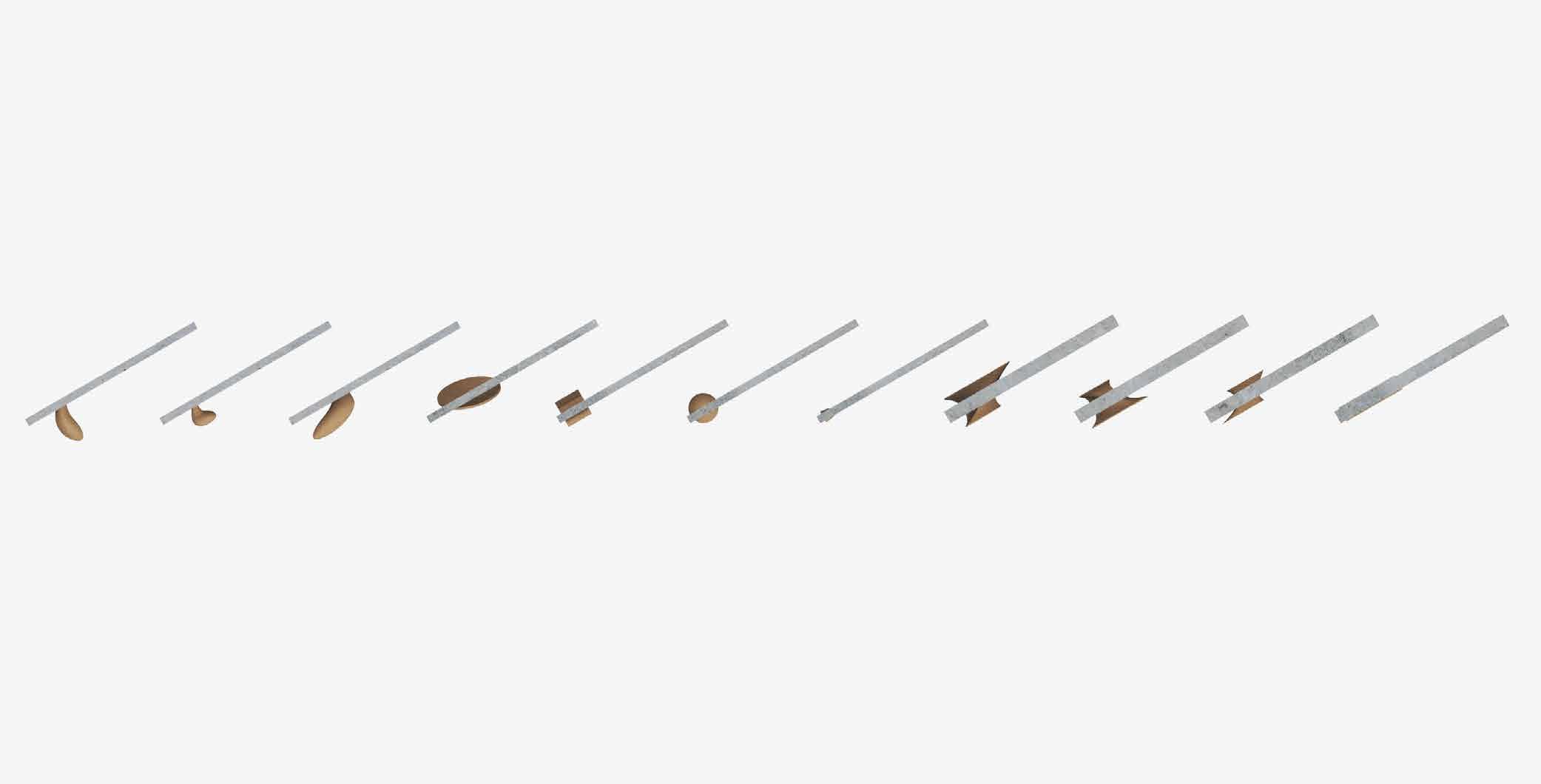
1 minute read
FABRICATION CUSTOMIZATION: PROTOTYPING
The design process for Project 1 began by considering the handle and its door as a handshake between the architecture and the individual. Gradually, the interpretation of the handle began to mirror that of the door as a threshold condition meant to be processed, intertwined with, and broken by the individual. The handle is no longer simply an operable side element, but now a component of the architecture.
