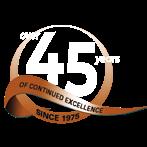
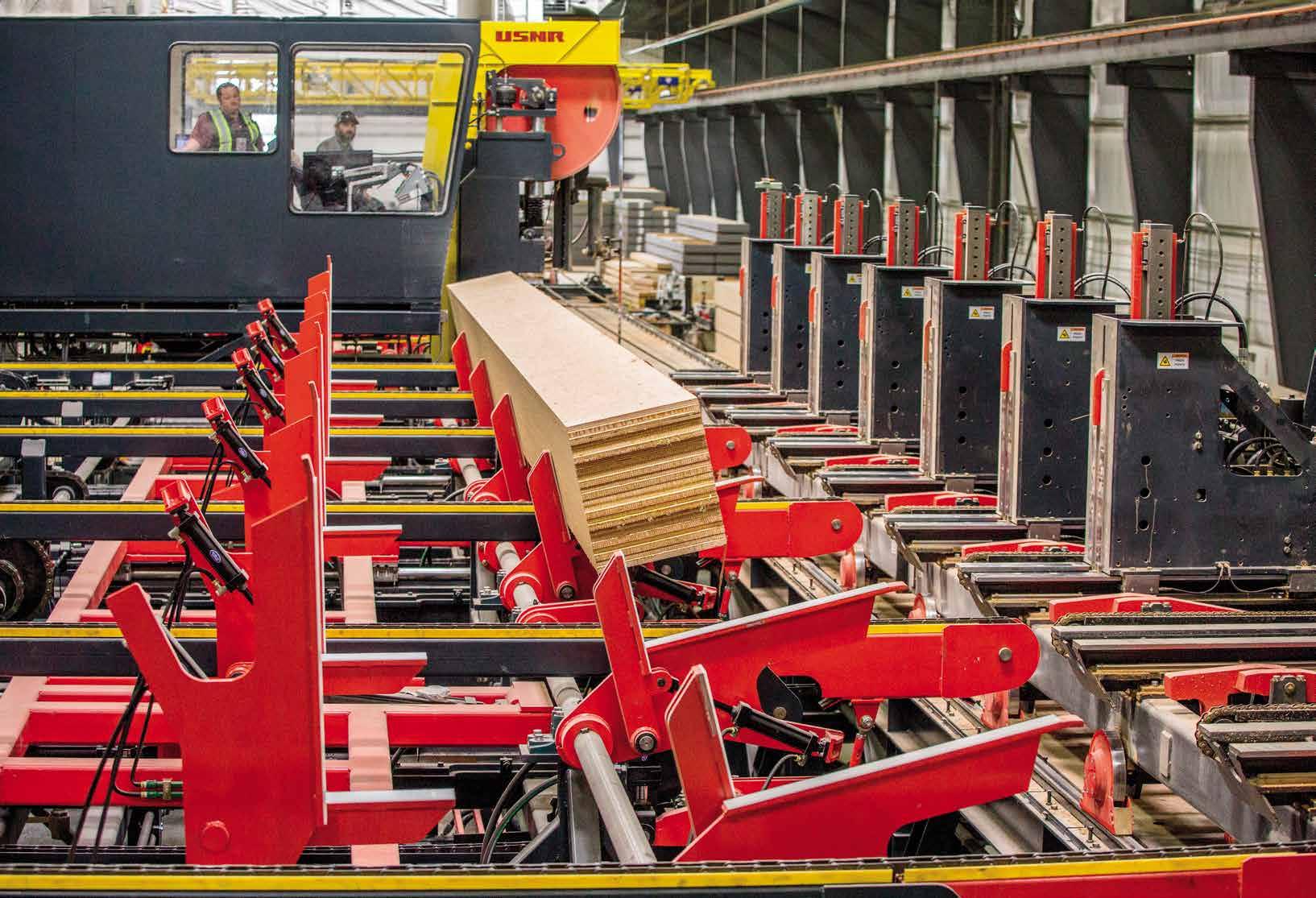

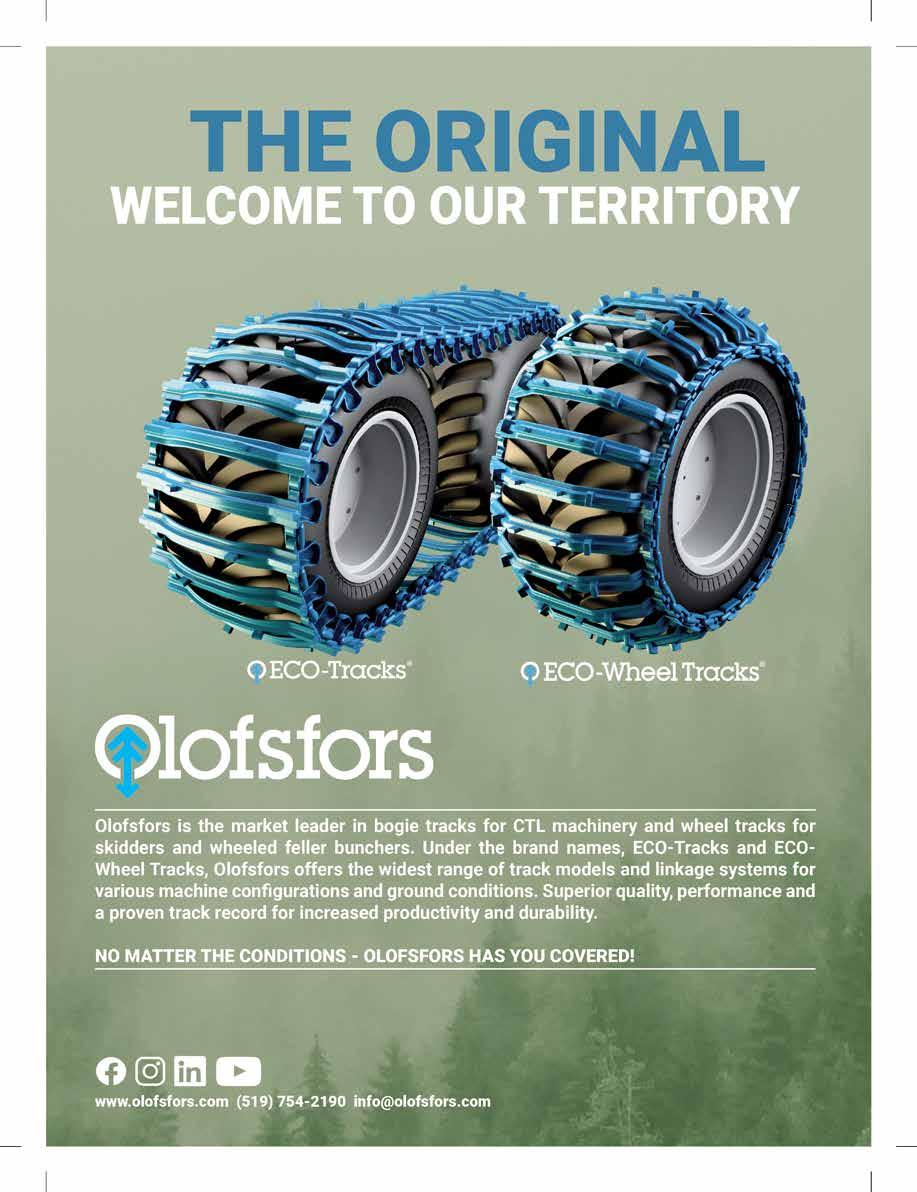
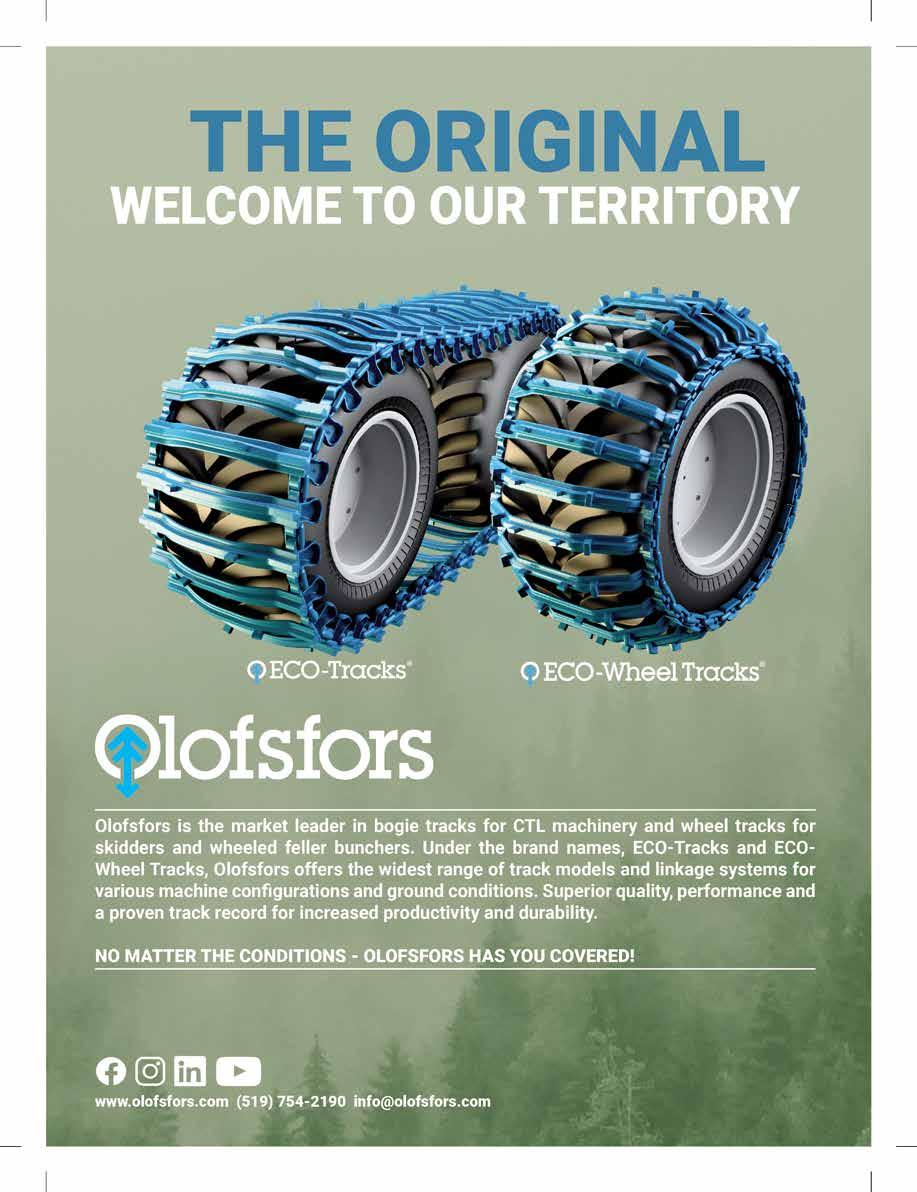
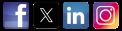
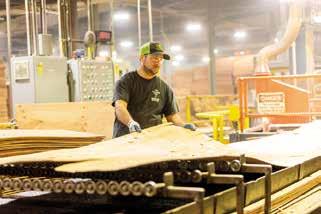
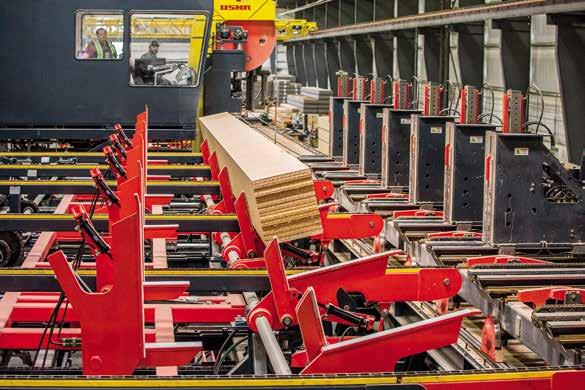
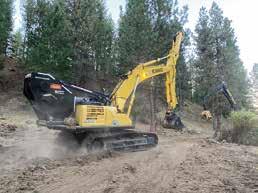
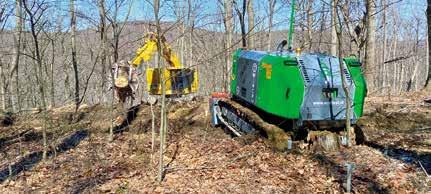
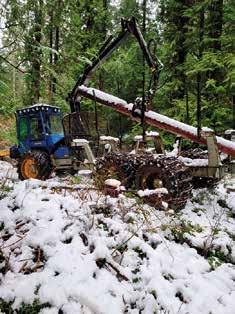
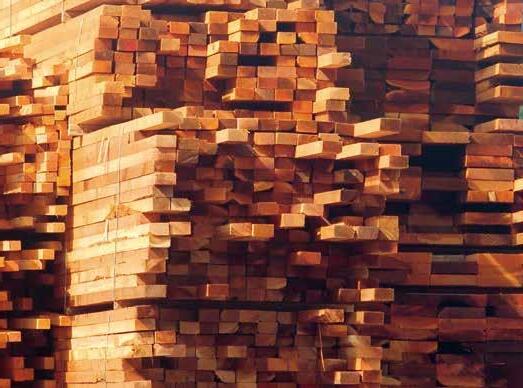
Wood for participating in an article in this issue of TimberWest.
