How Hydrogen-Based DRI Tech Is Shaping the Future of HBI Production
The U.S. hot briquetted iron (HBI) market is expected to grow from US$ 891.8 million in 2025 to US$ 1,346.4 million by 2032, driven by a 6.1% CAGR. The shift from traditional blast furnaces to Electric Arc Furnaces (EAF) in U.S. steel production is a major factor fueling HBI demand. EAF, which is more sustainable and uses HBI for cleaner steelmaking, will account for 75% of U.S. steel output by 2030. HBI’s compact form ensures better storage, handling, and reduced oxidation during transportation, making it ideal for long-distance steel production.
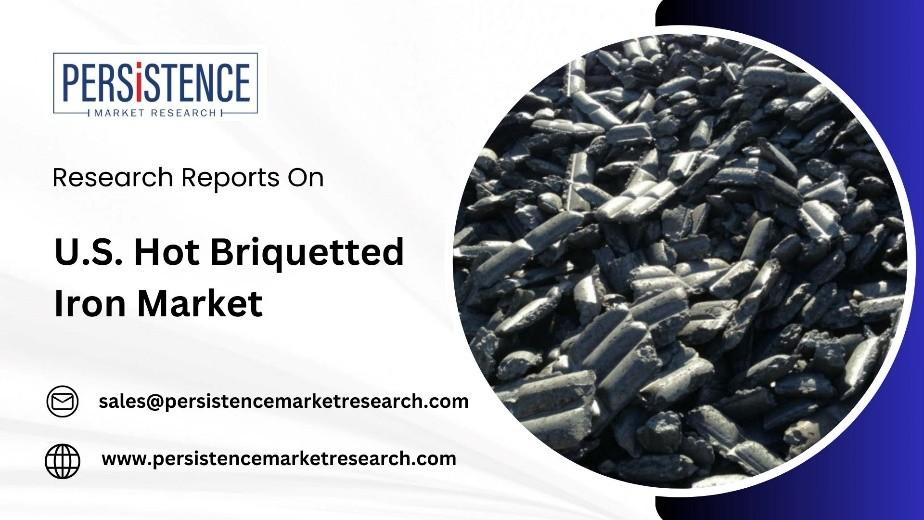
Additionally, the transition to low-carbon technologies, such as hydrogen-based Direct Reduced Iron (DRI), further supports HBI adoption. The Midwest region, with its advanced transportation networks and steel manufacturing facilities, is set to lead the market. HBI with 90%-92% Fe content, ideal for EAFs, is projected to dominate, offering an optimal balance of purity and cost-efficiency, contributing to reduced CO2 emissions. As the global steel industry seeks to decarbonize, hydrogenbased direct reduced iron (DRI) technology has emerged as a game-changing innovation—especially in the production of hot briquetted iron (HBI). With mounting environmental regulations, energy concerns, and a collective push toward sustainability, hydrogen-based DRI is redefining the pathway toward cleaner steelmaking. Here's how this groundbreaking tech is revolutionizing HBI production.
The Rise of Hydrogen in Steelmaking
Traditionally, the production of steel has relied heavily on carbon-intensive processes, primarily using coal and natural gas. However, the push for carbon neutrality has prompted steelmakers to explore low-emission technologies. Hydrogen—particularly green hydrogen produced from renewable energy sources—is increasingly seen as the cleanest and most scalable alternative for DRI processes.
Direct Reduced Iron (DRI) is a crucial input in electric arc furnaces (EAFs), which are themselves cleaner alternatives to blast furnaces. When DRI is compacted into hot briquetted iron (HBI), it becomes easier and safer to transport. By replacing natural gas with hydrogen in the reduction process, steelmakers can drastically reduce the carbon footprint of HBI production. This is a critical step toward achieving net-zero emissions across the steel value chain.
Technological Advancements in Hydrogen-Based DRI
Recent years have seen rapid innovation in DRI furnace design, process control systems, and gas reforming technologies. Major industrial players are investing in large-scale demonstration plants to test and refine hydrogen-based DRI production. Companies like Midrex and Tenova have developed modular DRI facilities capable of switching between natural gas and 100% hydrogen, offering flexibility during the energy transition.
