17 minute read
Saw, blades and cutting technology
Next Article
Saws, blades & cutting technology
Vertical panel saws – the essentials
Matt Pearce, MD of TM Machinery, the exclusive UK distributor of Striebig vertical panel saws, explains which factors should be considered when looking for a new vertical panel saw …
Common questions when looking to purchase a new vertical panel saw
Customers who have never used a vertical panel saw before, or someone who may not have used a modern vertical panel saw, often ask about the accuracy of the machine. This is because there is a misconception that vertical panel saws are designed for rough cuts only. This isn’t the case.
A good-quality vertical panel saw is as accurate as a top-of-the range beam saw or table saw, and we can guarantee that the Striebig’s accuracy is within 0.1mm on every cut. On top of this, the finish of the cut when teamed with a scoring blade means the board can be put straight through an edgebander without further machining or hand-finishing.
Can I cut a wide range of materials on a vertical panel saw?
Simply, yes. It’s just the tooling that may need to be adapted for individual applications. This can see the vertical panel saw being used to cut marble – this is achieved with a grinder disk and water sprays – glass-reinforced plastic, aluminium, composites, foam and timbers. The list is endless, if you have the right tooling.
How much space do I need to safely use a vertical panel saw?
It’s true that a vertical panel saw takes up considerably less floor space than a table saw or beam saw when cutting the same-sized boards. The main reason being, on a vertical panel saw, the board doesn’t move and doesn’t lie flat.
When working with jumbo sheets (2800 x 2070mm), a panel saw needs to be big enough to handle a 2070mm board on both sides and have additional space for the operator. This equates to a minimum space requirement of 7 x 3m. An equivalent vertical panel saw requires 4.5 x 2m. A further 450mm can be saved if the saw is wall-mounted.
Is the extraction good on a vertical panel saw?
Modern vertical panel saws are designed to meet European dust extraction regulations. Unlike older vertical panel saws, sometimes called wall saws, which didn’t benefit from secondary dust collection, modern saws have been designed to significantly limit operator dust exposure. Personal sampling tests are also regularly completed to monitor dust levels in and around the operating zone.
Should I choose a vertical panel saw over a panel saw?
There is no doubt that a flat-bed panel saw is a more flexible machine than a vertical panel saw. You can’t cut angles, bevels and mitres on a vertical panel saw – but, if you’re looking to cut large panels into smaller sizes, both vertically and horizontally, and do it quickly and accurately using very little floor space, a vertical panel saw is a better option for you.
Unlike a table saw, you’re not reliant on the operator keeping the board flush to the fence at all times to keep accuracy and cut quality high. On a vertical panel saw, the board remains stationary, offering easy handling and less margin for operator error. It also requires considerably less material handling – simply load the panel onto the table once, and slide the saw head through the panel. Larger models also offer adjustable feed speeds, and optimisation software that automates the entire process.
What to consider when purchasing a vertical panel saw
The vertical panel saw manufacturer
Regardless of what type of machine you’re buying, the best machines are made by companies that specialise in their craft. This is true of any manufacturer. Consider how long the company has been a specialist in the manufacture of this type of machine – if they have a good reputation within the industry, and if they are leaders in their field.
Build quality
The build quality is one of the most important factors to consider when buying a vertical panel saw. Just like cars, cheaper models often come with a wealth of gadgets to attract you, but it’s what is underneath that’s important. It’s the engineering and build quality that sets machines apart. That’s why we encourage customers to get hands-on with our machines. Don’t buy off a spec sheet – this will not allow you to see and feel the difference.
Return on investment
This is very individual, but it doesn’t just come down to the cost of the machine. It’s important to consider the overall reliability of your machine and its lifespan, too. Some vertical panel saws can work well for over 30 years. Due to precision engineering, you can also expect fewer errors, less material waste and a better finish, which in turn requires less re-cutting and offers significant time-saving benefits. To get the best return on investment, the machine needs to be reliable, accurate and offer consistently high-quality cuts. This can only be achieved with a robust framework.
Servicing and repairs
You need to consider the aftercare service your supplier offers before you buy a machine from them, and understand why they are different to other suppliers. It’s important to do your research – talk to existing customers – and ask the right questions. How many engineers do they have that have been trained on this machine by the manufacturer? How quickly can they get to you if something happens? Do they have spare parts, and are they readily available? Your choice of vertical panel saw cannot be solely made based on the machine itself.
