10 VII July 2022 https://doi.org/10.22214/ijraset.2022.46039
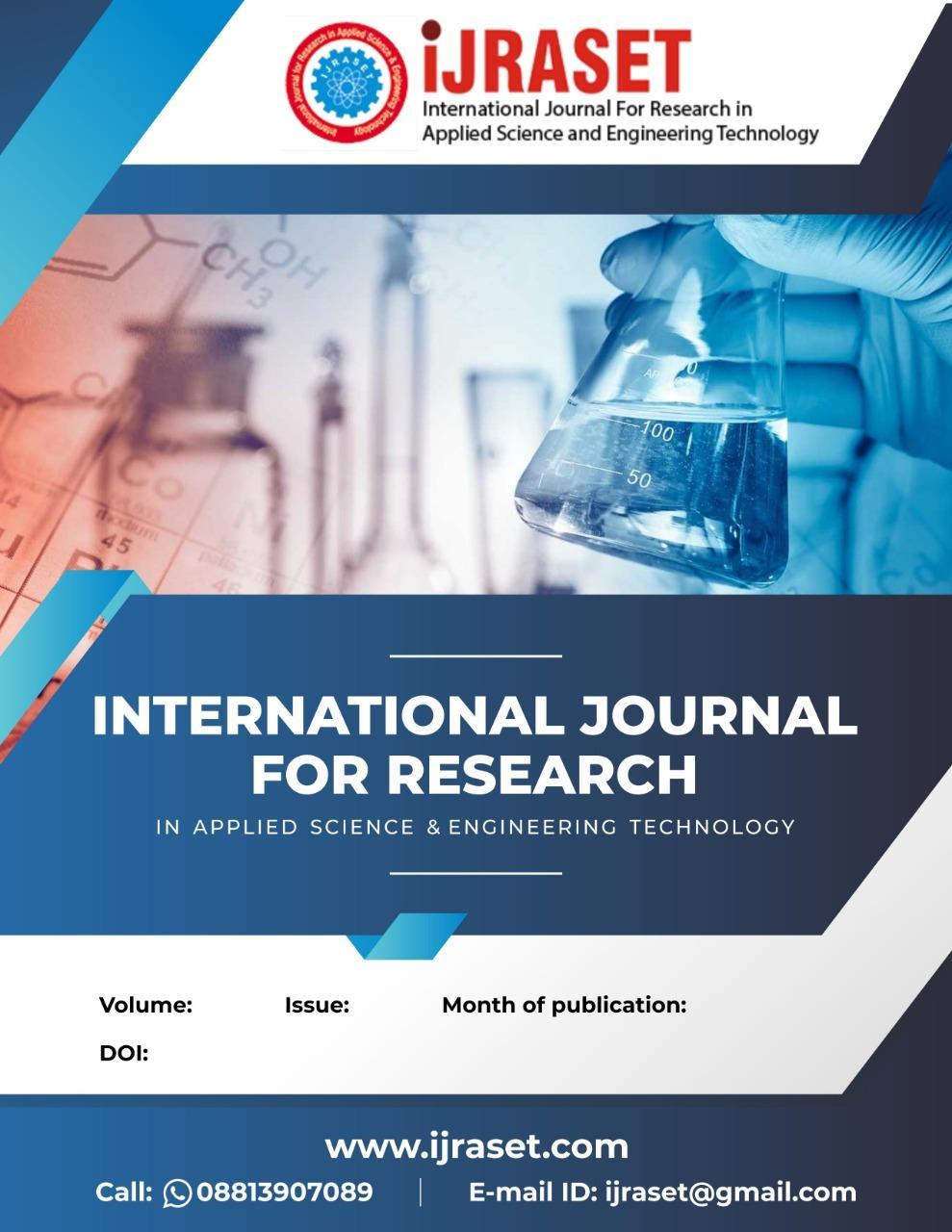
2) Glass Powder: Waste glass is easily available in shops is collected and made glass powder. Before adding this glass material into concrete we have to crush it first into desired size. For study glass powder size more than 800 μm and less than 1200 μm.
Tanveer Ansari1 ,Abhishek Mishra2 , Kumar Vanshaj3
International Journal for Research in Applied Science & Engineering Technology (IJRASET) ISSN: 2321 9653; IC Value: 45.98; SJ Impact Factor: 7.538 Volume 10 Issue VII July 2022 Available at www.ijraset.com 4898©IJRASET: All Rights are Reserved | SJ Impact Factor 7.538 | ISRA Journal Impact Factor 7.894 |
1MTech Student Structural Engineering, Institute of Engineering & Technology Lucknow
In order to form concrete business property, the utilization of waste materials in situ of natural resources is one in every of the simplest approaches. A massive amount of waste glass is generated all round the world. In India, 0.7% of total urban waste generated includes of glass. GBP produces over 4 million heaps of waste glass annually. Waste glass is crushed into given sizes to be used as mixture in numerous applications like water filtration, grit application, sand protect sport turf and sand replacement in concrete. Concrete is most generally used imitation construction material and its demand is increasing day by day. Glass is a waste material which is abundantly discarded after use though a considerable quantity is recycled. Disposing of glass may cause environmental hazards as it does not decompose. Hence in the recent years use of glass powder in concrete is found to be advantageous in making it a sustainable construction material. Glass powder has not only ben used as fine aggregate replacement, but also as cement replacement as some researchers have reported that it has some pozzolanic reaction. Depending on its fineness and composition of the raw material it exhibits different degrees of pozzolanic reactivity. Based on durability parameters, studies show that the rapid chloride penetration of concrete containing glass is less compared to conventional concrete. It is also evident from researchers that finer glass powder used up to 30% replacement to cement has been very effective in mitigating alkali silica reaction in concrete. In this study, the strength characteristics of an economical high strength concrete. The focus on the experimental investigation in this study is to determine the improvement in the properties of a high strength with glass powder and to study the durability parameters which will enable the researchers and construction industry to use these materials in their construction.