(See story on page 12.)
The family-owned Oregon company has quite a story to tell. They’ve successfully adapted to market challenges over the years. Their latest innovation was the development of the company’s mass ply panel wood products.
The manufacturing process relies on equipment developed and supplied by some of the leading machinery suppliers to the wood products industry and suppliers of automation technology, including two in Oregon.
Going forward, TimberWest plans to include regular coverage of the region’s wood products manufacturers in addition to its logging and forestry businesses. They go hand in hand and depend on each other. Whether it be a sawmill, a business that makes an engineered
wood product, a paper product, or some other wood product, we will be looking to tell their stories.
If your company operates a mill or other manufacturing plant that makes a product from wood, and you are interested in sharing your story, let us hear from you. We are particularly interested in companies that have expanded manufacturing capacity or have made significant improvements or upgrades to major machine centers in order to increase production and efficiency. If you are a supplier of equipment or technology to the woods products industry, feel free to get in touch and recommend a customer that has benefitted from its application of your product.
If you would like to recommend a company contact me, Anthony , or Tim Cox, our editor.
Anthony Robinson, CEO
arobinson@forestnet.com
Tim Cox, Editor timcox@forestnet.com
the logging and lumber segment of the forest industry in the Western United States with emphasis on the states of AK, WA, OR, ID, MT and CA, providing current information on timber harvesting techniques, sawmill operations, news, legislation, events, people and products pertinent to this market.
TIMBERWEST (USPS #024858) is published bi-monthly
WA, 98020. Periodicals postage paid at Edmonds, WA and at additional mailing offices. Copyright 2023. All rights reserved. Subscription rates to qualified subscribers are Free and all non-qualified subscriptions in U.S. are $22
The Oregon Board of Forestry voted 4-3 to approve the Habitat Conservation Plan, moving it forward for federal approval. The plan would scale back logging on 640,000 acres of state forests while seeking to protect endangered wildlife.
Before the meeting, log truck drivers –their rigs loaded with wood from Oregon state forests – and loggers, legislators, mill workers and others rallied outside the state Department of Forestry headquarters, calling on the board to reject the plan.
The Habitat Conservation Plan will shut down 57 percent of timber harvesting on the state’s forests for the next 70 years, which would lead to a loss of $35-$53 million in annual state revenue, according to opponents.
Tasha Webb with Oregon Natural Resource Industries said the lost revenue will impact counties and smaller tax districts and services like emergency response, school districts, and law enforcement.
“This is going to devastate small towns and schools and sheriff’s departments,” said Webb. “There’s 250 people and organizations on that list, so it’s going to be bad. Places like the north coast are heavily reliant on timber dollars. This is going to bring them to their knees.”
The Association pf Western Pulp And Paper Workers also released a statement saying the plan disregards the livelihoods of thousands of people and overlooks the sustainable forest management and economic stability in rural communities.
The plan is designed to bring western Oregon’s forests into alignment with the federal Endangered Species Act, preserving habitat for at least 17 threatened or endangered species.
Washington
Environmental organizations, led by the Vancouver Audubon Society, have started legal action against Washington, alleging negligence in safeguarding the habitat of the endangered western gray squirrel.
They filed a lawsuit in Clark County Superior Court accusing the state Department of Natural Resources and Public Lands Commissioner Hilary Franz of failing to designate critical habitats for the squirrel following its endangered status reclassification in November.
The western gray squirrel has been in steady decline due to urban development, wildfire damage, invasive species, and direct human impacts. The lawsuit emphasizes the species’ dire state, estimating that less than 1,500 of the squirrels remain in Washington.
The plaintiffs seek a court order to compel the Department of Natural Resources to comply with its duty to designate critical habitats.
The suit’s outcome could set a precedent for how endangered species are protected in Washington, influencing conservation efforts and forest practices statewide.
Roseburg Forest Products will permanently close its particleboard mill in Missoula, Montana, in May. The plant, which has manufactured particleboard for decades, employs about 150 workers.
The particleboard plant was built in 1969, and Oregon-based Roseburg purchased it from Louisiana-Pacific in 2003.
In announcing the closure, Roseburg said it is the "final step in the company’s strategic
plan to exit the particleboard manufacturing business and focus resources on other product segments, including medium-density fiberboard, engineered wood, plywood, and lumber."
“The decision to permanently close a plant is always difficult,” said Roseburg president and CEO Stuart Gray. “It is especially difficult with our Missoula operation as we complete our exit from the particleboard marketplace. Unfortunately, Missoula’s older platform and technology is simply not competitive from a cost structure perspective in a marketplace with many new, modern particleboard facilities."
"We know this closure will have a significant impact on our team members (in Missoula)," Gray continued. "And thus, our primary objective with this closure is to assist them through this transition as smoothly as possible.”
The company recently announced a $700 million investment in manufacturing in Oregon, including a new plant. It is also building a new lumber mill in North Carolina.
Montana Fish, Wildlife & Parks has notified the U.S. Fish and Wildlife Service that it plans to pursue legal action over the recent listing of wolverines as a threatened species.
Wolverines inhabit much, if not all, of available habitat, according to Quentin Kujala, chief of conservation policy for the state agency.
“We work closely with our neighboring states to ensure the continued conservation of these iconic species,” said Kujala. “Federal protections in this case will only get in the way of good conservation work.”
(continued on page 8)
The FireBox S330 has tons of advantages that grinding and hauling can’t match. It consumes just 3 gallons of diesel fuel an hour, compared to grinding, which guzzles 30 gallons. The S330 eliminates wood waste for as little as $5 a ton versus the typical $63 to $73. You’ll reduce fuel costs plus save on maintenance, hauling, and landfill tipping fees.
*Scan the code to learn the numbers
(continued from page 6)
In its listing notice, the federal agency switched course by identifying the Lower 48 states as a distinct population segment. This finding comes after it previously found the population of wolverines in the Lower 48 was connected to those in Canada. The finding came despite protections in Canada and states such as Montana to ensure wolverine conservation.
The Cascade-Siskiyou National Monument, a remote expanse of wilderness along the California-Oregon border, will not lose any of its acreage after the U.S. Supreme Court declined to take up two challenges to its expansion.
Logging interests and several counties in Oregon had asked the high court to strike down a 2017 addition to the monument. Their lawsuit claimed President Barack Obama improperly made the designation because Congress had previously set aside the land for timber harvests. By gaining monument status, the area won special protections, including a prohibition on logging.
The challenges to the expansion raised the additional, and broader, question of whether the president’s authority to create national monuments unilaterally under the Antiquities Act should be restricted. Critics of the 1906 law, who have commonly opposed bids for new designations, have argued it gives too much power to the executive branch. The Supreme Court decided not to address the issue.
The Cascade-Siskiyou National Monu-
ment was created in 2000 to protect what is considered an ecologically valuable juncture of the ancient Siskiyou Mountains and the younger volcanic Cascades. The monument was expanded by about 48,000 acres seven years ago.
The petitions against the monument’s expansion were filed by the American Forest Resource Council, a coalition of Oregon counties, and the Murphy Company, a timber supplier.
They argued that the Antiquities Act couldn’t trump federal regulation to preserve timber harvests on Oregon and California Railroad Revested Lands, known as O&C Lands. The federal lands were originally devoted to building a railroad between San Francisco and Portland but were later conveyed back to the government with conditions.
Oregon legislators began the short session in February hoping to fill gaps in wildfire funding, with three bills to address landowner wildfire protection fees, home hardening, wildfire prevention and response, and survivor compensation.
However, those proposals failed. Only one – which ensures that wildfire survivors do not need to pay state income tax on compensation and settlements from losses – passed the Legislature with unanimous votes in the House and Senate.
Experts say the lack of more, sustained funding means the state will continue to face larger, more expensive fires without reliable funding, including the 2024 wildfire season, which is expected to begin in a few months.