What sets Striebig vertical panel saws apart from the rest?
Striebig has been specialising in the design and manufacturing of vertical panel saws for over 70 years. The Swiss manufacturer focuses solely on the production of vertical panel saws, and its commitment to innovation has seen it become an industry standard across Europe.
The saw frame, saw beams and heavy-duty saw heads have been precision engineered to offer a reliable, robust and accurate cut. The frame itself is made from a single piece of heavy-duty steel that remains perfectly square throughout the duration of the machine’s lifecycle. This allows Striebig to use durable, fixed rollers on the frame. They are the exact same distance from the top of the frame, and do “The build quality is one of the most important factors to consider when buying a vertical panel saw. Just like cars, cheaper models often come with a wealth of gadgets to attract you, but it’s what is underneath that’s important. It’s the engineering and build quality that sets machines apart”
not change over the life of the machine. Other manufacturers use blocks that can be trimmed and rollers that lift. You don’t need to do this with a Striebig. This isn’t new innovation, it’s been the same for 60 years.
The simplicity and ease of use offered by a Striebig can’t be overlooked. It isn’t overcomplicated, and doesn’t include features that aren’t needed. Its moving frame system has been in place for 52 years. It’s totally mechanical and requires no compressed air. Similarly, the Control model has only had two facelifts since its launch 20 years ago, and the Compact, which was launched 22 years ago, has only undergone three changes, and they haven’t seen the machine’s fundamental features change. They have only been improvements in the technology.
The changes Striebig makes aren’t revolutionary, they are evolutionary, and as it continues on this path, the Swiss manufacturer will remain at the forefront of vertical panel saw manufacturing. >>
Striebig Edition 60
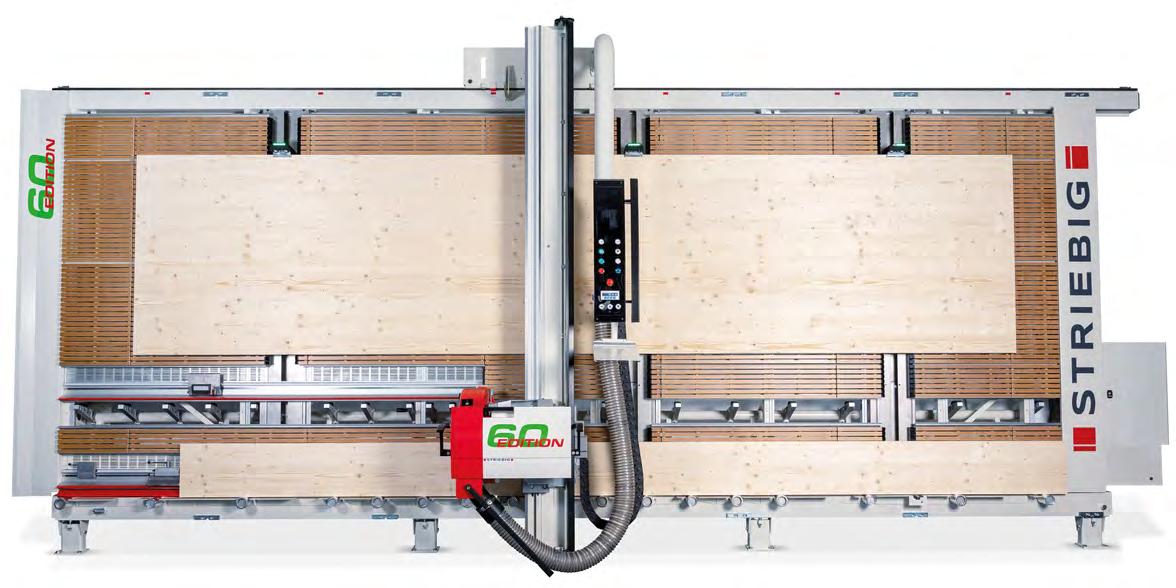
Striebig Edition 60 bottom trim
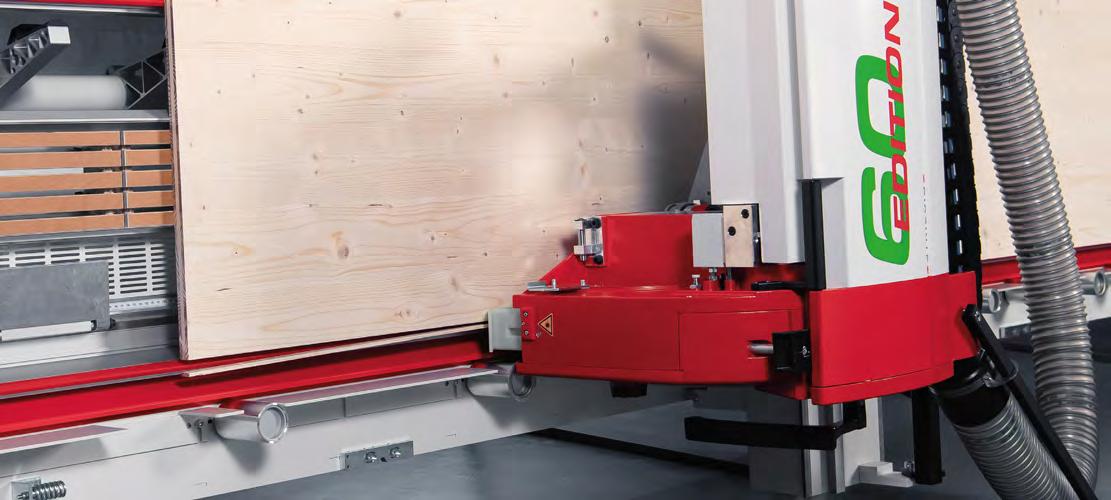
How to select the right Striebig model
What model is right for my business?
We tailor each machine to our customer’s requirements. We ask you for a clear idea of what you want to achieve, and with that we can guide you to the best model for you.
Every model is built around a single, precisionengineered welded frame. Effectively, this gives you the platform to cut board at 90° without any vibration, and it offers a cutting accuracy within 0.1mm. All models are made to the same tolerances regardless of their cost, and come with an automatic moving frame and fixed transport rollers. As well as the same heavy-duty ergonomics, additional features like scoring saws and digital read-outs are also built exactly the same way on every model. As you go up the range, what you get is more power, a bigger cut depth, more sophistication and more automation.