1) Cement, Water, Aggregate: Concrete is prepared by mixing various materials like cement, Water, aggregates etc. which are economically available. IS 8112 is used for the work. The fine aggregate used in this investigation was clean river sand, whose maximum size is 4.75 mm, conforming to grading zone II. Machine crushed granite stone is used as coarse aggregate . Two size of coarse is used; one 10 mm passing through 4.75 mm retained and other 20 mm passing through 10mm retained. As per IS: 2486 1964 recommendations the following properties of coarse aggregates were determined.
B. Methodology
3Assistant Professor CED, Institute of Engineering & Technology Lucknow
II. METHODOLOGY & EXPERIMENTAL INVESTIGATION
Keywords: Glass powder, Flexural Strength Test, Split Tensile Test Compressive Strength Test, Tensile Strength Test I. INTRODUCTION
Cementations composites satisfy various civil engineering requirements such as high durability or impact load resistance. To study the behaviour of reinforced concrete with different volume ratios, nearly 36 specimens were cast and tested for compressive test,24 specimens were cast and tested for tensile strength test and 12 specimens were cast and tested for Flexural test.
Abstract: The concrete trade is one in every of the biggest customers of natural resources because of that property of concrete trade is underneath threat. The environmental and economic concern is that the biggest challenge the concrete trade is facing, the problems of environmental and economic concern are self-addressed by the utilization of waste glass as partial replacement of fine aggregates in concrete. In order to improve the mechanical properties of concrete fine aggregates will be replaced by waste glass powder as 20% ,25 and 30% weight for M-45 design mix. The concrete specimens will be tested for compressive strength at 7 ,14 and 28 days respectively and Split tensile Strength at 7 and 28 days and Compressive Strength test at 28 days also the results obtained will be compared with those of traditional concrete.
Partial Replacement of Fine Aggregate by Glass Powder in Concrete
2Assistant Professor CED, Institute of Engineering & Technology Lucknow
A. Material Used
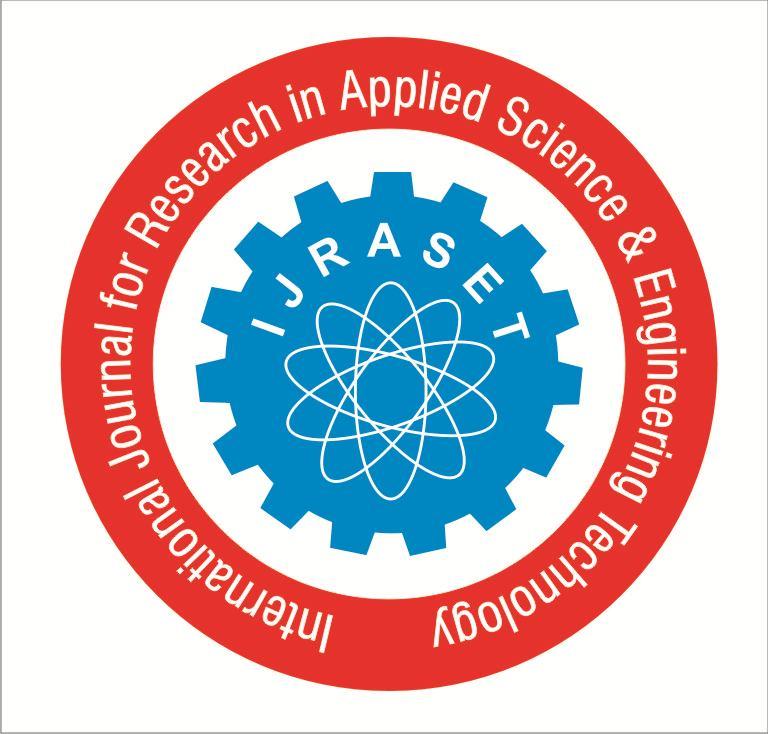
b) Compression test for glass powder mix concrete
4) Compressive Strength Test
5) Tensile Strength Test
a) Specific gravity
3) Test On Final Product Testing of specimen
a) Casting detail of specimen
6) Flexural Test For Flexural test, Total 12 beam specimens of size 750 x 150 x 150 mm were cast for M45 grade of concrete. The moulds were filled with different proportions of cement, glass powder. Vibration was given to the moulds using table vibrator. The top surface of the specimen was leveled and finished. After 24 hours the specimens were demoulded and were transferred to curing tank wherein they were allowed to cure for 28 days. After 28 days of curing, these cubes were tested on three point load testing machine as per I.S. 516 1959. The failure load was noted. The beam were tested and their average value is reported.
