We are Baroid
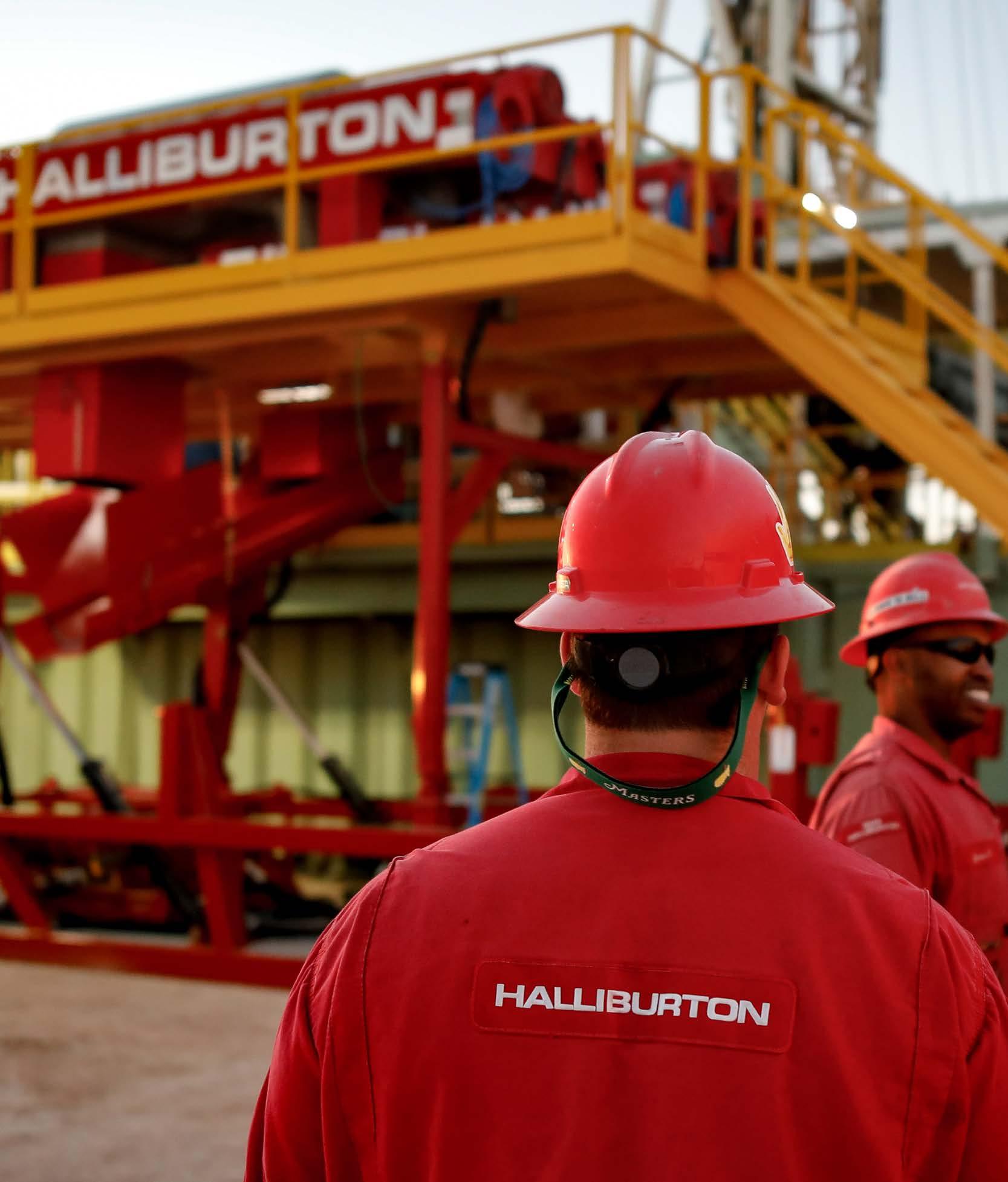
We are the largest and oldest mud company in the world, operating since 1929. Our value proposition — engineered fluid solutions customized to maximize wellbore value — focuses on creating tailored fluids that increase our clients’ operational efficiency to reduce costs, and/or increase the number of barrels they produce.
Nothing is more important than keeping people safe and protecting the environments in which they work. Our company-wide HSE and SQ initiatives encompass personnel safety in addition to process assurance and execution.
Halliburton even organizes our product service lines with attention to HSE and SQ in the process design, execution, training, and competency standards of the people performing the work.
We have continuously served the Marcellus and Utica basins for decades. During this time, our Five Mainstays — People, Technical, Black Book, Business Acquisition, System Rationalization — have endured and helped Baroid deliver unmatched service quality to our customers.
