12 minute read
Fittings & components
Next Article
B J Waller pushes solutions for joinery forward into 2022
B J Waller had a very interesting 2021, which has lined up an exciting 2022 for the company and the joinery industry as a whole.
Having been heavily involved with the launch and growth of The Joinery Network over the past few years, MD Luke Piper and his team at B J Waller have learned a lot more about the industry and its requirements from a joinery manufacturer’s perspective.
As part of The Joinery Network, B J Waller has helped numerous timber door and window manufacturers streamline their businesses, driving efficiencies and profit. Being part of this process has allowed the company to build strong relationships and gain real insight directly from the people that matter.
After listening hard then acting accordingly, B J Waller struck up a partnership with Smyth Group in September last year. Since this partnership was initiated, the companies have combined forces and have used a vast amount of industry knowledge and knowhow to create a full design, manufacture and supply package. These unique product ranges and services are designed specifically for manufacturers of timber windows and doors.
B J Waller is proud to introduce the Cardea range of ironmongery to its portfolio of joineryspecific hardware. Available in six finishes – white bronze, polished nickel, satin nickel, dark bronze, unlacquered brass and sherardised black – the range is designed to allow the homeowner to create complete consistency throughout the property.
Each finish has been created to complement a diverse range of architectural styles, from Georgian homes to barn conversions. B J Waller’s finishes are suitable for interior and exterior use, adding a rustic charm to timber windows and doors.
“The new partnership with Smyth Group not only sees the launch of Cardea, but we are already at varying stages with other new product ranges that we will continue to bring to market throughout 2022 and into 2023,” comments MD, Luke Piper.
“Using our dedicated team of tool- and patternmakers creating lost wax and metal tooling, and using the latest design software, we are able to create all of our designs in-house.
“Our products will benefit from the very latest sand-and-gravity casting facility – a forging operation creating metal tooling to produce incredibly accurate forgings, formed under 200 tons of pressure.”
