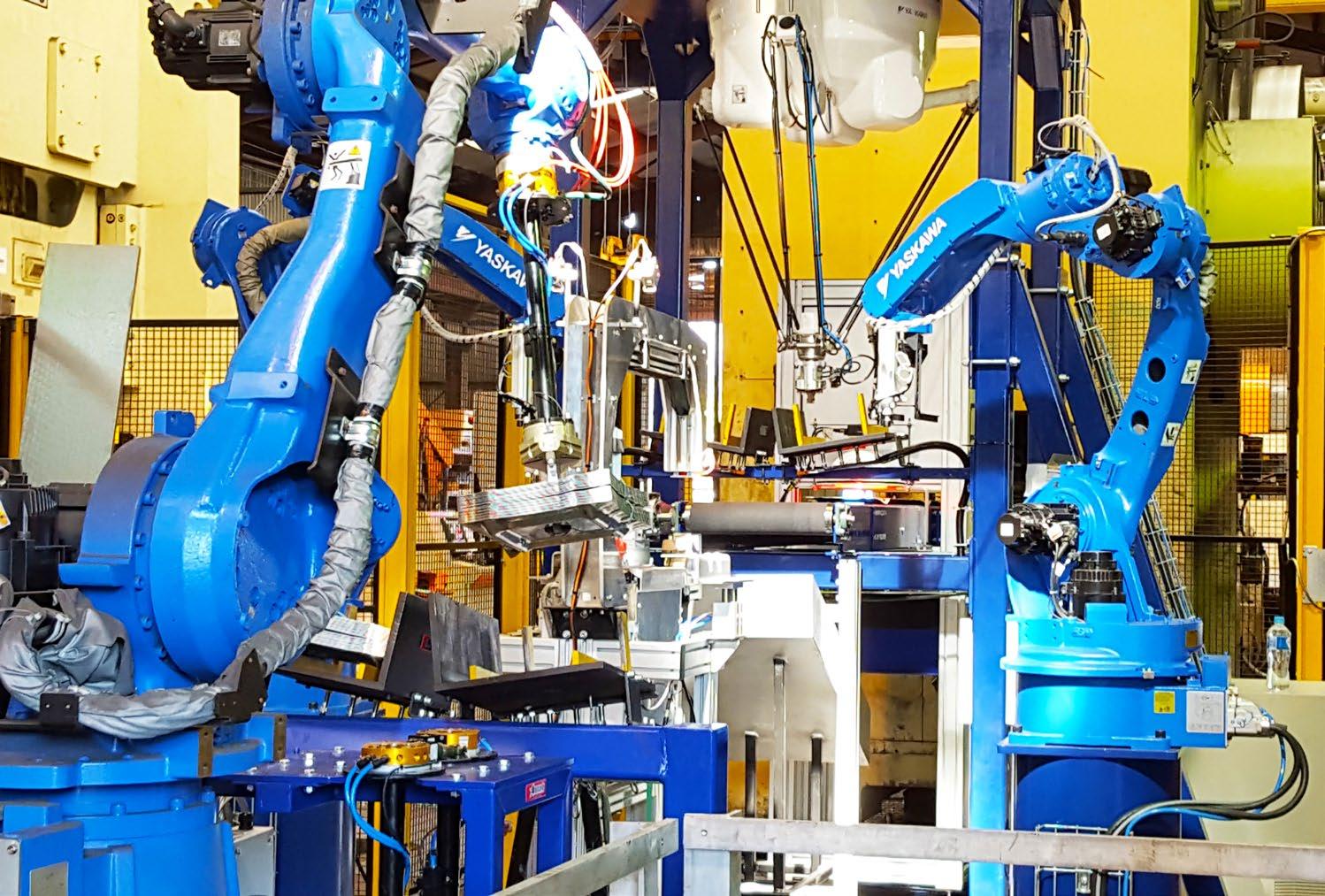
6 minute read
DSI Underground: A Holistic Approach to Lean Manufacturing
DSI UNDERGROUND IS AUSTRALIA’S LARGEST MANUFACTURER AND SUPPLIER OF SPECIALIST STRATA REINFORCEMENT AND SUPPORT PRODUCTS TO THE UNDERGROUND COAL AND METALLIFEROUS MINING SECTORS. WITH OVER 2,000 EMPLOYEES WORLDWIDE, DSI UNDERGROUND BOASTS OPERATIONS IN OVER 70 COUNTRIES ACROSS EUROPE, AFRICA, ASIA-PACIFIC AND THE AMERICAS. OVER THE LAST EIGHT YEARS, DSI UNDERGROUND HAS INVESTED IN A HOLISTIC PROGRAM OF PROCESS IMPROVEMENT INCORPORATING AUTOMATION, INDUSTRY 4.0 AND LEAN MANUFACTURING PROCESSES.
Complying with all technical standards, DSI Underground's solutions cover just about every mining application, from shaft sinking and horizontal drift excavation, through to shaft rehabilitation and emergency support.
