Hazel 4d Case studies
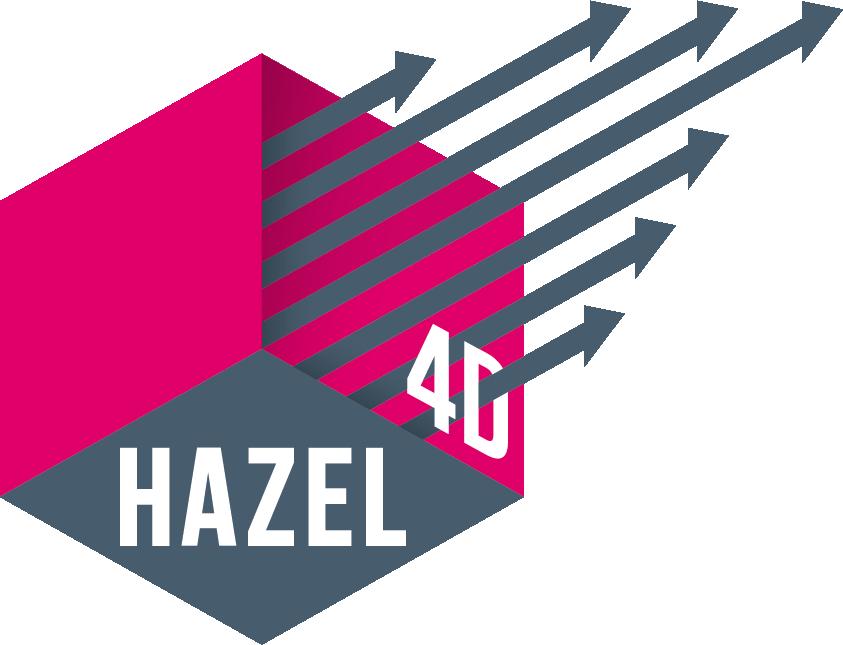
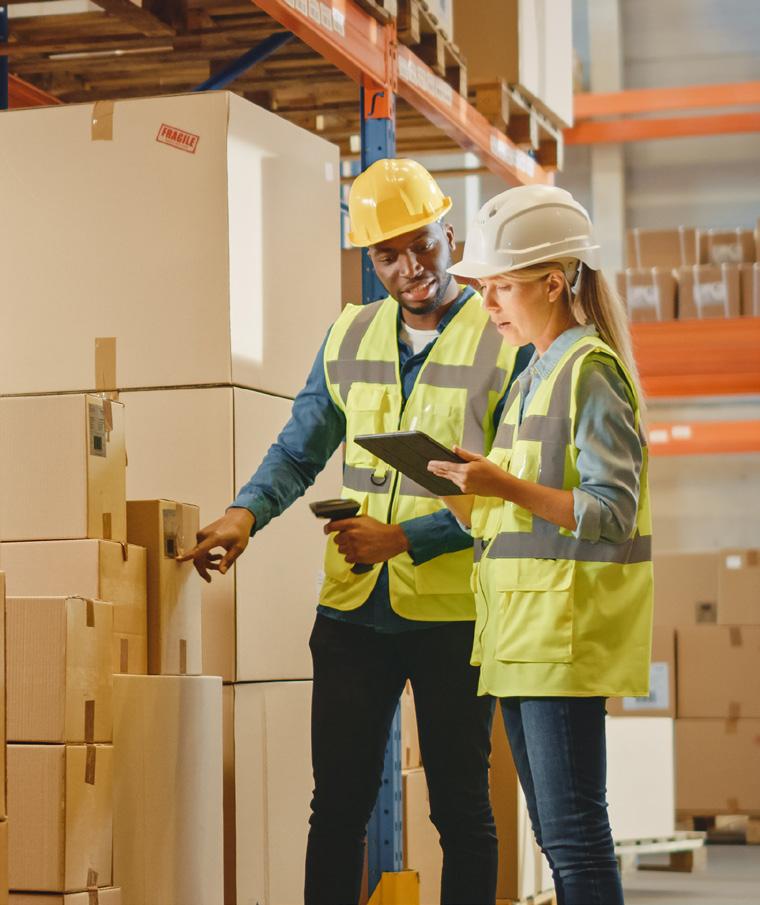
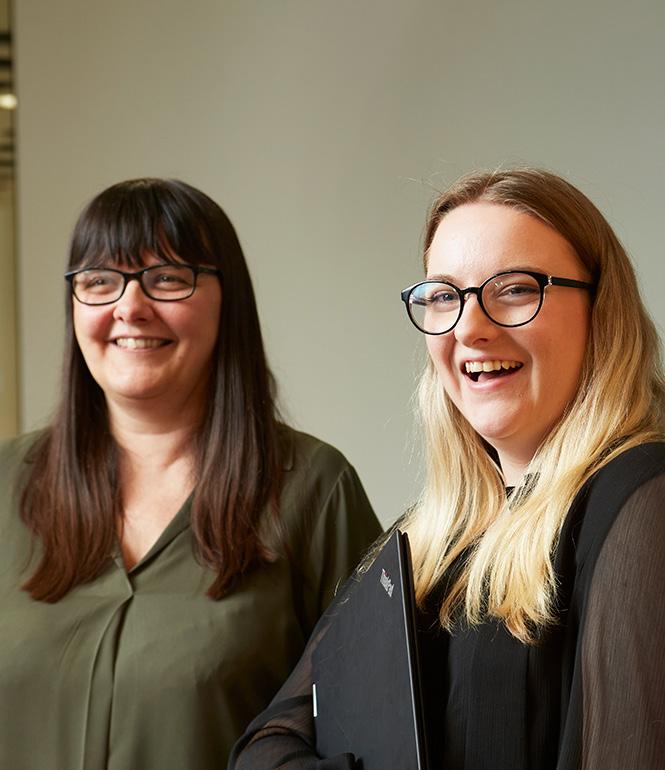
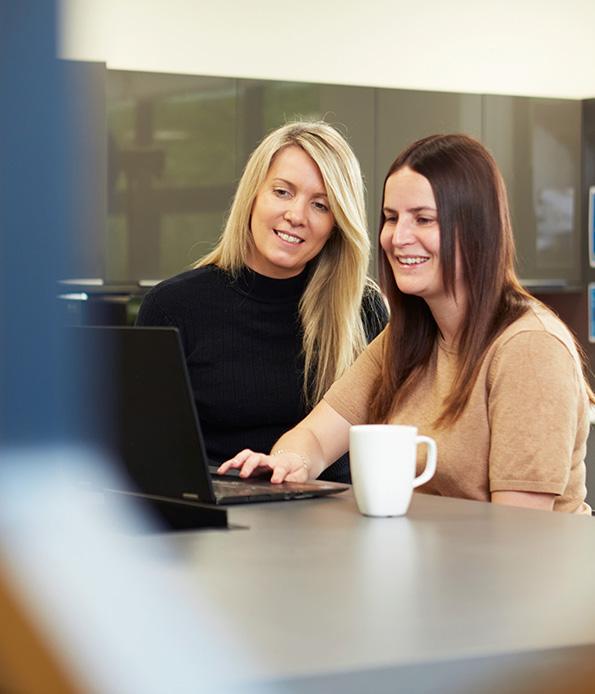
WE’RE NOT YOUR AVERAGE PACKAGING SUPPLIER.
WE’RE YOUR specialist packaging partner.
1. Morrisons…Net Zero Eggs
Transitioning to sustainable packaging
2. Banner…EVOlving Stability
Optimising the pallet wrapping process
3. Britvic…Bottling Success
Picking the right processes to minimise waste
4. Essentra…Essential Improvement
Introducing automation in box packing
5. Tayto...The Golden Touch
Guaranteeing stability in transit
6. Waterstones...a new chapter adding flexibility & capacity
Scan the QR code to See it in action
Improving efficiency and safety in the warehouse
As experts in transitioning to sustainable packaging, Hazel 4D worked with established partner Morrisons and their Chippindale egg factory to deliver an effective packaging solution with improved environmental credentials.
As a long-term customer looked to become the first UK supermarket to bring carbon neutral eggs to the market, product packaging was the final hurdle to overcome. Traditionally, outer cartons at the Chippindale eggs factory were always glued or taped, adding plastic content to the product packaging that conflicted with the environmental focus of the project.
As with most new product lines, forecast volumes weren’t clear and so the need for the solution to work with existing machinery and avoid capital investment were key deliverables.
Hazel 4D Our self-adhesive paper machine tape was able to run very successfully on their existing automatic tape machinery. 100% recyclable and biodegradable.
