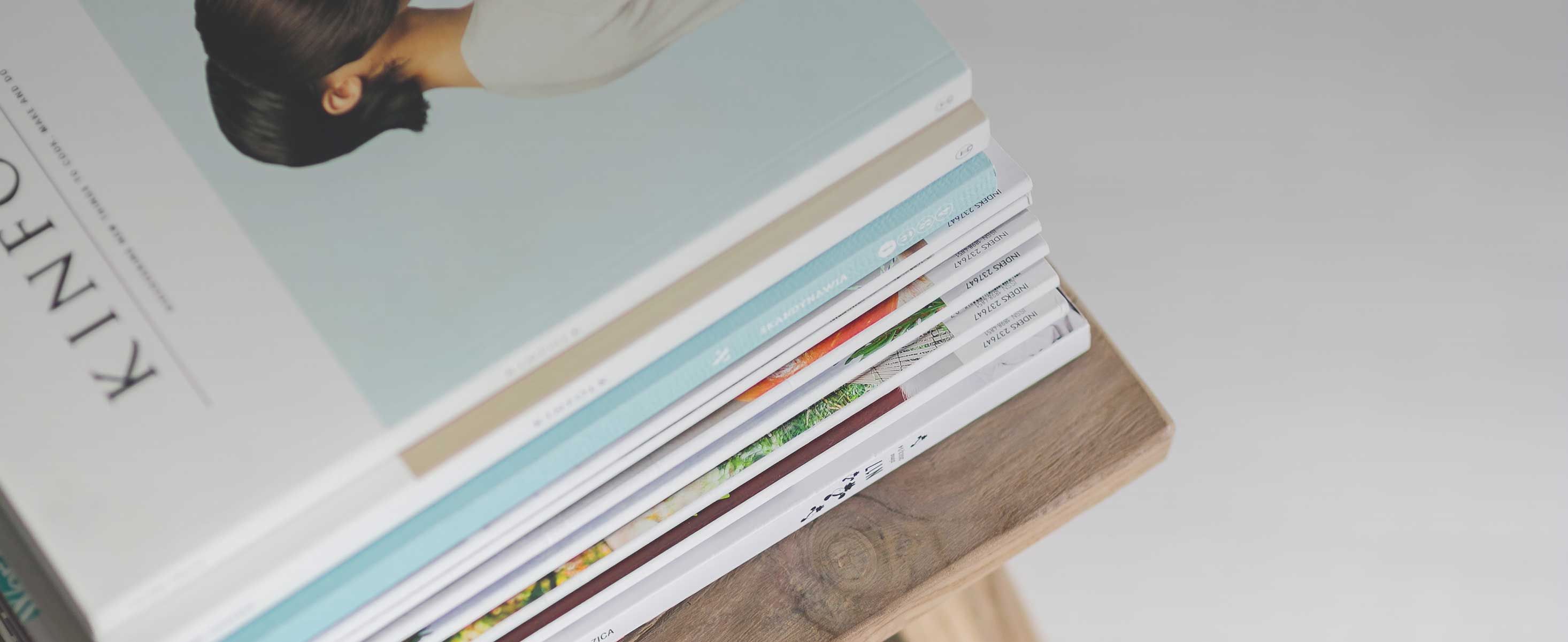
5 minute read
THE CENTRALIZED LUBRICATING SYSTEM
Construction
Your machine is fitted with three centralized lubricating devices, allowing to reduce to a minimum the time which is necessary for the daily lubrication.
These devices function automatically and ensure a cycle of lubrication of the three circuits every two hours (factory setting).
the lube pump 1 mounted to the left front of the hydraulic tank ensures lubrication of the swing ring teeth.
the lube pump 2 mounted to the right front of the hydraulic tank ensures lubrication of the swing ring roller races and of the bearing points of the working attachment.
the lube pump 3 mounted to the rear of the undercarriage (visible after removing the protective covering) ensures lubrication of the undercarriage (fig. 34).
Each lube pump consists of a transparent container, an electric driven pump and a control unit integrated in the lower part of the pump which starts and stops the lubricating procedures.
During a lubricating procedure, all lube points are lubricated, via a combination of progressive metering devices, in a certain sequence.
After completion of a lubrication procedure, the switch mounted to the exit for the last lube point (fig. 35, pos.?6) automatically turns off the pump.
Localization of the proximity switches for lubrication cycle end:
The proximity switch for lube pump 1 is installed on the metering device on the side of the hydraulic tank
The proximity switch for lube pump 2 is installed on the metering device on the side of the fuel tank.
The proximity switch for lube pump 2 is installed on the metering device on the inner face of the right frame of the bogey, common to the two rear axles (fig. 38).
The flow sequence and amount of lubricant for each lubrication point depend on the combination of the metering devices and lubrication lines.
Operation
A housing around the pinion of the swing gear contains all the necessary lubrication reserves for the swing ring teeth lubrication (fig. 33, pos. 7).
During operation, the lubricating pump 1 attached to the hydraulic tank turns on automatically and at regular intervals to replace this reserve.
Notice The centring of the swing gear inside the upper structure is lubricated simultaneously with the swing ring teeth. A grease distributor mounted below the lubrication unit to the hydraulic tank ensures the right repartition of the grease quantities to the swing ring teeth and to the gear seat.
