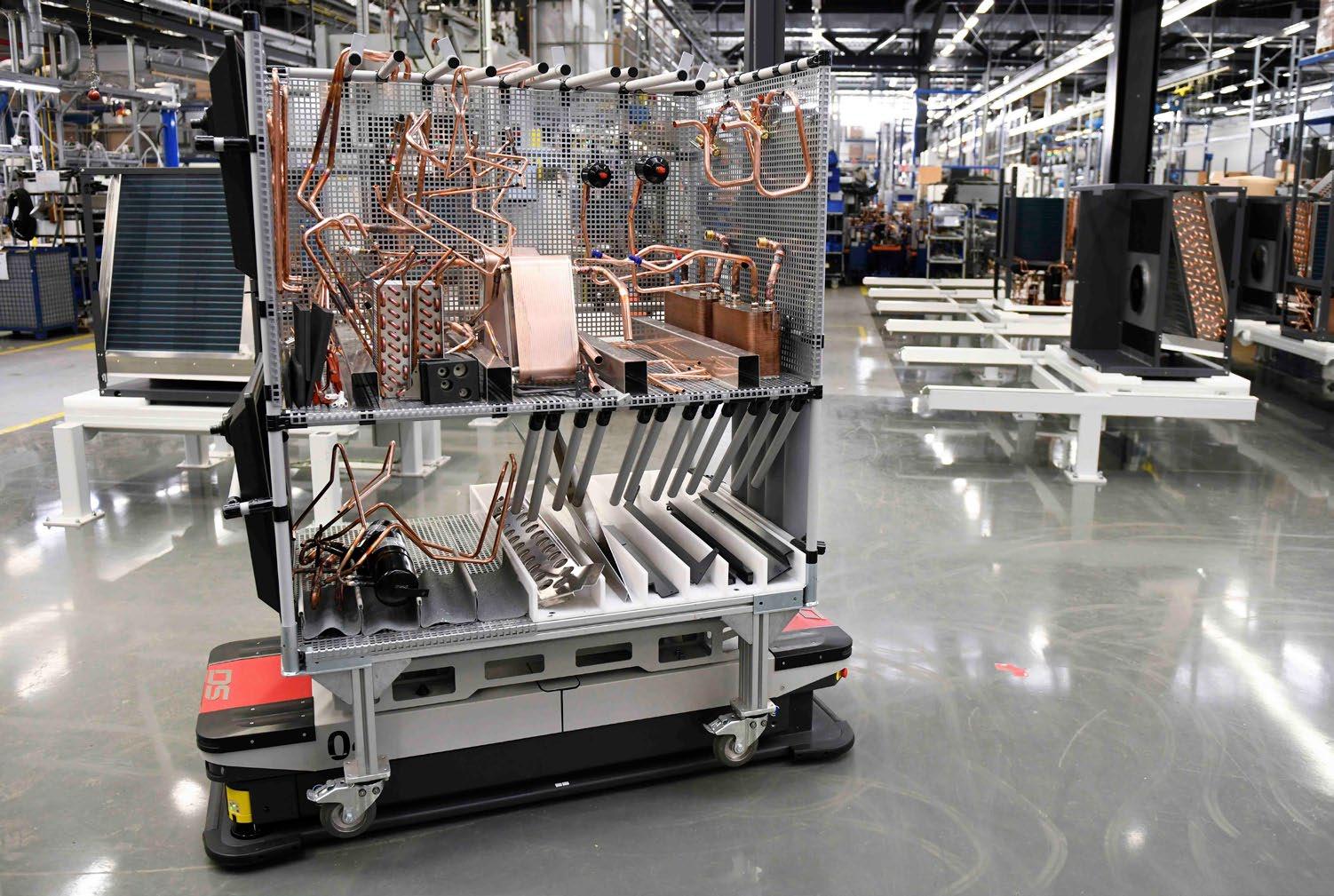
2 minute read
WERTVOLLE ERKENNTNISSE IN NAHEZU ECHTZEIT
Produktion und Lager getrennt voneinander zu organisieren und mit zwei separaten Systemen zu betreiben ist ein noch häufig verbreiteter Status Quo. Dem gegenüber steht das Konzept einer intelligenten Fabrik, das häufig auch „Smart Factory“ genannt wird. Denn eine intelligente Fabrik ist ein Konzept, bei dem eine Fertigung nahezu automatisch produziert und sich durch den Einsatz fortschrittlicher Technologien wie Künstlicher Intelligenz, Robotik, IoT und Analysen von Massendaten selbststeuernd kontinuierlich verbessert. Durch die umfassende Automatisierung werden Vorteile im Bereich der Effizienz, Flexibilität, Qualität und Sicherheit erreicht sowie nachhaltige Wettbewerbsvorteile geschaffen.
