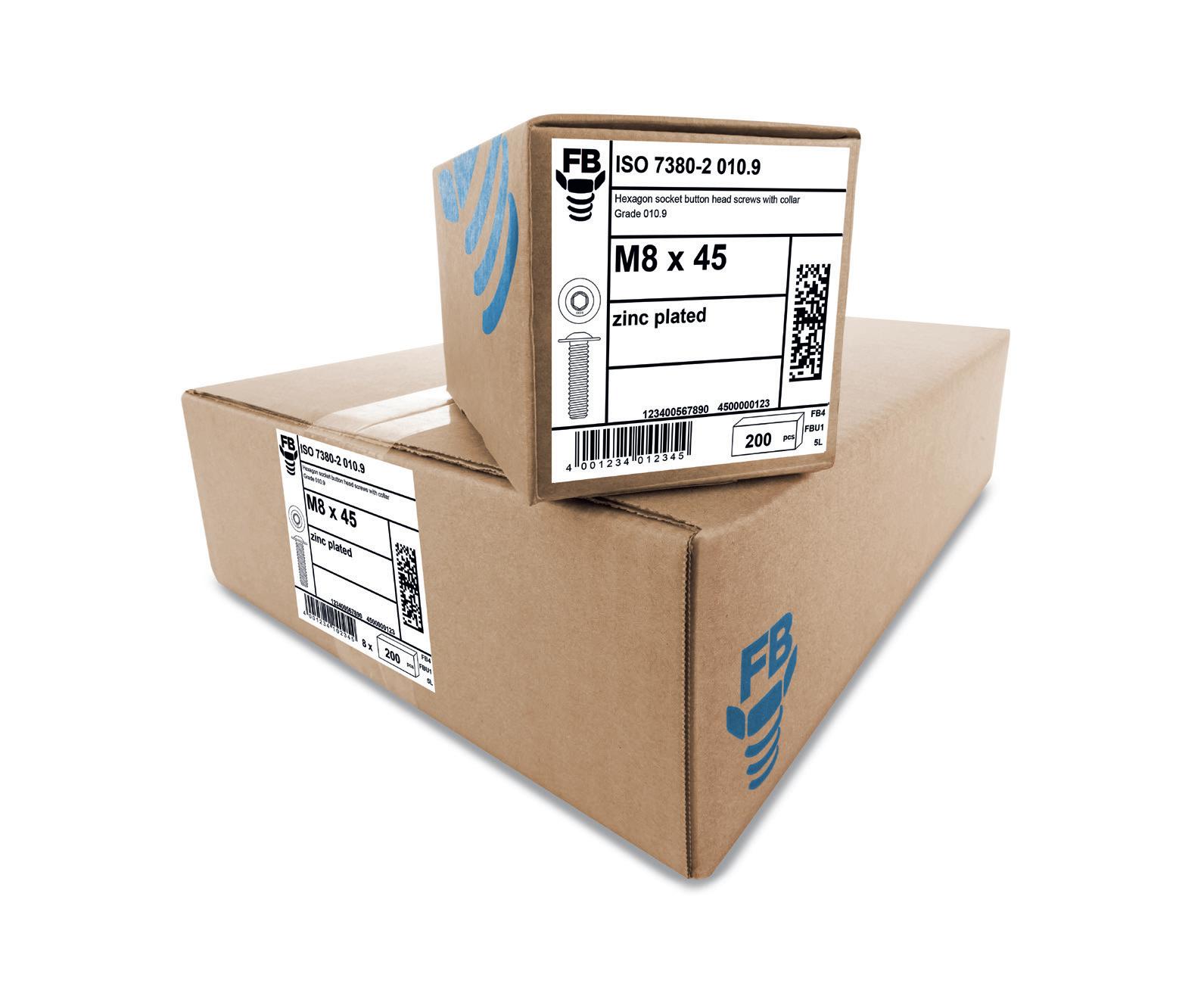
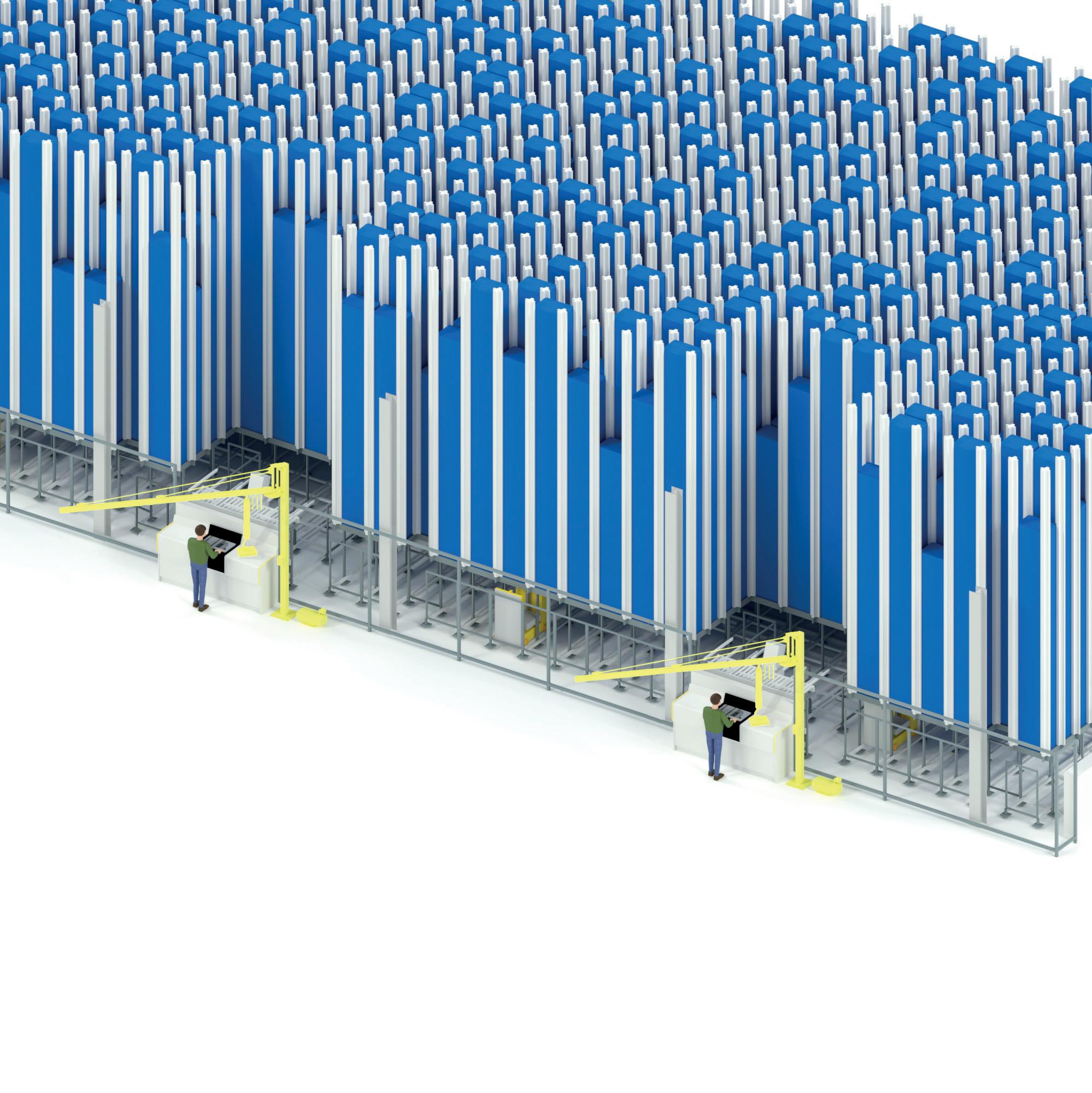
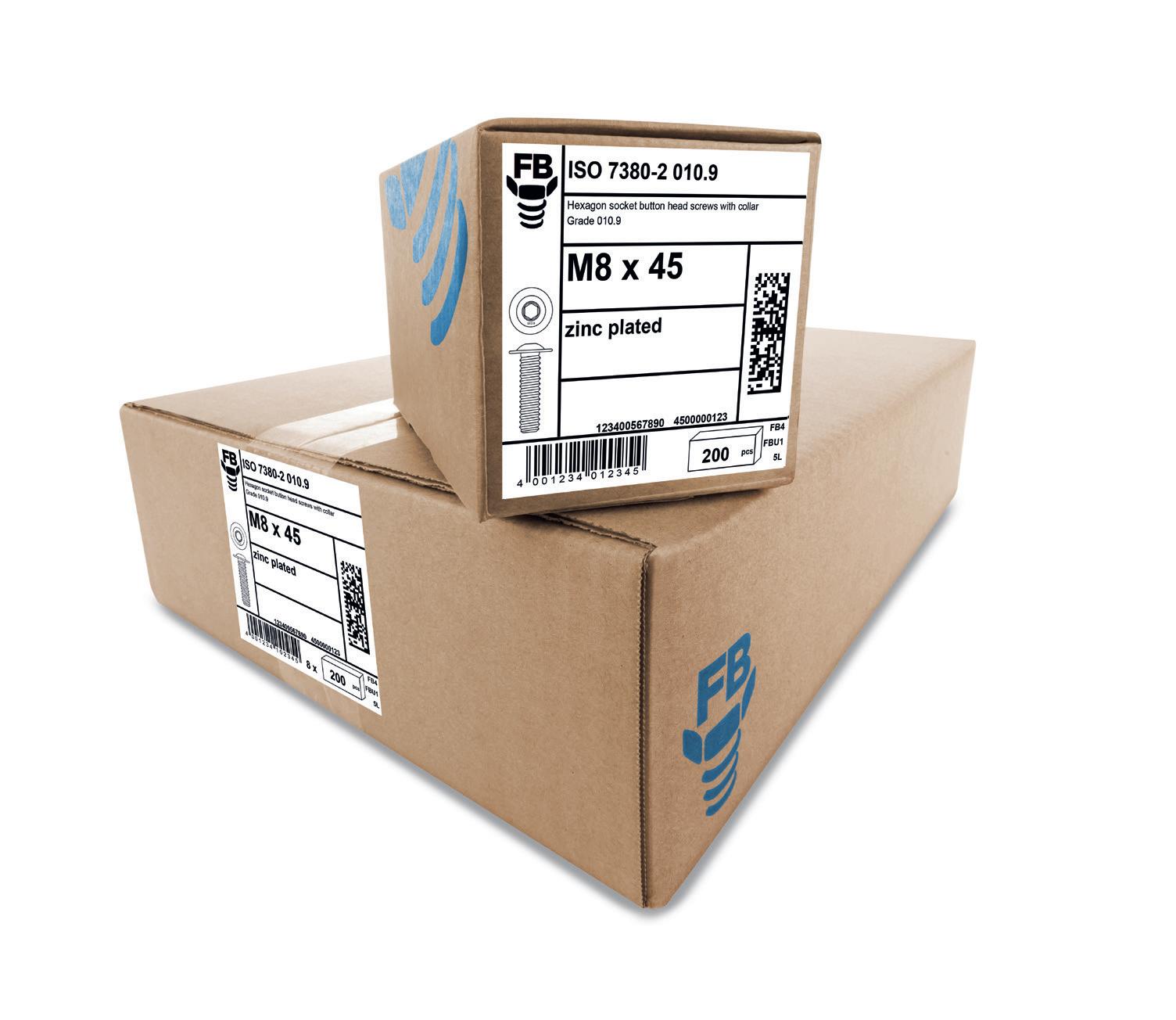
COMPETENT. GROWING.


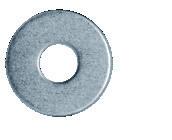


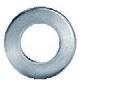








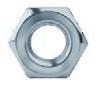

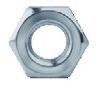

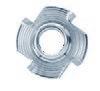





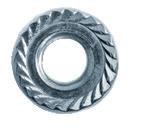

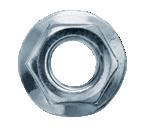

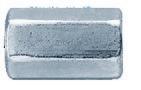

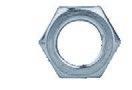

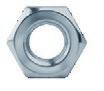











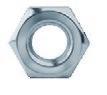





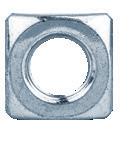



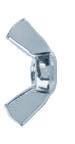
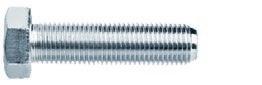
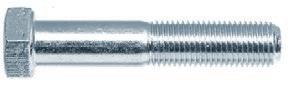
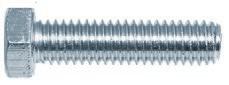
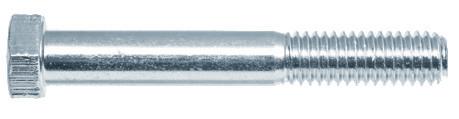

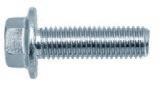
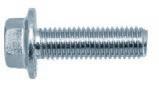
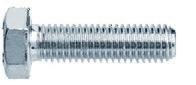
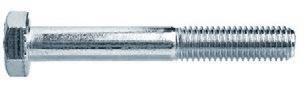
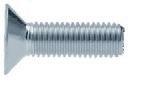
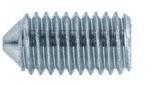
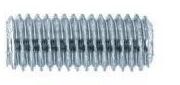
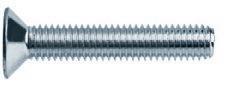
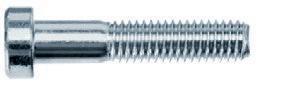

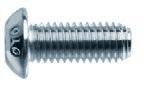

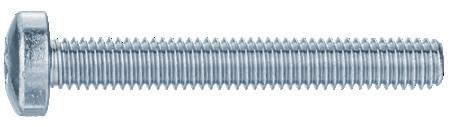
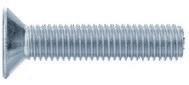
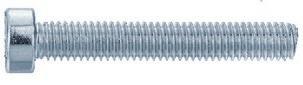
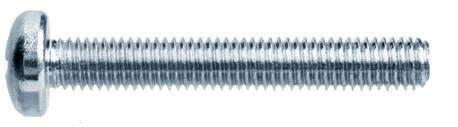
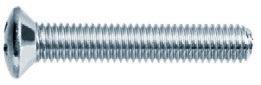

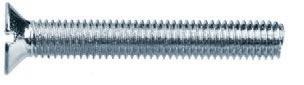
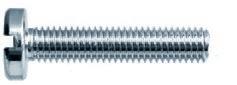
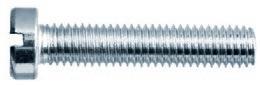

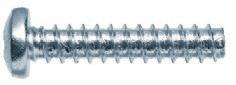
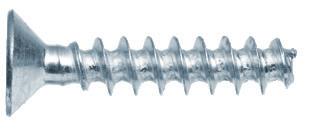
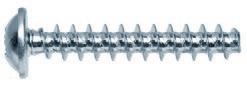
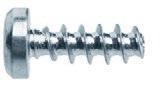
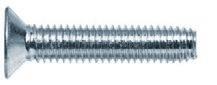
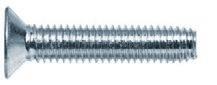
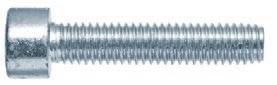
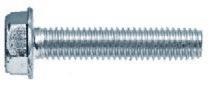
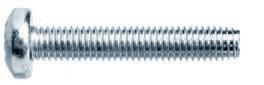
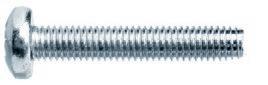

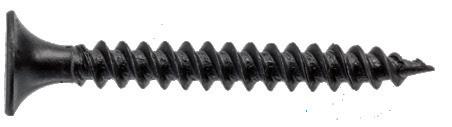
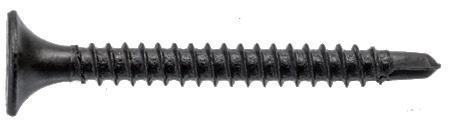
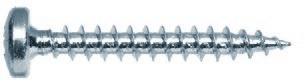

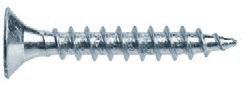
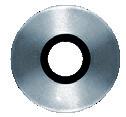
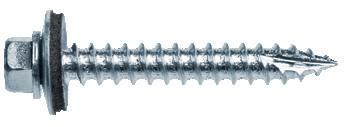

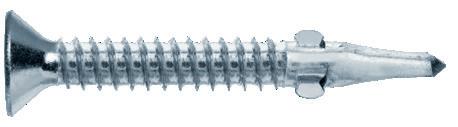
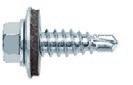
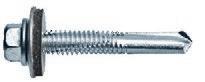


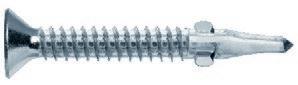
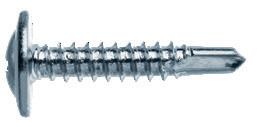
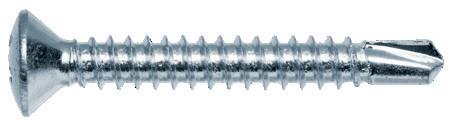
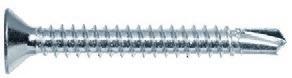
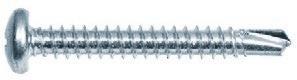
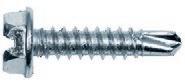
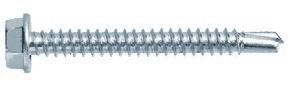



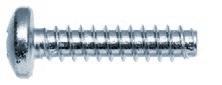
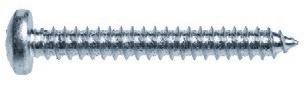


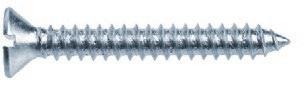
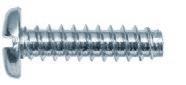
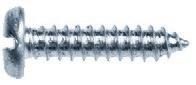
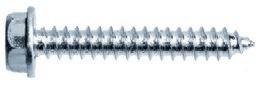
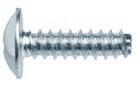
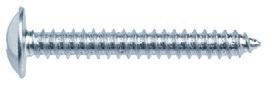
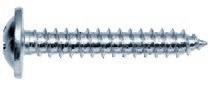

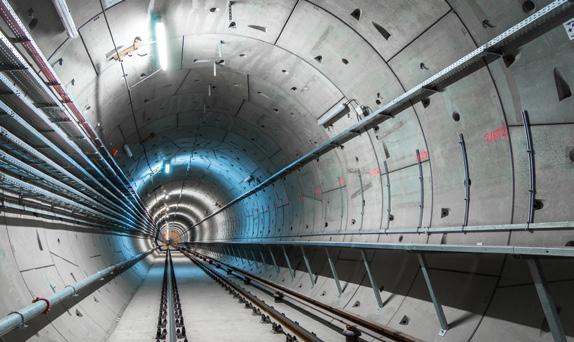
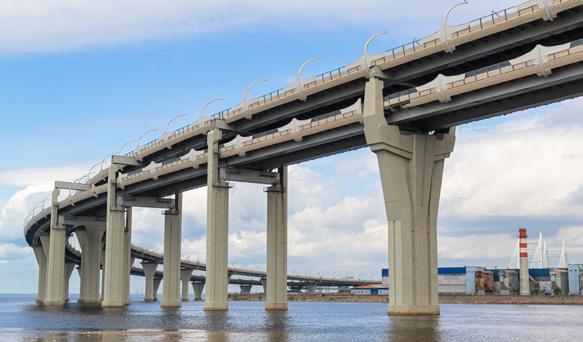
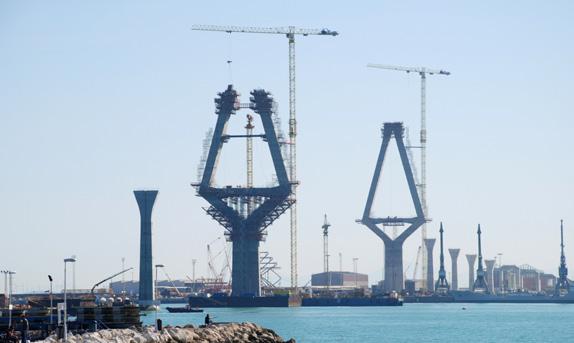
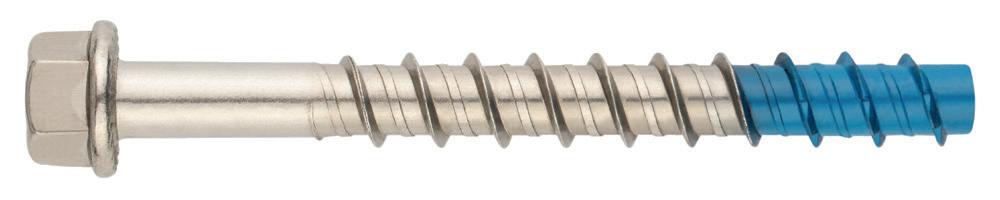
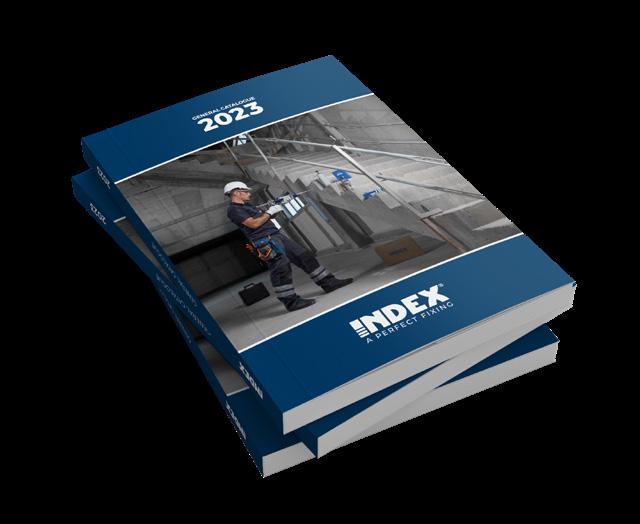

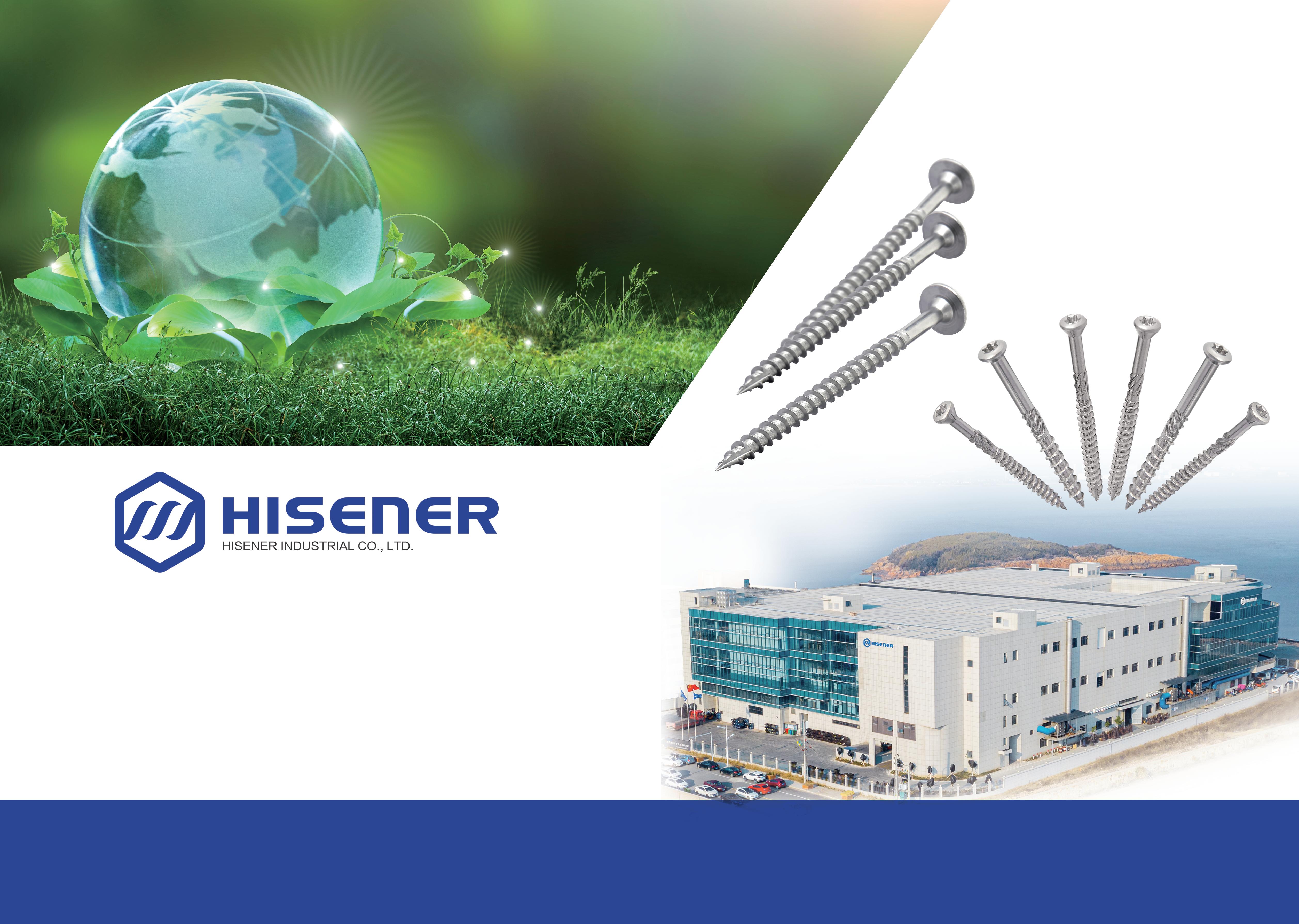
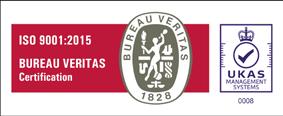
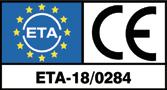


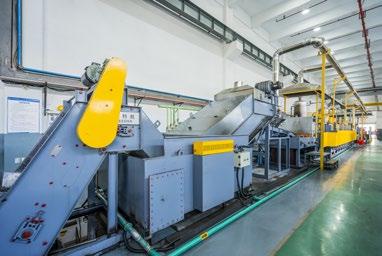
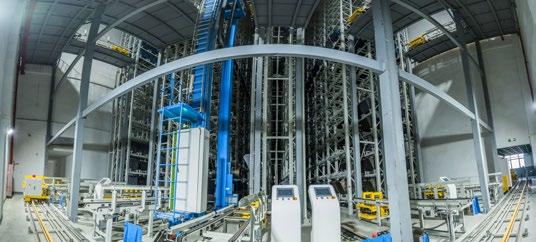
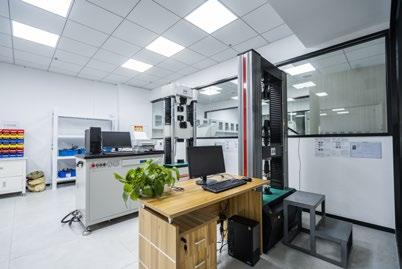

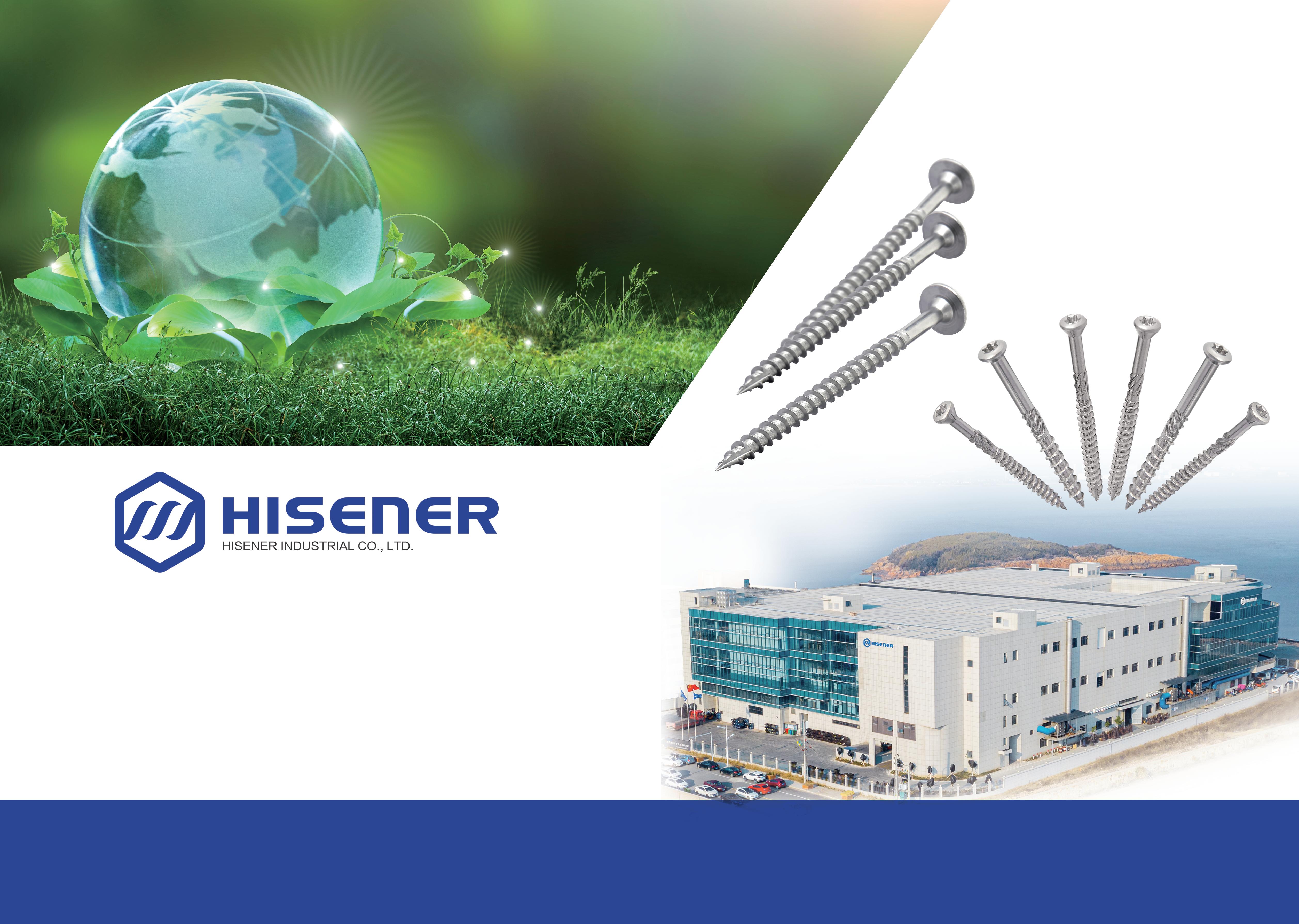

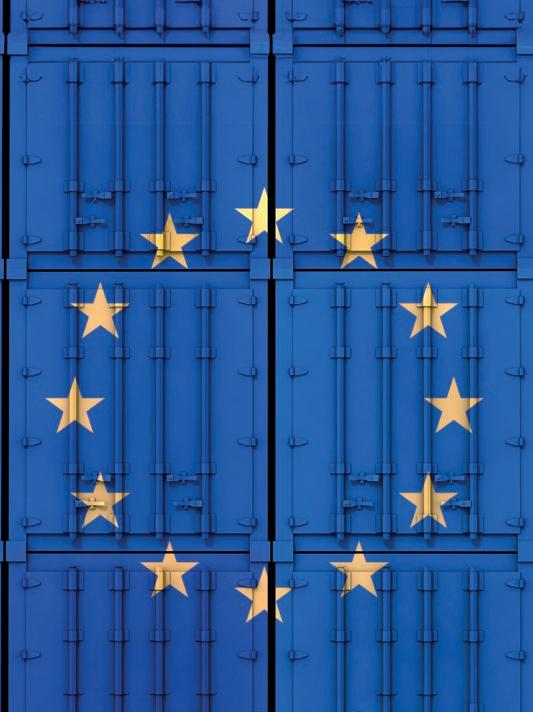
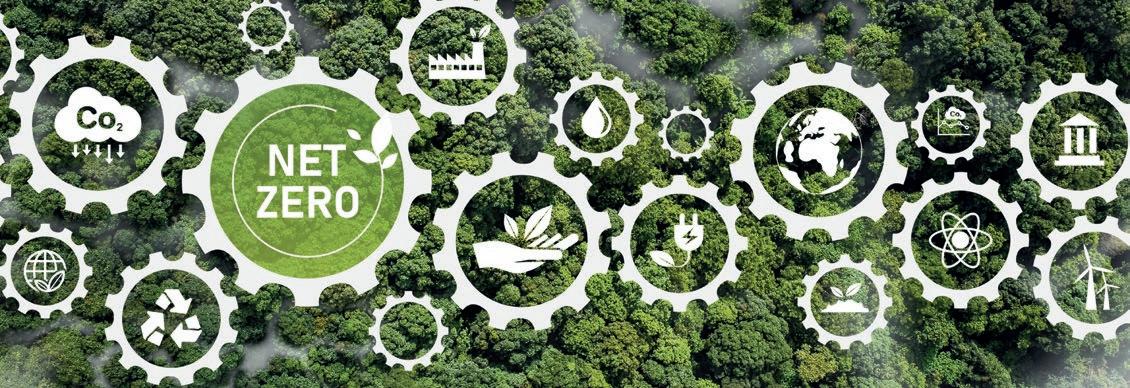

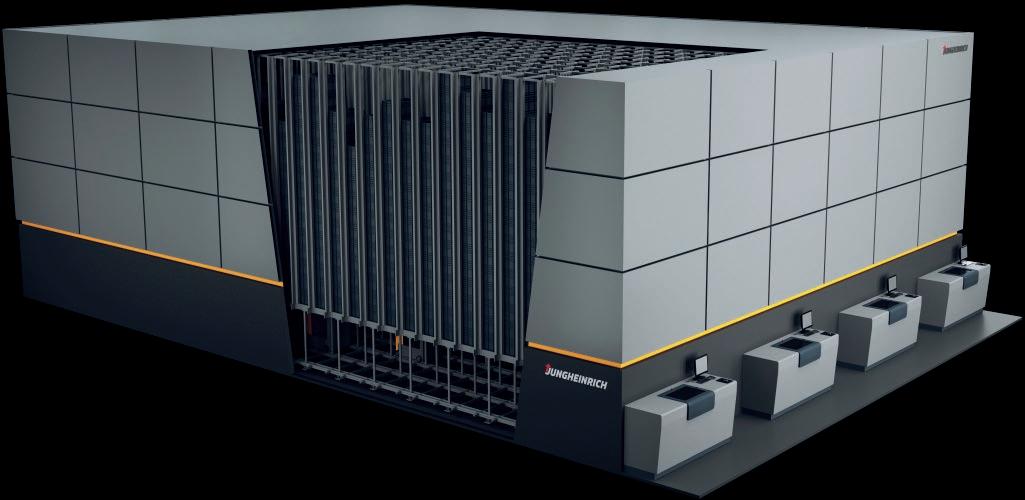
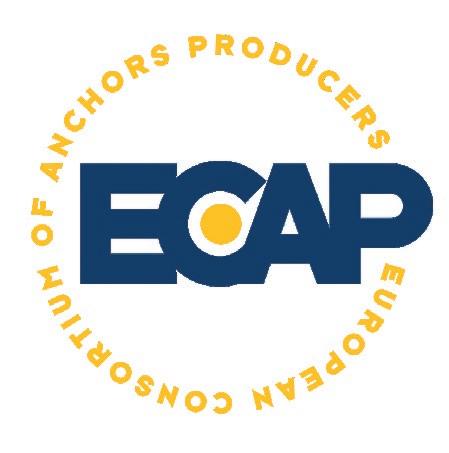
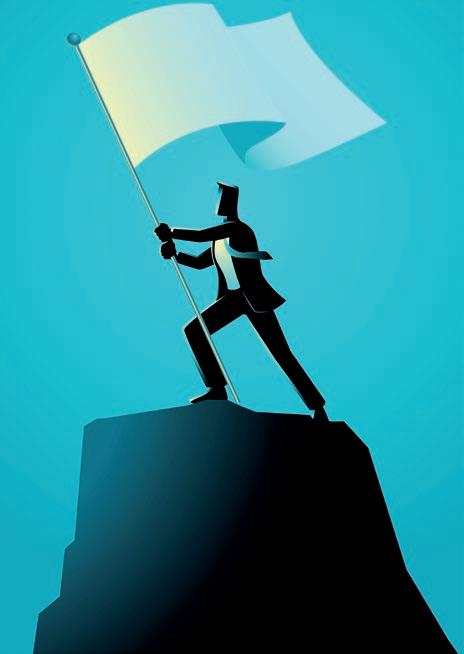
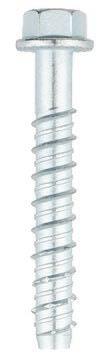
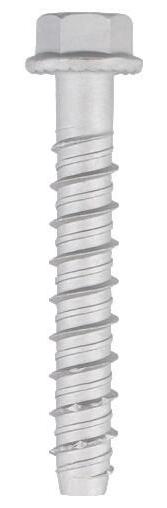
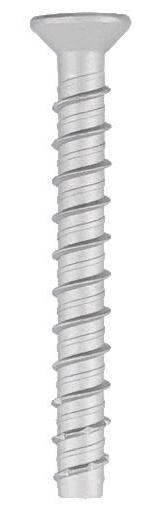
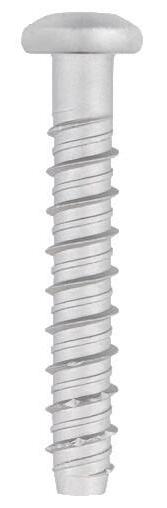
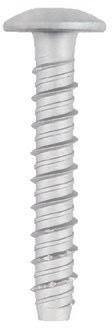
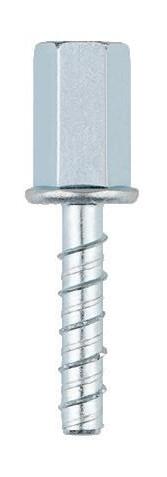


