
18 minute read
Volvo’s new DMX refines all-terrain trucking
from IMIESA February 2021
by 3S Media
Volvo’s FMX truck. A 38 t bogie allows for a gross combination weight of up to 150 t
Assembled locally at Volvo Trucks South Africa’s plant in Durban, the new-generation FMX series is designed with a core focus on driver ergonomics, safety and productivity.
Advertisement
Directly aimed at the construction and allied sectors, the new Volvo FMX features the heaviest addition to Volvo’s chassis range – a 38 t bogie that allows for a gross combination weight of up to 150 t. In addition, the front air suspension option has been updated, allowing for front axle loads of up to 10 t, or 20 t for double front axles.
For trucks with a steered tag or pusher axle, the steering angles have been increased, resulting in better manoeuvrability and reduced tyre wear. All these improvements add up to greater productivity and cost efficiencies for construction transportation tasks.
Another noteworthy feature is the new traction control panel, which helps the driver easily and quickly handle potentially dangerous situations, both on- and off-road. On Volvo FMX models in 4x4, 6x6, 8x6 and 10x6 configuration, this feature automatically engages the front axle at the exact moment it is needed, and disengages it when not.
The front drive axle is positioned to give the truck a better approach angle. It’s designed to be strong and streamlined. For added durability, the parallel rod behind the axle beam is integrated, making the sturdy axle casing the lowest point of the vehicle and significantly improving ground clearance when fully loaded.

FMX ENGINE OPTIONS Engines: Diesel engines are available with different emissions standards. The D11A is available in 330 hp/1 650 Nm and 370 hp/1 770 Nm, and the D13A is available in 400 hp/2 000 Nm, 440 hp/2 200 Nm, and 480 hp/2 400 Nm. Euro V variants are locally available on special request.
TRANSMISSION FMX: I-Shift and I-Shift with crawler gears, with software packages for different areas of application.
Safety features that help avoid accidents
The new Volvo FMX comes with the option of Adaptive Cruise Control, which works at all speeds down to 0 km/h. Further safetyenhancing features include Downhill Cruise Control, which sets a maximum speed to help prevent unwanted acceleration.
The electronically controlled brake system, which is a prerequisite for safety features such as forward collision warning with emergency brake, and Electronic Stability Control, is now standard. Volvo Dynamic Steering, with Lane Keeping Assist and Stability Assist, is also available as an option.
For particularly rough applications like mining, the Volvo FMX comes with an optional steel roof hatch with an emergency exit handle that removes the entire hatch.
“Whether a fleet is operating on- or off-road, you’ll need a chassis that’s built to handle a lot of action on a daily basis,” says Eric Parry, product manager, Volvo Trucks SA.
“With the new FMX, Volvo Trucks will tailor the chassis to support a customer’s success, using components and systems that are guaranteed to work reliably for many years to come,” Parry adds.
Rebuilding
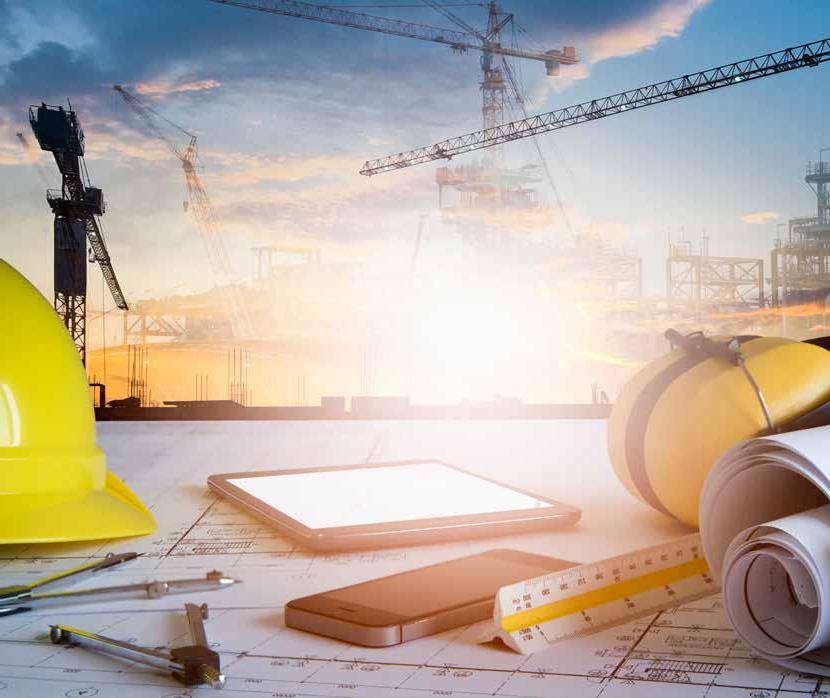
with PURPOSE

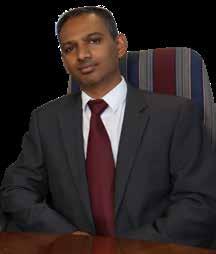
Sugan Pillay, president of CESA

The annual CESA Presidential Message highlighted the role of engineers in addressing poverty, inequality and unemployment. Sugan Pillay, president, CESA, touched on the compassion and empathy displayed by South Africans in 2020. “With the Covid-19 crisis, we saw an industry of people that act with more care for others. It is this spirit of ubuntu that CESA wants to promote. Our industry protects lives and livelihoods, and we need to always consider the tangible social and economic outcomes of the work we do.” Unpacking the 2021 theme, Pillay added that CESA will continue to mould consulting engineers to ensure they continue to protect lives through quality and safe infrastructure, and protect livelihoods through the creation of economic opportunities for the wider construction value chain.