Utilising a vast range of machining processes including milling, linishing, grinding, CNC turning, drilling and tapping, these pieces will be impressively finished to complement the UK’s joinery manufacturers’ striking timber windows and doors. 01353 647111 www.bjwaller.co.uk
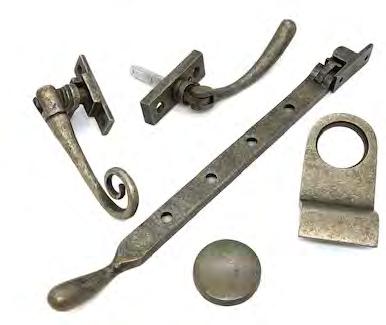
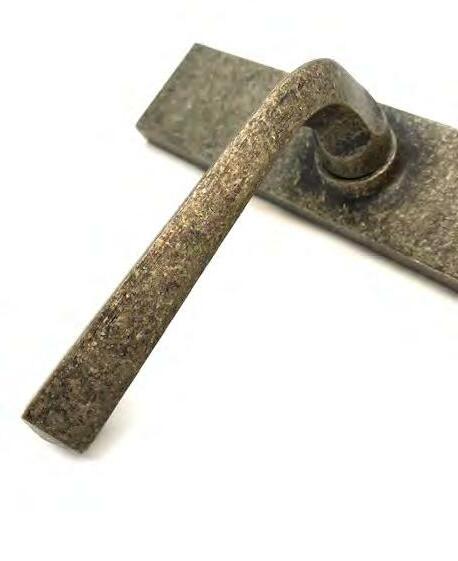
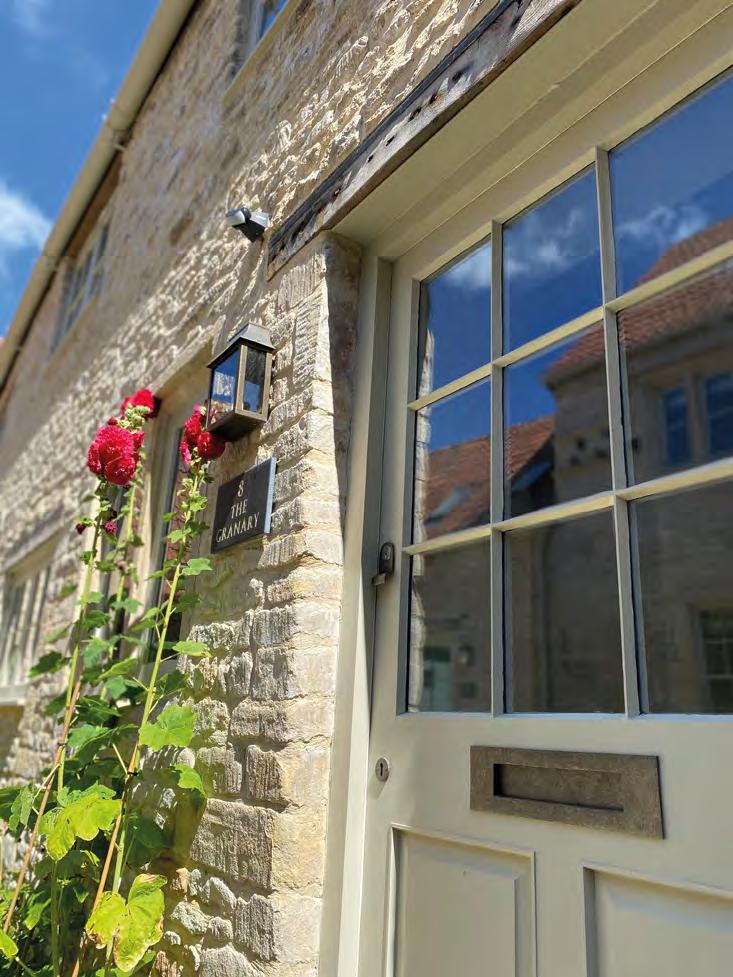
“As part of The Joinery Network, B J Waller has helped numerous timber door and window manufacturers streamline their businesses, driving efficiencies and profit”
Innovative fittings and components from Titus
Titus’ furniture hardware solutions have been improving homes around the world for decades. They increase the quality and facilitate the assembly of furniture, giving significant competitive advantage to manufacturers and improving the consumer experience.
Titus’ most popular components are the Quickfit TL5 Full Metal Jacket dowel, which provides optimal strength and reduces home assembly time by -50%, and the T-type concealed hinge, which has a tool-free 3Way snap-on mounting.
The T-type hinges, with integrated soft closing, are suitable for use on a wide range of doors, with thicknesses up to 34mm. Their unique 3way snap-on mounting system makes them exceptionally easy to install, even on large, heavy doors with multiple hinges.
The range has recently been extended to include pie-cut (bi-fold) hinges for corner cabinets, which fit standard drilling patterns and feature a convenient ‘double-lock’ opening. This means users can either open just one door leaf to get excellent access into the cabinet interior, or they can fully open the doors by locking the hinge cup, making the door leaves work as one.
The innovative Quickfit TL5 Full Metal Jacket dowels provide strong, reliable joints in all types of wooden materials, including MDF, chipboard and solid wood. This means that it is no longer necessary to use different dowels for different “Titus has been at the forefront of innovation since 1973, consistently developing precision components that make assembly seamless, enhance the look of furniture and improve competitiveness”
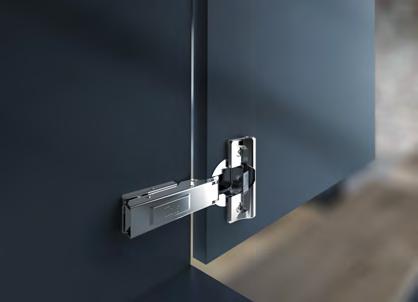
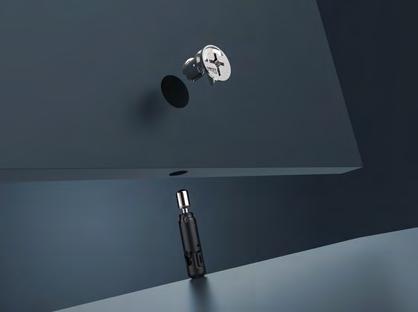
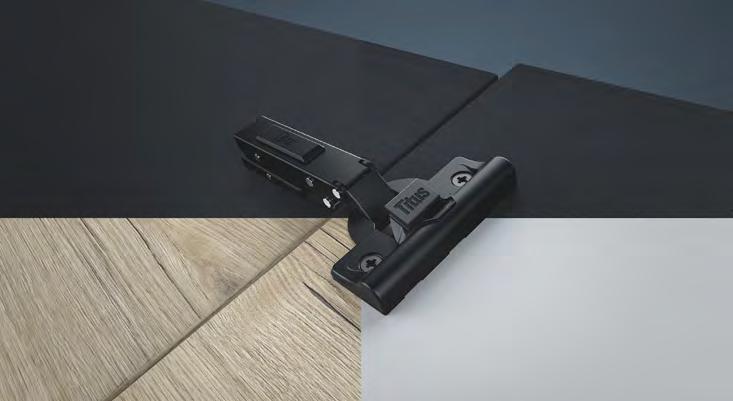
materials. In addition, the new dowels offer fast, tool-free insertion, reducing assembly time by up to -50% for home-assembled furniture. Alternatively, for maximum efficiency in volume production applications, they can be inserted automatically using Titus’ FastFit machines.