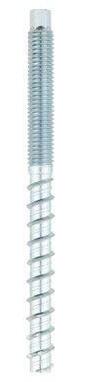


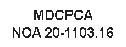
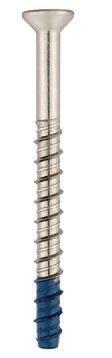
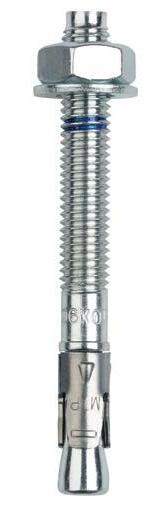


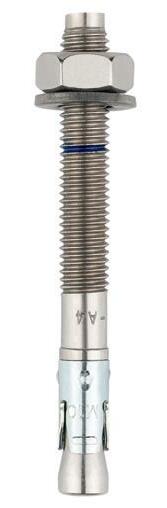
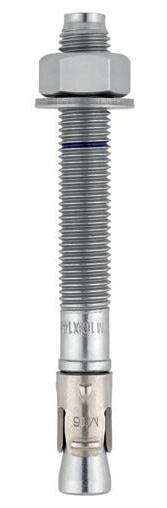
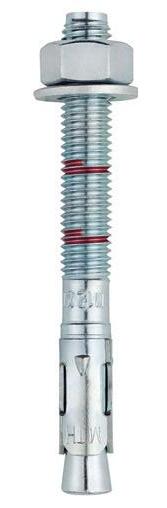
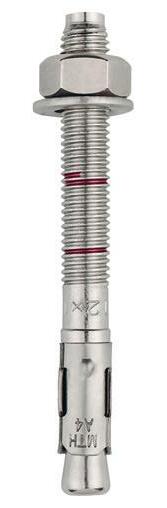
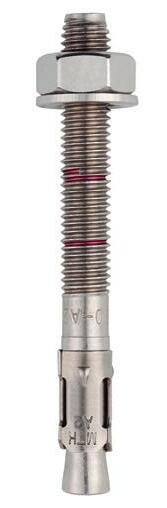
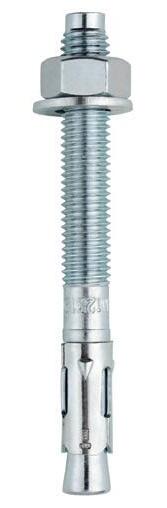

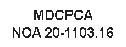
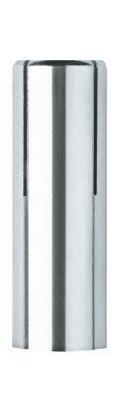
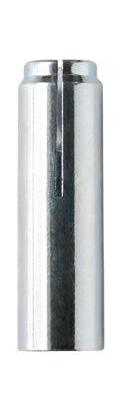

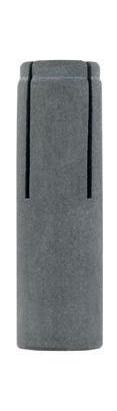
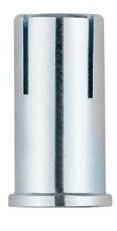

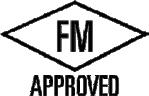
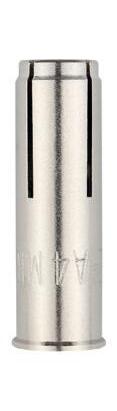