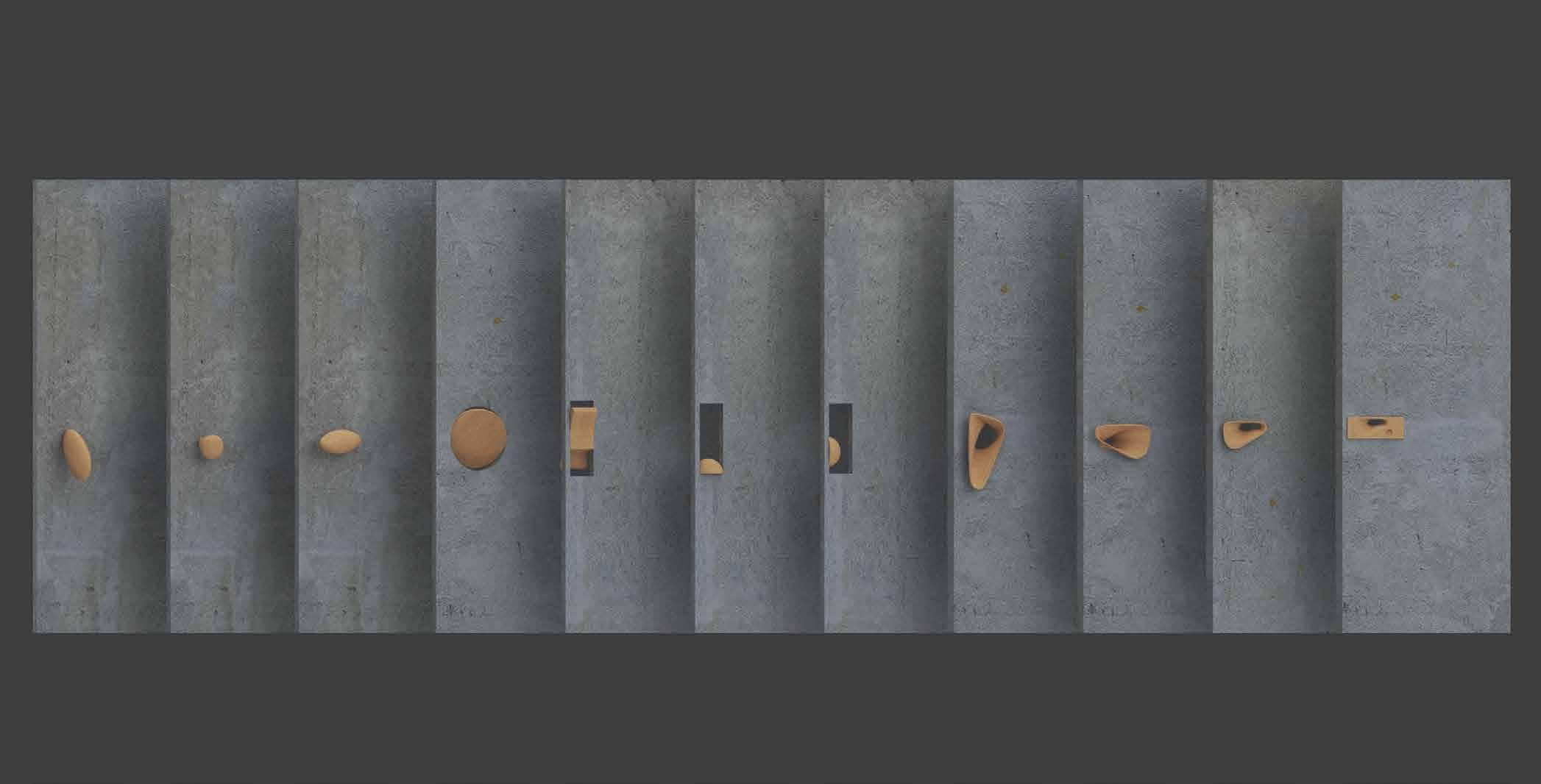
Advertisement
Such an interpretation presents the handle, then, as a moment of pause and a change in pace. It is a palette cleanser and a moment of limbo in order to provide contrast for the beginning of an experience. The juxtaposition of elegant organic wooden form layered upon the heft and tectonics of a concrete door are meant to both intensify this experience as well as speak to the fabrication of these objects.
