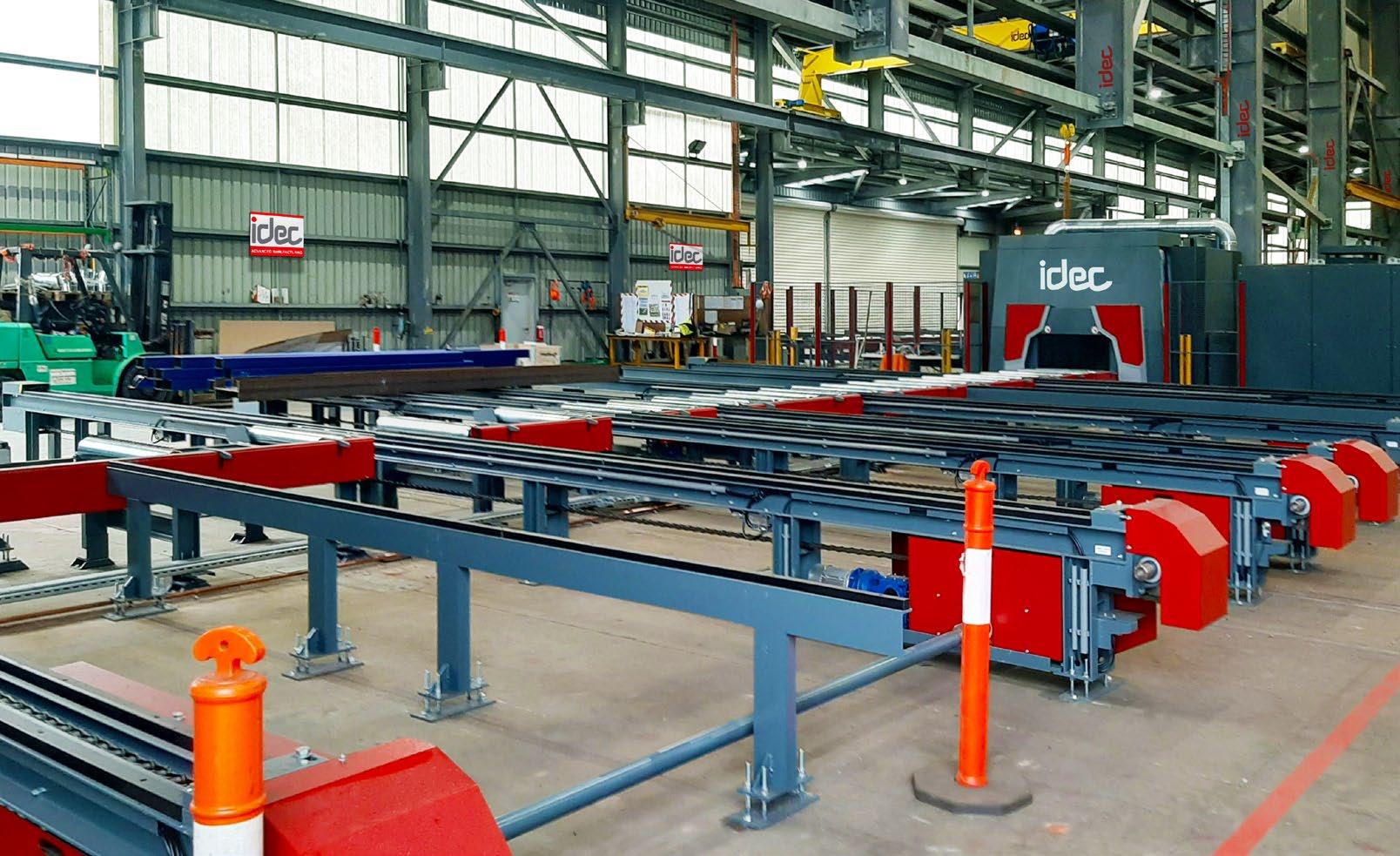
6 minute read
idec's Automation Journey: Increasing Competitiveness, Productivity and Innovation
BASED IN BRISBANE, IDEC SPECIALISES IN THE DESIGN AND CONSTRUCTION OF COMMERCIAL AND INDUSTRIAL BUILDINGS, AS WELL AS REMOTE INFRASTRUCTURE. THEIR IN-HOUSE CAPABILITIES INCLUDE WORKSHOP DETAILING, FABRICATION AND ERECTION.
IDEC RECENTLY RECEIVED A MADE IN QUEENSLAND GRANT. THIS QUEENSLAND GOVERNMENT INITIATIVE SUPPORTS LOCAL MANUFACTURERS TO INCREASE INTERNATIONAL COMPETITIVENESS, PRODUCTIVITY AND INNOVATION THROUGH THE ADOPTION OF NEW TECHNOLOGIES. AS A RESULT, IDEC HAS INVESTED IN THE LATEST VOORTMAN TECHNOLOGY INCLUDING AUTOMATED DRILLING AND SAWING MACHINES, A ROBOTIC COPING SYSTEM, AN INTELLIGENT INFEED-OUTFEED SYSTEM, AND INDUSTRY-LEADING MODELLING AND CONTROL SOFTWARE.