COMPETENT. GROWING.
At Fastener + Fixing Magazine our aim is to always include insights and reports on the key topics impacting the industry to truly keep our readership informed about the latest developments, which is undoubtedly true of this July edition.
Firstly, we have an unbeatable feature on sustainability within the fastener and fixing sector. Sustainability is undeniably a key focus for every market at the moment, with the fastener industry no exception. With that in mind, our special feature goes beyond ‘greenwashing’ and highlights those fastener companies making a real difference when it comes to sustainability.
To start the feature, there is an article from Sytze Dijkstra, Netherlands country manager at Simply Sustainable – an awardwinning ESG and sustainability consultancy, who explains what sustainability actually means and the steps every company can take to ensure they have a strategy that will lead them on the right sustainability path.
To add to this there is also a brilliant article from Peter Standring, technical secretary at Industrial Metalforming Technologies, who looks at the implications of sustainability for automotive fasteners. Plus, numerous companies – including Böllhoff Group, Brugola OEB Industriale SpA, WASI GmbH, Colombo Special Fasteners, Fontana Gruppo, Lederer GmbH, NOF Metal Coatings Group, Hague Fasteners Ltd, Growermetal SpA, KRONUS SIA, HEICO Group and several others – explain how they have approached sustainability.
Another ‘must read’ article is focused on a topic that will start to have a huge impact on the fastener market from Q3 of
Assistant Editor Rebecca England rebecca.england@verulammedia.com
2023 onwards – the EU’s Carbon Border Adjustment Mechanism regulation, better known as CBAM. To help make things a little clearer, we have a report from the European Fastener Distributor Association’s (EFDA) webinar on the impact of CBAM, which included a presentation from Andreas Schneider, of StahlmarktConsult, entitled: ‘CBAM and fasteners – what do European importers need to prepare for?’
Our Cover Story is focused on Fastbolt Group and how it is looking to invest in key areas to not only provide solutions for today’s needs, but also for future challenges. From speaking to Managing Director Ekkehard Beermann, it is clear there are a lot of exciting projects happening at the company – including the addition of a new warehouse and the installation of a new modern automated compact bin storage system.
The exclusive articles keep coming, next up we have an interview with Magnus Karlsson, vice-president global business development at Titgemeyer Group, who explains how the group has looked to develop its value proposition whilst continuing to meet the needs of its customers. Plus, regular contributor Ian Parker discusses how the move from internal combustion engines to hybrid and electric vehicles will impact the automotive sector and what it means for fastener requirements.
To finish off we also have special features on light-duty fixings, automotive application technology and nuts, washers + locking systems, plus a whole host of other news and insight.
Fastener + Fixing Magazine is a dedicated, trade–only publication which is circulated freely throughout the European trade.
Disclaimer
www.fastenerandfixing.com
Published by
Managing Director Jamie Mitchell jamie.mitchell@verulammedia.com
Content Director Will Lowry will.lowry@verulammedia.com
Deputy Editor Claire Aldridge claire.aldridge@verulammedia.com
Sales Director Mac Rahman mac.rahman@verulammedia.com
Business Development Manager –Italy
Emiliano Pagliaroli emiliano.pagliaroli@verulammedia.com
Business Development Manager –DACH & Europe
Chantal Ridings chantal.ridings@verulammedia.com
Production & Design Manager Lee Duskwick lee.duskwick@verulammedia.com
The Publisher cannot be held responsible or, in any way, liable for errors or omissions, during input or printing of any material supplied or contained herein although the utmost care is taken to ensure that information contained is accurate and up to date. The Publisher also cannot be held liable for any claims made by advertisers or in contributions from individuals or companies submitted for inclusion within this publication. The opinions expressed are not necessarily those of the Editor or Verulam Media.
Copyright Entire contents copyright © Verulam Media Ltd 2023. No part of this publication may be reproduced, stored in a retrieval system, or transmitted in any form or by any means without the prior permission of the publisher.
Annual subscription (6 issues) to non–trade and outside EU is €160.00
Verulam Media Limited, Office 121, Ashley Road 134, St Albans AL1 5JR Tel: +44 (0) 1727 743 882
Find us online:
Part of the Mack Brooks GroupNORMA Group reported moderate growth in the first quarter of 2023 with group sales up 3.5% over the same period in 2022 to €315 million (Q1 2022: €304.4 million). Organically, the company grew by 2.1% in the first three months of 2023.
NORMA attributes this growth primarily to higher selling prices to compensate for inflation related cost increases. Positive currency effects in connection with the US dollar contributed 1.3% to sales growth.
CEO Miguel Ángel López Borrego commented: “We managed to successfully pass on materials related price increases and generate moderate growth in what continued to be a challenging environment. With this quarter we are not, however, at the level we have targeted for 2023. We will continue to work to improve our internal processes so that we can operate more efficiently overall and take advantage of growth opportunities. We will increase our profitability in the course of the financial year.”
In the EMEA region, sales increased by 10.9% in the first quarter of 2023 to €138.2 million (Q1 2022: €124.6 million). Strong organic growth of 11.8% was diminished slightly by 0.9% due to negative currency effects. The primary growth driver was a significant upswing in customer demand in the European automotive sector. Business with standardised joining technology for industry applications also developed well.
In the Americas region, NORMA Group increased sales moderately in the first quarter of 2023 by 2.5% year-on-year to
€137.6 million (Q1 2022: €134.3 million). In addition to positive currency effects of 4.6%, price increases were the main contributors to this growth. Volume related sales in the region fell 2.1% organically in the period from January to March 2023. While business with joining solutions for general industry applications, and for vehicles, both developed positively, business with water management products declined in the wake of extremely strong growth in the prior year quarter. This business is, for the most part, driven by end users who have been reluctant to buy due to the prolonged severe flooding in California earlier in the year.
In the Asia-Pacific region, sales in the first quarter were €39.1 million, which represents a decrease of 14% compared to the same period in the previous year (Q1 2022: €45.5 million). Organically, sales were down 11.8%; negative currency effects reduced sales growth by an additional 2.3%. Compared with the prior year quarter, demand from the Chinese automotive industry in particular was significantly lower – an after effect of the Covid-19 pandemic and the associated restrictions in China. In the business with joining solutions for industry applications, the sales level of the previous year was also not achieved.
Würth Group has once again reported double-digit annual sales growth, with sales for the financial year 2022 reaching €19.9 billion, well above the previous year, when they were € 17.1 billion, corresponding to growth of 16.8%.
Robert Friedmann, chairman of the central managing board of Würth Group, said results for the past two years had been “a remarkable achievement”, considering the multitude of imponderables that have challenged the company since the start of the Covid-19 pandemic in 2020 and more recently the war in Ukraine –times during which customers have valued Würth Group’s reliable delivery capabilities and service.
Germany remains the most important single market in the group, with a sales share of 39.4%. The group’s German companies achieved a sales increase of 13.1%, due to both the stability of individual business models and very high product availability. The company’s Electrical Wholesale Unit and Würth Elektronik Group were particularly successful, but with a 21.4% sales increase, Division Wood achieved the highest growth among the divisions of the Würth Line, with Division Industry a close second at 20.9%. The group’s parent and largest single company, Adolf Würth GmbH & Co KG, increased its sales volume by 10.5%, including intra-group sales. The companies outside Germany also
reported a successful year with an overall sales increase of 19.4% from top performing markets in the Americas, as well as southern and eastern Europe.
Besides its 43,000+ sales force, and over 2,500 pick-up shops worldwide, e-business is one of the strategic growth areas of the group, with digital procurement channels having become an integral part of the company’s customer order routine during the Covid-19 pandemic. This trend is reflected in sales, where Würth’s e-business accounting for €4.1 billion of sales across the group.
With all this strong growth requiring similarly strong logistics processes, Würth Group’s strategy is set on exploiting the full potential of digitalisation and automation, which will also help meet social challenges, such as demographic change and the shortage of skilled workers. Commenting on this, Robert Friedmann said: “On the one hand, our logistics robots improve productivity. On the other hand, they relieve our employees of physically demanding tasks. Automated processes enable us to supply our customers quickly and reliably.”
Hilti Group increased sales by 5.4% over the first four months of 2023, reaching CHF 2.142 billion (€2.198 billion). In local currencies, growth amounted to 9.7%.
Hilti continued on its growth path and posted a sales growth of 10.3% in local currencies in Europe. An increase of 13.7% was recorded in the Americas region, with double-digit growth in both North and Latin America. In the Asia-Pacific region sales grew by 17%, led by strong results in South Asia and the Pacific region. On the other hand, the recovery in China is sluggish because of a delayed project business resumption after the Covid-19 lockdowns. Sales growth in the eastern Europe / Middle East / Africa region was at -15.1%, which was expected due to the ongoing war in Ukraine.
The Swiss franc remained strong against the euro, US dollar and other currencies, resulting in -4.3% points sales impact from January to April. “Interest rate hikes, continued inflation and geopolitical tensions still have a negative impact on the global construction market. However, we observe geographic differences with a negative sentiment in Europe, a mixed picture in the Americas and positive signals from Asia. We are adapting to this situation and our growth level for the first four months is in-line with our expectations,” explained CEO Jahangir Doongaji.
Hilti Group continues to expect a high-single digit sales growth in local currencies for the full year 2023.
DELO, a leading manufacturer of industrial adhesives for the automotive, consumer electronics and semiconductor industries, generated revenues of almost €205 million during the fiscal year 2022/23 – a 12% increase compared to the previous year.
Significant growth drivers for DELO included the Japanese and US markets, which is reflected in the Americas’ share of total sales, which rose to 18%, while the Asia market share of sales, traditionally the company’s largest market, fell to 48%. A further 34% of revenues were recorded in Europe. At the industry level, the main pillars were the semiconductor, automotive and consumer electronics industries.
Dr Wolf Herold, managing partner at DELO, said: “The past fiscal year was very successful, but at the same time very challenging. While Russia doesn’t play a role for us as a market, the war in Ukraine led to sharply rising raw material prices, complicated logistics to Asia and major uncertainties in energy supply.”
The company also benefitted from high inventory and great operational flexibility during this period, as was the case during the Covid-19 pandemic, which gave customers peace of mind through supply security. Also, similar to previous years, investments in R&D accounted for approximately 15% of DELO’s 2022/23 turnover, in
addition to which there was increased investment in international operations. For example, during this last fiscal year, DELO moved into new or enlarged premises in Shenzhen (China), Seoul (South Korea), Boston, as well as San José (USA). In addition, the search is currently underway for a new production site to be built in southeast Asia. Plus, in Windach, Germany, construction on a fully automated 6,000m 2 warehouse is set to begin this year.
As an employer, the company now has 100 more staff than it did a year ago, having welcomed its 1,000 th employee at the beginning of May; more than 200 further jobs are set to be created in the current fiscal year.
With our wood screws, available in a wide range of both sizes and finishes. The only thing we don’t know precisely is the whereabouts of all our products. But nonetheless we are sure that some are very close to you.
Achilles Seibert has confirmed that since April 2023 it has been working on a new warehouse annex that will see the German wholesaler increase its warehouse capabilities by 50%.
Since 1951 Achilles Seibert GmbH, known as Achill, has been a family run business that originally established itself within the market for its expertise in fasteners with small/long forms and dimensions, before developing its range to now include an extensive line of products.
“After a lot of preparation, we have finally started with our warehouse annex, which we are very pleased about,” explains Timo Scholle, managing director at Achilles Seibert. “The Covid-19 pandemic, and challenges within the international market, had a real impact on every wholesaler, but at Achill we were able to overcome these challenges and continue to grow. The new warehouse expansion will improve our supply capabilities and ensure we are able to take advantage of future opportunities within the market.”
Achill expects the warehouse expansion to be completed in September, with the installation of a high rack storage system.
CAMCAR Innovations® has announced that it has purchased the assets of its partner, Ttapdrive AS – the Norwegian company that created the ttap® brand of drive systems.
CAMCAR and Ttapdrive have already cooperated in a partnership for over 10 years to promote the TORX® ttap® drive system through many quality distribution channels in the construction industry. TORX® ttap® provides leading stability (anti-wobble) and stick fit – allowing increased productivity and lower injuries on job sites.
“The ttap® brand and technology fit very well with our mission to be a leading technology provider in the fastener industry,” states CAMCAR. “Try it and you will Feel the Difference™.”
CAMCAR Innovations® is a leading R&D organisation that develops and sources fastener technology that offers meaningful improvements in performance and assembly ease – solving real world problems. Its products are manufactured by a global network of quality manufacturers – making it easy for end users to find reliable and trusted sources.
In recognition of the growing opportunity to introduce the Nedschroef brand to more customers worldwide, Nedschroef Machinery has announced a joint venture with PMC in China to serve its business for the east Asia region.
PMC is an industrial group engaged in the design, manufacturing and sale of advanced machinery parts and components. Nedschroef explains that the joint venture is part of that transformation and confirmation that Nedschroef Machinery is committed to fulfilling its strategic growth plans. The company expects that sales and services outside Europe will exceed 65% of the total by 2030 and growth in the markets that make up the east Asia region are a key part of achieving that goal.
“This joint venture will help us better and more quickly respond to our east Asia customers’ needs,” explains Cees Sistermans, managing director at Nedschroef Machinery. “Our increased focus on customers outside Europe is an exciting time for us, since many east Asia countries have a well established cold and warm metal forming industry”.
The east Asia operation will be based in China and all Nedschroef Machinery functions critical to development and support the east Asia region are represented, including procurement, sub-assembly, marketing, sales, service, and others.
The acquisition of Polytec PT by the French-based Arkema Group, of which Bostik is part, strengthens Bostik’s product offer to serve the fast growing batteries and electronics markets.
This bolt-on acquisition is part of Arkema Group’s strategy to become a full system provider and support its customers to develop sustainable solutions for the batteries and electronics markets. For its part, Germany-based Polytec PT develops thermal interface materials for batteries and engineering adhesives for the electronics market, from its main production site in Karlsbad, and has annual sales of around €15 million. The company’s strengths and expertise in thermal interface materials are key to enabling battery fast charging, as well as efficient dissipation of heat, with Polytec PT having already built a solid position in this market.
The acquisition complements Bostik’s product range in engineering adhesives and, by leveraging the Arkema Group’s global reach, will enable it to hit a turnover of around €50 million after five years, in these high value applications.
“This acquisition is a great opportunity for Bostik and Polytec PT staff, who are already collaborating on new solutions, by allowing them to accelerate new developments and become a more significant player in the thermal interface materials and electronics markets,” explains Arkema.
in the course of 2023, as part of a rebranding process that better aligns Jeveka with Bossard’s brand identity and values.
Acquired by Bossard in October 2021, Jeveka has been recognised as a quality leader in technical fastening products, and it remains committed to delivering exceptional products that meet high-quality standards. Through its alignment with Bossard, the company will leverage the group’s global network and expertise, making more products and services available to its customers in the Benelux market. These solutions will help Jeveka’s customers and partners optimise processes, while increasing efficiency and productivity in a sustainable way.
“Over the coming weeks and months we will introduce our csutomers to Bossard products and services, including updates on our website, social media channels, and hopefully during a visit to our premises in Almere, the Netherlands,” mentions Jeveka. “We want to assure customers that our core values and principles will remain unchanged, and we will continue to deliver exceptional products and services, build strong relationships with our stakeholders, and create value for all.”
A.S.F. Fischer B.V has acquired the entire drilling brand, REX, including its associated product range, from the Dutch-based firm Hemmink B.V. All logistics and commercial activities of REX are being integrated as part of the merger.
Arnoud Booij, CEO of A.S.F. Fischer, explained the acquisition of the REX brand aligns perfectly with the company’s growth strategy. “We aim to continue being a reliable, stable, and forward thinking partner for our clients in the future. With the acquisition of the REX brand, we strengthen our position in the market and broaden our brand and product portfolio. Through the acquisition, customers of both companies will benefit from synergies in both logistics and commercial areas.”
REX has been a leading choice for professionals for over 75 years in the field of high-quality drills, chisels and hole saws. For its part, A.S.F. Fischer is known for brands such as Woodies®, Interdynamics®, QlinQ ®, Steelies®, Grabber ®, Fis®-Profi and Perfectmate®. This is the second recent acquisition for the company following its takeover of Herag last January.
High-strength bolts. One-part fastener - offers a higher load-bearing capacity than a hexagon bolt with a separate washer.
Quicker to apply than a standard hex bolt needing a separate washer.
Serrated option available for when vibration resistance is required.
Commonly used on production lines.
73 sizes available
BOXED
Nedschroef Machinery has announced Kriti Tools as its distributor for machine sales and after sale services in India. The agreement will commence immediately.
Aleading provider of cold and warm forming multi-stage horizontal metal presses and services, Nedschroef Machinery chose Kriti Tools Pvt Ltd due to its broad experience in the metal forming industry.
With after sales service an essential component for customers, Kriti Group personnel are being trained to handle customer service related to spare parts and filed service throughout May and June. Field service and spare parts fulfilment will be initiated by Kriti Group after training has been successfully completed.
Furthermore, Kriti Group will store Nedschroef Machinery spare parts inventory in Delhi to provide timely services to customers. Sadeesh Premananth, managing director at Kriti Group, commented: “We see good opportunities to cooperate and to team up to offer the best service possible to our customers.”
Cees Sistermans, managing director at Nedschroef Machinery, added: “We believe with a local presence we can get closer to our customers and respond quickly to their needs – satisfying customers and engaging them over the long-term”.
ND Industries Inc, a leading provider of fastener locking and sealing solutions, has announced that Humberto Avila has been promoted to general manager of its Dallas, Texas, processing facility. This advancement highlights Humberto’s dedication and contributions to the company throughout his 17 year tenure.
Humberto’s career at ND Industries began as quality manager of ND’s Los Angeles, California location. Over the past few years, he assumed additional responsibilities to prepare for this general manager position. During this time, he effectively managed and supervised day-to-day activities in production, sales and customer service.
Humberto’s work history demonstrates his commitment to continuous improvement. Notable among his accomplishments are the implementation of robust systems for collecting and tracking quality and production metrics. By utilising this data as a foundation for vital business decisions at the plant level, Humberto has been an instrumental force in driving ND Industries towards operational
Bufab Group has appointed Pär Ihrskog as Chief Financial Officer (CFO) – who will take up the position on 14th August 2023. In the interim, Frederick Neely will continue to serve as the acting CFO until Pär assumes his responsibilities.
Pär Ihrskog has a long and successful leadership career within SKF Group and has worked in various countries and positions – including serving as head of group business controlling. Most recently, Pär held the position as Group CFO/CIO for the Embellence Group. Pär has a degree as MSc from the Gothenburg School of Economics in Sweden.
“We are very pleased to welcome Pär to Bufab. He combines broad financial expertise with international experience and has a strong track record in listed companies. Pär will strongly contribute to our strategic ambitions and our continued growth journey ahead,” said Erik Lundén, president and CEO of Bufab Group.
excellence. Furthermore, his knowledge in product application design and testing protocols has paved the way for securing major accounts, including renowned companies such as SpaceX, Tesla and Airbus.
As Humberto assumes the role of general manager, he looks forward to leveraging his expertise in aerospace fasteners, combined with his knowledge of production and process design, to foster the continued growth and prosperity of ND Industries’ Texas facility.
“Taking on the role of General Manager presents an exciting opportunity to utilise my industry experience and contribute to the success of our Texas plant,” said Humberto Avila. “I am eager to lead our talented team towards achieving new heights of growth and excellence.”
Ahlsell Norge AS has entered into an agreement to acquire all shares in Lindqvist AS, a company that provides tools and supplies to craftsmen and the industrial sector in western Norway.
Lindqvist offers a wide range of power tools, hand tools, fasteners, and consumables, with its specialist expertise, service offering, and product range in drilling and cutting equipment, strengthening Ahlsell’s total offering.
“By combining our strengths and competencies, we can now offer our customers a broader product range together with our comprehensive logistics solutions,” reports Ahlsell.
Ahlsell and Lindqvist share the same vision of building a more sustainable society, and Lindqvist’s service workshop creates the opportunity for customers to extend the lifespan of the products they buy. “When Lindqvist’s expertise is combined with our strong sustainability work, we can offer customers even more environmentally friendly and cost-effective solutions,” underlines Ahlsell.
Lindqvist’s business includes an outlet, a warehouse, an online store and a workshop with operations in Bergen. The company has 10 employees and the turnover in 2022 amounted to NOK55 million (€ 4.7 million).
We were deemed worthy of the Deloitte Best Managed Companies Türkiye Award; as a result of the evaluation made by an independent jury under four main headings: strategy, competence & innovation, culture & dedication, governance & financials.
We are proud to receive an award in this program, which aims to highlight companies that contribute to the country's economy by applying the best management principles.
Rivit Srl, a specialist in blind rivets and riveting tools and part of FERVI Group, has appointed Francesco Montanari as its new CEO. Francesco joined FERVI Group in November 2022, initially serving as general manager of Rivit.
Francesco has a vast experience within international markets, graduating in electronic engineering from the University of Bologna – with several postgraduate executive programs (IMD in Lausanne, MCE in Brussels, SDA-Bocconi in Milan and Profingest in Bologna). He began his work at Andersen Consulting, now Accenture, with periods in the USA, Italy and France, dealing with marketing information systems.
Francesco then joined Datalogic in 1993 as product manager, then moved on to sales management, marketing management, and was then appointed director of marketing & communication. From 2002 to 2005, he was president and general manager of Datalogic France (Paris office), returning then to Bologna in 2005 as director of the mobile computer business unit.
Following the incorporation with PSC Inc, and the subsequent reorganisation of the Datalogic Group in April 2007, he was first appointed general manager and then product and services vice-president of Datalogic Mobile.
From 2012 to 2016, he was vice-president and general manager of the mobile computing business unit of Datalogic ADC, after the incorporation between Datalogic Mobile and Datalogic Scanning.
Within the reorganisation of the group, he was appointed chief marketing officer of Datalogic Spa, with responsibility for all corporate marketing and communications activities of the Datalogic Group.
“It is with great pleasure that I intend to make my experience available to consolidate Rivit’s positions on the global market, with the aim of both optimising the approach to the domestic market and to strengthen Rivit’s presence worldwide,” states Francesco Montanari. “We already operate with the two Rivit subsidiaries in India and Morocco, but we also want to organise a consistent approach to the local needs in all other countries, starting from those already served by Rivit. We start from a company that has been on the market for half a century, already a leader in some sectors, and which we are going to strengthen by working on a mix of products and services, also with external partnerships. The goal is to be even more of a reference point for fastening,”
Camcar Innovations® has announced the 2022 winners of its TORX® Drive System World Class Quality Award. Since its introduction in the 1960s, the TORX® Drive System has become the world’s leading high performance drive system for threaded assemblies in a broad range of applications and end user markets
Owner of one of the largest and longest running intellectual property licensing programs in the fastening industry, Camcar Innovations ® established the annual award program in 2005 to recognise its high performing, qualified licensees who demonstrate the greatest commitment to manufacturing high-quality, genuine TORX® products during the previous calendar year.
Six drive tool and twenty-two fastener manufacturers –representing the countries of China, Japan, Mexico, Singapore, Spain, Sweden, Taiwan, and the United States –were among the TORX® licensees receiving the award for their 2022 performance.
The recipients of the TORX® Drive System World Class Quality Award for 2022 are:
TORX® drive tool licensees
APEX Tool Group (Dayton, Ohio, USA).
Klein Tools (Mansfield, Texas, USA).
Progressive Chun Yip Co Ltd (Tianjin, China).
SNA Europe (Vitoria, Spain).
Snap-on Incorporated (Elizabethton, Tennessee, USA).
Zhejiang Younhang Automobile Components Co Ltd (Zhejiang, China).
TORX® fastener licensees
Acument Global Technologies (Belvidere, Illinois, USA).
Acument Global Technologies (Spencer, Tennessee, USA).
Acument Global Technologies (Monterrey, Mexico).
Arnold Fasteners (Shenyang) Co Ltd (Shenyang, China).
Bulten Hallstahammar AB (Hallstahammar, Sweden).
Bulten North America LLC (Streetsboro, Ohio, USA).
Celo S.A (Barcelona, Spain).
Celo SUZHOU (Taicang, China).
EJOT-ATF Fasteners de Mexico SA de CV (San Luis Potosi, Mexico).
Gateway Screw & Rivet (Glendale Heights, Illinois, USA).
Gosho Works Ltd (Yokohama-shi, Kanagawa, Japan)
Infastech/Tri-Star Limited (Tainan City, Taiwan).
ITW Shakeproof Industrial Group (Watertown Wisconsin, USA).
Lih Ta Fasteners Co Ltd (Taoyuan City, Taiwan).
Meira Corporation (Shinhazama, Seki City, Japan). Semblex Corporation IL (Elmhurst, Illinois, USA).
Sin Fu Shan International Corporation (Kaohsiung City, Taiwan).
Southco Inc, NY (Honeoye Falls, New York, USA).
Stanley Engineered Fastening (Decorah, Iowa, USA).
Topura America Fastener Inc (Bowling Green, Kentucky, USA).
TR Formac PTE LTD (Singapore). Unisteel Technology Co (Nantong City, China).
“Once again we applaud our TORX® drive licensees who have made the commitment to establish themselves as world class suppliers,” said Steve Dixon, director of Camcar Innovations® “The efforts on their part to accomplish this achievement, many of them for multiple years, have contributed to the growing importance of the TORX® brand and its representation around the world of the highest levels of quality assurance and performance. Camcar Innovations® is very proud of each of these companies and presenting this award confirms their overall positions as the best of the best.”
The Industrial Fasteners Institute (IFI) announced it is developing an apprenticeship program for machine operators that will be recognised by the US Department of Labor.
With an increasing number of skilled machine operators retiring each year, the need to transfer expertise to the next generation has become critical. IFI has partnered on the development of the apprenticeship program with the Marshall University Advanced Manufacturing Center (MAMC), which has written and implemented multiple programs in use across the US.
“The shortage of workers in fastener manufacturing will not resolve on its own,” said Dan Walker, managing director at IFI. “With each passing year, our industry continues to lose skilled machine operators to retirement, and that knowledge must be passed on to the next generation.”
IFI members “have decided to roll up our sleeves and create an apprenticeship program for our industry to help solve this ongoing problem”.
IFI Chairman Gene Simpson, of Semblex Corporation, said the program represents a significant collaborative effort: “An initiative as important as this needs to be driven by a group like the IFI. Many companies have their own programs that work well, but these are individual efforts with a heavy burden and mixed results.”
Simpson said by leveraging IFI’s knowledge and resources with MAMC, “the goal is to create a program that will create consistency and results for use by the entire industry”.
MAMC’s Apprenticeship Works, the National Advanced Manufacturing Apprenticeship Partnership, assists companies in developing and implementing DOL Registered Apprenticeships. Apprenticeship Works is funded entirely
through a US$4.5 million grant from the US Department of Labor – Employment & Training Administration.
Derek Scarbro, interim director at MAMC, noted the “fastener industry is a critical link in the supply chains of key sectors, from automotive and aerospace to defense. Creating a highly qualified workforce is imperative to strengthening American manufacturing”.
Unlike IFI’s current member training program, which primarily consists of webinars and day long instructor led training, the new apprenticeship program will provide a comprehensive framework for training machine operators. It will involve ‘hands on’ training in a company’s own facility, utilising their equipment and personnel as mentors for the apprentices. The program will also use self-paced online learning modules – developed through an IFI and the Workforce partnership training system.
Apprenticeship programs offer a structured learning experience with multiple levels of achievement and wage progression. Participants are paid to learn and gain ‘hands on’ experience in a production environment under the guidance of experienced operators. Manufacturers will benefit from the ability to hire individuals without prior manufacturing experience and train them under a recognised and structured learning program. Apprentices will acquire a transferable skill recognised throughout the industry, opening doors to employment opportunities with job security, increasing levels of responsibility and competitive wages.
The IFI has formed a committee of plant personnel and machinery suppliers, which is working towards making the program available to manufacturers within 12 to 18 months.
Henkel Adhesive Technologies began building a US$130 million manufacturing facility in China that will run solely on renewable electricity when completed, increasing supply capacity of its high impact adhesive products for domestic and international markets.
Located in Shandong Province, the 1.6 million square foot factory – complete with automated production workshops and an 86,000 square foot smart warehouse – will manufacture products for the electronics, automotive, medical, equipment manufacturing and aerospace industries.
Henkel hopes the facility “will showcase how smart technology and sustainability can influence adhesive manufacturing”.
“China plays an important role in our operations at Henkel and continues to demonstrate economic resilience and growth,” said Mark Dorn, Henkel executive vice-president of Adhesive Technologies. “Investing in the Kunpeng plant reflects our strong commitment to the future of our business in China and the Asia-Pacific region, creating value for our customers.”
Henkel points out the plant will use 100% renewable electricity and incorporate a range of sustainability features, including an advanced building energy management system, water circulation system and a ground source heating pump system.
These technologies are expected to reduce carbon dioxide emissions by more than 5,000 tonnes per year and reduce operational water consumption by 25%.
“Kunpeng, our state of the art facility, will set a new industry standard with its modernisation and sustainability design, keeping us ahead of the curve and meeting evolving customer needs,” added Rajat Agarwal, president of Henkel Greater China. “China’s focus on achieving high-quality and sustainable development creates unique opportunities for technology and product advancements.”
Stanley Black & Decker has announced its first quarter 2023 financial results, showing revenues of US$3.9 billion (€3.57 billion) – down on the same time last year due to lower consumer and DIY volume sales, as well as currency and strategic divestiture moves.
Donald Allan Jr, president and CEO at Stanley Black & Decker, said the company continued to build momentum and make strong progress towards streamlining and optimisation: “The organisation remains focused on our transformation plan, and we took additional steps forward to better serve our customers and deliver for all key stakeholders by reducing inventory, leveraging enhanced cost controls and optimising our global supply chain.”
He continued: “While the near-term demand environment remains dynamic, the long-term opportunity in our key markets remains compelling. We are making strategic investments behind our strong, iconic brands, innovation engine, as well as electrification and commercial activation, to position the business for sustainable growth and margin expansion.”
He added that he was encouraged by progress to date and was confident that by executing company strategy, Stanley Black & Decker was positioned for strong, long-term growth, cashflow generation, profitability and shareholder return.
Currently, the company’s primary areas of strategic focus include advancing innovation, electrification, and global market penetration, to achieve organic growth two to three times that of the market; streamlining and simplifying the organisation and investing in initiatives that more directly impact customers and
end users; and returning adjusted gross margins to historical 35% and above levels, by accelerating the operations and supply chain transformation to improve fill rates and better match inventory with customer demand.
In terms of its global cost reductions, the company has continued executing a series of initiatives to generate cost savings through corporate simplification and inventory reduction, with the ultimate objective of driving long-term growth, improving profitability and generating strong cash flow.
With the company continuing to execute against its strategy, and its various initiatives remaining on track, Stanley Black & Decker is set to generate annualised cost savings of approximately US$1 billion by the end of 2023, growing to approximately US$2 billion by 2025. Meanwhile, getting back to the first quarter of this year, the company was ahead of plan and achieved US$230 million of pre-tax, run-rate savings from lower headcount, indirect spend reductions and supply chain transformation.
To date, the company’s global cost reduction programme has generated US$430 million in run-rate savings towards its goal; and inventory has been reduced by approximately US$200 million, sequentially, versus the prior quarter, and is on track to deliver between US$750 million and US$1 billion of inventory reductions in 2023, which will support free cash flow generation.
Sales are strong though lower than records set in 2022, but the elephant in the room is inventory, State of the Industry panelists told the National Fastener Distributors Association (NFDA) annual meeting.
Lead times are starting to come down, panelist Dave Monti, of Fall River Manufacturing Co, told the NFDA. Record 2022 sales topped “two years of unusually large lead times,” Monti said. Now lead times are shrinking, partly due to better staffing. “A year and a half ago, we couldn’t hire,” Monti said. “But in the past six months, labor supply turned around and today Fall River is fully staffed.” While Fall River has raised wages for its 67 employees, Monti credits company culture for employee retention.
Randy Hrdlicka, purchasing manager for master distributor LindFast Solutions Group, said they have also raised wages, but agreed that the team also “appreciates being appreciated”. Hrdlicka said the fastener industry is still feeling the residual effects of Covid-19. After the post-Covid sales boom, there have been “small drops per month since April”.
“But is inventory a problem?” asked Cory Wing of rep firm Wing-Hamlin Co. After the shortages, are distributors padding forecasts? “People have short memories,” Wing commented.
Ed Smith, director of sourcing for distributor Würth Revcar Fasteners, said 2022 brought record fastener sales. Now customers are beginning to have time to look at domestic suppliers. “Buyers want more face-to-face time” and multiple
approved sources, Smith said he finds. “There is more price shopping. The shelves are full.”
Important for steady supply is suppliers, distributors and customers “communicating and forecasting”, Hrdlicka added.
A key number to forecasting prices are the steel costs from Taiwan’s China Steel, continued Hrdlicka. There are “slight declines” in the metals markets, he noted. Other markets tend to be close to China Steel’s numbers.
Monti sees opportunity in domestic fasteners. “We are seeing domestic sourcing up,” Monti said. In addition to the actual fasteners, buyers are wanting domestic certifications, he added.
Smith said there is more talk about fasteners coming from India. Turkey and Poland are also increasing fastener manufacturing, especially for Europe. Buyers want less product from Asia, more face-to-face time with suppliers and multiple approved sources, Smith commented. “Our customers are splitting contingency plans.”
“Differentiating yourself as a supplier is important,” Wing said. “Value-added is popular now.” Monti advised spending time training now. “It doesn’t help with current cost, but puts you in a better position for an uptick,” Monti said.
Taiwan’s National Aerospace Fasteners Corporation (NAFCO), a manufacturer of fastener products for the aerospace, electronics and high-end industrial sectors, saw its 2022 consolidated revenues reach NT$2.193 billion (€64.5 million), which amounted to a 53.76% increase compared to the same period the previous year.
NAFCO puts the figures down to the easing of the Covid-19 pandemic and reopening of borders, as well as a gradual increase in aerospace customer demand for its products. These latest figures also mark a three year high, the third highest in NAFCO’s history, and close to its pre-pandemic revenues in 2018.
Profitability also benefited from a higher utilisation rate and the appreciation of the US dollar, with a gross 2022 profit margin of 23.33%, an increase of 11.68%. Operating income over the same period was NT$127 million, with an operating profit margin of 5.78% and an overall 2022 net profit of NT$150 million.
Looking at this year, the company said demand for aerospace fasteners continues to be strong, with most orders visible for more
than 12 months. If market conditions change little, the company expects to maintain good revenue growth and profitability this year, as well as continue to increase production capacity in response to customer demand.
As if proving the point, the company recently announced its March 2023 revenues, which reached NT$263 million in a single month, an annual increase of 78.8%; the cumulative revenue for the first three months of the year hit NT$696 million, an annual increase of 64.02%.
In addition to aerospace fasteners, NAFCO has also been developing its automotive fastener business and the parts and components, designed in co-operation with tier one car manufacturers, are expected to gradually increase in volume and fuel revenue growth.
QST International and Boltun Corporation have jointly secured a NT$12 billion (€353 million) ESG (environmental, social and governance) linked syndicated loan to underpin the expansion of their portfolios from conventional fasteners to new products.
Both companies, QST International – as a manufacturer of automotive fasteners and metal parts – and Boltun Corporation – as a supplier of metal parts for industrial use – will focus on products that combine light metal, engineering plastic and carbon fibre to meet the needs of vehicle manufacturers for lightweighting, automatic assembly, assembly process streamlining, as well as energy saving and carbon reduction.
Leveraging their experience in EV fasteners, and certification by international automakers, the two companies are actively participating in customer collaborative R&D and supplier orientation programmes, gradually moving from OEM to ODM, while ensuring their activities align with environmental protection and energy saving trends.
A major part of their collaboration to meet long-term development needs, and to enhance global flexibility and competitiveness, will see the companies set up an overseas production base in Vietnam, acquiring about 35 hectares of land in an industrial zone, with an initial investment of US$100 million. Construction of the plant is expected to begin this year and production will begin in the first half of 2024.
Following a NT$200 million spend on upgrading equipment in both its Taiwan and Vietnamese plants, that began in 2021, Homn Reen has seen production capacity and speed at both its plants at least double, chiefly due to the replacement of older, one die, two punch equipment with new multi-punch machines.
The plant upgrades and resulting production improvements are part of General Manager Jack Lin’s vision to produce higher value product, as well as extending the range of screw sizes produced from between 4mm and 400mm. Lin believes many emerging countries can already provide low price, low end products, which has forced Taiwan’s fastener industry to shift to higher-end, higher cost products.
Previously, Homn Reen’s 40 years of experience making construction fasteners delivered about 2,500 tonnes to 3,000 tonnes of fasteners per month to domestic and overseas customers, produced on 320 sets of the older equipment in its Taiwan and Vietnam plants. Now, certified to IATF 16949, the company has successfully improved the production system, together with employees’ quality awareness, resulting in what it says is a “satisfied” repeat overseas customer base for its automotive products, with the company currently making it into tier two supply chains.
To meet environmental requirements for manufacturing automotive fasteners, the company has also installed an oil and gas filtration system on the production line, which supports Homn Reen’s move to deliver higher priced, higher quality automotive solutions, too.
The company’s environmental awareness is also the focus of its trial of the EU’s Carbon Border Adjustment Mechanism (CBAM), a carbon tariff on carbon intensive products, which will then be officially implemented in the future. Besides implementing a 5S workplace management system to improve efficiency and ensure quality, the company is in the process of taking a carbon inventory to understand its carbon footprint and move closer to carbon neutrality.
Other practical environmental steps include a NT$10 million investment to install 2,315m2 of solar panels on its Taiwan plant and its intention to use solar panels whenever additional space is available.
A three year, INR 1,000 crore (€111.8 million) capital expenditure programme has been initiated by automotive parts maker Sundram Fasteners, with the investment aimed at helping the company satisfy increased wind energy and electric vehicle (EV) demand.
After three years of modest expansion for the financial years 2020 to 2022, the company resumed its capex cycle this year – investing roughly INR 300 crore so far, with the remaining INR 700 crore of the programme to be used over the next two years.
On the electric vehicle side, OEM orders for EV parts from the company’s EV business have increased. Sundram also won a six year contract worth US$250 million (€229.8 million) from a major international OEM, with peak revenue of US$52 million (INR 426 crore) expected in 2026. The company’s US$375 million EV car order book will receive INR 300 crore of the anticipated INR 1,000 crore investment package.
As for its non-automotive sectors, which comprises of the wind energy industry, aftermarket, tractor business, and industrial divisions, the company wants this to account for 50% of revenues over the medium to long-term to overcome business cycles. In 2023, the aftermarket business has so far earned INR 600 crore, with industrial accounting for half of that. The company is also addressing energy pricing and variable costs, with the intention to use green energy sources and employ captive power suppliers to reduce costs.
Automation and robotics have huge growth potential in India’s steel industry, according to Atul Bhatt, chairman and managing director of state-owned steel company, Rashtriya Ispat Nigam Ltd (RINL).
Bhatt made the comments recently at the virtual launch of RINL’s ‘Open Challenge Programme (OCP) 2.0’, adding that equipment developed by start-ups will save energy and improve safety – resulting in a speedy return on investment for the company. He noted that the government’s focus on infrastructure development has made India’s steel industry the world’s second largest and fastest growing.
The OCP 2.0 programme, part of the Kalpataru CoE (Centre of Entrepreneurship) initiatives, aims to select startups specialising in Industry 4.0 technologies and – in a joint effort with the Software Technology Park of India, the Ministry of Electronics & IT, RINL, and the Government of Andhra Pradesh – intends to make India self-sufficient in Industry 4.0 technology.
Additionally, the CoE will feature laboratories dedicated to Industrial Internet of Things; industrial automation with artificial intelligence and machine learning; augmented reality and virtual reality; industrial automation with robotics and drones; and industrial automation lab with robotics and 3D printing. The CoE will incubate 50 physical and 125 virtual start-ups over five years. RINL and several other governmentowned enterprises, such as HPCL, NTPC, BARC, HSY, and BHEL, will be helped by start-ups and industry mentors.
Sterling Tools, a manufacturer of high tensile cold forged fasteners, previously announced its March 2023 standalone quarterly financial results, which showed the company generated net sales of INR 155.10 crore (€17.3 million), representing a 12% increase over the same period last year.
Despite this net sales growth, the company had a fall in quarterly net profit, which stood at INR 5.26 crore, a 30.84% decrease from INR 7.61 crore in March 2022.
However, the company’s EBITDA increased 13.69%, year-on-year, reaching INR 21.09 crore in March, up from last year’s INR 18.55 crore. At the same time, the company’s earnings per share
(EPS) fell to INR 1.46 in March from INR 2.11 for the same month last year. That said, with variations in financial performance, Sterling Tools’ share price has increased dramatically, finishing at INR 423.30 on the National Stock Exchange (NSE) of India on 8th May, having generated returns of 69.35% over the previous 6 months, and 214.96% over the last 12 months.
Originally founded in 1953, and currently a member of PCC USA, Metalac SPS celebrates its 70 th anniversary this year, as a fastener manufacturer that has established itself as a key supplier to end user markets, including automotive and aerospace.
When Ford Motor Company inaugurated its first serial assembly line in São Paulo City, Brazil, in 1953, Metalac was starting its activities, as a manufacturer of cylindrical head bolts with internal hexagon, in the very same neighborhood.
With new leadership from 1957, under the control of the Júlio Milko and Léo Braun, respectively a Hungarian and a North American, the company started a new era combining growth and fast modernisation.
A prime example being that by 1959 the company has already become part of the supply chain for several multinational automakers within Brazil, such as Ford, General Motors, Mercedes-Benz, and Volkswagen – allocating its bolting lines for installations in cars, trucks, and buses, including items for critical applications.
Associated with North American SPS Technologies since 1966, Metalac made one of its most important transformations when it moved to 42,000m 2 site in Sorocaba City, 110km away from São Paulo, in 1979.
Since 2003 all operations of SPS were sold to the Precision Castparts Corporation (PCC), a producer of a wide range of complex metallic products for aerospace and industry. Since then Metalac has become a source of aerospace fasteners, which has included robust investments in the local production of bolts and nuts for use in landing gears and braking systems on planes.
Today, Metalac has more than 300 direct employees, as well as a 37,000m 2 modern factory that has a production average of 53 tonnes per day, mainly to the automotive sector.
Systek Tecnologia hosted its inaugural bolted joints workshop at the Technological Park in Sorocaba City, to the west of São Paulo, with 117 people attending what Systek believes will be a periodic event.
Systek Tecnologia has more than 25 years of experience in the manufacturing and servicing of the equipment and technology involved in tightening, measuring, testing and control systems.
Lídio Andrade, director of Systek and main lecturer, commented: “Our motivation behind the workshop was to share the knowledge we have acquired as a business over the last 25 years on the various tightening, measuring, testing and control systems within the market and, through discussion and interaction, talk about how this relates to bolted joints.”
Attendees of the Systek workshop included Brazilian fastener manufacturers Brasimpar Industria Metalurgica, Lipos Parafusos, Metalac SPS, OMKE, Tekfor Group, and Grupo Tecnofix, as well as companies from other sectors such as MKS-Atotech, Metalfast Industria, Montman, Bosch, Dana, Gestamp, Hyundai, Kanjiko, Knorr-Bremse, Krupp, MWM, Scania, and Toyota, as well teachers and students from Senai (National Service of Industrial Learning).
Experts are predicting that more than 10,000 tonnes of fasteners will be used by the Brazilian motorcycle sector, if the current trends for Brazilian production continues for the remainder of 2023.
In March, 152,450 motorcycles were built in Brazil, which took the total number for Q1 of 2023 to 397,070 – a 21.37% increase on the same period in 2022 (327,139) and a 40.61% increase compared to Q1 2021 (See Table One). If this trend continues, then the total Brazilian production for 2023 has the potential to reach 1.7 million motorcycles.
According to Rubens Cioto, director of the Fastening Technological Center (Centro Tecnológico de Fixação), during the assembly process for each motorcycle, an average of 6kg of bolts, screws, nuts, and other fasteners, are used. Therfore if the annual production does reach 1.7 million, the number of fasteners would go over the 10,000 tonne mark.
Over the last five years Brazilian motorcycle production has continued to increase, with the only fall occuring during the height of the Covid-19 pandemic. There is also hope that the sector could overcome the two million barrier in 2024, a target that has not been achieved since 2012, when it reached 2.136 million units.
Sérgio Milatias, editor, Revista do Parafuso, www.revistadoparafuso.com.br
Meeting the ongoing demands of the market is something that Fastbolt Group has become accustomed to, with the business looking to invest in key areas to not only provide solutions for today’s needs, but also for future challenges.