Non-standard machine sizes can also be specified up to 800mm taller and 6m longer, if required.
What level of automation do I need?
There are a lot of advantages to automation, but not always ones you’d expect. It’s a common misconception that automation will halve your production times. but it’s important to remember that the saw needs to carry out the same cutting process, regardless of whether this is done manually or automatically.
In a vertical panel saw the automation works continuously, making light work of volume cuts. With minimal operator intervention, it offers a better cut quality due to the saw’s automated feed speeds, and it can cut unaided while an unskilled operator loads and unloads the saw. Automated features also protect the saw against operator misuse – it won’t let you do things in the wrong order or cut incorrectly – leading to fewer breakdowns and repair bills.
Striebig’s Base and Expert Cut optimisation software can also improve your workflow and reduce the skill level needed to optimise production. Optimisation software, which can be retrofitted to an existing machine if required, can create cutting lists that direct both the machine and the operator. It can also generate labels with barcodes, QR codes or descriptions for effective processing and stock management. Additional stock and waste management software can also be integrated into this for extremely efficient production.
What are the most popular extras on a Striebig?
Striebig’s scoring saw is different to others in the market. It’s a proper belt-driven, fully adjustable, high-speed scoring unit, like you would expect on a top-quality panel saw or beam saw. It is not a double-cut score system or a knife system. It is the same design on all models, regardless of their size or cost.
The Striebig’s full wooden backing system (TRK) also sets the Striebig brand apart. The TRK system improves dust extraction by providing a dust capture behind the panel, while also fully supporting the sheet material. Nothing beats this design when cutting thin or flexible panels. Other machines have supports placed 6in apart, which can lead to thin materials flexing. With the Striebig’s wooden backing, the support is never more than a few millimetres from the edge of the blade, leaving no opportunity for the panel to flex.
Striebig vertical panel saws can also cut specialist materials, thanks to their adjustable motor speed, rotation speed of tooling and feed speeds. The machine is equally as effective cutting through thick materials as it is grooving ACM. It can also be built to cut materials as deep as 130mm.
Is a Striebig vertical panel saw affordable?
