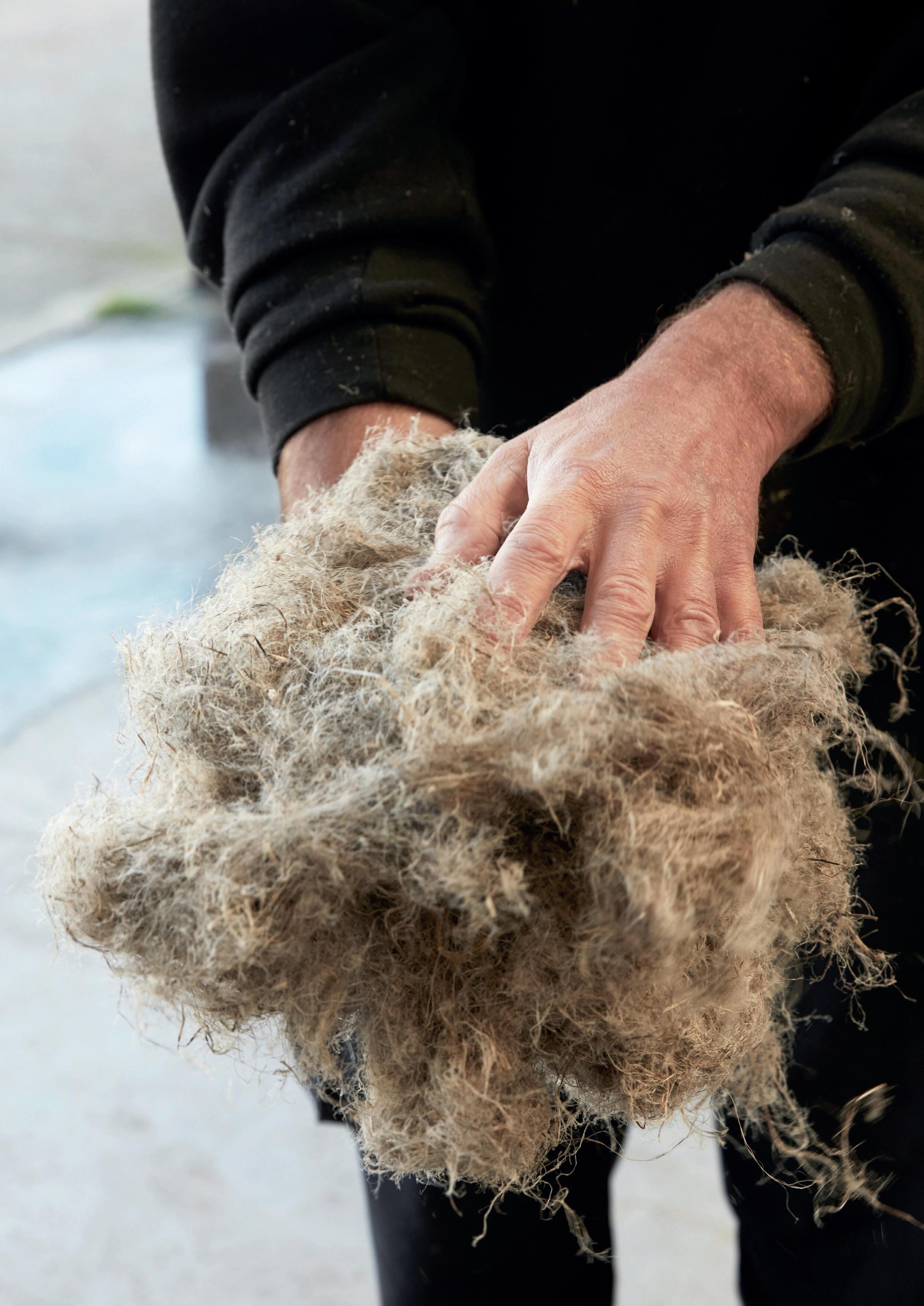
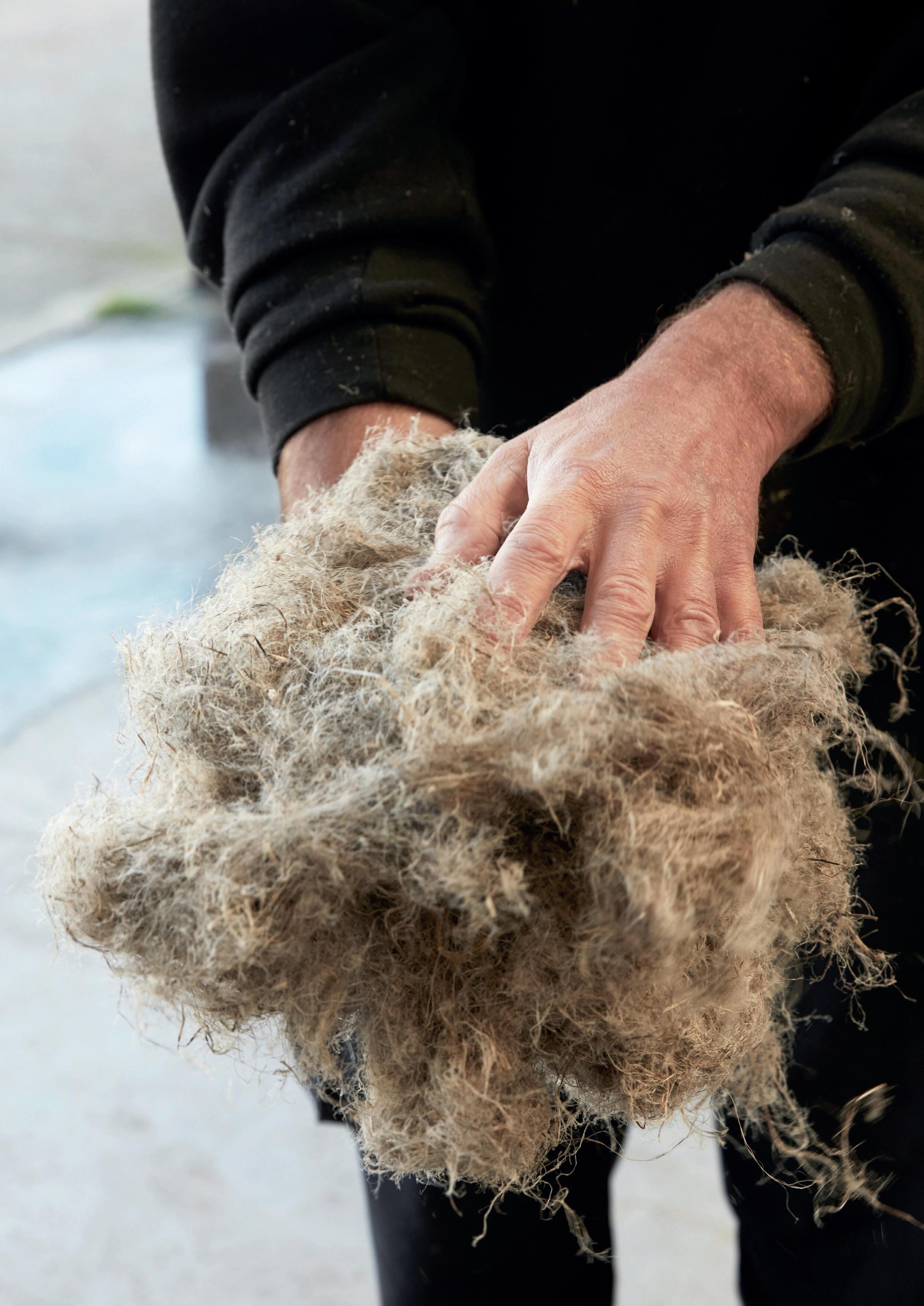
Impact Report 2024
Our intentions and progress to date

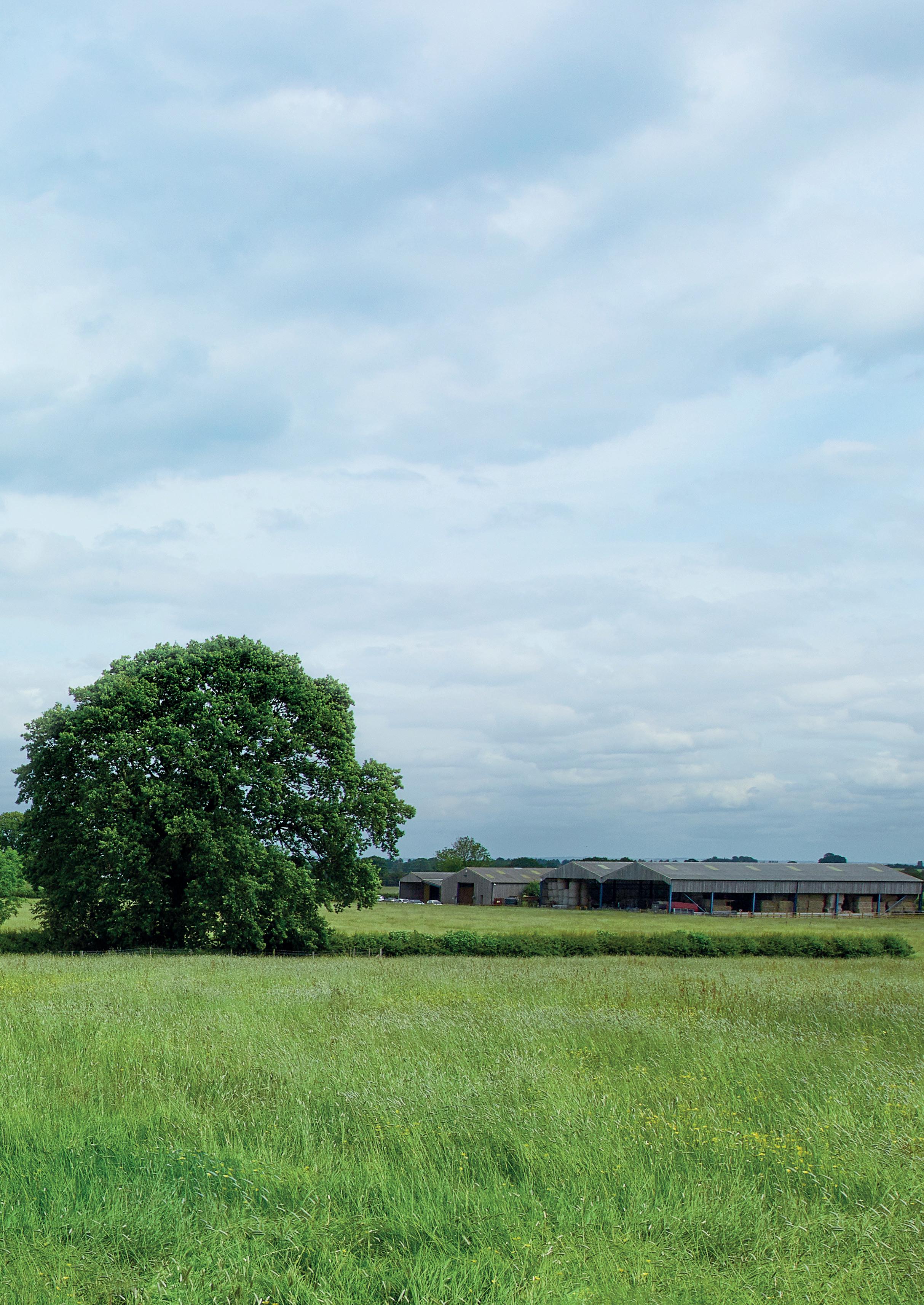
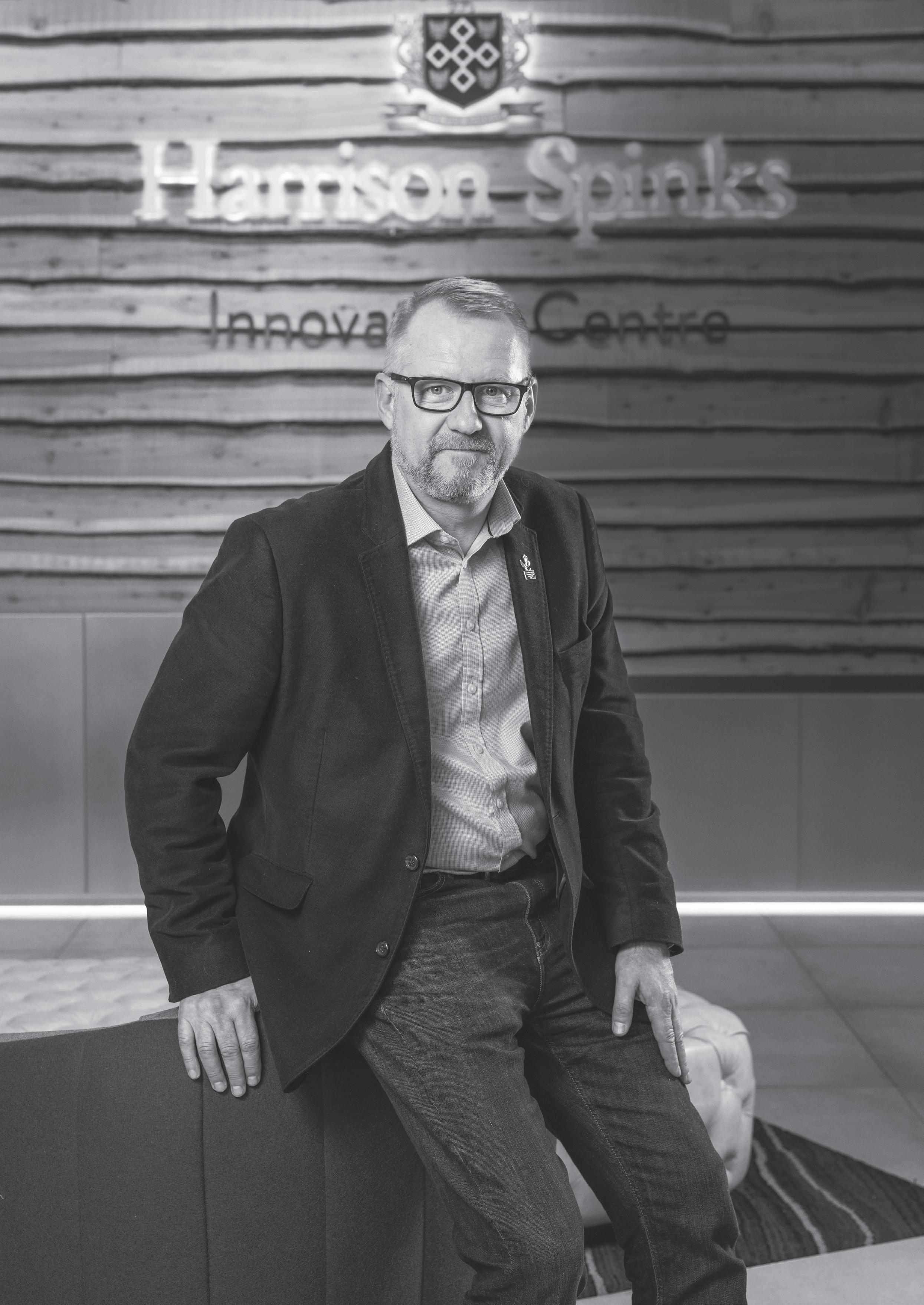
We are a family business that’s proud to say we’re cut from a different cloth.
We pride ourselves on doing things the right and responsible way. Even if it’s not always the most conventional. And in today’s world, we believe this is more valuable and more important than ever.
As we look ahead, we’ve been working hard on our long term sustainability roadmap and this, our Impact Report, shows how we’re making a fundamental commitment to deliver what’s important to us.
Taking the steps towards net zero. Tackling waste in innovative ways. Becoming nature net positive. And helping our colleagues and communities thrive.
We all know there’s a huge amount of work to do. But there’s an equally big appetite from everyone here to show how our industry can be a force for good.
I’m proud of all we’ve achieved to date and honoured that our business has been recognised with eight King’s and Queen’s Awards to date. But this is just the start. Together, playing our part in making the world happier and healthier is what gets us out of bed each and every day.
Simon Spinks Group ChairmanOur purpose
We are committed to turning our purpose into meaningful actions. Staying true to our unique approach and all the time thinking how we contribute to the sustainability of our planet and society.
In the last year, we have taken time to consolidate and reflect. Discovering where we can create the most value. This has allowed us to define our plans for the future with an increased level of certainty and confidence.
We all achieve more when we work as one. Our people, our retail and industry partners, and our customers.
Together, we are passionate creating a happier
We don’t wait for others to show us the right way. We lead the way and are creative, innovative and always looking for new and better ways of working.
Looking ahead, our focus is to:
• Address how we respond to the climate crisis through climate change adaptation and reducing our energy and material consumption.
• Continue to develop our responsible sourcing model to ensure our supply chain is as ethical as possible and to further reduce reliance on virgin materials.
• Continue our innovation in mattress and spring development, including industry-first approaches to product and component circularity. Designing and manufacturing with the goal of making each material usable again and again.
• Support our people and our community to thrive in uncertain times.
• Deliver a strategic shift away from overseas carbon offsetting, instead making a real and lasting difference locally.
We’re a fifth-generation family-owned business with a heartfelt belief in manufacturing in the right and responsible way.
passionate about and healthier world
When we do things right, great things happen. And that goes beyond making people feel comfortable. Our impact has the potential to reach so many.
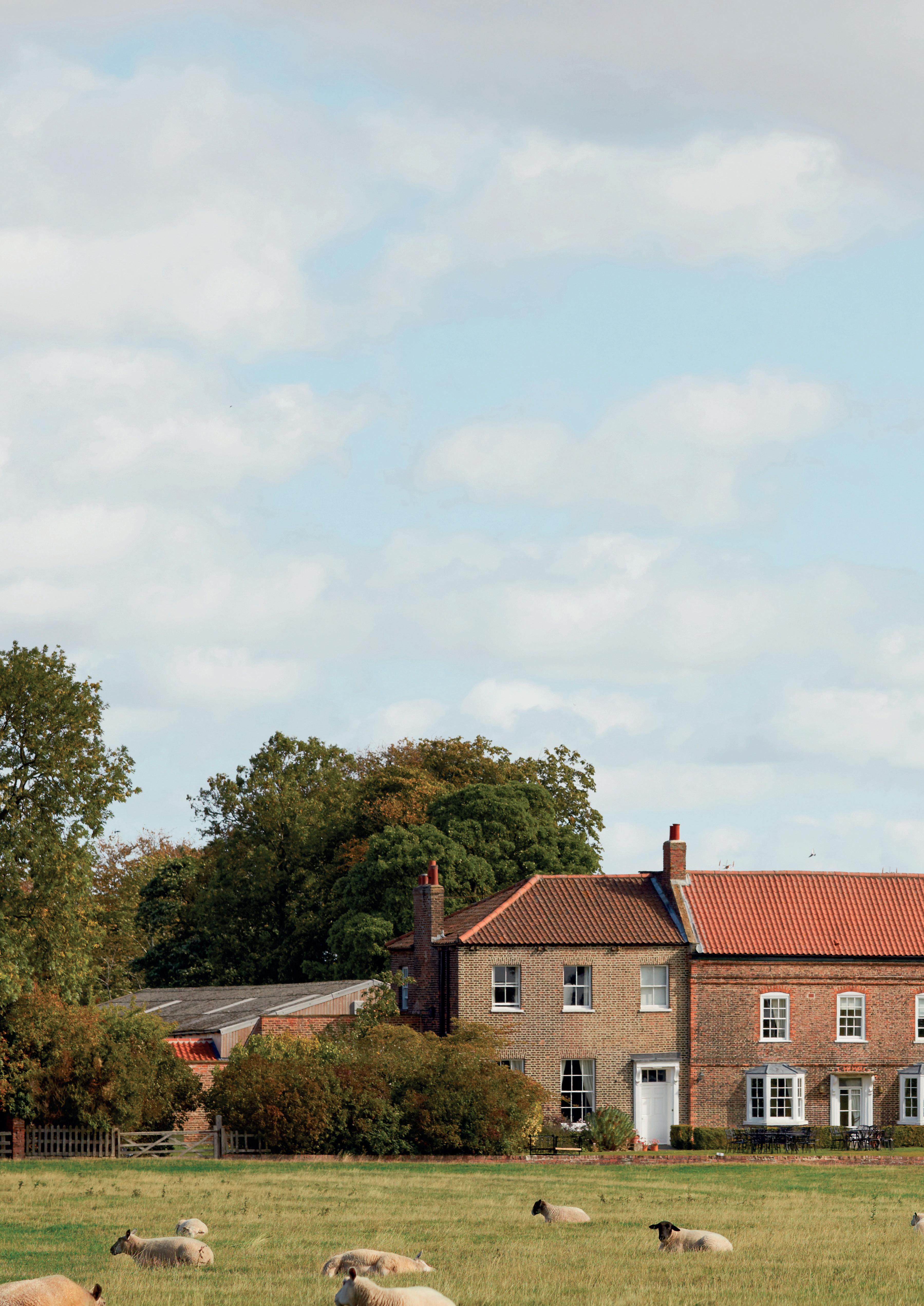
Doing things the right way
We’ve worked hard to foster a business-wide approach to sustainability. Making it front of mind from boardroom to factory floor.
Made locally, with a global outlook
We are a business that’s proud of our Yorkshire roots. The only UK bedmaker with our own farms, we have a unique connection with the land and our community. We feel the most effective way to make a positive difference locally is by taking a global view. It’s why we are proud members of the UN Global Compact.
UN Global Compact
The world’s largest corporate sustainability initiative, this is a voluntary programme run by the UN to realise 17 global goals in sustainability.
As a signatory, we annually monitor our progress and use the UN Sustainable Development Goals to help guide our sustainability strategy.
We have chosen 9 of the 17 goals to focus our efforts on as these represent the greatest impact on our business, colleagues and community.
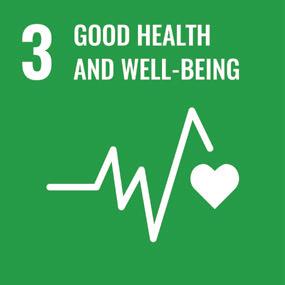
Ensure healthy lives and promote wellbeing for all at all ages
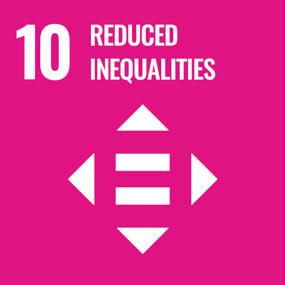
Reduce inequality within and among countries

Strengthen the means of implementation and revitalize the global partnership for sustainable development
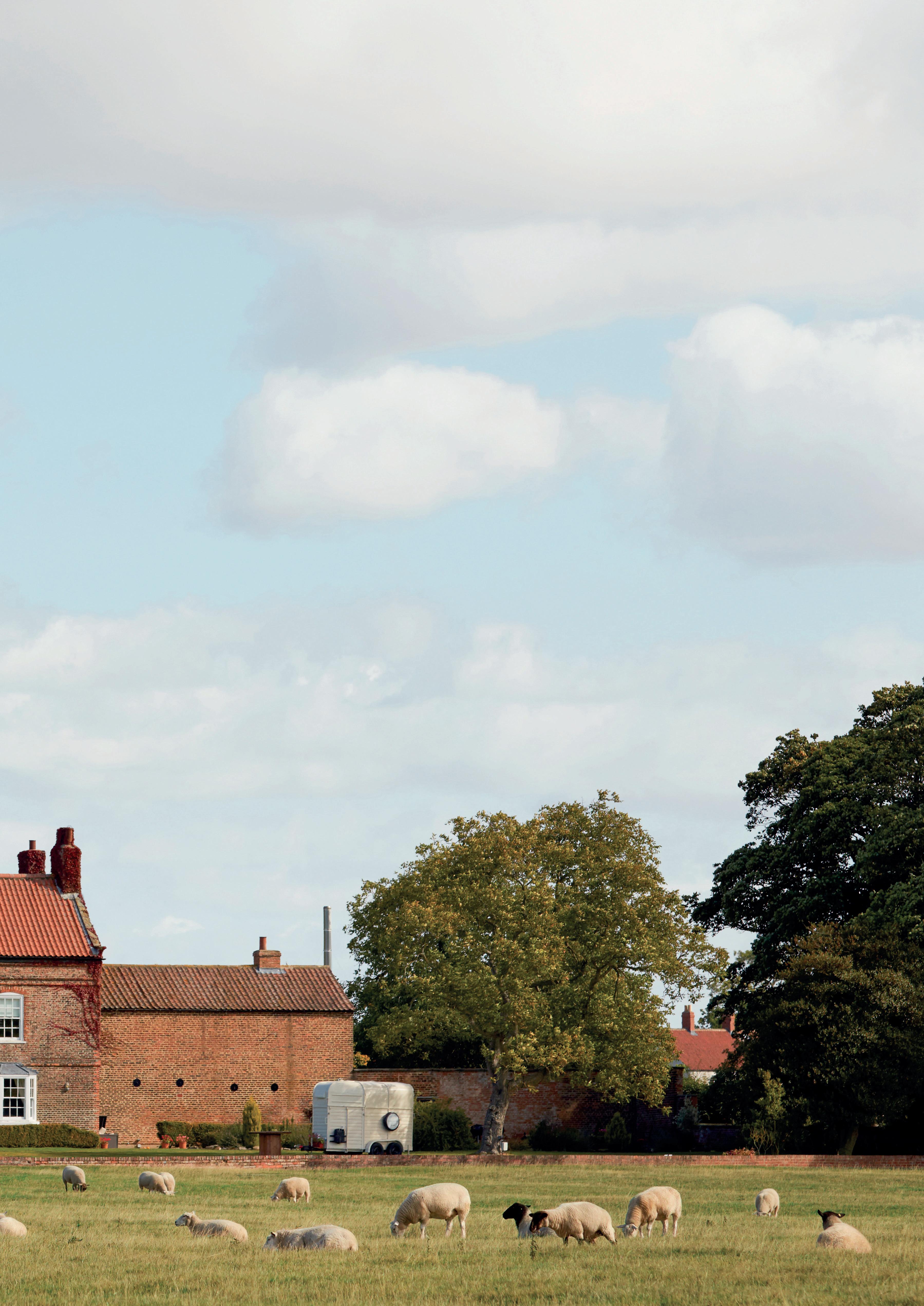

Achieve gender equality and empower all women and girls
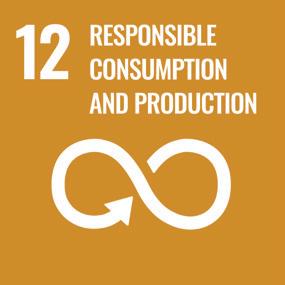
Ensure sustainable consumption and production patterns
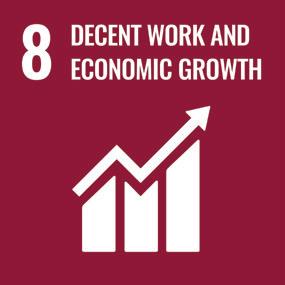
Promote sustained, inclusive and sustainable economic growth, full and productive employment and decent work for all
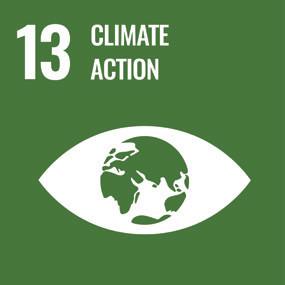
Take urgent action to combat climate change and its impacts
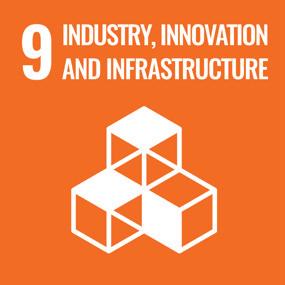
Build resilient infrastructure, promote inclusive and sustainable industrialization and foster innovation

Protect, restore and promote sustainable use of terrestrial ecosystems, sustainably manage forests, combat desertification, and halt and reverse land degradation and halt biodiversity loss
Our Sustainability Steering Group
It’s important we hold ourselves to account. We do this with the help of our steering group.
Led by our Non-Executive Director, Dr Louise Ellis-Jones, and our Sustainability Team, with representatives from all departments, the steering group creates a space for new ideas and for us to challenge the way we work.
The Sustainability Steering Group is accountable to our Board of Directors, who are ultimately responsible for making sure our operations align with our purpose and commitment to sustainability.
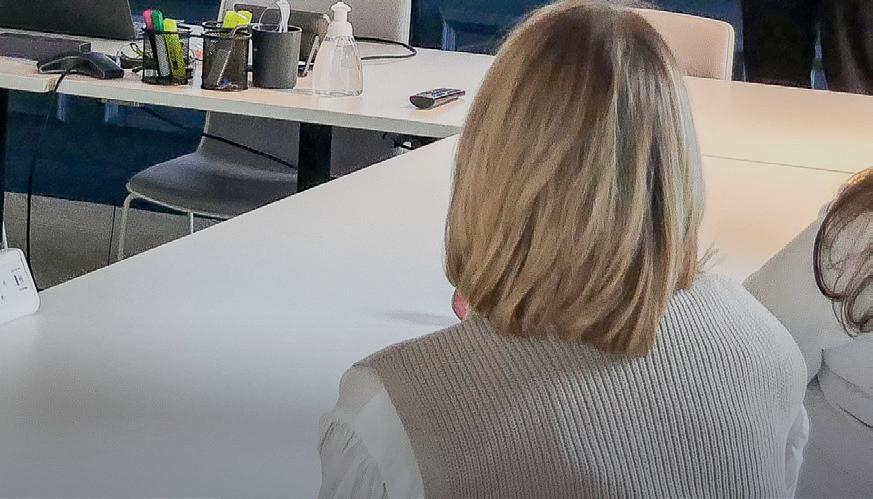



Reinforcing our foundations
1. Policy review
We have committed to a rolling policy review of all our processes, ensuring the foundations of our business reflect our current commitments and the ever-changing world.
2. Building our capacity
We truly believe everyone has a role to play in creating a happier and healthier world. We are making sure everyone has the tools, knowledge and confidence to make decisions and innovate.
3. Director engagement
We have always been a business that values and invests in sustainability. To empower the key decision-makers in the business, the Directors work closely with our in-house Sustainability Team to make sure the impact of the business is understood at all times.
4. Dispersed leadership
We have amazing people across our business who are experts in what they do. These key people own and drive forward our sustainability commitments. These leaders have clear goals and are accountable through the sustainability steering group.
5. Energy Champions
Our Energy Champions play a huge part in our emissions reduction. Their specialist, departmental knowledge has helped deliver savings across a number of areas including innovation, mattress and component production, weaving and NPD.
6. Sustainability training
Since the start of 2023, the Sustainability Team have been rolling out department-specific sustainability training. To date, over 200 people have received sustainability training and these interactive sessions are helping to embed sustainability into all parts of the business.
We’ve already delivered over 580 hours of sustainability training to our people.
Our business
We are two distinct businesses with the same purpose and values. Spinks, our components division and Harrison Spinks, our bed-making division. Sharing the same values and location, we work seamlessly together.
Mattress and bed manufacturing
The true bedmakers
Makers of proudly different mattresses and beds, each one is built on a belief in doing things the right and most responsible way. For our customers, and for everyone.
Handcrafted in our Yorkshire factory, using only the finest and sustainable materials. With natural fillings, homegrown on the Harrison Spinks farms. Springs from our components division. Even fabrics woven in-house too.
We make mattresses for several markets, including retail partners in the UK and overseas. These include high-street retailers (often under their own brand) and the independent retail sector (under the Harrison Spinks and Somnus brands) as well as hospitality and high-end interior design industries.
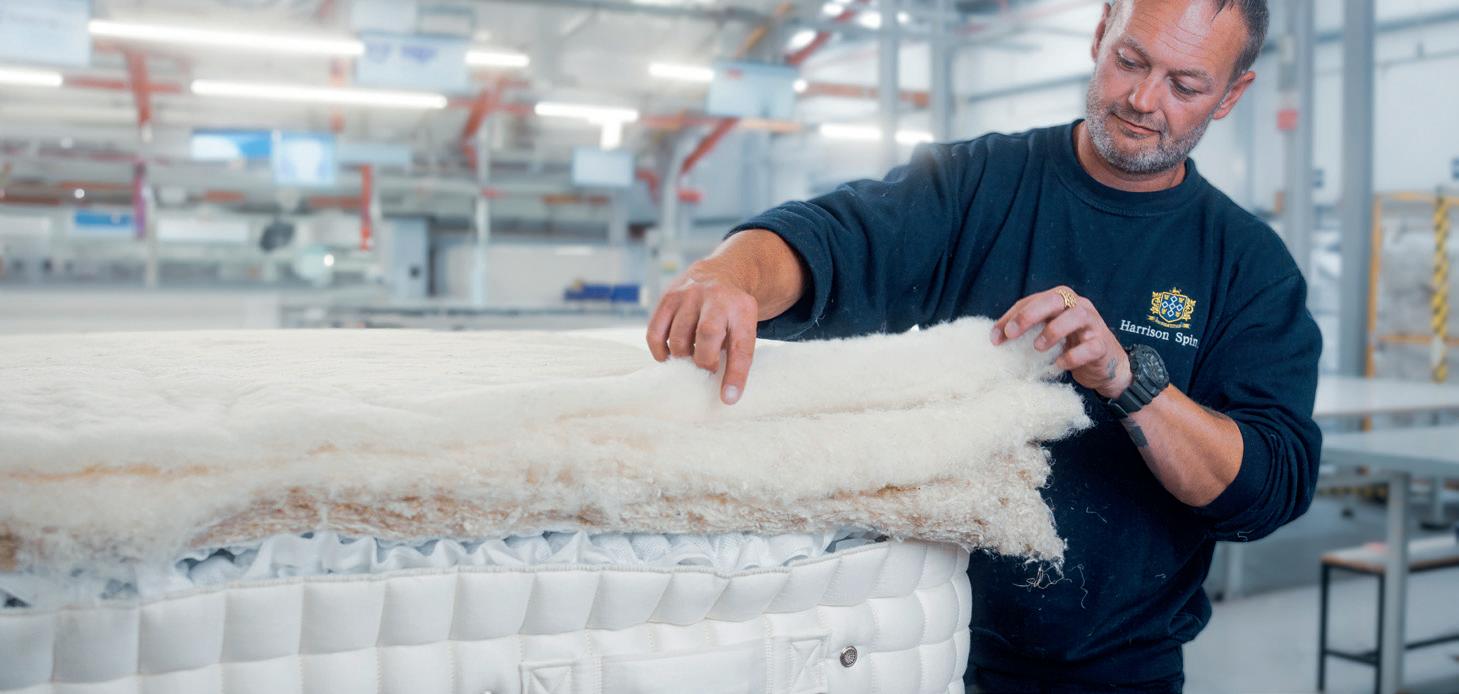
Components division
Sustainable comfort technology
We are the world’s leading manufacturer and supplier of awardwinning micro springs which are used predominantly within the bedding and upholstery markets.
We also transfer our technology and expertise to as many different applications as we can. Ranging from automotive, rail and bus seating, footwear and any markets where sustainable comfort is needed.
We believe that collaboration and sharing of knowledge are vital for delivering lasting change. It’s why we have made our spring-making equipment and intellectual property available to others, allowing them to benefit from the quality and efficiency of our products. This reflects our belief in supporting a collaborative environment within our industry.