Advertisement
DSI Underground's largest volume, and longest standing, product is their friction bolt. The friction bolt is a ground support system that consists of a high strength steel tube with a slot along its entire length. One end of the friction bolt is tapered to assist insertion into the bore hole whilst the other end has a welded steel ring to retain a bearing plate when installed into the mine roof.
The company also boasts newer products like the Kinloc bolt—a fast installation, non-resin anchored 30 tonne rock bolt. The system develops significant additional point anchor capacity via a threaded non-rotating head. The Kinloc bolt’s ability to better endure shifting ground conditions creates a new option in ground support where loading after movement is important.
NATIONAL PRODUCTION FACILITIES
DSI Underground has three production facilities in Australia. Their head office and main facility in Newcastle manufactures rock bolts for the mining and tunnelling industries. In Brisbane, their workshop produces hard rock products for the gold copper, zinc, lead markets. In Western Australia, where DSI Underground services the hard rock space, their Perth facility is focused on the production of friction bolts, plates and mesh.
As Derek Hird (Regional Chief Executive Officer, DSI Underground) explained, DSI Underground started their automation journey about seven or eight years ago, focused on productivity and competitiveness. "Our drive is keep to manufacturing in Australia. We could have offshored, but instead, we're investing in automation and are working with our suppliers to continue to be a low cost producer. With the globalisation of products and supply chains, we want to ensure that we remain globally competitive," said Hird.
"Automation and investing in technology is vital to the future of manufacturing in Australia. We need to preserve our in-country capability, particularly in the wake of COVID-19. We have seen massive supply chain interruptions, and massive issues with importing a range of products into the country."
Safety and efficiency improvements were also an important driver in DSI Underground's decision to invest in automation. "Our manufacturing processes were, and continue to be, very manual and repetitive, giving us a high conversion cost from a labour
perspective. This also gives rise to manual handling risks and hazards in the workplace," said Phil Cox (General Manager East, DSI Underground).
"We made the decision to address these issues step by step, prioritising those with the greatest opportunities for safety and efficiency improvements."
"We picked a couple of processes and, initially, our approach was to select an external contractor who specialised in automation to deliver a scope of work as a turnkey package. Unfortunately, we had limited success; the end result was not quite what we were after."
"So, we decided to recruit in-house mechanical and electrical engineers to design processes, and build and program machines to our specifications. Having internal capability has been more successful in our drive for automation. Our in-house team has access to our equipment and operators, and understands the factors that influence our products," said Cox.
"As a result, we've seen efficiency gains and improvements in the quality of our products. Automation drives a more predictable output."
"We’ve definitely seeing a decrease in working capital; there is less partially manufactured product sitting on the factory floor. This has allowed us to reduce our factory footprint," said Cox.
Hird explained that there have also been benefits for DSI Underground's clients. "Our agility, and therefore customer responsiveness, has improved. If we didn’t have the types of equipment we now have, things would take far longer to manufacture. When customers want "One of the main challenges we've faced has been obsolescence – the level and duration of support delivered by suppliers can be an issue. For instance, the controllers might not be available after a certain point in time, which means your investment is not as beneficial as first thought," said Cox.
"Using external suppliers, who lack in-depth knowledge of your product and processes is also challenging."
Hird agreed. "It's essential that you put time into really defining the scope of what you're trying to achieve. If you involve external suppliers, without fully scoping the project, it's almost impossible to achieve the desired result. It's also vital to allow realistic timeframes— it will take a lot longer than you anticipate."
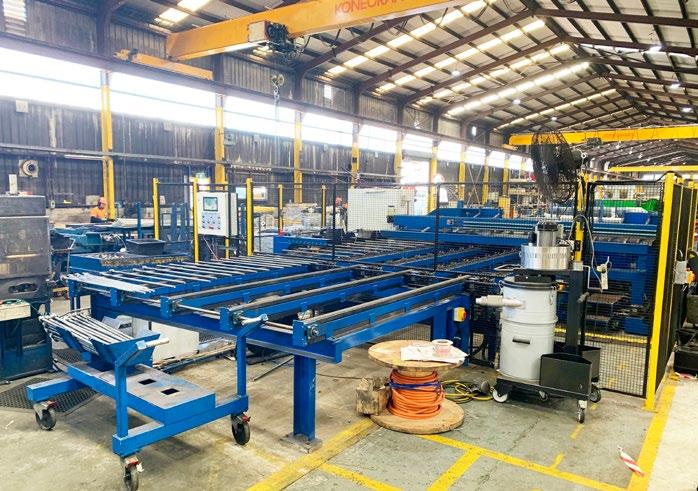
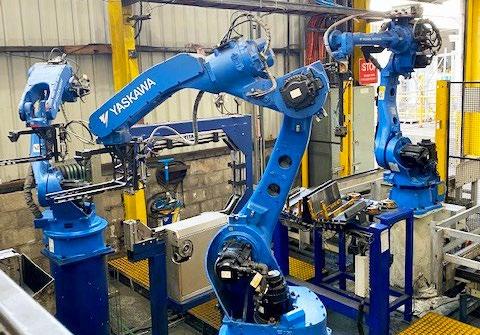
A HOLISTIC APPROACH
While DSI Underground has invested in robotic cells for packaging and palletising, as well as plate processing technology, their approach has not focused only on installing the newest, latest and greatest machinery. Instead, DSI Underground has improved its internal processes and Industry 4.0 methodologies.
