
16 minute read
Literature Review
SUMMER
LITERATURE REVIEW
Aggressive Hydraulics Purpose-Built Catalog
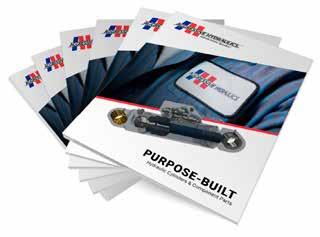
Purpose-Built Catalog Highlights:
• Custom hydraulic cylinder solutions • Unique solutions • Pre-engineered hydraulic cylinders • Expanded component parts offerings • State-of-the-art manufacturing
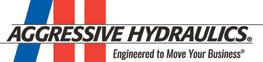
Want more information? We’re here to help. Email: Sales@AggressiveHydraulics.com Phone: 763-792-4000
Product Line Overview
PBVF-100D
HII
Hydraulics International, Inc.
Air Driven Liquid Pumps
Air Driven Gas Boosters
Air Driven Compact Gas Boosters
Air Pressure Amplifiers
PRODUCT LINE
OVERVIEW
Flow Meters
High Pressure Valves
Electric Driven Gas Boosters Package Systems
Hydraulics International, Inc. is a leading manufacturer of air and electric driven gas boosters, air driven liquid pumps, air pressure air amplifiers, high pressure valves, turbine flow meters and packaged systems. Our products offer the most comprehensive range of models to the fluid power industry whether is measured by ultimate pressure, discharge flow rate or fluid compatibility. Request a FREE copy today! DISTRIBUTOR INQUIRIES WELCOME
Hydraulics International, Inc.
818-407-3400 www.hiigroup.com An updated product catalog is available as an interactive pdf version on the Adaconn® + Inserta® website, and is the most up to date resource for new product offerings. Printed catalogs are available by request. New assemblies are planned for 2021, including a check valve flow rectifier manifold assembly. The interactive catalog will be updated throughout the year as this and other new products are introduced.
Adaconn® + Inserta® Blue Bell, Pennsylvania 215.643.1900 215.643.0192 www.adaconn.com www.inserta.com
Hydraulex Repair Services
Our Repair Services Brochure covers the types of components (pumps, motors, final drives, valves, control cards, amplifiers and cylinders) we can repair, why we’re an excellent choice for your repair needs, and also how the repair process works. View or download it by visiting our website at www.hydraulex.com.
Hydraulex
Toll Free: 800.422.4279 Tel: 586.949.4240 Email: sales@hydraulex.com www.hydraulex.com
Compressed Air Filtration
Brochure offers a comprehensive overview of the company’s complete line of compressed air filtration products. Highlighted is the patented family of Extractor/Dryers. These two-stage, point of use filters remove contaminates to a 5-micron rating with flow ranges of 15 to 2,000 scfm. Additional products available include the SuperStar Membrane Dryer, .01 Micron Filter, Refrigerated Extractor/ Dryer, and much more.
La-Man Corporation
800.348.2463 www.laman.com
New 120 page catalog includes popular styles of MAIN Manufacturing’s extensive offering of carbon and stainless Hydraulic Flanges and Components – ready for immediate shipment. Metric ordering information, weld specs, and dimensional information included. The “Quick Reference Guide” helps specify less popular items often stocked or quickly manufactured (generally 3-4 days) at our US plant.
MAIN Manufacturing Products, Inc.
Grand Blanc, MI 800.521.7918; FAX: 810.953.1385 E-mail: info@mainmfg.com www.mainmfg.com/fpj
NEW 2021 Product Catalog
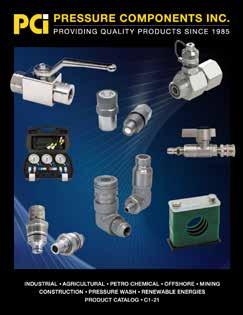
Pressure Components Inc., providing high quality components since 1985, is excited to announce our 2021 catalog with new offerings to run your business. PCI prides itself on exceptional customer service. Let us be your “trusted partner.”
440-349-4020 sales@pressurecomponents.com www.pressurecomponents.com Corrosive resistant properties make stainless steel gages suitable to a variety of applications. Oil-Rite offers 304 and 316 stainless steel liquid level gages in sizes from 3" to 60". A red line on a white background enhances liquid level visibility. Available with adapters and thermometer. Visit Oil-Rite’s online product catalog for new cut sheets and detailed information.