To complement its hardware range, Titus offers new TeraBlack (Titus Enhanced Resistance Application) versions with a darkgrey, non-reflective finish, that is not only visually appealing but also highly resistant to corrosion.
TeraBlack products fully meet the requirements of designers and consumers looking for unobtrusive yet attractive cabinet hardware. The product range includes new versions of the T-type hinges, TL5 Full Metal Jacket dowels, shelf supports and push latches.
To supplement its extensive range of fittings, connectors and components, Titus offers support and advice for manufacturers of bespoke and high-end kitchen cabinets and furniture. The team at Titus is always ready to discuss and develop solutions for even the most discerning manufacturers.
Titus is a leading component manufacturer specialising in the development and production of cabinet hardware, hydraulic dampers and automated assembly systems. A global brand, Titus has been at the forefront of innovation since 1973, consistently developing precision components that make assembly seamless, enhance the look of furniture and improve competitiveness.
Through innovative product design, engineering expertise and effective service, customers and partners of Titus are able to improve their productivity and quality, as well as reduce costs of assembly, manufacturing and other processes. Titus’ unique, Fit For Purpose approach enables high volumes with a consistent precision and repeatable quality. Uk.titusplus.com
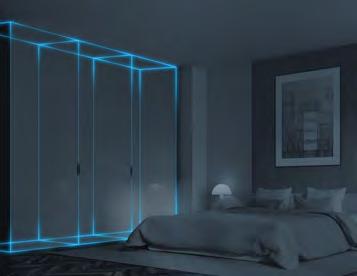
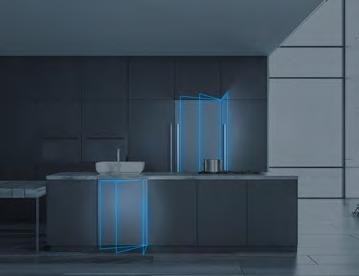
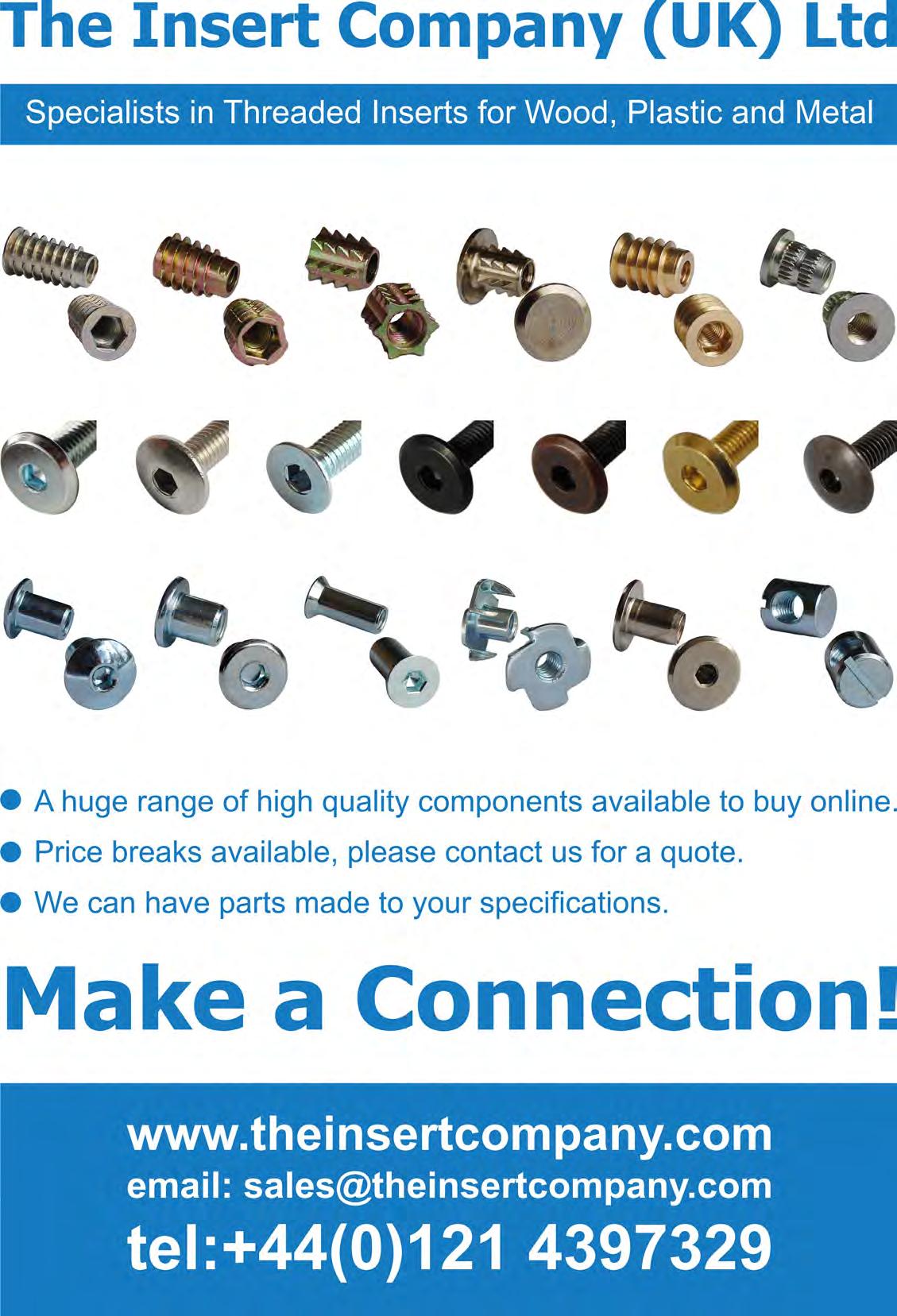
Biesse and Lamello – a solid partnership
Over the last 15 years, global woodworking machinery supplier, Biesse, and Swiss fixings specialist, Lamello, have been working in partnership to create innovative solutions that have changed the way CNC users join wood and panels, and eliminating the need for glue. Now, with the continual development of Biesse’s bSolid software and Lamello’s awardwinning P-System, it has never been easier to increase productivity and significantly reduce the production time and labour costs commonly associated with furniture manufacturing and assembly.