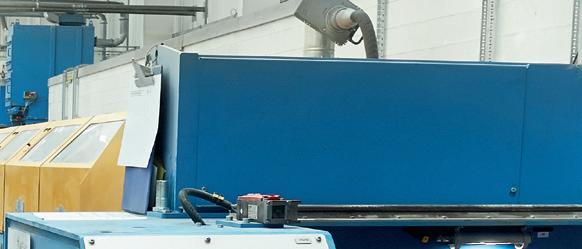
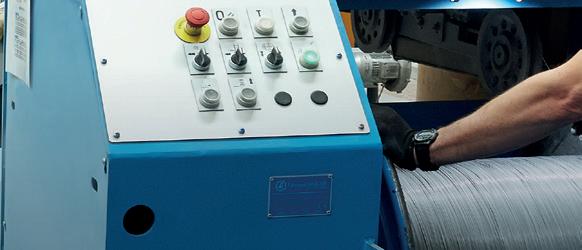
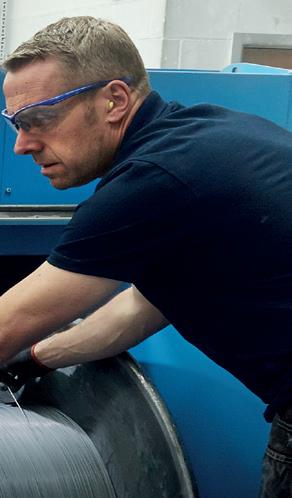

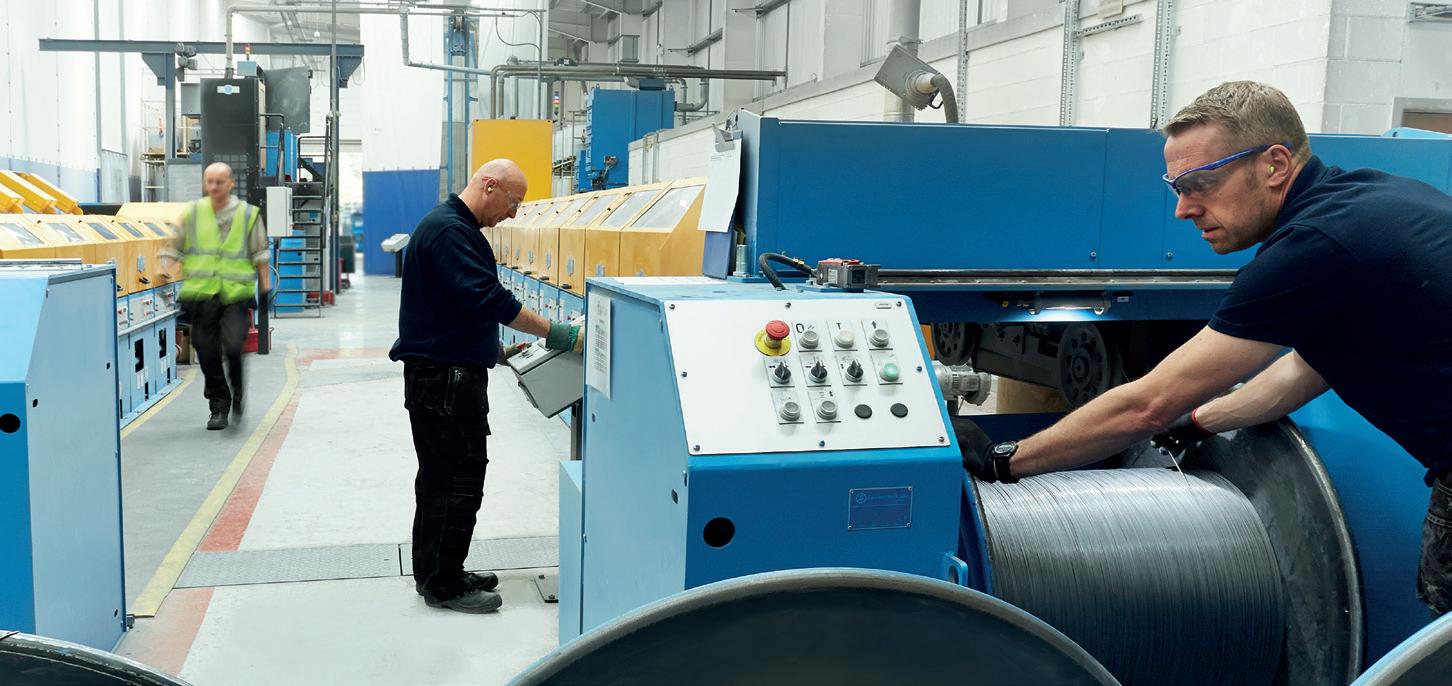
Our vertical manufacturing business model
Nothing reflects our commitment to responsible manufacturing more than our vertical integration model.
We are passionate about where everything comes from, how it’s made and its impact on our people and our planet. So, instead of buying in, we choose to grow, make and weave most of what we need. Our approach is unique within our industry and sits at the heart of our business model.
Our farms, unique spring-making technology and in-house weaving, take the concept of self-reliance to a whole new level. Giving us a level of accountability within our industry like no other. And despite the great progress, we continue to look for ways to change, evolve and better benefit the environment and society around us.
We’re proud to be one of the UK’s most vertically integrated manufacturers.
NATURAL FILLINGS
HOMEGROWN
Hemp, flax and wool grown on our farms.
DEVELOPMENT & INNOVATION
In-house teams dedicated to advancing spring and comfort technology.
SPRING MANUFACTURE WEAVING
WIRE DRAWING
Pocket and ultra-fine wire made on our own dedicated line to our unique spec.
In-house natural fillings dept Hemp, flax and wool from our farms. Plus recycled cashmere, British wool, silk and cotton from trusted suppliers.
IN PROGRESS
REGEN
We’re pioneering industry-leading ways to repurpose clean waste back into luxury fillings.
In-house spring-making dept Making our glueless core and Microcoil springs.
RESPONSIBLY SOURCED
British wool and other yarns from certified suppliers.
HARRISON SPINKS BED PRODUCTION
Where all our luxury beds are handcrafted by us.
In-house weaving dept State-of-the-art looms weave our exclusive FabriSafe™ FR-chem-free mattress fabrics.
100% recyclable fabrics, fillings and springs.
Logistics and support Delivering comfort and supporting our customers.
How we do it
Our passion for supporting a happier and healthier world can be seen in every part of our business.
Our departments, and crucially, how they work together, are at the heart of what makes our approach different, more innovative and more responsible.
Continuous innovation and development
Driven by our belief in continuous innovation, our in-house development team sits at the heart of our business. The dedicated team of 12 fulltime colleagues constantly challenge conventions and push our industry forward. We currently hold 99 patents granted worldwide for our unique technologies and have been recognised with eight King’s and Queen’s Awards since 2013.
Wire drawing
Concerned that no spring units on the market could offer what we were looking for in terms of quality and sustainability, we chose to make our own.
Our wire-drawing facility at British Steel’s site in Scunthorpe, is 50 miles from our factory. As this is where the raw material is located, it’s more efficient to make our wire here.
The 40,000 sq ft site is home to six Harrison Spinks wire-drawing lines. Each draws steel wire through multiple dies to reduce the diameter. Resulting in our signature pocket and ultra-fine wires used in making our core and micro springs.

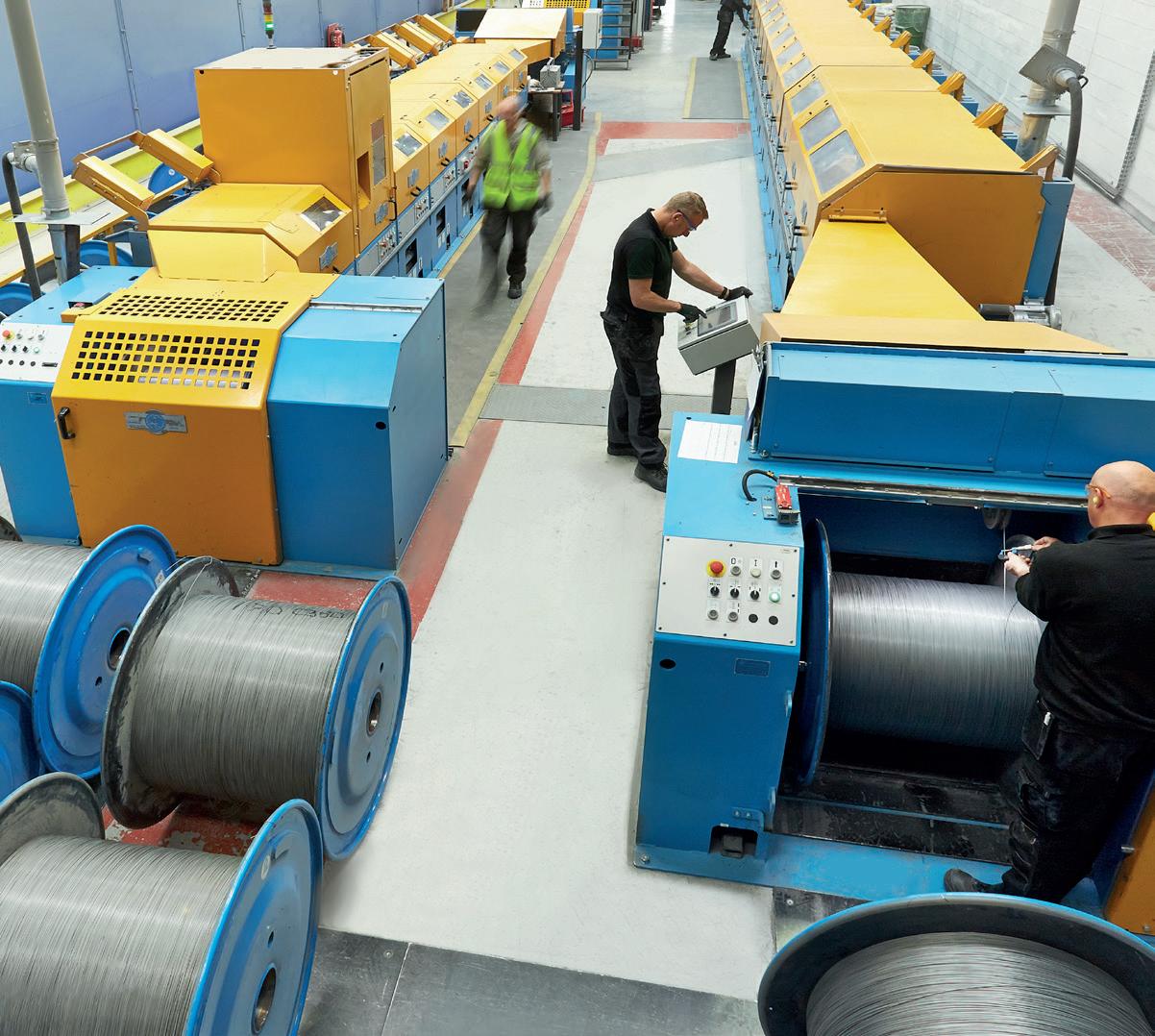
Spring manufacturing
We’ve developed unique spring-making technology to make our springs in the most energy- and material-efficient manner possible. Our equipment, designed and built at our factory in Leeds, turns this wire into our award-winning springs. Here, in-house production lines produce the finest and smallest springs available in the mattress industry. Each is ultrasonically welded into our pocket cloth, without the need for glue, making a 100% recyclable pocket spring core.
We’ve introduced cutting-edge tech that reduces the energy consumption of our pocket spring making by 60%.
See page 40
Our farm
Fourteen years ago, due to the lack of transparency and availability of local natural fillings, Simon Spinks made the bold move to buy a farm. This decision has changed our business completely.
Just 18 miles from our factory, we grow some of the most important elements of our beds: our natural fillings.
To support growth and demand, we purchased another farm at Ryther, North Yorkshire in 2021. Close to the original, it has allowed us to increase our hemp production acreage by 80 acres.
This means we now farm 180 acres of arable land, where we grow hemp and flax, and 200 acres of grassland where we raise our sheep.
We also process all our hemp and flax on-site.
On the farm, we convert approx. 20 tonnes of hemp straw per week into breathable fibres for our mattresses.
“Owning a farm gives us all a unique and unbreakable connection with the environment around us. We’ve seen how responsible farm management can not only impact our hemp and flax crops but also make a difference to local wildlife.”
Simon Spinks, Group Chairman Harrison Spinks
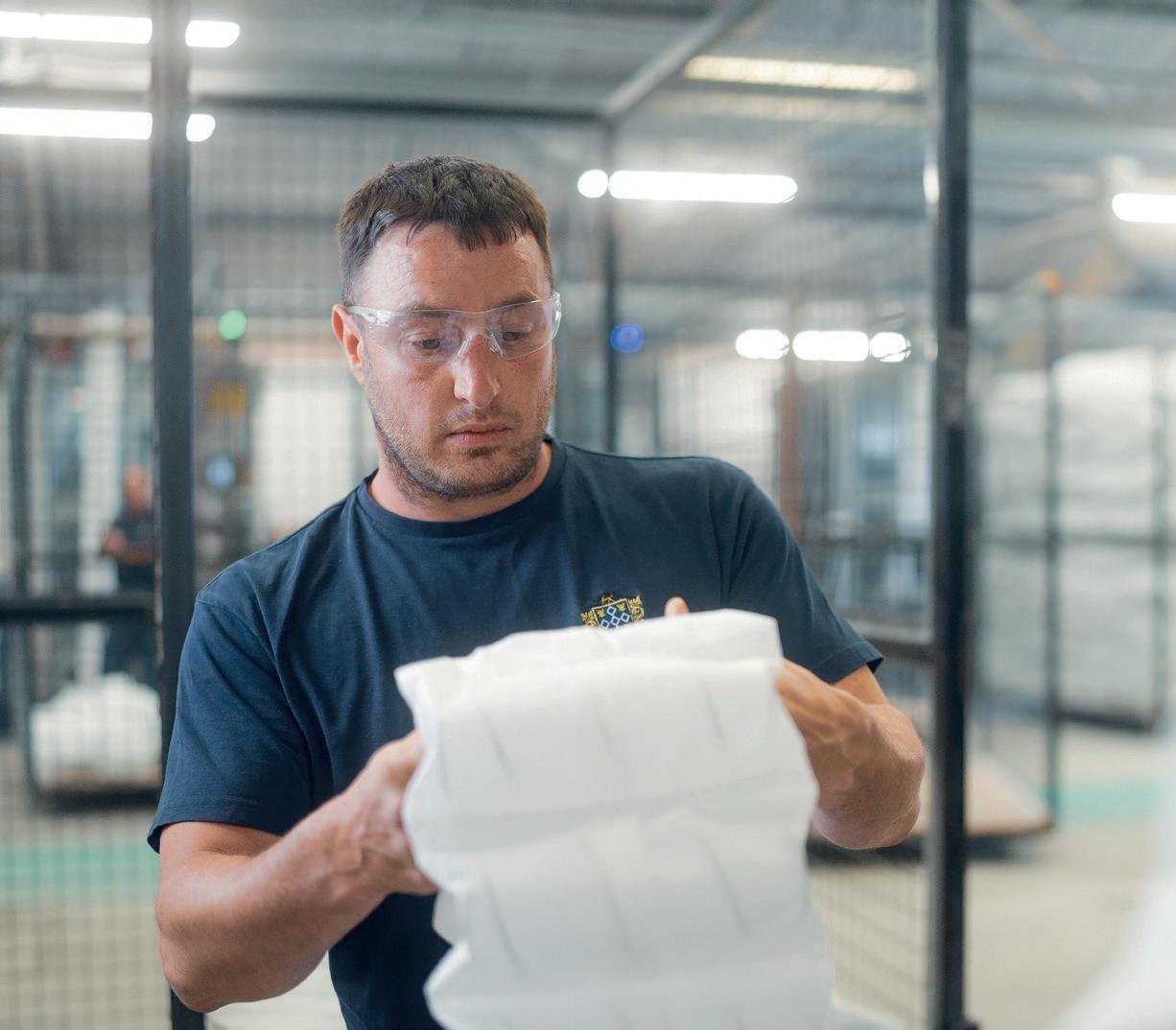
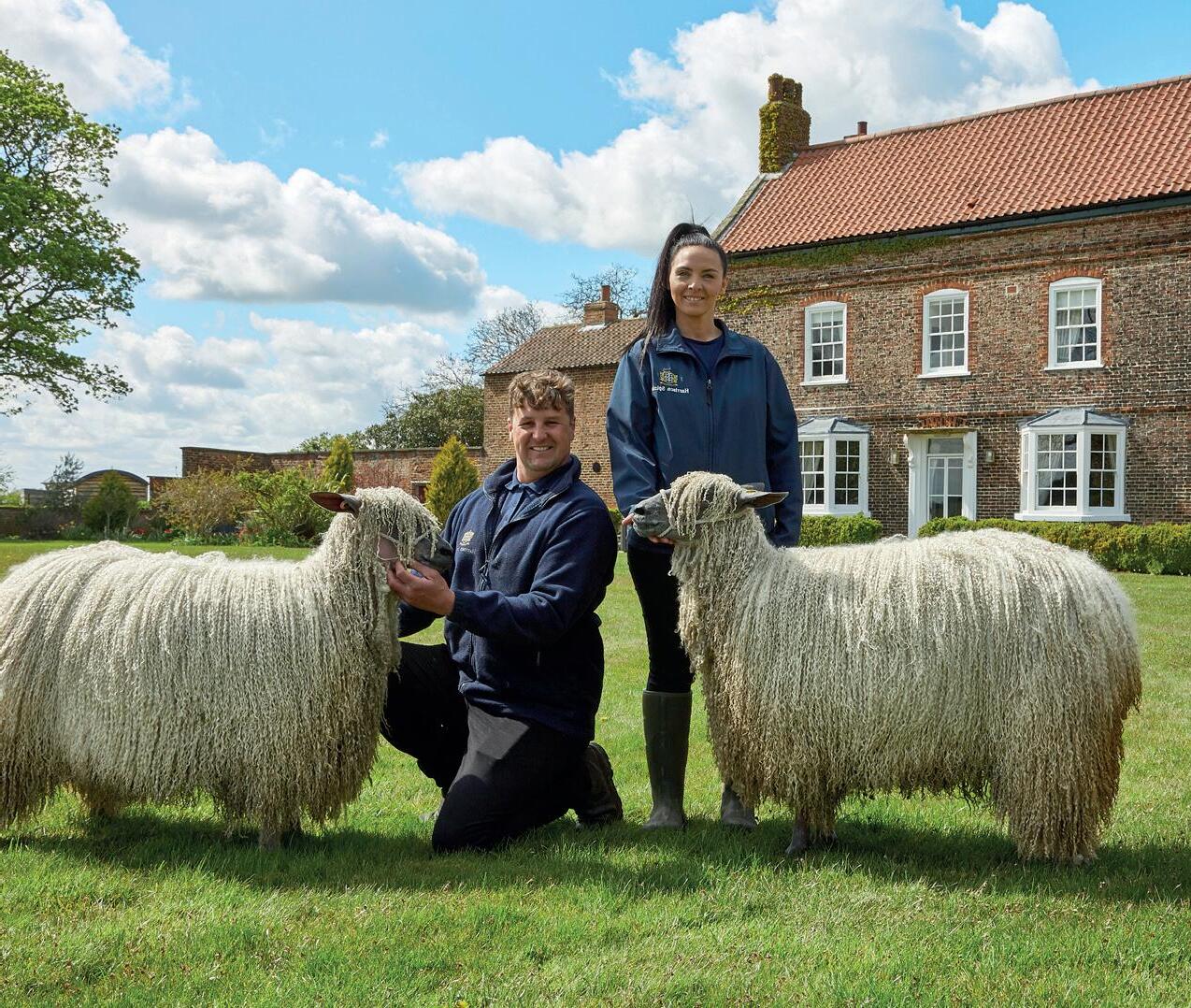
Our natural fillings
Natural, healthy and happy sleep is important to us. It’s why we are the only UK mattress manufacturer to blend our own natural filling layers, in-house.
We take our processed hemp and flax straight from the farm, and blend them with other responsibly sourced natural fibres.
We create over 10 tonnes of mattress-filling pads each week. All of which are fully recyclable at the end of life.
Our fillings department also produces biodegradable wool insulation pads to support the local food packaging industry, reducing their reliance on plastic.
In-house weaving
We are the only bed manufacturer to weave our mattress fabric. Not only proudly keeping the tradition of weaving tick in Yorkshire, but we do it in a sustainable way too. Our wool-based fabrics are inherently fire-retardant, meaning they don’t need any FR chemical treatments.
Weaving our chemical-free fabric saves over 28 tonnes of chemicals each year.
Our 10 looms, seven of which are air jets, are among the most modern and efficient equipment available. We weave approximately 400 linear kilometres of tick each year, which covers 100% of our needs.
Thanks to our partnership with local textile company Camira, we can weave an upholstery fabric using our homegrown hemp and responsibly sourced British wool, which is inherently fire-retardant and chemicaltreatment-free, in line with our mattress ethos.

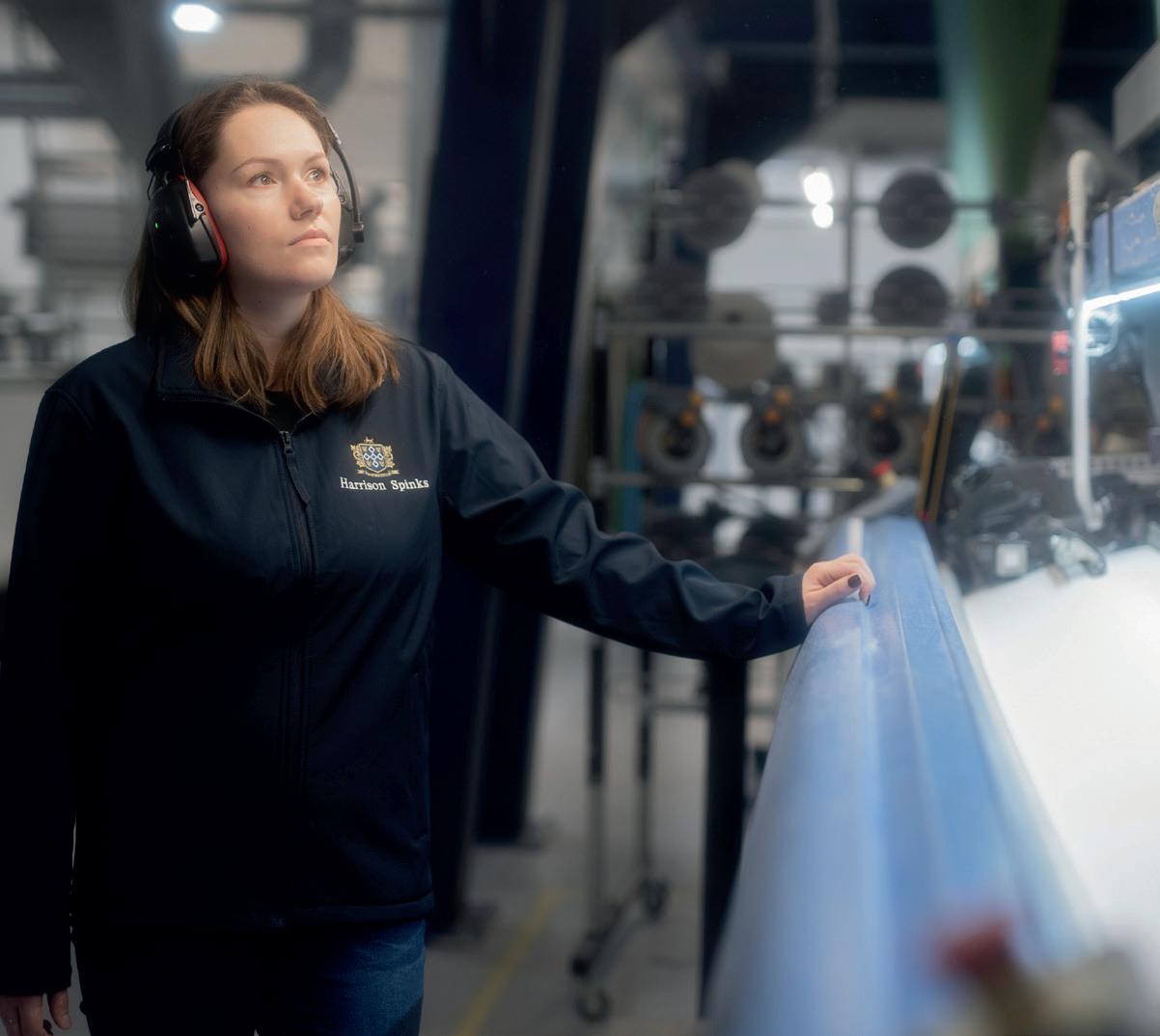
Mattress,
headboard and divan production
We believe the best way to make mattresses, headboards and divans is by hand. And that’s why we are meticulous about every material we use and the processes we follow.
Unlike any other bedmaker, we manufacture over 95%* of the mattress components in-house.
Our mattress production department in Leeds is where all these elements come together. Each is handcrafted to give the consumer many years of comfort.
Made in the same responsible way as our mattresses, and with the same meticulous eye for quality, our divans and headboards are also handcrafted on-site and only use FSC ® certified wood.
We
only make 100% glue-free and foam-free mattresses.
*By weight

