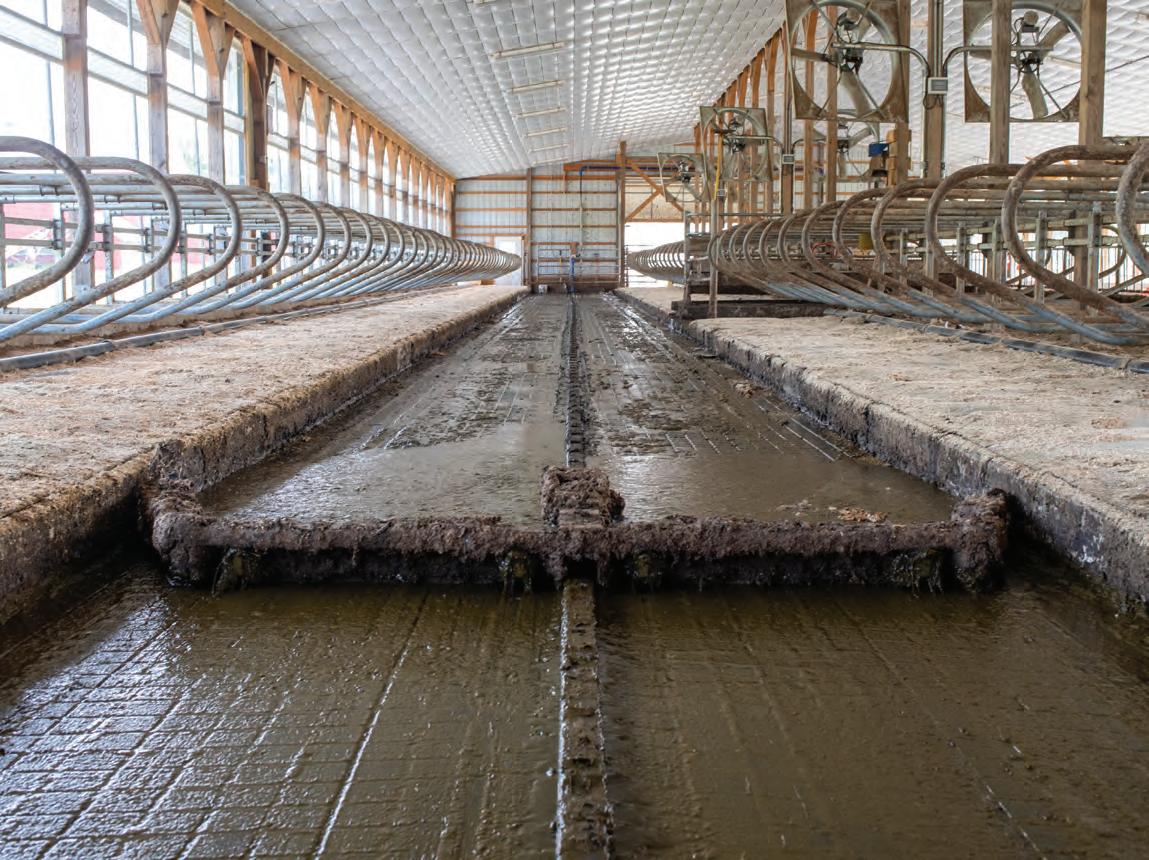
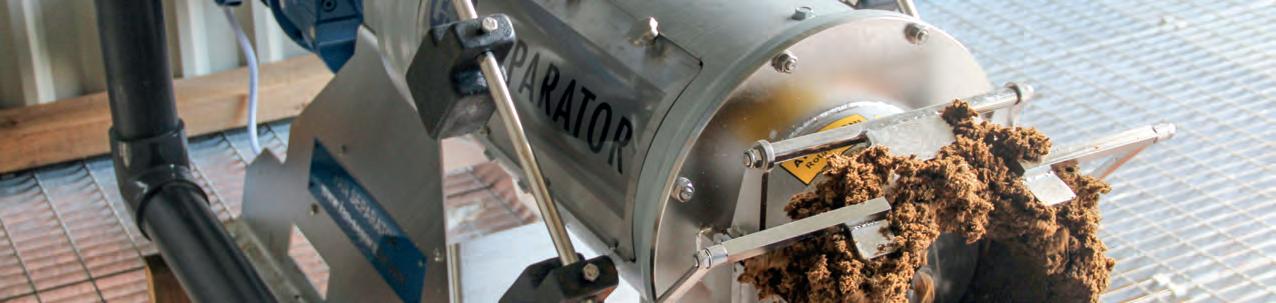
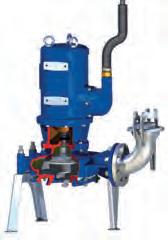
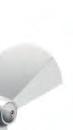

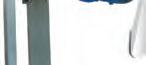

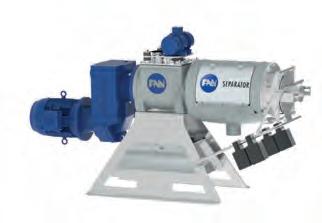
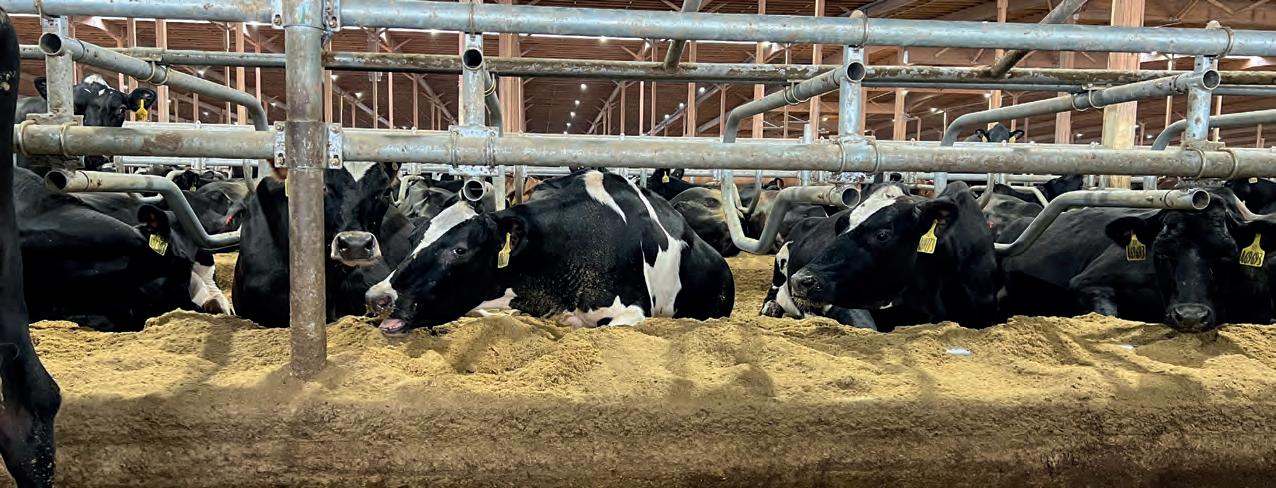
Managing Editor
Abby Bauer
Art Director
Todd Garrett
Editorial Coordinator
Jennifer Yurs
Director of Marketing
John Mansavage
Advertising Sales
Beth Gierke bgierke@nutrientmgmt.com
Advertising Coordinator
Patti Kressin pkressin@hoards.com
Online Media Manager
Patti Hurtgen phurtgen@hoards.com
Digital Marketing Manager
Michaela King mking@hoards.com
Publisher
W.D. Hoard & Sons Co.
Brian V. Knox, President
CONTACT INFORMATION
Editorial Office PO Box 801 28 Milwaukee Ave. West Fort Atkinson, WI 53538
Website: www.jofnm.com
Email: info@jofnm.com
Phone: 920-563-5551
In with the old, out with the new. As we begin this new year, it is a time to push out the old manure, if you will, and start fresh, setting goals for ourselves and our businesses. Similarly, manure and old bedding are pushed out of the freestall barn on this certified organic New York dairy farm using automated alley scrapers.