Fastener + Fixing Magazine last interviewed Ekkehard Beermann, managing director at Fastbolt Group, twelve months ago – when there were numerous challenges within the fastener sector. “Last year there were a whole host of outside factors that were impacting every business – product availability, freight availability and costs, raw material prices, the introduction of the anti-dumping duties, it seemed like a never-ending list,” states Ekkehard. “I’m glad to say that twelve months later the market has once again completely changed, but this time for the better –with prices having dropped due to raw material and freight issues returning to some sort of normality within Europe.”
Whilst Ekkehard is clear that the market is returning to a ‘pre-Covid normal’ there are new challenges companies are having to handle. “At the moment, most distributors are overstocked, as a lot of the old back orders held up by the pandemic were eventually shipped out to European warehouses. This has created a situation where there is now too much stock in the marketplace. This is a natural part of the process, especially after an extreme period such as the pandemic, and all the other factors, but it does create a new problem.”
Another topic that Ekkehard believes has still not been fully felt
slowed down the demand for products and in turn the potential impact of the anti-dumping duties,” explains Ekkehard. “Europe is currently well equipped with product and stock is readily available, which means there has been no real demand. When you look at the import volumes from the US market, these have also gone down compared to previous years, as there is a similar level of high stock. This means non-Chinese suppliers are less busy and products are more available, with lead times also stabilising. However, that doesn’t mean this will always be the case. Once the overstock situation within Europe and the USA starts to rectify itself, and orders start to increase, it could become more difficult to source products and that is when duties will start to be felt.”
Ekkehard adds: “When it comes to the fastener sector there is always something going on and that is why at Fastbolt we are continuously looking at ways we can handle current topics, as well as try to predict future problems.”
In order to meet the needs of the market, Fastbolt recently carried out a long-term analysis of ongoing needs and how it could provide solutions by investing within its internal intra-logistics. “From our analysis, we identified there was an ongoing need to
increase overall stockholding; move towards a more sustainable business model; and find a solution to the ever increasing shortage of skilled labour –which is an issue not only in Germany but all over Europe,” reports Ekkehard. “These are all huge challenges, which is why we decided to invest in solutions that will help us cope with these topics going forward.”
Ekkehard continues: “From our longterm analysis, we identified that we needed to invest in not only having more stock, but just as importantly to handle this stock in a more efficient manner, whilst reducing our ecological footprint. This means becoming less dependent on external energy supply and investing in reorganising and automating our processes, so we need less working effort and less labour per tonnes of goods received, picking lines picked and tonnes of good shipped out to our customers.”
With all this in mind, Fastbolt has decided to invest in building the next phase of its warehouse extensions, which it internally refers to as ‘Hall 4’. “When
it comes to increasing stockholding and planning for future requirements, it was obvious we needed to create more space and pallet locations,” states Ekkehard. “This new ‘Hall 4’, which we will start construction on in autumn, will accommodate some additional racking for stock and will be the new home for our entire packaging department.”
By moving the packaging department into the new ‘Hall 4’, it will free up space for a new modern automated compact bin storage system, the Jungheinrich PowerCube. “This is a very new technology from Jungheinrich AG and we will be one of the first customers to get this new system – which will start being installed at the end of 2024,” mentions Ekkehard. “Due to the process of building the new ‘Hall 4’, and then moving the packaging department to the new hall, we have to wait to start the process, but we are very excited.”
The Jungheinrich PowerCube system consists of storage bins that are moved
around via automatic shuttles, which work underneath the bin stacks. Based on a grid system, the shuttles can move in two directions and will enable the order picking of smaller parts and items. “Initially this system will be equipped with five shuttles, transporting the requested bins to and from three workstations,” highlights Ekkehard. “This will help us to stock and pick more efficiently, especially when it comes to the smaller quantities. It will also mean we need significantly less
space for a similar amount of stock if we used standard racking.”
Ekkehard adds: “The reason we chose the Jungheinrich PowerCube is it can be easily introduced to our existing warehouse system, and it is also very easy to increase the system’s capacity to meet our needs and our space availability. Initially we will start with almost 20,000 bin locations, which are dividable bins – meaning two separate compartments can be created. To add more capacity,
…Fastbolt has decided to invest in building the next phase of its warehouse extensions… as well as a new modern automated compact bin storage system, the Jungheinrich PowerCube.”
we either add more bins to stock more products or we can add more shuttles to increase the efficiency and boost the performance of the system.”
The new system will mark a big shift in Fastbolt’s intra-logistics and will enable it to further grow its product range, as well as operate more efficiently – especially when it comes to smaller stock and pick quantities. “It is undoubtedly a big investment and step for us as a business, but we are convinced we have a good solution and partner for the project. We are already planning the integration process and how it will fit into our existing warehouse management system – to make sure we can stock and pick products as efficiently as possible,” explains Ekkehard.
Alongside its intra-logistics investment, Fastbolt is also looking to continue to invest in further expansions to its product portfolio. “Over the last two years we have invested in increasing our product range, which did make our current space constraints even more of a challenge and was an important factor in the new hall and Jungheinrich PowerCube system,” mentions Ekkehard. “However, we believe the strategic expansion of our product range is crucial in the future success of the business. A prime example is the addition of new stock items for our nuts range, which we have added over recent years. We have received very positive feedback from customers on these new lines and some customers have changed the way they look at our range of nuts and the competence we can offer in this product field.”
To take the right decision regarding what products to added to its portfolio, Fastbolt has established a new role within the business – a product range manager. “We filled this position internally with
somebody who has been at the company for many years and knows the business, the customers, and the market, which has helped them within the role to focus on allocating areas for promising range extensions – whether it be new items, new sizes or new coatings,” explains Ekkehard. “A fundamental part of this role is the continuous monitoring and analysis of the existing range, not only for potential range extensions, but also to propose taking out some sizes or products that might not be selling as well.”
Ekkehard continues: “We sell our products to customers all over Europe and believe systematic expansion of our product range is fundamental to our ongoing sustainable growth as a business.
To meet the growth plans we have for our product range, we feel an analytical approach is a must and having only introduced the position a few months ago, we are already seeing a whole series of ‘high potential’ products for which it would be good for us to start stocking.”
Whilst Fastbolt is determined to expand its product portfolio, Ekkehard is clear the company will not become a full range provider. “With our business model we cannot and will not become a
full range provider, this is not possible for us. However, we will continue to focus on selected product families and develop areas where we see opportunities. We are currently selling 9,000 stock items and our plan is to grow our range to a level between 13,000 – 15,000 stock items in the future.”
He adds: “The fact we focus on selected product types gives us real strength when it comes to partnering with our customers. The selected range strategy is a selling point to our customers as they know the product areas we focus on and that we offer range competence, the required volume, competitive prices, and we have the know-how to ensure consistent product quality – all supported by first class customer support, as well as a range of additional services.”
From its three warehouses within Portugal, the UK, and Germany, Fastbolt can provide a wide range of services including a variety of logistics solutions, plus packaging and labelling options, direct containers, as well as digital supply solutions – including its popular fully integrated FBonline eCommerce platform (pictured left).
“FBonline has become a key service that keeps growing and is available to all our customers,” points out Ekkehard. “By using FBonline, customers can check our current stock and our future stock; place orders and work with their own item numbers; as well as upload Microsoft
The fact we focus on selected product types gives us real strength when it comes to partnering with our customers.”
Excel spreadsheets with hundreds of line items. They can even negotiate high value items or bundles of order lines and directly negotiate with the system in ‘real time’ without waiting for a reply.”
Fastbolt is able to continuously update and add features to its FBonline system thanks to its team of in-house programmers. “A big project the team has recently been working on is opening up FBonline to our suppliers,” highlights Ekkehard. “So far FBonline has been focused on the sales process to our customers, but through this new update suppliers can also now use the portal, see our demands and upload their quotes.”
Ekkehard continues: “To go up stream to the manufacturers enables us to place POs with less effort and also get a response from our suppliers quicker. It means we are a lot closer to the actual market and also the demand trends.”
The final aspect of Fastbolt’s business development is its commitment to a more sustainable business model, which has seen the company make several key investments. “Sustainability has become a key element of strategic business planning, with customers asking for our plans and steps regarding sustainability, along with regulation measures that will also have a major impact,” mentions Ekkehard. “That is why for this particular area we have created a permanent project team, called FBsave, who assess all the
sustainability topics and how to reflect the growing importance of sustainability within our business.”
Fastbolt has already invested in several areas of the company when it comes to sustainability, such as increasing the energy efficiency in its main German warehouse, as well as looking to reduce CO 2 emissions. Fastbolt has also invested in and equipped the first section of its warehouse roof with a solar panel installation, which is helping the company start the process of becoming even more self-sufficient.
“A major topic related to sustainability that all fastener importers will have to handle going forward is the Carbon Border Adjustment Mechanism (CBAM) regulation,” points out Ekkehard. “Whilst there might not be any cost implications until 2026, and there are still some details of CBAM we do not know, one thing is for sure – it will have a big impact on the market and will be a big challenge for all European importers.”
He adds: “Whilst most companies will agree with the reasoning behind its introduction, it will provide another aspect of complexity within the fastener sector and for our business. At Fastbolt we have a permanent presence on the supply side, which means we have strong exposure to the suppliers. This enables us to understand and handle requirements such as sustainability and regulations like CBAM, certainly much better than a company that simply orders from
whichever manufacturer happens to offer the lowest price. Once again, our FBsave project team will be working on this topic and ensuring we are meeting all the necessary requirements.”
With the steps it has taken, Fastbolt has positioned itself to go on meeting the needs of its customers, whilst also preparing for future challenges, which Ekkehard believes is key in meeting long-term strategic targets. “As a business our focus for the remainder of this year will be handling the adjustments within the market, and the overstocking, as we get back to ‘normal’ again. However, it is vital that during this period we do not slow down on the strategic and long-term development of the company, and we should not slow down on solutions for the future needs of a modern distributor. We cannot lose sight of the big picture of where we believe the market will go; the challenges we will face; and what our own specific solutions will be. The flexibility to adapt to the situation, but still follow our own strategic path, is the key for us as a business after such a turbulent time.”
He concludes: “Fastbolt will continue to focus on finding creative solutions to all of these challenges and ensure we are flexible in providing products and services to customers, supported by strong and powerful teams within each department, which enables us to create a high-level of customer service.”
www.fastbolt.com
On 7 th June the European Fastener Distributor Association (EFDA) held a special webinar for its national member associations, which included a presentation from Andreas Schneider, of StahlmarktConsult, entitled: ‘CBAM and fasteners – what do European importers need to prepare for?’.
With over 70 attendees, from the national member associations, joining the webinar, there was a clear interest in what Andreas Schneider – who has over 30 years of experience as an economist on the steel and raw material markets – had to say about the impact of CBAM.
The Carbon Border Adjustment Mechanism (CBAM) has certainty caused a lot of concern within the fastener industry since fasteners were included within the scope of the provisional agreement. The basic approach of CBAM is that when goods from third countries are imported into the
EU, they should bear a levy equal to the CO 2 costs of EU manufacturers.
Within his presentation, Andreas explained that it has taken a long time for CBAM to be introduced, but the formal adoption by the European Parliament was confirmed on 18th April 2023 and the CBAM regulation was published in the Official Journal on 16th May 2023 (L130/52). The CBAM regulation will concern imports originating from third countries into the EU, with the exception of Iceland, Norway, Liechtenstein and Switzerland. “The decisive factor is the origin of the goods,” highlighted Andreas. “If the goods are produced in third party countries and then exported via Switzerland into the EU, for example, the CBAM obligations will be fully enforced.”
The official start of the transition phase is January 2024, but there are some reporting obligations that will relate to Q4 of 2023.”
WE BELIEVE IN THE CAPABILITIES OF OUR EMPLOYEES TO SET HIGHEST STANDARDS AND TAKE OUR CUSTOMER-ORIENTED PERFORMANCE TO A NEW LEVEL THROUGH DIGITALIZATION AND TECHNOLOGY.
PUEHL A FAMILY BUSINESS 4.0
Andreas also pointed out that there is an option in the regulation that in the future, if a third country has a CO 2 pricing system that is comparable to the EU system, then that country might be exempted, which could be relevant for the UK. “As far as I know, the UK has only just started consultation in March regarding a similar regulation, so it is unclear whether they would be exempted in the future,” mentioned Andreas.
He also wanted to make it clear that CBAM does not involve all goods, only those listed in Annex 1 of the CBAM regulation. This includes products defined by CN codes of foreign trade statistics, such as cement, electrical energy, fertilsiers, hydrogen, aluminium, iron and steel (except ferro-alloys and scrap), as well as certain products made of iron and steel, including all fasteners (both carbon steel and stainless steel) listed under CN code 7318.
Andreas also made it clear that there is a clear political will within the European Commission to expand the number of goods covered by the regulation in the future, but it would not be before 2026/27.
Next up Andreas explained that CBAM will be implemented in two stages – the transition phase and the implementation phase. “The transition phase is primarily looking to set-up the whole system; to create the necessary authorities; and to start collecting the data – helping make the process clear to all the market participants,” explained Andreas. “The official start of the transition phase is January 2024, but there are some reporting obligations that will relate to Q4 of 2023. However, there will be no financial obligations during this transition phase.”
The full implementation phase of CBAM starts in 2026, at which point companies will need to comply with all obligations regarding registration, reporting and compliance, as they will become compulsory.
Andreas highlighted that importers – who import goods during any given quarter after 1 st October 2023 – will need to submit a CBAM report to the European Commission, no later than one month after the end of the quarter in question. “For instance, for the fourth quarter of 2023, importers will need to submit a report no later than 31 st January 2024.”
When it came to what needs to be included in the CBAM report, Andreas was clear that it is only parts (a) and (b) that were relevant to the fastener sector. “For the report you need to include part (a), which is the total quantity of each type of goods in tonnes, specified for each installation producing the goods in the country of origin. This means it is not enough to just mention the producer, you need to mention each installation where the goods are produced.”
When asked to clarify what installation meant, Andreas said his understanding was that it would relate to each factory or plant a single company had to produce fasteners. “The term ‘installation’ in the regulation, I believe, relates to every plant/factory where a product is produced. So, if there are several plants on one site then I believe you would have to report data for each plant on that site – not just for the one location – as the emission data for each plant might differ. However, this is not 100% clear and needs to be clarified.”
Another aspect of the report that importers will need to include is part (b), which is the actual total embedded emissions, expressed in tonnes of CO 2 , per tonne of each type of good.
There are two other aspects of the report that Andreas pointed out do not relate to fastener products. Firstly, the indirect emissions aspect, as there is an exemption for steel products, and the other aspect is carbon price due in the country of origin for the embedded emissions, which doesn’t apply as there is no common carbon price in any country.
When it came to working out how emissions are defined for producing fasteners, Andreas referred to Annex 4 of the CBAM regulation, which says steel and steel products are classed as ‘complex goods’ and for these products emissions are defined as two components – attributed emissions (caused directly by the production process) and embedded emissions (the input materials consumed in the production process).
“For both components, only emissions within the system boundaries are to be considered, which is not so easy to define when it comes to fasteners and the production of steel,” mentioned Andreas. “For example, you have coke, iron ore, and other elements, that go into the production of steel. This is why defining system boundaries of the production process is one of the main tasks of the coming implementing acts, as it is still not clear.”
“For fasteners, the focus will be on the CO 2 emissions from the fastener production itself and from the production of steel used for producing the fasteners,” clarified Andreas. “However, there are a lot of detailed questions that have still not been answered, which is why in the CBAM regulation the European Commission has been empowered to adapt implementing acts with further details, especially the information to be reported; the format of the reporting; as well as detailed information of emissions per country and for the different goods.”
He added: “There is still a lot of missing details and a lot of implementing acts that need to be published. Hopefully these will come by Q3 of 2023, but until then there are still many questions that need to be answered or explained.”
Whilst importers have until 2026 before the implementation phase begins, Andreas was clear that companies need to
…if there are several plants on one site then I believe you would have to report data for each plant on that site – not just for the one location…”
start working on defining roles within businesses when it comes to CBAM, especially with the transition phase starting in the third quarter of 2023. “It is essential that importers define the responsibilities within their company, as there will be several implementing acts with further details being introduced in the coming months,” highlighted Andreas. “These need to be followed closely for any potential impacts on your company.”
He continued: “There also needs to be somebody who takes over the internal coordination and checking of the progress when it comes to CBAM reporting. As of 1 st October companies are going to need to record the CBAM related goods they receive, which will need to be divided into CN codes, country of origin and by each manufacturing plant for each supplier. This might not prove easy to begin with, so planning now is essential. You will also need to be in touch with your suppliers and understand what information they already have available regarding their carbon footprint.”
Potential hurdles for companies when it comes to reporting the data is the difficulty in reporting the emissions values. “There is no standard method for calculating the carbon emissions either in the manufacturing of steel or in the manufacturing of fasteners,” explained Andreas. “Therefore, in most cases, there will not be exact data immediately. There will also be large variances between different companies and different factories of individual companies. Another factor is when it comes to the steel for fasteners, this can be made via a blast furnace or electric arc furnace – both routes are possible and the carbon footprint of each differs widely.”
One option that Andreas highlighted is for importers to wait for more implementation acts to be published, as this might provide standard values – making it a lot easier for companies, as they do not need to collect emissions data for each of their products, which could prove extremely time consuming. “The potential issue with waiting for the standard values is how they will be calculated and set,” warned Andreas. “CBAM was planned only for products that are participating in the European Emission Trading System, which is true for steel but not for fasteners. This means all the products already in the European Emission Trading System will have default values, but fasteners will not – so they still need to be established, which will not be an easy task and could lead to inaccurate default values.”
Andreas underlined that if the CBAM regulation is not followed then there are penalties that can be enforced from
2026. “In case of missing, incomplete or incorrect CBAM reports, the importer will be asked to correct them,” mentioned Andreas. “However, if the necessary steps to correct CBAM reports are not taken, or importers have failed to comply with the obligation to submit a report, the competent national authority should impose an ‘effective, proportionate and dissuasive penalty on the importer’. Whilst the amount of fine has not been determined yet, this wording within the regulation would suggest the penalty will not be a small amount.”
For the next part of his presentation Andreas talked through the steps involved during the implementation phase – including becoming a registered and authorised ‘declarant’; the need to purchase CBAM certificates in advance and how they will work; the reporting of CBAM declarations to the CBAM registry; the need to ensure the reported emissions are verified by an accredited verifier; as well as the determination of these emission values and how the preference is for third party manufacturers to register in the CBAM registry – inputting their own verified emissions data, which can then be used by accredited CBAM registrants.
“The full implementation phase may seem far away, but the transition phase starts in October and there will be a lot of implementing acts introduced and details confirmed over the coming months and years, so companies need to focus on this now,” stated Andreas. “CBAM is not just ‘another levy’. It will lead to massive changes in importing for all involved, which is why companies need to start focusing on it today.”
www.efda-fastenerdistributors.org
CBAM is not just ‘another levy’. It will lead to massive changes in importing for all involved, which is why companies need to start focusing on it today.”
Here we speak to Magnus Karlsson, vice-president global business development at Titgemeyer, about how the group has looked to develop its value proposition through a targeted acquisition strategy and a commitment to meeting the ongoing needs and challenges of its customers.
Titgemeyer Group is steeped in history and a leader within fastening technology. Can you give an overview of the group and its structure, as well as the different fastening elements it is able to develop, manufacture and sell?
“As a manufacturer with over 700 employees, at 16 individual sites across Europe, we offer a wide range of innovative products, including the market leading Starlock® push-on fasteners, one of the world’s widest range of circlips and retaining rings, as well as high performing lockbolts, plus several other fastening components and adapted assembly systems.
We have developed this product portfolio by strategically acquiring companies that bring extended and supplementary solutions to the portfolio – enabling us to offer a comprehensive range of new product categories to our customers.
For instance, in 2019 we acquired Cirteq, one of the world’s leading manufacturers of circlips, and before that we acquired Baker & Finnemore, the original manufacturer of the Starlock® push-on fastener. We also added the fastening assembly technology manufacturer Rivetec, which recently has been rebranded as Titgemeyer Tools & Automation.
These strategic acquisitions have created a number of synergies that have strengthened us in the marketplace, such as an expanded fastening technology expertise; a much broader customer platform; and a more flexible production capacity.
This is evident at our production site in Glusburn, UK, where we have combined the production of the Starlock the range of circlip products, which has created many synergies and made us a lot more flexible with our production and capabilities.
Other production sites include another facility based in Tipton, UK, which produces our range of lockbolts.
We also have more production sites in Germany that focus on non-fastener related production, as well as our site in the Czech Republic that includes our
high-end engineering team that focuses on assembly tools and automation systems.
A key benefit of these European production sites is that it enables us to have the whole production process in our own hands –for instance we have our own tool shop. Individual tools enable us to create bespoke Starlock® and circlip designs for the most complex and demanding applications. The tooling is often where the knowledge lies within a product, so having this capability inhouse is very important to us.
In addition to our manufacturing capabilities, we also have sales subsidiaries that cover almost every European country. This includes our Austrian sales subsidiary that covers Austria, Croatia, Hungary and Slovenia – with relevant languages spoken by the team; a subsidiary in Denmark, which has branches in Sweden and a newly opened branch in Finland – helping us cover the entire Scandinavian market; a Polish subsidiary that is responsible for the Polish and Baltic markets; a Turkish subsidiary that covers the Turkish and Arabian markets; as well as subsidiaries in the Czech Republic, France, the Netherlands and the UK. The rest of the European countries and the global markets are covered by our international sales department at our headquarters in
“We have a very strong brand and foothold in Europe and one of our main goals is to continue building on this legacy as a manufacturer, by unifying our operations and leveraging
including the extended solutions added from our acquisitions and to capitalise on the synergies that it brings. With these strategic initiatives, and our strengthened position as a manufacturer, we also see tremendous opportunities to expand our presence in the global market, growing with both current and new customers.
In fact, with increased international initiatives, we are thrilled to be witnessing a growing demand from the regions of North America and Asia. We see great potential for our solutions in these regions, due to their significant market volumes, and we are excited about the opportunities they present.
For every market, what enables us to stand out is that we are able to offer an extensive expertise within our field –in combination with some unrivalled fastening technology solutions – tailored to meet tomorrow’s challenges and trends.
A good example of what makes us stand out is our unique ‘one stop shop’ solution, offering both our type of fasteners, together with installation solutions that can optimise and automate assembly processes. This full solution is a major opportunity for customers to save costs, reduce risks and will also help meet potential future challenges with the lack of skilled workers on the assembly line, as well as capacity fluctuations and improving the quality of the installation.”
“Innovation is definitely of a strategic importance for us. By continuously inspiring customers with innovative solutions, as well as working close together with their R&D and design engineers in developing smart solutions, we can stay ahead of the game.
In fact, one of our success factors of us going to visit customers is that we are able to inspire them with innovation examples. We do not just visit companies with a catalogue and say ‘this is what we manufacture’. We explain to them that whilst some fasteners might be commodity products, what we supply at Titgemeyer goes beyond. We offer both standard fasteners and innovative, tailored solutions that are constantly updated to meet the specific needs of our customers.
A prime example is our range of newly innovated installation tools – the RL-2 Series – which were present on our stand at Fastener Fair Global. These are improved installation tools for blind rivets and blind rivet nuts, as well as lockbolts, that can be used for a broad range of applications – providing a higher pulling force, faster installation speeds and improved handling.
At Titgemeyer we are also able to work with customers to provide solutions to the changing demands of different markets. For instance, with the EV transition within the automotive sector over the last couple of years, manufacturers had to lower the weight of the vehicles, with one option being the decreasing of
some steel shaft dimensions within the vehicle. However, a smaller shaft dimension, with a harder surface, makes it more difficult to find the friction required to keep the fasteners in place. With that in mind, we worked on a new design of the Starlock®, which still works on the same principle – providing all the same benefits – but has been redesigned to include a more aggressive contact point when compared to the original Starlock®. This increases the pull off force in some cases – with almost four times the strength. This is only one example where we
…with increased international initiatives, we are thrilled to be witnessing a growing demand from the regions of North America and Asia.”The RL-2 series Titgemeyer’s headquarters in Osnabrück, Germany
can help our customers meet their specific challenges within the automotive market, whilst still ensuring safe connections.
Another good example is when it comes to the standard lockbolt, which includes a pin and collar to be securely pressed together. At Titgemeyer we have introduced the next generation of that system called the DeltaBolt®, which keeps the same principles, but by changing some of the designs, we have been able to increase the tensile strength by up to 50% in some cases –compared to the standard lockbolt.
Thanks to the knowledge and experience within our team, especially spearheaded with our application engineers, we can inspire and provide these types of solutions and help customers meet the challenges and trends of the markets.”
“As I see it, in addition to the global political dynamics, one of the biggest challenges is to continuously develop, communicate and leverage our expertise in developing smart solutions with a lower total cost for the applications – ensuring that we always stay at the forefront of this as a European manufacturer, no matter where the customers are in the world.
Our aim is to continue to provide this substantial value of expertise within our field, positioning ourselves as the preferred choice over manufacturers of commodity fasteners in low cost countries. For this purpose, we are investing heavily in new ways of developing and communicating our fastening technology expertise – through new and improved digital training and communication platforms. One example of this is our in-house video studio – that takes both our internal,
as well as external training, demonstrations and communication to another level of learning and understanding.
In regard to future opportunities, in my role I am actively exploring new markets, identifying trends and spearheading strategic initiatives that will have a significant impact on the overall direction and growth of the organisation.
The current world situation has made this very challenging, as mid and long-term planning and investments are no longer as straight forward as they used to be. As the business landscape has become more and more complex, and less predictable, I believe it needs an even higher level of adaptability and agility, to meet rapid changing needs. In light of this, I am a strong advocate for digitalisation, as a real game changing opportunity. Digitalisation empowers us to gain instant
Our aim is to continue to provide this substantial value of expertise within our field, positioning ourselves as the preferred choice…”
A Perry, a fourth generation family owned business – and a leading supplier of agricultural and architectural ironmongery, threaded bar, and fixings – recently hosted its Perry Open Day 2023. Here Assistant Editor Becca England reports on what proved to be hugely successful and insightful event.
Held from 6 th – 7 th June, the Perry Open Day welcomed over 100 customers and featured an array of product launches, networking opportunities, as well as underlining the company’s key capabilities and recent innovations – such as the exciting launch of Perry Fixings’ newly expanded product range, alongside its new sustainable packaging.
Officially released 1 st July, the Perry Fixing range has been expanded to include a variety of screws, nails, anchors, bolts, nuts and washers – enabling A Perry to offer more alternatives and solutions, especially in the agricultural sector.
Another significant attraction was the new eco-friendly packaging, including the Retail Friendly Shelf Box, the Retail Friendly Hanging Box, the Retail Friendly Shelf Tub, and the Retail Friendly Assortment Pack, which were on display for all visitors to have a first glimpse. In-line with A Perry Ltd’s ambition to be more sustainable, the new packaging aims to reduce the usage of plastic packaging by replacing it with a more environmentally friendly alternative. Notably, A Perry highlights that the eco-friendly packaged hardware range was recently “highly commended” during the DIY Week Sustainability of the Year Award 2023.
When asked how visitors reacted to the new range, Steve Perry, marketing director at A Perry, said: “A huge amount of interest was shown, people were excited by the benefits of both the new eco hardware packaging and in our Perry Fixing range. They loved that it was new and different to what’s out there, and could easily see the benefits – which we would have struggled to show as clearly without having the full displays on show.”
Guests were also offered the opportunity to experience a tour of the grounds, in which two showrooms had been constructed to demonstrate the full capabilities of A Perry’s portfolio, including its capabilities in equestrian and agricultural products, as well as garden art. The tour then continued to the production warehouse, where the company manufacturers threaded bars, fixings and other products in-house. The second warehouse demonstrated A Perry’s use of automation, where a warehouse management system had been implemented to increase productivity in component packaging processes.
A highlight of the event was the presence of the Mayor of Sandwell, who attended the occasion and emphasised A Perry’s contribution to the local community and economy. The
Perry Open Day also successfully fostered an atmosphere of collaboration, bringing together like minded individuals invested in the construction, DIY and retail sectors.
“The event provided a unique platform for us to strengthen our relationships with customers and prospects, resulting in expanded business opportunities and fruitful collaborations. Attendees had the exclusive opportunity to engage in one-on-one discussions with their dedicated account managers, exploring ways to enhance business growth and foster long-term partnerships,” highlighted A Perry.
“We are overwhelmed by the tremendous success of the Open Day,” added Steve. “The event not only showcased our commitment to providing innovative and sustainable solutions, but also allowed us to connect with our valued customers on a deeper level. We are excited about the new relationships forged during the event and look forward to continuing our journey of success together.”
As part of its ongoing commitment to excellence, A Perry stated that it plans to build upon the success of the Perry Open Day and continue providing unparalleled products and services to its customers. The company remains dedicated to delivering high-quality solutions, fostering sustainable practices, and nurturing lasting partnerships within the industry.
The past few years have been pivotal for corporate sustainability, the topic has firmly established itself high on the agenda of many businesses – even against the backdrop of a turbulent economy and cost of living crisis.
The UN climate conference in Glasgow, UK, in December 2021, was a major milestone. For the first time, the business community was at the table of global climate change negotiations and announced major commitments for emissions reduction. In 2022 and 2023, we have seen adoption of regulation aimed at improving and standardising sustainability reporting and tackling greenwashing. In addition, companies are getting to grips with their emissions reduction agenda and the transition to a low carbon economy.
Companies have different reasons for focusing on sustainability, but many are driven by a combination of three trends:
• Stakeholders such as customers, employees and communities are becoming more aware of the importance of sustainability issues. They are increasingly demanding greater transparency and accountability from companies on these issues.
• Global governments have begun to introduce regulations and guidelines for sustainability reporting, as well as specific regulations for sustainable product design, packaging and waste management, among others.
Whether you’re a customer in need of specific fastening solutions or an industry professional seeking insights, our video library is tailored to meet your needs.
Ever wondered what a Self Clinch Fastener looks like cut in half, or have you tried to visualise the appearance of a product or part when it is fully assembled?
Explore TR Fastenings’ media library for a comprehensive understanding of our wide range of fastening products and manufacturing processes. Access videos and resources tailored for engineers, designers and specifiers.
Scan QR codes for more information
TR’s Product Visualisers assist companies at the design stage. A range of options enables the user to interact with the products in a variety of ways such as assemblies, cutaways, magnification, material types and installation. It’s intuitive, clear and a great training tool too!
• There is growing evidence that companies with strong sustainability practices may be more resilient to risks and have better long-term financial performance. Investors and analysts are increasingly using environmental, social and governance (ESG) information to assess a company’s overall risk and potential return.
Corporate sustainability refers to how a company manages environmental, social and governance topics. Environmental criteria considers how a company performs as a steward of nature. Social criteria examines how it manages relationships with employees, suppliers, customers and the communities where it operates. Governance deals with a company’s leadership, executive pay, internal control and shareholder rights.
Sustainability is not a new topic for the business community. Many companies already have initiatives in place to reduce CO 2 emissions, for example, or to use raw materials more efficiently. Packaging has been an increasing focus for companies in manufacturing, logistics, wholesale, and retail. With companies looking into the possibilities for packaging solutions with a lower environmental footprint. This can include switching to more sustainable materials (e.g paper instead of plastics), using recycled content, and developing business models for multiple use or even packaging as a service.
These initiatives are important, and many are delivering a positive impact. However, what many companies lack is a systematic and strategic approach to their sustainability agenda. Consequently, sustainability initiatives remain fragmented, piecemeal and progress is not measured. As a result, people may question their relevance to the business.
Over the past few years, however, many companies have come to realise that sustainability is, quite literally, about the ability to ‘sustain’ their business activities in the future. It addresses real and increasingly urgent risks and opportunities that can have a material impact on a company’s operations.
A robust sustainability strategy mitigates negative impacts of the business activities on society or the environment that, if left unchecked, could come back to bite. Think about resource depletion that will damage a company’s ability to source the materials that it needs. Equally, it anticipates and manages risks and opportunities that developments in society and the environment present to the business. Risks may include disruption of company operations due to climate related extreme weather events, while the transition to a low carbon economy presents opportunities for new products and services.
In short, sustainability has become a strategic topic that can make or break the commercial success of a business. With this, its scope has broadened significantly. Sustainability is now about much more than reducing GHG emissions or tackling plastic waste. There is a whole range of environmental, social and governance issues that could affect – positively or negatively – the success of a company
in the medium term. In fact, the new European Corporate Sustainability Reporting Directive (CSRD) lists almost 100 sustainability topics, sub-topics, and sub-sub-topics, that companies should consider in their sustainability strategy – ranging from biodiversity to human rights, soil health, anti-corruption and social inclusion. The sector and place in the value chain are a major factor in determining which sustainability topics are most important for a company.
For manufacturers, there are important sustainability topics related to the sourcing of materials; considering the emissions, water, and resource footprint of their production; as well as labour conditions of workers in the supply chain and risks of human rights abuses, child labour or corruption.
Other sustainability topics relate to the environmental and social impacts of the manufacturing process itself and the use of the product, particularly waste and resource use. For distributors, sustainable and responsible sourcing is also an important topic, as well as the carbon footprint of logistics.
As sustainability has increasingly concrete implications for business success, companies must address it as part of their business strategy. By looking at the theme through a strategic lens, companies can determine where sustainability creates opportunities for the company, and where there are risks that it must anticipate.
A robust sustainability strategy is unique to the company and is integrated with the commercial strategy. It responds to the expectations of stakeholders and is in-line with recognised sustainability guidelines. It sets a clear ambition that recognises the scale and urgency of global sustainability challenges. It also introduces concrete actions and initiates a change in how the company operates.
With the broadening scope, increasingly commercial relevance, and high stakeholder expectations, sustainability is an increasingly complex topic for companies to tackle. Luckily, there is an increasing body of guidance and ‘best practice’ – meaning that companies that start their sustainability journey today can build on the experience of those that already have a robust sustainability strategy.
Developing a robust corporate sustainability strategy typically involves five steps:
1. Prioritise and focus on the most important sustainability topics for your business: A ‘Double Materiality’ assessment is the recognised ‘best practice’ approach for identifying the priority sustainability topics. It offers an analytical process designed to help companies assess the relative importance of environmental, social and governance and sustainability issues so they can focus company resources and disclosures on what really matters.
...what many companies lack is a systematic and strategic approach to their sustainability agenda.”
2. Measure your baseline: A robust sustainability strategy takes into account the starting point of the business, against which targets can be defined and progress can be measured. Carbon footprinting is the most common and well known example of setting a baseline. However, it is equally important to have a sound measurement of a company’s starting point on other strategic sustainability topics, be it diversity in the workforce or plastic waste generation.
3. Set targets, KPIs and measures to achieve these: Once a company has defined its strategic focus for sustainability, it needs to decide the ambition level it wants to adopt. Does it want to be leading in its sector on specific topics, or does it feel more comfortable to move with the majority of its peers? The ambition level then needs to be translated into concrete, measurable targets and KPIs, aligning with ‘best practice’ guidelines, such as the Science-Based Target Initiative (SBTi), and applicable regulation, like the EU Corporate Sustainability Reporting Directive (CSRD). With the targets in place, the company can focus on developing the plans that will help it address its strategic sustainability priorities by overcoming challenges and leveraging opportunities.
4. Define the governance of sustainability in the organisation: Setting out a clear sustainability governance process and determining appropriate resourcing of the strategy are prerequisites to the successful integration of sustainability into the business. This involves allocating responsibilities for sustainability at board level; agreeing on roles and responsibilities for strategic sustainability priority topics; and establishing internal and external reporting structures.
5. Measure and report progress: Companies can only make progress against their sustainability targets if they regularly
measure progress. Increasingly, companies decide to report on their progress externally, because of stakeholder expectations and regulatory requirements. In Europe, the EU Corporate Sustainability Reporting Directive is a game changer for corporate sustainability reporting. It will require ESG reporting on a level never seen before, capturing a whole host of companies that previously were not subject to mandatory nonfinancial reporting requirements, including public and private non-EU companies that meet certain EU presence thresholds.
Sustainability strategies in businesses have changed radically in the last five years. With the increase in stakeholder expectations and regulation, companies are now finding that a robust sustainability strategy is critical for their business. Starting a sustainability strategy journey may be daunting, but companies can build on decades of experience, and an increasing body of expertise, highlighting how sustainability can contribute to a company’s success.
Simply Sustainable is an award-winning ESG and sustainability consultancy, with offices in the UK and the Netherlands, focussed on delivering ambitious but achievable sustainability strategies, reporting and communications, as well as climate, carbon and net zero plans for our broad range of clients. As a recognised thought leader, the company’s highly qualified and experienced consultants provide tailored sustainability services, as well as deep expertise.
Working across all sectors and through holistic, reliable and innovative methodologies, Simply Sustainable seeks to understand a business, its people, its stakeholders, and ultimately, its impact. We help navigate the demands of ever evolving regulations, changing demographics, and provide intuitive insights and resilient solutions that create advantages for both business and society.
www.simplysustainable.com
With the increase in stakeholder expectations and regulation, companies are now finding that a robust sustainability strategy is critical for their business.”
Brugola OEB Industriale SpA is renowned within the fastener industry as a leading Italian manufacturer and for the invention of the
Once again, the company is at the forefront of the market, this time regarding sustainability. Here we speak to President Jody Brugola about the steps the business has taken in regards to sustainability and what it has planned for the future.
What does the word ‘sustainability’ mean to your business? What strategy and goals have you set yourself as a company?
“Put simply, sustainability is a fundamental part of our business and we try to support it every day – from big projects dedicated to the protection of the environment to the little actions that all employees can do at work.
That is why we have developed a concrete integrated sustainability strategy – with the aim of reaching carbon neutrality by 2035. Also, thanks to our partnership with Forever Bambù – the leading company in Europe for the planting of giant bamboo – we are looking to obtain a 70% reduction in emissions by 2030.”
“Our sustainability strategy was launched in 2019 and started by us replacing 25 tonnes of paper reels with eco-sustainable and reusable technical cloths, with an 80% reduction of paper. Moreover, we also aimed to recover 100 tonnes of oil derived from the production process of the screws, reducing the use of oils by 15%.
Another project involves us obtaining an efficiency increase in the production of compressed air – through the installation of new inverter compressors in the OEB1 plant, which allows very high energy savings (-40% on consumption for the production of air).
Other projects referenced our usage of plastic and saw us cut out consumption of plastic from 207 tonnes to 50 tonnes, two-thirds of which is regenerated plastic. Lastly, we are
implementing LED lighting in rooms, offices and production plants to decrease electricity consumption and mitigate CO 2 emissions.
In 2021, we also positioned ourselves as a pioneer of sustainability with support for the project to create new giant bamboo forests in Italy with Forever Bambù. Brugola has become an ambassador for sustainability of the Forever Zero CO 2 project, supporting three hectares of organic and symbiotic cultivation –equivalent to a certified carbon footprint mitigation of 780 tonnes of CO 2 per year until 2043. This is a multi-year project that foresees a completion with a total area of six hectares of afforestation by 2024.
We also have a set of key performance indicators (KPIs) that measure our environmental performance, which are monitored through dedicated management systems. We have been monitoring them for several years and have historical trends for these indicators.”
Since the start in 2019, the emission reduction project has gained increasing momentum leading to a decrease of around 25% in the amount of CO2 at the end of 2022.”hexagonal socket head cap screw.
Planting of Giant Bamboo in partnership with Forever Bambù
Replacing 25 tons of paper reels, with an 80% reduction of paper
Goal: Carbon neutrality 2035
Recover 100 tons of production oil, reducing the use of oils by 15%
New inverter compressors which allows -40% on consumption of energy
Implementing LED lighting to decrease electricity consumption
Use of CO2 emitted for aeroponic cultivation of fruit and vegetables
Since the start in 2019 decrease of around 25% in the amount of CO2 at the end of 2022
100 tons of oil have already been recovered in the last 12 months
“’Since the start in 2019, the emission reduction project has gained increasing momentum – leading to a decrease of around 25% in the amount of CO 2 at the end of 2022.
Furthermore, 100 tonnes of oil have already been recovered in the last 12 months, representing half of the oil used in production. The company is aiming to reach 70% by further optimising the six in-house heat treatment lines, which has already made it possible to reduce gas consumption by 8% and at the same time reduced the consumption of waste oils by 32%. Thanks to the new compressors and LEDs, energy efficiency interventions have also been made, reducing electricity consumption by 7%.
In the main plant, we have also planned a new way of recovering the heat generated by the compressors, which is now no longer dispersed into the environment but recovered to be used for heating the plant.
