
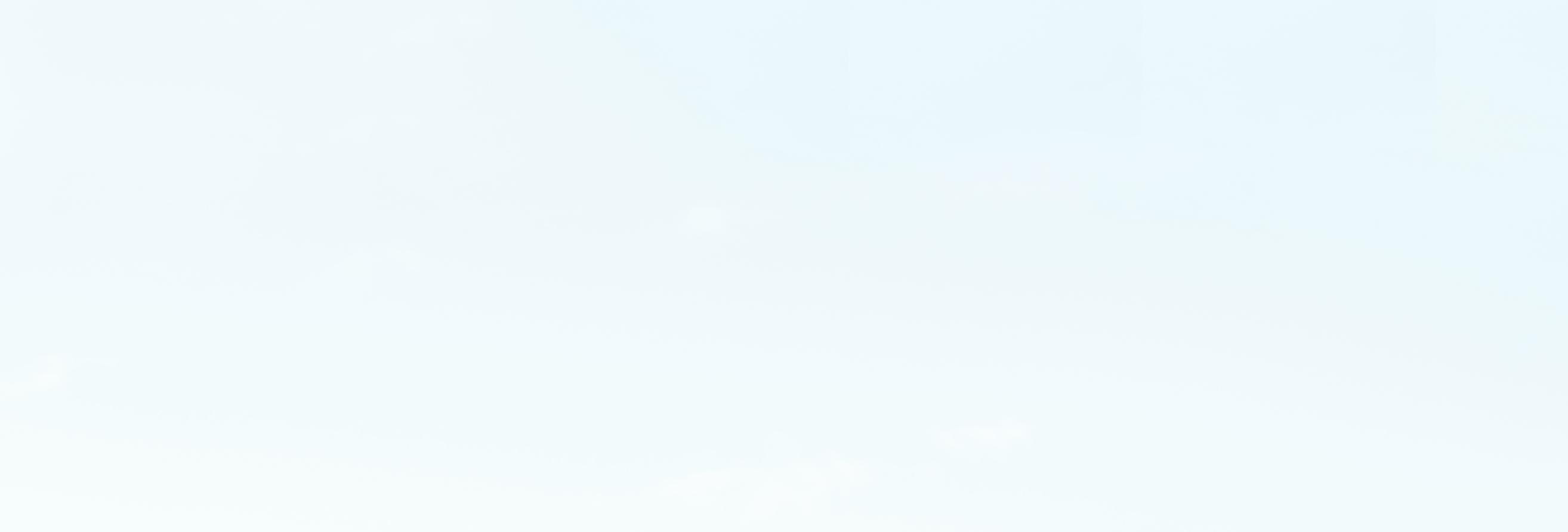
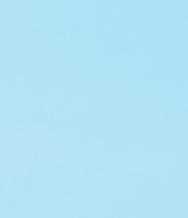
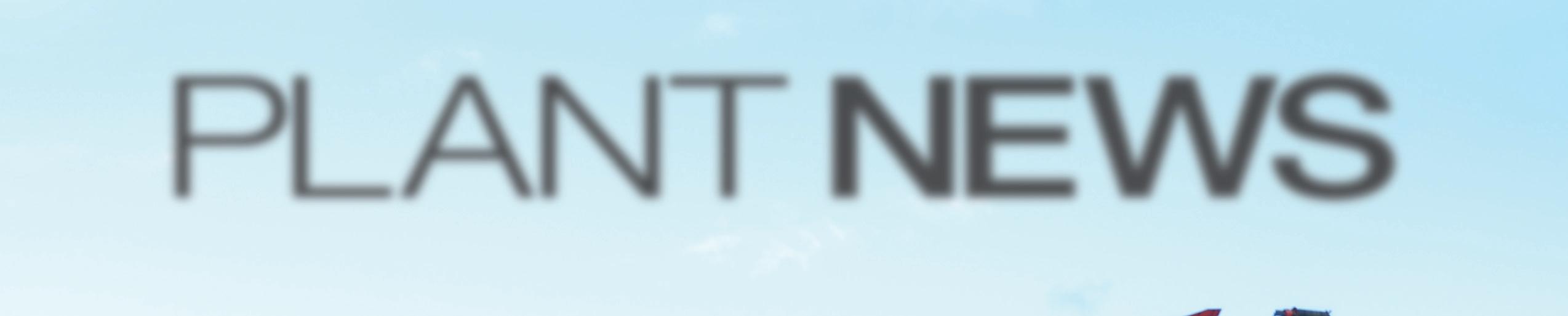
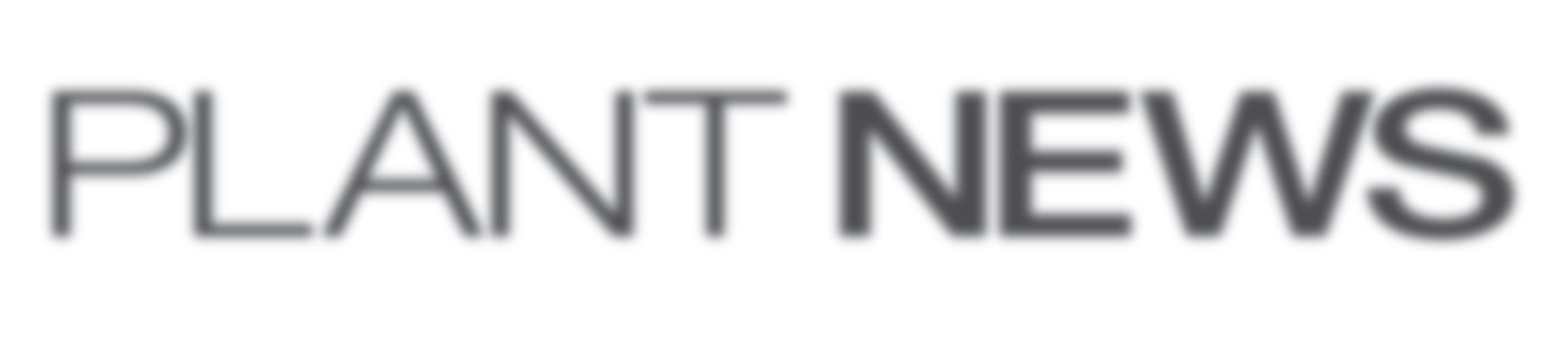




































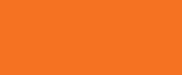
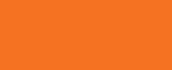
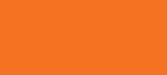


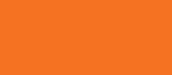
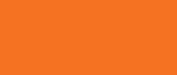


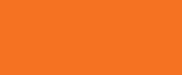
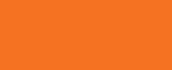
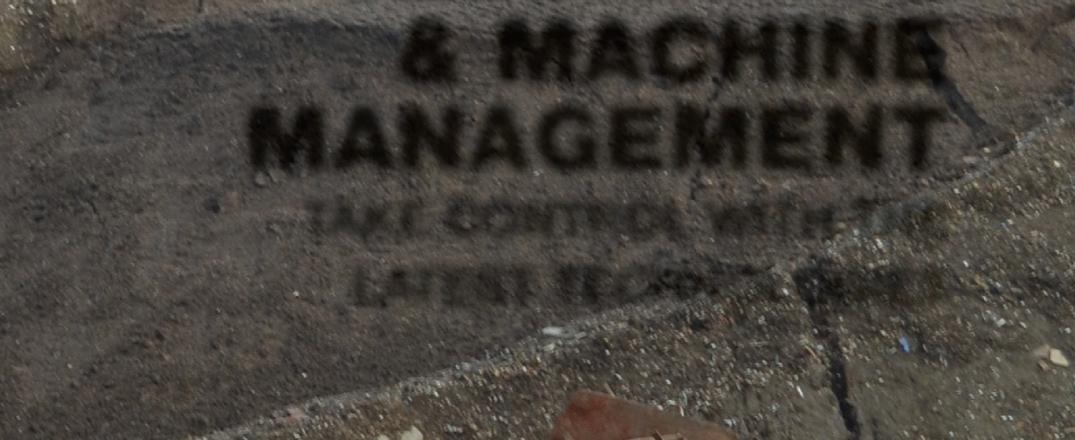
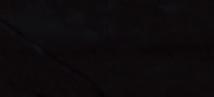
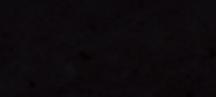

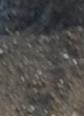
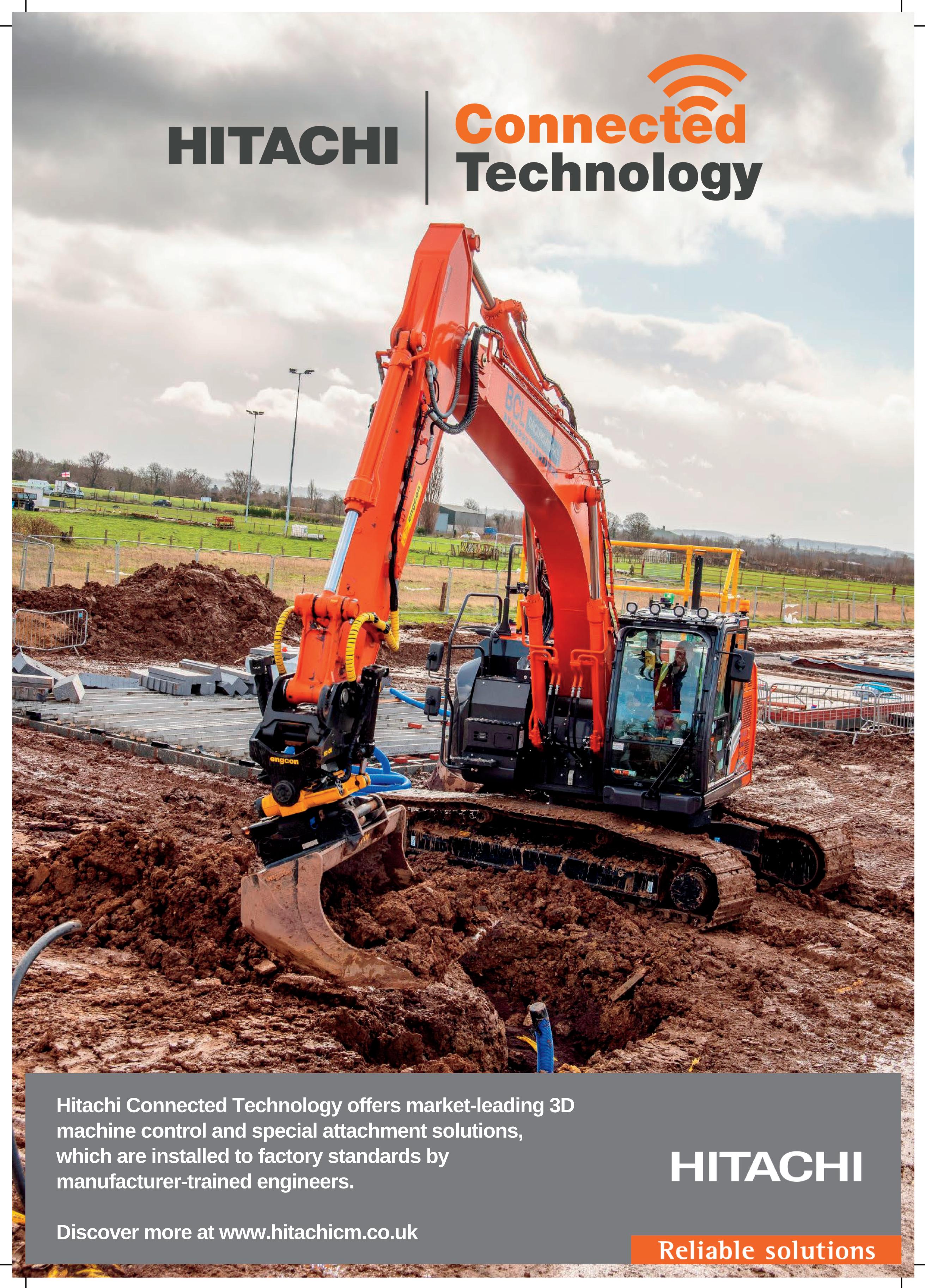
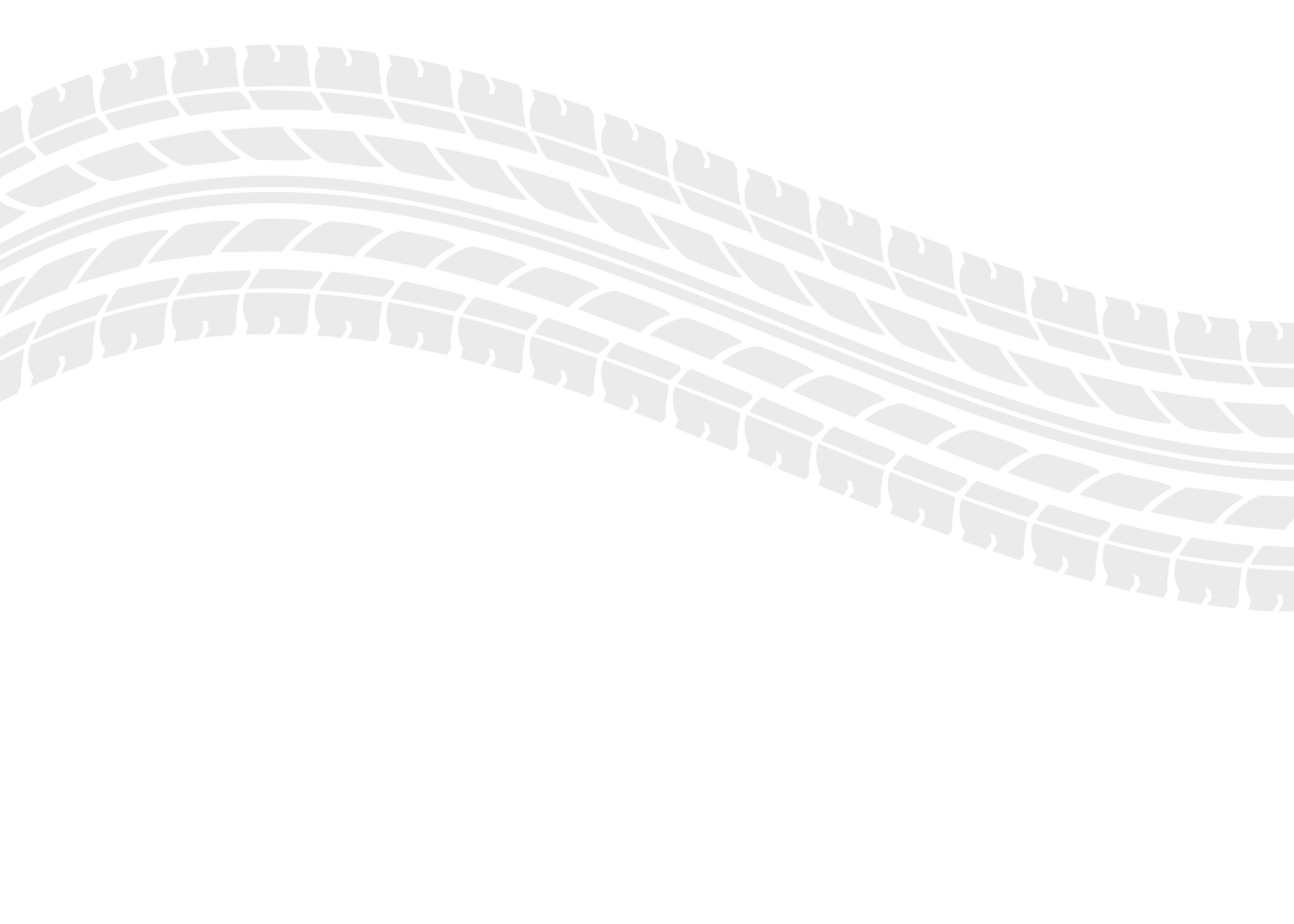

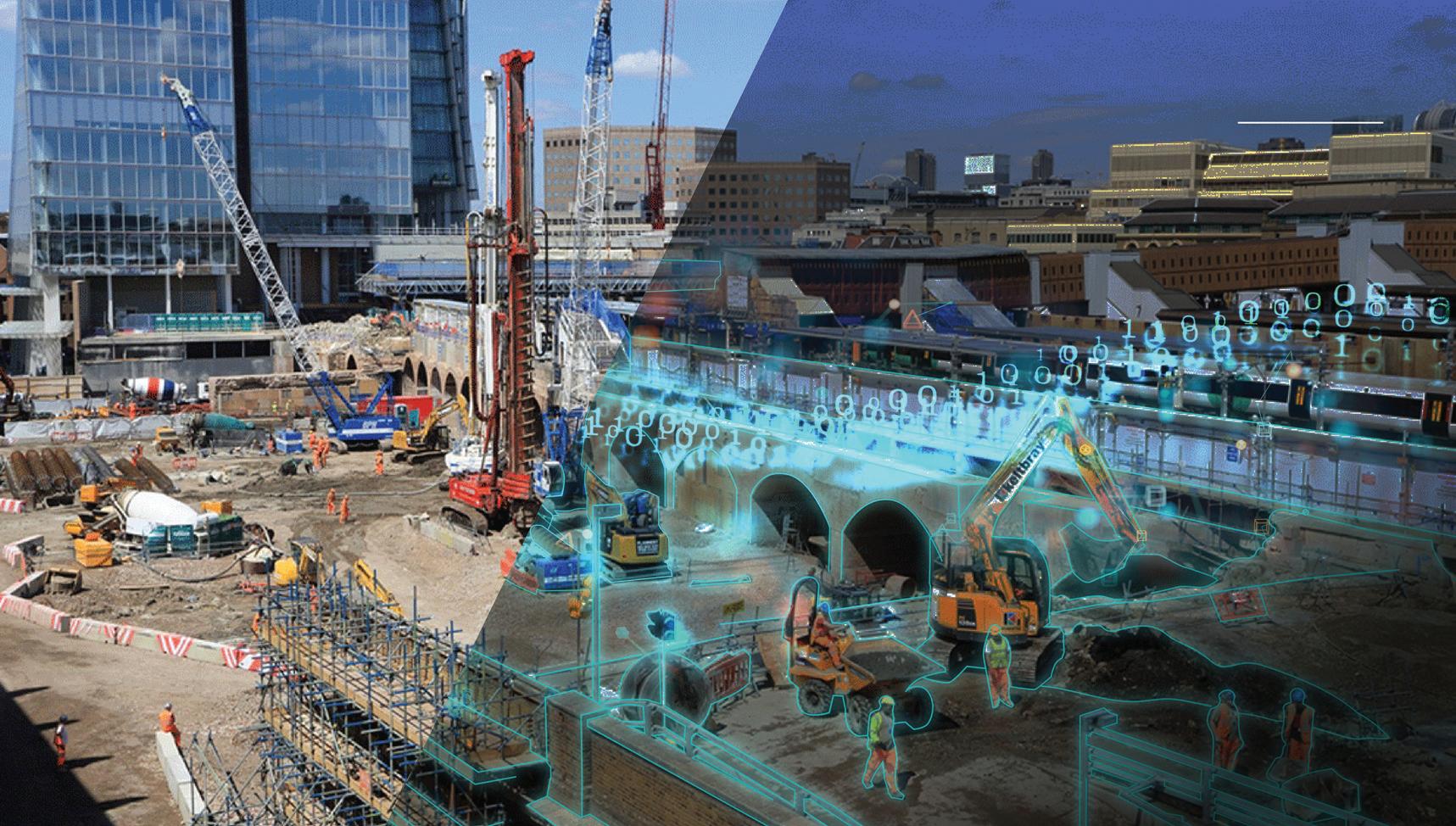

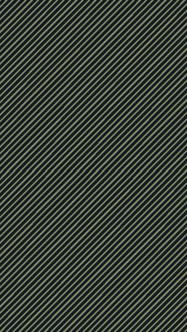
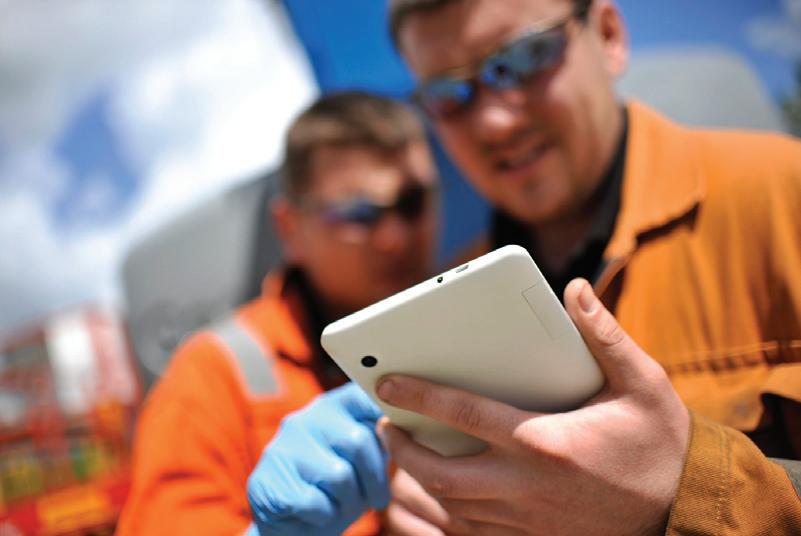
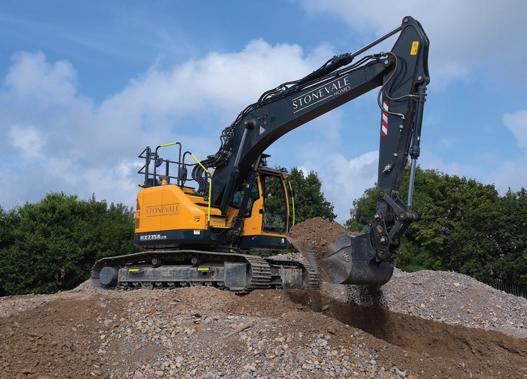
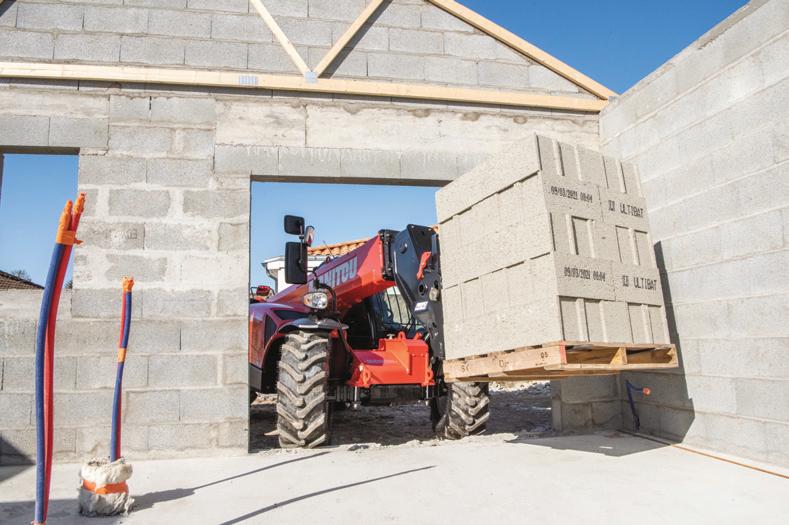
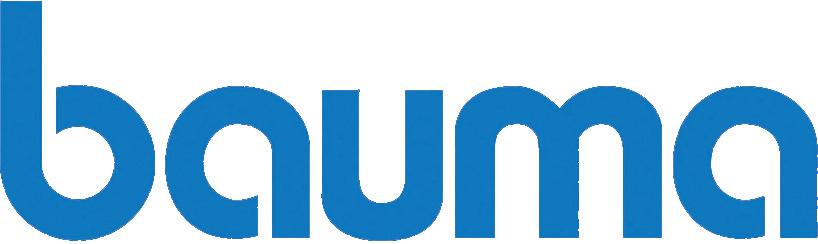
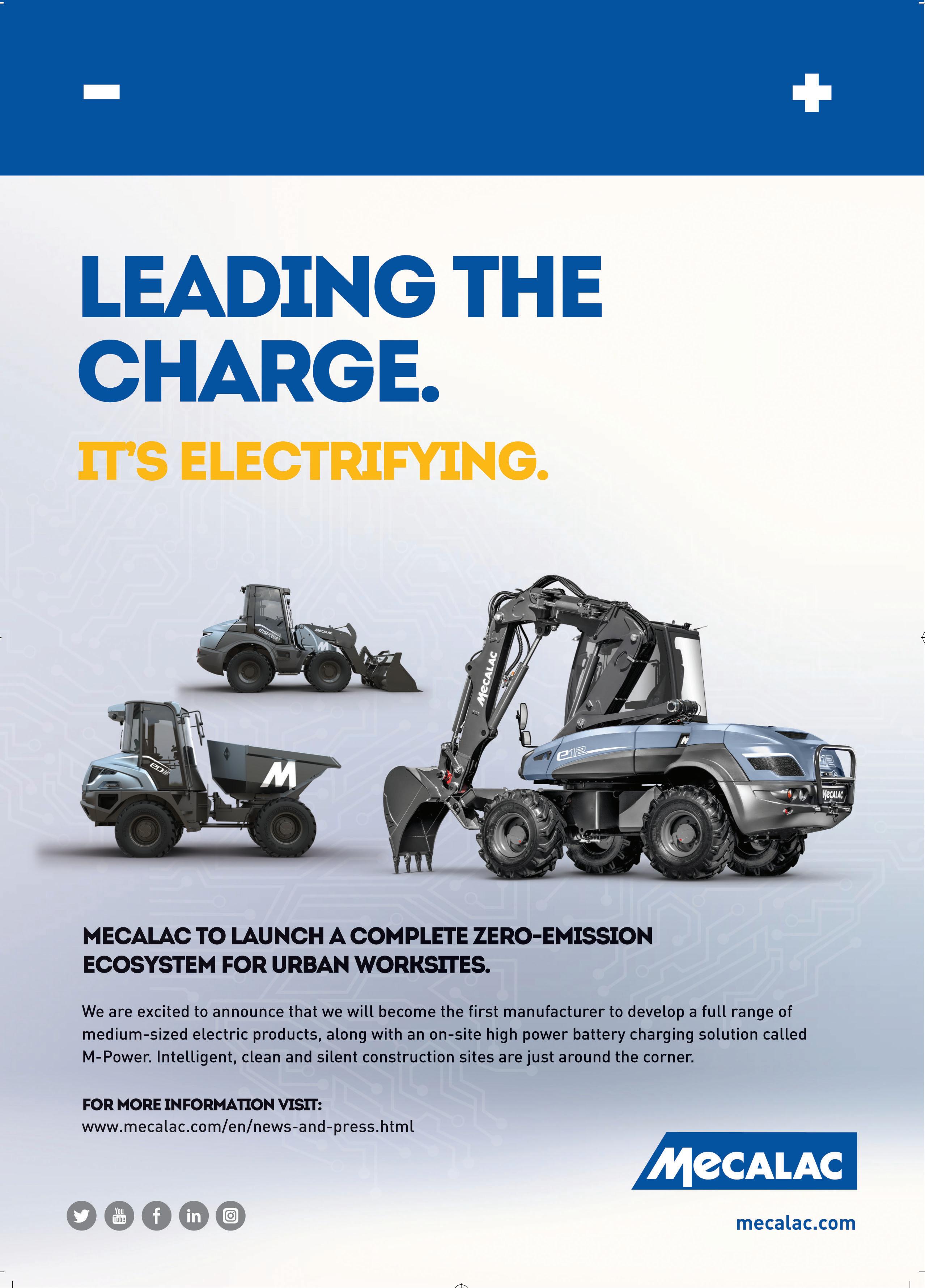
Editor LEE JONES ljones@hamerville.co.uk
problems with pretty much all of them.
Managing Editor TERRY SMITH tsmith@hamerville.co.uk
