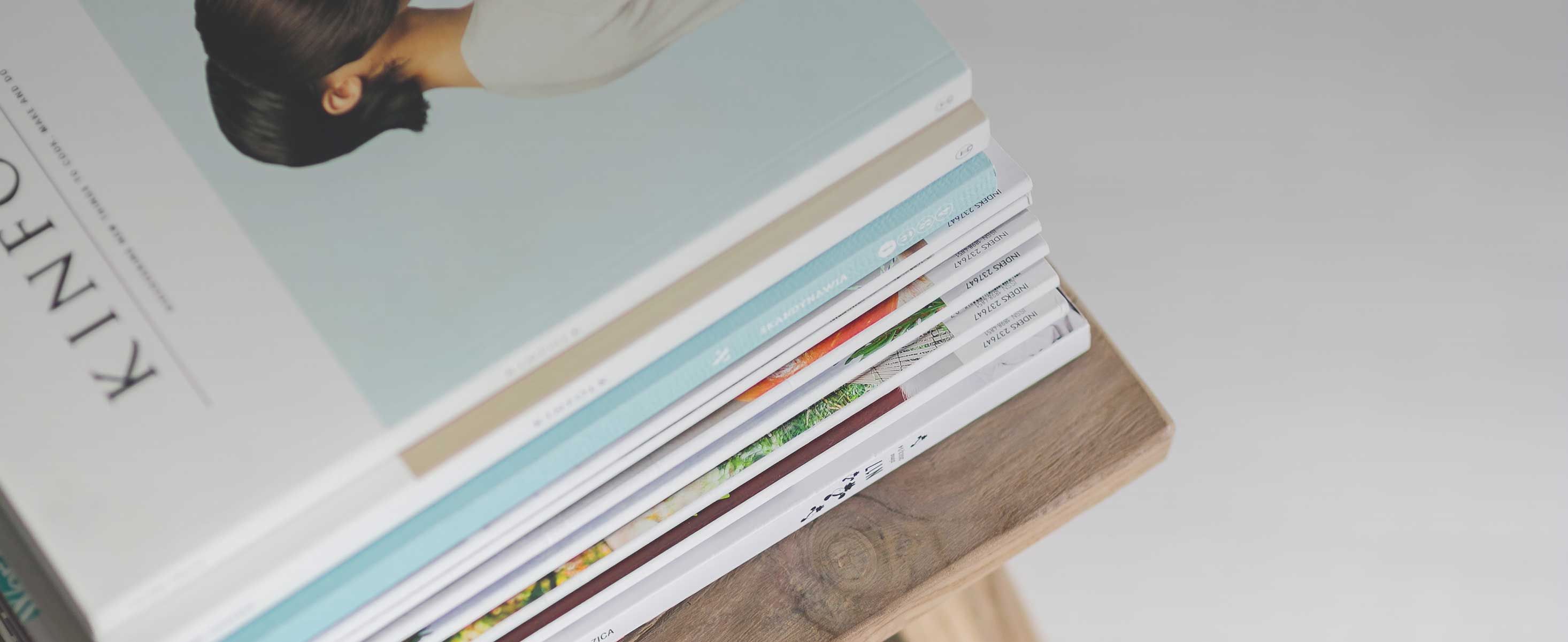
3 minute read
5 Tips for Applying Epoxy Coatings in Cold Weather
5Tips for Applying Epoxy Coatings in Cooler Temperatures
When epoxy resin and hardener are mixed together, a chemical reaction begins. The temperature of the surroundings, concrete, and epoxy mixture will affect the rate or speed of reaction, as well as the degree of cure. Warmer temperatures will accelerate this reaction, while colder temperatures slow it down.
1. WARM THE RESIN &
HARDENER BEFORE USE
To ensure a proper chemical reaction and promote optimal curing, warm the resin and hardener with heat lamps or keep them in a heated environment before use. If the epoxy is being used outdoors, a small, portable epoxy storage box can be built out of rigid sheets of foil-backed insulation, with a light bulb or an electric heating pad inside to maintain a temperature of 70-90° F. This will keep the warm resin and hardener near the work area and prevent the material from cooling off before it can be mixed and applied.
Keep the area heated during the epoxy’s full cure time. If the manufacturer’s literature says that the epoxy cure time is eight hours, assume that means eight hours at 70° F. If the substrate and environment temperature are lower, the cure time will be longer. As a general rule of thumb, for every 18° F drop in temperature below 70° F, the cure time doubles. Note: Unless specially formulated, most epoxies will never fully cure at below 50° F. Refer to the epoxy coating’s literature or contact the manufacturer for minimum recommendations. Then, ensure the coating environment stays at or above that temperature during application and for the entire curing period.
2. ENSURE PROPER MIX RATIO
It’s important to ensure that the resin and hardener are used in the proper mix ratio. Mixing off ratio can seriously compromise the epoxy’s ability to cure properly and achieve ultimate strength. The best practice is to mix the full kit of epoxy and to not attempt to break it down and mix smaller volumes.
The proper mix ratio depends on the product—another reason to carefully read the instructions. Many have a mix ratio of 1:1. However, mix ratios of 2:1, 3:1, and 4:1 are also common.
In some cases, the defects caused by off-ratio mixing are visually evident during application. The most apparent evidence is it not curing or reacting too quickly, causing cracks in the coating.
Other times, off-ratio mixes may have non-visual defects pertaining to the coating’s flexibility, chemical resistance, water-resistance, and hardness. For example, the coating could appear to be fine at first but could be easily scratched, discolor upon exposure to water or chemicals, or delaminate.
3. MIX RESIN & HARDENER
THOROUGHLY
The resin and hardener should be mixed together thoroughly and pre-mix parts A and B before combining. Then, mix them for approximately two minutes, minimum, with a slow speed drill and paddle mixer. Never mix by hand!
Scrape the sides and bottom during mixing. A smaller volume mixing vessel will improve the chemical activity because the limited surface area should hold heat better. For example, mix a two-gallon unit of epoxy in a threegallon container.
4. KEEP THE SURFACE &
ENVIRONMENT WARM
When applied to a warmer surface, the epoxy will thin out and flow much smoother and penetrate better, which will result in a stronger bond. If outside, construct curing tents around the area and use portable heaters or heat lamps. Note: Never use unvented open-flame heat sources, such as salamanders or catalytic heaters. The exhaust gases for these types of heaters can contaminate the surface, elevate moisture, and CO2 levels caused by the exhaust will affect the cure and ultimately lead to coating failure. Catalytic heaters do not appear to pose a problem unless used in a confined space, such as a curing tent or box.
5. CAREFULLY PREPARE
SURFACE BEFORE
RE-APPLICATION
A slower cure can allow an amine blush to form on the epoxy surface. The blush feels like a waxy film on the surface of the cured epoxy. If a second coat is necessary, before doing so, immediately wash the surface with warm water using a 3-M Scotchbrite pad. Before the water evaporates, dry the surface with clean, lint-free towels and sand any remaining glossy areas with medium-grit sandpaper. Remove all sanding residue before reapplication.
The application of epoxy primers must adapt to conditions.
The Euclid Chemical Company
Jennifer Crisman is director of marketing services at Euclid Chemical.
Adapted from ForConstruction-