

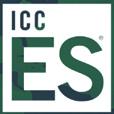






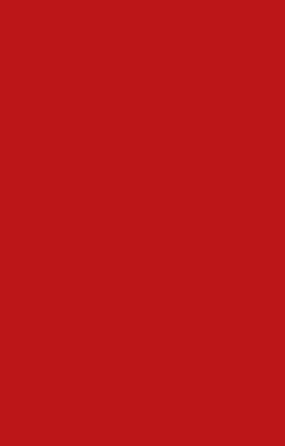




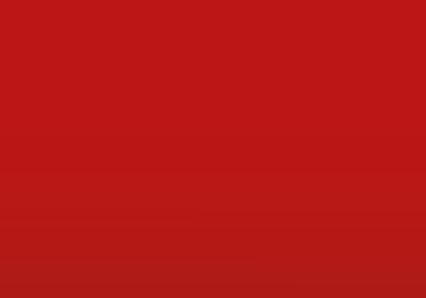
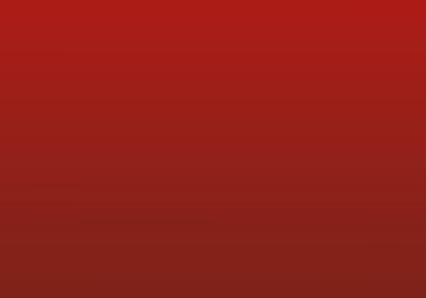
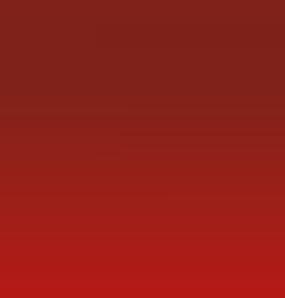
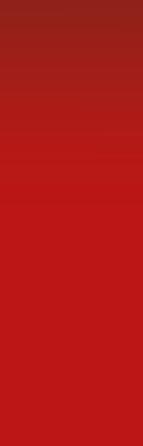
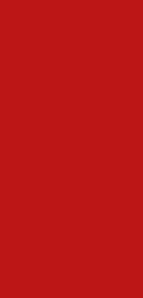


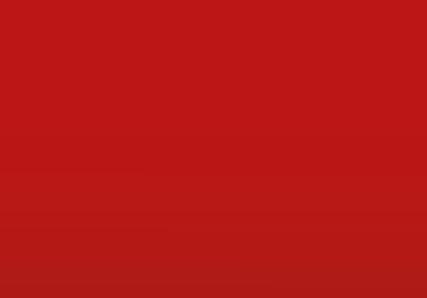
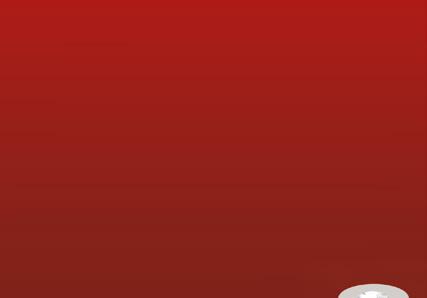

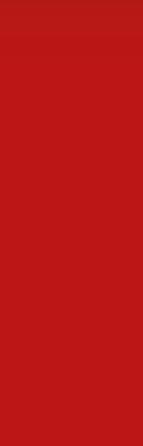

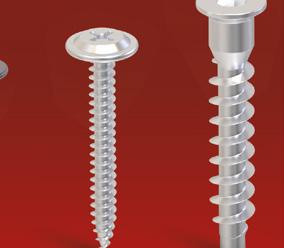
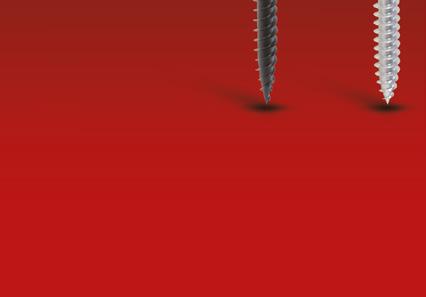
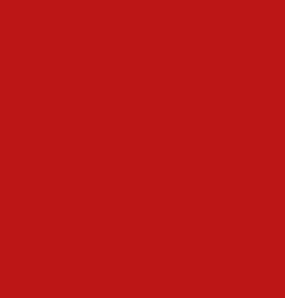
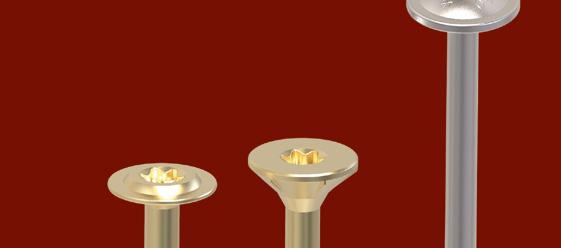
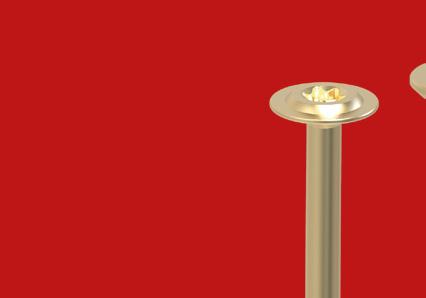
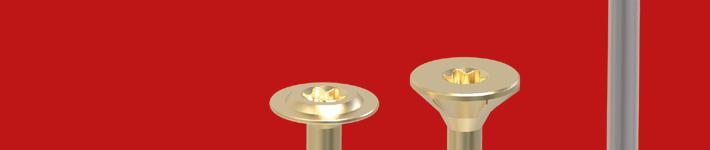
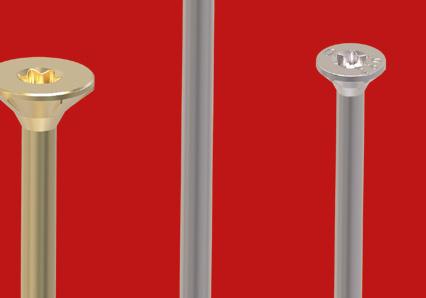
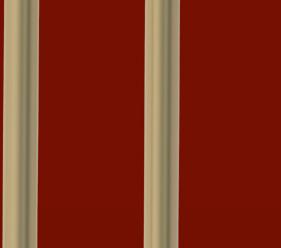
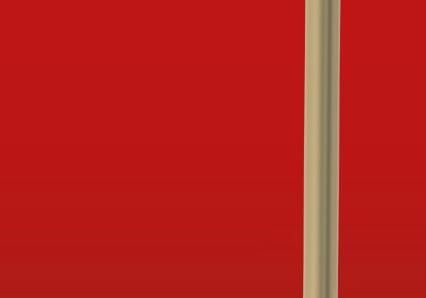
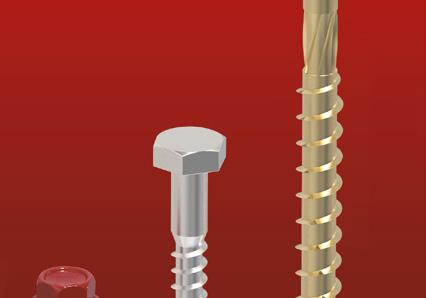
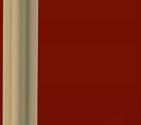
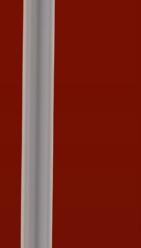
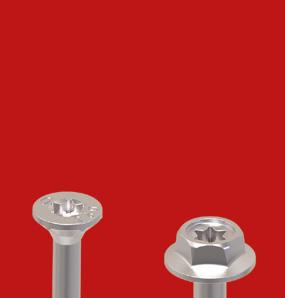


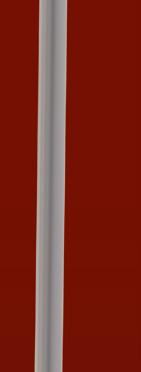
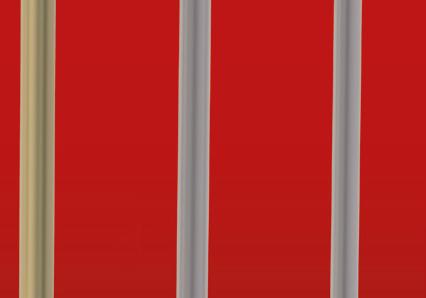
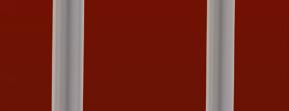
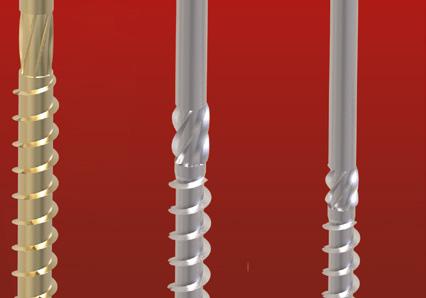
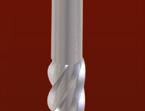

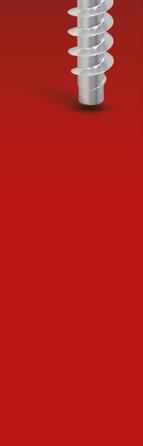
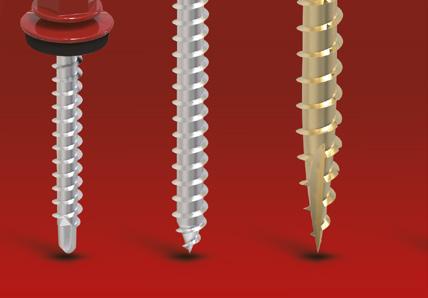

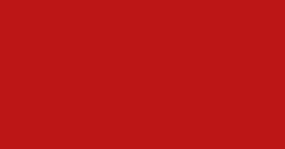
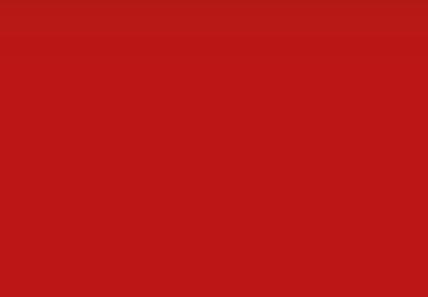
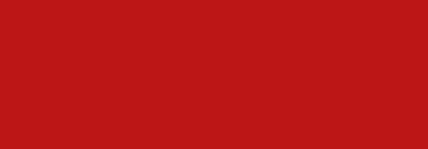
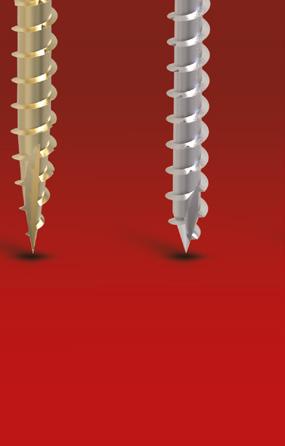
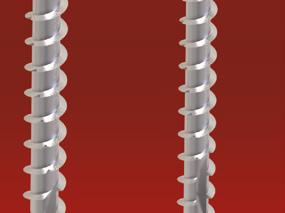
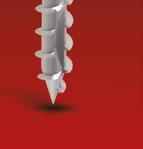
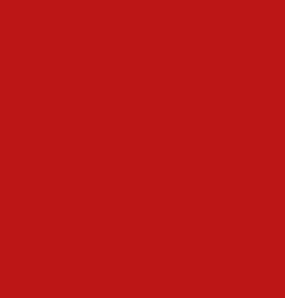
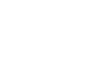

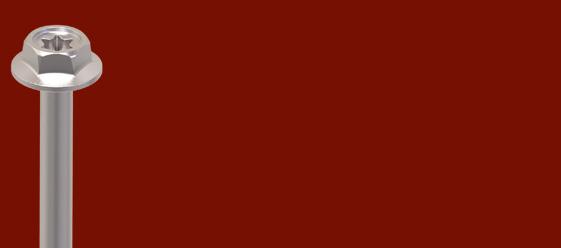


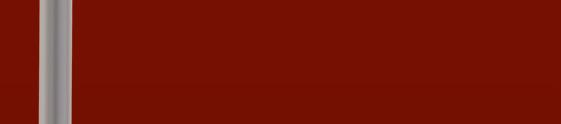
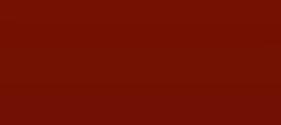


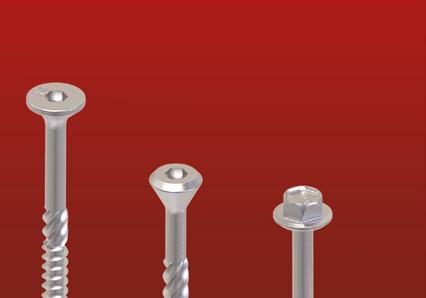
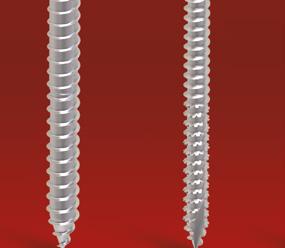

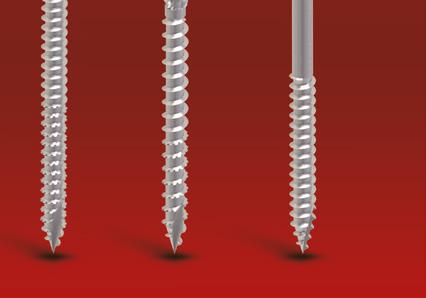


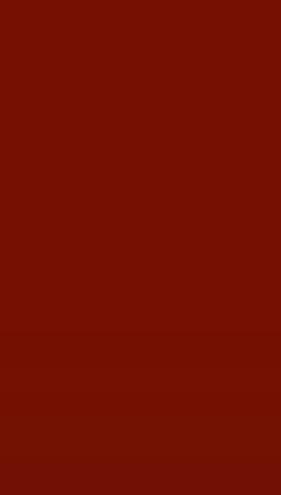
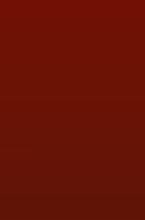
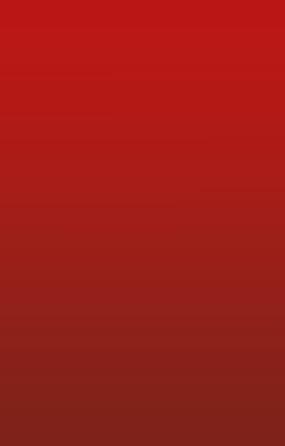
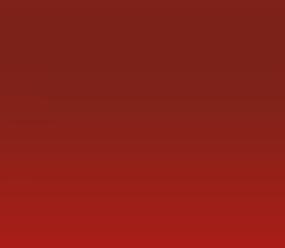
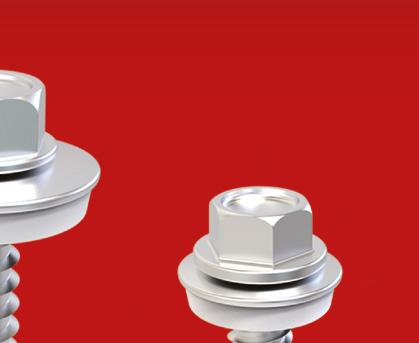

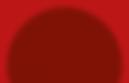
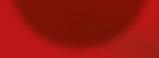
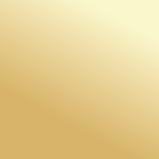


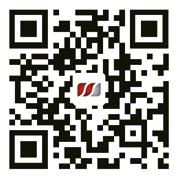
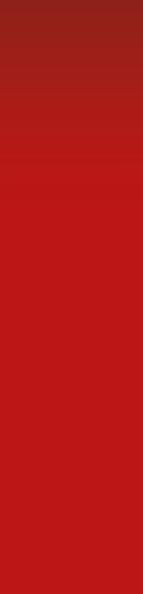
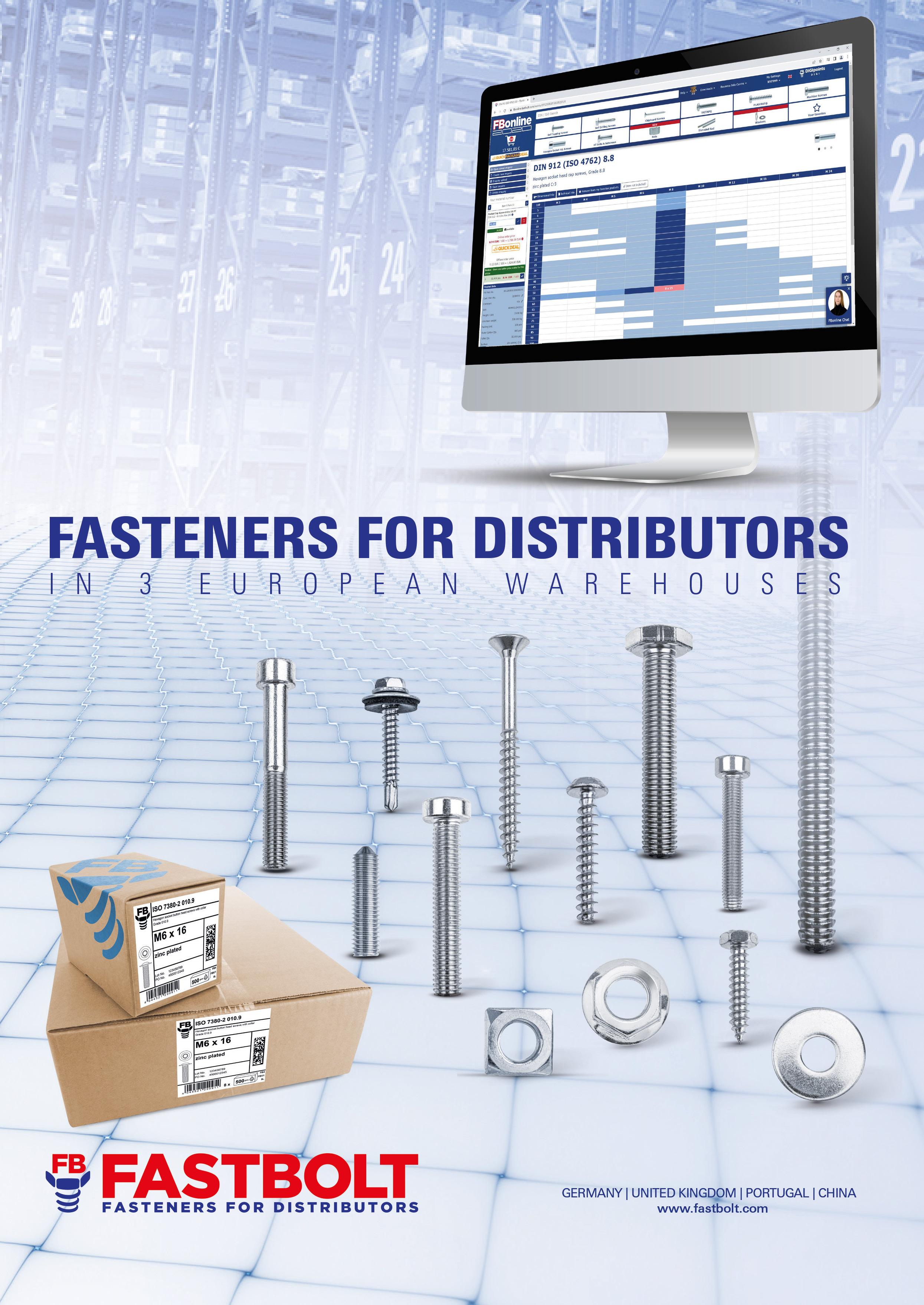
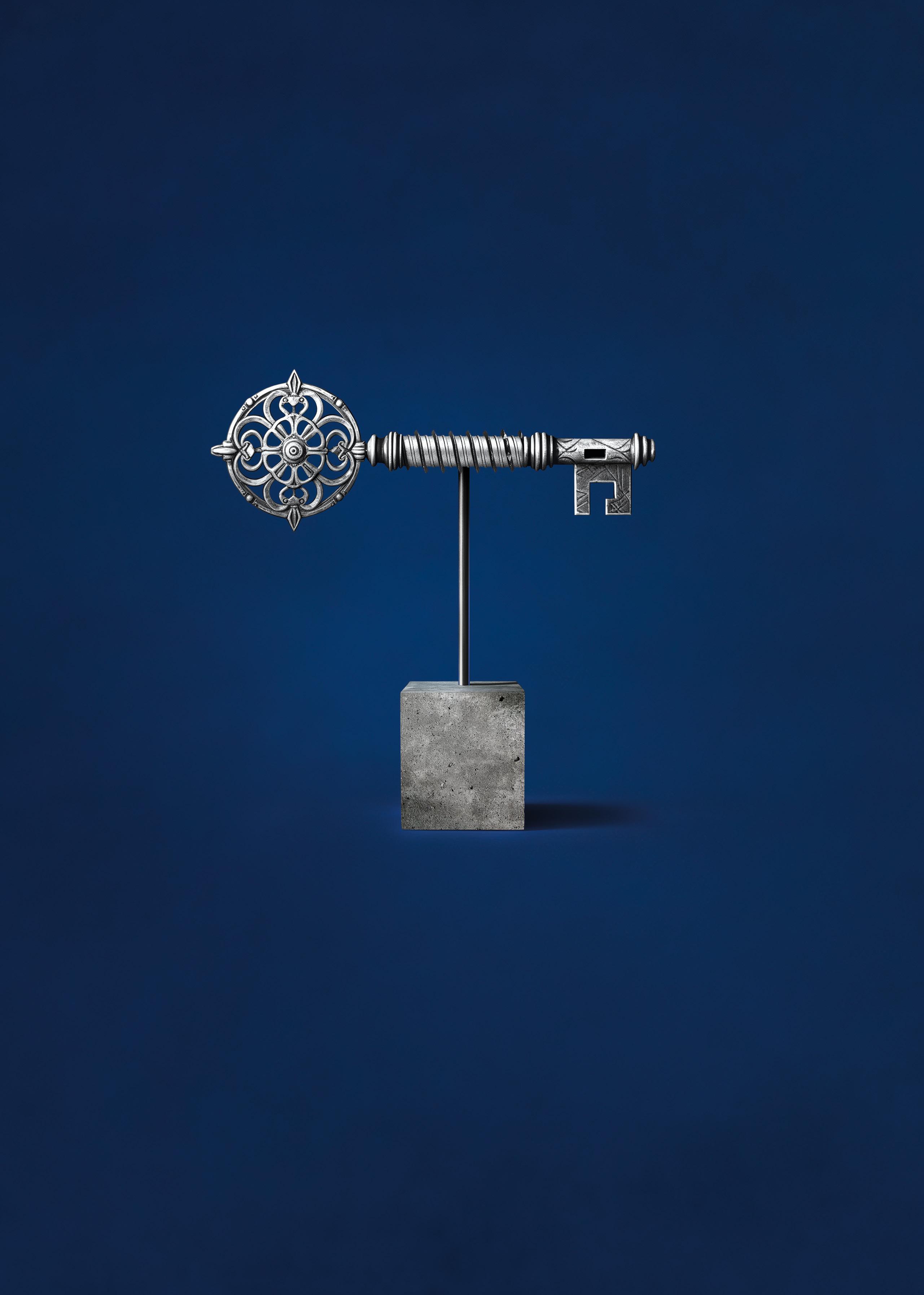