EditorAs far as our relationship to sustainable solutions goes, Hydro-treated Vegetable Oil (HVO) seems to be following an all-too familiar path. First there’s the honeymoon period, then the doubt and differences set in and, whilst we’re most certainly not at the acrimonious divorce stage just yet, there are some who have already called for a trial separation.
Over the last few months contractors and plant hirers have been veritably falling over themselves to embrace this drop-in fuel. It’s advocates point to the fact that it requires no modification to existing internal combustion engine machinery, makes a significant contribution to reductions in NOx and particulate matter, is biodegradable and, it is claimed, can offer up to 90% carbon savings when compared to diesel.
The eagle-eyed among you will spot the qualification in that last listed benefit, because critics argue that many of the ‘claims’ around the supply chain are difficult to verify. HVO is made from a variety of materials, including unused cooking oil, and most of them are not actually waste products that we are repurposing for construction plant operations – they are already used in other sectors and have a finite level of availability. Put pressure on this source of raw material, it is argued, and there will be a rush to others, most notably palm oil, which is a significant contributor to global deforestation, carbon emissions and extinctions.
Whilst publicly avowing that it remains fully committed to phasing out fossil fuels, Balfour Beatty has paused any usage of HVO until it’s provenance can be determined, and is urging the government to review its use in the UK. Similarly, the Environment Agency is already undertaking an appraisal of its sustainability credentials.
So, is this the beginning of the end for HVO? The reality is – as ever – rather more nuanced. None of the alternatives to what has hitherto been an addiction to diesel are currently scoring a perfect 10. There are pitfalls in practicality, cost, and supply chain
As a material lithium might be whiter than white in colour, but the mining of some of the rare earth metals that are used in the current generation of electric batteries is most certainly not. There have been many instances around the world where it has been criticised not only from an environmental standpoint but on issues of worker welfare and exploitation.
Few would argue that HVO does not have the upper hand over diesel in terms of local emissions, and even some of its champions would argue that it represents a transitional solution until the affordability of genuine zero emissions machinery brings it within reach of the majority. At the same, time the fuel’s leading manufacturers are working very hard to deliver a transparency of supply that will satisfy the cynics.