2) Tests on Fine Aggregate
a) Fineness test by sieve analysis
c) Split Tensile Test for glass powder mix concrete
For Tensile Strength test, Total 24 cylinderical specimens of size 300 x 150 mm were cast for M45 grade of concrete. The moulds were filled with different proportions of cement, glass powder. Vibration was given to the moulds using table vibrator. The top surface of the specimen was leveled and finished. After 24 hours the specimens were demoulded and were transferred to curing tank wherein they were allowed to cure for 7 and28 days. After 7 and28 days of curing, these cubes were tested on compression testing machine as per I.S. 5816 1999. The failure load was noted. The cubes were tested and their average value is reported. The formula used for tensile strengthP=maximumWhere,calculation: load in Newtons applied to the noted before testing. I = length of the specimen (in mm), and d = cross sectional dimension of the specimen
c) Initial and final setting time by using Vicat apparatus
b) Sieve Analysis
b) Standard consistency test using Vicat apparatus
International Journal for Research in Applied Science & Engineering Technology (IJRASET) ISSN: 2321 9653; IC Value: 45.98; SJ Impact Factor: 7.538 Volume 10 Issue VII July 2022 Available at www.ijraset.com 4899©IJRASET: All Rights are Reserved | SJ Impact Factor 7.538 | ISRA Journal Impact Factor 7.894 | C. Test 1) Tests on Cement In Cement, the tests conducted were:
For compression test, Total 36 cube specimens of size 150 x 150 x 150 mm were cast for M45 grade of concrete. The moulds were filled with different proportions of cement, glass powder. Vibration was given to the moulds using table vibrator. The top surface of the specimen was leveled and finished. After 24 hours the specimens were demoulded and were transferred to curing tank wherein they were