“The whole issue of funding for the fire reality that we have nowadays is still unresolved, and it leaves the Oregon Department of Forestry in a financially precarious position,” said Jim Kelly, chair
of the state Board of Forestry, which oversees the forestry department. “Even if we have a normal fire season, they’re going to be running out of money and running to the Emergency Board, which is a poor way to manage all of this.”
The proposals aimed at reducing landowner wildfire fees and finding new sources of wildfire funding from Oregon taxpayers or the timber industry and came in response to the Legislature in 2023 cutting funding to state fire agencies by 40 percent. The state’s general fund, which had been drawn on heavily for wildfire agency funding in recent years, had too many competing priorities, lawmakers said. The fees that landowners pay for protection went up in response – for some as much as 40 percent.
The federal government struggles to respond effectively after wildfires rage through communities, according to the
investigative arm of Congress.
In testimony to the Senate Homeland Security and Governmental Affairs Committee, the Government Accountability Office said recovering from wildfires is more complex than bouncing back from floods, hurricanes and other disasters. Federal officials must rethink how they coordinate efforts on housing and other challenges.
The GAO's director of homeland security and justice, Christopher Currie, said programs at the Federal Emergency Management Agency and the Department of Housing and Urban Development fall short in part because wildfires are different from other disasters and need both immediate and longterm assistance.
Sen. Mitt Romney (R-Utah) said he's been "astounded" to see as much as twothirds of trees dead in some Utah forests, with the federal government unable to salvage many of them for timber or other uses before they deteriorate.
THE
FOREST RESOURCE COUNCIL (AFRC) is urging the Pacific Northwest’s Congressional delegation to address challenges to the region’s forestry and wood products industry.
In a letter to the delegation, AFRC president Travis Joseph noted that western Oregon has experienced the closure or curtailment of three wood product mills since the beginning of the year. In addition, more closures and curtailments in the Pacific Northwest are likely. The common thread is a diminishing timber supply for manufacturers of wood products.
“All three western Oregon mills that announced closures or curtailments this year are surrounded by some of the most productive public forestland in the country,” said Joseph. “All three mills purchase and rely on public timber to operate and sustain workforces. All three mills cited the lack of timber supply as a significant factor in the decision to close or curtail operations.”
The region’s forestry and wood products industry supports more than 150,000 private sector jobs in Oregon and Washington and provides critical infrastructure for the federal government to improve forest health, reduce
wildfire risks on federal lands, and help meet growing demand for carbon friendly wood products.
Joseph’s letter highlights several factors contributing to this wood supply crisis. These factors include the aftermath of the 2020 Oregon Labor Day fires that decimated a vast swath of timberland, reducing timber availability for decades into the future. Additionally, legislative and policy changes, such as the Oregon Private Forest Accord and state forest management plans in Oregon and Washington, are further reducing the supply of raw material to these mills.
“In plain terms, log prices are driven by supply and demand,” noted Joseph. “In the Pacific Northwest, current milling demand for logs, driven by public demand for wood products, is higher than current and projected log supply. Either regional log supply needs to increase to meet public demand, or the Pacific Northwest will experience additional mill closures and losses in critical workforce.”
The demand for raw material can be met by responsible management of forests in the Pacific Northwest “or this demand will be met in other parts of the U.S., and from
countries that do not share our social and environmental values,” said Joseph.
Millions of acres of federal forestlands are at imminent risk from catastrophic wildfires, insects, and disease, according to Joseph. They are forests in desperate need of science-based, active management and restoration.
However, forest management depends on the existing and remaining forestry and wood products industry, including modern and efficient mills, loggers and forestry contractors, truck drivers and equipment operators, and the vast supply chains the industry supports.
Congress has responded by providing $6 billion to the U.S. Forest Service and Bureau of Land Management through the Bipartisan Infrastructure Law and Inflation Reduction Act to accelerate the pace and scale of treatments to remove hazardous fuels loads, improve forest health and resiliency, and to protect communities, property, infrastructure, and public health.
The Forest Service also proposed in its 2022 Wildfire Crisis Strategy the ambitious goal of treating an additional 20 million acres of National Forest System land over the ensuing decade.
System designed by Corvalis Tool and utilizing a specialty USNR carriage and bandmill (shown) cuts beams and columns. USNR also developed a press for curing scarf joints and supplied an edger.
Freres Lumber successfully adapted over the years to changing market conditions, reinventing itself to move forward instead of succumbing to market shifts that might have left it withering on the vine.
Its latest adaptation was the result of developing an entirely new wood product for the building industry – mass ply panels (MPP). It manufactures mass ply building components with the aid of equipment developed and supplied by some of the leading machinery suppliers to the wood products industry.
“We’ve always been about reinventing our business and innovating when adversity hits,” said Kylel Freres, vice president of operations. “That’s what we did back in the 40s and 50s, when we switched from lumber production to veneer.” The veneer was supplied to plywood makers. The company made another transition when the industry developed laminated veneer lumber (LVL), supplying veneer production to manufacturers of LVL. To make better use of downfall material that didn’t make stress grades for LVL, Freres Lumber purchased a plywood plant and began operating it.
“There’s risk involved with a new product,” added Freres. “We look at it as: How can we stay relevant for the next 100 years?”
The company was started by his grandfather, who cleared land for farmers and had a small portable sawmill that he moved with a steam donkey. It marked its 100th year in 2022. With its focus now on mass ply, the company rebranded that year, changing its name from Freres Lumber to Freres Engineered Wood.
Freres Engineered Wood is familyowned. Kyle’s cousin, Rob Freres, heads the company as president. Kyle and his brother, Tyler, manage the day-to-day operations.
The company uses 100 percent of the wood processed throughout its three entities: Freres Engineered Wood Products, Freres Timber, and Evergreen BioPower. Its operations employ nearly 500 people. Freres Timber owns more than 17,000 acres of timberland and harvests that timber on a sustained yield basis. Evergreen BioPower is a biomass cogeneration plant; it uses residual wood products for fuel to produce steamgenerated electricity for more than 5,000 households and heat for plant production processes.
The company is headquartered in Lyons, Oregon. It has six plants at three locations within less than 10 miles of each other. The
(continued on page 14)
(continued from page 13)
oldest and primary mills produce veneer, and the company also has veneer drying operations. It operates a small stud mill, a plywood mill where about half the company’s employees work, and the mass ply mill, which employs about 20 workers.
In 2015 market challenges were impacting the company’s operations for both plywood and stress graded veneer. At the same time, the Freres team knew their supply of Douglas Fir exhibited superior strength properties for a softwood.
Plywood and commodity sheathing products have come under a lot of pressure from substitute products like oriented strand board (OSB), noted Freres. OSB mills in the South have captured a share of the plywood market, and imports from Brazil now make up about 15 percent of the U.S. plywood market, according to Freres.
“We weren’t getting the value in the market…If we can explore markets that can truly use a strong wood fiber from the Northwest Douglas fir…that’s what we really wanted to focus on as opposed to bottom feeding Brazil and other producers.”
The brothers began researching cross laminated timber (CLT) that year. In Europe, CLT and mass timber was designed to
replace steel and concrete in high-rise building construction. They traveled to Germany with others in the management team and a group from Oregon State University and toured some CLT plants. “We couldn’t justify using that much wood,” said Freres.
“We looked at everything through a veneer lens,” explained Freres. In other words, “How can we potentially use our existing operations to develop a veneer-based product.”
Their research included meeting Gerhard Schickhofer in Austria, who’s PhD research on CLT in 1994 laid the groundwork for its development in Europe. They discussed their idea for developing mass ply panels from veneer. “He thought there was an opportunity there,” said Freres.
The company was no stranger to the engineered wood industry. It has been supplying veneer to companies that use it to manufacture LVL (Laminated Veneer Lumber) since the 1980s.
The Freres team did some aggressive research and development and made some mass ply panels, partnering with OSU faculty on initial design and testing. They quickly decided to move forward, breaking ground on a new plant in 2017 and manufacturing the first mass ply panels the following year.
The Freres did nothing short of develop a completely new type of engineered wood product: mass ply panels (MPP). They have patented MPP in the U.S., Canada,
Australia, and New Zealand. The company has continued to work with a number of universities for other types of testing. For example, Clemson University conducted tests to determine if MPP could withstand hurricane force winds.
Although its name may suggest otherwise, mass ply is not composed of sheets of plywood. Rather, it is composed of 1-inch layers of structural composite lumber (SCL), a veneer-based engineered wood product, certified under ASTM D5456. Unique SCL layups allow the mass timber panel to be constructed with stability across both axes of the panel.
Freres Engineered Wood has engineered MPP to enhance the natural strength of the wood while adding dimensional stability. Panels can be constructed with a combination of cross-grain and long-grain components. It can be processed to required specifications; floor, roof and wall panels can be manufactured as large as nearly 12 feet wide, 48 feet long, and 12 inches thick.
Mass ply can be used for any mass timber application, including floor, roof and wall panels. Mass ply is strong and fire-resistant, making it an acceptable building material up to 18 stories. It is also lighter, more economical, and more environmentally sustainable
than traditional building materials such as concrete and steel. Mass ply uses about 20 percent less wood than CLT and is as strong as other SCL products.
One of the benefits of veneer manufacturing is that it recovers more wood fiber than traditional lumber manufacturing and the process of breaking down a log. In addition, veneer manufacturing is ideally suited for taking advantage of small logs that are being harvested to restore forest health and mitigate wildfires. The small logs have little defects, small knots, and tight grain. Veneer also is easier to dry than lumber, noted Freres. A sheet of veneer can be dried to target moisture levels in as little as six to 12 minutes.
The Freres launched into mass ply panel production with a capital investment of $30-35 million that has since grown to $45 million. The 175,000-square-foot mass ply plant is “already too small,” said Freres.
He compared the process of making MPP to finger jointing. “It’s similar. We lay out blanks at the plywood mill and scarf them together to make an LVL product.” They are assembled in lengths of 32 to 48 feet, either 4 feet wide or using 2-foot wide material. The material is run through a
(continued on page 16)
(continued from page 15)
sander and stacked in preparation for laying up larger panels.
For the scarf line the company turned to local manufacturers for the design and equipment. The scarf line benefitted from working mainly with two Oregon companies, Corvallis Tool and PRE-TEC. Corvallis Tool, which develops machinery for wood products manufacturers, supplied the scarf
cutting head, conveyors, and a lamella traveling cut-off saw. PRE-TEC, which specializes in automation solutions, supplied scarf cutting robots and a robotic panel feeder. Washington-based USNR, a leading machinery supplier to the forest products industry, developed a new press for curing the scarf joints and also supplied an edger. Other suppliers that provided machine centers or material handling equipment included ApQuip, West Coast Industrial, and Costa Sanders.
