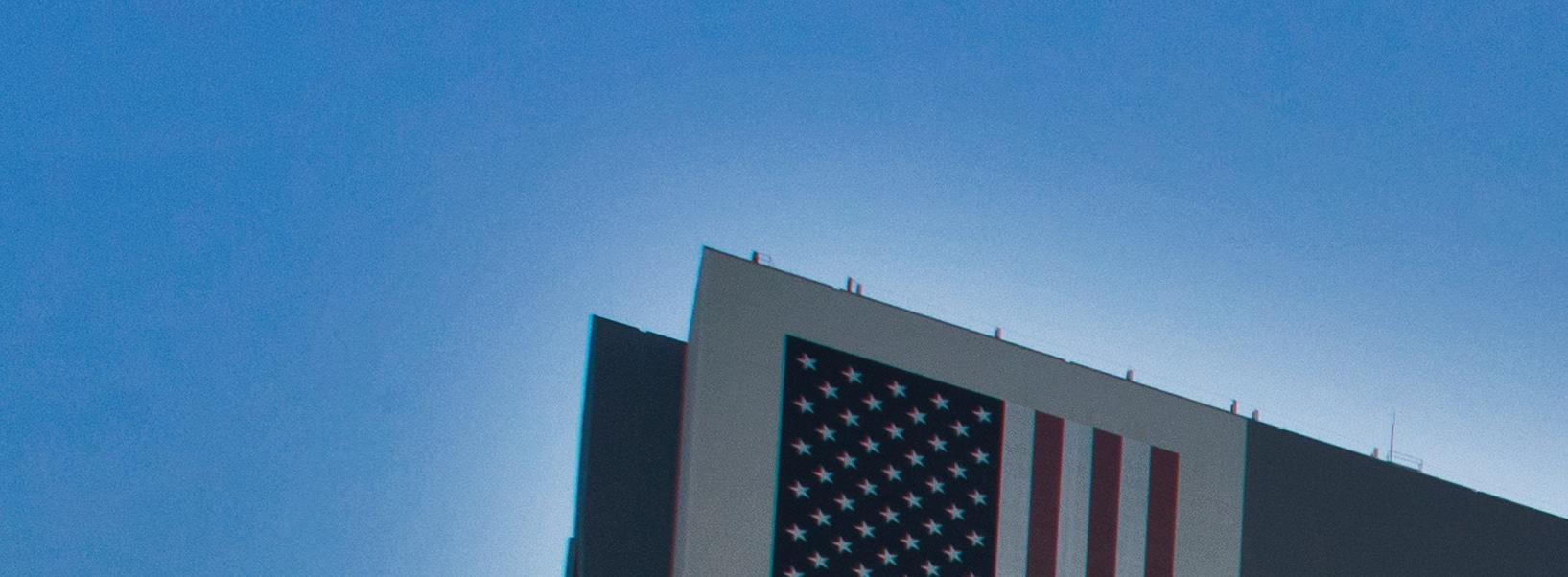
7 minute read
Ever Evolving, the VAB Readies Missions for the Moon, Mars and Beyond
BY JOE VANHOOSE, MANAGING EDITOR
Editor’s Note: For more stats about NASA’s Vehicle Assembly Building, be sure to check out ASCE’s write-up on Page 14.
As the Element Operations Manager for the Vehicle Assembly Building at NASA's Kennedy Space Center, Elizabeth Kline gets to call the VAB her office.
There aren’t any windows to look out of, but the view doesn’t suffer. The sheer size of the building – over 129 million cubic feet of volume – makes you feel like you’re outside, and the view above could be of the rockets that will ultimately take Americans back to the Moon and farther.
But it’s her coworkers and the scores of people working inside the VAB that make the iconic structure such a special place, Kline said.
“They get excited about what we're launching into space; it's really exciting and the work is a lot of fun, and we enjoy doing the work,” she said. “I know that during the Apollo program, those people working then were feeling the same excitement just even when they were building the building.”
The first crew of workers on the VAB were so excited that they left behind a message. There is a neatly written note on a beam on the ceiling of the building, out of sight from anyone on the bottom floor and out of reach for anyone except those who would have put the beam there.
On the beam is written a simple objective: “To the Moon.”
“It was the coolest thing I ever found, and you can't reach it so it had to be done while the building was being constructed,” Kline said. “So that was in the Apollo days.
"And I still feel that excitement in this building from everybody. There's an energy to this building in the work that we do.”
Evolving With New Missions
In her role, Kline is responsible for preparing the iconic facility to support flight hardware processing for Artemis missions.
“The work here never ends, it never ends,” Kline said. “It's a 1960s building that's close to the beach, and it’s mostly made out of metal, so it rusts a lot.”