The 2021 theme for Consulting Engineers South Africa (CESA) – rebuilding with purpose – explores how engineers can assist in implementing government’s South African Economic Reconstruction and Recovery Plan.
Covid-19 vaccine
Pillay encouraged the industry to be patient and understanding as government resources are diverted to funding the vaccine initiative. “Without doubt, the most pressing requirement is the roll-out of the Covid-19 vaccine. CESA and its members have the necessary skills and expertise like project and logistics management to assist with this undertaking,” added Pillay. He noted that municipal budgets set for infrastructure may be diverted and that CESA members should stand ready to assist in infrastructure that might be prioritised, such as hospitals and clinics. “This may also give the country an opportunity to create legacy infrastructure rather than temporary structures and, if carefully planned, resources that are currently being utilised for short-term interventions can rather be used to develop long-term solutions.”
Reflecting on 2020
CESA placed much emphasis in 2020 on strengthening the relationship between government and the private sector. This was showcased by the association’s involvement in the Sustainable Infrastructure Development
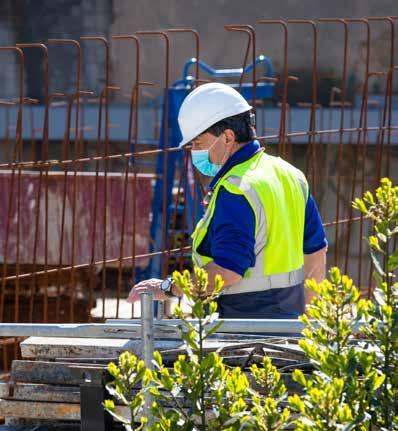
Symposium South Africa. The strength of this relationship will be instrumental in achieving the regrowth of the economy.
Sadly, Pillay remarked that South Africa still faces many of the same challenges as in prior years, with an ongoing demise of public decision-making processes, a lack of checks and balances within procurement systems, a loss of accountability among those tasked with leading change, and government’s slow and laborious efforts to curb corruption. This was reflected in the Auditor-General’s report, with only 7.5% of municipalities receiving a clean audit. There was delayed infrastructure delivery, and those projects that did see progress were hampered by obstructions from the so-called construction mafia.
There is ongoing communication between the SAPS and CESA in this regard and members are encouraged to report all incidents of violence and intimidation to the authorities.
A positive development in 2020 was the reopening of REI4P (Renewable Energy Independent Power Producer Procurement Programme), which will provide opportunities for contractors in the medium term and help improve the energy landscape in the longer term.
Rebuilding with ethics
While the current pace of change is too slow and there is a need for speed in the infrastructure development plan, infrastructure roll-out must be done carefully, or it will fuel corruption. “In our efforts to rebuild, let us maintain our focus and purpose on doing so with quality and integrity. If we are to truly save lives and livelihoods, we must operate with an unwavering focus on value, reliability and sustainability,” stated Pillay. In this regard, CESA highlighted: • the newly mandated management systems for its members based on international standards for quality, integrity, and sustainability. • the draft Public Procurement Bill where
CESA will continue to lobby for a more transparent procurement process with decentralised authority structures to ensure the necessary checks and balances are in place.
