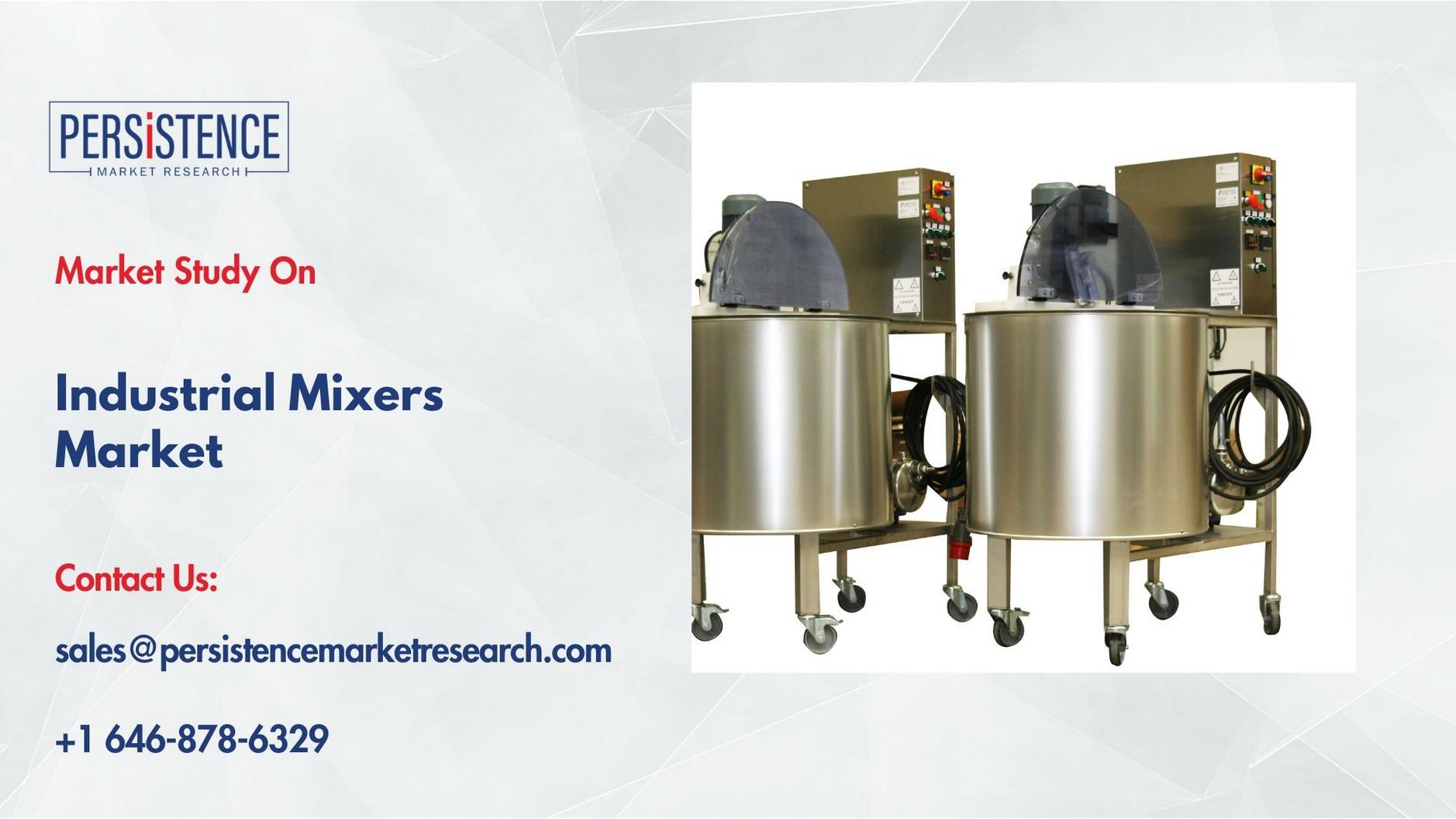
The industrial mixers market has become increasingly pivotal as industries across the globe seek more efficient and sustainable solutions for blending, mixing, and processing materials. These versatile pieces of equipment are used in a wide range of applications, including food and beverage production, pharmaceuticals, chemicals, cosmetics, and more. With advancements in technology and growing demand for high-quality, uniform products, the industrial mixers market is undergoing significant transformation. Understanding the latest trends and preparing for future developments in this industry can help businesses stay ahead of the competition and meet the evolving needs of their markets.
The global industrial mixers market size is projected to rise from US$ 2,839.4 Mn in 2025 to US$ 4,297.7 Mn by 2032. It is anticipated to witness a CAGR of 6.1% during the forecast period from 2025 to 2032. Highperformance industrial mixing equipment sales are expected to surge due to increasing focus on improving equipment adaptability, flow maximization, and production performance. Vendors are anticipated to provide innovative mixers with high sanitation levels as several industries are required to follow strict sanitary practices in their manufacturing processes.
1. Technological Advancements in Mixing Equipment
One of the most significant trends in the industrial mixers market is the ongoing development and integration of advanced technologies. Modern industrial mixers are being equipped with cutting-edge features that not only improve performance but also increase safety, energy efficiency, and ease of operation. These advancements include:
Automation and Smart Systems: Automation is becoming a key trend, particularly in industries like pharmaceuticals and chemicals where precision is critical. Smart industrial mixers that use sensors and real-time data monitoring are gaining traction. These systems ensure that mixing processes are optimized, reducing human error and increasing overall efficiency. Companies are now integrating their mixers with software that enables real-time monitoring of parameters like speed, temperature, and consistency, ensuring a high-quality product every time.
