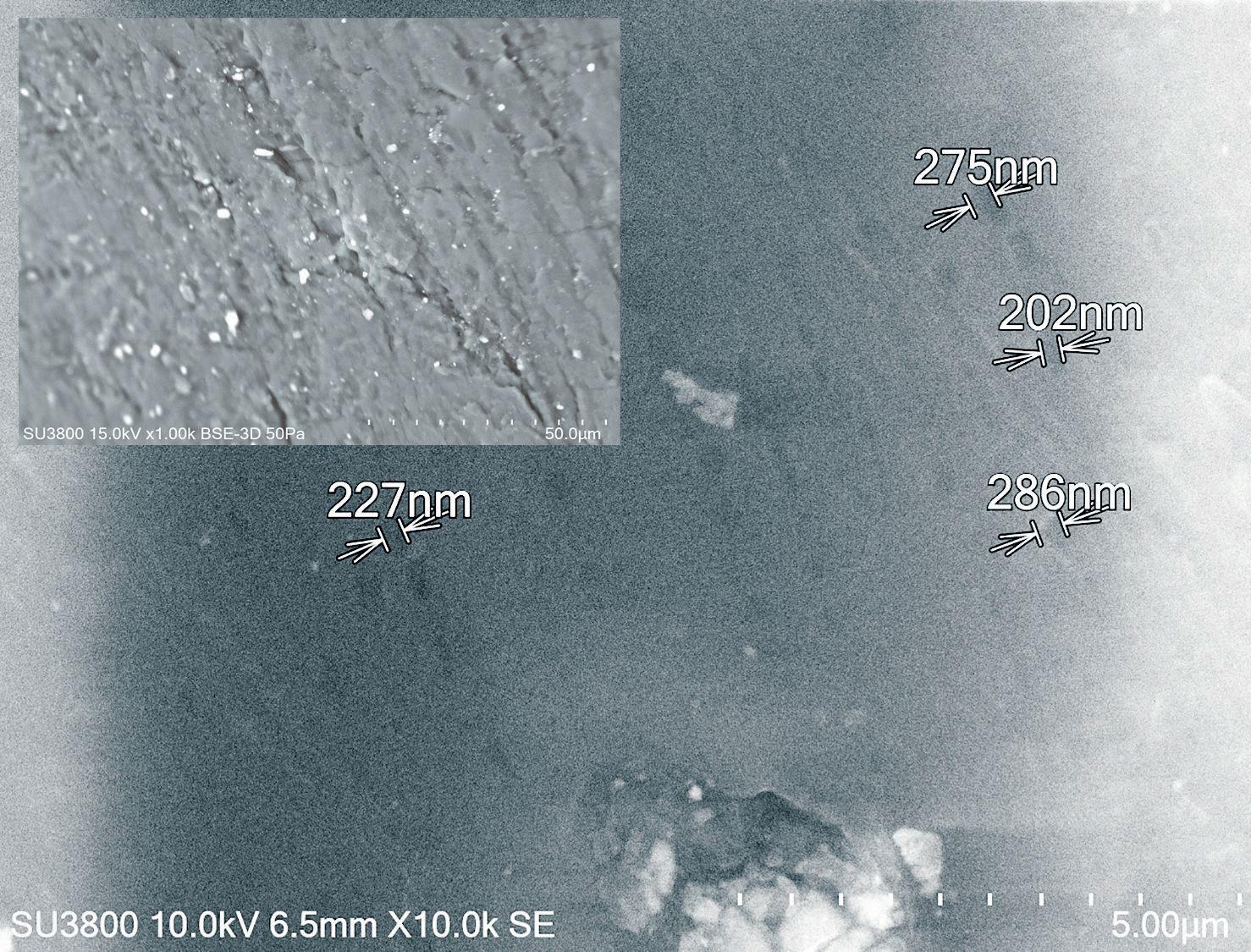
17 minute read
The importance of poroelasticity in soft contact lenses – pt. 2
The importance of poroelasticity in soft contact lenses
Evidence of the pore space of a silicone hydrogel contact lens as transport path for pore diffusion and molecular diffusion – Part 2
Advertisement
Scleral lenses, hybrid lenses or Ortho-K: To ensure safe use of these types of contact lenses, the main focus is on the oxygen permeability of the plastic material of the lens. The metabolism of the cornea and the limbus should suffer as little irritation as possible. The aim of this article is to explain how this transport mechanism occurs and why it is so important. By Alina Kinder
Little is currently known about the pore space in silicone hydrogel contact lenses. The creation of artificial pores or pore space can occur in various ways. The contact lens material is a copolymer, produced by polymerization of a number of different monomers. In the production of copolymer plastics, the type of structure and properties of the plastic are influenced by admixtures. The type of polymerization can also be used to control the size of the pore space. The cooling rates [19] of the individual manufacturing processes – whether they are produced by shape casting, centrifugal casting, or turning – are important for pore space design. Furthermore, changing pressure conditions during solidification of the plastic mass can lead to pores and pore spaces. With the turning process, the plastic material is supplied in solid form, permitting the design of the pore space to be controlled to a certain extent. The polymer manufacturing process does not lie within the sphere of influence of the contact lens manufacturer but rather that of the material manufacturer. In addition, it may be assumed that the first hydration, which transforms the contact lens material from a solid state into an amorphous or viscous structure, allows the actual pore space to develop or be formed. [20] During this process, soft contact lenses undergo a one-time increase in volume of approximately 30% which may correspond to the cavity volume. Thus the cavity in soft material, resulting from pore diffusion
and molecular diffusion, seems to be shaped differently from that in porous solids. It needs to be considered whether the Dk or Dk/t value really is always the same in the different hydration states. [21] When addressing this issue, it should also be clarified whether the Dk/t value needs to take account of the particular state of the aggregate.