Journal of Nutrient Management (ISSN# 26902516) is published four times annually in February, May, August, and November by W.D. Hoard & Sons Company, 28 Milwaukee Ave. West, Fort Atkinson, Wisconsin 53538 Tel: (920) 563-5551. Email: info@ jofnm.com Website: www.jofnm.com. Postmaster: Send address corrections to: Journal of Nutrient Management, PO Box 801, Fort Atkinson, Wisconsin 53538-0801. Tel: (920) 563-5551. Email: info@jofnm. com. Subscription Rates: Free and controlled circulation to qualified subscribers. For Subscriber
Services contact: Journal of Nutrient Management, PO Box 801, Fort Atkinson, Wisconsin 53538, call (920) 563-5551, Email: info@jofnm.com.
Copyright © 2023 W.D. Hoard & Sons Company. ALL RIGHTS RESERVED. Content may not be reproduced or used for any commercial activity without express written consent from W. D. Hoard & Sons Company
Lately, I often find the song “Take me home, country roads” stuck in my head. I taught my children the chorus, and now the John Denver classic has become one of the songs my son asks me to sing before he goes to bed each night.
Abby Bauer Managing EditorWhether you live where you grew up, are a few towns away, or moved across the country, that song is somewhat of an anthem for almost anyone who was raised in rural America. No matter where we go in life, the memory of those country roads can bring us back to where we came from.
Beyond their sentimental value, country roads are a critical link between the people who grow food and the people who eat food. Livestock trailers, milk trucks, grain carts, and more travel these dusty roads all year round to deliver products where they need to be.
Somewhat like a farmer’s body, years of hard work take a toll on rural roads. The breakdown of these pathways impacts the agriculture industry as well as the people who live in the countryside and travel these routes every day. Unfortunately, road repairs don’t come cheap.
It’s a pretty safe bet that town and county board members spend a decent amount of time discussing the roads in their area. It’s a puzzle to determine what roads need repair, which ones are the top priority, and what funding is available to complete these projects.
In some places, finger pointing may be directed at farms due to the volume of traffic that enters and exits the property. During manure hauling or corn silage harvest, the local roadways become a well-traveled route for some heavy equipment.
In an effort to prevent damage, some towns or counties have tried putting more stringent rules in place to limit wheel traffic on rural roads. While one can’t blame them for trying to protect this valuable asset, some of these regulations seem to unfairly target agriculture, and in certain cases, the restrictions could severely impact or even halt a farm’s ability to transport their products.
One such case surfaced in northwestern Wisconsin’s Price County. This county, like many others across the northern United States, places temporary weight restrictions on its roadways to limit travel of heavy vehicles during the spring thaw. Typically, exemptions are allowed for trucks that carry necessary items, such as heat-
ing fuel and septic services.
Milk haulers were also included on that exemption list until last spring, when Price County officials tried to invoke a weight limit that would have prevented milk pick up from some local dairy farms. In the end, an agreement was reached between the county and the milk hauler, and a permit was granted so that milk trucks could continue to travel down those country roads.
This winter, another county in the Badger State is trying to invoke stricter road rules. In Chippewa County, milk haulers must attend a mandatory meeting to learn about the county’s new permitting process and purchase a permit to haul milk this spring. Failure to obtain a permit may result in costly citations. There is concern that more counties could follow in similar footsteps.
High fuel costs, a truck driver shortage, and the long distance milk and other products need to travel already make transportation a challenge. Add to the mix restrictions that limit where trucks can drive, and farmers may find themselves in situations that could damage their business and livelihood.
What can be done to help prevent restrictions affecting the transport of livestock, raw goods, feed, and manure? First, stay connected to your local representatives. If they understand the important role county roads play for ag businesses, they will be more apt to work with farmers to find reasonable solutions that protect the roadways we all need.
Also, be mindful of practices that can cause damage. Watch axle weights, especially during times of the year when roadways are more vulnerable. Avoid driving on the edge of the road when possible, and look for opportunities to transport materials in other ways. For manure, draglines and underground pipes have already reduced the number of tankers rolling down the road, which is a win for the farmer and the township.
At the end of every farm driveway is a country road. We need these country roads to haul our products, drive to work, and for some of us, they lead us back home every now and then.
Until next time,
A request by the state of Ohio to transfer certain regulatory responsibilities regarding concentrated animal feeding operations (CAFOs) from the Ohio Environmental Protection Agency to the Ohio Department of Agriculture has been denied. The request was intended to streamline the permitting process and prevent duplication of efforts between the two agencies. The Environmental Protection Agency (EPA) indicated that the request was incomplete under codified federal regulations and the state did not attempt to correct the deficiencies of the application when given the opportunity. The EPA did leave the door open to consider a revised request in the future if it incorporated statutory and regulatory changes that meet the Clean Water Act requirements.
The Delaware Nutrient Management Commission voted to proceed with rare changes to the state’s nutrient management rules, which are typically only updated once every 10 years. The most notable change would close a loophole that may allow consultants hired by farmers to create state-mandated nutrient management plans to avoid an assessment of phosphorus risks. There is no solid evidence consultants have taken advantage of the loophole, according to the nutrient management program administrator, but this rule change, if adopted by the state’s General Assembly, would remove the opportunity.
Lactanet, the leading organization for milk recording, genetic services, and dairy farm management in Canada, will publish Methane Efficiency breeding values with the April 2023 genetic evaluations. After collecting more than 13 million milk mid-infrared spectroscopy records over five years, Lactanet analyzed the records to predict methane emissions and determined that it is possible to reduce emissions with genetic selection.
A methane index will be available for all Holstein sires marketed by Semex with the April release. The bull stud said that the index is 70% reliable for genomic bulls.
The Environmental Protection Agency (EPA) announced last month that it will gather information and conduct a detailed study to determine whether it needs to strengthen regulations for concentrated animal feeding operations (CAFOs). The agency has not revised its rules for the nation’s largest farms since 2008. In 2021, the EPA said it had no planned changes but is now reconsidering that decision in response to a lawsuit by environmental group Food and Water Watch.
The agency will seek more data from farms and will also consider practices and technologies that were not available when the rules were last updated. Revising water pollution rules typically takes several years, three full-time employees, and $1 million per year in contractor fees, according to the EPA. The study will determine if the potential environmental benefits of changing the rule will justify the significant resources required to make the update.
Congress passed and President Biden signed the Inflation Reduction Act on August 7, 2022. This legislation is basically the U.S. Senate’s version of the Build Back Better Act the House passed earlier. This law looks a lot like the Build Better Act.
With some estimates of costs running as high as $750 billion, this bill is arguably one of the biggest U.S. government programs to launch since The New Deal of Franklin Roosevelt’s era. It includes up to $40 billion in funding for farm and farm related programs. Perhaps the ones of most interest are biogas support, cover crops, and loan support.
In some ways, the big winner for agriculture is conservation. These programs would receive $19.5 billion in help to develop and expand conservation practices on farms. And, it would mean farmers could plan on programs actually being funded.
Some of these programs are very technical and paperwork intensive —and sometimes they run out of money. Still one item to really watch is the Carbon Sequestration and Greenhouse Gas Emissions Quantification Program. This could be very important because for carbon credits to be treated as commodities, they need to be quantified in a way the market is comfortable enough to buy and sell. The $300 million allocated to this area seems small, but the ability to truly quantify carbon sequestration would be huge because it is an important step in actually being able to turn carbon into
more of a tradeable commodity.
The Inflation Reduction Act also contains some money for debt relief that could be game changing for farmers with pressing money problems. Debt relief was proposed early with the American Rescue Plan, but that ran aground in the courts. The Inflation Reduction Act options would allow for forgiven loans and modifying terms of loans for “distressed borrowers.” The USDA will be responsible for developing guidelines for eligibility and for deciding which farmers are eligible because their farming enterprises are at financial risk.
Along with this program, there is also supposed to be help for farmers who have been historically underserved. This is geared for those who have
experienced discrimination in the past. There are also programs for avoiding land loss and career development.
Cover crop supports are also a big development. The bill would pay farmers $25 per acre, up to 1,000 acres, to plant cover crops through the 2026 crop year. It also includes a $5 per acre incentive for landowners to establish cover crops with renters as well.