2021 opportunities
Pillay encouraged CESA members to focus on various opportunities that could be leveraged in 2021 to strengthen the industry and economy: • SIPs (Strategic Integrated Projects):
The identified SIPs will play a great role in economic recovery, if they can break ground. Getting a few selected projects off the ground early will provide reassurance to the public and encourage investment confidence in South Africa. It will be an
‘immune booster’ to our ill economy. • Rethink spatial planning: With the pressing need for development in more rural areas, and the loss of emphasis on metros due to remote work and teleconferencing, there is a real opportunity to decentralise the development focus away from cities.
Growing cities bring a host of social and environmental challenges. Instead of people moving to metro areas to access services, we need to take those services to where people live.
Agriculture has been one of the better performing sectors in the economy, and if services can
be decentralised to those communities, it will relieve pressure on the metros and cities. Thus, smaller-scale farmers can be supported, food security can be enhanced, and local communities can be gainfully employed in construction and maintenance activities close to where they live. • Maintenance: South Africa’s dismal performance in the recent SAICE
Infrastructure Report Card means that it is vital that we undertake comprehensive infrastructure maintenance. It is essential for protecting lives. More emphasis on maintenance efforts can protect livelihoods too, as local communities benefit from such initiatives. • Professionalisation of the public service:
Government is looking at improving the skills of public servants and the role of the state in producing skilled professionals.
CESA stands ready to support this initiative. • Workforce: The mentoring of young people in the industry is vital. Furthermore, CESA has witnessed great success in industry transformation, and will continue to encourage diversity and inclusion within the consulting engineering profession. “For rebuilding to happen effectively, we need collaboration between all spheres of government. We need coordination between all role players. And we need to partner to build state capacity and ensure the necessary skills development takes place,” added Pillay.
PREPPING FOR
non-structural repairs
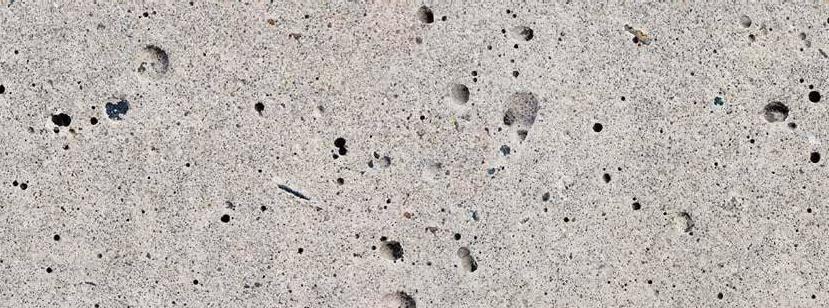
There are essential steps to follow before and during the repair of relatively minor yet unsightly concrete defects. Bryan Perrie, managing director of The Concrete Institute, outlines what to do – and avoid – when tackling these projects.

Bryan Perrie, MD, The Concrete Institute
Repairs to new concrete should be done as soon as possible after the formwork has been removed to reduce differential shrinkage and improve the bond between the original concrete and the repair material. Before doing the repair, all dust and detritus must be removed from the surface to be treated by, for example, washing vertical and near-vertical surfaces with clean water.
For manual repairs, suitable for small areas, feather edging – trying to seamlessly blend the repair material into the existing concrete – should be avoided. The outline of a repair should be cut with a masonry cutting disc or saw to ensure a square edge. Good adhesion between the original concrete and the repair material is essential and, to ensure this, the surface of the original concrete must be strong, rough and clean. Any loose or weak material must be removed with sharp chisels, driven by relatively light hammers. But it is important to remove the unwanted concrete in such a way that the remaining concrete is not badly damaged. Sandblasting, which can remove small volumes of concrete, is an excellent means of achieving a rough surface free of loosely adhering material.
When to use mechanical fixing
In cases where the repair areas are large (say over 0.1 m2), and especially where persons could be injured by falling fragments, it is strongly recommended not to rely solely on adhesion between repair and background concrete, but to provide mechanical fixing. Such fixing should be done with corrosion-resistant metal devices such as screws or rods, preferably of stainless steel. Fixing devices should be installed after the surface preparation is complete, but before the surface is cleaned.