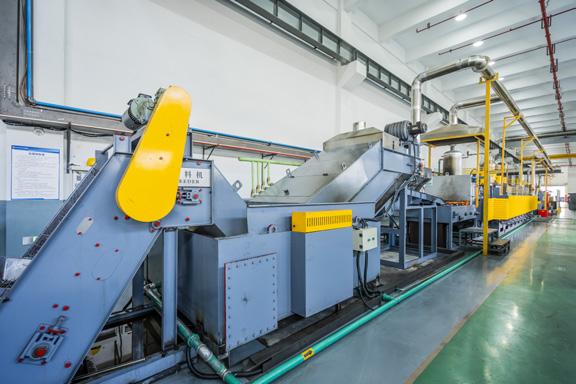

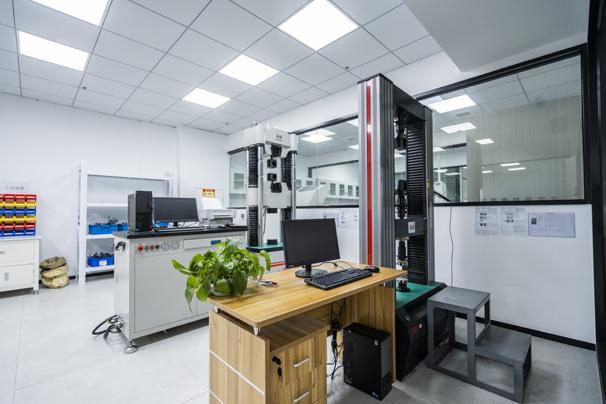


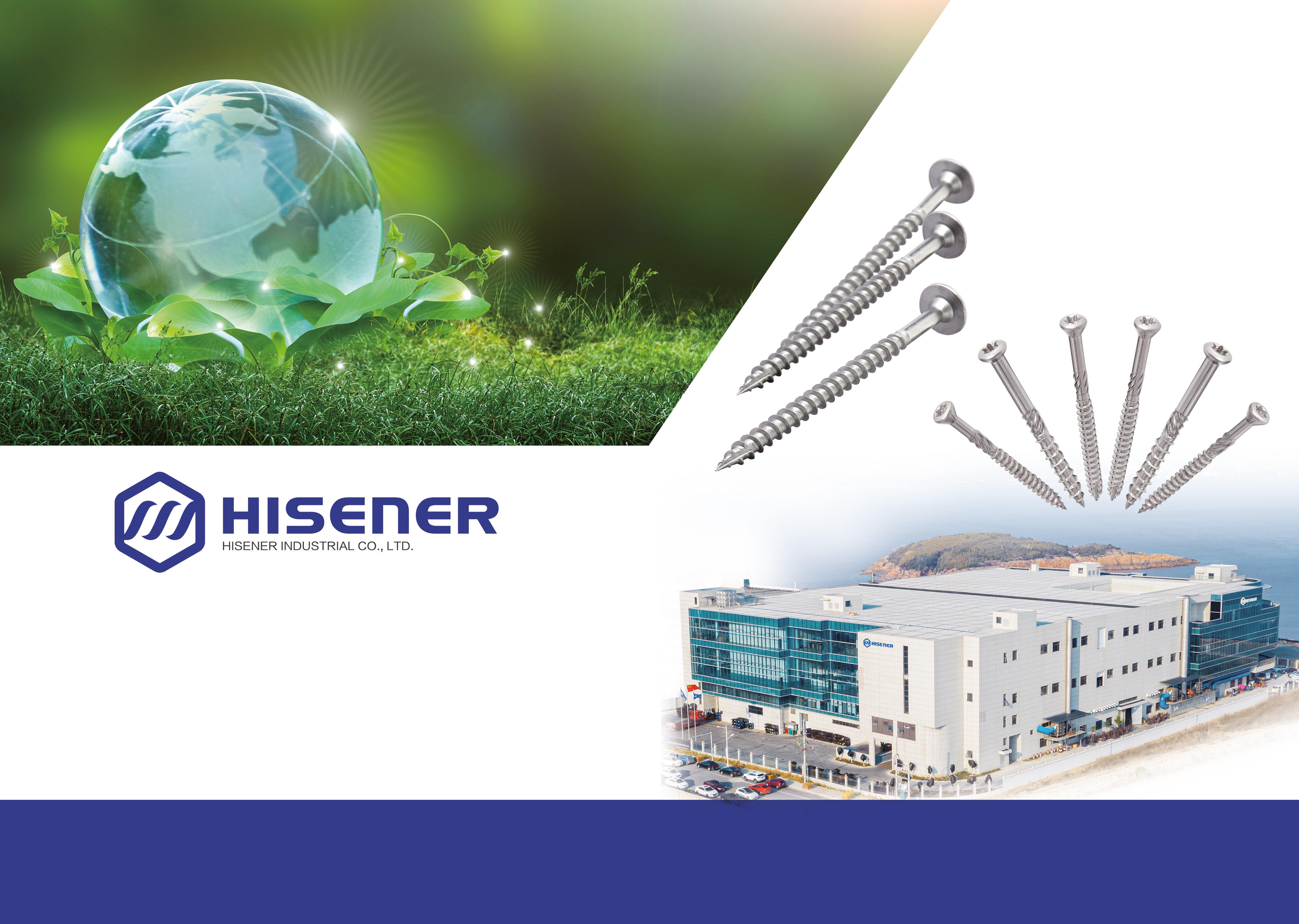
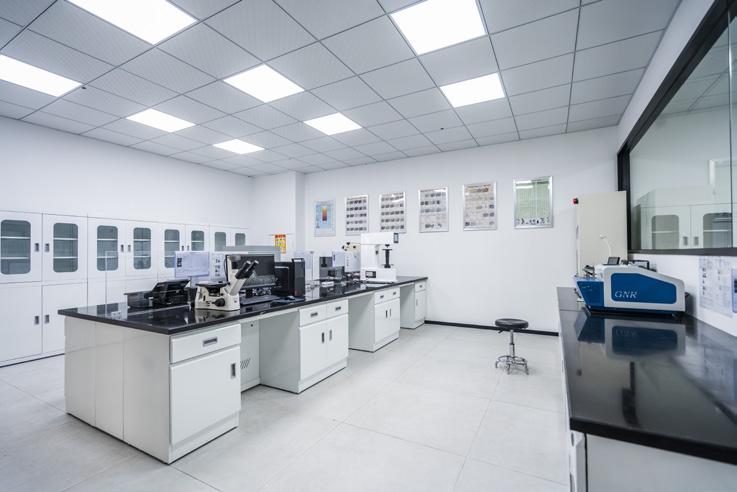
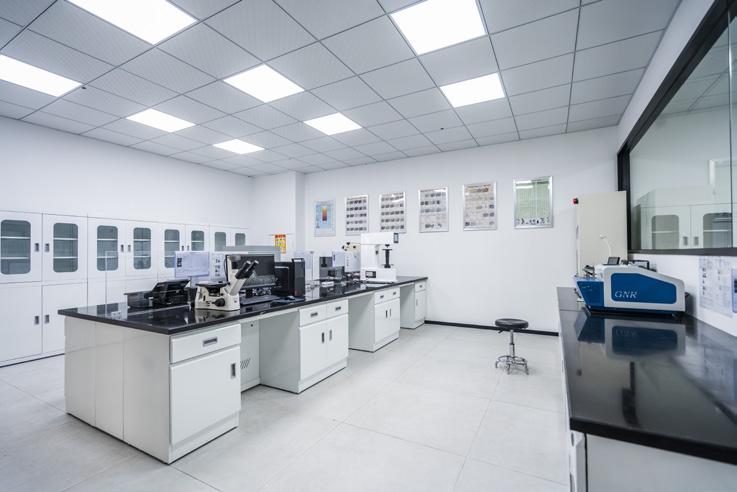
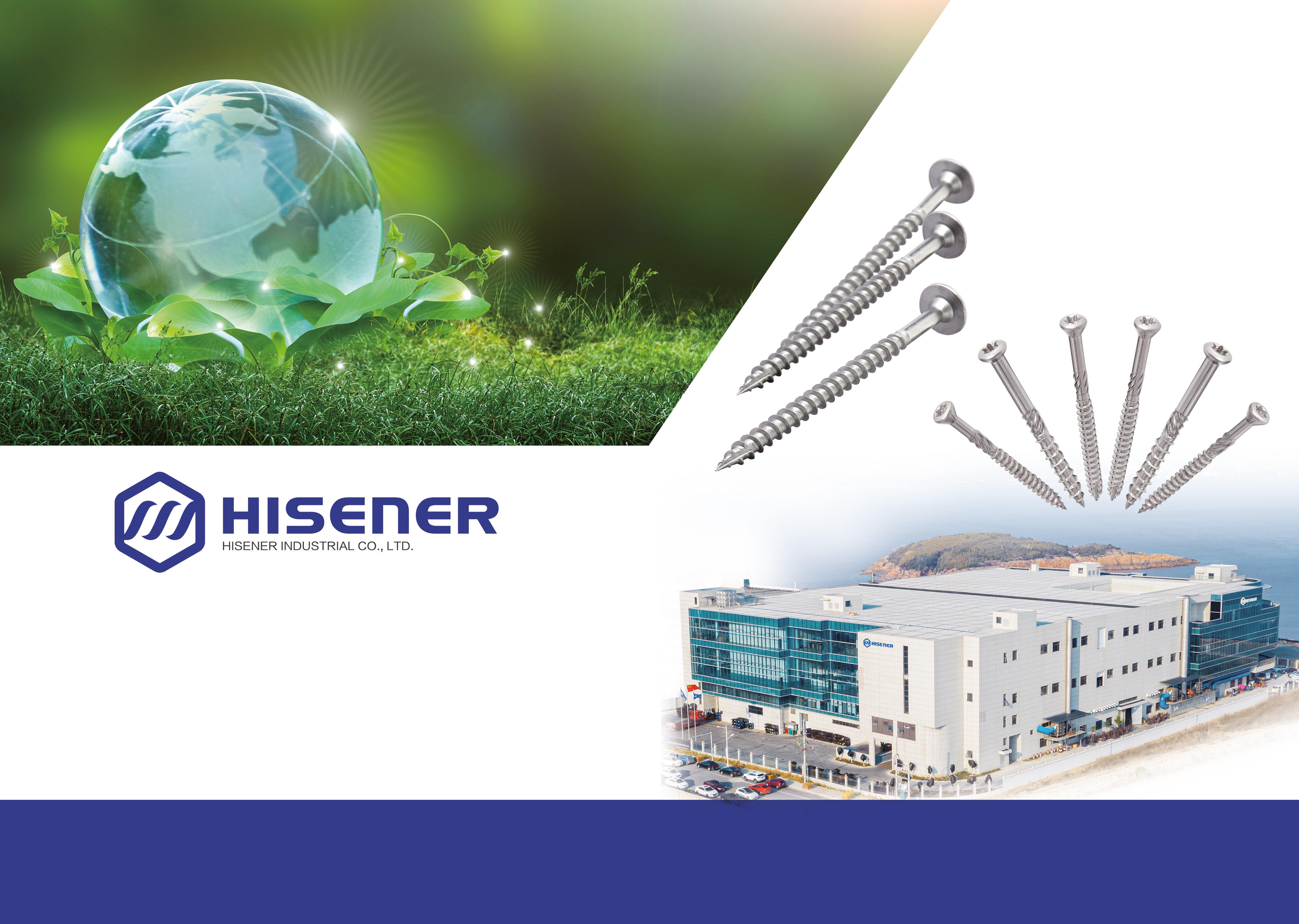
A durable and ecologically friendly woodscrew! The same bit for different diameters of woodscrews!
We believe in sustainability! The Hapax woodscrew with 4Top coating was designed with environmental consciousness in mind. The coating not only protects the screws but also ensures a longer lifetime, reducing the need for replacements and contributing to a greener, more sustainable approach to construction.
For pgb-Europe it is our daily aim to provide our customers with quality products and service to match. We have been an established supplier and manufacturer for fasteners and fixings for more than 60 years. It has been in our genes for 3 generations.
To save time and quickly find the correct screw bit, the recess for screw diameters 3.5, 4.0, 4.5 and 5.0 is unified to a Tx20 stick-fit recess. A free bit is included in each box!
Order now!
After attending the wire® Düsseldorf show in April I was reminded of the importance of a global reach and delivering quality leads and business opportunities.
Iam old enough to remember when the fastener machinery aspect of wire® Düsseldorf filled two halls, a far cry from the two thirds of only one hall it filled at this year’s show, with the remainder of the hall spring related technology. However, even with a smaller number of fastener related exhibitors, those that did exhibit reported a positive show – especially when it came to the international reach and the quality of the visitors.
It really does underline that there is simply no replacement for platforms that can deliver high-quality, genuine leads and business. As a magazine, with 25 years within the industry, it is the commitment to delivering valuable content to our readership and a ROI for our advertisers that continues to drive us forward.
A prime example of our ability to deliver this unique global insight is highlighted throughout the magazine, but especially in our Insight section – where we have news from the US, Japan, Germany, Italy, Ireland and the UK. Our Cover Story in this edition also focuses on ALFIRSTE, a Chinese manufacturer that specialises in the production of screws and anchors, with a reputation for its high-quality products and excellent service – with the company investing in new factories in Thailand, in order to continue to meet the needs of its customers when it comes to carbon steel products.
At the start of the Construction Fixings section, we have a thought-provoking article from Construction Fixings Europe that focuses on the planned concept and timeline for the transition from the existing Construction Products Regulation to the new
www.fastenerandfixing.com
Published by
Managing Director
Jamie Mitchell jamie.mitchell@verulammedia.com
Content Director
Will Lowry will.lowry@verulammedia.com
Deputy Editor Claire Aldridge claire.aldridge@verulammedia.com
Assistant Editor
Rebecca England rebecca.england@verulammedia.com
Sales Director Mac Rahman mac.rahman@verulammedia.com
Business Development Manager –Italy
Emiliano Pagliaroli emiliano.pagliaroli@verulammedia.com
Business Development Manager –DACH & Europe
Chantal Ridings chantal.ridings@verulammedia.com
Production & Design Manager Lee Duskwick lee.duskwick@verulammedia.com
version and the impact this could have on innovation within the construction sector.
Within our Manufacturing Technology section, we have an excellent feature on threading, machining and secondary operations, which highlights some of the latest machines and developments within this area. This includes how SASPI is able to constantly reengineer and update its thread rolling machines thanks to a combination of decades of know-how and its significant R&D potential; SMART Machinery talks about its innovative technological solutions and how they can be applied to thread rolling machines; Mule Technology explains how it is revolutionising thread rolling set-ups; and UTA Auto Industrial underlines how its advanced assembly machines can help optimise production processes.
Also within Manufacturing Technology, NOF METAL COATINGS GROUP reports on how it is already in the process of planning for the potential ban by the European Chemical Agency on PFAS, based on REACH, with the company using it as an opportunity to align its technical requirements on a global scale.
To add to this there is also a special Business Intelligence feature within Management + Systems that highlights some of the latest software solutions available, which can provide insight and analysis in order for companies to make more informed business decisions. Within Application Technology there is also a marine feature that looks at the challenges and solutions when it comes to fastening in marine environments.
Fastener + Fixing Magazine is a dedicated, trade–only publication which is circulated freely throughout the European trade.
Disclaimer
The Publisher cannot be held responsible or, in any way, liable for errors or omissions, during input or printing of any material supplied or contained herein although the utmost care is taken to ensure that information contained is accurate and up to date. The Publisher also cannot be held liable for any claims made by advertisers or in contributions from individuals or companies submitted for inclusion within this publication. The opinions expressed are not necessarily those of the Editor or Verulam Media.
Copyright Entire contents copyright © Verulam Media Ltd 2024. No part of this publication may be reproduced, stored in a retrieval system, or transmitted in any form or by any means without the prior permission of the publisher.
Annual subscription (6 issues) to non–trade and outside EU is €200.00
Verulam Media Limited, Office 3, 17 Holywell Hill, St Albans AL1 IDT Tel: +44 (0) 1727 743 882
Find us online:
for
Part of the Mack Brooks GroupIn the first quarter of 2024, Bossard Group recorded a decline in sales of 15.5% to CHF 257.4 million (prior year: CHF 304.5 million) in a continuously challenging market environment and as a result of the strong Swiss franc.
The decrease in local currency was 11.2%. In a quarter-on-quarter comparison, the record high comparative basis of the previous year is noticeable. As expected, demand in Europe continued to decrease, as it has since the second quarter of 2023. Sales declined by 12.2% to CHF 150 million (in local currency: -9.3%). Despite the challenging market environment, the first quarter saw continuing investments in future growth, additional efficiency and productivity improvements, including the successful rollout of the new ERP system in France.
Sales in America declined by 22.9% to CHF 65.8 million (in local currency: -18.4%). Since the record sales in the first quarter of the prior year, a normalisation of demand has been observed. With a decline in sales by 13.9% (in local currency: -5.2%) to CHF 41.6 million, weaker demand persisted in Asia as well. The appreciation of the Swiss franc was particularly noticeable in this market region. The continued two digit growth rates in India marked a gratifying exception, as Bossard benefited from nearshoring trends, a dynamic start-up landscape, and the above average growth in the focus industries of electromobility and electronics.
Based on current market observations, Bossard expects the economy to remain restrained in the first half of 2024. However, even this market environment also offers growth opportunities. Thus, the acquisition of new customers as well as the project pipeline make Bossard optimistic for the future. In addition, the continued trend towards nearshoring and the digitalisation of processes, with a focus on efficiency and productivity enhancements, further strengthens the demand for Smart Factory services in the current environment. The Group continues to stand by the communicated medium-term financial goals and the consistent implementation of Strategy 200.
Bulten Group has reported that net sales amounted to SEK 1.533 billion (€131.36 million) for the first quarter of 2024, an increase of 10.5% on the same period the previous year (2023: SEK 1.387 billion). Adjusted operating earnings totalled SEK 116 million, equating to an adjusted operating margin of 7.5%.
Bulten highlights that to achieve the strategic ambitions on the markets where it operates, and further increase innovative power, the organisation was restructured at the beginning of the quarter.
The new interdisciplinary regional structure is divided into three regions – Europe, Asia and North America – which were given responsibility for sales, manufacturing and financial results. There were also adaptations to the company’s engineering resources, in order to enhance product development and innovation.
“The year began with good sales and a sequentially improved operating margin. It is clear that efforts following the capacity challenges in Europe and the launch of a new regional organisational structure, combined with closer cost control, are starting to have an impact on financial results,” comments Christina Hallin, interim president and CEO.
“I am pleased to see the operating margin has improved on the three previous quarters, and it is satisfying too that our customer mix in automotive, along with sales in new customer groups, is contributing to stable growth. It is also worth noting that we have now had two consecutive quarters with sales in excess of SEK 1.5 billion. Again this quarter, our main priority has been to reduce the production backlog in Europe, which is adding extra costs. We have not yet caught up but have made good progress, and this can also be seen in the improved operating margin,” adds Christina.
LISI Group has achieved sales of €449.3 million in Q1 2024, up 12.5% compared to 2023. LISI AEROSPACE finished up 26.4% compared to the same period of last year, with LISI AUTOMOTIVE and LISI MEDICAL finishing down 1.2% and 6.9% respectively.
LISI AEROSPACE sales totalled €252.5 million at the end of the first quarter. Sales for Q1 in the ‘Fasteners’ business in Europe increased by 26.9% and in the US was up 22.7%, making it the strongest performer in the first quarter of 2024.
The ‘Structural Components’ business benefitted by the strong demand across the aerospace sector as a whole, with robust global air traffic levels resulting in strong aerospace market activity across all industry segments.
LISI AUTOMOTIVE’s annual revenue amounted to €157.3 million by the end of the first quarter 2024, down 1.2% on the same period the previous year. First quarter revenue was down by 0.6%, when adjusted for currency effects and excluding scope effects, which should be seen in the context of the 5.4% downturn in production for the division’s client base.
The structural change in the market is both technological and geographical with Chinese manufacturers, with whom LISI AUTOMOTIVE is forging relationships, taking market share. New product orders remain buoyant and largely follow the rapid developments in electric vehicle technology (powertrain and related systems) and new generation braking systems.
Finally, LISI MEDICAL’s sales revenue reached €39.7 million at the end of the first quarter 2024, down 6.9% on the same period in 2023 when it was at 27.7%. In addition to this negative base effect comparison, there was a one off adjustment to inventory levels. Manufacturing was also hit by a lack of raw materials. Sales revenue fell by 6.7%, when adjusted for exchange rate variations and excluding scope effects.
Despite a challenging market environment, NORMA Group still managed to achieve a robust margin in the financial year 2023. Thanks to increased levels of efficiency in production and logistics, the company achieved profitability at the prior year level despite a slight decline in sales.
Group sales in the 2023 financial year amounted to €1.22 billion (2022: €1.24 billion). The company achieved organic growth of 0.7% over the previous year. There was, however, a 2.4% burden on sales growth from negative currency effects in connection with the US dollar and the Chinese renminbi yuan. Overall, Group sales were down slightly, declining 1.6% compared to the previous year. Growth momentum came from business with joining technology for vehicles (Mobility & New Energy) in Europe.
What was at times weaker demand in key customer industries in America had a negative impact. In the first half of the year, business with water management products in the US was weaker due to extreme weather conditions. Strikes that took place and the subsequent production stoppages at major American automotive manufacturers had a negative impact on the automotive joining technology business.
“Despite the difficult market conditions, we achieved robust profitability that was in-line with our forecast. With our ‘Step Up’ improvement programme, we have succeeded in making ourselves more efficient and achieved an important interim goal. We will continue to systematically implement the programme and are now putting a stronger focus on additional growth opportunities. The recently completed acquisition of the Italian irrigation specialist Teco represents an important step forward in the expansion of our water management solutions business in Europe,” comments Guido Grandi, CEO at NORMA Group.
In the financial year 2023, adjusted earnings before interest and taxes (adjusted EBIT) totalled €97.5 million (2022: €99 million). The adjusted EBIT margin was 8% (2022: 8%). Earnings and margin were impacted by factors such as higher personnel costs. In addition to inflation related wage increases, there were additional expenses for extra shifts and temporary workers especially in the first half of the year to reduce production backlogs at European plants. Reduced material costs had a positive effect. Overall, more efficient management
of production and logistics capacities were key to achieving robust profitability. Especially in the fourth quarter, the adjusted EBIT margin of 8% was well above the level of the prior year (Q4 2022: 6.4%).
In the Americas region sales in 2023 declined organically by 4.5% year-on-year while currency effects reduced sales growth by an additional 2.4%. Overall, sales in the region reached €534.5 million (2022: €574.2 million), down 6.9% compared with the previous year. In the first half of the year, the US water business was weaker than in the same period of the previous year due to a weather related one off effect, but recovered again over the course of the year. Business with joining technology for industry applications declined. Sales of joining technology for passenger cars and commercial vehicles were also lower, partly as a result of strikes at US vehicle manufacturers that lasted several weeks.
In the EMEA region, sales in 2023 grew organically by 5.7%. Negative currency effects reduced growth marginally by 0.5%. Overall, sales in the region grew by 5.2% compared to the previous year to €514.7 million (2022: €489.2 million). The Mobility & New Energy business with joining solutions for cars with all types of drive systems increased significantly by 6.8%. In Industry Applications, sales rose by 0.6% thanks to improved product availability.
In the Asia-Pacific region, there was organic sales growth of 4% in 2023. Demand for joining technology from Chinese automotive manufacturers in particular increased compared with the previous year, leading to higher business volumes in the region. The sales increase was, however, offset by negative currency effects (-7.4%), meaning that sales in the region fell by 3.3% overall to €173.6 million (2022: €179.6 million).
Scell-it (UK) has expanded its presence in the UK by acquiring both Rivco Ltd and Kamtech Fasteners (ARK brand), strengthening its position as one of the leading distributors nationally of construction fixings, rivets, rivnuts and setting tools. This will further enhance the wide Scell-it (UK) Group brand range with names such as ARK, Huck®, FAR, RIVIT and Lobster.
Kidderminster-based Rivco was established in 1994 and is a longstanding player in the UK market, bringing an existing turnover of circa GB£3 million (€3.4 million) and a workforce of ten sales and warehouse staff. This acquisition complements the direction and vision of the Group’s growth strategy.
Kamtech Fasteners, based in West Bromwich, was established in 2015 and has a customer base that perfectly aligns with that of Scell-it (UK). This acquisition brings a further GB£1.5 million of turnover and four sales and warehouse staff to the newly formed Group. Steven Auld, the original majority shareholder of both acquired businesses, will continue with the Group in his new role as joint managing director, supporting the Group’s staff and customers.
Gary Moseley, joint managing director and one of the founding shareholders of Scell-it (UK), says: “We are thrilled to announce our acquisition of Rivco and Kamtech Fasteners, both businesses have
excellent reputations in the UK and align perfectly with the existing Group. From initial discussions it was clear that this acquisition would fit in perfectly with our existing culture and help strengthen our position in the marketplace.”
“These acquisitions reinforce Scell-it (UK) Group’s dedication to providing unparalleled supply at competitive prices to meet the precise needs of our customers. We will continue to look for opportunities to grow and Steven and I are excited to embark on this journey with both teams, leveraging our combined expertise to ensure a seamless integration for all involved.”
European partners, Scell-it SAS, based at the Group’s headquarters in France, echoes this growth vision. With established operations in Poland and Italy, it actively seeks further European acquisitions, propelling the total Group revenue beyond the current €50 million mark.
Nord-Lock Group, a global leader in bolting and engineering solutions, has announced Daniel Westberg as its new Chief Executive Officer. Daniel will assume his responsibilities as CEO on 1st August 2024.
Daniel comments: “I am honoured and excited to take on the role of CEO at Nord-Lock Group, a company with a rich legacy. The Group is on an exciting journey, and I look forward to unlocking new horizons and developing the Group and its four technology brands towards even greater success.”
For more than 20 years, Daniel has held various executive level roles within SKF Group and its different subsidiaries, both in Sweden and abroad, most recently Daniel served as president and CEO at Ewellix.
“The appointment of Daniel as CEO marks an exciting chapter for Nord-Lock Group and Latour. Daniel has proven to drive results and has consistently propelled the businesses he has led forward. With his international industrial background, strong commercial and technical understanding, Daniel brings a fresh perspective and strategic vision to the organisation,” says Johan Menckel, chairman of the board for Nord-Lock Group.
Daniel holds a master of science in mechanical engineering, and his strong technical acumen, along with a passion for innovation, has been instrumental throughout his career. Having lived and worked in Canada, Germany, and France, Daniel has an extensive global background. These diverse cultural encounters have brought enriched perspectives and provided valuable insights that Daniel now brings into his role as CEO at Nord-Lock Group.
First quarter revenues for Stanley Black & Decker reached US$3.9 billion (€3.6 billion), down 2% versus the previous year – as growth in DEWALT and Engineered Fastening was more than offset by lower infrastructure volume and muted consumer and DIY demand.
Donald Allan Jr, Stanley Black & Decker’s president and CEO, comments: “Our first quarter performance was the result of consistent, solid execution and continued progress against key operational objectives. We continue to see significant value creation opportunities tied to our strategic business transformation, and we remain focused on disciplined execution of our strategy. Looking forward, we expect mixed demand trends to persist across our businesses in 2024, and we are driving supply chain cost improvements designed to expand margins, deliver earnings growth and generate strong cash flow. At the same time, the long-term growth and market share gains we are focused on achieving, will be driven by introducing exciting new products within our most powerful brands – designed to deliver enhanced productivity for end users. We are funding growth investments intended to further accelerate innovation and differentiated market activation to capture these compelling long-term opportunities.”
He continues: “Stanley Black & Decker continues to become a more streamlined business, built on the strength of our people and culture, with an intensified focus on our core market leadership positions in Tools & Outdoor and Industrial. I am confident that by executing our strategy, we are positioning the company to deliver higher levels of organic revenue growth, profitability and cash flow to drive strong long-term shareholder returns.”
Patrick D. Hallinan, executive vice-president and CFO at Stanley Black & Decker, adds: “The actions we are taking to advance our strategic transformation are progressing successfully, and despite the tepid market backdrop so far in 2024, our profitability remains on an upward trajectory. We will continue our disciplined approach to cost management as we drive toward our target of 35% adjusted gross margins – while funding additional organic revenue growth investments. The organisation is focused on delivering margin expansion, cash generation and balance sheet strength, while working together to position the company for long-term growth and value creation.”
Owlett-Jaton has achieved certification to ISO 45001:2018, the Occupational Health and Safety Management System from the British Standards Institution (BSI), for its head office in Stone, Staffordshire.
ISO 45001 provides a framework to allow an organisation to proactively and continuously build and improve safety performance and culture to reduce risk. It demonstrates an organisation’s commitment to a safe, healthy and sustainable workplace. With a constant review and improvement process, established health and safety initiatives look to mitigate risks and improve operational performance.
“As a wholesaler, we understand our responsibility to protect the wellbeing of our employees and wider stakeholders. Our teams have worked hard to achieve accredited status. Attaining this global benchmark for occupational health and safety is a major achievement for all at Owlett-Jaton. Health and safety is always the first point on our agenda, and this accreditation recognises the team’s hard work
and dedication. We plan on continuing to improve how we operate,” commented Gareth Phillips, facilities and accreditations manager at Owlett-Jaton.
This is Owlett-Jaton’s third BSI certification, having already achieved certification to ISO 9001, the international standard for quality, and ISO 14001, the international standard for environmental management.
“We value our people and their health and safety is a priority. By ensuring our business meets the standards set out by ISO 45001 we can reduce risk and provide a safe working environment for all. The ISO 45001 accreditation is something we are very proud of as a business. We always strive to provide the highest standards of quality while maintaining the highest standards of safety and environmental responsibility,” adds Ian Doherty, CEO at Owlett-Jaton.
The Lesjöfors Group is increasing its global logistics network with the opening of a purpose-built distribution and sales centre in Haaksbergen, the Netherlands, to enable faster deliveries across Europe.
Lesjöfors Stock Spring Europe will service Lesjöfors’ extensive standard stock range across continental Europe, expanding the Group’s express delivery service already available in the Nordics. This latest investment is part of a strategic programme that has seen the Lesjöfors Group grow from a €250 million turnover company to €400 million in the last three years.
“Expanding our sales and distribution network into Europe is very exciting as we are now able to respond to customers’ demands for same day deliveries across our standard range of springs, gas springs, pressings, wire forms and adjacent products. Strengthening our market position in our rapidly expanding standard range, we’re
looking to this new logistics hub to secure our ambitions to be the number one supplier of quality standard items in the industry,” comments Ola Tengroth, CEO at the Lesjöfors Group.
Henrik Furhoff, head of business area standard at Lesjöfors Group, adds: “Our objective is to significantly accelerate the growth of our standard items across Europe and this investment is a crucial enabler for that. Our goal is to deliver the widest range of standard stock items, the best customer service and the fastest delivery. This new development continues the Lesjöfors Group’s ongoing expansion, enhancing our customers’ accessibility and convenience in our standard range.”
CELO, a global manufacturer of screws and fixings, has acquired Sistema Masa, a well reputed Spanish company renowned for its technical excellence and its innovative approach to the design, manufacture and installation of ventilated façade systems.
Sistema Masa was established in 1994 and has been designing and installing cutting edge systems for both national and international markets. With over 15,000 projects, Sistema’s international footprint extends to more than 50 countries, establishing it as a trusted partner for projects of all scales and complexities.
Both CELO and Sistema Masa were aligned in providing high-quality and time saving solutions that reduce overall costs. In fact, the new acquired portfolio includes six CE-certified façade mounting systems, as well as a premium products range that delivers remarkable efficiency gains in installation time, outpacing competitors in the industry.
To cope with an increasing demand for complex requirements in terms of sustainability, safety, protection, efficiency, and aesthetics, CELO Façades Technology will become CELO’s unit to support planners, architects, builders and façade contractors in developing building envelopes with market expertise, high-quality product systems, with a full customer service approach. Also, all systems related to structures for ventilated façades will use the commercial brand ‘Masa Ventilated Façade Systems’ as a guarantee of quality and heritage.
The acquisition of Sistema Masa not only contributes to increasing CELO’s business activities and offerings toward new business areas but also supports its commitment to promoting sustainable construction practices that meet the increasing demand for energy efficient buildings.
voestalpine has melted the first high-quality ‘green’ wire rod from hydrogen reduced pure iron and scrap at its site in Donawitz, Austria.
The hydrogen reduced pure iron was produced in the Hyfor pilot plant, while the landmark melting was carried out in the Group’s own Technikum Metallurgie research facility – a unique, small but complete, steel plant. The CO 2 reduced steel was further processed in the wire rod mill to produce roller bearing steel, which is characterised by its particular hardness and wear resistance. The production of high-quality, CO 2 reduced steel grades is one of the biggest technological challenges in the transition to ‘green’ steel production.
greentec steel is an ambitious and feasible phased plan with which voestalpine can make a valuable contribution to achieving the climate goals. “We have already made a successful start on our path to ‘green’ steel production and are advancing quickly with the construction of two arc furnaces powered by ‘green’ electricity in Linz and Donawitz. Parallel to this, we are researching various breakthrough technologies with partners from industry and science. The first ever melting of hydrogen reduced pure iron and its further processing into high-quality wire rod is a historic milestone,” comments Herbert Eibensteiner, CEO at voestalpine AG.
Hyfor is a joint research project of Primetals Technologies, voestalpine, Montanuniversität Leoben and K1-MET, with the goal of researching the use of hydrogen to reduce fine iron ore. In the future, the resulting hot sponge iron could be melted down in an electric arc furnace or used to produce hot briquetted iron (HBI).
“The Technikum Metallurgie provides us with an ideal test environment to quickly adapt our steels to the needs of our customers and to changed market requirements. I am very pleased that we are now also doing pioneering work in ‘green’ steel production and would like to thank all the researchers and employees for their commitment,” states Franz Kainersdorfer, head of the metal engineering division and member of the management board at voestalpine.
At the Technikum Metallurgie, voestalpine is conducting research into the production of new high performance steels, for subsequent processing into special rails, high-quality wire rod, as well as heavy-duty oil field pipes. The product development involves a CO 2 reduced route – the input material is melted using electricity from renewable energy sources.
In a first step from 2027, voestalpine will reduce its CO 2 emissions by up to 30% by partially replacing its current coal-based blast furnace technology with electric arc furnace technology – powered by ‘green’ electricity. This represents almost 5% of Austria’s entire annual CO 2 emissions, making greentec steel the largest climate protection programme in Austria.
The Group is aiming for carbon neutral steel production by 2050 and is researching intensively on several new processes, as well as investing in pilot projects that explore new pathways in steel production.
4PS by Hilti, a software supplier for the construction industry, is continuing its international growth course with the launch of 4PS Construction Software AB in Sweden. A team of dedicated experts will support the Swedish construction industry in digitising, optimising and automating business processes from Gothenburg.
Founded in the Netherlands in 2000, and part of the Hilti Group since 2023, 4PS is a leading player in the Dutch market and has since expanded its operations to the UK, Belgium and Germany. With more than 70,000 daily software users, 4PS has built a strong reputation for its in-depth expertise in the industry. This launch in Sweden confirms 4PS’ ambition to become an international market leader as a digitalisation partner for the construction industry.
“The start of 4PS in Sweden is a great opportunity for us to support the construction industry in Sweden with our innovative software solutions. We are very pleased that, strengthened by the Hilti Group, we can focus on realising our international growth ambitions. This launch in Sweden brings 4PS and Hilti closer to the goal of becoming the leading digitalisation partner in Europe,” comments Johan Bakker, director sales and marketing at 4PS.
“Our Cloud software solutions enable construction companies to make their business processes more efficient and sustainable. With 4PS, the Swedish construction industry can rely on software solutions from a supplier with a long-term orientation and a strong commitment to innovation,” adds Paula Middelkoop, director of product and development at 4PS.
A team of experts from 4PS International will accompany the start-up in Sweden and build a local team to support the Swedish construction industry in further digitalisation from Gothenburg.
Hafren Security Fasteners is commemorating 25 years of exceptional dedication and invaluable service from its esteemed colleague, Mike Williams – a significant milestone for a valuable member of TeamOrange.
Since joining Hafren on 3 rd May 1999, Mike has been a committed pillar of the organisation, embodying the company’s core values and mission of ‘stamping out the impact of theft globally’. Mike’s journey with Hafren Security Fasteners has been nothing short of remarkable. His unparalleled attention to detail and unwavering commitment to accuracy have made him an indispensable asset to warehouse operations.
“As the mastermind behind our warehouse organisation, Mike has meticulously ensured that every aspect of our environment thrives under his care, setting the gold standard for efficiency and excellence,” comments Hafren.
Beyond his professional achievements, Mike is also a passionate cycling enthusiast and a courageous cancer survivor, embodying resilience and determination in every facet of his life. His ability to overcome challenges with grace and perseverance serves as an inspiration to us all.
“On this momentous occasion, TeamOrange extends our heartfelt gratitude to Mike for his unwavering dedication, loyalty and support over the past 25 years. As we reflect on his remarkable journey with us, we are filled with immense pride and gratitude for the invaluable contributions he has made to the success of Hafren. Looking ahead, we are confident that Mike’s expertise, leadership and unwavering commitment to excellence will continue to shape the future of our organisation for many years to come. As we raise our glasses in salute, here’s to more years of ‘stamping out the impact of theft globally’ alongside our esteemed colleague.”
Harrison & Clough has appointed Malcolm Becker as national development manager, bringing with him over 30 years of experience to strengthen customer relationships and build product ranges to be supplied across the UK.
Beginning his career with Harrison & Clough as a warehouse operative 28 years ago, Malcolm quickly progressed through the business into a sales position as a product demonstrator and then up to head of product management. Malcolm has gained considerable experience across a variety of roles that involve having hands-on logistic, supply chain and key product expertise. After a brief stint away from Harrison & Clough, Malcolm seized the opportunity to return to his new role.
He now plans to apply his holistic knowledge of the fastener market, work closely with business development teams, expand product lines, and enhance merchant knowledge of its products with a particular focus on Metalmate®
“By leveraging my three decades of experience within the fastener and fixing industry, I plan to pass on my product expertise
to our merchants, better familiarise them with the specifics of our products and help them to boost customer satisfaction and ultimately drive sales. Whilst I plan on strengthening relationships with existing accounts and expanding on those opportunities, I will also jump on new market research to identify the most efficient routes to market,” says Malcolm.
Malcolm strives to solidify new and expanding ranges of fasteners and fixings by applying his product expertise to best match items to suit client needs. Mark Dorrington, business development director at Harrison & Clough, adds: “Malcolm’s long-term understanding of Harrison & Clough sets him to be a sales driving force. I am excited about the growth of our sales team and the wealth of expertise Malcolm will contribute to our collective knowledge.”
Sonderteile / Sonderwerkstoffe
Passengers aboard an Alaska Airlines plane that made an emergency landing after a Boeing fuselage panel blew off this year, have started to receive letters from the US Federal Bureau of Investigation identifying them as possible victims of a crime, Reuters reports.
The move indicates that the US Justice Department’s criminal investigation into Boeing is ramping up. “As a victim specialist with the Seattle division, I’m contacting you because we have identified you as a possible victim of a crime,” reads the letter from the FBI’s Seattle office. The letter says the incident is under criminal FBI investigation but adds that such inquiries can be lengthy and that “for several reasons, we cannot tell you about its progress at this time”.
The catastrophic failure occurred 5th January 2024 when a door plug blew off a new Alaska Airlines Boeing 737 Max 9 at 16,000 feet, imperilling 171 passengers and 6 crew members. The National Transportation Safety Board determined that the door plug was missing four bolts meant to secure it in place. However, a month after the NTSB determined that the bolts were missing, the agency is no closer to questioning any of the 25 door crew employees involved.
“To date, we still do not know who performed the work to open, reinstall, and close the door plug on the accident aircraft,” NTSB Chair Jennifer Homendy stated. “Boeing has informed us that it is unable to find the records documenting this work. A verbal request was made by our investigators for security camera footage to help obtain this information; however, they were informed the footage was overwritten.”
The seasonally adjusted Fastener Distributor Index bounced back to growth in February 2024 with a reading of 50.5 amid stabilizing demand. Following solid month-over-month improvement in January, the FDI saw further modest sequential improvement in February.
When looking at the underlying drivers, the FDI paints a slightly more mixed picture as three of the four components (sales, employment and customer inventories) were stable to lower from the previous month. Only the supplier deliveries index improved, which drove the overall month-over-month improvement in the headline FDI.
Looking at the sales index, 31% of respondents indicated sales came in above seasonal expectations, which was down versus the 44% in January, but essentially matched the 30% average over the past year.
The Industrial Fasteners Institute has elected Dan Curtis of MacLean-Fogg Company to lead the board as chair, along with Larry Spelman of J.H. Botts LLC as vice-chair and Gene Simpson of Semblex Corporation as ex-officio chair.
Founded in 1931, the Industrial Fasteners Institute (IFI) represents North American manufacturers of mechanical fasteners and formed parts –who are key suppliers to customers, government and the public –with IFI looking to advance the competitiveness, products and innovative technology of member companies.
New division chairs included Division I: Industrial Products – Chair Attsie Hashimoto, Unytite Inc; Division II: Aerospace Products – Chair Doug Carlton, Click-Bond Inc; Division III: Automotive Products – Chair John Medcalf , Agrati Inc; and Associate Suppliers Division: Chair Herb Gottelt, Metal Resource Solutions.
indfast.org
The Fastener Training Institute (FTI) has announced Birmingham Fastener will sponsor its two remaining Fastener Training Weeks in 2024 – the next being in Chicago, Illinois, from 19th – 23rd August and the final one in Cleveland, Ohio, from 18th – 22 nd November.
FTI is the leading non-profit provider of fastener product and technical training and expertly instructed courses. FTI’s flagship training, Fastener Training Week, is a week-long program dedicated to enhancing fastener knowledge across the industry, recognizing those who complete the course and pass a final exam as a Certified Fastener Specialist™. The week includes hands-on exercises, case studies, networking opportunities, learning labs, as well as plant tours to witness all stages of the manufacturing process.
Jo Morris, marketing director at FTI, commented: “Birmingham Fastener’s mission to provide customers with quality products aligns with our commitment to train the industry that uses them. We are thrilled to have its support.”
Birmingham Fastener, based in Birmingham, Alabama, is a leading manufacturer and distributor of fasteners. “With 16 locations from New York, to California, to Mexico, our company is fortunate to have the very best team and best customers in the industry. Our heavy foundation in manufacturing, and broad offering in distribution, have allowed us to become a renowned partner for companies in the Americas. We are forever indebted and will always be supportive of the fastener industry, as it is who we are at Birmingham Fastener,” says Rodney Holmes, vicepresident of sales for Birmingham Fastener. “Fastener Training Institute is dedicated to keeping our industry safe with robust training and Fastener Training Week is the pinnacle program, which develops the ‘best of the best’ fastener professionals. We are privileged to provide support.”
Fastenal Company reported fastener sales improved in February 2024, falling 3.5% to US$198.2 million (31.6% of overall sales) compared to a 6% decline in January. A year earlier, February fastener sales increased 8%.
Total February sales gained 7.7% to US$627.1 million (€582.5 million). Daily sales improved 2.6% to US$29.9 million. Sales in the US grew 2.4% to US$524.9 million, while sales in Canada and Mexico increased 4.8% to US$83.4 million.
Sales to heavy manufacturing customers rose 3.1%, with sales to non-residential construction customers falling 3.4% during February. Fastenal’s full time workforce increased 3.9% during the month to 20,999 employees. Distribution/transportation personnel grew 6.6% to 3,226, while manufacturing personnel declined 0.3% to 704 workers.
Boeing CEO Dave Calhoun said it could take until the end of 2024 to iron out sector wide supply chain problems that have hampered global jetliner production – with his projection echoing comments by Guillaume Faury, chief executive at Airbus, who told France Inter that production would regain pre-pandemic levels at the end of 2024 or even in 2025.
Referring to Boeing and its main European rival Airbus, Calhoun told the Qatar Economic Forum that “priority one for the two airplane manufacturers is stability. We have to resolve the supply chain issues and the surprise associated with it; and we have to resolve it once and for all.”
Calhoun added: “That is not a short-term job. It sounds like it might be, but I think it could take all of this year and probably all of next year.” In April Calhoun had reported progress in tackling the supply chain and repeated November guidance that “significant supply chain improvement” was unlikely “until well into 2024”.
Despite the overall pattern of disruption, Calhoun said that he did not think recent manufacturing problems with the bestselling 737 narrow body jet would defer those production schedules for more than “maybe a month or a month and a half”.
On future developments, Calhoun said the industry was unlikely to introduce all new jet designs before the mid-2030s. “I think in our industry, because of some of the constraints both in propulsion and the design of the wing, it’s going to be at least until the mid-2030s before we – in this case I’m just going to assume my competitor – will call out that airplane. That is not a short-term job.”
Under the leadership of President Jimmy Chang and General Manager Henry Chang, Special Rivets Corp has celebrated its 40th anniversary with a new plant in Thailand – called Apex International (Thailand) Co Ltd – representing a new chapter in the Group’s rivet production line layout and global business map.
With an average monthly production of 500 million blind rivets and 100,000 riveting tools, Special Rivets Corp (SRC) is one of the most representative and influential companies in the Taiwan fastener industry. Because of this knowledge, SRC recognised Thailand as a major production centre for the south-east Asian automotive industry. In order to serve more international fastener demand, SRC selected the East Coast Industrial Park in Chonburi to build a new 45,000m 2 factory.
The inauguration of phase one was held at the end of October 2023, with more than 160 important guests from Taiwan, China, and Thailand, as well as local officials, attending the ceremony. The new factory houses two new heat treatment furnaces, fully automatic plating equipment, as well as 1,500m 2 of office space to offer employees a more comfortable and efficient working environment.
“Our development goal is not only to make the Group bigger, but also stronger,” explains President Jimmy Chang. “Since our establishment, SRC has been aiming at exporting to the world and actively cooperating with major global suppliers to create a ‘win win’ situation. On the other hand, under the wave of globalisation, we’ve been developing many emerging markets, where customers are looking for trustworthy brands. SRC with its 40 years of reputation, combined with the price competitiveness generated from scale manufacturing, has made us the preferred choice in these markets.”
Automotive fastener company Spec Products, with its plant located in Sinji Industrial Park in Tainan City, is aiming to be the first screw factory in Taiwan to enter into Smart manufacturing – with the company also recently debuting on the Emerging Stock Board (ESB) of the Taipei Exchange (TPEx).
Expected to be in partial mass production by the end of this year, the second phase will aim to increase Spec Products’ self manufacturing rate from 15% to 30% within 2 – 3 years.
The company has also recently acquired a new 13,408m 2 piece of land, which is now under construction in Sinji Industrial Park to drive the operation and development in the next 5 – 10 years. The Sinji plant has a land area of 5,950m 2 and a floor area of 6,942m 2 and will also introduce Smart manufacturing – where raw wire rods go in and come out as finished fastener products. This plant will also use ‘Smart’ transportation vehicles.
The cost of the land in Sinji Industrial Park was approximately NT$240 million (€6.9 million) and the cost of building the Sinji plant is approximately NT$200 million. The plant is expected to be fully
operational next year or the year after, but the company is already testing machines and has already recruited staff.
“As a business we mainly produce screws of special specifications, at small volume, which are suited for Smart manufacturing. On top of that, the Sinji plant is located near leading semiconductor factories, which makes it harder for us to recruit manpower, so if we do not turn to Smart manufacturing, it will be extremely difficult to expand production. We will also introduce Artificial Intelligence to manage production. In addition, fastener production and profits mainly depend on dies, but our operators of the first generation are 60 years old. We hope to use AI to assist in developing and designing dies and retain our technical know-how,” comments Mr Hung-Chen Chang, president at Spec Products Corp.
In order to facilitate communication within the Taiwan fastener industry, and to discuss the current market situation, as well as its challenges, Taiwan CSC – the largest wire supplier to Taiwanese fastener manufacturers –held a ‘Production and Sales Meeting for Q2 2024’ on 5th March in Gangshan, Kaohsiung, Taiwan.
TIFI Chairman Tu-Chin Tsai put it bluntly in his opening speech that the current overall market situation can be said to be very poor.
Many fastener companies around the world are experiencing a squeeze on profits due to regional conflicts – such as the war between Israel and Hamas, as well as the war between Russia and Ukraine – and the higher costs caused by the USA’s 25% tariff on certain steel and aluminium products from China.
Many orders for small screws initially made out to Taiwan have been taken over by Chinese or Vietnamese companies, making a difficult situation for Taiwanese manufacturers. Under these market conditions, Chairman Tsai hopes that when Taiwan CSC announces its prices for next quarter, it will take into account the fact that it is already very difficult for the industry to receive orders and refrain from raising prices if it can.
In addition, in terms of the global industry’s most discussed trends of ESG, energy saving, and carbon reduction, Chairman Tsai also reminded the industry to keep up with the ‘net zero’ carbon reduction trend, and to pay closer attention to ISO 14064, ISO 14067, as well as other carbon management standards. He also urged companies to implement the relevant ‘net zero’ carbon emission declarations in accordance with the law and regulations.
He also asked Taiwan CSC to provide strong support to help the industry save energy and reduce carbon emissions, and to produce more wire products that meet the low carbon trend for the fastener industry. Chairman Tsai believes that although compliance with carbon reduction regulations may indirectly increase manufacturers’ costs, Taiwan’s serious and hardworking industry can do a good job. Moreover, when more countries start to propose ‘net zero’ carbon reduction measures, it may also create more opportunities for the Taiwan fastener industry to receive more orders and establish new collaborations.
