17 minute read
Installations
Covers Timber invests in Salvador crosscut technology from Daltons Wadkin
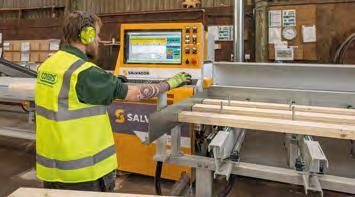
The installation of a Salvador SuperPush 250 chain-fed automatic crosscut saw has allowed Covers Timber and Building Merchants to keep pace with increasing production demands and provide flexibility in staffing within its feeder mills.
Having supplied timber and building materials across the South East for over 175 years, Covers now boast some 15 branches, with an extensive range of over 25,000 product lines. Wanting to satisfy growing customer demand, product manager Peter Openshaw saw an opportunity to help push the company ahead of the competition.
“We are fortunate that we have highly skilled salespeople, excellent production cability and a very positive attitude, being open to new opportunities,” comments Peter. “Our ability to source most things and improvise and adapt ourselves to reflect our changing market helps us achieve strong performance results. Our competitors are very good indeed, so this pushes us to try even harder.”
Following a thorough investigation of available crosscut saws on the market, Peter contacted Daltons Wadkin, sole distributor for Salvador in the UK and Ireland. “Peter’s requirements were very familiar – we have helped dozens of timber merchants with similar projects, and I knew immediately we had the right solution,” enthuses Daltons Wadkin’s sales director, Andy Walsh. “For high-production crosscutting, the Salvador SuperPush range is ideal – automatic push infeed, cutting list optimisation, heavy-duty construction, and easy to use.”
The Salvador SuperPush 250 is a programmable crosscut saw capable of processing up to 130m3 of timber per shift. Up to seven infeed loading chains ensure the machine is continually fed with individual or stacked workpieces, while the outfeed collection area is automatically cleared for uninterrupted production.
Covers’ investment in a Salvador has given it flexibility in staffing, which in turn has positively affected growth. Peter is keen to point out the benefits from a production point of view. “Automatic machinery cuts down on the labour required to carry out particular jobs,” he says. “We have found it difficult to recruit recently, and anything that reduces the need for labour helps with this problem.”

“For high production crosscutting, the Salvador SuperPush range is ideal – automatic push infeed, cutting list optimisation, heavy duty construction, and easy to use”
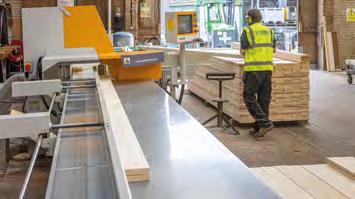
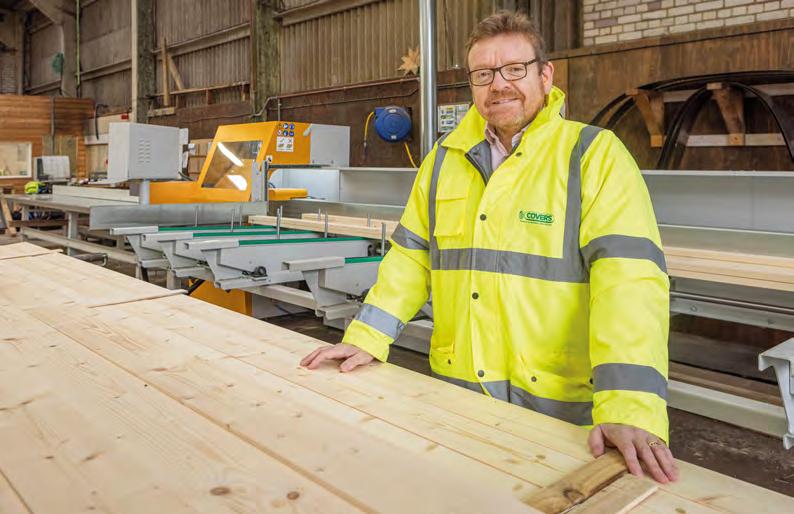
The Salvador SuperPush 250 is equipped with chain infeed loading
Intuitive operator control
Salvador SuperPush 250 automatic crosscut saw
Automatic outfeed collection allows the machine to operate uninterrupted
Turnkey delivery and commissioning was provided for Covers, expertly managed by the Daltons Wadkin project installation team. “We have a dedicated group of engineers within our service department whose sole focus is on delivering a frictionless installation and dedicated ongoing support when required,” comments Andy. “We go to extreme lengths to ensure all our customers receive the best possible service for the life of the machine.”
