
5 minute read
Machine intelligence
from IMIESA February 2021
by 3S Media
Weighing up the cost versus performance benefits of capital equipment investments is a deciding factor for business success. The upside is that technology is making the machines of today and tomorrow much smarter, says Waylon Kukard, sales manager, Wirtgen South Africa. By Alastair Currie
Within the Wirtgen Group, a key research and development (R&D) focus is the development of engineered 360-degree solutions, with a core emphasis on automation and interconnected machines that ‘talk to each other’ across the OEM’s diverse product range. In Europe, this is already a reality for the roadbuilding sector, with Wirtgen now establishing the groundwork for implementation in South Africa for the asphalt paving market.
Advertisement
“Wirtgen has developed a system where every equipment line is now linked: from the asphalt plant, to the trucks, paver, and the rollers on-site,” Kukard explains. “It all works via real-time intelligent communication, monitoring and reporting. This is one smart solution.”
During a typical construction shift, each stage of the asphalt delivery process is shared and experienced by the operations team. For example, the paver operator will receive an alert from the asphalt plant if things are on track or delayed, a notification when the trucks are on their way, and an update if any of these vehicles are going to be late due traffic congestion. The temperatures are constantly recorded and measured from the asphalt plant right through to truck delivery at the paver. The same information is seen by the roller operators on their monitors. The roller operators know exactly what the temperature is and what compaction was achieved. Once the work shift is completed, the contractor can then download a comprehensive report itemising every activity, with an exact breakdown of how all machines performed, and the actual asphalt tonnage delivered.
RoadScan
Wirtgen’s intelligent systems are supported by an integrated technology suite that includes RoadScan. “An infrared camera scans a measuring range of 10 m behind the paving screed,” Kukard explains, adding that the scan grid measures 25 cm x 25 cm over the complete width. “The temperatures measured range from 0°C to 250°C, with a tolerance of ±2°C.”
The measured values are stored on the paver operator’s console, ready for download when required via remote access. Downloaded data can then be analysed using the RoadScan Analysis app.
“Having a precise record will prove invaluable in countering potential issues surrounding pavement performance once the project has been completed,” says Kukard. “Examples would include the verification of cold spots that could lead to segregation. Contractors then have an opportunity to fix potential defects prior to client handover.”
Another R&D development is the presetting of Wirtgen Group machines for a ‘plug and play’ 3D interface with other specialist OEM products, like grade control systems. On a Wirtgen paver, for example, this enables automated control of positioning, direction, movement, depth and width. The operator can then concentrate on optimising the transfer of the asphalt feed from the truck to the paver.
Kleemann won an international safety award for its mobile crusher line, which features a series of lockout key points that prevent the machine accidently starting up during maintenance operations
Impactors
“South African contractors have traditionally been quite conservative in their equipment choices; however, we’re seeing a positive shift. There’s now a much greater appreciation for how technology helps maintain a competitive edge,” Kukard continues. “A prime example is the uptake on Wirtgen Group’s Kleemann mobile impact crushers.”
The first model to debut in South Africa was the Kleemann Mobirex MR 110 Z EVO 2 model, sold to a contractor in 2020 for the processing of thermal coal feedstock.
Currently the smallest in the range, larger units comprise the 130 and 150 series, all of which are set up to run autonomously. Key industries for these compactors include the roads sector, where impactors are well suited to processing recycled asphalt, and the general construction and waste management segments, including municipal landfills, for the recycling of building materials.
“From a circular economy perspective, impactors are ideal for producing recycled aggregates,” Kukard explains. “Another plus is that you don’t have to separate the material when it comes to concrete recycling.”
Once a building or structure has been demolished, the impactor is designed to process the concrete and steel reinforcement debris in one go in the crushing chamber. Then at the end of this
The surface temperature measured by Wirtgen’s RoadScan system can be monitored in real time on the operator’s display console. This enables the paving team to react swiftly to fluctuations in temperature – usually a sign of segregation

process, the machine has a magnetic device on the discharge conveyor that separates the steel from the aggregates being produced. However, these compactors are not designed for processing highly abrasive materials, like quartzite quarry materials, which can wear out the internal workings very quickly.
Best reduction ratios

Kleemann impactors are designed to take large lump sizes of feed material and reduce them down to a fraction of their original size. For this reason, the crushing process is highly aggressive since these impactors are designed to achieve reduction ratios well beyond the scope of a traditional cone or jaw crusher.
On the Kleemann Mobirex MR 110 Z EVO 2, for example, reduction ratios range from 10:1 and 15:1, depending on the feed material. In contrast, jaws and cones typically have a 4:1 reduction ratio. In addition, they are not designed to handle iron material, which would cause mechanical damage.
A jaw or cone crusher operates on the compression principle to break the material. A Kleemann impactor, on the other hand, functions by throwing the material against toggle plates within the crushing chamber. There are normally four impact bars attached to the central rotor; however, two can be removed depending on whether a coarser or finer product is required, which is further refined by the onboard settings.
“High production rates are achieved due to this crushing methodology. A 1 m concrete block, for example, can typically be resized into 150 mm particles,” says Kukard.
Because the crushing process is aggressive, there is a tendency for the machine to produce a higher percentage of fines compared to other crushing processes. This can be countered, though, by slowing down the rotor speed.
“Wirtgen’s objective is to produce efficient machines that produce quality products at a lower cost. Whether it’s an impactor or a paver, machine automation is a core part of achieving this, working within an overarching, intelligently managed and controlled operating system,” adds Kukard.
“Within the roads and allied markets, it’s the best way to ensure that projects are delivered on time, within budget, and to the exact design specifications thanks to best-in-class technology,” he concludes.
The Kleemann Mobirex MR 110 Z EVO 2 working in a recycling application
On the Kleemann Mobirex MR 110 Z EVO 2, reduction ratios range from 10:1 and 15:1, depending on the material feed
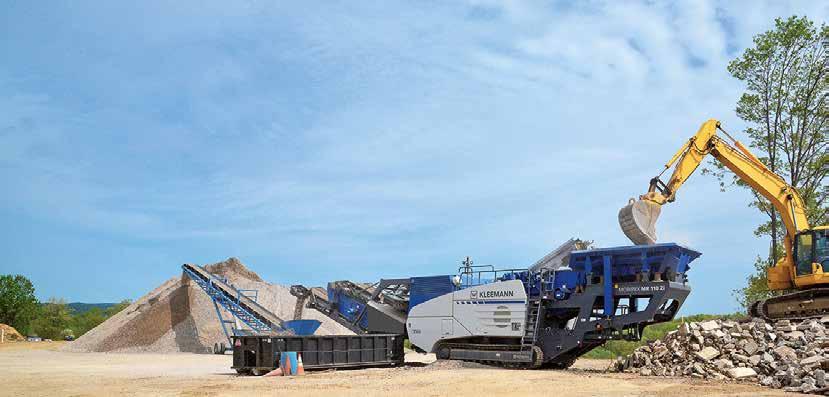