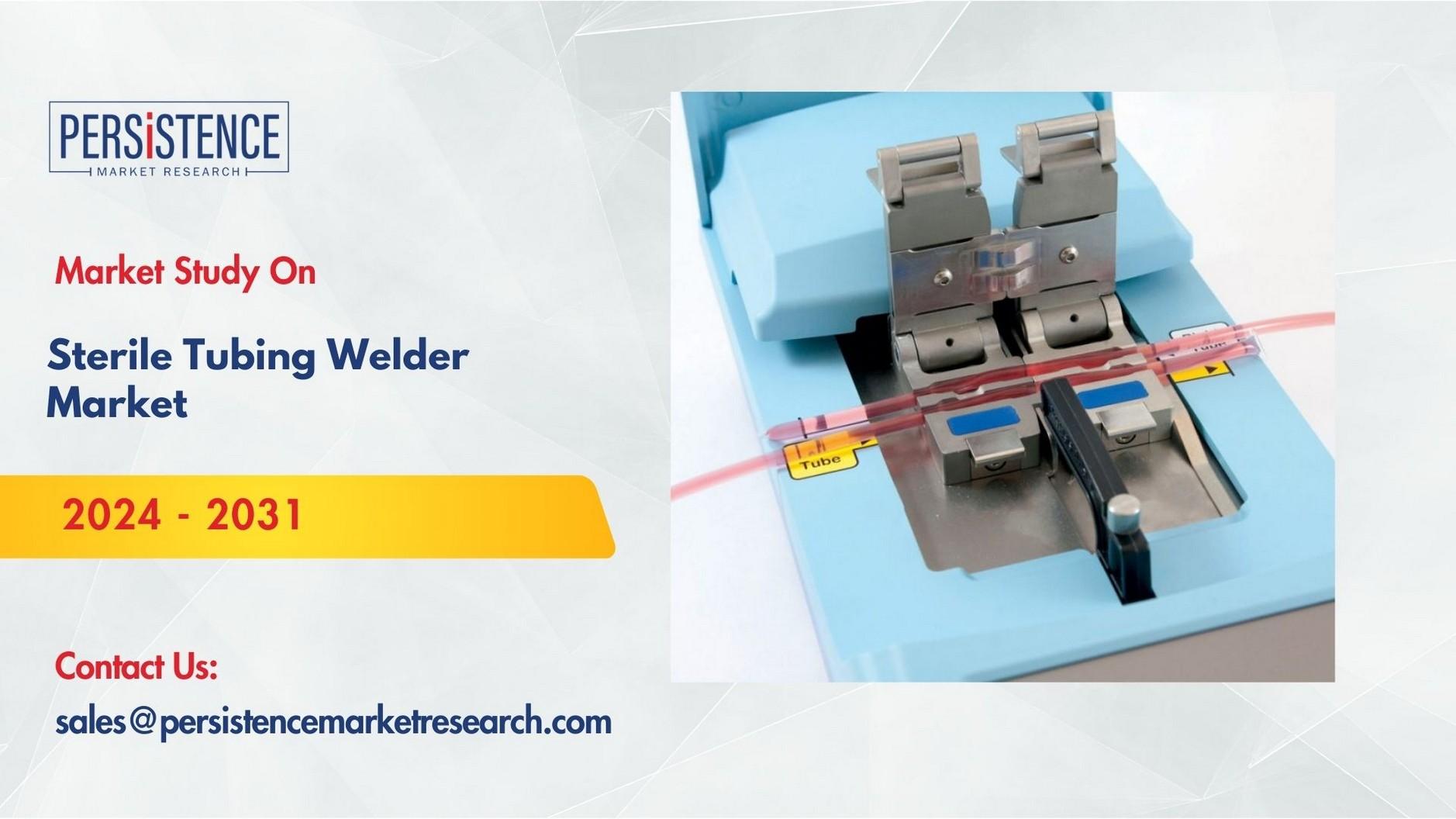
The sterile tubing welder market is poised for robust growth, primarily driven by its critical applications in the biopharmaceutical industry. This market is gaining momentum as biotechnology and pharmaceutical companies increasingly focus on ensuring sterile, contamination-free environments for manufacturing biologics, vaccines, cell therapies, and other life-saving treatments.