Theoretically, this could be a crucial development at a crucial time. Cover crops, of course, can do great things — hold soil in place, reduce nitrogen runoff, and help plants endure drought successfully. And one huge benefit for farmers who are required to buy nitro-
gen fertilizer is that cover crops can fix nitrogen in the soil and reduce the need for purchased fertilizers. Given the way fertilizer prices have been, there is a powerful incentive to look at alternative nitrogen sources.
Cover crops could certainly offer an alternative and, perhaps with government help, an increasingly cost effective one. It’s also possible the government financial supports will make people more comfortable with the inherent risks of adding a new crop rotation to the mix.
One of the most interesting programs for animal agriculture is the biogas provisions the bill contains. Some of the benefits are in the form of tax credits that have been created or extended. The American Biogas Council welcomes the passage of the Inflation Reduction Act. According to the American Biogas Council, there are 2,300 operational biogas systems in the U.S. However, 85% of the biogas potential has not been realized. The group estimates that 65 million tons of food waste and manure and other waste from 8 billion animals could be used to generate significant amounts of sustainable biogas.
One big benefit of the Inflation Reduction Act is more certainly that the tax credits will be there going forward. This gives investors greater ability to compare biogas with other investments because, at least theoretically, the tax credits should be more certain.
Again, according to the American Biogas Council, the U.S. has 2,300 operational biogas systems, but only about 15% of the potential for the biogas has been realized. Estimates are that high because the U.S. produces 65 million tons of food waste, manure, and other waste a year. This comes from an estimated 8 billion cows, chickens, turkeys and pigs and over 11 trillion gallons of wastewater each year. If the tax credits and other supports work, then biogas production should rise as more plants are built.
There were some programs that fell off the House version. For example, some agricultural research and rural water supports were eliminated.
The Inflation Reduction Act represents one of the biggest expenditures
for agriculture in decades. It’s possible it could offer significant benefits to the U.S. in the form of cleaner water and less nitrogen runoff based on greater use of cover crops. In addition, it could provide financially distressed farmers who qualify loan modification or forgiveness. Last but certainly not least,
the tax credits and assistance might make biogas more prevalent.
Cornell’s 81022MPL with the robust, yet compact EM19DBK Frame and Run-Dry™ Option tackles the toughest manure slurries. Featuring:
6000 GPM / 420’ TDH at BEP at 1800 RPM
7500 GPM max flow
High Efficiency
Low NPSHr
Proven Cornell construction for handling sand laden manure
Hard face seal with run-dry seal protection
With an 8” discharge, 10” suction and 3.5” solids handing, and built for high-operating pressures, MP pumps are specifically designed for coarse-abrasive slurry applications. Constructed of high chrome iron, with a Brinell hardness rating above 650.
Talk with your authorized Cornell dealer about finding the best model for your application.
Concentrated animal feeding operations (CAFOs) are intensely managed production systems that allow for improved efficiency and better care of the animals. Manure from these systems must also be intensely managed to avoid negative impacts on the environment.
Cattle feedlot pen surfaces are particularly challenging because the manure is directly exposed to the environmental elements of rain, snow, sun, and wind. Chemical, physical, and biological reactions occur on the feedlot surface that result in the release of a variety of compounds.
Airborne pollutants from CAFOs are comprised of particulate matter, biological materials, and gaseous emissions including carbon dioxide, methane, nitrous oxide, ammonia, hydrogen sulfide, and other odorous compounds. Because of the complex reactions that occur on the feedlot surface, when conditions change to prohibit the release of one gas, it can create an opportunistic environment for a second gas to be produced. This complicates the ability of producers to manage emissions from the feedlot surface.
Hydrogen sulfide is a colorless gas that has a characteristic rotten egg smell. It is formed during bacterial decomposition of human and animal waste and is present in emissions from sewage treatment facilities and landfills. Iowa, Minnesota, Nebraska, Rhode Island, and Texas
have ambient air quality standards for hydrogen sulfide emissions from CAFOs. These standards and potential nuisance issues prompt the need for mitigation of hydrogen sulfide and other sulfides from livestock facilities.
Ammonia emissions are commonly associated with livestock production. Nitrogen losses as ammonia can be quite high from beef cattle feedlots. Research has demonstrated that 51% to 73% of the nitrogen on the cattle feedlot surface can be lost as ammonia during the summer and 35% to 50% of nitrogen is lost during winter months. This pollutes the environment and limits the fertilizer value of the cattle manure.
A pH of 7 to 10 is ideal for ammonia volatilization, whereas a pH less than 6.5 will result in little ammonia volatilization. Therefore, lowering the pH
of the beef feedlot surface may reduce nitrogen volatilization and increase fertilizer value of the manure, which would be especially beneficial during the warm summer months.
According to the U.S. Environmental Protection Agency’s 2019 Inventory of U.S. Greenhouse Gas Emissions and Sinks, 9% of total U.S. greenhouse gas (GHG) emissions are from agriculture. Enteric methane emissions from ruminant animals represent nearly 30% of the agricultural GHG emissions, while manure management contributes 14% of total GHG emissions from the agricultural sector.
There is a lot of interest within agriculture to reduce GHGs. In October 2020, the Innovation Center for U.S. Dairy unveiled the Net Zero Initiative, an industry-wide effort to help U.S. dairy farms of all sizes and geographies implement new technologies and adopt economically viable practices to achieve carbon neutrality, optimize water usage, and improve water quality by 2050. This was followed closely by the National Cattlemen’s Beef Association’s commitment to environmental, economic, and social sustainability by announcing that U.S. cattle production would be climate neutral (or carbon neutral) by 2040. With these big initiatives, all technologies that affect odor or gas emission must also consider the impact on GHGs.
One way livestock producers can reduce these emissions is to apply products
to the feedlot surface that can prevent the release of these gases into the air. Aluminum sulfate, also known as alum, is one such product. The poultry industry has successfully used alum for almost 20 years to reduce ammonia emission. Alum works by lowering the pH of the poultry litter, which traps the nitrogen in the litter and keeps it from escaping into the air. This study was designed to see if alum could also work on beef cattle feedlot surfaces to reduce ammonia, hydrogen sulfide, carbon dioxide, nitrous oxide, and methane emissions.
Eight feedlot pens (30 animals per pen) at the U.S. Meat Animal Research Center feedlot were utilized. The pens had a central mound constructed on manure and soil and a concrete apron by the feedbunk. Four pens had 10% alum applied to the 20 feet immediately behind the concrete bunk apron. Four pens did not receive alum.
Samples of the feedlot surface material from each pen were collected one day before alum application, on the day of
application, and five, seven, 12, 14, 19, 21, and 24 days post-application. Samples were measured for pH and ammonia, hydrogen sulfide, carbon dioxide, methane, and nitrous oxide emissions. Addition of alum lowered the pH of feedlot surface material from 8.3 to 4.8 and the pH remained lower in alumtreated pens for 24 days. Although the pH was low, ammonia emissions were only lower at Day 0 and Day 5 for alumtreated pens compared to the pens with no alum treatment. Nitrous oxide emission was not affected by alum treatment. Carbon dioxide emission was lower for alum-treated pens than non-treated pens from Day 5 until the end of the study, perhaps due to suppressed microbial activity from the lower pH. Hydrogen sulfide emission was higher from alum-treated feedlot surface material compared to nontreated feedlot surface material, likely due to addition of sulfate with alum. Methane emission was also higher in alum-treated pens than nontreated pens. This may be because
the alum-treated pens appeared wetter, which creates an environment that produces methane.
The limited reduction in ammonia, along with increased hydrogen sulfide and methane emission, indicates that alum is not a suitable amendment to reduce emissions from beef feedlot surfaces. Future research will evaluate the use of aluminum chloride instead of aluminum sulfate to lower pH of feedlot surface material and retain nitrogen, without adding additional sulfate which is converted to hydrogen sulfide. Additionally, microbial amendments are being evaluated to determine if they can reduce gaseous emissions from the feedlot surface.
Historically, reduced tillage — defined as tillage that maintains plant surface residue and where nutrients are surface applied — was touted as the solution for phosphorus loss from agricultural fields. Examples include no-till, zone-till, strip-till, or vertical tillage.
This article elevates the issue of phosphorus loss without erosion by highlighting dissolved phosphorus loss pathways. Reduced tillage cuts back phosphorus loss risk through two main processes: by decreasing soil erosion and increasing soil’s infiltration capacity.
