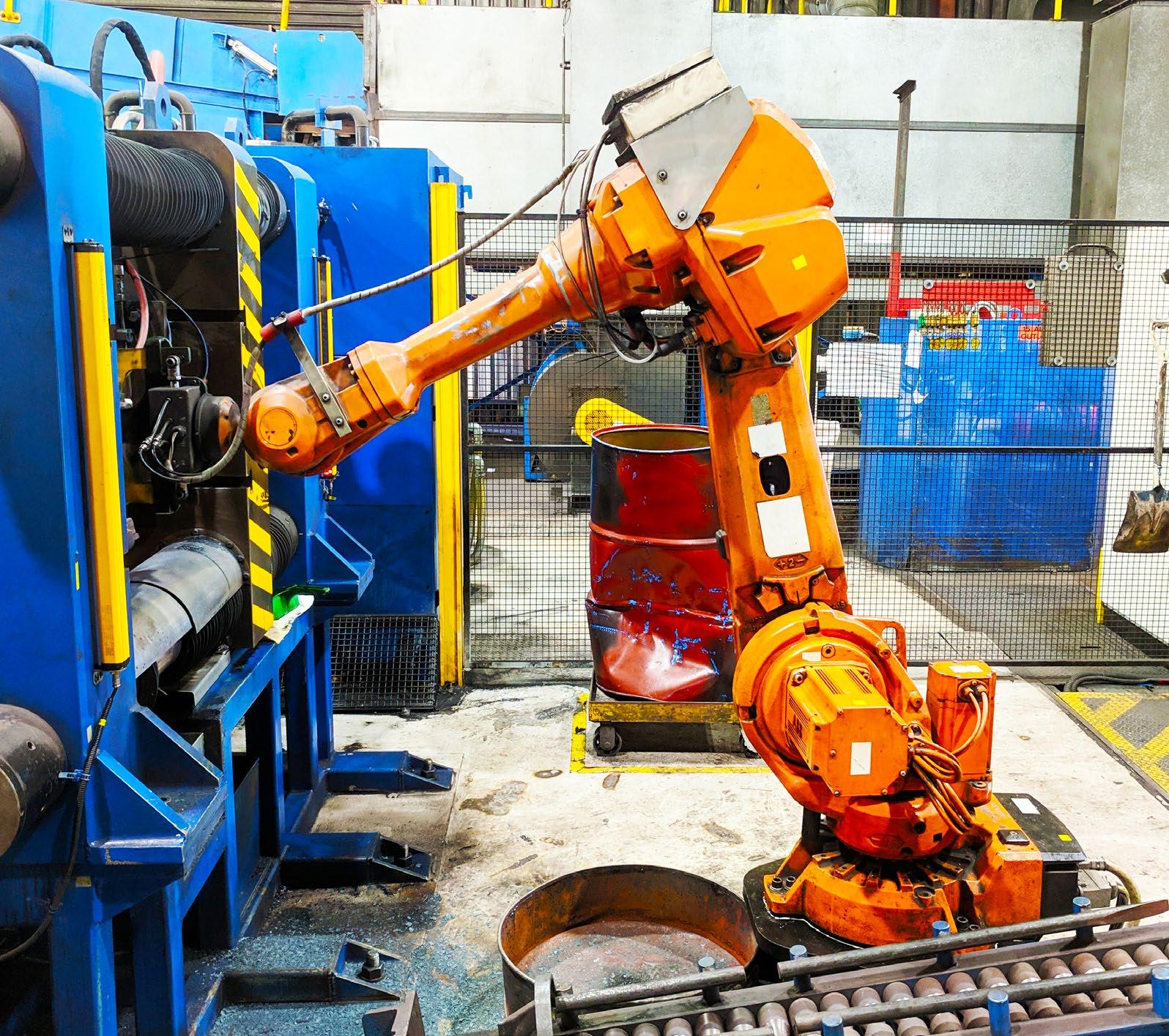
5 minute read
Molycop: Automation Builds a Better Working Environment
MOLYCOP'S 100-YEAR HISTORY HAS BEEN BUILT ON PROVIDING THE MOST INNOVATIVE, HIGHEST QUALITY PRODUCTS AND DELIVERING OUTSTANDING SUPPLY ASSURANCE. THEIR EXPERIENCED AND HIGHLY TRAINED TECHNICIANS ARE CONTINUALLY DEVELOPING SUPERIOR TECHNOLOGY SOLUTIONS AND PUSHING THE BOUNDARIES OF MINING CONSUMABLE PRODUCTS, TO MAKE CERTAIN NO MINE EVER STOPS OVER MOLYCOP. MOLYCOP EMBARKED ON ITS AUTOMATION JOURNEY IN 2011 IN A BID TO IMPROVE SAFETY AND BUILD A BETTER WORKING ENVIRONMENT.