We also provided the equivalent product in a hand tape version, along with free premium tape dispensers, for use when any manual taping was needing to be done.
The customer achieved on brand eco-friendly packaging and were able to deliver ‘planet friendly’ eggs.
Morrisons’ Packaging Advisor said “This new product launch went into our Yorkshire stores today, hopefully you will see some media engagement over the next few days as we are very proud to be the first supermarket to be able to offer net zero ‘Planet Friendly’ eggs on such a scale.
The tape used to seal the boxes finishes off the whole project nicely so hopefully customers will appreciate these eggs...”
delivering the 4 th dimension
£0 No capital costs
100% Recyclable okg No plastic
Experts in workplace supplies, Banner looked to us to help optimise their pallet wrapping process. When we first visited the customer their pay-per-wrap contract was almost up – the ideal time for us to step in to improve load stability whilst also reducing costs and plastic usage.
A lack of clarity in the pricing structure meant that Banner had inconsistent pallet wrapping prices with costs varying from 40p – 80p with little transparency or reporting capabilities.
The wrapping machines in use were only stretching the film around 200% resulting in a higher plastic consumption than necessary. Despatch operators were manually adding weight labels to the pallets by individually weighing the pallet on standalone scales and then writing the weight on a despatch label.
Our Solution
We replaced all the existing machines with our ultra highperformance wrapping machines and Extremus film. The pallet wrap can now be stretched to an incredible 300%, from a previous 200%, resulting in an immediate reduction of plastic usage per pallet to just 93 grams and a saving of over 35%.
The two new Atlanta turntable pallet wrapping machines include fully integrated weighing scales with linked label printers so that weight labelling is now as simple as a press of a button; increasing efficiency and accuracy and removing manual tasks.
We provide clear reporting on all packaging costs, including the pay per wrap cost, every month. The simple, transparent structure allows for one price for despatch machines and one for all the rest.
delivering the 4 th dimension
300% Material stretch
93g Fully recyclable plastic per pallet
35% Plastic reduction
24/7 Performance monitoring
A soft drinks manufacturer was generating huge amounts of plastic waste and experiencing high labour costs due to an inefficient pallet wrapping system.
By working with Hazel 4D to conduct film trials and testing they were able to pinpoint the problems and find cost-effective solutions that drove drive valuable improvements.
Three turntable wrapping machines had been poorly set up with inefficient programs, resulting in frequent film snappages. Operators were having to compensate for these snappages by overwrapping by hand whilst the turntable machine was in motion!! This doubled the amount of film used per pallet whilst also increasing labour costs and leading to H&S issues.
A backlog of pallets from the wrapping machines led to many being wrapped by “hand only”, a labour intensive exercise with a far longer wrap time of around 3 minutes per pallet.
The loads were also being wrapped too low onto the pallets, which was resulting in the film being pierced or split by forklift trucks, thus creating significant weak spots in the pallet wrap.
The customer was actively reducing the grade of material in their primary and secondary packaging, which had also had a detrimental effect on the overall stability of the pallets. Better wrapping programs were required to compensate for this.
Through extensive trials, Hazel 4D were able to demonstrate a significant improvement in load containment force (stability) and a far more consistent wrapping sequence. This was a result of switching to high performance Extremus NANO15 film, reconfiguring the wrapping program and making some minor mechanical upgrades to one of the machines.
Improved stability of pallets
Over 2 min of operator time saved per pallet wrapped
Almost double the number of pallets wrapped per roll of film, saving on machine downtime and plastic wastage
Reduced cost (and plastic tax) by
59% per pallet wrapped
Annual cost saving of approx
65% Reduced weight of plastic by £169,000
We started working with Hazel 4D at one of our co-packing facilities and we very much appreciated their support. They were able to quickly highlight the weak points in some of our pallet formats and they not only recommended alternative materials to use but also advised on stretch wrap program set up. Their intervention helped to reduce material usage and to eliminate returned loads from customers.
A leading producer of carton and leaflet packaging for the pharmaceutical, healthcare and personal care sectors. With it’s state of the art production facilities they manufacture high quality cartons for many of the leading brands.
With its automated manufacturing lines running smoothly the next challenge was to increase the possible throughput to make the whole operation more efficient. However, with the operators having to manually form and tape the cartons before filling them with product, this was not possible.