The finished panels are assembled much like lamellas – think engineered flooring. The materials are glued and pressed together, assembled like bricks, spanning the edge joints, in thicknesses ranging from 2 inches to 12 inches. The MPP layup operations were designed and equipped by Stiles Machinery, a Michigan-based company that had relationships with European machinery manufacturers whose equipment could be modified. One of the key machines in the manufacturing process is the press. It was supplied by Minda, a specialty equipment manufacturer. Stiles and Minda supplied other equipment for the press line, and the glue system was provided by Oest.
After the panels are bonded they go to a special CNC machine that uses both saws and router bits to cut openings for doors, windows, plumbing and electrical service, and for connections to other panels. “The CNCs are incredibly accurate,” noted Freres, within 1/16-inch. (The company was expected to install a new SCM Group CNC machine in February.)
Finished panels are essentially a custom product. “Nothing goes through the plant unless we have orders,” said Freres. Panels may vary by length as well as cut-outs for doors and windows and other modifications. “We never know until a project design.”
Freres Engineered Wood has added the capability to manufacture beams and columns up to 24 inches thick, known as mass ply lams, allowing it to supply more components for a building project. For beams and columns, the material is processed by a system designed by Corvalis Tool and utilizing a specialty USNR carriage and bandmill. Corvallis Tool supplied a beam ‘flipper’ and material handling equipment, and Wellsaw provided a precision end trim saw.
The specialty carriage was an interesting challenge, noted Freres: how to break down a piece of engineered wood as large as old growth timber. “We’re talking about taking technology that’s been around for 100 years and repurposing it for advanced engineered wood products.” The carriage had to be redesigned to handle a rectangular piece of wood instead of a round log. The project also necessitated the redesign of various handling equipment. “USNR was a great partner,” said Freres.
“The carriage and bandmill have really expanded the range of products we can produce. Now we can process material that is 24 inches thick. We can produce columns that are 24 inches thick and almost 48 inches wide. That is a substantial piece of wood that we would never have been able to process without the new equipment.”
The lion’s share of the company’s revenues come from sales of veneer and plywood,
followed by MPP and lumber. Veneer is still the company’s primary product by volume. About 30-50 percent is supplied to the company’s own plywood mill, mainly to make ‘blanks’ for MPP production. The remainder is sold to various markets.
The company is still in the lumber business to a small degree. The process of peeling logs for veneer leaves a core about 3 inches in diameter or a little larger. The cores are processed in batches by a Hewsaw to 2x3, 2x4, and other dimension lumber. The Hewsaw also is used to process scragg logs under 6 inches in diameter. The 2x material is sold green.
A large majority of MPP sales are along the West Coast. However, the company also has shipped panels to Texas, Florida, the Northeast, and Canada. Freres supplied 10-inch by 14-inch MPP columns that were used to construct a 19-story building in Oakland, California – the tallest wood building to date. Some have even been shipped to Saudi Arabia for construction of blast-proof structures.
“MPP is growing in market share,” said Freres. “It’s a growing market for us. We look at it as a growth opportunity.”
Tim Rude, owner of Rude Logging, has done almost every kind of logging, from shovel logging to tethered logging. He started with a chainsaw and a skidder and has
done just about everything except helicopter logging. It’s this versatility and ability to adapt with the times that has kept him busy for the last 25 years.
Rude grew up in Grant County and has lived there most of his life. His company is located in Prairie City, which is in a remote area of east-central Oregon.
Rude Logging is fairly self-sufficient for the most part. “I know many logging companies that depend on dealers and their mechanics, and other outside people to keep their business running,” said Rude. “Where we live, we’re isolated, and that is not an option.”
Rude Logging has to be ready to tackle
Tim Rude invested in this Kobelco and Tractionline winch tethering system (above and right) in 2022, purchasing it from Feenaughty Machinery. He added the Tractionline system to increase production on steep terrain.
anything in order to keep working. They are set up to handle just about any kind of breakdown, from machine work to in-framing truck engines.
“Keeping a great crew is very important,” said Rude. “We have several employees that have been with us for many years. Many are like family to us. Trying to keep morale up and treating them well has helped us stay strong in this day and age.”
The company’s fleet of equipment includes three Tigercat feller bunchers: models LX-830E, LS-855E, and LX830D. For
tethering machines working on steep terrain the company has a Tractionline winch system on a Kobelco 350LC-10 excavator.
Getting the wood to the landing is done with three Cat 525 grapple skidders and three Cat track skidders. Processing is done with two Link-Belt machines (4040 and LX240) and a 2954D John Deere swing machine, all matched with Waratah heads. The company also has three loaders for handling, sorting, and stacking logs and loading trucks:
(continued on page 20)
(continued from page 19)
two Link-Belt 210 loaders and a Link-Belt 4040. Rude Logging also is equipped with an assortment of road-building equipment: Kobelco, Link-Belt, and Kubota excavators and two Cat motor graders. The company has five log trucks and five lowboy trailers.
Overall, the equipment consists of newer models. Rude added two of the Tigercat feller bunchers (the LX-830E with a hot saw and the LS-855E with a felling head) last year; they replaced an older feller buncher. He bought the Tigercat machines from the Triad Machinery dealership in Prineville, which is about 20-plus miles east of Bend.
He’s become a believer in Tigercat. “The main thing is the reliability and low down time with the machine,” said Rude. “The company will go beyond ordinary measures to stand behind their product.”
He also invested in the Kobelco and Tractionline winch tethering system in 2022, purchasing it from Feenaughty Machinery.
(continued on page 22)
Rude Logging has three Link-Belt machines for handling, sorting, stacking, and loading logs. Two more Link-Belt machines are used for processing.
(continued from page 20)
ogy,” he said. “It was operator friendly, and the two-line system seemed to be potentially safer.
Derrick Hough, a sales rep for Feenaughty, said Rude thought the winch system to tether equipment on steep ground “could be fruitful.” Rude purchased a Kobelco-Tractionline combination that
Feenaughty had in stock.
“He’s a forward-thinking, productionbased guy,” said Hough. “Hard-working son of a gun. Always been fair and honest with me.”
“Aimee, his wife, has been outstanding to work with as well,” he added. “Tim and Aimee are as good as they come – in my book.”
Rude bases his selection of equipment on the track record of each brand, the dealer relationship, and their availability. Due to his company’s isolated location, strong support from a dealer is an extremely important factor in his decisions about equipment.
Rude Logging has 25 employees, including five truck drivers, two office workers, and a mechanic. The company operates several crews, with each crew consisting of four to six workers.
Rude Logging works primarily in eastern Oregon and southern Washington. The company does mostly thinning although it does some clear cut final harvests in western Oregon. The company usually operates 2-3 crews, each one working on a separate job.
Rude buys standing timber. Most jobs are federal timber sales, performing select cuts or thinning. Slash is left onsite and burned by the U.S. Forest Service on most sales.
Rude occasionally buys timber on private land, but it is getting harder to find.
Jobs vary in size from 40-60 acres to several thousand acres. Currently most of the wood being produced is saw logs. “The amount of pulp/fiber logs varies on the market,” noted Rude. Some federal timber sales require harvesting some pulp, usually 10-20 percent. “Most private jobs, it does not pay to remove it.”
There are three national forests in the region: the Malheur, Umatilla, and WallowaWhitman. At the time Rude talked with TimberWest, the new Tigercat LX830E was working on a federal timber sale, harvesting Douglas fir, white fir, and Ponderosa pine. Logs from the job were being hauled to mills for Woodgrain Inc., Boise Cascade, and Prairie Wood Products. The job will involve some steep slope logging in the future.
Depending on the job, the average haul is 75 to 100 miles to a mill. In addition to the five company trucks, Rude relies on 8-10 contract truckers to deliver logs to mills.
After graduating from high school Rude worked for an uncle who had a logging business. Then he earned a two year degree in welding and worked as a mechanic for another logging company. Just three years later – 25 years ago – he started his own company
with a used skidder he bought from a retired logger and a chainsaw. He hired a couple of men and operated as a small business for a couple of years. He met and married Aimee, now his partner in the business and the office manager, and a year later won a big contract with a major timber company in western Oregon. The company grew from four men to 30 employees.
When the recession hit in 2008-09, Rude focused on working in eastern Oregon. Initially forced to downsize somewhat, the company quickly staffed up to about two dozen-plus employees.
In current market conditions, the best prices are for Douglas fir, which Rude supplies to a Boise Cascade plywood mill. Ponderosa pine and white fir aren’t in high demand, and neither is pulp.
Like other logging contractors, Rude is battling rising costs from inflation. “Whether it’s inflation or lack of availability, the price of everything has gone up,” he said, “so our daily costs have increased.”
Rude Logging was the recipient of a merit award from the Oregon Department of Forestry in 2023 for its work on a steep slope site. The company used tethered logging operations while protecting a fishbearing stream.
“In challenging harvesting sites, they have shown extraordinary care and diligence to protect resources and meet landowner objectives,” Josh Barnard, the department’s forest resources division chief, said in announcing the award. “We’re proud to recognize the community spirit and leadership these operators have shown.
Rude and his wife run the business together. She has managed the company’s office for 20 years. She is a member of Oregon Women in Timber and also is a volunteer and executive board member of a local nonprofit organization. They have a 24-year-old daughter, Jozie, who is in the Army National Guard.
Rude’s father, Robbie, worked in the mill industry most of his life. He even .worked for Rude briefly when mills slowed down.
Rude keeps a pretty full schedule. He checks on jobs, prepares bids, reviews contracts. He also purchases parts and helps with or oversees equipment repairs.
Rude is on the executive board of Associated Oregon Loggers and also serves on the Grant County natural resource advisory committee. “We try to support where we are from,” he said. “In this small community we feel like it is very important.” Rude said.
WEST
Loggers got an opportunity to witness tethered timber harvesting up close as three manufacturers of winch-assist technology demonstrated their equipment in West Virginia
The three-day event was held in early March on the West Virginia University Research Forest in Bruceton Mills in northeast West Virginia, about 100 miles south of Pittsburgh, Pennsylvania.
It was organized by Patrick Donnelly, West Virginia University Extension safety and health research assistant for the Timber Safe grant program.
“Tethered and winch-assist steep slope logging keeps all employees in the protected cab of a machine,” noted Donnelly. The logging method greatly reduces the risk of being injured by falling limbs and trees, he added, and enables harvesting of timber that previously may have been inaccessible. “With advancements in technology, this type of logging is making its way into the
Eastern hardwood forests.”