The sterile tubing welder market is projected to witness a CAGR of 5.1% during the forecast period from 2024 to 2031. It is anticipated to increase from US$ 2.5 Bn recorded in 2024 to a decent US$ 3.6 Bn by 2031. Rising prevalence of chronic diseases and significant investments in the biopharmaceutical sector are set to fuel demand.
Sterile tubing welders play an essential role in biopharma manufacturing by providing a secure, sterile connection between tubing systems used in the production, storage, and transportation of biologics. Their ability to weld two pieces of tubing together without compromising sterility has made them indispensable in creating closed systems that minimize the risk of contamination.
In this article, we will explore the growth factors, trends, and market applications of sterile tubing welders in the biopharma industry, shedding light on how they contribute to improving safety, efficiency, and product quality.
What is a Sterile Tubing Welder?
A sterile tubing welder is a specialized device used in the biopharma industry to join two sections of tubing without exposing the interior to
contaminants. These systems are designed to weld two pieces of tubing together in a sterile manner, allowing for the transfer of liquids, gases, or other substances in a sealed, contaminant-free environment.
Sterile tubing welders are typically used for connecting fluid lines, such as those used in drug production, cell culture, blood processing, and similar applications. Unlike traditional welding methods, which may introduce foreign substances or contaminants, sterile tubing welders use heat, pressure, and time-controlled mechanisms to create secure and sterile connections.
Key Applications of Sterile Tubing Welders in the Biopharma Industry
The biopharma industry requires stringent quality control and contamination prevention protocols due to the sensitive nature of the products being developed, such as vaccines, biologics, and gene therapies. Sterile tubing welders help ensure these protocols are met by enabling safe, sterile connections in the following key applications:
1. Bioprocessing
Bioprocessing involves the production of biologics, such as monoclonal antibodies, therapeutic proteins, and vaccines. These biopharmaceutical products are typically manufactured using large-scale fermentation or cell culture processes, which require sterile, closed systems to prevent contamination. Sterile tubing welders are widely used to connect various parts of bioreactor systems, media bags, and filtration units, ensuring that the flow of liquids remains contamination-free.
In addition, the flexibility and ease of use offered by these welders streamline the manufacturing process, reducing the risk of human error and improving operational efficiency.
2. Cell and Gene Therapy Manufacturing
Cell and gene therapies are emerging as revolutionary treatments for a variety of conditions, including genetic disorders, cancers, and immune system diseases. However, the production of these therapies is highly complex and requires precise, sterile conditions to avoid contamination that could compromise product efficacy or patient safety.
Sterile tubing welders are essential in connecting tubing systems for harvesting, cell expansion, and gene editing processes. As the demand for personalized medicine and regenerative therapies increases, the role of sterile tubing welders in ensuring the sterility and integrity of production systems will become even more critical.
3. Blood and Plasma Collection
Blood and plasma collection for medical treatments, such as transfusions or therapeutic apheresis, requires specialized equipment that maintains the sterility of collected materials. Sterile tubing welders are used to connect blood bags, filters, and transfer lines, ensuring that the collection and storage process remains secure from contamination. These welders are also integral to the design of closed systems, which reduce the risk of exposure to air and external contaminants, thereby ensuring the safety of both patients and healthcare providers.
4. Vaccine Production
Vaccines require high standards of sterility and precision during manufacturing. The production process typically involves large-scale fermentation or cell culture systems, filtration, and purification steps—all of which require sterile tubing connections. Sterile tubing welders ensure that sterile fluid transfer is maintained throughout the vaccine manufacturing process.
As the global demand for vaccines continues to rise, driven by factors like the COVID-19 pandemic, sterile tubing welders will remain indispensable in ensuring the continued safety and efficacy of vaccine production.