Advertisement
Towards the end of World War I, Australia found it impossible to obtain supplies of railway wheels, axles and other steel products previously imported from England who, due to the war, were no longer in a position to export steel products. Consequently, Molycop's Australian operations began with the formation of Commonwealth Steel Company (Comsteel), and the establishment of its steelmaking operation at Waratah in Newcastle in 1918. During the 1930s, Comsteel diversified into grinding media to support Australia’s burgeoning hard rock mining industry.
Molycop’s product lines include grinding media, fasteners and the Comsteel range of forged railway wheels and axles. The main markets for grinding media are copper and gold mines in the Australasian region. In terms of rail products, Molycop caters for passenger and general freight, and their premium range of wheels is used in heavy haul in the Pilbara for iron ore - carrying the highest axle loads in the world.
The Comsteel range of products includes continuously cast anode pins for Australian and New Zealand aluminium smelters. Comsteel also supplies a range of ingots, from 1 tonne to 37 tonnes, for Australian forging operations. These forgings are used in applications like wind generation, heavy shafts and gears, and defence applications.
In addition, Molycop Engineered designs and manufactures a range of SAG and ball mill liner bolts for the mineral processing industry, Twistlock pins, and specialty fasteners.
THE AUTOMATION JOURNEY
Molycop embarked on its automation journey back in 2011, with the installation of a dual robot system for forging. This was quickly followed with the installation of a grinding robot in 2012. In 2017, both systems underwent capability improvements, before the installation of a second forging robot in 2018.
THE BENEFITS
As Samuel Regan (Business Improvement Leader, Molycop) explained, Molycop's decision to invest in automation was driven very much by the idea of creating a better working environment for their team.