For example, Midrex’s “HYFOR” (Hydrogen-based Fine Ore Reduction) technology allows for direct reduction using hydrogen without the need for sintering or pelletizing. This not only cuts emissions but also saves operational costs. Such innovations mark a pivotal shift in DRI tech, opening up new pathways for sustainable HBI manufacturing.
Environmental and Economic Benefits
The environmental benefits of using hydrogen in DRI production are significant. Replacing fossil fuels with green hydrogen can eliminate up to 90% of CO₂ emissions from the reduction process. In regions where carbon pricing mechanisms are in place, this shift can also bring substantial cost savings in the long run.
From an economic perspective, producing HBI through hydrogen-based DRI may require high upfront investment, but the payback comes in the form of long-term resilience and market competitiveness. As demand for low-carbon steel grows—driven by automotive, construction, and renewable energy sectors—HBI produced via hydrogen DRI becomes a premium product with high export potential.
Challenges Hindering Large-Scale Adoption
Despite its promising outlook, hydrogen-based DRI tech is not without challenges. Chief among them is the availability and affordability of green hydrogen. Current hydrogen production is largely dominated by grey hydrogen (derived from natural gas), which doesn’t offer the desired climate benefits. Scaling up green hydrogen infrastructure—electrolyzers, renewable power, and distribution networks—remains a key hurdle.
Additionally, retrofitting existing DRI plants or building new ones designed for hydrogen use demands significant capital investment. Technological adaptation, workforce training, and regulatory approvals are also part of the equation, making the transition a complex but necessary endeavor.
Regional Hotspots and Market Trends
Europe is at the forefront of hydrogen-based DRI adoption, thanks to ambitious climate policies, carbon pricing, and government-backed projects. Sweden’s HYBRIT initiative, a joint venture by SSAB, LKAB, and Vattenfall, produced the world’s first hydrogen-reduced sponge iron and is on track to scale up production by 2030. Germany and Austria have also committed to investing billions in green hydrogen steel projects.
The Middle East and North Africa (MENA) region, rich in solar energy, is emerging as a future hub for low-cost green hydrogen and HBI production. Countries like Saudi Arabia and the UAE are investing
in hydrogen-powered DRI plants to cater to European and Asian markets. Meanwhile, North America is leveraging its abundant renewable energy resources and policy incentives to build a hydrogen economy, creating new opportunities for HBI exports.
The Role of Policy and Industry Collaboration
Government incentives, carbon border adjustment mechanisms (CBAMs), and climate finance will play a critical role in enabling the hydrogen transition. By creating market-based mechanisms that favor low-carbon steel and investing in green hydrogen infrastructure, policymakers can accelerate the commercialization of hydrogen-based DRI.
Furthermore, collaboration between energy companies, steel manufacturers, equipment suppliers, and research institutions is vital. Public-private partnerships and industry alliances—such as the Green Hydrogen Catapult and the Mission Possible Partnership—are already driving coordinated action across the value chain. These efforts help de-risk investment, accelerate technology development, and build the necessary supply chains for hydrogen-based HBI production.
Future Outlook: A Cleaner, More Competitive Steel Industry
As hydrogen-based DRI technology continues to mature, it is poised to become the cornerstone of sustainable steelmaking. HBI, with its transportability and low-carbon credentials, will play a key role in decarbonizing the global steel supply chain. The synergy between green hydrogen production, advanced DRI furnaces, and international climate policies sets the stage for widespread adoption over the next decade.
While challenges remain—particularly around hydrogen scalability and economic feasibility—the momentum is undeniable. Leading steelmakers are already integrating hydrogen-ready infrastructure into their long-term plans. With rising global demand for green steel, hydrogen-based HBI will be at the forefront of a cleaner, more competitive future for the steel industry.
Conclusion
Hydrogen-based DRI technology is not just a theoretical solution—it’s already reshaping how HBI is produced and marketed. By reducing emissions, enhancing energy efficiency, and creating valueadded opportunities in green steel, this innovative tech is driving a transformative shift in one of the world’s most carbon-intensive sectors. The future of HBI production is being forged today—with hydrogen at its core.