Digital Assistant DAVID MOLLOY dmolloy@hamerville.co.uk
Group Advertisement Manager CRAIG JOWSEY craig@hamerville.co.uk 07900248102
Advertisement Manager JACOB TATUM jtatum@hamerville.co.uk 07825773737
Account Manager PAUL FITZGERALD pfitzgerald@cpnonline.co.uk 07917324995
Magazine Designer DONNA BOOTH Group Production Manager CAROL PADGETT
Construction Plant News is a business magazine for plant professionals, contractors, materials extraction and processing companies, waste and recycling operations, as well as local authorities. If you are not on our circulation list and would like to subscribe email circulation@hamerville.co.uk
To be removed from this magazine’s circulation please call 01923 237799 or email circulation@hamerville.co.uk.
Printed by Walstead Roche
Published by HAMERVILLE MEDIA GROUP
It is also still the case that no one alternative has emerged as the undisputed heir to the age of oil. Fast forward some decades from now and are we likely to be powering up with some form of battery electric, hydrogen or an as yet unexplored technology? Whoever has access to that particular crystal ball could make an awful lot of money. In the meantime it is becoming increasingly clear that opening up the industry to as many alternatives to diesel as possible is the most navigable road to net zero that lies open to us and, more importantly, it is the only strategy that the sector can currently afford.
Regal House, Regal Way, Watford, Herts WD24 4YF.
Tel: Watford (01923) 237799
Fax: (01923) 246901
Copyright © 2022
“Few would argue that HVO does not have the upper hand over diesel in terms of emissions, and even some of its champions consider it as a transitional solution.”
decline in thefts since the scheme was first launched, with recovery rates of registered equipment significantly higher than non-registered machines.
Cesar is the official scheme of CEA (Construction Equipment Association), promoted by the AEA (Agricultural Engineers Association) and powered by Datatag Id
ALL ROADS LEAD TO THE EXECUTIVE HIRE SHOW 2023
For further information
WWW.RDR.LINK/CAG001 i
As part of a £100 million project to produce super-efficient hydrogen engines, JCB has already showcased working prototypes of a backhoe loader and Loadall telescopic handler powered by hydrogen. The latest addition is a mobile hydrogen refueller that provides a quick and easy way for customers to refuel their machines on site. Around 97 per cent of construction machines have fuel delivered to them while working on site and customers are already used to a transportable fuel that can be delivered in minutes.
The EHS team has confirmed that the event will be taking place on the 8th and 9th of February 2023, at its established home – the Coventry Building Society Arena (CBS Arena), formerly known as the Ricoh Arena. The Innovation Trail will have a renewed focus on equipment that employs new power sources, and sustainable technologies, or which improves efficiency and environmental impact.
For further information
WWW.RDR.LINK/CAG003 i
The 2022 Bauma Innovation Award in the climate protection category has been awarded to the Liebherr R 9XX H hydrogen excavator. Developed by Liebherr-France SAS, the 50-tonne unit is powered by an H966 hydrogen combustion engine. In terms of power, dynamics and responsiveness, the R 9XX H2 hydrogen excavator gives nothing away to any conventionally powered machine and, on a “tank to wheel” basis – i.e. when used on a construction site – a hydrogen excavator emits almost no CO2
To find out more
WWW.RDR.LINK/CAG004 i
A new office in Warrington, northwest England will be able to offer faster access to spare parts for its appointed dealers and customers, and it will be able to hold a larger comprehensive stock.There’s a fully equipped workshop for product service and repairs and the potential to train dealers, service partners and end users in relation to technical upgrades, system knowledge and product developments.
For further information
WWW.RDR.LINK/CAG005 i
Retail sales of construction and earthmoving equipment in August were 6% above sales in the same month last year. This was the strongest performance since February when sales were ahead of last year’s levels by a similar amount. Telehandlers – for the construction industry – continue to show the strongest growth by a significant margin this year, at 24% up on 2021 levels. On a regional basis, the strongest sales so far this year continue to be in Yorkshire, at nearly 11% up on last year’s levels.
The leading wet civil and environmental engineering firm has identified eight key areas that can be tackled quickly by the sector in order to minimise time, energy and resources being wasted.
These eight areas are: Planning and coordination How materials and resources are used on site How the industry works with weather (and against it) to improve efficiency Energy, idle time and fuel Damage and abuse of equipment and working conditions
Quality – by terms of getting it right the first time and avoiding re-work
For further information
WWW.RDR.LINK/CAG006 i
The 5th biennial construction machinery exhibition will be held on 13-15 June 2023, at the East of England Arena and Events Centre, Peterborough. Spanning more than 150,000m2 of exhibition space, the show will give visitors an opportunity to see some of the latest plant and machinery operating in ‘real’ construction site conditions. Already over 145 companies have secured their stand space and 85% of the digging demonstration areas have been sold.
Our time –understanding our personal responsibilities to make sure we use our time as efficiently and effectively as possible
To watch a video that explains the What a Waste initiative visit
i
WWW.RDR.LINK/CAG009
For further information
WWW.RDR.LINK/CAG 007 i
Eminox and Speedy have joined forces to improve air quality.The project will lead by example, and will see the hirer’s generators retrofitted with an Eminox exhaust aftertreatment system which will cost-effectively upgrade power generators from Stage IIIa to Stage V compliant standards. This will enable equipment to be deployed where regulations such as London NRMM Low Emission Zone, Clean Air Zones (CAZ) and Medium Combustion Plant Directive (MCPD) are enforceable, and on projects such as HS2.
In conjunction with Leica Geosystems and Engcon, Hitachi Connected Technology recently hosted its first Dig Day at the Leica Geosystems Training School. The event attracted over 150 construction professionals across the two days and gave visitors a hands-on experience with a range of machinery, all equipped with Leica machine control and Engcon tiltrotators; an opportunity to test out all three products at once.
To find out more WWW.RDR.LINK/CAG010 i
For further information
WWW.RDR.LINK/CAG008 i
Whilst sustainability is just about the biggest issue we face as a species, when it comes to behavioural change, it is relatively small steps that can come together to make a real difference. With its Climate Change Action Plan, Costain is putting that principle into practice and achieving tangible improvements across the whole of its business in the process.
“Our plan sets out what Costain is going to do to achieve Net Zero between now and 2035 at the latest,” explains Group Climate Change Director, and architect of the initiative, Lara Young. “It builds on more than a decade of previous emissions-reducing policies, and the lessons that have been learned.”
First launched in 2020, it is a strategy that will target reductions in the company’s carbon footprint across its key areas of operation –including a zero emissions fleet – but just what does this currently look like to the boots on the ground? The easiest element for any fleet manager to influence is emissions and this has been reflected by a focus on unnecessary idling. As an industry, machines can still be idling for an average of 35-45% of the time they are in operation and that represents an significant waste of energy and unnecessary amount of emissions.
“It’s an easy win in terms of reducing the environmental impact of a project and is an equally good starting point in driving behavioural change,” Lara explains. “We know it’s an issue for the industry at large but, when we started on our journey, there was little reliable data available that demonstrated the
and machine management. Every one of its contracts has then been tasked with achieving a year on year 20 per cent reduction in their baseline idling figures. That data is then reported on our group dashboard which is accessible to everyone from the executive board to site managers.
subsequently introducing behavioural improvement plans. Our data identifies which teams and drivers are demonstrating best practice, which need further training and support, and we’re also investigating various retro-fit technologies for our machines.
“In the latter context, hybrid and electric plant is an obvious solution, whilst ensuring that stop/start functionality on conventional internal combustion engine machines is actually activated. The reasons for unnecessary idling will differ from site to site, and the solutions should be introduced accordingly, but the most common theme is often education, and unlearning certain working methods.”
A similarly multi-faceted approach is in evidence with Costain’s attitude to alternative
drivetrains, where a number of technologies have been embraced. Costain set out a mandate as far back as 2017 on minimum plant specs, and the guiding principle of its procurement is, wherever possible, to utilise machines with the lowest carbon footprint. In reality that can mean anything from battery-powered excavators, to hydrogen tower lights, or the use of hydrotreated vegetable oil (HVO), whilst equally driving the highest possible efficiencies from its conventionally powered units – hence the concern with idling.
Costain is also committed to moving the dial on client engagement on specification, whether that’s in engine tiers, challenging the types of machines that are used for what, and removing the need for the use of machinery at the design stage. The greenest form of energy is always the one you don’t use. That’s why the Climate
Change Action Plan focuses on ensuring that multi-tasking pieces of construction plant are deployed, or plant requirements are eliminated from a project entirely.
The company also works directly with manufacturers to provide an active test bed for new technologies and provides invaluable feedback on the results. These often require different organisational requirements – mostly obviously ensuring the infrastructure exists on site to charge electric machinery at the earliest possible stage, for instance – and a contractor that occupies multiple sectors is ideally placed to determine what is ultimately practicable. Costain is exploring how hydrogen can be manufactured cleanly and transported to site, for example, and how the infrastructure around zero emissions technologies can be made available.
“There is a huge amount of data that informs the plan,” Lara adds, “but that will always be at its most effective when it is translated into simple leading indicators which are applied across the whole of the business rather than on flagship projects. If you are to achieve net zero across the board you need a plan for every stage, but a shift in mindset will also be demanded. We can get there without the support of our supply chain and client base and there’s no reason why the successes and lessons we’ve learned can’t be shared with the sector as a whole.”
So, in that spirit of collaboration, what advise does she offer other organisations that may be only just beginning their net zero journey?
“There is now a huge amount of momentum behind the climate change agenda, but it’s important that they don’t become New Year’s Resolutions – there needs to be follow through. What is required is clarity on what can be addressed first and quickly without trying to tackle the whole carbon reduction and sustainability issue in one go, which is an overwhelming and quite daunting proposition. Keep it simple, don’t over complicate it, or get lost in the data.”
“Make sure ownership and accountability is a part of the plan – by holding individuals and companies to account. At the same time, it can’t just be about penalties because positive reinforcements and incentives should equally be in place.”