Preventing topsoil from leaving the field provides many agronomic and water quality benefits by keeping valuable soil-bound phosphorus nutrients in the field and soil out of surface waters. Reduced tillage leaves a protective residue on the surface, physically protecting the soil by intercepting powerful raindrops from hitting the surface and dislodging soil, which is then more susceptible to erosion.
Wisconsin’s Discovery Farms edgeof-field monitoring shows that around 50% of the total phosphorus that leaves fields in Wisconsin is typically in this particulate form. It is commonly lost in late spring and early summer when heavy precipitation is paired with no
canopy cover and unfrozen ground (Figure 1).
A second, less discussed, benefit is the ability of reduced tillage to raise soil’s water infiltration capacity. The reduction in disturbance allows for greater organic matter protection, worm activity, and microbial activity, which helps improve soil aggregate stability and create channels where water can infiltrate.
When the ground is unfrozen, fields that infiltrate more water effectively reduce the amount of water running off the field into surface water bodies. Less surface water leaving the field typically means less particulate and dissolved phosphorus loss. Smaller volumes of water carry less soil and interact with fewer sources of water-soluble phosphorus.
Reduced tillage can have trade-offs. The previously mentioned benefits mostly reduce phosphorus loss on unfrozen ground, which is typically when 50% of the phosphorus loss occurs in Wisconsin.
Recent research and monitoring have shown that reduced tillage can intensify dissolved phosphorus loss by increasing the amount of phosphorus at the soil surface. Dissolved phosphorus loss is not dependent on soil movement.
A Discovery Farms edge of field monitor collects year round information on the quantity and quality of surface water leaving a basin. This field has high residue and clear runoff water, but unseen dissolved phosphorus could still be leaving the field with the runoff.
Rather, it is driven by water interacting with organic and water-soluble forms of phosphorus, like residue, synthetic fertilizer, manure, or even phosphorus attached to soil. Dissolved phosphorus is often lost in winter months when the soil is frozen, snowmelt is occurring, and little infiltration into the soil can occur (Figure 1).
In reduced tillage systems, there tends to be a build up of residue or plant biomass on the soil surface, which are all sources of phosphorus. Long-term reduced tillage fields can
lead to higher phosphorus levels in the top inch or two of the soil due to broadcast applications of manure and synthetic fertilizer. This stratification of phosphorus at the soil surface creates a high risk for interaction between phosphorus sources and a large amount of runoff water via snowmelt, rain, or both.
These processes occur in Wisconsin and throughout the Upper Midwest. Twenty years of Discovery Farms monitoring has shown that annual total phosphorus loss between conventionally tilled and no-till fields is about equal. Soil loss is greatly reduced (Figure 2a and 2c) under no-till but, as discussed above, it can result in increased phosphorus losses in the dissolved form (Figure 2b).
In the Lake Erie watershed, where cover crops, reduced tillage, and other conservation practices have been heavily adopted, dissolved phosphorus loads have doubled in the 2000s compared to the 1990s. This occurred even though the total phosphorus loads have stayed relatively the same.
The benefits of reduced tillage to other soil and agronomic properties should not be overlooked. Small adjustments can be made to maintain the positives of reduced tillage while minimizing sources of phosphorus on the surface.
Here are some recommended strategies that can be used to mitigate dissolved phosphorus losses:
1. Reduce phosphorus applications and use crop removal to draw down soil test phosphorus (STP) over time.
Soil’s ability to bind phosphorus to its surface has led to it being a major source of phosphorus rather than a sink after years of application of phosphorus greater than crop removal. High STP values have doubled over the last 50 years. STP in the top inch of the soil is related to the amount of dissolved phosphorus loss in agricultural fields (Figure 3). A typical corn crop in Wisconsin only removes 3 to 5 parts per million (ppm) of phosphorus per year if no other
continued on following page >>>
Winter phosphorus loss through runoff is predominantly dissolved; in spring, the runoff is mostly particulate.
Annual total phosphorus (a) is similar between tilled and no-till fields due to the increase in dissolved phosphorus loss from no-till fields (b), even though soil loss (c) is greatly reduced.
phosphorus is applied. As a result, drawdown of STP can take awhile.
2. Place fertilizer and manure under the surface.
Banding or injecting fertilizer or manure below the top inch of the soil can help with soil stratification and dissolved phosphorus loss. Occasional deep tillage may help relieve soil fertility stratification, but it comes with a tradeoff of soil loss if no other erosion control methods are used.
3. Optimize the timing of phosphorus application in fields.
Avoid fertilizer or manure application when the ground is frozen (January to March), especially on snow, as it has little chance to interact with the soil before a runoff event occurs. Instead, the phosphorus has ample time to interact and dissolve into runoff water (Figure 4).
4. Choose to plant cover crop species that overwinter.
Winter-killed cover crops like brassicas and oats act to raise the amount of phosphorus at the surface. The cover crops take up phosphorus from different layers of the soil, but their cells rupture after frost and release phosphorus as the residue breaks down during periods of higher runoff risk. Frost hardy or overwintering cover crops have adapted to protect their cells with antifreeze proteins, reducing the amount of water extractable phosphorus.
Many farms have made significant strides in adoption of reduced tillage practices that work to lessen agriculture’s impact on water quality through erosion control. However, a blanket approach will not solve complex water quality issues. Reducing excess phosphorus at the soil surface through deeper fertility placement and STP drawdown is the next goal agriculture can work toward to reduce dissolved phosphorus losses associated with the reduced tillage systems. ■
The author is an ag and water quality outreach specialist with University of Wisconsin-Madison Extension.
There is a positive correlation between soil test phosphorus in the upper 1 inch of soil with flow weighted mean concentration of dissolved phosphorus in edge-of-field runoff.
Dissolved phosphorus drives phosphorus loss on frozen soils, and late winter manure application can elevate losses by two to four times compared to early winter application or no winter application. Manure application shortly before a snowmelt or a rain event on frozen ground drives the largest losses.
As livestock producers, our goal should be to expand the portion of the ration that contains ingredients humans can’t use.
We live at a time where memes — amusing or interesting photos or videos that are shared online — communicate sentiments in a new way. In a world with pandemics, an ever-growing political divide, military conflict, and varying levels of climate concern, there is no shortage of sentiments that need to be communicated!
To make a point about the public’s opinion regarding COVID-19, one meme noted that Santa had been reading your social media posts and he will be getting you a science textbook for Christmas. Regular folks can’t simply develop the right pandemic policy or interpret climate change. For most, the meme hits close to home. In a world where almost anyone can know a little bit
about nearly any topic, it is crucial that the court of public opinion be guided by those with more than a “little bit” of knowledge on such topics.
Much of my work with feeding dairy cows can be understood with the basics of fifth grade math and ninth grade science. I may not be right on the exact
school years, but the point is that there are basic laws of science and math that can correctly answer the questions we face in what seems to be a new world. Every industry is being asked or required to do better in numerous areas related to efficiency, sustainability, and using natural resources.
It is true that farmers are not new to the environmental movement. To be candid, agriculture has been far from perfect in the quest to work “along with,” instead of “against,” nature. Our history is not without a few black eyes along the way, but what industry doesn’t have a similar learning curve?
In response to the obvious problems related to plowing up the arid High Plains to plant wheat in the 1930s and the resulting Dust Bowl era, the Soil Conservation Service was created to leverage science and logic into better practices for farmers. Of course, this didn’t solve every problem, and the learning curve continues with ever-improving science and technology to reach new levels of environmental care.
Many of the principles that define success or failure in this race to be sustainable can be described by the classroom science and math mentioned above. The math presides over the dollars and cents of products purchased and products sold. The science presides over the unique task of utilizing the connection between animals and the land used to feed people.
There has been a noticeable uptick in the frequency of conversations with my clients about topics related to sustainability. Among these conversations are discussions about manure digesters, solar panels, electric feed delivery trucks, drought-tolerant forage crops, and numerous feed additives that reduce greenhouse gases. It is a lot to consider.
The opportunities related to improving efficiency of converting feed to human food is our firm’s area of expertise. It’s the upcycling of one set of nutrients into another set of nutrients. One set is mostly unusable by humans; the second set is high-quality human food ready to ship anywhere in the world.