By investing in these sustainability projects, we can promote resource efficiency, reduce waste and optimise the use of raw materials. This can result in significant long-term economic savings for the business.
Investing in sustainability projects also reflects our commitment to corporate social responsibility, promoting consumer trust, and creating a positive impact on the communities in which they operate.”
“The automotive sector, in which we operate, has become increasingly demanding towards its supply chain. Brugola has been accredited to environmental certifications since 2004, which were previously considered ‘nice to have’ for requests. However, they have now become essential requirements if you are to be a supplier to major players in the automotive market. The reason for this is some of the companies in the automotive sector assign a kind of rating to businesses that demonstrate strength, attentiveness and performance in environmental, social and governance aspects.
As a business we also expect our supply chain to be sustainable. It is important that when we ask them for what our
customers request, they are able to respond positively – whether that is regarding environmental certifications, sustainability or corporate social responsibility.”
“Our goal is to decrease our CO 2 emission by 70%, by 2030, and we are aiming for zero emissions by 2035. To achieve these goals we will continue the Forever Bambu’s project with the purchase of two more hectares of giant bamboo forests for CO2 compensation in 2024.
We are also working on an aeroponic cultivation project, which would allow us to use CO 2 emitted by our production process to be used in the cultivation of fruit and vegetables, which would then be used in the Brugola canteen.
To add to this, we will also continue with our internal activities to reduce CO 2 emissions, such as eliminating plastic and/or using regenerated plastic in the production process. We will work on soundproofing and improvements in the heat treatment department to optimise the lines and improve CO 2 emissions. Furthermore, we are studying cogeneration interventions for the simultaneous production of electricity and thermal energy.”
www.brugola.com
The automotive sector, in which we operate, has become increasingly demanding towards its supply chain.”
•
• Our head office and warehouse in Belgium are equipped with around 2,400 photovoltaic panels on the roofs, generating solar energy and creating a fully self-sufficient environment.
• We have installed LED lighting in our offices and warehouses lowering our energy consumption dramatically.
•
• Our warehouse is completely paperless and we strongly promote paperless invoicing.
• All waste is seperated from the packaging material upon arrival in our warehouses.
•
• We are making a transition in our fleet to plug-in hybrid and fully electric vehicles.
•
• pgb-Europe continues to strive towards a sustainable business model and to have a positive effect on the global environment, community and society. Will you join us?
•
More information: www.pgb-international.com
Conserving natural resources, creating value and standing up for people and society are particularly important to Böllhoff Group, which is why sustainability – in the three areas of ‘Planet’, ‘People’ and ‘Partnership’ – are an intrinsic element of its corporate strategy.
Michael W. Böllhoff and Wilhelm A. Böllhoff, managing partners at Böllhoff Group, explain: “We strive to make the corporate world behind the connections we create ever more sustainable – by constantly working on ourselves, our products, and our processes. In our ‘Planet’ area of activity, we focus on continuously reducing our carbon emissions. This means we are constantly moving towards our goal of fully carbon neutral operations by 2030 – including our direct emissions (Scope 1), as well as indirect emissions from purchased energy (Scope 2). To achieve this, we are taking specific measures at all Böllhoff locations worldwide.”
“However, today’s challenges demonstrate once again the critical importance of ‘People’ and ‘Partnership’ as the two other pillars of our sustainability strategy. The more insecure the global environment in which we operate, the more important it is to be there for one another and to take responsibility for one another. This is why we will continue to do our utmost in the future to ensure that we remain an attractive employer for our employees. We are also upholding our commitment to giving something back to society – through foundations, donation and personal engagement.”
In order to meet the sustainability aspect of its corporate strategy, Böllhoff Group has already taken several steps, including a well thought-through energy management system. “Climate change and the current energy crisis present every company with serious challenges,” states Michael W. Böllhoff. “After all, the future of the planet depends on what humanity does now and in the future – as well as what it does not do. One of the key questions for Böllhoff Group was how it could reconcile a secure and constant energy supply with the responsible use of natural resources.”
To do just that, Böllhoff used its energy management system to determine concrete savings potential, as well as continuously improve its energy efficiency. The Group also considered the source of its energy supply and is constantly expanding the proportion of regenerative energy sources in order to achieve the best balance between economy and environmental protection. “It is well known that the best energy strategy is to avoid consuming energy in the first place,” highlights Wilhelm A. Böllhoff. “Since 2015, we have operated a certified energy management system according to ISO 50001. This involves the detailed recording of energy flows and energy sources within the company. Potential savings can only be identified and realised if these parameters are known down to the last detail. Our focus is always on reducing energy consumption by increasing energy efficiency, which is why we use state of the art control technology and data acquisition systems company-wide. These help us to continuously evaluate the energy footprint of our production facilities, buildings and logistical processes – and to improve them in the long-term.”
Every day Böllhoff produces more than two million plastic fasteners in its injection moulding machines in Bielefeld, Germany. This involves many tonnes of plastic granules
…today’s challenges demonstrate once again the critical importance of ‘People’ and ‘Partnership’ as the two other pillars of our sustainability strategy.”
SCHNORR® is an international leader in engineering and producing safet y washers and disc springs for automotive, aerospace and mechanical applications
Original SCHNORR® safet y washers:
• Highly vibration-resistant
• Twofold effect from one component
• E x tensive range
Original SCHNORR® disc springs:
• Various applications
• Best price -per formance ratio
• Customized solutions
Please contac t us Together we will find your tailor-made solution.
being melted down before they can be processed in the machines – creating large amounts of waste heat – energy that the Group wants to reuse as much as possible.
That is why, in 2022, Böllhoff made plans to modify its heating system, which has led to a large proportion of the waste heat from the plastic production now being used to heat a nearby building. The company also continuously works on improving the efficiency of its machinery. At the Bielefeld site alone, Böllhoff has gradually replaced numerous hydraulic injection moulding machines with fully electric models. “Due to their design, fully electric injection moulding machines are more energy efficient than hydraulic ones,” points out Michael. “Depending on the product and its manufacturing requirements, however, 1:1 replacement is not possible with all machines.”
Regardless of the machine type, Böllhoff is also constantly auditing its production processes. In 2022, for example, the company assessed and optimised various machine parameters on its injection moulding machines; from the speed of the screw conveyor to the injection temperature. “Depending on the machine model, we achieved savings of up to 15% in electrical energy per injection moulding machine,” mentions Wilhelm. “We were also able to achieve savings in the plastic melting process in 2022 by installing highly energy efficient cylinder heating systems. As a result, energy consumption per machine fell by more than a third compared to 2021.”
In addition to improving energy efficiency, curating the energy source is a second important component of the energy management system at Böllhoff Group. The more regenerative sources the company uses, the more it reduces its carbon emission – directly and indirectly.
To take the next step, a planning project for expanding its own power generation was established in 2022 – with photovoltaic systems playing a significant role in the project. “Our goal is, by 2025, that every suitable roof at our largest German facilities in Bielefeld, Oelsnitz and Sonnewalde should be equipped with PV systems,” explains Michael. “Where we cannot cover our electricity needs with self-generated power, we increasingly rely on the purchase of electricity from renewable energies. Some locations, such as our large production site in Jundiaí, Brazil, have been using only green electricity for years. Since 1 st January 2022, this also applies to all production and logistics sites in Germany.
This domestic change alone reduces our carbon footprint by almost 4,000 tonnes of CO 2 per year.”
By having photovoltaic modules at each of Böllhoff’s production or logistics facilities in Germany – the company will start to achieve this goal in the second half of 2023. In the fourth quarter, a new photovoltaic system is to be put into operation in Sonnewalde, Brandenburg – with a total output of 500kWp. This Böllhoff site represents the core of the self-pierce rivet production for the entire Böllhoff Group. Around 2.2 billion of these fasteners are manufactured there every year – before they are used in applications such as car body construction.
“The existing photovoltaic system at our logistics site in Oelsnitz, Saxony, is also to be expanded in the second half of 2023 – from almost 100kWp to 400kWp,” reports Michael. “This will enable us to generate an even larger proportion of the electricity for our highly automated shipping processes for ourselves. This is an important investment, as Oelsnitz is our world’s largest logistics facility with a total area of over 16,000m 2 .”
Böllhoff Group is also currently working on the fifth expansion stage of its site in Wuxi, China, with the new building combining high production capacity with the concept of sustainability. Since the end of June 2022, the excavators have been working at the Böllhoff production and logistics site in Wuxi and by Q3 2023 almost 12,000m 2 of additional building space will have been created for the thread technology division.
Böllhoff has been represented in the Chinese market since 1998. In 2004, the company started its own production in Wuxi –the first Böllhoff production facility in Asia. Since then, capacity at the site has been expanded several times, most recently with the opening of a state of the art logistics centre at the beginning of 2019.
The new building will house production facilities and offices, as well as a company restaurant for almost 300 employees in Wuxi. During the planning phase, the focus was also on sustainability. For instance, the modern building complex, which is around 1.7 football pitches in size, will be heated using heat pumps. There are also plans to partially cover the site’s power requirements using an expandable photovoltaic system – with a potential output of up to 1.3MWp.
The thermal energy generated during production will be used for underfloor heating and the roof of the company restaurant will be ‘greened’ (i.e covered with plants).
Upon commissioning, Böllhoff’s production capacities in Wuxi will increase to around one billion parts per year. The location produces various fasteners for the Asian market, including RIVKLE® blind rivet nuts and screws, various threaded inserts, and fasteners made of plastic.
In order to meet the sustainability aspect of its corporate strategy, Böllhoff Group has already taken several steps...”
WASI is aware of its responsibility as a global player within the fastener industry, which is why it is always trying to find new sustainable ways to make a positive impact on the worldwide stainless fastener market – both through its internal processes, as well as regarding issues outside of trade and distribution.
One of WASI’s biggest sustainability projects was the construction of its photovoltaic system on the entire roof of its logistics building. “The installed solar panels generate 75% of our total annual electricity consumption,” points out WASI GmbH. “At peak times, the system even covers up to 100%. In addition to meeting our own needs, we are also able to offer solar panels and various roof substructures from our product portfolio to meet and satisfy the needs of today’s customers.”
When it comes to global shipping, WASI also want to try to reduce its environmental footprint. That’s why it has been an official climate protection partner of GLS since January 2022. “Through our partnership with GLS, we are able to support climate protection projects and thus compensate for our greenhouse gas emission,” explains WASI. “Of course, our goods must also arrive safely at our customers. That is why we have decided to use 100% recyclable packaging material from How2Recycle, as well as using our old packaging as a filling material. In this way, we guarantee safe transport that is also sustainable.”
Other projects that WASI has introduced include setting up charging stations for both e-cars and e-bikes –enabling its employees to travel to work
in a more environmentally friendly way. It has also implemented LED lighting and replaced energy inefficient old lighting. “It is not only our employees that are close to our hearts, but also our location and home,” underlines WASI. “Therefore, we have established several beehives, with bees able to fly around our bee meadow. A beekeeper comes by once a week to check on the bees and harvest the honey. We give away this honey as our own regional product to our customers.”
WASI concludes: “The aim of our projects is to influence both our employees and our customers, as well as the company itself. Our colleagues appreciate working in a business that is aware of environmental issues and acts accordingly. Our customers are also happy to know that their goods are delivered to them in a more sustainable way – with the environmental footprint in mind. WASI itself benefits above all from the photovoltaic system, from which we can supply ourselves to a large extent with green electricity and save immense costs.”
www.wasi.de
Here Pietro Colombo, commercial director at Colombo Special Fasteners, offers his thoughts on how, with commitment, it is possible to transition to a sustainable future, whilst handling the impactful effects produced by economic activities every day.
The planet is facing unprecedented challenges that pose a threat to the wellbeing of future generations. With a constantly changing world, the extreme events that once felt far away are now part of a new reality that we cannot turn our backs on.
Colombo Special Fasteners (CSF), a leading Italian company in the manufacture of special fasteners, takes actions every day that are aimed at generating long-term value for the company – contributing to its growth, improvement and development; the socio-economic well-being of the communities in which it operates; as well as the other players that make up its value chain.
Sustainability for CSF means the constant and concrete commitment to promote a business model aimed at the efficient and strategic management of the resources available. That is why the company’s strategy is made up of small steps that gradually contribute to integrating sustainability into the way it operates and into its habit – laying the foundations for a real transformation of the company’s culture when it comes to sustainability.
CSF has set sustainability goals that it is looking to achieve by 2025, including the completion of a new eco-friendly production site with solar panels to help meet the company’s energy needs; a centralised fume extraction system for the benefit of employees and the working environment conditions; implementation of an oil recovery and cleaning plan, as well as waste reduction; digitalisation of the production departments by completely eliminating the use of paper; and finally the promotion of good habits and responsible management of resources in each department, such as reducing water, plastic and paper consumption.
Steps the Italian company has already taken include 42% of the company’s energy needs being covered by solar panels
last year and 82% of contractors being located within a radius of 40km from the plant – creating environmentally and economically sustainable channels, as well as enhancing local businesses for mutual growth and in favour of an eco-friendly supply chain that consequently helps reduce road transport impact and times.
A series of other efforts and steps have also materialised due to CSF’s UNI EN ISO 14001:2015 certification, since 2008, which has been recognised in the implementation of the company’s policy.
A fundamental part of a good corporate culture starts with all those who form an integral part of it. Each of us, in addition to being part of a company, are part of society. The benefit of a series of sustainable actions is not only tangible in concrete aspects, such as the responsible use of resources by limiting waste, but also in other intangible aspects, such as well-being inside and outside the workplace.
The motivation of our employees is based on the harmony with the corporate objectives and values. Precisely for this reason, in small steps we promote solidarity actions that encourage them to give their best.
Another very important point to take into consideration is the possibility of
relying on a regional and national system – aimed at encouraging and facilitating innovative projects in favour of the ecological transition, with subsidised loans and grants. For instance, the new CSF plant in Cisano Bergamasco, in the north of Italy, is currently undergoing a complete makeover and by the end of the year it will be completely eco-friendly and totally Industry 4.0 compliant. CSF is also building a new heat treatment plant – following the acquisition of the heat treatment company CITT – which will also be completely Industry 4.0 compliant.
All these actions show that there is always an opportunity to contribute, we just have to find ways to do it. Even a small action can lead to a bigger goal.
www.colombofasteners.com
The motivation of our employees is based on the harmony with the corporate objectives and values. Precisely for this reason, in small steps we promote solidarity actions that encourage them to give their best.”
Owlett-Jaton, the UK’s largest wholesaler of fasteners and fixings, highlights that it was early to recognise the importance of environmental responsibility and became one of the first fastener and fixing wholesalers in the UK to be awarded environmental accreditation ISO 14001:2015.
Owlett-Jaton started the 18 month process to implement an environmental management system in 2017 and achieved accreditation in September 2019. Since becoming accredited, the company has reduced its carbon tonnage by 20% – whilst growing the business. Owlett-Jaton has also put in place KPIs, including measurement of Scope 1 and 2 emissions, water usage and waste generation. Targets are also reviewed regularly to ensure continuous improvement.
In achieving these improvements, the business has undertaken a wide range of initiatives, including sourcing all electricity from renewable sources; installing LED lighting across offices and the warehouse at its Stone site; as well as investment in lithium-ion battery powered mechanical handling equipment, which not only uses less electricity but eliminates the use of lead-acid batteries and the potential for hazardous chemical spills associated with their maintenance.
Owlett-Jaton has also introduced plug-in hybrid electric vehicles and battery electric vehicles to the company car fleet, together with the installation of on-site charging. To add to this, the consolidation of operations onto a single site has allowed the business to increase sales – whilst reducing its overall energy consumption by 20%.
Other iniatives by the company include all waste being segregated and recycled or re-used whenever possible. Plus, packaging changes have been made to improve the environmental performance of products, including all purchased cardboard packaging being fully recyclable and FSC sourced – with high recycled content; the introduction of paper gummed tape in place of polypropylene; as well as the reduction of the use of plastic packaging formats and switched to recycled materials.
Ian Doherty, chief executive at Owlett-Jaton, commented: “We are committed to sustainability and minimising the impact our activities have on the environment. Achieving ISO 14001 demonstrates our leadership in the market. Becoming more sustainable is the right thing for the planet, but I firmly believe it is the right thing for the business, our staff and our customers. We are constantly seeking ways to further reduce carbon and become more sustainable in all aspects of our operations. More and more of our customers are thinking this way too, and the requests for information and re-assurance in the extended supply chain are rapidly increasing.”
Sustainable practices are becoming more of a requirement for larger customers and Owlett-Jaton is committed to supporting these initiatives. More than ever, requests for 3 rd party audits, completed by external audit companies, are being received from customers focussing on their own environmental, social and governance (ESG) performance.
Having got its in-house initiatives in order, and in response to these increasing customer demands, Owlett-Jaton has been looking more closely at its extended supply chain – with a focus on responsible sourcing.
“Historically, supplier audits were predominantly product and quality based, they are now broader, taking into account environmental, sustainability and ethical considerations,” points out Ian. “With over 15 factories already audited in 2023, we are making significant steps to further cement our position as a leader in this area and meet the needs and expectations of our customers.”
www.owlett-jaton.com/environmental
TOGE Dübel, a German developer and manufacturer of anchoring systems – including metal anchors for the fastening of suspended ceilings, as well as insulation and fire protection panels –has ensured a short supply chain for a better environmental footprint.
For instance, all TOGE products are in-house developments and are largely produced at the company’s location in Nuremberg, Germany. When selecting suppliers and service providers, the company pays attention to long-term partnerships but also to regional proximity. TOGE already sources over 90% of the materials required for production from Germany or Europe within a maximum radius of 500km. In addition to shortening delivery times, the shorter transport routes significantly save CO 2 . TOGE plans for this to be increased to 98% in the next five years.
TOGE also attaches importance to sustainability in its energy supply. At the beginning of 2023, a photovoltaic system was installed on the roof of the company. This supplies electricity to cover TOGE’s own energy needs, with surplus electricity fed into the
local power grid. ‘Real time’ monitoring of the current performance of the photovoltaic system is available to TOGE via a website or App. For the time being, a total of 480 solar modules, with 395 watts each, have been installed. TOGE plans to double this number as soon as the energy supplier approves.
TOGE is also involving sustainability within its product development, by saving valuable resources. The company is currently working on a further line for concrete screws where a special manufacturing process enables a saving of 450kg of CO 2 per tonne produced. Here, too, production takes place on-site and the necessary components are supplied from the surrounding area. The screw will be launched on the market in Q4 of 2023 and TOGE reports it will have an ETA certification.
Here Peter Standring, technical secretary at Industrial Metalforming Technologies, looks to provide a snapshot of the current, somewhat turbulent situation within the global automotive sector and suggest how this may play out for those in the fastener industry in respect to the never-ending demand and need for vehicle sustainability.
As much as some people declaim vehicles, including their uses and users, in little over a century motorised transport has changed the world and virtually all human life. This has provided freedom for the individual; low cost transport for the public; and long/short distance carriage of commercial goods. Few of even the most outspoken voices calling for the condemnation of motorised vehicles could or would ever consider a return to the horse and cart.
Vehicle development has always transitioned between what has been technologically possible and the need for commercial viability – including Formula 1.
Can it be made cost effectively? Is it safe and reliable? Is it simple and easy to repair/replace? Will it make money? These questions and a thousand like them have been asked of automotive manufacturers since the car was invented. It is the positive answers
This type of construction was favoured by designers of passenger vehicles, providing freedom of style, improved stiffness and performance. Like the properties of an egg, the
…automotive sustainability isn’t a matter of whether you buy a polluting vehicle or not, that’s an environmental issue.”
as the regulations on emissions were lowered and also to counter the significant increase in vehicle mass – brought about over decades due to safety issues.
The development of simulation software for vehicle design had clearly demonstrated how the changes in ‘second moment of area’ (second moment of inertia in the USA) can be used to achieve significant stiffness in a vehicle structure by using selectively shaped metal sheet or tubing. Whilst the properties of all materials can be assessed/compared by subjecting them to a load versus extension test (stress/strain); in practice, the performance of any material when loaded, is determined by its shape (second moment of area) and stress/strain behaviour. This is why an apparently very thin suspension arm on a F1 racing car can function the way it does when loaded according to is design function, but will fail easily if loaded in a non-designed direction. Similar to corrugated cardboard being stiff when loaded in the direction of the corrugations, but possesses very little strength between them.
The automotive industry was able to
Clearly, in this fast flowing and ever changing world of technology, markets, and politics, the constant striving for scale of economies will produce further OEM consolidation. They will in turn, reduce the number of vehicle platforms and modules around which they build the product, whilst at the same time endeavouring to provide customised options to the purchaser.
At the turn of this century China joined the World Trade Organisation (WTO). The rest of the world, including industry, considered this would lead to stability and growth. Automotive pundits then turned to the potential for vehicle ownership inside China.
The well known table listing numbers of vehicles per thousand head of population for each major country shows the USA leading, having around 800 (0.8 per person). This raised the obvious and very serious question: ‘What if vehicle numbers in the populations of China and of course India
All mass produced vehicles are designed to be assembled in the most efficient manner. It naturally follows that were the assembly line to be reversed, all vehicles should be able to be disassembled in the same time.”
under discussion by the International Seabed Authority (ISA) and reflected in the newly agreed UN High Seas Treaty. It’s not the availability of the materials that is the problem, but the method and means by which they are obtained. Intensive suction dredging will, similar to the 19th century hydro-mining in the USA, simply wipe out the entire ecosystem.
Since mining the moon or Mars does not offer a short/medium term solution to our current extravagant waste of finite resources, perhaps ‘sensible’ recycling will?
Government regulators have little appetite to cross swords with major industrial sectors that provide significant employment and taxable income for their populations. So, as in the case of the automotive industry, when waste becomes an issue, they instruct the industry in question to sort out their own problem.
For the automotive industry, this requires them to take back the unwanted/scrapped vehicles and to ensure that the materials from which they were built are safely disposed of within the regulations. Vehicle OEMs have no financial interest in the vehicle they sold once
the vehicle all in pieces.
This image, coupled with the fact that on virtually all scrapped vehicles most parts are perfectly serviceable, suggests that maybe, someone is missing a huge trick? Rigorous quality control (zero defects), material audits and total traceability mean that nothing on a vehicle is either unknown or left to chance. All mass produced vehicles are designed to be assembled in the most efficient manner. It naturally follows that were the assembly line to be reversed, all vehicles should be able to be disassembled in the same time. Of course, this excludes the body in white where it is welded, brazed, bonded and/or riveted.
A current business model much favoured by OEMs is to lease, rather than sell the vehicle for a fixed period (terms and conditions apply). On return, the vehicle is then sent for auction or to a dealership and eventually, scrappage.
Now, assume that a vehicle manufacturer worked with their fastener specialists to develop methods of securing vehicle modules that could be disassembled on a ‘disassembly line’ post
So, the previously leased vehicle (leasing might become the only business model for the future) could be returned to the market as a fully warranted product for another lease period. Given the statistical data obtained from this new business model, it is possible that a single vehicle could be sold and resold a number of times – significantly increasing the OEM’s business.
More importantly, from a sustainability point of view, the ability to disassemble a vehicle as easily and as cost effectively as it would be to build it, would mean that at the end of life, all parts could be recovered. Given a true and factual knowledge of all component parts, a proportion of these could then be sold on by the OEM for use in other non-automotive related products, as semi-finished stock at perhaps the same purchase price as their initial purchase? The material and manufacturing costs savings on energy, CO 2 , etc, could be enormous.
The key here is recycling that pays for itself, all made possible by having the fasteners to make it happen. The saw tooth graph shown in Figure One provides a diagrammatic representation of an automotive leasing refurbishment/recycling system. Sale values are ‘A’, ‘C’, ‘E’, ‘G’ and ‘I’, the respective depreciated values at ‘B’, ‘D’, ‘F’, ‘H’ and ‘J’. In the example shown, depreciation over the leasing period is taken at 50% of the sale value. Refurbishment costs used in the model are taken as 25% of the previous selling price. Clearly, all percentages can be varied to obtain the optimum return on investment.
not one of sustainability. Despite requiring fewer components (ICE and transmission) and having a skateboard chassis, the manufacturing ‘footprint’ of electric vehicles is virtually the same as all other vehicles although the servicing is significantly less.
Tesla and other automotive manufacturers are lauding the fact that their ‘giga’ battery factories will provide a fully recyclable facility for their power units. Whilst this is encouraging, although difficult when the battery itself is designed as part of the vehicle structure, it does provide a start in the quest for vehicle sustainability.
However, at this stage, it is not unlike the introduction of lightweight aluminium spaceframe/bodied vehicles, which were developed to improve fuel efficiency and performance. This became less attractive and something of an embarrassment when it was realised that in a country the size of the USA – where vehicle ownership rated the highest in the world – initially, there were only four garages capable of effecting warranty repairs on aluminium alloy vehicles. Things did change, along with the cost of insurance (not very different to the early scrappage of crash damaged electric vehicles today).
Through involvement in this model the supply chain will share both the costs and benefits. Also, in-service life data will improve both quality and performance. Most importantly, refurbishment and recycling will create a direct benefit to encourage the design/ development of quick action fasteners for attaching/detaching both pre-assembled modules and the modules themselves. Such a model could become the ‘norm’ for other sectors that deal in manufactured goods.
The war in Ukraine introduced an energy crisis not seen since the Arab-Israeli War of 1973. Those driving electric vehicles were pleased they didn’t have internal combustion engines (ICEs) until they too realised the increase in electricity charges. At the time of writing this article, the sales of electric vehicles have slumped due presumably to the higher purchase costs over non-ICE vehicles and the inconvenience of battery charging. On the other hand, the prestige of Tesla and sales of its vehicles are increasing.
It should be recognised that in the context of this article, the purchase and use of non-ICE vehicles is an environmental choice
In many countries, legislation exists to ensure that every scrapped vehicle belongs to the OEM even though they may only make a small percentage of the whole. Over many years, the general profit margin of the OEM has averaged out at half that of their suppliers and only one third that of the dealers. Given this, it is quite astonishing that the industry has been so casual in tossing out, with little regard, what it has worked so hard to create.
Tesla has attempted to break the conventional automotive supply chain by re-energising Ford’s initial concept of vertical integration. However, this has been largely focused on digitisation, software development/application and electronic integration. For much of the rest of the vehicle, Tesla has, like all other OEMs, conventional supply chain partners.
If Elon Musk were to apply the concept of his ‘giga’ battery recycling facilities to the whole of the vehicle as proposed above, then every vehicle could have a number of affordable ‘leasing’ periods and still provide a payback at the end of life. The starting point would be a programme of discussion with fastener designers and manufacturers to create the means by which this could be made possible.
As for the sustainable future? This would involve a global automotive industry that provides safe, reliable, multi-price point vehicles through a local network, supported by regional OEM new build/disassembly plants and their satellite supply chain partners. The key, the right fasteners, in the right quantity, in the right place, at the right time. Given that, everything else is simple!
…assume that a vehicle manufacturer worked with their fastener specialists to develop methods of securing vehicle modules that could be disassembled on a ‘disassembly line’ post leasing.”
www.enkotec.com
Optimise efficiency with an automated production line, including intuitive digital manuals and advanced sensor technology, enabling fast decision making and easy troubleshooting with ENKOsmart software.
Produce sustainably with lower energy consumption, an oil-free manufacturing process, maximum wire rod utilization and minimum scrap materials.
Increase capacity with a bespoke ENKOline in-line nail production set-up, built to your needs and configured to make the most of your factory space.
For more information, contact sales@enkotec.dk
Scan or click the QR code to find your perfect configuration!
In May Fontana Gruppo hosted a Sustainability Day at its plant in Cornaredo, Milan, Italy, in order to reflect on the importance of sustainability and safety at work –enabling the company to engage with its employees and raise awareness about sustainability and best practices.
Fontana’s Sustainability Day was aimed at employees and their families and gave them the opportunity to see inside Fontana’s plants and to observe the production processes up close. It was also a chance to have fun in a specially created area that included workshops and games – focused on sustainability and safety for adults and children.
“Sustainability is not only about the environment, but also about giving attention to employees (safety, training and inclusion) and, in general, to stakeholders – combined with solid care for the social context of the territories in which our plants are situated,” explains Fontana Gruppo. “This, together with a wise corporate structure and strong business ethics, make us a world leader in this sector.”
The issue of environmental impact is certainly becoming increasingly central to all companies. In recent years, there has been a growing vision that transcends individual company efforts and is starting to encompass the entire supply chain. For this reason, Fontana Gruppo is committed to taking measures that can increasingly foster sustainability even before the formal demands come from customers.
“The industrial sector plays a crucial role in the global economy. As such, it is our responsibility in leading the transition to an increasingly sustainable economic, social and environmental model,” states Fontana. “To achieve this goal, all companies must pay close attention to the environmental impact of their products or services – through a comprehensive understanding of the entire life cycle – from raw material extraction, through production and distribution, to final disposal.”
The company adds: “Every business must also ensure that all processes involved in production are efficient, ensuring that
their products can be reused and recycled at the end of their lives. This is precisely the concept behind the circular economy, a production and consumption model that aims to close the resource extraction, use and disposal cycle; reduce the use of natural resources; and minimise waste by reusing and recycling materials.”
Fontana Gruppo explains it has been able to achieve its results within sustainability through a path of excellence that has lasted for nearly three-quarters of a century. This is based on the company’s business model, which is focused on solid values and principles of integrity, combined with a long-term vision and a great passion for building a sustainable future. For instance, all of its Italian plants have a UNI EN ISO 14001 certified environmental management system. This international standard sets and regulates the requirements for a virtuous ecological management system as a fundamental and necessary basis for building a company directed toward sustainable development.
A multinational corporation, headquartered in Veduggio con Colzano and with production and logistics locations on four continents, Fontana Gruppo also plans to increase its independence from fossil fuels and consequently reduce its carbon dioxide emissions, thanks to projects and interventions in energy self-production from renewable sources.
“With a view to the circular economy, our goal is to reuse waste from production processes for new purposes, thus avoiding the production of garbage and reducing water consumption,” highlights Fontana. “Annually, the carbon footprint is then updated, aiming to make us more aware of our environmental impact and, consequently, identify and act in areas that still need to be efficient and improved.”
The various actions that Fontana Gruppo has already carried out regarding sustainability have led to the achievement of benefits in terms of emission savings, resource use, as well as implementation of renewable energies. However, through information paths pursued with employees, a critical involvement has been obtained from the structures of all the regions in which the group operates. “Sustainability and safety have always been two indispensable pillars of our company and fundamental tools for improvement, continuity and growth,” concludes Fontana. “Values that even more today are the focus of our attention and that now constitute indispensable factors for any company intent on pursuing business objectives within a framework of corporate social responsibility.”
No matter what kind of corrosion protection you need, we have the right tool for you. Our Atotech corrosion protection solutions meet and exceed all industry requirements and cover the full spectrum of coating technologies: from pretreatment, zinc and zinc alloy plating processes, as well as zinc flake coatings to a comprehensive range of post-treatment systems with suitable coefficients of friction. The various possible combinations of our exceptional product range ensure outstanding corrosion protection with an attractive appearance and durability. Our unique products, global availability, and unsurpassed service capabilities make us a trusted partner for the fastener industry worldwide.
Learn more about our products at: www.atotech.com
For sustainability practiced, Lederer – a specialist for high-quality stainless steel fasteners, individual special and drawing parts, as well as efficient C-parts management – has now received the silver medal from EcoVadis, a provider of sustainability rankings.
Lederer attaches great importance to not only its own sustainability requirements, but those of customers worldwide. That is why the company was proud to be within the top four percent of the companies assessed by EcoVadis in the wholesale of metal and plastic goods. “We take our responsibility as a company for our impact on society, the environment, and the well-being of our employees, very seriously,” explains Dr Volker Lederer, owner and managing director at Lederer GmbH.
“At Lederer, sustainability, energy transition and climate protection are not just written words, we have been practising them for many years. As supply chains are becoming more and more complex, there are also increasingly important tasks for shaping our sustainability balance sheet. So far, our focus has been on the price, availability and quality of the products, but now ecological, ethical and social aspects are becoming more and more important.”
Volker continues: “In this year’s sustainability assessment by EcoVadis we achieved 64 points, improving by 13% compared to last year and only missing the gold medal by 3 points. Our goal for 2023 is to continue to focus even more on ecological aspects and to do even better in the sustainability assessment.”
Acting sustainably as a company has been a key policy for Lederer for many years. For instance, as a major buyer of electrical energy, Lederer switched two years ago to a provider of pure, certified green electricity. In fact, in April 2023, Lederer’s energy supplier confirmed that the electricity comes 100% from renewable energies and is 100% climate neutral, including all upstream chains. “Through climate protection projects of the green electricity label RenewablePLUS, all resulting CO₂ emissions are made climate neutral,” mentions Volker. “By switching to a provider of pure, certified green electricity, we are able to reduce our CO₂ output by almost 400,000kg annually. This year we also started to switch to hybrid and electric
vehicles, using our own charging stations to supply the vehicle fleet exclusively with electricity from renewable energy sources.”
In addition, Lederer has been part of an initial reforestation project, which has seen 500 trees planted on behalf of Lederer. “Our partner PLANT-MY-TREE® implemented these sustainable tree plantings with a planned project duration of more than 99 years in Utscheid, Rheinland-Palatinate in the southern Eifel of Germany,” points out Volker. “During this time, there will be no deforestation or economic use of the area and it is another contribution to CO₂ compensation by Lederer – helping to further protect the environment and climate.”
Lederer is also currently dealing with the topics of energy and resources, with ‘Smart Home’ solutions being considered for the offices, such as intelligent control systems to reduce energy consumption. In addition, Lederer deals intensively with heat pumps and photovoltaics. “The medium and long-term goal is to become largely independent of fossil fuels and to generate electricity for our own needs,” concludes Volker. “We do our utmost to work in a more sustainable and climate friendly way. In fact, you could say the material from which our core range of fasteners is made, stainless steel, is sustainable in itself. Stainless steel is a non-corroding material and is more durable and resistant than many other alloys. In the majority of cases there is no need for an additional galvanically applied coating to achieve the desired durability – helping to protect the environment and resources. This, and our world of values, are both an incentive and an obligation to live up to, including our responsibilities in other areas as well.”
www.lederer-world.com
As the inventor of anti-corrosion zinc flake technology, NOF Metal Coatings Group states it has always been one step ahead of the competition in supporting the development of the fastener industry – from both a technical and environmental point of view.
Since the late 1970s, with the launch of the famous DACROMET ®, fastener manufacturers have had access to a high performance, non-electrolytic anti-corrosion technology capable of solving the problem of hydrogen embrittlement for steel grades 10.9 and above. This innovation has enabled fastener manufacturers to save the large amount of energy required for hydrogen de-embrittlement of electrolytic coating solutions. At the same time, it has helped accelerate the development of high strength steel fasteners, reducing pressure on iron resources and steel production.
Improvements to NOF Metal Coatings Group’s waterborne zinc flake coating technology, driven by new environmental regulations, led to the development of GEOMET ®, which contains no form of chromium and still meets the fastener industry’s high demands for anti-corrosion performance. Since then, the company’s technology has gone from strength to strength –thanks to a wide range of customer specifications, particularly in the automotive, truck and renewable energy sectors.
NOF Metal Coatings Group’s coatings are composed of zinc and aluminium pigments dispersed in a sol-gel matrix. Thanks to their unique formulation, GEOMET ® coating systems are able to offer very high corrosion protection performance (over 2,000 hours NSS) with a limited amount of metallic pigments compared to conventional anti-corrosion coatings.
What’s more, its non-electrolytic coating process requires extremely low volumes of water and produces very little waste, bringing additional environmental benefits to the company’s
coating solutions, particularly at a time when natural resources have become even more precious than before.
“Our zinc flake coatings are among the most efficient, competitive and environmentally friendly solutions available on the market,” reports NOF Metal Coatings Group. “However, climate change has become more than just a reality, which is why our staff are committed to contributing to the development of more sustainable and industrial coating solutions.”
By pooling the strengths and minds of its multicultural research and development teams, located in Europe, Asia, and North America, NOF Metal Coatings Group’s top priority is now to further reduce its environmental footprint, with existing and new solutions.
“Four years ago, we started our first life cycle analysis with GABI, one of the most advanced software packages available on the market. Our aim was to measure and understand the various impacts of our solutions on the environment, in order to prioritise our development activities appropriately,” explains NOF Metal Coatings Group.
This initiative has already given the company a totally new perspective on its raw materials, chemistry and coating technology. “We now have the opportunity to better direct our development towards a lower environmental and CO 2 footprint, but above all towards less energy intensive processes. The teams at NOF Metal Coatings Group, enriched by the younger generation and their talents, will very soon be able to offer new, even more effective and environmentally friendly solutions for the fastener industry.”
www.nofmetalcoatings.com
Hague Fasteners, a UK manufacturer of special fasteners since 1971, has announced its commitment to sustainability in fastener manufacturing and has taken decisive action to minimise its carbon footprint and implement environmentally responsible practices.
As a responsible industry player and family business, Hague Fasteners Ltd is dedicated to mitigating the impact of its operations on the environment.
The company firmly believes in the importance of sustainable practices and aims to set an example for the fastener manufacturing industry, with a firm commitment to sustainability, as well as responsible and ethical sourcing.
Key initiatives undertaken by Hague Fasteners to reduce its carbon footprint include the ‘Hague Forest’ tree planting scheme, where the company has partnered with global reforestation projects in Madagascar and Haiti. Through this initiative, the company is planting a significant number of trees in these areas, which also bring many co-benefits such as poverty alleviation and community support. By actively contributing to these reforestation efforts, Hague Fasteners aims to offset carbon emissions, enhance biodiversity and create a greener environment for future generations.
Hague Fasteners also recognises the importance of capturing and storing carbon dioxide to combat climate change, which is why the company has invested in a Clean Development Mechanism Project and committed to offset its carbon footprint through till 2025. By actively monitoring and optimising its carbon sequestration efforts, and coupled with its Tree Planting
Scheme, Hague Fasteners has a long-term target of completely eliminating its carbon footprint.
In an effort to minimise plastic waste, and promote sustainability, Hague Fasteners has eliminated plastic packaging from its operations. The company has transitioned to eco-friendly alternatives, such as biodegradable and recyclable packaging materials.
To add to all this, Hague Fasteners is actively investing in research and development to identify and implement greener production methods. The company is exploring innovative technologies and processes that reduce energy consumption, waste generation, as well as overall environmental impact. By adopting these greener production methods, Hague Fasteners aims to improve operational efficiency while minimising its ecological footprint.
“We are fully committed to sustainability and take our responsibility to the environment seriously,” states Jon Hague, CEO of Hague Fasteners. “Our efforts to reduce our carbon footprint and promote sustainability in fastener manufacturing align with our core family values and long-term vision. We believe that by embracing environmentally friendly practices, we can play an important role in encouraging our industry to make a significant difference in the fight against climate change.”
www.haguefasteners.co.uk
Established in 1973, Inoxdadi, an Italian producer and distributor of stainless steel bolts, nuts, washers, threaded bar and a selection of fasteners, has already taken steps in its path to becoming a reliable and sustainable manufacturing partner to companies around the world.
Since its foundation the company has always looked to adapt to opportunities in the market and to meet customers’ requirements, with the topic of sustainability being no exception.
With its factory located in Gallignano, and warehouse and head office in Barbata, Italy, Inoxdadi uses cold forming and turning to produce a range from M2 to M100, as well as a thread rolling department that produces threaded bars and studs from 10mm to 3,000mm – in accordance with international standards DIN/ISO or according to customers’ drawings.
“When it comes to sustainability we have already introduced some projects that are helping us as a business and we have more projects planned for the future,” states Inoxdadi. “For instance, we have added photovoltaic systems to both our production site and our warehouse and offices. These two different systems help us create our own energy and reduces our reliance on fossil fuels.”
Other steps Inoxdadi has taken include changing the oils and detergents it uses during its production process from solvent-based to water-based solutions; as well as changing to packaging that has a lower environmental impact. “As a business we are aware of our responsibilities when it comes to sustainability and we have been working on our ‘green credentials,” says Inoxdadi. “We are already noticing some customers asking us about what steps we are taking in terms of sustainability and protecting the environment, so it is good that we already have these projects to point out, as well as future projects we are working on.”
Inoxdadi adds: “Currently we still believe that sustainability is a secondary factor, with a lot of customers still influenced by price. However, the balance between the two could change in the future.”
www.inoxdadi.com
Whilst the attention to climate change and the environment are at the center of the international debate regarding sustainability, Growermetal keeps shaping a process based on energy optimisation, resource recovery and the cutting of emissions.
Sustainability is a key principle for the Italian washer manufacturer, a value that guides Growermetal towards a more conscious, responsible and environment-centric development strategy. “By shaping our production model, several factors are at work, such as the need to meet the demands of European market standards; to align with the 2015 EU Green Deal for carbon neutrality; as well as create a more sustainable enterprise with a reduced footprint,” explains Paolo Cattaneo, CEO at Growermetal SpA. “Having a green vision can also lead to social and economic benefits, such as creating a better working environment for employees; making the company attractive for stakeholders; and bringing resource saving benefits.”
Growermetal has set itself four main objectives – the reduction of CO 2 emissions and the purpose of becoming carbon neutral; the reduction of the company’s footprint through structured actions aimed at enhancing the business environmental profile; the improvement of energy efficiency by using renewable sources and properly disposing of waste materials; as well as the promotion of the circular economy based on the use of clean energy sources and waste reduction.