For further information on the Costain Climate Change Action Plan
The six-acre north London O’Donovan Waste recycling centre is now home to a Hitachi ZW220-7 Wheel Loader. “Exceptional safety, comfort and uptime,” where amongst the reasons for the choice, as well as a comfortable, ergonomic workspace for the operator with outstanding visibility, on-board camera equipment and intelligent safety systems.
GOTO
WWW.RDR.LINK/CAG012
The benefits of Zoomlion scissor lifts include a light weight at only 895kg, a large platform capacity of 240kg and efficient electric direct drive system complemented by proportional controls. As part of a wider commitment to replace its powered access fleet with specialist hybrid or electric equipment, AFI Rentals has purchased 50 of the manufacturer’s 15E machines for its scissor lift hire fleet.
GOTO
WWW.RDR.LINK/CAG014
Lifting solutions specialist, GGR Group sold the world’s first 17m electric telehandler to Flannery Plant Hire at Bauma 2022 in Munich. The new 17m is part of the ‘Big Range Full Electric” machine series, which comprises the 14.42, 17.40 and 17.45 models, offering maximum lifting capacities of 4.2, 4.0 and 4.5 tonnes respectively.
GOTO
Anglia Access has strengthened its hire fleet with a bi-energy lithium-diesel Hinowa Lightlift 33.17 Performance IIIS, supplied by Hinowa’s UK and Ireland distributor, Access Platform Sales With a maximum working height of 32.5m, the machine is the largest tracked boom lift in the Hinowa range.
GOTO
WWW.RDR.LINK/CAG013
WWW.RDR.LINK/CAG015
BYLOR, the civil engineering joint venture helping construct EDF’s Hinkley Point C Nuclear Power Station, has deployed the might of one of JCB’s machines to handle thousands of tonnes of steel.Supplied by dealer Holt JCB, the 555-210R will be used in the construction of walls containing reinforced steel and handling the mesh panels.
GOTO
WWW.RDR.LINK/CAG016
A collaboration between Tecnogen and the PUNCH Group has resulted in a ‘World First’, by combining a Hydrogen Engine with Flywheel Power System technology, integrated into a generator. The John F Hunt Group, who are openly committed to achieving Net Zero emissions, has become the first company to purchase the new unit.
WWW.RDR.LINK/CAG017 GOTO
Family-run hire and contracting firm, Monk Plant Hire, has added five new Yanmar excavators to its growing rental fleet. Supplied by dealer, Ben Burgess, the zero tail swing models – ViO12,2A, ViO17, ViO26-6, ViO50-6B and ViO82 – were specified for their performance, durability and suitability for a wide range of applications.
WWW.RDR.LINK/CAG018 GOTO
“One of the key things for us when we were looking for an excavator was safety,” explains Andrew Popplestone, Director of Stonevale Homes. That’s why the zero-tail swing, Hyundai HX235A LCR crawler excavator’s ability to work in tight spaces – and 360° camera system – appealed. The A-series upper frame design also significantly increases lifting capacity.
Land & Water has become the first company in the UK to invest in brand new Kobelco SK210 Hybrid 15m Long Reach Tracked Excavators. The excavators use hybrid technology alongside lithium-ion batteries to power the swing motor. This, coupled with the newest and cleanest engines, brings a fuel saving quality to the end user of up to 17% in comparison to conventional ICE excavators.
WWW.RDR.LINK/CAG021 GOTO
The TriAgg Group has only been in business since October 2020 but now operates a plant fleet of over 80 units. The civil engineering, surfacing and drainage contractor, has also recently completed a substantial investment in new equipment supplied by Tring based Boss Plant Sales including Manitou telehandlers, Bomag tandem rollers, as well as Kubota excavators from BPS.
WWW.RDR.LINK/CAG020 GOTO
Even a cursory view of the scale of the Ace Liftaway operation will reveal that it is a company that recognises the value of investing in the right equipment, and the addition of a £4million state-of-the-art wash plant to its already extensive 15-acre recycling centre is a testament to that commitment. The
The full range of Ace Liftaway recycling services comes together as a one-stop-shop for its clients and JCB is central to its processes, with recent investments including 2 x 150X and 3 x 220X excavators as well as two 437 wheeled loading shovels, and a JS145W wheeled excavator with high rise cab. There’s also a 456 shovel hard at work, a 722 ADT and 560-80 Loadall, as well as Teletruk forklifts with telescopic boom.
In total there are currently 18 JCBs in the fleet, with the company acquiring between 35 machines from the Staffordshire-based manufacturer in any given year. These include five X Series units– two in the 15-tonne class and three at 22-tonne – all with full waste spec. “JCB is a company that listens to the industry and the development of the Wastemaster range is a demonstration of
that,” enthuses Philip. “It’s a sector that demands the likes of cab guards and light guards, and these are machines that are fit for purpose. There’s 10mm belly plates on our excavators and ram dipper guards. The dippers are also reinforced and there’s heavier duty track plates. Air filtration systems are critical in a waste environment in guarding against dust as are reversible fans. All our machines are supplied by Greenshields JCB, who is an excellent dealer, and we have a full-three-year maintenance contract with each one. They’re an honest company that finds solutions to problems and that’s what appeals.”
“We’ve found the X Series to be considerably more fuel efficient than their predecessors,” Philip, continues “and with the hours of operation we undertake that’s a significant consideration, especially with the end of the red diesel rebate and what has been a dramatic increase to our fuel bill.”
First introduced in 2018, the JCB X Series has been more than four years in development. Powered by a Stage V DIESELMAX engine a spacious JCB CommandPlus cab is 15 per cent larger than on previous models. Auto-stop and auto ideal help with fuel usage, and there’s increased bucket tear out, a new hydraulic regeneration system, larger diameter pipes and hoses as well as customisable proportional controls.
The Stage V Cummins B 6.7 litre engine on the latest 437 wheeled loading shovel delivers 195hp (145kW), there’s a choice of loader
arms and axle options to suit any application and a unique 5-speed transmission with optional torque lock-up.
The waste industry is hard on machines and on the workforce, and the units will accrue some significant hours of operation, but Ace Liftaway is a company that prides itself on looking after its equipment. “Every machine has a handover sheet”, explains Operations Manager, Russell Delves. “When it moves from
represents a guarantee from the operator that
in that we couldn’t go on tipping valuable resources that could be recovered into a hole in the ground,” Philip reveals. “Landfill has had its day and that’s what makes businesses like ours so vital.”
The big issue in waste is to avoid cross contaminating the materials you’ve just spent time and money recycling – but the considerable space available at Hampshire recycling centre that Ace Liftaway has owned since 2002, together with the extensive fleet of machinery, largely eliminates that problem.
When fully functional, the 90 tonne an hour CDE wash plant will provide a high quality 10mm, 20mm and 40mm stone as well as sand and grit. There’s already a metal recovery facility on site, whilst plastics are processed. The company also undertakes land restoration works and in addition to the recycling centre, Romsey is also the base for the Ace Loos business, whilst there are plans to move into readymixed concrete.
“I’m a great believer in buying British and making sure my money is invested in the UK economy,” concludes Philip, “because ultimately it benefits us all. JCB machines are a very good product, fit for purpose and great value. We understand the value of being a single source of waste and recycling services to our own clients and calling upon JCB for all our plant requirements makes equal sense.”
site – with five separate bays – staffed by eight plant engineers, including a welder/fabricator, and all of our machines go in the workshop for a full safety inspection every six weeks. There’s a brand-new authorised test centre and we have our own tyre changing facility. LiveLink has proved an invaluable servicing tool,” Russell adds. “It’s also useful in managing fuel usage, as well as securing the machines from theft and misuse.”
Whilst the Hampshire firm might now be in command of many millions in equipment it’s a success story that stemmed from far more humble origins. The Ace Liftaway journey began when its founder Philip Liddell invested in a Ford Transit and eight mini skips. The introduction of Landfill Tax – and a succession of subsequent legislative moves – has transformed the sector and today the company has more than 1,500 skips, as well as an extensive fleet of more than 50 trucks on the road. These include skip loaders, roll on/roll off vehicles, tipper grab loaders, tippers, tractor units and trailers and compactor trucks.
“I realised even before the legislation came
Protect your workforce and machinery with the Doosan Waste and Recycling Kit for Wheel Loaders
Even for the most conscientious of operators waste handling and recycling comes with inherent threats to health.
Airborne dust, dirt and other dangerous particulates and materials all have to be guarded against and Doosan is now providing an effective line of defence.
The first of its kind for Doosan wheel loaders, the Korean manufacturer’s Waste and Recycling Kit has been introduced for its DL-7 range and is available for all wheel loader models from the DL200-7 through to the DL480-7 – the segment of the range that is most widely used in this sector.
The main features of the Waste and Recycling Kit include:
Windshield guards
Rim covers
Road light protection (Front + Rear)
Arm cylinder cover
Articulation guard
Front frame cover
Belly protection (Front + Centre + Rear)
Air intake mesh
Wider fin air conditioner condenser
Solid tyres
Several of these features will be available as options, so customers can choose a kit of their choice to tailor their wheel loaders for their specific applications. Doosan is also preparing an aftermarket version for the UK market for those customers who decide to install it at a later date. With the new kit, operators will be able to work more safely and confidently on these job sites and, in addition, Doosan is providing a wider fin air conditioner condenser as standard to facilitate easy cleaning and maintenance.
The DL-7 wheel loader range is driven by powerful new Stage V compliant engines, with the manufacturer promising higher productivity, increased fuel efficiency and a low
cost of ownership, coupled with a comfortable environment for the operator.
The DL200-7 to DL480-7 models feature redesigned buckets offering up to 7% more capacity for easier and faster loading with maximum bucket capacities from 2.0 to 4.8 m3 This provides increased productivity for a very wide range of material-handling applications.
As well as waste and recycling, these include the transport and delivery of soil, sand, aggregates and other materials in industry, for
applications in construction, demolition, mining and quarrying. Doosan is also offering a wider choice of options to provide more work tools for a better match with applications, further increasing output.
The Z-kinematic lift arm in DL-7 wheel loaders delivers high breakout forces and lifting capacities, especially for heavy materials, and a large dump angle for efficiently unloading sticky materials. An optional high lift arm is available where higher dump heights and increased
versatility are required.
