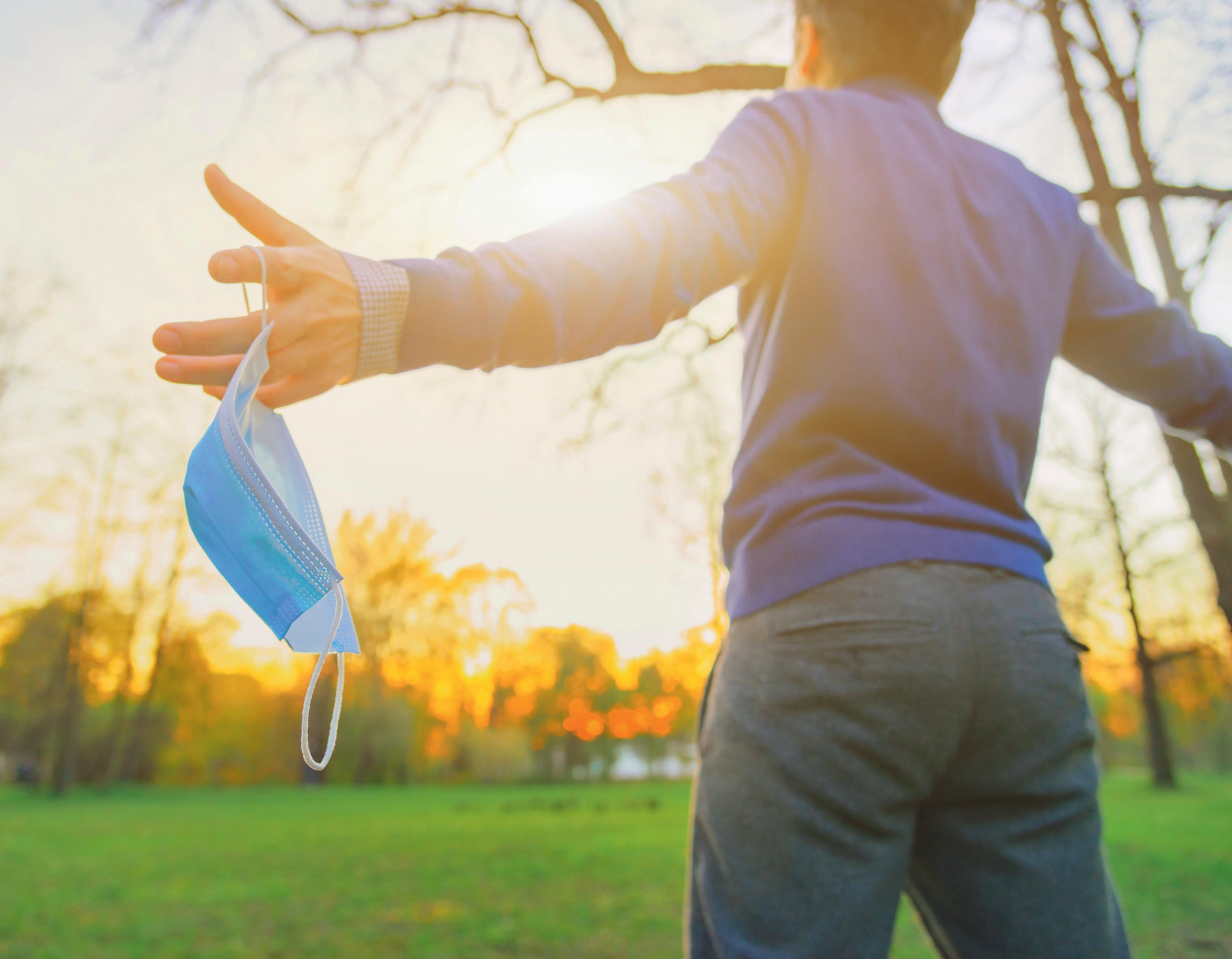
4 minute read
What a difference a year makes
Looking back at an unprecedented time
This article is different from my usual topics of tips, tooling, and technique. I will look at what was going on in Larsen Equipment Design (LED) and in our industry in May of 2020 as compared with May of 2021. I will look at three areas of the industry: Our partner labs, LED business, and LED suppliers. By Erik Larsen
Advertisement
Starting in early 2020, we were beginning to hear from our partner labs about their business situations. Orders were starting to slow, and the future was not clear. We at LED saw a similar trend. We saw no indication that our suppliers were having problems with filling orders to us. By May of 2020, business was very different along with every other aspect of daily life. Most of the labs saw an extreme down-turn in business as did our suppliers and us. Many of the labs and our suppliers put their workforce on furlough. This situation would prove to be a concern later in the year as orders started increasing requiring the workforce to return.