Oil-Rite Corporation
PO Box 1207 Manitwoc WI 54221-1207 Phone: 920.682.6173 Email: sales@oilrite.com www.oilrite.com
Hydraulic Live Swivels Catalog
Inline and 90° hydraulic live swivels. Available in sizes from 1/8" to 2-1/2", rated to 10,000 PSI, heat treated, superior quality alloy steel, chrome or stainless steel ball bearings, withstands heavy side loads, burnished (micro smooth) barrel bores, Viton® , Aflas® , or Teflon® encapsulated seals, zinc or nickel plated, available in 304 and 440 stainless steel, full flow - low pressure drop, rebuilding kits available.
Super Swivels
Phone: 763.784.5531 Fax: 763.784.7423 Website: www.superswivels.com
Make Your Voice Count!
LET US HEAR FROM YOU!
The 2021 salary survey from Fluid Power Journal and the International Fluid Power Society is live now until June 30. The survey provides a glimpse of industry pay levels and other meaningful information about fluid power professionals like you.
We encourage everyone in fluid power to complete the anonymous survey and be counted. It takes less than 10 minutes. We’ll publish the findings in September’s Fluid Power Journal.
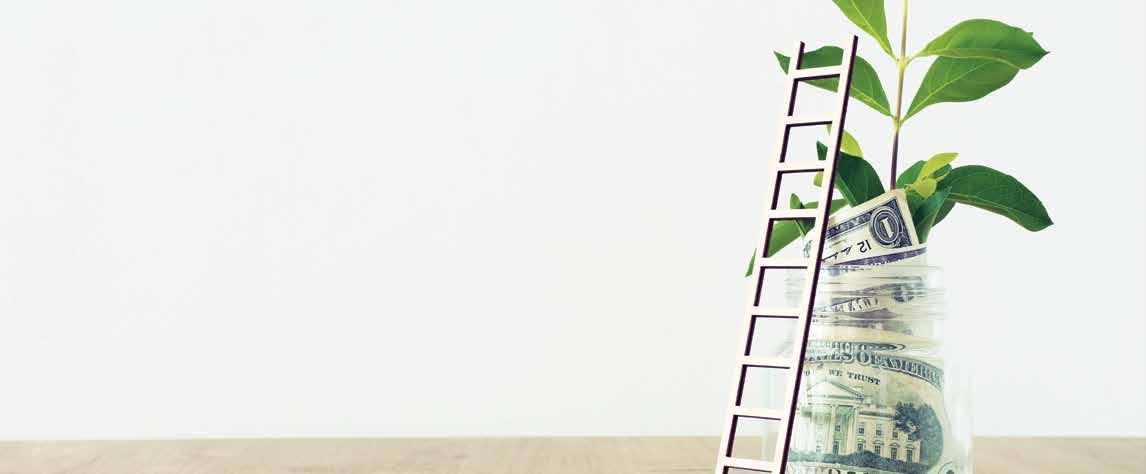
Take the survey by visiting www.fluidpowerjournal.com/2021-survey.
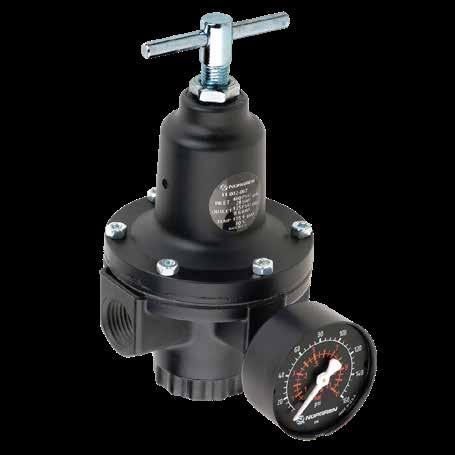
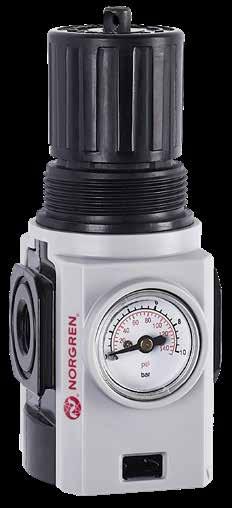
Clean Air Act Battling Contaminants in Pneumatic Components By Mike Parzych, Product Marketing Manager, Norgren Compromising compressed air Compressing atmospheric air converts it into potential energy that can be stored, distributed, and used as a source of power for pneumatic systems, tools, and processes. This compressed air retains nitrogen, oxygen, other gasses, water, hydrocarbon vapor, and solid particulates such as dust or heavy dirt measuring as much as a millimeter. Compressing this mix concentrates solid contaminants and heats the air so that it holds more water vapor. In addition, the oil that lubricates the compressor can enter the air stream as fine mist, aerosol, or vapor. Even air leaving oil-free compressors can pick up oil vapors from atmospheric air and pass them into Actuators, air motors, grippers, and many other pneumatic components in almost all industries use comthe air-distribution system. The now-hot air leaves the compressor, passing through a heat exchanger into an air storage receiver and distribution pipework. As the air pressed air, but performance requirements cools, water and oil vapor condense and turn and design parameters vary widely. In life Regulator. to liquid or emulsions. An efficient condensate sciences, for example, compressed air drives management drainage system can remove these small, lightweight, high-precision respirators. elements. But entrenched solid particulates and Patient-care devices require the same reli- any remaining water and oil vapor travel downability and controllability as rail-car braking stream into the distribution system. The air can systems, automotive assembly, metal stamp- then pick up even more contaminants such as ing, food and beverage dispensing, packaging, rust