“All of our CNC machines are predisposed to work with Lamello’s P-System,” says Paul Willsher, Wood UK commercial director at Biesse UK. “We pride ourselves on offering innovative and flexible machining solutions to our customers. That’s why our machines have been designed to work effectively with Lamello’s unique CNC connectors.”
It is this commitment to problem-solving that has formed the framework of this successful partnership. “When we talk to a customer, we don’t just focus on machinery,” Paul continues. “It’s our job to understand our customer’s processes and, ultimately, find ways to make their manufacturing methods more efficient, whilst improving on quality. Working with forward-thinking companies like Lamello allows us to offer our customers options and not conform to the one-size-fits-all approach.”
Available for demonstration at Biesse UK’s Tech Centre in Daventry, the Brema Eko 2.2 vertical boring machine and Rover A five-axis pod-and-rail CNC showcase just how easy it is to integrate Lamello’s fixings into production. Both offer one-hit machining – with the whole process being completed on one machine – which in turn offers exceptional speed, accuracy and consistency when machining Lamello’s P-system grooves.
“When using Lamello’s joining solutions on the Eko 2.2, its c-axis turns the Lamello aggregate in both the X and Y direction, eliminating the need for a second aggregate altogether,” explains Paul. “The machine has also been designed with an eight-position toolchanger that is fully programmable. This means the operator can easily switch between the required tools when changing direction, without incurring additional set-up time. This offers a simple, fast and precise drilling solution for both surface and/or corner processing when using the P-System.
“Alternatively, the Rover A uses a five-axis head that enables the P-System grooves to be cut at any angle, offering huge time-saving potential without impacting on the overall quality.”