Mr Ming Yuan Chen, vice-president of Taiwan CSC commercial division, said that he has observed the orders of some companies are
indeed not good. However, he also mentioned that after two years of de-inventorying in the global manufacturing industry, reports published by many scholars and experts on the GDP forecasts of most countries have shown an upward sign and the optimistic forecasts of many countries (including Taiwan) are above 3%.
Despite the downward trend in the market until Q4 last year, the demand this year should be better than last year as Q2 is traditionally a high season for the industry (statistics also show that the Q2 result has been always the highest of the year for the past decade) and the Q2 industry survey conducted internally by Taiwan CSC also indicates that demand will be 8% higher than Q1 2024. Therefore, even though there is still turbulence in the market, there is no need to be pessimistic as the overall trend is still forecast to ‘recover gradually’. As long as everyone has confidence, works hard, and enhances the company’s strengths of all aspects, there’ll be lots of opportunities this year.
It is understood that Taiwan CSC does not have any annual renovation plan at present. Its current capacity can fully meet the subsequent demand of the industry and the lead times are also expected to be advanced. In addition, in response to the trend of energy saving and carbon reduction, Taiwan CSC has provided the carbon emission data of Q4 last year to manufacturers for subsequent CBAM reporting, and will provide the data of the previous quarter to the industry on a regular basis in the first month of each quarter thereafter. If the industry has any needs or questions about carbon reduction, Taiwan CSC also has a team of industry experts and senior colleagues who can provide relevant information on the industry.
The International Trade Administration (ITA) of Taiwan’s Ministry of Economic Affairs has released an analysis of Taiwan’s exports from January to December 2023, which shows that Taiwan’s fastener exports amounted to approximately US$4.6 billion (€4.27 billion) for that period, down 25% year-on-year from 2022 (US$6.14 billion).
The margin of the export decline deteriorated from the 2022 figures mainly due to the impact of geopolitical conflicts, inflation, and slowing economic growth, which led to conservative orders from customers and thus affected export performance.
However, according to another International Economic and Trade Situation Analysis Report for January to December 2023 – published by ITA, S&P Global forecasts the growth of global exports and imports will turn positive in 2024 at 5.4% and 6.7% respectively, with major
Asian countries such as China, South Korea, Japan and Taiwan showing a more significant growing trend of over 5%.
In terms of metal prices, due to the gradual realisation of the benefits of production reductions by steel mills in the USA, Europe and China – coupled with the increasing steel prices in Europe and the USA – the Asian steel market is warming up, and iron and steel prices are expected to stop declining and rebound from the fourth quarter of 2023 onwards.
January 2024 was the biggest month in fastener imports since October 2013, with over 22,600 tonnes of fasteners (with a value of US$101 million) being imported – 14.7% more than the previous record of 19,700 tonnes that were imported back in October 2013 (at a value of US$103 million).
Comparing the Q1 of 2023 to Q1 of 2024, there was a 6.8% increase in fasteners imported, with 61,512 tonnes imported at a value of US$269.65 million in Q1 of 2024. Only 48,868 tonnes of fasteners were imported, at a value of US$252.38 million in Q1 of 2023.
The fasteners imported to Brazil were from some of the biggest global players, with around 48% coming from Asian countries – including China (29%), Japan (7.2%), South Korea (2.8%) and Taiwan (2.8%).
Brazilian motorcycle production is a sophisticated market and a strong consumer of fasteners – with more than 1.5 million motorcycles produced in 2023. This is not the only sector that has experienced expansion.
When we focus on the export of fasteners, in Q1 of 2023 Brazil exported US$41.48 million of fasteners (around 7,224 tonnes), with Q1 of 2024 only reaching US$36.28 million (5,391 tonnes), a decrease of 12.5%.
The trade fair season within Brazil has truly started, with several key shows taking place in April, including South America’s biggest construction show FEICON –one of the most important trade shows in Brazil when it comes to the fastener market.
FEICON took place between 2 nd – 5 th April at the São Paulo Expo, in São Paulo City. In fact, the show was so popular that there were not enough taxis or Uber services to serve the huge demand from so many visitors.
The 28th edition of the show had more than 100,000 visitors and around 600 exhibitors –including the most important local fastener manufacturers in the shape of INOX-PAR , Jomarca Industrial de Parafusos Ltda, New Fix Indústrie e Comércio Ltda, as well as other companies with mixed distributor activities that involve screws, bolts, and similar, as side products for the general construction sectors, such as Amatools Ferramentos, Walsywa Trade Metallurgical Products and the Waves Plus (a CBS Parafusos Group member).
Brazilian business RWD International, already an exclusive representative for the Chum Yuan brand in Brazil, has been appointed as a sales agent for Jern Yao Enterprise Co Ltd.
With a mission to increase Jern Yao machine sales and services within the region, RWD International and Chum Yuan Co Ltd were appointed as business partners of Jern Yao in Brazil by Paul Lin, commercial manager at Jern Yao, in November 2023.
Already present at many Brazilian fastener manufacturers’ facilities, Jern Yao Enterprises, a traditional brand for more than 30 years, has been proactive in its production of multi-stage machines that are dedicated to cold forming processes – with its lines divided into three series: Bolt formers, with 2 – 5 stages for forming screws; nut formers, with 5 – 6 stages for making nuts; and finally part formers, with 5 – 7 stages for pressing special parts.
You are dealing with an complex fastener sourcing situation? Instead of managing several (small) suppliers, concentrate on one!
4fastening creates simplicity through customized logistics solutions, a global network of suppliers in addition to the in-house production at KAMAX - Quality ensured as certified remote location according to IATF16949 as well as certified according to ISO9001, ISO14001 and TISAX.
You name it, we get it! Tailored services for non-standard parts. Smart small and large scale logistics, lean sourcing process, as well as fast and personalized interaction. Our ser vices enable you to concentrate resources on your core business.“
ALFIRSTE, a Chinese manufacturer that specialises in the production of screws and anchors – that has a reputation for high-quality products and excellent service, has invested in new factories in Thailand, in order to continue to meet the needs of its customers when it comes to carbon steel products.
Established in 2006, Yuyao ALFIRSTE Hardware Co Ltd has developed from a small local workshop into an international business with three factories that cover an area of 15,000m 2 – with a monthly production capacity of 1,500 tonnes. Across its factory the company uses only the latest production machinery, including heading machines, thread rolling machines, drilling machines, point cutting machines, straightening machines, multi-station machines, as well as other equipment.
This wide production capability has enabled the company to become renowned for the production of screws and anchors, especially timber screws (construction screws), chipboard screws, roofing screws, drywall screws, coach screws, self-drilling/self-tapping screws, sleeve anchors, metal frame anchors, as well as threaded rods. “Initially, we only produced standard parts,” mentions Michael Wu, sales manager at ALFIRSTE. “However, through the addition of leading experts, and the ongoing improvement of the laboratory, we have continued to grow our product portfolio and now have the ability to develop products in-house.”
In recent years the company has used this technical know-how to also develop the production of stainless steel products and bi-metal screws. “We see these two product ranges as a key factor in the future growth of the business,” underlines Michael. “At the same time, we have not given up optimising the production of our carbon steel products to make sure they continue to be competitive within the global market.”
Due to the EU anti-dumping tariffs that were introduced on certain carbon steel products from China in 2022, ALFIRSTE made the decision to set-up new factories within Thailand – in order to meet the ongoing demand from customers for such products. “We believe that setting up a factory in Thailand, specifically for the production of carbon steel products, can help customers avoid the high tariffs associated with products from China,” explains Michael. “When this factory is added to our factories in China, as well as our excellent service, high-quality products, and fast delivery times, it means we can provide customers with more choice. At the same time, it can allow us to gain a further foothold overseas and lay a solid foundation for exploring more markets and establishing more factories in the future.”
The main markets for ALFIRSTE’s products are Europe, the United States, and Russia, with the company reporting that the global market is also picking up. “We believe that there is a rigid demand for fasteners and there will not be much change in the trend in a short period of time,” reports Michael. “As long as we make our own products carefully, and improve the cost-effectiveness of our products, all problems will be solved and new opportunities will be created.”
Alongside the development its production capabilities, ALFIRSTE has also been committed to developing the quality of its products –helping to ensure customers receive only the highest quality solutions. “As a company we continuously look to optimise our production processes to guarantee we are consistently producing quality products that are customers can trust,” states Michael. “From the storage of materials to the delivery of finished products, each batch of materials and goods is tested by our laboratory. Every production process is also checked by our quality inspectors to certify only qualified products can enter the next production process.”
Many of ALFIRSTE’s products have successfully obtained CE, ETA and ICC certifications – with the company still developing new products. “With the economic recovery of the European Union and the United States, we will seize the opportunity to meet the greatest needs of customers with products that best meet market demand,” underlines Michael.
ALFIRSTE is able to deliver this quality thanks to its first-class quality department and fully equipped laboratory, which includes a salt spray test machine, a high and low temperature humidity box, image measuring instruments, a universal testing machine, a drilling testing machine, a Rockwell hardness machine, a metallographic specimen Mosaic machine, a Vickers hardness machine, a metallographic specimen polishing machine, a Fischer scope X-RAY, a torque testing machine, a concentricity metre, a bending measuring machine, a metallographic microscope, a SPECTRO spectrometer, a temperature and humidity metre, as well as standard callipers, groove depth gauges, torque wrenches, electronic scales and angle rulers.
“Our dedication to quality across every aspect of our business has enabled us to create strong relationships with customers, with our products
We believe that setting up a factory in Thailand, specifically for the production of carbon steel products, can help customers…”
being sold to around 20 countries,” points out Michael. “As a business we are always looking to create close partnerships with our customers, which is why we invest a lot of money in participating at exhibitions every year. We are also very proactive in inviting potential customers to our factory so they can see first-hand our capabilities. It is only by visiting our factory and seeing our production workshop, packaging workshop, and laboratory, that customers can really understand our commitment to quality. Every customer who visits our factories is full of praise for us and can see we are a trustworthy and reliable partner.”
During the development of its production processes, expansion of its product portfolio, and continuous focus on quality, ALFIRSTE has always ensured innovation is at the core of its business, which has been fundamental in the company’s success and growth. “Innovation is undoubtedly a core competitiveness for us,” states Michael. “The expansion of the business cannot be separated from the role of innovation, which in turn depends on investment in the company. The two complement each other, which is why, in order to continue to innovate, you need to continue to invest money.”
Michael continues: “Technological innovation also promotes industrial innovation and in the future fastener manufacturing will develop towards a trend of being more refined, higher quality and more humane. China’s fastener manufacturing industry is moving towards automation, digitalisation and intelligence. ‘Made in China’ is no longer limited to the mid to low end markets. Superior and stable quality and good cost performance will become the core advantages for Chinese companies to capture the mid to high-end markets in Europe and the United States. Continuously improving the competitiveness of enterprises and entering the high-end market is the direction of our efforts, which is why we are committed to innovation and investment.”
An area ALFIRSTE is currently investing, and therefore looking to innovate, is its sustainable development. “Since the establishment
of the business, we have looked to serve our customers, employees, and partners, in the correct way. It is the basis for the healthy and sustainable development of the business,” mentions Michael. “The topic of sustainability has become a key factor within every sector and as a company we want to make sure we are meeting the needs of our customers. That is why we are already taking the initiative to adopt cleaner production processes, which includes reducing raw material usage and waste generation, as well as using solar power. We are also actively cooperating with the EU and participating in the CBAM regulation. Additionally, we are also looking at ‘greener’ procurement and how we can work more effectively from an environmental perspective.”
Michael concludes: “Thanks to our sophisticated production equipment; innovative methods of production and material combinations; as well as in-depth product range; we are optimistic about our future place within the fastener industry. We are deeply aware that we must adhere to management principles and business ethics, such as integrity and respect, whilst focusing on quality, compliance with laws, cultural tolerance, supplier management, etc. These are the basis for the healthy and sustainable development of ALFIRSTE and it is only by doing this that we can realise our mission, and vision, and inherit and demonstrate our spirit.”
www.alfirste.cn
In March, the German Fastener Association (Deutscher Schraubenverband e.V.) held its 6th Alumni event of the Certified Fastener Qualification programme (DSV) at the Technical University of Dresden – with 140 certified fastener engineers (DSV) and certified fastener technicians (DSV), from various courses, attending.
Attendees were welcomed by Hans Führlbeck, general manager of the DSV, as well as Pasquale Gatto and Dr Andrea Eberhard, who are responsible for the DSV Fastener Academy. In addition to interesting presentations on the latest trends and current developments in the wide field of fasteners, all graduates received a special lapel pin showing they had successfully passed the exam courses for the ‘Certified Fastener Engineer’ (DSV) or ‘Technician Studies’ (DSV). Thanks to the lapel pin, every certified fastener engineer (DSV) and certified fastener technician (DSV) is now visible and recognisable to their business partners and colleagues in their day-to-day business.
In the evening, the participants had the now legendary networking get together in the cult tavern ‘Bärenzwinger’, a typical student pub in the old town of Dresden.
The 2024 advanced training courses available from the DSV Fastener Academy are listed online and available to everybody: www.schraubenverband.de/ubersichtfortbildungsangebote
In association with the 6 th Alumni, DSV also held the 15 th Workshop Industrial Fastener Assembly in cooperation with the Technical University of Dresden,
represented by Professor Dr Schmale, at the German Hygiene Museum in Dresden on 13 th March.
The well accepted workshop was attended by around 240 participants from all over Europe, including fastener manufacturers and retailers, OEMs, tier suppliers, as well as interested parties from the whole process chain. During the workshop, exciting presentations were held by fastener experts and engineers about industrial fastener assembly and related themes under the headline: ‘Sustainable, efficient, digital’. Many companies also used the workshop as
an opportunity to present themselves and their latest developments in the exhibition area in the lobby of the Hygiene Museum. DSV reports that the opportunity for professional discussion, all around fastener assembly, was well received by all participants.
The event, which has developed into the European meeting place for the fastener assembly industry, will take place again in Dresden in March 2027.
The annual DSV General Assembly will take place 13 th – 15 th June. Further to that, EIFI will have its annual General Assembly in Florence, Italy, on 23 rd – 26th May.
*120 pcs per minute.
Take stainless steel, process it with a special cold forging machine. Spend 0,5 second per step and repeat 4 times. Add a pinch of innovation, just enough. The special formula for dedicated electric vehicle applications.
Product: Long Bolts
Applications: Battery Pack | Power tubes rods | E-bike | Bike spokes | Stator Bolts
PennEngineering® is a company that has both innovation and new technologies at its core. Here, we speak to Gerard Quaid, vice-president of sales and marketing Europe, about how the company is continuing to push the boundaries and deliver the best possible fastening solutions.
How does PennEngineering® work with customers to provide optimal fastening solutions and services?
“What makes PennEngineering® so different from our competitors is that we aim to offer complete fastening solutions. Even with over 2,000 part numbers in our catalogue, we provide thousands of specifically tailored custom designed PEM® fasteners to meet the unique requirements of our customers’ applications.
We work closely with our customers to understand their applications and what they are trying to achieve with their end product. This enables us to ensure that a customer is presented with the most cost-effective, high performance fastener during the design and installation stage, which we fully support via our range of Haeger® and in-die installation equipment.
It’s all about the relationships we build and our customers having complete trust in us. We consider our customers more as partners because we share knowledge and collaborate. As part of this we encourage our customers to make use of our testing facilities and laboratories.
Over the past five years, our customers’ requirements have become increasingly challenging, particularly with the transition from internal combustion engines (ICE) to electric vehicles (EV). This transition has tested us and pushed PennEngineering® into new product development, as well as new industries, which is something I feel we have really excelled at.
If you look at some of the standards that our customers have to work with, from cleanliness to IP-rated fasteners, we are able to design a new fastening solution, produce it quickly, install it in the customer’s material of choice, test it in-house and then present all performance criteria back to the customer. Our customers rely on this service for each product generation as the requirements get stricter.”
What are the key markets for
What are the current challenges within these markets and where do you see opportunities?
“PennEngineering® originally started out serving the electronics market and has since moved across to a number of industries, such as
automotive, automotive electronics, consumer electronics, datacom and telecom, defence, EV, power management and charging, industrial and commercial, medical, as well as sheet metal and metal enclosures.
An area with opportunities at the moment is the rapid increase in busbar manufacturing for electric vehicles, power management and charging stations, which is pushing OEMs and tiers to look for new cost-effective solutions to reduce electrical resistance. Therefore PennEngineering® has launched PEM eConnect™ Contact Bushing, which can be used to make reliable electrical connections between copper or aluminium busbars, PCBs or cable terminals. This new range not only answers the need to be more cost-effective but also answers the specific needs of our customer base.
One of the most significant challenges currently facing the market is speed. Customers want products quickly and don’t want to be burdened by supply chain issues. This is where PennEngineering® is different. We make our products where they’re being sold and used – whether that’s in Asia, the USA, or Europe – so our customers can get their products quickly.
We have 25 locations worldwide, with over 4,000 employees and eight product development centres. Our European headquarters is in Galway, Ireland, where we produce over one billion fasteners a year with our cold forging, cold heading, screw machining, heat treatment and electric plating facilities.
In addition, in 2023, we set-up a Haeger® Europe facility in Galway, where we assemble the full range of Haeger® installation equipment as well as design and manufacture the tooling for fastener installation. This enables us to ensure installation confidence and optimal production performance, which is key in today’s market.
We are proud that PennEngineering® delivers the complete process to customers – right the way from the design to the end product. When we say ‘Made in Europe, for Europe’ we mean it. We have full control over our products and can bypass common supply chain issues that our customers are commonly facing.”
The unique high surface area knurl design pierces the corrosion layer on busbars creating a consistent electrical current connection without needing to plate the busbar itself. Ideal for making reliable electrical connections between copper or aluminium busbars, PCBs, or cable terminals.
• Innovative design
• Simple installation
• Consistent electrical connections
• Reduced total installed cost
What investments has the company made in recent years? Why did you decide to make these investments?
“PennEngineering® is constantly investing, but one of the most important investments has, and will continue to be, our employees. 10% of our workforce is in further education at any one time – with many completing engineering qualifications at a master’s degree level.
As well as this, one of the biggest investments we have made is the transition to digitalisation at our manufacturing plant in Galway. Whether that’s through new equipment or digitising old equipment, we now have full visibility over every piece of essential equipment on the shop floor. That means we now have visual control of multiple operational productivities via dashboards and integration between different business elements, which has been a key turning point for us –changing the way we operate every day.
Because of these investments, we were honoured with the Medium Lean Business of the Year Award 2023 from Lean Business Ireland for continuously innovating and thinking outside the box in the fastener industry.
We also recently announced the opening of a UK office in Burnley to renew our commitment to this important market. The site features a comprehensive stock of fasteners that will streamline logistics and provide customers with prompt access to the entire portfolio of PEM ® fasteners. We also have a new UK sales team to ensure we are readily available and accessible to meet the unique needs of our customers.”
Sustainability continues to grow in importance within markets. What steps has PennEngineering® taken on this topic and how do you see this area developing?
“PennEngineering® believes in doing what’s right for our employees, our communities, and the environment, so we are constantly looking at ways to stay ‘one step ahead’. With our manufacturing facility in Galway, we manufacture our products near our European client locations, as well as source our materials close to our manufacturing locations, to reduce the carbon footprint of material shipping. We have also made changes within the facility, such as updating the rectifiers on plating lines and upgrading equipment so it’s more energy efficient.
We also have a waste disposal programme that involves composting and recycling, as well as our water usage and how we can reduce it – whilst still efficiently operating our heat treatment furnaces and plating lines.
We have full control over our products and can bypass common supply chain issues that our customers are commonly facing.”
Reducing usage involves changing our process, including draining, filtering, etc. The Galway site has also recently attained ISO 45001 and ISO 14001 in 2024 and is run according to Lean Manufacturing procedures. All these efforts add up to PennEngineering® being a responsible and thoughtful manufacturer. Traceability and transparency is extremely important to us. We have a responsibility to work together with our facilities, customers and suppliers to encourage sustainable behaviour.
As part of our global environmental sustainability plan, we are committed to reducing our greenhouse gas emissions by 50% by 2030, with the goal of achieving carbon neutrality by 2040 and being a ‘net zero’ company by 2045. We have also implemented a sustainability team of around 30 people worldwide who review and provide suggestions that are aligned with business demand. Our sustainability report will also be released in 2025.
There is also a considerable drive from the EV market right now, in particular, to ‘track’ a product’s carbon footprint. Obviously, with the CBAM legislation, our customers are demanding more information, and rightly so. PennEngineering® takes away the headache of CBAM paperwork and submissions. We have carried out comprehensive studies and reviews of our manufacturing processes and, as a result, can supply documentation relating to the carbon footprint of our products. PennEngineering® customers do not need to worry about compliance in that area or risks to their supply chains.
PennEngineering® stays close to our customers and delivers innovative fastening solutions that enable our customers to develop new products. We want to help drive change and our commitment to sustainability and protecting our environment is reflected in the many efforts we practice every day.”
www.pemnet.com
Mark Revak has been working at Harrison & Clough – a leading UK distributor of quality fasteners and fixings, as well as related accessories and tools – for nearly 37 years. Here we talk to him about his career within the fastener industry and the steps Harrison & Clough has taken to ensure it continues to meet the needs of its customers.
Tell us about your career and the roles you have held at Harrison & Clough since joining the business.
“I joined Harrison & Clough (H&C) in October 1987 and initially started on the late shift picking in the warehouse. I then had multiple other warehouse roles, such as FLT, loading, checking, as well as a floor planning and process development. The latter roles reflected my eye for improvement in efficiencies and they were all a real learning curve in terms of product, systems and processes.
The journey through the warehouse environment was very beneficial, as I was able to understand all the roles and gather first-hand knowledge of how things truly worked. I then moved from the warehouse into the commercial team, initially in sales processing, and then went onto account management – forming the original key accounts sales team. As with the warehouse systems, the processes within the commercial side were very manual and I was a part of the team that brought automation to processes and pricing.
For instance, back in the early 1990s we had to write out every order in its entirety, which could mean writing every detail for a 200 line order. I therefore suggested that instead of all the details, why didn’t we just write the start of the part code, as that was the unique identifier. This proved to be a big success and helped us streamline the entire process, so that we could take even more calls.
When I made the move into the key accounts team, the idea was to build stronger relationships with customers – so that we could better understand their needs and help us further build the business. In essence, our aim was to provide the customer with whatever they asked for when it came to a product. We would do everything for the customer and having the key accounts team as a single point of contact was hugely popular, and still is today.
I then moved into business support and worked closely with the commercial, operational and technical support teams to implement a programme of continuous improvement, commercial pricing and data support – essentially looking to offer our customers support and ease of trading. As part of this, in 2015, I migrated to the operational side of the business – supporting the Warehouse Management System (WMS) and automated warehouse programme. The aim behind the WMS was to make the warehouse processes as efficient as possible and to make sure as few picks were being made to fulfil each order. It also helped us maximise our warehouse space and how we were using it. We went from operators picking 20 – 30 items an hour via a trolley, to picking more than 100 items an hour through shelving.
Today, I am back in the commercial environment and working on different projects. Whilst I have been at the company all this time, by moving around the different departments it feels like I’ve had a different job every few years, which has helped keep things fresh and let me see how different parts of the business work.
During the journey I have been incredibly fortunate to work with and be supported by some of the industry’s finest. Having been with H&C for so long, it is nice to be able to see all of the hard work paying off, especially when it leads to success for the business.”
“Clearly product origin has changed hugely over the period, with it moving from the UK, to Europe, to the Far East. Back in 1987, when I first started, the majority of the product was sourced in the UK and whilst you kept a reasonable stock, the waiting time for additional products was never more than a few weeks. Delivering to the customers was also a lot easier, we had distribution hubs throughout the UK and we had nationwide delivery via our notorious ‘green vans’.
However, when the price within the UK became too expensive the production soon moved to other parts of Europe and then to the Far East, so that today the majority of products are now sourced directly from Asia. Whilst this has led to a reduction in product price, the delivery times have increased significantly to a point where you can be waiting up to 12 months for an order to arrive – creating a whole new challenge for companies.
Communication methods are also massively different, back when I started postal orders, telex and telephone were a fundamental part of the business. Nowadays it is emails, EDI, and to a certain extent still telephone, that are the key contact points with customers. In fact, 75% of our business is conducted by email, which is totally
Don’t miss the chance to advertise in our feature on the worldwide fastener distribution market.
To advertise, please email sales@verulammedia.com or phone +44 (0)1727 743 882 Now is the time to let our global readership know about the stock, range and services you can offer to support customers.
different to how it used to be. However, whilst emails have become more prominent, we still believe that having a conversation with the customer and understanding their requirements is crucial – as that is how you grow and develop relationships. That is why we encourage all our sales team to follow up any email with a phone call, so they can make sure we are meeting customers’ needs.
Regarding other changes within the market, whilst the products have remained remarkably consistent, the major changes have been in the grades of material and plated finishes requested. Conformance, legislation and reporting are also areas that have rightly moved up the agenda and continue to change at a rate of knots. Unfortunately, our market seems to be at the end of the informational loop and as such has to react in relatively short time periods to these updates.
A big shift within the market is that product knowledge has essentially moved to be the responsibility of the wholesaler. Many customers have moved to supply a very wide range of products – meaning that a lot of specialisms have been lost. As a wholesaler you need to be able to offer a lot of services and support when it comes to the products, in order to be able to provide the right solutions to meet each individual customer’s needs. At H&C we can offer a wide range of products that is continuously expanding. Being part of the Dormole Group also means we have access to a wide range of products from other members of the Group, including ForgeFix and Toolbank. In the fullness of time this will enable H&C to have one of the largest ranges available within the market.”
What investments has Harrison & Clough made in recent years? Why did it decide to make these investments?
“Investment has always been a key area and at H&C our business models, practices, and support mechanisms, have moved forward massively thanks to us continuously investing in the business and the industry.
I think the levels of investment in product, customer support, systems, paperwork, and quality of products, can sometimes be overlooked in a marketplace that seems to delight in commoditising safety critical products. However, these investments have been necessary as we are finding that customers are increasingly requesting support on topics – such as CBAM regulations, Russian steel legislation, etc – and as a business this is a massive opportunity because if you can understand the legislation and explain it to the customer, in a simple format, then it gives you an advantage within the market.
As a business we recognise that covering legislation and data is going to be key to the business, now and in the future. Thanks to the development and investment within our current division operating
Investment has always been a key area and at H&C our business models, practices, and support mechanisms, have moved forward massively thanks to us continuously investing in the business and the industry.”
system, we have been able to reduce the number of desks you need to sell the products and instead we have moved these people over to data support and helping customers with these types of topics. This means that without increasing the cost base we have been able to ensure we are still providing a first-class service to our customers.
Other areas that we have also been investing include a new ERP system and a 135,00 square foot (12,500m 2) warehousing and distribution facility, which will encompass state of art automation and offer many benefits to our customer base. To add to this, throughout 2024 and 2025 we will also be introducing new products across 20 product groups –amounting to in excess of 2,500 individual SKUs. These investments are designed to enable us to offer more products to more customers and deliver them a lot quicker.”
“Our strategy is simple, to offer the widest range of products, combined with industry leading levels of service and support, in addition to a customer facing team that is fully emersed in the customer experience.
At H&C we supply a wide range of fasteners and fixings, which are complimented with industrial consumables and associated hand tools. As a part of the Dormole Group, we also have access to resources and support that compliment and drives continuous customer support initiatives.
In essence, we look to offer a tailored supply solution for any type of customer, including products and every element of support – whether it be goods supplied at optimum receipt intervals, data, digital support, fixed price agreements, customer-friendly paperwork, field support or training. We believe that opportunities are wrapped up in the challenges associated within these areas, which is why we are constantly working on providing multiple solutions – so every customer can access the products and support they need.”
SUNCO Industries is one of Japan’s leading master distributors, specialising in fasteners and related products, with a tradition and track record going back over 75 years. To ensure it continues to meet the needs of its customers, the company has consistently used innovation across its business in order to meet growing requirements.
Today SUNCO Industries Co Ltd collaborates with approximately 1,300 fastener manufacturers of high-quality products and serves 6,000 clients, including international customers. SUNCO’s strength lies in its extensive product line-ups, with the company boasting over 2 million types of items – predominately JIS (Japenese Industrial Standard) products, with 300,000 types consistently in stock.
“While JIS fasteners may not be the mainstream choice outside of Japan, their significance is underscored by the multitude of Japanese companies manufacturing automobiles, machinery and electronical products worldwide,” explains SUNCO. “We believe that Japanese screws stand as world leaders in terms of the security and reliability for the final product. This has been proven for a long time and we believe it will stay the same in the future. That is why we offer support to those looking to broaden their product range, including both JIS items and other standard products.”
A prime example is SUNCO’s new ONIBA PIAS, which is an innovative product that can be screwed directly into 4mm stainless steel material – with a cross recess 4mm diameter SUS410 drilling screw. “Our ranges of flat washer sizes and pre-assembled screws are also one of the widest in the world,” reports SUNCO. “We have, for example, machine screws in increments of 1mm length, threaded rods with varying 5mm diameter and products plated with trivalent zinc cr+3. We also deal with a wide range of fine pitch screws.”
SUNCO adds: “This approach has served us well in Japan and we are extending this service for overseas companies too. Our motto of ‘your special is our standard’ reflects our commitment to fulfilling our customers’ unique requirements.”
Throughout its inventory SUNCO’s commitment to quality is also unwavering. “We have a dedicated quality assurance department that conducts regular product checks and collaborates closely with our purchasing teams during supplier visits,” points out the company. “In addition, we are the organiser of Sanko-kai, which is the biggest fastener association in Japan. Sanko-kai has more than 170 suppliers as members, all of whom are striving to improve quality on a daily basis from various angles, including regular quality study sessions and awards for quality initiatives during the year.”
As a business SUNCO has also always been committed to innovation, especially when it comes to providing additional value to its customers. “We continuously invest in our logistics centres, where we have recently shifted our focus to accommodate small quantity shipments, even as little as a single unit, in order to cater to our customers’ diverse needs. To do this, our logistic centres have leveraged a unique mathematical model to enhance systematisation, efficiency and labour savings – creating a system that sets a new industry standard.”
SUNCO has also made investments within rotary racks for fulfilling individual item orders and additional rotary racks that are dedicated to small boxes to enhance the efficiency of small box picking. “Looking ahead, we plan to introduce one of the largest automated warehouses in the industry,” states SUNCO. “Our commitment extends beyond borders, addressing customer needs both locally and globally. We are actively expanding our reach into international markets, striving to meet the
swift and safe delivery of products that our domestic and international customers require. We recognise that not all customers need large quantities of niche sizes or products, which is why we use our logistical expertise and product range to promptly deliver the exact quantities our customers need, exactly when they need them.”
SUNCO has also looked to invest in digitisation in order to help it grow overseas sales, which is why it has launched an English version of its web catalogue, 3Qnet, which was initially aimed at domestic customers. “We have updated the system to enable the generation and download of pro forma invoices within the platform, with the option to purchase in Japanese Yen or US Dollars. Customers can also pay via PayPal and orders are dispatched the following day after payment is received,” points out SUNCO. “Upcoming enhancements include adding the capacity to search for products using DIN and ISO standard names, which correspond to JIS standards, and making it possible to carry out transactions in other currencies on 3Qnet, such as Euros and British Sterling.”
To add to this, SUNCO has also created an English language website that will be launched in June – with the new platform designed to help both existing and prospective customers gain a clearer understanding of the company and facilitate smoother communication.
SUNCO concludes: “There are numerous compelling reasons to consider Japan as a supply source, we excel in delivery time management and take pride in our high-quality products. Additionally, the recent weakness of the Japanese Yen has created a price advantage. We invite everyone to explore SUNCO and Japan as their solution to the instability in the supply chain.”
www.sunco.co.jp
CAMCAR Innovations® has a legacy of being an R&D company serving end users with novel designs that improve functionality, enable high manufacturability, and provide fastener manufacturers with value added solutions.
Founded in the USA in 1943, to the west of Chicago, CAMCAR Innovations® was set-up initially with the aim to find a better way to make a particular part for the air force. The initial idea was simply to convert from a machining process to a cold forging process, which not only made the part cheaper to manufacture, but meant it could be designed so it performed a lot better.
“Our origins started with an innovative idea and, to this day, innovation is still at the heart of our company,” states Michael Claassen, president of CAMCAR Innovations®. “We are an R&D company that creates innovative solutions to solve end user problems and we license these solutions to a high-quality and global network of manufacturers –equally distributed between the Americas, Europe and Asia. We also evaluate solutions created by others (companies or inventors) and master license those that we feel solve market problems – in essence becoming a broker for good ideas and helping them get into global production.”
CAMCAR Innovations® is best known for the TORX® and Strux® brands, although it is able to offer many other solutions to existing and new markets. “We are considered the drive system experts in the industry, but we also have a variety of other brands and solutions we can offer customers,” explains Michael. “The key to our success is twofold. First, our products bring market leading performance and simplicity of design that benefit end users and manufacturers. It is common for our products to reduce overall total ‘in place’ installed costs for end users. Secondly, we have created an ecosystem that ensures all our manufacturers make our products to a similar level of quality and consistency. We do this by tightly regulating the key manufacturing tools in process gauges, final inspection gauges, manufacturing and product standards, and in the case of drive systems, the drive bits and screwdrivers. Our brands represent our dedication to this quality and consistency. We like to say an end user who sources our brands can ‘source it and forget about it’ since regardless of which
of our manufacturers they choose, they can be assured to get the same quality part.”
The types of products that CAMCAR Innovations® can supply include drive systems that increase bit life or improve automated assembly; speciality thread forming screws that limit debris generation in magnesium casting assemblies; plugs that eliminate the need for unreliable rubber or chemical seals; fastening systems that eliminate joint slip under high shear loads; clinch systems that have market leading performance and allow end users to dramatically reduce the amount of part numbers they require for assembly; security drives for assemblies involving high voltage electronics; and banjo bolt replacement that solves quality problems with current banjo bolt designs; as well as many others.
Our origins started with an innovative idea and, to this day, innovation is still at the heart of our company…”
“Many of these products are new to our portfolio and we are currently on a product offensive, which will provide more than triple the solutions we have for the market,” points out Michael. “The first products in this campaign are a new family of Strux® clinch fasteners known as Strux SM™, Strux HM™ and a third as yet unnamed member. We have further plans to introduce additional products in the future.”
CAMCAR Innovations® is able to supply these products to a wide range of sectors, with its top five markets currently aerospace, automotive, industrial, electronics and residential or light construction. In addition to these markets, the company has also done some preliminary groundwork to assess the medical and powersports’ markets and believes that these sectors can benefit from the manufacturability and functionality of its products.
“Many economists are predicting a mild recession in 2024 with growth to follow. As a business, we noticed softness in some but not all markets. For the remainder of this year, we are taking the opportunity to get many of our new products in place to support the coming growth,” explains Michael. “For instance, automotive is going through a very disruptive period due to electrification. Government regulations are requiring adoption at a rate that is clearly higher than that which consumers are willing to follow. We expect the EV market to continue to grow, but not as quickly as governments’ wish. This tension has made planning especially difficult. Nonetheless, with technological disruption comes opportunities to
serve end users with new parts that solve unforeseen and known problems.”
He continues: “Many of these solutions will be suitable for other markets that are electrifying, such as powersports. We also see big opportunities in light and residential construction with our premium drive system that improves jobsite productivity and makes the construction worker’s job easier to perform. In the medical space, we see a couple decades of growth as major populations of ‘baby boomers’ and ‘Gen X’ begin to reach an age where medical care requirements increase. We believe this opens the doors for solutions we have, for example, improving the installation of bone screws. Overall, many markets have challenges but, for an R&D company, challenges are where we find opportunities for the next great product.”
CAMCAR Innovations® is best known for the TORX® and Strux® brands, although it is able to offer many other solutions to existing and new markets.”
The TORX® Drive System was the brainchild of Bernie Rheiland in 1965 – who was frustrated that drive systems were not able to apply a high torque without cam-out (as cross drives are designed to do) or without sacrificing assembly line bit life (common problems with square and hex drives).