Your budget is always a factor with any purchase. We don’t pitch a machine to match your budget. If we can’t supply a machine that works to your specification and budget, we will be open and honest with you. For many of our customers, finance is often a good solution. We don’t supply finance – we specialise in selling and servicing woodworking machinery – but we work with a well-respected woodworking machinery broker who is experienced in helping the industry. It’s often an affordable and simple solution when purchasing new and used woodworking machinery.
Why should I work with TM Machinery?
TM Machinery is the UK’s exclusive distributor of Striebig vertical panel saws. Our sales team, engineers and aftersales team have been trained by Striebig in order to offer you the very best service.
TM also has an unrivalled service division, holding over £350,000-worth of spare parts in its Leicester-based premises – including spares suitable for machines up to 50 years old. This investment in the brand allows our team to act quickly to solve problems on-site without the need for repeat visits.
But don’t just take our word for it. Word of mouth says a lot about a company, and we don’t shy away from sharing our customers’ stories with you. Talk to our customers, hear what they have to say, and get in touch.
0116 271 7155 sales@tmservices.co.uk www.tmmachinery.co.uk
Vollmer offers two-in-one solution
Cutting tool manufacturers have always had the inconvenience of producing solid carbide and PCD cutting tools on two separate machines – until Vollmer introduced its VHybrid concept. Now, Vollmer has eradicated this issue for cutting tool manufacturers, with its flexible new VHybrid 260 solution, which can grind carbide tools and erode PCD tools – all in one machine.
The exceptional new Vollmer VHybrid 260 combines the technologies of an innovative grinding machine and a powerful erosion machine, making it possible to switch easily between erosion and grinding functions.
Utilising Vollmer’s unique, multilayered machining technology, which was first proven in the VGrind series of machines, the vertical alignment of two spindles is a groundbreaking arrangement that allows the grinding and electrode wheel sets to precisely pivot the C-axis, ensuring optimal results.
This configuration allows users to combine both processes. If the tool requires both grinding and erosion, the VHybrid 260 can create one complete and highly efficient machining process for all tool production requirements.
The multi-layered spindle configuration allows the efficient grinding of carbide tools with diameters of up to 150mm on the top spindle, whereas the bottom spindle can accommodate both grinding and erosion. This enables the efficient machining of carbide or PCD tools up to a diameter of 150mm, thanks to the highperformance and finely tuned VPulse EDM erosion generator, which maximises productivity and performance while reducing production costs.
This ultra-precise erosion generator delivers surface finishes to a roughness of 0.1μRa, for the best-possible cutting tool quality, while electrode calibration and wear control that combines with a dressing device provide fully automated processing with
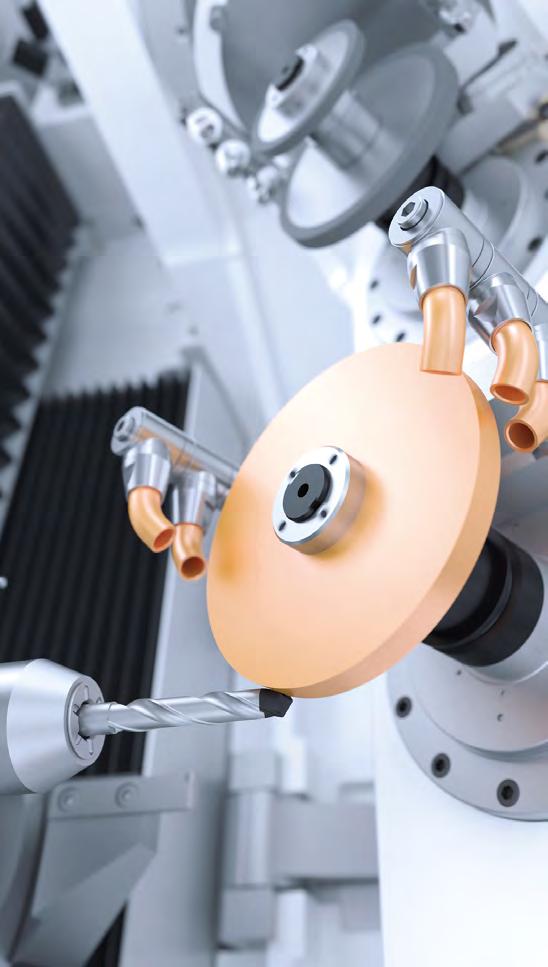
Vollmer VHybrid 260
“The exceptional new Vollmer VHybrid 260 combines the technologies of an innovative grinding machine and a powerful erosion machine”
unwavering quality levels.