and debris from old receivers, treatment commercial vehicles, industrial automation, equipment, and pipework. and energy production. Despite the differ- There is a clear connection between the ent scale of each of these applications and presence of moisture, particulate, and oil in the unpredictability of the environmental compressed air and a whole range of disruptions temperatures in which they operate, they all such as less-efficient processes and damaged depend on precision and control. tools and equipment.
Automotive manufacturing, for example, To remove the water and contaminants present employs compressed air for the painting, clean- in compressed air requires intervention just before ing, press-room, and assembly area production or after the compressor but before the air reaches lines, and it’s commonly used to operate robotic Precision the tools and equipment. Operators can apply end effectors. Compressed air is essential to regulator. many point-of-use air-preparation components create auto parts because it lifts, positions, at this point. One is an inlet filter, which prevents and moves fastening machines. But no matter dirty ambient air particles from entering the comthe application, for the system to perform as pressor in the first place. Another component is a required with the longest possible service life, water-removal filter installed between the outlet the air supply must be free of contaminants. and the air receiver; it reduces the moisture in the Oil, for example, can keep paint from adhering stored air. As air in the receiver cools and vapor to surfaces, and it can cause cracking, flaking, condenses, the liquid water and emulsions fall beading, or future corrosion. Unremoved water to the bottom to be drained. After the receiver, a can stick to pipe walls and block the path of the coalescing filter can remove oil aerosols and water compressed air. Solid particles such as rust can carried from the compressor. Another installaclog nozzles and compromise the surface of the tion to consider is a general-purpose filter. When finished product. placed at the main header, it removes water and
In machine shops, where compressed air particles 40 microns and larger. operates grinding machines, air guns, and water The air is compressed, moisture and oil vapors recovery units, if the air contains too much are condensed and drained, water is removed, moisture it can condense on colder surfaces, application requirements, compressed air must and large particles are filtered out. This general causing corrosion in the metal work piece or be clean, dry, and delivered at the appropriate level of air preparation may be enough for many the tooling. pressure. Unless contaminants are filtered out, industrial uses, but tools can extend their life
In short, because of the versatility and vari- they compromise proper operation and shorten and effectiveness with the addition of the right ety of pneumatic systems, regardless of the the life of the equipment. filtration, pressure regulation, and lubrication.
