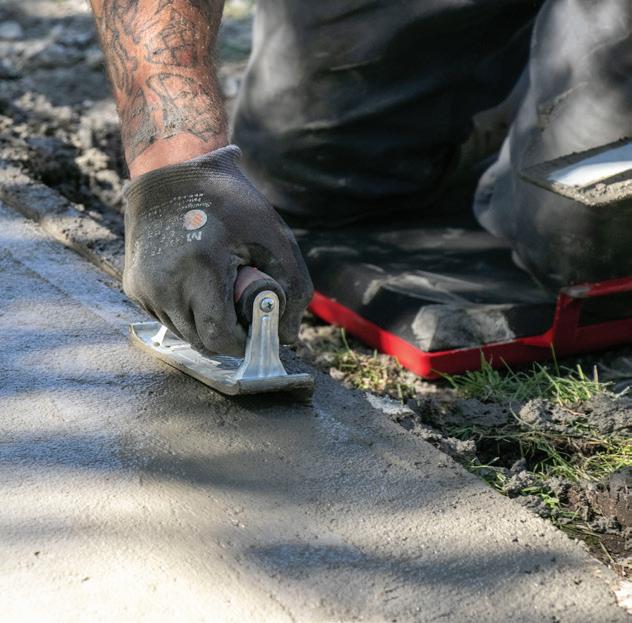
3 minute read
Zinc vs. Bronze Concrete Hand Tools
HAND TOOLS » BY MEGAN RACHUY
Photo Credit: MARSHALLTOWN Company
Bronze tools are the trusted means of achieving radius edges and straight control joints in concrete. Their rugged construction has the optimal weight distribution to provide professional quality results. For that reason, bronze tools are often fundamental for many concrete finishers. Yet this preference comes at a price. The monetary and human cost of bronze production is taking its toll on the industry, but it doesn’t have to. There is an alternative material available—zinc.
Although they differ in composition, bronze and zinc share similar properties. They rival each other in terms of hardness, durability, quality construction, and professional finish results. Zinc, however, has a few added perks.
Zinc production offers relief to the pocketbooks of contractors and manufacturers. For every bronze tool produced, two zinc tools can take its place. This results in less money wasted on tools that provide identical results. Plus, it’s safer for manufacturers to produce.
COMPOSITION & PROPERTIES
Bronze is an alloy of copper that has been in use for over 5,000 years. It is typically a combination of copper and tin, aluminum, or nickel (among others). Most concrete tools are 88-90% copper and 10-12% tin. This composition is great for tools due to its strength, hardness, and very high ductility. These properties also provide a high loadcarrying capacity, good wear resistance, and offer high durability. Unfortunately, it is also prone to corrosion.
With enough air exposure, a bronze tool can oxidize and turn green. This green layer, called patina, is often the first sign of wear. The patina can act as a protective barrier, but if chlorides are present (as from seawater, soil, or sweat), these tools can develop “bronze disease.” This is the death of a cuprous (copperbased) tool. It is a contact-contagious condition that works through the metal and destroys it. Once this happens, there is little chance to stop it. Zinc’s non-cuprous properties allows it to avoid this disease with a hexagonal closepacked crystal structure. It also possesses moderate hardness and can be made ductile and easily worked at temperatures slightly above the ambient. Side by side, bronze and zinc both have a hardness that is ideal for tools (on the Mohs Scale of Hardness for Metals, zinc = 2.5; bronze = 3).
THE COST OF PRODUCTION
The monetary and human cost of production is where bronze and zinc significantly diverge. Bronze production relies on two methods of production (sandcasting and die-casting), but neither are cost-effective for manufacturers. The result is manufacturers potentially passing this financial hardship onto contractors. Regardless of casting method, both involve grinding and deburring. This gives bronze tools their smooth, shelf- and job-ready finish creating dust that requires immediate filtration or ventilation. Without this, workers can develop a condition known as pneumoconiosis or “dusty lung,” a condition that causes scar tissue to build up in the lungs and can lead to chronic lung, liver, kidney, and even brain problems.
Because of these hazardous conditions, some U.S.-based manufacturers are no longer willing to put their workers at risk and ousourcing the job. But even those outsourced manufacturers are calling for an end to bronze production and the grinding involved.
With fewer manufacturers at home and abroad producing bronze, bronze tools will be harder to acquire, driving an increase to price.
Zinc production, on the other hand, doesn’t carry these same costs. This is due in part to the development of the rapid quenching zinc-lead blast furnace in the 1960s, which uses shock-cooling and vapor absorption to produce zinc. : • Low working temperatures lead to rapid cooling of the cast products and fast production for assembly. • More precise casting methods eliminate the need for grinding and deburring. It also helps to produce a better, smoother, and more crisp finish on the edges and control joints of concrete slabs. • Zinc suppliers are U.S.-based, lowering the cost of production and (subsequently) retail value.
Bronze and zinc share a high loadcarrying capacity and good wear resistance, ideal for concrete work, while zinc takes it a step further with immunity to bronze disease and a lighter, easier-to-use profile that provides contractors with similar results.
For concrete finishers, the difference between bronze and zinc is slim to none. Both provide concrete tools with a high load-carrying capacity, good wear resistance, and the ability to produce virtually identical finish results. Zinc just doesn’t carry all the same drawbacks—it’s lightweight, easy to use, resistant to bronze disease, and cost-effective.
Megan Rachuy is the content writer and editor for MARSHALLTOWN.
Adapted from
ForConstructionPros.com/ 21521651.
64 CONCRETE CONTRACTOR OCTOBER/NOVEMBER 2021 www.ForConstructionPros.com/Concrete