These worldwide customers are speaking out more often and with greater volume about their interest in how food is produced. I think going back to the fifth grade math, and especially the ninth grade science, is the path to satisfying the financial needs of those whose life’s work is milking cows and the dairy product consumers.
If you look at what consumers want, the dairy industry has made much progress already. Every efficiency one could measure is better now than even 20 years ago. This is not only good for the producer searching for a reasonable margin to feed their own families, but it’s also good for so many concerns related to sustainability and climate change.
The next gains will be more difficult to achieve and will likely put pressure on producer margins. Will the consumer be willing to pay a higher cost to help the farmer maintain respectable margins?
We are sitting on the cusp of a sea of change in this conversation. We are working with several potential feed additives that can make a significant reduction in methane production. And guess what — they also improve milk production efficiency and producer margins.
Going all the way back to nutrition class as a freshman in col-
lege, we were taught the role of methane in a cow’s rumen; this is not a new topic for our industry. We have been working for a generation now to find the best way to reduce this loss of carbon.
The Food and Drug Administration’s approval of monensin in dairy rations in 2004 offered the first tool for our industry to reduce methane. This technology had been utilized in beef production prior to that time and it is employed significantly in dairy and beef production today. What is next in this arena?
My challenge to our industry is to listen to consumers and engage with science to become even more efficient in producing milk and beef. Furthermore, our goal should be to expand the portion of beef and dairy cattle diets that is made up of ingredients unusable by humans. A falling trend over time for primary grains like corn in dairy rations will help us meet our goals.
In order to accomplish that and still meet the need for adequate margins, the nutritional science advancements for improving milk production efficiency with lower quality forages, human food by-product streams, and even animal genetics and husbandry will all work hand in hand. This will sustain our industry for generations to come. ■
Dairy farms of all sizes are challenged with properly disposing and managing the manure produced by their herds. The larger the dairy, the greater the challenge becomes in containing and managing effluent, solids, volatiles such as ammonia, and, more recently, odor. While manure is universally accepted as an indispensable source of plant nutrients and soil amendments, many dairies have limited access to adequate land or the ability to dispose of their
manure in a timely or an environmentally responsible way.
It’s an issue that can no longer be swept under the rug. For many years, the mainstream press has had a field day demonizing animal agriculture in general and dairy farming in particular as major polluters of nitrogen and phosphorus as well as volatile gases such as methane and ammonia polluting the atmosphere and emitting odors.
For all the challenges associated with manure, there’s a positive side to this
organic material as a source of renewable energy that goes well beyond its traditional use as a fertilizer. Emerging over the last decade is a growing industry focused on collecting and marketing the biomethane produced by the anaerobic fermentation of manure.
Near the town of Americus, Ga., Leatherbrook Holsteins milks 7,000 cows. Owner Adam Graft and his family have been dairy farming since 2005
This Georgia dairy farmer found a partner that allows them to produce renewable energy.Todd Garrett
and have been at their current location since 2008. Cows are housed in freestall barns containing fans and soakers. Sand is used for bedding. The diet consists of corn and triticale silages along with plant proteins, vitamins, and minerals.
The cows are milked 3x in two parlors — a double-50 parallel and an 80-cow rotary. Milk production ranges from 70 to 90-plus pounds of milk per cow per day and is profoundly affected by Georgia’s summertime heat and humidity.
In 2016, Graft began the process of building an anaerobic digestion system that met his requirements for properly managing manure and reducing odors. He noted that there are many companies that have entered the manure digestion and methane production business. However, not all are fully knowledgeable of how to construct large anaerobic digesters or offer round-theclock management of those systems.
Graft chose to work with Vanguard Renewables because of their successful
track record of installing and operating both manure only and co-digestion systems on dairies with a large range of herd sizes. They also supply the capital necessary to install the systems, eliminating the need for dairy farms to come up with the finances to fund such a project, which would be substantial. The anaerobic digestion system for
Graft’s 7,000 cows is an integrated system that quickly and efficiently moves the manure effluent to a series of digesters that are large enough to contain and continuously process the manure. This eliminates odor from the dairy and delivers a nutrient-rich end-product that can be applied to 3,000 acres of irrigated cropland. The key to odor control on all dairy farms is to prevent manure from decomposing or fermenting, which releases volatile gases into the air.
On freestall dairies like Graft’s, manure effluent, primarily coming from flushing freestalls, is quickly transported into sealed lagoons where the gases cannot escape. It’s in the sealed lagoons where the marketable by-product, methane, is produced, captured, processed on-site, and piped directly into the local natural gas utility’s pipeline.
According to Kevin Chase, co-foundercontinued on following page >>>
and chief development officer at Vanguard Renewables, any dairy farm, large or small, has the ability to produce methane from the manure produced. On smaller dairies, the company adds food waste to the manure in a process known as co-digestion. A manure-only digester is an expensive undertaking to build, manage, and maintain. Most importantly, there must be an adequate amount of manure available to justify the investment.
Chase says that for his company to consider a manure-only system financially viable, there needs to be a minimum of 5,000 to 10,000 wet-cow (milk-cow) equivalents available. He has systems in operation on both single sites as well as groups of dairy farms that are in close geographic proximity to share the infrastructure. The company looks specifically to partner with dairy farms that are interested in proactive approaches to mitigating environmental pollution and positioning their dairy farms in a positive light in their communities.
With the 7,000 milking cows along with the heifers and dry cows on the property, Leatherbrook Holsteins met the requirement to be a stand-alone methane producer that uses only the manure produced on the farm without having to add additional organic material to maximize methane production. The dairy derives two income streams through the partnership — a lease payment for the land being used and a payment for the manure used in the digestion process.
Graft explained that the digestion system reduces the massive amount of manure solids to about one-fourth the volume of material while still containing all the nutrients. The digestate material remaining after the digestion process is pumped out of the digesters and temporarily stored in a small lagoon. From there it’s pumped out to the cropland via a drag-hose system, which includes about 6 miles of underground pipeline.
The drag-hose system allows Graft to move a lot of fertilizer rapidly in a liquefied form, which enables it to be injected into the ground. This reduces the volatilization loss of spreading fertilizer on the ground surface and enables more nitrogen to be delivered for plant uptake. In addition to the more efficient delivery of nutrients, this system completely eliminates the need for daily hauling and spreading, or the need to stockpile solids, which creates the potential for odors, runoff, and ground water contamination.
The system at Leatherbrook Holsteins is designed to produce 200,000 million British thermal units (MMBtu) per year, which provides the energy-equivalent of over 58,000,000 kwh. According to the U.S. Department of Energy, the average home in the U.S. uses about 900 kwh of electricity per month or about 10,800 kwh/year. Therefore, the energy provided by the collected methane at Leatherbrook Holsteins can provide enough energy to power over 5,000 homes for a year. The raw biogas that comes directly out of the digester is not pure methane
and must be purified before it can be delivered to a local utility. The purification process is completed at the site and includes the removal of water vapor, carbon dioxide, sulfides, and nitrogen compounds, which are all by-products of the anaerobic process. The purified methane is then piped about 2 miles to a location where it joins a local utility’s natural gas line.
As U.S. dairy farms grow in size, they become bigger targets for a critical public and more vulnerable to environmental pollution and legal actions. While dairy farms are certainly not the primary producer of methane escaping into the atmosphere, they do need to take a proactive approach in helping mitigate unnecessary levels of this potent greenhouse gas that’s contributing to the changes in weather patterns around the world.
When opportunities exist, partnering with an environmental management company that provides technology, management, and capital is a brilliant way for dairy farms to manage manure and odors, capture a potent greenhouse gas, and cash in on its value as a renewable source of energy. At the same time, dairy farms can be part of the solution, not part of the problem, in protecting our fragile environment. ■
The bedding under their feet contains the first bacteria chicks are exposed to. For that reason, reusing litter — which contains a mixture of wood shavings, feces, uric acid, feathers, and chicken feed — rather than supplying fresh bedding can help build up the birds’ immune systems.
Joint research between the University of Georgia and the U.S. National Poultry Research Center investigated the role that bacteria play in poultry health and food safety. Beyond improving the immunity in chicks, they found that reused litter may also help prevent the transfer of antibiotic resis-
tance between bacterial species.