allowed to cure for 7,14,28 days. After 7,14,28 days of curing, these cubes were tested on compression testing machine as per I.S. 516 1959. The failure load was noted. The cubes were tested and their average value is reported. The formula used for compessive strength calculation: Compressive strength (MPa) = Failure load / cross sectional area
d) Three Point Load Test for glass powder mix concrete
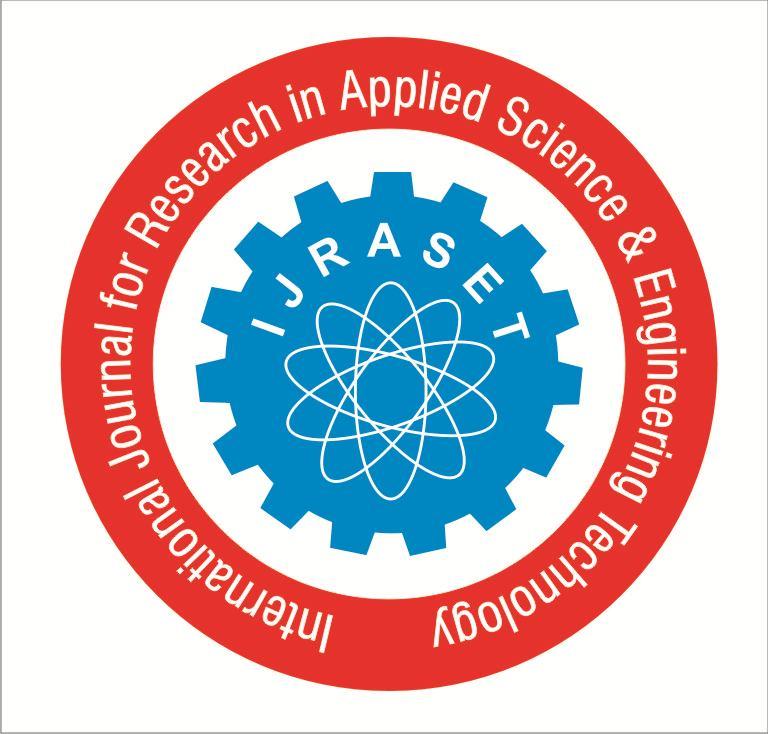
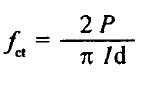
International Journal for Research in Applied Science & Engineering Technology (IJRASET) ISSN: 2321 9653; IC Value: 45.98; SJ Impact Factor: 7.538 Volume 10 Issue VII July 2022 Available at www.ijraset.com 4900©IJRASET: All Rights are Reserved | SJ Impact Factor 7.538 | ISRA Journal Impact Factor 7.894 | III. RESULTS AND DISCUSSION A. Compression Test 1) For 0% glass Powder replacement of fine aggregate: 2) For 0%& 20% glass Powder replacement of fine aggregate:%powderwithaggregatesofreplacmentoffineglass StrengthCompressive in N/mm2( 7 Days) StrengthCompressive in N/mm2( 14 Days) StrengthCompressive in N/mm2( 28 Days) 0% 35.33 48.12 53.83 % powderwithaggregatesofreplacmentoffineglass StrengthCompressive in N/mm2( 7 Days) StrengthCompressive in N/mm2( 14 Days) StrengthCompressive in N/mm2( 28 Days) 0% 35.33 48.12 53.83 20% 37.07 48.78 55.37
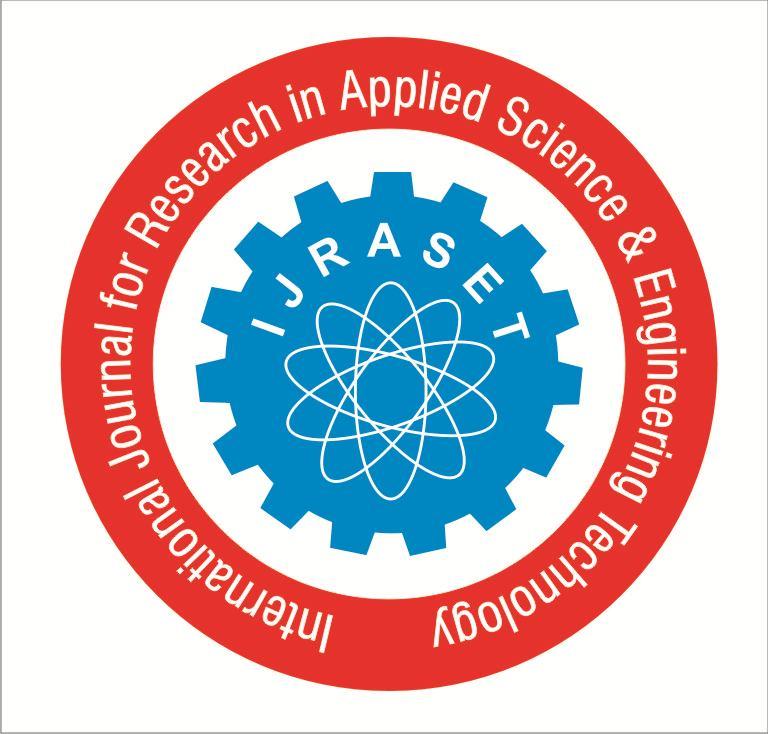
















International Journal for Research in Applied Science & Engineering Technology (IJRASET) ISSN: 2321 9653; IC Value: 45.98; SJ Impact Factor: 7.538 Volume 10 Issue VII July 2022 Available at www.ijraset.com 4901©IJRASET: All Rights are Reserved | SJ Impact Factor 7.538 | ISRA Journal Impact Factor 7.894 | 3) For 0%& 25% glass Powder replacement of fine aggregate: 4) For 0%& 30% glass Powder replacement of fine aggregate: B. Tensile Strength Test 1) For 