Advertisement
GLENN GIBSON (CEO, IDEC) ANSWERED SOME QUESTIONS FOR STEEL AUSTRALIA ABOUT IDEC'S AUTOMATION JOURNEY.
TELL US ABOUT IDEC'S HISTORY.
The idec story has roots deeply planted in industry and agriculture. Over 40 years ago, one of our Directors—Peter Gartshore—began marketing off-theshelf building kits, and from this, grew Big Country Buildings (BCB). BCB specialised in the design, fabrication and construction of custom-engineered steel buildings including hangars, warehouses and commercial facilities.
In 2006, Big Country Buildings rebranded to idec – an anagram of ideas, design, engineering and construction. This emphasises our ability to provide fully in-house steel design solutions. idec continues to grow and tackle complex projects. We operate with a corporate structure in conjunction with the support of a family run organisation.
WHAT DO IDEC'S OPERATIONS LOOK LIKE TODAY?
Today, idec is a multi-faceted design, fabrication and construction company that provides a true one-stop-shop solution. Our extensive in-house capabilities include design, processing, fabrication, rigging and construction across a multitude of sectors such as aviation, defence, local government, communications, energy, mining, education and major infrastructure.
WHAT ARE SOME OF YOUR MOST SUCCESSFUL MAJOR PROJECTS?
We have undertaken over 1,500 projects throughout our 40 year history, with each bringing its own challenges, learnings and rewards.
Notable projects include the VISY Can facility at Yatala which saw us deliver an 18,000m2 state-of-the-art facility as principal contractor in 2013. Moving away from the commercial space, we have been fortunate to work with numerous Tier 1’s on the delivery of Australia’s most well-known infrastructure projects, including the C-17 Hangar at Amberley, Land-121 Enoggera, Gold Coast University Hospital, AirportLink, Legacy Way and Cross River Rail.
WHAT IS THE SECRET TO IDEC'S SUCCESS?
Our secret to success is our people. From the outset, our clients deal directly with a member of our team, whether that be our estimators, engineers, designers, project management team or riggers. At every step of the way, all works are undertaken by idec employees – ensuring the highest quality outcome. Second to this is our ongoing commitment to innovation and technological advancement.
MADE IN QUEENSLAND GRANT
Made in Queensland (MIQ) is a $61.5 million Queensland Government program helping small and medium manufacturers to increase international competitiveness, productivity and innovation via the adoption of new technologies, and to generate highskilled jobs for the future.
Since 2017, MIQ has supported 84 advanced manufacturing projects across the state. It is expected to create more than 1,100 jobs over five years and generate more than $100 million in private sector investment. Of the 84 projects funded through MIQ, 40% are being delivered in regional Queensland. Eligible manufacturers can apply for grants between $50,000 and $2.5 million with matched funding.

LAWNTON AQUATIC CENTRE
The grandstand at Lawnton Aquatic Centre provides covered seating for 1,000 people, disability access, timekeeping facilities and storage areas. idec’s scope of works for the project included: structural design, steel fabrication and installation, civil works, pre-cast concrete seating, and cladding. idec engineered and built the structure to cantilever (using their built-up plate technology) over the bleachers for maximum visibility.
TELL US ABOUT IDEC'S RECENT INVESTMENT IN AUTOMATION AND TECHNOLOGY?
Our recent investment consists of three Voortman robots – the VB1050 Sawing Machine, V631 Drilling Machine, V807M Coping Machine – and an intelligent infeed-outfeed system. The utilisation of this robotic technology, coupled with our existing in-house design and detailing capabilities will ensure future competitiveness within the industry. This robotic steel processing line is currently the most advanced line in Queensland and is the first of a series of planned investments in automation.
WHY DID YOU DECIDE TO INVEST IN AUTOMATION?
idec has always been at the forefront of technological and industry advancement including the implementation of AS 5131 in 2016 as one of the first fabricators certified to Construction Category 3. Likewise, the conversation about investing in the emerging field of automation and robotics has been ongoing for a number of years. The Board and I could very clearly see the material number of improvements and opportunities which automation would bring our business including the creation of high-skilled jobs and
VISY WAREHOUSE
idec was contracted by VISY to construct a new large-scale warehouse to manufacture lightweight cans for the beverage industry. The facility included 18,000m2 of warehouse space and 1,000m2 of office space. idec's scope of works included concrete foundations and slabs, structural steel, precast concrete panels, cladding, building services, fire protection systems, internal office fitout and landscaping.