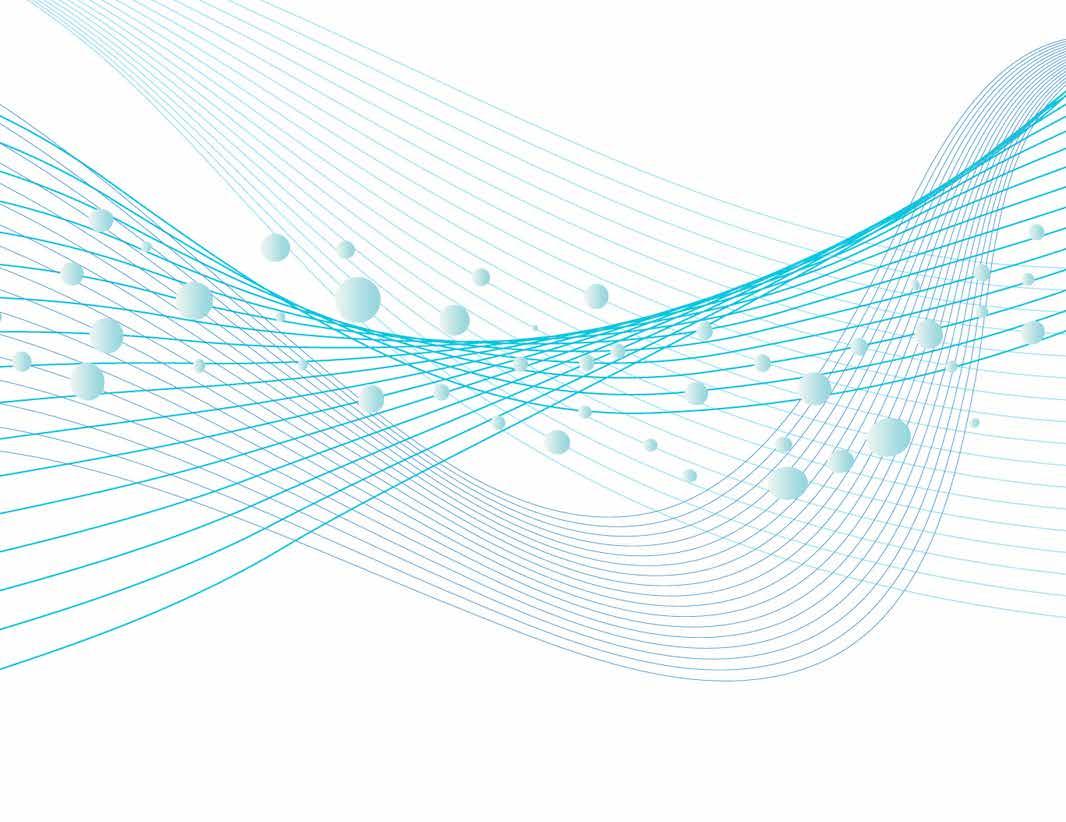
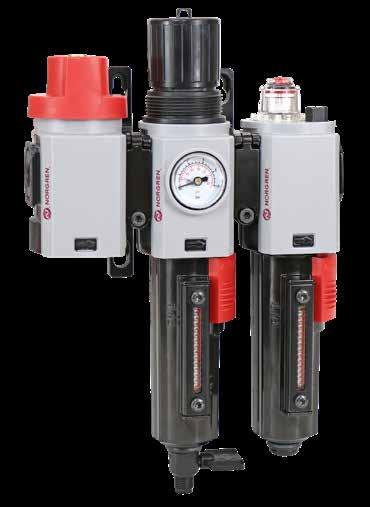
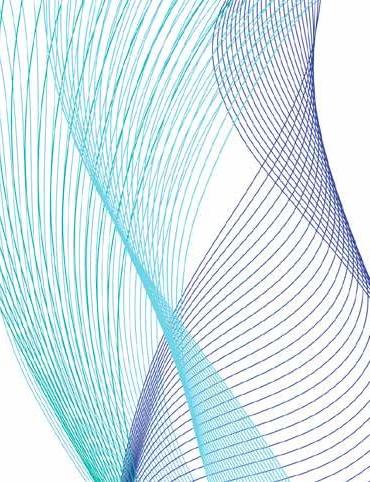
An application with high-speed pneumatic tools or process-control instrumentation requires filtering out particles down to 5 µm. Paint spraying and food-related applications require filtration down to 1 µm or less. But applying such a fine filter to the entire distribution system significantly increases initial equipment costs and maintenance in the form of filter replacement. It also drives up operating costs because a finer filter makes it more difficult for air to pass through, producing a pressure drop. And increasing air pressure to compensate raises the total cost for compressed air.
Generally, it is inadvisable to provide filtration finer than absolutely necessary because fine filter elements trap more dirt and become blocked more quickly. For an effective workaround, employ standard air-line filters as prefilters; this reduces the risk of overtaxing high-efficiency elements with coarse particles.
Oil is another contaminant found in compressed air. Oil can exist in three forms – oil/ water emulsion, aerosol, or oil vapor. While standard air-line filters can remove emulsions, only special coalescing filters can remove small particles between 1 µm and 0.01 µm. These filters are typically rated by the amount of air they can process at a given cleanliness level, normally a maximum remaining oil content of 0.01 ppm in the exit air. Flow that exceeds the rating increases not only pressure drop across the unit but also the remaining oil content. It also increases energy costs. Air-line filters mounted immediately upstream protect coalescing filters from particulate and water contamination.