The TORX ® geometry is based on a circular design so that drive angle and contact points keep stresses low, which improves bit life. In combination with six lobes, it is also able to handle high amounts of input torque and the straight side walls ensure that cam-out is minimal.
“The TORX ® Drive System has a number of advantages including longer bit life, minimal to no cam-out, the ability to manage high torques, and many variants –making it the most flexible drive system on the planet, with commonly available tools, as well as being easy to manufacture,” points out Michael Claassen, president at CAMCAR Innovations®
Today, the TORX ® Drive System has three main family members and many variants of each. The family includes TORX ® , TORX PLUS ® and TORX PARALOBE™ – all in internal and the first two in external drive configurations. Each successive family member comes with increasing drive system strength and corresponding improved bit life. The drive tools are also forwards compatible, although CAMCAR Innovations ® only recommends this in service situations where the correct tool is unavailable.
“The TORX PARALOBE™ is the newest member of the family and is exceptionally strong,” underlines Michael. “We see its use being focused to joint assembly where a lot of tension is needed in the bolt to ensure that proper long-term clamp load is maintained.”
Michael adds: “The variants of the TORX ® family offer solutions that lower automated cycle times (Autosert ® ), reduce problems with recess fill when organic coatings are used (Cleardrive® ), create strong connections with plastics (PlasTORX ® ), incorporate stick functionality with the bit (TORXALIGN ® ), offer lightweighting options (TORX PLUS ® Ultra Low Profile), add anti-tampering features (Torx ® Tamper Resistant) and offer stable drive features (TORX ® ttap® ), to name just a few. This again, is why we call the family the most flexible drive system on the planet. If a customer needs functionality that one of our variants does not cover, we can develop a new variant for them.”
CAMCAR Innovations ® is also continually improving the TORX ® Drive System as it continues to learn from its vast marketplace experience, whether functionally or from a manufacturability perspective. Additionally, new variants are launched as new needs arise to
ensure TORX maintain leadership as the most flexible drive systems on the planet.
“Only the TORX ® Drive System has global unified standards for the fastener, in-process gauges, final inspection gauges, manufacturing tools and drive bits,” states Michael. “This ensures a system that works, regardless of the authorised manufacturer who produces it. That is why we actively defend our brands and take action when notified of unauthorised use. Unlike TORX ® products, generic hexalobular parts have a standard for a final inspection gauge only. It means all tools and all in process gauges have been designed by hundreds of different individual tool shops, all coming up with a slightly different variation on the geometry. Sometimes the differences are imperceptible and may manifest as unnoticed increases in bit consumption and costs, whilst in other instances they display gross inaccuracies that can manifest in something as unacceptable as part failure. This lack of unified global standards generally never bodes well for a customer. An end user can’t be sure what they are buying or how it compares to parts from other vendors. That is why we are so protective of all our brands as our focus on details ensures they are a sign of true quality and reliability.” www.torxttap.com
Over the years, everything has been said and written about Brugola OEB Industriale SpA. It’s not surprising, considering how significantly the company has contributed to raising the profile of Italian fasteners globally.
Adistinguishing hallmark of Brugola OEB is its development of a special screw during its initial years, one that achieved legendary status – the iconic hexagon socket screw, famously named after its manufacturer and is still marketed as the ‘Brugola screw’. Today, Brugola OEB is a much more intricate and multifaceted entity than it was in the past, and it is constantly evolving due to forward thinking management strategies.
To better understand the evolution of this industrial business, it is necessary to carefully analyse the personalities of the owners and their management contributions. It all began in 1926 when Egidio Brugola founded OEB (Officine Egidio Brugola) to produce washers, special rings for engines and related components. Egidio had a deep passion for mechanics, exhibiting exceptional expertise and ingenious insights in the field.
The founder’s primary focus was to define and consolidate the product range. From 1964 the company’s management gradually fell into the hands of Giannantonio Brugola, then a mere 21 year old, who carried forward the
founder’s legacy with an innovative spirit and in sync with the changing times. The company inherited by Giannantonio Brugola had an extensive range of products and went through a significant period of renewal, which laid the foundations for establishing a prominent presence in the automotive sector.
The definitive change in production at the business occurred in the 1980s when the emphasis shifted towards manufacturing special screws for the automotive industry. This strategic move enabled Brugola OEB to gradually solidify its position as a leading manufacturer of ‘critical’ screws for endothermic engines – seizing an opportunity offered by favourable circumstances and Giannantonio’s astute strategic vision.
The advent of robotics in automobile manufacturing heralded the ‘zero defect’ concept, which ushered in an era of ‘total quality’. As a result, there was a need to look for new methods and technologies that would ensure maximum safety in terms of ‘zero defect’. To solve this important and difficult problem, under Giannantonio Brugola’s guidance, the company conducted studies and research focused on sophisticated control
technologies that would assess any alterations that might occur in a screw during the various manufacturing stages.
After Giannantonio passed away, his son Jody, who was still very young, took over the complete management of the family business. He was already familiar with the company because he had been working there for some time. Jody followed his father’s manufacturing approach, consolidating the position of Brugola OEB products in the global automotive industry and proudly maintaining their ‘Made in Italy’ distinction, among other achievements.
With great satisfaction, under the guidance of Jody, Brugola OEB surpassed the goal of €190 million in turnover in 2023 – with Jody having the aim to push the company towards a consolidated turnover of €200 million in the future. Jody’s accomplishments also include initiating two new areas of focus –the launch of an impactful sustainability campaign, and projects aimed at reducing CO 2 emissions, and an expansion of the company’s production area through strategic hiring to strengthen the workforce.
Jody’s dedicated efforts, leading to significant achievements, have received broad public recognition. This is highlighted by his nomination as a ‘Commander of the Order of Merit of the Italian Republic’ at the remarkably young age of 38.
Here Marco A. Guerritore chats to Jody Brugola, president of Brugola OEB, about the Italian fastener industry and what the company has planned regarding sustainability and 2024 in general.
President Brugola, how do you view the future of the Italian fastener industry in this rapidly changing world?
“A bright future lies ahead for the world of fasteners. Screws have been essential components of endothermic engines for decades and are now proving to be indispensable components of electric platforms – although this might require smaller and thinner fasteners for the new platforms.
I believe fasteners will remain important regardless of the type of engine, whether electric, endothermic or hybrid. While I believe hybrid and endothermic engines will continue to be key players in the coming years, the hydrogen engine might emerge as a solution for the future of the automotive industry.
Having said that, I believe the endothermic engine will still be around in the next few years. While we will continue manufacturing critical screws, and have done for several years now, we have also been focusing on developing new special components for cars. This will enable us to expand our product range in order to meet evolving market demands.”
Will the current crisis in the German market negatively impact the Italian fastener industry?
“Germany is certainly an important market for the automotive industry and a downturn there could impact the entire supply chain, not just the fastener industry.
At the moment, numbers and sales remain stable. We will monitor the evolution of the sales trend, which also includes electric platforms – the only ones currently that are not performing as well as expected are in Germany.”
Brugola OEB’s commitment to corporate sustainability and particularly the problem of CO 2 pollution is commendable. What exactly is the ‘Forever Bambù’ project?
“The ‘Forever Bambù’ initiative piqued my interest right away due to bamboo’s remarkable carbon dioxide absorption capacity, which is 36 times greater than that of other plants. It can also be used as a raw material in a variety of industries. Hence, we have partnered with a European leader in the cultivation of giant bamboo to offset our company’s CO 2 emissions. This activity aligns with our sustainability policies, aimed at decreasing our environmental footprint.”
What are the company’s goals for 2024? Will you be adopting an acquisition strategy in the future?
“In 2023 we manufactured 45,300 tonnes of fasteners, which was equal to a turnover of more than €190 million. Our goal for 2024 is to achieve a 10% annual growth target by developing new products and expanding our customer base. That is why our target for 2024 is 51,700 tonnes.
Regarding an acquisition strategy, while we are always open to future scenarios, at this time we are not considering acquisitions as a means of growth. Personally, I lean towards maintaining a family business model – since it allows us to make quick and flexible decisions.
Brugola OEB has grown significantly in recent years, partly due to the US subsidiary, and my goal is to maintain this growth trend, which requires ongoing commitment and significant investments.”
You plan on expanding your company’s workforce while implementing production automation. Do you foresee any conflicts between these two strategies?
“I believe that the human element will always play a fundamental role in the manufacturing of fasteners, even as we continue to strive for new forms of automation within our industry. I don’t believe they have to be at odds. On the contrary, automation and new technology can help to improve working conditions and increase resource efficiency.”
The Steel Dynamics Group started in 2011 with a vision – to improve service levels in the metals processing industry. Since then, the Group has experienced steady growth, expanding operations and its customer base across the UK, as well as investing in state of the art machinery and technology to improve efficiency and production capacity.
Today, with a turnover in excess of GB£57 million (€66.5 million) in 2023, as well as the recent inauguration of a state of the art 100,000 square foot (approximately 9,300m 2) stainless steel facility – complemented by a separate, dedicated 25,000 square foot carbon steel site, a production facility in Workington and a nuclear machining and apprentice centre – the Steel Dynamics Group is solidifying its position as a prominent player in the UK and European steel market.
The Steel Dynamics Group has been able to achieve this success through organic growth and strategic acquisitions, with the Group now consisting of four businesses that relentlessly work together to reduce costs and to help customers to flourish. Firstly, there is Steel Dynamics UK, the original company and a leading stainless steel stockholder and processor that supplies a range of mainstream stainless steel profiles to complex supply chains. With its top of the range, in-house processing equipment, the company supplies some of the most demanding high integrity applications.
Strategically located in the Walker Industrial Estate in Blackburn, Lancashire, Steel Dynamics UK has over 5,000 tonnes of stainless steel stock from European origin, coupled with a full suite of plasma, laser and waterjet cutting machines, including what the company says is the UK’s largest 14m x 4m waterjet cutting machine – enabling Steel Dynamics UK to produce the parts customers’ require, exactly when they need them.
In 2019, the Group acquired Bornmore Metals, a company that has been delivering premium quality non-ferrous products to customers all over the UK for more than 40 years. Specialising in supplying all-brass metal products, Bornmore Metals also carries a very impressive inventory of non-ferrous metals in all shapes and sizes, available for immediate delivery from the 26,000 square foot modern facility in Blackburn, Lancashire.
As well as offering an extensive stock range of non-ferrous metals to a wide range of markets, Bornmore Metals is also able to offer value added services to all its customers, such as cutting, polishing and coating. In addition, the company’s state of the art CNC bar cutting provides complete accuracy on all metals up to 20 inch diameter, and
Bornmore Metals also offers dull polishing and mirror polishing on brass, copper and stainless steel – on a quick turnaround thanks to its new in-house polishing machines.
The next business to be added to the Group was Offshore Stainless Supplies, which was acquired in June 2021. Specialising in stainless steel, duplex, super duplex and nickel alloys, Offshore Stainless Supplies has the ability to cold draw unique long lengths with close tolerance sections, in round, hexagon, rectangular and square sections, for the production of unique products such as valve bodies and fasteners.
With access to over 3,000 tonnes of stainless steel, duplex and nickel alloy grades, together with recent investments in cold drawing machinery and production facilities, Offshore Stainless Supplies is capable of producing custom lengths of up to 10.8m from rod coils, and up to 14m on its bar-to-bar draw benches. The company also holds 1,500 tonnes of cold drawn sizes on its shelves, rather than being manufactured on a lead time.
Offshore Stainless Supplies is also a large stockholder of 1.4003 stainless steel and has its own ‘cut to length’ facilities for 1.4003 sheet from coils, for both stock and specific customer orders.
“Whether customers’ require standard sizes or custom specifications, the Offshore Stainless Supplies’ facilities are equipped to fulfil orders of any scale with precision and reliability,” reports Simon Howorth, group marketing manager at Steel Dynamics. “The team at Offshore Stainless Supplies like nothing more than working with our customers to support the engineering challenges they present to them.”
The final business within the Steel Dynamics Group is P&P Non-Ferrous Ltd, which was acquired in December 2021. P&P Non-Ferrous has a proud history of supplying the UK non-ferrous market from its head office in the West Midlands and has a sales and distribution centre in Dorset, as well as dedicated sales offices in Bristol and Essex.
P&P Non-Ferrous is a specialist in aluminium, brass, bronze, copper and stainless steel – all held in stock and processed to customer requirements. “Whether it is a requirement for full bars, sheets, cut plates or billets, P&P Non-Ferrous will guarantee fast, accurate deliveries at
Producing UNS 32760 Super Duplex
Strain hardened bars for Fasteners to MDS D59/D59L Rev 3
very competitive prices. It has been supplying the industry for 40 years, so it’s rare that it doesn’t have exactly what a customer needs,” explains Simon. “With over 3,000 non-ferrous products in stock, and a dedicated cutting centre, customers are able to get in touch with the experienced team at P&P Non-Ferrous for their next multi-metal requirement.”
Within the last three years, each company in the Steel Dynamics Group has moved into new premises and manufacturing facilities, as well as having received machinery investments in state of the art processing equipment – all with a focus on sustainable UK manufacturing and ensuring machinery and facilities are energy efficient. “The Group’s dedication to continually invest in the latest technology means it has a broader offering of added value processing, finishing and inspection than any other metal service centre in Europe,” states Simon. “At Steel Dynamics Group we offer customers instant access to a comprehensive inventory of non-ferrous metal product lines. The Group strategy is to deliver profitable growth by leveraging our businesses in to emerging markets in the UK and worldwide. That is why the Steel Dynamics Group operates a best practice regime, which means continuous improvement in processes and sustainable manufacturing, quality standards, customer service and new technologies. This consistent investment allows the group businesses to review their cost bases to be lean, efficient and competitive. With recent acquisitions, new premises, investments in capital equipment, and significant stock holding in stainless steel, aluminium, copper, and brass, it’s a great time to talk to the Steel Dynamics Group about what we can offer.”
Extra steps that the Steel Dynamics Group has taken to provide a complete service to customers includes making sure its metal service centre is ISO 19443 accredited – making it the world’s only metal service centre to have received such an accreditation – reinforcing its position as one of the leading suppliers of stainless steel to the nuclear industry. “ISO 19443 is a quality management standard for the nuclear industry and our accreditation demonstrates our commitment to quality and health & safety, as well as providing customers with complete reassurance that all their materials meet the highest possible standards,” underlines Simon.
Earlier this year, Offshore Stainless Supplies also received the NORSOK approval to produce UNS 32760 super duplex strain hardened bars for fasteners to MDS D59/D59L Rev 3. The NORSOK standards are developed by the Norwegian petroleum industry to ensure adequate safety, value adding and cost effectiveness for petroleum industry developments and operations.
Specialising in stainless steel, duplex, super duplex and nickel alloys, Offshore Stainless Supplies has the ability to cold draw unique long lengths with close tolerance sections…”
“Obtaining the NORSOK accreditation is a significant achievement for Offshore Stainless Supplies and could be a potential game changer in the industry,” explains Simon. “It opens doors to high-value projects in the oil and gas sector – where adherence to strict quality and performance standards is paramount, especially projects that require NORSOK approved materials – giving us access to lucrative opportunities.”
Simon continues: “Being the sole UK manufacturer with NORSOK accreditation for producing UNS 32760 super duplex strain hardened cold drawn bars not only enhances the company’s reputation within the industry, but it is also a great opportunity to target international markets where NORSOK compliance is required or preferred, thereby broadening our customer base and revenue streams. Furthermore, Offshore Stainless Supplies is the only UK company that can cold draw stainless steel, super duplex and nickel alloy bars above 2.5 inch diameter. In fact, we have the capability to draw from up to 4 inch diameter due to the size and power of our draw benches.”
Offshore Stainless Supplies has also implemented a lot of changes over the last few months, particularly in the manufacturing facility, where it has made a number of efficiencies and process improvements to increase its production capacity. “Our cutting edge technology, skilled workforce and advanced infrastructure allows Offshore Stainless Supplies to efficiently cold draw large volumes of materials, ensuring seamless operations and enabling the company to respond swiftly to customer demands,” concludes Simon.
www.steel-dynamics.co.uk
www.offshorestainless.com
Through innovation, quality, reliability, as well as obtaining EN/AS 9100 accreditation for its quality management system, Growermetal’s history has been characterised by constant investments in the aerospace and defence sector – with the company stepping into a new phase of its evolution.
Thanks to its 70 year long expertise in parts development and manufacturing, the Italian manufacturer offers a wide portfolio of fastening solutions for the widest uses and the most challenging applications, including automotive, railway, construction, transportation, electromechanics, power generation, oil & gas, industrial and aerospace.
The aerospace sector in particular has become central since 2021, which is when Growermetal achieved EN/AS 9100 certification for its quality management system – aligning with the aerospace specifications. This accomplishment represented a significant milestone for Growermetal, as it opened the doors to aerospace and defence markets – setting the company among the most authoritative suppliers in the industry.
Two aspects in particular have contributed to this goal. Firstly, the company’s ongoing investments in research and innovation have given life to more and more efficient solutions, leading to the participation in important projects and to the launch of new designs. Secondly, the solidity of the in-house structure and the variety of services make Growermetal stand out as a reference point for customers looking for reliability and flexible solutions.
All this, together with the activity of the two sales branches of Growermetal Do Mercosul in Brasil and Growermetal USA in North America, has contributed to the creation of an international network and to the growing use of Growermetal products for aerospace applications worldwide.
“To understand the recent evolution undertaken by Growermetal, it may be useful to give a brief look at the context of the aerospace and defence market,” explains Paolo Cattaneo, CEO of Growermetal SpA. “Domestic commercial aviation lived an upward tendency in 2023, and the aerospace and defence sector in general witnessed a recovery in product demand. The market growth is expected to continue in the next few years, forcing companies involved in the aerospace and defence supply chain to deal with new challenges.”
Paolo continues: “The integration of digitalisation and cutting edge technologies in the process will be pivotal in this scenario, where reliability, safety and precision reign supreme. The digital transformation is expected to boost the creation of innovative products and enhance the logistics system – while minimising issues and compensating for longer lead times. At the same time, the unavailability of materials after the pandemic has been causing delays
in production and delivery – consequently causing a rise in costs. Therefore the shortage of raw materials will likely remain an issue for the manufacturers of components around the world.”
To deal with this challenging context, Growermetal feels the need to support customers with enhanced services. By maintaining a stock of raw materials and finished products, the washer manufacturer is able to manage potential lack of resources and minimise lead times in this complex situation.
Inaugurated in 2013, the automated warehouse is the expression of Growermetal’s focus on customer satisfaction, which has always characterised the company’s approach. With its self-supporting structure of more than 1,500m 2 of automated area, 11,000 storage locations, 17 storage levels, as well as five laser-guided shuttles and stacker cranes, the warehouse handles more than 4,000 items – moving the goods back and forward in an average 800 missions per day.
“Recently, this capacity has been improved through the combination of the packaging department, which has simplified the handling of the products, while expanding the possibilities of customisation,” points out Paolo. “All this contributed to a rise in flexibility, which is pivotal for highly demanding sectors such as aerospace and defence.”
Such a structure also ensures a ‘Just in Time’ service, in-line with the requirements of the aerospace ever-evolving market. This enables the company to bring many advantages, including a reduction
EXPERIENCE ALLOWS US TO FACE THE MOST CHALLENGING AEROSPACE APPLICATIONS.
Thanks to our advanced processes, treatments, testing and selection certified in accordance with AS/EN 9100 standard, we are the ideal partner to meet the aerospace industry requirements.
With a broad portfolio of washers and components, our products extend Growermetal’s quality and safety in the most challenging applications. This is how we spread innovation and push every limit.
of operating costs, while limiting waiting times, as well as easier monitoring and tracking of goods, plus increased production efficiency.
Another imperative aspect to take into account is the digitalisation of operations. Applied in the production or delivery process, digital technologies open the way to more efficient products and operations, which are essential when addressing the aviation industries that are regulated by demanding requirements and norms. However, to welcome and accelerate this global transformation the suppliers of the aerospace and defence sector are called to modernise their plants, tools and processes. The forward-looking investments in innovation and R&D of Growermetal suit this need, shaping a highly efficient manufacturing system.
From tooling design to surface finishing, every step of Growermetal’s integrated production is monitored and carried out to guarantee the alignment with the demanding standards of aerospace, where reliability, safety and precision are mandatory. For instance, in order to eliminate foreign parts and non-compliant parts, mechanical sorting and optical sorting, with sophisticated camera systems, are delivered in-house. In addition, Growermetal’s variety of services is combined with the constant upgrading of machinery, as shown by the commitment to equipping internal laboratories with the latest generation of measurement devices. The investments in research and development activities not only enabled the creation of a branded range of washer designs (that include Grower TenKeep®, Grower SpheraTech®, Grower Detecto® and Grower Reaction®) but also encouraged collaboration with partners and universities.
When it comes to the Growermetal offer, the range of products available includes special stamped parts tailored to customer requirements, as well as flat washers, spring washers, and safety washers, designed by the company’s engineers to meet aerospace standards such as MS (Military Standard) and NAS (National Aerospace Standard).
The versatility of Growermetal’s offering for aviation extends to the variety of raw materials available, ranging from steel, carbon steel, aluminium, titanium, inconel, brass, copper, bronze, stainless steel, and CRES materials, with an array of surface treatments. Customers can choose from electrolytic zinc plating, cadmium plating, passivation, anodisation, black oxide, mechanical zinc plating, and phosphating, among others, ensuring that their specific needs are met with precision.
“Aerospace applications are subject to high vibrations and extreme environmental conditions, necessitating adherence to rigorous international certifications and standards even down to the smallest detail,” reports Paolo. “To further ensure quality, transparency is paramount, which is why we provide customers with all the necessary technical and quality assurance documentation, aligning with the stringent requirements of the aerospace supply chain.”
Guided by the commitment to the aerospace sector, Growermetal has been forced to reinvent its production models and approach in a transformative way – whilst still maintaining the focus on its flagship products. In this evolution, the relationship with important players of the industry, research centres, and universities, was central and contributed to the creation of a innovation oriented network.
In 2023, another acknowledgment of Growermetal’s commitment to the aerospace industry was the company’s adhesion to the Lombardia Aerospace Cluster, a network that includes more than 100 companies, universities and research centres.
Looking at future steps, participation in important external projects comes along with internal strategic investments, as shown by the building of the GIC – Growermetal Innovation Center. “Started in 2023, this new multifunctional building will be inaugurated in 2024 –becoming central for future projects. It will include new areas dedicated to research and development, laboratories, classrooms for training and spaces for sharing ideas and projects, opening the way to unexplored opportunities for aerospace and defence customers,” reports Paolo.
To promote its services and consolidate its role in the sector, Growermetal has been focusing on some of the most important aerospace international exhibitions worldwide. The company has already taken part in a number of US shows, including HAI HELI-EXPO in Anaheim, Aerospace & Defense Supplier Summit in Seattle and MRO Americas in Chicago, as well as the new edition of the Aerospace and Defense Meetings in Sevilla, Spain.
The aerospace sector in particular has become central since 2021, which is when Growermetal achieved EN/AS 9100 certification for its quality management system – aligning with the aerospace specifications.”
Growermetal will also be travelling to the United Kingdom with the Lombardia Aerospace Cluster, to join the Farnborough International Airshow. The event will take place from 22 nd – 26th July at Farnborough International Exhibition & Conference Centre, bringing together the major international players of the aerospace and defence industry, from SMEs to multinational organisations.
The last pivotal event for the entire aerospace supply chain will be AEROMART 2024, 3 rd – 5 th December, which will connect OEMs, suppliers and manufacturers at Meett Exhibition Centre in Toulouse, France. Featuring more than 1,200 companies from 40 countries, this event will represent in 2024 the final chapter of Growermetal’s journey and another valuable occasion for the manufacturer to introduce its latest products and get in touch with new trends in the aerospace and defence supply chain.
www.growermetal.com
Kinefac® Corporation, a US-based precision machine tool manufacturer that is recognised as a world leader in metal forming technology, is taking a strategic approach to investment, service, and growth of its product portfolio, in order to provide innovative solutions that meet the needs of its customers and markets.
Founded in 1962 by Howard A. Greis (1925 – 2011) –with the vision of advancing cylindrical die rolling technology – the company grew from manufacturing precision cylindrical die thread and form rolling machines to advanced CNC metal processing systems, catering to the global market. Thanks to evolving customer needs, coupled with strong technical leadership, Kinefac® has also expanded its machinery product lines into other metal forming technologies, such as extrusion, radial forming, spring coiling, as well as centre-drive turning.
Today, Kinefac® manufactures a variety of metal processing machine tools, dies, and systems, including thread and form rolling machines, fillet and root rolling machinery, axial push/pull end-forming and extrusion machinery, radial forming and crimping machinery, centre-drive double-end turning machinery, deflection coiling machinery, as well as centrifugal chip spinning machinery. The company can also provide automation and handling solutions with integrated robots, vibratory bowls, conveyors, induction heating systems, as well as custom-built bar loaders and other associated handling.
tools can be found on all continents of the globe, including Antarctica, in both large-scale and small-scale manufacturing environments.”
“We do not just sell standard ‘off the shelf’ machine tools, we offer advanced manufacturing solutions that are specifically configured to meet customer needs,” explains David C. Willens, R&D director at Kinefac®. “These machines make everything from high precision threaded fasteners and actuators for automotive and aerospace applications to micro-sized spring coils for medical devices that go into the human body. Integrated automation and smart feedback sensory features have also become common place in recent years to meet increasing demands for precision, repeatability and control.”
The KineForm division of Kinefac® also manufactures precision cylindrical rolling dies for infeed, through feed, and incremental rolling – with standard and custom thread forms in a variety of high performance tool steels and treatments. The division can also provide die regrinding services with competitive lead times.
“As a business we are ISO 9001:2015 certified and ensure that we offer high accuracy machines, dies, and systems, that push the limits of precision in many different global industries,” states David. “In fact, our machine
Kinefac® is committed to further expanding its product portfolio and manufacturing capabilities to better serve its customers in the metal processing field. This is supported by listening to its customers and by ongoing research and development efforts aimed at introducing innovative solutions to address emerging market demands. “By staying at the forefront of technological advancements, and continuously enhancing our capabilities, we aim to reinforce our position as a leading equipment provider in the fastener manufacturing industry,” underlines David. “We believe innovation is key to the success of a technology driven business, as it helps promote sustainable growth and the opportunity to tackle evolving challenges.”
He adds: “At Kinefac® we strive to achieve total excellence through reliable customer service, technical support and by understanding and meeting those customer needs in the most robust, economical and highquality ways possible. For instance, through our Kinefac® application engineering and technical support – for new and existing projects – customers are able to maximise value and build their technical knowledge of the process. Our trained service technicians not only diagnose and service the equipment, but also offer operator and maintenance training in parallel for efficient production.”
Through its commitment to service and high-quality solutions, Kinefac® can support a wide range of markets, including automotive, aerospace, nuclear and power generation, as well as medical devices, to name just a few. “We see opportunities in a variety of markets and are always looking to see how we can develop what we can offer customers,” points out David. “For instance, the EV market is currently driving change toward lighter and hollow parts, which require precision forms such as splines, threads, worms and knurls. If you look at commercial planes, jet engines, and gas turbine systems, they are also using more and more precision threaded fasteners that are made of exotic alloys – with increased hardness and tensile strength. Medical procedures are also moving into areas of the human body that are requiring smaller and smaller
components, such as precision micro-coils in catheter and guidewire assemblies. Components with tighter tolerances, higher strength, and even micro downsizing, pose a challenge for achieving higher accuracy and precision in production. These trends will force innovation and create new opportunities to apply it and that is where we see opportunities.”
To add to its dedication to products and service, Kinefac® is also well aware of its sustainability responsibilities. That is why its machine tools are offered with options that use environmentally friendly servo-electric actuation systems that only run on demand during each cycle and only use power as needed – helping to eliminate the use of hydraulic oils, constantly spinning motors, as well as sound levels that can have an impact over long periods of time.
To add to this, the types of metal forming processes that Kinefac® machinery performs are a constant volume process and generally do not produce any material waste. This helps to eliminate the need for recycling and the additional costs associated with it. The company also offers a line of centrifugal equipment that enables customers that do produce chips or sludge, with cutting or grinding processes, to effectively separate coolant carry-off from the solids. This allows coolants and chips/sludge to be segregated and properly disposed of and/or reused after filtration, which means customers can take advantage of cost savings while reducing the environmental impact.
In order to continue meeting the needs of its customers Kinefac® has also been making strategic investments within its employees –through continued education – as well as in its in-house rolling die manufacturing operations – with state of the art grinding equipment
and climate control. “The need for driving innovation with technical skills and reaching the next levels of precision with high-efficiency are what influenced these investments,” reports David. “They will also guarantee that our customers receive robust technical solutions and high-quality tooling to further benefit their products. At Kinefac® we anticipate sustained growth in the future – driven by advancements in technology and increasing demands for efficient, higher precision manufacturing processes. That is why we are strategically positioned to capitalise on these opportunities – by investing in cutting edge technology, enhancing our expertise, and by fostering partnerships that enable us to meet evolving market needs effectively. By staying at the forefront of innovation, and maintaining a customer-centric approach, we aim to leverage these trends to drive further success and growth in the metal forming sector.”
For almost seven decades GRAEWE has been firmly established in the fastener market, with the company now achieving a turnover of approximately €50 million – whilst still maintaining the atmosphere of a family owned business that is characterised by a flat hierarchy and a short decision making process.
Since its inception, GRAEWE has proven itself as a specialist in threaded parts, complemented by cutting technology, with the business relying on its manufacturing facilities in Germany to carry out the necessary processes. The company is able to manufacture a variety of DIN and ISO parts and maintains an extensive stock. Additionally, it specialises in the customised production of bespoke parts and precision turned components, based on individual drawings. “Our broad product portfolio includes threaded rods, threaded studs, double-ended studs, stud bolts, head screws, as well as precision turned parts and assemblies,” underlines Martin Vollmert, international sales manager at GRAEWE GmbH & Co KG. “A lot of these products are manufactured in-house, while the remainder is sourced from our partner companies – all bearing the ‘Made in Europe’ quality label.”
GRAEWE takes its in-house production capabilities very seriously and is always looking to develop its capabilities. A prime example is its expertise in the production of high strength cold formed screws, which originated from its close partnership with the company GRAEWE Tadiv in Bosnia and Herzegovina, and has enabled it to strengthen its presence in this particular product market.
In addition, GRAEWE also made the decision to carry out the heat treatment of high strength threaded rods internally and has continuously expanded this area. “This vertical integration ensures excellent transparency in our processes, thereby ensuring consistently high product quality,” points out Martin. “Our customers also benefit from the fact that we are one of the largest manufacturers of high strength threaded rods in Europe.”
Martin adds: “As a reliable partner to both trade and industry, our company has developed into a respected manufacturer of fasteners over the years. This evolution not only showcases our adaptability to evolving market demands, but also our commitment to continuous innovation and enhancement.”
To ensure the quality of its products, GRAEWE also employs targeted supplier selection, rigorous incoming inspections, continuous production monitoring, highly qualified staff, as well as a modern machinery park. Its quality management system is also certified according to DIN EN ISO 9001, enabling seamless traceability of batches.
“Quality and availability are very important to us as they ensure everything runs smoothly,” mentions Martin. “That is why we always keep commonly used items in stock. Also, our trained and experienced team are not only able to assist customers with their purchases but also provides expert advice. Our primary objective is to establish long-term business relationships rather than focusing on short-term transactions.”
The primary markets for GRAEWE extend beyond Germany into central and northern Europe, with the company looking to offer its expertise to customers not only in metric threads but also in multi-start trapezoidal and special threads, as well as machining applications. “We consider ourselves an innovation partner to our customers and – as a manufacturer located in the heart of Europe – we know we can play a significant role in supporting the market and our customers,” states Martin. “The increasing fragility of global supply chains, growing demands for ESG (Environmental, Social, Governance) standards, as well as urgent climate goals, have prompted a heightened inclination towards ‘local sourcing’ for C-parts. Our customers recognise the need to source products in Europe, not only to operate fairly and sustainably but also to reduce their dependence on international supply chains, and by working with us they know they get high-quality products, produced locally, supported by a first class service.”
www.graewe.de
With visitors from 135 countries, this year’s wire® Düsseldorf saw a global spectrum of international visitors. Assistant Editor, Becca England, visited the show to find out how it’s still proving to be an integral part of the fastener industry exhibition calendar after 40 years.
Taking place from 15 th – 19 th April, the five day show saw 1,500 exhibitors from 60 countries showcase trends in wire and cable machines, wire and cable manufacture, glass fibre technologies, mesh welding machinery, as well as fastener and spring technologies across 67,400m 2 – making this year the biggest wire®, in terms of exhibitors, in its history.
Fastener manufacturers were mainly housed in hall 16, with exhibiting companies including Aachener Maschinenbau GmbH, Aichelin, Bonotto Packaging Srl, Can-Eng Furnaces International Ltd, Carlo Salvi SpA, Dimac Srl, Doss Visual Solution Srl,
EJOT SE & Co KG, ENKOTEC AS, GH INDUCTION, GWI Werkzeug und Stahl Vertriebs GmbH, HEROSLAM S.A.L, MANASSERO & C. Srl, MARPOSS GmbH, Mayes & Warwick Ltd, National Machinery LLC, NEDSCHROEF HERENTALS NV, Rockford Manufacturing Group Inc, SACMA Limbiate SpA, Tecno Impianti Srl, Teudeloff GmbH & Co KG, Videx Machine Engineering Ltd, Vision Engineering Ltd, and Weighpack International, among others.
With the record number of exhibitors underlining the importance the show still holds in the industry, the general consensus among fastener industry leaders present was that visitor numbers were quality –not quantity. “We have exhibited in previous years and felt that overall the show matched expectations with its good atmosphere and was the perfect opportunity to showcase our latest developments, see many of our clients, meet new prospects, and have some fruitful discussions. Whilst overall we felt that there were less people in attendance, we had many relevant and serious visitors to our stand,” reflects Lilia Prelević, marketing and sales enablement specialist at ENKOTEC AS.
ENKOTEC showcased its latest innovations, with live demonstrations of the next generation of its ENKOline – the company’s most autonomous in-line set-up to date. The company also used the show to introduce its brand new ENKOfence –a safety feature that enables the autostart/stop capabilities of the line. In addition to this, it also presented a new generation of collating equipment via live stream, as well as the unveiling of a new ENKOsmart Factory software solution –
a system which facilitates ‘real time’ monitoring of nail production facilities, enabling businesses to collect data and analyse their performance in order to make fact-based decisions and improve their efficiency.
Also offering machine demonstrations were National Machinery, exhibiting together with SMART Machinery. The companies offered demonstrations of its FXH2 Lightning double stroke cold header machine, capable of producing up to 400 parts per minute, as well as the SMART NG20 threader which rolls four features in one pass by adding a ring, thread, groove and point.
“The overall show volume was certainly better traffic than in 2022,” states Jerry Bupp, vicepresident sales operations and marketing at National Machinery. “However, we found we had some highquality conversations with visitors from all over the world. In addition to almost all European countries, we had visitors from Brazil, Turkey, the USA, Mexico, Canada and India.”
This years’ event gained global engagement, with visitors of the fair flying in from 135 countries including Austria, Belgium, Canada, Czech Republic, France, Germany, India, Italy, Japan, the Netherlands, Poland, South Korea, Spain, Sweden, Switzerland, Taiwan, Turkey, the UK and the USA. Trade fair organisers also noted that more visitors came from Central and North America, Turkey, as well as Asia, in comparison to previous shows.
Echoing this trend was returning Tube exhibitor GH INDUCTION, an induction machine manufacturer for heat treatment and heating solutions, that exhibited for the first time in the fastener hall, presenting its induction solutions for hardening trilobular and concrete screws, as well as wind turbine fasteners. “There were many visitors interested in our machines including fastener manufacturers, machine manufacturers, automotive parts manufacturers, as well as visitors from the wire and cable sector. Because of the show’s high global presence, only 15% of our visitors were from the German market and we had visitors from India, Turkey, Spain, France, the USA, as well as eastern European countries,” comments Olga Bader, senior marketing specialist at GH INDUCTION.
wire® is set to return to Düsseldorf in two years’ time, taking place from 13 th – 17 th April 2026.
The worldwide fastener industry will once again be visiting the Kaohsiung Exhibitions Centre, from 5 th – 7 th June, to attend the seventh edition of Fastener Taiwan – an exhibition dedicated to shining a light on the latest developments and highlighting high-value fastener innovations within the Taiwanese fastener market.
At the heart of Fastener Taiwan 2024 will be a focus on ‘green sustainability’, with a Sustainability Zone to provide a glimpse on how the Taiwanese fastener industry is leading the way with green manufacturing.
The Sustainability Zone will showcase eco-friendly practices and innovations, as well as sustainable developments.
There will also be a ‘high-value fastener gallery’ where visitors are encouraged to explore new innovations and engage in in-depth discussions on high-value fasteners. The gallery stands as a testament to the industry’s commitment to excellence and will showcase cutting edge technologies and applications, as well as defining the concept of ‘high value’. From advanced materials to precision engineering, exhibitors will unveil innovations elevating the industry, emphasising quality, durability and advanced functionalities.
To add to this, there will be the Fastener Industry Forum where visitors can learn more about international carbon rights, Artificial Intelligence, as well as Smart manufacturing. The forum aims to give attendees a valuable insight for navigating the challenges of a net-zero transition.