Logistics
and support
We understand the impact our deliveries have on the local community and the environment.
We believe that managing our fleet around our own needs is more efficient and more responsible than contracting out to a third party and losing transparency.
Our distribution team carefully manages our fleet which consists of 18 HGVs and three Luton vans. Delivering to our retailers, and including items such as point-of-sale material with bed deliveries, saving multiple deliveries and reducing transport miles.
Our main overseas customers are based in North America, Europe, Australia and Asia.
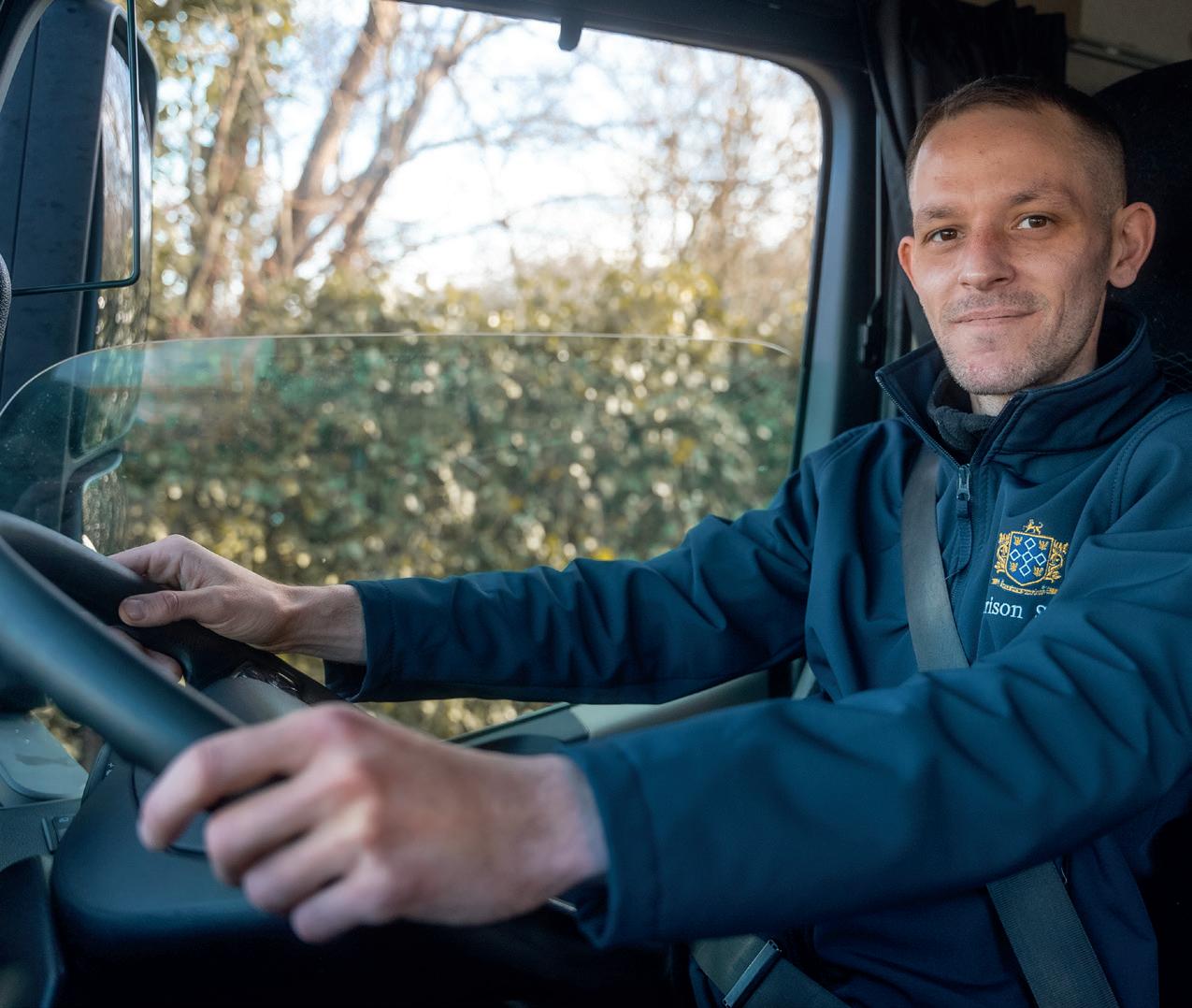
Our approach to sustainability
We are on a journey to become one of the most responsible manufacturers in the UK. Leading the way in vertical integration and product circularity.
As part of this journey, we consistently push ourselves to review and monitor our material impacts so we can understand where we can make the biggest difference to our communities and the environment.
We’re growing
Our core spring units are
We’re planting of flax – a more sustainable alternative than cotton of native hedgerows 120 ACRES 100%
2,750m
We’ve delivered over of sustainability training to our colleagues
330,000kWh free colleague health checks delivered 190 580hrs
More efficient wire process saves each year
We currently hold
99 PATENTS
Our new pocket coiling machine reduces energy consumption by
We’re providing compared to the previous process each month to children’s bed charity Zarach 60% 20 MATTRESSES
1%
All our mattresses and headboards are 100%
FOAM-FREE & GLUE-FREE
We’ve increased employer pension contributions by Weaving our own naturally fire-retardant fabrics saves of chemicals each year of all vacant roles this year will be filled by apprentices worldwide
SCOPE 2 EMISSIONS BY 11%
We’re upcycling cashmere offcuts, replacing over of virgin wool in just 12 months 1,400kg
10 TONNES 75 TONNES
OVER 28 TONNES 5%
We’ve reduced our We’ve reduced our We manufacture over Optimised deliveries have Electronic proof-ofdelivery system saves over We produce over We’ve permanently removed in the past financial year
SAVED 60,000
in the past financial year in-house. *By weight transport miles each year pieces of paper each year of recyclable mattress fillings each week of hot melt glue from our manufacturing process
SCOPE 1 EMISSIONS BY 22% 95%* OF COMPONENTS
250,000
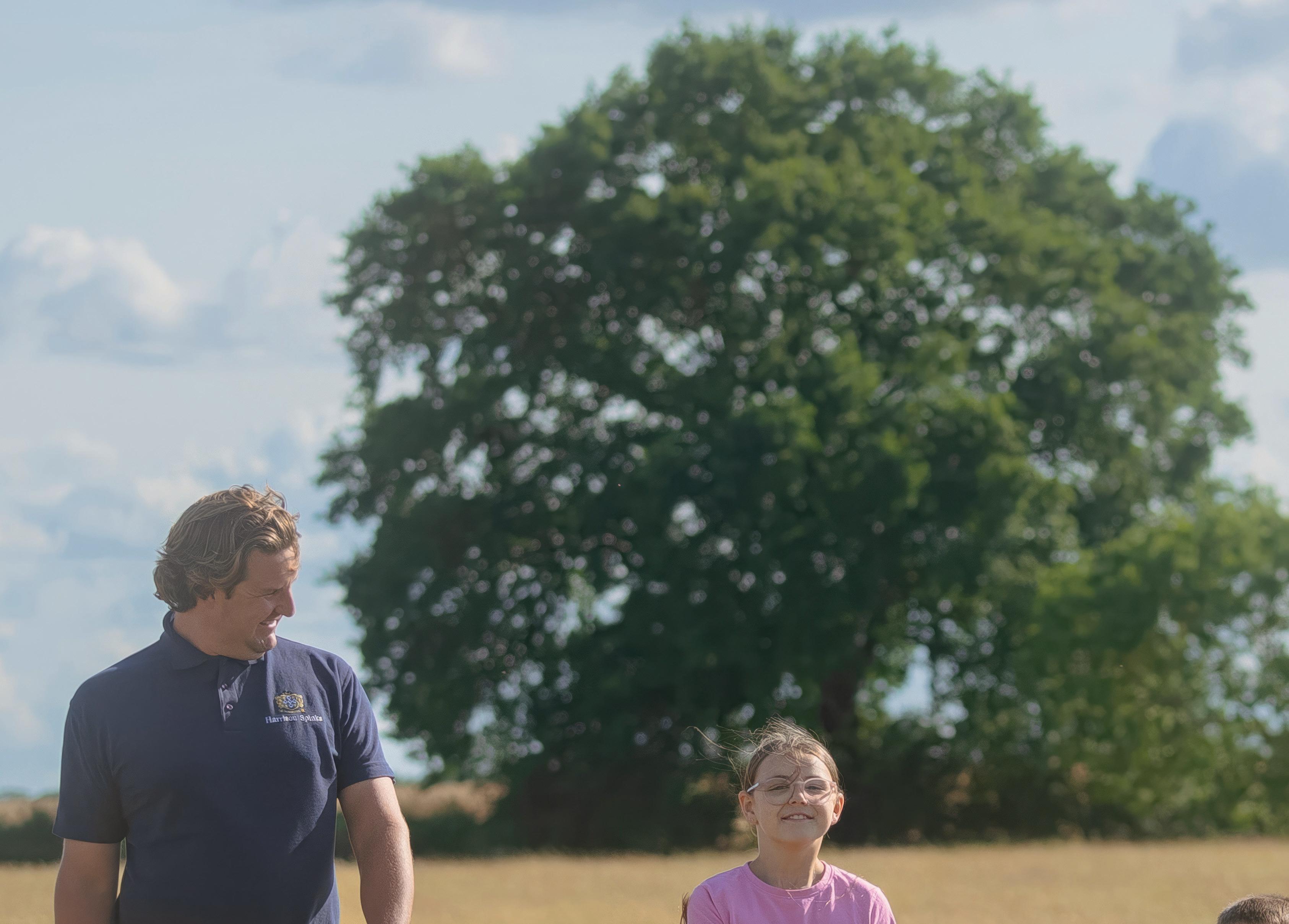
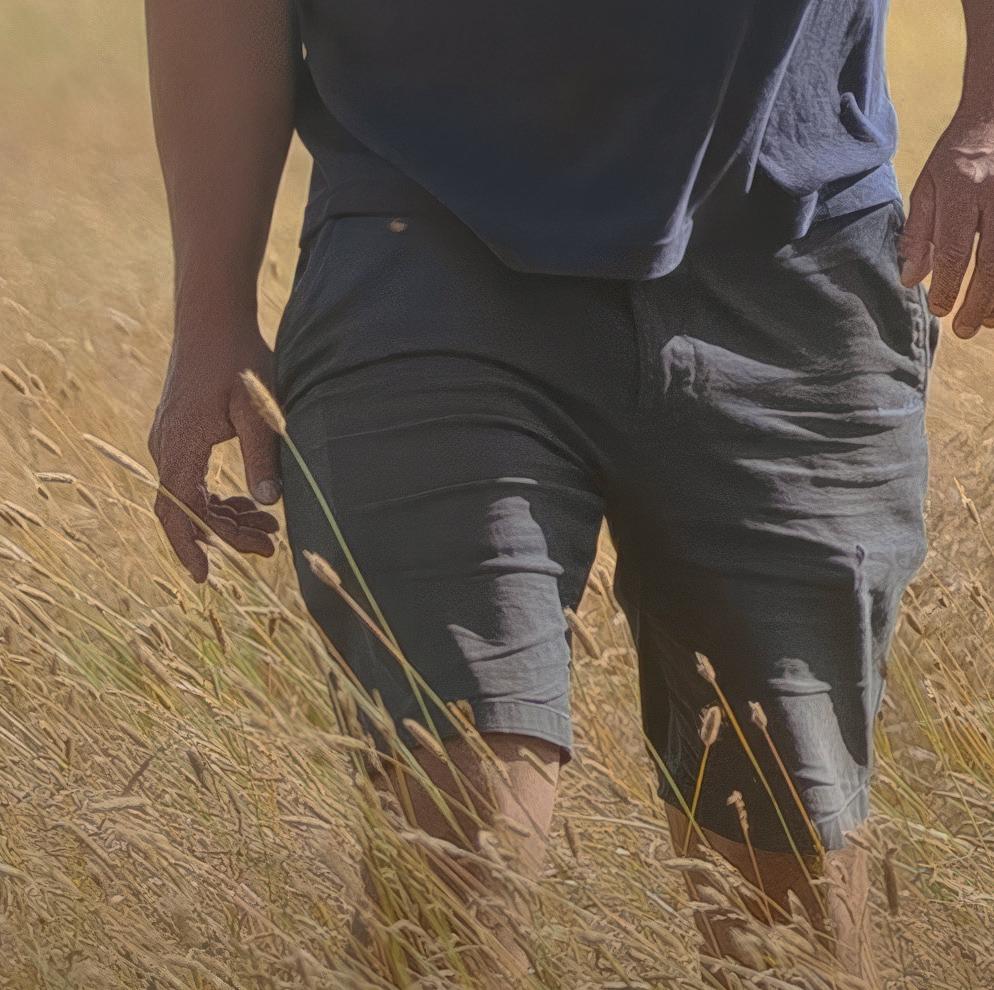
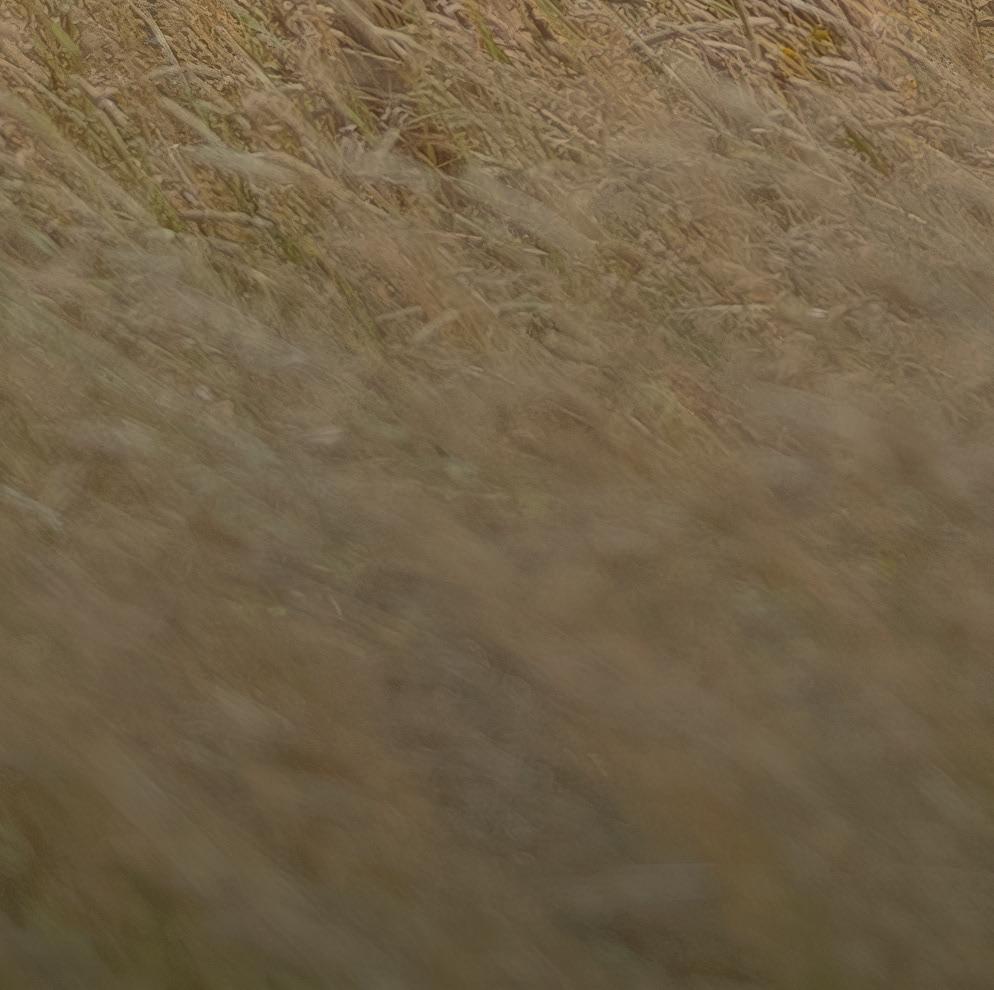
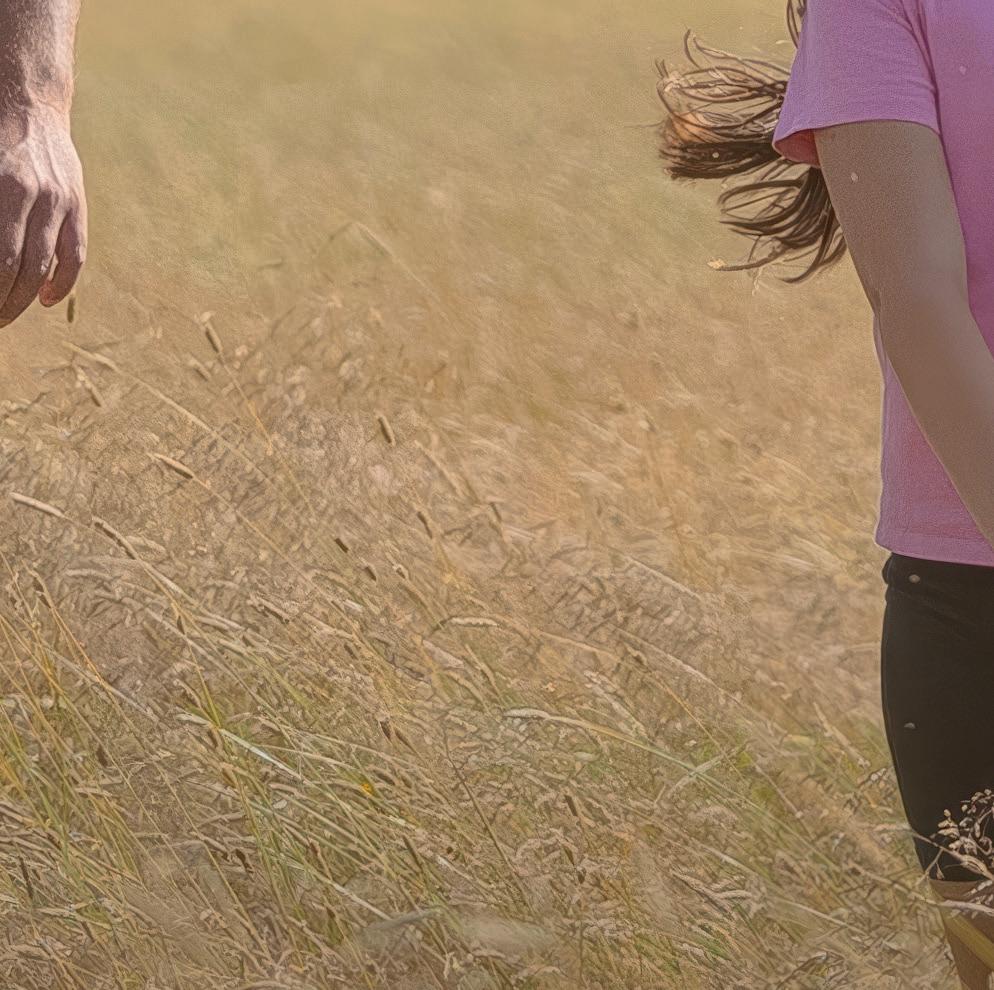
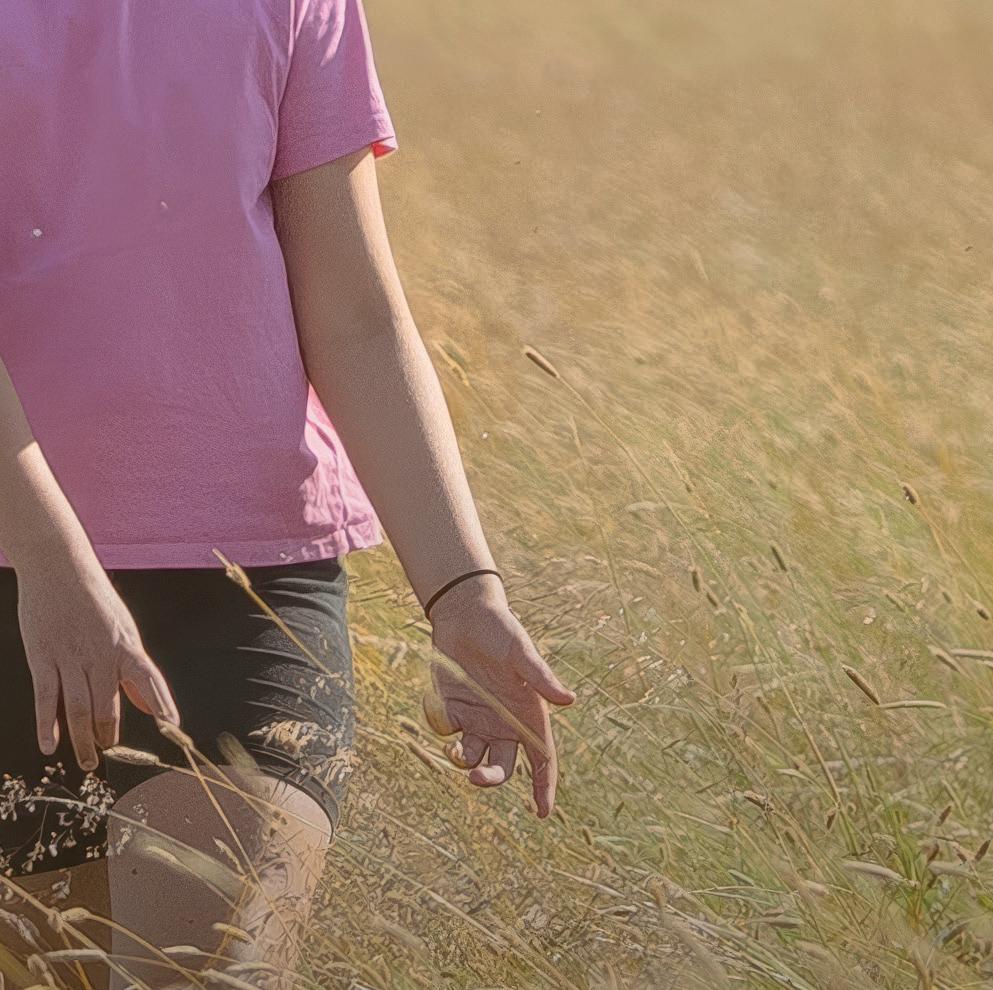
1. Protecting valuable materials through waste mitigation.
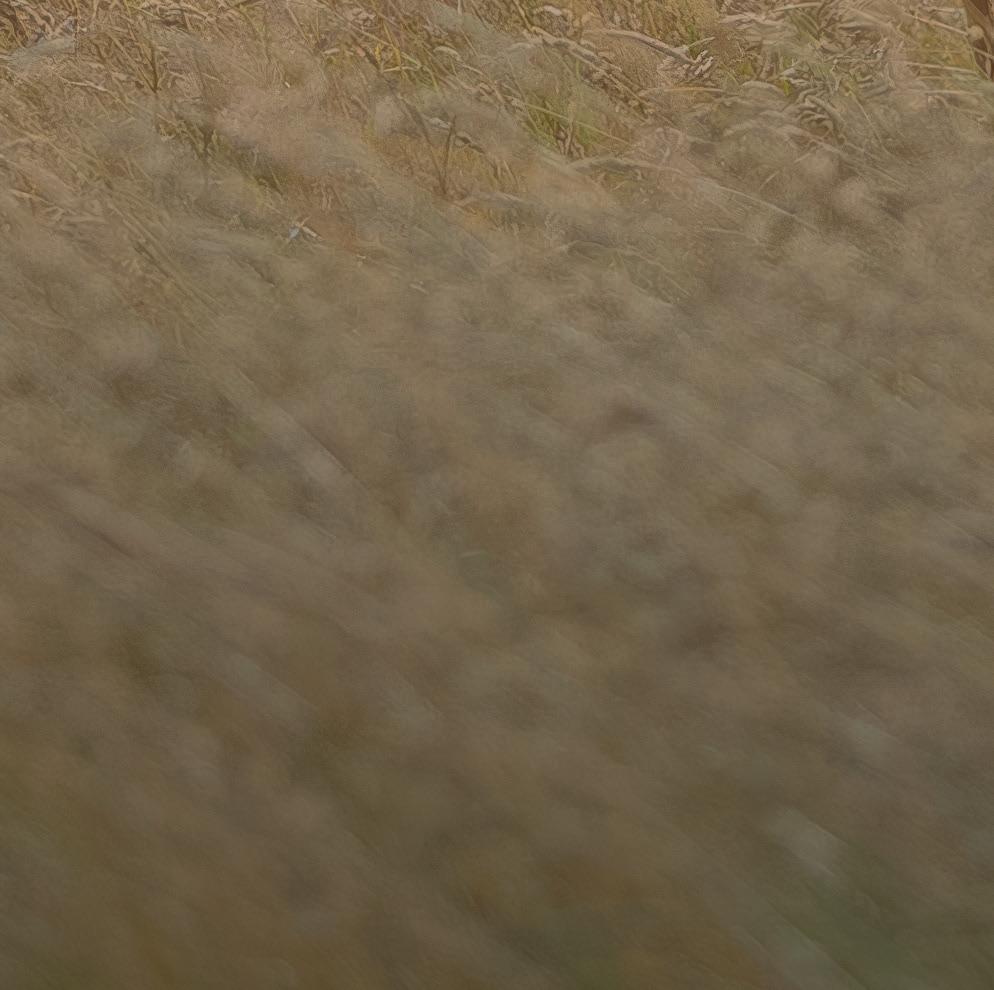
We are already making the big changes necessary to deliver a responsible approach that’s unique within the UK bed-making industry. These include:
2. Expanding our circular design philosophy by designing for disassembly and material recovery.


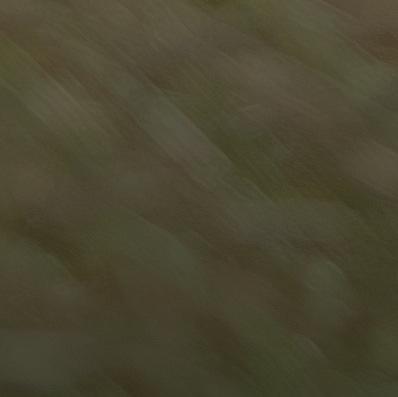

Environmental update
We are committed to becoming a net zero manufacturer, reducing waste across the business and becoming nature net positive, which means we will leave the habitat richer than how we found it. Not just at the farm (which will become an exemplar of sustainable production), but everywhere we operate, including urban areas.
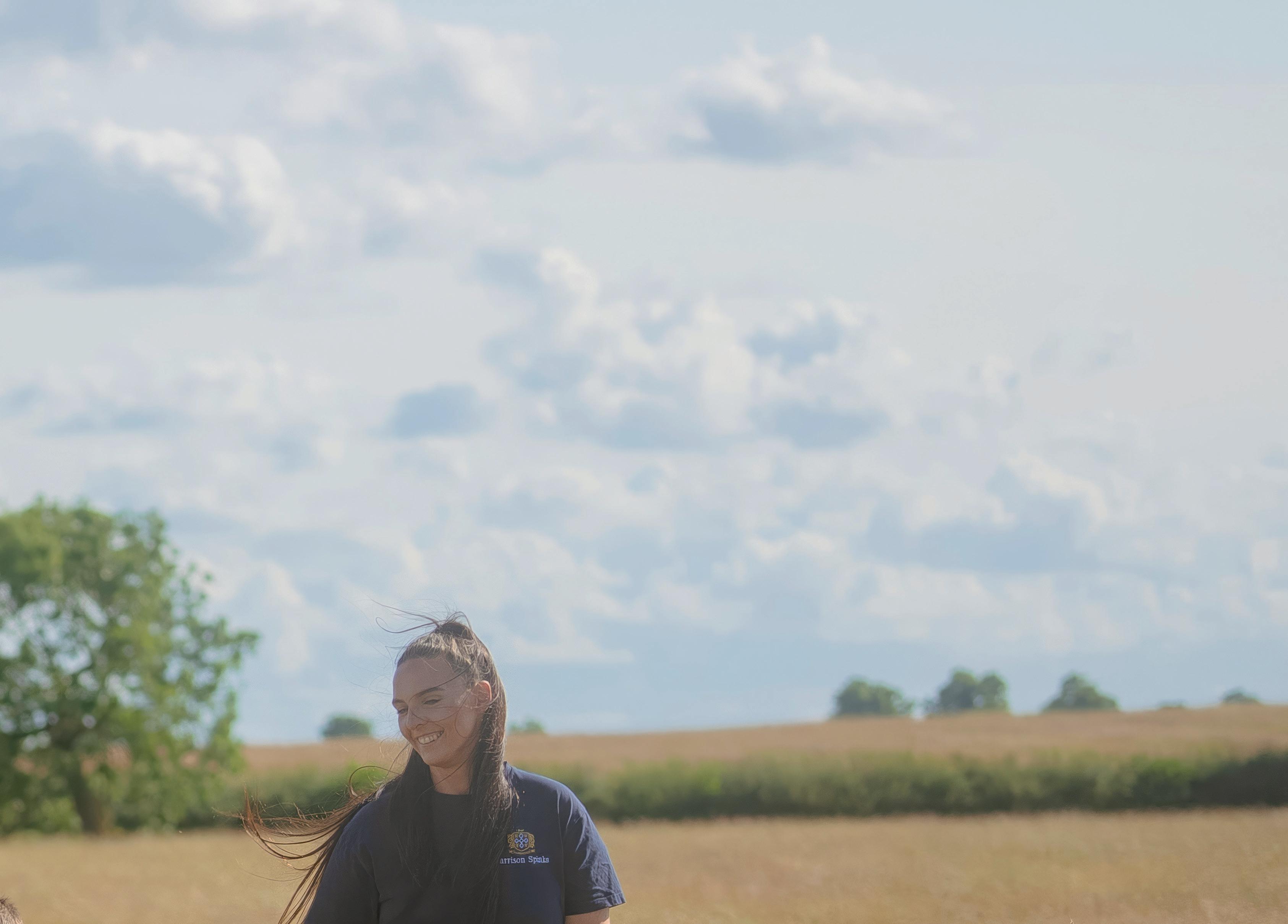
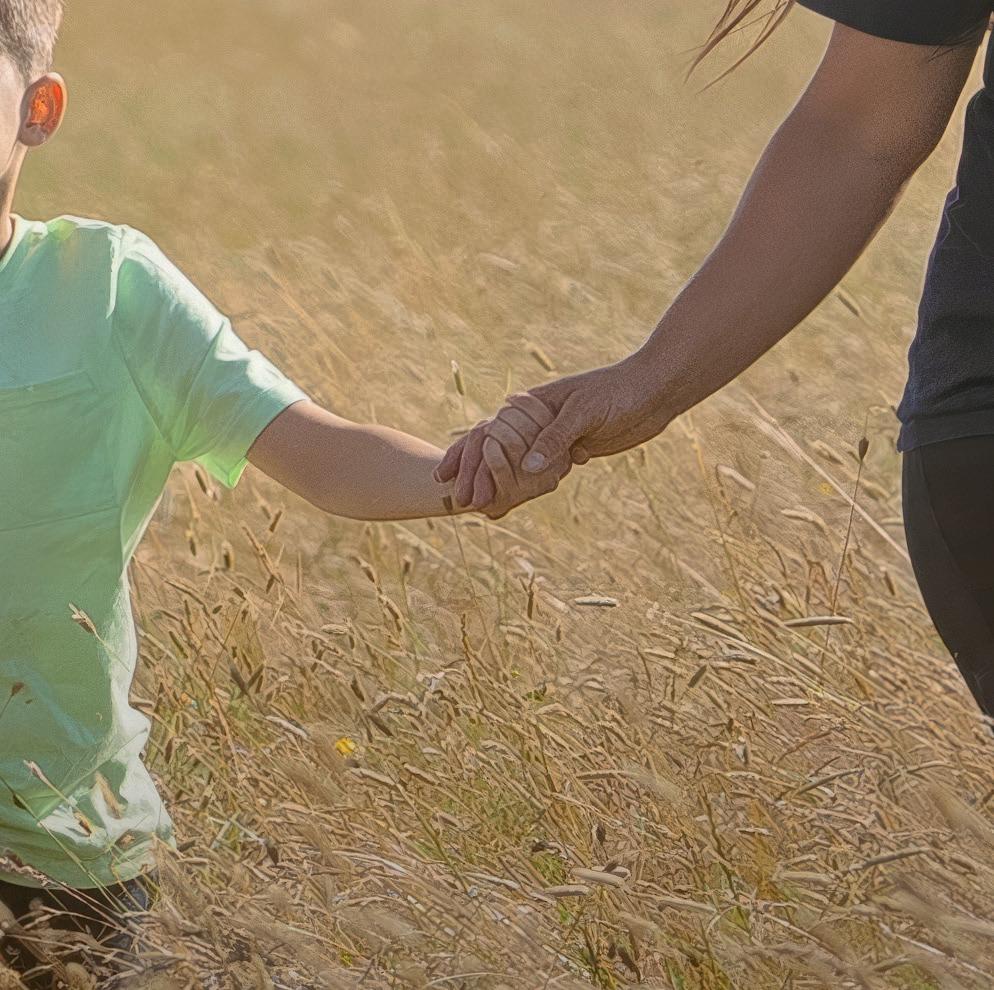


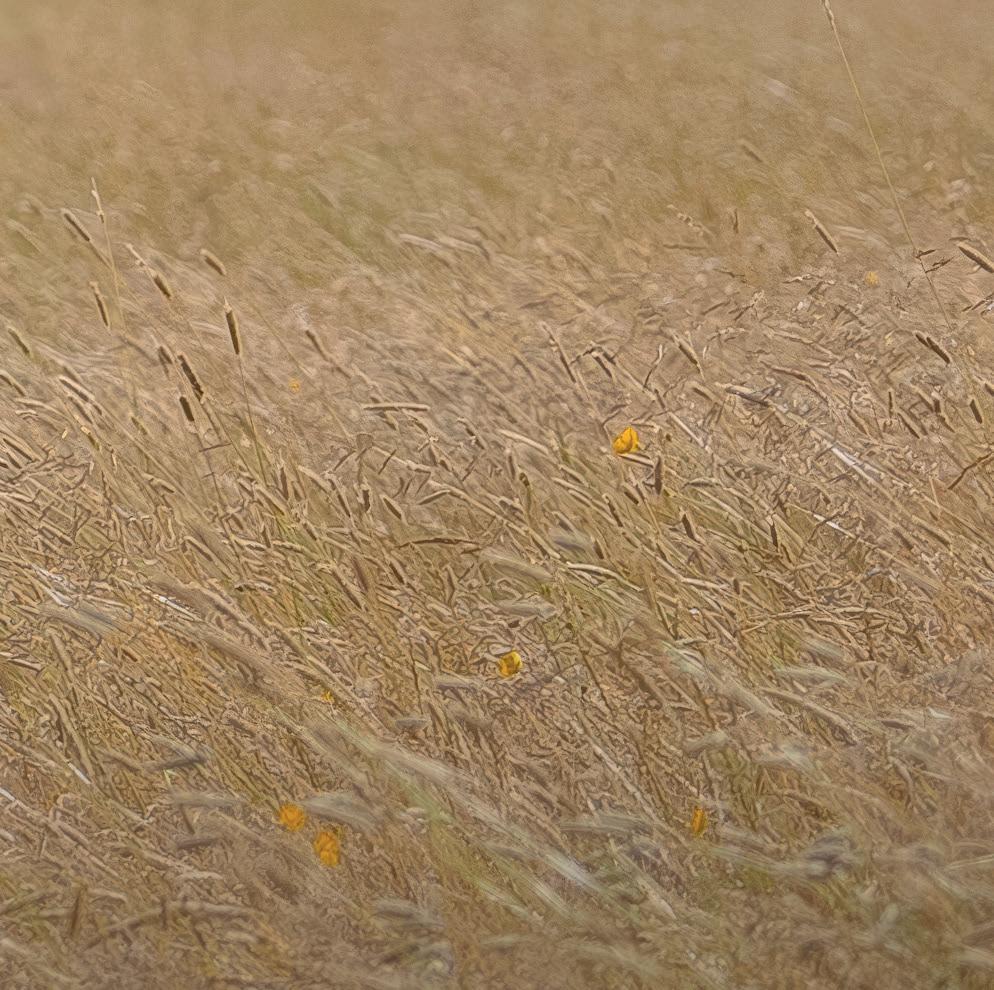
3. Reducing our social impact through responsible and ethical sourcing.
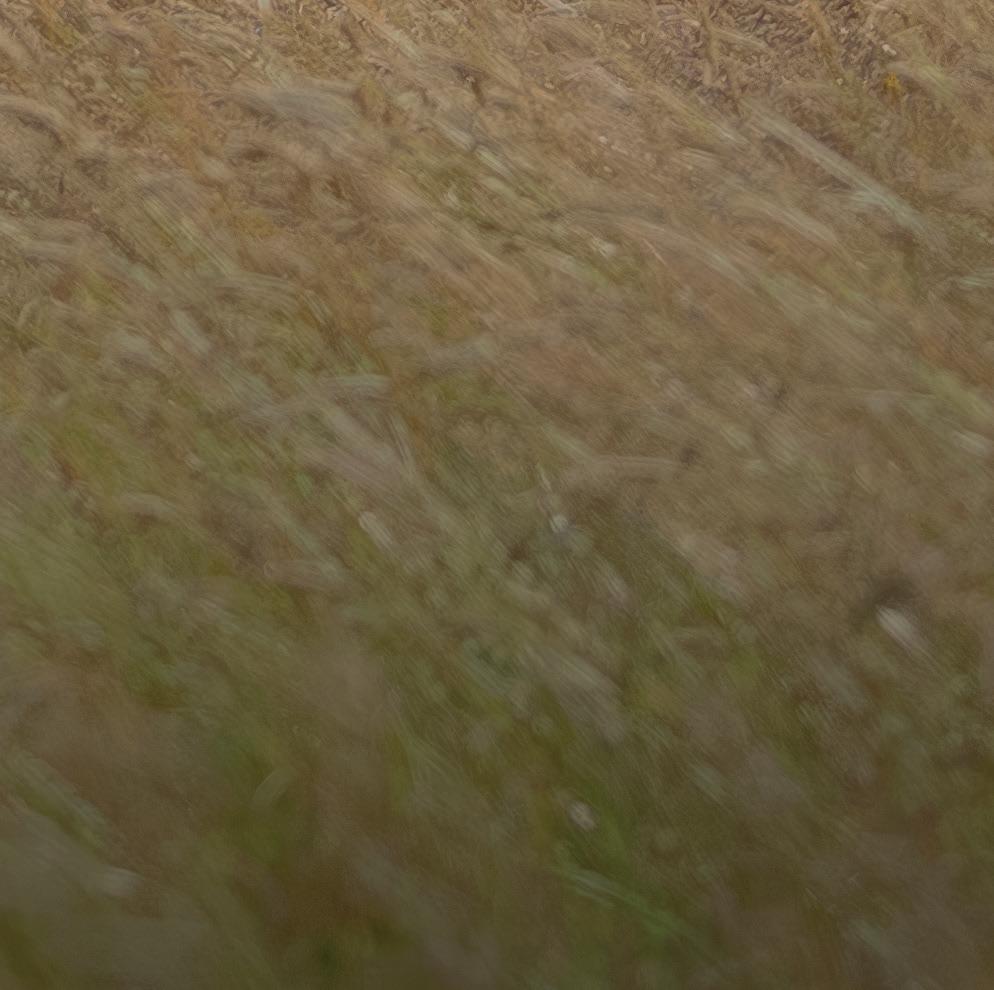

“In what will be game-changing for the industry, we are working towards developing processes to re-purpose components within our mattresses. This long-term goal will take huge steps in protecting the environment and will remain a focus for us for many years to come.”



Land and biodiversity
COMMITMENT: TO BE NATURE NET POSITIVE ACROSS ALL OUR OPERATIONS
Our farms at Hornington Manor and Ryther are working towards achieving fully organic. This means our hemp and flax fibres will be Soil Association-certified as organic. This will include the gardens and grounds of our adjoining wedding venue.
We’re already part-way through achieving this accreditation and we plan to be certified fully organic by September 2025.
We work in partnership, growing hemp and flax, with several local farms, facilitating crop rotation and maintaining good soil health. This system has allowed us to become one of the UK’s largest growers of industrial hemp.
Next year we will grow 120 acres of flax (an increase from 20 acres in 2023), this is to replace cotton fillings within our mattresses.
Flax is a comparable material to cotton in bed manufacture but needs no secondary pesticides, requires a fraction of the water, has significantly lower greenhouse gas emissions*, and is, of course, British-grown.

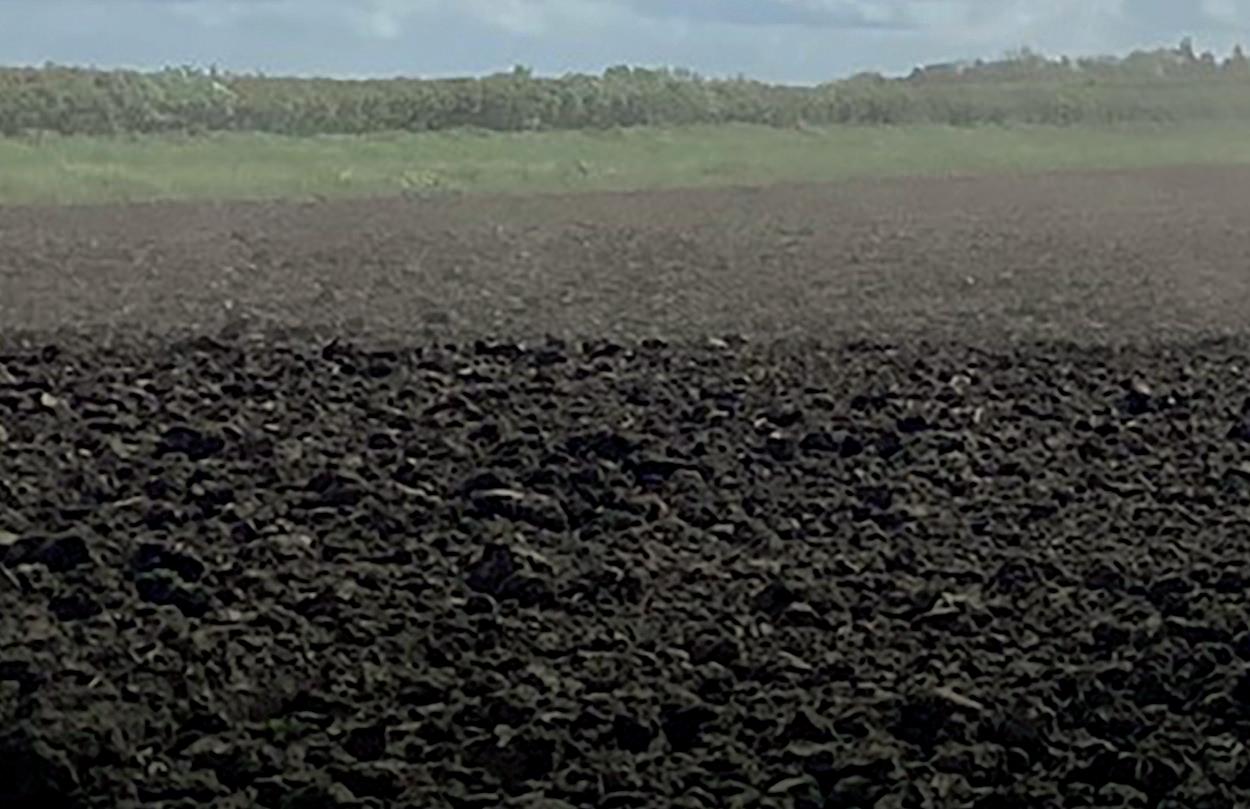

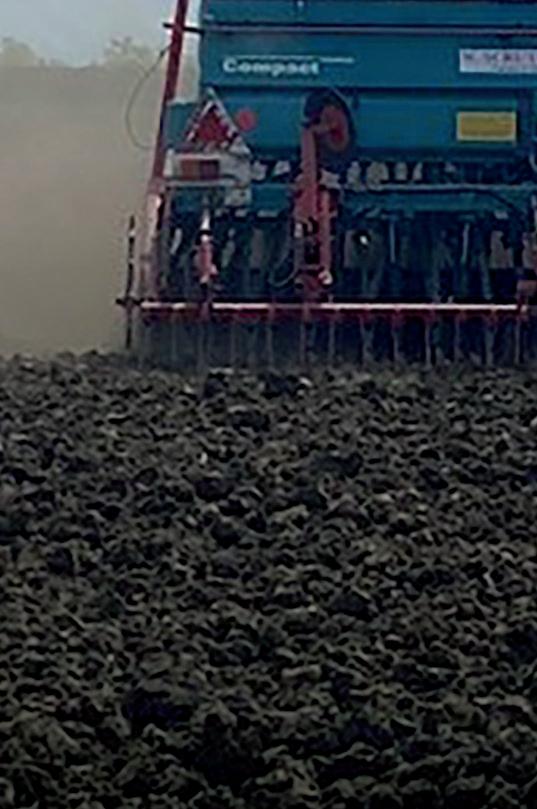
Encouraging biodiversity
Since we began farming in 2009, we have not used any secondary fertilisers or pesticides and only cut to make hay once a year, to allow ground-nesting birds to fledge and allow flowers to bloom. We’re boosting the natural habitat for birds further with a higher stewardship grant from Natural England. Enabling us to create and maintain 33 acres of wildflower, bird and butterfly margins.
We will also be adding 2,750m of new, native hedgerows to support animal welfare and encourage wildlife.
We have around 47 acres of Ings grassland on the farm, these are grazed throughout the winter and left unstocked from around March until July to allow ground-nesting birds to fledge. We have regular bird surveys and because of our farming practices, we have reintroduced several rare bird species back to the farm.
* Evaluating Environmental Impact of Natural and Synthetic Fibres: A Life Cycle Assessment Approach by Victoria Gonzalez. May 2023

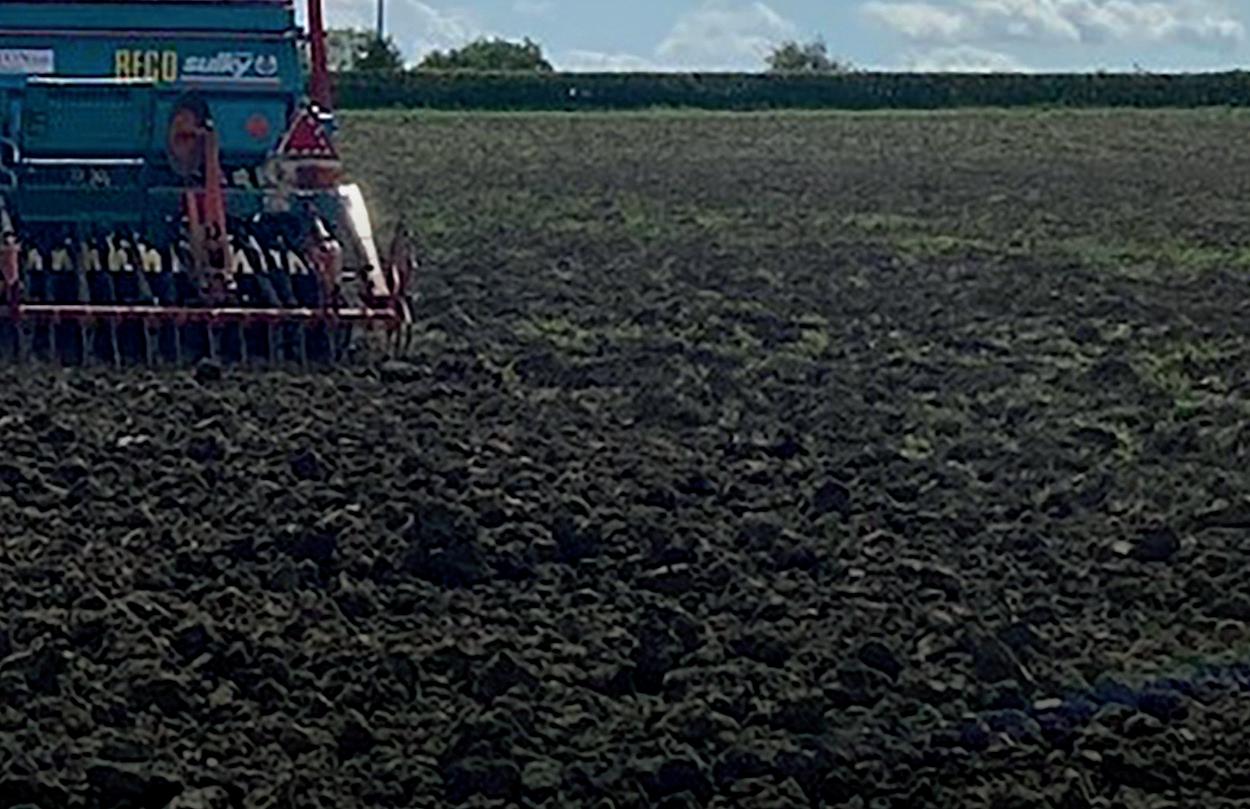
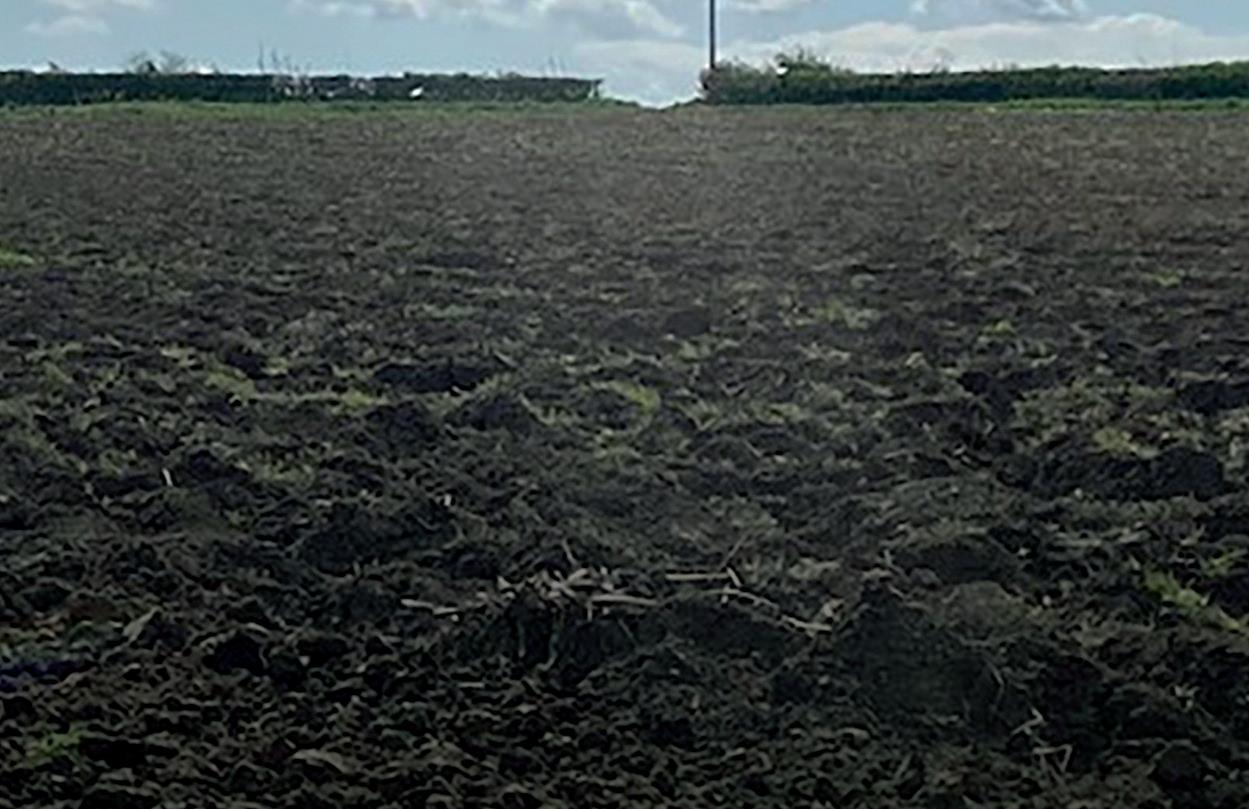
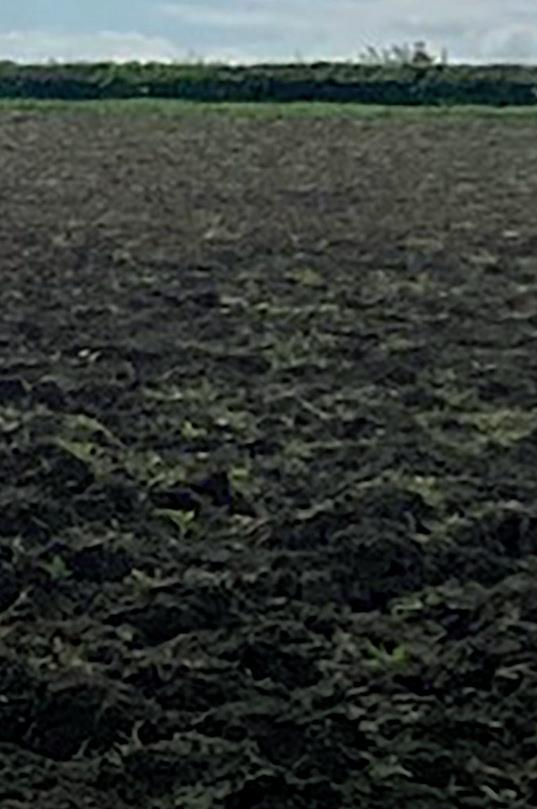
We won Breed Champion with our rare-breed Wensleydale sheep at the Great Yorkshire Show in both 2022 and 2023. At the Great Yorkshire Show 2023, we won every class we entered with our Wensleydales. We also won Champion Lamb at Masham Sheep Fair 2022, 1st in pairs at Masham Sheep Fair 2022 and Champion Female at Otley Show 2022 and 2023.
Wensleydales are classified as ‘at risk’, therefore we continue to support the survival of this breed.
We were awarded Vet Partners Sustainable Sheep Farm of the Year 2022, for our work in reducing the use of wormers in sheep and exceptional pasture rotation and management.