The idea for the event actually came from Jerry Sisler, a logger from western Maryland and a member of the Mountain Loggers Group, which is made up of loggers from West Virginia, Maryland, and Pennsylvania. Sisler said, “ ‘We need to do something about this,’ ” Donnelly recounted.
Sisler, a fourth generation logger, is the owner-operator of Sisler Construction and Logging, also known as SC&L. Although he lives in nearby western Maryland, where his business is based, most of his work is in West Virginia. Sisler halted his company’s logging operations for several days and donated labor and equipment to put in skid trails and landings for the demo.
The first day was cold and breezy, with morning temperatures in the 20s. In fact, the area had been under a winter storm advisory the day before, although it only received a scant dusting of snow.
The research forest is virtually all hardwoods, and Donnelly estimated 90 percent of the timber at the demo site was red oak.
After maneuvering machinery and equipment from the staging area to the actual
demo site, the first demo got underway on day one with Falcon Forestry Equipment. The company’s winch system, added to a modified excavator, tethered a track harvester that began working down a slope of about 70 percent. The harvester, using a hot saw, felled trees and topped them and bunched them in preparation for a skidder, working its way down the slope.
Falcon Forestry Equipment was followed by TimberMAX USA, which demonstrated a winch assist system attached to an excavator that was maneuvered into position. The TimberMAX winch was tethered to a skidder that followed the same path and began skidding logs up the slope. A second skidder picked up the logs at the summit and skidded them to a landing to be processed.
Falcon Forestry Equipment demonstrated this winch system at the West Virginia event. It is tethered to the harvester that is just beginning to work its way down the slope.
Finally, an Ecoforst T-WINCH was maneuvered into position at another location very nearby. The T-WINCH is self-propelled on tracks and is operated by remote control. It followed another track harvester to the other site and was quickly placed into position and tethered to the other machine.
(continued on page 26)
Timbermax USA demonstrated a winch assist system attached to an excavator. The Timbermax winch is shown tethered to a skidder as it begins its descent down the incline.
(continued from page 25)
The harvester, also equipped with a hot saw, began working down the slope much like the first one, felling, topping and bunching, while remaining safely tethered to the T-WINCH.
Representatives of all three manufacturers were on hand to field questions from loggers and discuss the equipment.
Donnelly knows of only three contractors in West Virginia who do tethered logging.
All three are located in the southern part of the state.
Mechanized logging was not embraced in West Virginia until the late 1990s, noted Sisler. Even now, a significant amount of logging is done by manual labor, felling trees by hand with chainsaws – notably in steep terrain. It is getting harder and harder to find men who want to do the work, so the industry is ripe for using tethered equipment, he suggested. It is more productive, more efficient, and safer.
Donnelly estimated that 50-75 percent of logging in West Virginia is done on steep terrain. Most of that work is done felling the timber by hand and skidding the logs with grapple skidders or cable skidders.
The participants got together for a safety meeting and briefing each morning, with coffee and doughnuts, and were transported via vans to the demo site, about five minutes away. After being dropped off at a staging site, they had a short hike down a skid trail to the demo area. Loggers also were treated to lunch each day of the event.
The event drew not only loggers from West Virginia but representatives of other contracting firms, including pipeline construction businesses, and suppliers as far away as Georgia and Colorado.
Sponsors of the event included Ecoforst, makes of T-Winch, TimberMAX USA, Falcon Forestry Equipment, Summit Attachments, Appalachian Winching Systems, Anderson Equipment, Kleis Equipment, Leslie Equipment, Newlons International Sales, Ricer Equipment, and Weyerhaeuser.
As word spread about plans for the event, it quickly snowballed and picked up interest and support from suppliers and others, including TimberWest, which developed a website to help promote the demo. “It was a small beginning that blew up very quickly,” said Donnelly.
“This was brand new for us,” said Donnelly. “Already people are asking about next year.”
When Dan Kloppman was 16 and started working summers and
Kloppman’s son, Noah, uses the crane to begin loading the company’s Rottne Rapid forwarder. Noah primarily operates the forwarder although he is learning to run other equipment.
foothills of Oregon’s Coast Range. His tree farm is an example of how private landowners can be adversely impacted by Oregon’s new Private Forest Accord Initiative.
Nichols Logging is based in Rainier, Oregon, which is bordered on the north by the Columbia River some 50 miles north of Portland and 50 miles east of the Pacific Ocean. The region is part of the largest temperate rainforest system in the world, stretching from Northern California to British Columbia. Northwest Oregon averages 54 inches of rain a year and has abundant forests of Douglas fir, Western red cedar, Sitka spruce, Western hemlock, and alder.
Kloppman offers a wide variety of
services, although he specializes in cut-tolength logging.
He takes pride in operating all of his own equipment, and he’s teaching his son to do the same. When he was looking to hire during the pandemic, he found all the good workers were too busy, and some loggers went out of business, so he purchased his own feller buncher and is learning how to operate it himself.
Kloppman has a fondness for Rottne cut-to-length logging equipment, which is manufactured in Sweden. Rottne, which manufactures harvesters, forwarders, and harvester attachments, has one dealer in the Pacific Northwest: Precision Machinery in Eugene, Oregon. Kloppman owns a Rottne SMV EGS harvester and a Rottne Rapid
forwarder. He has been favorably impressed by the machine quality and the fact that they require little maintenance. “I would love to add a new pair of Rottnes,” he said.
He recently purchased a used TimberKing TK1162 track feller buncher with a Waratah harvester attachment to work on steep terrain and in big timber. Kloppman usually operates the Rottne harvester or the TimberKing feller buncher. His son usually operates the Rottne Rapid forwarder and is also learning how to run the other equipment. The company also has a Timberjack 450C dual arch cable-grapple skidder. A Cat bulldozer is used for building roads and excavating on five gravel pits on Kloppman’s land, and he
(continued on page 30)
Kloppman purchased this used TimberKing TK1162 track feller buncher with a Waratah harvester attachment mainly to work on steep terrain and in big timber.
(continued from page 29)
also has an Allis-Chalmers wheel loader working in the gravel pits.
Kloppman likes the Rottne forwarder both because of the high quality and because he can do many repairs himself. “The tech support is there for the complex electronics,” he added.
Casey Ferguson, one of the owners of Precision Machinery, said his dealership would go broke if they had to rely on keeping Kloppman supplied with Rottne parts. Kloppman maintains the machines so well that they last a long time, he said.
Precision Machinery is a dealer for Rottne, Eltec, and the Ecoforst T-Winch line. The company signed an agreement last year to become the exclusive dealer in the Western U.S. for Eltec, which manufactures harvesters, feller bunchers, shovel loggers and log loaders. Precision Machinery also represents Quadco, Southstar, and LogMax forestry attachments.
LVF Machines, under the operation of Long View Forest in Hartland, Vermont, is the U.S. distributor of Rottne equipment. It recently opened a facility in Portland, Oregon. In addition to Precision Machinery, Rottne is represented by other dealers in the Great Lakes, Northeast, and Canada.
A member of Associated Oregon Loggers and the Oregon Small Woodlands Association, Kloppman harvests nearly 400,000 board feet of timber annually on his property and about another 100,000 board feet on other private forests. He mainly thins stands with timber that is 20-48 years old. “I have targeted the smaller landowner just because this type of equipment is generally not available to them,” he said, “and I’m just not interested in competing with the big boys.”
Most mills he supplies are located within about a 50-mile drive. They include RSG Forest Products in Mist, Stimson Lumber in Forest Grove and Clatskanie, and Interfor in Longview, Washington. Kloppman contracts Dale Witham and Teevin Brothers Trucking in
Rainier and Dass Trucking out of Vernonia.
Roger Nichols founded Nichols Logging in the Portland area in 1951. He cleared land for college campuses, using horses, cutting and selling 10-foot stakes for railroad cars. He bought 200 acres of land about 15 miles from Rainier in 1963.
“When this part of the county’s timberland was developed, the big guys bought the high country, and the smaller outfits like Roger’s bought the lower,” said Kloppman. “The place was primarily grass land that he planted to forest.
Nichols had a heart to help people in foreign countries suffering from natural disasters and military conflicts. He and his wife, Lynn, started a program called Teen Trees, using profits from making alder poles to buy goods for needy people abroad and sending them in shipping containers. To help them do that, they contracted with the former Comprehensive Employment and Training Act program for young workers, and Teen Trees and CETA shared the cost of hiring and training young workers.
In 1983, 16-year-old Kloppman was one of those workers. He was ‘adopted’ by the Nicholses two years later. “In high school, I was learning to work with metals in class as a career, and now those welding classes are serving me well in the woods,” Kloppman said.
“At Teen Trees I was made a full-time foreman, working with the high school and college kids,” Kloppman recalled, “and I led individual teams under him. We did about everything, including cutting alder sticks and poles with machetes and chainsaws and delivering them to the aluminum plant across the river in Longview, Washington. In addition, I helped gather, ship, and distribute the containers, which meant over the years I got to travel to 24 different countries.”
Kloppman’s two sons, Daniel and Noah, have worked for him. However, Daniel, the eldest, “let me know from the start that he didn’t want it as a career.” Noah has worked with him for two years “and loves the work.”
When Kloppman talks about the future, his outlook loses some enthusiasm, thanks to the onset of Oregon’s new Private Forest Accord Initiative, which took effect this year. The program has negatively impacted nearly 20 percent of his tree farm. The initiative bans any logging activity on land within 110 feet of the large, fish-bearing Clatskanie River, from the high water mark on both sides of the river, which runs for two miles through the middle of Kloppman’s property
When you add the width of the stream, it becomes a 255-foot-wide, two-mile-long swath through his land that cannot be logged, although Kloppman must continue to pay taxes on it. “The 90-acres of 30- to
100-year-old Douglas fir that has been taken away represents about a $2 million loss of revenue for me,” he said.
Kloppman testified against the initiative during the regulatory process. “We should be compensated for our loss,” added Kloppman, “and there was supposed to be a plan to do that by last July, but we haven’t heard from that either.”
“We were given one year to remove what we could,” said Kloppman, “with the caveat that we had to go through and mark each tree with a number, measure it, record how much the basal area is, and target the ones
to remove from the Riparian Management Areas (RMA).” Kloppman had to turn down work for regular clients last year in order to devote all his time to salvaging what he could on his own land.
The covid pandemic negatively affected the availability of other logging contractors and truckers, so Kloppman and his son have done most of the work on his land, hand felling since some of the timber is 90-plus years old.
