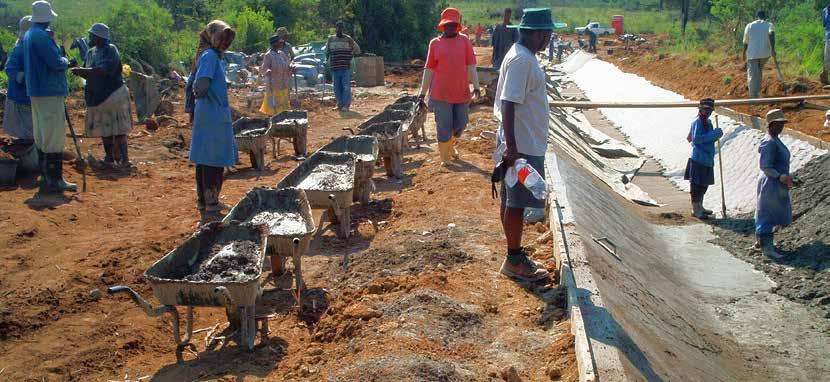
3 minute read
Labour-based canal construction
from IMIESA February 2021
by 3S Media
During the upgrading of the Hereford canal, 117 800 m 2 of geocells were used to add 29 km to the existing network, bringing the total length to around 44 km. The project was led by main contractor Group Five Civils, which was responsible for the earthworks that formed the canal’s parabolic shape.
This included the establishment of a compacted 200 mm river sand base on which the geotextile was directly placed and anchored, and the daily delivery to site of cement, sand and water for the community-based work teams. In turn, Hyson Cells was appointed as the specialist subcontractor for the installation of Hyson Cells system.
Advertisement
Today, the canal remains leak-free and continues to supply water to the surrounding farming community.
“On most of our LIC projects, one of our instructors provides on-site training for the contractor and labour on the best ways to rig and fill the cells. A critical component is the sand-cement grout fill material since the cell construction methodology requires an unconventional cementitious mix design,” explains Sally Hall, director, Hyson Cells.
“The end result, though, is a remarkable and consistent 30 MPa strength.”
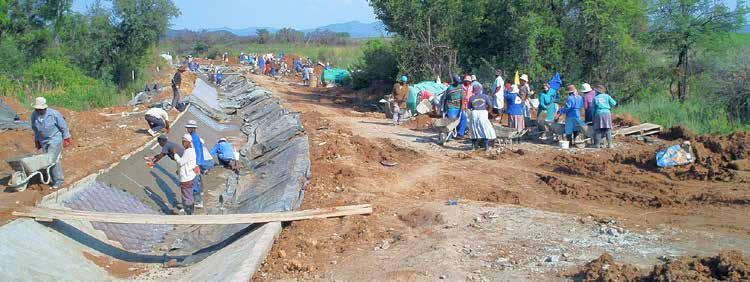
800 m 2 a day
For the Hereford upgrade programme, each of the four LIC teams was given an approximately 200 m 2 section to complete daily. Cell installation was straightforward, with the main tools required comprising 4 lb hammers and pliers.
Labour-intensive construction (LIC) techniques remain a crucial element in job creation as South Africa tackles growing unemployment in rural and urban areas. A classic case study is the 2004 upgrading of the Hereford canal in Groblersdal, included the establishment of a Limpopo, using Hyson Cells’ 3D compacted 200 mm river sand of which 10 were allocated the responsibility of rigging the geocell formwork.
For the fill component, each team had its own water tank, stockpile of cement and sand, and an allocation of 12 specially zinc-lined wheelbarrows.
“To keep things as practical as possible, the mixing and final transportation of the grout all takes place in the wheelbarrows – a practice we still apply today,” Hall continues, adding that each team member was allocated a specific job as either a mixer, wheelbarrow operator or cell installer/finisher. These teams were rotated during the day to prevent fatigue setting in.
The design mix is affected by the quality of the local sand. On the Hereford project, this changed constantly as the canal progressed, since sand was being extracted from different sources. To verify quality, routine testing ensured that the slump of 150 mm was optimal.
“The cement is mixed with the water first (with Hyson superplasticiser added) and not last, as is the normal practice. This ensures maximum availability of the cement for the hydration process,” Hall explains.
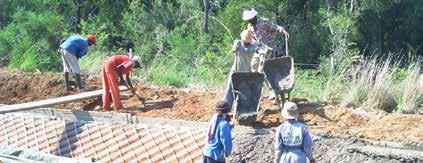
Self-consolidating
The mix has a high slump of typically 150 mm, which makes it flowable and easy to work with, as it is largely self-levelling. A further plus is that self-consolidating concrete (SCC) does not need to be vibrated.
“Going into 2021, the South African government has placed renewed emphasis on LIC as part of the Expanded Public Works Programme in addressing the triple challenges of poverty, inequality and unemployment. The advent of Covid-19 has made this even more of a priority,” she adds.
“For this reason, we need to embrace innovation, especially where alternative solutions are more cost-effective, create jobs and sustain communities. Our proven wheelbarrow mixer concept and SCC methodology underscore the benefits of that approach,” Hall concludes.