Chicks in the study were infected with a strain of salmonella that was not antibiotic resistant. Some of the animals were raised on fresh litter while others were housed on reused litter.
When the study was completed, chickens raised on reused litter had a lower salmonella positivity rate (66%) compared to the chickens raised on fresh litter (79%). It was also found that some of the chickens raised on fresh litter were infected with a multidrug resistant strain of salmonella — not the strain used originally to infect the chicks. None of the chickens
raised on reused litter were infected with that strain. Further investigation found that this resistance was transferred from E. coli bacteria living within the digestive system. This study showed the role reused litter can play in both animal health and controlling the spread of antibiotic-resistant foodborne bacteria, the researchers noted. It can also be a cost savings. One negative aspect is that reused litter may cause high ammonia levels to accumulate in broiler houses, which can affect human health. For this reason, some farms change out the litter at least annually. ■
Changes in manure regulations, volume, and equipment impact how it is managed today.
During a Hoard’s Dairyman webinar, Becky Larson, an associate professor and extension specialist with the University of Wisconsin-Madison, said, “While some things with manure haven’t really changed, there are a lot of opportunities to integrate new technology or processing on your farm.”
Manure systems start with production and collection and end with storage, transfer, and application. Between those steps, farms can integrate processing or treatment of manure. Larson explained that processing changes the characteristics of manure, while treatment aims to reach a specific goal for the manure.
From solid separation to anaerobic digesters to water treatment systems, farmers find themselves with more manure processing and treatment options than ever before. Larson recommended that farms set goals for
their manure system before settling on any one technology.
When identifying goals, she said, “Be specific.” Rather than falling in love with a technology and figuring out how it can work on your farm, Larson advised looking at what problem you want to solve or what improvement you want to make. Again, make those goals specific. For example, rather than setting a goal to reduce hauling costs, determine by how much you want to cut those costs. Or, rather than simply acknowledging you have too much phosphorus for your land base, figure out how much extra phosphorus needs to be removed from the manure each year.
Cost is a major factor in selecting a system, but there are other noneconomical factors that must be considered, such as having too many nutrients for the current land base, a need to reduce labor, or something with the current system that isn’t working.
To set goals and then select the best system, Larson said it is critical for a
farmer to know their system and have numbers to evaluate it.
“Data is really important,” she said. “You can’t do the analysis unless you know the components of your system.” Examples of data to collect include manure produced annually, hauling costs, and characteristics of the manure such as solids or liquid content. Also consider how far manure is being hauled, how much fertilizer is being purchased, and how a new manure system would fit into your big picture nutrient management plans. New manure technology must either fit into the existing system or the existing system will need to be changed to incorporate those components. Larson said to determine what is needed so that there are not surprise costs down the road.
To learn about available manure processing technologies, visit on.hoards. com/WB_101022 to watch the webinar, titled “Will manure processing technology work on my farm?” ■
In the last 20 years, many states have added requirements for record keeping of manure applications on farm fields. This is to make sure that applications are used effectively as plant nutrients and to help protect water quality. Each state has different rules for applicator certification and record keeping, and some states are more stringent than others.
Starting in 2013, Indiana required anyone that applied over 10 cubic yards or 4,000 gallons of manure or fertilizer be certified as a licensed fertilizer material applicator. The applicator needs to take an initial exam, and then once they are certified, they can maintain their license by attending three recertification programs over a five-year period.
Along with record keeping, this new Indiana rule also included several good management practices, such as developing a fertilizer action plan prior to application and following that plan. Part of that plan includes manure testing so it is known what nutrients are actually being applied per acre. The plan also included restrictions on where manure can be applied, such as not directly on water and saturated ground, or not near setbacks from wells, sinkholes, and property lines. The fertilizer rule also put restrictions on manure applications applied to highly erodible land and frozen ground.
One key part of this fertilizer rule is record keeping of manure applications. In Indiana, licensed fertilizer applicators are required to record the application within 30 days and to keep the
records for two years after the application is made. Please check your state’s rules. For instance, in Ohio, the records need to be done within 24 hours after the application and kept for at least three years.
Manure application records in the Hoosier State must contain, at a minimum, the following:
1. Address or location description of the application site. This can be detailed or vague and could vary from being a GPS-generated application map to recording it as “Grandpa’s back 40.”
2. Name of the certified applicator making or supervising the application. If the applicator is not the certified applicator, it may be a good practice to also put the actual applicator’s name in the records for your own reference.
3. The applicator’s certification number.
4. Rate applied. This can be in tons per acre or gallons per acre.
5. Nutrient value of the fertilizer material. This requires a representative sample of the manure to be analyzed for its nutrient content. If
purchasing the manure from another farm, make sure to have weight tickets and the analysis of the manure for your records. The manure analysis will be recorded as pounds of nutrient per 1,000 gallons or pounds of nutrient per ton.
6. Type of fertilizer used. Indicate if it is swine manure, dairy manure, poultry litter, or another source.
7. Method of application. Include details like broadcast, knifed in, variable rate, and so forth.
8. Date of application, including month, day, and year.
Indiana does not have a set form to fill out, but on the next page is an example of a form with columns for all the key information needed. Many states have a specific form to fill out for each application.
Records of the slope of the field and how much residue is present at the time of the application could be useful information on areas with highly erodible soils or if the ground is frozen or snow covered.
When looking at other states’ requirements, several items on their required lists that need to be recorded could be very helpful to have recorded for reference in case there is a problem in the future. For example, many states require that you list the total acres covered and the total amount of product used for the field. The weather conditions, such as temperature, precipitation, and wind speed and direction the 24 hours before, during, and after the application are required in some states.
In Ohio, the records must contain
Documentation for manure application serves many purposes, but requirements differ from state to state.
• They can aid in management decisions.
• They may provide liability protection.
• They could be used to justify insurance claims.
• They may be requested in real estate transfers.
• They could be included in a conservation plan.
the soil conditions during application, such as whether the soil is frozen or snow covered. In Nebraska, the records need to show the type of equipment used to do the application, date of calibration for spreading equipment, and days to incorporation of manure. Where the manure origi-
nated from and information for that farm is also on the records list.
Farms often keep records because they are required, but records can be very beneficial in the long run for other reasons, too, such as:
Remember to check with your state annually to see what certifications you may need to apply manure. Also determine what records you must keep and how long to hold on to those records. These rules could change year to year. ■
Global warming is the rise in heat retention within the atmosphere, caused by the buildup of greenhouse gas (GHG). The consequence of global warming is climate change, which in practice results in the higher frequency and intensity of extreme weather events, such as drought, storms, flooding, and others. These extreme weather
events can have a direct impact on production agriculture.
Nearly two-thirds of atmospheric carbon dioxide (CO2) is the result of burning fossil fuels. The remainder comes from deforestation or food production. Other important agricultural GHG are methane (CH4) and nitrous oxide (N2 O). Methane is primarily emitted from ruminant animals’ diges -
tive systems, during manure application, and when manure is in storage. Nitrous oxide is emitted mainly from fertilizer application and urine deposition in soils.
The solution to climate change involves reducing the emissions of GHG and improving carbon (C) sequestration. Reducing emissions from CH4 and N2 O is more difficult than
Over time, we can reduce emissions and capture more carbon in agricultural fields.
reducing CO2 because both CH4 and N2 O result from complex biological processes in agricultural soils. Carbon sequestration represents uptake of carbon from the atmosphere into the soil, creating a negative flow of emissions that can be used to balance out CH4 and N2 O emissions in reducing the total carbon footprint.
Carbon sequestration is the process of capture, via photosynthesis, and long-term storage of atmospheric CO2 Photosynthesis and plant growth draw carbon into plant cells, releasing oxygen. Once plants die, plant residues are decomposed by soil organisms (such as bacteria, fungi, and earth worms), transforming the plant material into organic matter. Carbon is also added to the soil system by plant roots through root death, root exudates, and root respiration.
As organic matter in the topsoil layers increases over time, it slowly moves down into the soil profile and becomes more stable. Eventually, the soil organic matter is further decomposed into a more stable form of organic matter known as humus. The accumulation of organic carbon in stable organic matter at deeper soil layers represent carbon stock. The carbon stock in the soil prevents it from being emitted to the atmosphere again.