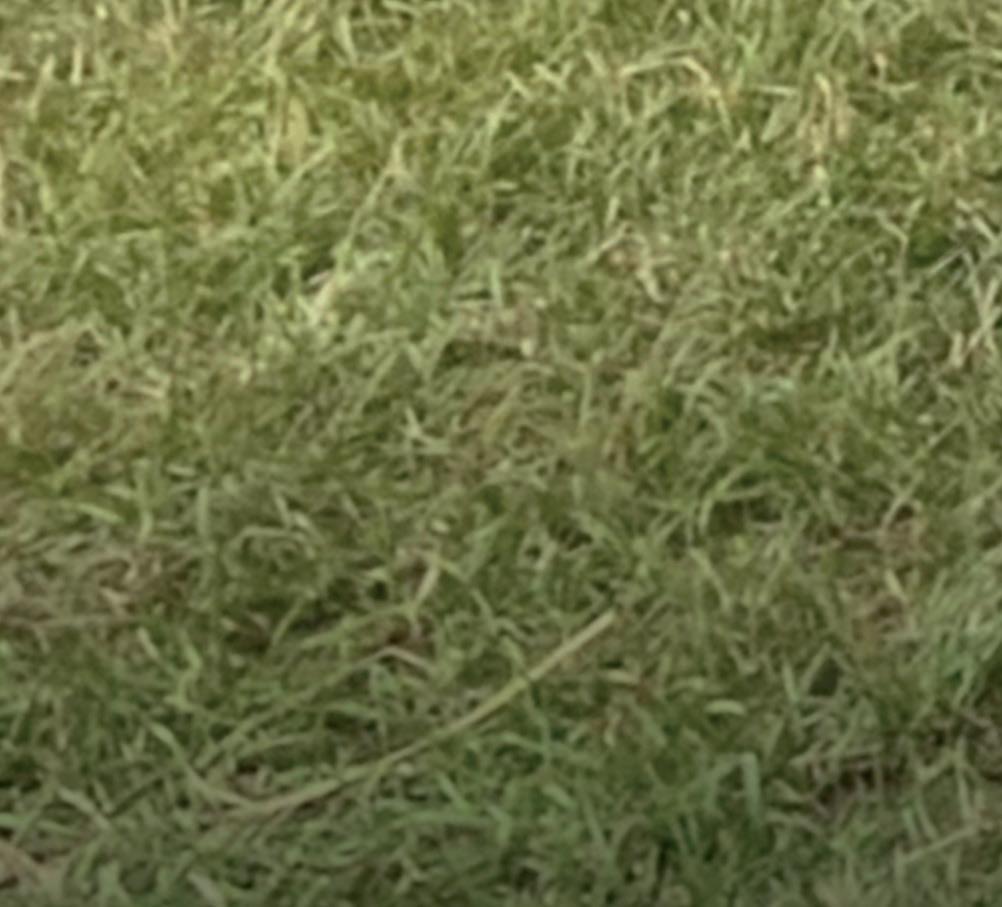
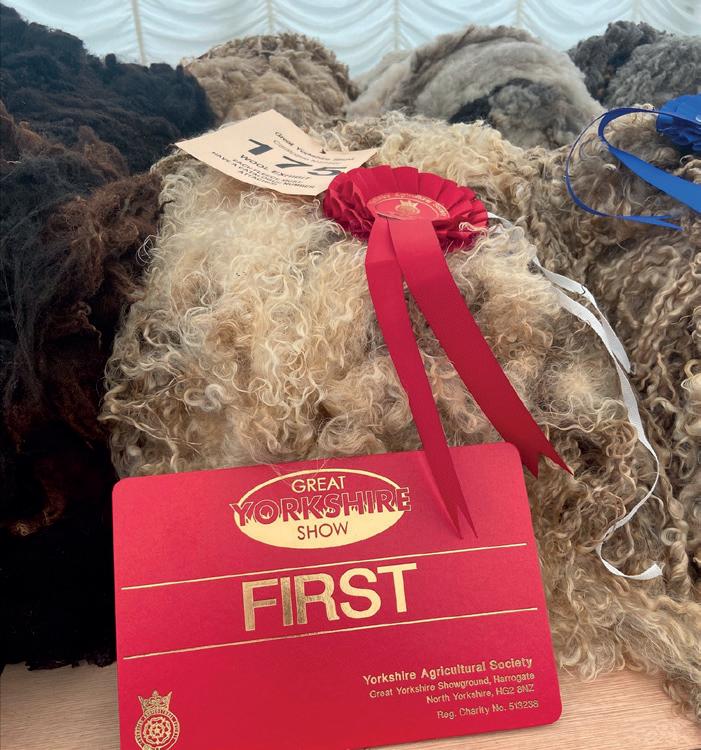
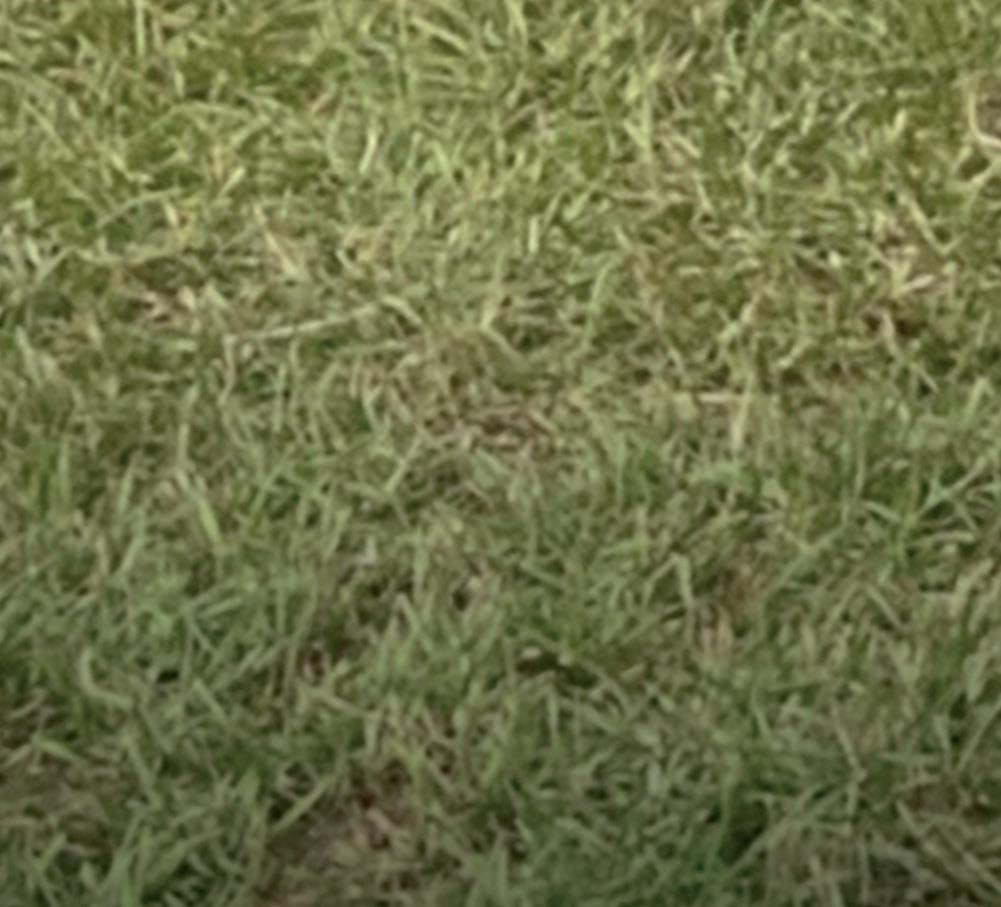
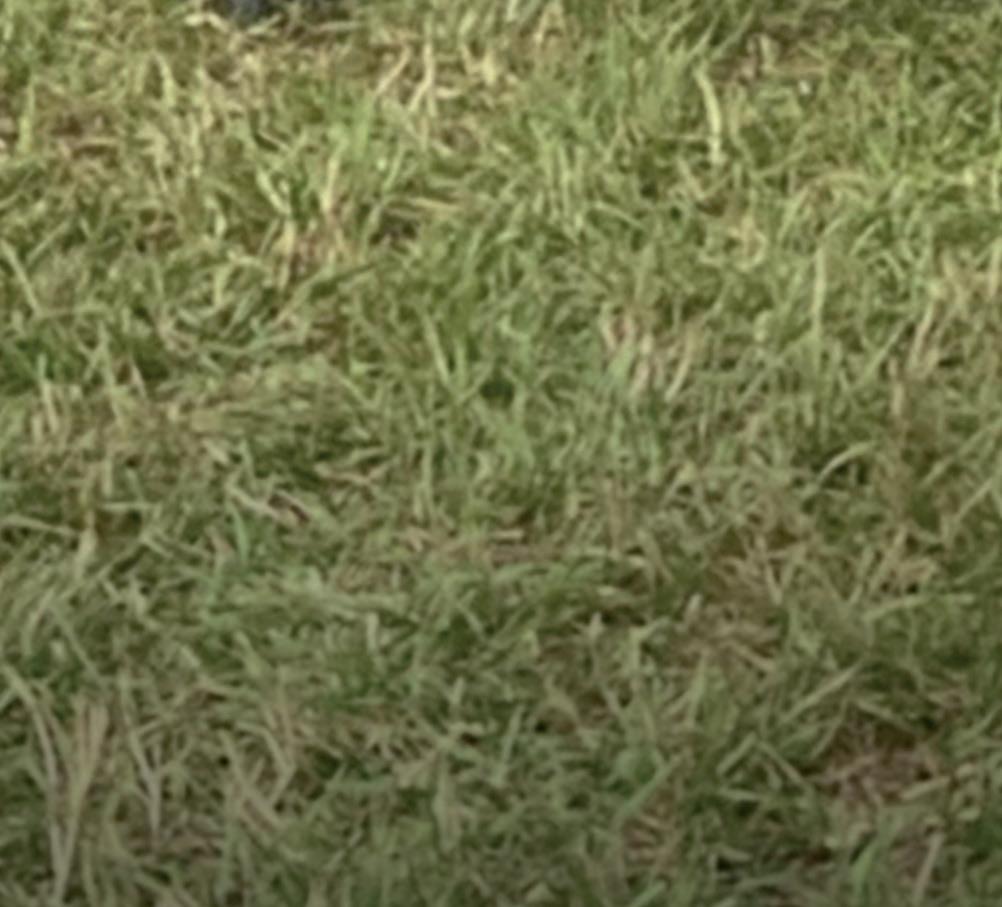
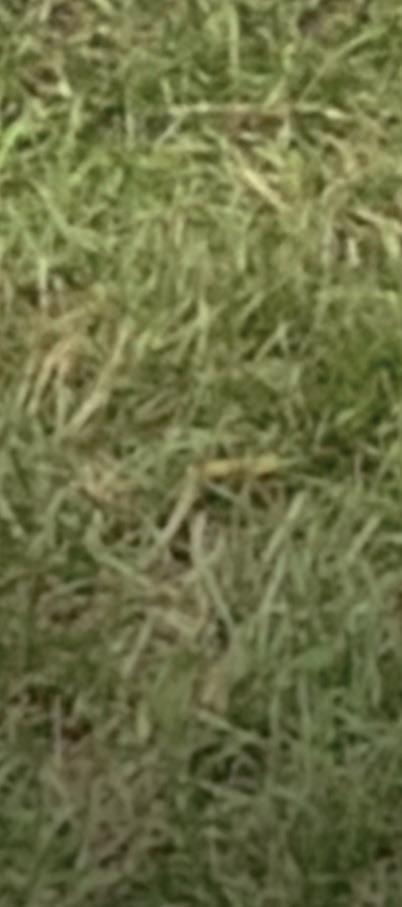
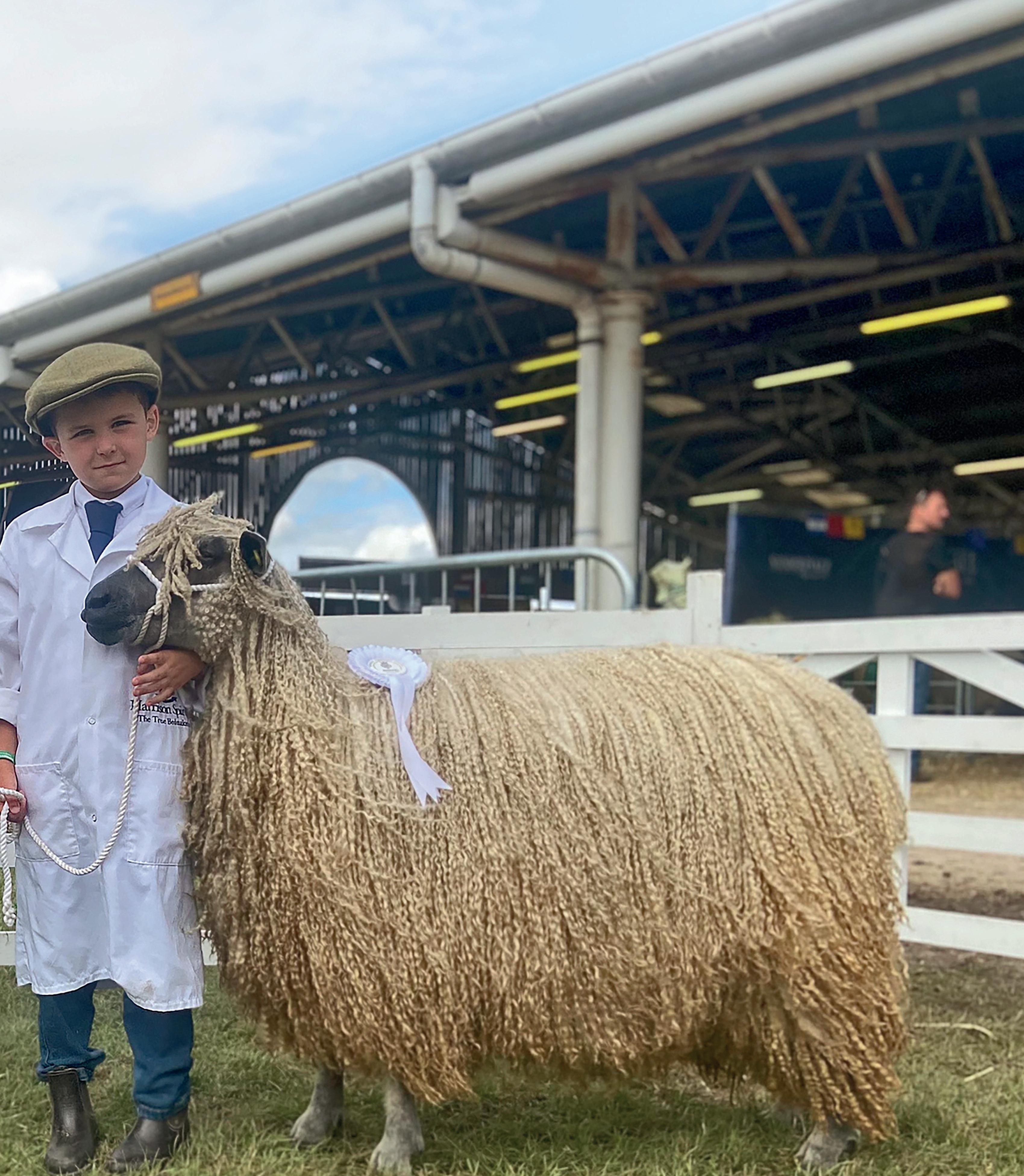
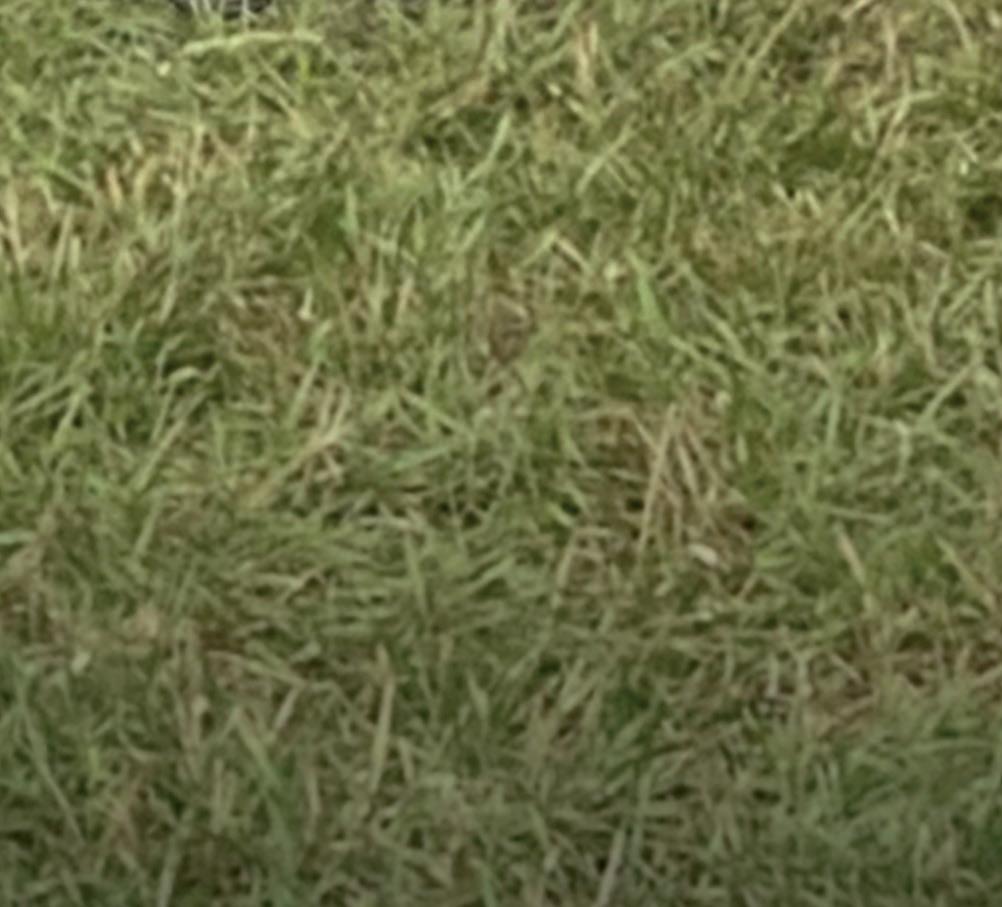
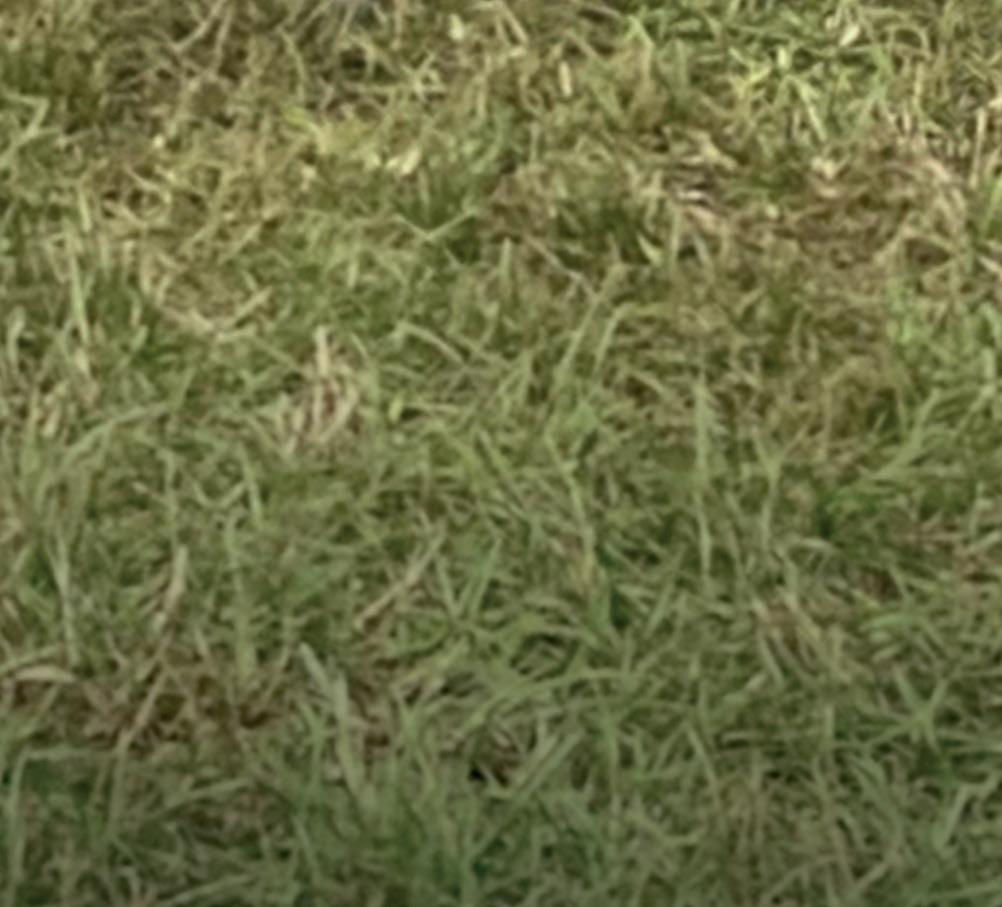
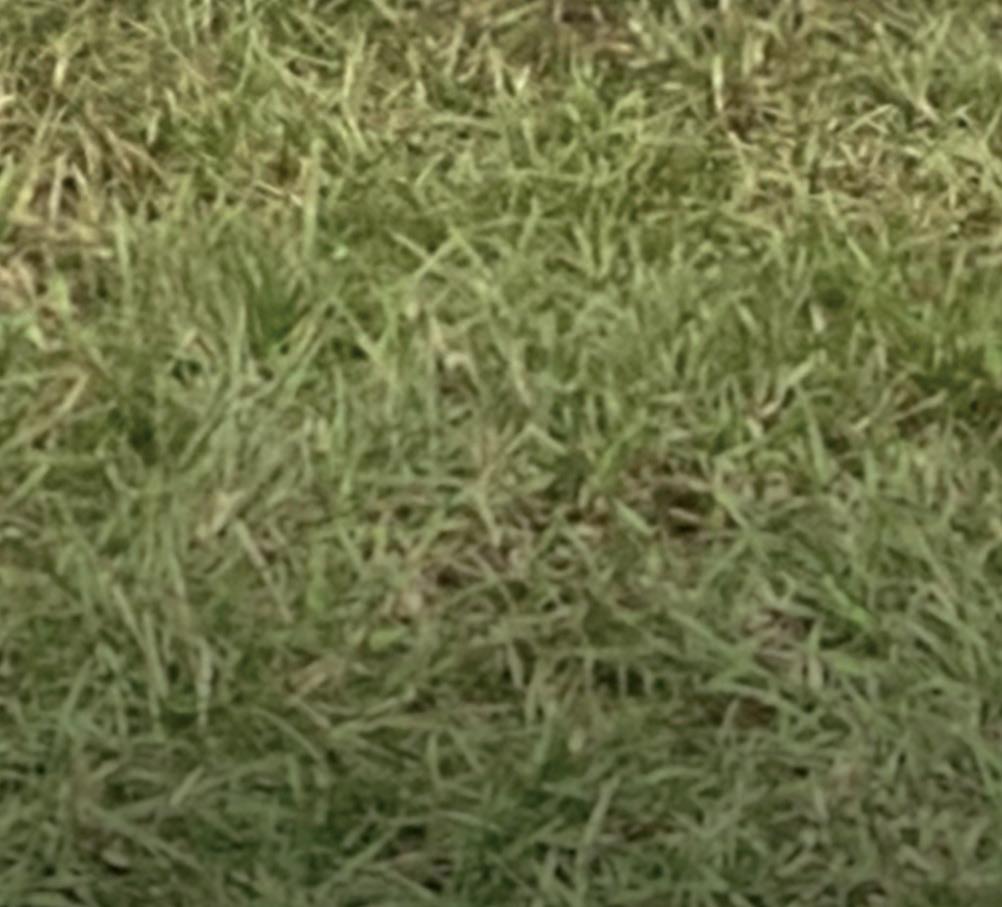

Consumption and circularity
COMMITMENT: TO BE FULLY CIRCULAR, WE HAVE INTERIM COMMITMENTS TO OPERATE AT ZERO PRODUCTION WASTE TO LANDFILL BY THE END OF 2025.
This year we have invested in additional equipment to re-purpose clean in-house production waste such as our natural, non-woven fillings, mattress borders and mattress tick. Putting these back into the production chain as fillings.
Our vision is ultimately to clean and re-purpose post-consumer mattress waste into new mattress fillings.
Our approach to waste for our homegrown hemp crops provides an insight into our attitude towards circularity. Every part of the plant is used, from thermally efficient, rot resistant and fire-retardant eco plaster to animal bedding. The remainder of the waste is used as biofuel to heat the farm and our on-site wedding venue.
Steel is by far the largest (by weight) component within our mattresses. Despite steel being infinitely recyclable, currently the majority of mattresses are going into landfill*. We are passionate about finding ways to ensure this doesn’t happen and have developed a core spring unit that is 100% recyclable.
We also partner with The Furniture Recycling Group, who segregate our end of life products from other manufacturers and methodically disassemble our mattresses by component. Our intention is to clean and re-purpose some of these components and reuse them in our mattress production.
* End-of-Life Mattress Report 2022. Prepared for the National Bed Federation by Oakdene Hollins. September 2022
100%
of the hemp we grow is used. Nothing goes to waste.

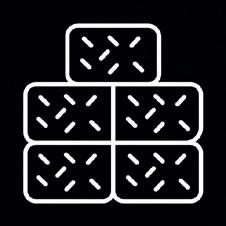
We collect over of waste each year 850 BALES
In-house waste-handling department
To reduce our impact, we have an in house recycling team. They collect around 50 bales every three weeks. What we can’t reuse ourselves is sent on to a recycling company for other companies to reuse and re-purpose, ensuring the waste does not go to landfill.
Our waste strategy
We’re focused on reviewing and reducing our waste.
To make sure we do this in the most effective way, we set up a waste taskforce to target specific areas and come up with innovative ideas to make use of waste elsewhere.
Focus groups were also used to gain a better understanding of the waste we create and to ensure that colleagues are aware that ownership and accountability is everyone’s responsibility.
Our business-wide waste strategy has shaped our thinking and we now see it as both a valuable commodity and a way to mitigate the use of new resources. We now have three clear objectives:
1. Reduce waste.
2. Improve our recycling streams.
3. Explore further options for our current environmental waste streams (including revenue).
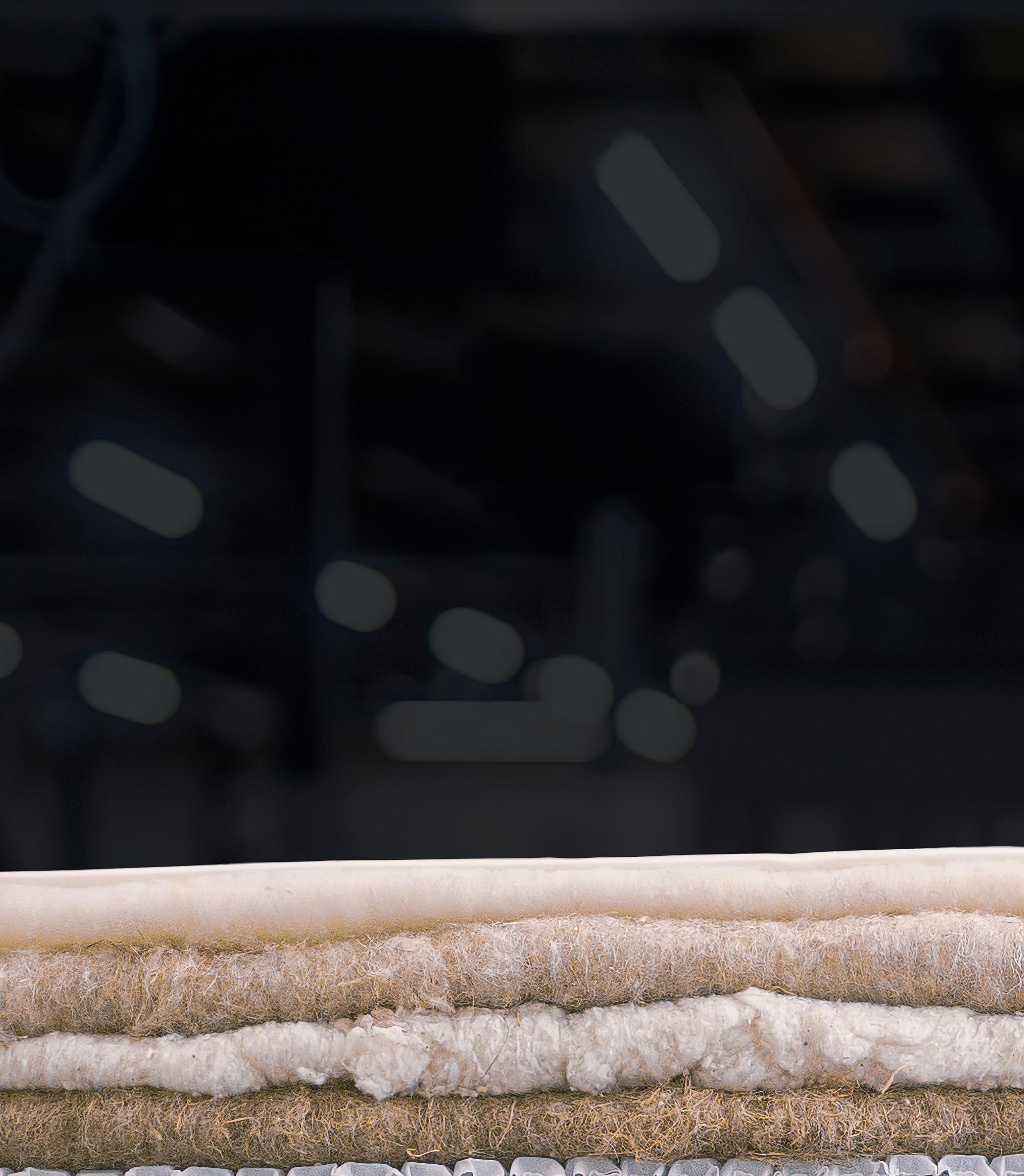