These targets are at the heart of the Greenmetal Project, an internal system aimed at aligning Growermetal’s conduct with the entire supply chain. “Our suppliers, materials, processes, and resources, are the pillars for environmental protection,” states Raffaele Motta, HSE at Growermetal. “We select our partners so as to reduce any negative impact and ensure compliance with the most demanding environmental regulations. This is why we invest in low impact materials for the production of our washers and parts, and at the same time we strive to minimise pollution and improve our environmental performance.”
The project goes hand in hand with Growermetal’s commitment to spreading a corporate culture and promoting
sustainable practices, with initiatives designed to directly involve the staff. These activities range from awareness raising meetings to the promotion of good daily habits, such as the installation of drinking water distributors, as well as specific training of the employees according to the department.
Among the most recent projects, Growermetal celebrated Safety Day on 28 th April and took the occasion to present its current and future sustainability goals to the entire team, sharing its main achievements. “Our safety management, together with the correct environmental policy and the alignment to our code of ethics, constitutes Growermetal’s Corporate Social Responsibility,” points out Raffaele. “With the Greenmetal Project, we have been able to verify how the direct commitment of the personnel, combined with investments in terms of structure, tools, and process, is fundamental to the creation of a greener culture. Events like the Safety Day enable us to talk with the staff and collect useful data.”
Over recent decades, many changes in the overall strategy have been introduced. While most have focused on reducing industrial waste, plastics, chemicals and pollutant emissions, others have been based on the recovery of materials and resources. This is the case of the system for automatic machines ‘switch off’ in case of inactivity; the reuse of oil and water from production processes; and the recovery of heat from thermal treatment processes to warm Growermetal’s departments.
In addition, the industrial rainwater harvesting system was implemented in May with the installation of two underground storage tanks, saving more than 2,000 cubic meters of tap water per year. “Thanks to the new system we
will be able to exploit an alternative source of water, using natural resources more efficiently.”
As proof of the company’s commitment, the internal performance is periodically measured and monitored by specific KPIs in order to assess the company’s success. An attention that has led to the obtainment of the ISO 14001 certification for Growermetal’s Environmental Management System, which underlines the effort in creating an effective environmental policy.
“We are now working with our board of directors to achieve the carbon footprint certification and the ISO 50001 certification, which would offer important new tools for monitoring the sustainable conduct,” reports Raffaele.
Defining attainable objectives, turning them into concrete actions, monitoring their progress, and evaluating their results, are the main steps that characterise the present and future approach to sustainable development. “As a company, we want to create a balance between our economic, social and environmental spheres, becoming an increasingly virtuous business model and creating mutual welfare for partners, employees and suppliers,” adds Raffaele.
Growermetal’s customers play a key role too. “We have activated projects with two important customers with the objective of aligning Growermetal’s sustainable conduct to their realities. In this way, we had the opportunity to define and share medium-term and long-term sustainability goals together with our partners. Mutual collaboration is a great opportunity to achieve them and build trusting relationships in the fastener field. We look forward to seeing the results of this teamwork,” finishes Raffaele.
Sustainability lies at the core of KRONUS’s mission and goals, with the company committed to promoting a greener future through its nature-friendly packaging that has gained recognition and widespread customer adoption worldwide.
KRONUS SIA underlines that the very essence of the business revolves around sustainability, zero waste production, and the creation of reusable products.
“We firmly believe that working together can achieve more and spread the message of embracing eco-friendly practices to a larger audience,” states the company.
In order to achieve its goals, KRONUS has developed a comprehensive sustainability strategy that encompasses several key initiatives. One of its primary focuses is using certified materials in its production processes, ensuring that its products meet environmental standards.
“Additionally, we strive to optimise the utilisation of production residues, minimising waste and maximising the value we extract from our resources,” points out KRONUS. “We also make regular investments in growth, enabling us to improve our sustainability practices and expand our impact continuously.”
Among KRONUS’ significant projects is the production of wooden packaging, which offers alternative and greener options for companies seeking to transport and store their products while maintaining product protection, safety and quality. The company has also been producing briquettes from wood waste, which it uses to heat its production premises. “We also sell these briquettes on the domestic market, providing a sustainable heating solution for others,” mentions KRONUS. “Furthermore, all of our production plants and warehouses follow a strict waste sorting policy, ensuring that waste is sorted correctly and disposed of in compliance with regulations.”
As part of its commitment to transparency and accountability, KRONUS is an active participant in an Environmental Product Declaration program. This means that the company diligently measures and strives to reduce the environmental impact of its products and services, generating transparent reports that enable it to track its sustainability performance and make continuous improvements.
projects often require an initial investment, KRONUS firmly believes that the long-term benefits outweigh the costs. “By embracing eco-friendly practices, we save money and contribute to maintaining a greener environment. Moreover, our commitment to sustainability is a powerful motivator for our customers, staff, and partners, to embrace a greener lifestyle and work toward a more sustainable future,” explains KRONUS. “When faced with the recent energy crisis and the significant increase in heating prices, our production spaces were efficiently heated using our own materials. This further reinforces our belief that investment in sustainability pays off in more ways than just financial returns.”
In today’s world, an increasing number of customers prioritise sustainability; sales processes based on fair-trade principles; and good employee working conditions when establishing business relationships. However, KRONUS has been dedicated to operating in a responsible and nature-efficient manner right from the start of the business. “When placing orders, it is crucial for companies to know the origin of the materials they receive and whether they are certified, and this is something we prioritise and provide assurance for,” highlights the company. “The global supply chain
is currently facing numerous challenges, but the importance of sustainable packaging should be addressed during these conditions. We firmly believe that our wooden packaging can play a pivotal role in alleviating this situation, saving both money and time. Our motto: ‘reduce, reuse and recycle’ encapsulates the essence of our packaging solutions.”
Designed for reusability and durability, KRONUS’ wooden packaging, including pallet collars, pallets, lids, and various accessories, can be used across all supply chain stages for up to 10 years – offering reusability and the possibility of it being recycled without causing harm to the environment. “The natural decomposition of wooden packaging allows it to be processed into other valuable products. Moreover, wooden packaging yields additional benefits by reducing costs, resource consumption, as well as overall environmental impact,” mentions KRONUS.
The company adds: “Adopting reusable packaging eliminates the need for disposable options, leading to a more sustainable and cost-effective approach. The problem of unsustainable packaging is evident, and reusable packaging holds significant potential to provide a solution. At KRONUS, we assist businesses in finding the most suitable and effective sustainable packaging solutions for their industries, facilitating their journey toward more environmentally friendly production practices.”
In-line with its commitment to sustainability, KRONUS also has ambitious plans for the future. “We recognise that the journey toward a greener future is an ongoing process and we are determined to improve and expand our sustainable practices continuously. One of our primary goals is to further reduce our carbon footprint by implementing innovative technologies, and renewable energy sources, throughout our operations. We are also actively exploring
partnerships with suppliers who share our sustainability values, ensuring our materials meet the highest environmental standards. Additionally, we aim to enhance our waste management systems, promoting even more efficient recycling and waste reduction practices. By collaborating with research institutions, and environmental organisations, we are also seeking to stay at the forefront of sustainable packaging solutions – constantly innovating and developing new eco-friendly products.”
KRONUS concludes: “By setting ambitious sustainability targets and embracing a proactive approach, we are dedicated to positively impacting the environment and inspiring others to join us on the path to a more sustainable future. Together, we can make a difference and create a better future for our planet.”
www.kronus.eu
Hungarian wholesaler Visimpex is looking to adopt sustainable practices within every facet of its business, including in its new modern technology centre – which will be built with sustainability in mind for every detail.
Built as part of a greenfield project, Visimpex’s technology centre will be one of the most modern and environmentally conscious buildings in the region, with solar energy used for electricity generation; a geothermal heat pump used for heating; the collection and harvesting of rainwater for irrigation; and electric car charging provided for both staff and visitors.
“Our management is characterised by its ‘green thinking’ and its commitment to being environmentally aware,” states Visimpex-Hungary kft. “It is part of the company ethos to convey this message and sentiment to every one of our 51 team members, as well as to all our existing and future customers.”
Visimpex’s commitment to sustainability is even underlined in its corporate colours, with the company deliberately using the colour green to signify how much value it places on sustainability.
“The new technology centre is a big example of how crucial sustainability is to us as a business, but when it comes to sustainability, we believe it includes even small acts, for instance a large part of our electricity needs are met by a solar power plant installed on the roof of our logistics centre,” mentions Visimpex. “Furthermore, to be more eco-friendly, we also use bicycles and electric scooters to get to work, the latter of which each colleague received as a gift from the company.”
Visimpex also believes that alongside introducing sustainable practices it is just as important to educate its staff about sustainability. “We believe it is important to educate, so we inform employees about all our efforts towards environmental
awareness and sustainability, while also setting good examples and encouraging them to do the same, not only at work but hopefully at home.”
Even the company’s product range has a role to play in sustainability and environmental awareness, as the company is a leading player within the solar mounting sector. “We launched our solar mounting business 13 years ago and by 2022 it had grown to account for 30% of our turnover,” points out Visimpex. “Today, we are proud to say that if you are looking for a solar mounting system in Hungary, you will surely think of the VISIMPEX SOLAR® system, as it is one of the fastest and most versatile systems – with one of the longest histories and several references in the market.”
When it comes to sourcing its products, Visimpex has a clear strategy of prioritising local suppliers where possible to help reduce the environmental impact of shipping the products. “We are always reviewing our sourcing options and if we discover a distributor for our products within Hungary, or the neighbouring countries, we always look to work with them if possible. Unfortunately, we are unable to source a significant proportion of our products from domestic or EU sources, so we do have to look further away into Asia. However, wherever the supplier, we demand they use durable, reusable paper packaging materials, which we also use when delivering goods to our customers.”
Visimpex is also considering sustainability when it comes to the expansion of its existing product portfolio. “We hope to introduce a new, innovative, niche product in this segment, which we can’t reveal more about at the moment, but we will look to introduce it to the market soon.”
Visimpex concludes: “We will continue to analyse what steps we can take as a business to become more sustainable and environmentally aware, as we believe these efforts will bring long-term, intergenerational benefits.”
www.visimpex.hu
In addition to new product ideas, and constant improvement of existing products, HEICO Group – the German manufacturer of bolt locking devices, pre-tensioning technology and cold forged parts – has invested greatly in sustainability, including the implementation of an environmentally conscious and resource saving production process.
Tobias Grobe, head of sales and marketing at HEICO, explains: “Today, sustainability is more relevant than ever. For a long time, we at HEICO have been continuously working on numerous projects to make our company more sustainable. For instance, a responsible treatment of people and nature, as well as energy and the resource saving manufacture of our products, are already part of our company ethos.”
By just looking at the company’s premises in a rural, but an infrastructurally well-developed region close to the Ruhr metropolises, it quickly becomes clear how much value HEICO places on sustainability and environmental awareness. The roofs of the production halls are adorned with a photovoltaic system; next to the production halls there is a company owned thermal power station; and all around the administration buildings, and halls, there are many green areas with fruit trees.
One of the highlights for the employees and visitors to the site is the HEICO animal park, which is also part of HEICO’s sustainability concept. The park not only serves as a home for animals such as goats, donkeys, mini horses, and alpacas, it is also used as a place of learning by local kindergartens and elementary schools.
The company’s own thermal power station, which is connected to a nearby biogas plant, supplies energy in the form of electricity and heat. HEICO also uses the thermal energy to heat its washing systems – while the electricity generated is fed into the general power grid.
Another important contribution to the sustainable use of energy is made by the painting systems – through heat recovery during the thermal afterburning in the painting process.
It is not only heat that is cleverly used in the modern production facilities at HEICO. The coolant for the inductors of the hardening plant is cooled by an open air cooler on the roof of the production halls. At an outside temperature of up to 17°C [62.5°F] the cooling medium can be cooled down in this way without an additional cooling unit.
“The HEICO-LOCK® bolt locking devices, as well as the products from the HEICO-TEC® series, meet the highest quality standards. Our intention is to produce durable products that can be reused several times and thus conserve our resources. A long product lifetime ensures proportionally more sustainability.” explains Tobias.
At the recent Fastener Fair Global show in Stuttgart, Germany, HEICO also launched a new product variant, HEICO-LOCK® Plus, that offers price conscious users an attractive alternative to securing their bolted joints.
The HEICO-LOCK® Plus is a bonded version of a hexagon nut and a wedge lock washer pair, which are available in steel and stainless steel. Also new are the tension bolts, which for now complete the HEICO-LOCK® product portfolio for pre-tensioning particularly large bolted connections.
www.heico-group.com
The KSP12-R combines typical SACMA solutions, proven by thousands of machines, with the most advanced mechatronic technology available in the market. Major set up adjustments are motorized for a quick and friendly changeover: S-feed wire feeder driven by torque motor, motorized wire stock gauge and DKO, threading starter driven by torque motor with self-learning function borrowed from Ingramatic rollers. The quality management is facilitated by two gates interfaced with the load monitoring system and discharging NC parts respectively after the header and after the roller. An optional sophisticated load control system is protecting the machine against overloads and is monitoring the forming and rolling processes. Scraps separators in different sizes are available when producing self-tapping screws.
Ask for more information to : info@sacmalimbiate.it
Lohmann, the German high-tech adhesive tape specialist, is renowned for its multifunctional bonding solutions for various industries and applications. Over its more than 170 year history, the company has developed many innovative products and technologies, which at the same time take sustainability aspects into account.
In recent years, Lohmann GmbH & Co KG has taken significant measures to reduce its environmental footprint and develop sustainable products, such as the latest addition to its product portfolio – the bio-based and solvent free ECO range of adhesive tapes.
The adhesive for the ECO range contains 50% bio-based raw materials and the tape is equipped with a recyclable liner, thus fit for a return into the regular circular economy. The ECO range is also manufactured with Lohmann’s solvent free TwinMelt technology, an award winning coating process that enables adhesive tape production with comparatively low energy consumption and reduced carbon footprint. What’s more, the production at all Lohmann’s German sites, as well as several European ones, is powered by 100% renewable energy, which also significantly reduces the environmental impact.
Lohmann’s sustainability efforts have also been recognised by third party organistions. The company has been awarded the EcoVadis silver seal, a globally acclaimed rating system for corporate social responsibility and sustainability. This rating demonstrates Lohmann’s commitment and its efforts across its supply chain, and business operations, in the areas of ecology, social responsibility and economy. With the silver certificate, the third highest award within the rating, EcoVadis certifies Lohmann’s sustainability commitment as ‘structured’ and ‘proactive’. The seal applies to all Lohmann sites worldwide.
“We are deeply convinced that holistic sustainable action is the best foundation for steadily improving the quality of life for present and future generations,” state Dr Jörg Pohlman, CEO at Lohmann, and Dr Carsten Herzhoff, COO at Lohmann.
Essentra Components, a provider of essential components and solutions, has exceeded its 2025 Scope 1 and 2 emissions targets and is reshaping its sustainability strategy to focus on helping customers achieve their sustainability goals.
According to the latest figures published in its 2022 annual report, Essentra Component’s manufacturing operations have reduced direct emissions by 27% and emissions intensity by 35% since 2019. These results exceed the 2025 target of a 25% reduction in emissions intensity, three years ahead of schedule. These results also support Essentra’s aims to reach net zero in its operations by 2040 and along its value chain by 2050.
The business is also ahead in other targets. In 2022, 12 component sites, double that of the previous year, achieved zero waste to landfill, and overall waste intensity has reduced by 25% against the 2019 baseline, again meeting its 2025 target ahead of schedule.
In publishing its results, Essentra has also revised and is expanding its sustainability strategy across five pillars: the planet, its components, its culture, its communities and Essentra’s customers. For the first time, it is also setting Scope 3 emissions targets, which will be science-based and independently assessed and reviewed in-line with the Science Based Targets initiative (SBTi). These new Scope 3 emissions targets will support both Essentra’s own ESG (environment, social and govemance) goals and those of its customers.
Essentra is also innovating with new sustainable materials. In 2022, it successfully completed 29 new product trials, and today, recycled
polymer makes up 10.8% of total polymer materials used. The plan is to use 20% recycled materials by 2025. Most LPDE (low-density polyethylene) products manufactured at the Kidlington site in the UK use 50% recycled content, and many are 98%. These component products help Essentra’s customers to reduce their own product emissions and avoid Greenhouse Gas (GHG) emissions in their supply chain.
Essentra has also made progress in sustainable packaging materials; all plastic packaging at Kidlington comprises 30% recycled materials, against Essentra’s target of 50% by 2030. More innovative technologies such as recyclable and bio-based plastics will also be explored to reduce the company’s and customers’ environmental impact even further.
Jennifer Spence, head of sustainability strategy at Essentra, says the business has made exceptional progress against its original sustainability targets: “Our new sustainability strategy is all about revising and upscaling our future commitments in reducing our emissions, achieving net zero and using more sustainable materials in our production processes.”
“Our aim is to reduce not only our own environmental footprint, but also support our customers in delivering their own sustainability targets. We’ll do this by continuing to innovate and advise on how our components can help develop a ‘win-win’ for us all.”
info(at)teudeloff.de sales.us(at)teudeloff.de sales.fe(at)teudeloff.de
(Europe) (America) (Asia)
Maximale Sicherheit für Mensch und Natur.
Geprüft – gesündere Produkte.
Zertifiziert durch
As the leading publication within the industry, Fastener + Fixing Magazine always ensures it is at the forefront of the market when it comes to the latest developments, including sustainability.
For several years Fastener + Fixing Magazine has been partnered with a PEFC certified printer and ensures that the printed magazine is produced using PEFC certified paper – enabling our readers to keep up to date with the latest news and developments, safe in the knowledge their printed magazine is produced sustainably.
The PEFC (Programme for the Endorsement of Forest Certification) is an international non-profit, non-governmental organisation dedicated to promoting Sustainable Forest Management (SFM) through independent third party certification. PEFC works throughout the entire forest supply chain to promote good practice in the forest and to ensure that timber and nontimber forest products are produced with respect for the highest ecological, social and ethical standards.
Buying from responsibly managed forests means respecting the forest owners – large and small – to maintain biodiversity, productivity and regeneration capacity. In Europe, where almost all primary forests are protected, paper comes from sustainably
managed forests where the cycle of planting, growing and harvesting is carefully controlled.
The PEFC’s distinctive ‘green trees’ logo (included on page 8 of every printed magazine) is a truly global brand and means customers and consumers are able to identify that every printed magazine is from sustainably managed forests and controlled sources.
Alongside guaranteeing that the magazine is produced using sustainably managed forests and controlled sources, Fastener + Fixing Magazine has also ensured that the plastic delivery bags used for every magazine are made from recyclable material and are also bio-degradable.
www.pefc.co.uk
…every printed magazine is from sustainably managed forests and controlled sources.”
The
Wedge
The
Tensioning
The Indian fastener industry congregated in Mumbai for a three day exhibition and business meetings, as well as to witness the latest technologies at Fastener Fair India 2023.
Taking place from 1 st – 3 rd June at the Bombay Exhibition Centre in Mumbai, Fastener Fair India 2023 attracted 6,579 visitors from all over India and the world, resulting in organisers reporting it as being a huge success.
The show featured a wide range of products and services from over 160 exhibitors, including fasteners, fixings, assembly and installation systems, storage and logistics services, fastener manufacturing technology, as well as construction fixings. Visitors had the opportunity to learn about the latest industry trends, network with leading experts, and do business with potential partners.
The show was a great success for exhibitors, with a substantial increase in the participation and a 71% growth in the exhibition area. This shows that the fastener and fixings industry is growing in India and that there is a strong demand for these products and services.
“We are very pleased with the success of Fastener Fair India 2023,” said Vicky Kumar, project manager for RX India – the organisers of Fastener Fair India. “The event was a great opportunity for industry professionals to come together and learn about the latest trends and technologies. We are grateful to our exhibitors and visitors for their support.”
With the success of the show, the next Fastener Fair India will take place from 26 th – 28 th July 2024, in Pragati Maidan, New Delhi.
The Taiwan International Fastener Show 2023 (Fastener Taiwan) came to a successful close in May – attracting just under 300 exhibitors and nearly 10,000 visitors across the three day event, from both domestic and international fastener markets.
Fastener Taiwan returned after a five year hiatus, due to the Covid-19 pandemic, and not only promoted communication and cooperation within the industry, but also injected new vitality and energy into it. The event, which is organised by the Bureau of Foreign Trade – MOEA, co-organised by the Kaohsiung City Government, and implemented by the Taiwan External Trade Development Council (TAITRA) and the Taiwan Industrial Fasteners Institute (TIFI), experienced a growth of 7.2% in visitor levels compared to the pre-pandemic shows.
Throughout the show, multiple international buyer groups visited and purchased products, including nearly 1,100 foreign buyers from 60 different countries, with the top five buyer countries being India, the USA, Japan, Germany and Thailand. Although the physical exhibition was closed on 5th May, the online exhibition continued until 16th May, attracting even more visitors and business opportunities.
In addition to exhibiting the latest technologies and innovations in the fastener industry, the exhibition organisers held multiple industry forums, procurement meetings, and the Manufacturers Win podcast, attracting many industry experts and scholars to share their experiences and achievements.
On the first day of the exhibition, the Fastener Taiwan organisers held the Global Fastener Forum, inviting the presidents of the three major fastener distributor associations, including the National Fastener Distributors Association (NFDA), the Italian Union of Fastener Distributors (UDIB) and the European Fastener Distributor Association (EFDA). Experts in related fields were also invited to exchange views on the future prospects of the global fastener market
under the impact of rising raw material and transportation costs, as well as anti-dumping measures in China.
Other hot topics were also discussed, such as the transformation to low carbon fasteners, Smart manufacturing, electric vehicles, in addition to solar and wind power fastener applications. The Global Fastener Forum attracted over 200 industry insiders from both domestic and foreign markets, all interested in the latest trends in domestic and international industries.
The second day of the exhibition included a carefully planned procurement meeting to assist industry players in discussions with buyers. In addition, TAITRA invited 49 international buyers from 18 countries, including Mexico, Germany, the UK, France, Brazil, New Zealand, Finland, USA, Canada, and the United Arab Emirates, to participate in 152 one-on-one procurement meetings with 24 industry players. Through this matchmaking event, the industry professionals gained an enormous amount of potential business opportunities.
The senior vice-president of SACMA Group, an Italian manufacturer of fastener production machinery, stated that this was SACMA’s first time joining Fastener Taiwan and with many potential business and cooperation opportunities obtained on-site, the results exceeded his expectations. Also, the procurement vice-president of F. Reyher GmbH expressed his affirmation of the innovative strength of Taiwanese fastener manufacturers at the exhibition. Both expressed a wish to continue to cooperate with high-quality fastener suppliers in Taiwan and excitement at the prospect of visiting the show again from 16th – 18 th April 2024.
Jalisco, Mexico
7 – 9 Sept 2023
www.fastenerfairmexico.com
The fastener event for Mexico.
Hand Tools and Fasteners Expo
Mumbai, India
1 Sept – 3 Sept 2023
www.iihtexpo.com
Handtools and fasteners exhibition.
wire China
Shanghai, China
4 – 7 Sept 2023
www.wirechina.net
Wire and cable, including fastener manufacturing technology.
Intersolar Mexico
Mexico City, Mexico
5 – 7 Sept 2023
www.intersolar.mx
Exhibition for the Mexican solar industry.
HUSUM Wind
Husum, Germany
12 – 15 Sept 2023
www.husumwind.com
Wind energy trade fair.
SchraubTec West
Bochum, Germany
13 Sept 2023
www.schraubtec.com
German regional trade fairs for screw connections.
parts2clean
Stuttgart, Germany
26 Sept – 28 Sept 2023
www.parts2clean.de
Leading international trade fair for industrial parts and surface cleaning.
Hardware + Tools Middle East
Dubai, UAE
2 – 4 Oct 2023
www.hardwaretoolsme.com
Tools, hardware, materials and machinery.
UK Construction Week
Birmingham, UK
3 – 5 Oct 2023
www.ukconstructionweek.com
The UK’s largest construction event.
International Fastener Expo
Las Vegas, USA
9 – 11 Oct 2023
www.fastenershows.com
Fastener manufacturers, distributors and users.
Fastener Poland
Kraków, Poland
18 – 19 Oct 2023
https://fastenerpoland.pl/en
6 th edition of the international trade fair for fastener and fixing technology.
Taiwan Hardware Show
Taichung, Taiwan
18 – 20 Oct 2023
www.hardwareshow.com.tw
Tools, building materials/DIY and houseware products.
International Hardware Fair India
New Delhi, India
2 – 4 Dec 2023
www.hardwarefair-india.com
Hardware and DIY sector.
Here Barbara Sorgato, secretary general of the European Consortium of Anchor Producers (ECAP), reports on the association’s recent General Assembly, which took place in Zurich, Switzerland, from 14th to 15th June.
ECAP members gathered to discuss together the strategy for the present and the future of their products, based on circular economy initiatives. Held in Zurich, the welcome from the Swiss members immediately swept away any clichés of cows, chocolates, and banks, that the non-Swiss consortium members may have inadvertently been thinking. Instead replacing them with those of an ancient democracy tailored on the microrealities of this nation, and an effervescent cultural melting pot.
This was underlined by demonstrations of the women’s strike across Switzerland, which took place on the first day of the meeting, with women of all ages – and men too – taking to the streets to fight against the devaluation of women’s work, both financially and socially, and in particular against wage inequality –which in Switzerland, as with many countries in the European Union, is unfortunately a rule of the market.
Through the demonstration, ECAP members were able to get to the heart of one of the aspects of the circular economy – gender
equality and inclusiveness – without even needing to be in the room. In fact, gender equality is something ECAP is aware of, as the association’s office is entirely managed by female employees, therefore lacking a male presence. Not having this male inclusiveness is a weakness of ECAP’s office and something that we will be working on.
Once the meeting began, members were handed a postcard with a QR code giving a link to ECAP activities. Along the lines of hotel rooms, which invite us to reuse towels, and restaurants that deprive us of their precious menus on satin paper, ECAP has applied sustainability through a digital approach – leaving members halfway between being aware of the right thing to do and regretting the wrong but more comfortable, alternative.
The Green Deal, digitalisation and the circular economy have been on ECAP’s agenda since 2019. However, talking about these topics in general is one thing; defining them for our products
Sustainability is not a marketing concept to better sell organic products, it is a revolution in our way of working, which takes us out of the comfort zone we have reached in recent years.”
SAVE TIME AND MONEY
FIX INSULATION DIRECT TO BASE MATERIAL
ACCURATE AND CONSISTENT
LOWER OPERATION FATIGUE
4 TIMES FASTER THAN TRADITIONAL METHOD
EASY MAINTENANCE OF TOOLS, LESS DOWN TIME
BOTH STYROFOAM AND ROCKWOOL
is another thing. As an association, we have extrapolated the part of the circular economy that allows us to address the issue at an association level, i.e at a common level – such as sustainability – whilst leaving the definition of the other aspects of the circular economy to the initiatives of individual companies. In fact, we must not forget that we operate in the paradox of having to deal with the circular economy while remaining completely within the mechanisms of the linear capitalist economy in which we find ourselves. Seen from this point of view, sustainability needs to be sold, even before being applied, and this is a marketing objective that a company hardly wants to share with competitors, even at an association level. If ECAP was to succeed in a common approach on sustainable fasteners, we could almost say that we have incorporated the circular economy into our DNA.
Sustainability of fasteners, as I have written in other articles in this magazine, is a transversal theme for all activities, at all levels. It cannot be closed in a folder or a drawer, because so many things we face today in ECAP are affected by sustainability. Consequently, not only the ECAP agenda but also our way of working requires a change and an adaptation to this new approach. It is difficult for us to talk about sustainability using the usual images of shoots, leaves and earth. Sustainability is not a marketing concept to better sell organic products, it is a revolution in our way of working, which takes us out of the comfort zone we have reached in recent years. It is a violent, uncomfortable change, if put in place at the speed we are doing it. For this reason, we represented it to the members with a quote from Charles Darwin: ‘It is not the strongest of the species that survives, nor the most intelligent that survives. It is the one that is most adaptable to change.’
During the General Assembly we were honoured to host Evangelia Tsiala, from Small Business Standards, as well as Oscar Nieto from the European Commission. They both answered the many questions posed by ECAP members on the present and the future of post-installed fasteners and wood connectors, under the actual Construction Products Regulation (CPR), as well as under its revision, as proposed so far.
Members tackled several topics related to the standardisation blockage and the so called CPR acquis, as well as practical aspects such as the legal provisions of the ETA transfer; the implementation of a Unique Identification Code in the new CPR; the legal status of Eurocodes and EOTA Technical Reports in European Member States; the consequences of having ETAs outside of the harmonised zone in the new CPR; the format of the future digitalised Declaration of Performance and Declaration of Conformity for fasteners with EADs and with CE Marking based on CEN standards; and the responsibility of the manufacturer in the new Declarations of Conformity.
Timber connectors is the sector that faces most of the challenges mentioned above. It is in fact here that we face the rewriting of the new Standardisation Requests, which
bring within them the issues of sustainability and the legal implementation of the new CPR. It is the test bed where the technicians of the ECAP Working Group face not only the technical challenges but those related to sustainability and the legal basis of the standards on connectors. It is also the sector where dialogue with other associations develops on several levels – because the upheaval taking place in the world of construction products makes us disoriented and in need of sharing views and information.
At the end of the first day, and to stay on the subject of sustainability, the members had dinner at the Hiltl restaurant – a vegetarian restaurant that has not been opened on a cultural whim, or the wave of sustainability fashion, but is a historic and traditional restaurant that was founded in 1898 by Ambrosius Hiltl, making it the world’s first vegetarian restaurant in Europe.
At the end of the second day of the General Assembly, members voted for the board for 2023 to 2026, with all members reconfirmed for another three years – rewarding the work done in support of the association and its European composition.
The board is made up of Lars Mortensen of Kyocera-Senco, Urs Joos of Jcons GmbH, Andrea Taddei of Bossong SpA, Nick Beardon of JCP Construction Products, Johannes Heye of pgb Group, Santiago Reig of INDEX and Gianluca Bertamino of Tecfi SpA.
The board in turn elected ECAP’s chairman for 2023 to 2026, with Mr Gianluca Bertamino, one of the founding members of ECAP, becoming the association’s chairman for the first time.
www.ecap-sme.org
Members tackled several topics related to the standardisation blockage and the so called CPR Acquis, as well as practical aspects…”
In celebration of both its 35th anniversary in the industry, and the opening of its new headquarters, Hydrajaws hosted an open day on 18 th May at its new site in Tamworth, UK. Assistant Editor Becca England attended to see the new building first-hand and report on the history, innovations and capabilities of Hydrajaws.
Established in 1988, Hydrajaws Limited works primarily in the construction industry, developing, manufacturing and selling a range of portable pull testers used to check the crucial holding force of anchors and fixings in construction materials. Today, the company has a global reach, with 70% of exports going abroad to over 65 different export markets. The company’s open day aimed to celebrate this impressive journey.
Upon arrival, guests were greeted warmly and served drinks while final preparations were made for an 11:30 start. These guests included representative members from Adi Supply Ltd, fischer Fixings Ltd, Ejot UK Ltd, Made in Britain and Rawlplug S.A. Visitor numbers exceeded the company’s expectations, as highlighted by Michelle Cross, marketing co-ordinator at Hydrajaws, who stated that “we were hoping for 30 visitors, but exceeded our expectations as 47 attended”.
Several speakers were present on the day, the first of which being Master of Ceremonies Dennis Chick – who officially welcomed visitors and briefly detailed the day’s itinerary, which included a tour of the grounds, followed by a buffet lunch, before the official opening ceremony of the building. The second speaker Stephen Hynes, managing director at Hydrajaws, discussed his role in the company and highlighted how Hydrajaws was “very much a family run business”.
Royston Morgan, chairman of Hydrawjaws, was the third speaker who talked guests through the history of the company, starting with its original product, the Model 0087. “This first generation model had a 20kN load gauge,” explains Royston. “To put this into perspective – this is 2 tonnes. Amazing to think
that such a small handheld device would be able to lift our friend here…” to which a life-size model of a rhino was unveiled to highlight the capabilities of the company’s first tester. These capabilities have grown to the modern models used today all over the world.
The growth of Hydrajaws was aptly demonstrated in Royston’s speech, as the evolution of each tester was shown, parallel to the growth of the company – illiustrated by the increased warehouse production over the years. The Tamworth building is the third workspace investment for the company in the past two decades, displaying the significant growth for Hydrajaws as the company continues to meet industry demand.
Royston was also sure to highlight the importance of familial support in the company’s history, which led to the fourth speaker, CEO Adrian Morgan, who expanded on his role in the business and how product innovations aided in company growth. The final speaker was guest speaker John Pearce, CEO at Made in Britain, who was sure to enforce “the importance of Great British manufacturing”.
Following the insight offered by these speakers, guests were then taken on a guided tour around the Hydrajaws production factory – where all tester kits are assembled, calibrated and packaged in-house. A live demonstration of the M2008 – the company’s latest model tester that has been used on many different construction projects around the world – was also shown to illustrate the capabilities of the tester and how it identifies whether or not an anchor is up to industry standards. Capable of pull testing up to 145kN (which would be equivalent to about seven rhinos) the product pull tests threaded studs that have been post-installed into a base material.
After a spot of lunch came the main event, the official opening ceremony of the new Hydrajaws building, performed by His Majesty’s Lord-Lieutenant of Staffordshire, Ian Dudson, CBE KStJ. The Mayor of Tamworth, Cllr Moira Greatorex was also in attendance to witness the ceremony.
“We feel the event strengthened relations with our suppliers and has enabled them to gain a greater understanding of our business. We’ve also received quite a number of congratulatory comments and appreciation from our guests,” concluded Michelle.
A new generation of fasteners for fixing thermal insulation, such as polystyrene, mineral wool, as well as wood wool, has been introduced by Polish specialist Klimas Wkręt-met – the ThermoDrive V2 fastener.
The new, versatile ThermoDrive V2 fastener can handle many inaccuracies in thickness, insulation surface and substrate discrepancies often encountered during construction. The fastener’s performance parameters, and its high load bearing capacity values, make it suited for fixing a wide range of External Thermal Insulation Composite System (ETICS) products, including on buildings undergoing thermal modernisation – ETICS on ETICS.
“Mechanical fasteners actually perform a number of functions in external wall insulation, one of which is load transfer – primarily protecting the ETICS system from wind suction forces and detachment from the substrate,” explains Klimas Wkręt-met. “Mechanical fasteners have the task of stiffening the entire insulation system, eliminating movement and deformation of individual insulation boards; limiting the formation of point thermal bridges; as well as protecting against failure due to loss of adhesion and load bearing capacity of the adhesive layer with the substrate. These are the basic parameters that should be met by mechanical fasteners in ETICS insulation systems.”
Klimas Wkręt-met believes it has gone a step further with the introduction of its ThermoDrive V2 fastener, which, while maintaining fundamental required parameters, can be used to attach polystyrene and mineral wool to, amongst other substrates, concrete, solid ceramic brick, ceramic hollow brick, elements made of lightweight aggregate, as well as cellular concrete.
The company points out that the ThermoDrive V2 fastener owes its versatile performance to its design, which it says integrates the advantages of well known products from both the WKTHERM-S and the ECO-DRIVE series of products. Attributes of these are characterised by easy and secure installation, reliability, and versatility, as well as offering the maximum achievable pull-out load.
Regardless of the chosen installation method, the fastener can be used effectively for a wide range of insulation thicknesses up to and including around 40cm. In addition, the unprecedented wide tolerance range for uneven substrates on the market means ThermoDrive V2 can be used with a variety of material surfaces within a single project, e.g solid and hollow materials side by side using only one fastener length. In addition, the design of the
guarantees a solid anchorage for the fastener even with hollow materials, hollow centres, and thin-walled internal masonry structures. Until now, even fastener sizes a few centimetres longer in a similar class would not guarantee as effective an anchorage, due to the shorter and limited anchorage zone and the greater likelihood of missing the zone in thin walls of the internal structure of the masonry element.
Regarding the mechanical fixing of ETICS, as well as ETICS on ETICS, the new fastener is ideal during the renovation of external walls of buildings made with large slab technology. From a formal point of view, it can be used in a concrete ‘texture’ layer with a minimum thickness of 40mm, achieving high strength parameters. This is due to its high performance parameters demonstrated during the certification process. According to Klimas, more than 90% of façade connectors/fasteners currently on the market do not have this capability.
For ETICS contractors and system providers, the very high rigidity of the plate, which increases the durability and safety of the insulation systems, is a major benefit. The sleeve of the fastener has also been designed in such a way that the screwed-in steel pin, which enables the insulation layer to be fixed, is sufficiently insulated and, as a result, ThermoDrive V2 is characterised by a minimum point, thermal conductivity coefficient. Particularly noteworthy, too, for a metal shank fastener with such a wide range of applications, is the fact that the point thermal conductivity value of only 0.001 W/K, applies irrespective of the thickness of the insulation to be fixed to the substrate.
For its part, Klimas Wkręt-met, which has been present in the Polish construction market for more than thirty years, has made a significant contribution to the development of the entire sector. The launch of ThermoDrive V2 is proof that the company is actively working on the evolution of a group of mechanical fastening systems for thermal wall insulation, compatible with the requirements of various ETICS insulation systems. The company is also actively involved in organisations such as the National Association for Thermal Insulation Systems, the European Association for Composite External Thermal Insulation Systems –EAE, and the French Association Le Mur Manteau, which together ensure the dissemination of complete technological solutions with documented quality.
Following an agreement with the European Organisation of Technical Assessments, here is a list of recent ETAs published in the last two months on the EOTA website.
It is important to note that existing ETAs may be amended or withdrawn so this list should not be considered definitive. For further information and a full list of valid ETAs visit EOTA’s website. If you have recently received an ETA, and would like to have it included in our table, please email us the full details at editor@verulammedia.com www.eota.eu
ETA
NUMBER
ETA - 23/0417 GFC VY200 Hybrid Injection Resin GFC Fasteners & Construction Products
ETA - 23/0429 Worldfix 500-Viniléster Worldfix S.A
ETA - 23/0466 PROCREA® Injection anchor CJL Commerce GmbH
300 Winter, V-PRO 300 Summer
Ankersystemen B.V
ETA - 23/0408 Mungo Injection System MIT800RE for concrete MUNGO Befestigungstechnik AG
ETA - 23/0412 STRONGHOLD SH-EP1 for concrete STRONGHOLD Systems (Asia) Pte Ltd
ETA - 23/0413 ANCORA CHIMICA BLUFIX VE+ 300ml BLUE SQUARE SEDA INVEST Srl
ETA - 23/0414 ANCORA CHIMICA BLUFIX PESF 300ml BLUE SQUARE SEDA INVEST Srl
ETA - 23/0416 GFC PE600 Pure Epoxy Injection Resin GFC Fasteners & Construction Products
DEFORM-NUT® SELF-LOCKING
Three dimensional nailing plates
ETA - 23/0184 ESSVE Purlin Anchors ESSVE Produkter AB
ETA - 23/0185 ESSVE Angle Brackets ESSVE Produkter AB
ETA - 23/0234 ESSVE Angle Brackets ESSVE Produkter AB
ETA - 23/0235 ESSVE Joist Hangers ESSVE Produkter AB
ETA - 23/0236 ESSVE angle brackets ESSVE Produkter AB
ETA - 23/0302 Knapp Solo MEGANT Connectors Knapp GmbH
ETA - 23/0353 SIHGA MassX Hold Downs SIHGA GmbH
Born from the fusion of riveted insert and selfblocking nut, DEFORM-NUT® SELF-LOCKING is the new anti-loosening deforming rivet: the ideal solution for fixing parts subject to risk of loosening and strong vibrations. DEFORM-NUT® SELFLOCKING can be easily installed on boxes, pipes, sheet metal, profiles and on all those supports that do not allow the insertion of nuts inside them.
PATENTED INSERT
Guaranteed anti-loosening without the use of additional components (threadlockers, elastic washers)
Available in zinc-plated steel and stainless steel
Available in various shapes and dimensions
Nylon ringWhen it comes to exterior construction jobs, tradespeople want a screw that can withstand the test of time and the unpredictability of the elements. With that in mind, Samac performance exterior screws are designed for any exterior wooden, ironmongery, or fencing project, where a long-lasting finish is required.
Samac Fixings Ltd uses Ruspert ceramic coating in silver or black to ensure its performance exterior screws can resist environmental corrosion, particularly when it comes to outdoor projects – where exposure to moisture and salt can significantly accelerate the corrosion process. “The Ruspert coating has an exceptional resistance to high moisture and salty conditions, ensuring the screws maintain their integrity and won’t degrade over time, even when used with treated timber,” explains Samac.
The screws are also designed with a pan or countersunk head. The large diameter of pan head screws makes them ideal for high torque assembly jobs, while the flat underside ensures a firm hold even with enlarged holes. The countersunk screws provide an aesthetically pleasing look and offer a neat and secure finish, reducing potential hazards like snagging.
Salt spray tested to 1,000 hours, Samac performance exterior screws are available in a range of sizes from 25mm up to 50mm in silver or black pan head, as well as 25mm up to 100mm (black countersunk), and 150mm (silver countersunk), and stocked by independent merchants across the UK.
Lindapter has added the Type SM decking fixing, which it reports is a zero impact fixing, with CE Marking, that has been developed to enable building services to be suspended from the SigDeck100 decking profile, manufactured by Sigmat.
Lindapter underlines that the new Type SM fixing offers contractors definite efficiency gains, as it can be installed on-site in a matter of seconds, without the need for specialised labour, costly equipment or electricity.
“These new fixings for securing building services are designed to fit inside the dovetail re-entrant channels of a composite decking profile, completely removing the need to drill through the deck into the concrete above, which can be hazardous and produce silica dust,” explains Lindapter. “In contrast to drilling, or shot firing methods, using the Type SM offers multiple safety benefits, including eliminating silica dust exposure, preserving the fire integrity of the decking profile and avoiding decking profile delamination.”
The system’s wedge and locking plate, made of pressed steel, has also been developed with a Bright Zinc Plated (BZP) finish to protect against corrosion and oxidation. To keep the wedge from rotating after installation, the locking plate is designed to fit over the wedge.
The Type SM offers a 3:1 safety factor and a capacity of 1.00kN per fixing.
INDEX® A Perfect Fixing has launched its new general catalogue of new products and ranges for 2023, which includes over 7,000 products, as well as news on new types of approvals and certifications.
The company’s steel or stainless steel accessories for cables and chains, for example, are designed to safely hold heavy loads and can withstand adverse weather conditions, making them perfect for outdoor applications – where they are mainly used to fix, support and protect steel cables, visible cables, ropes and chains. Within this category, INDEX® A Perfect Fixing has expanded its range of accessories with various additional functionalities, such as cable clamps for connections between cables; eye bolts, ideal for lifting objects under tension; shackle bolts for attaching chains and restraining a load; or thimbles, suitable for protecting cables.
For its current range of installation and fitting systems for solar panels, the company has also added several items and solutions, such as clamp assemblies, connectors, profiles, accessories and kits. For example, customer kits of two or three panels for different panel supports, coplanar and triangular, are available. If more than two or three panels need to be installed, expansion kits that allow more panels to be installed without incurring unnecessary costs are also available. These kits contain everything needed to expand an installation, but also allow the removal of unnecessary products, e.g duplicate clamp assemblies, therefore saving on costs and avoiding waste.
Also added to the company’s new product range and illustrated in the latest catalogue are such solutions as concrete anchors for high loads – MTH-AT and MTP-AT – an A4 TXE bi-metal stainless steel screw, and the TN4S-A, four segment nylon wall plug with wide collar. The new catalogue can be downloaded from the INDEX website. www.indexfix.com
Combining ease of installation with safety, when introducing high loads into concrete, the UltraCut FBS II screws from fischer are now suited to a wider set of applications, as a result of the latest technical developments to the range.
For instance, the FBS II 6-10 versions can now also be used in masonry, in accordance with the European Technical Assessment (ETA) certification. In addition, the new FSW adjustment disk, in conjunction with the FBS II 10 US gvz, enables sleepers and beams to be adjusted and aligned quickly and easily. This whole range of concrete screws combines maximum load bearing capacity with quick installation and come in both steel and stainless steel versions, both meeting ETA standards covering their use in cracked and non-cracked concrete, indoors and outdoors, as well as with seismic loads of performance categories C1 and C2. They are also rated to fire resistance level FRL R120.
