The Benefits of Predictive Maintenance for Electric Forklift Fleets
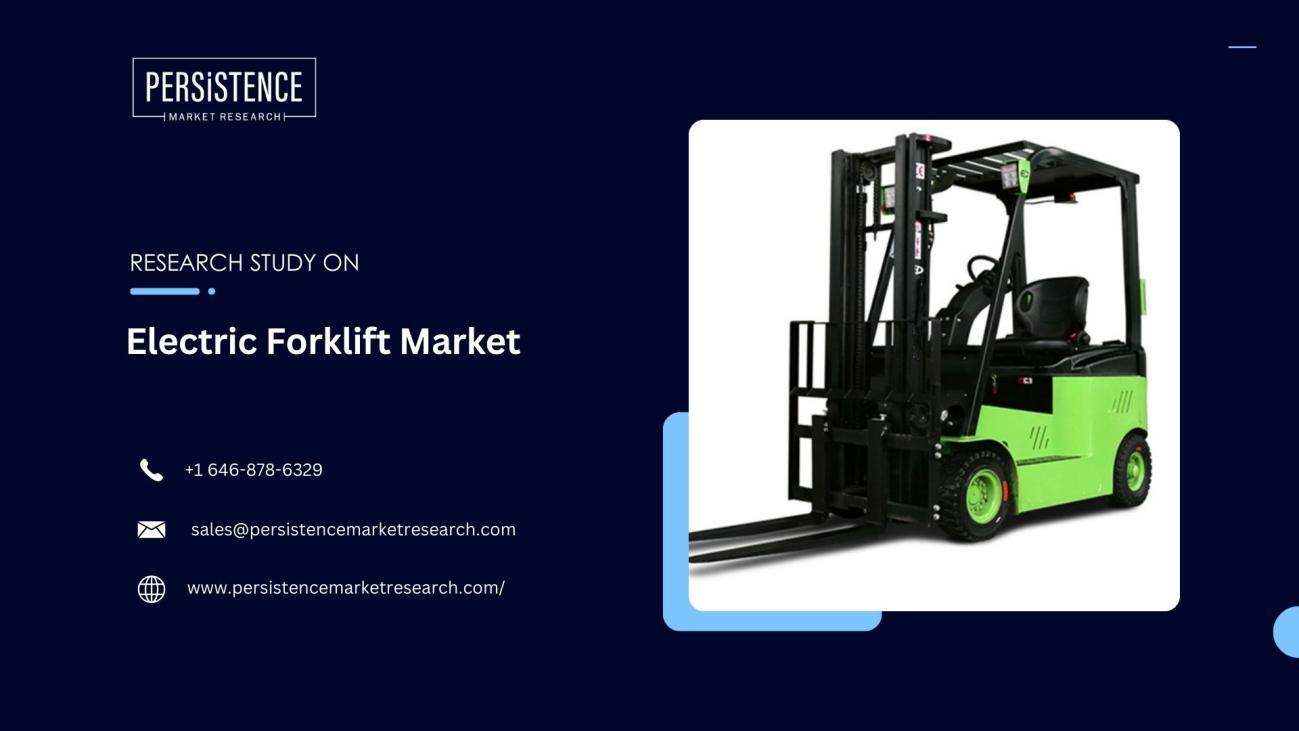
Electric forklifts are rapidly becoming the backbone of material handling operations across various industries. As businesses prioritize sustainability and operational efficiency, the adoption of electric forklifts continues to rise. However, with increasing reliance on these machines, maintaining their optimal performance is crucial. This is where predictive maintenance plays a vital role.
Predictive maintenance (PdM) leverages advanced technologies like IoT sensors, artificial intelligence (AI), and big data analytics to foresee equipment failures before they occur. This proactive approach ensures electric forklift fleets operate smoothly, minimizing downtime and reducing maintenance costs.
In this blog, we will explore the key benefits of predictive maintenance for electric forklift fleets and how it helps businesses improve efficiency, safety, and overall profitability.
Understanding Predictive Maintenance
Predictive maintenance uses real-time data collected from sensors installed on forklifts to monitor various performance indicators such as battery health, motor function, tire wear, and hydraulic system efficiency. By analyzing this data, fleet managers can predict potential failures and schedule maintenance before a breakdown happens.
Unlike reactive maintenance (fixing problems after they occur) or preventive maintenance (scheduled servicing at fixed intervals), predictive maintenance is data-driven and ensures that servicing is done only when necessary. This reduces unnecessary maintenance costs while improving asset reliability.