"One thing we've found is that there are certain things you shouldn't automate. There will always be parts of your process that need the human touch. You should automate the things that make sense to automate— and that will have the largest possible impact—rather than the processes on the fringe that might give rise to reliability issues," said Cox.
The company has also focused on lean manufacturing processes, training over 20 members of the team on the subject.
"The education of personnel within the business is vital. The whole business has to come along for the journey. We started a big education program around lean manufacturing with key individuals, which was a massive advantage. Without the buyin of your employees, automation will fail," said Hird.
THE CHALLENGES
The automation journey hasn't all been smooth sailing for DSI Underground.
MORE THAN JUST AUTOMATION
DSI Underground is also embracing new and emerging technologies such as connectivity and ‘digital twin’ to drive cost-saving and efficiencies into their customers’ operations.
"The work we're doing in the digital space is really exciting. We recently launched a product app, which we're expanding to include a customer interface tool. Customers will be able to use the app to access product information and PDS. We're also looking at expanding the functionality of the app to include seamless product ordering. DSI Underground is also investigating digital warehousing solutions and the use of digital twins from design and installation, through to service life monitoring," said Hird.
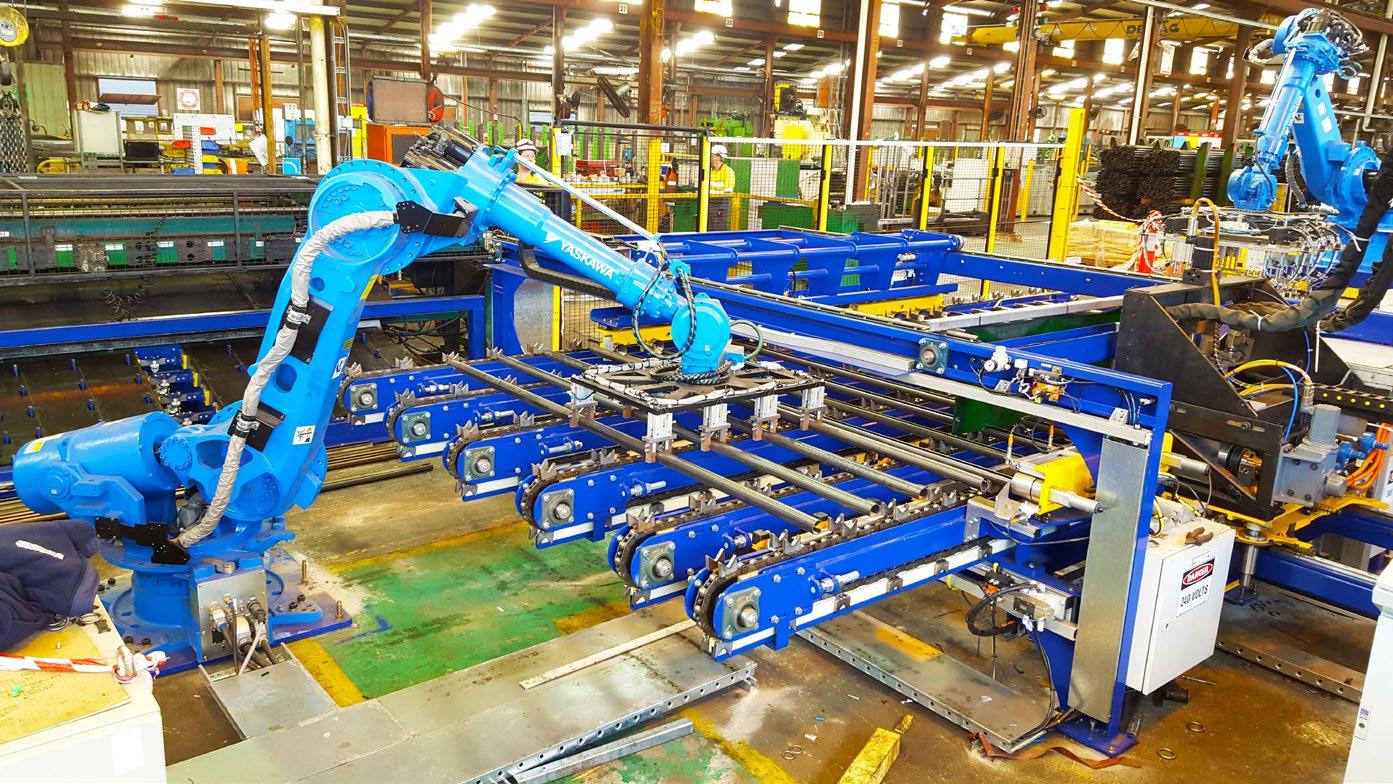