Oil vapor is typically present in such minute quantities that it can be ignored, except in sensitive applications such as food and beverage processing, pharmaceuticals, and breathing air. Passing the air through an absorbing bed of activated carbon after it flows through standard and coalescing filters removes the oil vapor.
After taking all contaminants into account, consider the degree of cleanliness for each machine or part of a plant. Using the right filter in the right location minimizes energy and maintenance costs. Always determine the volume of air involved in each stage because undersized, inappropriate filters are a prime cause of high energy costs.
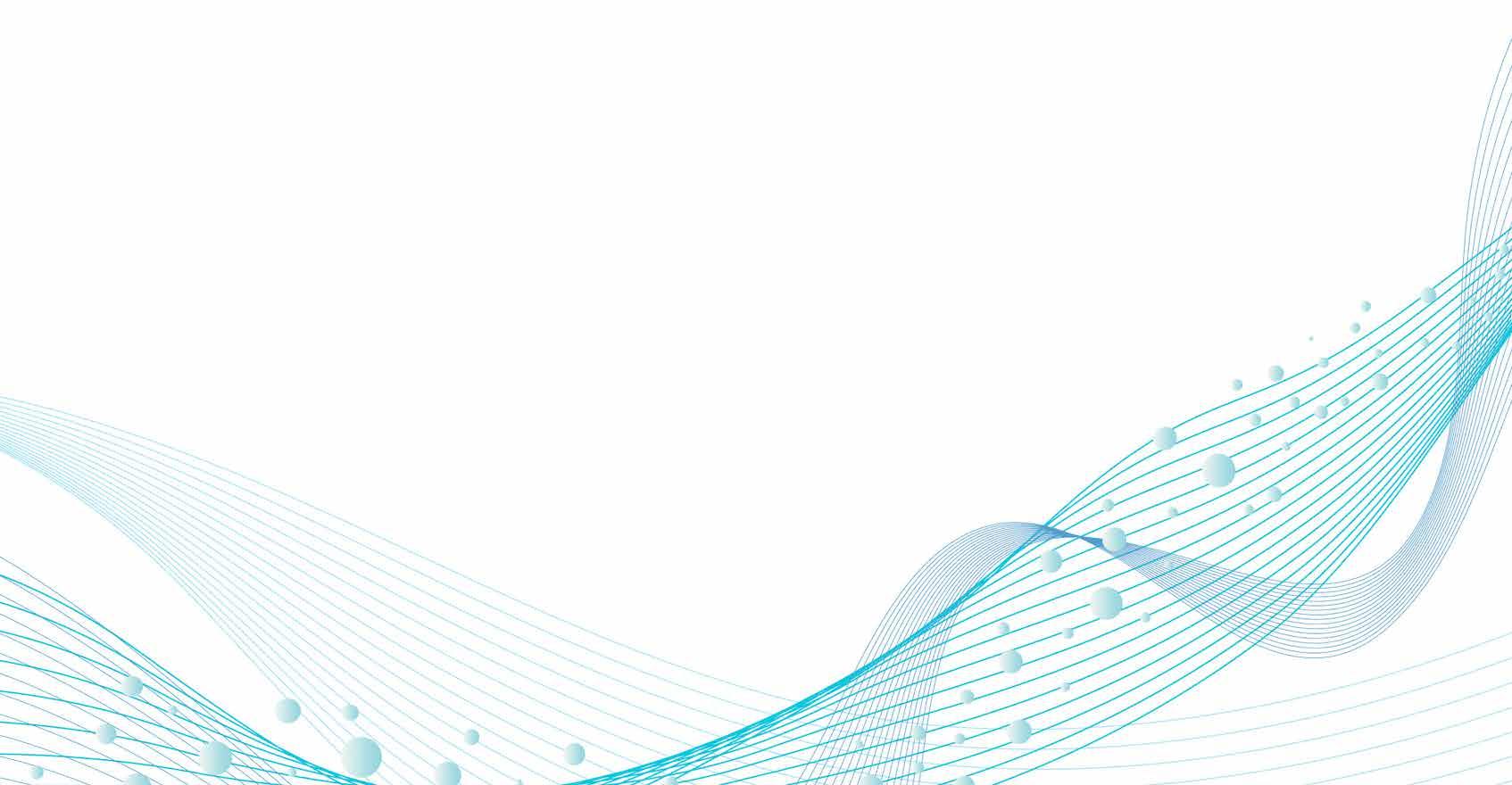
Point-of-use filtration
In selecting point-of-use filtration, the first thing to assess is the end-use equipment itself. What does it require? Find the answer in the operating manual. Manufacturers of tools and machines powered by air specify the appropriate level of filtration, beginning with purity classes of compressed air with respect to particles, water, and oil. After identifying that level, the end user can specify a filter that meets the requirements. But there are important variables to keep in mind. • Even after filtration at the main distribution point, additional contaminants may seep into the air stream via the pipework. • Residual moisture may condense as the air moves through the distribution system. • Harsh operating conditions, such as salt sea air, high humidity, or caustic environments, can compromise air-preparation equipment.