Die Grundvoraussetzung für diese Vision ist allerdings ein nahtloses Zusammenspiel von Produktion, Logistik und IT sowie eine leistungsstarke IT-Infrastruktur, die es ermöglicht, große Mengen an Daten schnell und zuverlässig zu analysieren. Dadurch können zielgerichtet Entscheidungen getroffen werden. Diese Steuerungsinformationen dürfen nicht auf spezifische Abteilungen beschränkt sein, sondern sollten durch eine offene und standardisierte Kommunika- tionsarchitektur zwischen verschiedenen Systemen ausgetauscht und im jeweiligen Kontext neu interpretiert werden.
Nur so kann eine Prozessmodellierung End-to-End (E2E) vorgenommen und eine optimale Abstimmung von Abläufen aus verschiedenen Abteilungen erreicht werden. Das ist letztendlich das angestrebte Ziel einer Smart Factory.
iEND-TO-END-PROZESS
Ein End-to-End-Prozess (auch als „von Anfang bis Ende“ oder „vom Kunden bis zum Kunden“) ist ein Prozess, der sämtliche Schritte von der Erfassung eines Bedarfs oder einer Anforderung bis hin zur finalen Lieferung oder Erfüllung einschließt. Dadurch können abteilungs- und systemübergreifende Synergien und Abhängigkeiten zwischen den einzelnen Prozessen erkannt und genutzt werden, um ein Höchstmaß an Effizienz zu erreichen.
INTEGRATION VON PRODUKTIONS- UND INTRALOGISTIKPROZESSEN
Weder Produktion noch Intralogistik eines Unternehmens sind für sich gesehen unabhängig. Produktion und Intralogistik sind eng miteinander verbunden, da die Produktion auf die Intralogistik angewiesen ist, um die Materialien und Werkzeuge bereitzustellen, die benötigt werden. Die Intralogistik ist auf die Produktion angewiesen, um Produkte innerhalb der Fabrik zu transportieren und einzulagern. Wird diese gegenseitige Abhängigkeit nicht mitberücksichtigt und handeln die beiden Abteilungen losgelöst voneinander, kann es vielfach zu Leerlaufzeiten und Überbeständen kommen, die zu höheren Produktions- und Lagerkosten führen.
BEISPIEL AUS DER PRAXIS (KONTEXT „MATERIALBEREITSTELLUNG“)
HERAUSFORDERUNG:
Maximale Materialverfügbarkeit bei minimalem Lagerbestand an der Linie.
PROBLEMSTELLUNG:
Die Probleme, die durch Silodenken und Insellösungen auftreten können, werden u. a. im Kontext der „Materialbereitstellung“ deutlich: Während das Manufacturing Execution System (MES) eines Unternehmens die Steuerung des Produktionsprozesses unterstützt und Verbräuche erfasst, verantwortet die Lagerverwaltungssoftware (LVS) die Überwachung der Bestände, um sicherzustellen, dass benötigte Materialien an den richtigen Stellen im Werk verfügbar sind. Gesetzt den Fall, dass beide Systeme nicht miteinander kommunizieren, wird entweder zu viel Sicherheitsbestand an der Produktionslinie gelagert oder Stillstände drohen, da benötigte Materialien nicht mehr verfügbar sind, bevor das LVS Nachschub bereitstellt. Kurzfristige Veränderungen der Produktionsplanung verschärfen diese Risiken, da Änderungen des Produktionsprogramms meist auch mit abweichenden Materialbedarfen an der Linie einhergehen, die oft innerhalb einer sehr kurzen Zeitspanne bereitgestellt werden müssen.