0% glass Powder replacement of fine aggregate: % powderwithaggregatesofreplacmentoffineglass StrengthCompressive in N/mm2( 7 Days) StrengthCompressive in N/mm2( 14 Days) StrengthCompressive in N/mm2( 28 Days) 0% 35.33 48.12 53.83 25% 37.86667 49.23 55.85667 % powderwithaggregatesofreplacmentoffineglass StrengthCompressive in N/mm2( 7 Days) StrengthCompressive in N/mm2( 14 Days) StrengthCompressive in N/mm2( 28 Days) 0% 35.33 48.12 53.83 30% 34.86667 46.9 52.22667 % of replacment of powderwithaggregatesfineglass strengthTensile in N/mm2 (7 days) strengthTensile in N/mm2 (28 days 0% 3.89 5.7
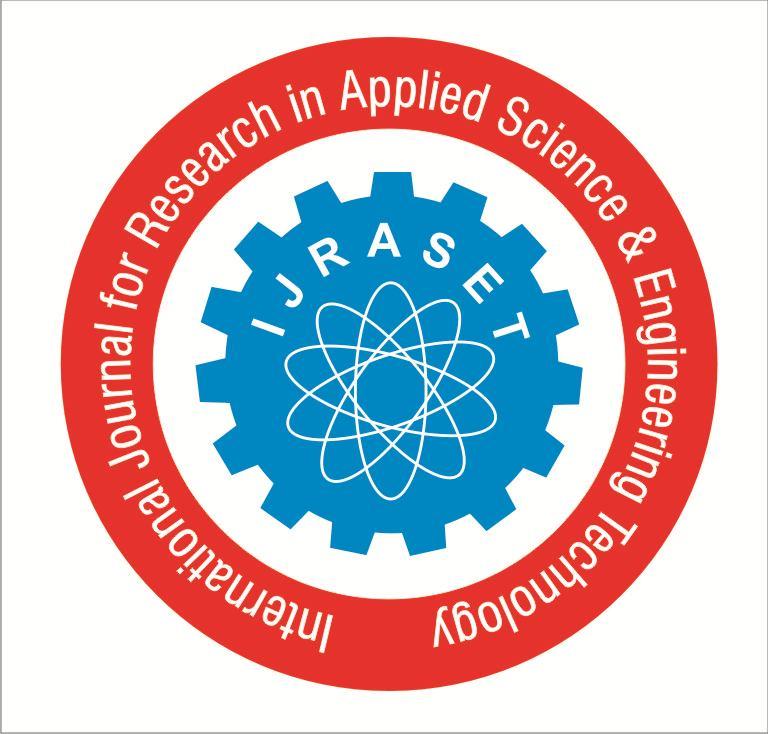
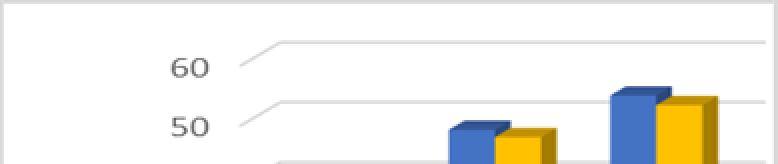
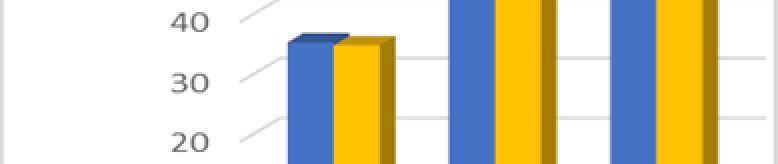
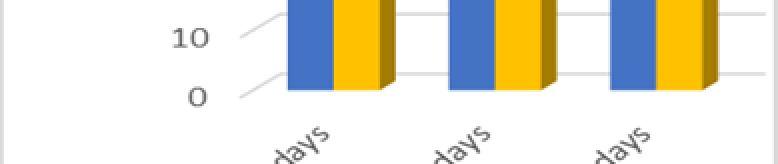
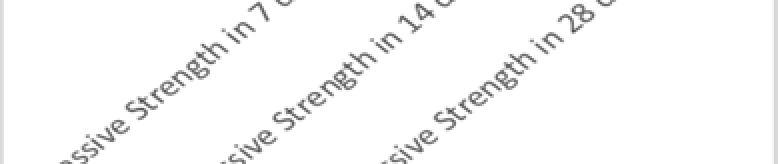
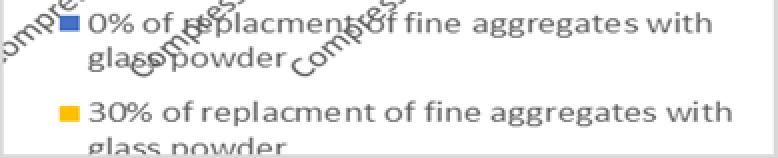






International Journal for Research in Applied Science & Engineering Technology (IJRASET) ISSN: 2321 9653; IC Value: 45.98; SJ Impact Factor: 7.538 Volume 10 Issue VII July 2022 Available at www.ijraset.com 4902©IJRASET: All Rights are Reserved | SJ Impact Factor 7.538 | ISRA Journal Impact Factor 7.894 | 2) For 0% & 20% glass Powder replacement of fine aggregate: 3) For 0% & 25% glass Powder replacement of fine aggregate: 4) For 0% & 30% glass Powder replacement of fine aggregate: % of replacment of powderwithaggregatesfineglass strengthTensile in N/mm2 (7 days) strengthTensile in N/mm2 (28 days 0% 3.89 5.7 20% 3.90 5.816667 % of replacment of fine powderwithaggregatesglass strengthTensile in N/mm2 (7 days) strengthTensile in N/mm2 (28 days 0% 3.89 5.7 25% 3.93 6 % of replacment of fine aggregates with glass powder Tensile strength in N/mm2 (7 days) Tensile strength in N/mm2 (28 days 0% 3.89 5.7 30% 3.77 5.673333
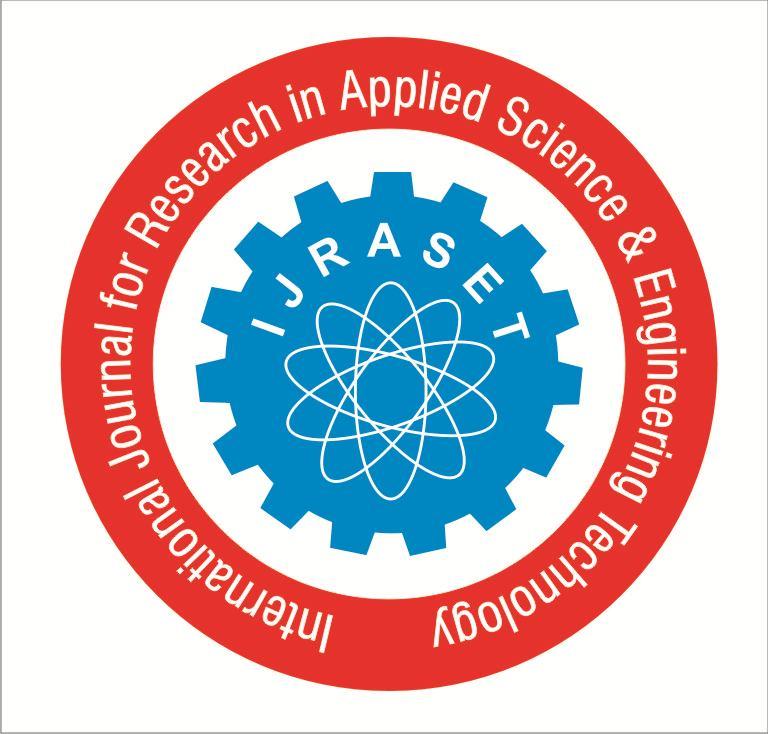