Fastener Taiwan is the only international B2B fastener show in Taiwan and serves as a trading platform for sourcing and procurement, with over 300 companies already confirming their participation, across 1,000 booths. Exhibitors will be showcasing a complete range of fastener products including raw materials, moulds, tooling, nuts, bolts, screws, as well as fastener machinery.
Presenting the entire integrated supply chain of Taiwan’s fastener industry confirms the show as an important international gathering, as well as a vibrant celebration of innovation and progress within the fastener industry.
The show is nestled within the dynamic industrial ecosystem of southern Taiwan, where a strategic hub consists of the entire supply chain, from upstream to downstream. Here, a multitude of enterprises, specialising in mould production, electroplating, and surface treatment, strategically position themselves near key manufacturing facilities.
This strategic alignment offers a distinct advantage. In contrast to the intricate process of procuring screws and nuts from overseas, often involving lengthy journeys and cross-border complexities, southern Taiwan boasts a network of suppliers within a half hour drive. This localised and efficient supply chain not only saves time but also significantly reduces procurement costs for businesses.
Online pre-registration for Fastener Taiwan 2024 is now open: www.fastenertaiwan.com.tw/en/register-pro-visitor/index.html
Kaohsiung, Taiwan
5 Jun – 7 Jun 2024
www.fastenertaiwan.com.tw
Specialist fastener show.
Aircraft Interiors Expo
Hamburg, Germany
28 May – 30 May 2024
www.aircraftinteriorsexpo.com
The world’s leading marketplace for airlines and the supply chain to meet.
Heat and Surface Treatment Show
Toulouse, France
5 Jun – 7 Jun 2024
https://en.a3ts.org
A major event for the materials processing industry.
Electric & Hybrid Vehicle Technology Expo
Stuttgart, Germany
18 Jun – 20 Jun 2024
www.evtechexpo.eu
Europe’s largest advanced battery and electric vehicle tech conference.
Intersolar Europe
Munich, Germany
19 Jun – 21 Jun 2024
www.intersolar.de
International exhibition for solar technology.
Manufacturing World Tokyo
Tokyo, Japan
19 Jun – 21 Jun 2024
www.manufacturing-world.jp
Asia’s leading B2B trade show for mechanical components and processing technology.
Automotive Manufacturing 2024
Bangkok, Thailand
19 Jun – 22 Jun 2024
www.automanexpo.com
An exhibition for automotive parts production technology.
Adhesives & Bonding Expo
Michigan, USA
25 Jun – 27 Jun 2024
www.adhesivesandbondingexpo.com
Innovative bonding products and technology.
ECCM21
Nantes, France
2 Jul – 5 Jul 2024
www.eccm21.org
The 21 st European conference on composite materials for academia and industry.
Fastener Fair India
New Delhi, India
26 Jul – 28 Jul 2024
www.fastenerfairindia.com
The fastener event for India.
Vietnam Maunfacturing Expo
Hanoi, Vietnam
7 Aug – 9 Aug 2024
www.vme-expo.com
Vietnam’s leading exhibition on machinery and technology for manufacturing.
Intersolar South America
São Paulo, Brazil
27 Aug – 29 Aug 2024
www.intersolar.net.br
Exhibition for the South American solar industry.
SchraubTec Bochum
Bochum, Germany
4 Sep 2024
www.schraubtec.com
German regional trade fairs for screw connections.
Returning to its regular venue date after the special edition in autumn 2022, this year’s EISENWARENMESSE –International Hardware Fair saw 38,000 trade visitors –of which 70% were international, from 133 countries, confirming the show as an important date in the global hardware industry calendar.
Taking place from 3 rd – 6th March, this year’s exhibition saw 92% of its 3,200 exhibitors come from 54 countries, presenting the current trends and new products in the tools and accessories, industrial supply, fixing and fastening technology, building supplies and home improvement sections.
Fastening and fixing technology exhibitors were mainly housed in hall 11.2 with companies such as Ambrovit SpA, ARaymond France SAS, Bossong SpA, EuroTec GmbH, Fixi Srl, Friulsider SpA, G & B Fissaggi Srl, I.N.G. Fixations, Ober SpA, pgb Europe N.V, Prebena Wilfried Bornemann GmbH & Co KG, F REYHER Nchfg. GmbH & Co KG, Rivit Srl, SIPA Srl, Tecfi SpA, TITIBI di Morandini Ermanno & C, VIPA SpA and Yuyao Alfirste Hardware Co Ltd exhibiting.
“All of the exhibiting companies praised the excellent quality of the visitors, underpinning its relevance as the key meeting point for industry trends and product innovations. The positive response and the return of many companies confirm that the March date fits in perfectly with the innovation cycle of the industry,” states Oliver Frese, chief operating officer of organisers Koelnmesse GmbH.
Thomas Dammann, chief executive director of the Central Association of the Hardware Trade e.V., emphasised the significance of the trade fair for the specialised trade: “In times of scarce resources and the current challenges, EISENWARENMESSE gave the specialised trade and B2B sector a very comprehensive overview of the European and international market for the tools and hardware industry. For the specialised trade it primarily served as a platform for new products, personal contacts, and the consolidation of partnerships, whilst keeping an eye on trends and new suppliers.”
The next EISENWARENMESSE – International Hardware Fair will be held from 3 rd – 6th March 2026, once again at the fair grounds of Koelnmesse. Taking into account the wishes of the industry for a stronger focus on the business days, it will now run from Tuesday until Friday.
Afera, the European Adhesive Tape Association, recently held the 11 th edition of its biennial ‘Tape College’, to teach the fundamentals and current technical essentials of adhesive tape technology to the entire tape value chain.
Held in Munich, Germany, the successful event saw the attendance of more than 120 tape related company delegates, including a significant number of professionals in R&D, customer and technical service, sales, marketing, engineering, production, processing and quality assurance, as well as general management.
Attendees represented 69 companies from 15 European countries plus the UAE. Afera members made up 71% of the participants – 44 from Afera member tape manufacturers and 38 from member suppliers of raw materials, machines and packaging.
“Not only did you all come here to benefit from a solid overview of the current technologies of the tape business, but you got to know many new faces – which is just as important,” said Evert Smit, Afera president and director of scouting for sustainability, technology and innovation at Lohmann GmbH & Co KG.
Lectures given by field experts focused on the selection, manufacture, conversion, application, testing, sustainability and EU regulation of tapes, included those entitled ‘Why tapes?’, ‘Tapes deconstructed’, ‘Tape production’, as well as ‘Tape use and testing’.
‘Why tapes?’ focused on a general introduction to adhesive tapes from Afera President Evert Smit. “We don’t need more solutions
for tapes, we need better solutions for solving future needs. Tapes, because of their versatility, help enable the (sustainable) future more than any other bonding technology,” he emphasised.
Caroline Sperling, manager of tesa SE’s customer solution centre in Europe, introduced attendees to Pressure Sensitive Adhesive (PSA) technology, providing a survey of the most important relationships between physical performance and application properties. She aligned adhesive tape technology available with the demands of today and tomorrow’s industrial processes.
Participants feedback was overall positive. “Afera’s ‘Tape College’ was an important event for the Scapa and Mativ teams because it provided a platform on which to learn, work and discuss the future of adhesive tapes. The event is also proof that suppliers, customers and tape manufacturers can work together to innovate faster,” commented Alexandre Despesse, R&D project leader outsourcing, Scapa (France).
Afera’s next event, the 67 th Afera Annual Conference will take place in Thessaloniki, Greece, at the Hyatt Regency from 25 th – 27 th September 2024.
Fastener Fair India 2024, the international exhibition dedicated to fastener and fixing technology, is set to take place from 26th – 28th July, at Pragati Maidan, New Delhi.
Offering a unique opportunity for industry professionals to connect, collaborate and stay abreast of the latest developments in the fastener and fixing industry, the exhibition promises to be an unparalleled networking platform, with over 10,000 industry peers and 200 leading exhibitors expected to attend.
Attendees can look forward to gaining insights into current global trends; meeting decision makers who are shaping the growth of the fastener industry in India; as well as participating in thought-provoking networking sessions. Additionally, the exhibition will showcase the latest technological innovations in the fastener and fixing industry –providing attendees with the opportunity to exchange groundbreaking ideas and technologies in a conducive environment.
“We are thrilled to bring this year’s Fastener Fair India back to New Delhi. This event serves as a catalyst for driving innovation and collaboration within the fastener and fixing industry, and we look forward to welcoming industry professionals from around the world,” comments Vicky Kumar, project director at RX India.
International Hardware Fair Italy returns on 8 th – 9 th May 2025 in Bergamo, strengthened by the success recorded in the 2024 edition of EISENWARENMESSE.
Asecond edition with high expectations will be held in May 2025, alternating in odd years with EISENWARENMESSE. In a continuously changing market, and an evolving international panorama that offers challenges and opportunities, the new edition’s main topics are the advent of Artificial Intelligence, sector trends and the development of European distribution.
Professionals from the hardware, DIY, garden and outdoor, safety, building, and fastener sectors, as well as electrical and industrial supplies from all over Europe, will meet again in Italy.
“A year ago we took on an important challenge, to build an all-Italian exhibition but with a European vocation to give voice to this sector, best expressing the strength of Italian companies – and the market proved us right. The first edition’s results were beyond our expectations, with more than 5,300 visitors from 30 countries. The location in Bergamo was also of great success with a modern structure, as well as being easy to reach from Italy and Europe,” comments Thomas Rosolia, CEO at Koelnmesse Italia.
Early bird tariffs for registrations are available until 31st May 2024.
In this article U. Bourgund, T. Holland-Letz, T. Pregartner and M. Umminger of Construction Fixings Europe focus on the planned concept and timeline for the transition from the existing Construction Products Regulation to the new version, as well as the impact this could have on innovation within the construction sector.
On 10 th April 2024 the European Commission (EC) published the result of the trilogue process (EU parliament, EU Council and EC) of a new Construction Product Regulation (CPR). The document covers all construction products specified on the basis of harmonised European Standards (hEN) and European Assessment Documents (EAD).
The final CPR document is currently still to be translated into the Member States’ languages, which then is the basis for final voting in the EU parliament. Even though the final document is only expected in the
ETAs only in product area 33 ‘Fixings’ as per March 2024, 202 EADs ‘pending for citation’ in total) with issued ETAs, which according to the new CPR are pushed back into the ‘request’ status. So far, no information is provided on what ‘request status’ means in practical terms. This is another element to provide legal uncertainty to the construction industry.
There also seems to be a period of about five years where current EADs have to be reworked according to the new CPR requirements (sustainability, digital elements, etc). These EADs are then the basis for the respective voluntary ETAs that can be used for the newly created DoPC (Declaration of Performance and Conformity). Since the ownership of the EADs are with the EC and the EOTA, these tasks are to be handled with the respective resources in those organisations. The manufacturers have no role during this revision process. There is also the intention to move a certain group of EADs into the area of hEN. Again the related concepts, mandates and resources are fully unclear.
On top of this, other sources from the EC clearly communicate that the delegated/ implementing acts for for the sustainability requirements, as well as the digital concepts, will not be available for the first product families until 2027. This means in other words, at best the transition of current EADs into the frame of the new CPR (into revised EADs or new hEN) can only start from 2027, which means three years are left until the deadline of EADs in 2030.
Considering the existing number of EADs is around 400, and by observing that the EC and EOTA have been publishing about 20 to 30 EADs per year, the likelihood of having all existing EADs transfer into the new legal frame within three years (at best) is close to zero.
Beyond this, if we assume that innovation projects for new products in construction take about two years – and manufacturers usually start investing in innovative products only if it is absolutely clear how the performance of the final product is going to be identified – it could mean that from the date of application of the new CPR, in November 2025, investment in innovative product will stop until new EADs are published. As a consequence, investments in innovative products could stop in the construction sector for several years at European level.
This means that harmonised European Standards (hEN) based on the current CPR will remain valid until a new hEN based on the new CPR is published up until 2039. An EAD based on the current CPR will become invalid in 2030, even if no updated EAD is published.”
In a nutshell, the fastener industry fears the following consequences as a result of the new CPR:
EADs not published under the current CPR will get lost during the transition period, corresponding ETAs may be repealed after the new CPR enters into force.
The transition period for EADs is far too short. Therefore, important EADs that were published within the ‘old’ legal framework will become invalid after approximately 2030.
The complete EOTA/EAD/ETA system will be paralysed at least for the following five years.
Investement in innovation may be stopped and national approval solutions will be preferred by the industry.
The European construction industry is in a difficult phase – triggered by material prices increase, raised interest rates for loans, etc. In this situation additional changes towards sustainability and more digital concepts are needed with no doubts. A new CPR that stops the necessary investment into innovation by repealing the developed EADs, and not replacing them on time with revised ones, is difficult to sell and hard to understand. This could result in leading industry sectors in construction being severely damaged.
What is the reason for allowing the stream of hENs to be smoothly and continuously adapted to the new CPR while the voluntary EAD route (the one for
innovative products and applications) is being disrupted? It is easy and sustainable to allow the EAD revisiting process (to satisfy the requirements from the new CPR) in a similar way like hEN.
Finally, the manufacturers need to find solutions to satisfy the customer needs for existing and new applications in the construction sector. Maybe the solution is to ignore the voluntary EAD route, the European ‘harmonisation’ legal framework and go back to Member States assessments for product qualification. At least this may result in transparency and predictability on an individual Member State level.
References
[1] Ulrich Bourgund, Thomas HollandLetz: ‘Construction Product Regulation (CPR) Revision - possible challenges for the ETA route’, Fastener + Fixing Magazine, Issue 143, September 2023.
[2] European Commission: Information provided at the Eurogypsum meeting, 15 th March 2024.
[3] Council of the European Union: Proposal for a Regulation of the European Parliament and of the Council laying down harmonised conditions for the marketing of construction products, amending Regulation (EU) 2019/1020 and repealing Regulation (EU) 305/2011, 5620/24, Brussels, 1 st February 2024.
As a leading Polish manufacturer of fastening technology, Klimas Wkret-met has looked to fuse the worlds of art and technology, in the service of corporate social responsibility, to create the Klimas Art Gallery, which includes art made entirely of screws.
Klimas Wkret-met explains that thanks to the words of Sahila Lavignia: ‘Create art that makes you happy. Create art that makes you better. Create art that makes money. Create art that changes the world’ the company has taken on this unusual project. Through the Klimas Art Gallery, the company has also been able to achieve three important goals at the same time – to support young artists, to support charity by donating paintings from the Klimas Art Gallery to auctions, as well as to promote ecological wood construction with Klimas products designed for it.
Klimas Wkret-met believes that screws are silent heroes. One of the smallest structural elements, usually invisible to the eye, they are responsible for the durability, stability and load-bearing capacity of a building. “Their power never ceases to fascinate us, which is why, as a leading fastener manufacturer, we are constantly improving them,” explains Maciej Strychalski, marketing director at Klimas Wkret-met. “This fascination also has another dimension, which is why we decided to present our woodscrews in an unusual way – combining art, technology and corporate social responsibility. As part of the Klimas Art Gallery, we have created a unique collection of industrial paintings made in screw art using our branded woodscrews.”
The extraordinary Klimas Art Gallery illustrates the potential of the screw art technique and now comprises 25 pieces, most of them inspired by the world’s most
famous paintings. However, the purpose of its creation is more than that. “It is not only to please the eyes, but also, in a broader sense, to do good. That’s why the paintings are regularly sold at charity auctions, the proceeds of which support the initiatives of foundations and associations close to the Klimas family,” mentions Maciej. “In the more than three decades of its existence, the Klimas brand has made a name for itself as a socially active and responsible brand, and the Klimas Art Gallery project is a crowning achievement – combining social and cultural goals and paying attention to the environmental aspects of business.”
www.klimas.com
Klimas Art Gallery in numbers 90,000 drives used 5,000 hours of work
Artwork weighs 900kg
Staht specialises in manufacturing digital pull testing equipment and software solutions –designed for various industries that require precise and reliable testing of mechanical fastenings amongst other products – with the company recently making several strategic investments to further enhance its product offerings and expand its market reach.
Led by Managing Director Rob Hirst, an ex-global product manager (installed systems) at 3M, Staht Ltd was founded in June 2020 to develop connected on-site testing equipment and software. A qualified mechanical engineer, Rob’s expertise has been pivotal in shaping Staht’s innovative product line – with his two decades of experience, as well as unwavering commitment to quality and innovation, ensuring Staht’s position as a leader in the industry.
“In a world where precision, reliability and durability are paramount, Staht stands tall as a premier manufacturer of pull testers that not only meet but exceed the rigorous demands of industries worldwide,” states Rob. “Our recent investments have been focused on product development, technological enhancements, as well as expanding the sales and distribution network, which we have identified as key areas for growing the business in the future.”
The first area that Staht has invested is in the development of new products, with the company introducing new testing equipment – such as the 25kN and the Staht LT (line tester), which have been designed to cater to specific sectors, such as fall protection and scaffolding. “The
investment included research and development, tooling, inventory and technical documentation,” points out Rob. “The decision to develop these products was driven by market demand for more versatile and sector specific testing solutions.”
Significant investments have also been made in enhancing Staht Connect, a software platform that integrates with Staht’s testing equipment. This includes investments in digital capabilities such as Bluetooth connectivity, Cloud data storage, and the development of mobile and web applications – with the aim to modernise testing workflow and ensure data is easily accessible and securely stored, which will help enhance customers’ operational efficiency.
Staht has also looked to invest in expanding its distribution network globally, including establishing direct sales and rental operations in Europe, as well as distributor-led operations across Europe, Canada, Australia and New Zealand. “This strategic expansion was decided upon to better serve a global customer base and respond more effectively to local market needs,” mentions Rob. “Thanks to investments in these key areas we are able to position the company at the forefront of innovation in the testing equipment industry and provide customers with a broader range of products, tailored to specific industry needs – allowing for more precise and efficient testing.”
Staht is able to work with fastener related customers by providing specialised digital pull testing equipment, which is essential for testing the strength and compliance of fasteners in various applications. The company’s offering includes kits, load cells, adapters, and other accessories, designed to meet the needs of industries that require rigorous testing of anchors, bolts and safety eye bolts. “Our equipment supports a range of force measurements, enhancing the reliability of fastener installations in safety critical environments,” explains Rob.
Staht’s product range includes digital pull testers with different capacities, such as the 60kN and 25kN models, which are suitable for a wide range of applications from construction anchoring to safety eye bolts in fall protection systems. “Our flagship product is the Staht t60 digital pull tester, which enables users to perform tests with ease – with less than 25Nm of torque a user can achieve 60kN,” highlights Rob. “The tester features a sunlight ready full colour screen, meaning it is visible in all light conditions – with the ability to display live and peak load simultaneously. The tester also has a USB rechargeable lithium-ion battery that provides eight hours of continuous testing, as well as a USB-C cable that allows a user to charge ‘on the go’.”
“For all our products we guarantee the quality through several rigorous measures, with each product undergoing extensive testing to ensure reliability and accuracy. This includes both in-house testing, external FEA testing, as well as field testing during the R&D phase,” reports Rob. “From sourcing high-quality materials to implementing advanced manufacturing techniques, Staht maintains strict quality control throughout the production process. We also ensure our products are designed to meet relevant industry standards and regulations, ensuring compliance with safety and quality benchmarks.”
www.staht.com
JCP Construction Products, the specialist fixings division of Owlett-Jaton, offers an impressive range of heavy-duty anchors. To further expand its offering, it has added two new ranges of high performance, ETA certified, multiple use, drop-in anchors.
These deformation controlled zinc plated anchors are suitable for multiple uses in non-structural applications in concrete, as well as in cracked and non-cracked concrete. They are perfect for suspending services with threaded rods or bolts, or fixing a permanent set socket to allow a fixture to be removed, amongst other uses.
The specific design provides the flexibility of using the anchor for applications with limited embedment depths, such as pre-cast and pre-stressed hollow core slabs. The internal thread is suitable for bolts or threaded studs.
Available in both lipped and non-lipped, they are ETA (ETAG 001-6) and CE approved, and offer fire resistance loading. The lipped version ensures the anchor is set flush, thus avoiding over-drilling.
ETA certified drop-in anchors represent the pinnacle of quality, safety and performance in construction fastening solutions. With their superior features and benefits, these anchors are the preferred choice for engineers and contractors seeking reliable and cost-effective solutions for their projects. Specifying ETA approved drop-in anchors demonstrates a commitment to quality and safety.
These new drop-in anchors offer an alternative to JCP’s non approved zinc and yellow plated and ETA certified A4-316 stainless steel ranges. Both of which are also available as lipped and non-lipped.
www.jcpfixings.co.uk
CONFAST has been selected as an official eCommerce distributor of Simpson Strong-Tie products, offering its customers a comprehensive selection of Simpson Strong-Tie products including the Strong-Bolt® 2 anchors in zinc, mechanically galvanised, 304 and 316 stainless steel finishes.
Simpson Strong-Tie is renowned for its innovative products and solutions that enhance the strength, safety and durability of construction projects. With a wide range of anchors, fasteners, and structural systems, Simpson Strong-Tie has been a trusted name in the construction market.
CONFAST is a provider of construction fasteners and accessories, serving customers in the construction industry with a commitment to quality, reliability and customer satisfaction.
This partnership brings together two industry players committed to providing high-quality solutions for the construction industry. “The CONFAST team is thrilled to become an official eCommerce distributor of Simpson Strong-Tie products. This partnership allows us to provide our customers with access to ‘best in class’ construction solutions that meet the highest standards of quality and performance,” comments CONFAST.
Applications can be carried out in a convenient, flexible and secure way with the new fischer FAZ II Plus bolt anchor, be it installing beams and joists or fastening other timber constructions in concrete – with the new anchor having a higher assessed (ETA) tensile load-bearing capacity and material strength than the previous generation.
Various versions of the fischer bolt anchor are available including the FAZ II HBS, made of stainless steel and zinc plated, which enables highly flexible and simple installation. Its extra large washer conforms to the DIN 1052 wood construction standard and improves the force transfer between bolt anchors and joists or beams. There is also the FAZ II Plus GS, which is suitable for applications combined with steel fixtures with slots or with tension anchors, and FAZ II Plus K, which can also be used at a low anchorage depth and requires little drilling.
The European Technical Assessments (ETA – 20/o897 and ETA – 19/0520) certify that the latest FAZ II generation features an even higher tensile load-bearing capacity and material strength, allowing fixing tasks to be completed with fewer anchoring points while maintaining the same level of safety. This results in lower costs and less effort required for applications, such as installing wood constructions in concrete.
Installations in water-filled drill holes can also be carried out without issue with the FAZ II Plus. In addition to aborted holes, compliant installation can be carried out. The assessment also covers nuts in accordance with ISO. Together with additional assessments (RWS, ZTV, ETK), the ETA covers high loads in the event of fire. Higher fire resistance values are
...the latest FAZ II generation features an even higher tensile load-bearing capacity...”
The latest assessments for various substrate materials have further expanded the range of applications. As such, the FAZ II Plus is suitable for C12/15-C80/90 concrete and solid limesand brick. A general design approval allows anchorages in steel fibre-reinforced concrete with the FAZ II, FAZ II R and FAZ II HCR variants, M6 – M24 diameter. An external, independent assessment has confirmed an anchorage service life of up to 120 years. The FAZ II Plus therefore lasts an entire century, making it ideal for large, long-lasting construction projects.
plugs in sizes M8 to M16. It can now be precisely finetuned according to the respective load requirement or the existing component thickness. This allows numerous fixing jobs in wood construction and many other trades to be implemented with shorter plugs, a smaller drilling depth and thinner concrete components, saving both time and money. Small edge and axial spacing and the variable anchoring depth allow optimal fixings under high loads, even in challenging conditions.
Features such as an assessed suitability for dynamic applications allow the powerful anchor to be used for other purposes with high requirements. The new ETA also confirms the suitability of diameter versions M16 – M24 in zinc-plated and stainless steel materials for medium dynamic loads in cracked and noncracked concrete. An additional Dynamic Set makes it easier to install dynamic applications safely. Regarding applications in seismic regions, the assessment covers seismic performance categories C1 and C2, both with and without the FFD filling disc for filling annular gaps, depending on the diameter.
The new ETA furthermore allows a variable anchoring depth of the
Users can process the FAZ II Plus bolt anchor in holes created with a hollow, hammer or diamond drill using pre-positioned, pushthrough or stand-off installation, depending on the situation. The cone bolt is pulled into the expansion clip by tightening the nut, expanding firmly against the wall of the drill hole. The anchor is then able to carry loads immediately.
Overall, the FAZ II Plus bolt anchor offers advantages with its high load-bearing capacity in concrete and its suitability for numerous fixing jobs in various trades. The comprehensive assessment covers secure fixings, even of unusual attachments. An additional ICC approval enables its simple application in buildings in the USA and countries in the Far East.
www.fischer-international.com
The smart new Samac Performance Plus woodscrews trade case, from Samac Fixings, is packed with hundreds of high performance woodscrews, making it ideal for every fixing job on-site.
Designed with a robust handle for seamless site-to-site transit, and built to absorb the bumps and knocks of construction life, this durable and robust case will protect screws from dust, debris and water.
The trade case is packed with the ultimate collection of 900 precision engineered screws, designed for excellence in any fixings task, with the screws designed with a Pozi-drive and robust double countersunk head to reduce the chances of head breakage and self-countersinking ribs, to help guarantee a sleek, flush finish every time.
With a specialised protective coating, these screws are also corrosion resistant, while the milling thread and serrated thread work in tandem to minimise resistance and prevent the dreaded wood split, ensuring a secure fit that lasts.
Bossong SpA is continuing its position as a reference point for chemical anchoring with the introduction of the new BCR HYBRID chemical anchor, which the company highlights meets the current needs of markets that require fast, universal, multipurpose and environmentally certified products.
With two ETA accreditations (ETA – 15/0559) and (ETA – 24/0016), updated in accordance with the Construction Products Regulation 305/2011, the new BCR HYBRID is a universal bi-component hybrid chemical anchor, without styrene, for medium/heavy loads and applications in concrete and masonry. The product also has CE Marking.
The first ETA (ETA – 15/0559) covers the BCR HYBRID according to EAD-330499 for non-cracked concrete, Option 7, in diameters from M8 – M24, and for bars with improved adhesion from 8mm – 16mm. As well as this, the BCR HYBRID is covered under Option 1 – performance for cracked concrete, for bars M10, M12, M14 and M16.
The product also has seismic qualification according to EAD-330499 and is qualified in seismic category C1 for diameters M12 – M16 and seismic category C2 for M12 diameter.
Approved for fixings with a variable anchorage depth, the BCR HYBRID provides high flexibility to the designer, as well as maximum anchorage depth of up to twenty times the nominal diameter of the threaded rod, with reduced edge distances – allowing its use even in structural elements with limited dimensions. The anchor can be used in dry, wet and flooded concrete, as the hardening reaction of the product even occurs in the presence of water.
The second ETA (ETA – 24/0016) covers the BCR HYBRID according to EAD-330076 for fixings on solid and hollow masonry under static action. Specifically, the product is certified for applications on eight
different masonry blocks, including solid masonry blocks, hollow masonry and AAC (autoclaved aerated concrete) blocks.
The threaded rods covered by the certification range from M8 – M16 in diameter, while the plastic cages for use on hollow bricks range from diameter GC 12x60 for M8 rods to cages GC 15x135 or GC20x85 for threaded bars M10 – M12. Also, for use on solid masonry, there are performances for bars with improved adhesion with diameters 8mm – 12mm, which follow typical applications of reinforcement on load-bearing masonry, adjustments, and reinforcements with reinforced plaster.
The BCR HYBRID product is also currently undergoing testing to obtain a third ETA-CE certification for applications on solid brick masonry under seismic action. Furthermore, the product is equipped with an EPD, an environmental product certification, which is currently in high demand – especially in public works and large construction sites where environmental product aspects are strongly considered. Thanks to the absence of styrene, it can also be used in enclosed environments.
The resin, due to its high adhesion value and ease of penetration into porosities and voids, also allows for secure fixing without expansion and therefore without tension in the base material during installation. The resin and hardener only mix during extrusion by passing the product through the dedicated mixer. No pre-mixing is required. It can also be used as a repair and filling compound.
www.bossong.com
EJOT Colorfast fasteners have been used in the creation of the metal building envelope for a new 60,000 square foot parcel hub near Wolverhampton, UK, which is designed to be amongst the UK’s most sustainable buildings of its kind.
Developed by Trebor Developments and Schroders Capital UK Real Estate Fund (SCREF), the new state of the art facility at Revolution Park will be a regional base for leading European parcel delivery company DPD, which has agreed a 25 year lease.
Installed by Halesowen-based UK Industrial Roof & Cladding, the building envelope is also designed with carbon savings in mind to an extremely well insulated standard, and it is here where 93,000 EJOT Colorfast over moulded fasteners made an important contribution.
Using a mix of EJOT Colorfast CF15 and CF19 JT3-3-5.5 X 25 self-drilling fasteners in conjunction with a TATA Steel Trisobuild built-up system for the roof, meant that a high-level of thermal insulation could be assured for a variety of reasons. Firstly, the design of Colorfast’s head and washer ensures that a consistent seal can be provided above the sheet to achieve a level of airtightness that may not be possible with other types of
colour matched fasteners, it also minimises the risk of water ingress.
Secondly, the materials used in the manufacture of Colorfast mean the level of heat transfer from outside to in and vice versa is limited. This is particularly the case for stainless steel fasteners of the type used here at Revolution Park, which conduct heat much less than their coated carbon steel equivalents. In addition, the nylon over-moulded head acts as an additional thermal insulator, as well as enhancing the building aesthetics.
The final sustainable dimension to Colorfast is product longevity. Stainless steel Colorfast fasteners are highly resistant to corrosion, which means they are approved for
use in building envelope designs that qualify for a 25 year TATA Platinum Plus Warranty. This is a guarantee derived from a tailored specification designed to offer long-term durability and building performance, with the result being lower cost of ownership through the life of the building.
In addition to the long-term functional benefits, Colorfast’s lasting colour also ensures that aesthetics are optimised throughout the building envelope’s design life. EJOT UK has developed over-moulding technology that ensures the fastener’s head is resistant to the effects of the weather and its colour is UV-stable to stay consistent with the panels it is attaching, regardless of which of the 400 or so colours are specified.
A new HD Max construction adhesive, from DAP Global Inc, has a premium hybrid formula with polyurethane strength, providing superior durability and powerful adhesion – even in extreme temperatures.
Featuring polyurethane strength, HD Max bonds virtually everything – from non-porous substrates such as aluminium, PVC, and mirror, to porous, textured materials such as brick, concrete and drywall – with exceptional adhesion and superior durability in both indoor and outdoor environments.
Whether working in heat or cold, HD Max has the ability to bond in extreme temperatures, as it can bond anywhere from 0°F to 120°F (0°C to 48.8°C). Its low odour formula also makes it ideal for interior use.
HD Max also elevates user experience with its ability to adhere to wet surfaces while being easy to gun and control, whilst delivering a solid and waterproof bond that’s reliable and flexible. It is available in a 28 fluid ounce cartridge, making it an excellent value hybrid formula for users looking to accomplish larger jobs.
“HD Max provides a premium hybrid formula that would be a workhorse adhesive for many projects, in many conditions. The 28 fluid ounce cartridge makes HD Max the perfect combination of value and performance, offering a hybrid solution for larger jobs,” comments Matt Nolder, adhesives product manager at DAP.
Exclusively only at www.noegel.de • schulte@noegel.de The QUEEN OF SCREWS no pre-drilling needed patented unique technology
Following an agreement with the European Organisation of Technical Assessments, here is a list of recent ETAs published in the last two months on the EOTA website.
It is important to note that existing ETAs may be amended or withdrawn so this list should not be considered definitive. For further information and a full list of valid ETAs visit EOTA’s website. If you have recently received an ETA, and would like to have it included in our table, please email us the full details at editor@verulammedia.com www.eota.eu
ETA - 24/0095 GFC Structa™6 Screw Anchor GFC Fasteners & Construction Products
ETA - 24/0115 Akfix C900 Polyester Chemical Anchor N/A
ETA - 24/0165 VinyMaxx FABORY GROUP
ETA - 24/0168 AcryMaxx FABORY GROUP
ETA - 24/0240 ChemMates™ Injection System VSF200 for concrete
Ideal Fasteners PTY Limited
ETA - 24/0271 REbond EP CARTRIDGE RECONCRETE Srl
Mortar systems for use in concrete
ETA - 24/0108 RETE DT0355EP and RETE DT0590EP (FRP meshes) ANGOLARE DT0355EP (FRP mesh corner element) N/A
ETA - 24/0113 OLY MESH GLASS SYSTEMS Olympus Srl
ETA - 24/0114 KIMITECH GFRP MESH Kimia SpA
ETA - 24/0132 XNET FORT 355, XNET FORT 590 (FRP meshes) and XNET FORT 355 A (FRP mesh corner element) N/A
ETA - 24/0149 NET GFRP System T&C Building Materials Srl
ETA - 24/0154 ARMORCRETE PLUS UNICALCE SpA
Mechanical fasteners for use in concrete
ETA - 24/0130 FASTA ROD concrete screw Drillfast Pty Ltd
Metal injection anchors for use in masonry
ETA - 24/0242 ChemMates™ Injection System VSF200
Ideal Fasteners PTY Limited
ETA
Anchor devices for fastening systems to timber structures
ETA - 24/0100
SOPREMA GmbH
SOPRASAFE ANCHOR - PRO-FXPFOSTEN-W/T personal fall protection equipment –anchor device
ETA - 24/0101 SOPRASAFE ANCHOR - PRO-FXPFOSTEN-C personal fall protection equipment - anchor device
SOPREMA GmbH
Screws and threaded rods for use in timber constructions
ETA - 24/0222 HSB Chipboard Screw and HSB Wood Construction Screw
Load-bearing anchors for steel structures
ETA - 24/0106 FARFALLA B38
HSB-Vertriebs GmbH
Mair Wilfried GmbH
ETA - 24/0107 FARFALLA B25 Mair Wilfried GmbH
Post-installed rebar with mortar under seismic action
ETA - 24/0144 2KPS EX100-31 Series for rebar connection N/A
ETA - 24/0167 AcryMaxx FABORY GROUP
Systems for post-installed rebar connections with mortar
ETA - 24/0270 REbond EP CARTRIDGE for rebar connections RECONCRETE Srl
ETA - 24/0241 ChemMates™ Injection System VSF200 forrebar
Ideal Fasteners PTY Limited
Eurotec’s concrete frame screws have been successfully tested in classes RC2 / RC2N and RC3, highlighting the robustness and versatility of the concrete frame screws – with the testing procedure involving two different types of loading to determine resistance.
The classification RC2 / RC3 refers to resistance against burglary attempts and is a security class according to European standards. In this context, ‘RC’ stands for ‘Resistance Class’ and RC2 represents a specific level of resistance against manual burglary attempts.
In determining resistance under static loading according to EN 1628:2021-06, the test specimen was loaded at specific points according to standard requirements, with permeability checked after each loading. These tests reflect real installation situations and ensure reliable performance in practice.
Furthermore, resistance under dynamic loading was determined according to EN 1629:2021-06. For this determination, a test specimen was mounted in a torsionally rigid test frame and subjected to impact from a pendulum body (50kg twin wheels/EN 12600) at various points.
The final test involved determining resistance against manual burglary attempts according to EN 1630:2021-06. In this procedure, based on DIN EN 1630, the burglary resistance is assessed by using defined tools to evaluate the resistance of the tested material against manual burglary attempts.
The successful classification of Eurotec’s concrete frame screw not only reaffirms its quality but also its commitment to meeting the highest standards. “At Eurotec we continue to offer innovative solutions that meet the requirements of modern construction projects – while also fulfilling the highest safety standards,” explained the company.
NOF METAL COATINGS GROUP is already in the process of planning for the potential ban by the European Chemical Agency on PFAS based on REACH , with the company using it as an opportunity to align its technical requirements on a global scale and to establish rigorous guidelines for the development of a PFAS-free range – helping it build a more global and rational product offer.
NOF METAL COATINGS GROUP designs, develops and manufactures patented waterborne coating solutions for metallic parts, such as fasteners, brake discs and chassis components – with its coatings mainly used to protect against corrosion and control the coefficient of friction in order to guarantee the reliability and longevity of assemblies.
With a worldwide network of more than 300 licensed applicators, the company’s cutting-edge GEOMET ® zinc flake technology is employed by major OEMs in the automotive, truck, construction, agricultural and energy sectors.
PFAS, or poly- (or per-) fluoroalkyl substances, form a large group of over 10,000 fluorinated compounds renowned for their anti-adhesive, waterproof and heat resistant properties. Widely used since the 1950s, in a variety of industrial sectors and everyday products, PFAS are often referred to as ‘the forever chemicals’ and are now coming under increasing scrutiny due to their long-lasting presence in the environment and toxicity.
The European Chemicals Agency (ECHA) is advocating a European ban on PFAS based on REACH , to come into force as early as 2027 for specific industrial segments. Meanwhile, in the USA, the Environmental Protection Agency (EPA) is actively examining PFAS and proposing regulations specifically targeting water contamination. Although a total ban is not expected in the USA, global supply chains will be impacted by the implementation of REACH regulations. Consequently, Asia and South America are also proactively preparing for the elimination of PFAS in order to safeguard and enhance their global production and import capabilities.
NOF METAL COATINGS GROUP is determined to continuously work on the reduction or elimination of all substances that have a negative impact on the environment.
Apart from PTFE, a fluoropolymer currently classified as a ‘polymer of low concern’ by the Organisation for Economic Cooperation and Development (OECD), the company does not use any other PFAS in its products. However, PTFE may be impacted by proposed restrictions.
The PTFE substance is specifically used in some lubricated coatings, which are applied to fasteners to control their friction coefficients. This makes assembly conditions more reliable and guarantees a safe joint throughout the service life of the final product.
NOF METAL COATINGS GROUP already provides PFAS free products including GEOMET ® 321 (silver anticorrosion basecoat), GEOMET ® 360 (brake disc anticorrosion basecoat), GEOMET ® 430 (dark grey anticorrosion basecoat), and topcoats PLUS® M (silicate based, lubricated topcoat with friction coefficient µ 0.12-0.18) and non-lubricated topcoats PLUS ®, PLUS ® 10 and GEOKOTE ® (organic topcoat with excellent mechanical and chemical resistance).
Driven by a deep commitment to evolution, sustainable practices, and environmental responsibility, NOF METAL COATINGS GROUP has always looked for innovative solutions to reduce its impact on the planet. In fact, as pioneers in the development of water-based zinc flake coatings, the company has always prioritised environmentally friendly alternatives. That’s why, in response to the growing awareness of the threat posed by PFAS, NOF METAL COATINGS GROUP has already initiated a transition to PFAS-free products.
Regardless of potential restrictions imposed by environmental authorities on PTFE, the company will offer a PFAS-free product generation. To achieve this ambitious goal, it has established a dedicated international task force – including R&D, environmental expertise and market insight. This transversal and international team ensures a comprehensive approach to the development process.
The research and the selection of alternatives to PTFE have focused on raw materials that comply with high environmental standards and are available worldwide to guarantee the uniqueness of formulations on all continents.
Beyond the sustainability, inherent to this project, NOF METAL COATINGS GROUP is seizing the opportunity to align its technical requirements on a global scale and to establish rigorous guidelines for the development of its PFAS-free range to build a more global and rational product offer, able to meet industry expectations but also to anticipate upcoming challenges.
Identical performance will be maintained to ensure a consistent product experience when switching to this PFAS-free range. Notably, the PFAS-free alternative of NOF METAL COATINGS GROUP’s current coatings will satisfy the requirements of major OEMs (VW 01131, MBN 10544, GMW 3359, etc) and will have the same outstanding behaviour in loosening tests (including at high temperature), multi-tightening and high-speed tightening; as well as helping avoid stick slip and being compatible with various counterpart materials (eCoat, aluminium and steel).
The company will also be working closely with its network of licensees, parts manufacturers, and OEMs, to minimise the technological impact of this transition. Extensive testing under
‘real life’ industrial conditions will be carried out to guarantee their good applicability, under identical conditions, at licensees’ plants. This will help ensure a level of reliability comparable to the one of current products and also that all the test criteria defined in OEM specifications are met.