Fig. 3: SEM (Hitachi SU3800) photos of the surface of an Efrofilcon A (silicone hydrogel material). Small Inset: Efrofilcon A before hydration; the surface shows surface damage from the blade. Large Inset: Efrofilcon A after the first hydration; the surface appears to have a porous surface structure.
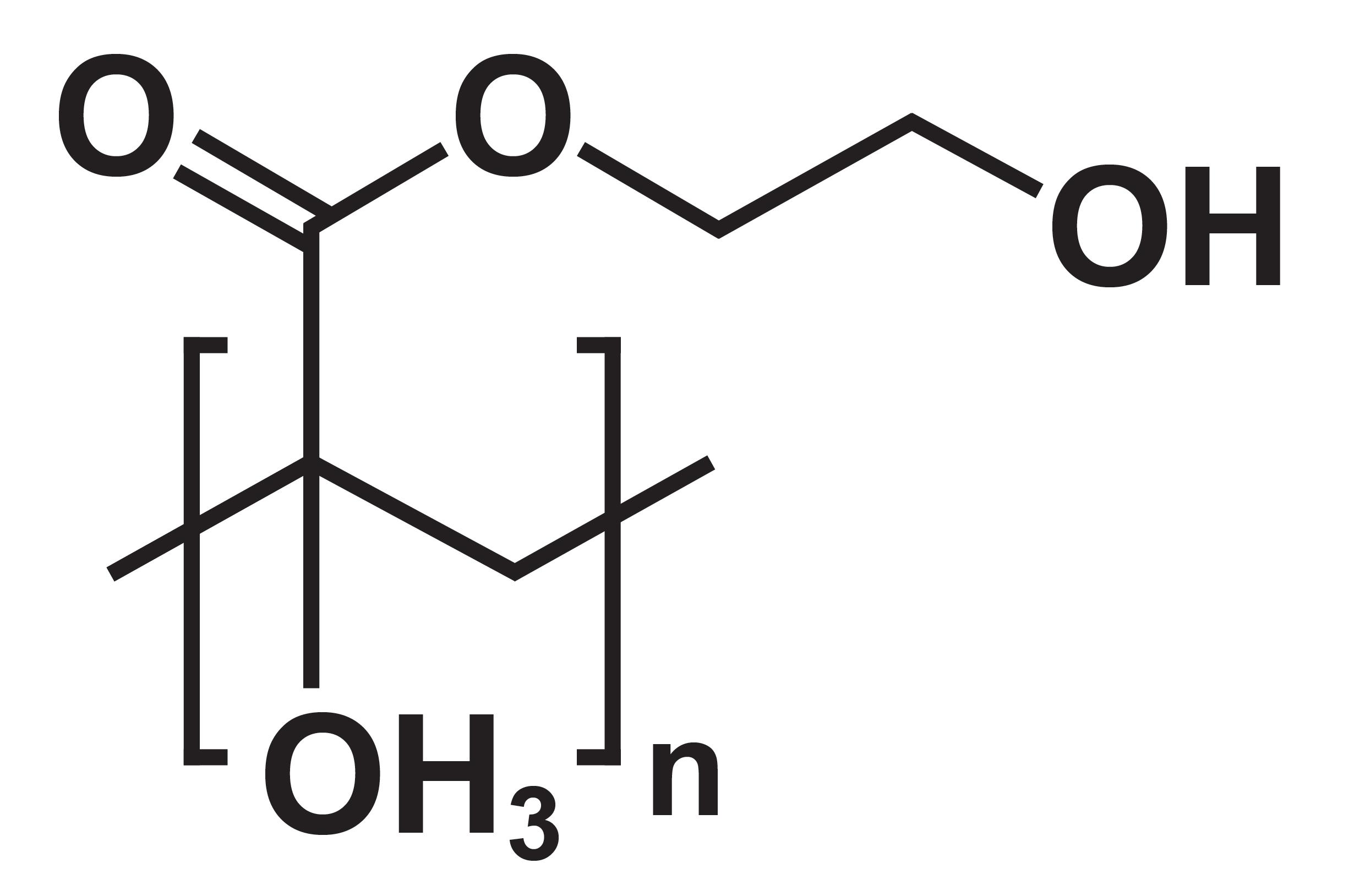
Fig. 4: Poly-HEMA; hydroxyethyl methacrylate polymer. A polymer that inhibits cell adhesion to growth surfaces in cultures. [22]
The type of polymerization and the composition of the individual components of the hydrogel or silicone-hydrogel plastic material are decisive for the material properties, and thus also for diffusion. The production and further development of the polymer material are key challenges for the material manufacturers. The composition of the material determines the wearing conditions of the contact lens on the eye, which are crucial for the health of the eyes. The manufacturing processes of the contact lenses are largely responsible for the geometry, comfort and vision. They are determined by the base curve (BC), the bevel, the size, the mobility and the surface lubricity. This calls for the expertise of the contact lens manufacturer. Different cross-links of the polymers with different properties of elasticity and deformability can be created by the various polymerization processes. A preferred form of the long polymer chains is the random coil, which can change its shape dynamically. This dynamic gives rise to the elasticity known in natural rubber. Structural cross-linking occurs when at least four polymers are bonded together. Due to the regular arrangement and repetition of the individual monomers in a polymer it can be called a lattice structure, although the material exhibits amorphous properties. The definition of the Dk value should be adapted to the likely aggregate state. Furthermore, the term poroelasticity needs to be introduced into contact lens optics, because the structural crosslinking and the resulting elasticity cannot be adequately described by Young's modulus (modulus of elasticity) alone. [23,24] The formation of this cross-linking during polymerization in the polymer material of a contact lens provides soft lenses with a pore space, leading to a corresponding effect on