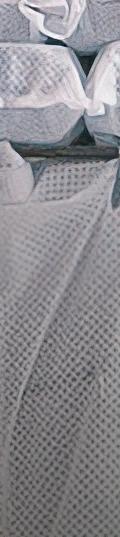
Responsible sourcing
Reducing environmental impact, conserving resources, whilst maintaining or improving product performance and cost-effectiveness is a huge focus for our team. We continue to work hard to identify, develop and use more sustainable materials.
Progress to date includes:
• Our relationship with British Wool and their Traceable Wool Scheme means we can trace the wool we use down to the farm. It also guarantees animal welfare and fair payment for farmers.
• We’ve partnered with Scottish luxury woven accessories manufacturer, Alex Begg, to upcycle their clean, high quality textile offcuts to use in our mattresses. (See page 34.)
• We are looking to introduce natural coir as a replacement for fillings such as horsehair and cattle tail where a guarantee provenance or animal welfare can not be found.
• We have reviewed and updated our suppliers to make sure we only work with businesses who can provide responsibly sourced (and organic where appropriate) cotton, mohair and peace silk.
• The same commitment to responsible sourcing applies to the manufacture of our bases, divans, ottomans and headboards. We only use FSC® certified timbers.
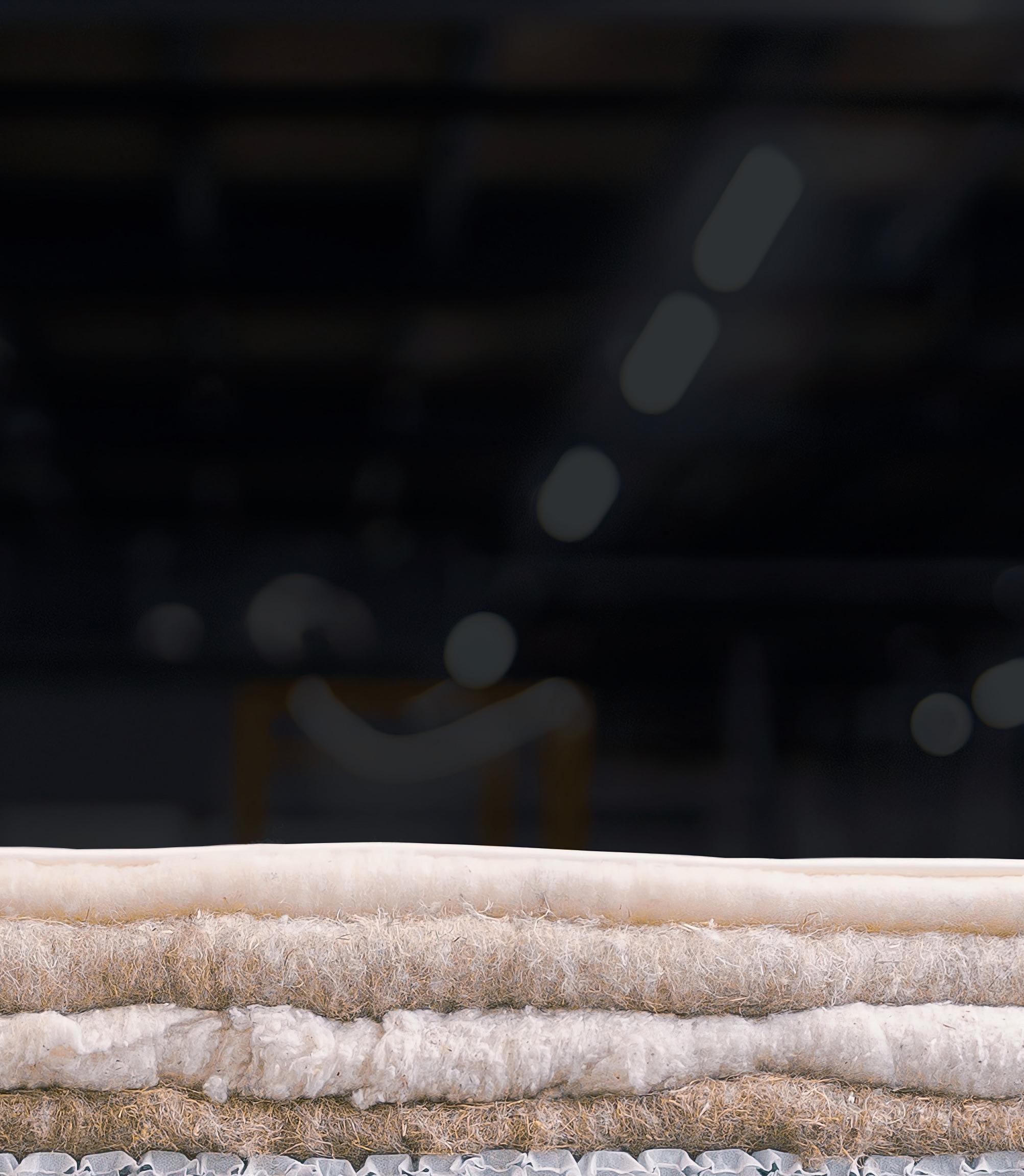
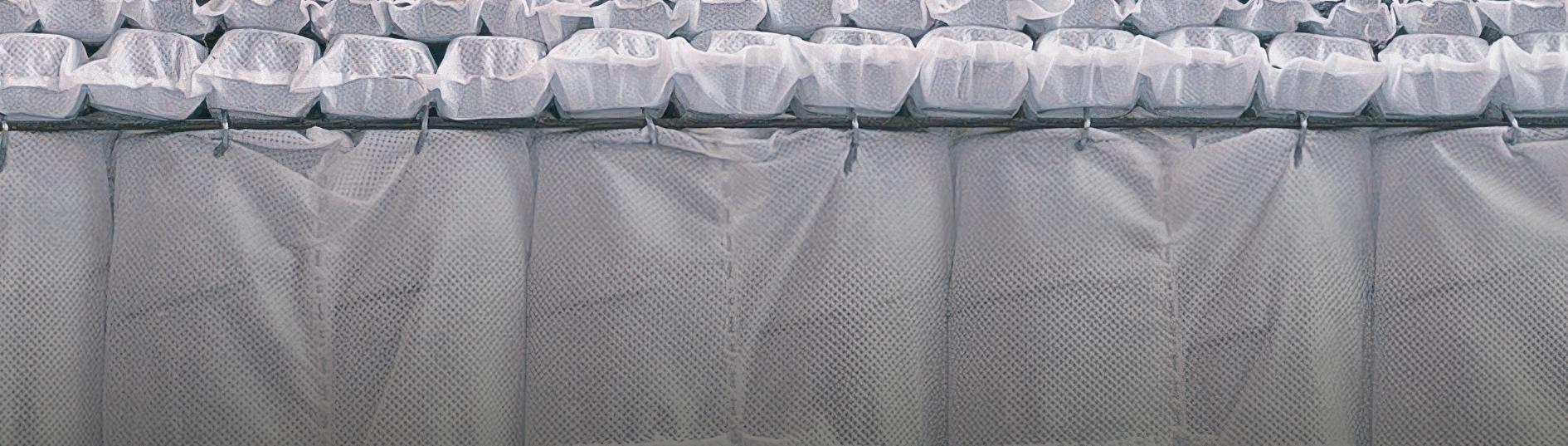

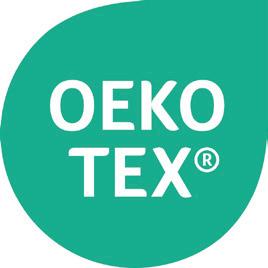
Chemical reduction
Weaving our fabric ourselves using naturally fire-retardant wool creates a luxurious sleep surface, while eliminating the need for FR chemical treatments.
Weaving
our FR chemical-free fabric saves over 28 tonnes of chemicals each year. (Based on previous FR processes)
100%
glue-free and foam-free construction
Our own spring systems are ultrasonically welded together instead of glueing. Plus, our ultra-responsive MicroHD spring layers remove the need for foams or latex. This has improved the recyclability and re-usability of our mattresses and removed circa 75 tonnes of hot melt glue annually from our mattresses since we revolutionised our production model.
Certifications
Our approach to circularity is evidenced by our commitment to gaining internationally recognised certifications.
Cradle
to Cradle Bronze certification
We’re proud to have achieved Cradle to Cradle Bronze (V3.1) certification for all our glue less springs. This means our springs have been assessed on material health, material reutilization/circularity, renewable energy and carbon management, water stewardship and social fairness. We were the first spring manufacturer to achieve this certification. We are now working towards V4, this prioritizes action across five sustainability focus areas: Material Health, Product Circularity, Clean Air & Climate Protection, Water & Soil Stewardship, and Social Fairness.
OEKO-TEX certified fabrics
Our polypropylene and polyester glueless springs are certified to STANDARD 100 by OEKO-TEX. This is a label for textiles that have been tested and proven to be free from harmful chemicals and substances. Based on rigorous tests and updated annually, OEKO-TEX is an international standard which provides peace of mind for our customers.
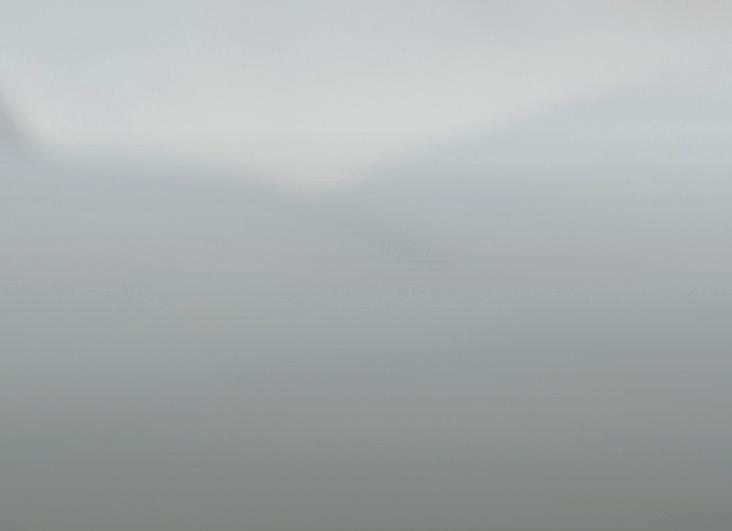
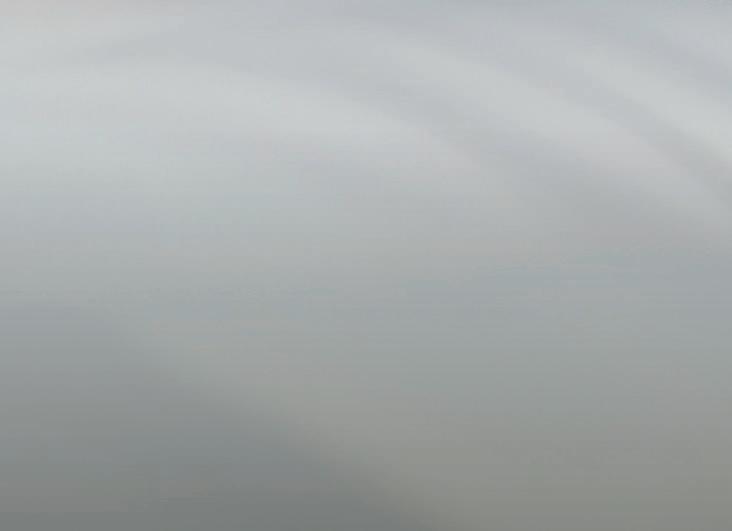
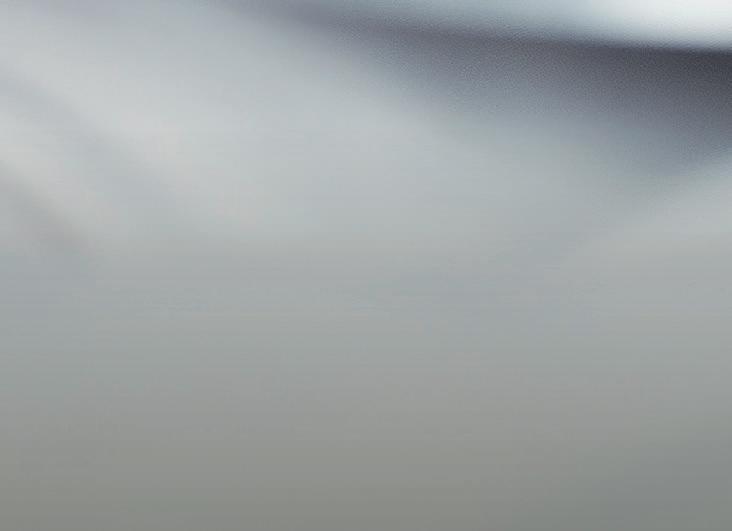
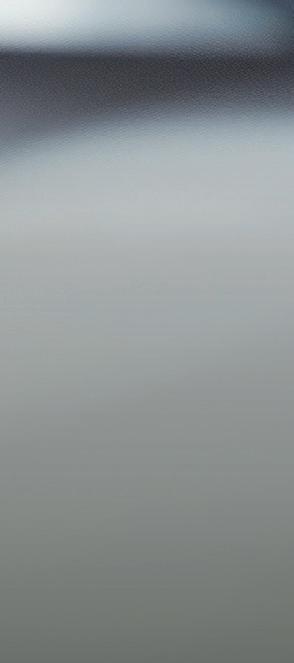
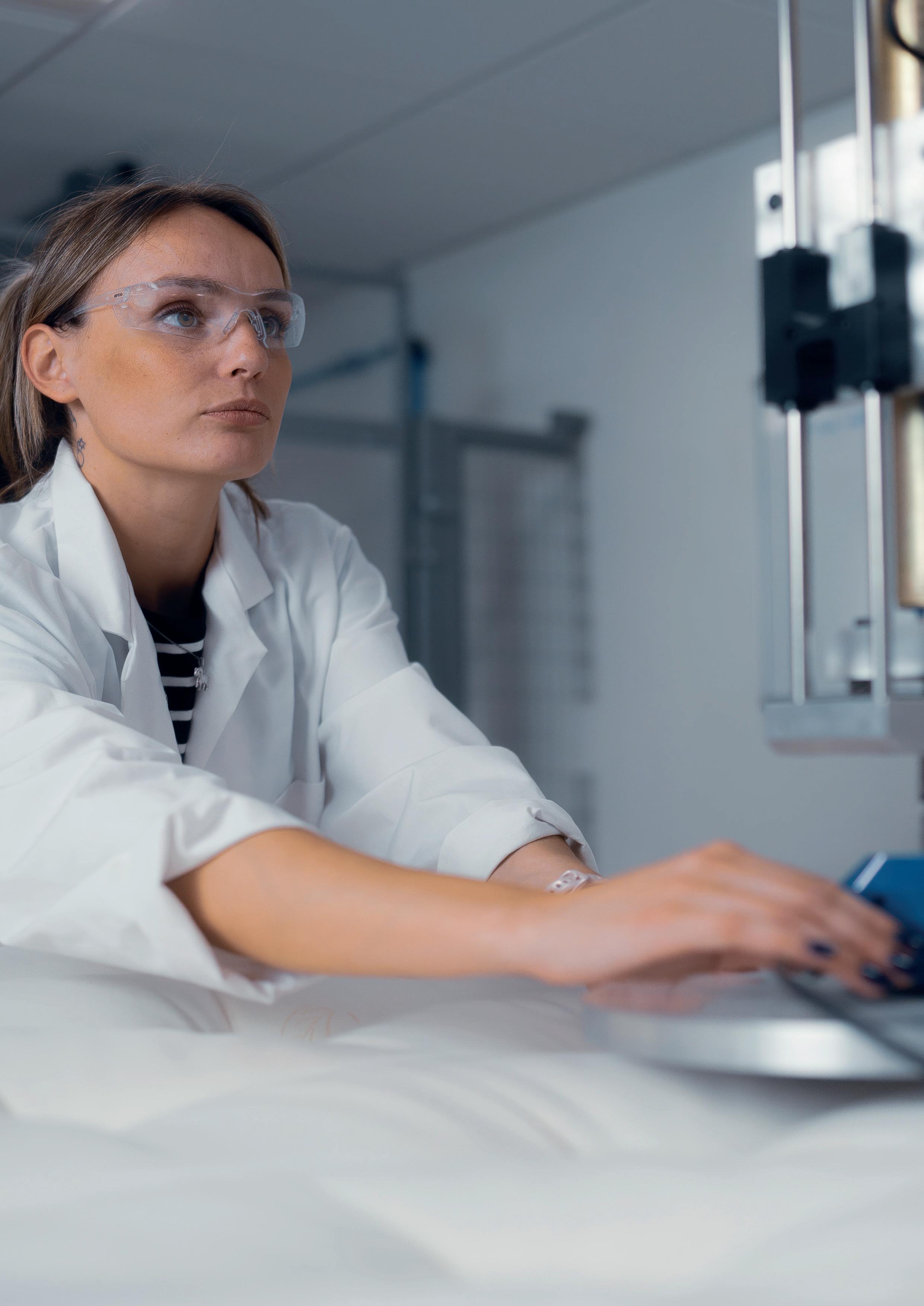
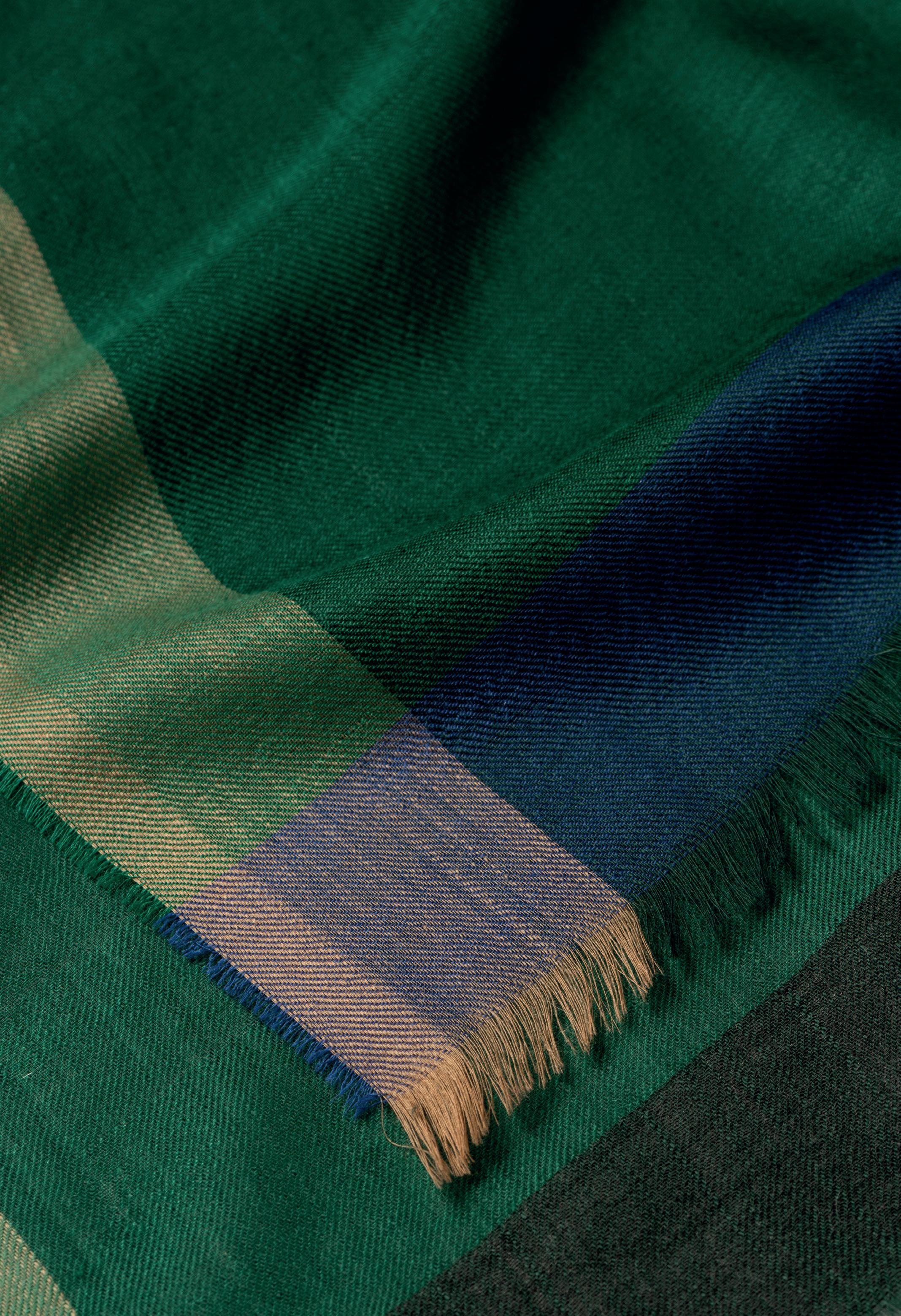
Alex Begg Partnership Case Study
Making upcycling fashionable
We’ve partnered with Scottish luxury accessories manufacturer, Alex Begg, to upcycle their clean high-quality textile offcuts to use in our mattresses.
The partnership aims to stop unused fabrics from being incinerated. Instead, we are turning Alex Beggs’ surplus luxury cashmere into sumptuous filling pads for our beds.
This replaces the need for over 1,400kg of virgin cashmere each year. Saving 2 tonnes of CO₂e from transport alone.
This innovative partnership supports our continued efforts to pioneer sustainable mattress manufacturing. Redirecting otherwise wasted resources and enabling us to responsibly source this luxury fibre for our range of mattresses.
The collaboration is also part of our bigger plan to decrease carbon emissions from direct operations by 95% within the next decade.
“We immediately recognised the business’s innovative approach to ethical and eco-friendly business practices, which is a value held at the core of the Harrison Spinks brand.
We then found that introducing this initiative offered a dual solution, as not only could the brand divert cashmere surplus away from incineration plants, significantly reducing carbon impact, but it has also allowed us to source high-quality materials with less impact on the environment.”
Richard Essery, MD, Harrison Spinks Technology
COMMITMENT:
WE WILL CONTINUE TO MEASURE OUR SCOPE 1, 2 AND 3 EMISSIONS TO HELP US UNDERSTAND AND REDUCE OUR IMPACT.
Over the last five years, we have been measuring our Scope 1 and 2 emissions. Because understanding our full impact is important to us, we also include Scope 3 emissions too.
Scope 1 (direct emissions) relates to our vehicles and gas consumption. In the last financial year, we saw a 23% decrease due to our electric vehicle policy, swapping 18 diesel vehicles for hybrid and electric cars, as well as a 20% saving in gas consumption due to process efficiencies in non-woven fillings and weaving finishing.
This equates to an overall reduction in Scope 1 emissions of 22% in the past financial year.
Scope 2 (indirect emissions) relates to our purchased energy. The majority of our manufacturing sites in Leeds are now powered by renewable energy. We have managed to reduce our consumption by 14% across all sites, again through process efficiencies.
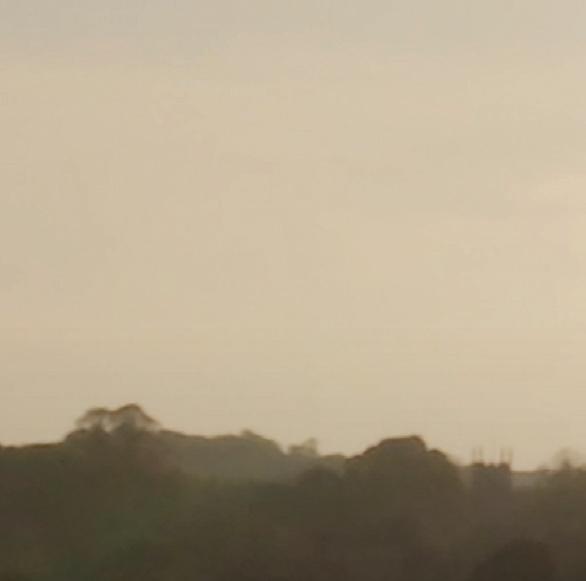

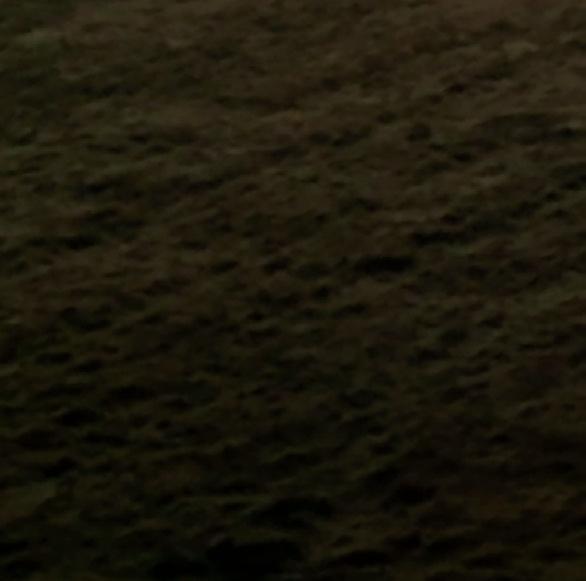
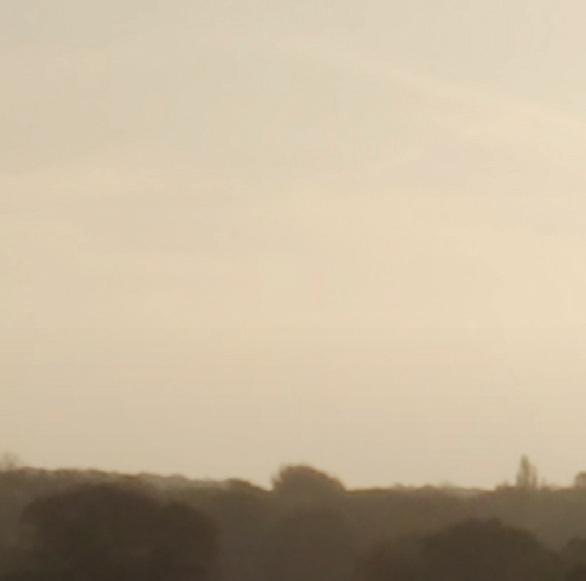
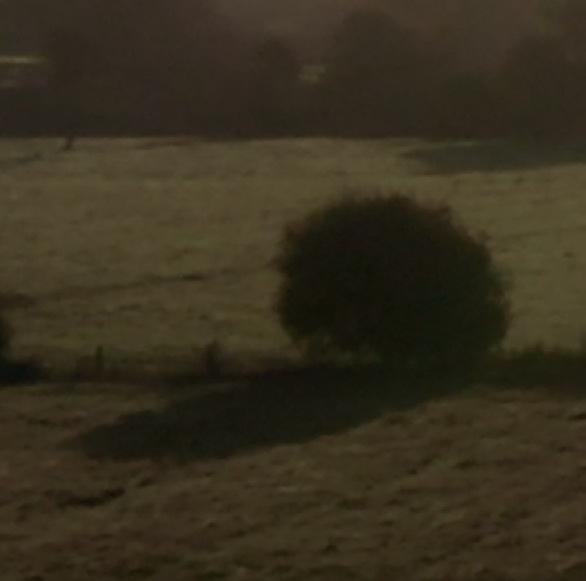
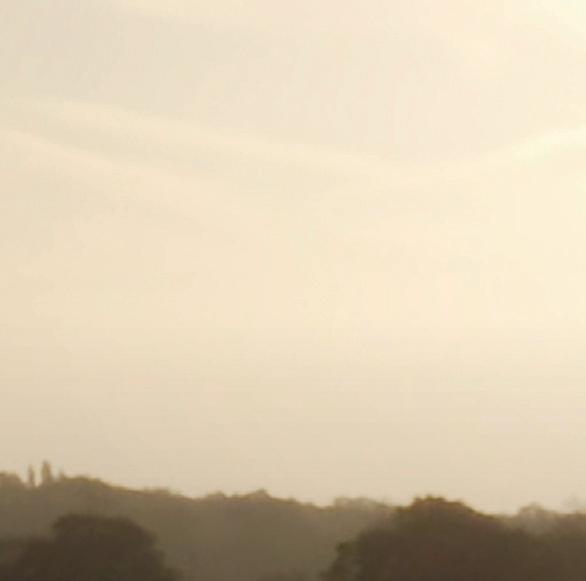
Overall this has resulted in a total Scope 2 saving of 11% based on these reductions and the general benefits of using green energy.
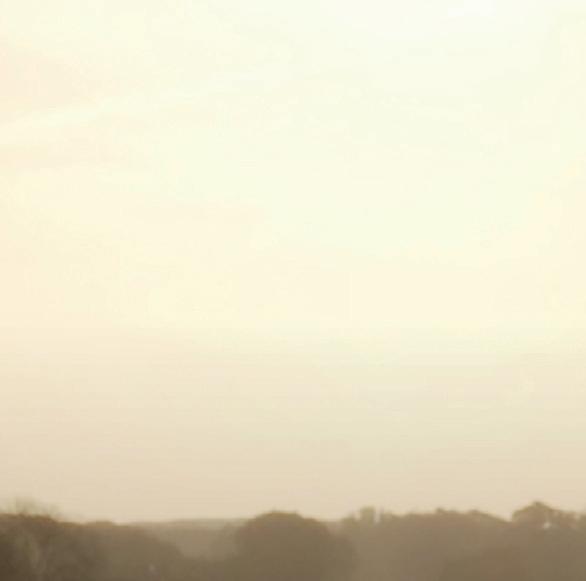

“We are committed to reducing our scope 1, 2 and 3 emissions and in doing so, we are helping our industry partners reduce their scope 3 emissions too. Our aim is to help our customers choose components for their products with the least environmental impact.”
Darren Marcangelo, MD, Spinks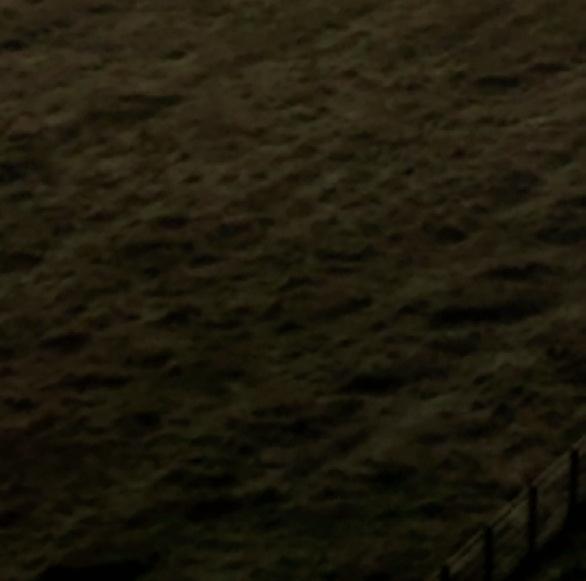
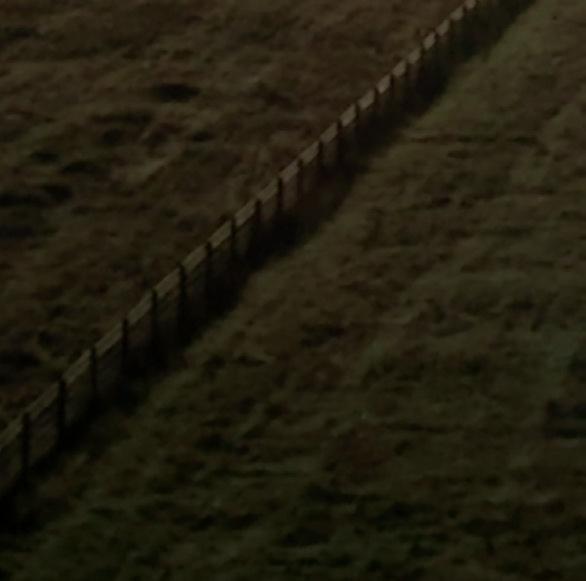


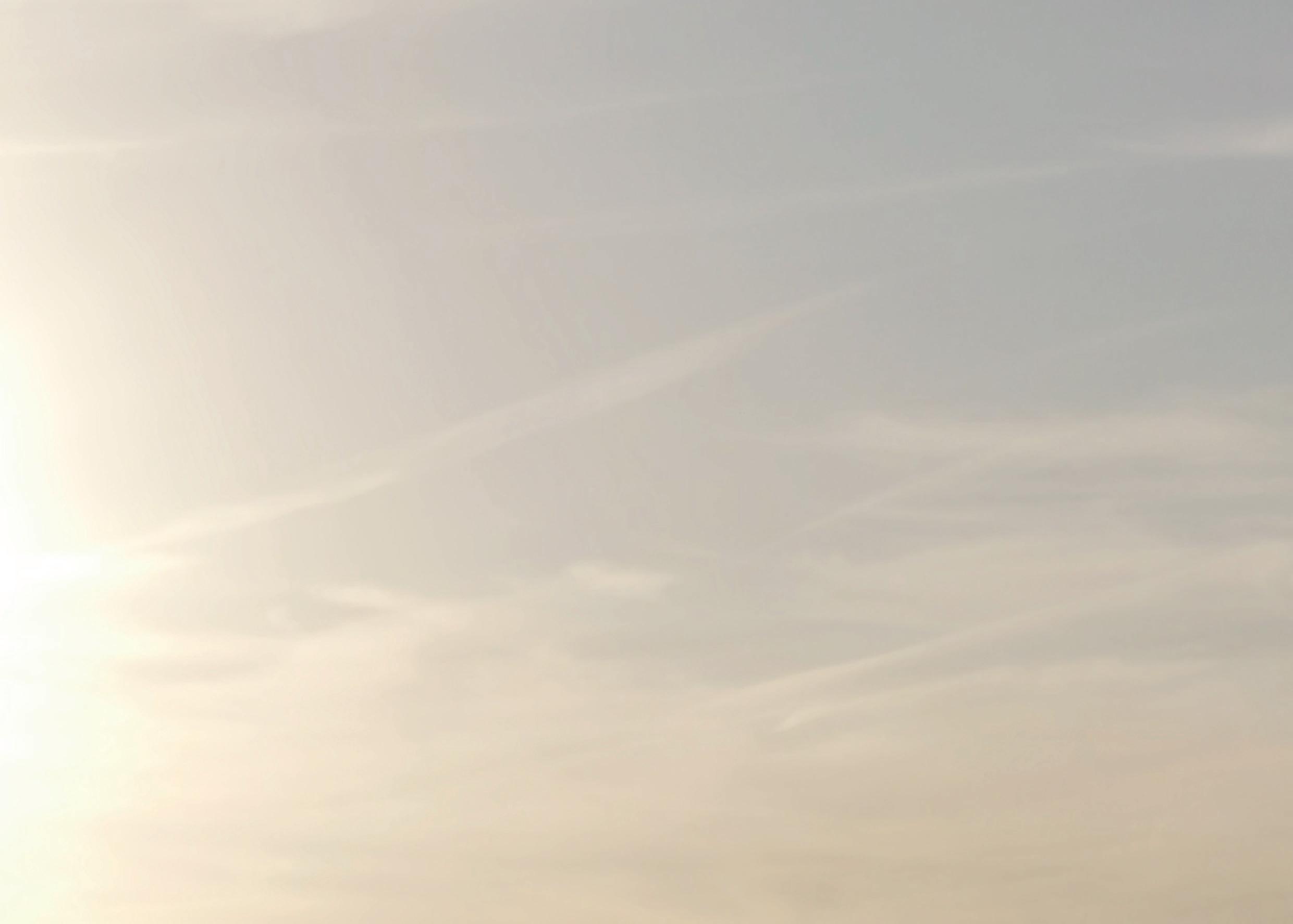
Scope 3 emissions include emissions related to our supply chain and business travel.
We have been collecting this data over the last three years, which relates to circa 93% of our emissions, which has helped form our strategy for total emissions reduction, under the framework of SBTi.
We’re already one of the largest growers of industrial hemp in the UK. The carbon benefits of growing hemp are huge. Based on last year’s crop of 210ha, the crop absorbed 3,150tCO₂ which is the equivalent of our full Scope 1 and 2 emissions in year 22/23.¹
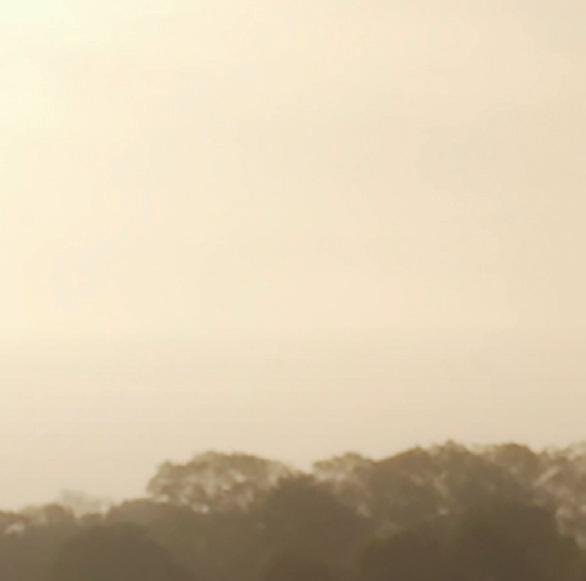
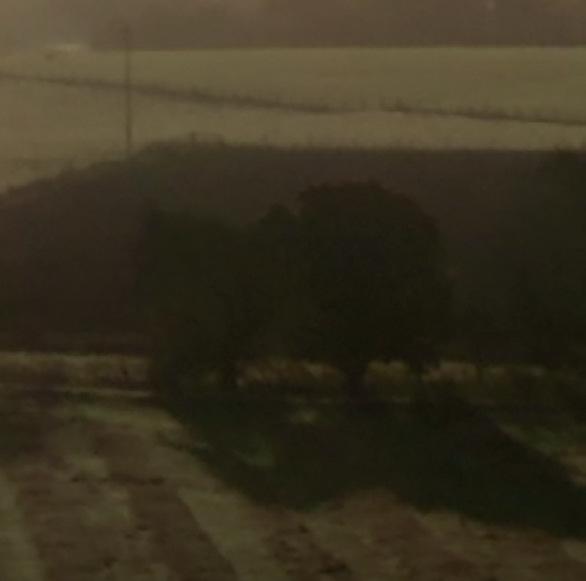
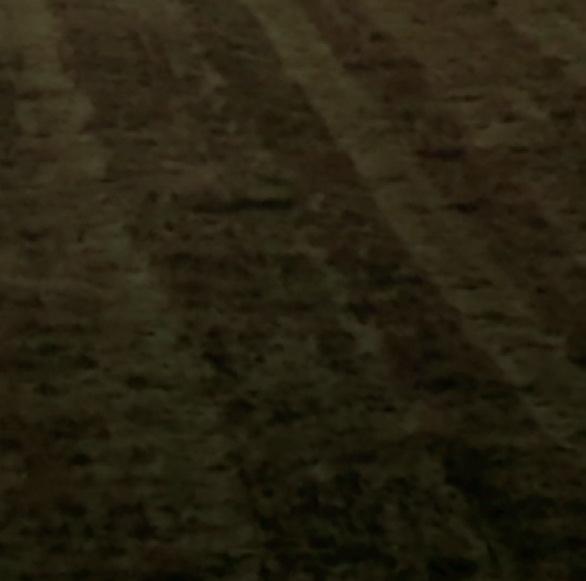