"At the heart of it, most automation is about reducing risk to operators. The business case for automation was built around the safety aspects. We were focused on removing people from risk, improving safety, and building a better working environment," said Regan.
The grinding wheel in particular presents
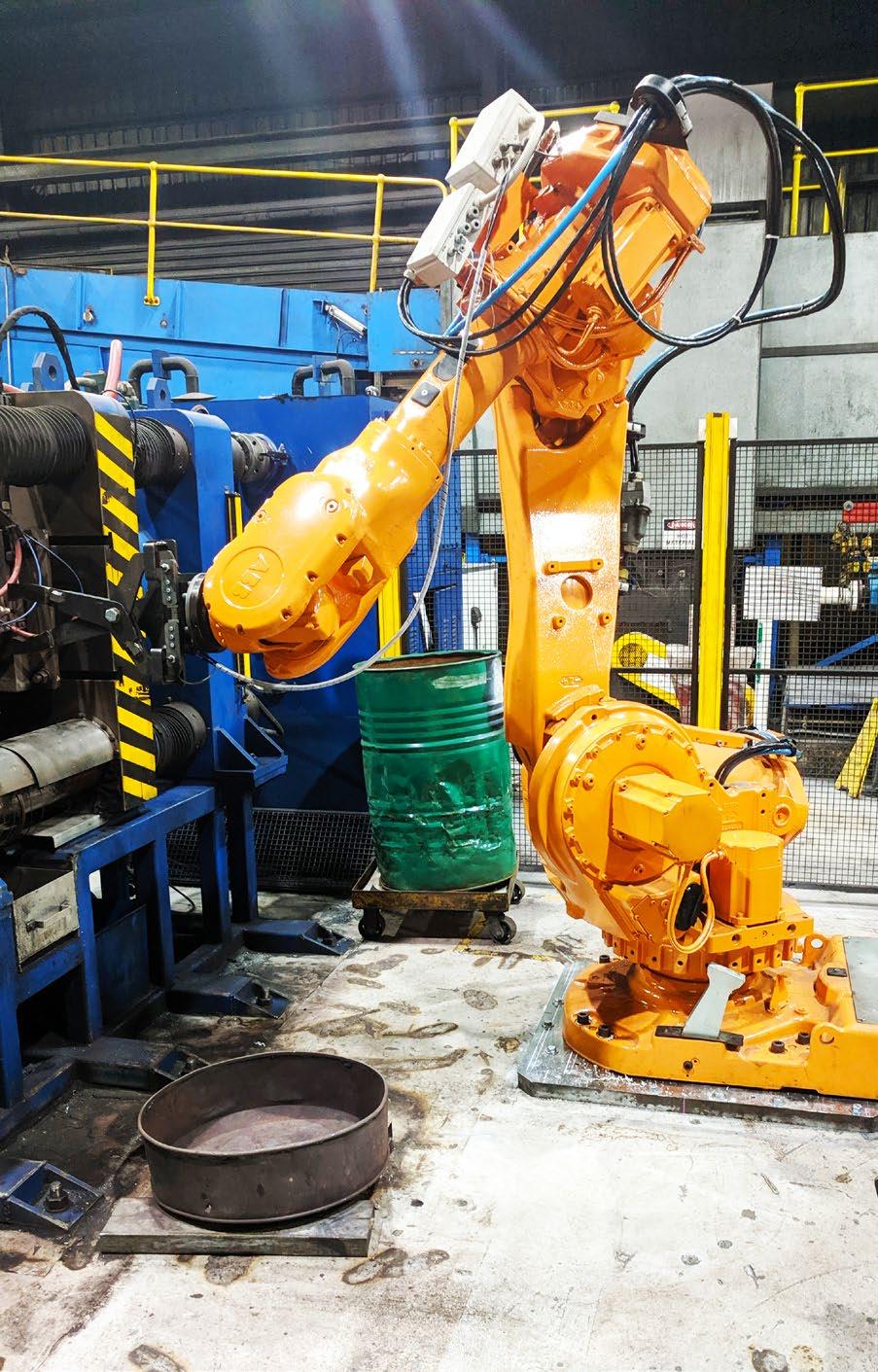
Molycop's griding media.
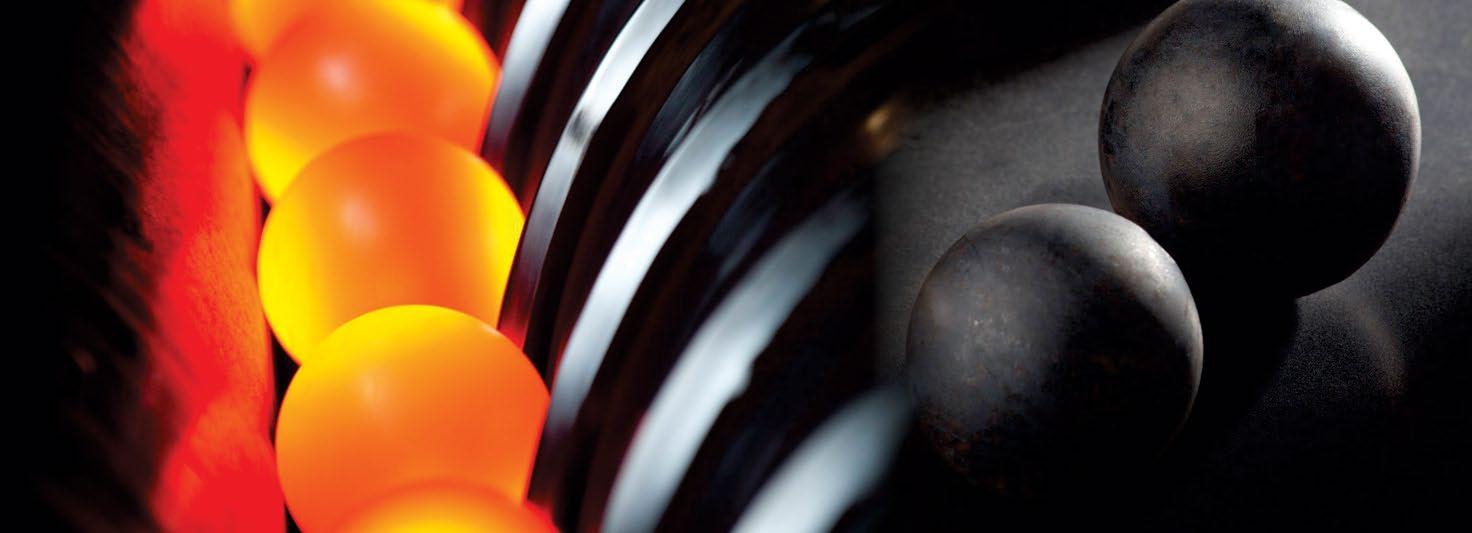
safety issues—running the grinding wheel over an extended period of time can cause RSI injuries due to the vibrations. Removing this was a real priority," said Regan.
The other clear benefit afforded by robotics is increased product quality and consistency. With the way the robotics work, they place the workpiece in the same place every time, which means that the final product is pressed perfectly every time."
IMPACT ON STAFF
"Overall, our staff have found the automation process really positive. A lot of our team members took the opportunity to upskill. Quite a few really embraced the changes and have become more involved in the business."
"A lot of the roles that get replaced or augmented by a robot are not necessarily what people come to work to do. You don’t get up in the morning and come to work wanting to use a grinding wheel for hours on end. People want to be in those higher-skilled, more interesting roles," said Regan.
THE CHALLENGES
As with any major business improvement project, Molycop faced some challenges along the way.
"Being a bespoke manufacturer, many of our jobs are smaller batch sizes, particularly on the bolt side of business, which makes bolts to order. This type of manufacturing requires flexible robotic solutions with broad scope. The robots can cope with these sorts projects, but it needs to be allowed for in your original project scope."
"The other major challenge comes with automating a rigidly manual process, like programming a robot to operate a griding wheel. It's challenging but also very rewarding – the payoff is definitely worth it," said Regan. Given the importance of project scope, Regan had this advice for other manufacturers considering embarking on the automation process themselves.