5. Aseptic Drug Transfer and Packaging
In the pharmaceutical industry, aseptic drug transfer and packaging are vital processes to maintain the sterility of finished drug products. Sterile tubing welders are used in the transportation of sterile drugs and in packaging systems where the drug is transferred from one container to another without any exposure to contaminants.
By enabling contamination-free connections between containers and drug delivery systems, sterile tubing welders play a key role in ensuring that medications are delivered in the safest and most sterile manner possible.
Growth Drivers for the Sterile Tubing Welder Market
Several factors are driving the growth of the sterile tubing welder market, particularly within the biopharma industry:
1. Increasing Biopharmaceutical Production
The biopharmaceutical industry has seen a surge in demand for biologic drugs, vaccines, and cell and gene therapies. As the production of these therapies scales up, the need for sterile, efficient, and reliable manufacturing processes has become more pronounced. Sterile tubing
welders help streamline the bioprocessing of these products, making them indispensable in the production chain.
2. Advancements in Cell and Gene Therapy
With the rapid advancements in gene editing, gene therapies, and cellbased therapies, there is an increasing demand for sterile systems that can handle complex, high-risk manufacturing processes. Sterile tubing welders are essential for maintaining the sterility of the systems used in these therapies, which are often produced in smaller batches under highly controlled environments.
3. Stringent Regulatory Requirements
The regulatory landscape for the biopharma industry is becoming more stringent, with authorities requiring manufacturers to adhere to strict quality control standards. Sterile tubing welders are critical in helping companies meet regulatory guidelines that demand contamination-free processes throughout manufacturing, storage, and distribution. The ability to provide secure, sterilized connections in fluid systems enhances compliance with FDA, EMA, and other global health authorities.
4. Growing Focus on Personalized Medicine
Personalized medicine is an emerging trend in healthcare that involves tailoring medical treatment to individual patients based on their genetic makeup. The production of these custom therapies requires small-batch manufacturing processes, which rely heavily on sterile, closed systems. Sterile tubing welders are crucial in enabling the sterile connections needed for these production systems, supporting the growing demand for personalized therapies.
5. Global Pandemic Preparedness
The COVID-19 pandemic highlighted the importance of biopharmaceutical manufacturing capabilities and the role of robust and sterile production systems in ensuring quick vaccine and therapeutic production. As countries and organizations invest more heavily in pandemic preparedness, the demand for sterile tubing welders, particularly in vaccine production, is expected to rise.
Key Market Trends in the Sterile Tubing Welder Industry
Automation and Integration: The integration of automated and digitally connected tubing welders is becoming increasingly popular. Automated systems reduce the likelihood of human error and improve the overall efficiency of the manufacturing process.
Additionally, the ability to track and monitor welding parameters in real-time enhances process control and sterility assurance.
Increase in Single-Use Systems: The use of single-use systems in biopharma manufacturing is on the rise. Single-use systems, which include pre-sterilized tubing, bags, and containers, are increasingly being paired with sterile tubing welders to reduce the need for cleaning and reprocessing between uses. This trend is helping companies lower costs and streamline their operations.
Emerging Markets: The growing biopharmaceutical and healthcare industries in emerging economies, particularly in Asia-Pacific, are expected to contribute significantly to the growth of the sterile tubing welder market. As these regions expand their pharmaceutical manufacturing capabilities, the demand for high-quality, reliable sterile systems will rise.
Conclusion: A Promising Future for the Sterile Tubing Welder Market
The sterile tubing welder market is set for significant growth, driven by advancements in the biopharma industry, particularly in areas like bioprocessing, cell and gene therapy, and vaccine production. The rising demand for sterile, contamination-free manufacturing systems underscores the importance of sterile tubing welders in modern biopharmaceutical operations.
As the biopharma industry continues to innovate and expand, the adoption of sterile welding technologies will be integral to ensuring that products are delivered safely and efficiently. With increasing regulatory pressures, the need for automation, and the growing focus on personalized medicine, the sterile tubing welder market is expected to remain a crucial segment of the healthcare and biopharma sectors for the foreseeable future.
Follow Us: Twitter | YouTube | LinkedIn