For more information on the Salvador range of crosscut saws, contact Daltons Wadkin on 0115 986 5201, email info@daltonswadkin.com or visit www.daltonswadkin.com.
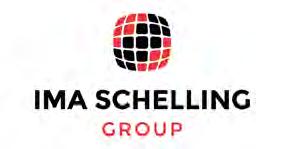
IMA Schelling UK enhances customer service with launch of new website
IMA Schelling UK is a subsidiary of IMA Schelling Anlagenbau in Austria, which is part of IMA Schelling Group, which celebrated 100 years of manufacturing in 2017 and is recognised as one of the most experienced saw manufacturers in the world.
IMA Schelling has always maintained a great relationship with all of our customers, and nothing was going to change that during lockdown.
Since the acquisition of IMA Klessmann UK in March of 2021, we have gone from strength to strength and can offer the full range of IMA Schelling group equipment to our customers, not just saws but also edgebanders and CNC machines.
We have also launched a new website in 2021– www.schelling-solutions.co.uk – to inform customers of our other services and product lines.
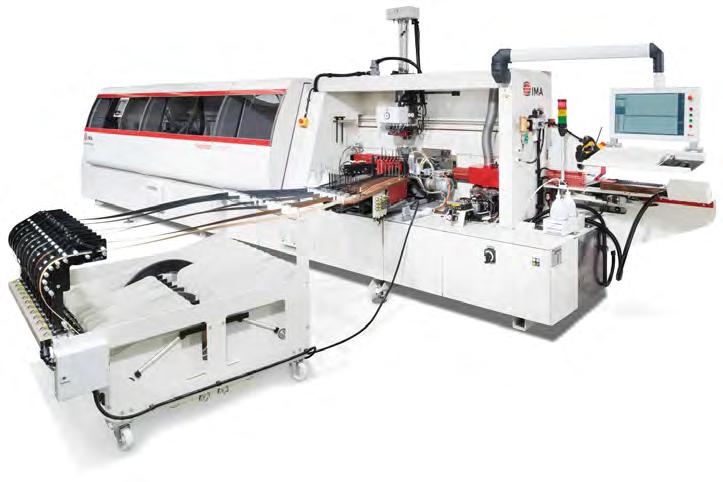
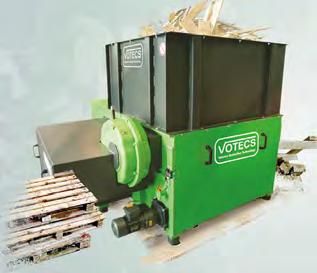
Customers can find other complimentary and supporting equipment, such as lifters and shredders (hoggers) for wood waste, alongside many other items of interest,
IMA Schelling aims to provide the right solution for its customers, no matter what your requirements are.