Working Attachment
All the lubrication points for the swing ring roller races (metering device pos. 22) and for the working attachment are connected to the automatic lubricating system 2 and are greased at regular intervals while working.
Only some bearings in the area of the digging tool may need to be greased manually (depending on the type of the bucket or of the grab).
Caution
When operating a machine fitted with special working attachment or tool, make sure to know all the lube points that are not connected to automatic lubrication system and that these points are greased by hand daily.
All the bearing points of the undercarriage (axles/bogeys, bogeys/undercarriage, bogeys/oscillating axle and oscillating axle/undercarriage), as well as the steering elements (pivots, foot and head for steering cylinder) are greased by the lube pump P3 via the different metering devices which are mounted to the structure of the undercarriage.
Note: the other bearings or ball joints are lubricated for life..
Operation And Monitoring Of The Lube Systems
Without any action by the operator, each lube pump automatically restarts lubricating after the a pre - adjusted "pause time" is over and stops after all points are lubricated.
When the lube pump 1 (resp. the lube pump 2 or 3) is greasing, the control light inside the push button S84-1 resp. S84-2 or S 84-3(fig. 39) is on continuously
The blinking of a control light S84 indicates that the corresponding lubrication circuit is defective (lubricating procedure did not stop after approx. one hour).
Possible causes:
Plugged or kinked lubrication line.
Defective switch or defective wire.
Not enough grease in the grease tank.
Problem in the 24 V electrical circuit for the motor. Immediately locate and remedy the cause of the trouble.
If the lubrication system is in working order, an additional lubricating procedure of each lube pump can be started any time by depressing the corresponding push button S84 for about 2 seconds.
Adjustment of the pause time PT
The pause time between two lubricating procedures can be adjusted, after removal of the protection cover 17 (fig. 41) and by turning the selector TS or moving the bridge HM (see fig. 42), so to obtain the desired "pause time" PT shown in following schedule
At factory, the pause time for the lube pump 1 had been adjusted to 4 minutes.
At factory, the pause time for the lube pump 2 had been adjusted to 2 hours.
At factory, the pause time for the lube pump 3 had been adjusted to 2 hours.
Grease consumption
At every stroke of a working piston in a metering device, 0.2 cm3 of lubricant are delivered..
With the pause time adjusted as factory delivered, this corresponds to a grease consumption of about 1.5 kg (3.3 lbs) for lube pump 1 and of 1.5 kg (3.3 lbs) for lube pump 2, every 100 working hours.
Safety lubrication
In case the lubrication pump does not work, all lubrication points connected to the centralized system may be lubricated via the lube fittings 8.1 and 8.2 (fig. 44) and using a grease gun.
Once a day or, if applying, once a working shift, connect a lubrication gun to these fittings and press about 150 cm3 of grease into the fitting 8.2 for the swing ring teeth lubrication, and about 150 cm3 of grease into the fitting 8.1 for all remaining lubrication points.
To Refill The Grease Containers
For lube pumps 1 and 2 see figures 45 and 46
For lube pump 3 see figure 47.
The grease level in the container of each pump must be checked weekly, and if necessary, the container refilled. For grease specifications, refer to lubricant chart.
Caution
Since the both lubrication pumps 1 and 2 are filled with grease according to different specifications, it is essential to notice, for refilling, that the outer pump 2 is for swing ring teeth, and the pump 1 situated most inside is for the centralized lubrication of the attachment bearings! However the lube pumps 1 and 3 contain the same grease.
The refilling of the grease tank 1 and 3 should only be done via the special fittings 14.1 respectively. 14.3.
Insert a grease cartridge in the special filling pump 16.1 (Id. No. 5608704), connect the pump to the fitting 14.1 / 14.3 and push the whole content of the cartridge into the container (fig. 46 and 47) .
The refilling of the grease tank 2 should only be done via the special fitting 14.2.
Insert a grease cartridge in the special filling pump 16.2 with label for swing gear teeth, connect the pump to the fitting 14.2 and push the whole content of the cartridge into the container (fig. 46).
Avoid refilling via the upper tank cover 5, since it could create an air pocket in the container and cause the pump to run dry
The order number for the different grease cartridges for general lubrication points and swing ring teeth are indicated on page 5.9.
Without the special filling pumps or grease cartridges, the tanks of the pump 1 and 2 have to be refilled through the grease fitting 18 (fig. 48), resp. the tank of the pump P3 via the grease fitting 18.3 (fig. 47) using a grease gun.
At each refilling of the grease tank, or every 1000 working hours, remove the plugs 19.1 and 19.2, check the filtering screens situated under these plugs for cleanliness and if necessary clean them (fig.45 and 49).
Changes In The Lubrication Circuit
Before you make any changes to the lubrication system (for example when changing the attachment configuration), always check with a LIEBHERR mechanic first
Never close off a line, which is not being used.
Only plug a line after the line has been removed on the outlet of the metering device. Only use plug (Id. No. 7011340) and seals (Id. No. 7011344)!
Do not close off the outlets 1 and 2 of a metering device, or the whole lubrication system would be blocked.