Quality is built into every facet of the VHybrid 260, and Vollmer demonstrates this with its innovative ‘wall concept’ which provides the highest-possible rigidity and vibration damping through its concrete polymer foundation. This is complemented by the effective spindle and motor-cooling technology, that creates greater thermal stability for unparalleled precision and power, while the vertical spindle configuration eradicates issues related to fixing and floating bearings.
Automation and ease of use are factored into every element of the new VHybrid 260, and this includes the tool-loading and unloading facilities. Here, Vollmer offers several options with its HC4 chain magazine, with space for 39 HSK-63A tools or up to 158 shank-type tools with a maximum weight of 5kg. Alternately, for manufacturers producing larger tools, Vollmer offers the HC4 Plus, which provides space for 160 shank-type tools or 40 HSK-63A toolholders with a tool diameter of 80mm. With larger tool diameters of up to 150mm, there is space for 20 HSK-63A toolholders with a maximum weight for individual tools up to 10kg.
The automation options also extend to the eight-tool grinding wheel changer, which ensures the right grinding wheel for the right tool is always supplied to the work envelope, with no manual intervention. As an option, coolant nozzles can be automatically exchanged with the wheel sets on both spindles.
From an operator ergonomics and ease-of-use perspective, Vollmer once again excels with its multi-function handwheel for easy axis adjustment, simple touchscreen control, optimal machine access and heightadjustable tilting control platform. This ease of use extends to the modularly designed ExLevel PRO software, which allows efficient, fast and easy machining of a wide range of tools in both grinding and eroding operations. This simplicity extends to tool simulation that can be set up directly at the machine or remotely.
To further enhance performance, precision and quality, Vollmer provides a multitude of optional extras. These include linear scales on all axes for even greater precision levels and performance, plus a steady rest to optimise grinding results when processing longer cutting tools that have the potential to deflect. Vollmer also offers automated gripper compensation as an in-process solution. This provides maximum precision when loading and unloading tools and reduction sleeves, reduces wear, and maximises stability. 0115 949 1040 www.vollmer-group.com
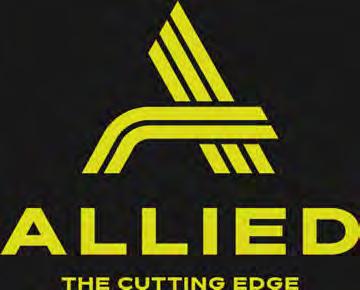
The Launch of AKE The Launch of AKE The Launch of AKE The Launch of AKE SuperSonic SuperSonic SuperSonic SuperSonicSaw Blades Saw Blades Saw Blades Saw Blades
• High productivity • Significant longer tool life • Reduction of costs • Noise reduction
In 2009 AKE launched the SuperPlus Saw Blade for table, vertical panel sizing and horizontal panel sizing machines. After the enormous success of the SuperPlus Saw Blade, AKE and Allied Tooling joined forces in 2021 to modify and improve the SuperPlus product, leading to the launch of the SuperSonic version. Our AKE SuperSonic Blade out performs all competition for life span, offering the lowest cost-per-cut available. With the new tooth geometry, mirror finish cutting edges and the innovative Black Belt Technology, you can expect the following: • Reduction in downtime • High productivity • Guarenteed high cutting • Significant longer tool life quality on all products • Reduction of costs • No jointing or other • Noise reduction repair work