A decision was made to invest in some simple carton erecting automation to provide ready cartons on demand. The Comarme F2000 system was chosen because of its compact footprint and flexibility to produce the full range of cartons used at the desired throughput.
Essentra’s Production Manager said “Its really a no brainer! The machines are paying for themselves in less than 6 months and means that our skilled operators can spend the time they need ensuring the production is of the highest quality and maximising throughput. We always thought it would be a bit of a struggle to fit this equipment in but we were pleasantly surprised with how little space is actually required for it.”
delivering
Increased production speed by 5000 units per hour
5% reduction in overtime costs across the whole line
Less operator fatigue and repetitive strain injury prevention
Consistently taped boxes eliminating damage to product
Its really a no brainer!
Payback in less than
6 months
The machines are paying for themselves in less than 6 months.
Production Manager
A food manufacturer was incurring excessive financial and operational costs due to ineffective stretch wrapping processes. The company was spending around £150,000 annually on stretch film, using 100 tonnes of plastic film and spending time and money repairing old machines.
Worn, damaged wrapping machines were causing stretch film to break and meant wrapped pallets were extremely unstable. The machines were unable to keep up with production during peak periods which resulted in bottlenecks and downtime.
Large supermarket chains were rejecting and returning damaged and leaning shipments, so warehouse operatives were spending a significant amount of time rewrapping pallets. The frustrated operatives were loading the stretch film incorrectly in an attempt to prevent film breakages and keep the machines wrapping. Their Warehouse Manager repeatedly commented ‘my guys deserve better’. The problem was costing them money, time and their reputation.
We audited their current machinery, testing for correct setup and each machine’s ability to stretch film and apply it in the most efficient manner. We then measured the amount of film used to wrap each pallet, the performance of the film, its strength and the amount wasted due to quality and poor machine set-up. Finally, we monitored the standard of pallet wrapping and listened to machine operators talk through the process and the practical difficulties faced when preparing pallets for transit.
We recommended making the switch to Extremus film and new state of the art turntable pallet wrappers, which when optimised could deliver up to 300% stretch. We created two bespoke wrapping programmes to suit their needs, whilst using the minimum volume of stretch film. Due to the combination of film and equipment used, the ROI on the new machines was less than 7 months. Careful training and ongoing contact as part of the maintenance contract with the team at Hazel 4D meant that the operations team was confident in using the system, and that savings were realised on an ongoing basis and the team could call Hazel 4D with any issues.
Huge, ongoing cost savings of 65% Reduced plastic waste by Reduced production downtime improved stability of pallets
£100,000 per year
More pallets wrapped per day
no film breakages reduced need for roll changovers
Not a single pallet has been returned from our customers.
Why didn’t we do this years ago!
Distribution manager
Hazel 4D was approached by Unipart Logistics & Waterstones to optimise and improve their packaging processes and product choices across their whole range of operations. The key focus areas were increasing automation, reducing plastic usage, and improving sustainability.
Through our consultative review, we quickly identified one major bottleneck in the packing process. At the end-of-line packing area several operators were manually erecting and sealing the bottom of boxes ready for packing. This process was time-consuming and was being further impacted during peak demand by ongoing labour shortages in the UK. Waterstones needed a solution that would not only address these issues but also help them stay competitive and responsive in a rapidly changing market.
To meet these challenges, we specified certain options from our range of Comarme automated machinery. This collection of cutting-edge automatic carton erecting and sealing equipment prepares boxes with folded bottom flaps, which are then closed with adhesive tape. With the ability to be easily adjusted to run other box sizes, it is a highly efficient and versatile solution, making it a perfect fit for Waterstones. Throughput was immediately increased with the additional capacity reaping rewards during increased sales.
One of the biggest advantages of increasing automation is the optimised and consistent use of consumables. Just by switching to a bottom case sealer, the first stage in this automation transition, we have removed 345392.58 meters of tape from their operation by stopping over taping at the bottom of the boxes, 214 miles of plastic gone.
delivering the 4 th dimension
<6 months ROI
214 miles of plastic tape saved
80 hours weekly labour savings
Working with Hazel 4D has been a game-changer for our packing operations. The implementation of automation has greatly improved efficiency and helped us in our progress towards our sustainability goals. We are thrilled with the immediacy of positive results and the significant gains we are already seeing. We would highly recommend Hazel 4D to any company looking to optimise their packing processes.