The DL-7 loaders also have smooth and responsive hydraulics and auxiliary hydraulic connections. All of the new DL-7 wheel loaders are equipped as standard with a 3rd spool valve with settable flow and detent function, providing a constant flow for hydraulically driven attachments. Operators can easily and comfortably control hydraulic attachments via the proportional switch on the joystick. Various bias and radial tyre options are also available from leading global manufacturers, to cover the widest possible range of conditions and applications.
In addition, the new wheel loaders can be ordered with a choice of different counterweights – options include 300, 400 or 500kg depending on the application.
The upgraded hydraulic system and major parts ensure greatly improved durability and maintainability. Providing increased peace of mind for the customer, the high reliability and quality of the new DL-7 wheel loaders are backed up by a standard full 3 year/5,000 hour warranty.
With power provided by new Doosan and Scania Stage V 6-cylinder engines, the DL-7 wheel loaders provide up to 5% greater fuel efficiency than the previous generation machines, whilst delivering impressive torque.
The new engines meet Stage V emission regulations without the need for exhaust gas recirculation (EGR), through the use of selective catalyst reduction, diesel oxidation
catalyst and diesel particulate filter (DPF) aftertreatment technologies. The soot cleaning cycle on the DPF has been improved to over 6000 h and the operator is fully informed about the status of the DPF via a soot level indicator on the new touchscreen display in the cab.
i
For more information on Doosan Construction equipment
WWW.RDR.LINK/CAG 025
quarrying and aggregates sectors who have chosen to have their heavy-duty off-road trucks or dozers given a new lease of life. For example, we’ve recently completed a full rebuild of a Cat D9 dozer for Stokey Plant Hire, one of the UK’s largest suppliers of material handling and earthmoving services. The firm originally purchased the machine from Finning in 2007 and towards the end of 2021 decided to go ahead with a certified powertrain (CPT) rebuild rather than purchasing a new dozer. This was the first rebuild that they had commissioned and have been so impressed with the quality and performance they’ve already commissioned additional similar projects.
We’re seeing increasing demand from companies in the waste sector, as sustainability becomes embedded in the way they operate at a commercial level – and so they can meet their own customers’ green credentials. We recently worked with the NWH Group, one of the UK’s leading recycling and waste management businesses. Their mission – to change the industry for the benefit of the planet –illustrates a clear rationale for choosing to have two of their Cat 950M wheel loaders rebuilt when they reached the end of their operating life, instead of buying new machines.
Rebuilding a machine is by far the most sustainable choice. If we look at the environmental impact of manufacturing a new cylinder head compared with using a remanufactured one, it generates 61% fewer greenhouse gases, requires 85% less energy and uses 86% less water. A remanufactured cylinder head also requires 85% less material than a new manufactured product and means there’s 85% less waste being sent to landfill.
parts for the rebuilt machine, such as the engine and hydraulics, are sourced through a combination of remanufactured parts fully certified through Caterpillar, via the Finning parts service exchange programme, or bought new.
Customers choosing a rebuild machine option will typically save around 55-60% on the cost compared with buying a new machine, which
Stokey, can be minimised by carefully planning the availability of any reconditioned or new components so that there is limited downtime on the rebuild.
The team of engineers at Finning HQ in Cannock is currently working on a Certified Machine Rebuild (CMR) of a Cat 836 landfill compacting machine for FCC Environment,
The industry is facing many challenges, one of which is lengthier lead times for new machines and equipment – an issue that’s affecting all machine manufacturers and suppliers. Choosing to rebuild a machine is a viable alternative and gives customers an additional option when they’re looking at renewing or replacing equipment in their fleets. The length of time it takes to rebuild a machine varies according to the scope of the work and can be dependent on the availability of reconditioned and remanufactured parts.
The duration of a rebuild, as is the case for
fleet management and succession plan.
As we move closer to meeting the net-zero targets, we expect more companies to consider rebuilding machines and we’re looking to invest further to develop infrastructure to meet this rise in demand. All our current rebuild facilities are already booking up well into 2023 as we explore ways to increase our capacity for customer rebuilds.
For more out more about the Finning rebuild service, or to register your interest in having a machine rebuilt WWW.RDR.LINK/CAG 026
“We’re seeing increasing demand from companies in the waste sector, as sustainability becomes embedded in the way they operate at a commercial level – and so they can meet their own customers’ green credentials.”
High performance with low operating costs – that’s the promise for the Cat MH3250 and MH3260 Material Handlers. Fuel efficiency has been enhanced, there’s a new cab concept and both models feature mechanical variable-gauge undercarriages
Aggregates specialist, BP Mitchell Haulage Contractors, has reduced its insurance premium and successfully fought ‘crash for cash’ claims after upgrading its vehicle camera systems. The move from a six-channel to an eight-channel DVR system from Durite included moving from smaller monitors in the cab to 9” monitors
Whether it’s sorting or loading, the smaller material handler segment is well served with the Sennebogen 824 G series –part of an extensive range. A wide choice of different equipment options is complemented by a crawler or mobile undercarriage, equipment lengths from 10 to 12m and/or ULM rod variants.
FOR MORE INFORMATION
WWW.RDR.LINK/CAG028
It was the decade-worth of service that Manchester-based, D Hughes Demolition enjoyed from a previous FMX model that prompted the company to invest in a Volvo FMX 420 8x4 rigid. Supplied by Thomas Hardie Commercials, the vehicle is mounted with a Hiab Multilift hookloader body and VBG drawbar coupling.
FOR MORE INFORMATION
WWW.RDR.LINK/CAG030 GOTO
The Brokk Surface Grinder 530 (BSG 530) is a material removal attachment for paint and asbestos, surface preparation and polishing on walls, floors and ceilings. Pairing the surface grinder attachment with the company’s remote-controlled operation also offers greater worker safety.
FOR MORE INFORMATION
WWW.RDR.LINK/CAG031 GOTO
Environment before profit is the message from O’Donovan Waste in switching to using solely Hydrotreated Vegetable Oil (HVO) biofuel for its entire fleet of 100 lorries. HVO is a an alternative to petrol and diesel that reduces carbon dioxide
hire businesses thousands of pounds. Given the current economic uncertainties and insolvency risk, companies cannot afford to
When pursuing a claim, hire companies will only be successful if they have sufficient evidence – including inspection reports, photographs, and signatures – that the equipment wasn’t supplied in this manner. However, it is a difficult and time-consuming task to gather and store this information when relying on paper-based processes. Even if this evidence has been gathered, in practice, it is possible that documents will be misplaced or damaged and hard to trace if not filed meticulously.
Digital data capture solutions eliminate this possibility by storing essential documents in one cloud-based location.
Construction workers, contractors, and managers can each share this documentation between one another from any location with an internet connection, without the risk of vital information going missing or being destroyed. Therefore, should a situation arise where companies need to pursue damage escalation, paperless processes ensure businesses are provided with the required documentation to succeed.
As construction workers are often spread between different sites, simple communication can become a difficult task. When companies rely on traditional, paperbased methods of data collection, communication difficulties are amplified. For example, if a worker collects vital documentation but is stuck in traffic on their way to the site, they may only realise on arrival that the details are incorrect and must be rectified before equipment can be released or work can begin.
Mistakes like this slow down the
Manchester-based, WorkMobile is an award-winning mobile data capture service that replaces paper forms. Using the API, data captured may be integrated into back-office or ERP systems and further extended into a bespoke workflow solution that includes a variety of management information reporting options.
workforce and have the potential to waste hours of productivity. Although this has a damaging effect through project delays, it has also been shown to result in costly overruns that impact on the company’s financial health. However, by digitising these processes with mobile forms, the data collected can be imported and stored directly within a cloud-based database. This means that any permitted employee can rectify document discrepancies immediately and with ease, preventing any costly project delays or reputational harm.
Everyone within the construction industry is aware of the importance of compliance, but the key to remaining compliant is to keep thorough and accurate documentation. However, as the nature of the industry means that workers often rush from one site to another, documents are often inefficiently logged or misplaced.
Storing documents in a tangible location, such as construction offices, always runs the risk of essential information becoming damaged or being destroyed. If compliance processes are breached as a result of this occurrence, companies may face legal costs if professional standards have been infringed.
On the other hand, digital data capture solutions can greatly enhance the company’s data integrity by collecting accurate information, ensuring all forms are fully completed, and minimising inconsistencies that threaten compliance. The ability of mobile forms to capture evidence such as timestamps, dates, and client notes helps managers to analyse data that is almost impossible to accurately collect without digitisation and increases employee accountability.
The construction industry is being stretched to its limits for a variety of reasons, but inefficient data processing doesn’t have to be one of them. By making this simple change, companies can maximise employee productivity and workplace communication whilst reducing the possibility of financial ill health.
sooner businesses implement digital data capture solutions, the sooner they
gain a real
For further information on WorkMobile visit
The
can eliminate avoidable mistakes and
competitive advantage.
“The ability of mobile forms to capture evidence such as timestamps, dates, and client notes helps managers to analyse data that is almost impossible to accurately collect without digitisation and increases employee accountability.”
not influenced by weather or light, so can be used at all times in all site conditions.
Hyundai’s SGS (Smart Guard System) is a smart obstacle detection technology that uses sensors around the machine with a deep learning function. The system emits visual and audible warnings when it detects a person within its working envelope.
The company has further developed its AAVM+ (Advanced Around View Monitoring) system for wheel loaders. This next-generation system will be launched in 2023, combining rear radar sensors, a steering angle sensor and the AAVM system, significantly improving safety to the rear of a loader. Like an automotive parking system, the technology displays the intended area of operation, highlighting hazards and reducing blind spots for the operator. The AAVM+ system defines the warning/danger zones, keeping false warnings to a minimum.
E-Bounds are a virtual electronic boundary or geofence that can be pre-set by the operator on site or by the manager in the office. The machine’s work equipment will not function beyond the electronic boundary, protecting personnel and facilities on site and preventing unauthorised machine use.
Through the use of HiMATE telematics customers have access to real-time diagnostics for preventative maintenance. The system can deliver operational reports and can be used to set geofenced working areas. Working through the HiMATE website, operators have access to troubleshooting guides, while fleet managers can access monthly equipment reports through the Fleet Manager app.