Further advantages of using the UltraCut FBS II include its reliable power transmission and installations free of expansion pressure, due to its precise fit. Patented thread geometry and its large core diameter introduce very high tensile and shear forces into the concrete, which means fewer fastening points are needed than was previously the case.
The UltraCut FBS II can also be re-used under certain conditions and allows small edge and centre distances, and offers power saving, safe assembly. As for loads, the concrete screw allows maximum flexibility, depending on the diameter, with up to three approved screwing or anchoring depths. Using the screw is also very simple, the user simply screws the UltraCut FBS II concrete screw into the drill hole using push-through installation, with no further drill hole cleaning required for vertical drilling in floor and ceiling areas or when using hollow drills with a suction function.
The FBS II 6-10 versions include FBS II versions with diameters 6mm – 10mm in electrogalvanised steel and with diameters 8mm – 10mm in multi-coated steel CP and stainless steel. These have been evaluated for anchoring in solid and perforated brick masonry, with brick types Mz bricks (EN 771-1), solid sand-lime brick KS (EN 771-2) and perforated sand-lime brick KSL (EN 771-2).
The screw can also be anchored directly into the brickwork, into the joint, as a single dowel, as a dowel group, or in plastered masonry. In the specific case of adjusting and aligning beams and sleepers using the new FSW adjusting disc, in conjunction with the UltraCut FBS II 10 US gvz hexagon head concrete screw, timber workers and carpenters can now make those adjustments more quickly and easily than before.
Until now, carpenters, usually in pairs, had to lift the beams and place wooden blocks of different thicknesses underneath them for adjustment. This method is very labour intensive. This is where the FSW adjusting disk comes in, with only a few steps required: Fasten the FSW together with the UltraCut FBS II 10 US gvz through the beam in the concrete, then put a second FSW upside down over the FBS II head, with the notch facing down. Then fasten it to the wooden beam with Power-Fast FPF-PT 5x40 screws, which enables the precise adjustment to be made. The wooden beam is screwed using an impact wrench, such as the fischer FSS 18V 400BL with torque control, aligned with millimetre precision by simply turning the FBS II back. The upper FSW can be dismantled and re-used.
www.fischer.de
With the original deadline for the UKCA certification process having been pushed from 1st January 2023 to 30th June 2025, manufacturers of structural timber fasteners and fixings are being encouraged by Warringtonfire to start product testing now, due to a shortage of approved testing facilities in the UK.
As a leading testing, inspection and certification company, Warringtonfire warns that manufacturers who opt to wait, run the risk of finding themselves with nowhere to test their products, as there are only a handful of UKAS accredited testing facilities in the UK.
Achieving UKCA accreditation can only be done by an approved body listed on the UK Government’s database and the UK Construction Products Regulation states that, from 30 th June 2025, manufacturers of structural timber fasteners and fixings – within the scope of the UK designated BS EN 14592 standard – must successfully complete the testing process using a UK-based laboratory, if they want to sell their products on the UK market.
Ben Sharples, commercial lead at BM TRADA, and sister company to Warringtonfire, explains: “UKCA Marking is very important for the construction industry, as it symbolises that the product being used conforms to the relevant standard.” He stressed the importance for fastener and fixing manufacturers not to be lulled into a false sense of security by the extended certification deadline, adding that only a few UKAS accredited bodies in the UK are able to test fasteners and fixings to UKCA certification, of which Warringtonfire is one.
Any products on the UK market after June 2025 must have completed testing, including products undergoing a change in their specification, such as fasteners and fixings that have changed design or coatings, which will need to be re-tested.
In-line with the situation, Warringtonfire has launched its state of the art Fastener Testing Laboratory, located in High Wycombe, UK, which can undertake assessments of performance
for structural timber fastener and fixing products, so products achieve their UKCA/BS EN 14592 approval. The facility includes a universal testing machine for compression and tensile testing, a series of bespoke testing rigs, and conditioning rooms for structural timber samples, and will offer a range of geometric and mechanical testing procedures for structural timber fixings, such as nails, screws, staples, dowels and bolts. The laboratory can also test steel fixings used to create joints between timber components or to attach other materials to timber.
Ben concluded saying that while many manufacturers already have UKCA certification for their products, many have not, and that as lead times for testing are long, with laboratory availability in short supply, manufacturers should get in touch with an accredited testing facility as soon as possible, “to ensure a smooth transition and prevent any disappointment down the line”.
In the world of zinc flake systems, it’s all about combination. Here, two different layers work together to ensure that steel components are reliably protected against corrosion and that the coating is equipped with additional properties. These two layers are a basecoat and a topcoat.
In automotive engineering, the construction industry, renewable energies, and many other industries, zinc flake coatings have been protecting components in a wide range of dimensions for decades. Despite a low coating thickness, usually only between 8µm and 20µm, it offers a high level of cathodic corrosion protection.
Basecoat and topcoat fulfil different functions in a coating system. The basecoat, which is applied directly to a component, determines the corrosion protection properties. It contains the zinc, which sacrifices itself in favour of the underlying steel if the surface is damaged. The topcoat is applied on the zinc flake basecoat and supports it. It increases the corrosion protection, by keeping corrosive media, such as water, salts or chemicals, away from the surface. However, customer requirements go beyond just corrosion protection. Therefore, a topcoat also provides functional properties of the system. Depending on the component and the demands, a topcoat can provide a coating with different, individually varying characteristics. It can be used, for example, to achieve resistance to mechanical or chemical stresses or abrasion. The colouring is also realised through the topcoat.
When coating components with metric threads, a defined coefficient of friction can be set as well.
With DELTA-PROTEKT ® TC 502 GZ, DÖRKEN has developed a product that focuses particularly on this property.
DELTA-PROTEKT ® TC 502 GZ has been specifically developed for the coating of bolts and nuts. The coating generally depends on the geometry of the component, but the spray process and dip-spin process are recommended. With the topcoat, a particularly narrow friction coefficient window can be set – even with multiple tightenings. Overall, it achieves a high-level of process stability.
Not only were heavy metals such as chromium, lead or cadmium avoided in the formulation – the product is even completely free of per- and polyfluoroalkyl substances (PFAS). The overall package of DÖRKEN ’s latest innovation is topped off with an appealing silver finish and increased corrosion protection.
With this new topcoat, DÖRKEN has addressed the requirements from the market. DELTA-PROTEKT ® TC 502 GZ meets a wide range of friction coefficient windows required in the specifications from various OEMs.
www.doerken.com
DELTA-PROTEKT ®
TC 502 GZ meets a wide range of friction coefficient windows required in the specifications from various OEMs.”Coatings The new topcoat from DÖRKEN is ideally suited to the requirements of components with metric threads
San Shing Fastech Corporation, a fastener manufacturer with 58 years of experience, has announced the integration of AI into its self-developed optical sorting machine during an open house event held at its factory in Tainan City, Taiwan, in May.
San Shing has been investing in AI for over two years, and this year, with the maturity of AI technology, the company has started testing AI in practical production. “Under the requirement of zero defects per million for automotive fasteners, Automated Optical Inspection (AOI) has become an essential part of the inspection process,” explains SanShing. “Through the ongoing research and testing we have been doing regarding the implementation of AI, we have discovered a number of positive effects.”
One of the main positives from AI is the improved convenience and reduced reliance on manual labour. By defining only the defective features, AI can automatically perform the optimal configuration by logging good and defective products into separate folders or selecting the defective features. This eliminates the need for tedious parameter settings and repetitive pre-production tests. It also simplifies the machine configuration process and reduces the operating time for personnel.
Another positive is the enhanced stability in inspections, allowing for slight deformations and contamination of a fastener. “Fastener products are often subject to deformations and may contain oil or dust due to processes like forging. In traditional Designed Rule Check (DRC) methods, there is a risk of false rejections leading to waste when inspecting fastener images,” explains San Shing. “However, AI has demonstrated the ability to identify the features of good and defective products, making it more suitable for inspecting fasteners with slight variations in appearance and optical environments affected by oil contamination.”
Currently, the final testing of AI is underway at San Shing’s sorting
facility and the company estimates it will announce the sales model of the AI optical sorting machines in 2024. In addition to the sorting machines, San Shing has also updated its in-house nut former, tapping machine, and nylon insert assembly machine, to meet the Industry 4.0 and latest CE safety requirements.
“If you have any related machinery needs, feel free to contact us for further discussion. We are happy to share our technological achievements with our customers,” concludes San Shing. www.sanshing.com.tw
One of the largest automotive bolt manufacturers in India recently added a VisionLab 3D Fastener Gauging System, from General Inspection LLC, a US manufacturer of gauging, sorting and inspection machines, to its production in order to streamline its first part inspection process.
VisionLab uses General Inspection’s patented 3D gauging technology to provide complete part dimensional layouts in less than five seconds. The machine can perform 360° dimensional inspection with detailed data reporting, plus options to provide 360° visual defect detection, end view inspection, as well as measure recess depth and recess concentricity.
The bolt manufacturer’s goal was to reduce inspection time, improve quality and cut down on calibration costs by replacing multiple manual gauges, such as micrometers, calipers, and optical comparators, which are inherently subject to human error. With Visionlab the company is able to complete first piece inspections in a fraction of the time allowing employees to concentrate on production tasks instead of manually measuring parts.
“Since introducing Visionlab the manufacturer’s production has significantly increased and errors have been eliminated, with the company able to measure much more frequently,” highlights General Inspection. “All dimensions, including lengths, diameters, radii, angles, and GD&T features, are measured and displayed with a pass/fail indication.”
Custom data reports can also be created and saved as CSV or Microsoft Excel files, but in this case the customer is utilising the ‘My Sequel’ built in server to connect directly to their SPC program. General Inspection underlines this saves time and money plus drastically improves quality by accurately measuring parts within two microns. Part feature tolerances are also assigned with the appropriate part number and stored in memory for quick recall.
Dimac’s new facility in Tortona, Italy, has undergone a remarkable sustainable transformation through the integration of geothermal and photovoltaic systems, showcasing the company’s commitment to reducing its carbon footprint and embracing renewable energy sources.
The installation includes a shallow geothermal energy plant, tapping into the earth’s natural heat for a reliable and consistent source of renewable energy. Underground water reservoirs are also utilised to provide heating and cooling throughout the facility, significantly reducing reliance on non-renewable energy and minimising carbon emissions.
Installed by GEONOVIS, a leading solution provider for renewable energies, the geothermal system utilises an open-loop system, extracting thermal energy from water sourced from the underground aquifer. A heat exchanger efficiently harnesses the thermal energy, with the cooled water returning to the reservoir without any chemical alteration. Further enhancing the system, a double compressor heat pump meets heating demands without the need for fossil fuel combustion or pollution. The system can be reversed for cooling during the summer season, ensuring optimal comfort.
Complementing the geothermal plant is a 65.95kWp photovoltaic power plant on the facility’s rooftop, supplied by SOLAND – a high-end supplier of solar plants. With approximately 335m 2 of PV modules, it generates over 77,000kW annually, reducing dependence on the grid. The solar panels directly convert sunlight into usable energy, contributing to a sustainable energy mix.
“The integration of geothermal and photovoltaic energy systems maximises energy output while minimising environmental impact,” explains Dimac Srl. “It reduces reliance on fossil fuels, lowers emissions and showcases corporate responsibility by helping us comply with stricter environmental regulations.”
“Our energy independence reduces vulnerability to fluctuating energy prices, ensuring long-term stability and resilience. Additionally, any surplus energy produced by the photovoltaic plant can be sold back to the grid, creating an additional revenue stream,” adds Dimac.
Marposs has announced the availability of its data management software, C-THRU4.0, designed to collect and process data from metal forming equipment, such as stamping presses and cold forming machines – equipped with Brankamp devices or T1 terminals.
Marposs’ C-THRU4.0 software enables a direct connection between a production level process monitoring system or T1 terminal and production control with an overarching ERP system to deliver machine, operating, order, maintenance, quality and process data in ‘real time’ to all departments of the company. The data collected can be used to reduce set-up and downtimes, optimise cycle times, increase machine utilisation, as well as document and evaluate process data, all leading to enhanced productivity and profitability.
The direct interconnection with process monitoring provides the production planning with well founded and detailed information, which is not available to conventional production control systems. This interconnection supports automation of workflows, automated report generation, identification of stop reasons, minimisation of set-up times and optimal planning of intervals for orders or maintenance. Production costs and quality are always transparent and traceable through the statistical recording and evaluation of performance indicators.
“Prior to this software we had to review data manually,” reports Joe Bortolameolli, product specialist at Brankamp. “With C-THRU4.0, the machine monitoring information is available in ‘real time’ through the company network, providing a transparent connection between machine, process and production.”
To initiate C-THRU4.0, data collected from the monitoring processes is coordinated with customers’ cost and resource information to provide a dashboard that meets customers’ needs. Any changes coming in from the customer side can be fed back to the forming machine. This interconnectivity and data flow supports the move toward the Industrial Internet of Things (IIoT) and Industry 4.0.
For customers in the metal forming industry, Marposs has also developed the TrendViewer software to provide them with the capability of downstream evaluation of their force curves in the forming tool. Each stroke from each stage can be viewed without gaps in time-lapse and special areas of the curve can be evaluated separately. This provides the possibility to determine
the tool wear of a rolling die for the first time by looking at the first half revolution of the screw.
“Nowadays, process monitoring is an integral part of the digitalisation strategy in metal forming technology. Uniform industry standards such as OPC-UA or MQTT enable us to work together with the customer on the implementation of the digital factory,” explains Marposs.
The monitoring devices of the Marposs Brankamp product line represent an important source of data and a means of communication for connecting the machines to the higher level management system. When analysing the stored process data, new algorithms are used to gain knowledge about the process, the machine condition and the quality of the products. The interaction between the analysis of the process data on the one hand and the production data on the other is an essential step in performing preventive maintenance, increasing tool life and achieving reproducible processes.
“The specific observation of curve sub-areas creates completely new analysis possibilities, as this data can be sent to higher level data analysis software systems by such methods as MQTT. This information, made available for the first time, enables a complete analysis of the individual processes and offers conclusions about process fluctuations, wear or other abnormalities,” explains Marposs.
www.brankamp.com
GEFRA has modified the design of its OPTISORT ST standard steel disk machine in order to inspect underneath the head of screws, based on requests from customers.
GEFRA explains: “One of our customers contacted us and said: ‘We need a system that can also inspect the surface underneath the screw head.’ After receiving similar requests from other customers, we decided to make it our new challenge.”
By tighten the screw with a defined torque, or if the screw also has a sealing function, it is mandatory to have a specified surface condition under the screw head without any impurities, cracks or adhesions of zinc. In some production processes it is not always possible to avoid any defects on this surface. For this, GEFRA’s customer asked for a sorting machine that was able to do all the well known testing of the fastener and additionally inspect the surface underneath the head of the screw.
GERFRA was able to solve this task based on its standard steel disk machine, OPTISORT ST. “The modified design enables the inspection system to take a look underneath the head of the screw, during the same single inspection cycle through the machine,” explains GEFRA. “For evaluation of the defects, all the familiar tools of our reliable and easy to use inspection software AUTOCONTROL can be used.”
GEFRA’s OPTISORT inspection and sorting machines are available in two different basic machine types: OPTISORT ST with steel ring disc for testing fasteners, screws, blind rivets and long rod shaped parts; and OPTISORT W with glass disc for testing nuts, washers, rivets and other flat parts.
New Automatic Combined Machine Model DT20-M
Drilling and Tapping Combined Machines are used to execute complementary operations in addition to tapping. Operations like drilling, boring, facing, chamfering are performed sequentially or in overlapping by exploiting the single positioning/clamping of the part under process. That way the output rate is strongly increased. To obtain a better production yield, it is possible to install 2 (DT20-M), 3, or 4 (DT12-M) working units.
Modularity is at the core of the machine with the two working stations which is enabling two autonomous working areas. The Flexibility is maximized with the possibility to work two geometrically different parts in completely independent processes.
Precision in operation is achieved using a structurally rigid design of frame, along with the engineered and innovative design of the positioning/clamping devices. Orthogonality and concentricity in conjunction with other dimensional/geometrical features, are lifetime guaranteed.
Ask for more information to : sales@hsautomazioni.it
AICHELIN Service has successfully optimised the thermal insulation of two industrial furnaces, after introducing new brickwork for the heat treatment plants of a different manufacturer.
As a long-term skills partner, AICHELN Service has been supporting Daimler Truck AG continuously with regular maintenance and repair works, as well as in projects regarding plant modernisation and optimisation.
In Daimler Truck’s Gaggenau site, in Germany, there are numerous heat treatment plants by different manufacturers, among them several AICHELIN plants. For the current project, the brickwork for a LOI Thermprocess plant needed to be renewed and optimised. The goal was to replace the entire brickwork in a rebuild time of only six weeks, including disassembly and reassembly, while increasing the energy efficiency of the plant and enabling significant energy savings. The result was that AICHELIN Service was able to reduce wall losses by 10% – 15%, with the optimised insulation thus contributing to higher energy efficiency.
Depending on the type and intensity of plant use, the thermal insulation, and in particular the brickwork in industrial furnaces, wears out after around 10 to 20 years and must be replaced entirely. The isothermal annealing system in question – a coherent, U-shaped installation consisting of one high temperature and one low temperature furnace – has been in use at the Gaggenau plant since 1971. The high temperature furnace is gas fired and achieves temperatures of up to 950°C; the low temperature furnace is operated with electric heating elements and reaches temperatures of up to 700°C.
To increase energy efficiency, the brickwork of the two furnaces should not simply be replaced 1:1. In addition to the complete renewal of the brickwork, the wall structure was to be reinforced and thermally optimised. Moreover, further
customer specific energy optimisations had to be implemented. Temperature measurements on the systems before the start of the project provided additional indications of further optimisation potential, including around insulation, the burner flanges, as well as the outlet and door openings.
AICHELIN Service GmbH took over the complete project planning, coordination, and implementation, as general contractor. The time constraints in this project were especially challenging, as a very narrow time window of only 30 working days, including Saturday work, had to be met. To achieve this, AICHELIN Service successfully coordinated four project partners in order to perfectly align and execute the various works.
The project started in November 2022. After the dismantling of the heating elements by Daimler Truck AG employees, the excavation work, as well as other preparatory work, was carried out by AICHELIN Service and its partners, such as the removal and reassembly of the burner flanges, welding work, weld seam tests, and more.
This was followed by the new brickwork and the reassembly of the heating technology before the subsequent test run in cold operation. The brickwork, with an optimised wall construction, was carried out with a suitably strong service team, which put together over 100m 2 of material ‘brick on brick’. In total, around 20 workers from the various partners, as well as the project managers and coordinators from AICHELIN Service and the customer, were deployed during the project. The final work was completed in December. The inspection and approval by the customer were carried out after the successful return to operation in late January 2023.
The post-process data evaluation offers the possibility to analyze and evaluate the entire process data for the first time. Important conclusions can be found about process variation, setting of monitoring limits and recognition of process influences during the whole production run. The knowledge acquired is helpful in determining the optimum process parameters and provides detailed conclusions about tool wear.
Videx Machine Engineering Ltd has expanded the capabilities of its bar-end extrusion machines for drawn and hot rolled bars, with them now available in a diameter up to 100mm.
he Videx Extrusion Machines (VEM) reduce the diameter of bars from major diameter to pitch diameter. The bars are extruded to enable thread rolling in an automatic process, without having to peel or turn the bar ends. The VEM line handles cold drawn, hot rolled (scaled), and ribbed bars, and is available as either independent machines or part of a line. Hand-Feed machines are also available for long bars, headed parts and bent shapes. When extruding hot rolled bars, the extrusion die breaks the scale and draws the bars to the pitch diameter, leaving a clean face that results in good thread quality. The VEM series is equipped with automatic oiling that applies extrusion oil around the bars before the extrusion starts. A typical line starts with a bar shear, which crops the bars to length and chamfers them prior to the extrusion. Other stations available are induction heating, forging of heads and thread rolling. Each model in the VEM line covers a wide diameter range, from 5m to 25mm and now up to 100mm. The VEM models are also available with higher tonnage ratings for upsetting, and heading, and can be supplied with 1 or 2 stations with either open dies and closed, as well as heading tonnage up to 400 tonnes. Fully automatic machines are also available, working from up to 25mm in diameter.
The Nakashimada MST Series part formers elevate your production to a whole new level. Six forging stations, maximum cutoff length of 110mm, maximum kickout of 100mm, soft landing blank delivery, arc-action transfer and a standard NCS-III automated control system. Advanced features engineered to take your cold part forming in any direction.
Increased speed, reliability and extreme precision.
Kistler Group showed visitors to this year’s automatica, held from 27 th – 30 th June in Munich, Germany, how test and measurement data throughout the process chain can play a critical part in resource efficient manufacturing.
Increasingly efficient use of production resources contributes to sustainable manufacturing – and leverages potentials for saving. Manufacturers in diverse sectors of industry need to rely on precise process data as the key to identifying these potentials. To meet this need, Kistler presented solutions at this year’s automatica that not only acquire and evaluate this data for every process step – but also show users the options for optimising their production.
Kistler showcased its diverse portfolio of joining, measurement and process monitoring systems, including innovations such as the highly sensitive 9172CD piezoelectric load cell, the range of mobile handheld test devices and the digitalised 5073B charge amplifier.
Data acquisition for consistent in-production quality monitoring paves the way to enhanced resource efficiency – and this begins with the very smallest forces. In response to this requirement, Kistler premiered its 9172CD piezoelectric load cell at automatica. This preloaded cell can measure compression and tensile forces of up to 1,000N directly after it has been installed. A new piezoelectric crystal developed by Kistler makes this load cell nine times more sensitive than conventional piezoelectric load cells. Because of its high sensitivity and compact design, the 9172CD is the solution of choice for use in demanding applications with small force ranges, such as semiconductor production or the medtech sector – and Kistler points out that thanks to three calibrated measuring ranges, users can rest assured that the measurement data they obtain is accurate.
To give users the ability to check their process parameters directly in-situ, Kistler’s portfolio also includes two new mobile measuring instruments with integrated charge amplifiers. These handheld test devices enable users to compare and verify the data from the sensors they operate with no need to waste time or resources on dismantling them.
The devices record the measured values and visualise the measurement curve on their integrated touchscreen. Model 5811A00 is particularly suitable for insulation tests to verify sensor and cable quality, while model 5811A01 – designed for industrial applications – features three channels for voltage input and IO-Link technology (among others).
The NCFE 2/5 electromechanical joining module is another Kistler innovation that promotes resource efficiency. This compact module is designed for simple but cost sensitive processes; its integrated process control ensures fast set-up and accurate guidance of the joining processes. The module also measures nominal forces in the 2kN and 5kN ranges; its interface with the maXYmos NC monitoring system makes it simple to integrate into the machine’s process environment; and it significantly reduces energy consumption compared to pneumatic solutions.
Kistler’s Joining Competence Centre is on hand to assist with correct planning of these joining processes. The centre offers users the opportunity to have various processes performed and tested with electromechanical joining systems at a test workstation, even before they start planning their systems. Thanks to this service, they can optimise and validate assembly and joining processes to ensure that no problems related to design or over dimensioning will arise either during commissioning or in ongoing operation, and that no costs will be incurred due to conversion work. Kistler’s experts are also standing by to support users with a comprehensive range of advisory support and services – regular inspections minimise downtimes and error rates ahead of time.
To round out its offering at automatica, Kistler presented its individually adaptable turnkey Smart Single Stations. As well as performing high precision process steps and product tests, these assembly and test systems help customers to cut their production costs, enhance their product and process quality, and conserve resources.
Software solutions from Kistler also provide support with achieving these goals. The jBEAM analysis software enables users to analyse and visualise huge quantities of data; and the MaDaM data management solution enables storage of datasets so they can be searched and compared with one another. These solutions open the way to ongoing data-based optimisation of production so that precious resources can be saved.
The desire for support and service has always been part of the DNA of J. LANFRANCO & Cie, which is why the French manufacturer has recently added even more capabilities and equipment to its quality department.
Through the investment J. LANFRANCO believes it has become one of the French flagships when it comes to selflocking safety systems – with the company complying to standards NF EN ISO 898-2, NF EN ISO 3506-2, NF EN ISO 2320 and NF E25-035-2. “Thanks to the investments in our capabilities, and further equipment, our company is able to reach the same level of quality expertise as private laboratories,” highlights J. LANFRANCO. “It guarantees our safety fasteners are designed to meet the highest standards in the railway, mining, nuclear, aeronautical and petrochemical sectors.”
One of the machines that the French company has invested in includes the AUTOMATICA, a new measuring bench that can perform torque/tension tests from M5 to M39 according to quality classes. “We have a new four-way sensor to measure the underhead and in thread coefficient for dimensions ranging from M16 to M39,” points out J. LANFRANCO. “We also carry out tests on imperial dimensions. With the level of precision of this bench, we can accurately measure the performance of the surface treatments and/or Filmogéne offered by our company. This acquisition ensures that our customers comply with the friction coefficients specified in the order, which is vital as this is directly related to the torque and tension in the assembly.”
Another investment by J. LANFRANCO includes the ZEISS binocular machine, which includes a magnification capacity of x 1,000 and the integration of measuring software, which enables the company to directly control the protection thicknesses of its products. “This is a destructive test and enables us to ensure that our products comply with the strictest constraints. The measurement of the minimum thickness on the workpiece ensures a good salt spray (red rust resistance) holding of our products,” reports J. LANFRANCO.
The company concludes: “These acquisitions have enabled us to strengthen our expertise as a manufacturer of safety fasteners. Through these investments, and our involvement in the development of new international standards, our company demonstrates its commitment to remain at the forefront of innovation and to be a major player in the global safety fasteners industry.”
www.lanfranco.fr
ZwickRoell Indentec has introduced a new touch screen Rockwell hardness testing machine, which is available in two variants, the ZHR4150 and ZHR8150, to accommodate either classic Rockwell or combined Rockwell, and Superficial Rockwell, hardness testing respectively.
Zwick explains that these recently launched products build on the long-lasting quality and success of the previous ZHR series and feature innovative touch screen displays to make Rockwell hardness testing even easier and more consistent.
“Like all ZwickRoell Rockwell hardness testers, these instruments support fast, accurate and efficient hardness testing across an extensive range of applications and industries,” highlights the company.
The touchscreen interface has been designed with simple user experience as its guiding principle. Simplifying test set-up parameters, testing procedure, and results handling, all ensure the latest machines are the most efficient and simple to use Rockwell testers available. Incorporating testXpert software, ZwickRoell users will already be familiar with the format and layout, whilst a multi-language option ensures that users can work in a convenient language, selected at the push of a button.
The ZHR interface is available in two variants, the basic interface on the ZHR4150 and advanced interface on the ZHR8150, both utilising 7 inch full colour resistive touchscreens.
The basic interface offers a simple, easy to use and read display, stores the previous 20 test results, features automatic scale indication, multi-language support and the ability to output data to testXpert software, USB stick or computer. The more advanced interface accommodates data statistics and averaging, in and out of tolerance evaluation limits, automatic scale conversions and curvature corrections, histogram display, sample standard deviation display and calculation limits. Both machine interfaces benefit from having the ability to integrate firmware updates through in-situ by ZwickRoell service engineers, enabling the latest firmware to be utilised throughout the lifetime of the machines.
All machine variants are supplied with a UKAS calibration certificate with technical support readily available from the company and cost-effective routine maintenance, and ongoing calibration, can be provided by factory trained engineers.
Instron’s next generation 6800 Series universal testing systems, and Industrial Series systems provide SUPERIOR FRAME STIFFNESS and the DURABILITY needed for testing a broad range of fasteners.
www.instron.com
WHEN FASTENER PERFORMANCE IS CRITICAL...
These training sessions focus on when manufacturers or agents call on independent distributors and how they need to modify their approach in order to be the most valuable resource in the vast quiver of brands supported by the distributor. One of the key areas I touch on in these training sessions is how to work with a distributor when you’re launching a new product into the field – especially how much effort is required to do so. Manufacturers often forget all the nuances required to make that new product introduction a success. Because of this substantial effort, distributors get a little resentful when the product is offered to local competitors too quickly. It can often feel like a kick in the teeth and will cause the distributor to minimise their interest in a new product, or even flat out refuse to bring it to their customers without an already established market. All this could be avoided if the manufacturer stepped back and recognised what was being asked when they expect their distributor partner to pioneer a new product. The most valuable commodity in any market is relationships. Years ago, a wise manufacturer shared something I will always remember: “The person that controls the relationships in the market, controls the
market”. Truer words were not said. It can often be overlooked that distributors have been cultivating relationships with their customers for decades. These relationships are built on trust and mutual understanding of goals. These long-term customers have been relying on distributors to bring quality, time saving solutions to the market. In a great relationship, customers expect the distributor to provide solutions that will help them make more money.
When a manufacturer asks their distributor customer to introduce a new product, or an upgrade, to that end user, they are really asking the distributor to put their reputation on the line. The protection of reputation is paramount to the success of any wholesale
Many of you know me as a trainer of distributors, but I occasionally jump over to the other side of the supply chain and provide training sessions that are focused on helping manufacturers and agents understand the independent distributor.
The person that controls the relationships in the market, controls the market”.
In a great relationship, customers expect the distributor to provide solutions that will help them make more money.”
distributor. Will the product save the customer time and money? Is the new product of a quality standard that it will not cause delays or put that customer is the middle of liability suit? Will the product be available if the customer says ‘yes’? All of these factors contribute to the perception of the distributor relationship.
Beyond the relationship investment, the distributor customer must also invest their inventory cash to support this new offering. Where is this money supposed to come from? Distributors don’t just saddle up to the company ATM and withdraw discretionary funds for new ventures. That money has to come from the reduction of investment in another product. The inventory cost associated with new products can be very expensive. Here is a scary statistic. Out of 10 new products invested in and launched, only 2 or 3 typically become ‘turning and earning’ inventory. The others tend to be dead on arrival. I have asked this question to distribution audiences for the past 19 years. Nothing is more consistent than the ratio described above. One of the common challenges is when a manufacture launches an upgrade to an existing product. What do you think happens to product 1.0 when 2.0 lands on the shelves?
It gets shoved to the side, moved to the top shelf, transferred to the back corner of the warehouse and ultimately winds up as dead stock.
Manufacturers who understand this phenomenon will often develop ‘lift programmes’. This boils down to the manufacturer buying back the old model inventory or funding some sales incentives to burn through the first generation material. Either way, this strategy will go a long way to having a distributor make an investment in the latest and greatest coming out of the manufacturer’s R&D department.
Training the sales team also takes time and effort. Wholesale is not like retail. Just because you put it on the shelves, even at the front counter, doesn’t mean that it will sell. Products need to be pushed. Manufacturers need to arm the team with unique selling features and reasons to share it with the customer base. I have seen a lot of products ‘die on the vine’ because the manufacturer failed to be excited about the new product in training sessions. Most distributors support well over 100 brands. If the rep isn’t excited, why should the distributor bother. Knowing the features and benefits of a product won’t cut it.
Now that I have touched on a few things wholesalers have to go through when launching a new product into the market, and I have definitely left out a few, you might start to understand why a distributor might get a little
irritated when a product lands in the hands of a competitor too quickly. Imagine going out and spreading the word to your relationships in the market, training your sales team to drive the features and benefits, investing thousands in inventory, only to have a competitor undercut the price of this new offering. It certainly leaves a mark. Imagine the
some level of market protection so that they can at least recoup their investment. Would an exclusive territory be appropriate?
A distributor can only dream. This probably isn’t going to happen, especially if the manufacture is a public entity. Short-term exclusivity or even price differentiation may be a more realistic approach. The main point is that when a manufacturer asks a distributor to leverage their relationships to introduce a new product, it is an expensive proposition. If that manufacturer wants to continue using their supply chain partner to launch the latest and greatest, they need to honour the
Jason Bader is a holistic distribution advisor who is passionate about helping business owners solve challenges, generate wealth and achieve personal goals. He can be found speaking at several industry events throughout the year, providing executive coaching services to private clients and letting his thoughts be known in an industry publication or two. Last year, he launched his first podcast, Distribution Talk. Episodes can be found at www.distributiontalk.com and most podcast applications. He can be reached via email at jason@distributionteam.com
Just because you put it on the shelves, even at the front counter, doesn’t mean that it will sell. Products need to be pushed.”
Würth Industrie Service and Dringenberg GmbH have collaborated to introduce the new CPS®KANBAN flex, a Kanban rack system for the seamless, secure and efficient supply of production materials via RFID Kanban.
In addition to previous classic bin levels in the form of typical shelving, the new system opens up a possibility of levels without a base, by using modular shelves with rails. The companies say this intelligent system sets course for a holistic, C-Parts management solution of the future.
The new CPS®KANBAN flex rack has a modular design offering a range of configurations, including the usual shelves, and modular shelves with rails, as well as drawers, or even shelves with dividers to accommodate longer items. Each base can be used individually, depending on different customer needs, and the modules can be reconfigured after each application, if required.
The use of rail technology significantly reduces the fire load compared to conventional shelves, and the rails, in combination with crossbars together with the system’s particularly upright profile, prevent individual bins from slipping unintentionally – so they always maintain their position. The rails are compatible with all bins regardless of the size, with the patented Würth small load carrier W-KLT®2.0 ensuring the absolute flexibility of the rack. Four rack variants with different rack depths (600mm/800mm), rack widths (1,000mm/1,300mm), and rack heights (2,000mm/1,600mm), are available for storing the bins. The standard rack usually consists of two upright frames, 18 traverses and also one iSHELF® base from the CPS®RFID family. If a bin is empty, the integrated shelves detect this immediately via an integrated sender/receiver unit in the shelf. The rack reads the Radio Frequency Identification (RFID) chip and transfers the information about the empty bin directly to the Würth Industrie Service in-house developed, Kanban Management System (KMS).
The grid solution on the front side of the rack gives scope to add more units and with optional perforated side panels or rear panels, CPS®KANBAN flex offers all-round potential for attaching individual accessories to CPS®ORSY factory equipment. In addition to bin fall protection for RFID levels, other attributes include fully extendable drawers with a load capacity of 200kg per drawer; shelves with partition inserts for long goods, such as cable ties or hydraulic hoses or loose items; as well as base panels, rear and side panels (closed or perforated), doors and additional accessories. The new modular system is sturdy with a high load bearing capacity of up to 800kg.
“Under the brand CPS® C-Product Service, Würth Industrie Service offers manufacturing industry customers highly flexible
kanban solutions for efficient and transparent optimisation of existing production processes. In particular, fully automated systems from the CPS®RFID family are well established and proven for replenishing production materials,” explains Würth Industrie Service. “Using RFID enables radio controlled data transmission directly from a customer’s production location to Würth’s central warehouse. With automated and demand oriented reordering of production materials, industrial companies can benefit from maximum supply and delivery security.”
At the heart of all this is the Kanban bin, which, in the case of Würth, is its patented Würth small load carrier, the W-KLT®2.0. This is available in various sizes according to the VDA standard and is equipped with an RFID tag by default, with each transponder easily identifiable through its unique data security number. In the ‘outgoing goods’ process, for example, the ID of a particular bin is linked with the corresponding outgoing goods item. Through the various RFID systems – in the case of CPS®KANBAN flex this is usually through the iSHELF® rack – the ID of the bins can be read and transferred to the KMS for either data transfer or for the automated reordering of C-Parts. The Kanban rack can also be used in combination with other system solutions, such as the battery operated iPLACER®, which is a demand logging module; with the digital rack label, iDISPLAY; or with the weighing bin iSCALE. All these combinations ensure absolute supply security. In addition, ORSY®mat systems used by C-Parts’ partners are also ideal additions to this whole warehousing ecosystem.
Bringing the predictive supply chain into traditional warehouse management is the goal of Austrian start-up TeDaLoS, which is active in industrial logistics and the use of wireless sensors connected to Cloud software – enabling customers to automatically monitor stock levels of everything from small parts for maintenance to raw materials for production.
As part of its business, TeDaLoS is able to supply its IoT-as-a-service business model, which provides location independent, wireless connectivity throughout Europe, and sees clients buy or lease relevant sensors that are connected with TeDaLoS Cloud software.
The ‘as-a-service’ business model enables ongoing costs to be charged as if by subscription, so these operating costs can be scaled up, or down, as required. During the Covid-19 pandemic, for example, this enabled customers to implement urgent projects despite budget challenges, with TeDaLoS “reaching the profit zone” in the middle of the Covid-19 crisis.
This was a period when many companies around the world became worried about stock availability, from material suppliers to industry, as well as wholesalers. However, because its automation technology services are quick and easy to implement, this has resulted in TeDaLoS realising a strong increase in customers from the wholesale sector.
According to Thomas Tritremmel, managing director at TeDaLoS GmbH, the fully automated solution can be put into operation simply, without technicians or IT, and does not appear with the TeDaLoS brand; even the Cloud software can appear in the wholesaler’s online layout as a white
label. “Sensors continuously measure weight or distances in containers, for example. However, no one orders screws and electrical maintenance material in kilogrammes,” stated Thomas. “Just as no one manages liquids in millimetres, according to the fill-level sensor. The Cloud is the universal translator between technology and materials management.”
TeDaLoS is now using this recent business momentum to incorporate AI and new technology into its offering, such as already proven Kanban recording technologies, Radio Frequency Identification (RFID), as well as newer smart sensor devices such as wireless radar, infrared sensors and others. On the data side, investments are also being made in application automation and machine learning based on data.
Thomas highlights that the company’s first AI modules have already been released for customer testing, adding: “Wholesalers don’t want to have to make daily deliveries of small quantities, and customers don’t want to fill up their warehouses. The predictive supply chain, through IoT sensor technology on-site, and specialised Cloud software, saves on staff deployment, warehouse space, and the number of kilometres driven, while still ensuring item availability. Of course, this can also be expressed in CO 2 savings.”
Infor, an industry Cloud company, has provided its CloudSuite Enterprise Resource Planning (ERP) solution to Delta Plus, a producer of personal protective equipment, in order to optimise its management processes.
Arange of other Infor solutions will also be deployed by Delta Plus, including Infor Factory Track TM warehouse mobility functions, Infor CPQ configure price quote tool, as well as Infor IDM optical recognition software – aimed at eliminating the need for supplier invoices. The Cloud environment is hosted by Amazon Web Services, AWS.
Julien Bonnin, CIO at Delta Plus, commented: “Our current IT tools are a hindrance to the development and deployment of new entities, and we wanted to equip ourselves with a modern IT system capable of supporting us internationally.”
He added that the professionalism of Infor’s team in helping define what Delta Plus needed, as well as the technological and functional performance of their solution, were just some of the things behind the decision.
Ronan Douerin, senior account executive at Infor, added: “This project is the result of close collaboration between Infor and the Delta Plus teams. Through workshops conducted with the group’s operational departments, Infor’s value engineering approach enabled the group to identify areas for improvement, which were then presented to Delta’s management committee.”
The project had its scheduled start in June, initially with 1,000 users benefitting from Infor’s new solutions, mainly in the functional areas of sales, inventory and supply chain management, financial and analytical management, and budget consolidation. However, this number is expected to grow as the group deploys and acquires new solutions on a regular basis.
Today, the average car has about 30,000 fasteners and many of them are plastic – coming in a huge range of types. However, the car industry is changing at an ever-faster rate, as we move towards ‘individual transport’ and the evolving requirements that it will bring.
The most apparent change today is the move from internal combustion engines (ICE) to hybrid and electric vehicles (EVs). Why does that affect fastener requirements? ICE servicing usually occurs once a year, but EV motors are rarely touched throughout the whole of their lives. So, the fasteners on ICE may often be released and re-fitted or replaced. On an electric powertrain, many must last for the whole of the vehicle’s life without being touched and this puts a whole new list of requirements on them.
One of the main changes is the application of different materials. Years ago, it was mainly nuts, bolts, and rivets, but now the automotive fastener business is taking on new materials for improved strength and also lightness and reusability – electric motors and batteries are heavy, so any weight reduction is welcome and this affects fasteners as much as any other components.
EVs use fairly high voltages and this may lead to electrical requirements for the fasteners, which was never a requirement on ICE vehicles. This means some EV fasteners have to be coated with insulation. Also, there is pressure for more widely applicable fasteners. With tens of thousands in most cars, it’s welcome if quite a few of them are the same. The development of common fasteners is an increasing requirement. There may soon be no specific fasteners for interior panels and exterior trim pieces – they will be for multi-use.
With fasteners, stronger does not always mean stiffer. In some applications, a degree of flexibility is welcome. Advanced plastics and even carbon fibre composites are under consideration, but the latter can be brittle. Carbon fibre is also expensive. Fastener engineers are focussed on the further development of steel and aluminium alloys for heavy-duty components, as well as engineering new types of plastic. For weight saving, 0.1g per fastener is significant.
Fastener failure is still a significant issue in the automotive field and a fastener with a bit of ‘give’ is often preferable to a more ‘rigid’ one. There are numerous examples when a fastener, although apparently well designed and built out of the best materials, is prone to failure. Even though the particular part has been tested in the laboratory, where it performed flawlessly, it’s a source of constant problems once installed in a vehicle. This is a clear case of misjudgment by the engineers – who looked at the fastener as a single item, not part of the whole car.
When installed in a car, fasteners are exposed to forces, vibrations, and stress, often exceeding the engineer’s expectations. So, it is very important to ‘over engineer’ the part – since they will need to endure forces coming from other sources or parts of the car. For example, a simple bolt that holds suspension components needs to hold everything in place and endure constant forces, vibrations and impacts coming from the road.
Sometimes the fastener design engineer doesn’t fully appreciate the severity of the conditions to which the items will be subjected. Road maintenance has been impacted by the costs of Covid-19 and other unexpected government spending, so in many areas roads are a lot rougher than they used to be and pothole damage is much more frequent now. This situation is likely to exist for some time and it impacts the fasteners on a vehicle just as much as other parts.
Today, there is little difference between OEM and aftermarket fasteners, but the two are likely to diverge. Aftermarket fasteners will probably stay pretty much as they are today, but OEM fasteners will move towards the permanent, more resilient and lighter designs demanded by hybrid and electric cars. Fasteners, such as lockbolts (which are firmly locked when tightened), blind bolts or wire