its elasticity. The elasticity of a contact lens is defined only by the modulus of elasticity (Young's modulus). However, in the context of wearing comfort and duration/rhythm, this one physical property is insufficient to fully describe the comfort and deformability during wearing. Thus, to improve wearing comfort, the industry is focusing on the design, surface roughness and coating of contact lenses. Another way to maximize wearing comfort is to modify the structure or composition of the contact lens. An integrated water gradient is designed to make the lens more comfortable to wear. This allows better wetting of the contact lens and improves stability in the core. Despite these efforts, no firm prediction can be made about the influence of the contact lens on the supply of oxygen to the cornea and wearing comfort. Not only the geometry of the cornea and the composition of the tear film but also the condition of the eyelids and the effects of the blink are important. During blinking, when pressure or frictional forces act on the surface of the contact lens, there is a momentary change in the cavity structure and oxygen may be released. The pore space of a contact lens is not a static space. On the one hand, particles/molecules that adhere and then detach again permanently change the volume of the pore space. On the other hand, the expansion and composition of the contact lens cavity depends very much on the surrounding conditions. Soft matter is an amorphous material that can be elastically deformed. During a normal blink, a pressure of 10.3 mmHg/ mm2 is exerted; during a conscious blink, pressures of about 51 mmHg/mm2 may be exerted [25] thus deforming the contact lens. Subsequently, wearing comfort appears to improve (as most contact lens wearers will confirm). This material property could well be defined by the magnitude of poroelasticity. It remains to be clarified whether this blinking effectively "squeezes out" oxygen from the pore space. Further, it also needs to be investigated which, or how many residual particles still in the pore space are detached from the pore walls. The blink of an eye can lead to speeds up to max. 20 cm/s. [26] The frictional force of the eyelid triggers shearing forces which act on the surface of the contact lens.