Both machines are operated by Biesse’s bSolid 3D CAD/CAM software. “Our software really sets us apart,” explains Paul. “When it comes to Lamello’s P-System, it is the only fixing in Biesse’s portfolio that is supplied with its very own macro. It’s been designed exclusively by Biesse, for Biesse, and as a result, we have the ability to adapt the macros for customers if required.
“This means if our customers’ production methods change at any point, our software can be adapted to meet their needs. Plus, if they want to start using Lamello at a later date or choose to incorporate a different Lamello fixing into their manufacturing processes, it only takes a few minutes for us to dial into their machine and turn the programme on, completely free of charge. It really is that simple. All that is left is for them is to buy the correct tooling to complete the job.”
What is more, the macro is user-friendly, and offers a full simulation of the workpiece during the cutting process. “This
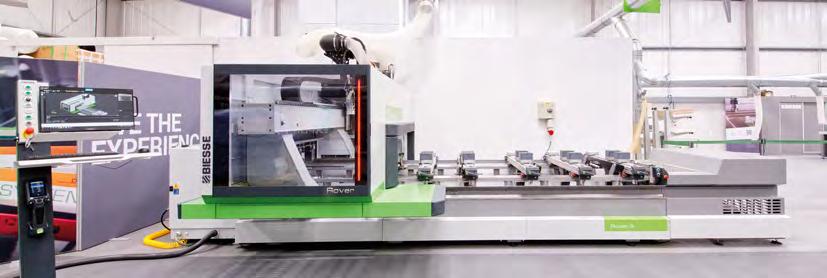
“Whether you’re using a three-, four- or five-axis CNC machining centre, Lamello offers a winning solution that can streamline your production and increase efficiencies”
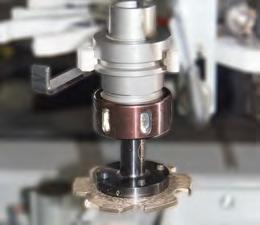
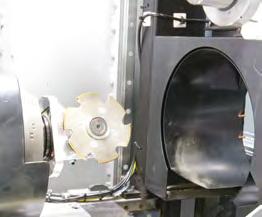
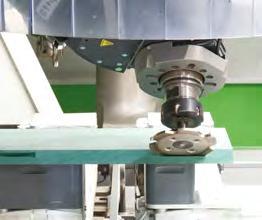
Biesse Rover A
highlights each stage of the cycle and allows for the user to change the position of the workpiece or individual machinery components before running the process fully,” says Paul. “These visual prompts can help the operator pre-empt any programming errors which could cause material wastage and production delays.”
Lamello’s macro can also be configured to only show fixings relevant to an individual business. “This simplifies the process even more,” admits Paul. “And, when new product comes to market, we work with Lamello to incorporate the new fixing into our software. The new macro is then supplied to our customers at no additional cost. We even train our customers on how to write their very own Lamello macros, allowing them complete control over their production processes, regardless of the application.”
Shaye Chatfield, Lamello area sales manager international for the UK and Ireland, adds: “Partnering with leading machinery manufacturers like Biesse allows us to showcase our CNC connectors in the best possible way – and with demonstrations available at their UK showroom, you can experience the benefits first-hand.
“Seeing the whole process in action really brings home how simple, fast and strong our fixings are, and how simple it is to integrate into your production. Whether you’re using a three-, four- or fiveaxis CNC machining centre, Lamello offers a winning solution that can streamline your production and increase efficiencies.” www.lamello.co.uk
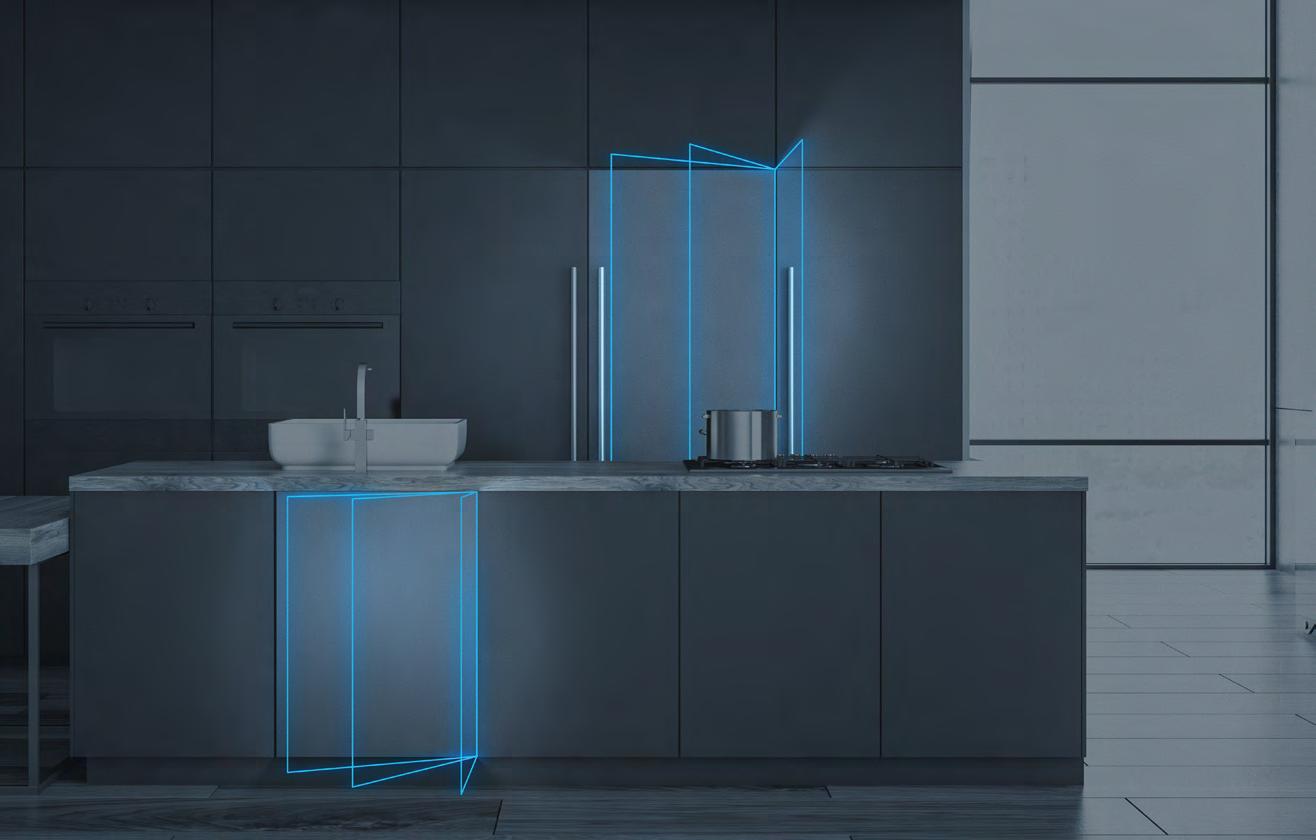

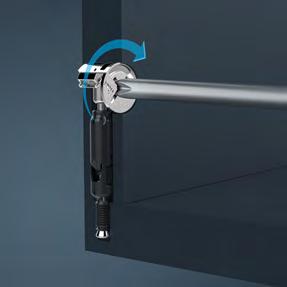

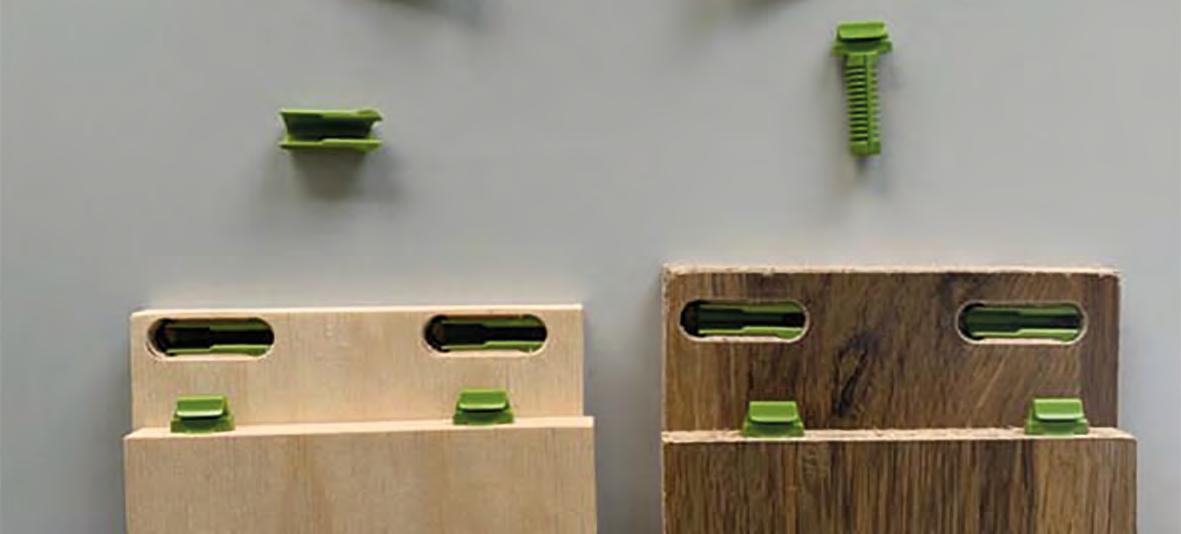
The OVVO family of award-winning connectors keeps growing
OVVO continues to expand its range of invisible wood-joining connectors, leading the way in furniture assembly components, making life easier for consumers and end-users, and delivering a more profitable and efficient solution for manufacturers.
