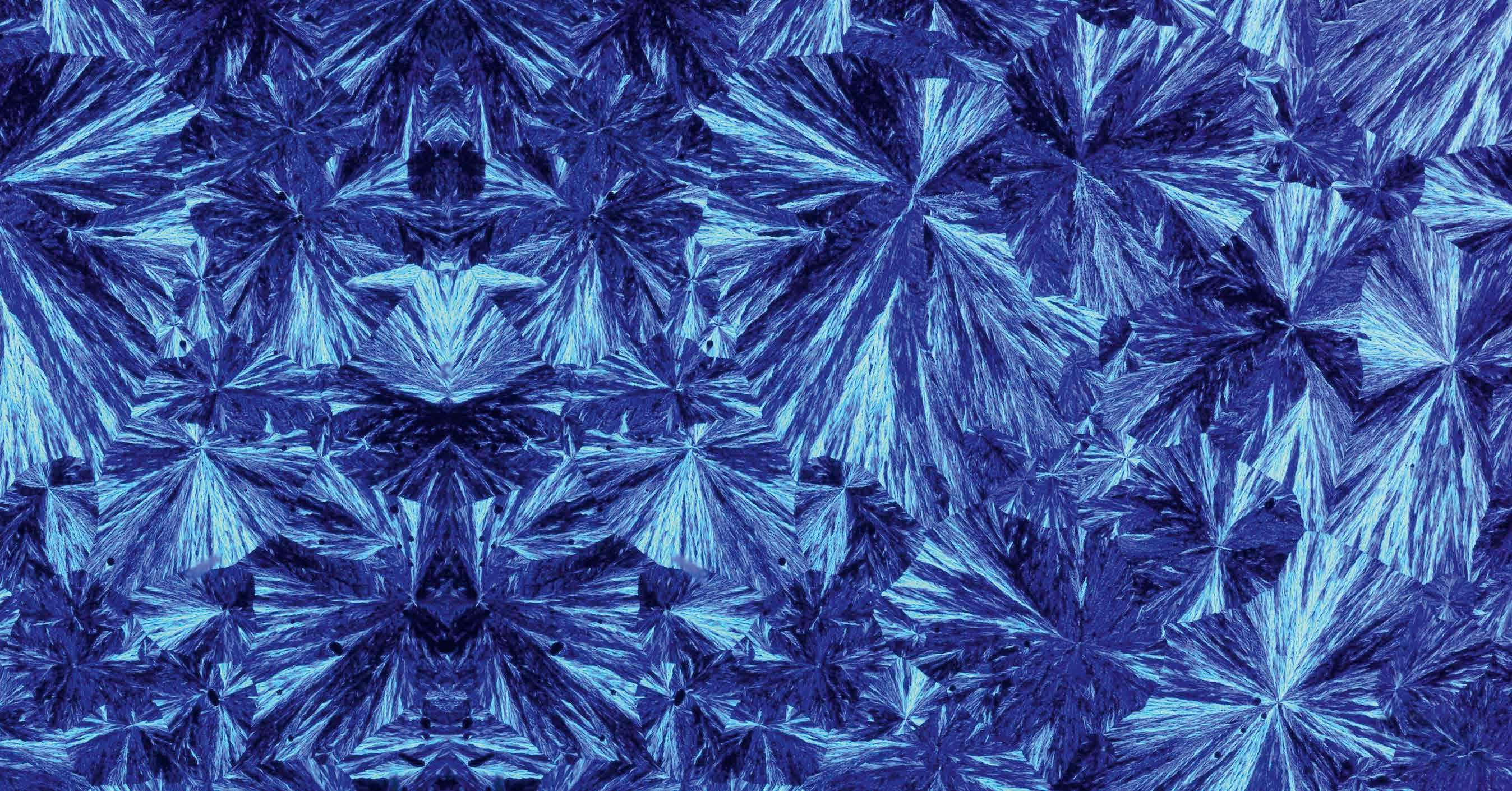
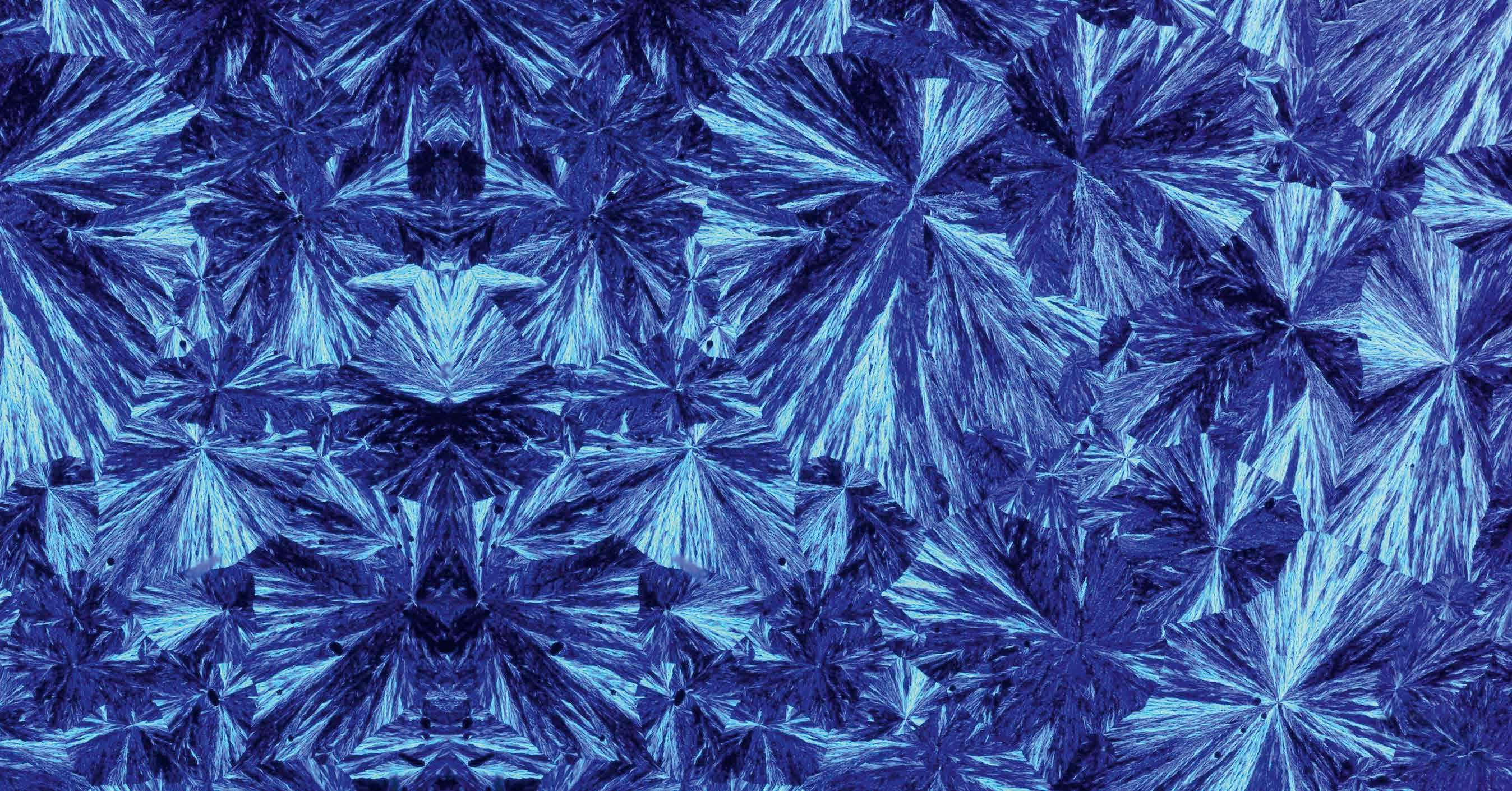
Breaking Ground in Sustainable Polymers: Solvent-Free Coatings

As sustainability gains importance, researchers at DTU Chemical Engineering in Denmark are developing innovative, solvent-free coatings to transform the industry. Professor Anne Ladegaard Skov and her team are working on new silicone-based coatings with industrial applications, aiming to reduce environmental impact while enhancing performance and scalability.
By focusing on cyclic silicones and polydimethylsiloxane (PDMS) ring polymers, these scientists aim to create solvent-free coatings that are both high-performing and environmentally friendly. This groundbreaking work not only challenges conventional polymer synthesis but also opens new doors for scalable, sustainable industrial applications. Professor Anne Ladegaard Skov and her team, alongside with Hempel A/S as collaborators focus on creating relevant silicone-based coating containing no or less solvent than the currently available coatings.