DINMORE & GRACEVILLE STATIONS
As part of Queensland Rail’s ongoing Station Upgrade Program, idec was contracted to detail, fabricate, protective coat and install steelwork for the upgrade of Dinmore and Graceville train stations. idec’s scope of work included: fabrication and erection of the lift shafts, fully-welded overpass sections, stairs and awnings; cladding and security screens; and high quality protective coating application.
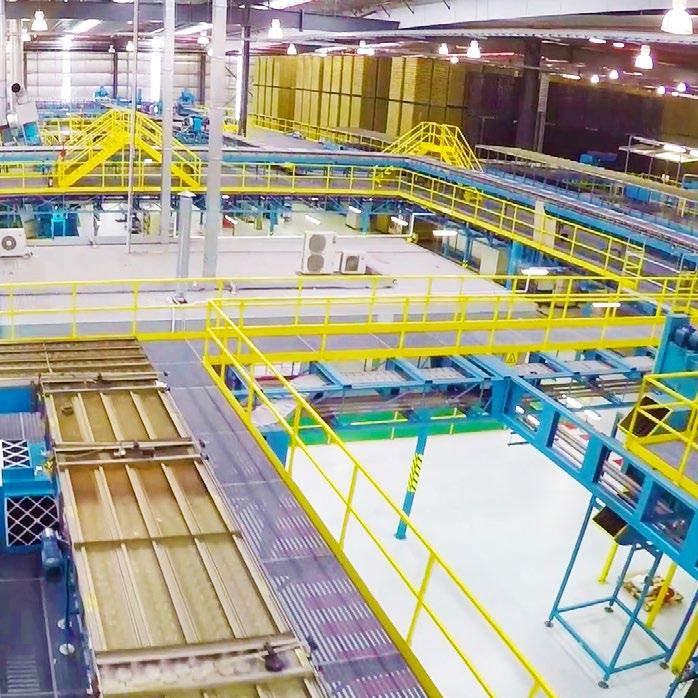
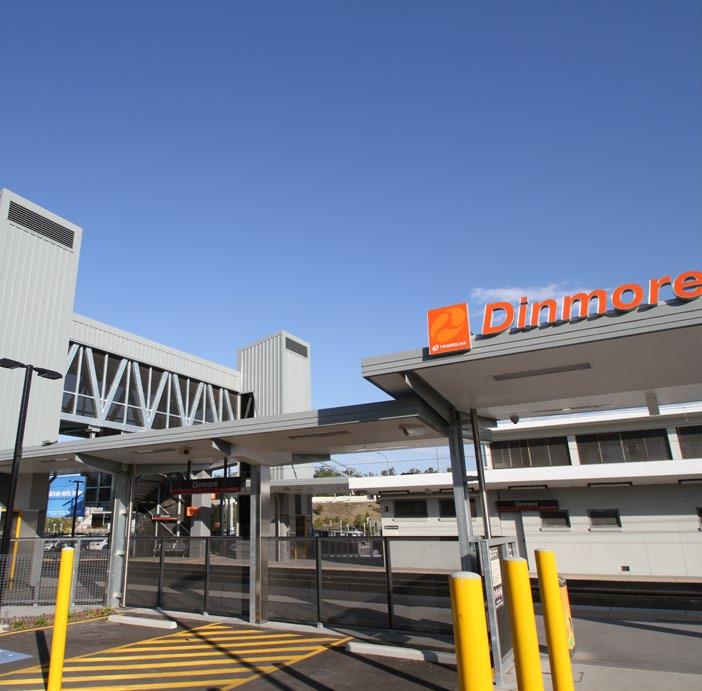
increased quality assurance.
WHAT IMPROVEMENTS HAVE YOU SEEN AS A RESULT?
We are still in the commissioning phase, with the sum of improvements not yet clearly discernible. However, I will say that the overall quality of processed steel coming off our new processing line is remarkably high thanks to our integrated analysis–design–documentation–detailing–processing model.
Our processing line is closely linked to our Digital Engineering Team and model information can be directly imported from 3D modelling software. This results in the consistent, reliable and accurate transfer of information between the shop drawing and fabrication process. The robot can mark out and scribe all fabricated components which reduces overall fabrication time and potential for error.
HOW DID YOU FIND THE GRANT APPLICATION PROCESS?
For an organisation of our size, the grant process afforded our executive team an opportunity to take a step back and view the company, its goals and objectives as a whole – while also focusing on the value for money of automation and overall return on investment. I recommend any manufacturer that is considering applying for the MIQ grant to begin the journey and see where it can take their business in terms of increasing their competitiveness, productivity and innovation through the adoption of new technologies – while generating high skilled jobs of the future. However, please be cognisant of the time and cost of a grant application.
WHERE TO NEXT FOR IDEC? WHAT DOES THE FUTURE HOLD?
We are excited about the opportunities that our robotic processing line will offer now and into the future, including the ability to upskill our existing staff particularly in the area of robotics and technology. Further to this, idec looks forward to a continual investment in automation which will see our company well-placed in the digital future while driving exceptional outcomes for our clients and their projects.