OVVO products are a range of cleverly engineered, award-winning, invisible connectors that make joining wood simple. The connectors are installed during the manufacturing process so the end-user can simply click together cabinets, shop fit-out components, door frame assemblies or furniture without the need for tools, screws, or glues. The result is an accessible, sustainable product that saves time, money and effort for consumers and manufacturers alike. Manufacturers can also benefit from significantly reduced shipping costs, as items can be shipped flat-packed.
The latest addition to the OVVO product family is the new V-0930 Releasable Drilling Connector (V-0930.RD25), which is specifically designed for panels as thin as 12mm.
This new invisible connector is designed for connecting cabinet parts and drawer boxes using simple drilled holes on one side of the joint, thereby simplifying the panel processing operations while continuing to provide all of the benefits of OVVO’s proven, tool-free assembly methodology.
Established in Ireland in 2014, the OVVO brand has gone from strength to strength, picking up numerous highly regarded industry awards along the way. Most recently awarded a High Product Quality award at interzum 2019 for the innovative V-1230 Connection system, the relentless quest to make life easier for people ensures that simplicity is at the heart of every new product – with each one developed, the OVVO range has become more accessible to manufacturers, with the ability to be integrated into existing production processes, and suitable for a wide range of production capabilities.
All OVVO connectors are designed for automatic insertion, and recently announced partnerships with leading software providers Cabinet Vision, TopSolid, iFurn, Swood and Cabinet Sense ensure that manufacturers can easily incorporate OVVO into their existing processes, and also into new product design and development.
The click-together connectors can also connect joints at angles that are not possible with bolts, nails and screws.
All OVVO connectors can be installed into a variety of materials, ranging from high-quality hardwoods to low-grade particleboard, and their recyclable plastic means any waste is put back into the production of the product.
OVVO works best in boards >12mm in thickness, and is available in a range of sizes to match any requirements. All connector sizes are available in both permanent and releasable options, extending the range of materials and opportunities to inspire creative design and innovative development.
Consumer demands are shifting more and more towards convenience and sustainability. OVVO helps its customers meet those demands and give their products a competitive edge. The OVVO team is on hand to support a switch-over to OVVO and help customers take the next step of innovation. www.ovvotech.com
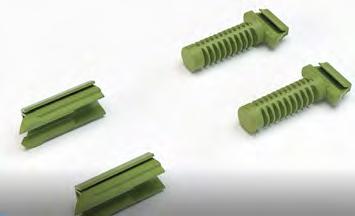
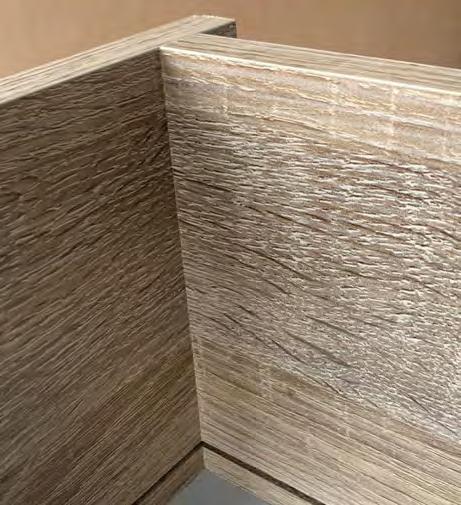