For further information, call IMA Schelling UK on 01937 586340
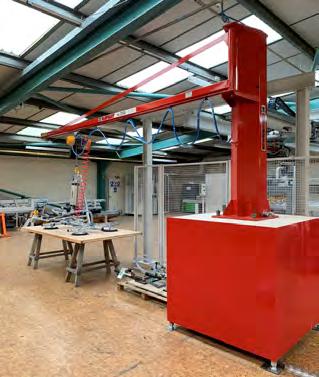
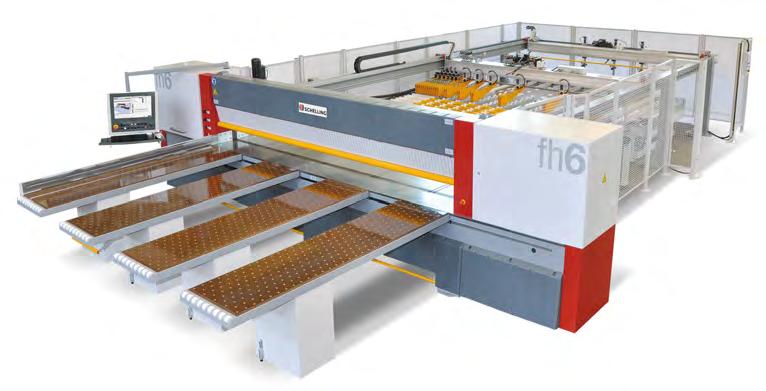
Extractly system is quiet, dust-free, and half the price to run
Extractly has commissioned an additional energy-saving extraction plant at Tom Howley’s kitchen manufacturing facility near Glossop, Derbyshire, where the custom-designed system serves the machining operations side of the company’s 5000m2 factory.
Established in 2004 by design director Tom Howley, the luxury kitchen brand has a nationwide presence through its 18 showrooms located across the UK, with another due to open later this year. Employing the highest-quality materials to produce bespoke fitted kitchens in oak, walnut and hand-painted finishes, Tom Howley kitchens range in style from classic to contemporary.
Through acquisition by Neville Johnson Group in 2011, the company is now part of the renamed Bespoke Home Interior Design Group (BHID), which also comprises Neville Johnson Furniture, Neville Johnson Staircases, and the London Door Company.
Over the years, and in common with many furniture manufacturers, the company has replaced older machinery with newer, faster equipment, as well as adding new machines to increase capacity. The well-equipped production facility now houses two CNC machining centres, with another due to be installed in the spring, along with numerous saws, spindle moulders and routers, plus two Boere widebelt sanders which alone account for over 35% of the factory’s total extraction requirement.
In summer 2021, in order to optimise workflow, a reorganisation of machinery was being undertaken at Tom Howley, and Extractly was contracted to reconfigure the ductwork arrangement and integrated Ecogate® equipment which was controlling extraction to an existing, externally sited filter
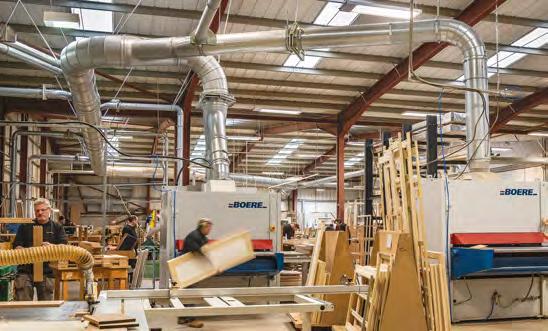
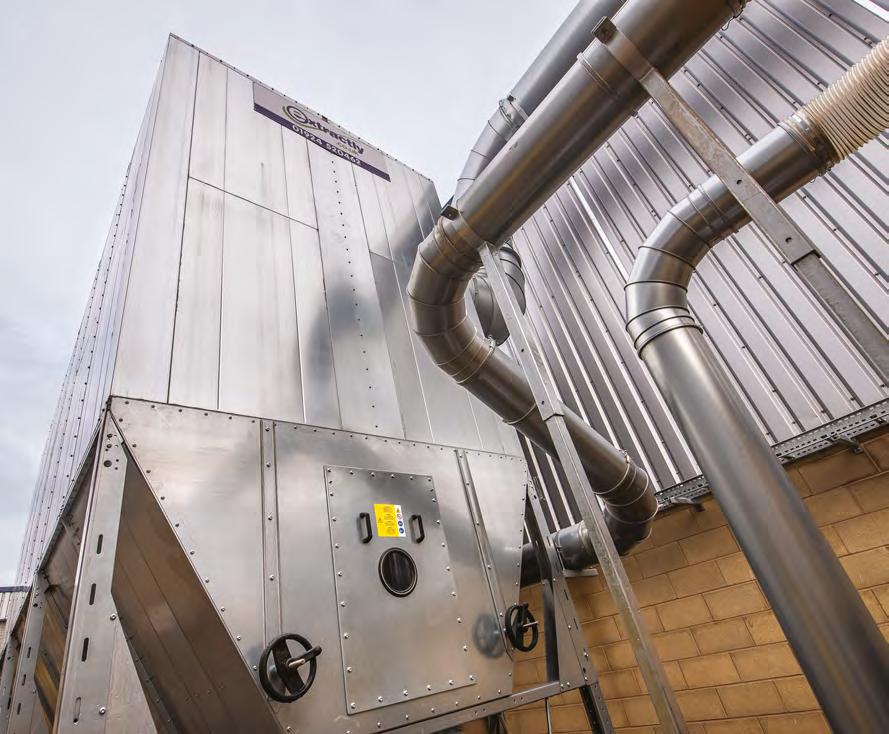
The two Boere sanders naturally require high-powered extraction when running but, with Ecogate® installed, energy consumption is significantly reduced when the machines are idle
unit, which continues to serve the finishing side of the factory.