International Journal for Research in Applied Science & Engineering Technology (IJRASET) ISSN: 2321 9653; IC Value: 45.98; SJ Impact Factor: 7.538 Volume 10 Issue VII July 2022 Available at www.ijraset.com 4903©IJRASET: All Rights are Reserved | SJ Impact Factor 7.538 | ISRA Journal Impact Factor 7.894 | C. Flexural Test 1) For 0% glass Powder replacement of fine aggregate: 2) For 0% & 20% glass Powder replacement of fine aggregate: 3) For 0% & 25% glass Powder replacement of fine aggregate: % of replacment of fine aggregates with glass powder Flexural strength in N/mm2 (28 days) 0% 7.02 % of replacment of fine aggregates with glass powder Flexural strength in N/mm2 (28 days) 0% 7.02 20% 7.53 % of replacment of fine aggregates with glass powder Flexural strength in N/mm2 (28 days) 0% 7.02 25% 7.62
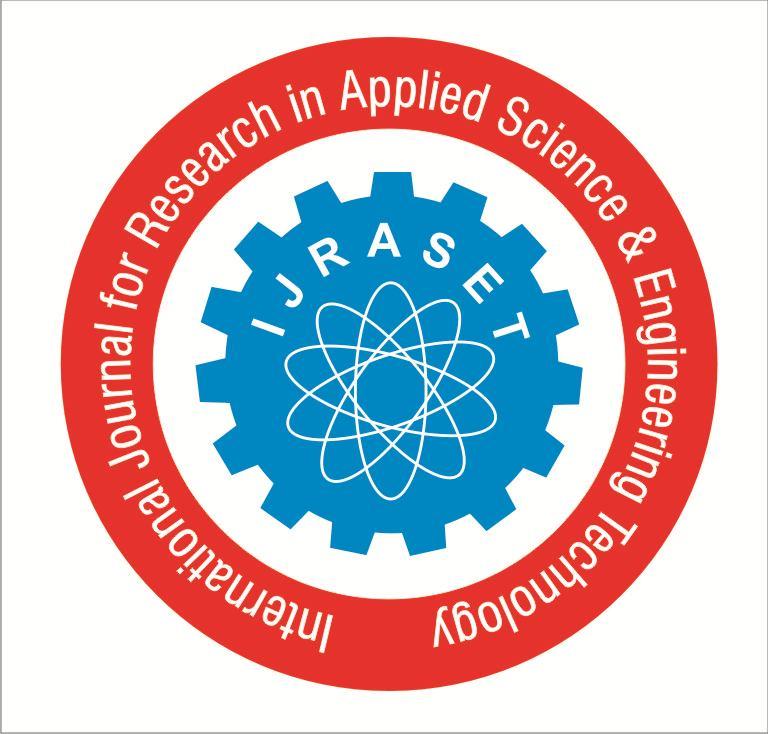













[11] Binwei, ‘‘Degradation of basalt fibre and glass fibre / epoxy resin composites in sea water, Corrosion Science,53,(1),(2011),426 431,https://doi.org/10.1016/ .corsci.2010.09.053
[9] I.D.G. Ary Subagia, Y. Kim, A study on flexural properties of carbon basalt/ epoxy hybrid composites, J. Mech. Sci. Technol. 27 (2013) 987 992, https://doi org/10.1007/s12206 013 0209 5.
[3] Carpenter, A. J. and Cramer, C.M, “Mitigation of ASR in pavement patch concrete that incorporates highly reactive fine aggregate”, Transportation Research Record 1668, Paper No. 99 1087, pp. 60 67,1999.
In this research we had found that
2) Tensile strength concrete of M45 grade of concrete using replacement of fine aggregates with glass powder at proportion 20%,25% and 30% for 7 days and 28 days . It was found that the compressive strength of concrete for 7 and 28 days were increased at 20% and 25% replacement of fine aggregates with glass powder about 2.11% and 5.27% as compared with conventional concrete at 28 days.