Kloppman has contracted with Steve
(continued on page 32)
(continued from page 31)
Berg and Berlog Inc. to help harvest big timber. He also has contracted with Ramos Reforestation for nearly 30 years. “We have had excellent results with them, probably 98-plus percent survival rate. They also do young plantation thinnings and competitive brush cutting around seedlings.”
“We used to run the cut-to-length nine months out of the year…for other landowners, and the rest of the time worked on our own property – logging, thinning, road building, reforestation, maintaining equipment.”
This year Kloppman expects to be able to resume doing cut-to-length logging for small landowners who are on long-standing contracts. That will be an opportunity for him to further train his son and for Noah to gain more experience. “He is the future of the company and the tree farm,” said Kloppman.
Kloppman still travels as a disaster relief volunteer with his church to places like Peru and Mexico. Between working and volunteer trips, he doesn’t do much vacationing.
“This year is going to be different though,” he said. He and his wife, Angie, made a trip to Hawaii in February to celebrate their 30th wedding anniversary.
Equipped with independent air-ride suspension and remotecontrolled front and rear hydraulic locks. A single operator can attach the transport dolly in minutes.
The patent-pending PT Tech Hydraulic Torque Limiter provides the ultimate driveline protection while allowing for ease of setting adjustments based on the grinding application.
Whether you are processing organic waste into compost, hog fuel, or mulch, the Nex Gen 6400XT Wood Hog Horizontal Grinder delivers more efficiency, versatility, power, durability, and now greater transportablity to keep pace with you. To learn more about the 6400XT with Dolly Transport System contact your local, authorized Morbark Dealer or scan the QR Code below.
Scan the QR Code with your mobile camera to access specs for the 6400XT with Dolly System
The 6400XT Hydraulic Belt Tensioning System, uses hydraulic pressure to tension the belt as soon as the engine starts, eliminating the need for adjusting the belt manually.
The Extended Maintenance Platform is designed to provide ample working space and easy access to the hammermill for changing screens and conducting maintenance.
Brandt Tractor: Serving All Canadian Provinces
Ph: +1 888.227-2638
www.brandt.ca
Pape Machinery: Serving Idaho, Oregon, Washington, California, and Nevada
Ph: 458-221-3156
www.pape.com
This year’s conference included a lineup of speakers who talked on steep slope logging regulations and other topics. Keynote speaker was U.S. Forest Service chief Randy Moore.
Loggers certainly were welcome at the 8th annual Oregon Logging Conference. The event drew a record number of industry professionals in February.
(continued on page 36)
(continued from page 34)
a dialogue between the Forest Service and those impacted by the agency’s decisions.
“We need to aggressively step into the partnerships that (Moore) laid out and hold the Forest Service accountable to work with the logging industry to save our forests,” said
Topics of current interest were the subjects of seminars and panel discussions. Many of those attending earned Professional Logger credits to stay certified and up to date on several issues. Subjects addressed included scaling and quality of lesser log species, steep slope logging, updates of the Private Forest Accord, the Washington Forest Practices Act, and how to influence unelected boards and commissions.
“The Oregon Logging Conference was packed with unique opportunities for forestry and natural resource professionals to network and learn more about their trades,” said conference manager Rikki Wellman.
More than 860 high school students and teachers from nearly three dozen schools attended the 6th annual Future Forestry Workers Career Day, held in conjunction with the conference. Industry professionals at this hands-on event provided students with information and the tools they need for entering the logging, forestry, heavy equipment operation, diesel mechanics, wildland firefighting and other related fields. Students learned about both current and future job opportunities. A forestry skills relay was included in the event. Students from high school forestry clubs competed in activities such as cable splicing, choker setting, crosscut and single buck sawing, compass and pacing, and more.
The log loader competition attracted 18 participants. The contestants demonstrated their skill, speed, and efficiency while operating a Link-Belt log loader. They had seven minutes to stack log blocks end-to-end, matching numbers or colors on predetermined marks on the ground.
(continued on page 38)
(continued from page 36)
The winner was Zane Bryant, owner of Bryant Logging; he claimed the top spot with a time of 3:09:98. Second place was Bryant Logging shovel operator Jeremy Staats with a time of 3:12:25. Third place went to Chuck Walker with a time of 3:32:94.
The Talk About Trees dinner-auction was a huge success with a sellout crowd of 480 people. It raised $143,000 to help support the Oregon Women in Timber Talk About Trees forest education program, which is of fered free to pre-Kindergarten through 8th grade students.
More than $28,000 was raised at auctions to benefit the Oregon Logging Conference Foundation scholarship program. Also, a fundraising dessert function collected more than $20,000 to benefit Paws Assisting Veterans, an organization that provides trained service dogs to veterans.
The Oregon Logging Conference is a significant boost to the local Eugene economy. Figures were not immediately available for the impact this year. However, last year the conference contributed nearly $9 million to the local economy. The figure was expected to be higher this year based on increased participation and attendance at the conference.
A number of forestry industry suppliers exhibited new products at the Oregon Logging Conference or made announcements coinciding with the event.
Triad Machinery debuted the Tigercat LS857 shovel logger. Based on the popular and successful 855E platform, the LS857 shovel logger represents a reimagining by Tigercat designers of what a steep slope carrier should look like.
The Tigercat LS857 shovel logger has more leveling capability, superior cable management in winch assisted applications, and a series of design enhancements, including increased boom lift and improvements to service access. The switch to in-tank hydraulic filters improves filtration and extends service intervals, and the shape of the fuel tank increases usable volume.
The LS857 exhibited at the OLC was equipped with Tigercat’s new live heel feller-director boom set. The new boom system has nearly 36 feet of reach, a live heel for added utility, and the versatile, highly productive 5195 directional felling saw pinned to the end of it.
Peterson Cat showcased a new Weiler M860 mulcher with a factory-installed 825 mulching head. Building on the Cat 586C site prep tractor, the Weiler M860 features a Cat C9.3B Tier 4 Final engine that generates 375 hp and a 113 gpm hydraulic pump. It can cut through trees up to 16 inches in diameter or clear a path more than 8 feet wide in one pass.
Dyna Products exhibited the new SC-16 Rapid Split firewood processor, which features an automatic cycle for increased productivity. The company also implemented robust safety measures, including interlocks that prevent the plunger from engaging when doors are open.
The log deck was redesigned to accommodate 4-foot logs on two deck arms and
8-foot logs on three deck arms. The engine was rotated 180 degrees, facilitating easier maintenance.
The SC-16 Rapid Split also introduces two standard vertical wedge holders, simplifying wedge accessibility and enhancing operational convenience. A new 4.3-inch LCD engine control panel features an intuitive interface for enhanced control and monitoring, and the panel features an emergency stop feature.
Wallingford’s announced a new partnership with HSP Gripen, a Swedish manufacturer of forestry grapples. Gripen grapples feature end position dampening standard on all models and a unique globe design. They provide the highest degree of filling with soft rolling and smooth releases, preventing clutter and allowing operators to focus on the next load.
Hoffman Boots displayed its new Grizzly boot. It features a stout 10-inch upper, carbon finish on the outside leather, and a waterproof membrane. The Grizzly, the newest addition to the Hoffman Boots line of outdoor boots, is available with a Vibram or calk sole.
FAE announced a partnership with Papé Machinery to bring its premium land clearing, construction, and agriculture equipment to more customers in the Pacific Northwest. Papé Machinery, a leading supplier of equipment for forestry and other industries, will sell FAE tracked carriers and attachments in Oregon, Washington, Northern Idaho, Nevada, and Hawaii. FAE tracked carriers with mulching attachments, like the PT300, already are used widely in the West, particularly for wildfire prevention.
Sennebogen, the German manufacturer of material handling equipment, including machines for handling, sorting, and loading and unloading logs at the landing and the mill, was notable for its large exhibit at this year’s OLC.
In just over 30 years in business, Tigercat Industries has shipped its 30,000th machine.
Tigercat began in 1992 with one product, little dealer representation, and produced just a handful of machines. Since then the company has grown steadily, expanding both its production capacity and product breadth.
Tigercat debuted the 726 feller buncher in 1992 at a forestry equipment show in Georgia. Within three years it was offering two drive-to-tree feller bunchers, two track feller bunchers, and two bunching shear models with distribution in Canada and the U.S. By 1997 Tigercat had a full product line to offer dealers in the U.S. South with the addition of a knuckleboom loader and the industry’s first successful, serial production hydrostatic skidder.
Since then the company has developed equipment for steep slope harvesting, vegetation management, and cut-to-length logging.
In recent years Tigercat launched a new brand, TCi, and put the TCi badge on its first dozer. The company also has developed a line of material processing products for chipping and grinding.
Tigercat is currently building an additional manufacturing facility. When complete the company will have over 1.4 million square feet of manufacturing capacity. It has over 160 dealer locations in 25 countries along with an extensive factory support network.
Rotochopper, a leading manufacturer of horizontal grinders, shredders, and screening equipment, held its annual Rotochopper University training program recently at the company’s manufacturing facility in St. Martin, Minnesota, for owners and
The comprehensive two-day class offers participants a deep dive into equipment operation best practices, preventative maintenance techniques, and troubleshooting strategies.
Attendees were treated to a range of activities, including a facility tour, handson demonstrations, and ample networking opportunities.
This year’s curriculum focused on crucial topics such as proper machine feeding, preventative maintenance procedures, and troubleshooting methodologies. Highlights from the hands-on demonstrations included instruction on installing main rotor bearings and adjusting sheave and tensioning the drive belt on Rotochopper grinders.
Nearly 60 people participated in the event representing companies from around the world.
“Rotochopper University continues to be an event that provides great benefits to our customers,” said Adam Asmus, Rotochopper service manager. “The connections made with our service team and fellow operators will undoubtedly benefit their operations for years to come.”
North America’s top 10 softwood lumber firms can produce 36.9 billion board feet of lumber and represent 49 percent of total North American capacity. Several of these companies closed facilities or reduced production in 2023.
West Fraser, the largest softwood lumber producer in North America at 7.0 billion board feet of capacity, slightly increased capacity in 2023 with the purchase of the Spray Lake sawmill in Cochrane, Alberta, to offset the closing of its sawmill in Perry, Florida.
OrePac Building Products, a wholesale supplier of interior and exterior building materials, and Western Timber Products, a specialty wood products manufacturer, announced a definitive agreement for OrePac to purchase the Western Timber business. The transaction was expected to be finalized in April.
The acquisition is a strategic addition to OrePac’s diverse assortment of products and services.