ORDER BACKLOG
in a similar fashion. We as machine tool manufactures however, operate on a weeks-long delivery schedule. In May of 2020, we had a backlog of work of about four weeks. While this situation was uncomfortable, we all had work to do. As we entered June, our backlog was two weeks, but we had orders to fill. As it turned out, June was the lowest month of work in-house for us. We did have an unexpected increase in business from a few labs that had lost local suppliers due to the general downturn. These labs needed custom items (tooling, replacement parts, etc.). Another source of orders were the medium size and multinational companies who were progressing with their plans as were set prior to the pandemic. Mergers and acquisitions continued. Typically, we see orders soon after these transactions are completed. Plus, we get to develop relationships with the
new engineers and staff. The over-all benefit of this additional business may have just enabled us to keep everyone at LED actively employed. Another source of work was research and development, both internal and for customers. Some customers decided to go ahead with projects as they saw the pandemic providing a window of opportunity. According to our government’s criteria, LED is an essential business, so we were able to stay open.
SOCIAL DISTANCING
It occurred to me that our partner labs, we at LED, and most of our suppliers share a working arrangement where each person had a cubical or workstation that is at least 6’ (2 m) apart. This arrangement, along with no retail customers, allowed us to fit in with the distancing requirements. May of 2021 has shown an almost complete reversal (both plus and minus) as compared to May of 2020. Most labs have seen a return of orders, but for various reasons, many needed to hire new people who require training. This situation puts an additional burden on lab managers. We saw a gradual upswing in orders after a level summer of 2020 and business has steadily grown to a current backlog of orders of 10-12 weeks. We have been able to weather the pandemic with our team intact but with administration staff working from home, which they still are.
SUPPLIERS
What effect has the pandemic had on materials and components? I have not heard from any labs about a shortage in lens material or consumables. Similarly, local utilities seem to have been able to maintain their services. However, costs may have fluctuated. At LED, we source material and components from a few dozen suppliers. These range from raw materials to purchased components. For raw materials, we use plastics, metals and wood. We have seen single digit percent price increases for plastic and metals, but up to 500% for wood used in shipping crates. Of course, these costs are a very small part of our over-all costs. Purchased components – electronics, motors, bearings – have seen price increases in the single digit percent and availability has remained at a few weeks. We do have a few suppliers who do post-processing of our in-house manufactured components. With our region being an aero-space manufacturing centre, it was hit hard by the pandemic and other problems. Our post processing suppliers are heavily tied to the aero-space industry. They furloughed a large part of their workforce. In the last few months, we have seen the usual turn-around time of a week grow to 3-4 weeks due to a lack of trained workers. We have been able to absorb the delay in our 10-12-week lead time, but we are managing the situation more closely to maintain the delivery schedule.
To say that we at LED have been fortunate is an understatement. We are also happy to see the optical industry and our suppliers returning to pre-pandemic business volumes. I am optimistic that our industry and associated businesses will come away stronger. n
Erik Larsen graduated from the University of Washington with a Mechanical Engineering degree in 1981 and started Larsen Equipment Design later that year. Erik Larsen has industry awards from CLMA and EFCLIN.