REFERENCES
[2] P Turgut and E.S. Yahlizade, “Research into Concrete Blocks with Waste Glass”, International Journal of Civil and Environmental Engineering 1:4 2009.
[14] V. Fiore, T. Scalici, G. Di Bella, A. Valenza, A review on basalt fibre and its composites, Composite part B: Engineering 74 (2015) 74 94, https://doi.org/ 10.1016/j.compositesb.2014.12.034.
1) For M45 grade of concrete using replacement of fine aggregates with glass powder at proportion 20%,25% and 30% . It was found that the compressive strength of concrete for 7,14 and 28 days were increased at 20% and 25% replacement of fine aggregates with glass powder about 1.29% and 2.31% as compared with conventional concrete at 28 days
[1] Asoka Pappu, Mohini Saxena, and R. Shyan Asolekar, “Solid Waste Generation In India And Their Recycling Potential In Building Materials”, Regional Research Institute (CSIR) and IIT Bombay, India.
3) Flexural strength of M45 grade of concrete using replacement of fine aggregates with glass powder at proportion 20%,25% and 30% for 28 days. . It was found that the compressive strength of concrete for 28 days were increased at 20% and 25% replacement of fine aggregates with glass powder about 4.14% and 8.55% as compared with conventional concrete at 28 days. From the above results discussion it is concluded that replacement of fine aggregates with glass powder at proportion 25% gives better result of compressive, tensile as well as flexural strength as compared to the conventional concrete
[10] Chaohuajiangke Fan, Feiwu, Da Chen, ‘‘Experimental study on the mechanical properties and microstructure of chopped basalt fibre reinforced concrete”, Materials and Design 58, 2014: 187 193, https://doi.org/10.1016/ j.matdes.2014.01.056
% of replacment of fine aggregates with glass powder Flexural strength in N/mm2 (28 days) 0% 7.02 30% 6.93
International Journal for Research in Applied Science & Engineering Technology (IJRASET) ISSN: 2321 9653; IC Value: 45.98; SJ Impact Factor: 7.538 Volume 10 Issue VII July 2022 Available at www.ijraset.com 4904©IJRASET: All Rights are Reserved | SJ Impact Factor 7.538 | ISRA Journal Impact Factor 7.894 | 4) For 0% & 30% glass Powder replacement of fine aggregate: IV. CONCLUSION
[7] John Branstonsreekanta das, Sara Y. Kenno, Craigtaylor, ‘‘Mechanical behaviour [8] of basalt fibre reinforced concrete”, Construction and Building Materials, 124, (2016): 878 886. 10.1016/j.conbuildmat.2016.08.009
[5] B.Ahmet Kızılkanat, ‘‘Mechanical properties and fracture behaviour of basalt and glass fibre reinforced concrete”, Construction and Building Materials, 100 (15), (2015): 218 224, https://doi.org/10.1016/j.conbuildmat.2015.10.006
[6] Jongsungsim,, Characteristics of basalt fibre as a strengthening material for concrete structures, Compos. B Eng. 36 (6 7) (2005) 504 512, https://doi.org/ 10.1016/j.compositesb.2005.02.002.
[13] Ahmad Altalmas, Farid Abed, Bond durability of basalt fibre reinforced polymer bars embedded in concrete under direct pull out conditions, J. Compos. Constr. 24 (2014), https://doi.org/10.1061/(ASCE)CC.1943 5614.0000544.
[12] V. Fiore, A. Valenza, glass basalt/ epoxy hybrid composites for marine Application, Mater. Des. 32 (4) (2011) 2091 2099, https://doi.org/10.1016/ j.matdes.2010.11.043.