The initial aim of the project was to create liquid coatings without the use of solvents. Traditional coatings often rely on volatile organic compounds (VOCs), which contribute to air pollution and pose significant health risks. By eliminating solvents, the team sought to minimise environmental impact while ensuring no residual stress in the materials and avoiding the release of toxic VOCs.
The research revolves around developing a thixotropic system—a material that becomes less viscous under stress and returns to its original state at rest. This property is particularly desirable for coatings, as it ensures easy application and stable performance. The team’s work combines long linear polymers with cyclic polymers, leveraging their unique properties to develop advanced materials with enhanced elasticity and performance.
Innovative Synthesis
A key breakthrough in the project was the development of a simple, one-pot reaction to synthesise cyclic silicones. These reactions resulted in the synthesis of both single rings and a network of rings. Initially, the focus was on single rings, as the team aimed to achieve threading, where linear polymer chains would penetrate through cyclic molecules to enhance structural integrity. However, threading did not occur as expected, which prompted a strategic pivot. Since the threading did not work as intended, the researchers decided to explore an alternative approach. They developed a network of interconnected polymer structures by combining two types of PDMS—one with
vinyl groups and the other with hydride groups. When mixed and exposed to a platinum catalyst, these compounds react to form strong, flexible networks that provide the desired mechanical properties for coatings without needing threading. The synthesis approach achieves impressively high yields and represents a significant improvement in scalability, making the technology viable for industrial applications. The team has also made strides in characterising these new polymer networks, a crucial step in understanding and optimising their performance.
Environmental Impact and Sustainability
The environmental implications of this research are profound. By eliminating solvents, the new coatings reduce the release of harmful VOCs into the atmosphere.
Additionally, the use of non-traditional materials further enhances the sustainability of the process. These innovations align with global efforts to mitigate climate change and reduce industrial pollution.
Moreover, the scalability of the synthesis process ensures that the technology can be adopted widely, amplifying its environmental
“A key breakthrough in the project was the development of a simple, one-pot reaction to synthesise cyclic silicones. By minimising waste and improving the lifecycle of coated products, these innovations contribute to a more circular economy.”
The Challenge of Threading
One of the primary hurdles in this research was the unexpected lack of threading. The researchers initially aimed to achieve threading—a process where long polymer chains penetrate through cyclic molecules to enhance the viscosity and structural integrity of the blend. However, they did not observe the desired threading behavior, which led them to shift their focus toward creating a polymer network instead. By carefully controlling the synthesis process and refining their approach, the researchers were able to develop a viable network that maintained the desirable characteristics of the polymers without relying on threading.
benefits. The team’s commitment to sustainability is evident in their efforts to create materials that not only perform well but also contribute to a healthier planet. The long-term environmental benefits extend beyond the direct reduction of VOC emissions. The coatings are designed to be durable, reducing the frequency of reapplications and the associated environmental costs. By minimising waste and improving the lifecycle of coated products, these innovations contribute to a more circular economy. Additionally, the ability to manufacture these coatings at scale means industries can adopt them without significant
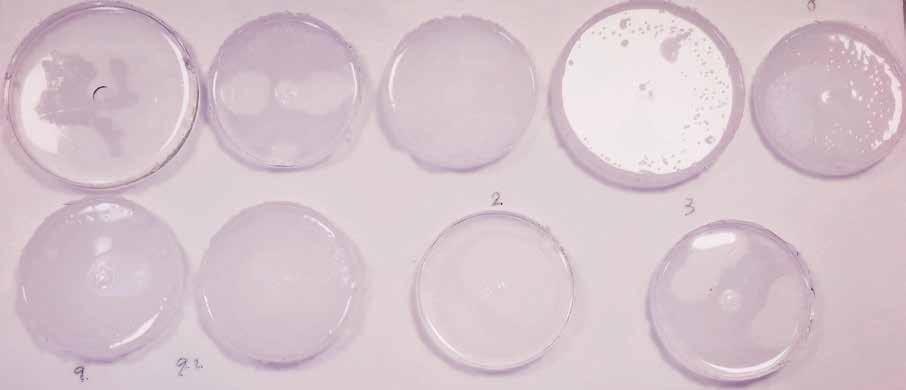

modifications to existing systems, ensuring smooth transitions and widespread adoption.
Applications and Future Directions
The potential applications of these solventfree coatings are vast. Industries that require protective coatings, such as construction, marine, and automotive sectors, stand to benefit significantly. The materials are particularly suited for large structures exposed to harsh environments, such as seawater and wind.