“Having worked with Western Timber Products for some time, I admire and appreciate the hard work and care of the team, which shows in the quality of the products they produce,” said Brad Hart, president and CEO of OrePac. “This investment supports our goal of bringing the industry more custom value-added products and services, with the speed and agility that makes OrePac a preferred source.”
Western Timber Products, headquartered in Coeur d’ Alene, Idaho, has produced a variety of high-quality decking, siding, and trim from their mills in Weiser and Council, Idaho since 1983. OrePac plans to expand and bolster those offerings even further.
Dan Seid, owner and president of Western Timber Products adds, wil stay on with the business to assist in the transition.
OrePac, based in Wilsonville, Oregon, is a family-owned and operated business, founded by the Hart family in 1977. It oper ates 10 locations across the western U.S.
. For more information, visit www. orepac.com.
After providing jobs to the Seeley Lake, Montana, community for 75 years, Pyramid Mountain Lumber will shut down operations this spring.
Company officials cited labor shortages, lack of housing, unprecedented rising costs, plummeting lumber prices, and the cost of living in western Montana as crippling Pyramid’s ability to operate.
The management group and board of directors worked on many of these issues for years to find a way to address them. Despite their best efforts, they see no way out of this current situation.
Pyramid will cut off logs on March 31, run the log inventory through the sawmill and surface, and sell all lumber before auctioning the mill equipment.
Mattracks, the inventor and manufacturer of the original rubber track conversion system, is observing its 30th year in business.
Designed, patented and released to the public in 1994 by Glen Brazier with inspiration from his then-11-year old son, Matt, Mattracks grew into the first rubber track conversion product of its kind and eventually into an entire industry surrounding it.
The original Mattracks model was built exclusively for full-sized pickups, transforming them into a dual-purpose machine. One huge advantage of the company’s revolutionary track design remains the “conversion” aspect, allowing the vehicle user to conveniently switch from tires to tracks or vice versa in less than an hour.
The Mattracks product line has experienced significant growth and continual innovation with over 170 different models. Mattracks rubber track conversion systems are manufactured for virtually any multiaxle vehicle including ATVs, UTVs, SUVs, trucks, heavy-duty agricultural and construction equipment.
Headquartered in Karlstad, Minnesota, Mattracks has hundreds of thousands of satisfied customers located across 150 countries and all seven continents.
On a winter afternoon in the Southeastern U.S., a truck driver had just arrived at the reload yard to transfer a load of crossties on rail cars for transport to a treatment facility. The crossties were processed from mixed hardwood logs and were approximately 8 feet, 6 inches long and by 7-8 inches in width. Each crosstie bundle was stacked five wide and four high. Weather was not a determining factor. The driver had served less than one year in his position at the time of the accident.
loads and unloads trucks, and the com pany always adheres to a safety practice of placing the forklift between the load and the truck driver during the unbinding process.
The driver ignored existing safety protocols for unbinding cargo and failed to recognize that the pack strapping was loose, thereby creating a fall hazard during the unloading process.
The driver began to unbind his fully loaded trailer of crossties, beginning with the binding straps at the front of the trailer. He failed to notice that a polyester strap that initially bound the top pack of crossties to the pack underneath was no longer in place.
The reload yard operator typically
As the yard operator exited his office and headed toward the loaded truck, he heard crossties falling from the far side of the truck and hitting the pavement. He heard the driver yell and found him lying on the pavement underneath three crossties: one across his head, one across his chest, and the third across his waist.
The injured driver was conscious and alert. The yard operator physically removed the crossties and called 911. The responding emergency medical service personnel transported the injured driver to a local hospital. He was subsequently transferred to a larger regional hospital.
A post-accident investigation and review of security camera video footage revealed that all packs of crossties
had a polyester strap completely around them when they initially were loaded on the trailer. It was theorized that the crossties may have shifted during the loading process, causing the polyester strap to become loose. Vibrations and wind pressure while traveling at highway speeds likely exacerbated the problem, eventually pulling the polyester strapping from the buckles.
The driver suffered multiple internal and external injuries and was hospitalized for an extended period of time.
• Always follow existing safety protocols to avoid injury while unbinding a load.
• Always check for loose binding straps and perform a visual inspection to see if cargo has shifted during transport.
• Double strap bundles and tie a knot to prevent polyester straps from backing out of buckles.
(Source: Forest Resources Association (FRA), a national advocacy organization representing the entire wood supply chain. Visit them at www.forestresources.org.)
Tigercat has introduced a mulching head for swing carriers in response to fire mitigation equipment requirements in western North America.
The new mulching head is designed to mount on a Tigercat LX830E carrier. This machine can tackle steep slopes and operate within dense stands to reduce build-up of woody debris as a mitigation measure to guard against wildfires.
The new Tigercat 4161-15 mulching head has a 59-inch mulching swath, 130degree wrist pivot, and a pin-on rake for added utility. Like all Tigercat mulching heads, it is strength-to-weight optimized and fitted with large bearings.
Many of the components, including the bearings, sprockets, seals and timing belt, are common to the Tigercat 4061 series mulching heads and so are field-proven. Hydraulic hoses are routed through the open tip boom into the top of the wrist, providing excellent protection. The replaceable wear liner is field serviceable, and removable covers allow easy access to all service points.
For more information, visit www.tigercat.com.
FAE has enhanced the versatility of its RCU55 and RCU75 remote controlled tracked carriers with the introduction of its new SCL/RCU55 and SCL/RCU75 stump cutters.
The new SCL/RCU is ideal for removing stumps in forests and parks, on roadsides, by riverbanks, or in farm settings.
Compact and easy to handle, the SCL/ RCU line features a heavy-duty shredding disc to tackle the most stubborn stumps and roots up to 45 cm deep for the SCL/RCU55 and up to 50 cm deep for the SCL/RCU75.
The SCL/RCU’s direct drive motor minimizes maintenance and makes it possible to have an extremely compact machine body. Hydraulic and proportional swing controls allow operators, while stationary, to swing the unit back and forth to grind larger material.
For more information, visit www.faegroup.com.
Johnson Controls launched the ANSUL® N-101 Clean Agent Vehicle Fire Suppression System. The system is specially designed to protect energized electrical equipment inside unoccupied electrical cabinets onboard heavy industrial vehicles.
Using a naturally occurring zero-global warming potential (0 GWP) nitrogen agent, the ANSUL® N-101 system provides a sustainable and electrically non-conductive fire suppression solution for Class C and E vehicle hazards in mining, forestry, heavy construction and other industries.
The dependable, compliant ANSUL® N-101 suppression solution leaves no residue or by-products. This means it will not cause damage to the protected electrical assets nor require clean-up because of discharge, making it a better option for people, equipment and the planet.
With an operational range of minus 65 F to 210 F, a simplified single-tank, singlenozzle design and heavy-gauge steel bracket construction, the system is engineered to withstand the harsh conditions found in rugged industrial environments. The system’s nitrogen cartridge is equipped with an electric-pneumatic actuator and is available in two sizes to support a wide range of vehicle applications.
For more information, visit ansul.com.
WarBird Protection Group launched its cutting-edge INTREPID line of hearing protection products—lightweight, rugged, comfortable, feature-rich electronic ear muffs.
Designed and developed to exceed expectations on the jobsite, shooting range, garden or in the workshop, the Intrepid line of ear muffs provide the premium protection and hearing enhancement technology that professionals and hobbyists alike demand.
WarBird’s new Intrepid hearing protection lineup includes the all-new Intrepid, Intrepid RC and the flagship ear muff, the Intrepid BT. Designed from the ground up to offer features that professionals demand, there is an Intrepid ear muff to fit just about everyone’s needs.
The Intrepid is the most affordable electronic hearing protection WarBird has to offer, providing protection in demanding environments without sacrificing comfort or function. For those seeking quality electronic hearing protection with digital Sound Active Compression, comfortable foam ear cushions, full dynamic range HD speakers and AAA battery power, the Intrepid checks all those boxes with a competitive price tag.
For more information, visit www.warbirdpro.com.
Tigercat has introduced its fifth harvesting head, the three-wheel drive 573.
The company demonstrated the new attachment processing logs on a Tigercat 875E logger at the Pacific Logging Congress Live In-Woods Show in Washington last fall. Since then Tigercat has field tested multiple units from Alberta to Australia and the results are in. The 573 is a high performing, reliable head for roadside processing and harvesting, according to Tigercat.
The Tigercat 573 head is best suited for medium and large tree profiles. Maximum cut capacity is 31 inches, and optimal performance is in timber 16-24 inches in diameter. The feed rollers close down to 2.4 inches, allowing the 573 to smoothly delimb and process smaller diameter trees and thus achieve higher value fiber recovery.
The compact frame design deftly handles poor stem form and contributes to tidy delimbing performance. The triangulated feed wheel arm configuration operates in locked three-wheel drive. This, combined with timed knife arms, provide the operator with fast picking and positive stem control for high productivity in roadside processing
(continued on page 44)
(continued from page 42)
applications. Independently mounted, trailing-arm length measuring ensures reliable tracking and accuracy.
The top knife and lower/back knife pivot on the same side of the chassis frame, aligning the position and flow of each stem centrally through the head. This arrangement promotes positive contact with all three feed rollers and the measuring wheel at all times. The result is better quality and accuracy, reduced fuel consumption, and greater processing speed. The orientation also provides the operator with a clear sightline to the measuring wheel.
The 573 is standard equipped with continuous rotation for ease of use and superior hose routing and protection. Quick, stable
WiFi connectivity between the cab and attachment modules reduces wire routing along the boom and provides excellent command response.
For more information, visit www.tigercat.com.
Loftness has expanded its line of stump grinder attachments with the 24SG Stump Ax. Featuring a 24-inch cutting wheel, the new model is designed for use with low-flow skid steers and excavators.
Similar to the original Stump Ax for higher flow power units, the 24SG has a rigid mount, allowing operators to work quickly by simply repositioning the power
Associated Oregon Loggers recognized Rick Gibbons as the 2023 AOL Logger of the Year. Gibbons, co-owner of Allen & Gibbons Logging in Canyonville, received the award at the AOL’s annual convention.
Gibbons has made “outstanding contributions in Oregon to the association, industry, community, society, economy, business, workers, and/or family,” the organization said in recognizing him.
“This award acknowledges a leader who demonstrates admirable courage, initiative, dedication, or achievement in Oregon’s forest contract business.”
AOL president Tom Dober recognized Gibbons for his successful business as an owner-operator as well as a generous donor to the association.
Gibbons has served as an AOL leader for the past 23 years. In 2001 he was elected to the executive committee and served 12 years, and he was chair of the political action
committee for 18 years. He served as president of the organization in 2009–10.