As a leading supplier of zinc flake coating technology, NOF METAL COATINGS GROUP is fully aware of its responsibility to support the global fastener industry in addressing the potential challenges posed by a PFAS ban. The company’s forward-looking development approach positions it to offer PFAS-free products in the very near future.
In addition, the industrialisation process of its PFAS-free coatings will be initiated in close collaboration with fastener manufacturers and OEMs, as well as its partners in the supply chain.
For instance, sampling and testing at fastener manufacturers and approval processes at OEMs is already ongoing.
www.nofmetalcoatings.com
Since the beginning of its activity in 2001, SMART Machinery has always been known for innovative technological solutions applied to thread rolling machines. The company’s unrivalled introduction system, managed by a linear motor, and the use of direct drive motorisation are defining features in the field of cutting edge machines.
SMART’s introduction device, a key point of the thread roller, is managed by a linear motor and controlled by sophisticated and dedicated software. All the adjustments, including stroke and timing of the introduction finger, along with placement and pressure of the blank moving into the die, are easily made from the operator panel.
All SMART models are also powered by a patented application of the direct drive motor, which provides full torque from zero speed along with higher energy efficiency than traditional motors. The direct drive motor minimises vibration and requires no maintenance – due to the total absence of chains, pulleys, belts and gears. Not only is the mechanism simplified with fewer mechanical parts, but it also equates to less energy consumption.
Thanks to the REGEN configuration, power produced from the deceleration of the main motor is managed through an additional electronic device that supplies the main motor. This means that instead of losing that power, as normally happens in standard machines, it is saved to be reused. This function allows for the recovery of at least 25% – 30% of the energy that would otherwise be lost, which is a significant saving and excellent example of sustainability.
The REGEN benefits are also increased when coupled with the SMART variable speed option. This increases the speed of the main motor during the idle motion of the main slide and then returns to normal speed when the slide approaches to roll a new part. Thanks to the variable speed the machine runs more total parts at the same nominal speed.
the Auto Setup program for a quick set-up of pre-stored jobs.
With today’s market demands, SMART machines are Industry 4.0 capable, with the ability to collect, store and analyse – while also presenting data relevant to the machine’s performance.”
However, a technologically advanced machine must be simple and user-friendly for the operator, so SMART has another added feature. Available today on the small/ medium size machines is the new stationary die pocket, which is fully motorised. The die block utilises hydraulic clamping with five servomotors, managed by the operator panel. All settings are made by electronic handwheel from the control panel and stored thanks to
The matching of dies driven by servomotor is accurate and repeatable and can be implemented with the automated die match option – to make all the necessary adjustments without any manual adjustments by the operator.
A sturdy bedframe of the machine is expressly designed to roll high-tensile screws after heat treatment, as requested by many automotive manufacturers and for exotic materials, such as titanium, waspaloy and inconel for the aerospace market. To satisfy the needs of some of these specials materials the machines can be equipped with special feeding rails with induction heating units able to reach temperatures up to 600°C – 800°C.
With today’s market demands, SMART machines are Industry 4.0 capable, with the ability to collect, store and analyse – while also presenting data relevant to the machine’s performance. Parts, service and technical assistance are available from any of National Machinery or SMART Machinery’s service locations. National’s worldwide coverage also allows for assistance to customers everywhere in many different languages.
www.smartmachinery.com
While cold forming threads have been around for over a century, setting up these machines remains a challenge. Traditional methods rely on experience and ‘feel’ for pressure adjustments, making it difficult to train new operators and achieve consistent results. Mule Technology is able to offer a refreshing solution – retrofit kits that transform existing flat die thread rolling machines into user-friendly and repeatable set-ups.
With its retrofit kit solution Mule Technology points out that it replaces subjective adjustments with a precise, mechanical memory system. The retrofit kits are compatible with any brand of flat die rolling machine – with the core lying in the Mule Keys™, a set of precision bars and discs that eliminate guesswork.
Complementing the hardware is Mule Recipes ™ , a Cloud-based software program that enables operators to record and store optimal settings (Mule Recipes) for future jobs, streamlining the process significantly.
For those unfamiliar with thread rolling set-up, it might seem straightforward. However, operators face a complex interplay of factors such as timing, pressure, and most importantly, die orientation. Traditionally, this involves adjusting screws and shimming the dies – a process heavily reliant on experience and intuition. Repeatability and optimal set-ups are elusive with this subjective approach.
Mule Technology eliminates the guesswork by offering four precisely recordable and repeatable adjustment points. The package includes a retrofit kit for the machine, a new stationary die pocket with a top clamp, inch or metric Mule Keys™, and the “Mule Recipes™” App.
The Mule Keys™ kit is the heart of the system, enabling precise die positioning. Each kit includes three components – bars, discs and disc inserts. Two bars are used, one at each end of the stationary die pocket. The kit provides various thicknesses (numbered for easy identification) to achieve the desired die distance (overall pressure).
The disc inserts have holes designed to fit the discs, which come in various thicknesses (alphabetically labeled). By adjusting these discs, operators can control die tilt (varying pressure on top versus bottom) and die rate (difference between starting and finishing pressure).
Since each bar and disc is clearly labelled, the optimal combination for a specific job can be documented as a Mule Recipe™, which ensures repeatable set-ups and eliminates inconsistencies.
“Mule Technology streamlined set-ups lead to faster changeovers, maximising machine uptime and increasing machine efficiency by 30%,” states the company. “This translates to increased production capacity and faster turnaround times – thanks to a 60% reduction in set-up times.”
Reduced set-up times also mean less wear on die during set-up, with the reduction or elimination of die break out – with consistent die pressure on the start and finish of the die – which helps all Mule customers experience extending die life. “We simplifiy complex set-ups, making it easy for operators of all experience levels to handle a wider range of parts and help increase responsiveness to changing customer demands,” highlights Mule Technology. “Customers report achieving a positive ROI within two years of implementing Mule Technology this rapid payback period demonstrating the cost-effectiveness of the solution.”
The company concludes: “By simplifying operations, boosting machine efficiency, and increasing production speeds, Mule Technology delivers a compelling combination of value and cost savings. This translates to a more competitive edge, allowing our customers to meet demands faster and with greater agility.”
www.muletechnology.com
Thanks to their reliability and excellence, advanced assembly machines – such as long screw assembly machines – from UTA Auto Industrial Co Ltd, are relied on by fastener manufacturers worldwide to help optimise production processes and maintain high-quality production standards.
Long screw assembly machines from UTA are designed to streamline production, by automatically assembling washers or anchors onto long screws. A cost-effective solution, these machines reduce manual labour and ensure consistent quality – whilst handling various screw sizes, as well as featuring automatic sorting functions to achieve impressive assembly rates, further enhancing productivity.
These assembly machines are available in several models including the SL04-300 machine for screws of 4.8mm – 6.5mm in outer diameter and 150mm – 300mm in length. Available as a two piece with CE certification, the SL04-300 has an assembly speed of 50 – 120 pieces per minute.
Another model, with a faster assembly speed of 100 to 250 pieces per minute, is the SD16-150, again for screws of 4.8mm – 6.5mm in outer diameter, but for screws of 25mm – 150mm in length. These machines have various sensors for feeding, assembly and outputting processes, as well as indicators on the front.
Through a combination of decades of know-how, and its significant R&D potential, SASPI is able to constantly reengineer and update its thread rolling machines to meet the actual and future requirements of customers –without losing the well known reliability and robustness.
The new generation of SASPI thread rolling machines feature a number of innovations that stem from its know-how and R&D capabilities, including a new cast iron body design – with SASPI stating that the cast iron shock absorption and heat expansion properties are unbeatable by other technologies.
Other features include servo driven camless machines; more user-friendly set-ups –with motorised rails and feeding systems, including carbide inserts for longer life and easier replacement; better ergonomics and fulfilment of the latest CE safety standards; state of the art technology implementation for patented die pressure adjustment; electronic handwheel jogging and touchscreen controlled die match – adaptable to the latest process monitoring technologies; a 15 degree single pusher system that ensures a longer die life and better thread quality; as well as wireless remote accessibility and Industry 4.0 connection (with MQTT and OPC-UA protocols), with a built in OEE performance control.
SASPI’s machines can also be equipped with an induction heating unit in which the pieces are heated to a certain temperature. “The machine can ensure the parts are heated to a desired temperature range so the material does not lose properties and only suitable parts are threaded,” explains SASPI. “With over 60 years in the industry, our machines have developed a strong presence in the aerospace, automotive, construction and household sectors.”
In addition to its thread rolling technology, SASPI is able to supply a wide range of secondary operation machines that are highly appreciated for their speed and precision, as well as their high technology and versatility. These machines’ main characteristics are their ability to do various
operations at the same time – shaving, drilling and broaching, as well as heading operations.
A key machine within the SASPI secondary operations range is the MPA automatic pointing machine, which is well known for being a very reliable and easy to use high-speed pointer. It is fully motorised (centring, rails, top rail, cutting depth, etc) and is a very versatile machine that can run parts from M2 (0.078 inches) to M14 (0.55 inches) in lengths from 4mm (0.19 inches) to 150mm (5.9 inches).
“One of the greatest features of the MPA is that every part is held as close to the end as possible during the machining process –regardless of the length,” mentions SASPI. “This means vibrations at maximum are avoided and we gain precision and finishing quality of the part, as well as tool life. This is a unique feature of SASPI machines.”
The MPA machines can be used for pointing and facing, drilling, and broaching, all types of materials, from different steel alloys and parts after heat treatment to materials used in the aerospace industry, such as titanium and inconel. The MPA machine is a 3 in 1 machine with a quick and easy changeover. Its
high-speed and robustness is also appreciated in the automotive industry and its high precision and delicacy with parts is highly recognised in the aerospace industry.
The latest version of the MPA is the MPA-14CL, with its main characteristic being the lack of cams. “Every single movement of the machine will be easily adjustable and configurable to customers’ needs. It will start as a pointing, drilling or broaching machine but its potential is beyond these processes,” reports SASPI. “This user-friendly machine introduces a brand new technology with all the experience and features of the well known SASPI MPA secondary operations machine.”
Another new machine available from SASPI is the new version of the DOM-16, a very reliable and easy to use secondary double operations machine that can be used for pointing and facing, as well as drilling and broaching of all type of materials, from different steel alloys to materials used in the aerospace industry such as titanium and inconel. It is equipped with one machining station for the pointing and drilling operations and a heavy-duty broaching station to broach different profiles. This type of machine is mainly made for the aerospace industry and is highly appreciated for its speed and precision, as well as its high technology and versatility. www.saspi.es
Videx Machine Engineering has expended its stud production lines by incorporating machining and extrusion stations – resulting in the upgraded machines being able to execute multiple operations in a single pass, replacing traditional automatic lathes in the production of straight parts with either turned or extruded ends.
Videx underlines that each turning station is capable of performing up to four operations at the same time, including facing, drilling, chamfering, turning and extruding the diameter – from major diameter to pitch diameter. The parts seamlessly transition between stations via quick servo transfer, enabling all stations to operate simultaneously, thereby optimising time efficiency and the swift completion of each part. For instance, while the first station turns a part, the second station can drill or face the subsequent part. Additionally, the machines can integrate other operations such as heading, flattening and marking.
Before undergoing secondary operations, the machines straighten wire from coil and cut it to the required length. Thread rolling follows the secondary operations in the same line, ensuring that customers receive the finished part fully automated, without any manual handling or operator intervention.
Videx’s oscillating straightener, equipped with four pairs of feed rollers and three straightening shoes, handles the wire straightening. The wire’s length tolerance and repeatability are maintained as it hits a positive stop before being cut off.
Since its inception 85 years ago, Carlo Salvi Machines has been synonymous with precision engineering and cutting edge technology in the realm of wire forming machinery – with the company using its 85th milestone as an opportune moment to reflect on the journey of innovation and excellence that has defined it as a business.
Founded on the principles of quality craftsmanship and unwavering commitment to customer satisfaction, Carlo Salvi Machines has continually pushed the boundaries of what’s possible in the world of wire forming. Its relentless pursuit of innovation has led to the development of revolutionary machines that have transformed industries and redefined standards.
At the heart of its success lies its dedication to understanding and anticipating the evolving needs of customers. This understanding has propelled Carlo Salvi Machines to introduce groundbreaking solutions that address the challenges faced by manufacturers across various sectors.
“One such innovation is our 1-die 2-blow header, a testament to our engineering prowess and precision manufacturing capabilities. This machine sets the benchmark for efficiency and accuracy, allowing for the seamless production of both solid and semi tubular rivets with unparalleled speed and consistency,” reports Carlo Salvi Machines. “In fact, our smallest machine from the series, the CS 001, is considered to be the Ferrari of doublestoke machines – allowing the customer to produce up to 660 parts per minute. As an Italian company, we have always been recognised worldwide for the efficiency and reliability of these kind of machines.”
Building upon this foundation, Carlo Salvi Machines’ 2-die 4-blow header further exemplifies its commitment to pushing the boundaries of possibility. With its advanced features and enhanced performance, this machine empowers manufacturers to tackle even the most demanding wire forming challenges with ease.
machines, capable of forming wire up to 22mm in diameter. The company points out that these machines represent the pinnacle of versatility and efficiency, offering unmatched flexibility in producing a wide range of intricate wire forms to exact specifications.
In order to commemorate its 85th anniversary in 2024, the company has also announced its latest innovation, a brand new double-stroke header. Carlo Salvi Machines explains that the groundbreaking machine is set to revolutionise the industry with its ability to form wire up to 10mm in diameter and a shank length of 165mm, coupled with a cut-off of 200mm. “With its unparalleled precision and efficiency, this machine is poised to set new standards for excellence in wire forming. The prototype is set to be ready by the end of the year, allowing us to enter 2025 with a larger machine fleet and an even larger range of solutions for our trusted customers,” concludes Carlo Salvi Machines. “As we look to the future, we remain committed to driving innovation and exceeding customer expectations. With our rich legacy of excellence as our guiding light, we are poised to continue pushing the boundaries of possibility and shaping the future of wire forming technology for years to come.”
DOSS Visual Solution Srl, a leader in the design and production of inspection systems for the quality check of precision metal components, is constantly committed to supporting customers with new and performing solutions.
DOSS’ solutions are able to measure and control numerous product characteristics, including shape, size, colour, firmness, edge/contour defects, cracks and holes, flatness, surface distribution – via 2D technology, as well as able to perform a complete reconstruction of peripherical view.
The possibility of connecting a very large number of cameras; of customising the lighting system; and the complete configurability of the acquisition and processing software; allows DOSS’ solutions to offer very high system flexibility – guaranteeing the possibility of addressing all industrial control problems with a single artificial vision system.
In an effort to improve quality and efficiency of the machine settings, as well as to make the batch change and maintenance operations easier, DOSS has developed some new functions that help make the vision inspection systems have an even stronger performance, amongst them Artificial Intelligence and Multishot.
“During the recent wire® show in Düsseldorf, Germany, we showed the result of this important technical effort, through a demo of our top machine the DS PRO, which touched on some crucial aspects of visual
British Steel has been granted planning permission to build an electric arc furnace at its Scunthorpe headquarters in the UK. The manufacturer’s proposed GB£1.25 billion (€1.45 billion) transformation – its biggest in more than a century of steelmaking – is subject to appropriate support from the UK government.
Xijun Cao, president and CEO at British Steel, said: “We’re extremely pleased to have received planning permission to build electric arc furnaces at our Scunthorpe and Teesside sites. It is a significant step forward in our journey to ‘net zero’ and we thank everyone who has supported our plans.”
He added: “The proposed installation of electric arc furnaces in Scunthorpe and Teesside is central to our journey to a green future – as they would help us reduce emissions of CO 2 by more than 75%. However, it is crucial we now secure the backing of the UK government. Our owner, Jingye, is committed to the unprecedented investment decarbonisation requires and our desire to dramatically reduce our carbon footprint, coupled with challenging market conditions, means its imperative swift and decisive action is taken to ensure a sustainable future for British Steel.”
Both proposed electric arc furnaces would replace the aging iron and steelmaking operations at British Steel’s Scunthorpe site, which are responsible for the vast majority of its CO 2 emissions. The company proposes maintaining current operations until a transition to electric arc steelmaking.
control, among which the regulation of light intensity and speed of the automation,” underlines DOSS. “The machine, with high computing power, is ready to welcome new developed algorithms, developed with Artificial Intelligence models, which have been validated and approved. Here we go beyond the concept of Industry 5.0, we are already at the interconnection aimed at completely delegating machine jobs to machines, those in which the human operator would not add any value.”
The Multishot technology introduced by DOSS allows an image acquisition of the same part at very high-speed, with different light conditions, by using the same vision unit. This results in a straightforward management of the machine, without being compelled to find a unique ideal light condition to detect the majority of the defects.
“The hardware features allow us to obtain, with a sole camera, results that were previously only possible with several cameras,” reports DOSS. “Experienced operators that are used to working with multiple cameras are delighted that they can now get the same results with one single unit.”
www.doss.it
Ransohoff, a division of Cleaning Technologies Group LLC – a renowned leader in innovative cleaning solutions, has unveiled the Washmaster MCW mini conveyor washer, which has been designed to meet the evolving needs of modern industries.
The MCW mini conveyor washer stands as a testament to Ransohoff’s commitment to excellence – offering an automated continuous wash system with a compact footprint, which the company states helps revolutionise cleaning processes while maximising efficiency.
Crafted using only the finest materials and components, and designed by industry leading engineers, it exemplifies superior quality and performance. Key features of the machine include a customisable option when it comes to processing items, with the option to use a flatwire belt or utilise custom fixtures tailored to specific needs – both of which provide versatility and adaptability to diverse applications.
The Washmaster MCW mini conveyor washer also feature an energy efficient design, which helps reduce utility usage, contributing to cost savings and environmental sustainability. Plus, optional loading and unloading automation further enhances efficiency and streamlines workflow, saving time and labour costs.
“At Ransohoff, we are dedicated to pushing the boundaries of innovation to deliver exceptional cleaning solutions that meet the evolving needs of our customers,” said Jeff Mills, vice-president sales at Ransohoff. “The Washmaster MCW mini conveyor washer embodies our commitment to excellence, offering unmatched performance, reliability and efficiency.”
Specialinsert®, since 1974 in the world of fasteners, thanks to the experience matured and to the continuous research, today it is able to supply the most innovative fastening systems.
Dimac states it has achieved a remarkable milestone with the limited edition version of MCV4 La Mille, a concept machine developed in cooperation with ITW Rivex France for the sorting department of their brand new plant in Ornans, France.
Beyond its ergonomic layout and user-friendly software, this high-speed piece of equipment integrates innovative inspection solutions, driven by high-resolution digital cameras and state of the art Artificial Intelligence algorithms. “The MCV4 La Mille stands as a testament to the successful partnership between Dimac and ITW Rivex, showcasing the commitment to excellence in the sorting department and setting new standards in the industry,” states Massimo Agrati, CEO at Dimac Srl.
Key features of the MCV4 La Mille include mechanical precision –with it ensuring consistent high output rates with rapid changeover procedures. Robust feeding rails, featuring integrated pneumatic propulsion circuits, also guarantee a jamming-free flow of parts towards the steel rotary table, which is driven by a brushless hollow motor of the last generation – with an integrated encoder ensuring the accurate triggering of the control stations. The rotary table of the MCV4 La Mille also boasts interchangeable dials with slots, where headed parts are seamlessly fed in. This feature enhances flexibility and adaptability to varying production needs.
“The machine can also achieve output rates of up to 700 parts per minute, and excels in sorting headed parts ranging from M6 to M8 by 35mm. Non-controlled pieces can also be seamlessly reprocessed without disrupting the continuous flow of incoming parts,” points out Massimo. “To add to this, the AI-driven side surface cameras station, positioned at 120° intervals, covers the entire 360° surface of the shank, identifying even the minutest defects in threaded or cylindrical areas.”
Powered by a modern PLC on Ethercat field-bus connected to the vision machine controller, MCV4 La Mille incorporates a high-resolution graphic card. The entire system is housed in an IP54 cabinet, with an active coolant system ensuring stability even in challenging environments. The MCV4 La Mille has also been developed to consider the requirements of IATF 16949 for the quality control of fasteners, ensuring adherence to the highest industry standards. Equipped with a side profile measuring camera, MCV4 La Mille also guarantees accuracy validated by MSA tests.
“Operating under the Windows 10® system, MCV4 La Mille is driven by the Dimac proprietary software platform that includes the Vision System MCVx, the MCV-PLC system for machine automation and the MCV-AI software for AI recognition,” points out Massimo. “This platform provides an intuitive user interface accessible to operators of all skill levels, featuring essential pop ups and simple filters for quick programming and recipe creation.”
Thanks to the Connectivity Pack, a suite of Apps for the machine connection online and remote programming, it is possible to retrieve sorting cycle data, statistics, and measurements, in SQL format ready to be exchanged with the company’s ERP system.
The MCV4 La Mille’s ergonomic layout ensures the operator’s comfort during programming and mechanical set-up. A mobile console with a 24 inch colour touch LCD, sliding wing doors for easy access, retractable trolley for NOK box handling, lockers for tools, and stainless steel dirt removal trays, enhance the overall user experience.
The machine also offers efficient output handling, with a driven conveyor belt at the rear side of the machine smoothly carrying conforming OK parts out into bins. Ancillary packing machines by Dimac can also be seamlessly integrated for automatic box filling and changing over. Non-conforming parts are efficiently managed, as they are evacuated into segregated NOK boxes housed inside the machine body and extractable by a dedicated trolley. One of the two NOK exits is programmable, allowing isolation of non-conforming parts based on a single inspection criterion selected from the comprehensive list included in the control plan. This meticulous process ensures a seamless workflow, emphasising the machine’s capability to uphold the highest quality standards in fastener production.
“With the MCV4 La Mille customers will discover unparalleled precision, speed, and user comfort – a testament to Dimac’s commitment to innovation towards a zero defect future and helping to ensure compliance with CE standards and IATF 16949 requirements for quality control in mechanical minute components production,” underlines Massimo. www.dimacsrl.com
Our patented SpaceSaver Series combines our innovative wire drawing technology with a robust payo turntable system to help better utilize valuable floor
Why buy a bigger building when you can buy a smaller wire drawer without sacrificing capacity?
Corrosion resistant stainless steel is widely used in industry and trade due to its outstanding properties. Despite its numerous advantages, particularly its resistance to corrosion in numerous media, stainless steel also has considerable weaknesses that sometimes severely limit its application.
One of these weaknesses is its susceptibility to cold welding or galling, which can occur particularly with screw connections. Surface hardening offers a solution to this problem.
Galling can be favoured by various aspects, such as insufficient surface hardness, excessive roughness or lack of lubricants. Nevertheless, fasteners are essential in many applications to allow for particularly frequent assembly and disassembly, or high tightening torques. It is therefore important to carefully tailor the properties of such elements.
When fasteners are jammed due to galling, their removal can turn out to be an enormous challenge, especially if it needs to be done without damaging the affected bolt or destroying the associated nut.
Surface hardening, a process in which only the surface layer (few to tens of microns) of a workpiece is hardened, has been proven to significantly improve the seizure behaviour of stainless steel screws. The diffusion-based process increases the hardness of the surface through solid solution hardening and subsequently reduces its susceptibility to plastic deformation. Depending on the material, the corrosion resistance is maintained or even improved, and the stiffness of the base material is not impaired.
Surface hardening is not an applied coating, but a diffusion-based thermo-chemical surface hardening process. Although classic processes for the surface hardening of corrosion resistant stainless steels have been available to the industry for some time, their application has two main disadvantages. Firstly, all classic processes such as salt bath processes are known to reduce corrosion resistance. On the other hand, the hardness values of stainless steels usually hardened with nitrogen or carbon drop very quickly, i.e the hardening depth is only a few micrometers and the underlying base material is very soft, which can potentially lead to the ‘eggshell’ effect.
In contrast, Expanite has developed its proprietary technology SuperExpanite®, having solved those shortcomings as a priority. With this technological process not only the outermost layer but also the underlying material is hardened to a greater depth, which also contributes to an improvement in corrosion resistance in many cases.
A two stage process is used in Expanite’s treatment for stainless steels, in which nitrogen is introduced deep into the surface area in the first step called ExpaniteHigh-T (high temperature process), whereby the material is hardened to approximately 300HV for austenitic materials and 850HV for alloys with martensitic structure to a depth of up to 1mm. In the second process step, ExpaniteLow-T, the workpiece is heated to temperatures below 500°C and the surface layer is hardened to 1,100HV – 1,300HV at a hardening depth of 5µm - 30µm (depending on the solution). The hardening is achieved by incorporating large amounts of interstitial carbon and nitrogen.
By combining the two process steps, the so-called ‘eggshell’ effect, which occurs in most surface hardening processes, is avoided. This offers a decisive advantage for numerous applications that require improved load-bearing capacity. The hardness profile can be seen in Figure One:
Figure One: Hardness profile of AISI 316L. Below the extremely wear resistant surface layer (produced in the ExpaniteLow-T process, approximately 1,200HV) lies a medium hard transition layer (250HV –300HV), which is created in the ExpaniteHigh-T process. Power curve fitted for visual aid
To test wear resistance, Expanite tested some 316L samples hardened using its SuperExpanite® process to ASTM standard G133. In this procedure (Figure Two) the SuperExpanite® treated test specimen is subjected to the reciprocating motion of 100Cr6 counterpart, under a contact pressure of 25N. The wear volume is determined after a sliding distance of 100 metres. The 316L sample with SuperExpanite® is 125 times more abrasion resistant than the untreated sample.
Figure Two: Wear measurement according to ASTM G133
www.schroederschrauben.de
AND DIGITIZATION OF FORMING PROCESSES FOR INDUSTRY 4.0
The post-process data evaluation offers the possibility to analyze and evaluate the entire process data for the first time. Important conclusions can be found about process variation, setting of monitoring limits and recognition of process influences during the whole production run. The knowledge acquired is helpful in determining the optimum process parameters and provides detailed conclusions about tool wear.
Following the ASTM G133, an ASTM G98 galling test (cold wear) was carried out with test specimens made of AISI 316L, the results of which are shown in Figure Three and Figure Four. In comparison to the unhardened test specimens, which already exhibit galling at a contact pressure of 35 bar, the test specimens hardened with SuperExpanite® do not show any galling even at a contact pressure of 2,758 bar. Even though the first plastic deformations occur at this pressure due to the yield strength being exceeded. The risk of galling is therefore eliminated in the case of both friction partners being hardened.
Although the basic intention of conventional surface hardening processes is to produce harder surfaces, this is usually at the expense of corrosion resistance. This is where the Expanite process comes in. Tests have shown that 316L samples hardened with SuperExpanite® can spend up to 1,000 hours in a salt spray chamber without showing signs of corrosion (Figure Five).
In some cases, the pitting corrosion resistance can even be significantly increased by the Expanite surface hardening process, even beyond the level of the unhardened base material. (Figure Six). This effect is caused mainly by the large amount of nitrogen dissolved in the surface layer. A common formula for calculating the pitting resistance equivalent number (PREN) for alloys not containing tungsten, is:
It is easy to notice a relatively large 16x modifier in front of the nitrogen content expressed in weight percent (wt %). This means that even small amounts of nitrogen have a significant positive influence on pitting resistance.
With the assumption of applicability of this equation for large amounts of dissolved nitrogen[1], usually between 5wt% and 13wt%[2], the PREN number can be calculated. For the AISI 316L alloy the calculated PREN numbers then range from around 100 even up to 230. A minimum of four-fold increase over untreated material, which
has a PREN number of around 24. The underlying ExpaniteHigh-T zone can be characterised with a PREN number of around 30, providing additional improvement even if the case hardening have been damaged or worn down.
A potentiodynamic polarisation curve for SuperExpanite® treated and reference AISI 316 material is shown in Figure Six. This test is a common tool used to evaluate the pitting corrosion potential and characteristics of a metal. There are several highlights that can be derived from the graph, showing the undeniable positive influence of SuperExpanite® treatment on the pitting corrosion resistance of austenitic alloys. Firstly, the open circuit potential of SuperExpanite® treated sample is around 100mV higher than for the reference, suggesting better corrosion resistance in the absence of galvanic coupling. The polarisation curve of the reference material also shows a much narrower passive region, which is characterised with many intermittent peaks (rugged line). Those lines indicate a sudden increase in current density (increased corrosion rate) and subsequent repassivation – initial pit formation. The plot obtained for SuperExpanite® sample is free of those irregularities, and the material stays in the passive zone for potentials almost twice as large, with much more gradual decline towards the breakdown potential.
Despite their widespread use, conventional surface layer hardening processes have various disadvantages. Harmful chemicals such as fluorides, chlorides, molten salts, etc, are used. SuperExpanite®, on the other hand, which is produced using the two stage process described above, is characteriaed by an environmentally conscious approach. Without the use of harmful chemicals, and no polluted wastewater, Expanite represents an environmentally friendly and sustainable alternative.
To summarise, the nitrocarburising process specially developed by Expanite delivers excellent results in terms of both hardness and corrosion resistance for all stainless steel materials, not just limited to individual alloys. The process is therefore recommended for all types of stainless steel screws and fittings to extend the service life of the corresponding components and thus ensure increased product safety and interchangeability.
References
[1] Bottoli, Federico, Morten S. Jellesen, Thomas L. Christiansen, Grethe Winther, and Marcel AJ Somers. ‘High temperature solution-nitriding and low-temperature nitriding of AISI 316: Effect on pitting potential and crevice corrosion performance.’ Applied Surface Science 431 (2018): 24-31.
[2] Christiansen, Thomas, and Marcel AJ Somers. ‘Controlled dissolution of colossal quantities of nitrogen in stainless steel.’ Metallurgical and Materials Transactions A 37 (2006): 675-682.
www.kaleliler.com.tr/en
Here, Volker Hiller, head of business unit mobile testing at Foerster Group, explains the importance of hardness testing for fasteners and how the Group is staying ‘one step ahead’ with its UCI measuring technology for the mobile hardness testing of fasteners – providing maximum flexibility and reliable results.
The non-destructive UCI test method (Ultrasonic Contact Impedance) was first used in 1965 under the name ‘SonoDur’ and the process electronically evaluates and digitally displays the Vickers hardness test indentation within fractions of a second, by a frequency shift. Due to the small indentation size and depth, the process is considered to be non-destructive.
Screws and fasteners must hold components together securely under a wide range of mechanical loads, with environmental conditions placing additional demands on the material properties, structure and surface condition. In addition, there are standards and regulations that fastener manufacturers must take into account, as well as material mix-ups when the raw material is received. This is where surface defect inspection for cracks plays an important role.
The final product is tested for strength, which is usually determined destructively on a selection of parts in a tensile testing machine. The bolts are sorted into property or safety classes with corresponding markings according to the standard. These markings are very extensive, as the many different types of bolts suggest.
Structural steel screws, for example, are divided into strength classes according to tensile strength and yield strength – with a uniform designation on the screw head or on the screw shaft. Since the tensile strength correlates positively with the hardness of the material, and empirical conversion rules exist – e.g according to EN ISO 18265, the hardness test is also repeatedly used for quality assessment for practical reasons. This is particularly important when a larger number of screws or bolts have to be inspected and/or the geometric dimensions are opposed to a tensile test. Although the
SONODUR 3 and UCI measuring probes
classic Vickers, Brinell and Rockwell hardness test is more flexible, it usually requires complex surface processing or the bolt must be cut up and frequently embedded for the testing process.
The situation becomes particularly volatile if, despite all precautionary measures, safety relevant bolts are already installed in the vehicle or on the construction site, for example, and subsequent removal is very difficult. This is where hardness measurement with UCI comes into play for confusion testing, as the measurement can simply be carried out directly on the installed part in any direction quickly and safely.
Now with 5% cobalt for stainless steel for even longer tool life. The new ULTIMATECUT Countersink 4S - with four unequally divided cutting edges for unique performance. Available in dimensions from Ø 10.4 to 40.0 mm. Decide on a faster and better result. More information is available from your specialized retailer or at www.ruko.de.
SCHNORR® is an international leader in engineering and producing safet y washers and disc springs for automotive, aerospace and mechanical applications
Original SCHNORR® safet y washers:
• Highly vibration-resistant
• Twofold effect from one component
• E x tensive range
Original SCHNORR® disc springs:
• Various applications
• Best price -per formance ratio
• Customized solutions
Please contac t us Together we will find your tailor-made solution.
us!
Screws and bolts are manufactured so they are optimised for the application. This includes surface coatings against corrosion or for optimum sliding properties and even local hardness or strength properties through thermal treatment. Thus, at predetermined points, such as bolt head, shaft, and end, the core hardness and surface hardness must be tested with defined test forces between HV 0.3 and HV 10.
Accordingly, the hardness testing methods must be adjusted to these tasks. Before measuring the material, surface coatings must be removed. Measurements on the shaft are difficult for Vickers hardness testing because the surface usually must be ground flat to properly capture the diagonals of the indentation. The test location on the screw must also be easily accessible, which often requires disassembly of the screw due to the complex setup of a testing machine. Finally, the screw must then also be correctly aligned (embedded and polished) in the case of a conical body, because otherwise, depending on the pitch, the optics cannot be focused well enough to evaluate the test indentation.
Depending on the requirements, various test methods are available. The most common methods include Martens (universal hardness), Vickers (HV), Rockwell (HR), Brinell, Knoop, Shore, Barcol and Buchholz.
The essence of UCI hardness testing is the measurement of the acoustic impedance of a body via the frequency shift of a rod vibrating in resonance with Vickers diamonds. The hardness of the material is determined from the frequency shift (Δf) at a certain predefined test force.
SONODUR 3: Portable hardness testing for maximum flexibility and reliable results
Here, the Vickers hardness scale forms the reference for each material. The UCI devices are adjusted to materials with a modulus of elasticity of approximately 210 GPa and can be precisely set to the new task by means of a comparative measurement with a Vickers hardness testing device. This is needed only once because the setting data can be retrieved from the memory again in a reproducible manner.
...screw testing with UCI is very easy and fast through one time comparison with the Vickers scale.”
Thus, screw testing with UCI is very easy and fast through one time comparison with the Vickers scale. Since the UCI probes are pin shaped with thin test tips, they are suited for hardness testing in hard to reach positions.
Nevertheless, the boundary conditions from the application of the UCI method must be observed at this point. The surface must be clean or polished, but not necessarily bright. In addition, the measurement location must be accessible for the probe tip. The component must also be solid and decoupled from possible component resonances. Resonances can usually be recognised by strongly scattered and excessively high or much too low measured values, which are far outside the expected range.
Shafts can still be measured up to 3mm in diameter without special precautions, according to standard DIN 50159-1. With test forces between HV 0.1 UCI (motor measuring probes) and HV 10 UCI (handheld measuring probes), screws can be measured as a whole or also embedded, both manually and in a stand.
Due to the rapidity of UCI measurement, combined with its high precision, a large number of measurements are possible compared to classical methods. As a result, entire measurement series can provide a detailed picture of the treatment result achieved by scanning the shaft.
Foerster Group’s product portfolio includes tools for mobile on-site hardness testing, as well as automated mass production. In addition, the Group offers hand and motor probes of the SONO series with different test forces from 1N to 98N, according to the UCI method, as well as hand sensors for different applications with the Leeb rebound method.
Among the UCI hardness testers, the SONODUR 3 for mobile testing is predestined for difficult testing tasks. It currently has the widest range of probes and accessories in the market. The mobile SONODUR 3 is robust, suitable for industrial use and specially designed and built for rough everyday use. It has a high functionality level similar to that of modern smartphones. The powerful energy concept also has up to eight hours of battery life in continuous operation.
Using the touchscreen, extensive series of measurements can be quickly searched for faulty measurements and evaluated –SONODUR 3 will locate the suspicious measured value. In addition, both the test management (conversion tables, CAL adjustment function and penetration time) and the documentation possibilities (data formats CSV, .txt, HTML, wireless, USB, photo) form a strong argument for the use of SONODUR 3.
The mobile high-tech all rounder is used for quality control in incoming goods and during production, as well as for rapid hardness testing of metallic materials after heat treatment or surface processing. The system is also excellently suited for hardness testing with positions that are difficult to access and for mobile weld seam testing in confined spaces. The layer hardness measurement with several measuring points and its easy adjustment functions on almost all fine grained homogeneous materials round off the SONODUR 3’s range of applications.
The right hardness test method depends on the material being tested and the specific requirements of the application. Understanding the differences among the available options helps determine which method will give the best results.
The most common methods used for testing the hardness of metals are Rockwell, Brinell, Vickers and Knoop. Each of these methods employs different indenters and loads to measure the material’s resistance to plastic deformation. A key distinction between Rockwell testers and Brinell, Vickers and Knoop testers is that the latter three use optical technology, while Rockwell does not, which generally makes it less costly, quicker and easier to test, and the surface finish of the specimen is not so critical. This makes it one of the most commonly used method for metals hardness testing. The optical methods involve the use of a camera system, generally consisting of a digital camera, a light source, and lenses with various magnification strengths.
Other factors to consider when it comes to harndess testing include:
Rockwell testers measure hardness based on the depth of penetration of an indenter into the surface of a material under a known load. Superficial Rockwell is used when the material being tested is relatively thin or has a surface layer that is significantly harder or softer than the bulk material. Brinell, Vickers and Knoop testers measure hardness based on the size and dimensions of the indentation created by a precisely shaped indenter and the load applied.