Over on the machining side, however, planned installations of new, high-speed, dust-producing equipment would require a significant increase in extraction capacity. As factory manager, Alan Ashmore, explains: “The previously installed, internally sited filter unit was going to need at least an upgrade, but probably replacement, so we approached Extractly for a quotation to bring the system up to specification.”
After a full review of current and expected future extraction requirements, Extractly’s proposal included decommissioning the old filter and replacing it with a new, externally sited unit.
“There were three key areas that needed consideration at Tom Howley: the requirement for increased extraction capacity; the need to expand the energy-saving Ecogate® system; and, since the only sensible option was to install a new fan and filter unit outside the building, to protect neighbouring residential properties from excessive noise pollution,” says Extractly director, Jake Oldfield.
“The filter unit Extractly installed at Tom Howley is a Nederman NFKZ3000 5+1 – a six-module unit fitted with Nederman’s patented, highperformance, polyester Superbag filter bags”
With projected airflow demand approaching 55,000m³ per hour, and suction provided by a 90kW main fan, Alan Ashmore had highlighted from the outset that it was crucial for the extraction system to be silenced to an acceptable level for residents living less than 50m from the location earmarked for the new dust plant.
To ensure there would be no environmental impact at residential properties closest to the site, Extractly commissioned a BS4142 noise impact survey from specialist Beechfield Design Consultancy (BDC).
Armed with environmental noise measurements and using acoustic calculations, BDC established requirements for noise attenuation at the site, and designed and manufactured bespoke absorptive silencers. Fabricated from galvanised steel sheet, these particular silencers are designed to reduce the sound generated by turbulent air inside the fan, as well as the noise which travels down the ducting.
Internally, the enclosures contain sound-insulating materials, sandwiched within sheets of perforated steel, and spaced to allow efficient, unimpeded flow of dust-laden air through to the filter unit.
Extractly’s engineers installed the noise attenuation equipment at the same time as the new fan and filter unit, and the design will ensure sound levels at the nearest properties are equivalent to normal background levels.
The filter unit Extractly installed at Tom Howley is a Nederman NFKZ3000 5+1 – a six-module unit fitted with Nederman’s patented, high-performance, polyester Superbag filter bags. Filtered dust waste drops into the hopper below, where a drag-chain conveyor transfers the collected waste to a rotary valve discharge unit. A series of five 1.1kW regeneration fans enable filter bag cleaning to be carried out automatically during operation, and waste dust is transferred, pressure-free, directly to a covered box cart.
Designed for continuous operation and to handle high dust volumes, these units are manufactured to strict safety and emissions standards, and are fully ATEX compliant. In addition, the modular construction will allow Tom Howley to add further modules if future equipment acquisitions further increase demand for dust extraction.