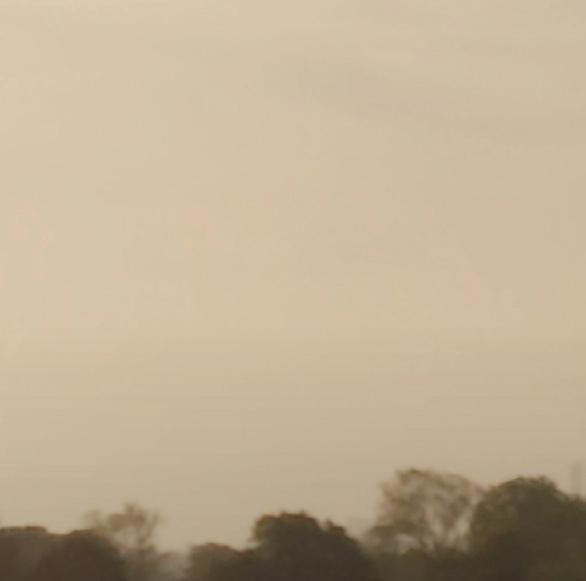
¹ University of Aberdeen “Regenerating Scotland’s Hemp Industry for Health, Climate and a Green Economy” Dec 23
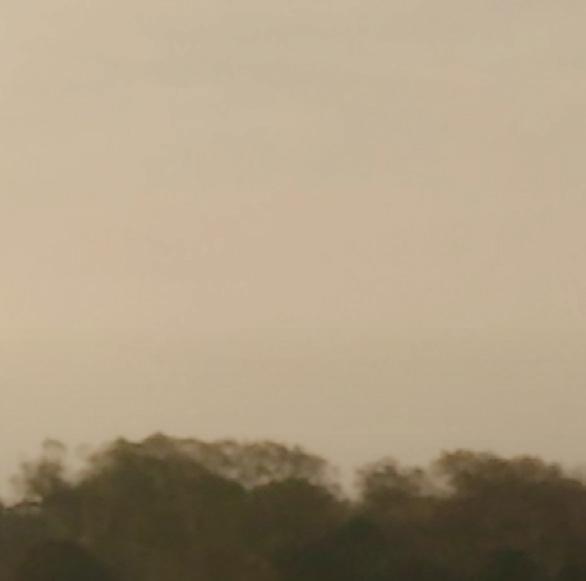
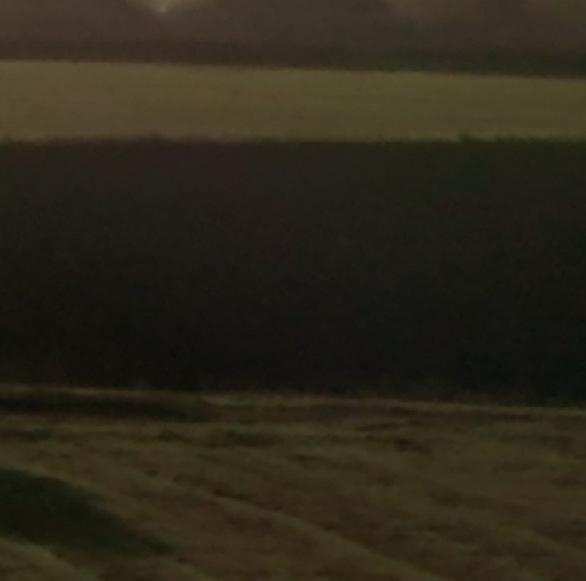
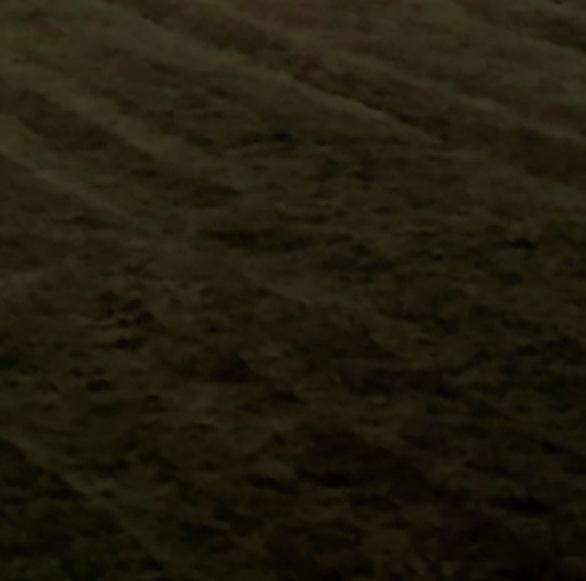

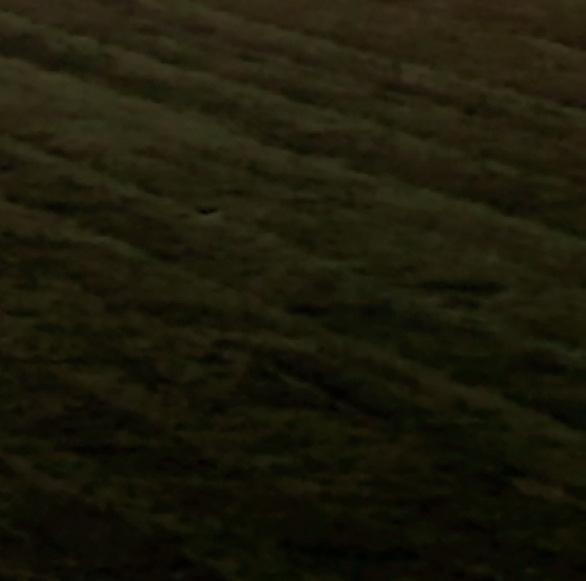
Science Based Targets initiative
COMMITMENT:
WE WILL BE NET ZERO BY 2050, SETTING A CLIMATE PATHWAY IN LINE WITH THE SCIENCE BASED TARGETS INITIATIVE.
In August 2022 we committed to reducing our emissions in line with current climate science. Through the Science Based Targets initiative Net Zero Standard, we’ve joined the Business Ambition for 1.5ºC campaign.
This means we are committed to meeting the long-term target of net zero by 2050, and to holding ourselves accountable to near-term targets in the next 10 years.
We are currently in the ‘committed’ stage of Science Based Targets and are working to get our net zero strategy approved by SBTi.
We’re also a supporter of the National Bed Federation Pledge for Our Planet. A commitment for bed manufacturers to address global environmental damage through sustainable decision-making and taking responsibility for the impact our products have on the environment.
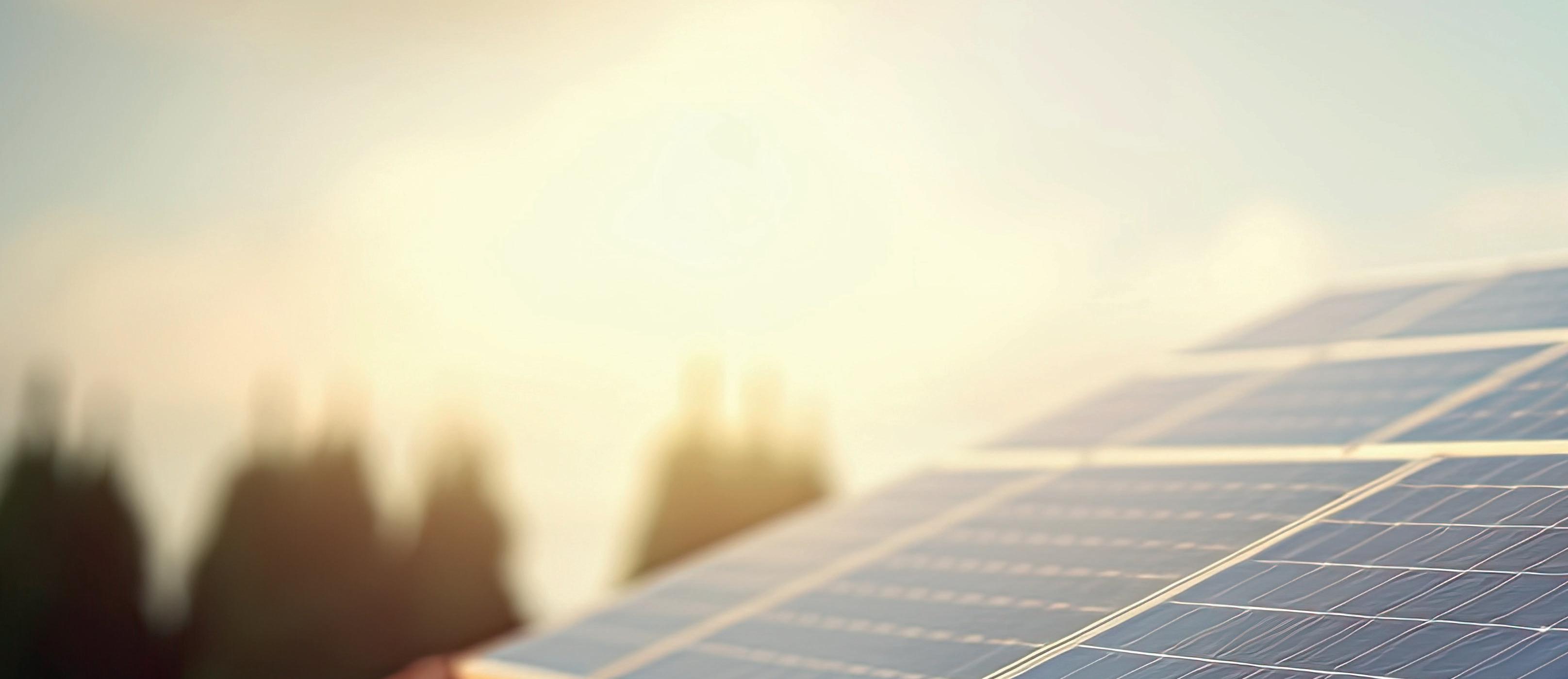
Energy reduction
As a business, we are focused on reducing our energy consumption. To facilitate this we set up an energy taskforce who have delivered process efficiencies across many key areas within the business. Some of the areas we have looked at are as follows:
• Replacing compressors with new efficient models.
• Reviewed equipment and infrastructure identifying air leaks and inefficiencies.
• Reviewed all equipment shut-down procedures.
• Replaced all Leeds factory lighting (where appropriate) with LED.
• Change in production hours. (See page 48.)
To fully understand our energy use, we’ve taken steps to measure energy use by department.
Energy use by department for FY 22-23 compared to FY 21-22
Note: In FY22-23 we added to our wire drawing equipment. Resulting in a slight increase in energy use.

Reducing our emissions by design
We have produced a new pocket coiling machine (Sky300) which will reduce power and raw material consumption.
To our knowledge, this will be the fastest single-head pocket coiler currently available in the world (pat pending).
Sky300 has reduced energy consumption of our pocket spring-making by 60% from our previous process (4.17kWh vs. 1.65kWh).
We aim to share this technology in our sector and beyond to allow others to benefit from these savings. In addition, we have simplified the process to avoid the need for de-coiling. This saves 0.75kWh per coiling device.
Our static ‘no twist’ wire packaging innovation provides significant energy savings too.
Saving approximately 330,000kWh of electricity per annum.
(This is based on 77 wire pay-off swifts rated at 0.75 kWh, running five days per week for three shifts, 48 weeks per year.)
Over the last year we have also reviewed our purchase specifications for the polypropylene non-woven material we purchase to encase our micro coils.
Modifying the polypropylene roll dimensions and increasing the meterage in roll had the following impact.
Digitisation
Thanks to an Innovate UK Sustainable Smart Factory grant, we’re working with the Manufacturing Technology Centre and Bespoke Automation Control Services Ltd to use automatic detection and control to reduce scrap, electricity and emissions.
Our unique approach is helping us meet the Innovate UK Project objectives.
Reducing energy use by 30%, material reduction by 15% and CO₂ reduction by 40%.
Changing
shift patterns to reduce carbon
Representing one of our biggest initiatives within our bed manufacturing division in the last year, we have moved to a four-day week with extended shift hours. With no production taking place on Fridays, we have cut energy use and associated direct and indirect carbon emissions.
Centralised operations have also moved to a compressed 4.5-day week, with a vastly reduced number of people commuting to the office on Fridays.
The longer and more efficient working days, as well as increasing production facilities, has improved employee satisfaction and raised productivity.
Transport
We’re determined to take a more responsible approach to logistics.
We’ve updated our fleet of HGVs to more efficient models and optimised route planning to reduce the number of trailers on the road each day from an average of seven to six.
This simple step saves over 60,000 delivery miles each year.
We’ve also moved to an electronic proof-of-delivery system. Replacing the paper system which used over 250,000 pieces of paper per year.
Our company car fleet is now all hybrid or electric. We will continue to monitor EV and hybrid technology for our HGV fleet. Currently, the infrastructure isn’t at the level we’d need to support our daily deliveries.
The Wild Ingleborough programme Case
Study
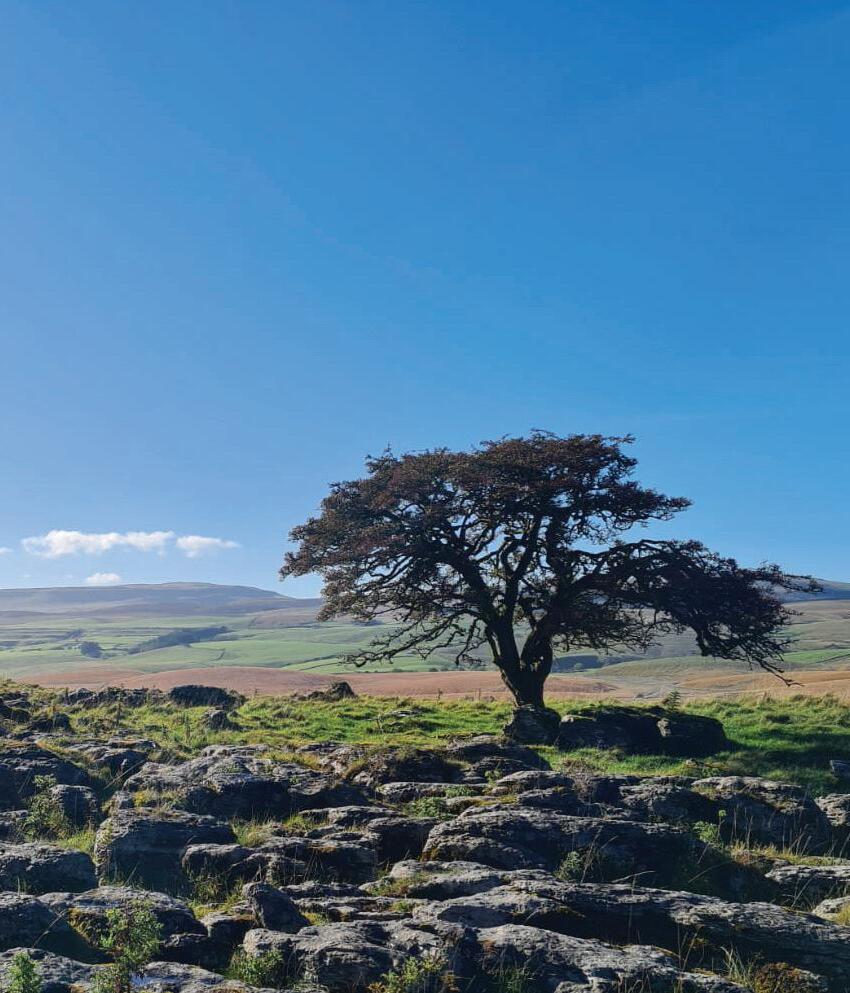

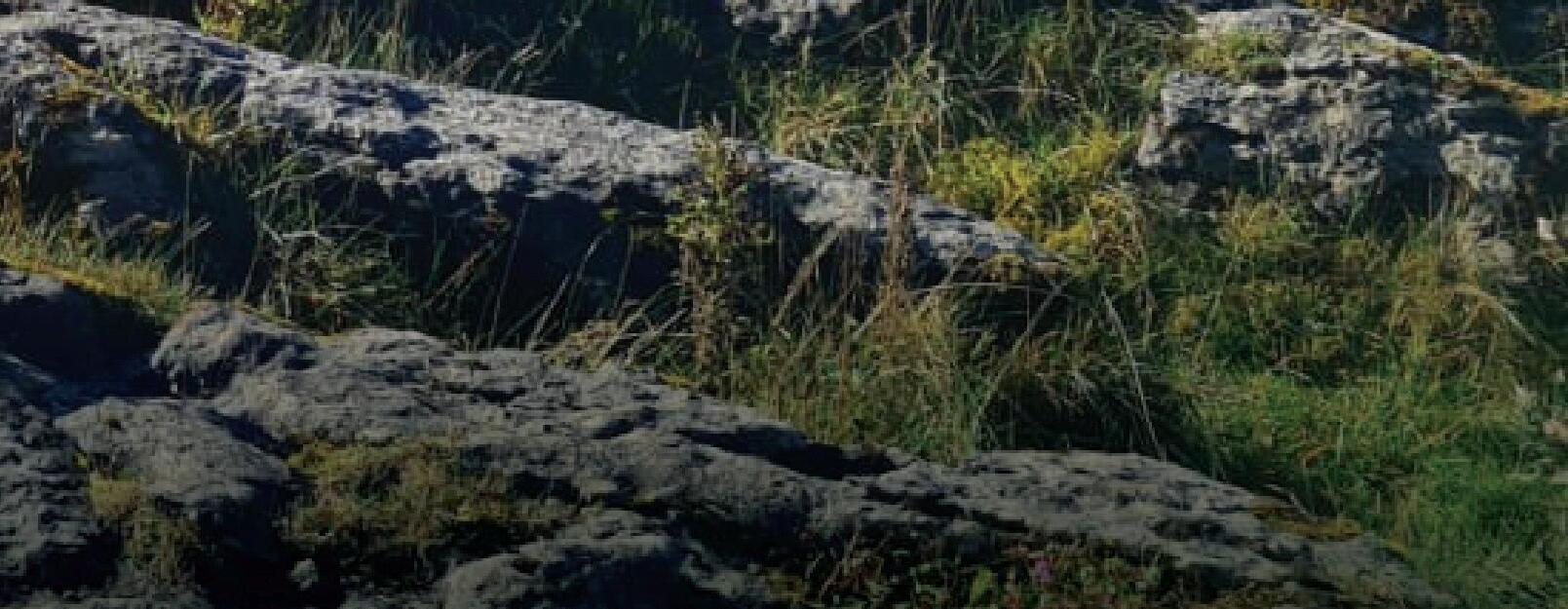
Switching from offsetting to rewilding
With offshore options lacking the transparency we were looking for, we decided to focus our efforts a little closer to home.
The Wild Ingleborough programme is a long-term commitment to address climate change and landscape-scale habitat restoration, led by Yorkshire Wildlife Trust with WWF, Natural England, University of Leeds, United Bank of Carbon and The Woodland Trust.
Working with the local community, its goal is to allow nature to recover in parts of North Yorkshire and the Yorkshire Dales. This includes natural regeneration and restoration of land, the recovery of rare and endangered plant species, increasing employment in wildlife conservation and supporting local farmers to promote environmentally positive production.
We feel supporting the Wild Ingleborough programme, instead of overseas carbon offsetting, is a much more responsible and transparent way in which we can help tackle climate change and wildlife habitat loss. It’s why we are investing significantly in the programme over the coming years.
“Wild Ingleborough is a fantastic initiative which aligns with our purpose and values as a family business rooted in Yorkshire.
We are very excited to be part of such a progressive and groundbreaking project which will drive forward our understanding and response to both nature restoration and climate impact.
What we are focused on is shifting the agenda forward to emphasise measurable action and finding long-term alternatives to more traditional carbon offsetting to create a positive outcome here in this country.”
Louise Ellis-Jones, Harrison Spinks Non-Exec Director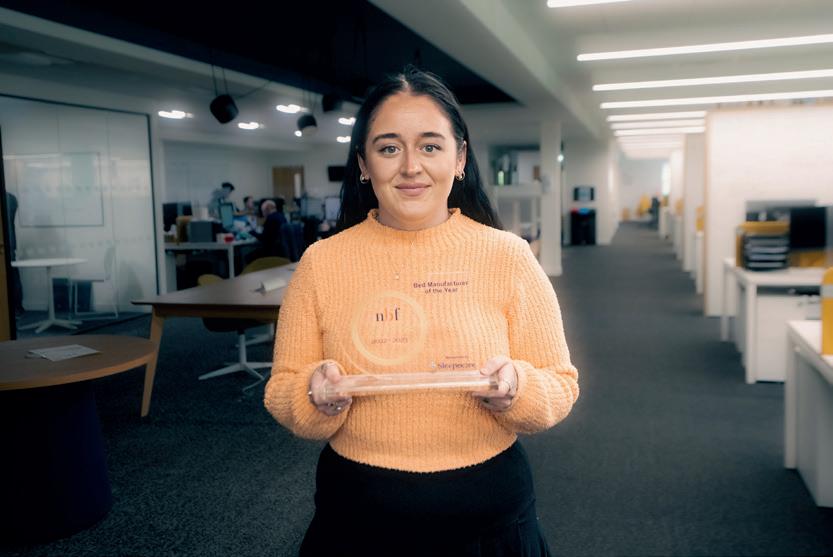
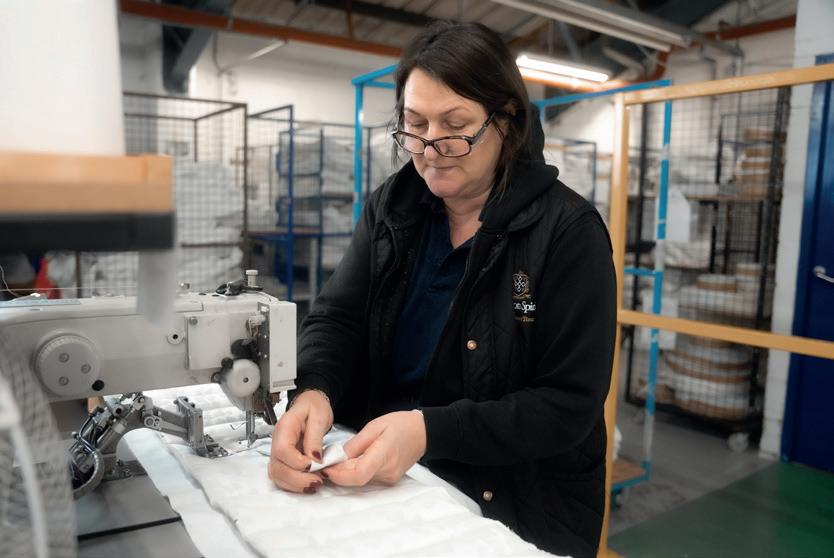

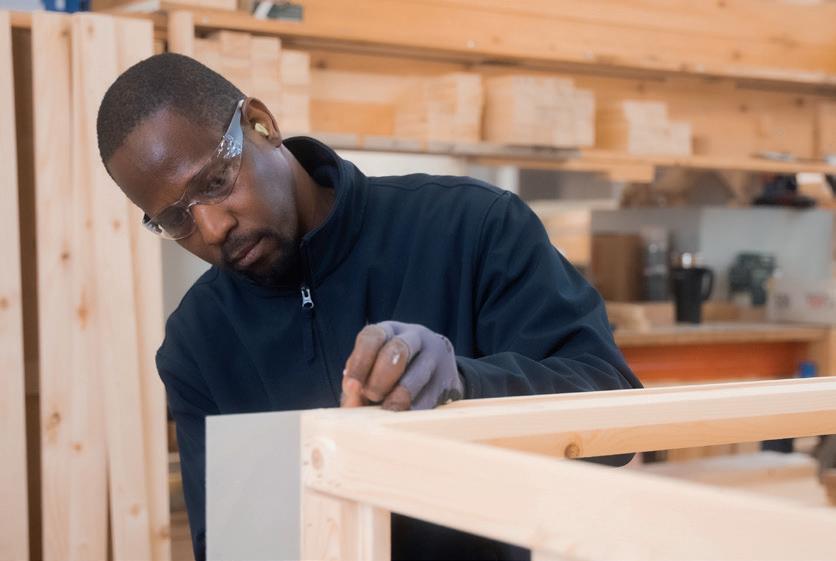
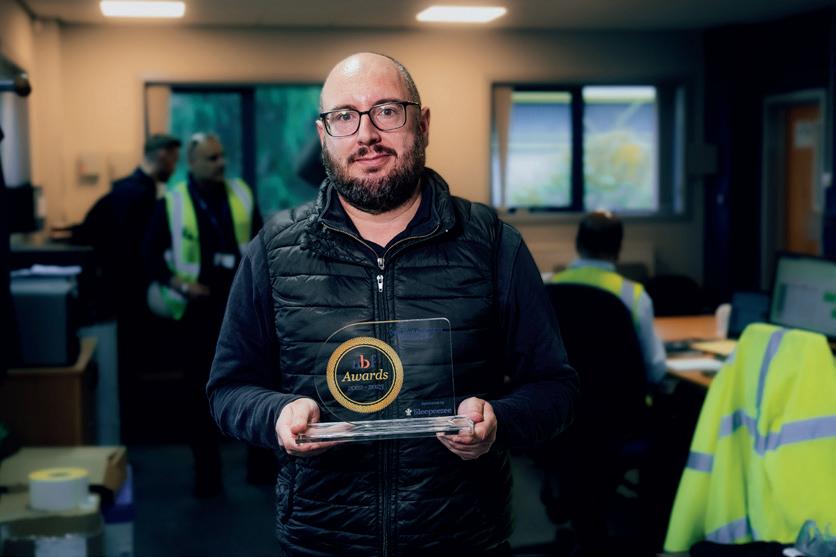
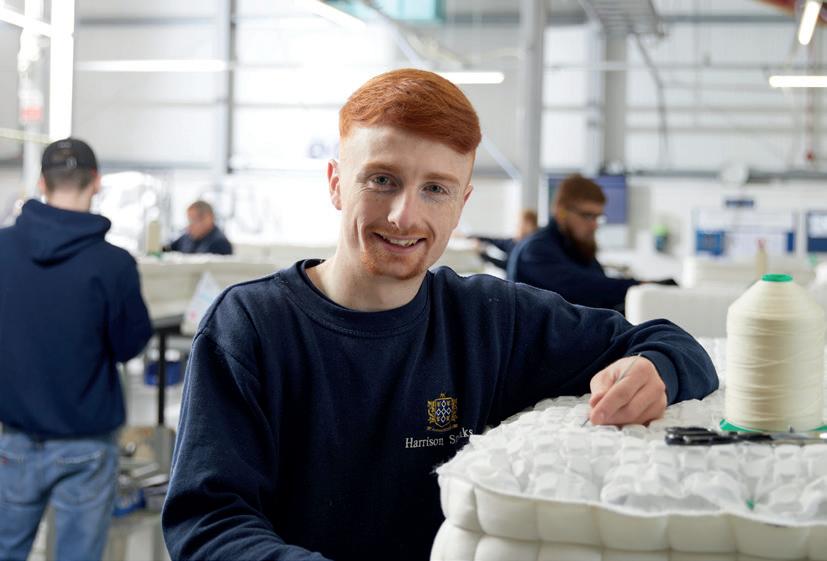
Social update
We are committed to play our part in creating happier and healthier communities. Making a difference to people’s lives by improving social mobility, promoting wellbeing and active lifestyles, and importantly, creating a business and community that is open and inclusive.
As a major local employer, we feel we can deliver these commitments in so many ways. We have therefore formalised a clear social strategy committed to the development of our people and our community. We’ve already started to make significant changes:
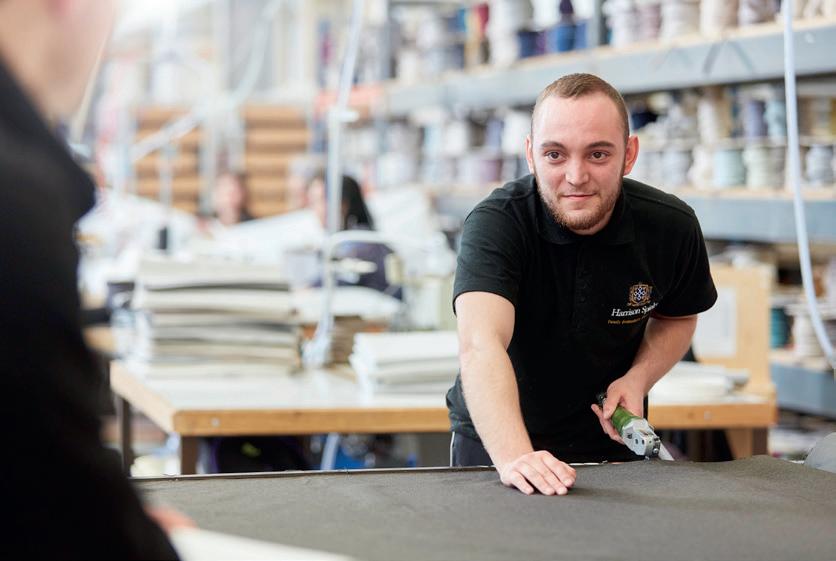
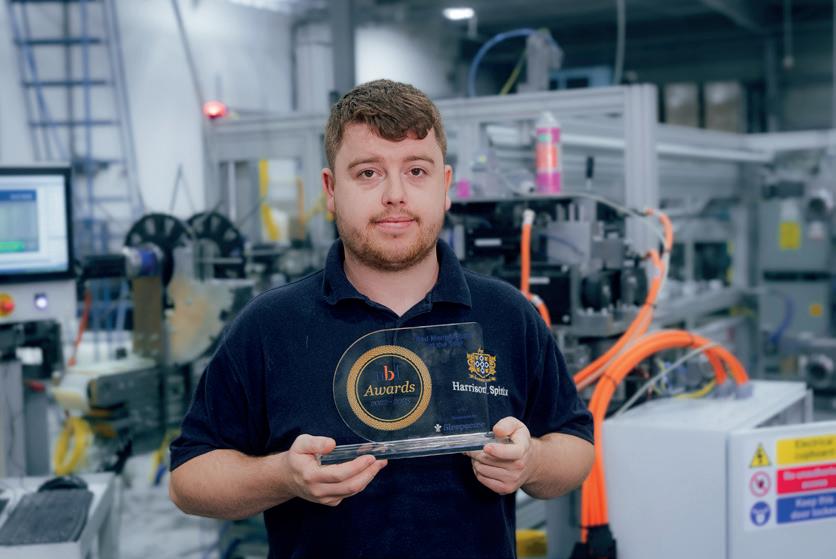
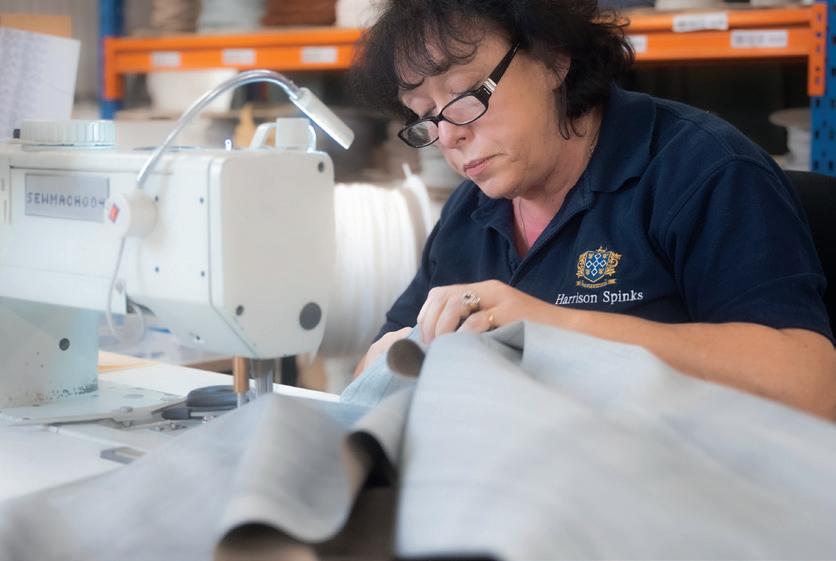
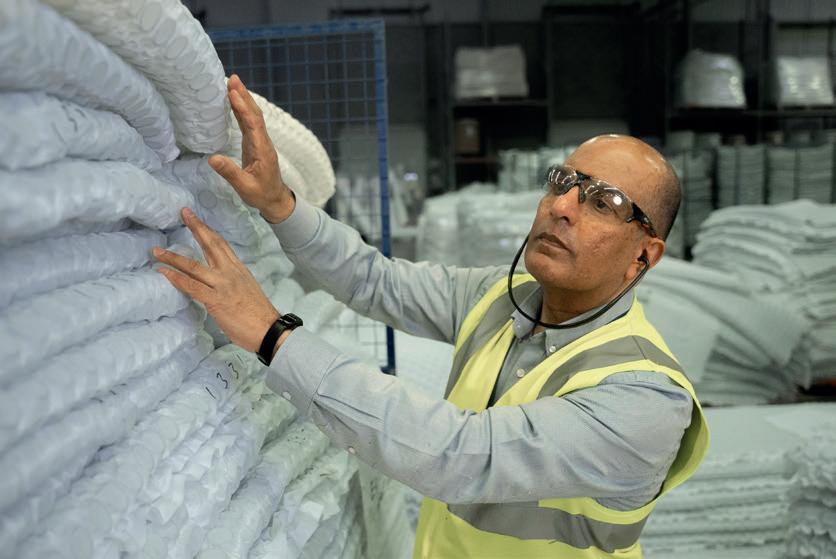
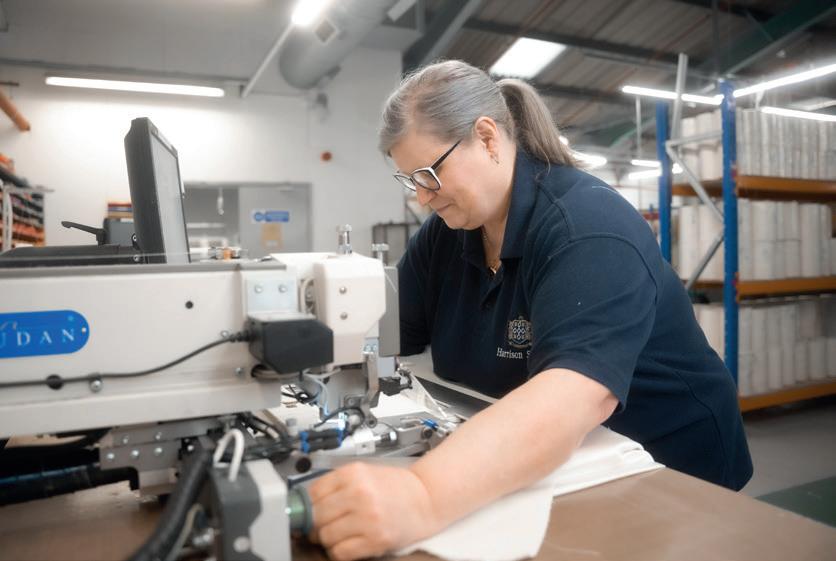