To ensure strong adhesion of fresh concrete or mortar to a substrate of hardened concrete, the substrate should have enough suction to absorb the water film at the interface but should not desiccate the repair material. This limited suction can
be achieved in different ways, depending on the age and density of the concrete. If the concrete is fairly new – say within 48 hours of being placed – simply allowing the surface to become visibly dry should suffice. Concrete with low absorptiveness does not require pre-wetting and should be repaired in a dry state.
Primer slurry
The substrate should be primed with a slurry immediately before the repair material is placed. The primer slurry should be a mixture of equal volumes of cement and dry plaster sand with sufficient water to achieve a ‘paint consistence’. Neat cement paste is difficult to mix and is therefore not recommended. Polymer emulsion may be added to the mixing water – one part emulsion to two parts water is usually satisfactory.
Primer slurry must be applied as a thin coating to the substrate using suitable brushes. Do not allow primer to accumulate in depressions in the surface or dry out before applying. Priming must therefore be done immediately ahead of repairing and is best done over a small area at a time. Polymer emulsion on its own must never be used as a primer.
Rate of absorption
Older concrete should be assessed for absorptiveness by wetting the surface: if the water is rapidly absorbed, the rate of absorption would be too high; and if the water is hardly absorbed, the rate is too low. Concrete with high absorptiveness should be saturated for some hours before repairs are carried out. Surface water must then be removed, and the surface allowed to become visibly dry, with repairs undertaken straight away. Remember never to attempt repairs to concrete that has a water sheen.
Good compaction is essential in concrete repairs. Semi-dry mixes must be compacted by heavy tamping and plastic mixes applied with heavy pressure on the trowel or spatula.
Aesthetics
Where appearance is important, repairs should be finished to match the texture of the surrounding concrete using tools such as wood floats, steel trowels, sponges, wire and nylon brushes. If colour matching is essential, it should be noted that repairs tend to be darker than the original concrete when dried out. So, white Portland cement may be substituted for about a third of the grey material if such a colour match is required. The optimum substitution ratio should be determined by test: carry out a repair in an unimportant area and assess colour once the repair material has hardened and dried.
Repairs must be moist cured for at least seven days. Plastic sheeting, fixed along the edges to the concrete with pressuresensitive tape, is effective to trap moisture and ensure adequate curing. Good-quality, membrane-forming curing compounds may also be used but remember that drying of the concrete repairs may be retarded if these curing compounds are not removed from the surface.
After completion of the curing period, polymer-modified repairs must be allowed to dry out completely before being subjected to wet conditions. This allows the emulsion to coalesce and become water-resistant.
For more information, visit www.theconcreteinstitute.org.za or email info@theconcreteinstitute.org.za
Fixing minor defects: to ensure strong adhesion of fresh concrete or mortar to a substrate of hardened concrete, the substrate should have enough suction to absorb the water film at the interface but should not desiccate the repair material

PROFESSIONAL AFFILIATES
AECOM siphokuhle.dlamini@aecom.com AFI Consult banie@afri-infra.com Alake Consulting Engineers lunga@alakeconsulting.com AQUADAM (Pty) Ltd sales@aquadam.co.za ARRB Systems info@arrbsystemssa.com Asla Construction (Pty) Ltd johanv@asla.co.za Aveng Manufacturing Infraset werner.booyens@infraset.com Bigen Africa Group Holdings otto.scharfetter@bigenafrica.com BMK Group brian@bmkgroup.co.za Bosch Munitech info@boschmunitech.co.za Bosch Projects (Pty) Ltd mail@boschprojects.co.za BVI Consulting Engineers marketing@bviho.co.za Civilconsult Consulting Engineers mail@civilconsult.co.za Corrosion Institute of Southern Africa secretary@corrosioninstitute.org.za Development