Countering such situations requires components with robust construction and specialized
Filter/regulator/ lubricator with shut off.
sealing materials. Some applications benefit from the addition of multistage filtration: a prefilter, a fine-particle filter, and a coalescing filter to remove oil. Using a prefilter to remove larger particles prevents the finer filter from clogging and prolongs the service life of the finer filter element. Applications benefiting from threestage filtration range from instrument air for precision fluid control to large offshore oil rigs using compressed hydrocarbon gas.
Regulating pressure
All pneumatic equipment has an optimum operating pressure. Exceeding that pressure won’t yield greater productivity; it will, in fact, cause excessive wear while wasting compressed air. To use compressed air most efficiently, reduce the pressure of air leaving the compressor to the precise level the application requires.
Systems tend to operate at two pressure levels: compressed air stored in a receiver at high pressure (which optimizes filter performance and energy efficiency), and air used by actuators and other devices, usually at a pressure 10% to 20% lower. This arrangement ensures the compressor is not constantly running.
Regulators, that is, pressure-reducing valves that control pressure, have two important performance characteristics: regulation, maintaining consistent outlet pressure regardless of inlet pressure, and flow, maintaining consistent outlet pressure regardless of flow rate. The precision of regulation and required flow dictates the type and cost of the regulator.
Most regulators fall into one of four categories: general purpose, pilot operated, precision, and special purpose. Most general-purpose regulators are diaphragm types, though piston versions are used where equipment demands higher flow capacity for a given size. Adjusting manually operated knobs or handles lowers downstream pressure without actuating downstream equipment. To adjust a nonrelieving regulator to deliver lower pressure, cycle downstream equipment or use a 3/2 shutoff valve to expel excess air.
Pilot-operated regulators control outlet pressure by means of an air-pressure signal produced by a precision regulator. This means, for example, it’s possible to mount the regulator in large distribution mains but control it remotely from the shop floor. Engineers usually use this type of control when a continuous process requires a large, steady air flow.
Precision regulators are normally used for instrumentation applications in which fast response, exact repeatability, and control of outlet pressure are necessary. These units have a limited range but superior flow and regulation characteristics. Precision regulators also can relieve up to 90% of their flow for specialized applications, such as tensioning belts, paper rolling, and balancing.
Special-purpose regulators can be based on any of the other types with application-specific modification. For example, they may be constructed of special materials like stainless steel, have high relief flows, or operate with a plunger instead of a hand wheel.
Combination filter/regulators clean air and control pressure in a compact unit, saving space and costs. Specialized filter/regulators remove fine particles of oil, offering precise regulation.
Lubricants
To ensure that operating equipment performs efficiently without excessive resistance to wear, we need to introduce a lubricant, usually oil. (Continued on page 54)
(Continued from page 53) Aerosol oil-fog lubricators use reservoirs or bowls filled with oil, which, when generated, have relatively large oil particles that cannot rise or travel far before dropping out of the air stream. Therefore install oil-fog lubricators near the equipment they are meant to service but never below it.
There are also microfog lubricators, which atomize the oil in the bowl, creating particles less than 2 µm in size. This fog can travel upward and for long distances through complex feed lines. Microfog units can also ensure proportionate distribution through numerous lubrication outlets, making it ideal for multiple valve-control circuits. Only about 10% of the oil in a microfog system becomes an aerosol, so it works well in applications requiring only small amounts of lubricant. By adjusting the drip rate, oil delivery can be raised to approach that of an oil-fog lubricator.
One other type of lubricator is a positive-displacement injection pump. It does not continuously deliver lubricant like aerosol lubricators but instead injects the same amount of lubricant every cycle. This type is often used on conveyor chains where several injectors can be joined together on a manifold to treat different points at the same frequency.
