HA11_S
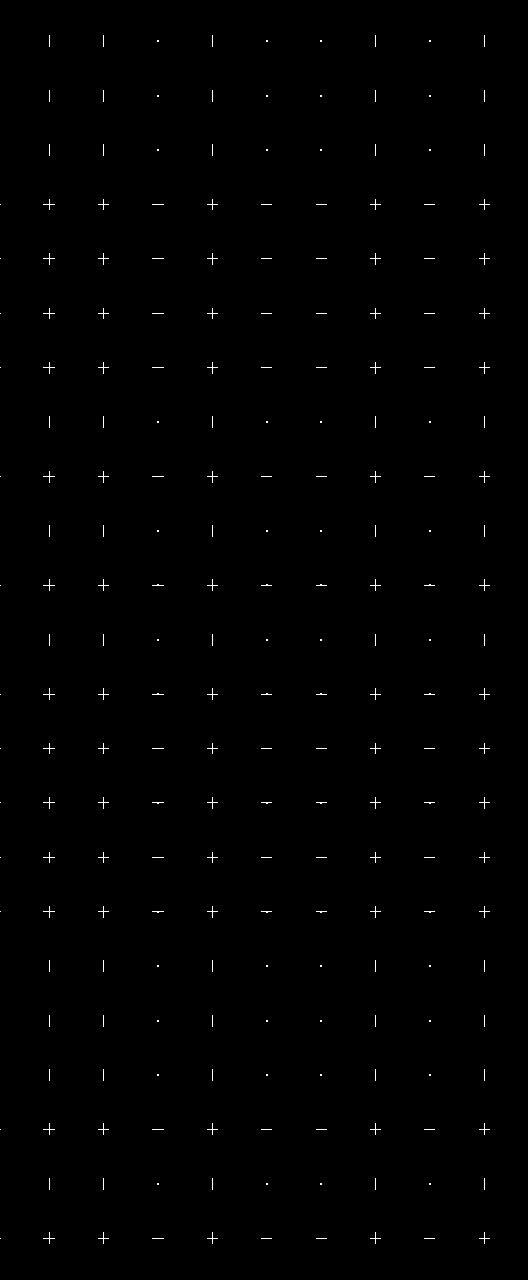
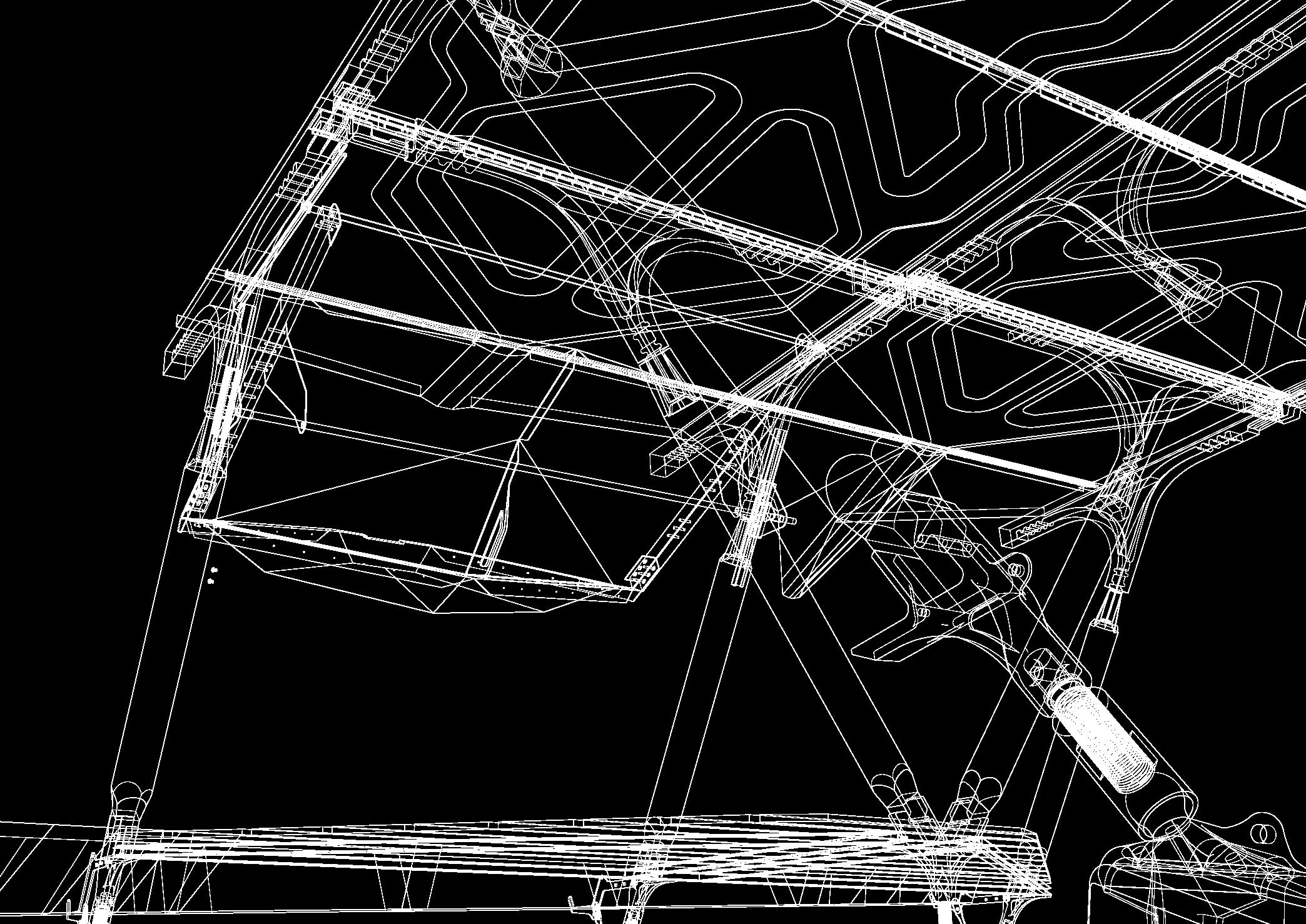

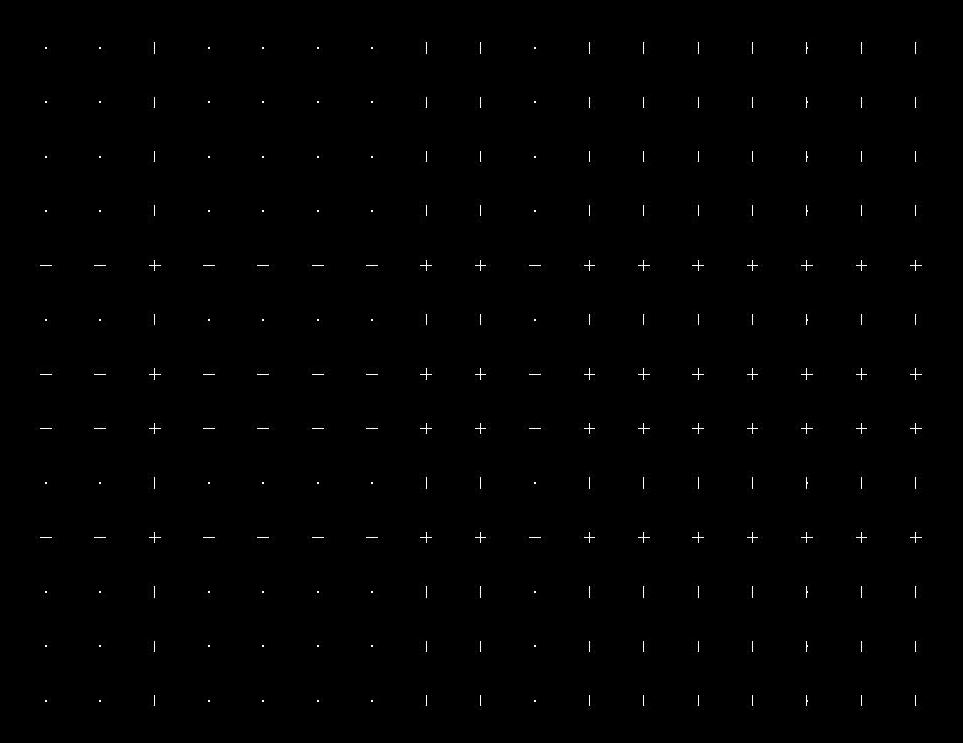
HA11_S is a timber seasoning shelter located in the woodland habitats within Flimwell Park. The design of the shelter emerges from a need for the park’s foresters, and other users, to store felled logs whilst they cure and season, as their internal moisture is lost. This is whilst performing a dual function that enables its users and park visitors to unwind amidst the woodland landscape.
With multiple entry points to the structure, the project is a 5m x 4.5m timber frame assembly, supported by aluminium connections, on top of which is a steel roof system designed to guide the water to the surrounding pools and streams. The structure choreographs the interrelationship with water whilst furnishing the woodland with the infrastructure to facilitate timber production, by protecting wood from rainfall.
Hybrid Assembly11 by Studio1 of DfM features 11 components that seek to unite the indeterminate nature of timber construction with the rigid but malleable properties of aluminium components. Inserted into the choreographed processes of timber production, the apparatus we constructed is a meditation on the act of making with timber.
The project adopts advanced fabrication technologies to produce individual components within HA11_S. An organic form, round timber upright supports a cold bent timber substructure through a CNC-machined joint. Connections between this timber skeleton, the roofing and footings, were cast with aluminium and finished using CNC for more accurate and stable fastenings. The roof and kinetic panel direct waterflow downwards with the help of channels incrementally formed through robotics.
Strategically nested on an edge condition between storage of timber, the repository and shelter, where the woodland meets the Flimwell laboratory, an explorative relationship is formed through the connective tissue between forest and function, shelter and rain, human and nature.
The sustainability of HA11_S, Timber – Seasoning Shelter is based on materials and contemporary processes for the manufacturing of the components.
The structure mainly consists of aluminum and timber products, creating a hybridization between those two materials, completing the needs of each one, working as one shape.
The timber components of the structure in the skeleton, were sourced by timber locally. Minimizing the transportation needs of the raw materials, represents a tremendous opportunity to help the environment and contributes to green manufacture. The reduction of shipping and storage needs, leads to decreased emissions and energy usage.
Another intention was to minimize the unnecessary processing of the materials, trying to reduce the energy consumption, both in testing and making. In that case, timber logs were used in the structure, machined only in the ends, and used in the main skeleton of the structure. A step with a research ambition to create a machining process in pure, unshaped materials by using less energy in multiple aspects.
The aluminum components were investigated in the casting procedure, in complex shapes for the down part of the structure, the feet. The effort was to investigate methods of accurate casting and on a second step to machine the joints of the cast components with precision.
Through the whole components processing, the intention was to avoid material waste. So, through making jig solutions, unneeded materials were used both in testing and final making procedure of the components, aiming to consume less and re-use.
Finally, another research intention throughout the whole project was to create accurate components that would be assembly on site. The reason for that was to reduce the transportation cost, that would have a ready structure or the need for machines on site, in case of less precise components. So, by analyzing the structure’s and site’s needs, each component was manufactured and designed so to fit perfectly with each connected component, creating a method of assembling on site.
The key characteristic of this project is to elevate and showcase the flow of water across the site. Our ambition is to seamlessly direct rain water from the roof to the ground with the aid speciality designed components. The roof, kinetic panel and the gutter play an important part to receive, direct and collect water. Utlising key manufacturing techniques such as robotic milling, metal bending and kinetic mechanics, these components deliver a unique aesthetic to the project through metallic composition.
We explored different methods of bending timber, including steam bending and glue lamination. Also experimented with different wood species including ash, douglas fir, and beech. During the experiment, we discovered that an important feature of bent timber is spring-back.This project emphasises the possibilities of catalysing the spring-back of bent timber, taking advantage of the known behaviour to strengthen the designed timber joint.
Offers freedom in fabricating complex joineries geometry with minimum material waste. For a small quantities production, aluminium sand casting can be more economical. Moreover, due to its ease of machining properties, a tight tolerance can be achieved by an essential post-process of milling (CNC/Manual)
To focus on physical changes of the material. Due to the excellent Ductility and Plasticity of steel, the shape of the metal raw material is changed by tapping or squeezing during processing using local compression force to obtain forgings. Ultimately, using ISF is becomes an achievable solution to carry the water channel.
The upright components were CNC milled using a jig capable of holding organic log forms of varying size and shape. There were multiple flips required in the process and two styles of joint.
The project required various environmental factors to accommodate specific functions of the design.
The site was chosen with regards to these factors that suit the design specificity as well as accommodate the project efficiently.
Relatively even ground, minimised time to un-earth and level.
Located toward the bottom of the Flimwell site, the large surface area was prone to minimum tree cover which resulted in large amounts of sunlight and maximum exposure to rain water
Unchallenging installation of timber piles to reach sufficient depth for maximum stability for our foundations.
Multiple tools were necessary to predict and accurately model each individual joint, due to the organic and irregular forms of the round timber.
Each step of the design workflow informed the following stage of the process. Having an understanding of the material at hand was key to securing a suitable jig within the CNC milling machine.
The jig had to be adaptable to cope with the variety in shape and diameter of the individual logs. Diameter variations went from 90mm to 130mm. This was important to keep in consideration when iterating the joints to a final version that was capable of withstanding these size deviations.
LIDAR Scanned Log Fusion Modelled Upright Creaform Scanned Prototype Rhino Modelled UprightsType B
Type A Type C
calibration point calibration point calibration point
The chosen site is rich in clay which might cause foundation of a light structure to shift overtime. To keep the shelter’s base relatively stable, a combination of timber pile and precast concrete pedestal is used.
Timber pile system offers an ease of construction that minimize the need of ground excavation to reach the bedrock layer. It also has advantages over commercially available screw piles in terms of surface friction ability. Meanwhile, the precast concrete pedestal provides extra weight on to the piles (45kg each) to reduce the risk of soil movement. Moreover, the concrete pedestal and aluminium footpad keeps the ground moisture away from the timber upright component.
Absolute dimensional accuracy in construction is nearly impossible to achieve. For this reason, three kind of forgiving details are applied on each set of the footing component; slotted hole, ball joint, and threaded joint.
The concrete pedestal is a mixture of 1 part cement, 2 part sharp sand, and 4 part of 20mm agregate. A tensile reinforcement was made at the bottom part of it using cross flanges (welded to the base plate) of 6mm steel plate that is inserted during the cast proccess. The threaded rod was anchored using chemfix resin.
The footpad component was made from symetrical two part mould that has 1° of draft angle on the bottom surface. A small draft angle combined with rubber cushion is needed to ensure a good fit between footpad and concrete component. The fabrication proccess started from 3D print the pattern, making the sand mould, pouring the alloy, clean-up, and manual milling.
GROUND
In order to respond to the need to be repeatedly produced, sand casting is adopted in this case as the best suitable method for its character for saving materials and is more environmentally friendly than the material removal method. However, the surface of the finished product using sand casting is relatively rough. For the accuracy of the interface, secondary processing(CNC) is required to provide more accurate dimensions.
CNC Setup1
Machining time: 19 min 53 sec [T1]2D Contour, EM20 [T2]2D Contour, EM12
CNC Setup2
origin CNC Setup1
The fingerprint produced by the robot arm is very regular compared to the traditional processing methods. Moreover, controlling stepover(the space between tool passes during the operation) parameters and taking the rebound rate of metal moulding (the stress response rate of the structural stress produced by the metal properties) into account can effectively save the time for adjusting the curvature repeatedly. Furthermore, control the thickness accurately not to damage the material by stretching back and forth; the two are pronounced differences between Automation and Artificial equipment.
High Land Lake
Valley
A collection point and reservoir for the water.
Adjustable to allow efficient capture of water.
Robotically milled and bent to hold the water.
Pully mechanism for adjusting level and height of the panel.
Integrated pattern design to allow efficient flow of rain water. The pattern will enhance structural strength of the panels in order to withstand wind and other external factors.
Steel was utlised for this component due to its flexibility and high strength to weight ratio. The material can be formed by high pressure and therefore the pattern can be implemented.
Highest-Level 5 ° Slope Drain
There are three tracks and two shunt designs on the overlap connection position to reduce rainwater slip flow rate and cover a more comprehensive range of catchment areas. Regarding modification of the edging, in the previous failed experience, the robot accidentally hit the edge when moving by the pillow effect of the bulge area. Afterwards, the edging toolpath offset 10mm inward, allowing the tool to continuously apply pressure on the sheet.
This section presents the design and fabrication of a passive-dynamic system, conceived take advantage of harvested rainwater, converting potential energy into kinetic energy. Within the larger architectural context of the HA11_S: Timber seasoning + Shelter project in Flimwell park, this system will provide the structure with a dynamic adaptive apparatus, designed to protect the wood stacked in the shelter from rain and allow an optimal ventilation in absence of precipitation. The intention is to investigate how kinetic systems can promote a better use of natural resources in buildings, adapting their configuration to different scenarios. Furthermore the research aims to exploit the performative aspect of water through a physical and visual engagement with the user. Rainwater, in fact, plays a key role in shaping natural landscapes such as Flimwell Park and this research project aims to enhance the relationship between water and the site.
Painted and treated to ensure minimal damage to the material as well as provide an aesthetic form of colour to the project.
Joined together through riveting for maximum strength and water tight fittings.
The gutter is the longest component implemented within the structure. The primary purpose of the gutter is to collect and navigate water to the nearest allocated pond.
Despite having such an important purpose, the gutter is a unique addition to the design to bring forward a combination of post-modern aesthetic with metallic fabrication.
Material : 3mm Steel
Made from 6 Steel sheet components
The end point has been specifically designed in order to feed the water into the pond.
The gutter was fabricated via metal bending, precision cutting and rivet fitting.
The sharp edges were bent to an angle of 150 degrees in order to ensure safety for the user.
The gutter was brought to the site in two parts. The component was joined on site via rivets and placed on designated supports connected to the feet joint.
Assembly was the most special part of this project.Having not been to the site before, it was a challenge to assemble the all the pre-fabricated components to match their designated function. Nevertheless, with the use of our structured assembly process and accurately machined components; the build was relatively fast and efficient .
Components were fabricated at B Made Here East and brought to Flimwell Park for assembly. This form of modular, dry construction allowed efficient time management during construction.
The adjustable tolerances within the components aided the security and precision assembly of the structure in the harsh conditions.
The structure was designed in a way to cope with the issues facing a construction of multiple components containing varying levels of tolerance and assembly alignment. This flexibility meant that readjustments when assembling could be easily worked with.
During the process, challenges and inaccuracies included the plate height underneath the concrete pads and the dimensions of roof panels due to deformation during the fabrication. These differences to the digital model were overcome with the use of a threaded connection to the feet, and a finger joint to the upright components.
This project gave us an important mission. To be able to understand the process of manufacture and implement within a design that can be fabricated at a specific location. Our ambition was to explore the world of hybridisation, to understand properties through creative collaboration between timber and aluminium. However, we as a team, feel that we have delivered a project that investigates more than just these two materials via a plethora of manufacturing processes that showcases pioneering capabilities of multiple material compositions.
As a team we are proud to have been able to explore, design, investigate and construct a project that represents various methods of manufacturing techniques. Through problem solving, team building and thorough material testing, our investigations have helped us improve our knowledge between the timber and metallic world considerably. A project that demonstrates specific design manufacturing methods via purpose, specific functionality and aesthetic design.