threaded inserts, all offer better safety, durability and withstand higher loads. Their patents are slightly more complex than for standard rivets or nuts/bolts, but they have superior performance.
It’s important that the right fasteners are available at the right time for the manufacture of the whole vehicle, so the fastener supply chain is of critical significance. Production lines will have innovative processes with minimal downtimes, fully automated stock management and advanced communication between workstations. In such a production environment, fastener supply (and quality) is an essential aspect. Suppliers are creating new kits and assemblies that will reduce the servicing and installation times. Concentrating on the delivery aspect of the fastener industry will help shorten the production times – making final products not only cheaper but easier to complete. Vehicle manufacturers will not want to stop production lines for any reason, certainly not a lack of fasteners.
Introducing and eventually producing new fastener designs requires prototyping as a crucial part of the process. In the prototype stage, engineers use different materials, production processes or approaches and thoroughly test the fastener before giving it the ‘green light’ and shipping the large quantities to OEMs. They are investing state of the art prototyping facilities that makes testing more accurate and gather a wealth of information about specific designs.
Using a digital drawing, firms construct the first prototypes quickly. Those fasteners are not yet ready for thorough testing. However, they are useful for showing the ‘real life’ dimensions of the product, potential design flaws and areas that could use improvement. Then the material is chosen, bearing in mind whether the item is designed to withstand high or low temperatures, high stress, or if it needs to be replaced regularly or permanently fixed in the car.
There is a wide arrange of special materials and automotive coatings that can be used for many applications. Although most might be simple things, precision and accuracy are the keys to transforming the idea into a functional component. Cold forming is a unique way of shaping metal at near room temperatures. This process might be slower and more expensive but offers more advantages in terms of durability and strength of the final product. It is a crucial benefit for customers who develop fasteners made of steel or aluminium.
Clients often need small scale prototype production, so a supplier might provide them with a Minimum Order Quantity
(MOQ) of just 25 pieces. Such an approach, along with high precision manufacturing, provides clients with the chance to try several designs or materials in a short time; gather more data in testing; and make better decisions.
To patent and sell designs, extensive legal work needs to be done. A company may offer PPAP Level 3 and International Material Data System (IMDS) if needed for easier patenting and classification of products. This may be helpful for smaller companies that don’t have legal departments and are unaware of the need for extensive documentation.
The fastener should match the material it is attached to. For example, if high-quality steel screws have plastic washers, it is quite possible that the washer will fail over a long time, leaving a loose screw and potential part separation. So, when installing a fastener or designing a whole assembly, it is crucial to match the materials and have basic knowledge of the forces the fastener needs to withstand. Most of the fasteners used in the engine bay or suspension need to be steel since they are exposed to extreme heat and chemicals. At the same time, fasteners used in the interior or for holding the specific body panels are usually made from plastic. Quality plays an enormous part in the world of automotive fasteners. Just because two pins or clips look the same doesn’t mean they will perform the same and have the same life expectancy. Top manufacturers invest a lot of time and effort in high-quality materials, thoroughly tested in various conditions. The price difference is not there by chance and inexpensive fasteners are often much more costly in the end. Don’t be surprised if the reason for fastener failure is simply poor quality materials or poor production/testing processes.
Even though most automotive fasteners are simple mechanical devices, with pretty straightforward fitting, installation is still one of the main reasons for failure. The most common problem is
over tightening of bolts and screws, which can make them crumble and fail. Sometimes, fasteners are misplaced and installing the wrong one in the wrong application could result in failure and potential mechanical troubles. Even the best designed fasteners made of the highest quality materials are prone to fail. Bolts, nuts and screws are especially prone to heat cycling, and vibration, and even the slightest amount can be a problem over a prolonged period. No matter how tight they might be, if the vibrations are strong enough, the fasteners will fail eventually.
There are numerous cases of plastic fasteners affected by aggressive chemicals used in a car wash or detailing process. Even though the plastic is made to be durable, it is generally not tested for absolutely all chemicals used in car cosmetics. It is a rare occurrence, but it does happen, and it is mainly due to the poor quality of fasteners installed and overly aggressive chemical compounds used.
Steve Wynn, sales manager for Industrial Fastening Solutions at EJOT UK, explains: “Fastener development, product modifications, and new joining systems allied to differing vehicle construction materials and methods, have all evolved and they are part of the electrification revolution we are already seeing. There is a shift in product deployment across the range. For example, the escalation in the need for printed microcircuit boards – usually set into a light aluminium casting – is the domain of EJOT’s micro screw range. These threadforming screws provide the performance at a miniaturised level that designers would normally expect to achieve with much larger screws, as an alternative to soldering, gluing, clipping or welding.”
EJOT’s ALtracs Plus threadforming screws offer advantages for EV applications as they act as heat sinks – removing heat that is dispersing throughout the system – whilst providing a strong and vibration resistant joining.
Steve continues: “Electrification has created a shift in the prevalence of products such as micro screws, which are deployed
already to a lesser extent in ICE vehicles. In addition, the ‘infotainments’ that are prioritised by a new generation of vehicle buyers are also increasing the requirement for these types of joining solutions.”
According to Mordor Intelligence, the worldwide automotive fasteners market was valued at US$22.8 billion by end of 2022 and is expected to reach US$27 billion (€25.2 billion) by 2027. This represents a solid CAGR of above 2% during the forecast period.
The Covid-19 pandemic hindered the growth of the automotive industry across the world. Asia-Pacific, being the largest exporter of automotive fasteners, was deeply affected during the crisis, highlights Mordor. The disruptions in supply chain activities; the interruption of large-scale manufacturing; as well as restrictions on travel; resulted in a slowdown of market.
However, it has recovered well. Japan, China and India are booming in the market – due to presence of automotive giants including Toyota, Suzuki, Mahindra & Mahindra, Isuzu, Dongfeng, SAIC Motor and TATA Motors. In addition, production capabilities have also been improved, which show immense growth potential in the market.
Moreover, growing demand for lightweight vehicles is predicted to provide lucrative opportunities for market players during the forecast period. In addition, as manufacturers are also shifting from standard fasteners to customised fasteners, this new development will help drive demand in market.
Asia-Pacific is projected to account for a notable share of the automotive fasteners market – due to an increase in sale of vehicles across the region. An increase in aftermarket sale of vehicles across the region is also predicted to boost demand for the automotive fasteners market.
So there has never been a more interesting, or more demanding, time to be in the automotive fasteners business. These tiny items look quite unimportant, but are vital to the safe and efficient operation of vehicles.
As electrification takes over, the older designs will disappear and the newer ones will become prevalent. The rate of change may be governed by the tolerance of society to ICE vehicles. Apart from historic vehicles, they may be scrapped a lot sooner than most people think and the automotive fastener business will have to move fast to keep up. The demands on automotive fasteners will also continue to grow as vehicle systems will be expected to last longer and longer without maintenance.
Loosening of nuts and bolts is a problem that unites professionals and hobbyists in a quest for the ultimate, secure bolted joint. Here Nord-Lock Group shows how its wedge-locking washers provided the answer for spare-time drag racer Sam Retke.
Whether designing for massive infrastructure construction projects or getting absorbed in a spare-time pet project, the common goal at Nord-Lock Group is always to secure the bolted joints as effectively as possible.
A prime example is Sam Retke, who for most of his free time can be found in his garage back home in Las Vegas, USA, working on his VW drag racer. A sales representative by profession, he has been racing since 2016 – but had the car racing bug since being a boy. “I used to watch track racing on TV,” mentions Sam. “My uncle Brian was a VW guy when I grew up, so that’s why I got into VW racing. But I’m self-taught, learned from reading articles and watching YouTube videos.”
Sam competes in quarter mile drag racing (approximately 400 meters), where often spectacularly rebuilt and painted VW models race each other. His current car, a 1984 VW Rabbit, hasn’t made it down the track yet, but the initial goal is 10.5 seconds.
This kind of speed is very hard on race cars, especially as they are incredibly stiff and shake a lot. As a result, the extreme vibrations can easily make nuts and bolts come loose. For example, if critical components such as transmission mounts fail, or a bolt backs out, it can change the geometry of the engine or transmission, which leads to breaking.
“I have definitely ‘ovaled’ out some holes due to bolts coming loose,” points out Sam. “I have also had some issues with a few bolts coming loose for accessories bolted to the engine, such as belt pulley tensioner and water temp housing.”
Sam had tried thread locker to solve the problem, but even that didn’t fix it permanently. Then he learned about a more durable solution from a drag racing friend who had used Nord-Lock wedge-locking washers on his 1992 VW GTI with great success.
“I found a hardware store near me that stocked Nord-Lock wedge-locking washers, and I now have nearly one hundred in different sizes in my shop,” highlights Sam. “I use them on basically every location that will accept them, including on critical components, such as the transmission mounts. They are incredibly well suited for any suspension components due to the vibrations.”
The only areas where he doesn’t use the wedge-locking washers are “components that require a special torque procedure, such as 149ft/lbs [202 joules], back off 180°, tighten to 50ft/lbs [68 joules] and then turn 60°. The one I’m currently using outside of the official heat rating is my turbo connection to the exhaust manifold. I’m
not aware of any problems, but I often check as the heat rating is up to 800°F [427°C] higher than the official rating”.
Having VW car racing as a hobby brings a lot of camaraderie and joy. “The VW racing community is pretty close,” mentions Sam. “We go to car shows together and help each other out, for example with parts.”
He adds that the preparing might be the most fun part. “Having your buddy over, drinking a few beers, ensuring everything’s working, and then the lead up to the events.”
The hobby also helped him get through the Covid-19 lockdown with sanity intact. “I had nowhere to be and a lot more free time. So, I’d go out in the garage and work on the car for eight hours a day sometimes. It was perfect to have something to get ‘super deep’ into.”
With things yet again relatively normal, Sam is looking forward to more racing and is constantly working on his car. “When I have a hobby,” says Sam. “I go all in, and I’m never satisfied. So, I always go to a shop to get more things done, such as the cage and more safety stuff, and to ensure I am futureproofing the car to go faster in the future.”
www.nord-lock.com
As car thieves become more sophisticated in their methods, the automotive industry must stay one step ahead by making car parts harder to steal. Here Hafren Fasteners explains how using antitamper fixtures and fixings can not only prevent theft from happening but improve the safety of the vehicle, protecting both the owner and the manufacturer from costly repairs and liabilities.
Tamper resistant fasteners and fixing can play a crucial role in ensuring the safety and integrity of a vehicle, by holding together a variety of components, from engine parts to body panels, as well as security features such as alarms and immobilisers.
One of the vulnerabilities of a modern car is the keyless entry system, with thieves able to use a device to amplify the signal from a car key and trick the vehicle into thinking the key is nearby. Once access to the car is gained, it can be driven away without suspicion. In response, automotive manufacturers have been looking to implement physical deterrents, such as anti-tamper fixings, as part of their overall theft prevention strategies. These fixings, typically made of hardened steel with unique shapes, and patterns – making them difficult to remove without the proper tools, are designed to prevent unauthorised access to a vehicle’s components. This makes it harder for thieves to steal valuable parts that can be sold on the ‘black market’.
“With a long history of providing specialist security fasteners to the automotive industry, Hafren Fasteners offers expert knowledge, advice and partnership in the field of security fastener solutions. Our aim is to stamp out the impact of theft globally.”
www.hafrenfasteners.com
In 2022, electric car manufacturer Polestar and Bulten began a collaboration running up to 2030, in which Bulten will provide fasteners produced in a climate neutral value chain, in order to make the Polestar 0 the world’s first climate neutral electric car.
Andreas Josefsson, key account manager at Bulten, felt it only natural that Bulten should be involved with Polestar 0. “We already have so many aspects in place – sustainable manufacturing processes, access to renewable energy supply, and for several years now, a focus on sustainability in our production chain. We can benefit from the fact that we made the transition to sustainability early on.”
The unique project challenges the early stages of the traditional development process. Polestar has set the project up on a networking basis, with involved parties working together and identifying joint solutions that meet the challenges inherent in the climate neutrality requirement. This places some tough demands on the project parties, but it is also a unique opportunity to be involved in tomorrow’s automotive manufacturing, today.
“We will need to think along new lines. The key to success in the project is the fact that Bulten is involved early on in the process, right from the development stage,” points out Emmy Pavlovic, SVP technology and innovation at Bulten. “We are convinced that we can use our experience and expertise, while also suggesting innovative solutions that lead to the best possible delivery given the need for climate neutrality. Essentially, Polestar 0 highlights the problems that we can best solve together, such as the challenge the industry is facing regarding surface treatment. We
can’t all sit and think in isolation, we have to work together – just as we are doing in this project.”
Polestar 0 is currently in its first phase, research and pilot study, and for Bulten the team initially comprises of expertise in sustainability and innovation. In these early stages, a lot of time is also devoted to establishing a relationship with Polestar, and on collecting data and mapping Bulten’s emission points in its current production process. With time, more parts of the organisation will be brought in, eventually involving expertise from the entire value chain – something Emmy regards as a strength: “Above all, I think that this project will be important internally. It will be clear to everyone just what we can achieve together and that we’re helping to make sure that the world’s first climate neutral electric car leaves the drawing board and actually gets made.”
Collaborating with Polestar, Lesjöfors has designed and developed the pioneering suspension springs on the Polestar 2 BST edition 270 – the limited edition performance car created to push the boundaries of electric performance.
Taking the DNA of the Polestar 2, Polestar explains the BST edition 270 is an expertly tuned, handling focused, limited edition performance EV, hand finished to exact specifications, using select, zero tolerance performance parts.
To meet the extraordinary execution required, Lesjöfors was asked to deliver on the zero tolerance performance parts, developing bespoke suspension springs to secure the performance levels being asked by these advancements in EV frontiers.
Establishing a live workshop in the Lesjöfors factory, in the middle of Sweden, with a Polestar test car, suspension spring designs were manufactured, mounted and tested around the roads of the factory and the suspension spring performance was evaluated and fine tuned between the Polestar and Lesjöfors engineers.
Securing the winning suspension spring, Joakim Rydholm, head of chassis development at Polestar, commented: “It
was so cool to build and test the suspension spring function on-site, in the factory. Lesjöfors’ service is unique. They have a deep understanding of spring precision. They developed springs that were made just for this car – you could almost say handcrafted with generations of spring specialist knowledge that therefore uniquely delivers the level of quality and performance we require.”
Olof Jonsson, sales manager for Lesjöfors AB, added: “When Joakim called us and revealed that his CEO wanted to take the DNA of the hugely successful Polestar 2 and reimagine it into a limited edition performance car, which had to be in production in 12 months and needed some very special springs, we knew we had an exceptional project to deliver.”
Olof continued: “We have a perfect partnership with Polestar. With them, we work as one team. Everyone from the design departments to the material
scientists to the operators on the coilers to the paint shop, all worked and learned together to deliver the results Polestar were looking for.”
The success of the project has led to a new development enabling regular Polestar 2 owners to order a new lowering kit from Polestar, complete with two front and two rear Lesjöfors suspension springs.
www.lesjoforsab.com
INDEX® A Perfect Fixing, a manufacturer and industrial supplier of fixing systems with more than 30 years’ experience, is able to offer a complete range of quality solution for all types of rooftop photovoltaic installations, including in quality EN AW 6063 T6 aluminium and Atlantis C4-M-coated steel.
INDEX® A Perfect Fixing opts for pre-assembled systems and its own profiles, designed to facilitate assembly and maintenance tasks, with new designs aimed at improving performance and reliability.
The incorporation of this new range, focused on the renewables sector, is an example of INDEX® A Perfect Fixing’s commitment to continuous improvement and innovation. “The development of this new range has been a challenging research and innovation project that led to the incorporation of cutting edge technologies in materials/coatings and the need to design new profiles and assembly systems to deliver innovations to today’s market,” reports INDEX® A Perfect Fixing.
The company is also able to provide comprehensive advice regarding the different systems, their suitability for the installation location, custom calculations and component breakdowns. “Understanding the needs of all our users is crucial, which is why we look to offer this technical service,” points out INDEX® A Perfect Fixing. “We are able to provide customers with
technical support for the design and calculation of fixings, as well as the option for site visits and technical training. In addition, on our YouTube channel users can watch installation tutorials for the different installation systems available.”
A large proportion of the products included in the new range are produced in Spain, which is necessary to guarantee the high-levels of quality and innovation required. The company also works with cutting edge suppliers in their respective sectors that adhere to the highest certification standards established by European legislation.
INDEX® A Perfect Fixing is also able to offer customers kits for 2 or 3 panels for the different types of installation (coplanar and triangular). These kits contain everything needed to install panels, eliminating unnecessary products and therefore saving money and avoiding waste. “Through our kit calculator, available on the website, users can select the desired number of panels and it will automatically tell them the basic kit and extensions required to perform the installation,” mentions INDEX® A Perfect Fixing. www.indexfix.com
JPB Système announced important developments that further increase the functionality and accuracy of its Smart Washer device at the Paris Air Show, which took place in June.
JPB Système believes that the development is a “disruptive sealing technology” that can improve MRO efficiencies by reducing the need to manually check torque levels – thanks to a touchless and wireless measurement functionality of bolt axial loads. Engineers can be quickly alerted to fasteners that are too tight, or too loose, and can address them accordingly to limit aircraft downtime.
“While the washer performs the fundamental role of a standard product, it also uses intelligent connectivity by incorporating a proprietary strain gauge, as well as a transmission system into the washer,” explains JPB Système. “This smart reader device relays information directly to maintenance engineers.”
By leveraging improvements in strain gauge technology, the company has been able to respond to the needs of users with a smaller Smart Washer variant that is much easier to integrate and retrofit, while delivering the same functionality benefits as its larger counterpart. The Smart Washer thickness has also been reduced from 7.6mm to 5mm. Its smaller size also enables the new washer
to be used across an increased number of areas within the aircraft, while the original 7.6mm washer has proven itself increasingly suited to experimental scenarios in ‘on the ground’ test environments. The smaller size of the new 5mm Smart Washer also leads to a weight reduction of one-third, which contributes to overall objectives for improved weight reduction, critical aboard any aircraft.
Jonathan Beaumel, mechanical design engineer at JPB Système, comments: “Despite a turbulent three years faced by our own company, as well as many others in the aerospace industry, we have continued to listen to feedback from our Smart Washer beta customer sites as we develop the solution. In doing so, we have directly addressed some important observations and have integrated the appropriate updates to Smart Washer to further improve its functionality and flexibility.”
It is not unusual for there to be uncertainty as to the installed integrity of a bolted joint. A common check, completed to assess whether a nut has been tightened to the correct torque, or whether some loosening has occurred, is known as a residual torque measurement.
This method involves the measurement of the torque needed to rotate a bolt, or nut, by a small angle, typically two to five degrees, in the tightening direction and is normally used by most industries to assess the torque value of a previously tightened fastener.
The advantage of the residual torque approach is that retightening the fastener after the check is no longer required; measuring the ‘break-loose’, or untightening torque, won’t be the same as the original tightening torque, in addition to which, re-tightening would be needed after the measurement is completed. ‘Break loose’ is the term given to measurement of the torque in the untightening direction and is less than the residual torque for a newly tightened fastener. When untightening the bolt, or nut, a lower torque than the tightening torque is needed, since the thread extension torque component assists in the untightening; a parallel can be drawn with it being easier to push an object downhill than it is uphill.
While the term residual torque is usually used, it is somewhat of a misnomer, since there is little, or no torque present in a tightened fastener, rather, the torque measured is a function of the preload in the fastener, the thread geometry, and the friction conditions present. Normally the movement of a fastener is sensed by the person completing the test.
Although not widespread, there are torque audit wrenches available that measure the torque value after a couple of degrees of rotation. Using such a wrench removes the human judgement involved. Alternatively, the fastener and joint can be marked and the nut, or bolt head, rotated until movement is noted. One issue that can arise on longer bolts is
that if the nut is only rotated a small amount, the friction grip between the nut and the surface is broken without overcoming the friction grip between the threads. This results in a significant measurement error.
One common reason for completing residual torque measurements is that some concern has been raised about the integrity of assembled joints. This may be due to a loosening issue having been experienced on one or more joints, or, perhaps, bolt fatigue failures having occurred. Also, the longer the time between completing a residual torque measurement and an installation date, the greater the uncertainty that the torque measured remains a faithful representation of the bolt preload. Over time, on most joints, especially those without a grease having been applied, friction tends to increase. Such a friction increase results in a higher torque being needed to rotate the fastener, which can mask the fact that the bolt preload has dropped below acceptable limits.
Having set out some of the limitations of the approach, residual torque measurements can, nonetheless, often provide crucial information on whether a larger structural integrity issue is present, though, usually, there are few alternatives to completing such checks in order to decide on what action, if any, is needed.
While there may be several other reasons why bolt preload can reduce over time, the detail of these might form the subject of future articles. Online training courses on the technical aspects of bolting are available from Bolt Science.
www.boltscience.com/pages/training1.htm
Haemers, a family company since 1932, is a leading and innovative manufacturer of washers and non-standard nuts – with a range of more than 5,800 different sizes.
In its Belgian factory, Haemers is able to produce both small and large series, from inlays to a fully automated production of ferrous and non-ferrous elements – both from coils and sheets. In terms of dimensions, the company can offer an almost endless combination and this with tolerances from 0.05mm to 0.1mm.
Haemers highlights that all kinds of materials can also be processed, including steel, stainless steel, aluminium, copper and even cardboard. “In addition, harder steels and washers with a hardness of 300HV can also be processed. In this segment, there are never any tooling costs,” explains David Mulnard, who runs the family business together with his aunt Caroline Haemers (pictured below).
Modern machinery forms the basis for Haemer’s highquality products, including eccentric presses, a hydraulic press, guillotine shears and a modern equipped tool shop. Various modern industries such as mechanical engineering, automotive, construction, furniture industry, agriculture, etc, all benefit from the performance and quality of Haemers products.
The Belgian company can also offer customer specific packaging solutions through its fully automated packaging machines for (trade) boxes, plastic bags and jute sacks. “We also offer private label packaging, which is provided with neutral labelling or with the customer’s branding. Details such as the article number, barcode, production date, etc, can be applied too – making everything completely
Although the company will soon celebrate its 100 th anniversary, Haemers continues to invest on a daily basis to guarantee customers an even better service. For instance, early this year, further steps were taken in the automation of press work. “Since March, our degreasing and deburring line for washers and presswork has become fully operational. This has quadrupled our capacity and the machine is almost fully automatic. From 2024, the deburring line should also be fully automatic. This will allow finished products to be transported to our warehouse by AVG or AMR, which we believe is unique in the sector,” mentions David.
In addition to investing in the deburring line, a robot has recently become operational for press work – enabling the company to process larger series and stay competitive. “Alongside our machines, our people are also the basis for our high-quality products,” David stresses. “Various quality checks are carried out throughout the production process and employees are continuously retrained. In the packaging department, the pieces undergo one last thorough final check before being delivered to the customer, which is still done manually. Since 2017, we have also been ISO 9001:2015 certified.”
David continues: “Since wages and transport costs are rising sharply in China and other countries, more and more companies are bringing back production from abroad. At Haemers we make it a point of honour to produce and automate everything as efficiently as possible, which allows us to offer very competitive prices to our customers. Our high flexibility, availability, and autonomy, are the beating heart of Haemers – with almost a century of experience spread over four generations.” www.nvhaemers.be
Precise tolerance
All possible combinations in terms of internal and external diameter
Both small and large series production, already from 50 pieces onwards
Tolerances of 0,1 and 0,05mm are no exception
Washers with a 100% flatness are perfectly possible
All standards, such as ISO7089, ISO7093, DIN125A, DIN9021, DIN7349, AFNOR NFE, KARROS, DIN522 A/C, ISO4759-3, …
The processed material concerns iron, stainless steel, plastics, copper, brass, aluminium and even cardboard
Extended range of packaging solutions in bags, small boxes or pallet boxes. In accordance with the customer’s requests
Private label packaging possible
Growermetal’s range of fasteners has seen an increased number of exclusive designs that join a strong heritage of standard washers, including a combination of geometries and performances – all united by the aim to provide safer and more efficient solutions.
From development to production, from treatments to quality control, Growermetal’s manufacturing system has been structured to meet customers’ expectations in terms of performance, efficiency and safety in every application.
Alongside its production capabilities, Growermetal SpA is also able to supply a wide range of solutions, with its expanding portfolio of washers helping establish Growermetal’s name in the national and international markets.
With more than 7,000 items produced, divided into washers and special parts according to customers’ specifications, the range offers many features – such as high resistance to loosening in the presence of vibrations, dynamic loads, heat, temperature and other challenging conditions.
In terms of functions and industries, Growermetal’s products makes it a trusted supplier for the automotive, railway and aerospace sectors, and many other application fields.
During the last decade, Growermetal’s investments have been focused on updating the production model through advanced machines and R&D projects. Today, the company is exploring new ways to safety, by combining the standard washers of its historical heritage with new designs – an approach that has led to a branded line characterised by exclusive geometries.
Grower TenKeep® is not only the first branded washer manufactured by Growermetal, it is also an example of the new path undertaken by the company. Launched and awarded with 3 rd place at the Route to Fastener Innovation Competition at Fastener
Fair Global in 2019, Grower TenKeep® is the result of hundreds of different geometries tested by the R&D team, with the objective to provide the maximum performance against loosening of the bolted joints.
The result is a safety washer with two differentiated sides, where ‘Side A’ is in direct contact with the head of the screw or nut and ‘Side B’ touches the bearing surface. The two work in combination, whenever ‘Side A’ prevents the loosening of the bolted joint connection, the particular knurling of ‘Side B’ remains solid to the bearing surface without damaging it, thanks to the exceptional grip. In addition, the chamfer on the hole that characterises ‘Side A’ helps the user to orientate the washer correctly.
The different tests, which included the so-called ‘Helicopter test’, proved the washer to be successful even when subjected to dynamic loads or in the presence of severe vibrations – typical of railway and infrastructure applications. Consequently, the performance of Grower TenKeep® is durable, with a high mechanical resistance and a very good level of untightening torque in comparison to the tightening torque.
After being amongst the winners for the 2019 edition of the Route to Fastener Innovation Competition, Growermetal was again a winner during the 2023 edition at Fastener Fair Global for its Grower SpheraTech®
This product is the combination of a spherical top washer and a conical seat washer, which are among the most common locking technologies of the fastener sector. Where does the innovation of this product lie? One of the potential problems related to the use of similar products is washer loss, which is why Growermetal’s team created the permanent assembly of the two parts – eliminating the risk of incorrect mounting and part loss during application.
In addition, Grower SpheraTech® facilitates the assembly while providing the same function of the traditional products, locking uneven or non-parallel bearing surfaces through the compensation of the angle of inclination. Thanks to the pieces coupling, it is possible to reach a superior locking function and preserve the bolted joint connection from damages or breakages – caused by the bending of the head or the shank of the screw.
Recently, Growermetal has added a series of new washer solutions that integrated into the wide portfolio of standard products. Developed by the company’s engineers, thanks to investments in R&D projects, the line includes cutting edge fastening systems.
An example are the high thickness and precision flat washers, which are particularly suitable and widely used in the automotive industry. These special products are engineered and manufactured by the company according to customers’ technical specifications and drawings, to guarantee the best performance for different applications.
Together with these washers, another innovation is constituted by metallic pieces with EPDM inserts. Through the integration of the EPDM elastomer in the composition, the parts benefit from a great resistance to extreme outdoor conditions or high temperatures, as well as an improved compression performance. Growermetal is therefore able to develop and design moulded part projects, where the washer and the EPDM part are costamped or glued, with a remarkable improvement of performance during application.
Finally, in order to boost the flexibility of its offer, Growermetal has specialised in the production of special blanked and bended parts, entirely designed, manufactured and engineered in-house by experienced technicians – following customer specifications. This service leads to the maximum customisation possible of the parts, in-line with demanding applications and the company’s aim to provide the most effective fastening solutions in the market.
www.growermetal.com
As a family-owned business in the third generation, R + FK Schulte KG (rfks) has been a reliable partner for washers, stamped parts and screw locking devices for 85 years –with all its products 100% manufactured in Plettenberg, Germany.
With the aid of more than 50 state of the art stamping machines, and the expertise of well trained specialists, rfks has established itself as a market leader, according to DIN/ ISO standards, throughout Europe. At the same time, the company also distributes special parts according to individual customer requirements as a basic capacity.
“What sets us apart from direct competitors is our versatility and know-how in both worlds. We are at home in DIN/ISO standards, as well as customised special parts,” emphasises Peter Schlütter, sales manager at rfks. “Our in-house construction and tool manufacturing unit enable us to provide individual solutions for each customer – covering a wide range of thicknesses from 0.05mm to 12mm.”
Through constant new investments, rfks keeps up with the increasing demands of the market and its customers. For instance, last year rfks’ CEO Carl Philip Schulte invested in three new stamping machines – two 500 tonne presses and one 250 tonne press, as well as a vibratory grinding centre, enabling the company to increase its production capacity by over 30%.
“Our new vibratory grinding centre provides added value not only to us, but also to our customers. Previously, we often outsourced this process step due to capacity reasons. Since performing this step in-house, we benefit from reduced processing time, increased flexibility and overall greater efficiency in our production. Furthermore, a significant update of our ERP system awaits us this year to ensure even greater warehouse transparency for every employee,” explains Carl Philip Schulte.
“At rfks, we rely on long-term, sustainable partnerships and thanks to our comprehensive service, we are able to support our customers whenever and wherever we can. Through a proactive day-to-day business, as well as continuous communication with our customers, we have positioned ourselves optimistically for 2023 and beyond,” declares Peter Schlütter.
www.rfks.com
J. LANFRANCO & Cie has obtained approvals and certifications from the main manufacturers and equipment manufacturers of the railway, nuclear, aeronautical, mining, and petroleum sector, for safety applications undergoing severe vibration stresses.
In its range of fasteners, and thanks to its double-slot self-locking technology, J. LANFRANCO offers a range of all-metal nuts that are particularly suitable for applications requiring resistance to loosening during stresses and efforts exerted during their use.
The benefits of J. LANFRANCO all-metal nuts for customers include substantial time and labour savings – by eliminating daily or monthly tightening checks of fasteners; compatibility with impact keys, which eliminates the need for specialised equipment such as torque keys for certain sectors; as well as an increase in profits for customers, resulting from the decrease in the number of maintenance checks and downtime linked to fasteners.
Included within J. LANFRANCO all-metal nut range is the ESL self-locking nut, which features two calibrated slots in the top turret of the nut. These slots are located on two different planes and offset by 180 degrees. The nuts are reusable and ensure mounting and disassembly without any loosening or binding.
“In the field of rolling stock, all safety functions are ensured by our ESL nuts and customers are able to reduce unplanned downtime and increase production – all whilst reducing maintenance times,” points out J. LANFRANCO.
Another product within the all-metal nuts range is the THU self-locking nut, which features two calibrated slots in the top turret of the nut – located on the same plane and symmetrically opposite. The THU is frequently used in fixing rail joint bars where the issue of vibration and securing fasteners assembly is vital.
To add to this there is also the ERM self-locking nut, which has a similar design to the ESL nut but includes an added mobile conical washer. The ERM is recommended for all common or safe assemblies with potential for initial tension loss. “The conical washer makes it possible to compensate for the shape defects of the support phase (foundry, etc) and will restore the energy stored during compression and maintain part of the tension in the assembly,” mentions J. LANFRANCO. “Due to this the ERM self-locking nut is widely used in fixing the catenary, switches and electrical connections – where the problem of vibration and electrical continuity is crucial.”
www.lanfranco.fr
Wright, a specialist US manufacturer of hand tools for the industrial, contractor and MRO markets, has recently introduced WrightSquare™, which uses the proven WrightDrive 2.0® technology on the square end of a socket, where it attaches to a ratchet or impact gun.
Wright highlights that its patented WrightSquare™ design provides 10 times more contact area than conventional designs. By relocating load and stress away from corners, it enhances performance and increases socket life. The solutions’ optimised flat contact areas remove forces from a fastener’s corners and optimise the protrusions for each fastener size – to add grip to the wrench.
Using premium Wright-alloy steel increases the product’s strength and, according to the company, precision broaching gives users “the most consistent quality and tolerance levels achievable”.
Tom Futey, president and co-owner at Wright, comments: “The patented WrightSquare™ gives users a noticeable performance enhancement by providing more contact, torque and grip on the square end of the socket.”
Nearly all Wright branded products are US made and carry lifetime guarantees against defects in workmanship.
A new web-based platform designed to simplify and streamline the sourcing process for fasteners and hardware has been launched by eSupplier.com – designed to make it easier for businesses to manage all aspects of their sourcing process from a single dashboard.
The Fastener & Hardware eSourcing Tool enables users to handle multi-currency sourcing with ease and features an advanced cost calculator that provides pricing details for each part supported – with every cost aspect of the sourcing process, from custom duty to shipping costs, automatically calculated. This means the landed cost is provided directly at the user’s warehouse workstation.
The platform also does away with the hassle of manual sourcing work via email, phone calls, or WhatsApp, and provides ‘ready to use’ templates for users to communicate with suppliers clearly and precisely, thereby reducing human errors.
“Whether buying locally or globally, this new platform simplifies the sourcing process,” states eSupplier.com. “The Fastener & Hardware eSourcing Tool also automates various other tasks associated with procurement, such as creating and distributing RFIs and RFQs, as well as evaluating quote proposals. Additionally, if negotiation with suppliers is required, the platform’s automated eNegotiation tool can expedite the process.”
eSupplier.com adds: “The new online platform, which is available now, including a free trial, is designed to save time and reduce errors that might otherwise arise in the procurement process, allowing informed purchasing decisions to be made quickly by managing supplier relationships effectively.”
Cordless rivet guns are becoming more popular and finding more applications in a variety of industrial applications. However, for traditional cordless rivet guns, two fundamental problems exist – that of productivity and safety. To eliminate these, Abrasiv AS has introduced a new technical solution that features a patented electromagnetic accelerator.
Abrasiv’s new rivet gun system, developed and patented by the University of West Bohemia in Pilsen, the Czech Republic, speeds up the riveting process, as there is no need for the mechanical movement of the gun to move the mandrel into the container. The system enables a riveting gun to hold a rivet firmly in any position and reduces the risk of rivet gun damage caused by a blocked mandrel inside the mechanism. On the health of the user, the new system also reduces the risk of carpal tunnel syndrome.
At the heart of the Abrasiv solution is a patented electromagnetic accelerator, which enables the automatic transfer of the rivet mandrels from the mouth of the cordless or electric riveting gun into the container. In addition to this function, the accelerator allows the rivet to be held in the rivet gun without increasing the force required to insert it. The main advantages of the new solution are its high reliability, low energy consumption, the absence of mechanical rods and springs, as well as minimal space requirements. The accelerator is also incorporated directly into the rivet gun without having to re-design the main structural parts. Modifying the rivet gun does not result in any significant weight increase and neither does it impact battery life.
According to Abrasiv, the current solution is original, mainly with regards to the inclusion of the electromagnetic accelerator, and is very reliable for magnetic rivet mandrels. The company also points out that the development of solutions for non-magnetic mandrels is ongoing.
Haeger®, a PennEngineering® company and provider of highly engineered fasteners and fastener installation solutions, has announced the inauguration of its state of the art Haeger® Machine Demonstration facility at its European headquarters in Oldenzaal, the Netherlands.
Designed to showcase the industry leading capabilities of Haeger® insertion machines, the Haeger® Showroom and Tech Centre is now open to industry professionals – offering a unique, immersive environment and opportunity to witness technology in action. From demonstrations and training sessions to plant tours, visitors will have the chance to experience first-hand the power and precision of Haeger®’s solutions.
With cutting-edge machinery, and expert technicians on hand, guests will gain insights into how Haeger® machines can streamline operations and maximise productivity. The showroom hosts Haeger®’s full line of machines, which feature SingleTouch Part Handling Technology. The machines also allow insertion of up to four different fasteners in a single handling of a part. This capability delivers the most significant boost to hardware insertion productivity since the introduction of automatic tooling systems.
“We are thrilled to introduce the Haeger® Showroom and Tech Centre as a dynamic platform for showcasing our industry leading solutions,” said Mary Ann Fleming, president of Haeger®. “This facility
represents our ongoing commitment to innovation and our dedication to providing our customers with the most advanced manufacturing technology available in Europe and worldwide. We invite professionals from the manufacturing industry to schedule their visit and witness the transformative potential that Haeger® machines can provide.”
For nearly 40 years, Haeger® has pioneered and manufactured machines and tooling systems for inserting nearly every type and size of self-clinching fastener. Haeger® states its engineers can solve insertion challenges that no one else can, whether it’s engineering, production, or technical service. The launch of the Haeger® Showroom and Tech Centre aligns with Haeger®’s mission to redefine innovation in the manufacturing sector. By combining industry first technology, unparalleled expertise, and a customer-centric approach, Haeger® aims to empower manufacturers to enhance their operations, achieve greater efficiency, and drive overall growth.
To schedule a visit to the Haeger® Showroom and Tech Centre, interested individuals and industry professionals are encouraged to contact Haeger®’s European headquarters directly.
Here UK-based Hafren Fasteners explores why its specialised anti-tamper security fasteners are an essential part of protecting green energy infrastructure and ensuring a sustainable future.
In the global quest for a greener and more sustainable future, renewable energy infrastructure such as solar farms, wind farms, as well as electrical components, play a crucial role. These vital installations help reduce reliance on fossil fuels and combat climate change. However, securing these valuable assets from theft and vandalism is a growing concern. Enter tamper-resistant fasteners, the unsung heroes of the security world.
Green energy infrastructure, including solar farms and wind farms, represents a substantial investment and a critical part of our sustainable energy ecosystem. Unfortunately, the increasing value of the components used in these installations has attracted the attention of criminals. Theft and vandalism not only result in substantial financial losses but also disrupt the generation of clean energy.
Tamper-resistant fasteners act as a deterrent against theft and vandalism. These fasteners are designed with unique features that make them extremely difficult to remove or tamper with using conventional tools. By incorporating these fasteners into renewable energy infrastructure, it creates a formidable barrier against unauthorised access, reducing the risk of theft and vandalism.
Securing key electrical components, such as control panels, junction boxes, and inverters, is vital for the smooth operation of renewable energy systems. These components are often located in remote or easily accessible areas, making them vulnerable to theft and tampering.
Tamper-resistant fasteners provide an extra layer of protection for these critical components. Their unique designs make it nearly impossible to remove or tamper with the fasteners without specialised tools or knowledge. This added security helps prevent unauthorised access to electrical systems, safeguarding their functionality and ensuring uninterrupted clean energy generation.
Sustainability is not just about clean energy generation; it also involves preserving resources and reducing waste. Tamper-resistant fasteners contribute to the long-term sustainability of green energy infrastructure in several ways:
Deterrence: By incorporating security fasteners into renewable energy installations, potential thieves and vandals are discouraged from attempting to disrupt or steal valuable components. This deterrence factor reduces the
need for costly replacements and repairs, minimising waste and resource consumption.
Extended lifespan: Tamper-resistant fasteners ensure that the components of renewable energy infrastructure remain intact and function optimally for longer periods. By preventing unauthorised access, these fasteners help avoid unnecessary damage, extending the lifespan of the installations and reducing the need for premature replacements.
Minimal environmental impact: Hafren Fasteners prioritises the use of the greenest materials and durability – ensuring that its fasteners withstand harsh weather conditions and maintain their integrity over time. By reducing the frequency of repairs or replacements, these fasteners minimise the environmental impact associated with manufacturing and disposal. Ultimately, the most environmentally friendly materials are corrosion resistant, durable, are high in recycled content, easily recycled, offer long service life, and promote reduced resource use.
As globally we strive to secure a sustainable future, the protection of green energy infrastructure is paramount. Tamper-resistant fasteners play a crucial role in safeguarding solar farms, wind farms, and key electrical components, from theft and vandalism. By incorporating these specialised fasteners, we create a strong deterrent, protecting valuable assets and ensuring uninterrupted clean energy generation.
Not only do security fasteners prevent unauthorised access, but they also promote long-term sustainability by minimising waste, extending the lifespan of installations, as well as reducing the environmental impact associated with repairs and replacements. By embracing these advanced security measures it is possible to safeguard green energy infrastructure and pave the way for a brighter, more sustainable future.
www.hafrenfasteners.com
Hilti’s innovative products have once again been recognised globally for their exceptional design and functionality, with Hilti’s Nuron tools receiving a total of 21 awards, including eleven Red Dot Awards and ten iF Design Awards.
Hilti points out that its Nuron range of products continues to capture the imagination of global customers and award juries alike. The key highlights of the range are the high performing SIW 4AT-22 cordless impact wrench, which is 20% lighter and shorter, allowing for easier access in tight spaces. The B 22-55, B 22-85, B 22-110, B 22-170 and B 22-255 battery platforms also come with a new, industry leading interface and smart housing design to withstand the harshest jobsite conditions, as well as fully potted electronics for better protection against moisture and dust.
Another two-time winner is the TE 2000-22 cordless jackhammer, which delivers the same demolition performance as the corded flagship model TE 2000, but eliminates the hassle of having to find mains power and the risk of trailing cords. The DSH 600-22 and DSH 700-22 battery cut-off saws also offer the same performance as a 60cc gas powered saw but with less maintenance and up to twice the lifespan of a gas powered saw –due to the brushless electric motor. These four products from the Nuron range won both Red Dot and iF Awards.
The all-new Nuron 22 volt platform is the culmination of extensive Hilti research, development, and testing. It can help contractors replace corded and gas powered tools while streamlining the management of multiple tool types. Nuron unifies over 90 tools under a single 22 volt battery platform, with Hilti highlighting they provide outstanding performance, safety and user comfort. “With Nuron, customers can simplify their jobsite operations, reduce costs and maintain productivity without compromising. The platform powers a broad range of tools, including drill drivers, saws, grinders, concrete vibrators, as well as rotary and demolition hammers.”
These flagship Nuron cordless products are viewed as a completely new generation of higher performance power tools that offer better features, such as enhanced moisture and dust resistance, Active Vibration Reduction (AVR), Dust Removal Systems (DRS), battery charge and state of health indicators, brushless motors and much more.
STANDARD LISTED - YOU KNOW WHO’S BEST BUT CONTACT US FOR ALL THE REST...
Non-preferred Metrics ~ Intermediate Sizes
Short and Long Lengths ~ Slotted Grub Screws
A4/80 Bolts & Socket Caps ~ 6 Lobe (TX) Drive Screws
All Metal Self-Locking Nuts ~ Studding Connectors
Online Product Guide: