NSW, AUSTRALIA
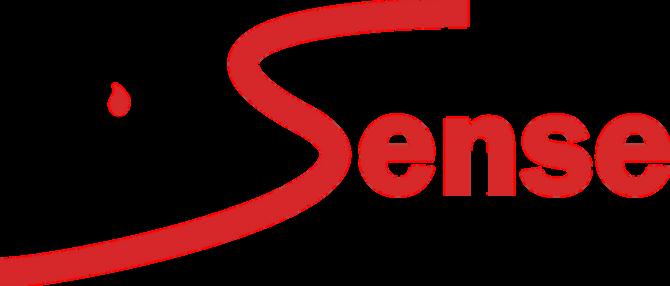
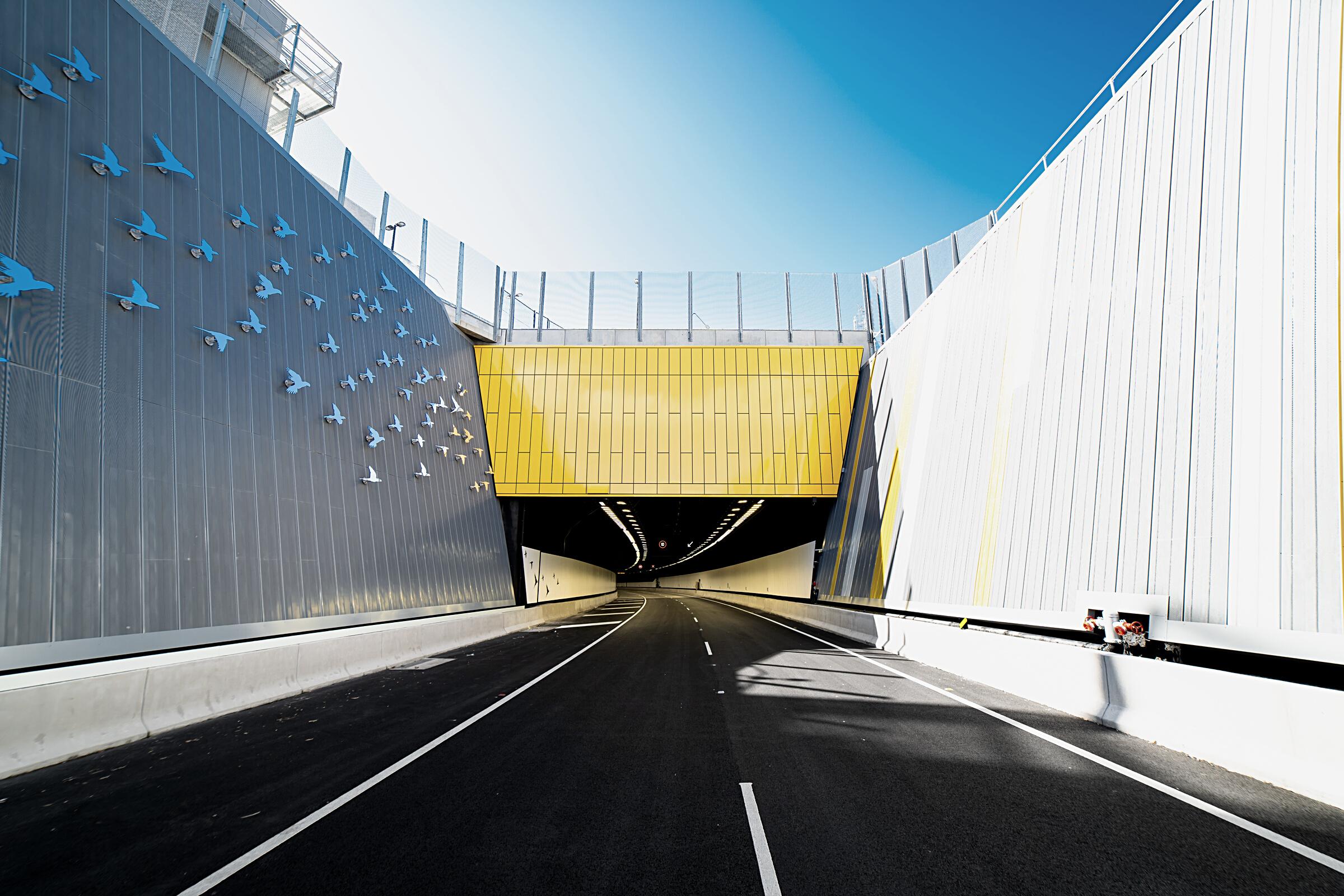
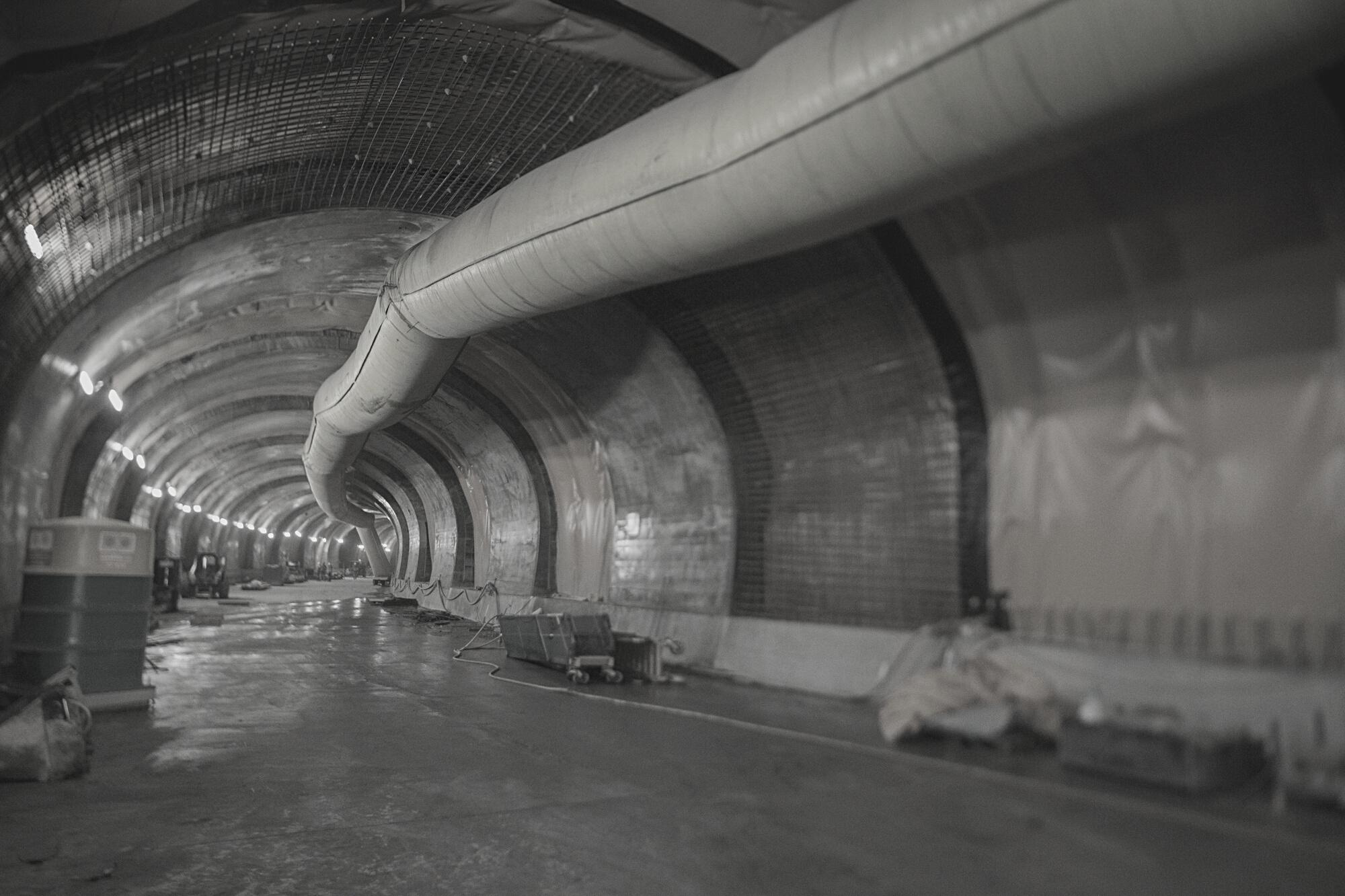
NorthConnex is a twin road tunnel in NSW which links the M1 Pacific Motorway at Wahroonga to the M2 Hills Motorway at West Pennant Hills This motorway is used by private and commercial vehicles to access the Sydney CBD and for travelling between Brisbane and Melbourne At 9km long, it is the longest and deepest tunnel in Australia The project total reached $3 billion which makes it Australia’s largest underground road project
The Motorway Control Centre (MCC) is located at West Pennant Hills with a Disaster Recovery Site (DRS) located at Wilson Road, Pennant Hills The northern facilities building at Wahroonga contains the fire pump room and two high capacity fire water tanks amongst other services
The fire detection system within the NorthConnex tunnel is based around a comprehensive, high speed network of FireSense 3030 fire panels These panels are connected to remote Data Marshalling Panels (DMPs) controlling the field input/output. A combination of addressable smoke, heat and duct probe detectors, manual call points, hydrocarbon gas detectors and combined sounder/strobes are installed throughout the cross passage and back of house service areas of the tunnel
The DMPs are connected directly to the tunnels deluge system which control and monitor all aspects of the sprinkler system This includes deluge valve activation, pressure switches and isolation valve monitoring Similarly, the DMPs are also connected to the foam deluge system
Advanced fibre optic linear heat detection cables, connected to dedicated linear heat control panels protect the tunnel carriageways These are linked to the fire detection network via high level Modbus interfaces
The fire system is also linked to the Operations and Maintenance Control System (OMCS) and the Plant Management Control System (PMCS) via high level Modbus interfaces
FireSense supplied a number of dedicated Graphical User Interfaces (GUI’s) consisting of touchscreen graphic PCs displaying actual architectural backgrounds This allows for fast, accurate, real-time diagnosis of all fire system events.