The Rockwell method uses an indenter with either conical or spherical shape. Brinell hardness testing also uses a hard spherical
indenter, but as already mentioned, rather than measuring depth, measures the diameter of the indentation. Vickers and Knoop hardness tests use a diamond shaped or pyramidal indenter, where the diagonals of the indentation are measured and the hardness value is calculated based on the applied load.
Rockwell methods are well suited for a wide range of materials, especially for metals and alloys, and in many cases the key consideration is the shape and surface of the sample to be tested. The information content gained also plays a role. Most often a single measurement is carried out, which provides general hardness information on the material or area being tested. Rockwell is often used for steel, aluminium, any other metals, as well as plastics and ceramics.
The Rockwell method is further categorised into various scales. Commonly used scales are:
Rockwell C: Typically used on materials with high hardness values, such as tool steels, castings and heat treated materials.
Rockwell B: Comes into play for softer material, including non-ferrous metals like aluminium, copper alloys, brass and softer steel.
Rockwell A: Used on thin, hardened surface layers and shallow case hardened parts. It is suitable for testing more delicate materials because it uses a smaller force compared to other Rockwell scales.
Rockwell T: One of the superficial Rockwell methods and used for thin materials or surface layers, including steel sheets, coatings and plating. The test forces are even lower than with Rockwell A.
Brinell is mostly used for slightly softer metals, but also for large or rough surfaces (when high test forces are used), coarse grained material, and/or high loads up to 3,000kgf. It is commonly applied for tests on materials with a relatively low hardness range, such as non-ferrous metals, castings and softer steels. Materials that fall into a very high hardness scale, or thin and small components, tend to be better suited for Knoop or Vickers testing.
Vickers methods are widely used for microhardness testing, which is essential for measuring the hardness of small or thin materials or for analysing the hardness of specific microstructures in a material. This makes it valuable for examining thin films, coatings, and small features in various industries. Vickers is also often used for series measurements or mappings. This also includes CHD (case hardness depth), SHD (surface hardness depth) and NHD (nitriding hardness depth).
Knoop hardness testing is used primarily when the material being tested is thin, small, or has anisotropic properties. It is especially suitable when measuring the hardness of brittle materials such as ceramics, very thin coatings, and individual microscopic features. It is used on composite materials, where it allows for targeted hardness assessments on individual constituents within the material. Knoop hardness testing is often used in R&D applications for materials characterisation, failure analysis and mechanical property investigations. It provides valuable insights into the microstructural properties and mechanical behaviour of materials.
The load selection depends on the material being tested, the desired indentation size and the specific requirements of the application. In general, the recommendation is to choose the highest possible load. This minimises the influence of the surface treatment on mounted, cut or ground specimens. Also, with a higher load, the metallographic structure becomes more irrelevant. For specific materials or applications, there may be standard recommendations or specifications that suggest suitable loads. Industry standards or material specific guidelines can provide valuable information on load selection.
Another common distinction is made between micro and macro hardness testing. Here, a basic differentiator is the application of lower loads and higher loads for different methods.
Micro hardness testing involves applying a lower test load, typically ranging from a few grams to a few kilograms, while macro hardness testers use heavier loads ranging from kilograms to tonnes. Micro hardness testing uses high magnification to accurately measure the dimensions of the small indentation. The test indentation is examined and measured using a microscope or an optical system. In macro hardness testing, the indentation is typically observed and measured without the need for high magnification.
Micro hardness testing is commonly used for examining small or thin samples, coatings, CHD Rows, NHD Rows, SHD Rows, hardness mappings or localised areas of interest. It is widely employed in materials science, metallurgy, and research applications to study microstructures, phase transformations, as well as hardness variations within a material. Macro hardness testing, on the other hand, is suitable for larger samples and provides a more general measurement of hardness for quality control purposes, material selection, or assessing bulk properties.
Standard material testing of screws is very versatile and places extensive and complex demands on the testing system. On the one hand, there are screws in a variety of sizes and types, which must be guaranteed to be clamped as specified in the ISO 898-1 standard, and on the other hand the standard describes various types of tests. In order to be able to cover all of these different requirements, Hegewald & Peschke offers a clamping device with a modular accessory system.
Appropriate sample holders are inserted into a clamping device specially developed for screw testing. This enables simple and quick sample clamping and prevents the introduction of transverse forces into the screw. The sample holders are adapted to specific screw sizes as well as to carry out different types of tests, such as diagonal pull tests. This ensures the entire range of screws can be tested with one clamping device, from very short to very long screws with large threads; to include turned screws, finished shoulder head screws, nuts and even complete sets; as well as standard thread and fine thread screws.
Another challenge when testing screws according to DIN EN ISO 898-1 is the
determination of special parameters, such as the elongation at break ‘A f’ and the 0.0048 ‘d’ yield strength of entire screws. For this purpose, an attachment strain gauge is used in the testing system, which records the change in length over the total length of the screw. To do this, the tactile strain gauge is placed on the screw from above and below in specially designed openings in the sample holder and in the clamping device.
All parameters for carrying out the tensile test are set in the LabMaster material testing software, according to ISO 6892-1. During the test, the testing machine control regulates the testing speed in accordance with the specifications of ISO 898-1 – including speed switching when the 0.0048 ‘d’ yield strength ‘F pf’ is reached. The resulting force
displacement curves and the characteristic values are then automatically determined and displayed in the testing software.
The clamping devices for screws are optimally tailored for use in the testing machines of the inspekt series from Hegewald & Peschke Meß-und Prüftechnik GmbH. For testing screws with different strength classes and sizes, the tensile testing machines are available in a wide load range with test forces of up to 2,000kN. The clamping devices are characterised by great flexibility and always ensure standard testing according to DIN EN ISO 898-1. In addition, thanks to their modular structure, they can also be expanded later if the customer develops new testing requirements.
BUSINESS INTELLIGENCE FEATURE
Business Intelligence is quickly becoming an essential tool for wholesale distribution businesses of all sizes. With the right solutions in place, these organisations can gain unprecedented insight into their operations and make smarter decisions that drive revenue, profitability and customer satisfaction. So, how can wholesale distribution businesses leverage Business Intelligence to gain a competitive advantage?
Business Intelligence (BI) is a powerful tool that helps businesses collect and analyse data from various sources to gain insight into their operations and make informed decisions. BI can help wholesale distribution businesses track sales performance; identify trends in customer behaviour; optimise inventory levels; and improve overall operational efficiency.
BI utilises advanced software applications, tools, and techniques, to transform raw data into valuable insights that can be used to guide business strategies and improve decision making. Through BI, wholesale distribution businesses can gain a competitive edge by identifying areas for improvement and taking action based on the data.
BI can also be used to analyse various types of data, including sales and financial data, customer data, inventory data and more. By combining data from different sources, wholesale distribution businesses can gain a complete picture of their operations and make data-driven decisions to drive growth and success. In short, BI provides businesses with the necessary tools to turn their data into actionable
Business Intelligence provides businesses with the necessary tools to turn their data into actionable insights that can help drive growth, profitability and success…”
insights that can help drive growth, profitability and success in today’s fast paced and highly competitive wholesale distribution market.
Data is one of the most powerful tools in today’s business world.
Wholesale distribution businesses, like many other industries, generate large amounts of data through their daily operations. This data can
be used to improve a company’s competitive edge and drive profitability. BI is the key to unlocking this potential.
BI refers to the technologies and processes used to analyse and interpret data in order to make informed decisions. IT provides insights into business operations, performance, as well as customer behaviour. By using BI, wholesale distribution businesses can uncover hidden trends and patterns in their data and leverage that information to make better business decisions.
There are many examples of wholesalers using BI to gain a competitive advantage. For instance, a wholesaler might use it to identify sales trends by product line or region, or to track inventory levels in ‘real time’ to avoid stock-outs. This kind of data-driven decision making can help a wholesaler better manage their supply chain and respond quickly to changes in demand.
As a wholesale distribution business, you want to make sure you’re operating efficiently and effectively to maximise profits. One way to do that is by monitoring Key Performance Indicators (KPIs) that are relevant to your industry.
These include picking accuracy – low accuracy can result in wasted time and money as incorrect orders are filled; as well as picking and packing costs – including all costs associated with picking and packing orders, such as labour, equipment, and supplies, which can help identify ways to reduce costs and improve efficiency. Other KPIs that can be tracked include staff utilisation – low labour utilisation can indicate inefficiencies in processes or staff shortages; equipment utilisation – low utilisation can indicate that you have too much equipment or that you need to improve your scheduling; as well as lead times – the longer the lead time, the more you need to plan ahead and manage inventory levels. By monitoring these KPIs and using the data to make informed decisions, wholesale distribution businesses can improve their operations, reduce costs and provide better service to customers.
One way data can help improve customer relationships is by identifying patterns in customer behaviour. By analysing past purchasing habits, wholesalers can predict what their customers might need in the future and proactively offer relevant products
and services. They can also use this information to tailor their marketing and communication efforts to better resonate with their customers’ preferences, and expectations, and also to identify cross selling opportunities.
Data can also be used to optimise pricing and promotions to enhance customer loyalty and drive repeat business. Wholesalers can use pricing analytics to determine the right pricing strategy for each customer and product.
Data-driven insights can help wholesale distribution businesses identify opportunities for optimising operations, increasing productivity and reducing costs. Machine-led insights are essential for achieving maximum ROI throughout the value chain. One emerging field that combines multiple data science techniques to extract insights from event logs is process mining. Process mining allows companies to analyse their operations in ‘real time’ and make data-driven decisions to help improve efficiency, quality and overall performance.
However, many organisations fail to align operational decisions gleaned from analytics with their financial implications, which can ultimately impact the bottom line. It’s essential to align financial strategies with outcomes instead of stakeholders. That way, businesses can make sure that they’re using data to drive operational efficiency in a way that supports their long-term financial goals.
When it comes to leveraging data to improve operational efficiency, advanced analytics should be used wherever there’s a profit to be made or loss to avoid. By applying analytics to every aspect of the supply chain, from inventory management to shipping and delivery, companies can optimise their operations and improve their bottom line. For example, analytics can be used to identify bottlenecks in the shipping process, which can help to reduce shipping times and costs. In addition, predictive analytics can help companies forecast demand and ensure they have the right amount of inventory on hand to meet customers’ needs.
In summary, data is a valuable resource for wholesale distribution businesses. By using BI to analyse and interpret this data, businesses can gain insights into their operations, performance, and customers, which can be leveraged to drive profitability and maintain a competitive edge. As technology continues to evolve, the ability to harness the power of data will become increasingly important for the wholesale distribution industry.
Profast Group, a distributor of fasteners and fixings, headquartered in Ireland, has used Business Intelligence and data analytics software from Phocas Software to revolutionise its sales methodologies; optimise its inventory management practices; and enhance its customer interactions.
Committed to delivering high-quality products and exceptional customer service, Profast set out to enhance its operational efficiency and strengthen customer relationships in the face of evolving market dynamics.
Acknowledging the need for data-driven insights and increased operational efficiency, the company sought the expertise of Phocas Software, a well established provider of Cloud-based Business Intelligence and Financial Planning & Analysis solutions in the fastener and fixing industry.
Phocas integrates seamlessly with Profast’s Enterprise Resource Planning (ERP) system, Merlin Business Software from Aptean, and through the combined use of Phocas Analytics and CRM, has united the company’s sales, stock and purchasing data.
Profast now has ‘real time’ visibility into its sales performance, pipeline forecasts and inventory levels to help better manage sales teams. Profast can also easily see what customers are buying, and not buying, to increase ‘share of wallet’. For example, thanks to unlocking customer insights through Phocas, Profast can now adopt a more consultative sales approach; embedding itself into its customers’ projects and timelines. By better anticipating demand and offering proactive solutions, the Profast team have positioned themselves as strategic partners rather than mere suppliers.
“Data is very important because if you’re not reviewing your performance, how do you actually know how you’re performing? It allows you to be able to identify where extra resources and support are required,” comments Stephen Clarke, head of sales at Profast Ltd.
Fastener and fixing distributors handle thousands of SKUs and generate huge sums of data throughout their supply chains, in particular logistics and eCommerce. Whilst this data is invaluable, too much data can result in information overload, which can be counterproductive. Another challenge is that this plethora of data traditionally sits across multiple siloed systems, which potentially includes
the business’ ERP, Customer Relationship Management (CRM) software, Warehouse Management System (WMS) and Human Resource Management System (HMRS).
Due to the complexities this presents for tasks like sales forecasting, management teams have traditionally had to rely on finance or IT to build bespoke reports for them. Not only is this time-consuming, but these reports are typically static spreadsheets that quickly become outdated and can pose a risk to business decision making.
Modern Business Intelligence and data analytics software, such as Phocas, helps businesses to relieve these common data challenges by bringing data together from different sources to monitor KPIs in ‘real time’. “Whether it’s sales revenue, margins, dead stock, or OTIF. Phocas really does simplify the complex spreadsheets and information that we could present it with from our ERP or CRM systems, and compiles it on the one dashboard,” says Stephen.
“Phocas provides instant access to transaction level data in an easy to use tool that can be relied upon to build a comprehensive picture of what’s happening across the business.”
With technology, companies need to continually adapt and adopt, so when Phocas launched AI-powered databases with natural language queries this year, the company immediately saw the potential for the novice user. Business Intelligence solutions that offer the added benefit
of integrated AI functionality, make datadriven insights even more accessible to people across the business. This is especially the case for newcomers to the world of analytics who can use natural language prompts to query their specific sales, purchasing and operations databases without needing to rely on technical support.
Leveraging the AI-powered Business Intelligence and dashboarding capabilities of Phocas, Profast has successfully navigated economic challenges, optimised operations and strengthened customer relationships. By embracing new technology, Profast continues to evolve within an ever-changing business landscape and raise the bar for service excellence.
“We’re always great at identifying our strengths and maybe not as good at identifying what we need to improve on. The dashboards and the data in Phocas definitely help make that very real, in black and white,” concludes Stephen.
To survive and thrive in today’s economic climate, manufacturers and distributors need a deeper understanding of their business data. If they are not willing, or able, to set-up and run an in-house Business Intelligence team, but seek all the benefits it can provide, the next best alternative is investing in dedicated software. Armed with the right information, at the right time, businesses can eliminate chance and gut feeling in decision making, once and for all.
The newly developed iTERMINAL from Würth Industrie Service GmbH & Co KG enables complete digitalisation of the Kanban rack, which can be accessed in ‘real time’; signals the exact location of the required item; as well as being centrally accessible on a monitor.
Currently being used by selected customers as part of a pilot phase, Würth Industrie Service points out that the iTERMINAL is a digital information board, which will allow manufacturing companies to interact quickly, easily and directly at the storage location. The system is characterised by a user-friendly interface and combines all the functions of the Kanban rack with absolute transparency.
When used alongside iDISPLAY, Würth Industrie Service’s digital rack label, the search function is simplified. As soon as the customer selects a specific item using the search function on the monitor, the iDISPLAY at the respective storage space lights up. Both the systems communicate with each other using a wireless connection, which means that customers do not have to rely on a separate network.
Instead of initiating the search function on the monitor, there is an alternative option to use a connected barcode scanner. By scanning the barcode, it is clearly visible, on which rack level, in which bin the required product is placed. Therefore, iTERMINAL reduces the search time by avoiding unnecessary walking distances, which frees up more time for value adding activities.
Most importantly, maximum transparency is achieved with all the information about different storage locations, as well as multiple Kanban racks, available at a glance.
K.Optimize Artificial Intelligence (AI), from international technology group Körber AG, is now enabling companies to add a ‘supply chain booster’ application to product suites to focus on strengthening operational efficiency and bring full transparency to the warehouse.
AI featured supply chain boosters focus on boosting and/or increasing operational efficiency. Some of the key capabilities include monitoring of machine availability; root cause analysis to identify and better understand operational errors; and downtime as well as optimisation of operational capacity.
“Our new product suite really adds value for all our customers. With the supply chain booster, we can bring full transparency to the warehouse, which will enable our customers to make data-driven decisions. They will be able to easily find the root cause of errors and downtime and with our AI, the machine can even automatically compensate for errors with no human intervention,” explains Ricardo Elvas, digital portfolio manager at Körber.
“Körber is an established leader in the supply chain logistics market. With over 4,000 global installations, our digital team has the expertise to deliver the solutions that our partners need for a seamless operation. Our customers continue to experience increased complexity in their deliveries, so the solutions have had to become smarter. With this booster, businesses can more efficiently manage their large-scale supply chain challenges,” concludes Ricardo.
Global energy tech solutions and material handling equipment company, Pramac, has teamed up with Swiss autonomous navigation company, BlueBotics, for its first range of mobile robot solutions – X-ACT –designed to operate in dynamic environments such as warehouses and factories.
At present three robot models are available – HYBRIX, APTIX, and AMRIX, all driven by ANT navigation and managed by BlueBotics’ ANT server fleet management software. The robots are all sold under Pramac’s new business unit, Lifter Mobile Robotics.
“Designed in compliance with ISO standards, X-ACT robots are designed to evolve a business’ logistics processes to the next level – there is a solution for virtually every use – with flexible solutions, perfect for upgrading traditional and advanced logistics. Thanks to our collaboration with BlueBotics, the X-ACT range integrates perfectly in a warehouse without the need for additional infrastructure, granting maximum safety. All of its technologies are quick and easy to use and grant a quick return on investment, plus X-ACT systems can be easily configured, updated and monitored using our Cloud solution,” explains Federico Piersimoni, business group director of Pramac’s material handling division.
The first model available is HYBRIX – X-ACT’s collaborative mobile robot pallet truck. It features autonomous movement and unloading, with pallets loaded onto the robot manually. The HYBRIX is easy to deploy, programme, and use, thanks to its fully integrated ANT navigation software. HYBRIX is the easiest solution with which to upgrade a company’s existing logistic processes as it can be quickly integrated into every existing workflow without the need of additional infrastructure.
APTIX, by contrast, is X-ACT‘s fully autonomous pallet truck robot model. This stacker solution is designed to move goods in warehouses automatically, from picking to drop off, with precision and efficiency. Finally, AMRIX is X-ACT’s fully autonomous platform robot. This omnidirectional unit load solution is designed to transport boxes, crates, pallets and general goods throughout a warehouse.
“These X-ACT robots are a worthy addition to Pramac’s portfolio of material handling equipment. These solutions are perfectly designed to help companies kick start their logistics automation programmes easily and in a way that makes sense for their operation,” concludes Dr Nicola Tomatis, CEO at BlueBotics.
Infor, the industry Cloud company, has introduced industry specific GenAI and ESG reporting capabilities to help customers improve productivity and report on their environmental footprint.
IInfor GenAI is built to leverage customers’ industry data and processes to bring substantial productivity gains in the industries served. For example, automatic assignment of attributes for products in distribution, creating exception summary for complex projects in industrial manufacturing, takes away unnecessary work that users do today.
Infor ESG Reporting helps customers address the increased pressure and changing requirements from internal and external stakeholders to report on their environmental footprint. With Infor ESG Reporting, customers have the data and analytics to help drive more meaningful, measurable, and actionable change, while reporting on their environmental footprint with improved accuracy, transparency and consistency.
Infor’s modern solutions, from ERPs to supply chain solutions, run critical operations in a variety of industries including manufacturing and distribution, and the power of GenAI –combined with unique industry capabilities and insights – give
customers immediate power to leverage the right data and workflows to help realise more value, more quickly. Additionally, the solutions adhere to stringent security and data privacy best practices, driven by Infor’s OS platform.
“We’re constantly listening to customers’ pain points and anticipating opportunities that enable customers to be successful and competitively advantaged. When it comes to building solutions that are hyper productive, our vision is to minimise the time customers spend in applications so they can maximise their time focusing on their specialised work and creating value. Achieving this requires more than just humans and Artificial Intelligence working together. It also requires the right understanding of industry subsegments and individual workflows. As a company built around industry specificity, Infor understands the context of how people work so that we can build those best practices into our products to help enhance productivity.
Infor GenAI is designed with this in mind,” comments Soma Somasundaram, president and chief technology officer at Infor.
The UK is the greatest sailing nation on Earth and its boating and shipping history goes back thousands of years. For instance, yachting goes back hundreds of years and the Americas Cup actually started on the Solent, the strait between the Isle of Wight and the mainland of England, in 1861. Sailing is huge around the shores, and inland lakes, of the UK – with the sailors and boats needing to be robust, but what about the fasteners that hold them together?
The sea, salty air and sun are the enemies of many materials and can lead to corrosion and fastener failure when it comes to boat and ship maintenance. Boats and ships can also experience huge loads in storms, which means the fasteners must be up to the job. Pontoons and docks suffer similar conditions and again the requirements on fasteners are many.
Leyton Fasteners, a UK supplier of industrial nuts, bolts, washers, and fixings, explains: “You can’t afford for fasteners critical to the structure of maritime vessels to rust and fail. The risks involved are simply too significant. You need to have peace of mind that your fasteners will stand the test of time.”
In the challenging world of maritime applications, ensuring the structural integrity and safety of projects is paramount. The cornerstone of this reliability lies in selecting the right marine fasteners. Among the many factors to consider, load-bearing capacity stands as a critical one, but others include installation procedures, coatings, maintenance and, of course, corrosion resistance.
Fasteners are among the maritime components for which load ratings are specified by organisations such as the American Boat and Yacht Council (ABYC). The right load-bearing capability can be found by consulting these specifications.
“In the challenging world of maritime applications, ensuring the structural integrity and safety of projects is paramount.”
Including safety margins in the load-bearing capacity calculation is a good idea. Catastrophic failures can result from overloading fasteners, so including a margin of safety adds a degree of security and guarantees that fasteners can withstand unforeseen strains. Making the proper material selection and installation of maritime fasteners is also equally important. Fasteners operate at peak efficiency, they retain their structural integrity and are also corrosion resistant when installed correctly.
Pre-drilling holes for fasteners is crucial, particularly in composite or hardwood materials. Pre-drilling guarantees that fasteners sit firmly and keep wood from breaking. Use of a torque wrench will prevent over-tightening or under-tightening. While under-tightening might lead to loose items, over-tightening can damage fasteners or the material they’re fastening. It is important that users tighten the fasteners evenly and gradually, they need to refrain from pushing them into position – as this may cause an unequal tension distribution.
Fasteners should also be the appropriate length for the job. They shouldn’t go in too far, as this surprisingly could reduce the fastener’s grip, but just far enough into the material to provide a strong connection. When sealing fasteners, especially in below waterline installations, use a marine grade sealer, as this lowers the chance of corrosion by preventing water intrusion.
It is key that fasteners and materials of the same metal type are used whenever feasible. This helps prevent galvanic corrosion, which happens when different metals come into contact, particularly in salt water.
Applying coatings and platings is also essential for improving corrosion resistance and extending fastener life. Galvanising is a zinc coating that offers a barrier that prevents fasteners from corroding. This is an affordable choice that works well for a variety of nautical applications. However, it’s not really suitable for below waterline applications.
Ceramic coatings have a remarkable ability to resist corrosion. They perform well in severe marine situations because they offer a long-lasting barrier against moisture and exposure to seawater.
Selecting the appropriate alloy of stainless steel can improve corrosion resistance. Due to its increased nickel and molybdenum content, Grade 316 stainless steel provides better resistance to corrosion from seawater. This makes stainless 316 fasteners a great option if they are subjected to continuous water contact and dynamic pressures. They are also generally more resistant to corrosion than their 18-8 counterparts because of the molybdenum content. For above water conditions, austenitic stainless steel Grades 1.4401, 1.4404 and 1.4542 will be sufficient but for anything that is to be submerged – it should be at least 6% molybdenum.
Docks and piers require solid and long-lasting fasteners. It is advised to use stainless steel fasteners, such as expansion anchors, lag screws and throughbolts. It is also crucial to ensure proper installation methods are used, such as pre-drilling and applying marine sealants. Underwater structural fasteners need to be able to endure extended submersion. Titanium or Grade 316 stainless steel fasteners
are frequently the best options for these uses. To guarantee their functionality, routine maintenance and inspections are essential. The US Marine Boat Supply reports: “Compared to the common type 304 or type 18-8 stainless steels, type 316 stainless provides the highest resistance to rust and corrosion when it comes to fasteners and/or pipe fittings. Type 316 stainless steel can withstand harsh conditions and is an absolute must in any type of salt water (marine) environment.”
Where possible, fasteners should be regularly cleaned and they should be lubricated with a corrosion resistant substance. This preserves functionality and aids in protecting against exposure to salt water. Fasteners that exhibit noticeable wear or corrosion should be changed right away. Leaving broken or corroding fasteners may be a false economy, causing structural integrity to be compromised. Users should also consider using sacrificial anodes or other galvanic protection techniques to protect fasteners against galvanic corrosion from dissimilar metals.
Stainless steel is known for its corrosion resistance in many environments in which carbon and low alloy steels would corrode. The corrosion resistance is a result of a very thin (about 5 nanometers) oxide layer on the steel’s surface. This oxide layer renders the surface electrochemically passive in the presence of corrosive environments.
The passive layer forms because of the chromium added to stainless steel. It must have at least 10.5% chromium for the passive layer to form. The more chromium that is added, the more stable the passive layer becomes, and the better the corrosion resistance. Other elements such as nickel, manganese and molybdenum can be added to enhance stainless steel corrosion resistance.
Another requirement for the formation and maintenance of the passive layer is that the steel surface must be exposed to oxygen. Corrosion resistance is greatest when the steel is boldly exposed and the surface is maintained free of deposits. If passivity is destroyed under conditions that do not permit restoration of the passive film, then stainless steel will corrode much like a carbon or low alloy steel.
Covering a portion of the surface, for example, by biofouling, painting or installing a gasket, produces an oxygen-depleted region. It is anodic relative to the well aerated boldly exposed surface, possibly resulting in the corrosion of the covered region.
Under certain circumstances, the passive layer can break down at localised spots on a well exposed stainless steel surface. When this happens, the metal can corrode in these spots. This is called pitting corrosion. One common cause of pitting corrosion is exposure to aqueous environments that contain chloride. Examples are coastal atmospheres, road salt combined with rain water, and even tap water containing high levels of chloride.
During the fabrication of stainless steel components or structures, it is possible to degrade the corrosion resistance. This occurs when austenitic stainless steels (such as 304 grade) are exposed to temperatures between about 425°C and 870°C. If the exposure time is too long, then the areas near the metal’s grain boundaries lose their corrosion resistance and can be preferentially attacked when exposed to a corrosive environment. The grains fall out and the metal loses strength. The increased susceptibility to corrosion by this change in microstructure is called sensitisation.
The only metals that are completely corrosion resistant are gold and platinum. While stainless steel isn’t completely corrosion resistant, it is much more economical and practical. It also far surpasses other common (and cheaper) metals when it comes to corrosion.
Brass is an alloy of copper and zinc, known for its strength and corrosion resistance, and is often used in marine applications, particularly in cabin fittings. Brass also often boasts a higher tensile strength than stainless steel, ranging from 40ksi – 85ksi (thousand pounds per square inch), depending on how much zinc is present in the alloy.
However, only certain classifications of brass fasteners should be used below the waterline – due to the process of dezincification. Zinc is corroded by the chloride in seawater, meaning high zinc brass alloys would have very little structural integrity after prolonged exposure to salt water. They will also readily tarnish when exposed to seawater, usually leaving a green patina.
Silicon bronze contains copper, tin, silicon and sometimes small amounts of other metals, such as zinc and manganese. This alloy is highly resistant to corrosion and is particularly effective in salt water environments, where other metals may corrode quicker. It forms a protective oxide layer on its surface, preventing further corrosion and ensuring long-lasting performance. When building a wooden boat, users should consider using silicon bronze fasteners because they complement wood perfectly and provide superior corrosion resistance.
There is also titanium fasteners, which have the unique ability to rapidly regrow their protective passive layer in the presence of oxygen –giving them unparalleled resistance to salt water environments. They’re also naturally lighter than other metal alloys and composites, making the material an excellent choice for weight sensitive vessels. Like silicon bronze, titanium boasts the ability of resistance to extreme temperatures and fluctuations, making it an ideal material for marine applications.
When choosing the appropriate fasteners, it’s essential to understand the distinctions between coarse and fine threads. Every thread has particular benefits and drawbacks, with fine threaded fasteners generally stronger in tension and shear. They will also be less likely to loosen over time and permit finer tightening adjustments, as well as being more easily tapped into harder materials. Coarse threads on the other hand have more profound and broader ridges, making them less prone to cross-thread problems and stripping. They are also resilient enough to endure little scratches and work well.
Coarse threaded fasteners are appropriate when cleanliness may be an issue – since they can function well even in ‘less than ideal’ settings. Because coarse threads are less likely to seize when tightening, installation can be completed more quickly and effectively. They are also more appropriate for various applications because they gall less frequently than fine threads.
Galling is a form of wear caused by adhesion between sliding surfaces. When a material galls, some of it is pulled with the contacting surface, especially if there is a large amount of force compressing the surfaces together. Galling is caused by a combination of friction and adhesion between the surfaces, followed by slipping and tearing of the crystal structure beneath the surface.
This will generally leave some material stuck or even friction welded to the adjacent surface, whereas the galled material may appear gouged with balled-up or torn lumps of material stuck to its surface. Galling is most commonly found in metal surfaces that are in sliding contact with each other.
It is especially common where there is inadequate lubrication between the surfaces. However, certain metals will generally be more prone to galling, due to the atomic structure of their crystals. For example, aluminium is a metal that will gall very easily, whereas annealed (softened) steel is slightly more resistant to galling. Steel that is fully hardened is very resistant to galling.
Galling can cause fasteners to be impossible to undo (cold welding) and may even lead to catastrophic failure, which is why galling prevention is highly recommended.
One common cause of pitting corrosion is exposure to aqueous environments that contain chloride.”
During the worst shipping crisis in history, Mecklenburger Metallguss GmbH reinvented the ship propeller, using Nord-Lock wedge-locking washers on underwater propeller caps, to help the world’s largest container ships sail through the storm.
It’s late in the evening and heavily loaded lorries escorted by police cars, blue lights flashing, move through the sleepy town of Waren, north-eastern Germany. Yet the residents of the quaint little houses aren’t worried; they know it’s just another ship propeller about to leave town. Waren, with some 20,000 inhabitants, is home to Mecklenburger Metallguss (MMG) – a world leader in the design and production of propellers for large container ships. One of its creations, a 131 tonne, huge six blade propeller for Maersk, holds the world record for the largest ship propeller.
It’s a tricky transport challenge. Hamburg, Germany’s largest sea-port, is more than 200km away and stopping on the autobahn is time-consuming for the convoy of long and heavy vehicles. Some years ago, a whole A-road, along with two railway tracks, had to be moved as the company grew and propeller transports kept jamming the traffic. So, what is an XXL ship supplier like MMG doing this far from the sea?
“We started manufacturing propellers 70 years ago, as the area was a Soviet occupation zone and the east German shipbuilding industry had to be rebuilt after the war,” explains Jörn Klüss, head of design and construction at MMG and a Waren native. “Back then, ship propellers were a lot smaller. Today, the know-how in the region is what makes us stay.”
Cargo capacity has grown 1,200% over the past 40 years. Fifteen years ago, ships moved 5,000 TEUs (twenty foot equivalent unit, a standard 6.1m shipping container). Today, ultra-large container ships load 22,000 TEUs.
However, container demand collapsed during the financial crisis in 2009, and orders for new propellers stopped. “What saved us was our ‘Retrofit’ programme – a new generation of propellers that optimises efficiency in old ships,” comments Jörn.
Until then, propellers were built for ships operating at the highest possible speed. After the crisis, ships started slow steaming with engines running below capacity to cut fuel consumption. Ships that used to cross the oceans at 25 knots (46.3km/h) slowed down
The first underwater assembly of a propeller cap with Nord-Lock washers was carried out in 2014 on a large European container ship.”
to 18 knots (33.3km/h) or less. “The slower an engine runs, the larger you can go on the propeller. By analysing individual operating profiles, we adapted the number of blades and the diameter to determine the most efficient individual propeller,” says Jörn.
The company also analysed the propeller cap – the part of the propeller behind the blades that protects the steel components of the propeller shaft from seawater corrosion. It created a new energy saving cap (MMG-escap) with a new fin design that
straightens the hub vortex, reducing the required torque and preventing wear on the rudder. These innovations made it possible to increase efficiency by up to 10%, saving roughly €200,000 for an Asia-Europe voyage.
Many shipping companies showed interest in upgrading old propellers with the MMG-escap, which alone increases propulsion system efficiency by up to 3%. Conventionally, propeller caps are fitted to the propeller with bolts secured by a chemical locking adhesive. However, this requires the ship to dock for at least three days, incurring docking fees of about US$15,000 per day, plus the cost of removing the ship from its sailing schedule.
“We started thinking about attaching the new cap underwater, using divers, but that excludes the use of adhesives, which need oxygen to harden. That is how we found out about wedge-locking washers and the inventor of this technology – Nord-Lock,” adds Jörn.
However, the strictly regulated shipping industry relies on classification societies to ensure safety at sea and define technical standards for ship construction and operation. A ship cannot operate without classification,
as it won’t get insurance or freight orders. The NordLock washers hadn’t been tested and approved for use with the special copper alloy used in the propeller cap, so a certification that the washers efficiently secured the propeller cap was urgently needed. Every shipbuilding country has its own classification organisation, and MMG works with all of them. In this case, they contacted DNV GL, one of the largest.
“If the shipping company and classification society agree, you may implement an application and perform a subsequent verification. The NordLock washers already had multiple certifications and DNV GL was motivated to test for another one due to our innovative steel-copper alloy combination,” explains Jörn
The first underwater assembly of a propeller cap with Nord-Lock washers was carried out in 2014 on a large European container ship. Three divers only needed one and a half days to do it during regular port time and without docking fees – a success. MMG, DNV GL and Nord-Lock met in September 2016. Less than a year later, the washers had been tested and approved.
“The shipping industry is very conservative, but we’ve convinced them of the diver solution’s merits, and Nord-Lock is now our new standard for all bolted joint applications,” concludes Jörn. www.nord-lock.com
Stainless steel is a metal used in various applications – due to its durability, heat and corrosion resistance. Here, APM Hexseal explores what stainless steel is and the different types available, whilst also describing the advantages of its use in various applications.
Stainless steel is an alloy composed of varying amounts of manganese, silicon, chromium and low carbon steel. The chromium content in stainless steel provides lasting corrosion resistance in oxygenated environments, and extreme temperatures, and can deliver exceptional durability when hardened. While stainless steel is typically an alloy composed of the four components above, select grades add molybdenum and nickel to improve the corrosion resistance.
While there are several compositions, for a steel alloy to be considered stainless steel, it must contain at least 10.5% chromium or more. Various grades of stainless steel exist to deliver performance in a broad spectrum of applications.
There are five primary types of stainless steel – austenitic, ferritic, duplex, martensitic, Precipitation Hardening (PH) – as well as various grades to choose from, with the 300 and 400 series being the most popular. Austenitic is the most popular stainless steel type that improves formability and weldability with nitrogen, manganese and nickel additives. Another type, ferritic, is a chromium-based, magnetic stainless steel used in limited applications – with a carbon content of 0.10%. Duplex is a 50/50 combination of austenitic and ferritic stainless steel that offers resistance and strength but does not withstand welding well.
As well as these, martensitic is a stainless steel type similar to ferritic steel that offers higher strength than ferritic but less resistance than austenitic steel – due to its higher carbon content. Lastly, Precipitation Hardening (PH) is a stainless steel type with aluminium, niobium, copper additives, and exceptional strength, due to an aging heat treatment.
Stainless steel offers various advantages that make it a preferred choice in many applications including strength, cleanliness, aesthetics, corrosion resistance, recyclability, as well as durability. It is also a high strength alloy that can maintain strength at extremely low and high temperatures, making it desirable for many applications. Stainless steel also prohibits pathogen and bacterial growth – meaning it can be easily cleaned and maintained.
maintenance and ease of cleaning also make it ideal for sanitary applications.
Stainless steel also has excellent resistance to water staining, rust and corrosion. It can handle various environmental conditions with extreme temperatures and pressures. The corrosion resistance of stainless steel comes from the chromium content that creates a self repairing barrier over the surface of the metal to resist corrosion, rust and damage. Grades of stainless steel with increased molybdenum, titanium, and nickel content, can enhance the alloy’s properties, including corrosion resistance. After a stainless steel product has exceeded its lifespan, it can be recycled to make other stainless steel products.
Stainless steel is one of the most durable metals used and can be made lightweight and maintain a high toughness to reduce buckling under heavy loads. It can also hold heavy weights in extreme environmental conditions, including high and low temperatures.