Advertisement
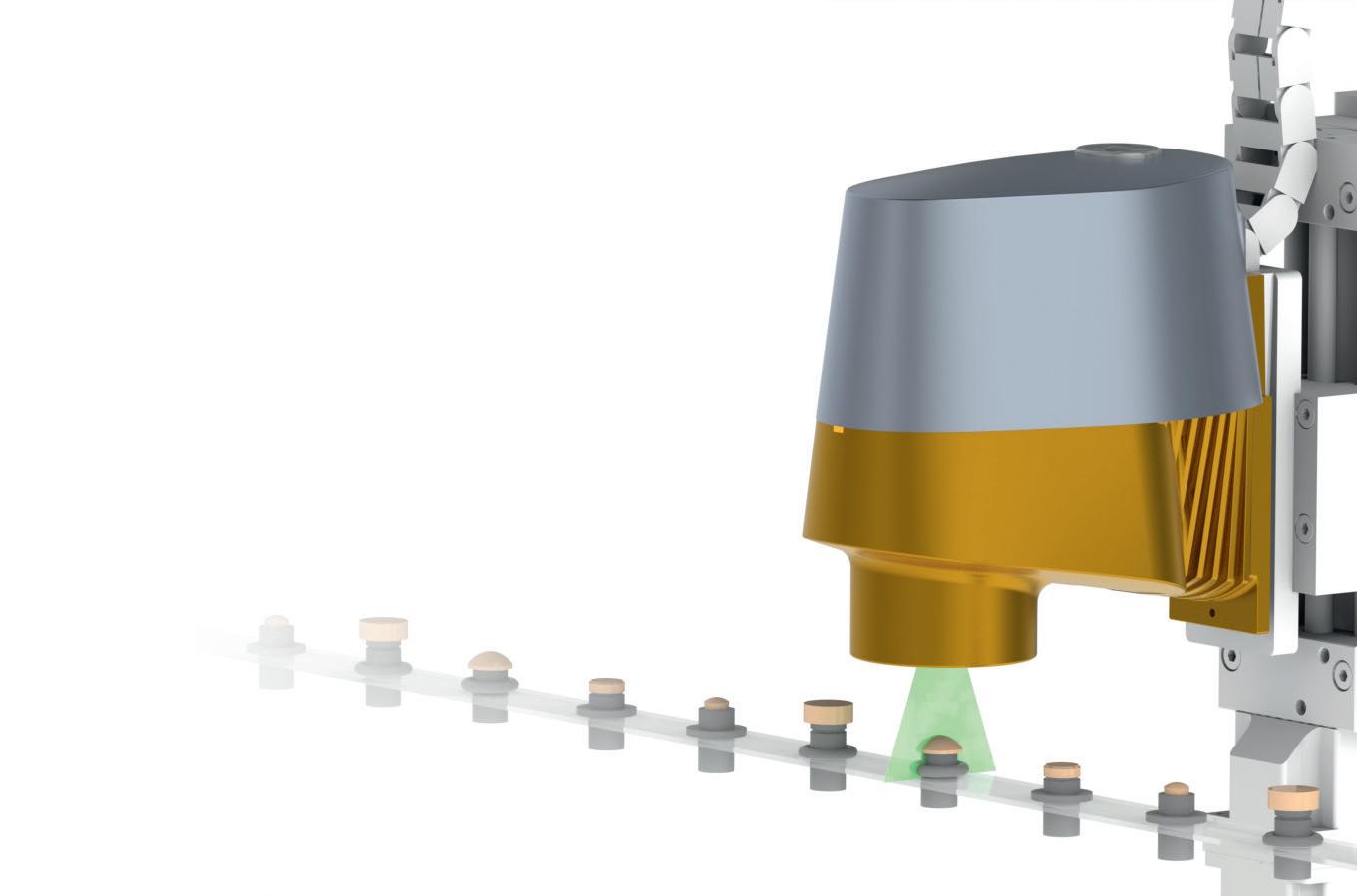