Montgomery, Pennsylvania
Zanesville, Ohio
Montgomery, Pennsylvania
Zanesville, Ohio
9,550 barrels liquid storage
10,300 cu/ft barite bulk
10,500 sq/ft of warehouse storage
8,750 barrels of liquid storage
Engineering fluid and waste management solutions customized to maximize wellbore value.
Our team is committed to providing the best possible service and promotes instructional effectiveness to ensure our engineers deliver distinctive service quality in every customer interaction.
Our Five Mainstays are critical elements in delivering distinctive service quality. These elements — People, Technical, Black Book, System Rationalization, and Business Acquisition Process — are specifically designed to achieve our value proposition.
We relentlessly pursue and create custom fluid solutions that increase our clients’ operational efficiencies to reduce costs and/or increase the number of barrels produced.
SYSTEM RATIONALIZATION
How we manage our product portfolio
Baroid
BLACK BOOK
How we execute our services
PEOPLE
How we develop our people
A Step Ahead
BUSINESS ACQUISITION
How we win work
TECHNICAL
How we develop our solutions
WE ARE BAROID | PAGE 3
Halliburton develops and deploys innovative fluid technologies that help you produce more for less. We engineer advanced separation solutions for maximum performance by removing unwanted solids at the surface, recovering fluids for reuse in the active system, and optimizing your rate of penetration.
With industry-leading expertise and a customized approach, our teams are prepared for any resource play, anywhere in the world. Using rigorous practices and advanced digital technologies, we engineer solutions that boost overall performance while improving safety.
We believe in maximizing the value of your asset by listening, aligning, executing and continuously improving.
Operators in the Northeast U.S. are hyper-focused on maximizing drilling performance while reducing the risk of major downhole issues. This pursuit is progressively more challenging as the complexity of wells increases.
Conventional Fluids
INVERMUL ENVIROMUL
Halliburton offers a family of non-aqueous fluids formulated for our Northeast U.S. customers. They not only provide increased equivalent circulation density control, but do so without sacrificing hole cleaning efficiency and resistance to barite sag.
High Performance
BaraXcel
Mud Plants and Laboratories
Halliburton delivers security of supply with multiple stock points and liquid mud plants across the Northeast region that deliver high capacity in the basin — reducing time to the well head.
Specialty Fluids
BaraXcel DrilN
BaraECD
Providing customized engineered solutions to maximize wellbore value is the operating directive for Halliburton laboratories worldwide. Halliburton Baroid’s technical infrastructure includes research and development, technical services, technical support, and quality assurance. Dedicated scientists and engineers staff these laboratories equipped with standard and state-of-the-art equipment for evaluating drilling, drill-in, and completion fluids and products.
Separation solutions from Halliburton provide operators with a wide range of high-value services designed to maximize fluid performance and minimize environmental impact. We do this with a specific focus on providing measurable reductions in operational expenses.
Thanks to process-driven execution, tailored design, market-leading technologies, and extensive experience, Baroid fluid separation systems help operators reliably achieve higher profit margins.
Maintaining fluid properties helps increase drilling efficiency and overall performance. Predictable fluid densities and rheologies are critical to keep wellbore integrity intact.
Effective solids removal is a key component to ensuring fluid consistency.
Halliburton has a range of separation technologies and services to help you clear unwanted solids from your circulating system to extend the life of your fluids and maximize rates of penetration (ROPs).
Solids Control & Fluid Processing
• Shale Shakers
• High volume centrifuges
• Cuttings dryers
• High-flow filtration
• SwiftPlant® fluid mixing and storage facilities
• On-the-fly (OTF) mixer
• Hydraulic shearing unit
• BaraMesh® shale shaker screens
• BaraMag® Swarf Separation & Recovery
BaraOmni is compact, mobile technology that treats cuttings and drilling fluids. This technology removes ultrafine low gravity solids — allowing operators to recover and reuse fluids.
SUCCESS STORY
Waste Handling & Transfer
• Augers
• Skip & Ship
• BaraStream pneumatic conveying systems
• HCB™
• SV400™
• Cuttings Transfer Tanks
Waste Treatment & Disposal
• BaraOmni
• Thermal Treatment Unit (TTU)
• Thermal desorption unit (TDU)
• Thermo-mechanical cuttings cleaner (TCC)
• Dissolved air flotation units
• Full-circle cuttings reinjection process
• Wastewater treatment
• Solidification / stabilization
A major operator in the Northeast U.S. wanted to extend their laterals, drill in record time and reduce budget on location. Maintaining the integrity of the drilling fluid was critical to safely and successfully protecting the wellbore and achieving their goals.
WE ARE BAROID | PAGE 7
Halliburton collaborated with the operator to implement a total fluid solutions program to help the customer achieve a world record 12,340 feet in 24 hours. The program included custom drilling fluids and adapted shaker screens. The separations strategy helped maintain the fluid integrity and protect the wellbore during the operation.