"The most important thing is to define the scope of the project well, and to make sure that scope is reasonable. You need to know exactly what you want to end up with and be clear on the deliverables – they need to be specific and measurable," said Regan.
"It's best to focus on high volume products and processes associated with the core business. Later on, you can increase the scope of your automation with improvement projects. Starting with a project scope that is too broad can make it extremely difficult to get the right robot cell, or makes the robot really expensive and hard to implement."
Another key tip for a successful automation journey is to leverage the experience and knowledge that your operators have built, working with the machinery every day.
"It's so important to utilise the knowledge of the operators who use the machinery. We learnt a lot talking with the operators. We found out little things—like tricks they were using to ensure the machines worked at full capacity—that weren’t immediately obvious, but when pointed out made a lot of sense," said Regan.
CONTINUOUS IMPROVEMENT
With technology ever evolving and improving, the automation journey is one that is never really complete. Molycop is already working on further improvements to their grinding robot, which was only upgraded a few years ago. Their team is also investigating the benefits of automating other processes within their facility.
"Automation and investment in technology is really important—it's the key to being competitive in a global sense. Robotics are really where you can find an edge. Labour isn’t cheap in Australia and keeping the workforce safe is really important. Robots can help to manage both of these aspects. Robots allow manufacturers to pay their workers a higher wage, to perform a higher function, in a working environment that is much safer," said Regan.
"Robotics offer a higher quality of product if set up properly and give you the market premium to stay competitive. If quality is the goal, and robotics are the pathway to that goal, then Australian businesses need to take that on-board and leverage the power of automation."
"Robots are the way forward," said Regan.