Gibbons contributed to AOL conventions and board events and donated thousands of dollars to help fund the AOL’s federal political action committee.
The Oregon Logging Conference has announced its officers and staff for 2024-25.
Serving as president is Jayme Dumford of Thompson Tree Farms in Corvallis. First vice president is Mike McKibbin of Stimson Lumber Co. in Tillamook. Second vice president is Terry Mann of L & L Inc. in Sutherlin, and third vice president is Bodie Dowding of Pacific Fibre Products in Vancouver, Washington.
Serving as treasurer is Milt Moran of Cascade Lumber Consulting in Sweet Home.
Rikki Wellman of Eugene will continue in her role as manager of the OLC.
unit, rather than articulating the attachment itself. It also has an angled hitch and forward-reaching boom to provide superior visibility and control.
Visibility is further enhanced with Leonardi’s Phantom Wheel. This cutting wheel has cutouts, which create a see-through effect during operation. It is equipped with Tomahawk teeth, which offer some of the fastest grinding times in the industry.
Powered by a 110cc high-torque radial piston motor, the new Stump Ax is compatible with 17-35.9 gpm flow ranges and requires 30-80 hydraulic horsepower. It can be ordered with either a universal skid steer mount or a custom excavator mount.
For more information visit www.loftness.com.
The 2025 Oregon Logging Conference will be the 87th annual gathering and will take place Feb. 20-22 at the Lane Events Center and Fairgrounds in Eugene.
The board of directors of the Forest Resources Association named Tim O’Hara interim president. O’Hara succeeds Keith Gray, who resigned for personal reasons.
O’Hara joined the FRA staff as government affairs and Lake States region manager in 2018. He was promoted to vice president of government affairs in 2020, leading the association’s lobbying and policy efforts.
O’Hara’s policy expertise and deep knowledge of the industry will continue to serve FRA well, said board chairman Pete Stewart. “With 30 years of experience in the forest products industry, Tim brings a wealth of experience and expertise to FRA at an important time,” said Stewart.
“He has made a tremendous impact during his tenure at FRA to date,” said Stewart, “and we have no doubt he will continue this momentum as FRA’s interim president. The strength of our skilled association staff will allow FRA to continue to advance the critical policy and business issues we face.”
The association represents the interests of over 330 organizations and businesses in the forest products industry. Its members are represented in 49 states and include forest landowners, suppliers, consuming mills, associated businesses, and state forestry associations.
April 14-16
Western Wood Products Association Annual Meeting, Vancouver, WA 503-224-3930, www.wwpa.org
April 17-19
MSR Annual Workshop, Charlette, NC 608-310-6768, www.msrlumber.org
April 24-26
Olympic Logging Conference, Victoria, BC 360-202-7014
www.olympicloggingconference.com
April 29 - May 2
American Wood Protection Assoc. Annual Meeting, Portland, OR 205-733-4077, www.awpa.com
April 29 - May 1
Forest Resources Assoc. Annual Meeting, Nashville, TN 202-296-3937, www.forestresources.org
May 3-4
Loggers’ Expo at Champlain Valley Exposition, Essex Junction, VT 315-369-3078 www.northernlogger.com
May 3-4
Sequim
May 13-16
National Indian Timber Annual Symposium, Cherokee, NC 503-282-4296, www.itcnet.org
May 17-18
Montana Logging Association
45th Annual Meeting, Missoula, MT 406-752-3168, www.logging.org
June 4-6
Forest Products Society International Conference, Knoxville, TN 608-231-1361, www.forestprod.org
June 4-6
Sustainable Forestry Initiative
Annual Conf., Atlanta, GA 613-747-2454, www.sficonference.org
June 4-6
International Conference on Wood Adhesives, Knoxville, TN 706-443-1337, www.forestprod.org
June 22-25
Assoc. of Consulting Foresters of America National Conference, Ponte Vedra Beach, FL 703-548-0990, www.acf-foresters.org
June 25-27
Pellet Fuels Institute Annual Conference, Charleston, SC 703-522-6778, www.pelletheat.org
June 25-27
National Conference of Private Forest Landowners, Denver, CO 404-325-2954, www.forestlandowners.com
June 29-30
Buckley Log Show, Buckley, WA 360-829-0474
www.cityofbuckley.com/logshow
June 30-July 4
Sedro-Woolley Annual Logger Rodeo, Sedro-Woolley, WA 360-770-8452, www.loggerodeo.org
July 12-14
Amboy Territorial Days Logging Show, Amboy, WA
360-247-5101, www.tdays.org
July 12-14
South Fork Loggers Day Festival, South Fork, CO
719-873-5512, www.southfork.org
August 1-3
Lumberjack World Championships, Hayward, WI 715-634-2484
www.lumberjackworldchampionships.com
August 5-7
Association of Equipment Distributors (AED), Leadership Conference, Austin, TX 630-574-0650, www.aednet.org
August 8-11
Morton Loggers Annual Jubilee, Morton WA 360-523-4049, www.loggersjubilee.com
August 16-18
Woodsmen's Annual Field Days, Boonville, NY 315-942-4593
www.woodsmensfielddays.com
August 20-23
IWF 2024, International Woodworking Fair, Atlanta, GA 404-693-8333, www.iwfatlanta.com
I’D LIKE TO START with a ‘thank you’ to those of you taking the time to read this, and to keep you reading, I’ll share a quick joke that is pertinent to this topic. You’ll see why at the end.
A logger went to see his doctor. The doctor said, “Unfortunately, I have some bad news and some even worse news for you.” The logger nervously asked the doctor to give him the bad news first. “The bad news is you only have 24 hours to live.” The logger said, “What could possibly be worse than that?” The doctor said, “I should have told you yesterday.”
We’re going to take a look at two catastrophic Western wildfires, the 1933 Tillamook Fire that burned on the Oregon Coast, and the 2021 Dixie Fire that burned in Northern California.
The following short description of the Tillamook Fire comes from a 320-page book titled “Tillamook Burn Country: A Pictorial History.” It is a comprehensive documentation of one of America’s most horrific wildfires, written by Ellis Lucia.
The Tillamook burn raced through over 300,000 acres of mostly Douglas fir and was described this way by a reporter: “From the summit of the Coast Range to tidewater lines, it is simply one vast and dense forest. It is a forest area of the giant breed, with trees ranging from eight to 30 feet in circumference and reaching upward from 150-300 feet.” In August 1933, the Oregon coast weather was extreme, humidities dropped to record lows, and a bad fire that had been burning for several days “exploded with the ferocity of an H-bomb.” In 20 incredible hours, the Tillamook Fire “rampaged over 220,000 acres, burning fine trees at an astounding rate of 600,000 board feet an hour.”
What occurred on that burn-scarred landscape in the following decades was truly a “legacy of achievement” by citizens, foresters, and loggers. “The flames had hardly died and the embers cooled when foresters and loggers launched what was one of the great salvage efforts of all time.”
At the time, the entire burn area was privately owned. To get this burn salvaged and restored, private timber interests met with local, state, and federal officials, who all agreed to the formation of the huge Consolidated Timber Company. This was a bold cooperative
enterprise at a time when such things were considered sinful, “almost bordering on Communism.” Consolidated immediately spent $1.5 million for railroad construction, $800,000 for truck roads, and $1.25 million for locomotives, cars, and rolling stock.
The salvage and restoration began. When it was finished, 7.5 billion board feet of the estimated 10 billion board feet that had been killed had been salvaged and converted to lumber. Seventy-three million trees were planted with an additional 1 billion Douglas fir seeds dropped from helicopters.
Although a private undertaking, the U.S. Forest Service offered this advice and encouragement: “Measures to rehabilitate the burn should be taken, the cornerstones of which are intensive protection, hazard reduction, intensive salvage logging, and reforestation.” No environmental impact statement was written – the environmental impact spoke for itself.
Decades later, Ellis Lucia summarized the impact of the salvage and restoration work: “What once was a bleak, desolate land is again alive and beautiful.”
That was then; this is now.
The Dixie Fire started in the Feather River Canyon of northern California on July 13, 2021. When finally contained on October 25, the fire had burned through 963,000 acres of Sierra Nevada forests and became the most expensive wildfire suppression effort in U.S. history, costing $637.4 million. The fire damaged or destroyed several communities, including Greenville, Canyondam, and Warner Valley.
Two years have passed since the Dixie Fire was contained. Estimates of the total timber destroyed range from 10 to 12 billion board feet on private and public timber combined. The bulk of the private timber has been salvaged. Upwards of 10 billion board feet of public timber remains standing, most of it worthless as lumber at this point. Between 2021 and 2024, the Forest Service Dixie Fire salvage program is estimated to yield 64 million board feet or .64 percent of the burned timber. The Dixie Fire landscape is destined to rot, grow brush, and reburn.
There is no Ellis Lucia documenting the Dixie Fire story. The scenario that exists on the Dixie Fire today reflects the deterioration of forest management that has been quietly progressing through the Western
timber-producing states for over four decades, accelerating dramatically since the turn of this century. The extreme environmental groups are being allowed to ‘manage’ our forests by litigation.
The result is that grossly overcrowded forests rot from insect attacks and burn in catastrophic wildfires while America increasingly imports lumber from other countries. Consider these figures from the U.S. International Trade Commission: In 2020, the U.S. imported $44.6 billion of forest products; 16 percent of U.S. imports (over $7 billion) came from China, the country that is the leading importer of lumber in the world.
A logger sat before the California Legislature at a hearing called to discuss the condition of California’s forests. His testimony was quick and to the point. He told the chairman, “I have some bad news, and some even worse news for you.” The chairman asked the logger to tell the bad news first. “The bad news is that even though California is one-third forested, it now imports over 75 percent of its wood products. In 1985, California had 150 sawmills. Now, in 2023, only 27 sawmills remain.
The chairman replied, “I had no idea… What could possibly be worse than that?” The logger said, “We’ve been telling you this for over 50 years. Now America, with almost 780 million acres of forests, is the second leading importer of lumber in the world, only behind China.”
The joke I started with and the story of the logger both have bad news and then worse news. The difference is, the patient in the joke has no hope. He dies. For the logger, there is still some hope, but only if legislators and agencies recognize that time is getting short for our Western forests, and they must take bold action.
Like the legacy of the Tillamook Fire, our legacy needs to be one of achievement. The apathy of the Dixie Fire stands in the way.
(Mike Albrecht is president of the American Loggers Council and a past president of Associated California Loggers and the Sierra Cascade Logging Conference. He has a master’s degree in forestry from Duke University and is a Registered Professional Forester in California with more than 45 years of experience in forest management and the forest products industry.)