The installation has also benefited from the inclusion of a second Ecogate® greenBOX12 controller, doubling the capacity of the existing on-demand energy-saving system. Ecogate® technology works in conjunction with a variable speed drive unit, which automatically adjusts and optimises the running speed of the main extraction fan as individual woodworking machines come on line or shut down.
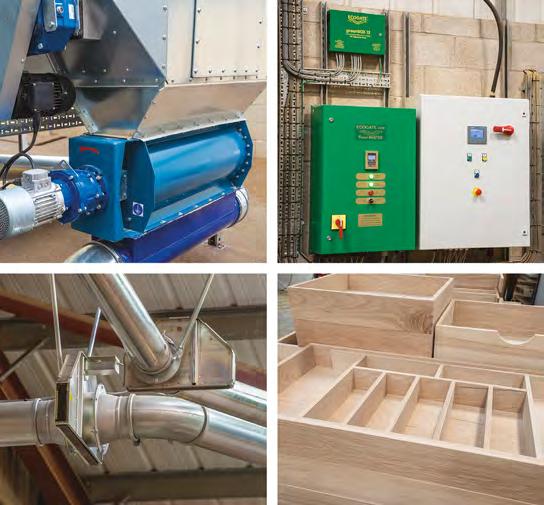
Top left: Rotary valve unit discharges filtered waste pressure-free Top right: Ecogate technology controls extraction throughout the factory Bottom left: Ecogate automatic dampers fitted to all machines Bottom right: Bespoke cabinetry produced at Tom Howley
When compared to standard installations, where the fan operates continuously at full power, an Ecogate® system can typically reduce energy consumption by over -50% — with the resulting cost savings becoming more dramatic as energy prices continue to rise.
Extractly’s technical director, William Kenyon, who has been involved with Ecogate since the technology was introduced to the UK woodworking industry back in 2010, explains how these savings are made: “With Ecogate®, sensors on each machine constantly monitor usage, and extraction is independently controlled, in realtime, to match the requirements of each individual piece of woodworking machinery.
“Since the extraction system only operates when machines are running, the total extraction volume requirement is significantly reduced, creating potential for huge energy and cost savings, as well as lower noise levels – both at the fan, and inside the factory.”
Extractly completed the installation over the Christmas downtime and commissioned the system in time for full production to get under way as the company returned to work again in the new year.
Adam Slack, Howley’s production supervisor, says: “Everyone is delighted with the job Extractly have done here. We now have a fully automated, future-proofed system which just gets on quietly and efficiently with the task of dust extraction — levels of both dust and noise on the factory floor have been reduced significantly.
“We were also very impressed with the standard of work, and the way Extractly handled every aspect of what was a very time-contingent contract.” 01924 520462 info@extractly.co.uk www.extractly.co.uk
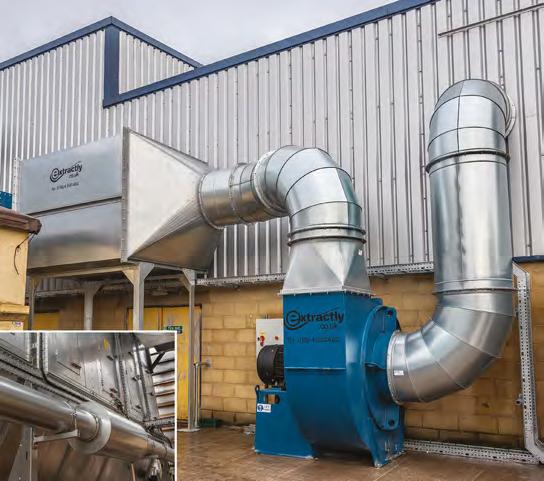
“Everyone is delighted with the job Extractly have done here. We now have a fully-automated, future-proofed system which just gets on quietly and efficiently with the task of dust extraction”
JDH Joinery ramps up production with new Homag equipment
JDH Joinery, a diverse manufacturer of joinery products, has seen a marked improvement in its production volumes following the recent installation of a Homag Sawteq B-130 panel saw.