The second important aspect of carbon sequestration is that soil organic carbon (or soil organic matter) improves soil health by promoting water and nutrient retention, which are essential to plant and soil microbes’ growth. Better soil health will, then, enhance farm productivity, as well as reduce CO2 in the atmosphere.
Plant roots provide soil organic carbon primarily in the form of root litter and the release of organic material, including exudates, dead cells, and mycorrhizal biomass. Roots can also contribute to organic carbon input by forming soil aggregates and protecting organic carbon from the act of microbial decomposition. The region between plant roots and the soil in which plants grow is often referred to
as the rhizosphere, and the process of carbon addition directly from roots is called rhizodeposition.
There are two main processes that add carbon to the soil:
1. Accumulation of organic matter and conversion of organic matter in humus.
2. Root exudates and other root-borne organic substances released into the rhizosphere during plant growth and sloughing of root hairs and fine roots.
The carbon inputs directly via roots result in organic carbon gain, particularly when the input is of stable organic matter. It has been reported that photosynthetically fixed carbon in cereals and grasses is rapidly transported toward the root, reaching the soil within one hour. During one vegetative season, cereals and grasses can allocate about 1,400 to 2,000 pounds of carbon per acre below the ground. This accounts for nearly 5% to 20% of all photosynthetically fixed carbon transferred to soils through root exudates.
Recently, the importance and role of plant roots to carbon sequestration has been deeply investigated. It has become clear that organic matter inputs from roots contribute to organic carbon stabilization much more than aboveground plant inputs. More than 200 carbon compounds released from plant roots through rhizodeposition are reported.
The compounds released by plant roots that deposit in the root sphere are many and complex, ranging from mucilage, root border cells, extracellular enzymes, simple and complex sugars, amino acids, and vitamins. Belowground inputs are up to five times more efficient on stabilizing soil organic matter than aboveground residues. The carbon storage capacity of the soil is twice compared to the atmospheric carbon.
The rise in soil organic matter via roots results in more atmospheric carbon storage. More soil organic matter also leads to greater soil fertility, better soil tilth, water-holding capacity, and reduced soil erosion. It makes plants, and the entire agricultural field, more resistant to stress and better able to
withstand the climatic fluctuations that are expected to happen because of climate change.
The carbon content of most agricultural soils is now about one-third less than its native condition of either forest or grassland. Fortunately, modern agriculture has changed this scenario, reduced the net loss of soil carbon, and provided multiple options of strategies to restore soil carbon.
Practices that increase root growth and amount will intensify the carbon addition by roots to soils. Crop species with greater roots can deposit carbon in deeper layers — where it is protected from tillage and erosion — and contribute to carbon stocks. Introduction of perennial crops elevate carbon sequestration through root growth and cut down in soil disturbance. The use of cover crops during fallow periods provides year-round carbon sequestration and reduces soil loss via erosion. By reducing tillage, soil exposure to air is reduced, slowing down the decomposition of organic matter, which releases CO 2 back to the atmosphere.
The addition of legumes into grass pastures has positive effects on both plant yield and root production. Legumes, due to their capacity of biologically fixing nitrogen (N), provide additional nitrogen supply to the grass growing in the mix. The grass will uptake nitrogen, reducing its content in the soil, favoring legumes to continue nitrogen fixation. The positive interaction between these different plant types results in greater yield and stability of production.
Higher levels of biomass production, the return of greater proportions of crop residue to the soil, and diversification (via cover crops and mix of species, such as grass-legumes in pastures) provide soil protection from loss. They also result in greater inputs of carbon sequestration. ■
Bazooka Farmstar is excited to launch the updated Riptide Vertical Pit Pump for their manure agitation line-up. The improved Riptide Vertical Pit Pump has been redesigned to provide a simpler solution for end-users that can move high volumes of liquid manure with less maintenance. Its standard features and heavy-duty construction makes it a good choice for custom applicators and smaller operations.
The new Riptide is 15% more efficient than the original model, allowing it to move up to 5,850 GPM. The improved Riptide features a single 8-inch vertical pipe and a 20.5-inch Bazooka Farmstar Submersible Pump.
The Riptide is available with a twopoint hitch, two styles of three-point hitches, and a trailer-mounted version.
The trailer-mounted version, with its patent-pending folding technology, is an excellent option for users that work at multiple sites. The folding tongue allows users to move between sites faster, decreases set-up time, and more easily maneuvers the pump into the pit. The trailer configuration utilizes a single PTO shaft for operation, reducing the risk of downtime with fewer joints, boosting visibility and efficiency when placing the pump in the pit and eliminating the need to transport additional PTO shafts.
The agitation nozzles fold within the submersible pump’s diameter, creating a slim profile for pit entry. When the nozzles are folded, Riptide has a 34-inch total width.
To learn more, visit www.bazookafarmstar.com or call 1-800-775-7448.
VES-Artex introduces the Intelligent Soaker, a new animal cooling system that only sprays water when an animal is present and when temperatures fall within established parameters. This system has the proven benefits of a soaking system, while also reducing water used for animal cooling by as much as 70%.
“Simple on/off soakers run on a schedule whether there are animals present or not, representing a massive waste of water and energy. Cows spend 70% of the time away from the feed lane lying down, standing on the stalls, and being milked, and during this time, traditional soakers continue to operate. There is a lot of potential for water savings, but heat abatement is challenging to optimize because the negative effects of insufficient cooling can be extremely detrimental to animal well-being and production,” says Mario Mondaca, R & D Hardware Development Engineer at VES-Artex.
“That being said, the Intelligent Soaker does this not by reducing the amount of water the animal gets, but by reducing the amount of water you waste. With increasing concerns about water availability and social pressures on dairy producers, the Intelligent Soaker will allow farms to provide heat abatement while achieving a more sustainable operation,” Mondaca added.
The Intelligent Soaker is easy to install. Sensors gauge real-time weather conditions and will trigger when an animal is present. The system is plug and play for new and existing soaking systems and can be easily retrofit with existing nozzle technology. For more information, visit www. ves-artex.com.
ANAEROBIC DIGESTER SERVICES
Agricultural Digesters LLC
88 Holland Ln. #302
Williston, VT 05495
802-876-7877
info@AgriculturalDigesters.com
www.AgriculturalDigesters.com
BEDDING SEPARATION
McLanahan
200 Wall Street Hollidaysburg, PA 16648
814-695-9807
sales@mclanahan.com
www.mclanahan.com/solutions/dairy
COATINGS
Industrial Solutions
5115 S. Rolling Green Ave. Ste. 211 Sioux Falls, SD 57108 605-254-6059
www.isusananoclear.com
ENVIRONMENTAL SOLUTIONS
Future Enviroassets LLC
Cincinnati, OH 45215
513-349-3844
LF@futureenviroassets.com
www.futureenviroassets.com
Hall Associates
23 Evergreen Dr. Georgetown, DE 19947-9484
302-855-0723
hallassociates@mediacombb.net
Tomorrow Water
1225 N. Patt St. Anaheim, CA 92801 714-578-0676
info@bkt21.com
tomorrowwater.com
Trident Processes Inc. 10800 Lyndale Ave. S. Bloomington, MN 55420
1-800-799-3740
frank.engel@tridentprocesses.com
www.tridentprocesses.com
MANURE SEPARATION
Boerger LLC
2860 Water Tower Place Chanhassen, MN 55317
844-647-7867
www.boerger.com
MANURE STORAGE
Pit-King®/Agri-King® Inc.
18246 Waller Rd. Fulton, IL 61252
www.agriking.com/pit-king/ 1-800-435-9560
WASTE HANDLING EQUIPMENT
Cornell Pump Co. 16261 SE 130th Ave. Clackamas, OR 97015 503-653-0330
www.cornellpump.com
Doda USA
255 16th St. S. St. James, MN 56081 507-375-5577 dodausa.com
R Braun Inc. 209 N. 4th Ave. St. Nazianz, WI 54232 920-773-2143 www.RBrauninc.com
WASTE HANDLING NUTRIENT SPREADERS
Kuhn North America
P.O. Box 167 Brodhead, WI 53520 Kuhn-usa.com
Oxbo International 100 Bean St. Clear Lake, WI 54005 800-628-6196 oxbo.com
WATER TECHNOLOGY
Bauer North America Inc. 107 Eastwood Rd. Michigan City, IN 46360 800-922-8375
bnasales@bauer-at.com www.bauer-at.com
Press Technology & Mfg. Inc. 1401 Fotler Street Springfield, OH 45504 937-327-0755
dberner@presstechnology.com
Don’t see your company listed? Send your company information to marketing@ jofnm.com with Professional Directory in the subject line.