Bank of SA divb@dbsa.org.za Dlamindlovu Consulting Engineers & Project Managers info@dlami-ndlovu.co.za DPI Plastics Farhana@dpiplastics.co.za EFG Engineers eric@efgeng.co.za Elster Kent Metering Mark.Shamley@Honeywell.com ERWAT mail@erwat.co.za GIBB marketing@gibb.co.za GIGSA secretary@gigsa.org GLS Consulting nicky@gls.co.za Gorman Rupp Cordeiro@gormanrupp.co.za Gudunkomo Investments & Consulting info@gudunkomo.co.za Hatch Africa (Pty) Ltd info@hatch.co.za Herrenknecht schiewe.helene@herrenknecht.de Huber Technology cs@hubersa.com Hydro-comp Enterprises info@edams.co.za I@Consulting info@iaconsulting.co.za Infrachamps Consulting info@infrachamps.co.za INGEROP mravjee@ingerop.co.za Integrity Environment info@integrityafrica.co.za IQHINA Consulting Engineers & Project Managers info@iqhina.co.za iX engineers (Pty) Ltd hans.k@ixengineers.co.za JBFE Consulting (Pty) Ltd issie@jbfe.co.za JG Afrika DennyC@jgafrika.com KABE Consulting Engineers info@kabe.co.za Kago Consulting Engineers kagocon@kago.co.za Kantey & Templer (K&T) Consulting Engineers ccherry@ct.kanteys.co.za Kitso Botlhale Consulting Engineers info@kitsobce.co.za Lektratek Water general@lwt.co.za Makhaotse Narasimulu & Associates mmakhaotse@mna-sa.co.za Malani Padayachee & Associates (Pty) Ltd admin@mpa.co.za Maragela Consulting Engineers admin@maragelaconsulting.co.za Mariswe (Pty) Ltd neshniec@mariswe.com Martin & East gbyron@martin-east.co.za M & C Consulting Engineers (Pty) Ltd info@mcconsulting.co.za Mhiduve adminpotch@mhiduve.co.za Mogoba Maphuthi & Associates (Pty) Ltd admin@mmaholdings.co.za Much Asphalt bennie.greyling@muchasphalt.com Mvubu Consulting & Project Managers miranda@mvubu.net NAKO ILISO lyn.adams@nakogroup.com Nyeleti Consulting merasmus@nyeleti.co.za Odour Engineering Systems mathewc@oes.co.za Prociv Consulting & Projects Management amarunga@prociv.co.za Rainbow Reservoirs quin@rainbowres.com Re-Solve Consulting (Pty) Ltd maura@re-solve.co.za Ribicon Consulting Group (Pty) Ltd info@ribicon.co.za Royal HaskoningDHV francisg@rhdv.com SABITA info@sabita.co.za SAFRIPOL mberry@safripol.com SALGA info@salga.org.za SAPPMA admin@sappma.co.za / willem@sappma.co.za SARF administrator@sarf.org.za.co.za SBS Water Systems mava@sbstanks.co.za Sembcorp Siza Water info-sizawater@sembcorp.com Sigodi Marah Martin Management Support lansanam@sigodimarah.co.za SiVEST SA garths@sivest.co.za Sizabantu Piping Systems (Pty) Ltd gregl@sizabantupipingsystems.com SKYV Consulting Engineers (Pty) Ltd kamesh@skyv.co.za SMEC capetown@smec.com Sobek Engineering gen@sobek.co.za Southern African Society for Trenchless Technology director@sasst.org.za SRK Consulting jomar@srk.co.za Star Of Life Emergency Trading CC admin@staroflife.co.za Syntell julia@syntell.co.za TECROVEER (Pty) Ltd info@tecroveer.co.za TPA Consulting roger@tpa.co.za V3 Consulting Engineers (Pty) Ltd info@v3consulting.co.za Vetasi south-africa@vetasi.com VIP Consulting Engineers esme@vipconsulting.co.za VNA info@vnac.co.za VUKA Africa Consulting Engineers info@vukaafrica.co.za Water Institute of Southern Africa wisa@wisa.org.za Wam Technology CC support@wamsys.co.za Wilo South Africa marketingsa@wilo.co.za WRP ronniem@wrp.co.za WSP Group Africa ansia.meyer@wsp.com Zutari Rashree.Maharaj@Zutari.com

Weatherproof GLAZING
Situated within close proximity to Cape Town’s V&A Waterfront, the 117 On Strand Street building recently underwent further development with the addition of new apartments and offices. The building houses a commercial gym, three floors of premium-grade office space, two floors of retail stores, and 117 apartments. Sika’s products were used throughout for the structural glazing component to ensure a sustainable solution.
Working in unison with Compass Glass and Mazor Engineering, Group 5 Construction was the primary contractor.
The insulated glass units were bonded to each other in the Compass Glass factory using Sika’s Sikasil IG-25. Thereafter, the insulated glass panelling was bonded to the powder-coated metal frame using Sikasil SG-500 and Sika Aktivator-205 in Mazor’s factory. Sikasil IG-25 is ideal as a secondary edge seal for insulating glass in structural glazing applications. It is used in combination with Sikasil SG-500, which is a two-component structural glazing silicone.