Design Iteration
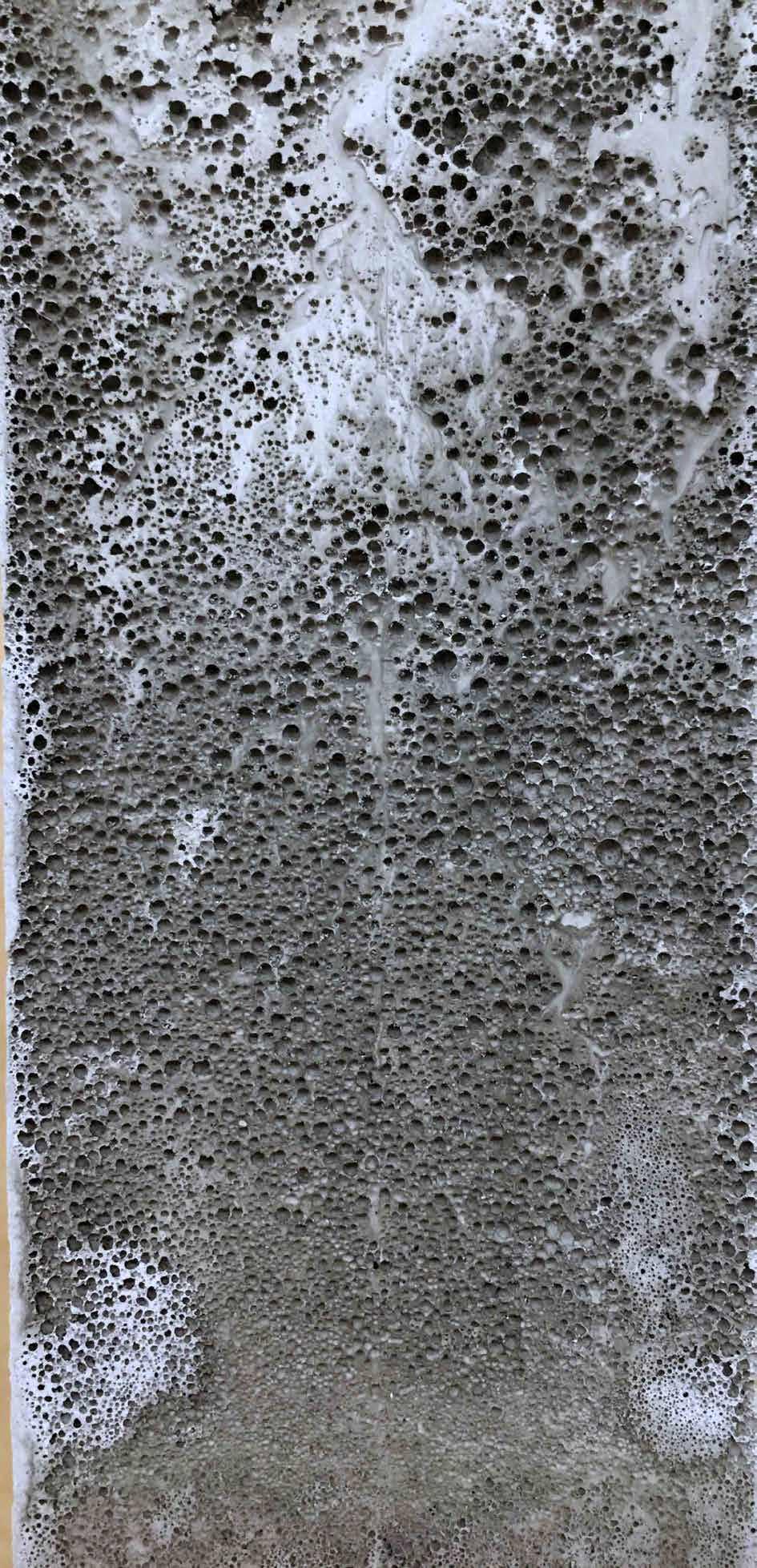
The handle becomes a pair of ears through the door, providing a tone of grey between the black and white of inside and out. The individual which percieves the architecture may now, in turn, be heard by it. The experience may present itself as something greater than man and object.