The company designs and produces a wide array of high-end furniture products for office fit-outs, kitchens and bedrooms. Its highly skilled team of joiners work with an extensive range of materials, including panel-based products such as MDF, laminates, veneers, melamine-faced boards, hardwoods, softwoods and solid surface materials.
Established in 2016, JDH joinery operates from a 6000ft2 facility in Chester. It has a fully equipped machine shop, assembly area, spray shop, storage facility and office space.
After observing a significant increase in demand for its products, the company recently invested in a Homag Sawteq B-130 panel saw. According to company director, Joseph Hannigan, the company’s joiners can now manufacture twice as many panels with the Homag panel saw than they previously produced using a manual sliding table saw. “The company’s joiners can now manufacture twice as many panels with the Homag panel saw than they previously produced using a manual sliding table saw”
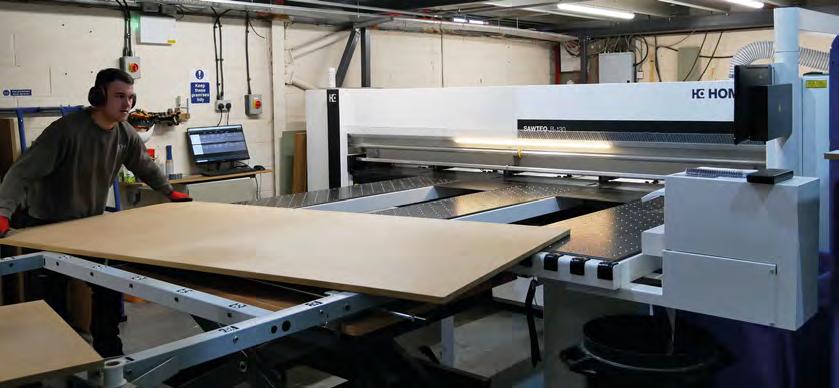
Optimised material processing delivers increased yield and less waste
“It can accurately and quickly cut a large volume of material into components,” enthuses Joseph. “The new panel saw now enables us to label the panels ready to be moved onto our CNC or edgebanders. The machine’s software also passes production information to these other machines and assembly areas. These advanced features have effectively optimised our material processing so we can achieve a far better yield and create less waste.
“For such a powerful machine, it also benefits from a small footprint. The control software – CADmatic 5 – is easy and intuitive to use, and will enable us to take advantage of more advanced software applications (such as Tapio) in the future.” Joseph also mentions the exceptional service he received from Homag. “I was impressed with the expert advice provided by the Homag sales representative, and with the timely Homag installation and comprehensive operator training,” he says. “Homag is therefore at the top of my list of wood-processing equipment suppliers I would recommend to others.”
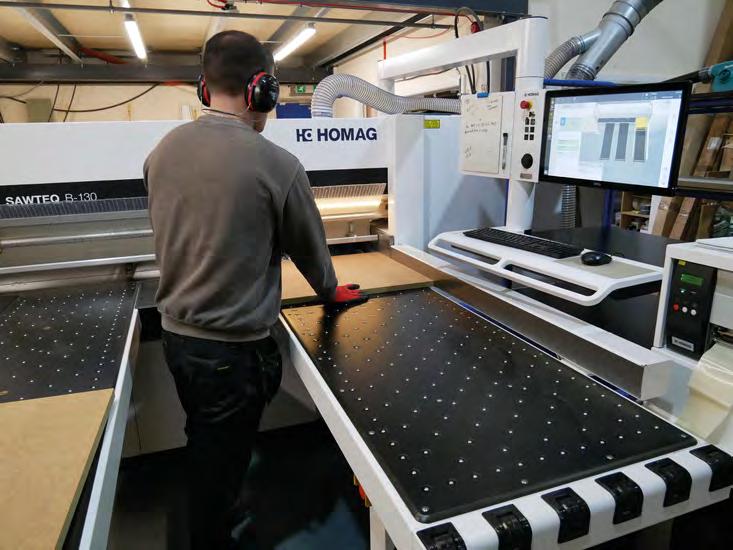
Homag equipment came highly recommended
As part of his panel saw selection process, Joseph visited the Homag exhibition stand at the Ligna woodworking show – a world-leading trade fair for woodworking and wood-processing plants. When assessing the machine’s features before purchase, the most important benefits Joseph specifically required from a new panel saw were operational efficiency, ease of use and integration into the existing workflow.