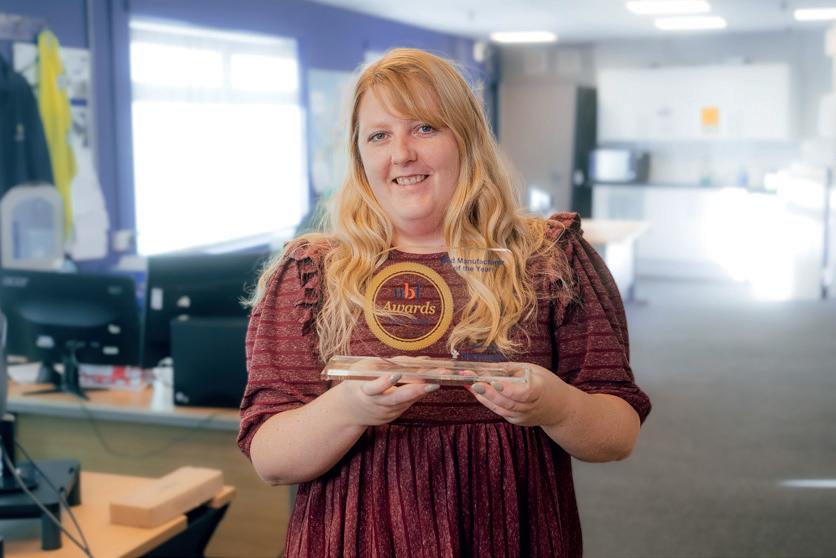

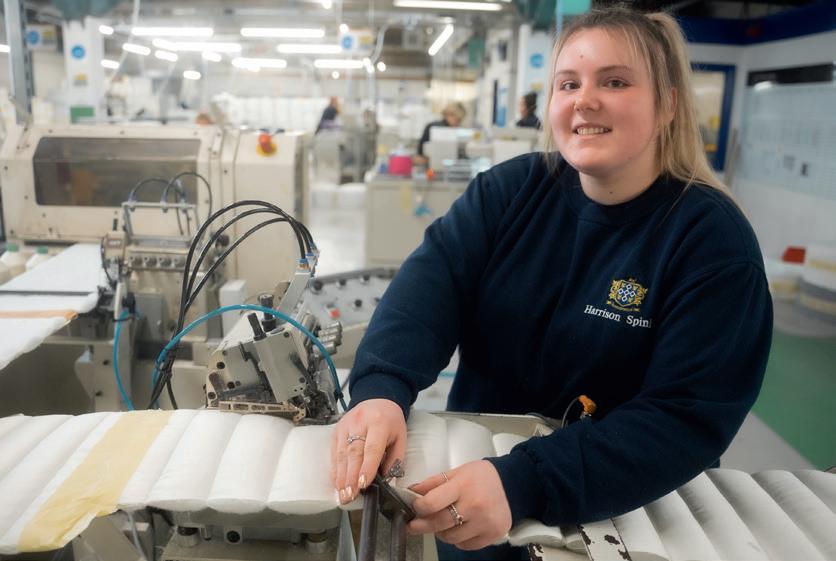
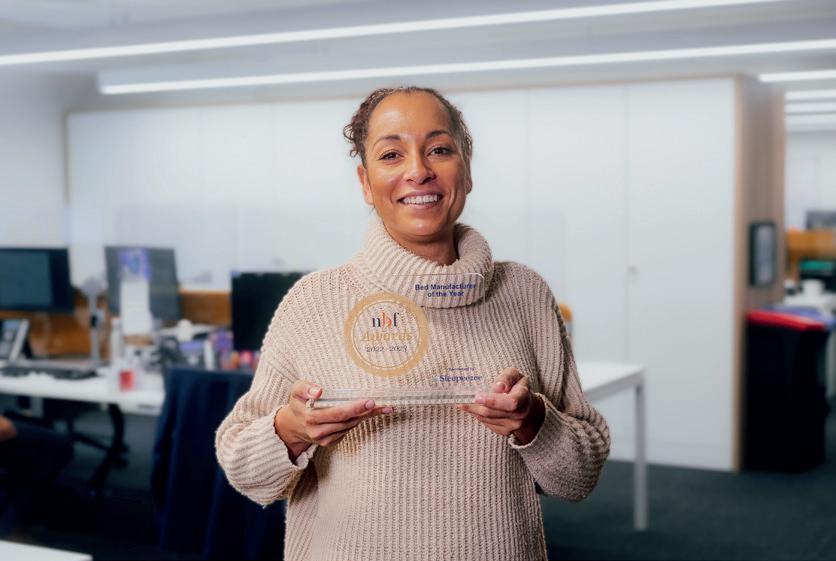
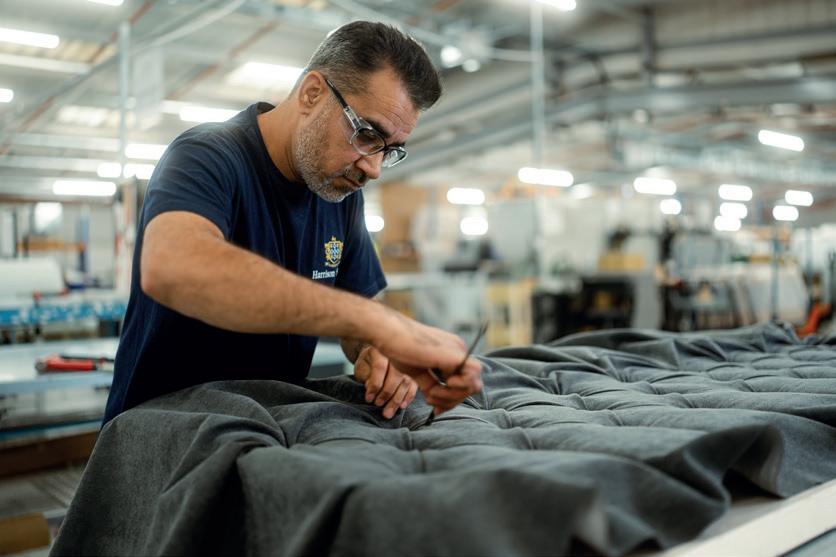

1. Investing in our colleagues to give them the skills and confidence, as well as the health and wellbeing opportunities, they need to succeed.
2. Put into action programmes to increase diversity across all areas of the business.
3. Strengthen our charitable partnerships to make sure we are making the biggest difference to the people who need it most.

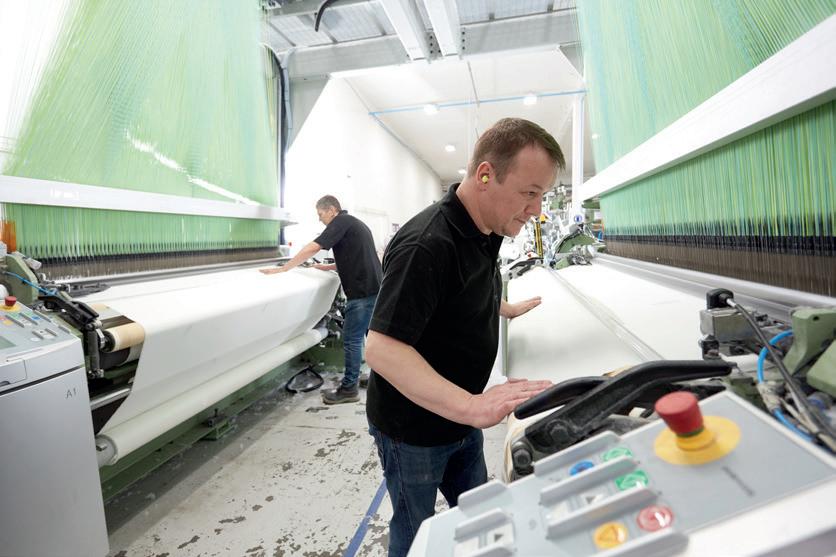
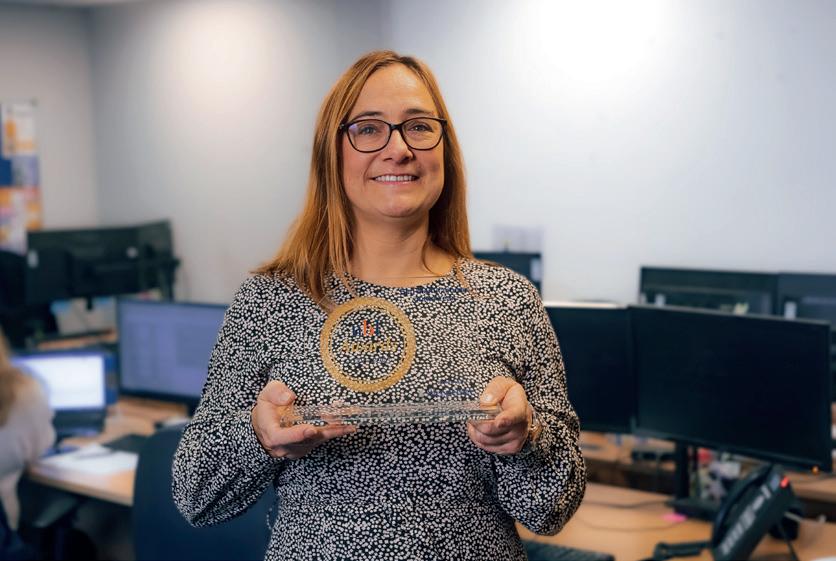
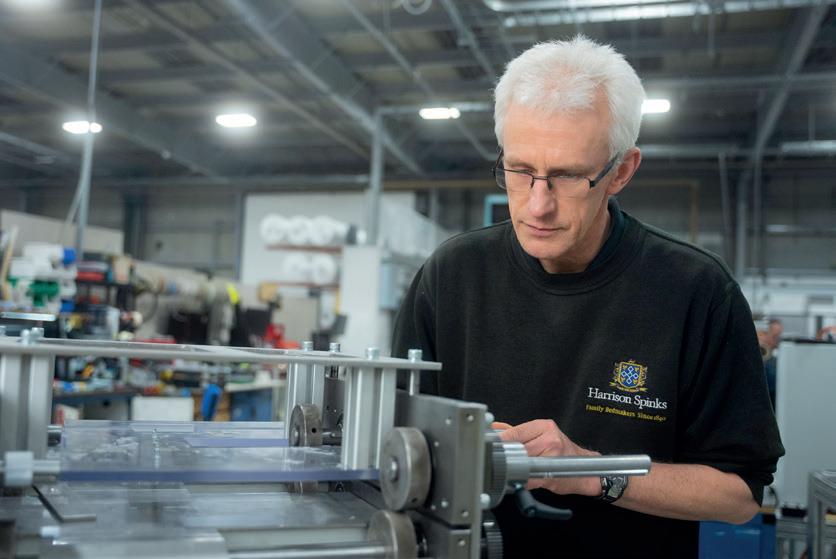
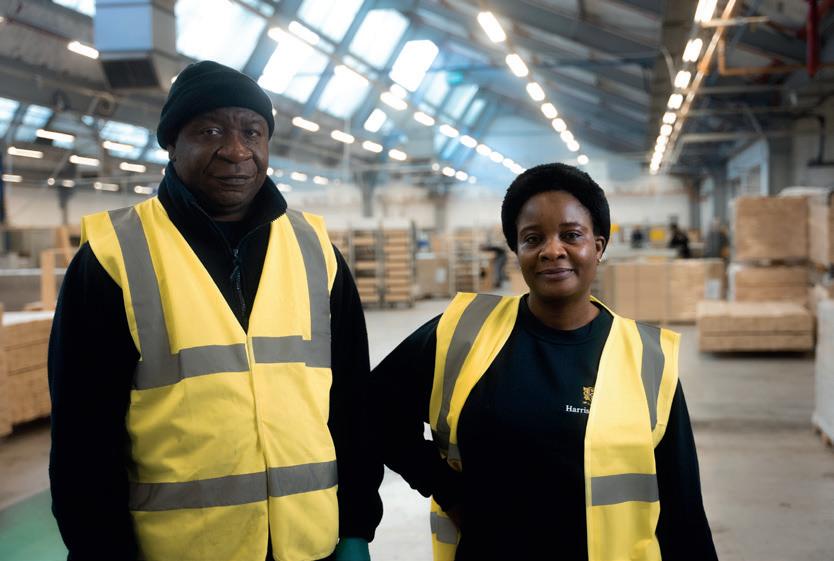

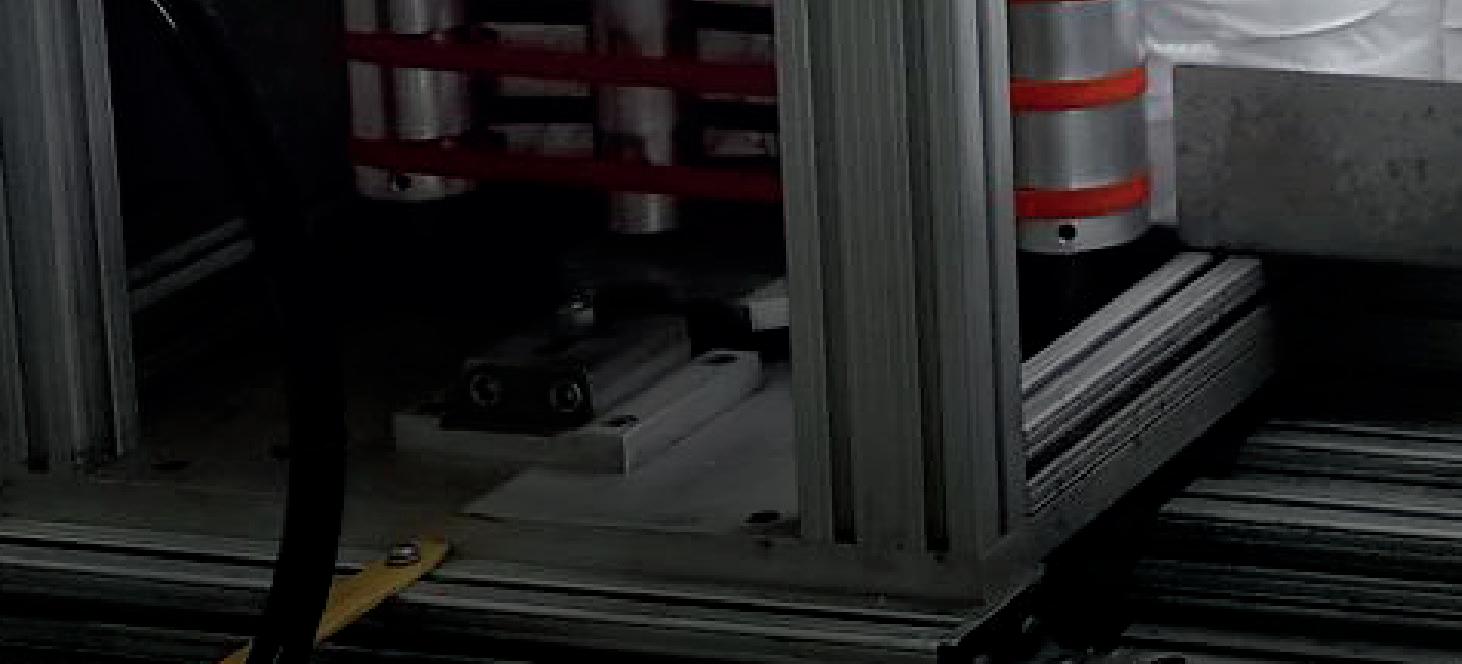
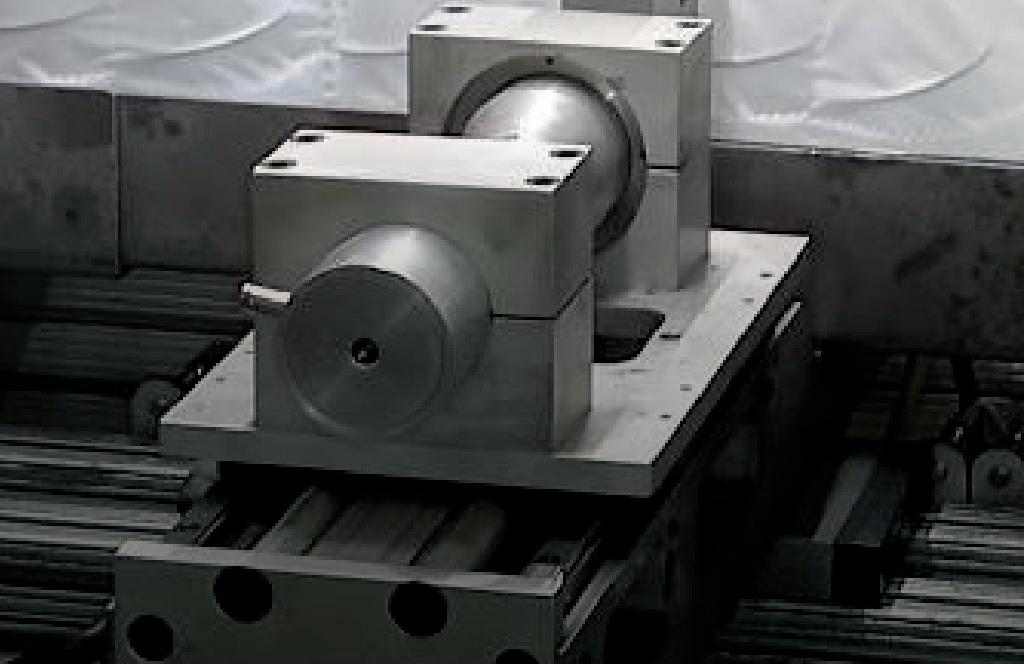

Our people COMMITMENT:
WE WILL BE RECOGNISED AS AN INCLUSIVE EMPLOYER WHO MAKES A POSITIVE DIFFERENCE TO PEOPLE’S LIVES.
Modern
slavery
To ensure modern slavery and human trafficking is not taking place within our business or supply chain, we require our Tier 1 suppliers to provide us with their updated Modern Slavery Statement each year. Plus we’re undertaking additional training across our procurement and management teams to further our knowledge and learn how we can support anyone who may be vulnerable.
Our apprenticeship strategy
We’ve implemented an apprenticeship strategy to attract the best talent into the business, as well as using apprenticeships to upskill our current workforce.
5% of all our vacant roles will be filled by apprentices.

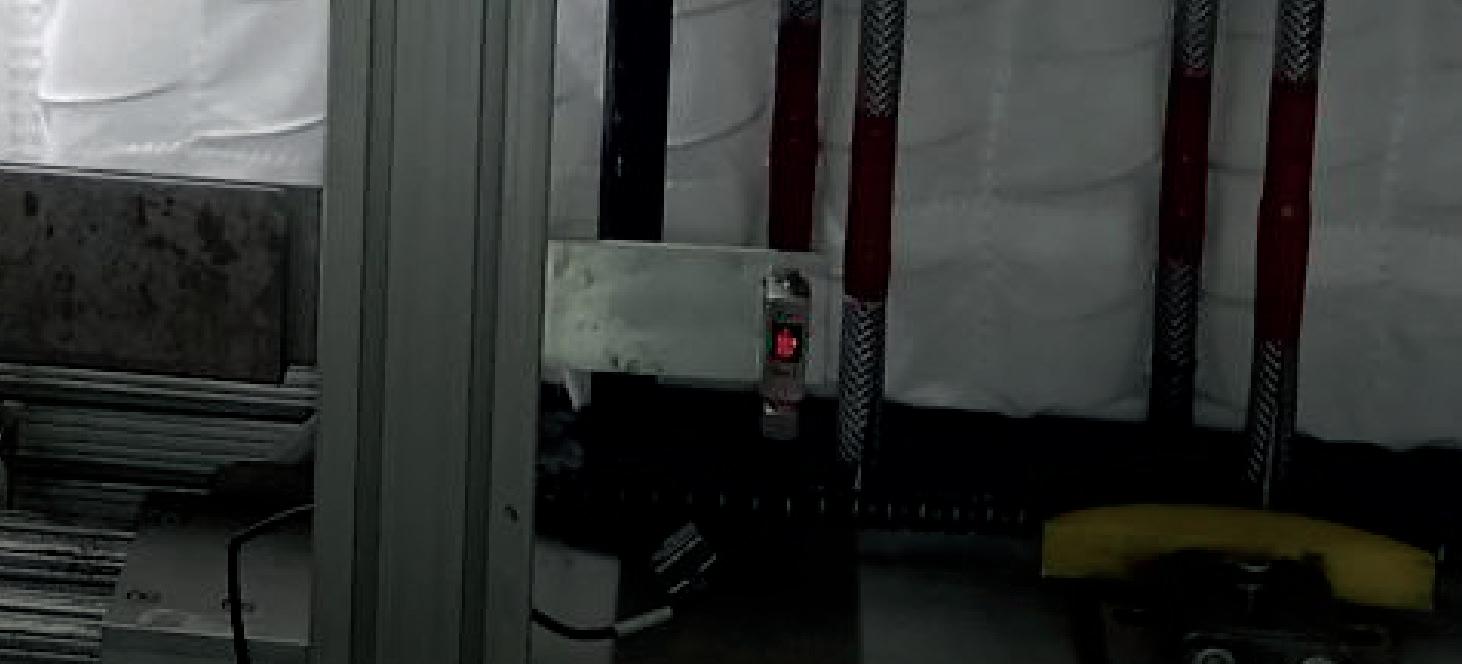
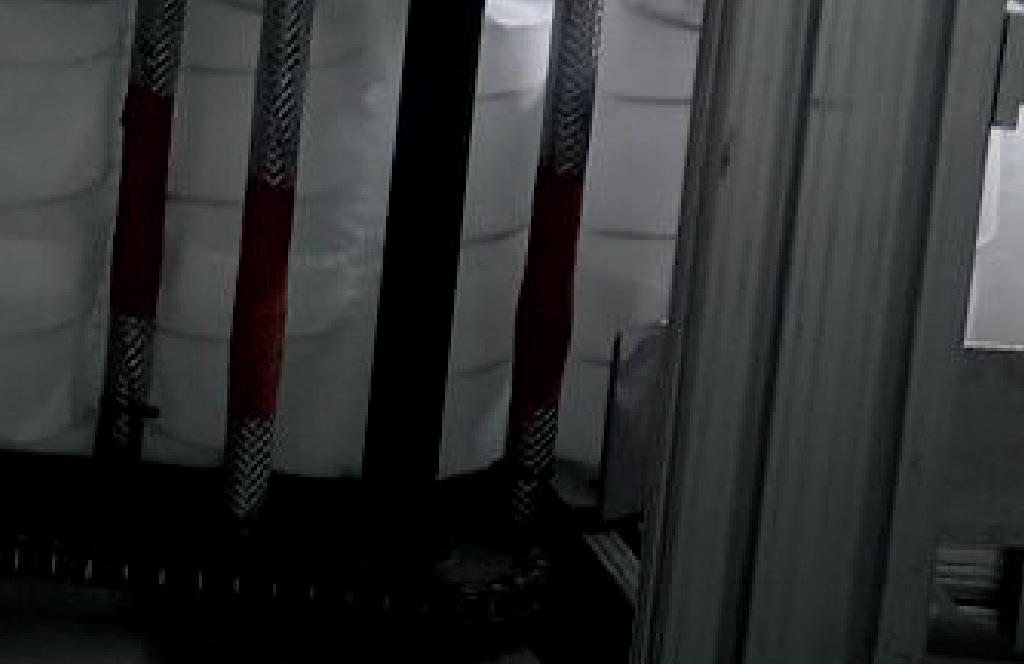
People development
We invest in the growth and upskilling of our workforce through continuous learning and professional development opportunities.
In addition, we have implemented a new appraisal system and are rolling out individual development plans. This will ensure everyone receives the relevant training, allowing them to develop the skills and knowledge essential for personal development while aiding business succession planning for key roles.
Upskilling our leaders
In addition to our apprentice strategy, we are upskilling over 50 of our team leaders and managers. Focusing on the soft skills needed to deliver their roles most effectively.
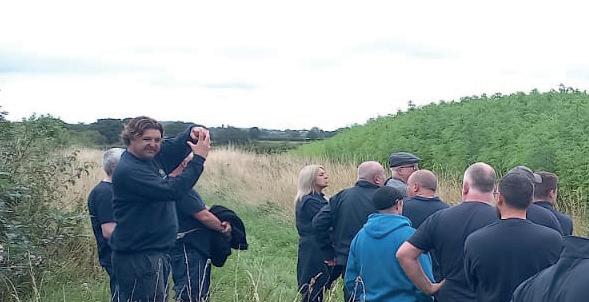
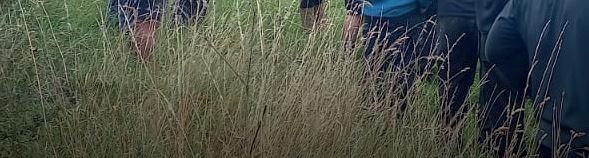
Helping prioritise colleague work and home life
After consulting with our colleagues, and following a trial period in late 2022, from January 1st 2023 we changed our bed factory to a single shift working four longer days, instead of five standard days operating a two-shift system.
This initiative has been hugely successful and will deliver improvements in both health and wellbeing, as well as productivity.
Changes to our office-based support functions followed shortly after. Switching from a five-day week to a compressed 4.5-day week, with a greater focus on flexibility and hybrid working.
To support colleagues longer-term, in 2023 we funded an increase in employer pension contributions by 1%.
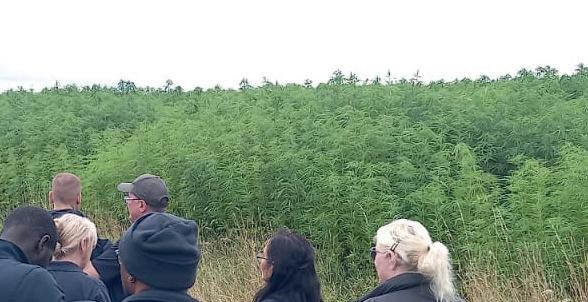
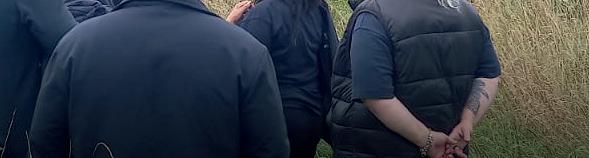
Creating happy and healthy champions
We feel it’s important that all colleagues understand our entire business model, not just the area they work in. Our farm visits play a huge part in this. This year, 80 team members have attended tours at our farm to broaden their knowledge of our natural story, including animal welfare, hemp production and to truly understand how we do things differently.
In 2024 we expect to increase farm visits to circa 300 and to embed this as part of our induction programme.
Our focus on Equality Diversity & Inclusion continues
We have developed an ED&I strategy to help us become an even more diverse workforce.
We are continuing to work with local charities to look at employability schemes, promoting us as a diverse employer, ensuring job adverts are using inclusive language, advertising roles beyond the mainstream job routes and using a diverse interview panel.

We’ve identified that women make up only 20% of the workforce in our manufacturing departments.
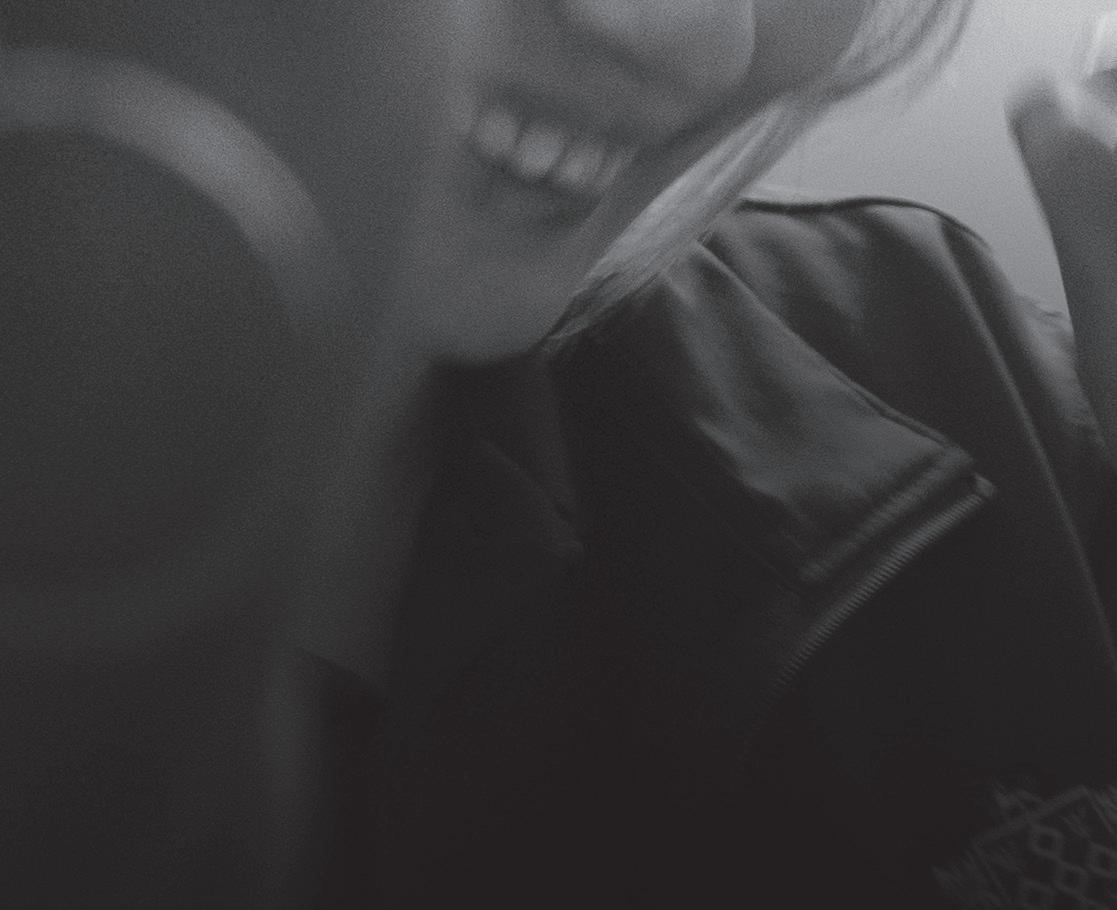
But we’re working hard to address this.
We are actively engaging with women across manufacturing events, webinars and social media. We’re also attending STEM careers events to promote opportunities within Harrison Spinks.
Our goals for the future include:
• Continuing our support of flexible working patterns.
• Engaging with local schools and colleges to raise awareness of the opportunities for women within our industry.
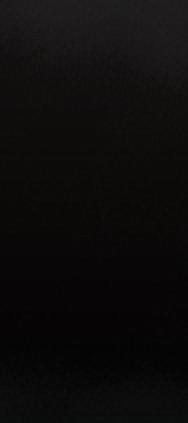

These include:
health checks
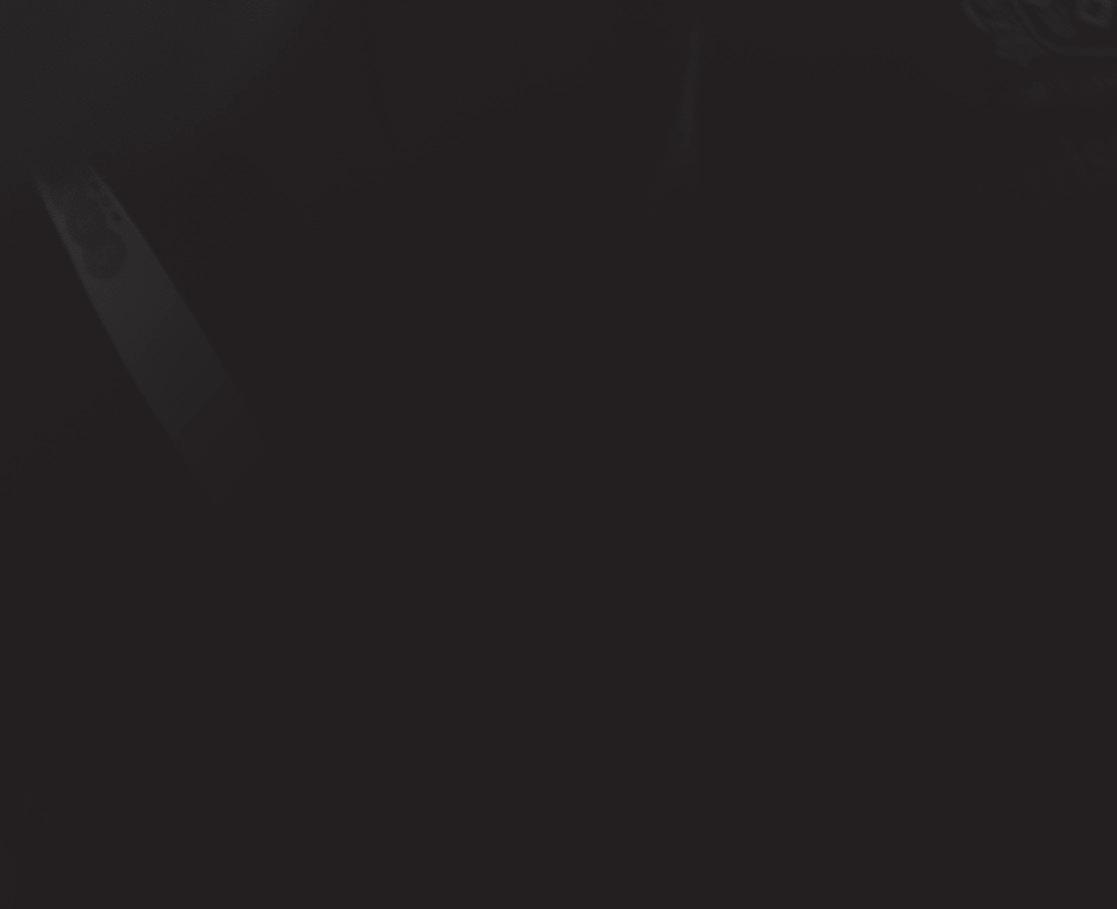
Our health & wellbeing plan
We’re committed to creating a supportive, happy and healthy work environment.
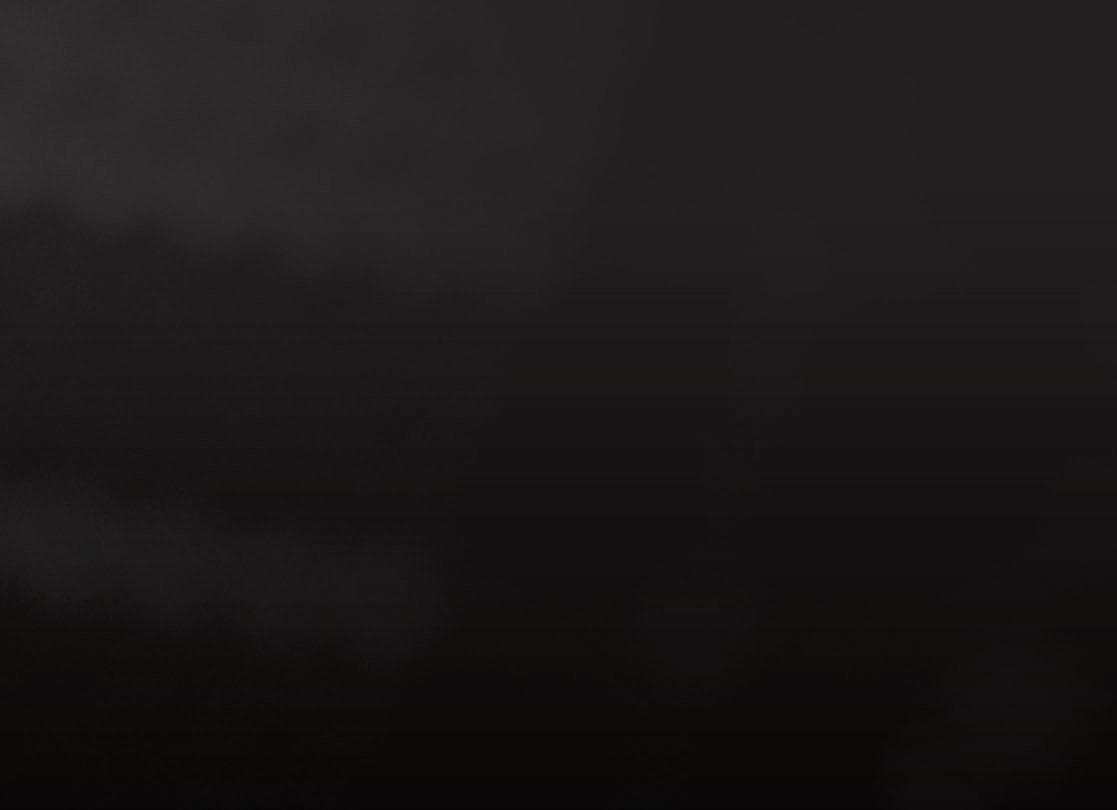