Energy-Efficient Models: As energy costs continue to rise and environmental sustainability becomes a priority, industrial mixers are being designed with greater energy efficiency in mind. Newer models feature energy-saving motors, improved blade designs, and optimized mixing mechanisms that consume less power while maintaining or even improving performance.
High-Performance Materials: The demand for mixers that can handle more challenging and complex materials is pushing manufacturers to invest in high-performance materials that can withstand the stress of mixing abrasive, high-viscosity, or corrosive substances. Stainless steel and other corrosion-resistant alloys are commonly used for their durability, especially in industries like food processing, pharmaceuticals, and chemicals.
2. Demand for Customization and Specialized Mixers
With the increasing complexity of products and materials, there is a growing demand for customized mixing solutions that cater to specific industry requirements. The need for mixers that can handle unique processes, such as delicate blending for food and beverage applications or the creation of complex chemical formulations, has led to the rise of specialized industrial mixers.
Manufacturers are increasingly offering customized solutions that are tailored to meet the unique specifications of their clients. Whether it's for small-batch production or high-volume manufacturing, these specialized mixers can be designed to provide precise control over factors like temperature, pressure, and speed. This trend is particularly strong in sectors such as pharmaceuticals, where exact formulations are critical for product safety and efficacy.
3. Sustainability and Green Manufacturing Practices
Sustainability is becoming a key driver in many industries, and the industrial mixers sector is no exception. As businesses face growing pressure to reduce their environmental footprint, they are increasingly
focusing on energy-efficient and environmentally friendly solutions. The move toward sustainable manufacturing practices is pushing the demand for mixers that offer:
Reduced Waste: New technologies in industrial mixers are helping to reduce waste by improving the consistency and yield of mixed products. These systems minimize the need for reprocessing and ensure that materials are used more efficiently.
Eco-friendly Materials and Coatings: The adoption of ecofriendly materials, such as biodegradable or recyclable components, is becoming more widespread. Some companies are incorporating environmentally friendly coatings to reduce the release of harmful chemicals into the environment, particularly in industries like food production and cosmetics.
Lower Carbon Footprints: The development of mixers that consume less energy, require fewer raw materials, and generate less heat has led to lower carbon footprints. Companies are also exploring the use of renewable energy sources in their manufacturing processes to meet sustainability goals and government regulations.
4. Integration of Industry 4.0 and IoT
Industry 4.0, characterized by the integration of digital technologies and automation, is another trend reshaping the industrial mixers market. The industrial internet of things (IoT) is enabling companies to enhance the capabilities of their mixers by connecting them to centralized monitoring and control systems. This integration offers several advantages:
Predictive Maintenance: IoT-enabled industrial mixers can be equipped with sensors that track the health of the equipment in real-time. By monitoring parameters like vibration, temperature, and wear, manufacturers can predict when a mixer will require maintenance, reducing downtime and preventing costly breakdowns.
Remote Monitoring and Control: The ability to monitor and control industrial mixers remotely is an attractive feature for companies looking to streamline operations. Operators can access real-time data from anywhere, enabling them to make adjustments or troubleshoot issues without being physically present on the production floor.
Data Analytics for Process Optimization: With Industry 4.0 technologies, manufacturers can gather valuable data from their
mixing processes and use analytics to optimize production. This can lead to better product quality, reduced energy consumption, and improved process efficiency.
5. Growth in Emerging Markets
As emerging economies continue to expand, particularly in regions such as Asia-Pacific, Africa, and Latin America, the demand for industrial mixers is expected to rise significantly. In Asia-Pacific, countries like China, India, and Southeast Asian nations are witnessing rapid industrialization, which is driving the need for efficient production equipment across various sectors, including chemicals, food processing, and pharmaceuticals.
With an expanding middle class, rising disposable incomes, and increasing urbanization, these regions are also seeing a higher demand for consumer goods, such as processed foods and personal care products. This is fueling the need for industrial mixers that can handle large-scale production while maintaining product quality and consistency.
Moreover, as the regulatory environment in these regions evolves to improve quality standards, manufacturers are adopting more sophisticated mixing technologies to comply with international norms. This is expected to drive market growth in emerging economies where the adoption of advanced manufacturing equipment is on the rise.
6. Challenges and Competitive Landscape
Despite the growing demand and opportunities in the industrial mixers market, businesses face several challenges. One of the primary hurdles is the high initial investment cost associated with purchasing and installing advanced mixing equipment. While the long-term benefits, such as increased efficiency and reduced operational costs, justify the investment, smaller businesses or startups may find it difficult to afford such equipment.
Additionally, as the market becomes more competitive, companies must focus on differentiation through innovation, quality, and customer service. This is leading to increased investment in R&D and partnerships between manufacturers and end-users to develop customized solutions that meet specific industry needs.
7. The Future of the Industrial Mixers Market
Looking ahead, the industrial mixers market is set to experience continued growth, driven by technological innovation, the demand for more sustainable and energy-efficient products, and the need for high-quality, customized mixing solutions. Manufacturers that embrace digital transformation, invest in smart technologies, and adopt environmentally
friendly practices will be better positioned to capitalize on market trends and meet the evolving demands of industries worldwide.
In conclusion, the industrial mixers market is evolving at a rapid pace, influenced by technological advancements, changing customer needs, and a growing emphasis on sustainability. As industries seek more efficient, reliable, and eco-friendly mixing solutions, the demand for state-of-the-art industrial mixers will continue to rise, offering opportunities for businesses to innovate and grow in a competitive marketplace.