Die zentrale Prozesssteuerung wird erreicht durch die Integration der drei SAP-Systeme für Produktion, Lager und Geschäftsebene.
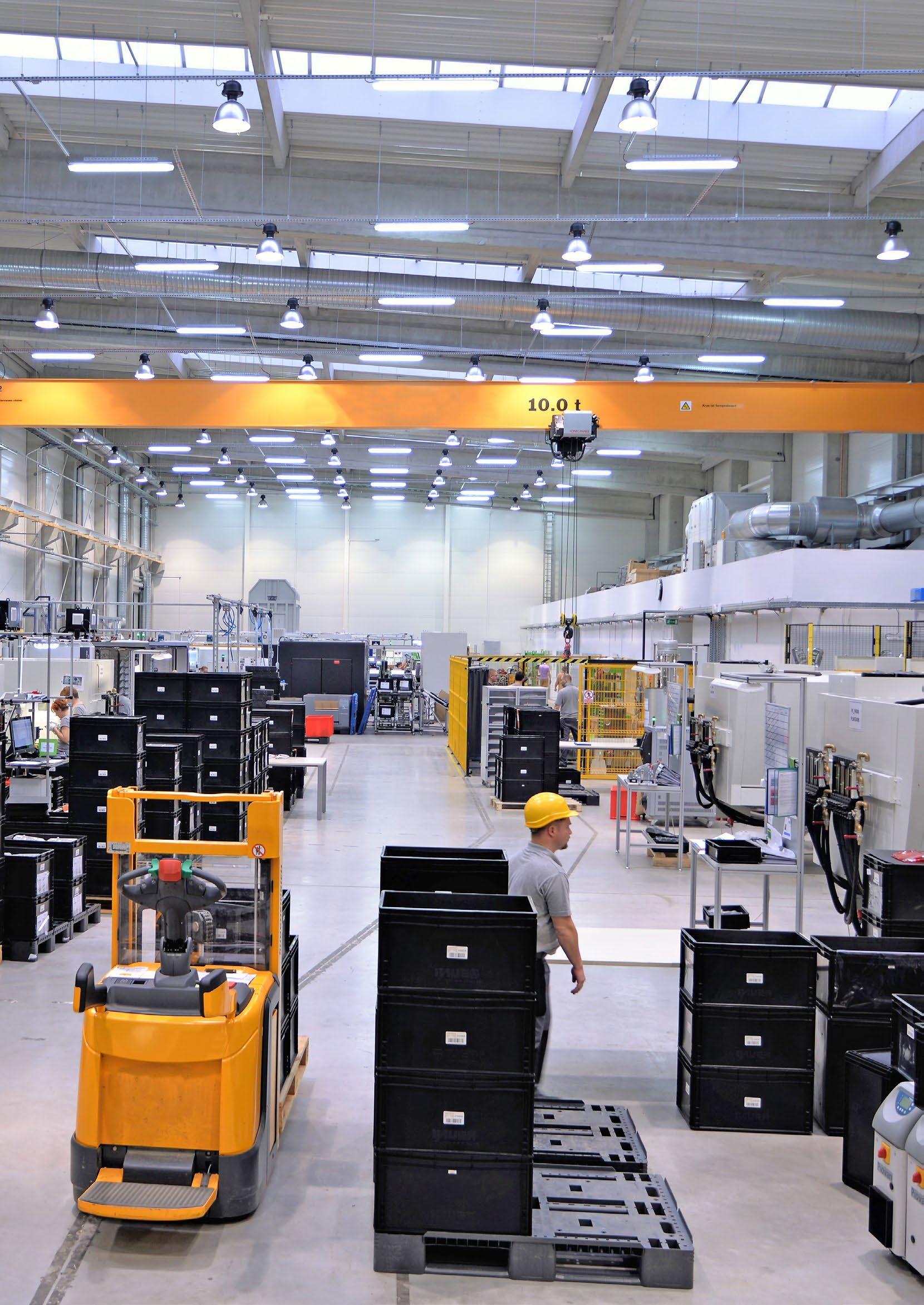