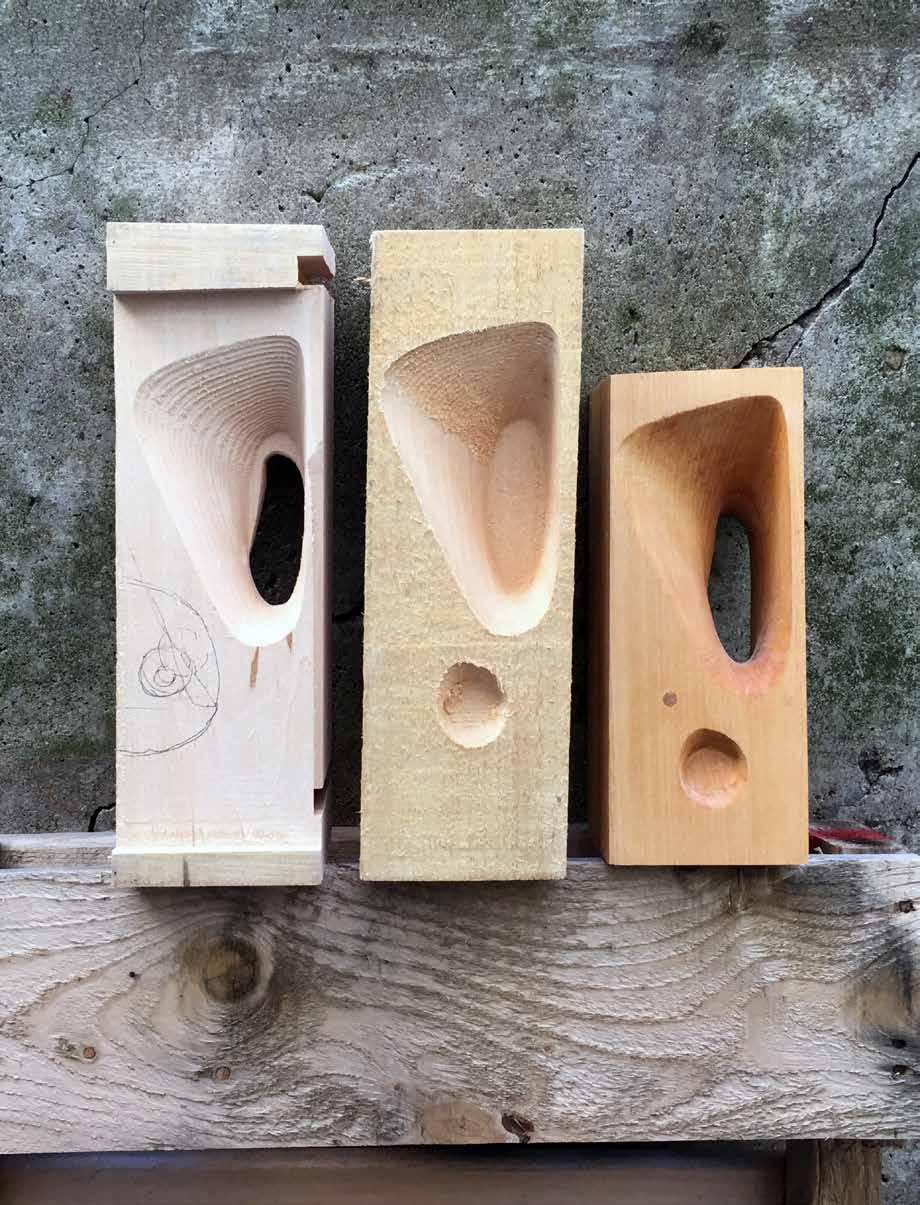
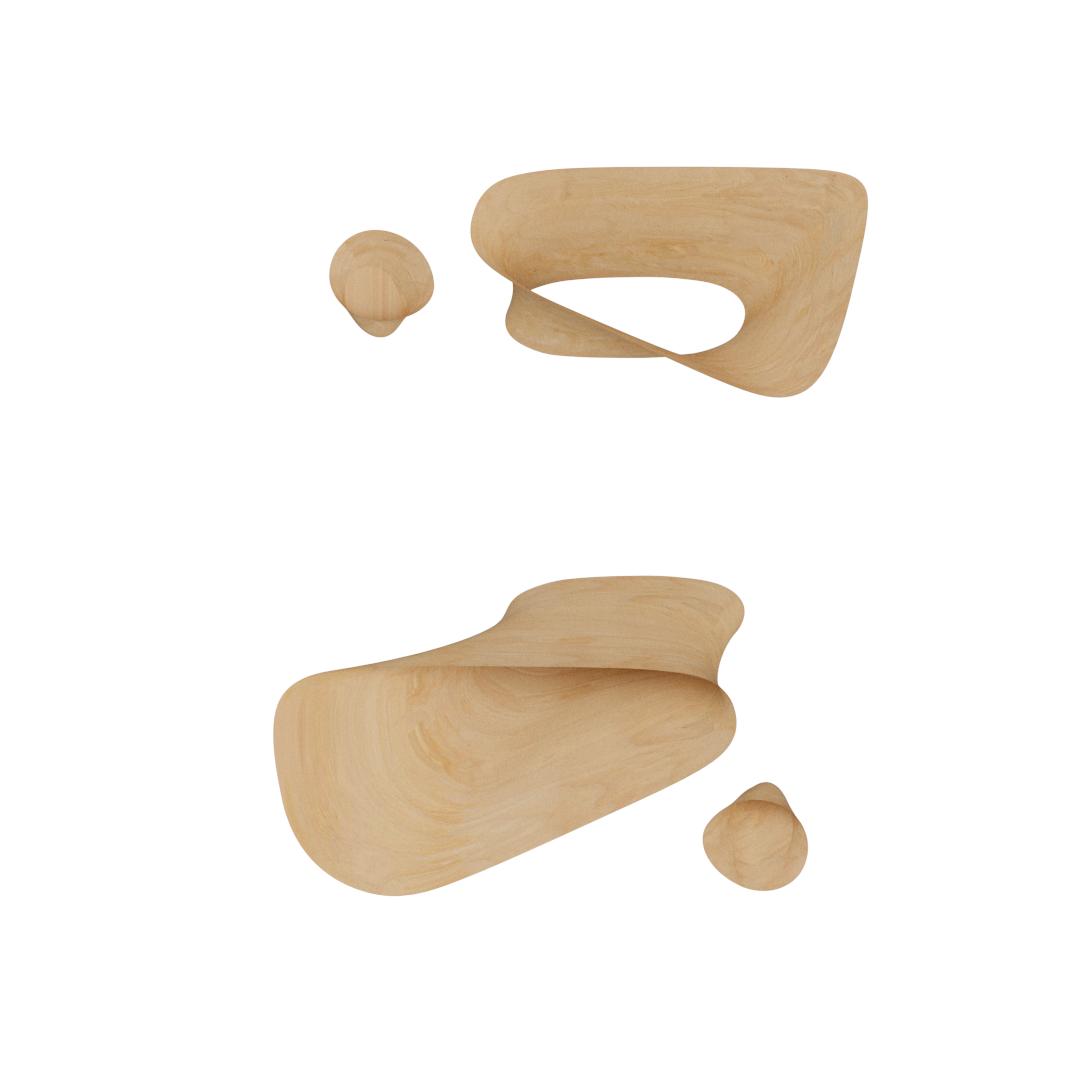
“... silhouette explains plasticity: it is the outline of things which explains their volume ... pictures represent objects seen from in front, but their depth is implied in the lines.”
- Bernhard Hoesli (Oppositions, Apres le Purisme)
Methodology
Fabrication was done through four axis milling and was our shop’s first time experimenting with this process. After many failed posts, machining collisions, and broken end mills, we eventually mastered the process. Due to the depth of the handle, it was determined that the stock had to be split and machined in two seperate parts, then pinned back together. This roundabout subsequently provided options for potential mounting methods and an opportunity to compose the pins as a part of the handle face.