Midwest Forage Association/ Wisconsin Custom Operators Symposium
February 20 to 22, 2023 Wisconsin Dells, Wis.
Details: midwestforage.org
Minnesota Pork Conference
February 21 and 22, 2023 Mankato, Minn.
Details: mnporkcongress.com
Western Dairy Management Conference
February 27 to March 2, 2023
Reno, Nev.
Details: wdmc.org
Midwest Manure Summit
February 28, 2023
Green Bay, Wis.
Details: midwestmanure.org
Conservation Tillage and Technology Conference
March 14 and 15, 2023
Ada, Ohio
Details: ctc.osu.edu
Professional Dairy Producers of Wisconsin Business Conference
March 15 and 16, 2023
Wisconsin Dells, Wis.
Details: pdpw.org
Midwest Poultry Federation’s PEAK 2023
April 11 to 13, 2023
Minneapolis, Minn.
Details: midwestpoultry.com
Biogas Americas
Annual Conference
May 15 to 18, 2023
Chicago, Ill.
Details: biogasamericas.com
World Pork Expo
June 7 to 9, 2023
Des Moines, Iowa
Details: worldpork.org
If you would like us to include your event on our list, please send details to info@jofnm.com.
Iassumed to have seen everything of importance after 45 years of nutrient management. That changed in 2022. About a decade ago, I assisted a significant client in siting and permitting a fully integrated egg laying farm from scratch. One aspect of site selection included a large isolation radius from other poultry. Biosecurity is always a top priority, but highly pathogenic avian influenza knows no boundaries, and infection was detected in late August 2022.
The state veterinarian confirmed the disease as it spread rapidly through all 15 buildings on this farm. USDA APHIS soon took control for containment and eradication. Their rapid response and expertise were impressive during this critical time.
Every bird was euthanized and removed from the barns. Eggs were disposed of and manure could not leave the premises. Any movement in and out of the farm was under tight biosecurity measures. Transporting 4 million dead hens (weighing 7,000 tons) to a landfill was ruled out because of disease transmission risk during transport. What could be done?
Burial isn’t an option. The high nitrogen content of decomposing carcasses could impact groundwater with nitrate. USDA mandated composting, which can be an effective method of mortality processing. The recipe they specified for compost windrows was one part carbon (ground wood) that formed an 18-inch thick base 17 feet wide, one part carcasses layered on top of this base, four parts manure on top of this, and then an 8-inch cap of wood. The windrow height totaled 8 feet.
Over 100,000 cubic yards of wood was sourced to assemble these piles. A cornfield owned by the farm was harvested for early silage and a neighboring field was rented for the compost operation. In all, 87 compost rows were formed. The total of 38,000 lineal feet was equivalent to 7.2 miles.
The protocol was to turn the piles for two weeks while checking temperatures to ensure proper composting. The piles had to achieve 131°F for at least three consecutive days. USDA brought in subject matter experts to turn and
government thing.
All samples eventually passed, and a mammoth land application effort began. Then an unexpected obstacle emerged: Word on the street was the product was worthless because of the wood. I needed to provide farmers — who desperately depend on manure from the farm to mitigate high fertilizer prices — with data to put that rumor to bed.
monitor the piles. Water was added as needed to keep the optimum moisture for composting.
Then the piles had to sit undisturbed for another two weeks. After this time, the virus was destroyed. Now what?
Once we had USDA “clearance” to move the material, it came under EPA regulations to meet Class II compost specifications. After that, it could be land applied under the farm’s state permit conditions.
We sampled each windrow for salmonella, fecal coliform, 503 metals, and other compost parameters. Raw manure can be spread on the same farm ground for the same farmers with just an N-P-K test, but once it’s “compost,” we have different criteria. It’s a
It was intuitive that the compost should be very similar to manure analysis, since it was over 80% manure (including nutrient-rich birds). Breaking into the piles, there was no evidence of carcasses. I compared historical manure samples with compost samples and confirmed that the compost had at least 90% the nutrient value of manure. The compost was discounted and all sold accordingly. Turning liabilities into assets has been a focal point of my career.
Barns were disinfected and tested absent of the virus in November. Hens have begun laying eggs again since early December. We pray to never repeat this situation, but the reality is that it could happen all over tomorrow. ■
I needed to provide farmers — who desperately depend on manure from the farm to mitigate high fertilizer prices — data to put that rumor to bed.
Sand bedding is ideal for dairy cows, but it doesn’t always mix well with manure management systems. This is especially true with anaerobic digesters. However, well-designed, robust sand-manure separation systems are proven to help recycle sand bedding efficiently and economically, enabling users to recoup and recycle the vast majority of sand. Plus, these sand separation systems can also increase anaerobic digestion utilization by virtually eliminating sand from the digester-feeding manure stream.
Here’s how you can create a favorable manure management environment with sand bedding on your dairy farm, even if you don’t have a digester yet.
“Sand is the gold-standard bedding choice because of its cow health and milk production benefits,” says Renee Schrift, Business Line Director – Agricultural Systems at McLanahan Corporation. “It has so many advantages because it’s a forgiving, drier, comfortable surface for cows, and it’s inorganic, so the stall bacteria load is usually extremely low.”
According to researchers at the University of Wisconsin and USDA, the use of sand bedding compared to manure solids and mattresses results in higher milk production, lower mastitis treatment rates and lower somatic cell count.
Using sand bedding isn’t necessarily difficult, it is simply different to manage than using organic bedding.
How do you optimize the benefits of sand bedding while reducing challenges for manure handling systems? Separate and recycle it, of course.
“Success begins with capitalizing on physics, gravity and engineering know-how,” explains Schrift.
Keep in mind:
• Sand is abrasive, so choose equipment designed and proven to withstand the harshness of sand. This means equipment that operates at low speeds and is constructed using wear-resistant materials like abrasion-resistant steel plate or rubber. Components in high-wear situations must either be harder than sand grains or resilient enough to deflect without deforming.
• Secondly, sand is more than twice as dense as manure and therefore settles, making sand separation a realistic proposition.
“In fact, our systems can capture 95% of sand for recycling while removing an additional 3% of fines from manure,” Schrift adds.
As a result, dairies that recycle sand can cut their bedding cost significantly. For example, a 500-cow dairy using 50 pounds of sand per cow per day at $15 a ton spends $68,438 a year on sand. With a sand separation system that conservatively recovers up to 90% of sand for reuse, the dairy can save $61,594 a year by recycling their sand bedding.
These figures demonstrate that with a well-designed sand-manure separation system, high sand recovery is possible and economically beneficial for herds of all sizes.
Since sand separation technology can virtually remove most sand from manure, these systems go hand-in-hand with anaerobic digesters.
Without separation beforehand, sand bedding is incompatible with anaerobic digestion systems.
With sand-manure separation, sand can be recycled for reuse as freestall bedding, and the manure effluent can be anaerobically digested for optimal digester efficiency and gas production.
The key is to collaborate with your partners to design the best system to fit your needs. Also, every farm is managed differently, so it’s important to determine the total solids in manure effluent, knowing there may be seasonal fluctuations.
“Be sure to choose an anaerobic digester partner who can design and build a digester to suit the way you manage your dairy, taking into consideration first and foremost what is best for the cows,” suggests Schrift.
Ultimately, effective sand recycling helps improve a dairy’s bottom line, whether you invest in a digester for your system or not.
There’s more value in that manure than you may think. Containing a proprietary enzyme blend, microorganisms, co-factors and a patented Bacillus strain, Pit-King’s enzymes quickly break down undigested manure solids, while its unique microorganism combination continues manure solid decomposition and also helps reduce compounds like ammonia.
After 60 days, an on-farm trial showed Pit-King® treated manure featured less solids content, lower levels of ammonia and greater amounts of molecular nitrogen without altering overall mineral composition, resulting in less volatile manure that is also more pumpable.
Want to learn more about how Pit-King® can help your operation?
Pit-king