Lend Lease Bouygues Joint Venture (LLBJV) engaged FireSense directly for the supply of all fire detection equipment and cabling with the install and commissioning provided by a separate qualified fire contractor. This was beneficial for all parties, as we were able to work very closely with the LLBJV engineers to fine tune the technical requirements of the project This approach ensured total control of the system design from start to finish
FireSense were engaged for the production, testing, complete programming and onsite commissioning assistance of all aspects of the fire detection system All panels were manufactured locally and tested in the FireSense Testing Centre
The equipment FireSense supplied included:
2 main fire indicator panels
5 graphical user interfaces
6 linear heat detection controllers
8 hydrocarbon gas detectors
10 Modbus high level interfaces
61 sub fire indicator panels
180 data marshalling panels
6,000+ individual point devices
6,000m fibre optic linear heat cable
FireSense 3030 and LHDC PanelsThe NorthConnex project faced a number of unique challenges due to the significant size and complexity of the tunnel FireSense identified potential difficulties early on in the scope and sought to provide a solution to each.
Challenge: Specified delivery schedule requirements due to size, scale and complexity of the project
Solution: FireSense worked closely with the builder and fire contractor to streamline the delivery process. We packaged and provided detailed labelling of all equipment including the exact location the equipment was to be installed Pallets were shrink wrapped to protect products and minimise delays on site
Challenge: Necessity of a two hour response time for support staff to be on the project site.
Solution: FireSense have 3 offices across the east coast of Australia with our Head Office in Norwest, NSW. All of our panels were custom built in Sydney only 20 minutes from the project We have a large team of experienced technical staff within each branch whom supported ALL aspects of the fire system build
Challenge: Limiting the amount of time that contractors spent on site due to logistical and safety reasons.
Solution: Fire contractors needed the equipment to be preprogrammed “out of the box” so they did not face any downtime during the construction and commissioning phases FireSense made a progressive initiative to establish a dedicated Fire Testing Centre in Sydney allowing us to setup 100% of panels to program and test all aspects of the fire system in a controlled environment This included over 250 different panels, controllers and interfaces, the first of its kind in the fire industry The fire system was the first of many sub-systems in the tunnel to finish commissioning months ahead of the target date. The FireSense Testing Centre is now used for all of our major projects to ensure exceptional and efficient installation on site
Challenge: Having 24 hour access to staff who are knowledgeable on the project specifics
Solution: FireSense understands the risks that large projects face and the extended duration of the construction It is for this reason we mirror imaged staff roles at all times across every aspect of the project That way, if a staff member fell ill or took leave, we had backup staff to take over at a moments notice.
Challenge: Customers are untrained to use the specific technology needed to manage the tunnel's fire detection system
Solution: The Linear Heat Controllers used in the tunnel were a new innovation requiring hands on training from the supplier located in Boston, USA. FireSense sent 5 staff members including our Managing Director to Boston for an intensive 3 day training course so that we could provide local support to NorthConnex We also developed and presented a detailed training package for Transurban and the incumbent fire contractors servicing the tunnel upon opening.
Challenge: Extensive documentation required to back up all aspects of the project
Solution: FireSense employs an in house team of designers and drafts people that work closely with our customers to ensure the needs of the fire system design can be clearly communicated to all parties involved We regularly go well beyond our contract obligations by generating additional documents, schematics and drawings to exceed our customers’ expectations
Challenge: Sourcing products that are capable of handling the high level project requirements.
Solution: Some enhancements were required to the Modbus gateway during the design phase of the project. The Modbus gateway is a crucial element in the fire system passing high level information between the fire system and the Linear Heat Detection Controllers, the OMCS and PMCS We collaborated with manufacturing technicians from around the globe on engineering enhancements to the Modbus gateway to tailor a perfect product solution for the NorthConnex project.
Including fire equipment specialists in the upfront design ensured the optimal system was designed to meet the project scope
Allocation of an experienced project team enabled the fire detection system to be completed on time and within budget
100% pre-programmed and tested systems ensured all issues were resolved before installation on site, reducing time on site.
Factory Acceptance Test (FAT) carried out in the FireSense Testing Centre minimised the amount of time spent testing on site
Mirror imaging of technical staff roles ensures that backup resources are available to take over if required, eliminating any down time.
Locally trained staff ensures fast response times and removes dependency of third party suppliers.
Advanced training for end users improved the confidence of system controllers allowing for immediate resolution of faults