POROELASTICITY
Against this background, further research is required to determine whether the blink of an eyelid is capable of elastically altering the pore space of a silicone hydrogel contact lens to such an extent that adherent molecules can be dislodged. The term poroelasticity is scarcely used in contact lens optics, although poroelasticity well describes the elastic behavior of a porous plastic as well as defining the stiffness of the porous plastic. In fact, poroelasticity would be the material property that can realistically describe the dynamic behavior of a soft contact lens during wear. Current properties used can only define the contact lens in a static state (in the lab). The improvements in vascularization of the cornea observed since the introduction of the silicone hydrogel material have been attributed to the silicone content, and thus to the apparently improved circulation of oxygen. [27] It needs to be investigated whether the change in rigidity of more modern materials has not also improved the durability of the contact surface. Due to the extreme flexibility of the hydrogel material, very strong frictional forces may arise at the contact surfaces, which in turn may stimulate vascularity. [28] In contact lens optics, the diffusion of oxygen into the tear film
is based on liquid diffusion. However, what has been discussed so far suggests that the transport of oxygen through a contact lens is more adequately described by pore or molecular diffusion than by simple diffusion processes. Pore diffusion and molecular diffusion are processes widely used in physics and chemistry to describe the material property of amorphous bodies. For porous materials, the actual diffusion in liquids or solids does not apply while the diffusion within the pore space is more significant. Pore diffusion takes into account the tortuosity (turns) of the cavity as well as the transport path, which covers a much greater distance than just the material thickness of the contact lens. Molecular diffusion does not leave out of consideration the interaction between the pore wall and the solute, so that the adsorption processes of the solute particles are included in the diffusion process.
ILLUSTRATION OF DIFFUSION THROUGH A PORE SPACE
The pore space itself now needs to be investigated. As a possible experimental approach, colored liquid can be diffused through the pore space as detached particles. This method of liquid staining can be used to demonstrate the effect of pore diffusion within a contact lens. The existence of cavities in a silicone hydrogel contact lens can be demonstrated by studying the diffusion over time (via video). On the basis of the known diffusion coefficient and the measured time, the Einstein-Smoluchowski equation (1) is used to determine the transport distance, which may be longer than the known center thickness of the contact lens.
D = <x>2/2t [m2/s] (1)
The path taken by the oxygen (dissolved in the tear film)
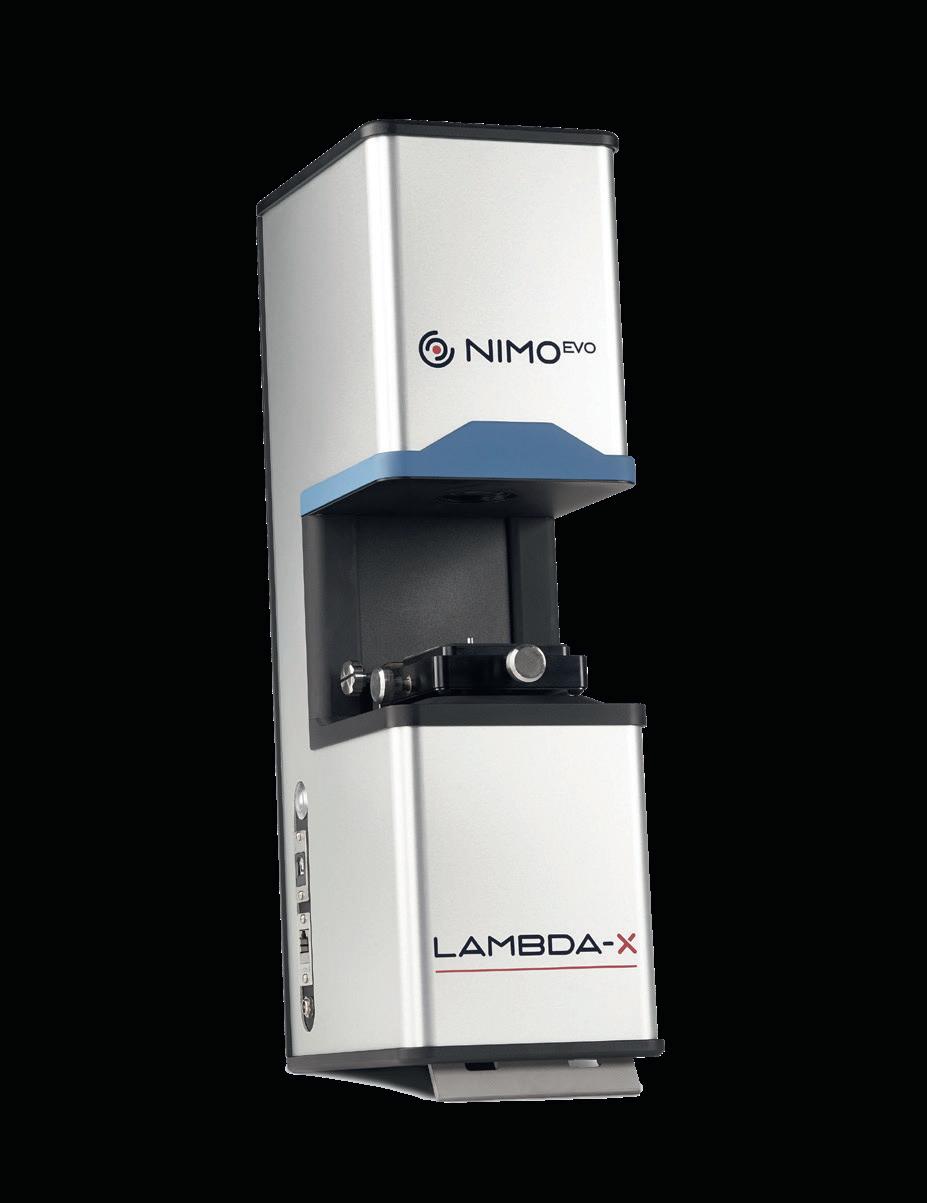
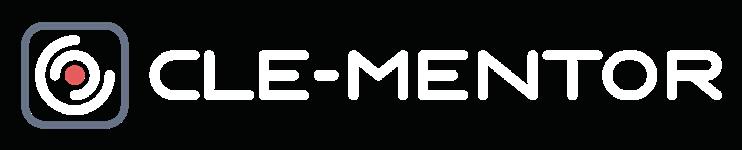
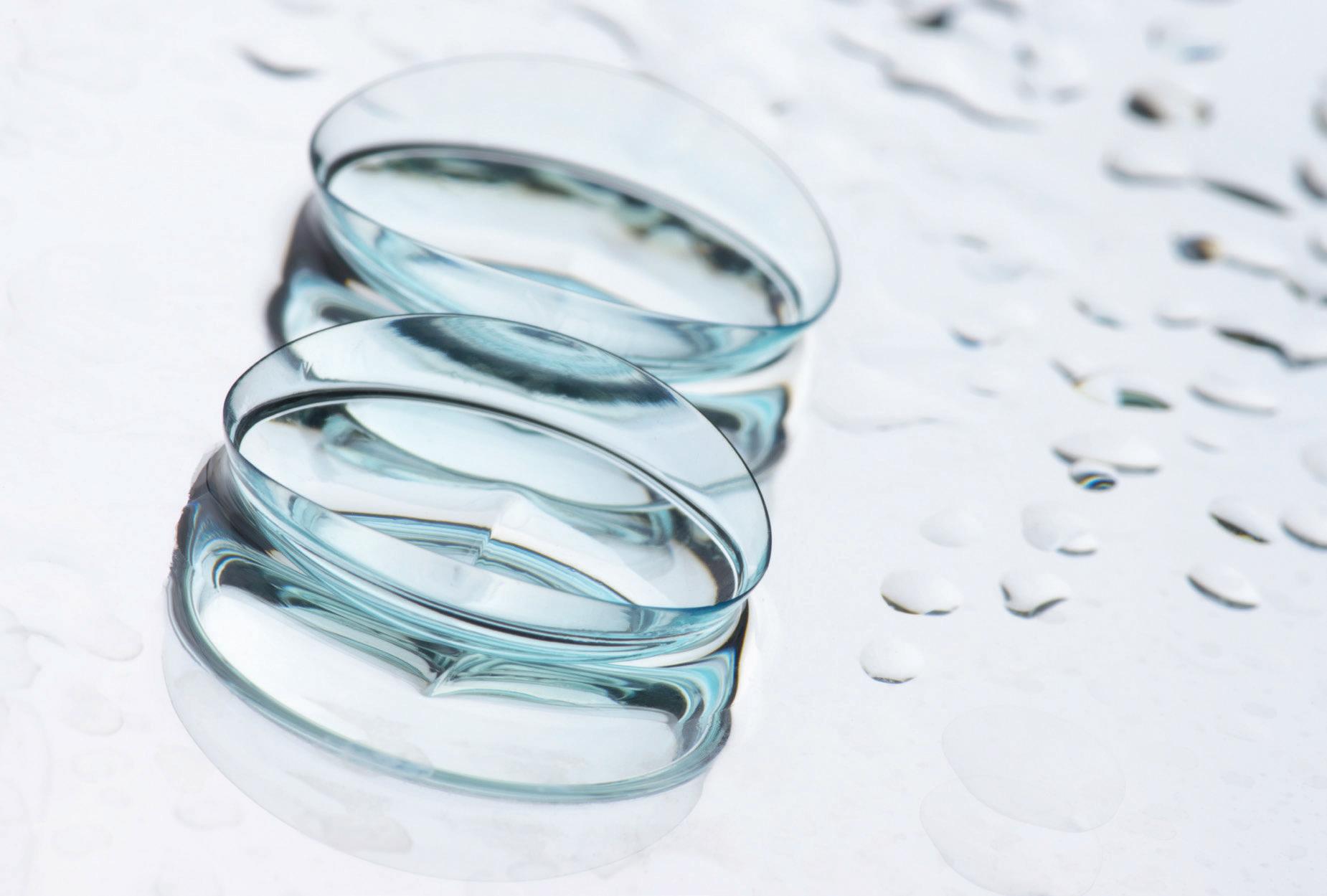
through the contact lens can be recorded and the time evaluated accordingly. Subsequently, the path length x can be determined via the diffusion constant D, which is known, and the measured time t using the Einstein-Smoluchowski equation. As oxygen is difficult to dye, physiological saline solution stained with fluorescein can be used as a substitute. The diffusion of fluorescein is an obvious way of investigating diffusion. To measure fluorescein diffusion, the diffusion path of two contact lenses was examined and compared, in order to demonstrate the effect of pore diffusion.