Joseph opted to purchase the Homag panel saw after reviewing the panel saw specifications of other brands and the recommendations from many professionals in the woodworking industry that had long-term experience of using the Homag Sawteq B-130 panel saw.
His own experience of the efficient operation and reliability of other types of Homag machinery used in his workshop also played a role in his decision to select the Homag brand for his new panel sawing requirements.
For a demonstration or more information on Homag’s machinery or software, contact Adele Hunt at Homag UK on 01332 856424. info-uk@homag.com www.homag.com
Longwood Joinery enhances product quality with Hoffmann’s CB-M end profiler
Longwood Joinery has been manufacturing quality windows, doors and staircases since 1972, and is a committed member of the British Woodworking Federation (BWF) and the Construction Industry Training Board (CITB). The current owners, Paul Shooter and Andrew Humphries, took charge in 2008 when the original owners decided to retire.
The company has a welldeserved reputation for delivering quality products on time, and has developed close relations with its customers. Although Longwood Joinery supplies many of the major house builders, such as Persimmon Homes, Linden Homes and many more, it still offers its individual customers the highest level of project consideration and impressive value for money.
The company prides itself on working to the highest standards within the industry for performance and quality, with investment in the latest machinery to further enhance and innovate the manufacturing process.
Having been Hoffmann customers for many years – using the Hoffmann MU-2 in the production of handrails and staircases – Paul and Andrew were keen to bring Hoffmann reliability, accuracy and speed into the window-production side of the company. The Hoffmann CB-M end profiler – a resourceful counter-profiling machine for the production of crossbar joints – was designed exactly for this purpose.
After various discussions with John Galvin, director at Hoffmann UK, Paul visited the Hoffmann stand at the 2019 Harrogate Woodworking Show for a demonstration of the Hoffmann CB-M. This practical bench-top version is ideal for the small- and medium-size manufacturer. It produces precise, tear-free counter profiling on the ends of Georgian bars in furniture, windows and door manufacturing. Two variable speed, counterrotating router motors – left / right – create the counter profile on the end of the bar accurately, and fit without chipping or tearing. The variable-speed motors can be adjusted for the optimum speed to produce the best possible finish. Choice of speed is relevant to the profile shape and the wood species.
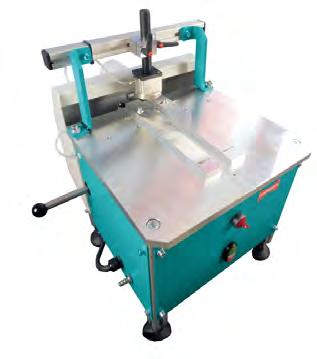

“We can now cut the glazing bars to suit the required profile of each individual piece, allowing a much tighter joint with less filling needed before finishing”

The machine is supplied without tooling, as each customer will require tooling to suit their own particular profiles. The application of this joint would be in Georgian window design, doors and furniture. When sealed doubleglazed units are used, the profiles are attached to the surface with a dedicated adhesive tape.
Paul was so impressed with the demonstration at the show that a sale was agreed there and then. “The Hoffmann CB-M end profiler has certainly increased the quality of the finished product,” he says. “We can now cut the glazing bars to suit the required profile of each individual piece, allowing a much tighter joint with less filling needed before finishing.” Longwood Joinery is using the CB-M to produce Georgian glazing bars on its doors and windows. 01524 841500 info@hoffmann-uk.com www.hoffmann-uk.com
Joinery company saves money by turning waste into free heating
A Lancashire joinery company has purchased a woodwaste heater from Wood Waste Technology to save money on its operating costs.
Station Yard Joinery manufactures highend bespoke furniture from its woodworking machine shop in Earby, Lancashire. When the business moved into its current unit about a year ago, the 4500ft2 building, with its high roof, proved to be a cold place to work in the winter months.