Third-party fleet management systems can also make use of Hyundai’s Hi CARE technology, with standard protocol APIs allowing the transfer of data to external operating systems. Hyundai is also working with engine supplier Cummins to deliver ECD (Engine Connected Diagnostics), making it easier for engineers to pre-diagnose faults and to ensure single-visit repairs on site.
For further information on Hyundai Construction Equipment WWW.RDR.LINK/CAG 034
Packed with articles on a wide range of industry topics, www.cpnonline.co.uk is the first place to visit for all the latest news in plant and machinery – from the smallest skid steers and micro excavators to the giants of the tower crane market, or the heavyweights in crawler excavators, weʼve got it covered. Get the latest information on the industryʼs biggest deals, as contractors and plant hirers renew their fleets in our Fleet Additions section, as well as all of the newest products to hit the market. Our website is updated daily, bringing you the most important industry news quicker than ever before.
Vimprovements and compliance. Whether making equipment easier and safer to manoeuvre or providing construction companies with a comprehensive picture of how equipment is being operated, the technology is helping to reduce collisions and protect vulnerable people.
On average, seven workers die each year after collisions involving vehicles or plant on construction sites in the UK, while 93 more are seriously injured. On top of this there are also those incidents involving vulnerable people that occur on the road network or at the entrance of a site.
A combination of cameras and sensors gives the driver a complete view around the plant via an in-cab monitor. Front, side and rear cameras ensure equipment is covered from all angles, while corner, side and rear sensors warn of nearby people – such as workers, pedestrians or cyclist – especially in blind spots. The system can also be linked to specific driving manoeuvres, so a driver can view the appropriate camera when, for example, the left-hand indicator or reverse gear is engaged.
Moving forward, AI is going to play a far greater role in video telematics and become increasingly embedded in camera hardware. The latest intelligent detection cameras adopt deep learning technology to provide real-time insight. They can identify and track vulnerable
people, making it possible to trigger an alert to the driver – and even activate an external, audible alarm – when someone enters virtual exclusion zones around the plant.
With traditional proximity sensors, alerts can be triggered by inanimate objects, so there is a risk that drivers become complacent and takes less notice of an alarm because of false positives. The AI-powered detection camera can locate people up to 20 metres away in realtime, establishing the severity of risk dependent on their proximity to the equipment. With such high levels of accuracy and range, it provides the driver with increased reaction time and reduces the possibility of collisions.
Video telematics technology is no longer simply a driving aid, because increasingly forward-facing cameras and mobile digital video recorders (MDVRs) are connected to a cloud-based platform. Recorded footage and supporting data of any collision, near miss or harsh driving event is therefore uploaded and can be viewed almost instantly.
With traditional telematics you might see that one piece of plant has had three harsh breaking events, but without more information this is just general trend information. By using video footage alongside telematics data, it is possible to see what the information is really saying. If video shows someone doing something risky that is linked to the event,
then a more meaningful intervention can be made to improve safety. It also allows driving styles to be measured and analysed, so steps can be taken as part of wider safety strategy and training initiative.
Construction businesses can also monitor compliance using captured video and data. Almost any activity can trigger a recording by combining video telematics with event tracking on the equipment. Because cameras can be fitted almost anywhere on the plant, it is possible to ensure drivers are not ignoring safety procedures and investigate following a complaint or incident.
There are also multiple voluntary and mandatory safety standards operating within the UK that are designed to mitigate collisions related to the movement of construction plant and vehicles. In some instances, construction sites may enforce multiple specifications including Construction Logistics and Community Safety (CLOCS), Fleet Operator Recognition Scheme (FORS) and Direct Vision Standard (DVS), which require some form of camera system. Therefore, adopting a compliant video telematics solution has an important role to play in meeting safety requirements.
Having driver performance information at your fingertips can facilitate an effective feedback loop. This makes it possible to praise drivers when they are performing well but have that opportunity to mention areas of improvement around harsh driving
A driver app can further complement a telematics solution, enabling construction companies to better communicate with drivers and ensure they are following vehicle safety procedures.
By providing drivers with an individual score, viewed alongside company and peer group averages, its possible to create a competitive element that can quickly translate to responsible driving, safety and efficiency benefits.
With PTO (Power Take Off) / Event tracking, it is now possible to have full visibility of all aspects of platform equipment activity. PTO sensors integrate seamlessly with the on-board tracking unit and can capture data from a wide range of analogue and digital inputs. Tracking units can also be integrated directly with engine management systems to provide greater understanding of the performance and usage of assets.
The integration of cameras with telematics software allows plant operators to bring together consistent and accurate driver behaviour details with video footage in a single platform, without the hassle of using multiple systems. The latest artificial intelligence-enabled cameras are being used to prevent accidents from happening in the first place by targeting
innovation can boost plant performance according to Steve Thomas, Managing Director, Inseego UK
Many of Synergy Hire’s large infrastructure clients require the rental firm’s excavators to be fitted with a slew and height restriction system. As a consequence, the hirer was the first company to fit Xwatch as standard on its Hitachi fleet and it’s the ease of use for operators – with just a few pushes of buttons necessary – that appeals.
FOR MORE INFORMATION
WWW.RDR.LINK/CAG037
A machine-control solution that enables compact excavators to carry out designs easily and accurately is now available from Leica Geosystems . The iCON site excavator technology introduces three new components: a new software
New functionality from rental software supplier, MCS , enables hirers to take site photographs and GPS details to help locate equipment on site quickly and easily. When it comes to servicing or collection, drivers or engineers will know precisely where on-site
Hire companies can monitor equipment damage, and improve the management of reclaim charges, with the help of BigChange . Its Job Management Platform provides an audit track of condition of all assets, with inspection reports supported by time and location referenced photographic evidence, including photos taken on site when delivered and collected.
FOR MORE INFORMATION
WWW.RDR.LINK/CAG040 GOTO
A radar sensor for collision avoidance in even the most extreme weather or harsh industrial conditions has been introduced. The SICK RMS1000 Radar Sensor achieves long-range resolution and distance accuracy where radar technology is selected because of the harsh operating conditions, such as in heavy rain, thick fog, heavy snow or dusty environments.
FOR MORE INFORMATION
WWW.RDR.LINK/CAG041 GOTO
The ConSite Air machine management development from Hitachi Construction Machinery (Europe) NV (HCME), provides an option to update software and access diagnostics remotely. As a result, remote software updates can be carried out without the need to visit the machine and remote access to diagnostics enables remote assistance.
FOR MORE INFORMATION
WWW.RDR.LINK/CAG042 GOTO
As the demand for new housing increases, construction site conditions become increasingly challenging on people and machinery. Manitou has designed the MT (Manitou Telehandler) range to meet ever changing demands. Whatever the work site environment, Manitou Telehandlers have been designed with modern technology to maximise the productivity and safety of drivers.
The range consists of a choice of units from 4 – 18 metre lift height, with models featuring compact dimensions and some compatible with an access basket. Frame leveling is now standard on the 11 – 18 metre models which gives greater accuracy when placing loads. The 14 – 18 metre MT models are now equipped with a heavy-duty engine cover made of Telene, thermo hardened resin which absorbs shocks without deformation. As a result, they have increased resistance to impacts on site as well as to heat and vibrations. They’re easily repairable in case of cracks or paint touchups and, thanks to their optimised weight, are straightforward to transport.
The MT 14 – 18 range offer the following features:
Perfect maneuverability and three steering modes – 2- or 4-wheel steering crab mode
Impact-resistant cabs with 360-degree visibility
Easy handling thanks to a clear and modular dashboard, intuitive controls and a JSM (Joystick, switch and move) that provides flexibility and precision of movement.
Optimum safety thanks to highperformance stabilizers, several braking. systems and a particularly robust design Wide stabilisers for frontal and lateral stability.
75 hp or 100 hp engine.
The ‘Safety Pack’
Manitou offers options to increase safety when working on site. The stop & start
solution automatically stops the engine when the machine is idling without a driver in the cab, based on a time (delay). To adapt to the needs of each professional, this time can be configured from 1 minute up to 30 minutes.
You can also upgrade your cab for a
It’s a home win with the Manitou MT Construction range
crossing bar over the window and a reversing radar with sonor and visual indicators in the cab. With the orange seat belt, it can easily be identified to ensure safety when driving the machinery. A red beacon is installed on the roof with automatic pop-up display and alerts on the harmony dashboard to ensure protocols are followed. Pedestrian and obstacle detection is also an option within 2.5 metres of the machine.
If you’re looking for a smaller, more compact machine without compromising on lift and capacity, the French manufacturer has responded to this need with its new MT 730
typical domestic sized garage door.
The MT 730 H, MT 930 H have maximum lift capacity of 3 tonnes and can reach 7m and 9m respectively. The MT 930 HA model has the added benefit of being able to carry a man platform making it truly versatile. All models feature a new floating fork carriage that folds back the forks during transit reducing the length to just 4.67m for transport. With the launch of two new attachments, a new 2m narrow bucket dedicated to heavy bulk, or folding forks, you now have a powerful piece of equipment intended for the most confined spaces.
Manitou Group prioritises lowering TCO across the board. Users of the new MT compact range can now analyse their hydraulic oil to identify when it needs to be changed. Situated under the boom, there are two access points for easily collecting oil samples, making it an easy and clean solution.
engine when idling. It can be configured from 1 minute to 30 minutes and restarts the engine when the accelerator pedal is pressed or via movement of the JSM joystick. The fuel savings, wear on components and the noise reductions are particularly significant. Reducing potential idle time has the potential to prolong the requirement for a DPF regeneration, resulting in less down time on site.
i
To find your local dealer
WWW.RDR.LINK/CAG 043
To discover the Manitou compact i
The construction industry has undergone enormous changes over the last three decades, particularly through digitisation, an increased focus on site safety and the move towards standardisation and modern construction methods. Even as recently as the last three years, life on the construction site has shifted dramatically, with Covid-19 changing the way we manage projects and interact on site.
So, it’s no surprise that the nature of site accommodation has also changed beyond all recognition over the years. What started out as little more than a basic shelter, has now been transformed into any number of sophisticated, modular buildings which can be configured to almost any given specification and layout.