Silicone hydrogel contact lens Efrofilcon A: • Copolymer of silicone & fluorine and a lactam group N-vinyl pyrrilidone • 74% water content • Dk-value of 60*10-11 ml(O2)*cm2/ml*mmHg*s or a Dk-value of 45*10-11 ml(O2)*cm2/ml*hPa*s (center thickness = 0.266 mm, Ø = 16 mm).
Hydrogel contact lens Filcon II 3: • Copolymer of MMA and a lactam group N-vinyl-pyrrilidone • 75% water content • Dk-value of 43*10-11 ml(O2)*cm2/ml*mmHg*s or a Dk-value of 32*10-11 ml(O2)*cm2/ml*hPa*s (center thickness = 0.225 mm, Ø = 16 mm).
These contact lenses were not coated and differ merely in their base material which in one case was a silicone material and in the other a MMA-VP material.
To prove that systematic errors can be excluded, a reference group consisting of two very similar hydrogel contact lenses was created.
Advertisement
Metrology solutions for CLE
Measuring a contact lens in about one second
The reference group consisted of:
Hydrogel contact lens Hioxifilcon B: • Terpolymer of glyceryl methacrylate • 49% water content • Dk-value of 15.8*10-11 ml(O2)*cm2/ml*mmHg*s or a Dkvalue of 11.9*10-11 ml(O2)*cm2/ml*hPa*s (center thickness = 0.235 mm, Ø = 16 mm).
Hydrogel Acofilcon B: • Terpolymer of glyceryl methacrylate • 49% water content • Dk-value of 15.8*10-11 ml(O2)*cm2/ml*mmHg*s or a Dkvalue of 11.9*10-11 ml(O2)*cm2/ml*hPa*s (center thickness = 0.225 mm, Ø = 16 mm).
These contact lenses, too, were uncoated and differed only in the base material. The Dk value and water content were the same. The effect of the pore space xPD can be determined based on the specified center thickness x and the actually measured diffusion path xerm.
Contact lens
Center thickness of contact lens x [mm] Efrofilcon A 0,266 Filcon II 3 0,225 Hioxifilcon B 0,235 Acofilcon B 0,225
Diffusion path xerm = √(D*2t)[mm]
0,67 0,73 1,61 1,65 Effect of the pore space xPD = xerm/x
2,52 3,24 6,85 7,33
Tab. 2: Influence of the pore space based on the increased diffusion path measured (for given diffusion coefficients). Instead of the assumed diffusion paths corresponding to the center thickness of the contact lenses, 2.52- to 7.33-fold longer transport paths were measured. The Efrofilcon A lens had a shorter path than the Filcon II 3 reference lens, due to the composition of the copolymer material and the resulting different pore space. The control group with the same two hydrogel contact lenses also showed a transport path significantly longer than the actual center thickness of the two contact lenses. The diffusion paths determined for the two contact lenses Hioxifilcon B and Acofilcon B of 1.61 mm and 1.65 mm respectively were very similar due to their similar material composition. When the diffusion constants D and Derm are compared to each other, this results in the effect of pore diffusion EPD.
Contact lens
Diffusion coefficient of fluorescein D [m²/s] Efrofilcon A 0,42*10-9 Filcon II 3 0,42*10-9 Hioxifilcon B 0,42*10-9 Acofilcon B 0,42*10-9 Diffusion coefficient determined from time Derm = x2/2t [m²/s] 6,71*10-11 4,01*10-11 8,93*10-12 7,77*10-12 Effect of pore diffusion EPD = D/Derm
6,26 10,48 47,01 54,04 This table clearly shows that the resulting diffusion coefficient Derm – determined over time – appears to be of an order of magnitude less than the diffusion coefficient D of fluorescein dissolved in physiological saline would suggest. Assuming fluorescein diffusion is conclusive, the pore diffusion in the contact lens made of the silicone hydrogel material is about six times higher than expected; in the reference lens it is about ten times higher. Due to its larger pore space, the silicone-hydrogel contact lens allows faster diffusion than the hydrogel material. In the reference group, the diffusion coefficients found were much smaller, so that the effect of pore diffusion was even up to 50-times greater than anticipated. As far as is known, Fluorescein diffusion as discussed here has never been used to investigate the mode of diffusion through soft contact lens materials. Thus the aim here is to demonstrate the existence, effects and magnitude of pore spaces in contact lenses.