[4] T.M Borhan, C.G.Bailey, ‘‘Structural behaviour of basalt fibre reinforced glass concrete slabs. Materials and Structures, 47, (2014): 77 87, https://doi.org/ 10.1617/s11527 013 0046 0
This investigation intent to evaluate the effective utilization of glass powder on concrete. A concrete grade M45 was designed as per IS 10262:2000 for this concrete mix. The water cement ratio 0.33 was adopted. The main aim of this investigation to find the improvement in compressive strength,tensile strength and flexural strength of a given mix by replacement of fine aggregate with glass powder at proportion 20%,25% and 30%
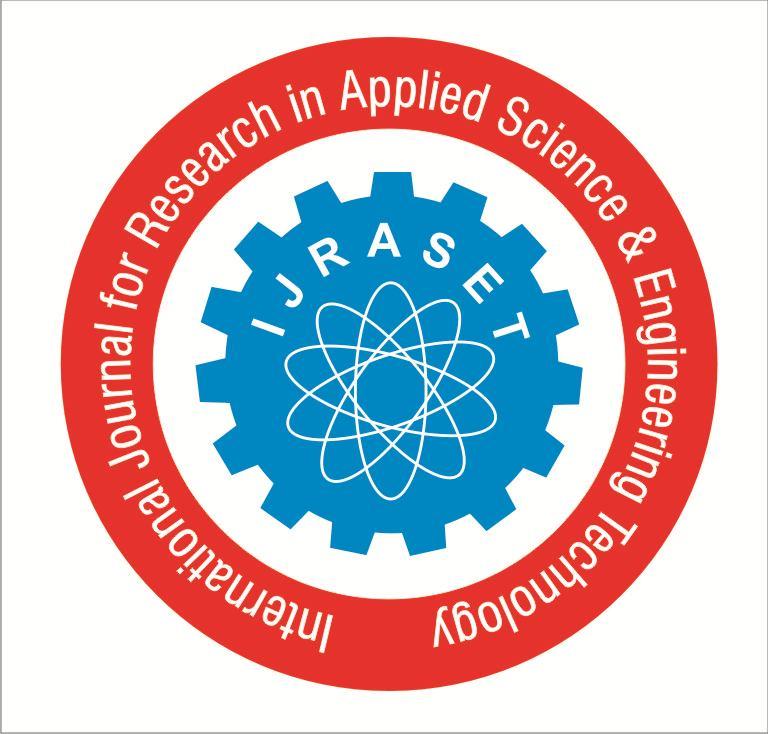






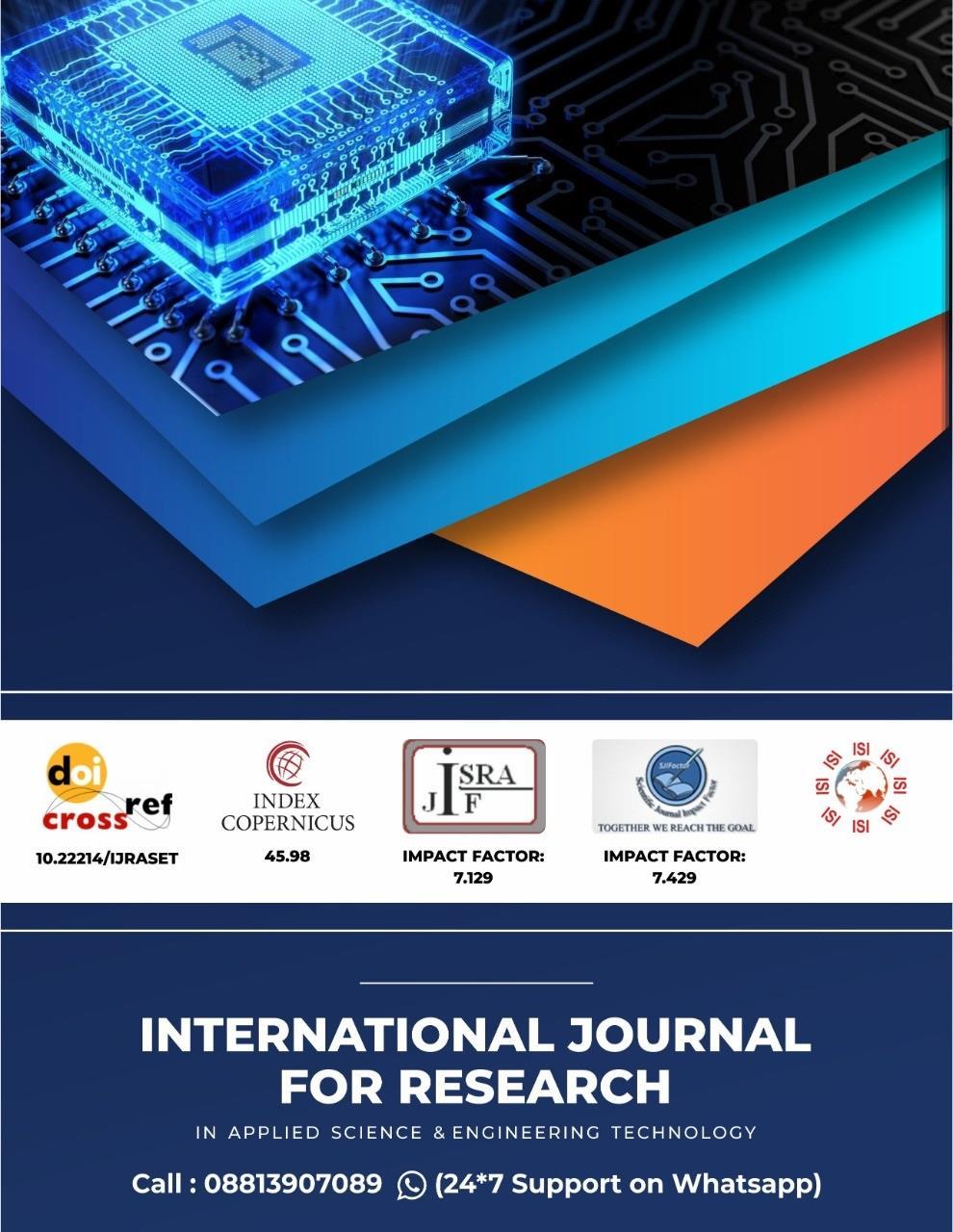