During on-site installation, the glazing was finished off with a final seal using Sikahyflex-305 AP. This is a one-component, neutral, moisturecuring weather sealant designed for durability under severe conditions. It has excellent resistance to water and is UV stable.
Successfully completed in November 2019, 117 On Strand Street’s meticulous glazing finish continues to withstand the elements while providing panoramic views of the Atlantic Ocean, Table Mountain, and the Cape Town central business district.
During on-site installation, the glazing was finished off with a final seal using Sikahyflex-305 AP
Construction has preserved and protected the outer heritage walls of the existing structure, which date back about 100 years
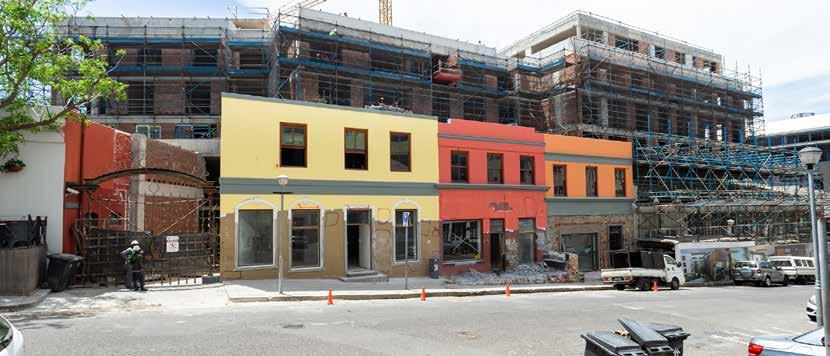
A CUBE AT A TIME
Variable ground conditions at a mixed-use development in Cape Town demanded some innovative solutions from contractor A t the Old Cape Quarter project in De Waterkant, four floors of luxury apartments are being added to retail and office GVK-Siya Zama Construction and readymix specialist AfriSam. “There was no option but for concrete to be delivered in smaller volumes, otherwise the space. This meant substantial strengthening of concrete would harden in the trucks before the foundations and columns to accommodate it could be used,” Robb explains. “AfriSam the increased load. According to Garth worked closely with us to find a solution, which Robb, contracts director at GVK-Siya Zama was to deliver just 1 m3 of readymix at a time.” Construction, this was not a straightforward process, with insufficient space in the Logistics and teamwork basement areas for normal class 3 formwork. Readymix trucks usually carry 6-8 m3, so
“We made extensive use of biscuit columns, carrying just a fraction of this had severe where we added reinforcing around the old implications for efficiency. However, the existing columns and core-drilled at an angle situation demanded flexibility from both from above – adding grout to beef up the partners, says Melanie Ross, territory manager, column sizes,” he says. “We core-drilled AfriSam, and the needs of the customer had through the base to transfer the load on to the to come first. piling, with a number of columns and bases “Also, the pours could only start in the needing to be demolished and reconstructed.” afternoon, and often continued beyond the About 10 different concrete mixes
A key complication was that concrete could 18:00 deadline agreed on between the were employed during the project to only be poured manually into the biscuit contractor and the authorities,” says Ross. “So suit various applications columns by wheelbarrow, through 60 mm extended permissions were obtained, and the core holes from the slab above. Each column AfriSam-contracted drivers agreed to put in the 10 different concrete mixes for different took up to an hour to pour, with admixtures extra time until pours were completed.” applications. These came from the company’s accelerating the hardening rate of this highly AfriSam supplied over 9 700 m3 of readymix Woodstock plant, about 8 km from site and its fluid 60 MPa concrete. to the Old Cape Quarter project, and about Peninsula Quarry plant at Durbanville.

INDEX TO ADVERTISERS
APE Pumps
African Utility Week
Afrisam South Africa
15
48
16
Anton Paar Southern Africa
37
Ctrack
10
Development Bank of Southern Africa 22 Flowtite SA
OFC
IMESA
Keller
18, 44, 54 12
Macsteel
OBC
Quality Filtration Systems 17, 19 Rand Water
2, 11
Rocla
41
SABITA
SAPPMA
SIKA
Sizabantu Piping Systems
Terraforce
VEGA Controls SA
Wirtgen SA