We’ve introduced these assessments to help colleagues proactively monitor and improve their overall wellbeing.
To date, 190 colleagues have taken advantage of these free health
A focus on menopause
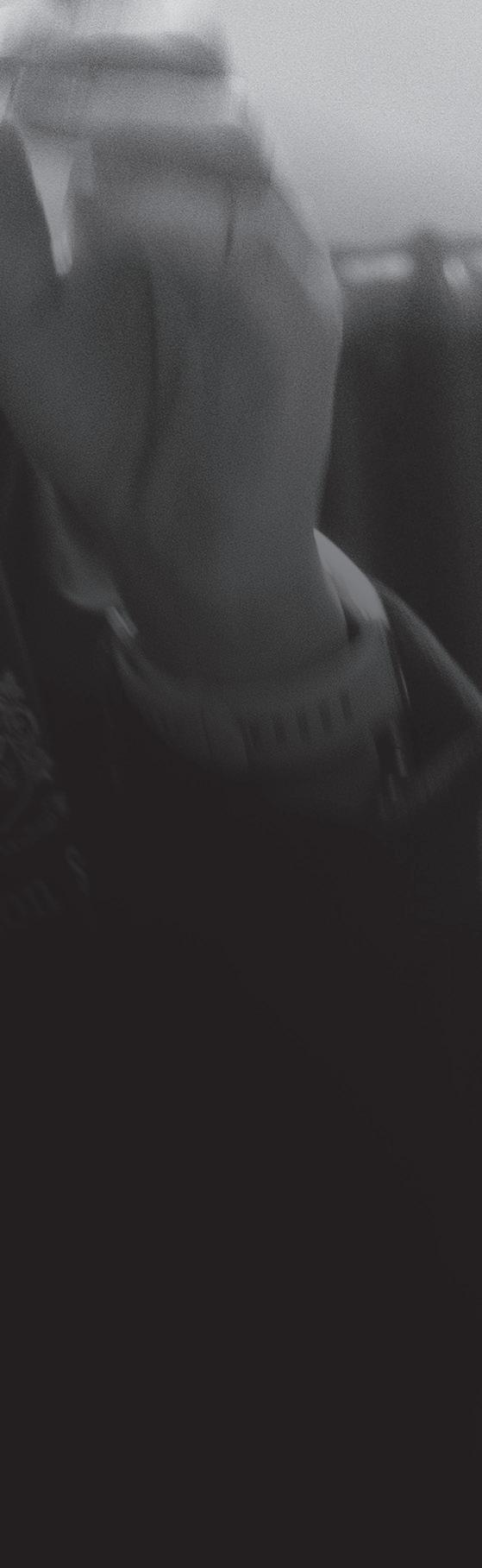
checks.
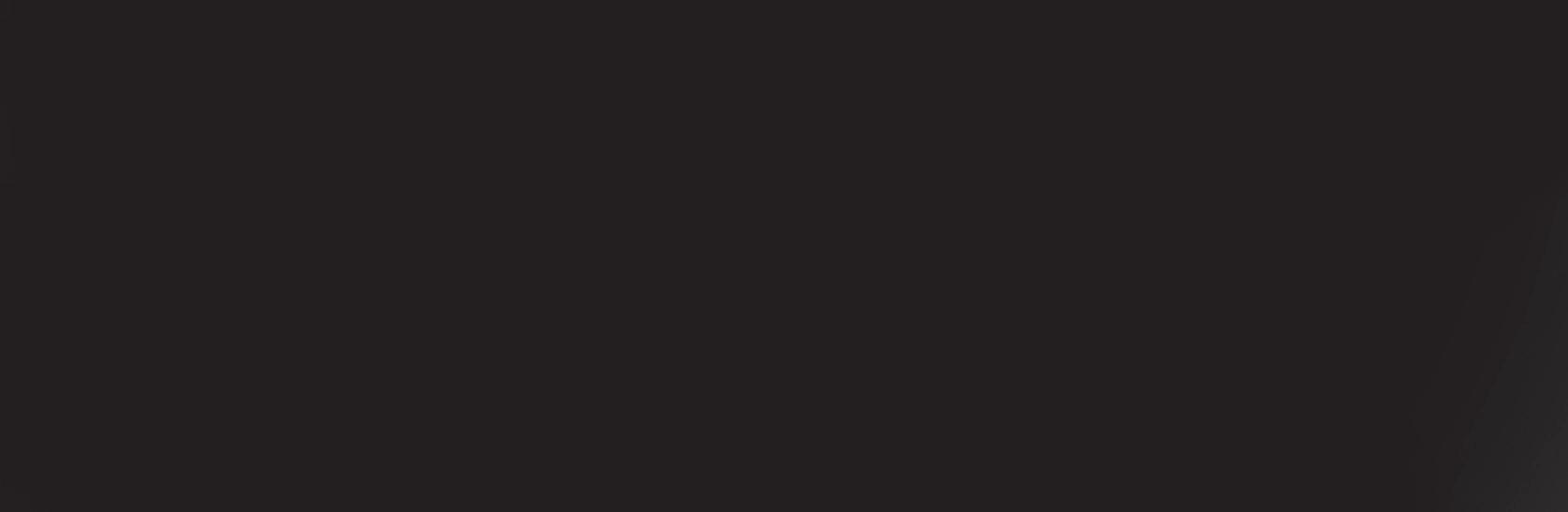
Our initial menopause focus group was hugely successful. A menopause booklet, created by the group, has been shared with the whole workforce. In addition, we are training line managers, understanding symptoms and how as a business we can support the women who are experiencing menopause symptoms.

A supportive community that embraces diversity and inclusivity. And a place where every person is encouraged to take charge of their physical, emotional and mental health wellbeing.
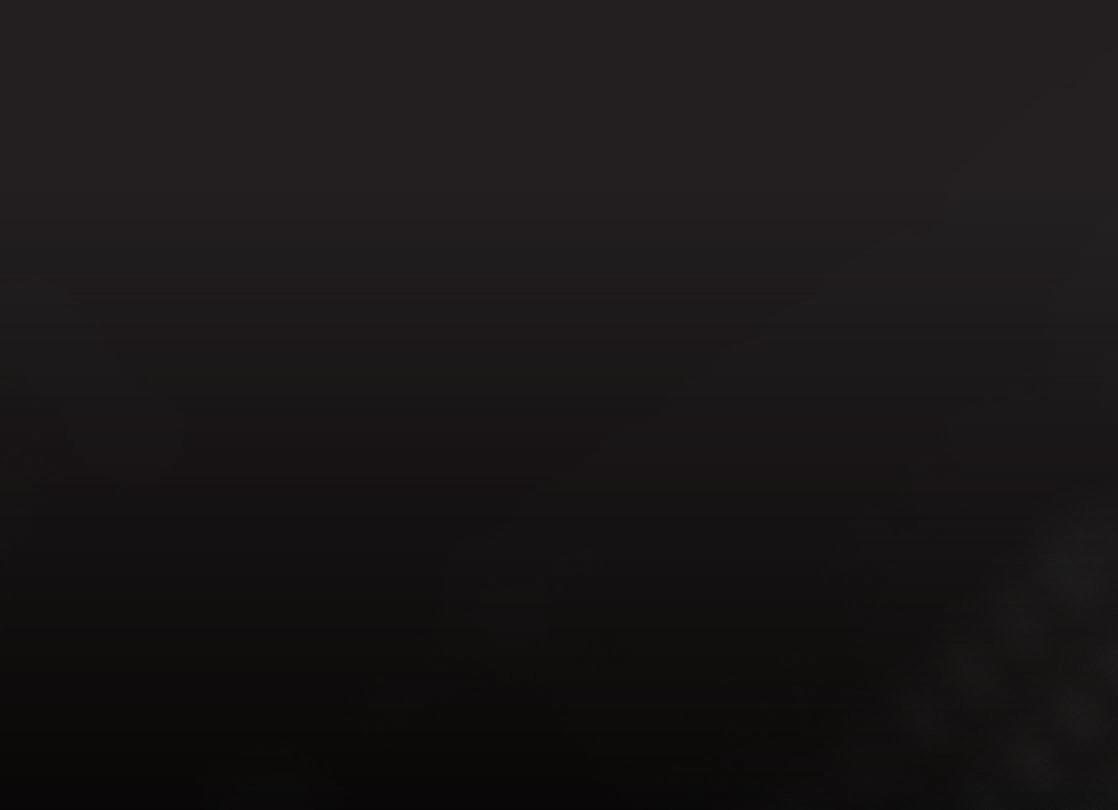
Wellbeing Day
In 2023, an additional day was added to everyone’s holiday allowance. We encourage colleagues to use this day to take time for themselves.

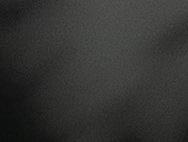


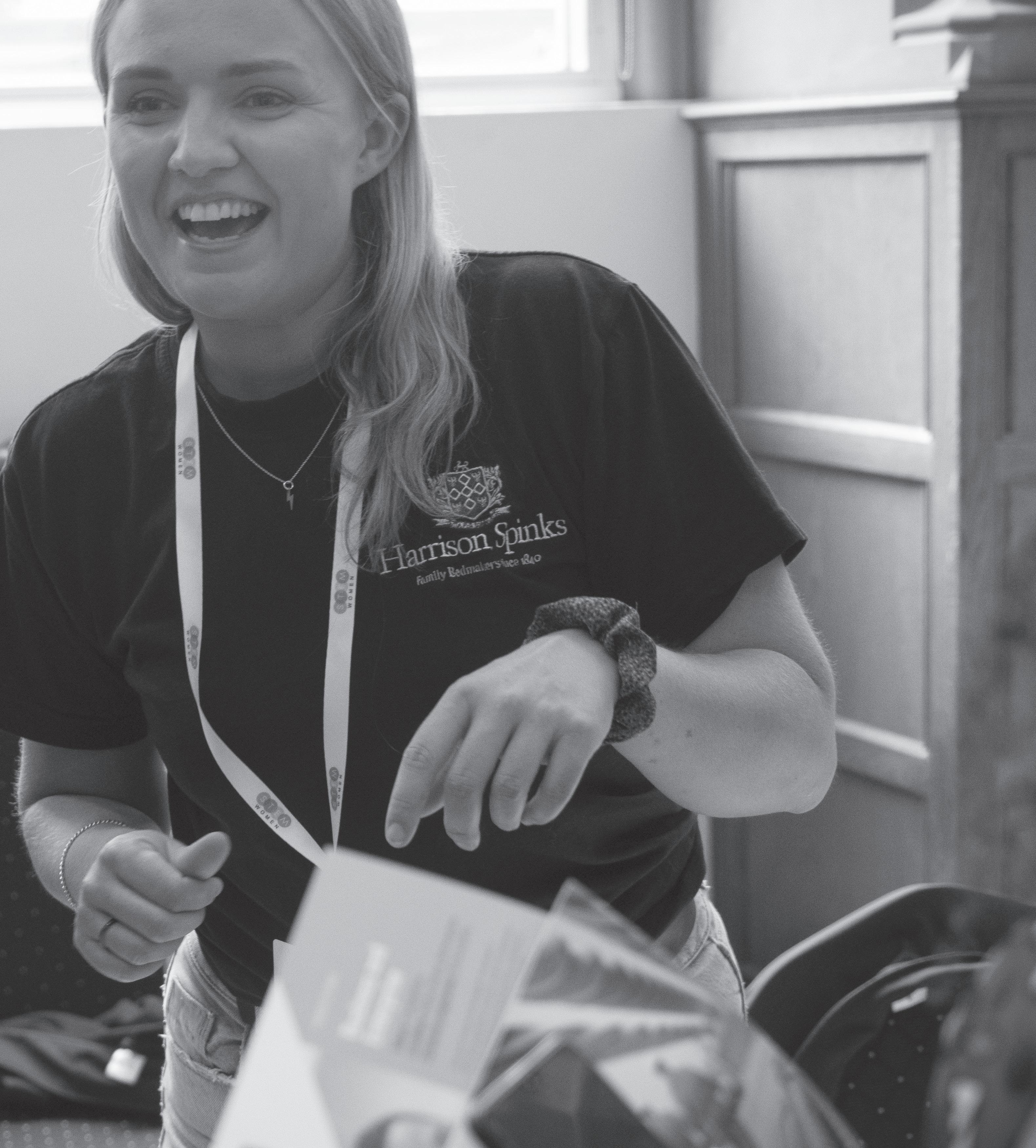
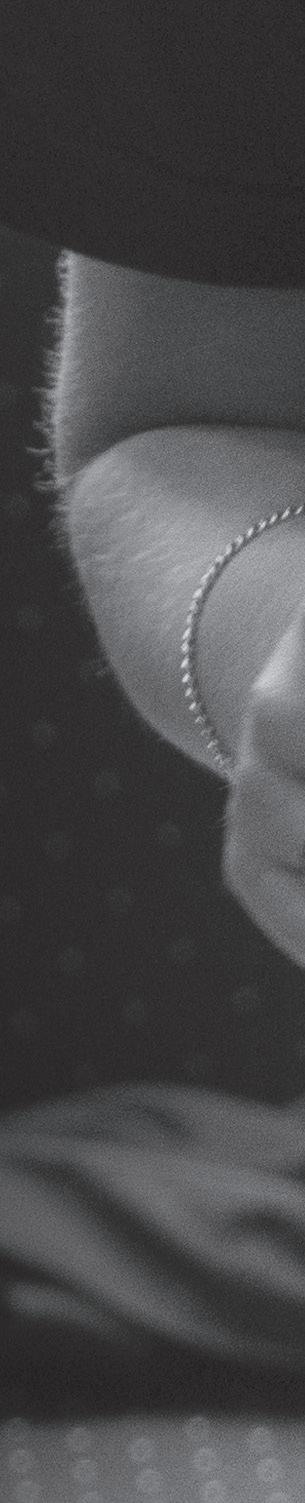
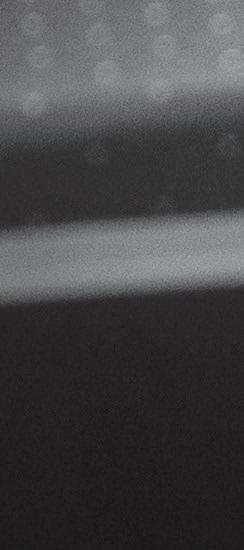
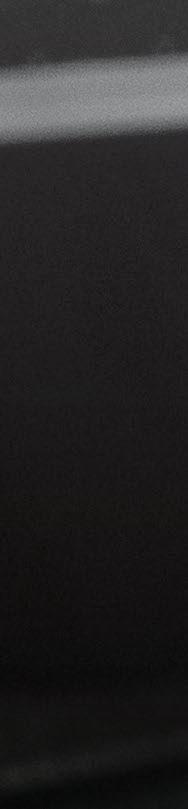

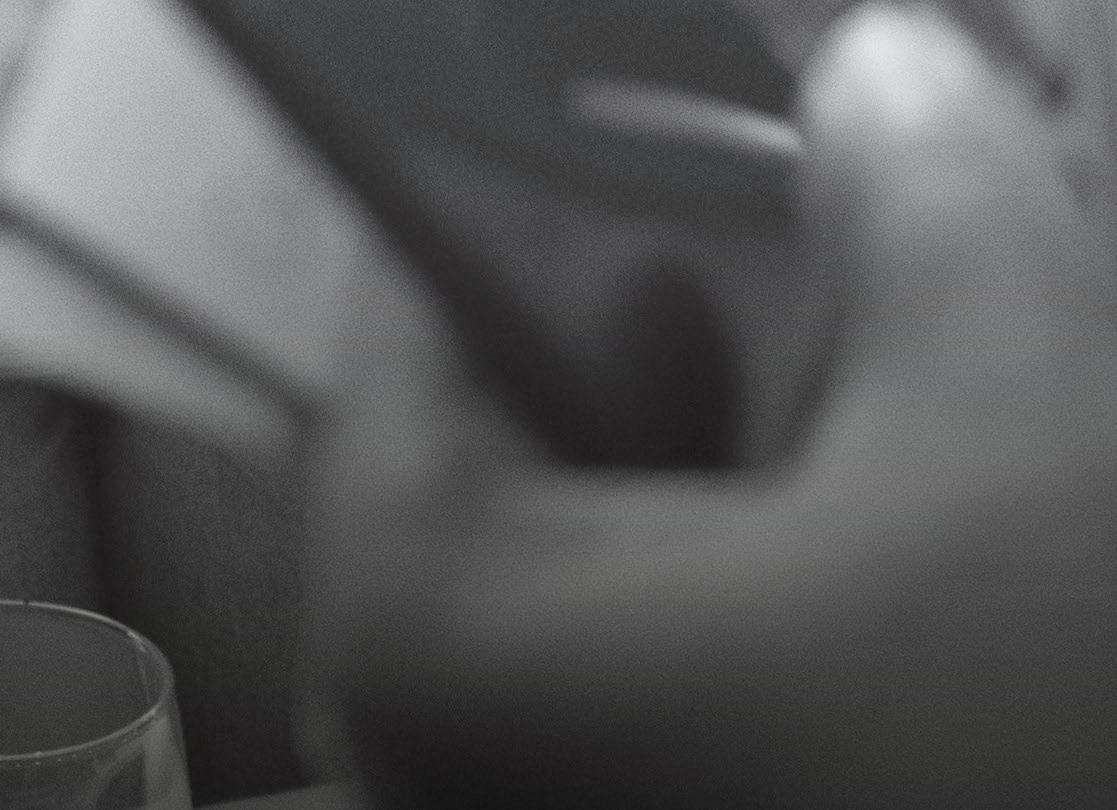
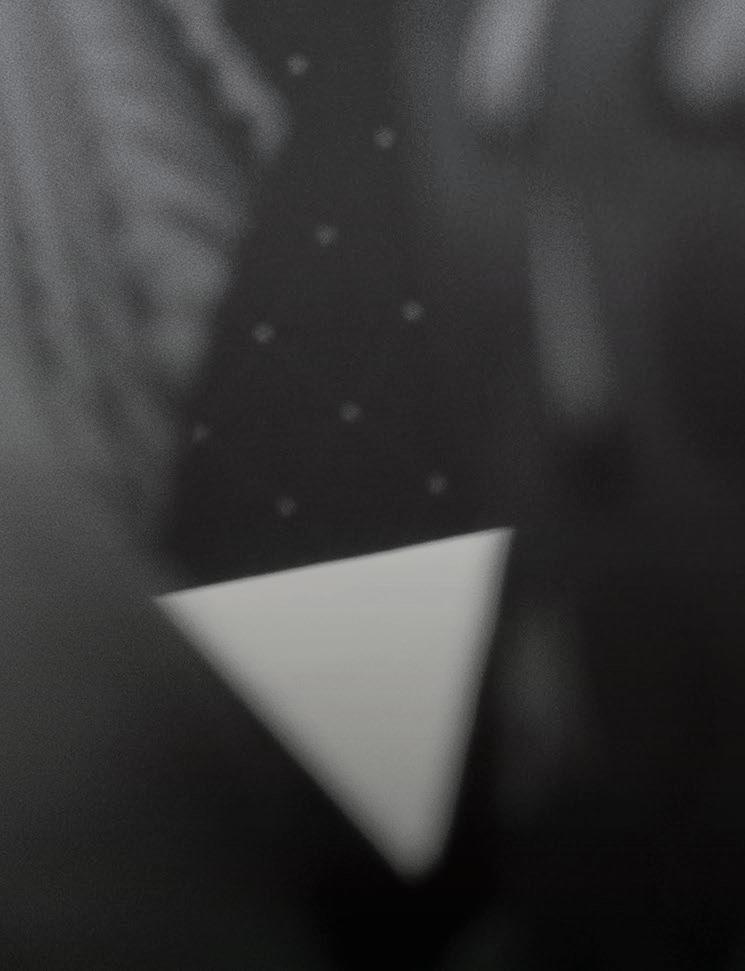
Our community COMMITMENT:
WE WILL WORK WITH THOSE AROUND US TO IMPROVE SOCIAL MOBILITY AND SUPPORT HEALTHY AND INCLUSIVE COMMUNITIES.
School collaborations
To inspire the next generation, over the last year, we have attended numerous school events and have plans for even more over the coming year. Some of our highlights include:
• We worked in partnership with Edu4tex and Tingley-based Woodkirk High School to deliver a textile project.
• We attended Cockburn School Careers Fair to discuss manufacturing roles with Y7 – Y11 students.
• We attended school assemblies at Stephen Longfellow Academy. The school supports vulnerable students who may have been expelled from other schools.
• We are also partnering with Leeds City College, organising manufacturing events and helping deliver their T Level Engineering programme. Supporting students to gain industry experience and completing 315 hours in the workplace whilst studying.


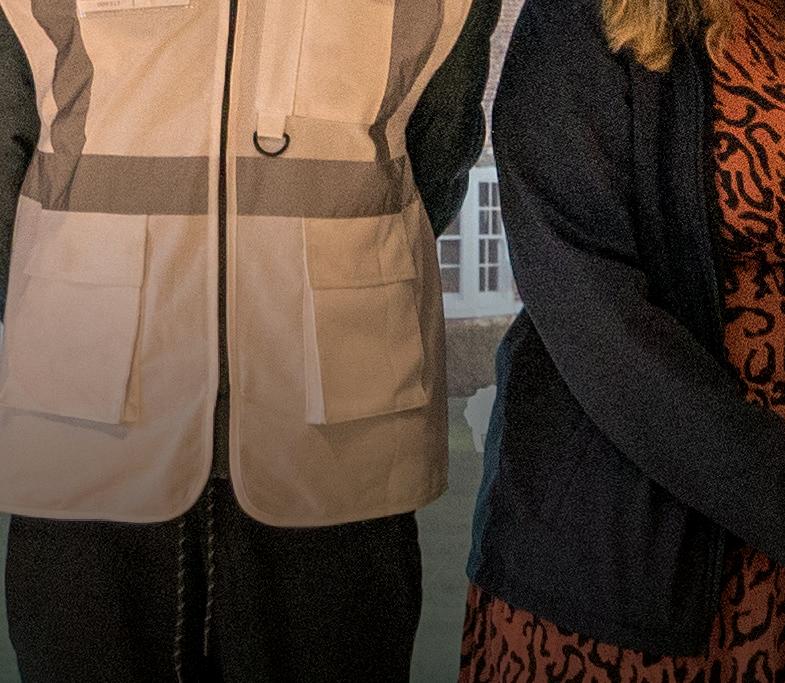
Champions Community Support and Health
Using the power of sport to educate, motivate and inspire, we work closely with Champions Community Support and Health to develop opportunities for young people in our area.
The charity identified that families who are struggling financially don’t have the funds to access sports clubs and organised activities for their children. As a result, young people are becoming increasingly inactive, isolated and, in some cases, turning to gangs and anti-social behaviour. Today they support hundreds of families with free sports sessions and free meals, with 98% of those on their database coming from BAME backgrounds.
We are proud to play a part in their success, supporting Christmas gifting since 2021. Plus, to deliver long-lasting change, we delivered our first CV and interview skills workshop for those at school leaving age, and are planning a tour of the factory and exploring job shadowing.

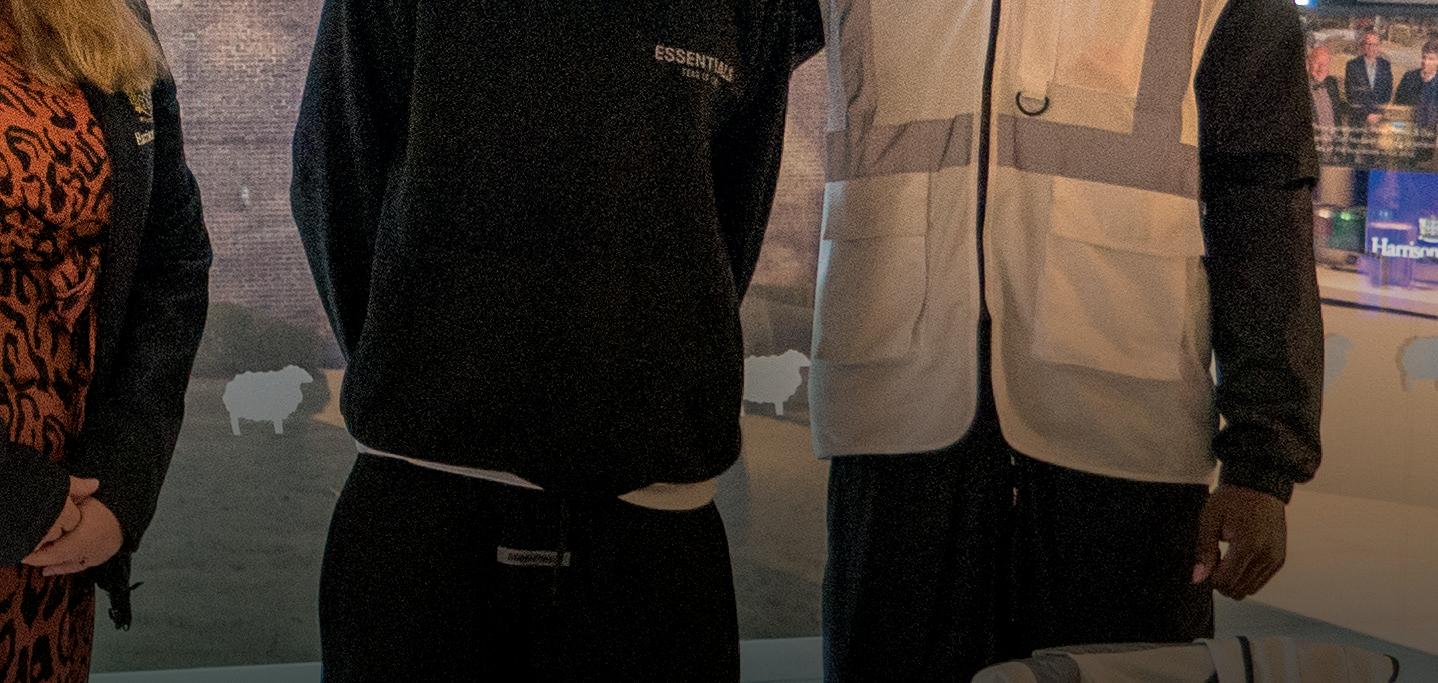
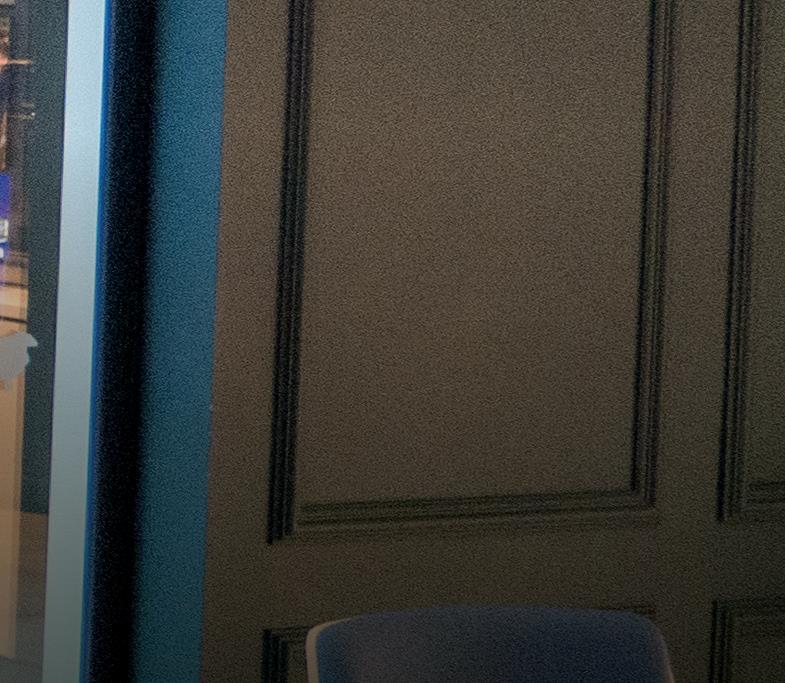
Helping give every head a bed Case Study

We are proud to partner with Leeds-based charity, Zarach. With their aim of giving ‘every head a bed’ they are dedicated to helping children in poverty get a good night’s sleep.
Knowing how important a proper bed can be to a young person, we had to get involved.
Partnering with local schools, Zarach is able to identify children living through a poverty crisis, where parents are continually struggling to provide the basics for their children. For many families, beds are an expense they simply can’t afford.
That is why we have committed to providing 20 custom-made mattresses each month to support children and families in poverty.

Amy Green, Funding and Communications Manager at Zarach, said:
“Our mission at Zarach is to end child bed poverty in England and give children the opportunity to engage in their education.
Too many children are sleeping on cold, hard floors, sharing with multiple siblings and even in the bath. Sadly, we have heard it all. However, we believe that through our work, and together with Harrison Spinks and their generous donation of mattresses, we can continue to make a difference.
Ensuring children have a warm, safe place to rest each night begins to level the playing field...creating a place for growing bodies to develop, a place for privacy and a space to call their own.”
Sustainability timeline
2009-2028
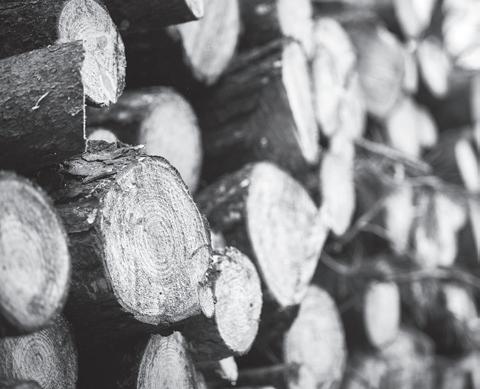
2009
Purchased Harrison Spinks Farm
2011
Started managing our 56-acre FSC® certified woodland
2010
The first hemp crop was harvested from the farm
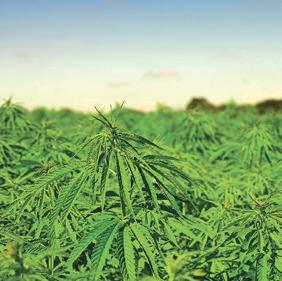
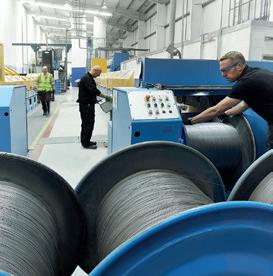
2014
Started drawing our own wire from British Steel ensuring high-quality, locally sourced product
2013
Awarded first Queen’s Award for Enterprise in Sustainable Development
2015
2018
Started to record our carbon footprint, informing decisionmaking for emissions reduction
Purchased our own looms and began to weave FRchemical-free mattress fabric
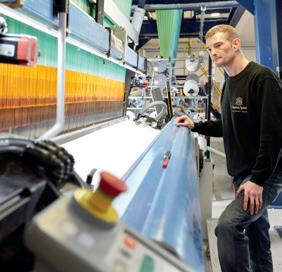
2019
Awarded second Queen’s Award for Enterprise in Sustainable Development Invention of glue-free Cortec™ spring, winning Component of the Year at the National Bed Federation Show

2020
Achieved glue-free, foam-free, FR-chemicalfree production of all UK mattresses
2022
Dr Louise Ellis-Jones joins the business as a Non-Executive Director
Officially stated our commitment to the Science Based Targets initiative
Became a member of the UN Global Compact
Became first spring manufacturer to achieve Cradle to Cradle Bronze certification
Formalised compressed working hours
2021
Two sustainability professionals trained within the business that helped embed sustainability
Started to measure our carbon footprint inhouse, including Scope 3
Charity partnership with Zarach started
2023
2024
Biodiversity study for Leeds sites and farm
Achieve responsible sourcing certification for some of our natural fillings
Support the Wild Ingleborough programme, including involving colleagues in volunteer work
Begin using materials from our regenerated fillings line
Deploy solar PV at Hornington Manor
Near-term and net zero emissions targets approved by SBTi
Work towards ISO 14001 Certification
Working towards achieving Cradle to Cradle 4.0
Awarded third King’s Award for Enterprise in Sustainable Development
5-year sustainability roadmap created
Colleague sustainability training starts
Launched responsible sourcing strategy
Established a new baseline for our waste reduction strategy
Energy-saving taskforce created to achieve energy reductions
Partnership created with Wild Ingleborough –carbon offset project
Rollout of our enhanced benefits package
Company health checks implemented
Awarded two King’s Awards for Innovation and International Trade
2025
2026
Responsible sourcing review of adhesives, tufts, and labels (phase 3) by 2028 2030
Publish the first public Carbon Footprint Report, including all three emission scopes
Sustainable Innovation Fund to propel new sustainability initiatives suggested by employees
Continue responsibly sourced strategy – yarn (phase 2)
Organic farming –certified organic
2028
Fully implement the roll out of the employee benefits package
1
Our future intentions
We all recognise how much work we still have to do. Both in further developing our vertical manufacturing model, further increasing efficiencies across all production processes, reducing waste and making a valuable contribution to the lives of our colleagues and the community.
Whatever the challenge, we are, and will always be, 100% committed to creating a happier and healthier world for us all.
ENVIRONMENTAL
To agree our net zero pathway through our approved SBTis.
Gain organic status at the farm by 2025 and produce our first organic crop by 2026
We’re investing in the latest solar PV technology at our farm to reduce our reliance on fossil fuels from the grid.
This is projected to generate 400,000 kWh per year which will support our natural and recycled fibre production, as well as powering events at Hornington Manor. Surplus electricity will be exported to the grid.
2 3 4 5 6
Be the first in our industry to achieve certification for sustainable weaving.
7 8
To be as transparent as possible, we are also looking to gain the correct certifications. These include: Responsible Mohair Standard, Global Organic Textile Standard, Global Recycled Standard and Better Cotton Initiative.
We will digitalise our wire drawing with an aim of reducing CO₂ by 40%.
To further encourage biodiversity on our farm, we will also be adding 2,750m of new, native hedgerows to support animal welfare and encourage wildlife.
Transitioning all non HGV or long-distance company vehicles to electric.
1
We will be undertaking Modern Slavery training to further our knowledge on the issue and see how we can expand upon what is already in place.
This could include Tier 1 factory audits and delving deeper into the supply chain to include Tier 2 and Tier 3+ suppliers.
We will create a health and wellness calendar with regular updates on topics such as stress management, nutrition, fitness, mindfulness and more.
Future health initiatives include delivering more mental health workshops to foster an environment where employees feel they can openly communicate and talk about any mental health issues.
6
We are committed to supporting our charity partner Zarach over the coming years.
We will roll out a programme of wellness challenges to promote physical fitness and a sense of community.
To help even more of our colleagues understand our business, and unique connection with the natural environment, in 2024 we expect to increase farm visits c.300 and to embed this as part of our induction programme.
7
3 5 2 4 Feedback
We will continue to support Champions Community Support and Health, both directly and in terms of offering apprenticeship and work placements.
Sustainability is a collaborative effort. And we’ll get to where we want to be quicker if we share ideas.
If you have any feedback on any of the initiatives and innovations in our Impact Report, we’d love to hear from you.
sustainability@harrisonspinks.co.uk
Sustainability awards to date:
The Queen’s Award for Enterprise in Sustainable Development 2013
Insider Made in Yorkshire Green/Sustainable Manufacturer Awards, Winner 2018
The Queen’s Award for Enterprise in Sustainable Development 2019
Furniture News Awards, Best for Sustainable Thinking Award 2022
Interiors Monthly Awards, Sustainability Award Winner 2022
Vet Partners Sustainable Farm Award, Sheep Category Winner 2022
The Yorkshire’s Business Excellence Awards, ESG Winner 2023
BFM Future of Furniture Awards, Sustainability Winner 2024
BFM Future of Furniture Awards, Sustainability Champion 2024
Yorkshire Sustainability Excellence Awards, Circular Economy Excellence Winner 2024
The King’s Award for Enterprise in Sustainable Development 2024
www.harrisonspinks.co.uk