One exciting application is in marine environments, where coatings are critical for protecting ships and underwater structures from corrosion and fouling. Traditional marine coatings often contain harmful substances that leach into the water, affecting marine ecosystems. The solventfree coatings developed by this team offer a safer alternative, ensuring durability without environmental compromise.
The next step for the researchers is to optimise the system further by incorporating fillers to achieve specific properties required for coatings. This involves fine-tuning the formulation to enhance performance while maintaining sustainability. The team is also exploring the integration of additional functional properties, such as anti-fouling and self-healing capabilities, which could revolutionise the industry further.
Challenges and Resilience
Despite the significant progress, the journey has not been without challenges. The initial issue of threading posed a substantial obstacle, requiring innovative solutions and persistence. Additionally, characterising a completely new type of polymer network demanded meticulous research and experimentation.
Another significant challenge lies in bridging the gap between laboratory-scale research and industrial-scale production. While the synthesis methods have shown promise at smaller scales, scaling up without compromising quality or efficiency requires continuous optimisation. This process involves not only refining the
LIQUID COATINGS
Liquid coatings without the use of solvents
Project Objectives
This project aims to create coatings without toxic volatile organic solvents, reducing the release of harmful substances into the environment. In pursuit of this goal, we discovered a new material with intriguing properties and have dedicated significant time to its development and characterisation. This new material shows great promise in formulating a completely solvent-free coating.
chemical processes but also ensuring that the production infrastructure can support the new materials.
Furthermore, the transition from laboratory experiments to market-ready products requires addressing regulatory hurdles. Industries adopting these materials must meet stringent environmental and safety standards, adding another layer of complexity. The team is actively engaging with industry stakeholders to facilitate this transition, ensuring compliance without compromising innovation.
Transforming Polymer Science
The development of solvent-free coatings using cyclic silicones and PDMS ring polymers represents a paradigm shift in polymer science. By addressing critical environmental challenges and pushing the boundaries of material innovation, this research paves the way for a more sustainable future.
As the team continues to refine their materials and explore new applications, their work serves as a testament to the power of science and innovation in solving global challenges. The coatings industry, and indeed the broader field of material science, stands on the cusp of a revolution driven by these groundbreaking discoveries.
The journey of creating solvent-free coatings from cyclic silicones and PDMS ring polymers underscores the potential of innovative science to address pressing environmental issues. By eliminating harmful solvents, achieving high-yield synthesis, and ensuring scalability, this research not only enhances industrial capabilities but also aligns with global sustainability goals. With further optimisation and application development, these materials promise to leave a lasting impact on industries and the environment alike.
As industries worldwide grapple with the dual challenges of performance and sustainability, the work being done in this field offers a beacon of hope. The integration of cyclic silicones into scalable, high-yield processes marks a significant milestone, one that could inspire similar advancements across other sectors of material science.
Project Funding
This project is funded by the Independent Research Fund Denmark under grant agreement 1127-00282B.
Project Partners
• Hempel A/S
• Professor David R. Clarke, Harvard University
• Professor Dimitris Vlassopoulos, Foundation for Research & TechnologyHellas (FO.R.T.H.)
Contact Details
Project Coordinator, Anne Ladegaard Skov, Professor and head of the Danish Polymer Centre, Department of Chemical and Biochemical Engineering, Technical University of Denmark. Søltofts Plads, 227, 122 2800 Kgs. Lyngby
Denmark
E: al@kt.dtu.dk W: https://www.kt.dtu.dk/research/dpc
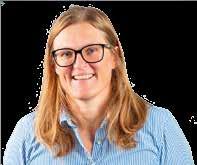
Anne Ladegaard Skov is Professor of Polymer Technology at the Technical University of Denmark, where she is head of the Danish Polymer Centre. She is internationally recognised for her group’s work on silicone polymers and elastomers for advanced applications, including wound care, coatings, and soft robotics amongst others.
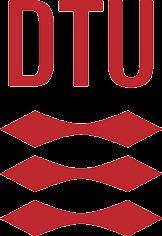
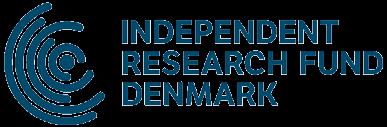
Anne Ladegaard Skov
The Danish Polymer Centre (DPC) Group, Technical University of Denmark, 2024.
Polydimethylsiloxane (PDMS) ring polymer film samples.