Kline started working at Kennedy Space Center in 1993, first as an operations and mechanisms engineer for Lockheed Martin. In 2006, after NASA announced the end of the Space Shuttle program, Kline joined NASA as an orbiter project engineer. In 2012, she started transitioning and retiring components from the Shuttle program.
“So, we went through everything then in the VAB, everything in the OPF (Orbiter Processing Facility), and we also turned over some of the facilities to other programs that would be able to use them, but we kept the Crawler Transporter Facility because of course we're still going to use crawlers,” Kline said.
Going through everything in the VAB was a particularly huge job because the same process wasn’t undertaken after the Apollo program. Kline and her team even found a lot of mid-century furniture.
“There were offices we found that looked like people from Apollo just sat their stuff down and left, and it was all still there,” she said.
There are other components that are still original to the building, like the 2,000-ton bridge crane on top that needs to be upgraded. Replacement parts are hard to come by.
Other components from Apollo were modified for the Space Shuttle program. The platforms in the high bays that served the Apollo rockets weren’t quite right for the Shuttle, so they were removed, modified and then used in a different order.
“The problem with that is every time you had to retract one of the platforms, you were retracting a bank of two or three platforms,” Kline said. “For the Artemis program, we put in a whole new set of individual platforms, so whenever we needed to retract a platform, it was so much easier because you could just retract one and not have to retract a bank of three.”
New Solutions For New Rockets
For the assembly teams to be able to work on the new Space Launch System (SLS) rockets in High Bay 3, the new platforms had to be able to move in close, retract and re-connect as segments are added, and retract for the Crawler Transporter to move the rocket on the Mobile Launcher out of the VAB to the launch pad.
RS&H designed 10 levels of work platforms engineered to encircle the SLS vehicle at determined mating, testing and integration points along the vehicle. Each half of the giant steel platforms measures about 38 feet long and close to 62 feet wide, weighing as much as 325,000 pounds.
“To put it in perspective, you can park 20 Ford F-150s on one half of a platform, so they are huge.” said Andrew Nelson, vice president of Aerospace for RS&H.
The design incorporated 20 common platform frames to improve fabrication economy, paired with two sets of custom vehicle-specific inserts, enabling the platforms to change out major or minor inserts as needed to support differing elevations along the SLS vehicle or to adapt to another vehicle altogether.
The platform halves are installed in Towers E and F and attached to rail beams that provide structural support and the ability to move vertically in one-foot increments. Each half contains independent drive mechanisms, programmed to retract and extend via a single operator’s input.
Each platform rides on four Hillman roller systems on each side — much like how a kitchen drawer glides in and out. Dual articulating energy chains are used to provide pneumatics, fire protection, electrical and communication cabling throughout translation.
Depending upon where platforms are located, workers are able to access platforms from level elevator landings. In the event of an emergency, however, everyone needs to evacuate to a 2-hour fire-rated enclosure of the building’s stairs. To accomplish this, RS&H designed movable ramps and corridors to connect to the platforms, no matter where they may be positioned.
“Every lighting connection, every electrical connection, every compressed air connection, every fire protection connection had to have flexibility built in,” Nelson said. “As a result, everything – . moveable ramps, corridors. electricity, fire, hydraulics, lighting, pneumatics, water, everything – had to be flexible.”
The platforms have already processed the Artemis One mission, and more are likely on the way for the VAB, Kline said.
Activity continues to move at a blistering pace inside the VAB. With construction on the building and the rockets inside it happening concurrently, scheduling becomes paramount.
“So we're constructing a rocket to go into space, but we're also modifying the building at the same time,” Kline said. “We have to just look at the schedule and see who takes priority – of course, the rocket always wins there.
“We just work through the conflicts and try to give (construction crews) space where we can, but again, the rocket comes first. So they have to work around us a lot of times. And we keep a close eye on the schedule for everybody.”
A building made out of so much steel changes its shape and dimensions daily in the Florida heat, which must be taken into account on any project within.
“The whole building does sway and it also expands and contracts in the heat of the day; it'll expand, and then at night it will retract up to 6 inches,” Kline said.
Air conditioning is also ineffective in a building with so much volume.
“It gets very hot, but there are roof louvers that we can open that help the hot air escape, and we also open the big doors at the top,” Kline said. “It's 450 feet to the top of that door, so we can open that top door, and it lets the breeze come through, but you know, it is a continuing safety message to tell people to stay hydrated because it does get hot in here.”
The office may be hot and hectic, but Kline wouldn’t have it any other way.
“I very much enjoy my job integrating things here in the VAB and keeping track of everybody and helping everybody get their work done,” she said. “It's a great job!”