» 12,340 feet in 24 hours (514 hourly average ROP)
» Instantaneous ROP of 900-plus feet per hour
» Operator average for this pad was 3.9 days per 10,000 feet
» No tripping or casing delays
Increased Drilling Performance
• Low volatility with water influx better stability
• Increased ECD control and excellent hole cleaning
• Increased penetration rates
Increased Access to Reservoirs
• Superior return permeability, low lift pressure
Superior Hole Cleaning
• Reduced NPT associated with barite sag, lost circulation and ECD control
Cost Savings
• Improved logistics and rig space use
• Reduction in diesel consumption
Custom Application
• Decreased wellbore limitations
• Stable performance over a wide temperature and density range
No Ogranophilic Clay and Lignite
• Increased rate of penetration
• Less product less footprint — reduce total cost of ownership
Organophilic Clay and Lignite
• 1960’s Clay Technology
Fatty Acid and Polymers
• No organophilic materials
Fluid Design
• Higher solids
• Low tolerance to water flows and LGS
• Low solids for faster penetration rates
• High tolerance to water / solids contamination
Fluid Performance
More solids & losses = more chemical and base oil used to stabilize fluids
Unique fragile gel structures for lower downhole losses
Cost
Higher wellbore construction costs due to lost circulation
Lower product and base oil used
Reservoir Performance
Possible formation damage, reduced return permeability
Superior return reservoir permeability
SUCCESS STORY
Operator drills monobore with BaraXcel™ high-performance non-aqueous fluid system, setting lateral ROP record
An operator in the Bakken Basin challenged Halliburton to deliver a integrated solution to drill a monobore with the same AFE days as standard wells.
By listening to the technical challenges and through collaboration with the operator, the Halliburton team developed an engineered drilling solution. This included the BaraXcel™ high-performance, non-aqueous fluid system with dual centrifuge BaraG-Force Vac VCD solids control system, along with Sperry’s 6¾-inch iCruise® intelligent rotary steerable system (RSS), matched with an 8½inch GeoTech® GTi54WMO lateral drill bit, powered by a 7-inch. NitroForce® high flow, high torque motor.
The solution helped the operator maximize asset value by delivering a drilling fluid stable enough to leave the standard 8.75-inch wellbore exposed while delivering ROP performance comparable to the standard NaCl Brine in the lateral section.
The well was delivered 0.28 days ahead of AFE, with an average dogleg severity (DLS) of 0.62°/100, and a 3.5% increase in ROP, while keeping surface torque under 26k ft/lb. Additionally, the monobore well design was proven to be effective for this type of application, identifying future savings and reliability in the completion arena, further optimizing customer assets.
The BaraG-Force VacVCD system played a critical role in setting the ROP record.
Halliburton is connecting its leading technical processes with newly developed chemistries to maximize your wellbore. Engineered fluid systems, such as BaraShaleTM and BaraXcelTM, are revolutionizing how we manage the wellbore.
These systems connect with the BaraLogixTM digital platform to deliver previously unseen insights and predictable outcomes. Live data interacts with vast historical offset
data, artificial intelligence, cloud-based software and in-field technical experts to help predict risks before they become problems. HindSight20/20TM gives operators a secure platform to visualize their fluid performance.
Our versatile and adaptive fluids systems help manage risk, improve wellbore stability and enhance performance.
The HindSight 20/20 platform provides a secure platform for operators to visualize their drilling fluids programs.
REAL-TIME SERVICE
WELLBORE PRESSURE MANAGEMENT
• Hydraulics while drilling, tripping, circulating, or static
• Swab/surge with pumps running
• Cradle-to-grave cuttings tracking
• Automated ROP and Trip speeds optimized in real time on the driller’s screen
• DrillAhead predictive hydraulics
• Real-time transient gel and temperature modeling for tripping, circulating and drilling
BaraLogix Real-Time Service
combines Drilling Fluids Graphics (DFG), advanced hydraulic software, surface measurement automation, and predictive analytics to improve casing to casing time.
Sensors capture data from the Density & Rheology Unit (DRU) and feed it into secure cloud databases.
Advanced Fluids Optimization (AFO) engineers and artificial intelligence compile, sort and analyze data. They then provide intervention and mitigation steps.
Drilling Fluids Graphics (DFG) interface for trending and analysis.
AFO engineers collaborate with fluid engineers and operator personnel to implement recommendations for efficiency improvements.
halliburton.com
Sales of Halliburton products and services will be in accord solely with the terms and conditions contained in the contract between Halliburton and the customer that is applicable to the sale.
H014334
8/1 © 2023 Halliburton. All Rights Reserved.
halliburton.com