CONCLUSION
Based on the results, when considering diffusion through a contact lens the concepts of porosity and tortuosity need to be taken into account in order to get closer to a more realistic understanding of diffusion. It is now evident that the concept of diffusion in a liquid on its own is not able to describe the complex process of particle transport. Two different diffusion processes take place in the two different soft contact lens materials: In the hydrogel contact lens material, diffusion takes places through the aqueous phase, while in the silicone-hydrogel contact lens it is the interplay between pore diffusion and molecular diffusion that is the driving force behind oxygen diffusion. With diffusion through the water phase in the hydrogel contact lens material, Brownian motion describes the diffusion process, allowing oxygen to diffuse through the contact lens. Random fluctuations of the water molecules are responsible for oxygen flow. The amount of diffusion is temperature dependent. With the manufacturing process of hydration, the contact lens material undergoes expansion. During blinking, pressure or frictional forces are exerted on the surface of the contact lens. This causes a brief change in the material structure, enabling oxygen to be pumped clear. Poroelasticity can adequately explain this "oxygen pumping" process and should thus be included in the description of the wearing comfort of a contact lens on the eye. When considering diffusion in liquids, the viscosity of the solvent plays a role. The equation below refers to the viscosity η of the solvent and not the viscosity of the contact lens material. An increase in viscosity due to particles in the tear film leads to a slowdown of diffusion. The slowdown is not affected by the viscosity of the contact lens material itself.
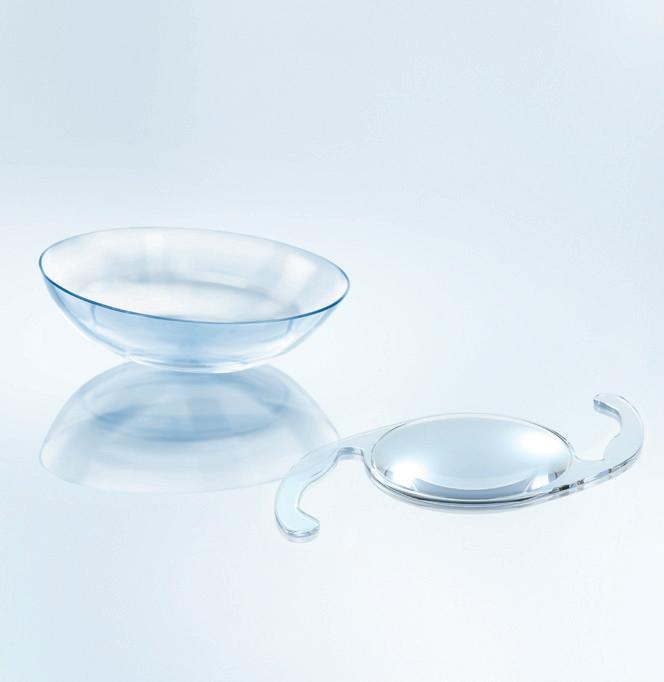
D = kBT / 6ηπR0 kB = Boltzmann constant (1.380649 x 10-23 J/K) T = Temperature η = Viscosity R0 = Hydrodynamic radius (2)
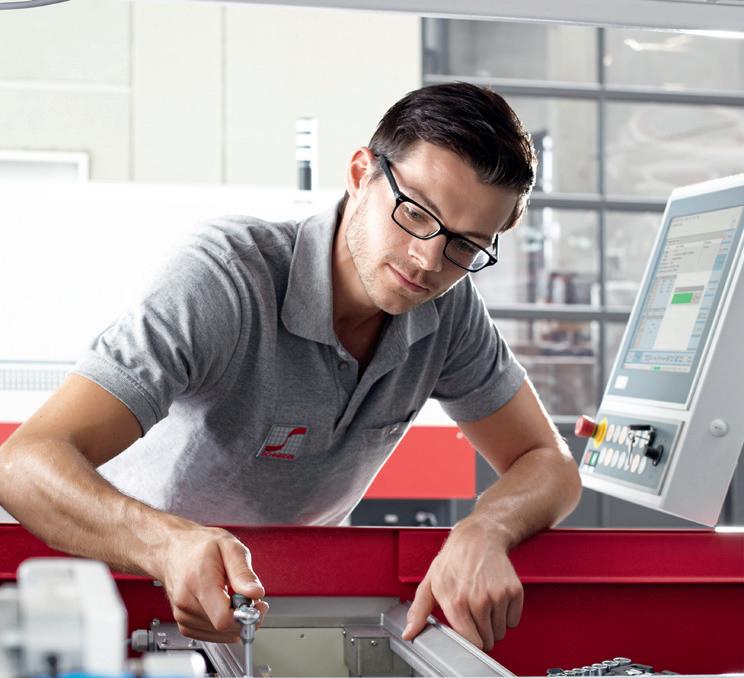
In the fluorescein diffusion above, the fluorescein dissolved in the reference group needed a much longer diffusion time than expected. Here diffusion occurs through the water content in the hydrogel material. The amount of oxygen diffusion via the pore spaces in the hydrogel material still requires further investigation. Two diffusion processes play a major role in silicone hydrogel materials. One of these is pore diffusion, where the solvent diffuses through the pore space. The other is molecular diffusion, which takes account of the adsorption and capillary action of the solution in the pore space. The adsorption of solute particles in the phase or boundary layer of the pore walls changes the extent and nature of the pore space. This process is recurrent and thus does not represent a steady state. The capillary action within the pore space leads to different rates of diffusion which in turn affect the diffusion time. Pore diffusion can well represent the processes of diffusion in silicone hydrogel contact lenses. The interaction of pore diffusion through the cavity, and molecular diffusion which describes the diffusion rate through the shape of the cavity with the capillary action in the pore space, can be described by the material properties porosity and tortuosity. In addition, a more realistic insight into the amorphous nature of the polymeric contact lens material is achieved through consideration of the poroelasticity. The deformability of the material and the related development of forces such as suction and pumping forces in this connection should no longer be ignored. n
