructive testing, thermal analysis CFRP-reinforced metal structures, composites, structures, defects, damage, detection and inspection, structural condition monitoring etc.
NDT testing of steel structures is in recent use. Acoustic emission (AE) was used in the study. . Failures of CFRP-Steel Bonded Plates in Rigorous Laboratory Test and Failures of CFRP-Steel Bonded Bars in Tensile Fatigue Test. The results show that AE is effective in fault phase detection. and defining failover methods. However, AE only works for mutational defects and cannot be used to test static defects, which are very common in engineering. Piezoelectric sensors were also used to monitor CFRP metal beams through boning. The results show that the real impedance part decreases with increasing ossification. In this method, piezoelectric sensors must be closely connected to the beam under test and can only inspect a limited area. Lamp-wave-based indirect ultrasonic testing has been shown to be effective for detecting fatigue cracks in CFRP steel-reinforced plates. Non-linearity caused by fatigue cracks appeared in the recovery rate. But the samples were tested and there were inconsistencies in their purchase information. Therefore, advanced signal processing is required for fatigue crack detection. Cracks on metal substrates of CFRP steel sheets were monitored by antenna sensors. The results show that cracks can be detected by analyzing the received signals with a vector network analyzer. However, the antenna sensors must be attached to the CFRP area with epoxy resin glue. At this point, a loud noise can be heard from the unstable part of the antenna. However, ECPT research on CFRP-strengthened steel structures is still very limited. Previously, the only ECPT distribution of steel members in CFRP reinforced steel structures was studied. Compared with single metal or single CFRP, CFRP reinforced steel structure has different electrical and thermophysical properties. This type of structure continuously produces a range of electromagnetic and thermal responses during ECPT. Therefore, this study aims to improve the ability of ECPT to test CFRP-strengthened steel structures by investigating the thermal responses of such a composite structure during ECPT testing.
Carbon Fiber Reinforced Polymer (CFRP) is a type of composite material consisting of carbon fiber and polymer. The carbon fiber provides strength and stiffness, while the polymer acts as a cohesive matrix that protects and holds the fibers together. CFRP is produced in strips, rods and sheets using various manufacturing techniques such as filament winding, pultrusion and hand laying.
ISSN: 2321-9653; IC Value: 45.98; SJ Impact Factor: 7.538
Volume 11 Issue I Jan 2023- Available at www.ijraset.com
Analyzing and describing the damage process quantitatively is crucial to increase the structure's functionality and reliability. Nondestructive testing (NDT) can optimize a CFRP structure, such as weave order, fiber orientation, local fiber and epoxy concentrations, and manufacturing process, which is a crucial prerequisite for component lifetime performance. Planar, perpendicular, and volumetric faults can all be found in material and can all be found with NDT. The induction and recovery of eddy currents in the test object, which heavily depends on the design and placement of the current sensor in any structural application such as buildings, bridges, etc., is one of the most crucial difficulties in current testing. A single air-injected coil or a multi-turn coil wound on a particular material former can be employed as the sensor's transmitter and receiver, respectively. There may be a wide range of coil count, former material, former shape, and sensor size options for some applications.
A. Aim
Eddy current pulse thermography will be used in the construction industry to find internal flaws in CFRP-reinforced steel constructions.
This project's primary goals can be summed up as follows:
1) Based on ECPT, an NDT approach is presented for CFRP-reinforced steel structures found in buildings and bridges.
2) The suggested technique is a promising means of identifying numerous internal flaws.
3) The non-destructive characterization of CFRP utilizing flow methods is the goal of this project's research.
4) It was examined how the microstructure of CFRP samples related to the signal of various induction probe types.
5) The materials must be inspected during production and maintenance to enhance the performance of CFRP.
6) To support the test procedure and show how the probe and sample were assembled, 3D Finite Element Method (FEM) computer simulations were created.
7) Develop a CFRP characterisation technique for building flow tests while awaiting the creation of test infrastructure.
ISSN: 2321-9653; IC Value: 45.98; SJ Impact Factor: 7.538
Volume 11 Issue I Jan 2023- Available at www.ijraset.com
The research paper and literatures collected on the various topics is listed below.
1) Malekmohammadi H. et. al. 2020, This piece by Eddy An developing method for non-destructive testing and evaluation of conductive materials is current stimulated thermography. However, because of extensive lateral heat diffusion, quantitative measurement of subsurface defect depth in metallic materials using thermographic techniques is challenging. The use of flowpulse compression thermography to identify surface and surface flaws in an aluminum sample at various depths is demonstrated in this research. The fault zone was fine-tuned using kernel principal component analysis and low-order sparse modeling, and the fault depth was calculated using a cross-point function.. The displacement feature has a monotonic connection with the depth of surface and subsurface defects, according to the experimental findings, and it can also identify whether a defect is inside or outside the eddy current skin depth. Additionally, a comparison of the characteristics and impulse response of aluminum and composites is provided
2) Tao Liang a., et. al. 2016, Effective flaw identification using eddy current pulse thermography is discussed in this article. With impact energies of J, 6 J, 8 J, and 10 J, impact injuries were created artificially. The CFRP driven by the high frequency AC coil exhibits a non-uniform distribution of eddy current due to structural degradation. According to Joule's law, the distribution of heat can be used to describe eddy current. And the damage has an impact on how heat moves through CFRP. The surface temperature captured by the infrared camera as a sequence of thermal images serves as a representation of the heat change. After that, defects are examined using heat distribution and thermal imaging patterns. Additionally, the amount of CFRP damage is minimal and cannot be readily seen from the initial thermal imaging because to J's low energy. To eliminate tiny flaws, a wavelet transform and principal component analysis (PCA) are integrated in a multi-resolution statistical analysis method. This technique discussed the capacity to identify damage from impact energy and enhanced the information from thermal imaging to discern flaws.
3) Abdeslam Aoukili et. al. 2018, In this article's current flow testing, the material's penetration depth is regulated by the conductivity of the examined material as well as the testing frequency. An developing nondestructive technology called transient eddy currents, also known as pulsed eddy currents, employs pulsed excitation to cause a brief electromagnetic response as a result of flaws in a deep conductive structure. With traditional methods like harmonic eddy currents or ultrasonography, such faults are challenging to inspect. The theoretical understanding of the impulse fluorescence phenomena has been discussed in a number of recent scientific articles, along with the planning of related experiments. The output signals were simulated as a function of the input electrical excitation signal using a finite element solution of the governing equations. In this work, a sensor simulation based on pulsed current is produced taking into account the B-scan technique, with the aim of evaluating the detectability of minor faults by observing the impedance changes of the detecting sensor.
4) Jürgen POHL et. al. 2016, Active thermographic techniques are discussed in this work as potential non-destructive testing tools for light carbon fiber reinforced plastic (CFRP) constructions. Thermal contrasts can be produced by a variety of excitation methods, including optical flashes, heat lamps, air jets, ultrasonic drives, electromagnetic induction, etc. Due to their ability to identify faults, sources that only have the benefit of selectively activating defects, such as ultrasonic excitation (here caused by vibrothermal effects), are of special interest. The typical benefits of active thermographic systems include large area testing and deep sensitivity, but for effective application, active heating and signal processing parameters must be taken into account.
5) Yoonjae Chung et. al. 2020, In this work, pulse thermography was used in an experimental study to find internal flaws in industrial pipelines and nuclear power plant secondary systems, which were the predominant deterioration processes. By drilling flat bottom holes (FBH) in the steel plate, material losses resulting from wall thinning were simulated. To assess the suggested technique's detection capacity, FBHs of various sizes and depths were taken into consideration. An infrared camera was used to examine the impact of the applied heat flux after a brief, high-energy light pulse was applied to the sample's surface. Thermography's three most well-known signal processing methods, principal component thermography (PCT), pulse phase thermography (PPT), and thermography signal reconstruction (TSR), have all been used to analyze raw thermal data.
6) Wenwei Ren a. et. al. 2013, In this study, various desirable features specific to NDTandE situations are provided by differentiating the value of this difference over an acceptable time interval. Divergence and shock energy are presented together with their relationship to transient thermal patterns and divergence, respectively. The relationship between composite structures and material condition, as well as the positive and negative values of decay, are examined. As a result of separation patterns and image regions, quantitative non-destructive evaluation (QNDE) of ECPT damage is performed. The outcomes of this suggested method demonstrate how severely the impact energy affect the fault zones. The work that is being proposed can be utilized to locate and measure CFRP impact damage, which is then employed in life cycle analysis and condition-based maintenance.
ISSN: 2321-9653; IC Value: 45.98; SJ Impact Factor: 7.538
Volume 11 Issue I Jan 2023- Available at www.ijraset.com
7) Guozeng Liu et. al. 2022, In this document, carbon fiber reinforced Carbon fiber reinforced composites (CFRP) are frequently utilized in aerospace and other industries in this article. The surface of the CFRP structure is vulnerable to impact and damage during maintenance, endangering the quality and safety of the CFRP. The sample is heated actively using a halogen lamp. A sample with impact damage is analyzed using the built-in optical pulse thermography (OPT) test equipment while being excited by lengthy pulses. Using an A655sc infrared camera, the thermal response of the impact damage samples was measured. The Pulse Phase Method (PPT), Thermal Signal Reconstruction (TSR), and Total Harmonic Distortion are used to process the original infrared image sequence.. The outcomes demonstrate an improvement in the signal-to-noise ratio (SNR) of the original images treated by PPT, TSR, and THD, while a notable improvement in SNR is observed for THD. Optical pulse thermography produces a more effective impact damage detecting effect.
8) Jing Xie et. al. 2021, In this paper The efficiency of current pulse thermography (ECPT) in identifying interior flaws in CFRPreinforced steel constructions is examined in this study. This paper discusses a number of internal failures of CFRPstrengthened steel structures, such as delaminations, gradual impact damage in CFRP, steel cracking, and debonding at the CFRP/steel interface. The impact of these faults on the structures' electromagnetic and thermal response is examined theoretically. To validate the theoretical findings, numerical and experimental experiments are carried out on CFRPstrengthened steel plates with different flaws. The faults under study can be examined by ECPT and expressed as lowtemperature zones in ECPT thermograms, according to numerical and experimental data. To further examine the thermal sensitivity of the CFRP surface, temperature variations and evolution of temperature profiles are examined in addition to the temperature characteristics of thermograms. Additionally, based on the outcomes of the experiments, it was shown that ECPT is successful in repairing the size and shape of faults.
9) LIU Zhiping et. al. 2016, In this article: The development of non-destructive testing (NDT) techniques for flaw detection and evaluation is receiving a lot of attention as interest in the use of composites and cellular sandwich panels in industrial sectors grows. In this study, the magnetic field intensity and conductivity were employed as two parameters to define different kinds of flaws in carbon fiber reinforced plastic (CFRP) laminates and tile panels. Pulsed eddy current (PEC) was also explored. The experimental findings demonstrate the effectiveness of the suggested approaches in detecting and assessing conductive and non-conductive insertion faults with low-energy effects from J to 12 J.In comparison tests with radiothermography and shearography, the efficacy of PEC scanning was established, and its benefits were examined.
10) Qiuji Yi, et. al. 2016, In the aerospace sector, finding flaws in carbon fiber reinforced composites (CFRP) with complex geometries has proven to be a difficult task. This article uses eddy pulse thermography (ECPT) and microwave NDT to locate and analyze a polluted bond and five unidentified wear patches in a CFRP specimen. It is motivated by the 2019 Aerospace NDT Student Challenge. Signal-to-noise ratio and detection probability are used to analyze and compare the results of the applicable approaches. The findings indicate that microwave NDT is ineffective in identifying human-induced bond wear or loosening. High SNR values allow for the detection of one polluted bond and four out of five carriers in ECPT.
11) A. Taram, et. al. 2016, Using electromagnetic induction to create heat flow in a material and capture its thermal reaction using an infrared camera constitutes eddy current thermography in this study. Changes in the distribution of heat are the basis for fault detection. It can be applied as either pulses or amplitude modulations and is a quick and accurate way to find surface flaws in metallic materials. In order to identify and quantify faults in steel material that has been supplied, modeling work employing pulsed eddy-flow thermography is described in this research. Software for Finite Element Analysis is Flux2D.
12) Xin Li , et. al. 2008, According to this study, a significant issue with many real-world applications of the material, particularly in the aerospace industry, is the lack of adequate inspection procedures for carbon fiber reinforced plastic composites (CFRP). This study uses eddy current techniques to characterize CFRP in a non-destructive manner. The signal of several induction probe types and the microstructure of CFRP samples were shown to be correlated. The electrical conductivity of the material's volume equivalent was measured using Deeds and Dodd's analytical solution as a foundation, which offers a means of anticipating and spotting material flaws such fiber breakage.. A high-directional probe was used to characterize the direction of the fiber in both unidirectional and multidirectional CFRPs. In order to support the experimental approach and demonstrate the interaction of probes and samples, 3D finite element method (FEM) computer simulations were created.
Research organizations and industry have both worked on CFRP NDT characterisation during the past few decades and made substantial advancements. The selection of an NDT method depends on the particular requirements and circumstances of the material and application, as was mentioned in the preceding section.
ISSN: 2321-9653; IC Value: 45.98; SJ Impact Factor: 7.538
Volume 11 Issue I Jan 2023- Available at www.ijraset.com
However, there are a number of highly developed and economically effective NDT techniques, such as the current flow method, ultrasonic NDT, and scanning acoustic microscopy, for characterisation of CFRP. Additionally, thermography and an X-ray scan are useful techniques for identifying CFRP.
The following is how the proposed work is intended to be completed:
1) Research on carbon fiber reinforced plastic (CFRP) in the building sector.
2) Research done on eddy current pulse thermography to find impact damage
3) CFRP Modeling - Modeling Techniques and Simulation
4) Materials Finite Element Modeling
5) Design-based system development and CFRP test preparation.
6) Equipment needed for the intended work
7) Software - The sample and probes were analyzed using computer FEM software.
The term "SFRR," which stands for Sarbon Fiber Reinforced Rlastis, refers to a somrosed combination of sorbon fiber and other materials or somrossor elements at the massrossor level that can solve individual and optimal errors and SFRRs. Scientists at the Royal Aircraft Factory in Farnborough, United Kingdom, employed carbon fiber from 1963 to 1996 to create new and improved aircraft that needed to be robust, light, and long-lasting.
SFRR parts have been used for almost 40 years in the construction, automotive, and aerospace industries. They are lightweight, have outstanding mechanical qualities, and are incredibly durable. Additionally, during the past 20 years, scientific organizations and businesses have focused more of their attention and resources on FRP surfaces that surround conventionally formed offshore oil platforms. On the other side, the French Republic, which is notably weak as a leading edge, is affected significantly by the rising availability of advanced substrate materials. Fast and dependable processing greatly enhances the creation and application of "FR.".
An infrared camera records the inspection object and the sample's response. The PT is renowned for its testing speed since the pulse's duration, which ranges from 2 to 10 milliseconds, depends on the sample's thermal conductivity. The temperature rises instantly after the sample is heated because the surface absorbs the light energy. The surface temperature inside the sample starts to decline as a result of the heat wave's spread. When the rate of heat degradation differs across the sample's surface, defects can be identified. When the rate of heat degradation of the sample surface varies, defects can be noticed.
ISSN: 2321-9653; IC Value: 45.98; SJ Impact Factor: 7.538
Volume 11 Issue I Jan 2023- Available at www.ijraset.com
Piezoelectric sensors, which are used in this manner, can only inspect a small portion of the beam and must be firmly attached to it. It was discovered that fatigue cracks in CFRP steel joined plates could be located using ultrasonic testing, which is based on a nonlinear Lamb wave. There was nonlinearity in the frequency representation of the detection data brought on by fatigue cracks. Controlled samples, however, also add nonlinearity to the detection data. As a result, detecting fatigue cracks requires complex signal processing. Cracks in the steel base of CFRP steel joint plates were examined using dust bins. The findings indicate that cracks can be examined by using a vector network analyzer to examine the detection signals. However, epoxy resin adhesive is required to affix the antenna sensors to the CFRP surface. Strong noise can also be produced by an unsteady antenna connection [15].
In the beginning, only the ECPT of steel members in steel structures enhanced by CFRP was looked into. CFRP reinforced steel structures have distinct electromagnetic and thermophysical properties when compared to single steel or single CFRP. As a result, during ECPT, such a structure would show various electromagnetic and thermal responses. Therefore, the purpose of this work is to examine the thermal responses of such a hybrid structure under ECPT management in order to confirm the ability of ECPT to control CFRP-strengthened steel structures.
The usefulness of Eddy Surrent Rule Temperature (ESRT) in assessing SFRR-reinforced steel buildings was examined and confirmed in this work. We looked into internal flaws including the SFRR sonnet/metal interface, SFRR layer crack, metal substrate cracking, and SFRR low-shear failures. Theoretical analyses and test results lead to the conclusion that ESRT successfully examines different sorts of flaws in reinforced steel structures before SFR, offering a foresighted and trustworthy approach for estimating the service life of this somrosita structure. Future research will concentrate on how well E can identify flaws and contributing elements in various varieties of FR/structural steel structures, such as adhesion and FR ck sk layer systems. In this study, metal structure wall damage is found using pulse heat technology. Updated TSR, CT, and other fundamentals for thermal imaging and analysis. Based on enhanced error detection and SNR, the effectiveness of each signal processing technique was assessed. Based on the findings, it was determined that applying the method can lead to considerable gains in feature detection and SNR values. TSR offers considerable advances in the detection of enhanced spatial and temporal tuning as well as the capacity to produce time-lapse photos, albeit it offers images with a lesser resolution than green thermal imaging. TSR, however, might be impacted by variations in outcomes between situations or cases.
[1] Yi, Q., Malekmohammadi, H., Tian, G. Y., Laureti, S., & Ricci M. “Quantitative evaluation of cracks’ depth on a thin aluminum plate by using eddy current pulse-compression thermography”, IEEE 2020, Transactions on Industrial Informatics , 16(6), 3963-3973
[2] Tao Liang a, Wenwei Ren a,⇑, Gui Yun Tian a,b,⇑, Mutaz Elradi a, Yunlai Gao b , “Low energy impact damage detection in CFRP using eddy current pulsed thermography”, Elsevier 2016, Composite Structures 143 (2016) 352–361
[3] Abdeslam Aoukili1,a and Abdellatif Khamlichi, “Damage detection of cracks in carbon fibre reinforced composites by pulsed eddy-current testing”, MATEC Web of Conferences 191, 00003 (2018).
[4] Jürgen POHL ,”Active Thermographic Testing of CFRP with Ultrasonic and Flash Light Activation “,19th World Conference on Non-Destructive Testing
2016
[5] Yoonjae Chung 1, Ranjit Shrestha 2 , Seungju Lee 3 and Wontae Kim 4,”Thermographic Inspection of Internal Defects in Steel Structures: Analysis of Signal Processing Techniques in Pulsed Thermography”, MDPI/2020.
ISSN: 2321-9653; IC Value: 45.98; SJ Impact Factor: 7.538
Volume 11 Issue I Jan 2023- Available at www.ijraset.com
[6] Wenwei Ren a, Jia Liu a, Gui Yun Tian a,b,⇑, Bin Gao b, Liang Cheng b, Hailong Yang ,”Quantitative non-destructive evaluation method for impact damage using eddy current pulsed thermography ,” Elsevier /2013
[7] Guozeng Liu(1), Weicheng Gao(1)*, Wei Liu(1), Yanze Wei(1), Jianxun Xu(1), Rui Li(2), Runhong Shen ,”Study on impact damage defects of carbon fiber reinforced composites by optical pulse thermography” IEEE/2022
[8] Jing Xie, Changwei Wu, Lemei Gao, Changhang Xu ⇑, Yinsheng Xu, Guoming Chen,” Detection of internal defects in CFRP strengthened steel structures using eddy current pulsed thermography” , Elsevier /2021.
[9] LIU Zhiping1,a,LI Xuan1,b, LI Mingchang2,c,LIU Xingle1,d,KE Liang1,e , “Research of Detecting Methods of Welding Cracks in CFRP-Steel Structures Based on Eddy Current Pulsed Thermography” Materials Science Forum/ISSN: 1662-9752, Vol. 860/2016.
[10] Qiuji Yi1, Adi Mahmud Jaya Marindra1, Junzhen Zhu1,*, and Abdoulaye Ba2 ,” Detection of Unknown Defects in CFRP Using Eddy Current Pulsed Thermography and Microwave NDT “IEEE/ 2016.
[11] Detection of Subsurface Defects in Steels using Pulsed Eddy Current Thermography by A. Taram, C. Roquelet, M. Anderhuber P. Meilland, K. Mouhoubi, JL Bodnar- 2016
[12] Characterization of Carbon Fibre Reinforced Composite by Means of Non-Destructive Eddy Current Testing and FEM Modeling by Xin Li, W Yin, Ze Liu, Philip J. Withers , A J Peyton-2008.
[13] Non-contact characterisation of Carbon Fibre Reinforced Plastics in hybrid aluminium / CFRP sheets using multi-frequency eddy current sensors-2009.
[14] Probability of Detection for Eddy Current Pulsed Thermography of Angular Defect Quantification-2018.
[15] Emmanuel P. Papadakis, “Quality degradation due to shipment of nonconforming product under statistical process control in the absence of quarantining”, Materials Evaluation, Vol. 51(11), pp. 1274–1278, 1993.
[16] P J James, “The role of non-destructive testing in the control of boiler tube failures”, Insight, Vol. 37(2), pp. 179-183, 1995.
[17] Chuck Hellier, “Handbook of Non-destructive evaluation”, McGraw-Hill Professional, 2001, ISBN0-07-028121-1; ISBN0-07-139947-X.
[18] K. N. Hitchcock, “Design evaluation through improved non-destructive testing technology”, British Journal of NDT, Vol. 33(4), pp. 167-171, 1991.
[19] P.J. Heffernan, “Fatigue behaviour of reinforced concrete beams strengthened with CFRP laminates”, PhD thesis, Royal Military College of Canada, 1997.
[20] J. Waller, “Carbon fibre cement composites”, Civil Engineering and Public Works Review 67, 789, pp. 357 361, 1972.