Having experienced the benefits of woodwaste heaters at a previous company, MD of Station Yard Joinery, Martin Conboy, decided the business should invest in one, so contacted Wood Waste Technology.
Following a survey and a quote, the business purchased a WT5 that was installed by Wood Waste Technology’s experienced engineers. It provides much-needed heating for the workshop in winter, but also provides free disposal of the large amount of waste wood generated from the manufacturing process.
Having previously invested in a dust collection system and a briquetting machine, Station Yard Joinery also has the ability to recycle some of its waste into briquettes, to be used in the woodwaste heater alongside its general wood waste. “It makes no sense to spend hundreds of pounds on skips to get rid of our wood waste when we can burn it to convert it into heat for the factory,” says Martin.
“We’ve definitely made the right decision for our business by investing in the woodwaste heater. It’s a great piece of kit which will keep us warm and save us money.
“In addition, we’re looking forward to recycling our dust into briquettes, which will burn really well in the woodwaste heater!”
MD of Wood Waste Technology Kurt Cockroft adds: “It’s great that the team at Station Yard Joinery can burn their waste and briquettes in the heater to generate warmth in the workshop, instead of paying for skips to take it away.”
Wood Waste Technology offers a full range of woodwaste heaters, from small, handfired units to larger, fully automatic systems, and offers site survey and design, as well as manufacture, installation and ongoing maintenance. The company also services all types of woodwaste heaters, and supplies genuine spares up to -60% cheaper than other suppliers.
In addition, Wood Waste Technology is the UK’s official distributor for Gross Apparatebau – a German manufacturer of dependable, precision-engineered shredders and briquetters. The company is also a distributor for Putzmaus boiler tube cleaning systems – a powerful but gentle routine maintenance solution that is quick and easy to use, and helps to increase boiler efficiency and lower operating costs. For more information on saving or making money by using wood waste, call 01785 250400 or visit www.woodwastetechnology.com, www.grossuk.co.uk or www.putzmaus.co.uk.

Automatic crosscut saws

Daltons Wadkin offer a comprehensive range of automatic programmable crosscutting systems for straight and angle work complete with powerful optimisation and defecting software as standard.
production costs reduced by up to 5-15%
50%
less wood used
Visit our Nottingham showroom for a demonstration
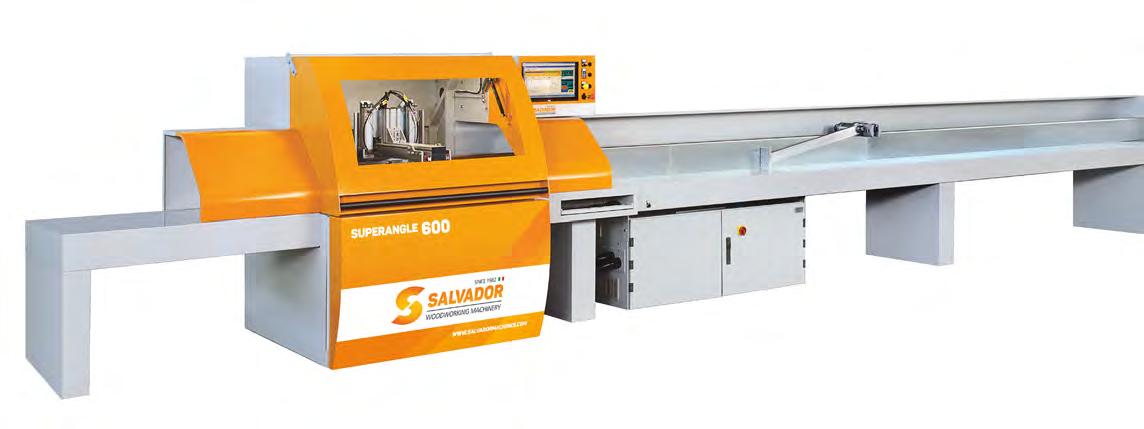