Most valves and cylinders powered by pneumatics are prelubricated and in most applications do not require additional lubrication during their service life. Once they reach the end of their lubrication life, nonrepairable cylinders must be replaced. Other components can be repaired, but technicians must apply new grease before they are put back into service. In addition, contaminated air gradually compromises the original grease lubricant and shortens the seal life.
Lubricated air prolongs the life and performance of prelubricated components. Applications that have high cycles, operate at high speeds, or use large diameter bearings can generate heat that speeds up the deterioration of internal lubrication. Lubricated air is also essential for equipment that is not prelubricated, for example, pneumatic hand tools such as screwdrivers.
Lubricated air extends cylinder life, but it also washes out the original lubrication. So once lubricated air is introduced, it must always be used. The amount of oil for sufficient lubrication varies with each pneumatic device, so it is important to follow equipment manufacturers’ recommendations. From regular inspections and servicing, technicians can determine the optimum setting and adjust the amount delivered.
Compressed air is powerful, so it is important to have safety features built-in to the pneumatic system to protect equipment and personnel.
The first safety consideration is overpressure protection. Components in pneumatic systems often have a pressure rating lower than what is generated by the compressor. If for some reason the regulators do not maintain safe working pressure (SWP), downstream components exposed to excess pressure can malfunction or fail.
The most common overpressure protection is a relief valve. This device holds system pressure at a constant level at or below the stated SWP. Relief
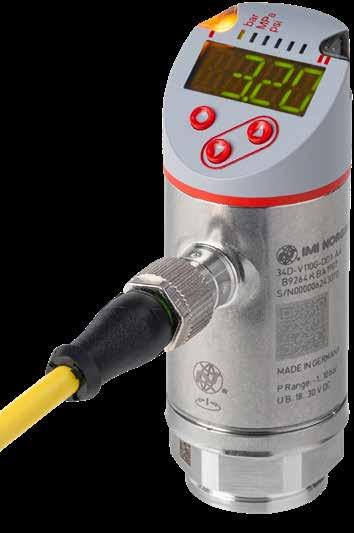
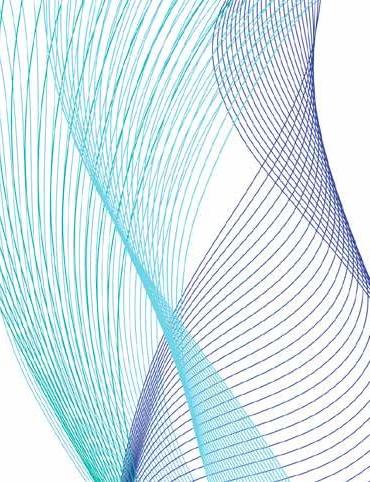
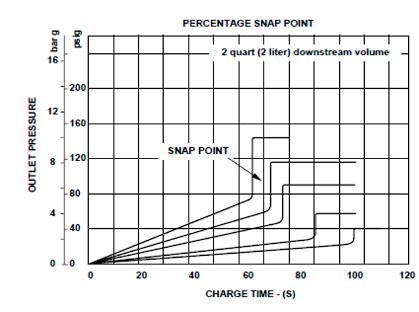
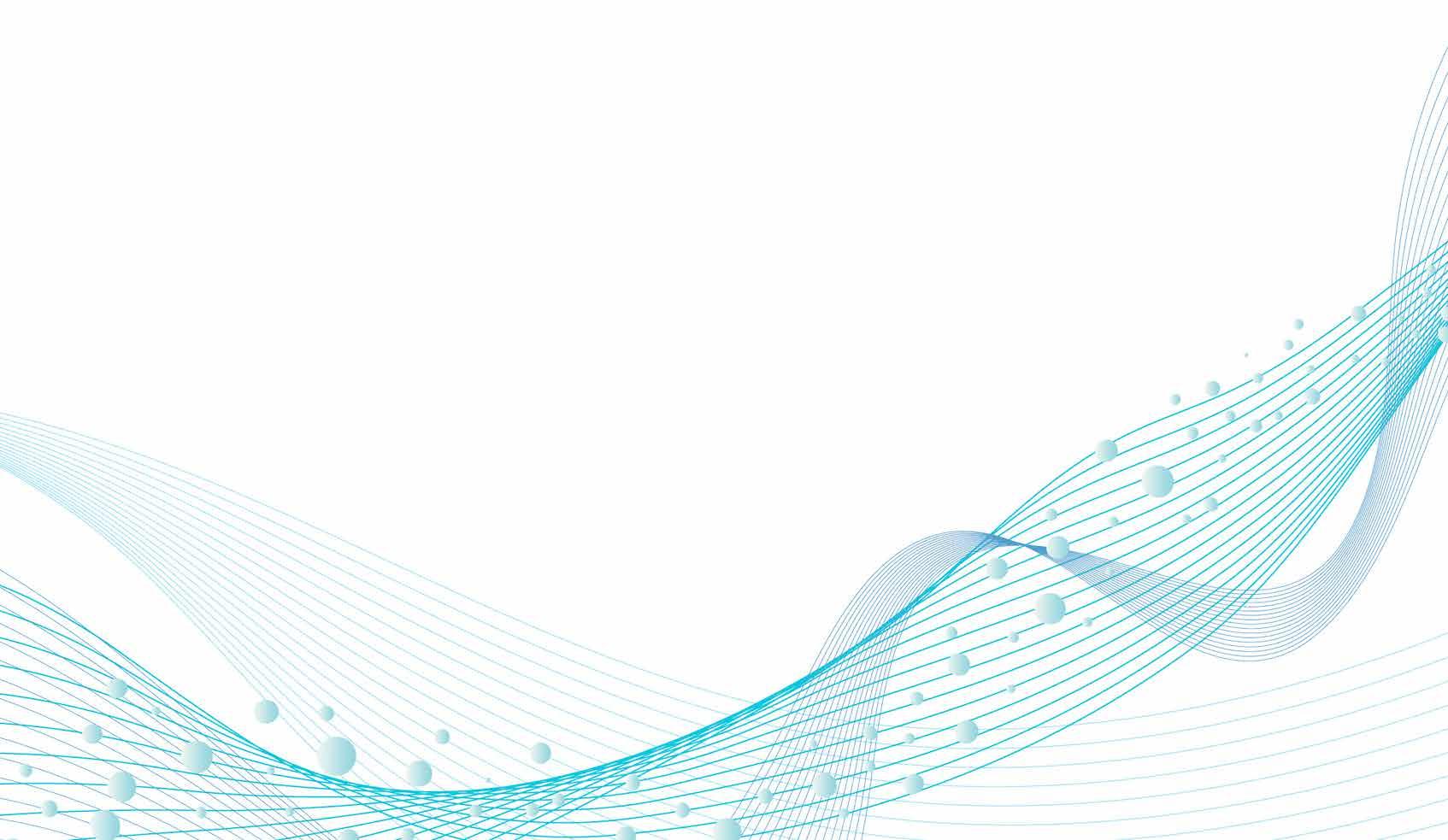
Pressure sensor.