In 2009 AKE launched the SuperPlus Saw Blade for table, vertical panel sizing and horizontal panel sizing machines. After the enormous success of the SuperPlus Saw Blade, AKE and Allied Tooling joined forces in 2021 to modify and improve the SuperPlus product, leading to the launch of the SuperSonic version. Our AKE SuperSonic Blade out performs all competition for life span, offering the lowest cost-per-cut available. With the new tooth geometry, mirror finish cutting edges and the innovative Black Belt Technology, you can expect the following: • High productivity • Significant longer tool life • Reduction of costs • Noise reduction • Reduction in downtime • Guarenteed high cutting quality on all products • No jointing or other repair work
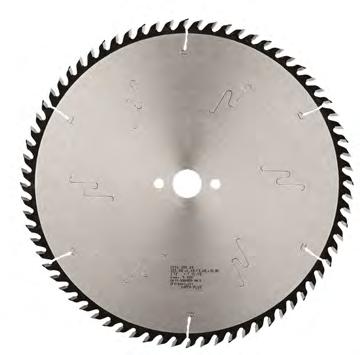
In 2009 AKE launched the SuperPlus Saw Blade for table, vertical panel sizing and horizontal panel sizing machines. After the enormous success of the SuperPlus Saw Blade, AKE and Allied Tooling joined forces in 2021 to modify and improve the SuperPlus product, leading to the launch of the SuperSonic version. Our AKE SuperSonic Blade out performs all competition for life span, offering the lowest cost-per-cut available. With the new tooth geometry, mirror finish cutting edges and the innovative Black Belt Technology, you can expect the following: • High productivity • Reduction in downtime • Significant longer tool life • Guarenteed high cutting • Reduction of costs quality on all products • Noise reduction • No jointing or other repair work
In 2009 AKE launched the SuperPlus Saw Blade for table, vertical panel sizing and horizontal panel sizing machines. After the enormous success of the SuperPlus Saw Blade, AKE and Allied Tooling joined forces in 2021 to modify and improve the SuperPlus product, leading to the launch of the SuperSonic version. Our AKE SuperSonic Blade out performs all competition for life span, offering the lowest cost-per-cut available. With the new tooth geometry, mirror finish cutting edges and the innovative Black Belt Technology, you can expect the following: • Reduction in downtime • Guarenteed high cutting quality on all products • No jointing or other repair work
Working materials: • Roar chipboard • Melamime faced chipbaord • Roar MDF • Melamime faced MDF • High pressure laminate • Solid surface • Plywood • Melamime faced plywood • Solid wood • Softwood • Hardwood Working materials: • Roar chipboard • Melamime faced chipbaord • Roar MDF • Melamime faced MDF • High pressure laminate • Solid surface • Plywood • Melamime faced plywood • Solid wood • Softwood Working materials: • Roar chipboard • Melamime faced chipbaord • Roar MDF • Melamime faced MDF • High pressure laminate • Solid surface • Plywood • Melamime faced plywood • Solid wood • Softwood • Hardwood Working materials: • Roar chipboard • Melamime faced chipbaord • Roar MDF • Melamime faced MDF • High pressure laminate • Solid surface • Plywood • Melamime faced plywood • Solid wood • Softwood • Hardwood www.alliedtooling.com sales@alliedtooling.com +44(0)1202 675767 • Hardwood www.alliedtooling.com sales@alliedtooling.com +44(0)1202 675767 www.alliedtooling.com sales@alliedtooling.com +44(0)1202 675767 www.alliedtooling.com sales@alliedtooling.com +44(0)1202 675767
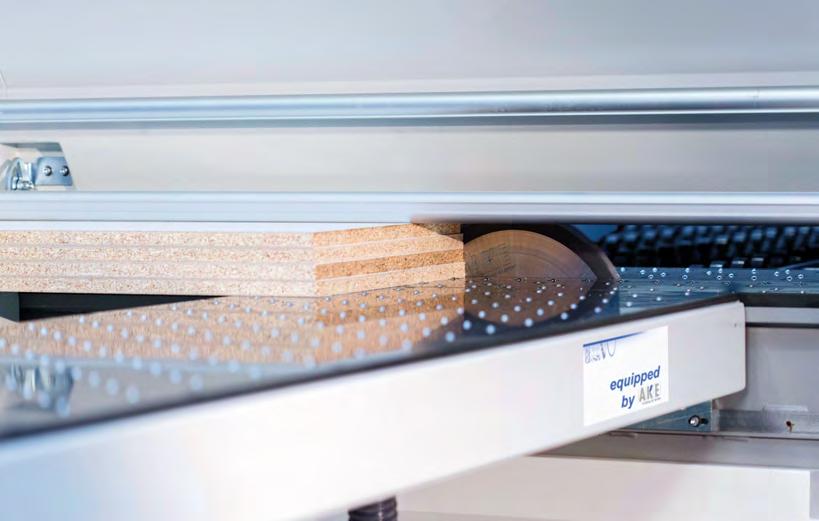