Key Benefits of Predictive Maintenance for Electric Forklift Fleets
1. Reduced Downtime and Increased Productivity
Unplanned forklift breakdowns can bring warehouse operations to a halt, leading to costly delays. With predictive maintenance, fleet managers can anticipate potential failures and address them before they disrupt workflows. This results in fewer unexpected downtimes, allowing businesses to maintain smooth and efficient operations.
2. Cost Savings on Repairs and Maintenance
Traditional maintenance approaches often involve excessive repairs or premature part replacements, which increase operational costs. Predictive maintenance eliminates these inefficiencies by servicing only the components that need attention. By catching issues early, businesses can prevent minor defects from escalating into costly repairs or complete forklift failures.
3. Extended Equipment Lifespan
Forklifts are significant investments, and extending their lifespan can improve a company's return on investment. Predictive maintenance ensures that forklifts operate in optimal condition by preventing wear and tear from escalating. Proper maintenance also preserves battery performance, motor efficiency, and other critical components, thereby prolonging the forklift’s usability.
4. Enhanced Safety for Operators
Malfunctioning forklifts pose safety risks to operators and other warehouse staff. Brake failures, battery malfunctions, or hydraulic leaks can lead to accidents and injuries. By continuously monitoring the health of forklifts, predictive maintenance helps prevent hazardous situations, ensuring a safer work environment.
5. Optimized Fleet Management
Fleet managers can use predictive maintenance data to make informed decisions about their forklift operations. By analyzing performance trends, they can determine which forklifts require servicing, when to retire aging units, and how to allocate resources more effectively. This improves overall fleet efficiency and resource utilization.
6. Better Battery Management
Electric forklifts rely on battery power, and improper battery management can lead to reduced efficiency and premature failures. Predictive maintenance systems track battery performance metrics such as charge cycles, temperature, and voltage levels. This allows managers to optimize charging schedules, prevent deep discharges, and extend battery life.
7. Minimized Environmental Impact
Electric forklifts are already a greener alternative to traditional internal combustion forklifts. Predictive maintenance further enhances sustainability by reducing unnecessary part replacements, lowering energy
consumption, and minimizing waste. By maintaining forklifts in peak condition, businesses can contribute to environmental conservation while improving operational efficiency.
8. Data-Driven Decision Making
The data collected from predictive maintenance systems provides valuable insights into fleet performance, equipment utilization, and maintenance trends. Businesses can leverage this data to refine operational strategies, optimize maintenance schedules, and enhance overall productivity. This results in more effective long-term planning and resource allocation.
The Growing Market for Electric Forklifts
The adoption of electric forklifts is rising globally, driven by advancements in battery technology and a growing emphasis on sustainability. According to Persistence Market Research’s projections, the electric forklift market value was estimated at US$53.4 billion in 2024 and is expected to reach US$137.0 billion by 2031. The market is predicted to achieve a steady CAGR of 14.4% from 2024 to 2031
With such rapid growth, businesses must invest in effective maintenance strategies to maximize their fleet’s efficiency and longevity. Predictive maintenance presents an innovative solution that aligns with the industry’s expansion, helping companies achieve cost savings and operational excellence.
Implementing Predictive Maintenance in Your Fleet
To incorporate predictive maintenance into electric forklift fleets, businesses should consider the following steps:
1. Deploy IoT Sensors: Install sensors on forklifts to monitor key performance indicators such as temperature, vibration, and battery health.
2. Utilize AI and Analytics: Use predictive analytics software to process data and identify potential issues before they cause failures.
3. Automate Alerts and Reporting: Set up automated alerts to notify maintenance teams of potential problems, allowing for proactive intervention.
4. Train Staff and Technicians: Ensure operators and maintenance teams are familiar with predictive maintenance tools and can interpret data effectively.
5. Integrate with Fleet Management Systems: Combine predictive maintenance with existing fleet management platforms for seamless monitoring and optimization.
Conclusion
Predictive maintenance is transforming the way businesses manage electric forklift fleets. By leveraging data analytics and IoT technology, companies can enhance productivity, reduce costs, and ensure workplace safety. With the electric forklift market projected to grow significantly in the coming years, predictive maintenance will play an increasingly critical role in maintaining fleet efficiency and sustainability.
By adopting predictive maintenance strategies, businesses can future-proof their operations, maximize equipment lifespan, and stay ahead in a competitive market. Investing in this technology today will lead to long-term benefits, ensuring that electric forklift fleets remain reliable, cost-effective, and environmentally friendly for years to come.