valves should operate only when the system exceeds regulated pressure, so they need to be set to a pressure higher than that for the regulator. Frequently, relief valves are situated too close to the system operating pressure, causing the relief valve to vent air during normal operation.
The relief device must also be sized to match or exceed flow through the parts of the systems it protects, without system pressure rising above the acceptable overpressure level.
Finally, consider start-up. Loading during start-up can cause unnecessary wear on moving parts, and sudden movement can injure personnel. Soft-start valves prevent such problems. They let air gradually bypass from a compressor to the pneumatic system. Adjusting the valve controls the rate of pressure buildup. The valves usually have a spring-operated internal poppet design, set to open, or “snap,” when pressure reaches between 40% and 70% of full-line pressure. It is more economical to set these devices near the equipment they are intended to protect rather than fit a larger valve to the whole distribution system.
We’ve mentioned many of the challenges to proper air preparation presented by such variables as harsh environments. Numerous industrial processes require extremely high pressures, and these must be carefully monitored. When faced with such conditions be aware of the various kinds of sensors capable of detecting pressure and switches that can open or close a connection based on the pressure level. Options include simple but effective electromechanical pressure switches, electronic pressure switches with few moving parts and offline programming, and pressure transducers or transmitters that convert pressure into an analog electrical signal.
A recent study from Research and Markets estimates that the smart pneumatics market will grow by nearly 7% between now and 2026. This growth depends on equipment effectiveness, which is itself determined by IIoT factors. Predictive maintenance will save up to 12% over scheduled repairs, reducing overall maintenance costs up to 30% and eliminating breakdowns up to 70%. For fluid power systems, says the report, this “means a whole new level of condition and remote monitoring.” In short, compressed air generation, properly installed and maintained, can deliver years of trouble-reduced operations.