With over 60-years’ experience in this
sector, we like to think that we understand the needs and challenges of life on-site and have a wide range of solutions to match.
Here, we look at how site accommodation has developed over the years, with the focus now shifting towards staff welfare and changing needs to site management and sustainability.
The earliest, timber-constructed site cabins date back to the 1950s, when we became the first to design cabins specifically for construction workers. At that time, they consisted of little more than four walls, a door and a floor. In the mid-60s, steel stackable site accommodation that could be heated began to appear. By 1995, we were the first to incorporate WCs and welfare
facilities in stackable site accommodation.
Things have moved on considerably in recent years, with modular building hire shifting from individual cabins to configurations that support meetings on site with large groups of people, including architect and client meetings.
Companies no longer see hired site accommodation as being solely individual modules (although they remain a large part
Algeco explores how staff welfare and well-being is driving new developments in modular site accommodation
of the mix). The way forward is now flexible layouts where several modules can be positioned together to create an open plan space.
Temporary site accommodation can be built to almost any size or specification, with endless layout and configuration options. Whole site accommodation villages can be created using scores of linked and stacked units, depending on workforce size. Internal walls can be removed for a large open plan office or added in to create quieter workspaces. Staff welfare areas, kitchens, storage facilities and shower blocks can be incorporated according to individual site requirements.
Once the building is in place, all kinds of sophisticated systems can be added, from IT networks and comms systems and smart technology. 360O turnkey solutions are available, right down to delivery and installation of kettle and toasters, so sites can be up and running from the moment the accommodation arrives on site.
Modular site accommodation is evolving to meet the changing needs of today’s construction companies. Staff welfare and good mental health in the workplace are being prioritised more than ever before, so it’s no surprise that site accommodation for hire has
site buildings.
As well as catering for the needs of a diverse workforce, temporary modular buildings offer increased site visibility, security and fire protection, ensuring staff safety and providing attractive, high-quality accommodation. This in turn widens the talent pool and combats the skills shortage by helping to attract skilled workers who previously may not have considered a career within construction.
Modular temporary buildings are also wellinsulated, energy-efficient, recyclable and designed with sustainability in mind. In fact, the green features of site buildings are a huge part of their appeal, as Algeco Business Development Manager for the housebuilder sector, Jonathan Pringle notes:
‘The construction industry is very focused on climate change. Companies are looking at how they can work more efficiently and sustainably, and many have set challenging targets to reduce emissions.
control. They can even use smart technology to monitor, manage and reduce carbon and electricity usage.’
Crucially, all elements of these buildings can be recycled and reused once the project is complete, drastically reducing waste and extending the product’s life.
Flexible, open-plan environments Covid-19 has accelerated the adoption of modular site accommodation within the construction industry. Jonathan comments:
‘The pandemic created a pressing need for customisable, flexible, open-plan environments. Modular buildings promote safe, collaborative, hybrid working and allow for layout changes even after the building is in place, which is important when working practices and regulations are constantly shifting.’
It’s clear to see that site accommodation has evolved beyond all recognition in recent years. But what does the future hold? According to Jonathan:
‘The challenges we’re seeing today with supply chains and an unstable economy mean that companies need to be as lean as possible. Modular site accommodation can be quickly increased and decreased in size according to changing needs. It can even be moved from site to site, to accommodate peripatetic project teams. It’s efficient and it maximises productivity, which will be important in the coming years.’
‘The focus on sustainability and climate change will continue to grow and I think we’ll see increased innovation to support this. Modular site accommodation is here to stay, but it will continue to evolve along with the needs of the people it accommodates.’
They will no doubt play an important role on a variety of sites for years to come. However, over the last ten years we have seen the humble site cabin evolve into highly sophisticated modular site accommodation.
find out more about Algeco WWW.RDR.LINK/CAG 045
To
i
“Modular site accommodation can be quickly increased and decreased in size according to changing needs. It can even be moved from site to site to accommodate peripatetic project teams. It’s efficient and maximises productivity.”
bauma is the construction plant industry’s biggest stage and many manufacturers used it to debut new machines and solutions.
The machinery of tomorrow on the Bobcat stand included the world’s first all-electric compact track loader – the T7X. With an operating capacity of 1,374 kg and zero CO2 emissions, a 60,5-kWh lithium-ion battery pack, can deliver four hours of continuous use. In addition the hydraulics have been completely replaced with an electrical drive system.
Innovations from Doosan at the world’s largest construction trade fair include the manufacturer’s XiteCloud ‘All-in-One Platform’ for smart construction, its ‘Transparent Bucket’ system in operation and the DX225LC-7X ‘Smart’ Crawler Excavator. The Korean manufacturer also demonstrated its DoosanCONNECT App.
WWW.RDR.LINK/CAG047
The low noise, zero-emission design of the Doosan DX20ZE two tonne electric miniexcavator is combined with the features and high performance of the equivalent dieselpowered unit. With a width of just 950mm, it can pass through narrow passages and is ideal for operating indoors or in areas where low noise and/or night-time work is necessary.
WWW.RDR.LINK/CAG048
The engcon ready option for the Doosan DX225LC-7X series of excavators provides an
Danfoss is powering a new fully electric crawler crane. The 80-ton SANY SCE800TB-EV includes a motor and inverter supplied by Danfoss Power Solutions’ Editron division and a Danfoss Power Solutions D1P hydraulic pump. The crane will cut carbon emissions, improve air quality, and reduce noise.
GOTO
WWW.RDR.LINK/CAG049
integrated solution between the tiltrotator control system and machine, with all the builtin functions and features. The machine can easily be equipped with the tiltrotator manufacturer’s MIG2 Grips and the 3rd generation control system, DC3.
WWW.RDR.LINK/CAG050
The latest 70t Manitowoc crane features the longest boom and strongest load charts in its class. Its MAXbase technology allows for simpler and more flexible outrigger placement
An electric range and a new branding were both revealed by Ausa at the Munich event. The D151AEG is the company’s first electric dumper with a 1,500 kg payload. The all-terrain T164E has a maximum lifting height of 4 metres and is the first electric telescopic handler with a 1,600 kg payload.
GOTO
WWW.RDR.LINK/CAG054
A solution ideal for small to mid-sized building projects is the billing for the Potain MDT City crane range. The MDT 159 which comes equipped with the new manufacturer’s CONNECTTM telematics system and owners can choose between two trolleys – a DMP unit with permanent double reeving for maximum lifting power or an SM/DM Quick Lock trolley for the flexibility to change reeving.
The intelligent electric system on Komatsu’ s fully electric wheel loader prototype includes an electric traction motor, lift, tilt and steering electric cylinders, power electronics, system control computer, battery, and battery management system. The same manufacturer also revealed a 20-ton class electric hydraulic excavator powered by a lithium-ion battery system.
WWW.RDR.LINK/CAG052
There’s a shift to electric in the Manitou portfolio as well as seven new models: four new aerial work platforms, and two new rotating telehandlers, including the first 100% electric compact telehandler. Bauma also played host to four new medium-height telehandlers, whilst there was a reinforced compact presence with a new range of articulated loaders and the Ultra Light Manitou (ULM).
WWW.RDR.LINK/CAG053
Under the theme “Keep on growing with a strong partner”, SANY unveiled a diverse range of new machines at this year’s bauma, including the 1.8-tonne SY19E electric mini excavator. Other new additions include the 4-tonne rated capacity STH1440 and STH1840 telescopic handlers. This was joined by a SW305 heavyduty wheel loader with a 2.3m³ bucket capacity and operating weight of 14.5-tonnes.
WWW.RDR.LINK/CAG056
The ZX130LCN-7 HE13 super long front (SLF) excavator has a 13m reach and is ideal for dredging rivers and lakes, bank maintenance and slope-finishing tasks. The 13-tonne Stage-V compliant Hitachi machine benefits from the HIOS V hydraulic system which helps to deliver up to 9% less fuel consumption than the previous model.
GOTO
WWW.RDR.LINK/CAG057
Under the motto “Meet the Future”, Wacker Neuson presented the DV45 Dual View Dumper. The APU3050e is the first battery-powered reversible vibratory plate with direct drive and the TH412e electric telehandler made its debut. In addition, the third generation of the WL20e E-wheel loader with a powerful lithium-ion battery was unveiled.
GOTO GOTO
WWW.RDR.LINK/CAG058
The “Green Heart of bauma” belonged to Sennebogen in 2022 with two batterypowered machines both in the crane and in the material handling area – the 30-t 825 Electro Battery recycling material handler and the 50-t 653 Electro Battery telescopic crawler crane. A Dual Power Management System permits both battery-powered and mains-powered operation.
WWW.RDR.LINK/CAG059
Two new loader models, Avant e5-27 and Avant e5-13, will be equipped with Avant Tecno ’s OptiTemp batteries (27kWh and 13kWh) featuring what is described as a unique thermal management system. The technology keeps the temperature optimised and gives you the same capacity in hot and freezing weather.
WWW.RDR.LINK/CAG060
Modular, smart and emission-free electric access platforms were the highlight of the
first prototypes of mobile and retrofittable eDRIVE battery packs enable quick and easy conversion to emission-free operation.
GOTO
JLG Industries and Hinowa continued their relationship at bauma with the EC Boom Series Mark II, represented by the EC520AJ. Updates include an advanced battery technology, with an improved capacity of 10kW, including the option to upgrade the pack to 20kW for prolonged duty cycles and autonomy. There’s also a 4x4 drive option.
GOTO
A new control system, new tiltrotators, an app and joysticks combine to make up the Rototilt Control concept. Eoin O Connor, machine operator and winner of Rototilt’s competition – Excavator Hero 2021, described the joysticks as a “game-changer. The operation of the tiltrotator itself is on another level, effortless operation actually” says Eoin.
GOTO
WWW.RDR.LINK/CAG063
WWW.RDR.LINK/CAG062
An all-new, all electric 3-tonne dumper has been introduced by Thwaites . Four maintenance free, long-life, lithium-ion (dry-cell) batteries, operating at 48V, are fitted. Each battery is rated at 5.75kWh, with two highly efficient electric motors (one for traction, one for the hydraulic services) giving the operator the control and manoeuvrability expected from a Thwaites dumper.
GOTO
WWW.RDR.LINK/CAG064