These benefits enable stainless steel to be relied on in a number of applications in a variety of industries, including marine infrastructure, aviation, railway and bridge construction.
It is for these reasons that APM Hexseal uses stainless steel as standard for its sealing screws, sealing nuts and sealing washers, as well as having stainless steel inserts in many of its switch boots. “We only use the best raw materials in our products,” comments the company. “Using our 75 year experience, we can also make any of our products stainless,
Lesjöfors has recently gifted a set of gas springs that are able to endure every extreme of the Scandinavian environment, from rough seas to high winds, as well as hot summers to icy winters, to the Swedish Sea Rescue Society (SSRS).
SSRS’s Victoria Class of rescue vessels were looking for a marine grade, high-quality gas spring that would act as a critically essential component part for the rescue hatches on the vessels. Lesjöfors therefore gifted and helped fit a set of gas springs, allowing the SSRS teams to vigorously test the components over several months, to ensure Lesjöfors held the solution to the gas spring supply.
“The SSRS was looking for help and it was our pleasure to volunteer some samples that enabled them to fix an issue and to assess how we might be able to support their long-term future. Not that I had any doubt about our products, but I was delighted when their team confirmed that we were their number one choice for gas spring supply. We know our products are expertly designed and manufactured to achieve the highest performance levels. However, knowing the SSRS also recognise this, and for us to be part of their rescue fleet, fills us with great pride,” explains Per Lindros, sales stock and gas spring manager at Lesjöfors AB.
The SSRS is involved in approximately 90% of all sea and lake rescues. An astonishing statistic achieved by its 2,500 volunteer crew members, who operate 24 hours a day. What is even more exceptional is that all of this is achieved without any government funding and the charity is reliant on memberships, donations and fundraising to save lives at sea.
Poland-based CS Kompozyty (CSK) has created a low emission solution for the production and operation of small recreational boats, using the Crestomer structural adhesive from Scott Bader, as well as the company’s range of marine grade Crystic resins and gelcoats.
Creating the world’s first hydrogen powered boat meant designing a hull up to 6m that met displacement, capacity, stability, strength and safety requirements. Scott Bader therefore used low emission technologies, including infused laminates manufactured from its renowned Crystic VE679-03PA resin and LS30PA gelcoat.
The project combined environmental, social and commercial aspects – reducing emissions during the construction of the boat, increasing the availability of hydrogen in marinas, as well as creating a simple construction that’s easy to manufacture and therefore produces less waste.
CSK is part of the CSV Group, which serves 400 customers in Poland across three main industries – composites, painting and propulsion systems for yachts and motorboats. The company has worked closely in partnership with Scott Bader since 2006.
A rapid increase in busbar manufacturing is pushing OEMs to look for new solutions to reduce electrical resistance and be more cost-effective. ECCB™ PEM eConnect™ Contact Bushing from PennEngineering® can be used to make reliable electrical connections between copper or aluminium busbars, PCBs or cable terminals.
Current solutions on the market have many limitations. These include unplated busbars that have the risk of corrosion, which increases resistance. Silver plating is then applied to busbars in a rack plating method that is slow, expensive and complex.
ECCB™ PEM eConnect™ Contact Bushing is answering these needs. It uses a high surface area knurl design to pierce the corrosion layer on busbars creating a consistent electrical current connection without needing to plate the busbar itself.
Designed for installation into straight punched holes without additional surface preparation, the ECCB™ PEM eConnect™
Click here to watch the PEM eConnect™ Contact Bushing installation
Contact Bushing also breaks aluminium and copper oxide layers on busbars for low resistance connections and are suitable for use in panels with sheet hardness HRB 50 / HB 82 or less. For installation, PEM eConnect™ current carrying pins provide superior electrical connections in applications that demand superior performance from internal components. Available in self-clinching and broaching mounting styles, these installation systems are for use with electric vehicles including EV charging systems, EV powertrain, EV power distribution, as well as industrial switchgear.
www.pemnet.com
A specially developed adhesive from DELO has played a substantial role in the development of Bosch’s 48V mild hybrid battery for automotive manufacturers, helping to reduce carbon emissions.
With 48V batteries reducing vehicle carbon emissions by up to 15%, the new battery systems from Bosch have been optimised for manufacturing processes and are so compact that they allow vehicle manufacturers maximum flexibility during installation, with the battery measuring just 140mm in height. This means it can be placed in discreet places such as the trunk or under the passenger seat.
The key to the compact design lies in its thermal design and so Bosch has worked with partners to develop particularly robust lithium ion cells. They even work at temperatures of up to 75°C and thanks to their greater heat resistance, a simpler cooling concept is possible.
DELO’s adhesive has a good thermal conductivity of 1W/(m·K), which means that battery cells can be bonded into the battery housing and the heat generated during operation can also be dissipated efficiently. As a result, the adhesive combines structural bonding and a thermal management system mounting in one step – instead of having to manually fix battery cells and then use gap fillers for heat dissipation. Saving one process step, this adhesive simplifies production.
The product is flame retardant in accordance with the industry standard UL 94 V-0, designed for the entire temperature range of the battery, and offers high strength on battery cells and typical housing materials. Its tensile shear strength on aluminium is 18N/mm².
Secure placement on the surface, no dancing or slipping, no sharp edged chips and high assembly speed – these are the properties of the recently expanded EJOFAST ® self-drilling screw range from EJOT.
Now including drilling screws with a diameter of 6mm, the JF3-2-6.0 is particularly useful in the solar sector, for example being used to mount solar substructures on trapezoidal profiles –using short rail systems. Just like all other EJOFAST ® self-drilling screws, the JF3-2-6.0 enables slip-free positioning and chip-reduced screwing, thanks to a particularly finely crafted tip geometry, but with a slightly increased diameter compared to the JF3-2-5.5. The JF3-2-6.0 completes the range of EJOFAST ® self-drilling screws for solar applications and, together with the JF3-2-5.5, forms the perfect team for all applications.
The slim, single-start drill tip does not produce any sharp edged chips that get stuck in the material and have to be laboriously removed. The special thread shape also allows for high assembly speeds, which allows installers to work much more efficiently.
In addition, EJOT has a broad portfolio for solar mounting including the self-drilling EJOT solar fastener with sealing washer and ORKAN dome. The stainless steel connecting element is suitable for mounting PV systems on roofs with trapezoidal profiles, sandwich elements and corrugated fibre cement panels. It transfers all tensile and compressive forces directly into the substructure. The range is rounded off by a selection of sealing elements and adapters.
STANDARD LISTED - YOU KNOW WHO’S BEST BUT CONTACT US FOR ALL THE REST...
Non-preferred Metrics ~ Intermediate Sizes
Short and Long Lengths ~ Slotted Grub Screws
A4/80 Bolts & Socket Caps ~ 6 Lobe (TX) Drive Screws
All Metal Self-Locking Nuts ~ Studding Connectors
Tel: +44 (0) 117-972 8560
Fax: +44 (0) 117-972 8570 sales@avonstainlessfasteners.co.uk www.avonstainlessfasteners.co.uk
Unit 10, Riverside Business Park, St Anne’s, Bristol, BS4 4ED
With the original Flowform®, Arnold Umformtechnik developed and established a joining solution on the market that met the increasing demands of sheet metal joining. Now the company is responding to growing customer requirements with the new Flowform® Plus.
Compared to the conventional Flowform®, the developers at Arnold have changed the dimensions of the Flowform® Plus from a diameter of 5mm to a diameter of 4mm. In addition, the geometry of the flow form tip has been optimised and the heat treatment process adapted so that the performance remains virtually the same.
Depending on the head and length, the new Flowform® Plus 4.0 weighs around 3g, meaning a weight saving of 25%. When extrapolated to the total number of screws used in a vehicle’s body, this adds up to quite a bit of weight. For example, the weight of 500 elements of the conventional Flowform® 5.0 per vehicle is 2kg, with 500 elements of the Flowform® Plus 4.0 per vehicle it is 1.5kg. This alone means a saving of 500g.
This is important when the automotive industry is focusing on weight reduction against the backdrop of ever decreasing CO 2 emissions.
In principle, the Flowform® Plus is designed for higher strength steel sheets and thicker sheet combinations. By using aluminium components, thicker joint combinations with several layers can also be created. In the past, this meant that the top and middle layers of three layer joints were pre-punched. The use of Flowform® Plus now allows thicker material combinations of up to 7.5mm to be joined without pre-punching, depending on the joining materials.
This is due to the lower material displacement caused by the diameter reduction, which results in a smaller gap between the sheets and less friction surface – due to the smaller dimensions.
With regard to the fastener, higher strength is achieved by selecting a suitable material in combination with a suitable heat treatment process. Due to the smaller diameter of the Flowform® Plus, and therefore also the smaller head diameter, the screw is also suitable for applications where only a small flange width is available.
“We joined a three layer sheet metal joint with 2.5mm thick aluminium sheets with both the conventional and the new Flowform® element. The result clearly showed less gap formation with the Flowform® Plus. It was also possible to join without a pilot hole. In applications with adhesive, which is usually the case, the adhesive is also trapped if a pilot hole is avoided and therefore cannot escape to the pilot hole,” says Heiko Miller, application sales engineer Flowform® at Arnold Umformtechnik GmbH & Co KG.
“Joining without a pilot hole is much more cost-effective in terms of the cost efficiency of the process, as the user does not need expensive camera technology to check whether the screw hits the centre of the pilot hole during the joining process.”
The new flow form is suitable for use in car body shell construction, aluminium steel mixed construction, for profile intensive construction methods, for one sided accessibility, for hybrid connections, as well as for battery packs.
Panduit Corp has launched a range of medical and food production specific antimicrobial and metal detectable cable ties that help prevent contamination with their antimicrobial properties.
Made from a metal impregnated material, making them identifiable by metal detection devices on production lines, the cable ties and fasteners comply with Hazard Analysis and Critical Control Points (HACCP) specifications, the North American standard of the US Food and Drug Administration, and the hygiene regulations of the European Union.
In addition, the components are provided with an Environmental Protection Agency registered, antimicrobial and ionised additive that prevents the growth of various bacteria, moulds and fungi on the product surface in independent laboratory tests in accordance with ISO 22196:2019 and ASTM G21-15.
This reduces the formation of harmful germs and odours, improves hygiene and increases safety in critical areas of application. The cable ties ensure a reliable hold in the operating temperature range between -60°C to 85°C in accordance with UL746B and are resistant to chemicals.
The material mix of nylon 6.6 and the integrated mini metal parts facilitate machine identification and the bright blue colour allows the components to be quickly identified by eye. This means that the cable ties can be quickly detected and, if necessary, removed during the various production phases.
Panduit’s antimicrobial cable ties are an innovative solution for fastening cables and wires effectively, simply and securely. At the same time, they inhibit the growth of microorganisms and improve hygiene in environments with a high germ load for greater safety.
Henkel has introduced two next generation medical grade, cyanoacrylates-based instant adhesives –Loctite® 4011S and Loctite® 4061S – which offer improved safety and performance.
Formulated without CMR (Carcinogenic, Mutagenic or Reproductively hazardous) ingredients, the new adhesives are designed to offer increased strength during and after heat cycling. Loctite® 4011S and Loctite® 4061S are designed to meet the specifications of their predecessors, Loctite® 4011 and 4061, for easier validation in existing medical applications, with both products tested to ISO 10993 biocompatibility standards.
The adhesives develop handling strength in seconds on most substrates and provide high bond strength on a range of materials – including plastics, rubbers and metals. After 1,000 hours of exposure to 120°C heat, Henkel states these adhesives offer greater shear strength on steel than other instant adhesive formulations, making them ideal for bonding various types of catheters, as well as tube sets, surgical robots and other medical housings.
“Henkel is committed to medical quality systems and good manufacturing practices as a pioneer for sustainable solutions.
Panacol has a wide range of adhesives for various automotive bonding applications, including those for the stress relief of wires on commutators; the bonding of magnets in electric motors; balance compensation in fan rotors; as well as general bonding applications in the field of eMobility and automotive electronics.
UV adhesives in Panacol’s Vitralit® range are particularly suitable for relieving stress on wires at the commutator. These adhesives are easy to work with and can be applied to the wire/commutator connection and cured in seconds using UV light. The benefit of fast curing makes these adhesives the perfect solution for producing high volumes of commutators in short cycle times.
Also available are the newly developed, dual curing (UV/moisture) adhesives for bonding magnets in electric motors. Despite the opacity of the magnet, UV curing the adhesive ‘squeeze out’ will tack and hold the magnet in place. The adhesive beneath the magnet, as well as in shadowed rotor pockets, will cure using atmospheric and surface moisture. All curing occurs at room temperature.
Panacol also offers a fast curing acrylate adhesive for balancing fan rotors. This high-density, UV adhesive can be jet dispensed into the balancing pockets of fan rotors. Balancing can be accomplished quickly and precisely without the use of metal weights. This process can significantly shorten production cycle time and significantly reduce component rejects.
The launch of these new, next generation instant adhesives are formulated to meet the highest safety standards, addressing the need for safe and effective medical device assemblies – demonstrating our long-standing commitment to the medical industry,” comments Philipp Loosen, vice-president and head of industrials EIMEA and global key accounts medical at Henkel.
The EPDM bonded washer from UTA is a simple pressure gasket, which provides leak-proof sealing from water, gases and other fluids – making it suitable for applications with various screw connections.
The conical design directs flow of facing materials to form a seal conforming to both the fastener and sealing surface. The EPDM rubber can also vulcanise to a variety of metal materials to ensure a robust and enduring bond, making it suitable for a number of applications including stainless steel, galvanised steel, aluminium, as well as galvalume.
With a temperature resistance ranging from -40°C to 200°C (428°F), the EPDM bonded washers are available in M4, M5, M6, M8, M10 and M12 variants with outer diameters of 9.5mm – 29mm.
“We have grown to a remarkable position in the sealing washer market and we are dedicated to providing customers with diverse sealing solutions. Our high-quality bonded washers are widely used in industrial, commercial and residential construction, giving our products an international reputation as reliable, trouble-free sealing and cushioning washers,” comments UTA Auto Industrial Co Ltd.
The latest Master Bond adhesive, UV15RCL, is a low viscosity, cationic type UV curing system suitable for various bonding and sealing applications. Thanks to its special colour changing feature, users have a visual indicator for when the UV light has reached the polymer.
Originally a red colour, the material changes to clear once exposed to UV light, although Master Bond highlights that this change in colour does not indicate a full cure. By giving immediate visual feedback, UV15RCL offers processing and handling advantages over conventional systems. For bonding and sealing applications, the product adheres well to metals, glass, ceramics and many plastics, including acrylics and polycarbonates.
Curing under UV light typically takes 30 – 60 seconds with a broad spectrum UV lamp emitting light with a wavelength range between 320Nm – 365Nm. The minimum energy required for this curing process is 20 – 40 milliwatts per cm 2
The adhesive features a high glass transition temperature (Tg) of 90°C to 95°C, however, when post cured for 1 – 2 hours at 125°C, the Tg can increase to 125°C to 130°C. UV15RCL has a service temperature range from -80°F (-62.2°C) to 350°F (176.7°C). This non-solvent based system also cures tack free and has a low viscosity of 115 cps – 350 cps, making this material ideal for spin coating. Additionally, the adhesive is an excellent electrical insulator, with a volume resistivity exceeding 1,014 ohm-cm.
UV15RCL is available in a wide range of packaging options, including syringes, ½ pint, pint, quart and gallon containers.
Hafren Security Fasteners has acquired all property, rights, titles and interests of the System Zero® product range of security screws and associated tooling, establishing itself as the ‘go to’ provider for cutting edge security fastener solutions.
The System Zero® security screw product range, well known in the electronics industry and previously owned by PSM International, has advanced features designed to thwart tampering and unauthorised access, complimenting Hafren Security Fasteners’ line-up of specialist and unique anti-theft screws, nuts and bolts for fastener distributors and end users . System Zero® ’s unique head style requires a dedicated security driver tool for installation and authorised removal. The combination of the driver tool with the head design gives high torque transmission, which in turn generates high clamp loads. The unique design also offers effective tamper resistance in its applications, as well as robust performance and exceptional drive capabilities. System Zero® screws are available in zinc plated steel and A2 stainless steel in machine screws sizes from M2.5 to M6 and gauge self-tapping screws from 2.9mm – 4.2mm in diameter.
With this acquisition, Hafren is poised to capitalise on the rising demand for robust security solutions, especially in industries where the integrity of fasteners is paramount. Whether it’s in critical infrastructure projects, sensitive installations, or everyday construction, the need for secure and reliable fasteners has never been more pronounced. As well as this, the acquisition, complete with tooling and trademarks, demonstrates Hafren’s commitment to staying at the forefront of technological advancements, but also positions the company as a global leader in security fastener solutions. www.hafrenfasteners.com
The role of fasteners and fixings in safe security is crucial but often overlooked. Here, Keynetics explains why the choice of fixings can be the final deciding factor as to whether a key safe passes or fails during an attack test.
Any security product that is fixed to a substrate in a public space is generally only as secure as its fixings. Key safes are no exception. The integrity of a key safe isn’t solely reliant on its resistance to tampering and vandalism, although this is undeniably crucial. The quality and size of the fixings used to attach it to a wall are equally pivotal. Without secure security fixings, the key safe runs the risk of being easily removed from a wall in a matter of minutes, if not seconds, potentially leading to a property break-in, costly key and lock replacements, and undermining end users’ confidence not only in a specific product, but in the entire concept of keys storage at the point of entry – all due to a single underperforming key safe fixing.
When it comes to key safe fixings, size matters. It is common sense that when under attack, chunky, large structural bolts would hold a key safe in place far more effectively than smaller anchors or mere woodscrews, which some key safe brands offer as a standard securing method. However, numerous professionally executed attack tests that Keynetics has conducted underscores that the quantity and quality of fixings is equally important. When tested in ‘real world’ scenarios, fixings of identical size do not necessarily ensure identical performance.
Keynetics’ accreditation with LPCB (Loss Prevention Certification Board) encompasses two critical facets of key safe robustness –attacking the key safe itself and detaching it from a substrate. The latter is significantly dependent on both the fixings used and the product’s design.
For Keynetics, this means conducting extensive research into fixings and ongoing testing, which sometimes includes a trial and error approach to identify the best performing fixings for the key safe applications. Furthermore, the company provides different types of fixings sourced from selected suppliers, all based on the type of substrate, such as brick, concrete or metal.
While key safe installation may seem straightforward and takes little time, it must be done correctly to eliminate potential security risks, especially in commercial applications, which is why Keynetics offers a nationwide installation service for all key safes. Alternatively, full training and support materials are provided to clients’ installers to ensure the process is executed correctly, preventing any missteps that could compromise key safes’ security rating and certifications, as well as providing reassurance to end users that keys are stored safely.
When it comes to preventing unauthorised access to vital components, or contributing to application integrity, security screws are utilised in a multitude of industries, including the automotive industry.
That is why Norm Fasteners manufactures high-quality security bolts and nuts specific to customer requirements, in accordance with automotive regulations.
Security screws are a critical component when ensuring vehicle safety as they help to prevent unauthorised access or tampering to important mechanisms, such as airbag modules or seatbelts. These fastenings also contribute to maintaining vehicle integrity during collisions by securing structural components.
Norm offers an in-depth range of security fasteners, including wheel bolts and nuts, engine bolts, weld nuts, and suspension nuts –all engineered with precision and manufactured using cutting edge technologies for the automotive industry.
Designed for operational excellence, Norm security fasteners are manufactured in compliance with IATF 16949 and VDA PSCR standards and are used across multiple other key industries, including electronics, aerospace, and pharmaceutical, among others.
www.normfasteners.com
The new Plas-Tech 30-20 ® screws from TR Fastenings increase fastening possibilities in plastic applications for industries such as automotive, tech, infrastructure, and medical, helping to give TR customers more advantages in their production processes.
Manufactured in TR’s facilities, the Plas-Tech 30-20® range has been developed by the company’s global technical engineering teams and possesses an optimised thread profile, which gives an advanced performance in a wide variety of plastic materials.
Plas-Tech 30-20 ® screws are new to the market but come as part of the company’s established Plas-Tech® range, having been specially developed to offer several advantages over conventional thread-forming screws in plastic. These features include a 20% finer pitch, which helps to reduce installation times, as well as a lower flank angle to help improve axial resistance.
Also available with various protective coatings, the Plas-Tech 30-20 ® screw range features a reduced thread angle, which helps to lessens axial displacement during application, with a faceted thread profile directing material flow to reduce radial stress. The screws are also equipped with a large core thread profile to provide high torsional and tensile strength.
The smooth installation process of Plas-Tech 30-20® heightens its resistance to vibration and can be installed with a calibrated pneumatic or electric driver. As well as this, the fasteners can also be removed and reinstalled a number of times.
The Plas-Tech 30-20 ® screw range includes pan head, flange head and countersunk head varieties, enabling TR customers to choose the ideal option for each application. Thread diameters are available from 3mm, 4mm, 5mm and 6mm, and available in lengths ranging from 6mm – 30mm.
E-Z Lok, a manufacturer and distributor of threaded inserts for metal, plastics and wood, has introduced the E-Z Press™ inserts, specially designed for post-moulding installation in either thermoset plastics or thermoplastics.
Aslotted design with a diamond knurled outside diameter allows for ‘cold’ installation, which also enables optimum torque and pull-out resistance. Cold installation of threaded inserts reduces the costs of mouldings and eliminates the need to ‘chase’ threads after moulding. Furthermore, they also help to reduce waste caused by misaligned and faulty inserts and assist in proper installation when there is no precise hole depth.
When the E-Z Press™ insert is installed, it compresses slightly along the slot. As the fastener is threaded into place, the insert expands and the diamond knurl is pressed into the wall of the hole, securing the insert in place.
E-Z Press™ inserts are available in three styles –flush, flanged and reverse slot. All three types press into place for fast and easy installation, and anything from a rubber mallet to an arbor press can be used for installation.
Consistency of critical joints is essential to ensuring product quality and safety, as incorrect tightening and torque checks can lead to product failure, resulting in costly rework. Because of this, Atlas Copco Tools and Industrial Assembly Solutions has developed the STRwrench Advanced to give manufacturers ‘real time’ quality assurance analysis of manual safety critical joints.
Research by Atlas Copco has found that a single minute of downtime due to a safety critical joint failure can cost up to GB£10,000 in lost production. STRwrench Advanced has therefore been designed so it can still collect data in the event of a network shutdown.
STRwrench Advanced is Wi-Fi enabled with a large touchscreen interface, specially designed to be used with safety gloves. It delivers precision residual torque and breakaway torque checks and, featuring an integrated controller, enables joint check analysis in ‘real time’, reporting data to Atlas Copco’s quality assurance platform, QA Supervisor (QAS), which provides manufacturers with full assembly traceability. This software can be integrated into customer QA systems for auditing even the most challenging assembly processes.
“Our new STRwrench Advanced is a key component of Atlas Copco’s Smart Integrated Ecosystem that’s been developed to support manufacturers across all sectors, in a collective journey to Smart factory production. STRwrench Advanced provides a flexible and scalable QA process to ensure product quality and safety, whilst minimising the financial impact of assembly line shutdowns and product rework,” comments James McAllister, general manager at Atlas Copco Tools and Industrial Assembly Solutions.
BRALO Group has recently added to its extensive range of tools with the BT-18N – a new battery operated tool for blind rivet nuts suitable for a variety of riveting applications, as well as offering great speed, power, durability and reliability.
asily programmable and easy to maintain, the BT-18N riveting tool comes equipped with a battery, charger and easily interchangeable M3 to M10 nosepieces and mandrels. Its cordless nature makes it especially ideal for outdoor or overhead working areas.
With a pulling force of 18,000N and a capacity to set nuts from M3 – M10, BT-18N ensures power and durability with a brushless motor and an 18V lithium ion battery, either 2.5 Ah or 5.0 Ah. To allow for suitability to a wider range of applications, BT-18N features two adjustable parameters.
The first is stroke regulation or ‘S’ mode, which has 10 programmable memories for stroke regulation. When working in ‘S’ mode, the riveting tool uses its full pull force, but limits its stroke to the programmed stroke, making it an ideal working mode for a repetitive application, such as when the same nut is being riveted on the same material with the same thickness. This not only allows flexibility in the application, but also ensures the rivet nut is optimally positioned every time.
The second is tensile force regulation or ‘P’ mode, which also has 10 programmable memories for its regulation. When working in ‘P’ mode, the amount of force used by the tool to rivet the nut is regulated, however, the thickness of the base material may not always be the same. When working in this mode, the BT-18N uses a quality control system and warns with an acoustic signal if the nut has not been riveted properly, either by an incorrect adjustment or because it is not correctly supported on the base material.
The tool also features automatic threading and unscrewing capabilities, as well as an auto unscrewing button to avoid jamming. It also possesses a digital counter that shows the number of nuts placed, which can be reset to zero should the user need to restart the count.
BRALO also offers kits that can be supplied as optional
The new BTW-Series battery torque wrench from Enerpac has been designed for fast set-up and speed during bolting applications, enabling operators to quickly move between bolting jobs, while achieving pinpoint torquing precision.
Featuring an anti-slip pistol grip, as well as a trigger for sturdy control and operator comfort, the BTW-Series torque wrench uses a patented planetary gear with optimum tooth design for smooth and consistent torque. It also has a robust reaction arm to provide a strong reaction point when torquing, as well as a low maintenance brushless motor that enables maximum productivity. The BTW-Series is also manufactured with hardened alloy steel to withstand the elevated levels of torque.
Including the reaction arm and battery, the BTW-Series weighs just 4.7kg – making it ideal for use by a single operator. With its compact design, the handheld tool is also ideal for difficult to reach applications or where physical space is limited.
The torque wrench is also equipped with an integrated digital motor vectoring system, delivering accurate and repeatable torque up to 8,130Nm, as well as an intuitive LCD display that allows the required torque, either in Nm or ft.lbs, to be set at the touch of a button.
Available for ¾ inch to 1½ inch square drive sizes, the BTW-Series torque wrench is supplied with two Enerpac 18V 5.5Ah lithium-ion batteries and a 60 minute fast charger. For added flexibility, the BTW-Series torque wrench will also work with any compatible Cordless Alliance System (CAS) battery.
Here Dr Bill Eccles of Bolt Science addresses the challenges of tightening multiple bolts in a joint, as well as the effects this can have on the individual preloads within the group –a phenomenon known as elastic interaction.
Most joints consist of several bolts and since these bolts are often not tightened simultaneously; tightening one bolt has an effect on the preload of other previously tightened bolts in the group. Such an effect is called elastic interaction, or alternatively bolt crosstalk.
Ensuring that the bolt loading is even is critical in gasketed joints to help minimise possible leakages, but obtaining an even bolt load distribution is not clear cut since the final bolt load usually differs from the initial bolt load. The mechanism that causes this is illustrated in Figure One.
As demonstrated in Figure One, the outer two bolts have been tightened to compress the joint. The middle bolt has also been tightened to compress the joint directly underneath it, an action which has led to further compression of the joint under the two other bolts, thus leading to a loss of preload in these bolts.
In Figure Two, two classical examples of tightening sequences are shown, one for a rectangular array of bolts and the other, a circular array. Both are sequences that have been shown to result in providing a reasonably uniform bolt load, meaning they will minimise the preload scatter within a joint. On many gasketed joints, and on solid, non-gasketed joints that are critical, a multiple pass tightening sequence is often used. With such a sequence, each bolt is tightened more than once to help reduce the preload reduction caused by tightening the other bolts in the joint.
Tests have shown that the elastic interaction between bolts in a joint can have a significant effect on the preload (a reported reduction of
35%). The ‘softer’ the joint is – as in a joint with low stiffness – the larger the elastic interaction effect can be. A gasket typically results in a low stiffness joint, so tightening the bolts incrementally, multiple times, is often needed to achieve an even loading.
There are other tightening sequences that have been shown to produce a reasonable uniform bolt loading. For example, work completed in Japan demonstrated that after ensuring the joint surfaces are parallel to each other, going around the bolts in the joint and tightening them several times until no further rotation occurs was shown to provide acceptable results.
FUJIFILM has even manufactured a film that will allow the pressure distribution within a bolted joint to be determined. This can be useful in checking and optimising a tightening sequence. The film is inserted between the plates of the joint and then the joint tightened. The subsequent colour change in the film determines the localised pressure, an effect caused by microcapsules in the material designed to react to various degrees of pressure, releasing their colour forming material at a density that corresponds to the pressure.
If more information is needed on tightening sequences, Dr Bill Eccles recommends the publication ASME PCC-1-2022. This is a standard that provides guidelines for pressure boundary bolted flange joint assembly.
Designed to save time and meet the varied needs of its users, the new compact T4930 E-Driver electric screwdriver from C.K Tools enables users to quickly and accurately complete a job with ease, in far less time than a manual alternative.
Specially developed to tackle projects varying from heavyduty electrical jobs to small precision tasks, the E-Driver is a versatile and portable companion that can quickly and accurately drive screws and fasteners without fatigue.
Powered by a rechargeable USB-C 3.6V battery, the E-Driver offers cordless usage with up to 200 minutes of operating time per charge. Its ergonomic design allows for a comfortable grip and with intuitive forward and reverse buttons, the user can change the direction of rotation to tighten and loosen screws with ease. The torque adjustment dial, which can be set up to 6Nm through the motor and up to 20Nm by manual rotation, enables clear and easy adjustment to ensure fasteners are tightened effectively.
The E-Driver also comes complete with a rechargeable cable and a high performance PZ2/SL4 double sided screwdriver bit, made from durable chrome vanadium, to withstand a wide variety of tasks.
“This latest addition to our range is a toolbox essential for users who need to drive screws and fasteners, in a fraction of the time. The E-Driver will make light work of screwing and unscrewing tasks and introduce a whole new world of convenience for busy professionals,” comments Brinley Buckley Roberts, brand manager at Carl Kammerling International Limited.
EXPRESS SERVICE
automated storage 95%products in stock
40.000 REFERENCES
standard products screws,bolts,nuts,washers
ONLINE ORDERS
24h delivery service live warehouse stock
When it comes to fastening components in confined areas, it is important to have the right tool to hand. The versatile ratcheting spanner No 17F from STAHLWILLE has been specially designed to reach areas in these restricted work spaces.
No 17F provides the user with the convenience of a conventional ratchet, which can tighten or loosen screws without the need to keep removing and reattaching the tool, with the compact dimensions of a spanner that is also available with a flat ring side –making it possible to work in tight spaces where a conventional ratchet wouldn’t be able to reach. Also, the integrated ratchet with 72 teeth and a working angle of just 5° guarantees precise and efficient work.
A rounded finish to the tool ensures that there is a non-slip feel, allowing users to work reliably, even with oily hands. There are two other important features that distinguish No 17F. Firstly, there is no switch on the tool for changing direction – to work in the opposite direction, users simply turn the spanner over. Secondly, the ring
Available in 15 sizes, from 8mm – 24mm, the spanner is ideal for all standard bolted joints.
With a growing emphasis on environmental responsibility, it is an ideal time to review current work practices for businesses using solvent adhesives in their manufacturing processes. That’s why Chemique Adhesives has been pioneering innovative and sustainable bonding solutions as a greener alternative.
When switching to safer adhesive options, water-based and hot melt adhesives provide an eco-friendly solution by minimising the impact of pollutants – due to the absence of VOCs (Volatile Organic Compounds). Their versatility, ease of use and ability to form a strong bond make them a preferable option across various industries. Moreover, they can provide a cost-effective option when compared to traditional solvent-based adhesives.
Both types of adhesive offer versatility in application, whether through automated or manual processes. Hot melts are typically applied using bead or spray techniques, while water-based adhesives are commonly administered via spray or roller methods. By adjusting the formulation and viscosity appropriately, these adhesives can effectively meet diverse production needs.
Chemique’s experienced technical sales and service team can provide innovative solutions by conducting a thorough review of a company’s existing bonding process and suggesting a safer type of adhesive. The company also offers on-site or laboratory testing to prove the recommended adhesive will not only provide a less hazardous option, but will also offer cost savings, improved efficiency and increased output. As well as this Chemique Adhesives can install and regularly service all required equipment for added peace of mind.
“For nearly forty years we have made progressive steps towards replacing solvent-based solvents from the workplace with our cutting edge water-based and hot melt adhesive systems. These pioneering products not only promote a healthier workplace but also play a key role in reducing our environmental impact,” comments Stuart Francis, managing director at Chemique Adhesives.
In busy commercial vehicle and industrial workshops, users require strong and dependable breaker bars for larger wheel and chassis nuts, and bolts, that can handle huge torques, as well as very tight or corroded fasteners. For this, Laser Tools has designed two new extendable ratchet handles that can be used as breaker bars without damaging the ratchet mechanism.
The new tools, a ¾ inch drive version and a 1 inch drive version, are equipped with a ratchet lock-out button that enables them to be used as breaker bars. Both tools have been manufactured from strong, shock-resistant chrome vanadium steel, with a chrome plated finish and knurled hand grip.
The ¾ inch drive version is equipped with a tough 43 tooth ratchet mechanism and the telescopic handle has six fixed positions, extending from 620mm – 1,020mm. Once the lock button is pressed, the ratchet is protected to a maximum load of 1,412Nm.
The 1 inch drive version is a 43 tooth ratchet and also features a six position handle, one that extends from 610mm – 1,000mm. Once the ratchet is locked, the maximum load capacity is 2,515Nm.
With more than 50 years of experience in fastening systems, Rivit has developed a range of specific solutions for the photovoltaic sector that includes consumables such as blind rivets, rivet nuts, bushings for panel ballasts, as well as special screws and tools for their installation, all designed to meet the needs of the energy sector.
Popular consumables include blind rivets such as the Gtreriv, with its neoprene gasket ideal for trapezoidal sheet metal and sandwich panels, and the Lockriv for wide hole diameter tolerance. Also available are rivet nuts including the Tubriv and Jackriv, both of which are ideal for the installation of photovoltaic systems on various types of coverages and roofs, as well as the Rivlock breakstem bolts, for assemblies requiring a strong seal and high resistance to mechanical stress, especially for fastening parts subject to high vibration.
For installation, Rivit’s battery operated riveting tools 700 Series, and the RIV720, provide the power of brushless motors and long life batteries that allow easy and durable fastening. As well as this, among the hydro-pneumatic riveting tools offered by Rivit is the 500 Series of light and handy riveting machines. Finally, there is also the possibility of relying on an efficient manual tool such as the RIV7.
Thanks to many years of experience and continuous research, development, and innovation, Rivit solutions help to guarantee extreme effectiveness and reliability, but also durability, high resistance to
weathering, as well as ease of installation. The Italian-based company is also able to provide customers with ad hoc solutions, created on request for the specific needs of the sector.
Expanding on its innovative systainer® range, TANOS has introduced two new Systainer 3 models, S 76 and S 147, specially designed for the storage of small parts on the construction site or in the workshop.
The new small parts cases S 76, measuring 76mm x 265mm x 171mm, and S 147, measuring 147mm x 265mm x 171mm, are ideal companions for use outside and offer enough space for a well assorted selection of accessories. The interior of the suitcases can also be flexibly adapted to the users’ needs, with options for the colour design of the individual case components, as well as brand personalisation.
The special lid contour of the Systainer 3 S 76 and S 147 ensures that all individual parts remain in their intended place even during bumpy transport. In addition, the clever storage solutions can be provided with different inserts, so that tools and larger individual parts can also be stowed away as needed, with integrated theft tags reliably protecting the inside of the suitcase from unauthorised access.
TANOS also provides an additional storage solution with these models, the Systainer 3 Rack, which offers space for up to six Systainer3 S 76 in a portable shelving system. A mechanical pressure mechanism also ensures an intuitive removal option, while its own locking system guarantees the safe transport of the integrated Systainer3 S by hand, on the rolling board or in the vehicle. This enables large quantities of small parts to be clearly stored and safely transported.
An expanded quarter turn lock range from WDS Components now features a new design with additional cam sizes, including new offset dimensions up to 24mm, enabling use of locks with virtually any size door.
Quarter turn locks provide quick, secure fastening for a range of industrial and commercial applications, including workplace and changing room lockers, industrial cabinets and enclosures, machinery, HVAC systems, as well as office furniture. Named after the locking style, the fastener is operated with a 90° open or close turn.
While the locks can be driven with a key alone, designs in the WDS range also include L handles and wing knobs. These designs provide increased grip and leverage to suit the door size and type, as well as environmental conditions – such as moisture and grease.
For ease and flexibility of fitting, a wide range of lock sizes are available, enabling installation on practically any size or type of door. Each model features an industry standard 20mm lock barrel, combined with a 45mm long cam. To allow for door depths up to 34mm, various cam styles also feature an offset of up to 24mm. Hook cam designs also provide extra security by fastening onto a pin, while a compression cam style features a pin wheel that pulls the door shut to achieve a tighter lock.
The devices are manufactured from a variety of materials, including zinc plated steel die cast – providing corrosion resistance and strength, as well as 304 stainless steel for extra corrosion resistance. A chrome-plated version reinforces against wear, while black and grey powder coatings add colour choices. WDS also provides a cost-effective plastic quarter turn lock range that is ideal for enclosures and cabinets.
Additionally, to prevent ingress and add protection against moisture and dust, all WDS quarter turn lock designs feature a seal that provides IP65 protection. This prevents entry of dust as well as water from low pressure jets.
3 Star Rivet 121
310 Express 154
A. AGRATI SpA 39
Abbey Clamps 15
Achilles Seibert GmbH 11
Acton 141
Albert Pasvahl GmbH + Co 9
Alexander Paal GmbH 25
Ambrovit 13
APM Hexseal 143
Astrotech Steels Private Ltd 89
Avon Stainless Fasteners Ltd 145
Bäcker GmbH & Co KG 125
BBA Fasteners Srl 97
Bendfast 162
Berardi Group 135
Berdan Bolt 69
Bomet 124
Bossong 93
Bralo 155
Bülte GmbH
Kunststofferzeugnisse 93
CAMCAR Innovations (Geniune TORX®) 51
CAMCAR Innovations ( TORX® ttap) 53
CEIA 100
Chavesbao 21
Colombo Special Fasteners 47
CZ Fasteners Parts Co Ltd 162
Dimac Srl 113
Don Quichotte B.V. 123
Doss Visual Solution Srl 111
DS Fasteners 151
Fast Trade 59
Fastbolt 2
Fastener + Fixing Magazine 45
Fastener Fair Global 77
Fastener Fair Italy 73
FastFixSearch.com 127
fischer International 91
Fixi Srl 15
Fong Prean Industrial Co Ltd 161
Fürniss GmbH 95
G & B Fissaggi Srl 93
Gala Precision Engineering 33
Graewe GmbH & Co KG 66
Growermetal 61
Hafren Fasteners Ltd 151
Halfmann Schrauben GmbH 29
HAŠPL AS 117
HEICO Befestigungstechnik GmbH 153 Hisener 4, 5
I.N.G. Fixations 91 Index 3
Inoxdadi 145
Jiangsu Yongyi Fastener Co 31
Enhancement of certifications in seismic zones
New range with reduced embedment for a wider choice of applications
New coatings for enhanced durability and usage in extreme environments
Improved load performance and reduced edge distances and spacings
It's how to achieve streamlined installation processes.
That’s why we are introducing the Nord-Lock® Combi Nut. This product reduces the number of parts your operators have to deal with by combining our world-famous washers with a nut. The result? A faster, safer way to get the job done.