This is part 2 of this article. Read part 1 in GlobalCONTACT 2021_02 and in our app.
More information on using the GlobalCONTACT app on page 46
References are available on request from the editorial office or are listed in the GlobalCONTACT app. Advertisement
Alina Kinder (EurOptom, Master of Science (Klin. Optometry)) is a lecturer at the Professional School for Optometry in Cologne (HFAK). She also works as an examiner on the examiner board of ECOO diploma and optometrist (ZVA/ HWK).
Living Innovation
www.schneider-om.com
Design the future with us!
The family-owned SCHNEIDER GmbH & Co. KG is one of world’s leading manufacturers of machines and system solutions in the fields of ophthalmics and (ultra-) precision optics. Known as the pioneer of freeform technology, we set new industry benchmarks by putting a heavy focus on R&D and new technologies. As a full solutions provider, we offer our customers innovative solutions, ranging from the small individual machine to large and fully-automated Industry 4.0 lens production systems. Our company has more than 480 employees and is located in Germany, the USA, Brazil, Thailand and China.
Join our innovative team and apply for: Specialist CL & IOL (f/m/nb)
Location: Fronhausen, Germany
Your responsibilities
_ Take full ownership for commissioning, installation, training, and servicing of our high-tech machines for custom contact lens (CL) and intraocular lens (IOL) production worldwide _ Provide high-level customer support and expert training regarding all technical, quality and process aspects _ Liaise with customers as well as internal departments to ensure satisfactory customer experience _ Collaborate with our specialist departments to support machine optimization and product development _ Enhance internal knowledge and transfer skills internally _ Perform quality assurance and conformity testing of CL & IOL machinery, this includes the evaluation of lens geometries and surface inspection _ Pilot test operation and presentation of machinery _ Test and obtain machine acceptance of contact lens machines, including
FAT & PDQ
Qualifications
_ Technical degree or relevant technical diploma/certificate _ Fundamental knowledge of contact lens or IOL manufacturing processes _ Experience in customer support _ Knowledge of measurement and metrology devices for contact lenses or IOL inspection _ Knowledge of analytical troubleshooting of CNC machinery’s hardware and software functionality
Benefits
_ Interesting and demanding tasks in a highly innovative environment _ State-of-the-art workplaces _ Flexible working hours _ Company pension scheme _ Workplace Health Promotion _ Numerous perks in a number of shops _ High-quality and fresh food offers in the inhouse restaurant _ Employee events
Join our team to shape the future of the optical industry with us!
www.schneider-om.com/career/
SCHNEIDER GmbH & Co. KG
Biegenstrasse 8–12 D-35112 Fronhausen Phone: +49 (64 26) 96 96-360 www.schneider-om.com