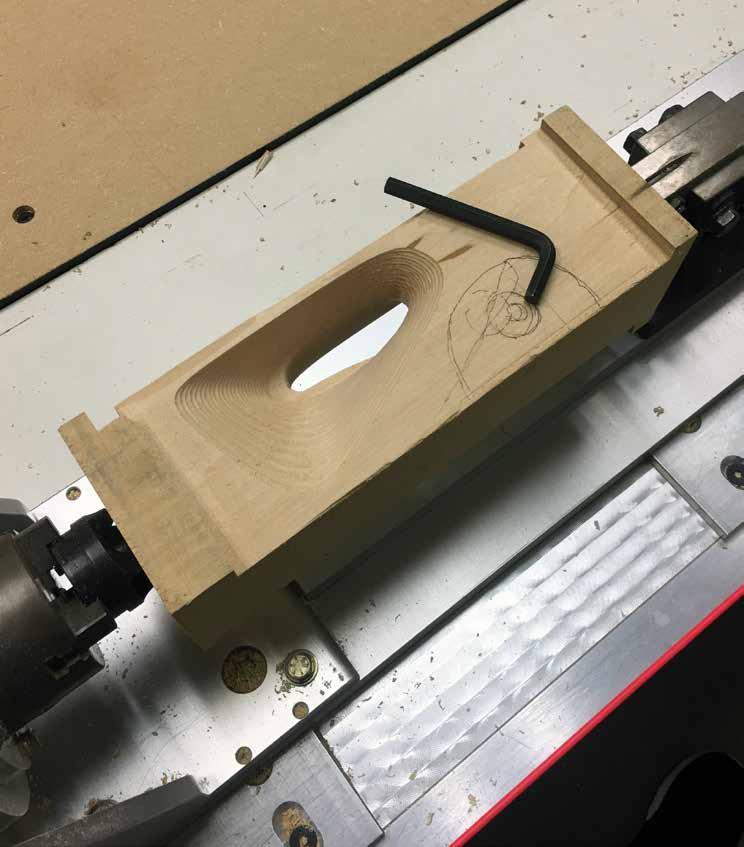
Fabrication
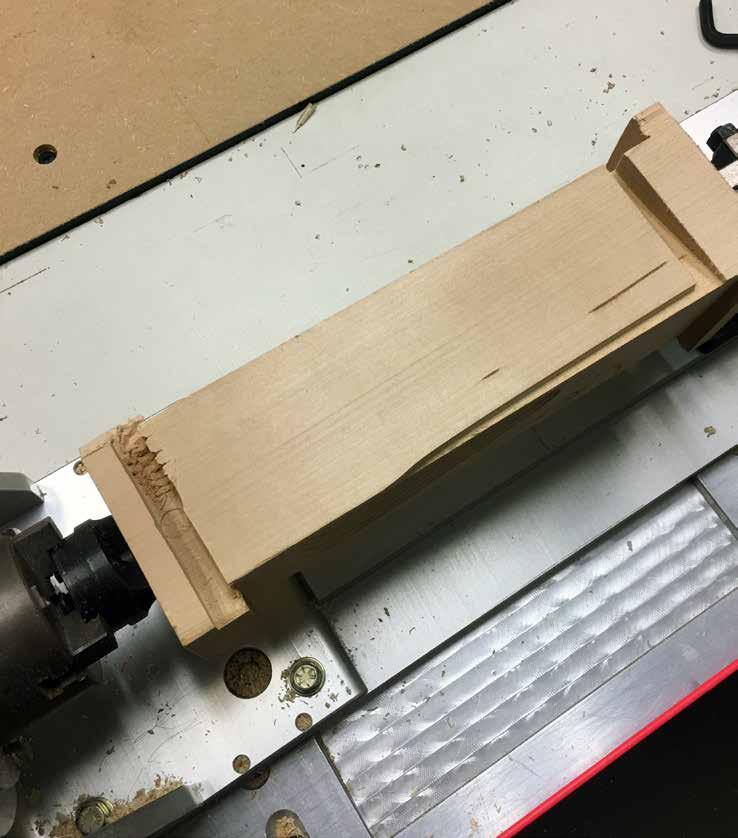
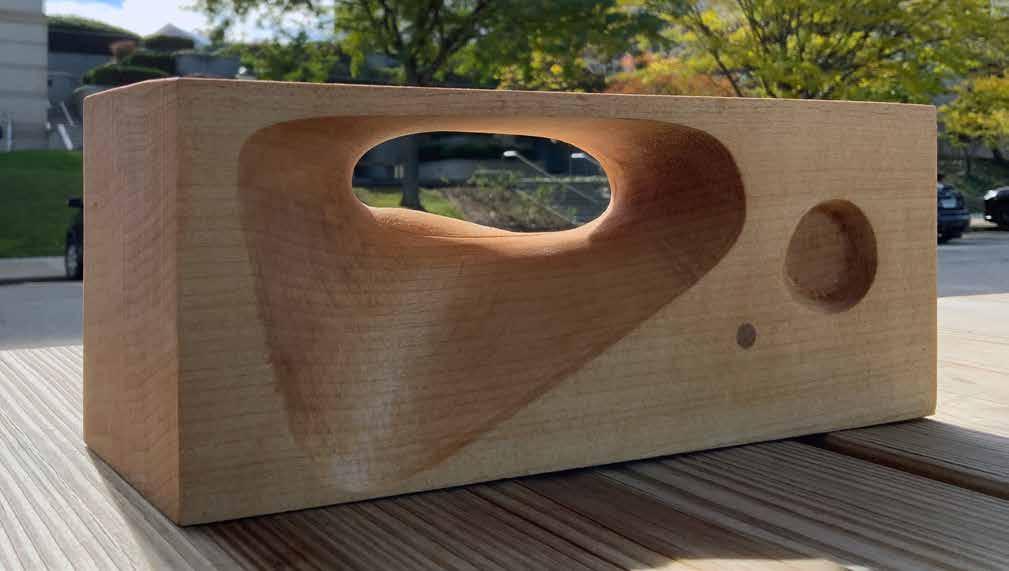
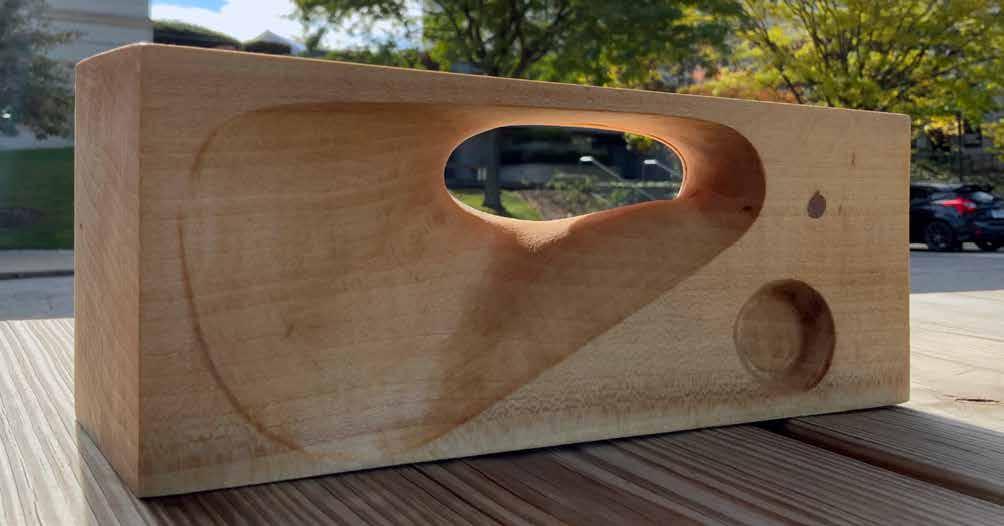
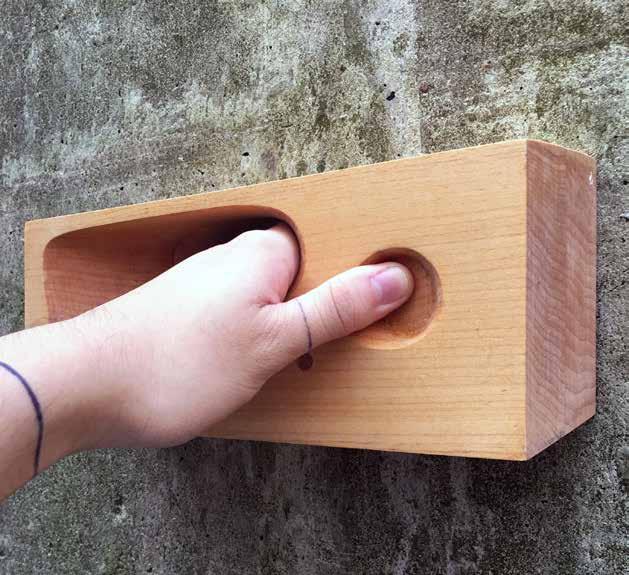
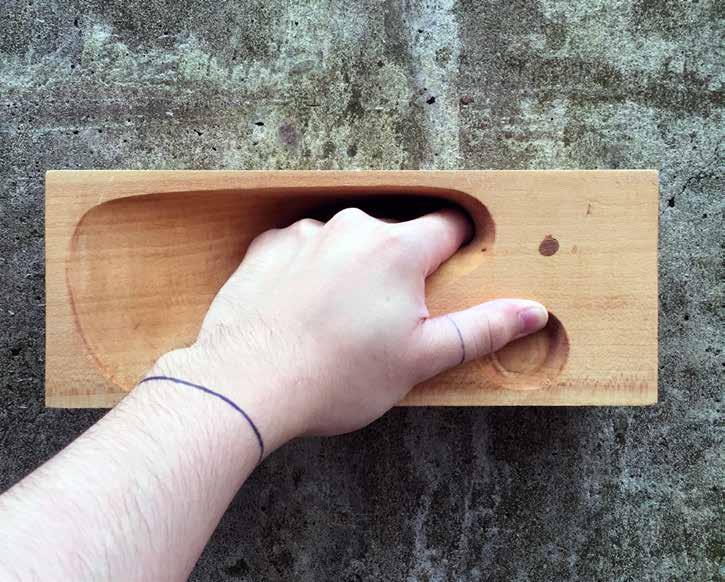
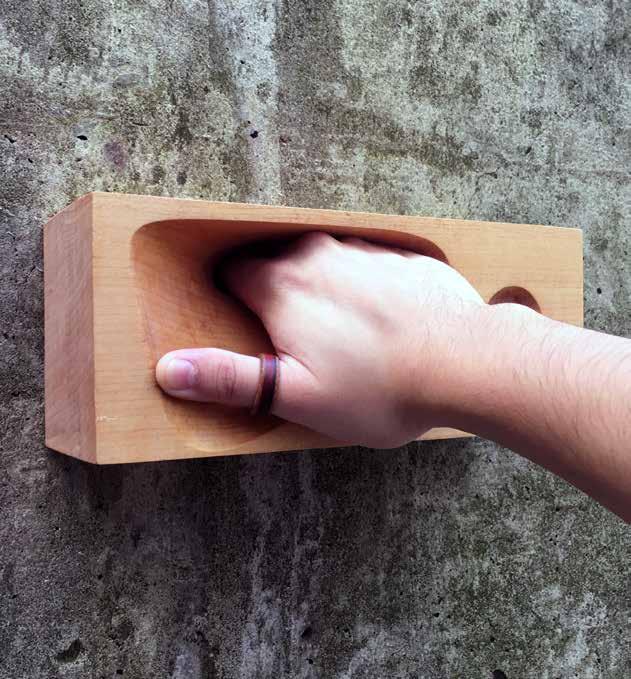
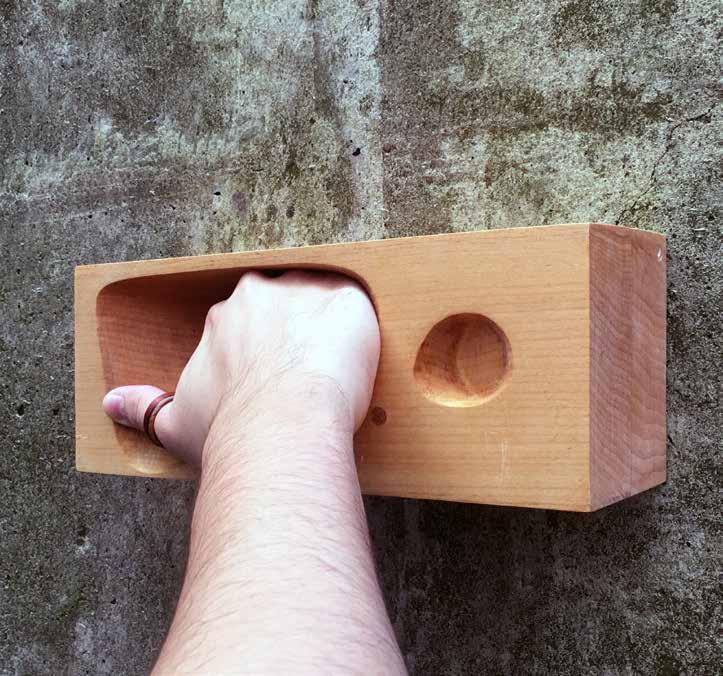